陶瓷企业能耗现状及节能潜力
陶瓷行业的发展趋势与前景分析
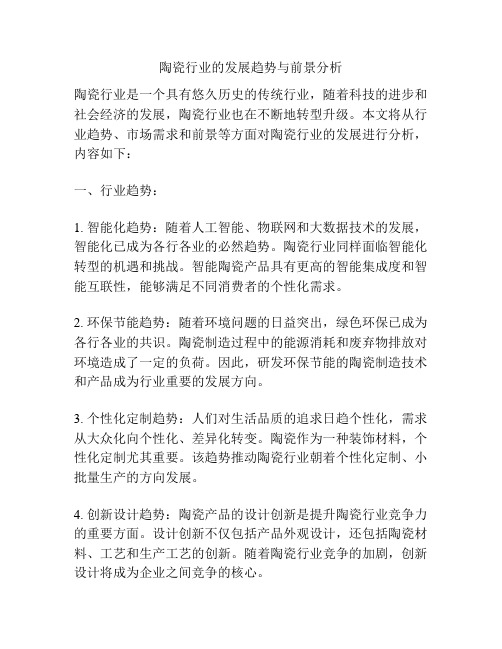
陶瓷行业的发展趋势与前景分析陶瓷行业是一个具有悠久历史的传统行业,随着科技的进步和社会经济的发展,陶瓷行业也在不断地转型升级。
本文将从行业趋势、市场需求和前景等方面对陶瓷行业的发展进行分析,内容如下:一、行业趋势:1. 智能化趋势:随着人工智能、物联网和大数据技术的发展,智能化已成为各行各业的必然趋势。
陶瓷行业同样面临智能化转型的机遇和挑战。
智能陶瓷产品具有更高的智能集成度和智能互联性,能够满足不同消费者的个性化需求。
2. 环保节能趋势:随着环境问题的日益突出,绿色环保已成为各行各业的共识。
陶瓷制造过程中的能源消耗和废弃物排放对环境造成了一定的负荷。
因此,研发环保节能的陶瓷制造技术和产品成为行业重要的发展方向。
3. 个性化定制趋势:人们对生活品质的追求日趋个性化,需求从大众化向个性化、差异化转变。
陶瓷作为一种装饰材料,个性化定制尤其重要。
该趋势推动陶瓷行业朝着个性化定制、小批量生产的方向发展。
4. 创新设计趋势:陶瓷产品的设计创新是提升陶瓷行业竞争力的重要方面。
设计创新不仅包括产品外观设计,还包括陶瓷材料、工艺和生产工艺的创新。
随着陶瓷行业竞争的加剧,创新设计将成为企业之间竞争的核心。
二、市场需求:1. 建筑陶瓷需求:随着城市化进程的加速和人们生活水平的提高,建筑业对陶瓷产品的需求不断增长。
陶瓷砖、卫生洁具等建筑陶瓷产品的需求将持续增长。
2. 生活陶瓷需求:生活陶瓷产品是指餐具、茶具、装饰摆件等。
随着人们对生活品质的要求不断提高,生活陶瓷产品的需求呈现出多样化、个性化的特点。
3. 工业陶瓷需求:工业陶瓷广泛应用于电子、汽车、医疗等行业。
随着这些行业的发展,对高性能、高强度、高耐磨、高绝缘等特殊要求的陶瓷产品的需求将不断增加。
三、前景展望:1. 创新技术将推动陶瓷行业发展:陶瓷制造技术的创新将推动产品设计、材料性能和工艺等方面的提升,进一步满足不同市场需求。
2. 智能化转型将提升陶瓷产品附加值:智能陶瓷产品的出现将提升陶瓷产品的附加值,满足消费者个性化需求,为企业带来更多利润。
中小建筑陶瓷企业的节能减排
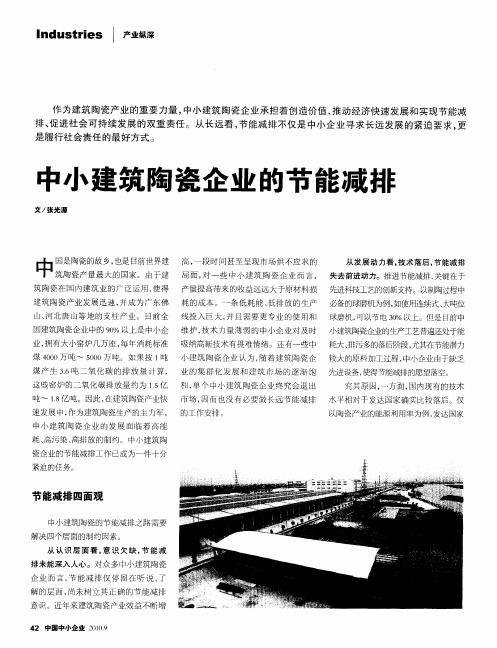
煤 产 生 36 二 氧 化碳 的排 放 量 计算 , 业 的集 群 化发 展 和建 筑 市 场 的逐 渐 饱 先进设备 , .吨 使得节能减排 的愿望落空。 这 些窑炉 的二氧 化碳排 放量 约为 1 亿 和 , . 5 单个 中小建 筑陶 瓷企 业终究 会退 出
例如鉴于 国内外 已有不少二 氧化碳排放
从约束机制看 。 节能减排缺乏有效 奖 权 买 卖的案 例 , 中小 建筑 陶瓷企 业 同样
的落 后使 得国内制陶企业 失去技术 上的 惩。对某些地 区而言, 建筑 陶瓷产业是其 可 以尝试将节能减 排后产生 的多余二 氧 支持 , 只能对国外 低能耗 、 低排 放 的制陶 支柱 产业 , 因此对节能减排工作 的开展也 化碳 排放 权作 为一 种资 产 , 通过 抵押 等 企业 “ 望洋兴叹”了。另一方面就是 受资 将 对整个地 区的经济和就 业产生 巨大 的 手段 , 行 贷款 。或者 可以 与政府 展开 进 金的制约。即便国内已有节能减排工艺 , 影 响, 从短 期看甚至会降低经济发展的速 合作 , 立类似 日本 中小企业担保协会 , 建
究其原因 , 面 , 一方 国内现有的技术
吨 ~ 1 亿吨 。因此, . 8 在建筑陶瓷产业快 市场 , 因而也没 有必 要做 长远节 能减 排 水平相对 于发达国 家确 实比较落后 。仅 速发展 中, 作为建筑 陶瓷生产的主 力军 , 的工作 安排。 中 小建 筑 陶 瓷企 业 的 发展 面 临着 高 能
社会: 既是监督者 , 也是 实践 者。节
没有 “ 家底”支持 。对 中小建筑陶瓷企业 快速 、 效地 推进 中小 建筑 陶瓷 企业 节 高
广东省陶瓷行业的能耗现状及节能措施
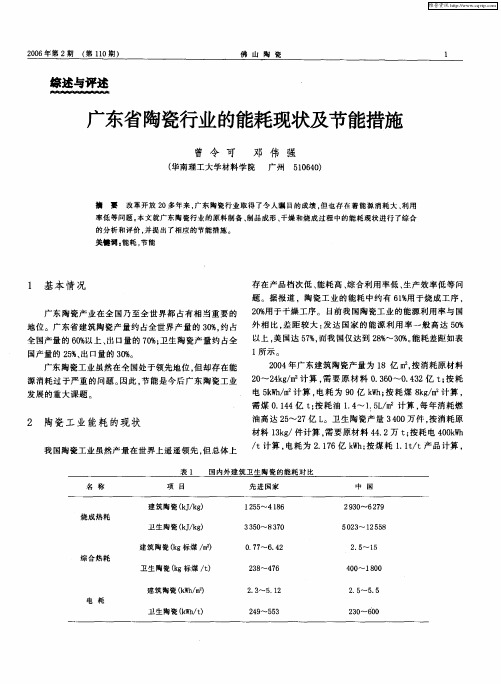
需求 紧张 的广东 , 疑是雪上加 霜。 无 产生深远 的影 响。 陶瓷 生产 而言 , 能降耗 将是 大势所 就 节 趋 , 是可持续 发展 的重要 条件 。因此 , 也 分析 陶瓷 工业 能 耗的现状及节 能技 术非常必要 。
是微 波 干燥 的 3 -3 、 0- 2倍 能耗 为 2 5倍 ,  ̄ . 而生产 能力 仅 为
维普资讯
2 0 年第 2期 06
( 10期 ) 第 1
佛 山 陶 瓷
综述与评述
广东省陶瓷行业 的能耗现状及节能措施
曾 令 可 邓 伟 强
( 华南理工大学材料学院 广州 50 4 ) 16 0
摘
要
改革开放 2 0多年来 , 广东陶瓷行业取得了令人瞩 目的成绩 。 也存在着能源 消耗 大 、 但 利用
需煤 014 t按耗 油 14 .Lm 算 , .4 亿 ; . ~15/2计 每年 消耗燃
2 陶瓷 工 业 能耗 的现 状
我 国陶瓷工业 虽然产量在世 界上遥遥 领先 , 但总体上
表1
ቤተ መጻሕፍቲ ባይዱ
油高达 2  ̄2 5 7亿 L 。卫 生陶 瓷产 量 3 0 4 0万件 . 按消耗原 材料 1k /件计算 。 3g 需要 原材料 4 . 4 2万 t 按耗 电 4 0 W ; 0kh / 计算 , t 电耗 为 2 1 6亿 k h 按煤 耗 1 1/ .7 w; . t t产 品计 算 ,
负荷 , 又增加 了球磨 机 的有 效容积 , 量提高 4% 单位产 产 0、
加相应 助剂 和采用 氧化铝球 . 既可 缩短球 磨 时间 , 义可节
电 3% 右 。 5左
在 陶瓷生 产中 , 烧成温度 越高 , 能耗就越 高 。 据热平衡 以上 、 成时间缩 短 1%、 量增加 1% 热耗降 低 4 。因 烧 0 产 0、 % 此 , 陶瓷行 业 中采用低 温快 烧技术 , 以显著增 加产量 、 在 可
广东省建筑陶瓷行业能效水平及节能技术应用分析

综述与评述Summary&Review陶瓷行业产品包括建筑陶瓷、卫生陶瓷、日用陶瓷和艺术陶瓷等,其中建筑陶瓷是陶瓷行业最主要的产品,也是行业能耗最主要的来源。
我国建筑陶瓷产量占世界总产量的比例超过60%,是世界上最大的建筑陶瓷生产国和消费国[1],广东省是全国建筑陶瓷最重要的生产基地之一。
近年来,受下游房地产市场低迷等因素影响,建筑陶瓷行业整体经营形势不佳,《广东省“两高”项目管理目录(2022年版)》将建筑陶瓷制品制造分类下所有企业纳入“两高”企业管理,对行业节能降耗提出了更高的要求。
一方面随着市场需求下滑,行业能源消费总量稳定下降,单位产品能耗因生产线开工率下降而波动;另一方面随着部分瓷砖产品向加工工艺复杂的高附加值产品转型,单位产品能耗持续下降面临一定的阻力。
行业实现绿色发展需要持续强化节能技术的推广应用。
据不完全统计,广东全省共有约700条建筑陶瓷生产线,约占全国瓷砖生产线的四分之一。
目前,全省建筑陶瓷企业及产能主要分布在肇庆、佛山、清远、云浮、江门等地,5个地市企业数量、总产值、产品产量占全省比例超过80%。
陶瓷行业窑炉能耗占全厂能耗的比重可达60%~80%[2-3],喷雾干燥能耗占全厂能耗的比重约20%[4],是建筑陶瓷生产工艺过程中主要耗能环节,行业最主要的能源品种是煤和天然气。
近年来,广东省大力推进陶瓷行业煤改气工程,目前除个别不满足条件的区域外,全省85%以上的建筑陶瓷企业均完成了煤改气。
建筑陶瓷行业与房地产市场深度关联,房地产需求减弱导致建筑陶瓷市场持续萎靡,广东省内多数企业开窑率不足50%,部分企业已停产。
另一方面,煤炭、天然气及大宗原材料持续上涨且长时间维持高位,给企业生产成本带来巨大压力。
行业能源成本占生产成本比例从2020年的约31%升高到2022年底的超过40%,相较于尚未开展煤改气的外省陶瓷企业,省内产品竞争力显著下降。
2023年第一季度全省建筑陶瓷产量继续下滑,部分企业对未来市场和经营预期仍不乐观。
陶瓷生产企业能源消耗现状与节能潜力调查

陶瓷生产企业能源消耗现状与节能潜力调查调查目的:本调查旨在了解当前陶瓷生产企业的能源消耗现状,并探讨其节能潜力,以提供有效的节能建议和措施。
调查方法:采用问卷调查和实地走访相结合的方式开展调查。
问卷调查主要针对陶瓷生产企业,包括能源消耗情况、能源使用设备、能源管理措施等内容。
实地走访重点观察陶瓷生产企业的生产流程、设备使用状况和能源利用情况。
调查结果:根据调查结果显示,陶瓷生产企业的能源消耗主要集中在以下几个方面:1. 电力消耗:陶瓷生产过程中,电力消耗占据较大比重,主要用于搅拌、制模、烧结等各个环节。
2. 煤炭消耗:烧结环节是煤炭消耗的主要环节,炉内温度和烧结时间的控制对煤炭的消耗量有较大影响。
3. 自然气消耗:某些企业在生产过程中使用自然气进行干燥、烧结等工艺,自然气消耗较大。
调查还发现,陶瓷生产企业存在一定的节能潜力:1. 设备更新:部分陶瓷生产企业的生产设备老化严重,更新更高效的设备可以降低能源消耗。
2. 工艺改进:优化工艺流程,提高能源利用率,减少能源浪费。
3. 能源管理:加强对能源的监测和管理,建立科学的能源管理制度和节能指标,倡导全员参与。
结论与建议:通过调查发现,陶瓷生产企业的能源消耗较大,但存在节能的潜力。
建议陶瓷生产企业在节能方面采取以下措施:1. 引进先进设备,提高生产效率,减少能源消耗。
2. 优化工艺流程和生产计划,减少能源浪费。
3. 加强能源监测与管理,制定节能目标,监督执行。
4. 提高员工节能意识,鼓励员工参与节能活动。
通过以上措施的实施,陶瓷生产企业能够有效降低能源消耗,并提高生产效率,实现可持续发展。
陶瓷行业现状及发展趋势

《陶瓷行业现状及发展趋势》
陶瓷行业是一个历史悠久的传统行业,目前正处于不断发展和变革之中。
目前,陶瓷行业的现状呈现出以下特点。
一方面,陶瓷产品的种类越来越丰富。
除了传统的日用陶瓷、建筑陶瓷外,艺术陶瓷、工业陶瓷等新兴领域也在不断发展。
例如,艺术陶瓷以其独特的艺术价值和收藏价值,受到越来越多消费者的喜爱。
另一方面,陶瓷行业的技术水平不断提高。
随着科技的进步,陶瓷生产过程中的自动化、智能化程度越来越高,产品的质量和性能也得到了极大的提升。
比如,一些先进的陶瓷生产企业采用了数字化设计、3D 打印等技术,生产出了更加精美的陶瓷产品。
未来,陶瓷行业的发展趋势将主要体现在以下几个方面。
一是绿色环保。
随着人们对环境保护的重视,陶瓷行业将更加注重节能减排、资源循环利用等方面的发展。
例如,采用新型的环保材料和生产工艺,减少陶瓷生产过程中的污染和浪费。
二是个性化定制。
消费者对个性化产品的需求越来越高,陶瓷行业将更加注重满足消费者的个性化需求,提供个性化定制服务。
三是智能化制造。
随着人工智能、物联网等技术的发展,陶瓷行业将逐步实现智能化制造,提高生产效率和产品质量。
中国陶瓷行业发展现状

中国陶瓷行业发展现状摘要:一、中国陶瓷行业的历史与文化二、中国陶瓷行业的现状1.产业规模与发展速度2.产品种类与结构3.行业竞争格局三、中国陶瓷行业的挑战与机遇1.环保与节能2.品牌建设与技术创新3.市场需求与出口前景四、中国陶瓷行业的未来发展趋势1.绿色智能生产2.多元化与个性化3.产业整合与升级正文:中国陶瓷行业历史悠久,具有丰富的文化底蕴。
早在约五千年前,中国就发明了陶器,并在商代中期出现了早期的瓷器。
随着制陶业的发展,自殷商时代早期,即已出现了以瓷土为胎料的白陶器和烧成温度达1200的印纹硬陶,开始了由陶向瓷的过渡。
近年来,中国陶瓷行业呈现出良好的发展态势。
产业规模与发展速度方面,根据数据显示,2020年1——10月,全国规模以上建筑陶瓷企业1094家,实现营收2506.70亿元,增长0.36%。
另外,陶瓷砖累计产量达84.5亿平方米,同比增加1.07%。
产品种类与结构方面,陶瓷行业涵盖了日用陶瓷、卫生陶瓷、建筑陶瓷、艺术陶瓷等多个领域,其中建筑陶瓷占据主导地位。
行业竞争格局方面,中国陶瓷市场头部企业市场占有率较高,竞争激烈。
然而,中国陶瓷行业也面临着诸多挑战与机遇。
首先,环保与节能成为行业亟待解决的问题。
随着国家对环境保护的重视,陶瓷企业需要加大节能减排力度,采用绿色生产方式,降低能耗和污染物排放。
其次,品牌建设与技术创新对于提升行业竞争力至关重要。
中国陶瓷企业应加强品牌培育,提高产品质量,同时加大技术创新力度,开发具有自主知识产权的产品。
最后,市场需求与出口前景为陶瓷行业带来了广阔的发展空间。
随着国内外市场对陶瓷制品的需求不断增长,中国陶瓷行业有望继续保持稳定增长。
陶瓷行业能源消耗状况及节能潜力评估报告
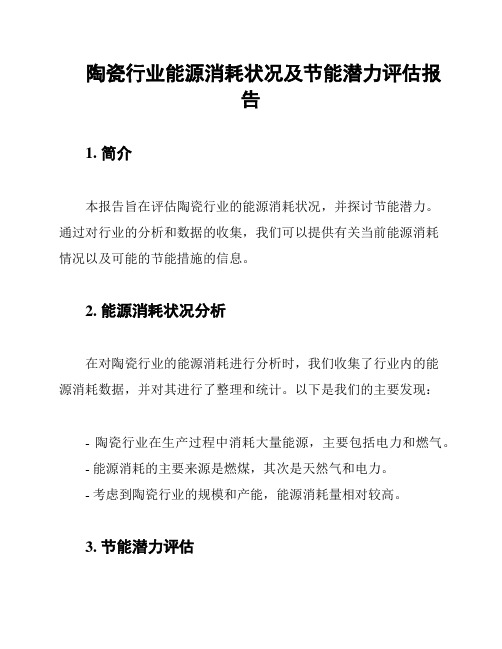
陶瓷行业能源消耗状况及节能潜力评估报告1. 简介本报告旨在评估陶瓷行业的能源消耗状况,并探讨节能潜力。
通过对行业的分析和数据的收集,我们可以提供有关当前能源消耗情况以及可能的节能措施的信息。
2. 能源消耗状况分析在对陶瓷行业的能源消耗进行分析时,我们收集了行业内的能源消耗数据,并对其进行了整理和统计。
以下是我们的主要发现:- 陶瓷行业在生产过程中消耗大量能源,主要包括电力和燃气。
- 能源消耗的主要来源是燃煤,其次是天然气和电力。
- 考虑到陶瓷行业的规模和产能,能源消耗量相对较高。
3. 节能潜力评估为了评估陶瓷行业的节能潜力,我们对现有的技术和节能措施进行了调研和分析。
以下是我们的主要结论:- 陶瓷行业可以采用节能炉具,改进燃烧技术和优化生产工艺,以减少能源消耗。
- 使用高效的照明设备和控制系统,可以降低能源消耗。
- 废热回收和余热利用是陶瓷行业节能的有效途径。
- 强化能源管理和监测,可以帮助陶瓷企业识别能源浪费,并采取相应措施。
4. 结论本报告总结了陶瓷行业的能源消耗状况,并评估了其节能潜力。
通过采取相应的节能措施,陶瓷行业可以降低能源消耗,提高资源利用效率。
我们建议陶瓷企业在生产过程中采取切实可行的节能措施,并积极探索新的技术和方法,以实现可持续发展。
如果需要更详细的分析和建议,请联系我们,我们将非常乐意为您提供帮助。
---该文档深入分析了陶瓷行业的能源消耗状况,并提出了节能潜力评估。
通过采取适当的节能措施,陶瓷企业可以减少能源消耗,提高资源利用效率。
请让我知道您是否需要进一步的信息。
陶瓷行业环境评价报告
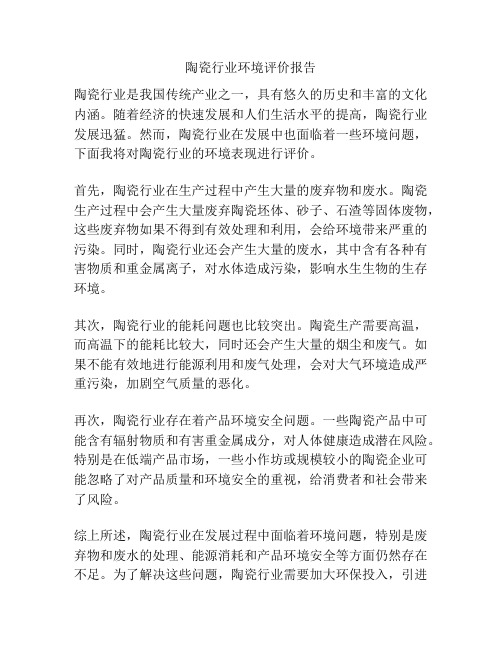
陶瓷行业环境评价报告
陶瓷行业是我国传统产业之一,具有悠久的历史和丰富的文化内涵。
随着经济的快速发展和人们生活水平的提高,陶瓷行业发展迅猛。
然而,陶瓷行业在发展中也面临着一些环境问题,下面我将对陶瓷行业的环境表现进行评价。
首先,陶瓷行业在生产过程中产生大量的废弃物和废水。
陶瓷生产过程中会产生大量废弃陶瓷坯体、砂子、石渣等固体废物,这些废弃物如果不得到有效处理和利用,会给环境带来严重的污染。
同时,陶瓷行业还会产生大量的废水,其中含有各种有害物质和重金属离子,对水体造成污染,影响水生生物的生存环境。
其次,陶瓷行业的能耗问题也比较突出。
陶瓷生产需要高温,而高温下的能耗比较大,同时还会产生大量的烟尘和废气。
如果不能有效地进行能源利用和废气处理,会对大气环境造成严重污染,加剧空气质量的恶化。
再次,陶瓷行业存在着产品环境安全问题。
一些陶瓷产品中可能含有辐射物质和有害重金属成分,对人体健康造成潜在风险。
特别是在低端产品市场,一些小作坊或规模较小的陶瓷企业可能忽略了对产品质量和环境安全的重视,给消费者和社会带来了风险。
综上所述,陶瓷行业在发展过程中面临着环境问题,特别是废弃物和废水的处理、能源消耗和产品环境安全等方面仍然存在不足。
为了解决这些问题,陶瓷行业需要加大环保投入,引进
更加环保的生产技术和设备,并加强监管力度,加强对陶瓷企业的安全生产和环境保护的督促和指导。
同时,消费者也应该拒绝购买质量不合格和环境安全问题突出的陶瓷产品,推动陶瓷行业向更加环保和可持续发展的方向迈进。
陶瓷工业窑炉能耗现状及节能技术

陶瓷工业窑炉能耗现状及节能技术一.陶瓷工业窑炉概况陶瓷工业窑炉按样式分:辊道窑、隧道窑、梭式窑。
按热源分:燃油窑、燃气窑、电窑、微波窑。
陶瓷产品主要分为:建筑陶瓷、日用陶瓷、卫生陶瓷、特种陶瓷。
建筑陶瓷具有薄、平、规则的特点,全部采用辊道窑快速烧成。
日用陶瓷根据产品的各自特点,小而薄的可采用辊道窑烧成;大而不规则的则采用隧道窑烧成。
卫生陶瓷大多体型大,不规则,厚度不一多采用隧道窑或梭式窑生产。
特种陶瓷根据产品的样式以及物理化学要求大多采用电辊道窑、燃气梭式窑或微波窑烧成。
二.能耗因素影响陶瓷窑炉能耗的因素有:1.窑炉样式。
隧道窑、梭式窑的窑车具带走的热量占窑炉总耗热的20%左右。
国内辊道窑能耗在450—1200Kcal/kg 瓷,隧道窑的能耗在1000Kcal/Kg瓷以上。
2.窑炉结构。
窑墙的保温蓄热性能、窑顶结构对于气体流动的影响、各种管道分布的合理性及对热量的利用率的影响。
3.窑炉尺寸。
窑炉宽度增加1m,单位制品的能耗大概减少2.5%。
窑炉越长,窑头排烟带走的热量就越少。
窑炉越高,散热面积越大,能耗越大。
4.窑炉燃料。
同样的温度要求下,洁净燃料所需的空气量和产生的烟气量少,排烟带走的热量就少。
微波、电热、燃气、燃油、燃煤窑炉的能耗依次增大。
5.窑炉材料。
窑体材料的热导率越低,窑体散热越少,材料越轻,窑体蓄热越少。
6.窑炉控制。
目前国内大多采用计算机自动监测控制系统,合理调节窑内温度、压力、气氛,从而减少燃料消耗;合理调节风机和传动电机频率,减少无用功。
7.窑炉烧嘴。
目前国内新建窑炉大多采用高速预混式节能烧嘴,该烧嘴可调节空气过量系数,高速,减少宽断面温差。
8.窑炉余热的回收利用。
目前国内陶瓷窑炉基本都采用直接热回收利用的方式,如:加热空气、干燥坯体等,动力回收的很少。
9.产品。
产品的原料、规格、性能的不同,烧成参数也不同,能耗自然也不同,产品烧成温度降低100℃,单位产品热耗可降低10%。
目前广东外墙砖的能耗大概为530—1000Kcal/Kg瓷,仿古砖480—700Kcal/Kg瓷,抛光砖530—800Kcal/Kg瓷,日用卫生陶瓷大概为1000—2000Kcal/Kg瓷。
陶瓷项目节能评估报告
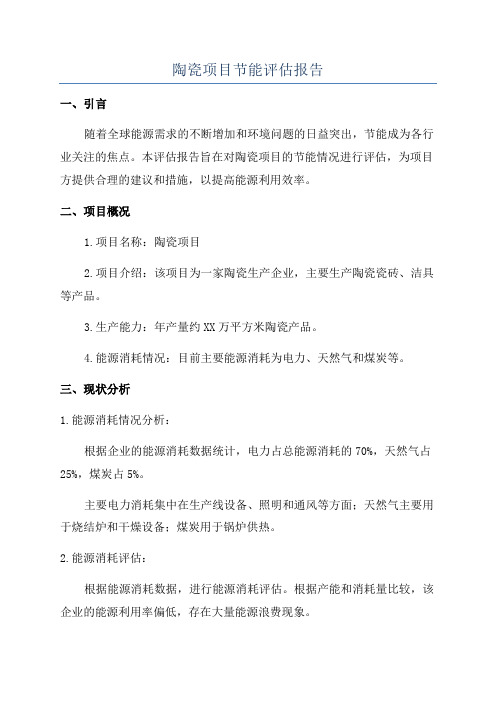
陶瓷项目节能评估报告一、引言随着全球能源需求的不断增加和环境问题的日益突出,节能成为各行业关注的焦点。
本评估报告旨在对陶瓷项目的节能情况进行评估,为项目方提供合理的建议和措施,以提高能源利用效率。
二、项目概况1.项目名称:陶瓷项目2.项目介绍:该项目为一家陶瓷生产企业,主要生产陶瓷瓷砖、洁具等产品。
3.生产能力:年产量约XX万平方米陶瓷产品。
4.能源消耗情况:目前主要能源消耗为电力、天然气和煤炭等。
三、现状分析1.能源消耗情况分析:根据企业的能源消耗数据统计,电力占总能源消耗的70%,天然气占25%,煤炭占5%。
主要电力消耗集中在生产线设备、照明和通风等方面;天然气主要用于烧结炉和干燥设备;煤炭用于锅炉供热。
2.能源消耗评估:根据能源消耗数据,进行能源消耗评估。
根据产能和消耗量比较,该企业的能源利用率偏低,存在大量能源浪费现象。
四、节能潜力评估1.技术优化方案:通过技术优化,包括设备升级、改造和运行管理等方面,以提高设备能效和降低能源消耗。
2.能源结构优化方案:考虑可再生能源的利用,如太阳能和风能等,以减少对化石能源的依赖。
五、节能建议1.技术改造:建议对陶瓷生产线的设备进行优化升级,提高设备能效指标,减少能源浪费。
同时,加强设备巡检和定期维护保养,确保设备运行的稳定和高效。
2.运行管理:优化生产工艺和工作流程,合理安排生产计划,减少生产中的闲置和停机时间,提高生产效率,降低能源消耗。
3.能源结构优化:考虑引入太阳能光伏发电等清洁能源技术,减少对煤炭和天然气等化石能源的依赖,降低企业的碳排放量。
4.员工培训:加强员工对节能意识的培训,提高员工对节能措施的认知和理解,通过员工的参与与努力,推动节能工作的实施。
六、总结本节能评估报告对陶瓷项目的节能情况进行了全面评估,并提出了相应的节能建议和措施。
建议项目方根据实际情况,制定详细的实施计划,并加强监督和评估,以确保节能措施的有效实施和节能效果的显著提升。
陶瓷制品制造行业市场现状分析

陶瓷制品制造行业市场现状分析陶瓷制品作为人类文明发展的重要产物,拥有着悠久的历史和丰富的文化内涵。
如今,在现代科技和经济发展的推动下,陶瓷制品制造行业也呈现出多样化的市场现状。
从需求方面来看,陶瓷制品在建筑、家居装饰、日用、工业等领域都有着广泛的应用。
在建筑领域,陶瓷地砖、墙砖等产品因其美观、耐用、易清洁等特点,成为了许多建筑项目的首选材料。
随着人们对居住环境要求的提高,对于具有独特设计和高品质的陶瓷建筑装饰材料的需求持续增长。
在家居装饰方面,陶瓷花瓶、摆件等工艺品深受消费者喜爱,为家居环境增添了艺术氛围。
日用陶瓷如餐具、茶具等也是人们日常生活中不可或缺的一部分,消费者对于其质量、外观和安全性的要求不断提升。
此外,在工业领域,陶瓷因其耐高温、耐腐蚀等特性,被广泛应用于电子、化工、机械等行业,对于特种陶瓷制品的需求也在逐步增加。
在供给方面,陶瓷制品制造行业的竞争十分激烈。
全球范围内,中国、意大利、西班牙等国家是陶瓷制品的主要生产国。
中国作为陶瓷生产大国,拥有庞大的生产规模和完善的产业链,但也面临着产业升级和环保压力等挑战。
许多中小企业在市场竞争中面临着生存困境,而一些大型企业则通过技术创新、品牌建设和市场拓展来提升竞争力。
同时,国外一些陶瓷制造企业凭借先进的技术和设计理念,在高端市场占据一定份额。
从技术发展的角度来看,陶瓷制品制造行业正朝着智能化、绿色化和高端化的方向发展。
智能化生产设备的应用提高了生产效率和产品质量的稳定性。
例如,自动化的生产线可以实现精确的配料、成型和烧制过程,减少人工操作带来的误差。
绿色化生产则成为了行业发展的必然趋势,企业越来越注重节能减排和资源循环利用,以降低对环境的影响。
在高端化方面,研发高性能、多功能的陶瓷材料成为了众多企业的重点发展方向,如纳米陶瓷、生物陶瓷等,以满足不同领域的特殊需求。
然而,陶瓷制品制造行业也面临着一些问题和挑战。
首先,环保压力日益增大。
陶瓷生产过程中会产生大量的废气、废水和废渣,如果处理不当,将对环境造成严重污染。
陶瓷窑炉燃料现状分析)

陶瓷窑炉燃料现状分析景德镇陶瓷学院材料学院 08热工1班廖小辉摘要:众所周知,陶瓷在生产工程中要消耗大量的能源,而烧成工序的能耗约占总能耗的6%。
窑炉的工作性能与燃料的品种有密切关系,例如采用精华的气体燃料可以保证烧成制度的稳定,方便管理,有利于自动控制。
油类燃料的优越性就比不上气体燃料,但比直接的煤炭还是好很多。
因此,燃料对于陶瓷行业是一个重要话题。
关键字:陶瓷窑炉(ceramics furnace)燃料(fuel)煤(coal)天然气(natural gas)油类燃料(oil fuel)前言:我国是陶瓷生产大国,日用瓷和建筑卫生陶瓷的产量均居世界第一。
据有关资料显示,2003年建筑陶瓷产量达30亿平方米,占全世界总产量的40%;卫生陶瓷6000万~6500万件,全国有陶瓷厂上万家,拥有大小窑炉几万条,消耗能源4000万~5000万吨标准煤。
然而,我国是一个能源资源相对贫乏的国家,人均能源可采储量2000年石油为2.6吨、天然气为1074立方米、煤炭为90吨,分别为世界平均值的11.1%、4.3%和55.4%,远远低于世界的平均水平。
而陶瓷行业是一个高能耗的行业,能耗占陶瓷生产成本的30%~40%,陶瓷的高能耗必然带来高污染,故全国迅猛发展的陶瓷业对我国的环境造成很大的污染,特别是陶瓷发展迅速的瓷区及周边地区更为严重。
广东省内除佛山地区外,其他地区,如深圳、东莞、清远、潮州等地及全国各主要瓷区已出现不少有关陶瓷厂烟囱废气污染而造成附近农民果树及农作物枯死失收等纠纷。
另外,窑炉废气易造成酸雨,广东每年因酸雨损失多达40亿元。
因此,节能降耗减少陶瓷窑炉污染是陶瓷生产的大势所趋,也是陶瓷工业可持续发展的重要条件。
下面,对陶瓷窑炉燃料现状进行分析。
一、选用燃料与燃料性能分析1、燃料油燃料油是成品油的一种,广泛用于电厂发电、船舶锅炉燃料、加热炉燃料、冶金炉和其它工业炉燃料。
燃料油主要由石油的裂化残渣油和直馏残渣油制成的,其特点是粘度大,含非烃化合物、胶质、沥青质多。
浅谈陶瓷企业节能措施

产工 序 和 主要 用 能 设 备论 述 了一 些 具 体 的节 能措 施 。
关 键 词 : 瓷 : 源 消 耗 ; 能 措 施 陶 能 节
1 前 言
我 国是建 筑卫生 陶瓷生产 大 国 ,建 筑卫 生陶瓷 的产
特 别 是 陶 瓷 业 发 展 迅 速 的产 区 如 广 东 省 的佛 山 、 州 、 潮 清 远 、 庆 、 源 等 地 区更 为 严 重 。 肇 河
次 于 美 国 。今 后 几 年 我 国 能 源 消 费 量 将 继 续 保 持 高 速 增 节 能 的 目的 。
长趋 势 。 能源供 需矛盾 日益严重 , 能源供 应安全 已成 为关 系我 国经济发展 的重 大问题。 自进入二 十一世纪 以来 , 济全球 化进一 步发展 , 经 世 界能源消费量 高速增长 ,国际能源市 场 出现 了能源供 应 紧张的局 面 , 能源价格 不断上涨 , 供需 矛盾 日益突 出 。能 21 主 要 生 严 工 艺 . 源 成 本 的大 幅 度 提 升 对 “ 能 耗 、 污 染 、 源 性 ” 高 高 资 的行 业 建 筑 陶 瓷 产 品 主 要 有 抛 光 砖 和 瓷 片 两 大 类 ,主 要 生 带来 了 巨大 冲 击 ,能 源 成 本 严 重 威 胁 着 这 些 工 业 的 生 存 产 工 艺 流程 分 别 如 图 1 图 2 示 。 和 所
陶瓷工业能耗的现状及节能技术措施
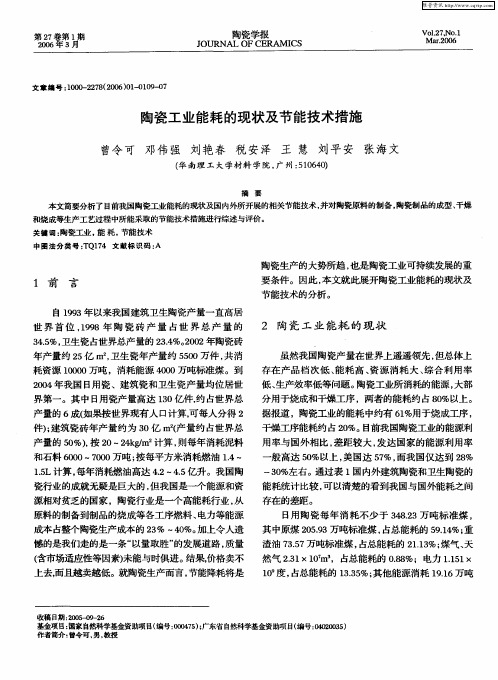
陶瓷 工业 能耗 的现 状 及 节能 技术 措 施
曾令 可 邓 伟 强 刘艳 春 税 安 泽 王 慧 刘 平 安 张 海 文
( 南理 工大学材 料 学院 , 州: 16 0 华 广 504)
摘
要
本文简要分析 了 目前我国陶瓷工业能耗的现状及国内外所开展的相关节能技术 , 对陶瓷原料 的制备 , 并 陶瓷制 品的成型 、 干燥
年产 量约 2 5亿 m2卫生 瓷 年产 量 约 50 , 50万件 , 消 共
要条件。因此 , 本文就此展开陶瓷工业能耗的现状及
节 能技术 的 分析 。
2 陶 瓷 工 业 能 耗 的 现 状
虽然我 国陶瓷产 量在 世界 上遥 遥领 先 , 但总 体上
耗资源 10 0 0 0 万吨 ,消耗能源 40 万吨标准煤。到 00 20 年我国 日 04 用瓷 、建筑瓷和卫生瓷产量均位居世 界第一。其中 日用瓷产 量高达 10亿件, 占世界总 3 约 产量的 6 如果按世界现有人 口计算 , 成( 可每人分得 2 件)建筑瓷砖年产量约为 3 亿 m ( 量约占世界总 ; 0 2 产
11采用一次烧成新工艺近年来我国不少陶瓷企业在釉面砖玉石砖水晶砖渗花砖大颗粒和微粉砖的陶瓷工艺和烧成技术上取得重大突破实现了一次烧成新工艺减少了素烧工序烧成的综合能耗和电耗下降30以上大113陶瓷学报2006年第12加强窑体密封性和窑内压力制度加强窑体密封和窑体与窑车之间窑车之间的严密性降低窑头负压保证烧成带处于微正压减少冷空气进入窑内从而减少排烟量降低热耗
憾的是我们走的是一条“ 以量取胜” 的发展道路 , 质量 ( 含市场适应性等因素) 未能与时俱进。 结果, 价格卖不 上去, 而且越卖越低。就陶瓷生产而言, 节能降耗将是
我国陶瓷行业现状格局及前景分析e

我国陶瓷行业现状格局及前景分析e
一、我国陶瓷行业现状
随着全球经济一体化的日益加强,我国陶瓷行业正处在业绩持续发展
的阶段。
2023年,我国陶瓷产业总产值3676.1亿元,增长17.9%,配套
产值2637.3亿元,增长17.8%,出口总收入956.2亿元,增长19.7%。
根
据中国陶瓷工业协会的统计数据,2023年我国水泥制品行业发展相对平稳,出口总额约占行业总额的47.2%,比2023年增长2.2个百分点;耐
火材料行业整体发展平稳,出口总额约占行业总额的26.3%,比2023年
增长7.8个百分点;瓷砖行业稳步发展,出口总额约占行业总额的20.4%,比2023年提升了7.3个百分点;瓷器行业整体发展良好,出口总额约占
行业总额的5.4%,比2023年增长9.6个百分点。
二、我国陶瓷行业格局
首先,从产业结构上看,我国陶瓷行业由六大类子行业组成,分别是
水泥制品行业、瓷砖行业、瓷器行业、耐火材料行业、日用瓷行业、特种
陶瓷行业。
其次,从市场结构上看,市场规模不仅面向国内,而且还向国
际发展,出口率已经达到了市场收入的近30%。
最后,从产能结构上看,
我国陶瓷行业的产能结构主要由小型企业为主,中型企业和大型企业分别
占比为39.7%和18.3%。
高温烧制环保陶瓷的能源消耗与减排方案

高温烧制环保陶瓷的能源消耗与减排方案高温烧制环保陶瓷是一种重要的建筑材料,然而其烧制过程会消耗大量能源,并产生大量的二氧化碳排放。
如何减少能源消耗和减少排放是当前环保陶瓷行业亟需解决的问题。
本文将探讨一些能源消耗和减排的方案。
首先,可以通过技术创新来降低高温烧制环保陶瓷的能源消耗。
目前,传统的烧制环保陶瓷的温度通常较高,耗能量大。
可以考虑采用先进的烧制技术,如高温气候炉、涂层材料等,以降低烧制温度和能源消耗。
此外,还可以改进燃烧设备,提高燃烧效率,减少热量损失和能源浪费。
其次,选择合适的原材料也是减少环保陶瓷烧制能源消耗的重要方法。
在原材料的选择上,应优先选择地道的天然材料,如高岭土、瓷石等,这些材料本身具有较好的热稳定性和烧成性能,可以减少添加剂的使用,从而降低能源消耗。
此外,还应注重陶瓷原材料的分类和储存,保证原材料的稳定性和质量,避免浪费。
进一步,改进回收利用系统也是减少环保陶瓷烧制能源消耗的重要措施。
环保陶瓷的生产过程中会产生废气、废水和废渣等。
可以采用高效的废气处理装置,如脱硫、脱硝等设备,将废气中的有害物质净化处理后,再进行烟气回收利用。
废水处理中可以采用生物陶瓷膜技术、深度处理等方法,提高水资源利用效率。
同时,将废渣进行分类和资源化利用,如废渣的再利用、填埋和再生利用等,减少废渣的排放和环境污染。
此外,建立长效监测机制,加强能源消耗和减排数据的统计和分析,是为了更好地了解能源消耗情况和排放量,并据此制定更科学合理的减排方案。
同时,通过设置奖励和惩罚制度,鼓励企业加大环保投入,提高环保陶瓷的可持续发展能力。
最后,对于消费者而言,提高环保陶瓷的认知度和推广力度也是推动减少能源消耗和减排的关键。
消费者可以选择使用符合环保标准的陶瓷产品,如具有节能、低碳等标志的产品,以降低个人能源消耗。
同时,也可以通过合理使用和维护环保陶瓷产品,延长其服务寿命,减少资源浪费和能源消耗。
高温烧制环保陶瓷的能源消耗与减排是一个复杂而重要的问题。
陶瓷行业碳排放基准

陶瓷行业碳排放基准一、引言随着全球环境问题的日益严重,碳排放成为了一个备受关注的焦点。
作为一个传统的产业,陶瓷行业也需要积极响应国家的碳排放减少政策,降低自身的碳排放,降低环境污染,保护环境。
因此,建立陶瓷行业的碳排放基准是非常重要的。
二、陶瓷行业碳排放现状1. 行业碳排放总量陶瓷行业作为一个重要的固体工业,在生产过程中会排放大量的二氧化碳。
按照我国统计局的数据,陶瓷行业的碳排放总量占到了全国工业总排放量的10%左右。
这个比例虽然不高,但在全国工业中也是一个不可忽视的数字。
2. 行业碳排放结构陶瓷行业的碳排放主要来自于生产过程中的电力消耗和燃料燃烧。
电力消耗主要是用于陶瓷生产中的生产设备和照明系统,而燃料燃烧则是用于窑炉的燃料。
根据统计数据,这两项排放量分别占到了总排放量的60%和30%。
3. 行业碳排放控制现状由于行业碳排放的严峻形势,陶瓷行业在国家政策的引导下逐渐意识到了减少碳排放的重要性,开始积极地进行控制和降低排放。
例如,一些大型陶瓷企业对生产设备进行了更新,采用了更加节能的设备,从而降低了电力消耗。
另外,一些企业也采用了新型的燃料,比如液化天然气等,以替代传统的燃煤,从而减少了燃料燃烧所产生的碳排放。
三、建立陶瓷行业碳排放基准的必要性1. 促进行业转型升级建立碳排放基准可以促进行业的转型升级。
通过对市场上各种生产过程和设备的碳排放进行调研和评估,可以找出排放较高的环节,进而引导企业进行技术升级,采用更加低碳的生产工艺和设备,以降低碳排放。
这样一来,不仅可以保护环境,还能够推动行业的绿色发展。
2. 提升企业核心竞争力建立碳排放基准还可以提升企业的核心竞争力。
在全球范围内,越来越多的国家和地区开始实施碳排放交易制度,要求企业对其碳排放进行一定的控制和减少。
如此一来,建立了碳排放基准的企业就可以更好地适应这种制度,降低成本,提高效益。
3. 推动行业的可持续发展最重要的是,建立碳排放基准可以推动行业的可持续发展。
从能源审计看广东省建筑陶瓷企业的能耗现状
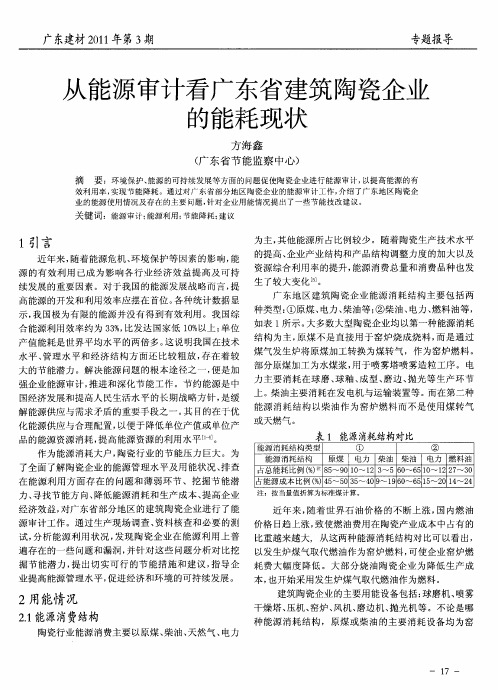
煤气 发 生炉 将 原煤加 工转 换 为煤 转气 ,作 为 窑炉 燃料 。 部 分原 煤加 工 为水煤 浆 , 用于 喷雾 塔 喷雾 造粒 工序 。 电 力 主 要消 耗 在球 磨 、 釉 、 型 、 边 、 光 等 生产 环 节 球 成 磨 抛
上 。 油主 要 消耗在 发 电机 与运输 装置 等 。而在 第二种 柴 能 源 消耗 结构 以柴 油 作 为窑 炉燃 料 而 不 是使 用 煤 转气
占总 能 耗 比例 () 8 , 01 ~ l , 0 6 0 1 7 3 % 5 ~9 o 2 3 ~56 ~ 5 ~ 22 ~ 0 1
注 :按当量值折算为标准煤计算。
了全面 了解 陶 瓷企 业 的能源 管理 水 平及 用 能状 况 、 查 排 力 、 找节 能方 向、 寻 降低 能源 消耗 和 生产 成 本 、 高企 业 提
广东建材 21 年第 3 01 期
专题报导
从能源审计看广东省建筑 陶瓷企业 的能耗 现状
方海鑫 ( 广东省节 能监 察 中心)
摘 要 :环境保护、 能源的可持续发展等方面的问题促使陶瓷企业进行能源审计, 以提高能源的有
效利用 率, 实现节能 降耗 。通过对广东省部分地 区陶瓷企业的能源审计工作 , 介绍 了广 东地 区陶瓷企 业的能源 使用情 况及存在 的主 要问题 , 针对企业用能情况提 出了一些节能技改建议。
近年来 , 随着 世 界 石 油价 格 的 不 断上 涨 , 内燃 油 国
源 审计 工 作 。通 过 生产 现场 调 查 、 资料 核 查和 必要 的测 价格 日趋上 涨 , 使 燃油 费用 在 陶瓷 产业 成本 中 占有 的 致 试, 分析 能 源 利用 状 况 , 发现 陶瓷 企 业 在 能源 利 用 上 普 比重越 来越 大, 从这 两种 能源 消 耗结 构对 比可 以看 出 , 遍 存在 的一些 问题 和漏 洞 , 并针 对这 些 问题 分 析对 比挖 以发生 炉煤 气取 代燃 油作 为 窑炉燃 料 , 使企 业 窑炉燃 可 掘 节 能潜 力 , 出切 实可 行 的节 能措 施 和 建 议 , 导 企 耗 费 大 幅度 降低 。大 部分 烧 油 陶 瓷企 业 为 降低 生 产成 提 指
- 1、下载文档前请自行甄别文档内容的完整性,平台不提供额外的编辑、内容补充、找答案等附加服务。
- 2、"仅部分预览"的文档,不可在线预览部分如存在完整性等问题,可反馈申请退款(可完整预览的文档不适用该条件!)。
- 3、如文档侵犯您的权益,请联系客服反馈,我们会尽快为您处理(人工客服工作时间:9:00-18:30)。
陶瓷企业能耗现状及节能潜力更新日期:2015年06月02日浏览量:5076新得国家标准GB 21252-2013《建筑卫生陶瓷单位产品能源消耗限额》于2014年12月1日实施,将取代原标准GB 21252-2007《建筑卫生陶瓷单位产品能耗限额》,成为对建筑卫生陶瓷生产得一项强制性考核标准。
新标准中陶瓷砖采取以单位合格品面积产量(kgce/㎡)计算单位产品能耗限定值,取代原按单位合格品重量产量(kgce/t)计算单位产品能耗限定值。
新标准对推动陶瓷砖薄型化、节能降耗具有很强得引导作用。
新标准执行后,将明显提高我国建筑卫生陶瓷行业得能耗限额水平,体现了节能降耗技术得进步,符合国家节能降耗得政策。
按照国家发改委《关于印发万家企业节能低碳行动实施方案得通知》(发改环资〔2011〕2873号)、《国家发展改革委办公厅关于印发万家企业节能目标责任考核实施方案得通知》(发改环资〔2012〕1923号)、省经信委《关于印发“十二五”广东省万家企业节能低碳行动实施方案》(粤经信节能〔2012〕95号)等得要求,每年度政府部门均制定了《年度企业节能考核工作方案》。
按方案,所有具有一定规模得陶瓷生产企业,均被列入了年度考核。
政府负责节能监管部门得明确:在对陶瓷企业2015年度得节能考核时,将全面执行按GB21252-2013标准得能耗限额计算产品单位能耗来进行考核。
本文主要通过对当前比较有代表性得陶瓷生产企业得能耗现状,分析陶瓷企业得生产能耗能否达到限额得要求?能否通过政府部门得每年度节能执法、核查?目前企业得总能耗与分工序能耗数据如何?若采取当前企业已有采用得行之有效得节能措施将可降低能耗多少?为陶瓷生产建设资源节约型、环境友好型企业,推进节能技术进步、加强能源管理提出建议及方向。
二、陶瓷企业能耗现状为了解当前陶瓷企业得能耗水平,我们收集了来源自企业统计、上报政府部门并经过审核得广东省某市42家企业2014年度生产得共55个陶瓷砖产品得生产能耗数据。
其中:吸水率E≤0、5%陶瓷砖共36个产品;吸水率0、5%≤E≤10%陶瓷砖共7个产品;吸水率E>10%陶瓷砖共12个产品。
按新得国家标准GB 21252-2013《建筑卫生陶瓷单位产品能源消耗限额》计算,其中,抛光砖产品共生产产量为7008644吨,折合290150976平方米,总消耗能源1708638tce(其中电耗为165127万kWh,折标准煤202941tce),平均单位产品生产能耗为5、86kgce/m2,电耗为5、69kWh/m2,煤电消耗比为88、12:11、88;外墙砖产品共生产产量为435762吨,折合30248611平方米,消耗能源115296tce(其中电耗为10124万kWh,折标准煤12442tce),平均单位产品生产能耗为3、71kgce/m2,电耗为3、80kWh/m2,煤电消耗比为89、21:10、79;仿古砖产品共生产产量为491961吨,折合28173471平方米,消耗能源95705tce(其中电耗为8705万kWh,折标准煤10698tce),平均单位产品生产能耗为3、92kgce/m2,电耗为3、53kWh/m2,煤电消耗比为88、82:11、18;釉面砖产品共生产产量为2149967吨,折合120636179平方米,消耗能源527846tce(其中电耗为36039万kWh,折标准煤44292tce),平均单位产品生产能耗为4、25kgce/m2,电耗为3、48kWh/m2,煤电消耗比为91、61:8、39。
生产抛光砖(吸水率E≤0、5%)得31个产品能耗平均为5、86kgce/m2;生产外墙砖(吸水率E≤0、5%),由于砖厚度比抛光砖薄很多(产品单位面积重量为14、56kg/m2),5个产品能耗平均为3、71kgce/m2;生产仿古砖(吸水率0、5%≤E≤10%)共7个产品能耗平均为3、92kgce/m2;生产釉面砖(吸水率E>10%)共12个产品能耗平均为4、25kgce/m2。
该42家企业得陶瓷砖产品能耗均低于GB 21252-2013《建筑卫生陶瓷单位产品能源消耗限额》得限额要求。
这与该市陶瓷企业对节能工作十分重视,近几年来积极投入资金推进节能技术改造与加强企业能源管理有很大关系。
三、关于能耗限额计算若按原标准得单位合格品重量产量能耗限定值(kgce/t)折算为新标准得单位合格品面积产量能耗限定值(kgce/㎡),即如果企业得生产能耗已达到原标准得能耗限额得话,其所生产得产品单位面积重量需要达到:吸水率E≤0、5%陶瓷砖为22、94kg/m2;吸水率0、5%≤E≤10%陶瓷砖为17、33kg/m2;吸水率E>10%陶瓷砖为16、88kg/m2。
反之,如果企业生产得产品单位面积重量超过上述得数值,将达不到新标准得能耗限额要求。
也就就是说,企业生产产品单位面积重量越小得,将更有利于达到限额要求。
而对生产超过产品单位面积重量得企业,则提高了限额要求。
究竟目前企业生产得陶瓷砖单位面积重量得现状如何?能否达到折算陶瓷砖单位面积重量?据表1统计得55个产品得数据,吸水率E≤0、5%陶瓷砖、吸水率0、5%≤E≤10%陶瓷砖、吸水率E>10%陶瓷砖几个类型得产品平均单位面积重量数据,生产得31个抛光砖产品平均陶瓷砖单位面积重量为24、34kg/m2,超过新旧标准折算陶瓷砖单位面积重量折算数值;所生产得5个外墙砖产品平均陶瓷砖单位面积重量为14、56kg/m2,低于新旧标准折算陶瓷砖单位面积重量折算数值;所生产得7个仿古砖产品平均陶瓷砖单位面积重量为19、86kg/m2,超过新旧标准折算陶瓷砖单位面积重量折算数值;所生产得12个釉面砖产品平均陶瓷砖单位面积重量为17、83kg/m2,超过新旧标准折算陶瓷砖单位面积重量折算数值。
除了个别企业得产品能达到产品单位面积重量要求外,目前我们大多数陶瓷企业生产得产品仍然大于按新、旧标准折算陶瓷砖单位面积重量。
即:如果企业得综合能耗已经达到了旧标准得能耗限额得话,按其现在生产得产品单位面积重量,该企业将完全达不到新标准得能耗限额。
其中:抛光砖为8、28kgce/㎡,将超标6、15%;仿古砖为5、96kgce/㎡,将超标14、62%;釉面砖为5、71kgce/㎡,将超标5、74%。
我们可按本企业得产品单位面积重量,按此计算一下就是否在新、旧标准转换时对本企业能耗计算得影响。
就是否考虑采取减薄本企业产品得厚度来达到节能目得。
如不考虑此措施,则将需要在其它节能措施得实施上更加努力。
四、各工序能耗状况1、原料加工工序能耗我们曾经测定了生产抛光砖、仿古、釉面砖得30家企业得原料加工工序得能源消耗情况。
生产抛光砖得16家企业平均原料加工总能耗为57、09kgce/t粉料,其中电力消耗为55、61kWh/t;生产仿古砖得4家企业平均原料加工总能耗为60、07kgce/t粉料,其中电力消耗为65、37kWh/t;生产釉面砖得10家企业平均原料加工总能耗为53、56kgce/t粉料,其中电力消耗为44、09kWh/t。
这些企业得原料加工工序使用燃料大多为水煤浆也有部份兼使用煤焦油。
计算原料加工得燃料消耗时均按照实际燃料用量并对燃料化验实际检测得热值换算成粉料生产标准煤消耗,原料生产电耗为企业计量统计得实际用电量×折标系数(0、1229kgce/kWh)计算。
2、压砖工序能耗我们曾经对较有代表性得生产不同规格得压砖机进行了用电量测定,所测定得产品得用电单耗见表6。
考虑到由于各企业压砖机单位时间压砖次数、每次压砖件数随着窑炉产量与产品转换经常调整,故我们不再分产品品种与规格,仅取所测定得平均值作为压砖工序能耗,即取平均0、053kgce/m2。
3、窑炉烧成工序能耗窑炉烧成工序就是陶瓷企业能耗(特别就是燃料消耗)最大得工序。
我们采用了2012年《全国窑炉(陶瓷砖)能耗调查》时实际对窑炉进行热平衡测定得生产抛光砖、仿古、釉面砖得41条窑炉得能源消耗情况。
其中生产抛光砖得22条窑炉平均总能耗为2、73kgce/m2,其中电力消耗为0、44kgce/m2;生产仿古砖得8条窑炉平均总能耗为2、11kgce/m2,其中电力消耗为0、37kgce/m2;生产釉面砖得11家企业平均总能耗为2、71kgce/m2,其中电力消耗为0、34kgce/m2。
计算窑炉得燃料消耗时均按照实际测试消耗燃料量并对燃料化验实际检测得热值换算成窑炉烧成生产标准煤消耗,窑炉烧成电耗也为实际测量得各风机得实际用电量×折标系数(0、1229kgce/kWh)计算。
4、抛光或磨边工序能耗调查了生产抛光砖、仿古砖、釉面砖得20家企业得抛光或磨边工序得能源消耗情况。
生产抛光砖得15家企业平均电力消耗为77、79kWh/t,折算能耗为9、56kgce/t产品;生产仿古砖、釉面砖得5家企业平均电力消耗为11、97kWh/t,折算能耗为1、47kgce/t产品。
这些企业抛光或磨边工序电耗为企业电能仪表计量统计得实际用电量×折标系数(0、1229kgce/kWh)计算。
按表3所统计得实际产品单位面积重量计,则折算为成品砖后抛光或磨边工序得能耗为:5、各工序能耗比例按以上测算得各工序能耗,仅为对某些企业得各工序进行测定所得到得数据,未能与对上述某市42家企业2014年度生产得共55个产品得生产能耗数据对应。
与这些数据未能同时测定有关,但也反映了各工序能耗得现状。
窑炉烧成工序能耗占企业总能耗得份额最大,其次为原料生产工序能耗。
如何降低该二工序得能耗,就是企业节能得主攻方向。
其中:窑炉烧成工序得燃料消耗仍占该工序总能耗得比例在83%以上,原料生产工序得燃料消耗仍占该工序总能耗得比例在88%以上,降低燃料消耗应当就是这二个工序降低能耗得关键。
而原料生产工序与窑炉烧成工序得电能消耗则占企业总用电量得85%以上,降低电能消耗也就是这二个工序降低企业产品能耗得关键。
五、节能措施对各工序能耗得影响我们从以上对陶瓷企业生产能耗现状及对各工序能源消耗得分析,可见陶瓷砖产品生产仍然属于较高能耗得产品。
为了降低产品生产能源消耗,陶瓷行业近年来不断地采取设备改造成、更新工艺、强化企业内部能源管理等措施,产品生产能耗已经得到逐年下降。
当前我国政府与社会舆论呼吁“节能、减排、降耗”,政府相关部门制订严格得能源消耗与污染物排放指标,对超标用能、超标排放得企业采取限产、处罚或关停得措施。
在不久将来得“十三五”期间,将对用能企业制订“碳排放”指标,用能单位将要依据碳排放总量进行“碳交易”。
而近年来,政府部门要求企业使用清洁能源,陶瓷企业“煤改气”已首当其冲,大大增加企业得能源成本。
陶瓷企业与节能技术供应商多年来致力于开发适用得节能技术,也收到一定得节能效果。