外螺纹车刀对刀方法【技巧】
数控车床上修复螺纹时的对刀问题

数控车床上修复螺纹时的对刀问题孟生才安工大职业技术学院摘要:针对数控车床修复钻杆螺纹及精加工蜗杆时,怎样使刀尖对准原螺旋线从而修复螺纹的问题,提出利用光电编码器的零位信号,通过光电隔离电路控制外部指示灯和发声器,通过发光和声音确定修复螺纹的零位和起始位置,实现旧螺纹的修复和蜗杆的精加工。
该方法结构简单,对数控机床无大的改动,使用方便,效果较好。
关键词:已有螺纹修复对刀光电编码器零位信号一、问题的提出:问题1:某地质企业大量加工钻杆螺纹,由于钻井内的温度高,压力大,所以其连接的锥管螺纹牙型容易损坏。
因地质钻杆材料的性能高,优质管材大都是进口的。
为节约材料,锥螺纹不是全部切除,而是修复。
以外螺纹为例(见图1),修复时,把端面切掉一定的长度L,台肩面也相应地切除厚度为L的余量,再把直径增大了的外锥面加工到要求的尺寸,最后再沿着原来螺纹螺旋槽的轨迹,把变浅的螺纹沟槽加工到设计深度,即可把损坏了的螺纹修复一新,使钻杆得到重复利用。
而锥螺纹的大端有轴肩,螺纹精度又高,所以修复起来难度较大。
因为该机械厂已购买了数控车床进行锥螺纹的加工,效率大大提高,但锥螺纹的修复却因为螺纹对刀时难以对准原螺旋槽,起始位置找不准,总是乱牙,所以修复成了棘手的的问题。
图1锥螺纹修复方法问题2:数控车床在加工蜗杆和高精度螺纹时,往往都要分粗、精车,这就要有两把刀。
现在大多数厂是同时对好两把刀,中途不换刀一次加工完工件。
但在实际加工中,经常会出现刀具磨损,或者刀具损坏的情况,此时需要将刀取下,换好新刀后,重新加工,这时又存在着在已加工螺纹上的准确对刀问题。
二、该问题的已有解决方法:1、NUM数控系统设置了“螺纹继续切削”功能。
其思路是采用手工对刀的方式,在任意位置得到原有螺纹某点处的位置及主轴对应的转角,以此作为螺纹切削功能—G33 指令中的两个参数,系统根据这两个参数自动计算出起刀点对应的主轴转角。
加工时,当主轴转至该转角时,发出指令信号,使伺服轴进入随动状态。
三角形螺纹车刀刃磨及车削方法
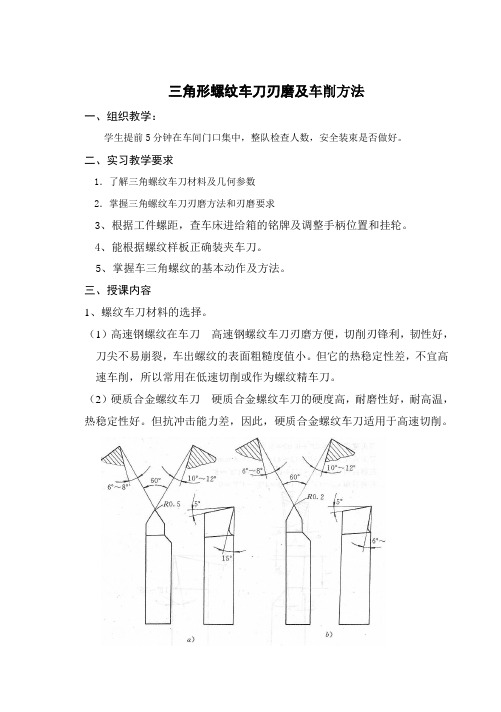
三角形螺纹车刀刃磨及车削方法一、组织教学:学生提前5分钟在车间门口集中,整队检查人数,安全装束是否做好。
二、实习教学要求1.了解三角螺纹车刀材料及几何参数2.掌握三角螺纹车刀刃磨方法和刃磨要求3、根据工件螺距,查车床进给箱的铭牌及调整手柄位置和挂轮。
4、能根据螺纹样板正确装夹车刀。
5、掌握车三角螺纹的基本动作及方法。
三、授课内容1、螺纹车刀材料的选择。
(1)高速钢螺纹在车刀高速钢螺纹车刀刃磨方便,切削刃锋利,韧性好,刀尖不易崩裂,车出螺纹的表面粗糙度值小。
但它的热稳定性差,不宜高速车削,所以常用在低速切削或作为螺纹精车刀。
(2)硬质合金螺纹车刀硬质合金螺纹车刀的硬度高,耐磨性好,耐高温,热稳定性好。
但抗冲击能力差,因此,硬质合金螺纹车刀适用于高速切削。
2、刃磨螺纹车刀有四点要求:1)当螺纹车刀径向前r p=00时,刀尖角应等于牙型角;当螺纹车刀径向前角r p>00时,刀尖角必须修正。
2)螺纹车刀两侧切削刃必须是直线。
3)螺纹车刀切削刃应具有较小的表面粗糙度值。
4)螺纹车刀两侧后角是不相等的,应考虑车刀进给方向的后角受螺纹升角的影响而加减一个螺纹升角φ。
3、螺纹车刀具体刃磨步骤1)先粗磨前刀面;2)磨两侧后刀面,以初步形成两刃夹角。
其中先磨进给方向侧刃(控制刀尖角εr /2及后角α0+φ),再磨背进给方向侧刃(控制好刀尖角εr及后角α0—φ);3)精磨前刀面,以形成前角;4)精磨后刀面,刀尖角用螺纹车刀样板来测量,能得到正确的刀尖角5)修磨刀尖,刀尖侧棱宽度约为0.1P;6)用油石研磨刀刃处的前后面(注意保持刃口锋利)。
4、刃磨时应注意的问题1)刃磨时,人的站立姿势要正确。
在刃磨整体式内螺纹车刀内侧时,易将刀尖磨歪斜。
2)磨削时,两手握着车刀与砂轮接触的径向压力应不小于一般车刀。
3)磨外螺纹车刀时,刀尖角平分线应平行刀体中线;磨内螺纹车刀时,刀尖角平分线应垂直于刀体中线。
4)车削高阶台的螺纹车刀,靠近高阶台一侧的刀刃庆短些,否则易擦伤轴肩,5)粗磨时也要用车刀样板检查。
数控车床对刀原理及方法步骤(实用详细)

数控车床对刀原理及对刀方法对刀是数控加工中的主要操作和重要技能。
在一定条件下,对刀的精度可以决定零件的加工精度,同时,对刀效率还直接影响数控加工效率。
仅仅知道对刀方法是不够的,还要知道数控系统的各种对刀设置方式,以及这些方式在加工程序中的调用方法,同时要知道各种对刀方式的优缺点、使用条件(下面的论述是以FANUC OiMate数控系统为例)等. 1 为什么要对刀一般来说,零件的数控加工编程和上机床加工是分开进行的。
数控编程员根据零件的设计图纸,选定一个方便编程的坐标系及其原点,我们称之为程序坐标系和程序原点。
程序原点一般与零件的工艺基准或设计基准重合,因此又称作工件原点.数控车床通电后,须进行回零(参考点)操作,其目的是建立数控车床进行位置测量、控制、显示的统一基准,该点就是所谓的机床原点,它的位置由机床位置传感器决定。
由于机床回零后,刀具(刀尖)的位置距离机床原点是固定不变的,因此,为便于对刀和加工,可将机床回零后刀尖的位置看作机床原点.在图1中,O是程序原点,O’是机床回零后以刀尖位置为参照的机床原点。
编程员按程序坐标系中的坐标数据编制刀具(刀尖)的运行轨迹。
由于刀尖的初始位置(机床原点)与程序原点存在X向偏移距离和Z向偏移距离,使得实际的刀尖位置与程序指令的位置有同样的偏移距离,因此,须将该距离测量出来并设置进数控系统,使系统据此调整刀尖的运动轨迹.所谓对刀,其实质就是侧量程序原点与机床原点之间的偏移距离并设置程序原点在以刀尖为参照的机床坐标系里的坐标。
2 试切对刀原理对刀的方法有很多种,按对刀的精度可分为粗略对刀和精确对刀;按是否采用对刀仪可分为手动对刀和自动对刀;按是否采用基准刀,又可分为绝对对刀和相对对刀等。
但无论采用哪种对刀方式,都离不开试切对刀,试切对刀是最根本的对刀方法。
以图2为例,试切对刀步骤如下:①在手动操作方式下,用所选刀具在加工余量范围内试切工件外圆,记下此时显示屏中的X坐标值,记为Xa。
数控车床对刀步骤
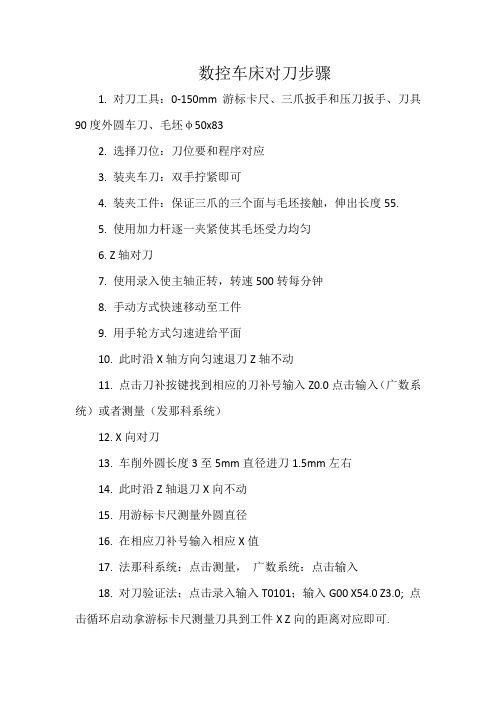
数控车床对刀步骤
1. 对刀工具:0-150mm游标卡尺、三爪扳手和压刀扳手、刀具90度外圆车刀、毛坯φ50x83
2. 选择刀位:刀位要和程序对应
3. 装夹车刀:双手拧紧即可
4. 装夹工件:保证三爪的三个面与毛坯接触,伸出长度5
5.
5. 使用加力杆逐一夹紧使其毛坯受力均匀
6. Z轴对刀
7. 使用录入使主轴正转,转速500转每分钟
8. 手动方式快速移动至工件
9. 用手轮方式匀速进给平面
10. 此时沿X轴方向匀速退刀Z轴不动
11. 点击刀补按键找到相应的刀补号输入Z0.0点击输入(广数系统)或者测量(发那科系统)
12. X向对刀
13. 车削外圆长度3至5mm直径进刀1.5mm左右
14. 此时沿Z轴退刀X向不动
15. 用游标卡尺测量外圆直径
16. 在相应刀补号输入相应X值
17. 法那科系统:点击测量,广数系统:点击输入
18. 对刀验证法:点击录入输入T0101;输入G00 X54.0 Z3.0; 点击循环启动拿游标卡尺测量刀具到工件X Z向的距离对应即可.。
数控车床的对刀与刀具补偿(附图)

数控车床的对刀与刀具补偿(附图)一、对刀对刀的目的是确定程序原点在机床坐标系中的位置,对刀点可以设在零件上、夹具上或机床上,对刀时应使对刀点与刀位点重合。
数控车床常用的对刀方法有三种:试切对刀、机械对刀仪对刀(接触式)、光学对刀仪对刀(非接触式),如图3-9 所示。
1、试切对刀1 )外径刀的对刀方法如图3-10 所示。
Z 向对刀如(a) 所示。
先用外径刀将工件端面( 基准面) 车削出来;车削端面后,刀具可以沿X 方向移动远离工件,但不可Z 方向移动。
Z 轴对刀输入:“Z0 测量”。
X 向对刀如(b) 所示。
车削任一外径后,使刀具Z 向移动远离工件,待主轴停止转动后,测量刚刚车削出来的外径尺寸。
例如,测量值为Φ50.78mm, 则X 轴对刀输入:“X50.78 测量”。
2 )内孔刀的对刀方法类似外径刀的对刀方法。
Z 向对刀内孔车刀轻微接触到己加工好的基准面(端面)后,就不可再作Z 向移动。
Z 轴对刀输入:“Z0 测量”。
X 向对刀任意车削一内孔直径后,Z 向移动刀具远离工件,停止主轴转动,然后测量已车削好的内径尺寸。
例如,测量值为Φ45.56mm, 则X 轴对刀输入:“X45.56 测量”。
3 )钻头、中心钻的对刀方法如图3-11 所示。
Z 向对刀如(a )所示。
钻头( 或中心钻) 轻微接触到基准面后,就不可再作Z 向移动。
Z 轴对刀输入:“Z0 测量”。
X 向对刀如(b )所示。
主轴不必转动,以手动方式将钻头沿X 轴移动到钻孔中心,即看屏幕显示的机械坐标到“X0.0 ”为止。
X 轴对刀输入:“X0 测量”。
2、机械对刀仪对刀将刀具的刀尖与对刀仪的百分表测头接触,得到两个方向的刀偏量。
有的机床具有刀具探测功能,即通过机床上的对刀仪测头测量刀偏量。
3、光学对刀仪对刀将刀具刀尖对准刀镜的十字线中心,以十字线中心为基准,得到各把刀的刀偏量。
二、刀具补偿值的输入和修改根据刀具的实际参数和位置,将刀尖圆弧半径补偿值和刀具几何磨损补偿值输入到与程序对应的存储位置。
螺纹对刀方法

N90G92X16.16Z-124.0
N100G00W0.03
N110G92X16.16Z-124.0
N120G00W0.02
N130G92X16.16Z-124.0
N140G00W0.01
说明:(1)程序中W-0.14的数值可根据对刀时齿右侧面与刀具左刃间隙及齿左侧面车削情况确定;
(2)程序中具体走刀次数可根据实际加工余量调整。
4、结论
采用上述方法可以在数控车床上车削卧式车床无法加工的非标准模数蜗杆或非标准螺距梯形螺纹,并可利用数控车床刚性好、加工精度高的优势获得精度较高的蜗杆或梯形螺纹。但上述方法加工效率较低,适用于单件小批量生产。
N220G00W-0.02
N230G92X16.16Z-Байду номын сангаас24.0
N240G00W-0.01
N250G92X16.16Z-124.0
N260G00X100.0M09
N270G30U0W0M05
N280M30
对精度要求较高的蜗杆,我们一般采用两把车刀,即一把粗车刀、一把精车刀进行车削。在数控车床上粗车蜗杆后换刀精车时,往往因为对刀问题,使车削无法继续进行,从而限制了数控车床在蜗杆车削方面的应用。
过去一段时间,我们在解决数控车床精车蜗杆对刀问题方面进行了一些尝试,找到了一种有效的方法,现以配置FAUNC-0TC系统的CK7815D数控车床车削阿基米德蜗杆(ZA型)为例简要介绍如下。
(5)蜗杆精车,调用蜗杆精车程序,先以背吃刀量为0.04~0.01mm逐渐递减精车齿槽一侧,至表面粗糙度符合图样要求,再用同样方法精车齿槽另一侧,保证图样要求的表面粗糙度及齿厚尺寸。
对刀方法
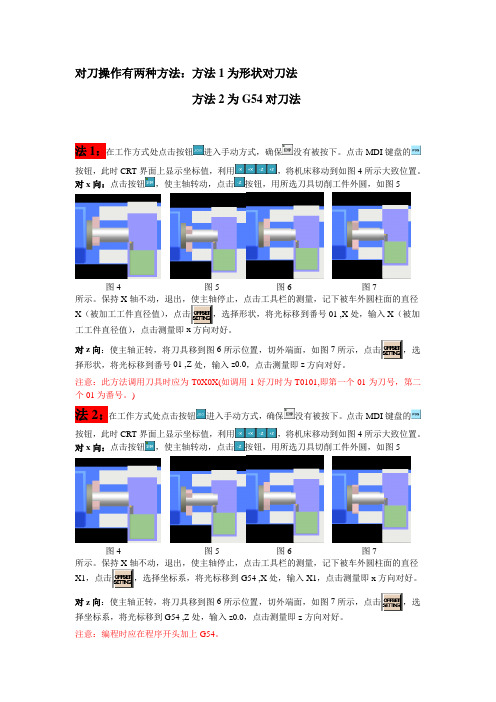
对刀操作有两种方法:方法1为形状对刀法
方法2为G54对刀法
法1:在工作方式处点击按钮进入手动方式,确保没有被按下。
点击MDI键盘的
按钮,此时CRT界面上显示坐标值,利用,将机床移动到如图4所示大致位置。
对x向:点击按钮,使主轴转动,点击按钮,用所选刀具切削工件外圆,如图5
图4 图5 图6 图7
所示。
保持X轴不动,退出,使主轴停止,点击工具栏的测量,记下被车外圆柱面的直径X(被加工工件直径值),点击,选择形状,将光标移到番号01 ,X处,输入X(被加工工件直径值),点击测量即x方向对好。
对z向:使主轴正转,将刀具移到图6所示位置,切外端面,如图7所示,点击,选择形状,将光标移到番号01 ,Z处,输入z0.0,点击测量即z方向对好。
注意:此方法调用刀具时应为T0X0X(如调用1好刀时为T0101,即第一个01为刀号,第二个01为番号。
)
法2:在工作方式处点击按钮进入手动方式,确保没有被按下。
点击MDI键盘的
按钮,此时CRT界面上显示坐标值,利用,将机床移动到如图4所示大致位置。
对x向:点击按钮,使主轴转动,点击按钮,用所选刀具切削工件外圆,如图5
图4 图5 图6 图7
所示。
保持X轴不动,退出,使主轴停止,点击工具栏的测量,记下被车外圆柱面的直径X1,点击,选择坐标系,将光标移到G54 ,X处,输入X1,点击测量即x方向对好。
对z向:使主轴正转,将刀具移到图6所示位置,切外端面,如图7所示,点击,选择坐标系,将光标移到G54 ,Z处,输入z0.0,点击测量即z方向对好。
注意:编程时应在程序开头加上G54。
确定对刀点的方法
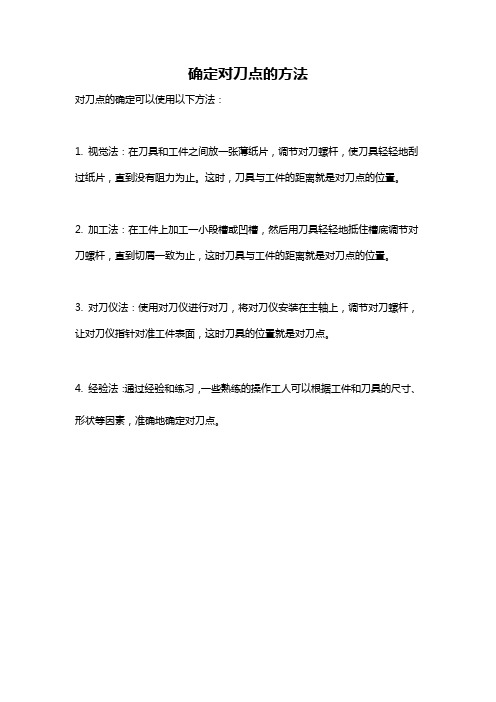
确定对刀点的方法
对刀点的确定可以使用以下方法:
1. 视觉法:在刀具和工件之间放一张薄纸片,调节对刀螺杆,使刀具轻轻地刮过纸片,直到没有阻力为止。
这时,刀具与工件的距离就是对刀点的位置。
2. 加工法:在工件上加工一小段槽或凹槽,然后用刀具轻轻地抵住槽底调节对刀螺杆,直到切屑一致为止,这时刀具与工件的距离就是对刀点的位置。
3. 对刀仪法:使用对刀仪进行对刀,将对刀仪安装在主轴上,调节对刀螺杆,让对刀仪指针对准工件表面,这时刀具的位置就是对刀点。
4. 经验法:通过经验和练习,一些熟练的操作工人可以根据工件和刀具的尺寸、形状等因素,准确地确定对刀点。
浅谈车削螺纹训练中的常见问题

论坛大家谈编辑︱杨晴︱E-mail:zhiyezazhi@DISCUSSION笔者对车削螺纹时常见故障及解决方法总结如下。
一、啃刀1.故障分析车刀安装得过高或过低,工件装夹不牢或车刀磨损过大。
2.解决方法(1)及时提高车刀高度,使其刀尖与工件的轴线等高(可利用尾座顶尖对刀)。
在粗车和半精车时,刀尖位置比工件的中心高出1%D左右(D表示被加工工件直径)。
(2)把工件装夹牢固,可使用尾座顶尖等,以增加工件刚性。
(3)车刀磨损过大,引起切削力增大,顶弯工件,出现啃刀。
对车刀加以修磨。
二、乱扣1.故障分析当丝杠转一转时,工件未转过整数转而造成。
2.解决方法(1)当车床丝杠螺距与工件螺距比值不成整倍数时,如果在退刀时,采用打开开合螺母,将床鞍摇至起始位置,那么,再次闭合开合螺母时,就会发生车刀刀尖不在前一刀所车出的螺旋槽内,以致出现乱扣,应采用正反车法来退刀,即在第一次行程结束时,不提起开合螺母,把刀沿径向退出后,将主轴反转,使车刀纵向退回,再进行第二次行程,这样往复过程中,因主轴、丝杠和刀架之间的传动链始终脱开,车刀始终在原来的螺旋槽中,就不会出现乱扣。
采用倒顺车法时,主轴转向不得太快,否则会使机床的传动件受冲击而损坏,在卡盘处应装有保险装置,以防主轴反转时卡盘脱落。
(2)对于车削机床丝杠螺距与工件回转比值成整倍数的螺纹工件和丝杠都在旋转,提起开合螺母后,至少要等丝杠转过一转,才能重新合上开合螺母,这样当丝杠转过一转时,工件转了整数倍,车刀就能进入前一刀车出的螺旋槽内,就不会出现乱扣。
三、螺距不正确1.故障分析螺纹全长或局部上下不正确,螺纹全长上螺距不均匀或螺纹上出现竹节纹。
2.解决方法(1)挂轮搭配不当或进给箱手柄位置不对,可重新检查进给箱手柄位置或验算桂轮。
(2)车床丝杠本身的螺距误差或主轴和丝杠的轴向窜动,螺纹局部上螺距不正确,预防措施为,车削螺纹前,将主轴与丝杠轴向窜动和开合螺母的间隙进行高速并将大滑板的齿轮与传齿条脱开,使大滑板能匀速运动。
怎样用车床车螺纹(包括正反丝) 车螺纹的步骤与方法

.;. 怎样用车床车螺纹(包括正反丝) 车螺纹的步骤与方法问题:怎样用车床车螺纹(包括正反丝)车螺纹的步骤与方法:(低速车削三角形螺纹 Vく5米∕分) 1、车螺纹前对工件的要求: 1)螺纹大径:理论上大径等于公称直径,但根据与螺母的配合它存在有下偏差(—),上偏差为0;因此在加工中,按照螺纹三级精度要求。
螺纹外径比公称直径小0.1p。
螺纹外径D=公称直径—0.1p 2)退刀槽:车螺纹前在螺纹的终端应有退刀槽,以便车刀及时退出。
3)倒角:车螺纹前在螺纹的起始部位和终端应有倒角,且倒角的小端直径く螺纹底径。
4)牙深高度(切削深度):h1=0.6p 2、调整车床:先转动手柄接通丝杠,根据工件的螺距或导程调整进给箱外手柄所示位置。
调整到各手柄到位。
3、开车、对刀记下刻度盘读数,向右退出车刀。
4、合上开合螺母,在工件表面上车出一条螺旋线,横向退出车刀,并开反车把车刀退到右端,停车检查螺距是否正确(钢尺)。
5、开始切削,利用刻度盘调整切深(逐渐减小切深)。
注意操作中,车刀将终了时应做好退刀、停车准备,先快速退出车刀,然后开反车退回刀架。
吃刀深度控制,粗车时t=0.15~0.3mm,精车时tく0.05mm。
六、螺纹的测量: 1、单向测量法: 1)顶径的测量:螺纹顶径的尺寸,一般都允许有较大的误差,外螺纹顶径可用游标卡尺或千分尺测量,内螺纹顶径可用游标卡尺测量。
2)螺距的测量:螺距一般可用钢尺测量, 3)中径的测量:(1)用螺纹千分尺测量螺纹中径。
(2)用三针法测量螺纹中径。
三针法测量螺纹中径是一种比较精密的测量方法。
2、综合测量法:综合测量法就是对螺纹的各项尺寸用螺纹量规进行综合性的测量七、安全生产: 1)车螺纹前检查车床正反车操纵机构及开合螺母等,以防操作失灵。
2)在吃刀时注意不要多摇进一圈,否则会发生车刀撞坏,工件顶弯或飞出等事故。
3)不能用手模螺纹表面,更不能用棉纱去擦正在旋转的螺纹工件,以防发生事故。
04【教案】 项目四 数控车床常用刀具的对刀方法

课题项目四数控车床常用刀具的对刀方法教学内容教学目标知识目标1、了解数控车床机床坐标系统2、了解数控车床工件坐标系统3、了解数控车床机床坐标,绝对坐标和相对坐标及余动量之间的关系技能目标1、会安装刀具对中心高2、会建立工件坐标系操作3、会使用相对坐标操作机床4、会目测校正工件素质目标1、对零件加工过程能建立工件坐标系统的概念2、对刀具运行的位置能判断出加工轨迹是否正确,是否会撞机教学重难点重点:了解数控车床机床坐标,绝对坐标和相对坐标及余动量之间的关系难点:会建立工件坐标系操作教学准备PPT、数控车床教学时间第四周教学过程备注一、情景描述数控车床的加工过程是刀具按编制的程序对工件进行自动切削完成的,而程序就是按坐标位置编制的刀具运动指令,那么这个工件的坐标系统是如何建立的?需要进行怎样的操作过程?二、刀具安装与检查要点1、根据零件加工特征选择相应的刀具,根据切削材料选择对应的刀片,并注意刀具相关角度。
2、刀具安装时所安装刀位号应与程序编制一致。
如编程为T0101,则刀具应安装在01号刀位上。
3、刀具安装时,伸出长度应根据加工条件,不宜伸出过长,确保刀具加工的刚性。
一般伸出刀杆的1.5倍为宜。
内孔特征加工时,刀具伸长尤其注意。
4、刀具安装时,应确保刀尖与车床主轴的中心等高。
内孔特征刀具可略高于主轴中心高。
可采用车削端面的方法来观察,可以通过加垫刀片的方法调整高度)三、外圆车刀安装与检查视频展示:四、对刀进解与练习1、外圆粗车刀对刀2、外圆精车刀对刀3、外圆槽刀对刀4、外圆螺纹刀对刀五、切削参数的应用与选择切削用量是指切削深度(吃刀深度)、进给量和切削速度。
1、背吃刀量ap的确定背吃刀量主要根据机床、刀具、夹具和零件的刚度而定。
粗加工时,在系统刚性允许的条件下,尽可能选择较大的背吃刀量,以减少进给次数,提高生产率;精加工时,通常选取较小的背吃刀量,-般为0.1-0.5mm,以保证加工精度及表面粗糙度。
中职教育-《车工技术项目训练教程》课件:项目12.1 外三角螺纹车削的基本知识.ppt

3.如何防止乱牙和重新对刀 乱牙指车螺纹时,在第一刀车削完后,车削第二刀
时,螺纹刀不在车削的螺旋槽内,这样会切掉前面已加 工好的螺旋槽称为乱牙。当被加工工件的螺距与车床丝 杠的螺距不是整数倍时,会出现乱牙现象。这时我们可 采用开倒顺车的方法来加工螺纹,可以避免乱牙现象。 重新对刀是指在加工螺纹时刀具发生崩刃等情况,刀具 须刃磨,刀具刃磨安装后,为了防止乱牙,须重新对刀, 重新对刀的方法是选择较低的机床转数,按下开合螺母, 控制小刀架,使刀尖对准已加工过的螺旋槽中心,然后 继续加工。 4.背吃刀量的选择:车螺纹时,其总背吃刀量ap =0.65 P(P为螺距)中滑板转过格数n可用下式计算:
③其它角度:根据粗车、精车要求,要刃磨出合理的前 角、后角;粗车刀前角大、后角小,精车刀正好相反; 刃磨后的左右两边刀刃必须呈直线,无崩刃;刀头不能 歪斜,牙型角半角相等。
(a)高速钢三角形螺纹车刀 (b)硬质合金三角形螺纹车刀 图12-4 三角形螺纹车刀的刃磨角度
(2)刃磨方法 ①粗磨后面:先磨左侧后面,双手紧握刀,使刀柄与砂 轮外圆水平方向成30°,垂直方向倾斜约8°~ 10 °, 慢慢靠近砂轮,当车刀与砂轮接触后略使劲加压,均匀 移动进行磨削。再磨右后面。边磨边用磨刀样板检查直 至达到要求。 ②粗磨前面:前刀面与砂轮水平成10°~ 15°的倾斜, 同时使右侧切削刃略高左切削刃。慢慢靠近砂轮,当前 面与砂轮接触后略使劲加力进行磨削。 ③精磨:各个面的精磨方法与粗磨相同。 ④刃磨刀尖:刀尖轻轻接触砂轮后做圆弧形摆动即可, 如图12-5所示。
③斜进法:当螺距较大、螺纹槽较深、切削余量较多时, 粗车为了操作方便,除中滑板直进外,小滑板只向一个 方向移动,这种方法称之为斜进法,如图12-10c所示。 此方法只用于粗车,且每边牙侧留0.1 ~ 0.2 mm的精车 余量,精车时,应采用左右切削法车削。
车螺纹的步骤与方法

精心整理车螺纹的步骤与方法:(低速车削三角形螺纹Vく5米∕分)1、车螺纹前对工件的要求:1)螺纹大径:理论上大径等于公称直径,但根据与螺母的配合它存在有下偏差(—),上偏差为0;因此在加工中,按照螺纹三级精度要求。
螺纹外径比公称直径小0.1p。
螺纹外径D=公称直径—0.1p2)退刀槽:车螺纹前在螺纹的终端应有退刀槽,以便车刀及时退出。
342345,精车时tく11测量,内螺纹顶径可用游标卡尺测量。
2)螺距的测量:螺距一般可用钢尺测量,3)中径的测量:(1)用螺纹千分尺测量螺纹中径。
(2)用三针法测量螺纹中径。
三针法测量螺纹中径是一种比较精密的测量方法。
2、综合测量法:综合测量法就是对螺纹的各项尺寸用螺纹量规进行综合性的测量七、安全生产:1)车螺纹前检查车床正反车操纵机构及开合螺母等,以防操作失灵。
2)在吃刀时注意不要多摇进一圈,否则会发生车刀撞坏,工件顶弯或飞出等事故。
3)不能用手模螺纹表面,更不能用棉纱去擦正在旋转的螺纹工件,以防发生事故。
车螺纹的步骤与方法:(低速车削三角形螺纹Vく5米∕分)1、车螺纹前对工件的要求:1)螺纹大径:理论上大径等于公称直径,但根据与螺母的配合它存在有下偏差(—),上偏差为0;因此在加工中,按照螺纹三级精度要求。
螺纹外径比公称直径小0.1p。
螺纹外径D=公称直径—0.1p2342345,精车时tく11232123机床的精度和螺纹车刀刃磨的质量。
螺纹梳刀是螺纹机床上常用的刀具,其制造精度较高(一般情况下,螺纹梳刀的螺纹齿由螺纹磨床磨出),普遍用的是4个一套。
在汽车制造等机械行业中应用较多,消耗量也较大。
因为螺纹梳刀是成套使用,只要其中损坏一个,就要全套报废,造成浪费。
螺纹梳刀实质上是多齿的螺纹车刀,它既有切削部分又有校准部分,所以螺纹梳刀要比用螺纹车刀加工出的螺纹质量好。
由于螺纹梳刀在大规模生产中消耗较多,就可在报废的螺纹梳刀中选一个较好的平体梳刀(也称平体板牙)按图所示加工出梳刀夹持器,将平梳刀夹持其上,用在普通车床上加工长螺纹零件。
数控车床螺纹对刀方法

周知,在光电编码器内部有一个圆光栅,能随工作轴一 示。对 刀 结 束 后,将 扳 动 开
起转动;还有一个指示光栅,是固定不动的;当圆光栅 关断开。最后启动螺纹程序
转动时,其上有一条零位狭缝转到与指示光栅上的零 就可进行螺纹修复加工。在
位狭缝对齐时就会发出零位信号。如果把输出零位信 光电隔离器的输入端接入一
器内部,操作者无法知道零位信号位置,所以不能准确 合回路而发光。这时操作者见到指示灯发光,就停止
对刀。如果把零位信号从内部引向外部,操作者对刀 转动主轴。然后通过手摇脉冲发生器或点动按钮控制
时能知道零位信号位置,即可实现准确对刀。
刀具移到距螺纹槽底 ! 个导程的右侧端头起始位置,
根据上述思路,分析光电编码器内部结构。众所 并加上径向余量,如图 1 所
! 数控车床切削螺纹方法
数控车床切削螺纹简图如图 H 所示。由异步电动 机通过传动比 !H 驱动车床主轴带动工件转动,要完成 切削螺纹必须准确做到工件转一转,刀具进给一个导 程 "。异步电动机的转速可通过变频器控制实现,但转 角位置是不可控的。要具备切削螺纹的功能,必须用 一个光电编码器与主轴 H I H 传动连接[J]。当主轴旋 转时,编码器同步转动,并发出一系列脉冲信号进入数 控系统,再由数控系统进行运算控制,发出指令控制伺 服电动机及刀具做进给运动实现切削螺纹。为了使螺 纹切削在进行两次以上的走刀时不乱扣,在光电编码 器中的光栅盘上设有一条固定的零位狭缝[%],光电编
!""#$%&&’() *%&+", -". !+.%/, 01&&’() "( 020 3/&+%
’() *+,-./,’(0 12-3,4( 5+2+6-3,7)(89 7:-;:( 9,-<: =-2>/?<2@A 6B C/D+-6.63A,E,-F+6: $%&&!&,’G8)
外圆车刀对刀
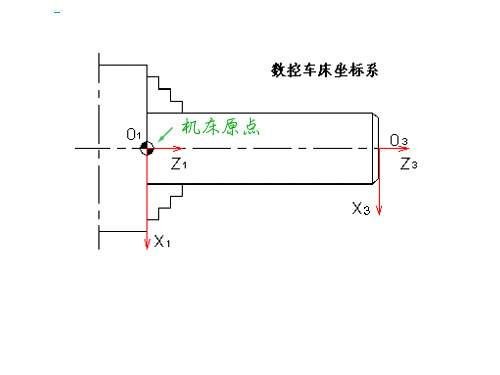
• 机床参点
• 机床参考点是机床坐标系中一个固定不变 的位置点,是用于对机床工作台、滑板与 刀具相对运动的测量系统进行标定和控制 的点。
• 对刀前为什么要回参考点?
• 机床参考点的位置是由机床制造厂家在每个进给 轴上用限位开关精确调整好的,坐标值已输入数 控系统中。因此参考点对机床原点的坐标是一个 已知数。
刀具偏置设定工件坐标系
• 通过对刀将刀偏值写入参数从而获得工件 坐标系。这种方法操作简单,可靠性好, 他通过刀偏与机械坐标系紧密的联系在一 起,只要不断电、不改变刀偏值,工件坐 标系就会存在且不会变,即使断电,重启 后回参考点,工件坐标系还在原来的位置。
• O0001
• G98 • T0101;
• G50 X50. Z50.
• S800 M03 • G00 X55. Z2.;(快速运动至循环起点) • G90 X46. Z-19.8 F150; • (X向单边切深量2mm,端面留余量0.2mm用来精加工) • X42.;(G90模态有效,X向切深至42 mm) • X38.; • X34.; • X31. ;(X向留单边余量0.5 mm用于精加工) • X30. Z-20 F100 S1200;(精车) • G00 X50. Z50.; • M30;
• 零点偏置 G54 一 G59 指令 零点偏置是数控系统的一种特性,即允
许把数控测量系统的原点在相对机床基准 的规定范围内移动,而永久原点的位置被 存贮在数控系统中。因此,当不用 G92 指 令设定工件坐标系时可以用 G54 一 G59 指 令设定六个工件坐标系即通过设定机床所 特有的六个坐标系原点(即工件坐标系 1 -6 的原点) 在机床坐标系中的坐标 值.(即工件零点偏移值)。该值可用 MDI 方式输人相应项中
数控车床对刀方法

数控车床对刀方法机床能对加工对象的适应性强,适应模具等产品单件生产的特点,为模具的制造提供了合适的加工方法。
下面店铺给大家整理了数控车床对刀方法大全,欢迎大家前来阅读参考。
一,直接用刀具试切对刀1. 用外园车刀先试车一外园,记住当前X 坐标,测量外园直径后,用 X 坐标减外园直径,所的值输入 offset 界面的几何形状 X 值里。
2. 用外园车刀先试车一外园端面,记住当前 Z 坐标,输入 offset 界面的几何形状 Z 值里。
二,用 G50 设置工件零点1. 用外园车刀先试车一外园,测量外园直径后,把刀沿Z 轴正方向退点,切端面到中心( X 轴坐标减去直径值)。
2. 选择 MDI 方式,输入 G50 X0 Z0 ,启动 START 键,把当前点设为零点。
3. 选择 MDI 方式,输入 G0 X150 Z150 ,使刀具离开工件进刀加工。
4. 这时程序开头:G50 X150 Z150 …… . 。
5. 注意:用G50 X150 Z150 ,你起点和终点必须一致即X150 Z150 ,这样才能保证重复加工不乱刀。
6. 如用第二参考点 G30 ,即能保证重复加工不乱刀,这时程序开头 G30 U0 W0 G50 X150 Z1507. 在FANUC 系统里,第二参考点的位置在参数里设置,在Yhcnc 软件里,按鼠标右键出现对话框,按鼠标左键确认即可。
三,用工件移设置工件零点1. 在 FANUC0-TD 系统的 Offset 里,有一工件移界面,可输入零点偏移值。
2. 用外园车刀先试切工件端面,这时 Z 坐标的位置如: Z200 ,直接输入到偏移值里。
3. 选择“ Ref ”回参考点方式,按 X 、 Z 轴回参考点,这时工件零点坐标系即建立。
4. 注意:这个零点一直保持,只有从新设置偏移值 Z0 ,才清除。
四,用 G54-G59 设置工件零点1. 用外园车刀先试车一外园,测量外园直径后,把刀沿Z 轴正方向退点,切端面到中心。
数控车床多把刀具加工螺纹的对刀方法

数控车床多把刀具加工螺纹的对刀方法
于文生
【期刊名称】《金属加工:冷加工》
【年(卷),期】2012(000)009
【摘要】我们在数控车床上进行螺纹加工时,通常采用一把刀具进行切削。
在加工大螺距螺纹时,因刀具磨损过快,会造成切削加工后螺纹尺寸变化大、螺纹精度低。
经过多年的探索,我们摸索出了一种在数控车床上切削加工螺纹时,分粗、精车刀进行。
【总页数】1页(P55-55)
【作者】于文生
【作者单位】胜利油田胜机石油装备有限公司,山东东营257067
【正文语种】中文
【中图分类】TG62
【相关文献】
1.数控车床换刀加工梯形螺纹原理分析
2.数控车床加工内外螺纹的对刀技巧
3.数控车床螺纹加工中对刀方法的优化选择
4.数控车床换刀加工梯形螺纹原理分析
5.实训教学中用数控车床加工梯形螺纹时出现扎刀现象的原因及解决方法
因版权原因,仅展示原文概要,查看原文内容请购买。
- 1、下载文档前请自行甄别文档内容的完整性,平台不提供额外的编辑、内容补充、找答案等附加服务。
- 2、"仅部分预览"的文档,不可在线预览部分如存在完整性等问题,可反馈申请退款(可完整预览的文档不适用该条件!)。
- 3、如文档侵犯您的权益,请联系客服反馈,我们会尽快为您处理(人工客服工作时间:9:00-18:30)。
螺纹在日常生活中的应用十分广泛,机械机床、大型设备、航空航天、汽车车零件,船业以及很多连接件中存在着各种各样的螺纹,那么应用最广泛的是普通三角螺纹,普通三角螺纹分为内螺纹和外螺纹,外螺纹加工相对于外圆和内孔的加工比较简单,在数控车床上加工外螺纹关键是掌握螺纹指令格式及各参数的含义,学会螺纹小径的计算,当然也不能忘记加工前的试切对刀,今天教大家正确安装外螺纹车刀的方法以及试切对刀的方法,一起来看看吧。
螺纹的车削加工是数控机床加工中比较常见的,现在主要通过使用可转位刀片来获得高生产效率和高生产安全性,如图所示:
螺纹切削的刀片类型:
全牙型刀片:螺纹切削时可获得高生产效率,这些刀片最为常用,它们可切削出包括牙顶在内的整个螺纹牙型。
V牙型刀片60度与55度:由于这些刀片不能切削牙顶,因此必须在进行螺纹切削之前就将螺栓外径和螺母内径车削到正确直径。
多齿刀片:适用于大批量生产中的高效、经济性螺纹切削,与全牙形刀片很相似,但有两个或更多的齿。
螺纹车刀的安装要求:
1. 刀尖应与车床主轴线等高。
2. 车刀刀尖对称中心线应与工件的轴线垂直,其底面应平放在刀架上。
3. 螺纹车刀安装时应用螺纹角度样板给予校正位置,位置装正后,应用刀架螺钉压紧,至少用两个螺钉并交替拧紧。
螺纹车刀的安装步骤:
1.螺纹车刀刀尖对中心高。
2.角度样板校正车刀,使刀尖对称中心线与工件的轴线垂直。
3.刀架两个螺钉交替拧紧。
试切对刀的过程:
1. 装夹工件及车刀
2. 在手动操作方式下,启动主轴,用当前刀具在加工余量范围内试切工件外圆,车的长度必须能够方便测量,X轴不要移动,沿Z的正方向退出来,停主轴。
3. 测量所车的外圆尺寸Xa.
4. 按“OFS/SET”键,按CRT屏下“刀偏”软键。
5. 按CRT屏下的软键“形状”。
6. 将光标移到刀具号相对应的位置后,输入“Xa”,然后按CRT屏下的软键“测量”,在对应的刀补位上生成对应刀补值。
7. 在手动方式下,用外圆车刀把端面车平整,再使用螺纹车刀刀尖对准工件端面,沿X正方退出来,Z方向不动,停主轴。
8. 按“OFS/SET”键,进入“形状”补偿设定界面,将光标移动与刀位号相对应的位置后,输入“ZO”,按CRT屏下的软键“测量”,在对应的刀补上生成准确的刀补值。
对刀注意事项:
对刀时,刀具接近工件过程中,进给倍率要小,避免产生撞刀现象,其次螺纹刀对刀时采用刀尖对刀,与编程采用的刀位点一致,编程时刀头宽度尺寸应考虑在内,而一般情况下,外圆车刀对刀完成后,螺纹刀可以在其车好的端面和外圆面触碰一下进行试切对刀。
扩展资料:
数控车床外圆刀,切断刀,螺纹刀对刀方法:
1)外圆刀对刀
①按下功能键[PROG],进进程序画面。
再按下[MDI],进进[MDI]模式,通过操纵面板在光标闪动输进“T0101;M03S500;”,按[INSERT]键,将程序插进。
再按[循启动]按钮,执行程序,换外圆刀,同时主轴正转,转速500r/min。
②在JOG或手摇方式下将刀具移至工件四周(靠近时倍率要小些),切削端面,切削完毕,保持Z轴不变,按[+X]退刀,按下[主轴停按钮,或按下[复位]键,此时主轴停止转动。
③连续按功能键[OFFSET SETTING],将G54下X及Z值均设定为0,按动屏幕下部“外形”对应软键进进10所示的画面。
光标移至G01,键盘输进“Z0”按丈量,完成1号刀Z向对刀。
④再次调至JOG或手摇方式,切削外圆。
切削一小段足够卡尺丈量外径的长度后,保持X轴不变,方向退出Z轴,使主轴停止,丈量所切部分的外径。
例如车削外径为30mm,则进进“工具补正/外形”画面后,光标停在G01一行上,键盘上键进“X30”,按“丈量”完成1号刀X向对刀。
⑤1号刀对刀完毕,将刀架移开,退至换刀位置四周。
2)切断刀对刀①在MDI方式下,调切断刀,按[主轴正转]按钮使主轴旋转。
②在JOG或手摇方式下,将刀具移至工件四周,越近时倍率要越小,使切断刀的刀尖与已加工好的工件端面接触,闻声摩擦声或有微小标听在G02一行上,键进“Z0”,按“丈量”,完成2号刀Z向对刀。
③用与步骤(2)相同的方式,将刀具从径向靠近工件。
当切断刀的刀刃与已加工好的工件外圆接触时,停止进给,工具补正/外形”画面里,将光标听在G02一行上,键进“X30”,按“丈量”,完成2号刀X向对刀。
④完成切断刀对刀后,刀架移开,退到换刀位置,使主轴停转。
3)螺纹刀对刀①在MDI方式下,调螺纹刀,按[主轴正转]按钮使主轴旋转。
②在JOG或手摇方式下将刀具移至工件四周,越近时倍率要越小,使螺纹刀的刀尖与已加工好的工件端面平齐,并接触工件的外圆。
③在“工具补正/外形”画面里,将光标停在G03一行上,键进“X30”,按“丈量”,输进数值,完成3号刀X向对刀;键进“Z0”,按“丈量”,完成螺纹刀Z向对对刀。
④刀架移开,退到换刀位置,主轴停转。