弹簧的热处理
弹簧热处理工艺流程
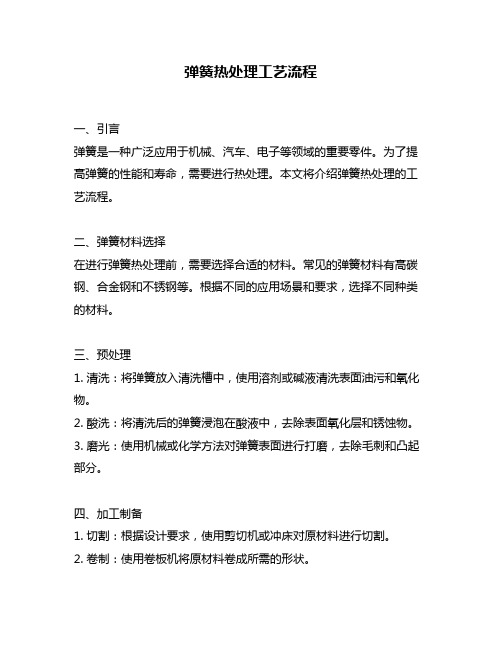
弹簧热处理工艺流程一、引言弹簧是一种广泛应用于机械、汽车、电子等领域的重要零件。
为了提高弹簧的性能和寿命,需要进行热处理。
本文将介绍弹簧热处理的工艺流程。
二、弹簧材料选择在进行弹簧热处理前,需要选择合适的材料。
常见的弹簧材料有高碳钢、合金钢和不锈钢等。
根据不同的应用场景和要求,选择不同种类的材料。
三、预处理1. 清洗:将弹簧放入清洗槽中,使用溶剂或碱液清洗表面油污和氧化物。
2. 酸洗:将清洗后的弹簧浸泡在酸液中,去除表面氧化层和锈蚀物。
3. 磨光:使用机械或化学方法对弹簧表面进行打磨,去除毛刺和凸起部分。
四、加工制备1. 切割:根据设计要求,使用剪切机或冲床对原材料进行切割。
2. 卷制:使用卷板机将原材料卷成所需的形状。
3. 预成形:将卷好的原材料放入预成形机中,进行初步成型。
4. 终成形:将预成形后的弹簧放入终成形机中,进行最终成型。
五、热处理1. 固溶处理:将弹簧放入固溶炉中,加热至固溶温度。
保持一定时间后,快速冷却至室温。
此过程可以消除材料内部的应力和组织不均匀性。
2. 淬火处理:将固溶后的弹簧放入淬火槽中,快速冷却至室温。
此过程可以提高弹簧的硬度和韧性。
3. 回火处理:将淬火后的弹簧放入回火炉中,加热至回火温度。
保持一定时间后,快速冷却至室温。
此过程可以改善弹簧的韧性和塑性。
六、表面处理1. 酸洗:将经过热处理的弹簧浸泡在酸液中,去除表面氧化层和锈蚀物。
2. 磨光:使用机械或化学方法对弹簧表面进行打磨,去除毛刺和凸起部分。
3. 镀层:根据需要,可以对弹簧表面进行镀铬、镀锌等处理,提高其耐腐蚀性。
七、质量检验1. 外观检查:对弹簧的外观进行检查,包括尺寸、形状、表面质量等。
2. 力学性能测试:对弹簧的硬度、韧性等力学性能进行测试。
3. 化学成分分析:对弹簧材料的化学成分进行分析。
八、包装运输将经过质量检验的弹簧进行包装,标注相关信息,并进行运输。
九、总结弹簧热处理是提高弹簧性能和寿命的重要工艺。
弹簧的热处理

, 沉淀硬化的不锈钢钢丝 , 钢
带和铜镍合金材料以冷成形工艺制作的弹簧 ,成形后需进行时效硬化处理 .
第三种 ,凡是用热成型和以退火材料冷卷的弹簧,均需进行淬火回火处理。
弹簧的淬火和回火
1 弹簧的淬火 淬火就是把钢加热到临界温度A C3 或 AC1 以上保温一定时间,使其奥氏体化,再以大于临界了冷却速度急剧了冷却,从而获
性 , 并采用高温快速加热的方法 , 对中小弹簧 , 可用脱氧良好的盐浴炉进行淬火加热 .
弹簧淬火宜在油中冷却 , 以避免变形和开裂 . 用尺寸较大的碳钢材料制造的弹簧 , 当
要求不高时 , 可用水冷 . 为了减小变形量 , 除了采用正确的加热和冷却方法外
, 有时还采用专用淬火夹具进行
成形淬火 , 例如板簧在弯板机上淬火 , 中 , 小型螺旋弹簧装在心轴上或专用夹具上进行加
50CrVA
820± 10
820± 10
870± 10 870± 10 850± 10
320--340 270
320--340 290 260 300
15--20 15
15--20 30 60 30
46--48 52--54 46--48
52 55--57
52
表 5--8 螺旋压缩弹簧轴心线对两端面的垂直度允许偏差
得马氏体组织的热处理方法。
对于一般热卷螺旋的弹簧,热弯板簧以及热冲压的蝶形弹簧,最好是在热成之后, 利用其余热立即淬火。这样可以省去一次加热,减少弹簧的氧化脱碳程度,既经济又改
善了弹簧的表面质量。例如 60Si2MnA 钢板弹簧目前采用的热处理工艺是在 900— 925℃
弯片之后,在 850— 880℃入油淬火。若受条件限制,也可在成形之后重新加热淬火。
弹簧的材料及热处理

弹簧的材料作为弹性元件的功能材料,高弹性无疑是材料最重要的性能;同时,由于弹簧通常是在变应力的条件下工作,从而要求材料具有优越的耐疲劳性能。
另外,为了便于加工成形,减少突然性的失效,材料应具有足够的塑性和韧性。
弹簧制造最初是采用木、竹类等天然材料,进入工业化时代后,金属材料开始广泛应用于弹簧制造领域。
随着机械产品功能的不断扩展,性能指标的不断提高,对弹簧的要求也不断提高,逐步形成了各类特殊的、专用的弹簧材料。
目前用量最大、用途最广的弹簧材料当属弹簧钢,弹簧钢具有高强度、高屈强比的特性。
为满足特殊工况的使用要求,不锈弹簧钢及特殊耐高温、恒弹性合金等材料也开始用于弹簧制造,大大地拓宽了金属弹簧的选材范围。
在非金属材料方面,近年来随着化学橡胶工业地快速发展,橡胶、聚胺酯类和增强型塑料材料也广泛被应用于弹簧产品,并在减振、降噪音等领域得到广泛应用;以氮气或气液为介质的空气弹簧也广泛应用于冲压模具、主机减振、恒力器具、超高温弹性结构等领域;陶瓷材料具有耐高温(800℃以上)、耐腐蚀、耐磨损等特殊性能,也开始作为弹簧材料在一些场合应用。
弹簧材料的种类主要分为金属材料和非金属材料两大类。
主要讲下金属材料,常用的金属弹簧材料如下所示:弹簧钢碳素弹簧钢:典型牌号有70、65Mn、T8等合金弹簧钢:典型牌号有SOCrV、55CrSi、60Si2Mn等弹簧用不锈钢:典型牌号有12Cr18Ni9、06Cr19Ni9、07Cr17Ni7A1等弹性合金铜合金:锡青铜、硅青铜、鼓青铜、白铜和黄铜镍及镍合金:纯镍、镍铜合金、镍钻合金、镍铭合金其他特殊合金:高速工具钢、弹性元件用合金、记忆合金等钢的热处理原理热处理工艺是将钢在固体下加温到指定的温度,隔热保温必须的时长,之后以指定的方法降温到室内温度的这种热处理。
热处理的功效:提高材料使用性能和工艺性能,多方面挖保温掘原材料的潜能,增加部件的应用寿命,提高产品品质。
除此之外,也可以除掉材料经锻造、铸造、电焊等工艺导致的各种各样瑕疵、优化品粒、清除残余奥氏体、减小残余应力,使组织和特性更为均匀。
弹簧热处理常见的问题及预防

弹簧热处理常见的问题及预防热处理是指材料在固态下,通过加热、保温和冷却的手段,以获得预期组织和性能的一种金属热加工工艺。
而在弹簧的热处理过程中会出现这样那样的问题,那么我们该如何预防那些问题的出现呢?弹簧热处理常见问题一:开裂和变形弹簧淬火后的开裂和变形是热应力和组织应力共同作用的综合结果。
热应力是弹簧在淬火加热和冷却的过程中材料表面和内部存在温差造成热胀冷缩不一致造成的。
组织应力是由于奥氏体和其转变产物的比容不同以及弹簧的表里各部分之间的组织转变时间不同造成的内应力。
热应力的特点是弹簧表面受到压应力,内部受到拉应力。
组织应力的特点是弹簧表面受限时发生永久变形,如果超过强度极限,弹簧机会开裂。
一般说,大多数弹簧的线径都比较细,热应力相对比较小,占主要的组织应力,尤其有些弹簧在水淬以后组织应力很大,如控制不当容易造成开裂。
预防淬火裂纹,从热处理方面应该减少内应力着手,在淬火的过程中注意一下几点:(1)过热倾向较大的弹簧材料如65Mn,Si-Mn系弹簧钢,加热温度不宜取的太高,以免过热。
(2)在保证淬透的情况下,尽量使用冷却性能温和的介质。
对线径较粗,油淬不能淬透,要改用水淬的弹簧,加热温度可以适当降低20-40℃,水冷到250℃左右即可出水空冷,以减少组织应力。
(3)淬火后的弹簧要及时回火,水淬的弹簧最好能立即回火,油淬弹簧一般也应在8h内回火完毕,一时来不及回火的弹簧应先进行一次低温消除应力回火。
弹簧和其他刚性零件不同,柔度大,加热时容易变形,为减少变形,可使用淬火压床进行定型淬火,在回火时则可采用定型夹具,套芯棒、管子或对弹簧间距加入楔子等办法把变形矫正后回火。
弹簧热处理常见问题二:过热和过烧淬火加热温度过高或在高温下停留的时间过长,都会使奥氏体晶粒粗大,淬火后得到粗针状的马氏体组织,甚至出现魏氏组织,弹簧过热后脆性上升,疲劳性能下降,容易形成淬火裂纹,或弹簧早期失效。
弹簧过热后可以通过细化晶粒的退火予以补救。
热处理中的弹簧热处理技术

热处理中的弹簧热处理技术弹簧热处理技术是热处理行业中非常具有代表性的一种技术。
在现代工业制造中,弹簧作为一种重要的弹力元件,广泛应用于各个领域,而弹簧的弹性、耐疲劳和寿命等等特性都会直接影响到弹簧在实际生产中的稳定性和可靠性。
因此,为了提高弹簧在使用时的性能,人们常常使用热处理技术进行加工。
在本文中,我们将重点探究弹簧热处理技术的相关知识。
1. 弹簧的热处理目的弹簧的热处理可以显著改善其力学性能和疲劳寿命。
一般来说,弹簧的热处理目的是提高弹性模量、硬度和强度,同时降低塑性变形、蠕变、疲劳破坏等不良现象的发生。
此外,通过热处理,还可以控制弹簧的形状和尺寸,并提高表面质量和耐腐蚀性,以满足实际应用的需要。
2. 弹簧的热处理方法(1)淬火淬火是一种常见的弹簧热处理方法。
通过加热弹簧至一定温度,并迅速冷却,可以使弹簧的结构发生改变,从而提高其硬度和强度。
不过,淬火后的弹簧普遍具有较高的脆性和低的韧性,对于某些特殊要求的弹簧来说并不适用。
(2)回火回火通常是在淬火之后进行的一种调质工艺,也是常用的一种弹簧热处理方法。
通过将淬火后的弹簧重新加热至一定温度,并缓慢冷却,可以降低其脆性、提高韧性和弹性模量。
通过回火,可以使弹簧达到既有硬度又有韧性的最佳状态,从而提高其疲劳寿命和可靠性。
(3)冷加工变形冷加工变形是指在室温下对弹簧进行轻微变形的一种处理方法。
通过适当的冷加工变形,可以使弹簧的表面产生一定的压应力和残余应力,从而提高其疲劳寿命和耐蠕变能力。
此外,冷加工变形还可以使弹簧的尺寸稳定性更好,使其在使用时更加稳定可靠。
3. 热处理中的注意事项虽然弹簧热处理技术可以显著提高弹簧的性能和寿命,但在实际操作中也需要注意一些问题。
(1)温度控制弹簧热处理的温度控制非常关键,温度过高或过低都会影响热处理的效果。
因此,在进行弹簧热处理时,一定要掌握好热处理温度,尽量减少温度波动和温度差异。
(2)冷却速度弹簧热处理中的冷却速度也非常重要,不同的材料和不同的热处理工艺也需要不同的冷却速度,过慢或过快的冷却都会影响热处理效果。
304弹簧热处理

304弹簧热处理弹簧的基本概念和应用领域弹簧是一种能够在受到外力作用时发生弹性变形并能恢复原状的机械元件。
它广泛应用于各个领域,包括工业制造、交通运输、家居家具等。
弹簧的主要作用是储存和释放能量,用于吸收冲击、控制振动、保持连接等。
304不锈钢的特性和应用304不锈钢是一种常见的不锈钢材料,具有良好的耐腐蚀性、耐高温性和良好的加工性能。
它广泛应用于食品加工、化工、医疗器械、建筑装饰等领域。
304不锈钢弹簧由于其优良的性能,被广泛应用于汽车制造、电器制造、机械制造等行业。
304弹簧的热处理工艺热处理是指通过加热和冷却等工艺操作,改变材料的组织结构和性能。
对于304不锈钢弹簧的热处理,主要包括退火、固溶处理和时效处理。
退火处理退火是指将材料加热到一定温度,保持一定时间后缓慢冷却的过程。
退火处理可以消除材料内部的应力,改善材料的塑性和韧性。
对于304不锈钢弹簧,退火处理可以提高其延展性和弹性,减少弹簧在使用过程中的变形和断裂。
固溶处理固溶处理是指将材料加热到固溶温度,保持一定时间后迅速冷却的过程。
固溶处理可以使材料中的固溶体达到均匀分布,提高材料的强度和硬度。
对于304不锈钢弹簧,固溶处理可以提高其抗拉强度和硬度,使其更适合承受较大的载荷。
时效处理时效处理是指将材料加热到一定温度,保持一定时间后再进行冷却的过程。
时效处理可以使材料中的析出相达到最佳状态,提高材料的强度和耐腐蚀性。
对于304不锈钢弹簧,时效处理可以提高其抗氧化和耐腐蚀性能,延长其使用寿命。
304弹簧热处理的工艺参数在进行304弹簧热处理时,需要注意以下工艺参数的选择:温度热处理温度是影响材料组织和性能的重要参数。
对于304不锈钢弹簧的退火处理,一般选择800-900℃的温度范围;固溶处理一般选择1050-1150℃的温度范围;时效处理一般选择500-600℃的温度范围。
时间热处理时间是影响材料组织和性能的另一个重要参数。
对于304不锈钢弹簧的退火处理,一般选择1-2小时的时间;固溶处理一般选择30分钟到1小时的时间;时效处理一般选择2-4小时的时间。
65锰弹簧热处理硬度

65锰弹簧热处理硬度一、概述65锰弹簧是一种常见的弹簧材料,主要由碳、锰等元素组成。
为了提高其硬度和强度,常对65锰弹簧进行热处理。
热处理是通过加热和冷却工艺来改变材料的组织结构和性能的过程。
二、热处理工艺65锰弹簧的热处理工艺主要包括加热、保温和冷却三个步骤。
1. 加热加热是将65锰弹簧材料经过加热炉加热到一定温度范围内的过程。
加热温度的选择需要根据弹簧的要求和材料的特性来确定。
一般来说,加热温度较高,会使得弹簧的硬度和强度提高,但也容易导致材料的塑性降低。
而低温加热则会使得弹簧的硬度和强度降低,但塑性增加。
2. 保温保温是指将加热后的65锰弹簧材料在一定温度下保持一段时间的过程。
保温时间的长短也是根据具体要求来确定的。
保温时间过短会影响材料的组织结构的转变,保温时间过长则会导致材料的晶粒长大,从而影响材料的性能。
3. 冷却冷却是将保温后的65锰弹簧材料迅速冷却到室温或其他指定的温度范围内的过程。
冷却方式有多种,如水淬、油淬、空冷等。
冷却速度的快慢对材料的性能有重要的影响,通常快速冷却可以得到较高的硬度,而慢速冷却则可以提高材料的韧性。
三、热处理硬度影响因素65锰弹簧的热处理硬度受多个因素的影响。
1. 原材料成分弹簧的硬度受其原材料的成分影响,特别是碳和锰的含量。
一般来说,碳含量越高,弹簧的硬度和强度越高,但塑性会降低。
而锰的含量主要影响弹簧的韧性,适量的锰可以提高弹簧的韧性。
2. 热处理工艺参数热处理工艺参数的选择对于弹簧的硬度也有重要的影响。
加热温度、保温时间和冷却速度等参数都需要经过实验和调整来确定。
不同的工艺参数会导致材料组织结构的不同以及硬度和韧性等性能的变化。
3. 材料的组织结构材料的组织结构是决定其硬度的重要因素之一。
经过热处理后,65锰弹簧的组织结构通常为马氏体。
马氏体具有较高的硬度,但也容易产生脆性。
因此,在热处理过程中需要控制马氏体的形成和分布,以获得适当的硬度和韧性。
四、热处理硬度测试方法热处理后的65锰弹簧硬度的测试可以采用多种方法。
弹簧的热处理
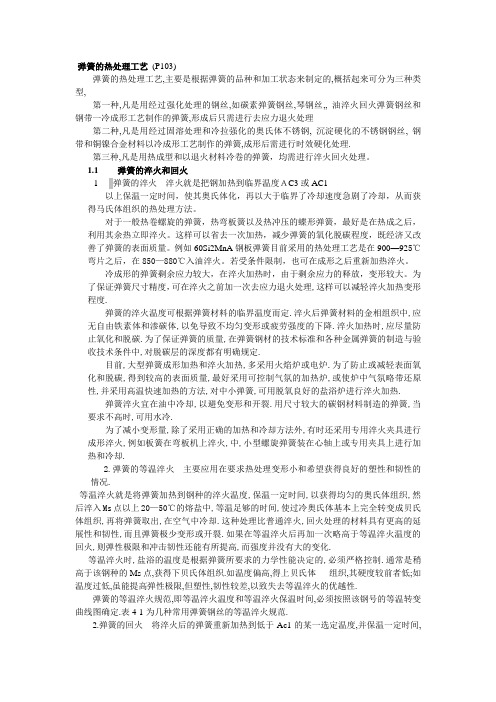
弹簧的热处理工艺(P103)弹簧的热处理工艺,主要是根据弹簧的品种和加工状态来制定的,概括起来可分为三种类型,第一种,凡是用经过强化处理的钢丝,如碳素弹簧钢丝,琴钢丝,, 油淬火回火弹簧钢丝和钢带一冷成形工艺制作的弹簧,形成后只需进行去应力退火处理第二种,凡是用经过固溶处理和冷拉强化的奥氏体不锈钢, 沉淀硬化的不锈钢钢丝, 钢带和铜镍合金材料以冷成形工艺制作的弹簧,成形后需进行时效硬化处理.第三种,凡是用热成型和以退火材料冷卷的弹簧,均需进行淬火回火处理。
1.1弹簧的淬火和回火1弹簧的淬火淬火就是把钢加热到临界温度AC3或AC1以上保温一定时间,使其奥氏体化,再以大于临界了冷却速度急剧了冷却,从而获得马氏体组织的热处理方法。
对于一般热卷螺旋的弹簧,热弯板簧以及热冲压的蝶形弹簧,最好是在热成之后,利用其余热立即淬火。
这样可以省去一次加热,减少弹簧的氧化脱碳程度,既经济又改善了弹簧的表面质量。
例如60Si2MnA钢板弹簧目前采用的热处理工艺是在900—925℃弯片之后,在850—880℃入油淬火。
若受条件限制,也可在成形之后重新加热淬火。
冷成形的弹簧剩余应力较大,在淬火加热时,由于剩余应力的释放,变形较大。
为了保证弹簧尺寸精度,可在淬火之前加一次去应力退火处理,这样可以减轻淬火加热变形程度.弹簧的淬火温度可根据弹簧材料的临界温度而定.淬火后弹簧材料的金相组织中,应无自由铁素体和渗碳体,以免导致不均匀变形或疲劳强度的下降.淬火加热时,应尽量防止氧化和脱碳.为了保证弹簧的质量,在弹簧钢材的技术标准和各种金属弹簧的制造与验收技术条件中,对脱碳层的深度都有明确规定.目前,大型弹簧成形加热和淬火加热,多采用火焰炉或电炉.为了防止或减轻表面氧化和脱碳,得到较高的表面质量,最好采用可控制气氛的加热炉,或使炉中气氛略带还原性,并采用高温快速加热的方法,对中小弹簧,可用脱氧良好的盐浴炉进行淬火加热.弹簧淬火宜在油中冷却,以避免变形和开裂.用尺寸较大的碳钢材料制造的弹簧,当要求不高时,可用水冷.为了减小变形量,除了采用正确的加热和冷却方法外,有时还采用专用淬火夹具进行成形淬火,例如板簧在弯板机上淬火,中,小型螺旋弹簧装在心轴上或专用夹具上进行加热和冷却.2.弹簧的等温淬火主要应用在要求热处理变形小和希望获得良好的塑性和韧性的情况.等温淬火就是将弹簧加热到钢种的淬火温度,保温一定时间,以获得均匀的奥氏体组织,然后淬入Ms点以上20—50℃的熔盐中,等温足够的时间,使过冷奥氏体基本上完全转变成贝氏体组织,再将弹簧取出,在空气中冷却.这种处理比普通淬火,回火处理的材料具有更高的延展性和韧性,而且弹簧极少变形或开裂.如果在等温淬火后再加一次略高于等温淬火温度的回火,则弹性极限和冲击韧性还能有所提高,而强度并没有大的变化.等温淬火时,盐浴的温度是根据弹簧所要求的力学性能决定的,必须严格控制.通常是稍高于该钢种的Ms点,获得下贝氏体组织.如温度偏高,得上贝氏体组织,其硬度较前者低;如温度过低,虽能提高弹性极限,但塑性,韧性较差,以致失去等温淬火的优越性.弹簧的等温淬火规范,即等温淬火温度和等温淬火保温时间,必须按照该钢号的等温转变曲线图确定.表4-1为几种常用弹簧钢丝的等温淬火规范.2.弹簧的回火将淬火后的弹簧重新加热到低于Ac1的某一选定温度,并保温一定时间,然后以适宜的冷却速度冷却的工艺方法,叫做回火.回火的目的是:获得所需要的力学性能,稳定弹簧的组织和尺寸以及消除内应力.表4-1 几种常用弹簧钢的等温淬火规范表1-8 美国弹簧标准名称和标准号(P20)。
弹簧材料的热处理技术
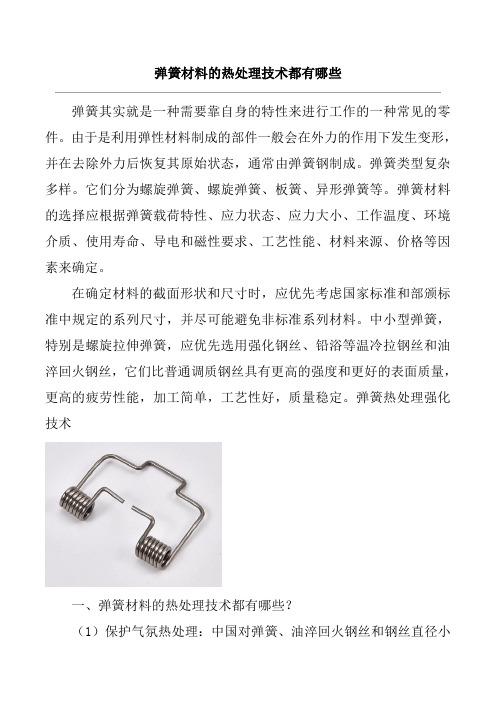
弹簧材料的热处理技术都有哪些弹簧其实就是一种需要靠自身的特性来进行工作的一种常见的零件。
由于是利用弹性材料制成的部件一般会在外力的作用下发生变形,并在去除外力后恢复其原始状态,通常由弹簧钢制成。
弹簧类型复杂多样。
它们分为螺旋弹簧、螺旋弹簧、板簧、异形弹簧等。
弹簧材料的选择应根据弹簧载荷特性、应力状态、应力大小、工作温度、环境介质、使用寿命、导电和磁性要求、工艺性能、材料来源、价格等因素来确定。
在确定材料的截面形状和尺寸时,应优先考虑国家标准和部颁标准中规定的系列尺寸,并尽可能避免非标准系列材料。
中小型弹簧,特别是螺旋拉伸弹簧,应优先选用强化钢丝、铅浴等温冷拉钢丝和油淬回火钢丝,它们比普通调质钢丝具有更高的强度和更好的表面质量,更高的疲劳性能,加工简单,工艺性好,质量稳定。
弹簧热处理强化技术一、弹簧材料的热处理技术都有哪些?(1)保护气氛热处理:中国对弹簧、油淬回火钢丝和钢丝直径小于15毫米的回火钢丝进行保护性大气热处理。
保护气氛热处理可以消除表面脱碳和氧化,提高材料的表面质量。
(2)感应加热或保护气氛感应加热热处理:这一过程通常在螺旋弹簧形成之前在金属丝上进行。
一些弹簧工厂将钢丝热处理与弹簧制造结合起来,以降低成本。
感应加热处理强化效果好,感应加热速度快,有利于细化晶粒,减少表面脱碳,能充分发挥和提高材料的强度和韧性。
(3)表面氮化热处理技术:近年来,高应力气门弹簧或其他高应力离合器弹簧也采用了表面氮化技术,以实现可靠的疲劳寿命。
更先进的技术是低温气体渗氮。
渗氮温度一般为(450 ~ 470)℃,气体渗氮时间为(5 ~ 20)小时。
弹簧喷丸强化工艺(4)组合喷丸技术:组合喷丸通常也称为多重喷丸工艺。
最经济的方法是使用二次喷丸。
这是通过用不同直径的射弹喷丸来实现的。
较大的颗粒首次用于获得残余压应力和表面光洁度。
(5)应力喷丸技术:应力喷丸也是一种相对经典的喷丸工艺,只是因为它难以应用于大规模生产,但近年来,由于应力喷丸设备的快速发展,它在大规模生产高应力汽车悬架弹簧方面取得了很大进展。
如何提高弹簧的强度和韧性
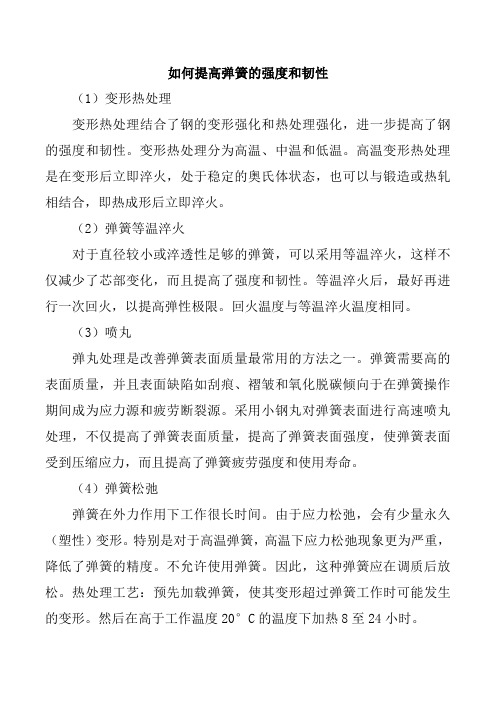
如何提高弹簧的强度和韧性
(1)变形热处理
变形热处理结合了钢的变形强化和热处理强化,进一步提高了钢的强度和韧性。
变形热处理分为高温、中温和低温。
高温变形热处理是在变形后立即淬火,处于稳定的奥氏体状态,也可以与锻造或热轧相结合,即热成形后立即淬火。
(2)弹簧等温淬火
对于直径较小或淬透性足够的弹簧,可以采用等温淬火,这样不仅减少了芯部变化,而且提高了强度和韧性。
等温淬火后,最好再进行一次回火,以提高弹性极限。
回火温度与等温淬火温度相同。
(3)喷丸
弹丸处理是改善弹簧表面质量最常用的方法之一。
弹簧需要高的表面质量,并且表面缺陷如刮痕、褶皱和氧化脱碳倾向于在弹簧操作期间成为应力源和疲劳断裂源。
采用小钢丸对弹簧表面进行高速喷丸处理,不仅提高了弹簧表面质量,提高了弹簧表面强度,使弹簧表面受到压缩应力,而且提高了弹簧疲劳强度和使用寿命。
(4)弹簧松弛
弹簧在外力作用下工作很长时间。
由于应力松弛,会有少量永久(塑性)变形。
特别是对于高温弹簧,高温下应力松弛现象更为严重,降低了弹簧的精度。
不允许使用弹簧。
因此,这种弹簧应在调质后放松。
热处理工艺:预先加载弹簧,使其变形超过弹簧工作时可能发生的变形。
然后在高于工作温度20°C的温度下加热8至24小时。
弹簧热处理工艺和过程
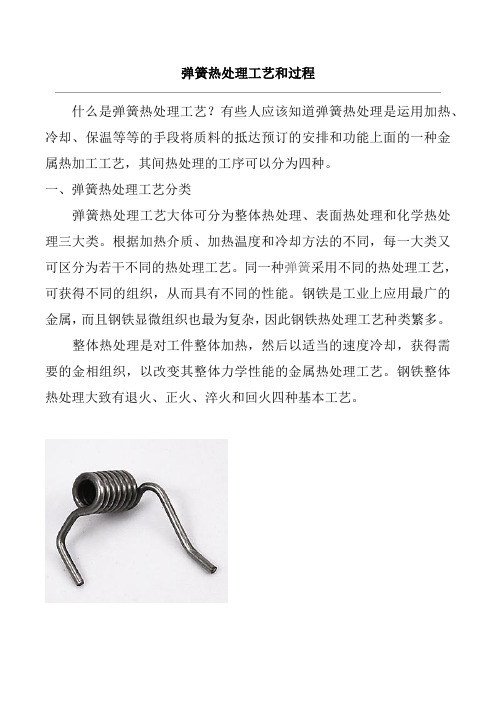
弹簧热处理工艺和过程什么是弹簧热处理工艺?有些人应该知道弹簧热处理是运用加热、冷却、保温等等的手段将质料的抵达预订的安排和功能上面的一种金属热加工工艺,其间热处理的工序可以分为四种。
一、弹簧热处理工艺分类弹簧热处理工艺大体可分为整体热处理、表面热处理和化学热处理三大类。
根据加热介质、加热温度和冷却方法的不同,每一大类又可区分为若干不同的热处理工艺。
同一种弹簧采用不同的热处理工艺,可获得不同的组织,从而具有不同的性能。
钢铁是工业上应用最广的金属,而且钢铁显微组织也最为复杂,因此钢铁热处理工艺种类繁多。
整体热处理是对工件整体加热,然后以适当的速度冷却,获得需要的金相组织,以改变其整体力学性能的金属热处理工艺。
钢铁整体热处理大致有退火、正火、淬火和回火四种基本工艺。
二、弹簧热处理工艺过程弹簧热处理工艺一般包括加热、保温、冷却三个过程,有时只有加热和冷却两个过程。
这些过程互相衔接,不可间断。
弹簧加热是热处理的重要工序之一。
弹簧热处理的加热方法很多,最早是采用木炭和煤作为热源,近而应用液体和气体燃料。
电的应用使加热易于控制,且无环境污染。
利用这些热源可以直接加热,也可以通过熔融的盐或金属,以至浮动粒子进行间接加热。
弹簧加热时,工件暴露在空气中,常常发生氧化、脱碳(即钢铁零件表面碳含量降低),这对于热处理后零件的表面性能有很不利的影响。
因而金属通常应在可控气氛或保护气氛中、熔融盐中和真空中加热,也可用涂料或包装方法进行保护加热。
加热温度是热处理工艺的重要工艺参数之一,选择和控制加热温度,是保证热处理质量的主要问题。
加热温度随被处理的金属材料和热处理的目的不同而异,但一般都是加热到相变温度以上,以获得高温组织。
另外转变需要一定的时间,因此当金属工件表面达到要求的加热温度时,还须在此温度保持一定时间,使内外温度一致,使显微组织转变完全,这殌时间称为保温时间。
采用高能密度加热和表面热处理时,加热速度极快,一般就没有保温时间,而化学热处理的保温时间往往较长。
弹簧的热处理(一)

弹簧的热处理(一)来源:每天学点热处理弹簧及弹性元件,是量大面广的基础零件,可以说是无处不在。
在动力机械、电器、仪表、武器中作为控制性元件,也是非常关键的零件。
它的基本功能是利用材料的弹性和弹簧的结构特点,在产生及恢复变形时,可以把机械功或动能转换为形变能,或者把形变能转换为动能或机械功,以达到缓冲或减振、控制运动或复位、储能或测量等目的。
所以,在各类机械设备、仪器仪表、军工产品、电器、家具、家电甚至文具、玩具中都广泛使用弹簧。
影响弹簧质量和使用寿命的因素很多,如设计、选材、生产工艺及工况条件等等。
其中,材质和热处理对弹簧的各种性能及其使用寿命有重要的甚至是决定性的影响。
本文分四个主题,分别介绍各类机械设备中常用的弹簧材料和典型弹簧的热处理,对于特殊用途的弹性材料和元件的热处理只做扼要介绍。
一、弹簧的分类、服役条件、失效方式和性能要求1 弹簧分类弹簧种类很多,可按形状、承载特点、制造方法、材料成分和不同用途进行分类。
每一类中又分为若干小类和不同规格。
GB/T1805弹簧的标准中列出了22种,弹簧行业1990年提出的内部标准《弹簧种类》中,把弹簧分为15个小类。
弹簧行业多按形状分类,在机械制造业中多按用途分类或按上述两者综合命名。
如表1 。
▼表1 弹簧的分类典型螺旋弹簧及板簧如图1所示。
▲图1 典型螺旋弹簧及板簧2 弹簧的服役条件和失效形式2.1 弹簧的服役条件和应力状态弹簧的服役条件是指它的工作环境(温度和介质)及应力状态等因素。
工作温度可分为低温(室温以下)、室温、较高温(120℃~350℃)、高温(350℃以上)几个档次。
工作环境介质有空气、水蒸气、雨水、燃烧产物、以及酸、碱水溶液等。
普通机械弹簧一般是在室温或较高工作温度、大气条件下承受载荷。
也有用于耐蚀、承受高应力等各种特殊用途的弹簧。
工作持续时间也是一个值得考虑的重要因素。
▲气门弹簧是要求最严苛的弹簧之一弹簧的载荷特性由弹簧变形时的载荷(P或T)与变形(F或)之间的关系曲线表示。
弹簧热处理的工序及详细过程
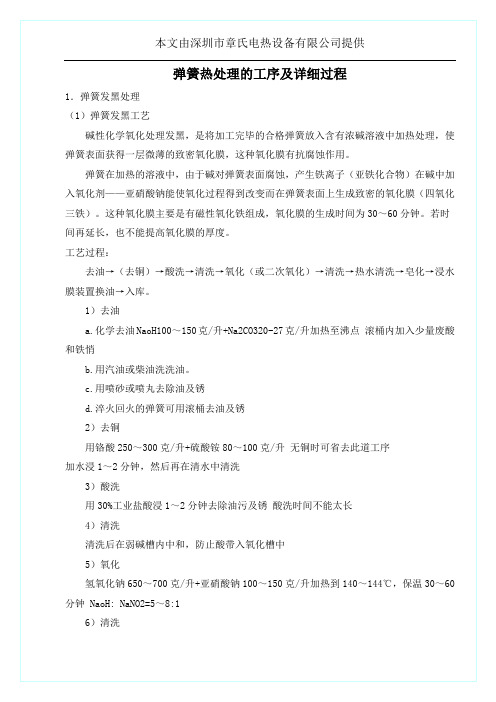
9)磷化槽添加磷酸锰铁盐与硝酸锌按1:2,钝化槽中的废重铬酸钾要集中统一处理,皂化槽中要经常补充皂片或三乙油酸皂。
10)若不要钝化时,可省去操作规程Ⅵ。
11)磷化前弹簧的喷沙、喷丸清理与磷化的间隔不得超过4小时,清理好后弹簧必须放入清洁的料框内。
(3)磷化质量检验方法
3)清洗
自来水冲洗去除酸性
4)磷化
磷酸锰铁盐30~35克/升,硝酸锌55~75克/升温度70~80℃保温10~15分钟,总酸度48~60游离酸2.5~6.7硫酸根≦0.5
5)清洗
自来水冲洗
6)钝化
重铬酸钾(K2Cr2O2)80~100克/升 90~100℃
7)清洗
自来水冲洗
8)清洗
热水90~100℃清洗1~2分钟
1)浸泡法
3%氯化钠NaCl,温度15~25℃,浸2小时无锈为合格。
2)点滴法之一
硫酸铜CuSO20.5N 40毫克氯化钠Nacl10% 20毫克,硫酸。0.1N0.8毫克。
点滴后不起黄时间越长质量越好,3分钟内不变色者为合格。
3)点滴法之二
硫酸铜CuSO4、SH20 66克/升,氯化钠NaCL32.5克/升,盐酸HCL 1:10 1.2克/升,点滴3分钟以上不发黄者为合格。
4)浸泡法
硫酸铜5%溶液,浸1分钟后工件表面不出现黄色为合格。
在检验工件磷化质量的同时,必须对磷化槽液进行定期化验总酸度、游离酸、酸根参数以确保日常的工件磷化质量。
3)按发黑工艺技术要求加入一定量亚硝酸钠(符合5~8:1);
4)用温度计测量发黑槽液湿度,确保槽液温度140~144℃,若温度过高要加水,并控制好加热电源;
5)发黑前,弹簧必须经充分的酸洗和清洗,拉力弹簧必须垂直装框,便于清洗;
弹簧热处理及强压立定工艺
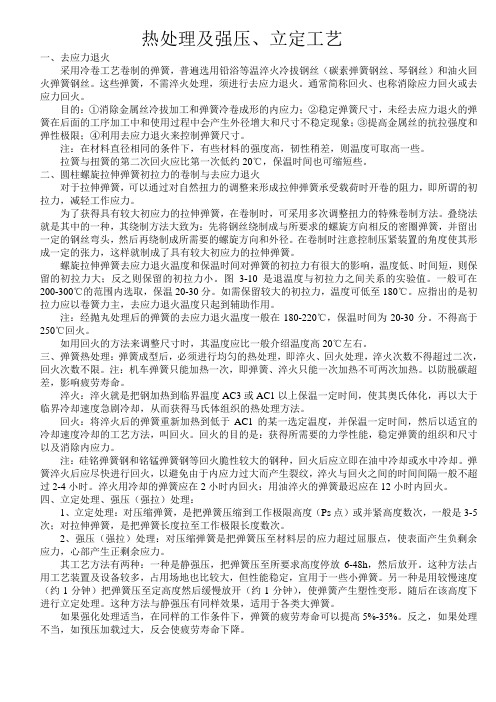
热处理及强压、立定工艺一、去应力退火采用冷卷工艺卷制的弹簧,普遍选用铅浴等温淬火冷拔钢丝(碳素弹簧钢丝、琴钢丝)和油火回火弹簧钢丝。
这些弹簧,不需淬火处理,须进行去应力退火。
通常简称回火、也称消除应力回火或去应力回火。
目的:①消除金属丝冷拔加工和弹簧冷卷成形的内应力;②稳定弹簧尺寸,未经去应力退火的弹簧在后面的工序加工中和使用过程中会产生外径增大和尺寸不稳定现象;③提高金属丝的抗拉强度和弹性极限;④利用去应力退火来控制弹簧尺寸。
注:在材料直径相同的条件下,有些材料的强度高,韧性稍差,则温度可取高一些。
拉簧与扭簧的第二次回火应比第一次低约20℃,保温时间也可缩短些。
二、圆柱螺旋拉伸弹簧初拉力的卷制与去应力退火对于拉伸弹簧,可以通过对自然扭力的调整来形成拉伸弹簧承受载荷时开卷的阻力,即所谓的初拉力,减轻工作应力。
为了获得具有较大初应力的拉伸弹簧,在卷制时,可采用多次调整扭力的特殊卷制方法。
叠绕法就是其中的一种,其绕制方法大致为:先将钢丝绕制成与所要求的螺旋方向相反的密圈弹簧,并留出一定的钢丝弯头,然后再绕制成所需要的螺旋方向和外径。
在卷制时注意控制压紧装置的角度使其形成一定的张力,这样就制成了具有较大初应力的拉伸弹簧。
螺旋拉伸弹簧去应力退火温度和保温时间对弹簧的初拉力有很大的影响,温度低、时间短,则保留的初拉力大;反之则保留的初拉力小。
图3-10是退温度与初拉力之间关系的实验值。
一般可在200-300℃的范围内选取,保温20-30分。
如需保留较大的初拉力,温度可低至180℃。
应指出的是初拉力应以卷簧力主,去应力退火温度只起到辅助作用。
注:经抛丸处理后的弹簧的去应力退火温度一般在180-220℃,保温时间为20-30分。
不得高于250℃回火。
如用回火的方法来调整尺寸时,其温度应比一般介绍温度高20℃左右。
三、弹簧热处理:弹簧成型后,必须进行均匀的热处理,即淬火、回火处理,淬火次数不得超过二次,回火次数不限。
弹簧和紧固件的热处理
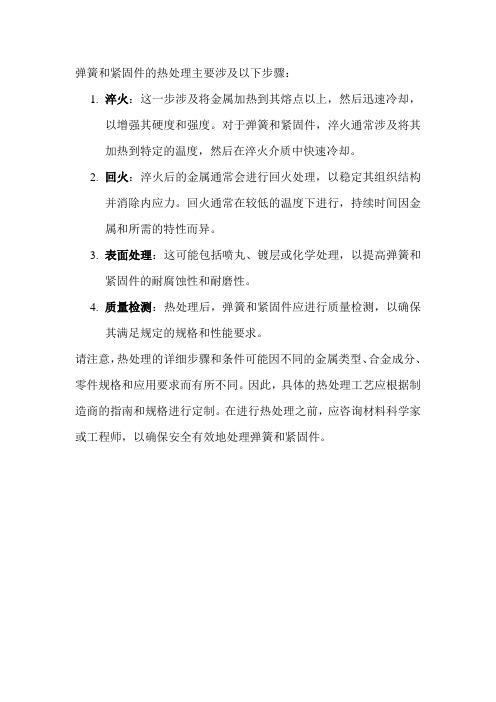
弹簧和紧固件的热处理主要涉及以下步骤:
1.淬火:这一步涉及将金属加热到其熔点以上,然后迅速冷却,
以增强其硬度和强度。
对于弹簧和紧固件,淬火通常涉及将其
加热到特定的温度,然后在淬火介质中快速冷却。
2.回火:淬火后的金属通常会进行回火处理,以稳定其组织结构
并消除内应力。
回火通常在较低的温度下进行,持续时间因金
属和所需的特性而异。
3.表面处理:这可能包括喷丸、镀层或化学处理,以提高弹簧和
紧固件的耐腐蚀性和耐磨性。
4.质量检测:热处理后,弹簧和紧固件应进行质量检测,以确保
其满足规定的规格和性能要求。
请注意,热处理的详细步骤和条件可能因不同的金属类型、合金成分、零件规格和应用要求而有所不同。
因此,具体的热处理工艺应根据制造商的指南和规格进行定制。
在进行热处理之前,应咨询材料科学家或工程师,以确保安全有效地处理弹簧和紧固件。
弹簧热处理硬度要求

弹簧热处理硬度要求一、工作条件以及材料及热处理要求1.条件: 形状简单,断面较小,受力不大的弹簧要求: 65 785-815℃油淬,300℃400℃、500℃。
600℃回火,相应的硬度HB512、HB430、HB369,75,780-800℃油或水淬,400-420℃回火,HRC42-48.2.条件: 中等负荷的大型弹簧要求: 60Si2MnA 65Mn 870℃油淬,460℃回火,HRC40-45(农机座位弹簧65Mn 淬火回火 HB280-370)3.条件: 重负荷、高弹簧、高疲劳极限的大形板簧和螺旋弹簧要求: 50CrVA、60SiMnA 860℃油淬,475℃回火,HRC40-454.条件: 在多次交变负荷下工作的直径8-10mm的卷簧要求: 50CrMnA 840-870℃油淬,450-480℃回火,HB387-4185.条件: 机车、车辆、煤水车或板弹簧要求: 55SiMn、60Si2MnHRC39-45(hb363-432)(解放牌汽车板簧:55Si2Mn HB363-441)6.条件: 车辆及缓冲器螺旋弹簧、汽车张紧弹簧要求: 55Si2Mn、60Si2Mn、60Si2CrA 淬火,回火,HRC40-47或HB370-4417.条件: 柴油泵柱塞弹簧、喷油嘴弹簧、农用柴油机气阀弹簧及中型、重型汽车的气门弹簧和板弹簧要求: 50CrVA 淬火,回火,HRC40-478.条件: 在高温蒸汽下工作的卷簧和扁簧,自来水管道弹簧和耐海水浸蚀的弹簧,Φ10-25mm要求: 3Cr13 HRC39-46 4Cr13 HRC48-50 HRC48-49 HRC47-49HRC37-40 HRC31-35 HRC33-479.条件: 在酸碱介质下工作的弹簧要求: 2Cr18Ni9 1100-1150℃水淬,绕卷后消除应力,400℃回火60min,HB160-20010.条件: 弹性挡圈δ4,Φ85要求: 60Si2 400℃预热,860℃油淬,430℃回火空冷,HRC40-45.二、备注1.弹簧热处理一般要求淬透,晶粒细,残余奥氏体少.脱碳层深度每边应符合:<Φ6mm的钢丝或钢板,应<1.5%直径或厚度;>Φ6mm的钢丝钢板,应<1.0%直径或厚度.2.大型弹簧在热状态加工成型随即淬火-回火,中型弹簧在冷态加工成型(原材料要求球化组织或大部分球化),再淬火-回火.小型弹簧用冷轧钢带、冷拉钢丝等冷态加工成型后,低温回火3.处理后可经喷丸处理:40-50N/cm^2的压缩空气或离心机70m/s的线速度,将Φ0.3-0.5mm(对于小零件、汽门弹簧、齿轮等)、Φ0.6-0.8mm(对板簧、曲轴、半轴等)铸铁丸或淬硬钢丸喷射到弹簧表面,强化表层,疲劳循环次数可提高8-13倍,寿命可提高2-2.5倍以上。
弹簧钢的最终热处理应是淬火+中温回火
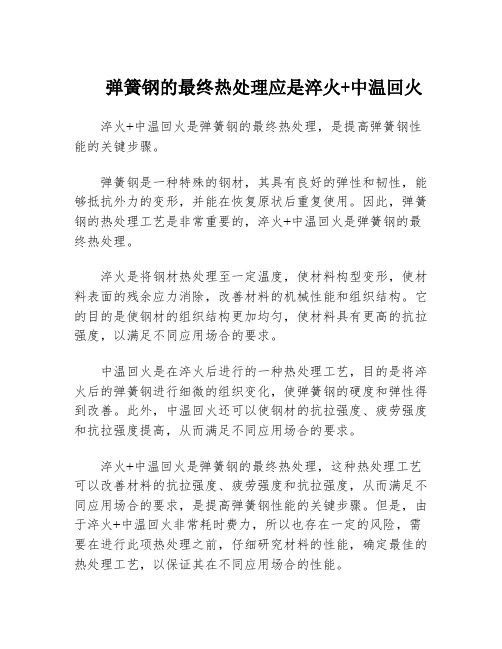
弹簧钢的最终热处理应是淬火+中温回火
淬火+中温回火是弹簧钢的最终热处理,是提高弹簧钢性能的关键步骤。
弹簧钢是一种特殊的钢材,其具有良好的弹性和韧性,能够抵抗外力的变形,并能在恢复原状后重复使用。
因此,弹簧钢的热处理工艺是非常重要的,淬火+中温回火是弹簧钢的最终热处理。
淬火是将钢材热处理至一定温度,使材料构型变形,使材料表面的残余应力消除,改善材料的机械性能和组织结构。
它的目的是使钢材的组织结构更加均匀,使材料具有更高的抗拉强度,以满足不同应用场合的要求。
中温回火是在淬火后进行的一种热处理工艺,目的是将淬火后的弹簧钢进行细微的组织变化,使弹簧钢的硬度和弹性得到改善。
此外,中温回火还可以使钢材的抗拉强度、疲劳强度和抗拉强度提高,从而满足不同应用场合的要求。
淬火+中温回火是弹簧钢的最终热处理,这种热处理工艺可以改善材料的抗拉强度、疲劳强度和抗拉强度,从而满足不同应用场合的要求,是提高弹簧钢性能的关键步骤。
但是,由于淬火+中温回火非常耗时费力,所以也存在一定的风险,需要在进行此项热处理之前,仔细研究材料的性能,确定最佳的热处理工艺,以保证其在不同应用场合的性能。
总之,淬火+中温回火是弹簧钢的最终热处理,它可以改善材料的机械性能和弹性,提高其在不同应用场合的性能,是提高弹簧钢性能的关键步骤。
但是,由于这种热处理工艺耗时费力,所以应在进行此项工艺之前,仔细研究材料的性能,确定最佳的工艺参数,以保证其在不同应用场合的性能。
弹簧的热处理质量检验的要求
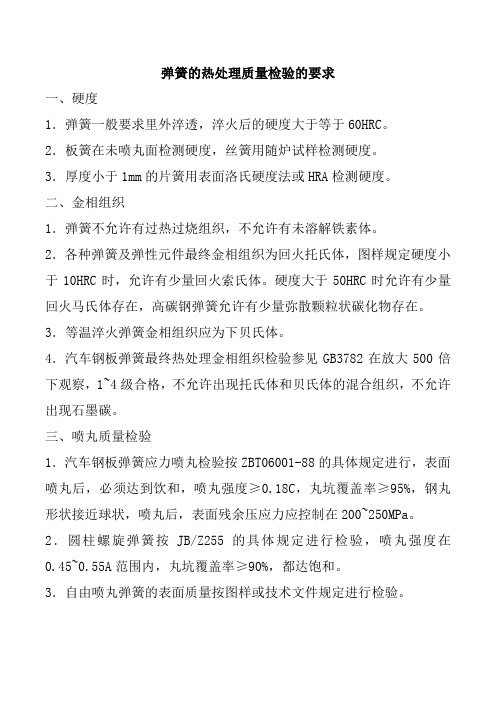
弹簧的热处理质量检验的要求一、硬度1.弹簧一般要求里外淬透,淬火后的硬度大于等于60HRC。
2.板簧在未喷丸面检测硬度,丝簧用随炉试样检测硬度。
3.厚度小于1mm的片簧用表面洛氏硬度法或HRA检测硬度。
二、金相组织1.弹簧不允许有过热过烧组织,不允许有未溶解铁素体。
2.各种弹簧及弹性元件最终金相组织为回火托氏体,图样规定硬度小于10HRC时,允许有少量回火索氏体。
硬度大于50HRC时允许有少量回火马氏体存在,高碳钢弹簧允许有少量弥散颗粒状碳化物存在。
3.等温淬火弹簧金相组织应为下贝氏体。
4.汽车钢板弹簧最终热处理金相组织检验参见GB3782在放大500倍下观察,1~4级合格,不允许出现托氏体和贝氏体的混合组织,不允许出现石墨碳。
三、喷丸质量检验1.汽车钢板弹簧应力喷丸检验按ZBT06001-88的具体规定进行,表面喷丸后,必须达到饮和,喷丸强度≥0.18C,丸坑覆盖率≥95%,钢丸形状接近球状,喷丸后,表面残余压应力应控制在200~250MPa。
2.圆柱螺旋弹簧按JB/Z255的具体规定进行检验,喷丸强度在0.45~0.55A范围内,丸坑覆盖率≥90%,都达饱和。
3.自由喷丸弹簧的表面质量按图样或技术文件规定进行检验。
四、变形检验1.最大负荷试验时试样负荷大于工作负荷一倍左右,如产生微量塑性变形,但尺寸符合技术要求者仍可使用。
2.弹簧尺寸公差,形状和位置公差的检验应在永久变形试验之后进行。
五、力学性能检验1.疲劳寿命应达到国家标准规定或图样技术要求。
2.落锤式冲击试验时,不允许有弹簧断裂。
3.冷卷弹簧钢丝应作缠绕试验、弯曲试验、扭转试验。
六、探伤1.表面或心部不允许有裂纹、孔洞,弹簧在喷丸前应进行探伤,常用磁粉探伤、荧光探伤,探后退磁。
2.奥氏体不锈钢弹簧用超声波探伤,退磁。
七、表面质量1.不允许有氧化皮、麻点、裂纹、毛刺、损伤、锈蚀、斑痕、气泡、夹杂、夹层、折叠等缺陷。
2.表面处理的弹簧,应进行耐蚀检验。
11种常见弹簧热处理工艺概念解释
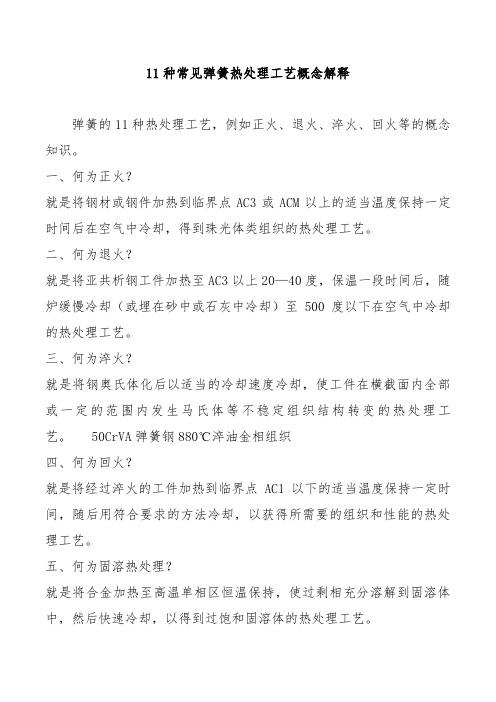
11种常见弹簧热处理工艺概念解释弹簧的11种热处理工艺,例如正火、退火、淬火、回火等的概念知识。
一、何为正火?就是将钢材或钢件加热到临界点AC3或ACM以上的适当温度保持一定时间后在空气中冷却,得到珠光体类组织的热处理工艺。
二、何为退火?就是将亚共析钢工件加热至AC3以上20—40度,保温一段时间后,随炉缓慢冷却(或埋在砂中或石灰中冷却)至500度以下在空气中冷却的热处理工艺。
三、何为淬火?就是将钢奥氏体化后以适当的冷却速度冷却,使工件在横截面内全部或一定的范围内发生马氏体等不稳定组织结构转变的热处理工艺。
50CrVA弹簧钢880℃淬油金相组织四、何为回火?就是将经过淬火的工件加热到临界点AC1以下的适当温度保持一定时间,随后用符合要求的方法冷却,以获得所需要的组织和性能的热处理工艺。
五、何为固溶热处理?就是将合金加热至高温单相区恒温保持,使过剩相充分溶解到固溶体中,然后快速冷却,以得到过饱和固溶体的热处理工艺。
井式回火炉六、何为固溶处理?就是使合金中各种相充分溶解,强化固溶体并提高韧性及抗蚀性能,消除应力与软化,以便继续加工成型。
七、何为时效?就是合金经固溶热处理或冷塑性形变后,在室温放置或稍高于室温保持时,其性能随时间而变化的现象。
八、何为时效处理?就是在强化相析出的温度加热并保温,使强化相沉淀析出,得以硬化,提高强度。
九、何为钢的碳氮共渗?就是碳氮共渗是向钢的表层同时渗入碳和氮的过程。
习惯上碳氮共渗又称为氰化,目前以中温气体碳氮共渗和低温气体碳氮共渗(即气体软氮化)应用较为广泛。
中温气体碳氮共渗的主要目的是提高钢的硬度,耐磨性和疲劳强度。
低温气体碳氮共渗以渗氮为主,其主要目的是提高钢的耐磨性和抗咬合性。
十、何为调质处理?就是将淬火加高温回火相结合的热处理称为调质处理。
调质处理广泛应用于各种重要的结构零件,特别是那些在交变负荷下工作的连杆、螺栓、齿轮及轴类等。
调质处理后得到回火索氏体组织,它的机械性能均比相同硬度的正火索氏体组织为优。
- 1、下载文档前请自行甄别文档内容的完整性,平台不提供额外的编辑、内容补充、找答案等附加服务。
- 2、"仅部分预览"的文档,不可在线预览部分如存在完整性等问题,可反馈申请退款(可完整预览的文档不适用该条件!)。
- 3、如文档侵犯您的权益,请联系客服反馈,我们会尽快为您处理(人工客服工作时间:9:00-18:30)。
弹簧的热处理弹簧钢的特点—弹簧主要在动载荷下工作,即在冲击、振动的条件下,或在交变应力作用下工作, 利用弹性变形来吸收冲击能量,起缓冲作用。
由于弹簧经常承受振动和长期在享变应力作用下工作,主要是疲劳破坏,故弹簧钢必须具有高的弹性极限和高疲劳极限。
此外,还应有足够的韧性和塑性,以防止在冲击力作用下突然脆断。
在工艺性论方面,弹簧钢应具有较好的淬透性和低的过热、脱碳敏感性。
降低弹簧表面粗糙度能提高疲劳寿命。
为了获得所需的性能,弹簧钢必须具有较高的含碳量。
碳素弹簧钢的含碳量在0.6-0.9%之间,由于
碳素弹簧钢的淬透性差,故只用于制造截面尺寸不超过10-15mm 的弹簧。
对于截面尺寸较大的弹簧,必须采用合金弹簧钢。
合金弹簧钢碳含量在0.45-0.75 %之间,加入的合金元素有Mn ,Si ,W ,V ,Mo 等。
它们的主要作用是提高淬
透性和回火稳定性,强化铁素体和细化晶粒,有效地改善弹簧钢的力学性能,其中Cr ,W ,Mo 还能
提高钢的高温强度。
在热状态下成型的弹簧(直径或厚度一般在10mm 以上)
在冷状态下成型的弹簧(直径或厚度一般在10mm 以下)
热成型弹簧的热处理工艺--用这种方法成型弹簧多数是将热成型和热处理结合在一起进行的,而螺旋弹簧则大多数是在热成型后再进行热处理。
这种弹簧钢的热处理方式是淬火+中温回火,热处理后组织为回火托氏体。
这种组织的弹性极限和屈服极限高,并有一定的韧性。
冷成型弹簧的热处理工艺--对于用冷轧钢板、钢带或冷拉钢丝制成的弹簧,由于冷塑性变形使材料强化,己达到弹簧所要求的性能。
故弹
簧成型后只需在250C 左右范围内,保温30min 左右的去应力处理,以消除冷成型弹簧的门应力, 并使弹簧定型即可。
耐热弹簧钢的热处理--内燃机的气阀弹簧是在较高温度下工作,有的还存在腐蚀性气氛,因此必须选用特殊的弹簧钢和合适的热处理规范。
弹簧淬火时常见的缺陷及防止措施
(1)脱碳(降低使用寿命)--1、采用盐浴炉或拄制气氛加热炉加热。
2、采用快速加热工艺。
(2)淬火后硬度不足,非马氏体数量较多,心部出现铁素体(产全残余变形,降低使用寿命)--1、选用淬透性较好的材料。
2、改善淬火冷却剂的冷却能力。
3、弹簧进入冷却剂的温度应控制在Ar3 以上。
4、适当提高淬火加热温度。
(3)过热(脆性增加)--1、严格控制成型及淬
火
加热温度。
2、加强淬火时的金相检验
(4)开裂(脆性增加,严重降低使用寿命)--1、控制淬火加热温度。
2、淬火时冷到250-300C 时, 取出空冷。
3、及时回火
提高弹簧质量的措施
(1)形变热处理--将钢的变形强化与热处理强化两者结合起来,以进一步提高钢的强度和韧性。
形变热处理有高、中、低温之分。
高温形变热处理是在稳远的奥氏体状态下产生形变后立即淬火,也可与锻造或热轧结合起来,即热成型后立即淬火。
形变热处理己应用于汽车板簧生产中。
(60Si2Mn)
(2)弹簧的等温淬火--对于直径较小或透透性足够的弹簧可采用等温淬火,它不仅能减少变形, 而且还能提高强韧性,在等温淬火后最好再进行一次回火,可提高弹性极限,回火温度与等温淬火温度相同。
(3)弹簧的松弛处理--弹簧长时间在外力作用下工作,由于应力松弛的结果会产生微量的永久(塑性)变形,特别是高温工作的弹簧,在高温下应力松弛现象更为严重,使弹簧的精度降低,这对于一般精密弹簧是不允许的。
因此,这类弹簧在淬火,回火后应进行松弛处理--对弹簧预先加载荷, 使其变形量超过弹簧工作时可能产生的变形量。
然后在高于工作温度20C 的条件下加热,保温8-
24h。
(4)低温碳氮共渗--采用回火与低温碳氮共渗(软氮化)相结合的工艺,能显著提高弹簧的疲劳
寿命及耐蚀性,此工艺多用于卷簧。
(5)喷丸处理--划痕、折叠、氧化脱碳等表面缺陷往往会成为弹簧工作时应力集中的地方和疲劳断裂源。
若用细小的钢丸高速喷打弹簧表面,不仅改善弹簧表面质量,提高表面强度,并使表面处于压应力状态,从而提高弹簧疲劳强度和使用寿命。
操作注意事项
(1)热处理前检查表面是否有脱碳、裂纹等缺陷。
这些表面缺陷将严重地降低弹簧的疲劳极限。
(2)淬火加热应特别注意防止过热和脱碳,做好盐浴脱氧,控制炉气气氛,严格控制加热温度与时间
(3)为减少变形,弹簧在加热时的装炉方式,夹具形式和冷却时淬入冷却方法。
(4)淬火后要尽快回火,加热要尽量均勺。
回火后快冷能防止回火脆性和造成表面压应力,提高疲劳强度。
质量检查
热处理前--(1) 钢材的轧制表面往往就是制成弹簧后的表面,故不应有裂纹、折叠、斑疤、发纹、气泡、夹层和压入的氧化皮等。
(2)表面脱碳会显著降什弹簧的疲劳强度,应按规定检验脱碳层的深度。
热处理后--(1)肉眼或低倍放大镜观察弹簧表的不应有裂纹、腐蚀麻点和严重的淬火变形。
(2) 硬度及其均匀性符合规定。
大量生产时,允许用锉刀抽检硬度,但必须注意锉痕位置应不影响弹簧的最后精度。
(3)金相组织应是托氏体或托氏体和索氏体的混合组织。
(4)板簧装配后,通常还要进行工作载荷下的永久变形以及静载挠度试验。
各种弹簧钢的热处理规范及硬度要求
钢号淬火温度淬火介质硬度要求回火温度冷却介质硬度要求应用范围
65780-830水或油400-600线
弹簧垫圈
径小于12-15mm的螺旋弹
簧、
65Mn 810-830油或水>60370-400水42-50 5-10mm 的板簧片及7-10mm 的卷簧
50CrV 850-870油>58400-5 5 水45-50截面较大和较重要的板簧片
及螺旋弹簧
50CrV 850-870油>58370-4 20 45-52 300C 以下工作的高温弹簧
60Si2MnA 860-880 油>60 500-520 水HB363-444 厚度8-12mm 的板簧片
耐热弹簧钢的材料选用和最高使用温度的热处
理规范
钢号最高使用温度热成型(度)火温度回火温度
60Si2MnA 250 880-900 860-880 油 350 50CrVA
300 880-900 850-870 油 430-500
4Cr13 400
850-1050
980-1050空冷 540-560 冷 拉 18-8 型不锈钢丝 400 卷 去应力回火 400C,15-60min W18Cr4V 600
1000-1200 280-1290 油或空冷 700
冷 1
常用弹簧钢的等温淬火规范
钢号加热温度温保持时间硬度等温淬火温度HRC
T10A800+-10250-360
65 65Mn 10-3040-53
820+-10
15-3046-48
820+-10
320-340
320-34015-30
50CrVA850+-10
30-45
60Si2MnA 87+-10
270 /
52-54 / 46-
48
300
280
50CrV 钢气阀弹簧低温碳氮共渗(软氮化)与普通热处理后疲劳性能比较热处理工艺断裂应变周次断裂后残余变形(mm) 室内耐大气腐蚀试验
860C 油淬,420C 回火
1h 1.78*10000 2.4 发黑后未上油,14 天后出现锈斑
860C油淬,480C软氮化3h>=100*100000.2850 天以上未生锈
860C油淬,510C软氮化3h>=100*100000.6850 天以上未生锈
例; 压缩螺旋弹簧50CrV 43-50HRC 外
径C 31.5 线径C 3.5 总高度50
工艺流程; 冷卷—定型处理—切断修正—淬火—矫正回火—检验修正—最后回火—检验、喷砂、表面处理。