连铸板坯表面裂纹形成原因及控制措施
连铸坯表面裂纹形成及防止分析

浸入式水口对中,防止偏流 合理的浸入式水口设计(合适的出口直径,倾角) 合适的水口插入深度 合适的频率和振幅
(3) 结晶器振动
2 铸坯表面纵裂纹
(4) 出结晶器铸坯运行 二次冷却均匀性 (5) 调整钢水成分 钢中碳含量避开包晶区,C向下线或上线控制 钢中S<0.015% 残余元素Cu、As、Zn控制<0.1%
图2-4 拉速对纵裂纹的影响
2 铸坯表面纵裂纹
(3) 保护渣 液渣层厚度<10mm,纵裂纹增加(图2-5)。
图2-5 液渣层厚度对纵裂纹的影响
2 铸坯表面纵裂纹
(4) 结晶器液面波动 液面波动<±5mm,纵裂纹最少(图2-6);
图2-6 结晶器液面波动对纵裂纹的影响
2W (T1 T2 ) W
连铸坯表面裂纹 形成及防止
宋晔
内容
1 2 3 4 5 前言 铸坯表面纵裂纹 铸坯表面横裂纹 铸坯表面星形裂纹 结论
1.前言
连铸坯质量概念: ◆ 铸坯洁净度(夹杂物数量、类型、尺寸、 分布) ◆ 铸坯表面质量(表面裂纹、夹渣、气孔) ◆ 铸坯内部质量(内部裂纹、夹杂物,中 心疏松、缩孔、偏析) ◆ 铸坯形状缺陷(鼓肚、脱方)
2 铸坯表面纵裂纹
2.3 影响表面纵裂纹产生的因素
(1) 钢水成分
◆ [S]>0.015%,纵裂纹增加(图2-2);
◆ [C]=0.12~0.15%,纵裂纹产生严重(图2-3)
图2-2 钢中[S]与裂纹指数的关系
2 铸坯表面纵裂纹
பைடு நூலகம்
图2-3 含碳量对板坯宽面纵裂纹的影响
2 铸坯表面纵裂纹
(2) 拉速 拉速增加,纵裂纹指数增加(图2-4);
连铸坯表面裂纹形成及防止(理化中心)

-
15
横裂纹产生原因
(1) 横裂纹产生于结晶器初始坯壳形成振痕的波谷处,振痕越深, 则横裂纹越严重,在波谷处,由于:一是奥氏体晶界析出沉淀物 (AlN,Nb(CN)),产生晶间断裂(如下图); 二是沿振痕波谷 S、P元素呈正偏析,降低了钢高温强度。这样,振痕波谷处,奥 氏体晶界脆性增大,为裂纹产生提供了条件。
不均匀性强,振痕深,表面易产 生凹陷或横裂纹;生产实践表明, C避开这个区间时,振痕浅了, 铸坯边部横裂减少; (2)降低钢中[N],防止氮化物沉 淀; 2. 结晶器振动特点 (1)振痕深度增加,横裂纹增加 (如图所示);
图: 振痕深度与横裂纹产生几率的关系
-
18
(2)振动频率f增加,振痕变浅,横裂纹减少(如图所示); (3)负滑脱时间增加,振痕深度增加(如图所示),方圆坯 tN=0.12~0.15s,板坯tN=0.20s。
图 铸坯表面的网状裂纹
-
23
铸坯表面星形裂纹产生原因
铸坯表面星形裂纹沿一次晶界分布,裂纹边界有脱C现象,说明是 在结晶器内高温下(1400℃)坯壳奥氏体转变之前形成的。
图 振动频率与振痕深度的关系
-
图 负滑脱与振痕深度的关系
19
Байду номын сангаас
3. 合适二冷强度
调整二冷水分布,在矫 直前铸坯温度>850℃,避 开脆性区(如图所示);
合适二冷水量并降低铸 坯横向中心与边部温度差, 避免回热温度过高。
图 矫直温度与横裂纹关系
-
20
防止横裂纹措施
(1) 采用高频率,小振幅结晶器振动负滑脱时间tN与拉速v成正比, 与频率和振幅f成反比。为防止横裂纹,就要减浅振痕,则必须降 低,要降低,则必须采用高频率(100~400min-1),小振幅 (±5mm)的结晶器振动机构。
连铸坯在凝固过程中形成裂纹的原因

连铸坯在凝固过程中形成裂纹的原因随着市场竞争的日趋激烈,产品的质量已经成为占有市场的主要砝码,连铸坯作为炼钢厂的终端产品,其质量直接影响着轧材单位的产量和轧材质量,据统计炼钢厂连铸坯质量缺陷中约70%为连铸坯裂纹,连铸坯裂纹成为影响连铸坯产量和质量的重要缺陷之一,下面将对铸坯在凝固过程中裂纹的形成做简要分析:一、铸坯凝固过程的形成铸坯在连铸机内的凝固可看成是一个液相穴很长的钢锭,而凝固是沿液相穴的固液界面在液固相温度区间把液体转变为固体把潜热释放出来的过程。
在固液界面间刚凝固的晶体强度和塑性都非常小,当作用于凝固壳的热应力、鼓肚力、矫直力、摩擦力、机械力等外力超过所允许的外力值时,在固液界面就产生裂纹,这就形成了铸坯内部裂纹。
而已凝固的坯壳在二冷区接受强制冷却,由于铸坯线收缩,温度的不均匀性,坯壳鼓肚、导向段对弧形不准,固相变引起质点如(AlN)在晶界的沉淀等,容易使外壳受到外力和热负荷间歇式的突变,从而产生裂纹就是表面裂纹。
二、连铸坯裂纹形态和影响因素连铸坯裂纹形态分为表面裂纹和内部裂纹,表面裂纹有纵向、横向角部裂纹、表面横裂和纵裂、网状裂纹和凹陷等,内部裂纹有中间、中心和矫直裂纹等。
连铸坯裂纹的影响因素:连铸坯表面裂纹主要决定于钢水在结晶器的凝固过程,它是受结晶器传热、振动、润滑、钢水流动和液面稳定性所制约的,铸坯内部裂纹主要决定于二冷区凝固冷却过程和铸坯支撑系统(导向段)的对弧准确性。
铸坯凝固过程坯壳形成裂纹,从工艺设备和钢凝固特性来考虑影响裂纹形成的因素可分为:1、连铸机设备状态方面有:1)结晶器冷却不均匀2)结晶器角部形状不当。
3)结晶器锥度不合适。
4)结晶器振动不良。
5)二冷水分布不均匀(如喷淋管变形、喷咀堵塞等)。
6)支承辊对弧不准和变形。
2、工艺参数控制方面有:1)化学成份控制不良(如C、Mn/S)。
2)钢水过热度高。
3)结晶器液面波动太大。
4)保护渣性能不良。
5)水口扩径。
6)二次冷却水分配不良,铸坯表面温度回升过大。
连铸板坯表面裂纹的成因

图1 中间罐温度与拉 速的对应图
图1 中间罐温度与拉 速的对应图
2)浸入式水口对中 2)浸入式水口对中
浸入式水口与结晶器不对中极易产生偏 流冲刷坯壳,还能引起结晶器液面翻腾, 保护渣不能形成均匀渣膜,导致传热不 良,坯壳厚薄不均而引起裂纹的发生。 投产初期采用人工下装式浸人式水口, 水口不易准确对中,尤其热换水口时, 更难保证对中,这些都可能导致裂纹的 发生。
5)保护渣的行为 5)保护渣的行为
现场所用保护渣的流动性不好。研 究表明,保护渣熔融不充分,粘度 过大,使流人坯壳和结晶器间隙的 渣膜不均匀,会导致摩擦力的变化 及坯壳冷却不均匀,造成坯壳厚薄 不均,引起裂纹的发生。
4 采取的措施
1)提高出钢温度的命中率,确保过热度为15℃±5t,重 新制定中间罐温度与拉速的对应表,见表1。 2)拉速升降时必须按每分钟≤0.15m/min的幅度操作,以 保证结晶器液面波动较小。 3)引进浸入式水口快速更换装置,换水口过程仅需3s, 更换水口迅速、准确、平稳及对中良好。 4)改进保护渣,要求保护渣粘度合适,熔化均匀及形成 的渣膜厚度适中。为此,保护渣的熔点由1145℃调为 1 0 7 0 ℃ , 粘 度 由 0 . 2 3 8 Pa·s(1300℃) 调 为 0 . 1 4 2 Pa·s(1300℃)。 5)对Q235等裂纹敏感性强的钢种,结晶器宽面水量由 200m3/h调为185m3/h。
连铸板坯表面裂纹的成因 及防止措施
1 2 3 4 5 前言 铸机状况 铸坯表面裂纹的影响因素 采取的措施 效果
1 前言
连铸板坯裂纹是影响连铸机产量 和铸坯质量的重要缺陷,轻者要 进行精整,重者会导致拉漏或废 品,影响铸机生产率和铸坯质量。 本文就生产中出现的铸坯表面裂 纹进行分析,并提出减少裂纹的 措施。
连铸坯表面裂纹形成及防止
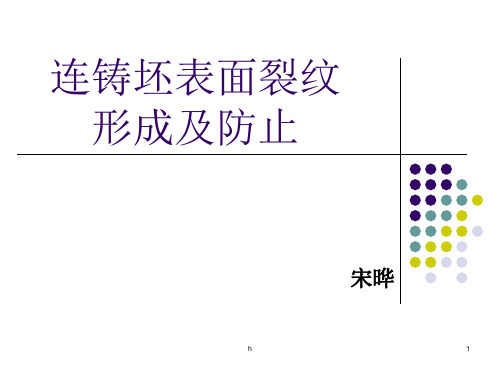
h
17
3 铸坯表面横裂纹
3 铸坯表面横裂纹
3.1表面横裂纹特征
横裂纹可位于铸坯面部或棱边
横裂纹与振痕共生,深度2~4mm,可达7mm,裂纹深处生成 FeO。不易剥落,热轧板表面出现条状裂纹。振痕深,柱状晶 异常,形成元素的偏析层,轧制板上留下花纹状缺陷。
铸坯横裂纹常常被FeO覆盖,只有经过酸洗后,才能发现。
连铸坯表面裂纹 形成及防止
宋晔
h
1内容Βιβλιοθήκη 1 前言 2 铸坯表面纵裂纹 3 铸坯表面横裂纹 4 铸坯表面星形裂纹 5 结论
h
2
1.前言
连铸坯质量概念: ◆ 铸坯洁净度(夹杂物数量、类型、尺寸、 分布) ◆ 铸坯表面质量(表面裂纹、夹渣、气孔) ◆ 铸坯内部质量(内部裂纹、夹杂物,中 心疏松、缩孔、偏析) ◆ 铸坯形状缺陷(鼓肚、脱方)
h
18
3 铸坯表面横裂纹
3.2横裂纹产生原因 (1) 横裂纹产生于结晶器初始坯壳形成振痕的
波谷处,振痕越深,则横裂纹越严重,在波谷 处,由于: -奥氏体晶界析出沉淀物,产生晶间断裂 -沿振痕波谷S、P元素呈正偏析,降低了钢高 温强度。
这样,振痕波谷处,奥氏体晶界脆性增大,为裂 纹产生提供了条件。
(2) 拉速
拉速增加,纵裂纹指数增加(图2-4);
图2-4 拉速对纵h 裂纹的影响
12
2 铸坯表面纵裂纹
(3) 保护渣 液渣层厚度<10mm,纵裂纹增加(图2-5)。
图2-5 液渣层厚度h 对纵裂纹的影响
13
2 铸坯表面纵裂纹
(4) 结晶器液面波动 液面波动<±5mm,纵裂纹最少(图2-6);
15
2 铸坯表面纵裂纹
(2) 结晶器钢水流动的合理性
连铸坯表面纵裂纹产生原因及控制措施

左 右 1 00 mm
。
2 3 1 .
.
宽 大 纵 裂 纹 宽 度 深 度 :
丨 0 - 20m m ,
2 0 - 3 0m m ,
长达几米 严重时会贯穿 板坯而报废
,
。
22 .
表 面 纵 裂 纹 原 因 分 析
2 2 .
.1
纵 裂 纹 起 源 于 结 晶 器 的 弯 月 面 区 初 生 凝 固
0 2 -
1
1
> 2 1
钢 液 面 波 动 范 围 mm ,
图 4 液 面 波 动 对 裂 纹 指 数 的 影 响
2 .
2. 4
结 晶 器 冷 却 效 果 及 热 流 的 影 响重 要 纵 裂 纹 一 般 均 发 生 在 结 晶 器 内 部 在 结 晶 器
,
,
结 晶 器 冷 却 效 果 对 连 铸 坯 纵 裂 纹 的 影 响 非 常 内 部 先 形 成 微 裂 纹 进 入 二 冷 区 后 发 展 成 明 显 的 裂 ,
,
晶器
流
于 W M 7 1 .
M2
/
宽面 铜板平 均热 流 为
侧 面 平 均 热 流 M W M 4 6 1 .
-
1.
2 /
,
为
<z>
>
右 1
cr >
i . i
a M
議
图 5 结 晶 器 热 流对 裂 纹 指 数 的 对 应 关 系
板 表 面 纵 裂纹 发 生 率 最 小 M W 3 l .
l- 1.
/ m2 ,
坯
。
经 统 计 分 析 侧 边 铜 板 热 流 与 宽 边 铜 板 热 流 之
倒角连铸坯角部纵向裂纹形成机制及控制
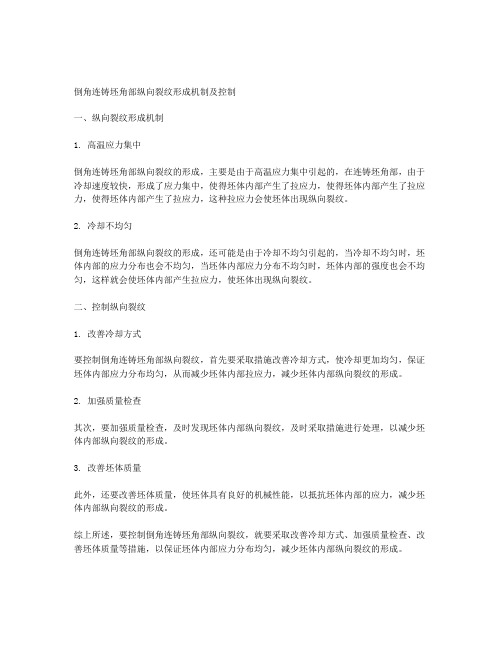
倒角连铸坯角部纵向裂纹形成机制及控制
一、纵向裂纹形成机制
1. 高温应力集中
倒角连铸坯角部纵向裂纹的形成,主要是由于高温应力集中引起的,在连铸坯角部,由于冷却速度较快,形成了应力集中,使得坯体内部产生了拉应力,使得坯体内部产生了拉应力,使得坯体内部产生了拉应力,这种拉应力会使坯体出现纵向裂纹。
2. 冷却不均匀
倒角连铸坯角部纵向裂纹的形成,还可能是由于冷却不均匀引起的,当冷却不均匀时,坯体内部的应力分布也会不均匀,当坯体内部应力分布不均匀时,坯体内部的强度也会不均匀,这样就会使坯体内部产生拉应力,使坯体出现纵向裂纹。
二、控制纵向裂纹
1. 改善冷却方式
要控制倒角连铸坯角部纵向裂纹,首先要采取措施改善冷却方式,使冷却更加均匀,保证坯体内部应力分布均匀,从而减少坯体内部拉应力,减少坯体内部纵向裂纹的形成。
2. 加强质量检查
其次,要加强质量检查,及时发现坯体内部纵向裂纹,及时采取措施进行处理,以减少坯体内部纵向裂纹的形成。
3. 改善坯体质量
此外,还要改善坯体质量,使坯体具有良好的机械性能,以抵抗坯体内部的应力,减少坯体内部纵向裂纹的形成。
综上所述,要控制倒角连铸坯角部纵向裂纹,就要采取改善冷却方式、加强质量检查、改善坯体质量等措施,以保证坯体内部应力分布均匀,减少坯体内部纵向裂纹的形成。
连铸板坯角部横裂产生的原因及应对措施

铸坯角部横裂产生的原因及应对措施板坯可以在表面上观察到纵向裂纹,在尾部观察到中线裂纹。
要了解板坯中的角裂纹及孔隙,必须用沿板坯边部进行火焰切割处理,切割出50mm宽,2〜3mm深的槽。
在检查板坯的裂纹时,在高强低合金钢(HSLA)、包晶钢、中碳钢中发现了角部横裂,但是在低碳铝镇静钢中却很少发现裂纹。
包晶钢含有Nb,因此,角裂的百分比极高。
虽然在板坯的疏松边发现了角部横裂,但板坯中的大多数裂纹出现在板坯的固定边。
几乎板坯中所有的角部横裂纹与振动痕迹方向一致。
在出厂前,必须对板坯中的角裂纹和针孔进行处理。
处理板坯中出现的裂纹将增加产品成本,降低生产能力,耽误产品出厂日期。
经过火焰切割后的板坯样品送到米塔尔研究实验室进行分析,以便确定其中角部横裂纹的发生原因。
为减少角部横裂纹,米塔尔公司LazaroCardenas(MSLC)的操作人员、维修人员、技术人员组成了一支精干的团队,以降低板坯角部横裂纹的发生。
裂纹起因当铸流表面遭受到热力应变、机械力应变或相变时,若该应变量超过了铸件材料的最大应变值,板坯就会发生横裂。
在下列条件下板坯可能产生裂纹:(1)铸流表面温度下降至低延展区以下,拉伸应变导致铸件产生裂纹。
(2)结晶器上热收缩应变引起板坯内部热断裂,产生裂纹。
(3)结晶器上或结晶器附近所施加的外力引起表面热拉裂。
产品的延展性低是出现裂纹的主要原因。
影响板坯横裂的因素还包括化学作用。
减小温差,降低震动是避免板坯裂隙发生的主要措施。
角部裂分析对板坯切削样本(削痕深度2〜3mm)进行化学成分分析的结果如表1。
在这种钢中发现了严重的角部裂纹,主要原因是该种钢的Nb、V和C含量高,特别是C对包晶钢非常敏感。
理论上讲,Nb(C,N)在1090°C开始析出,当温度下降,析出量快速增长,当温度降低到900C时主要析出物为V(C,N),温度进一步下降到800C时,晶间继续析出。
众所周知,在温度降低过程中,Nb基及V基析出物沿奥氏体晶粒边界析出。
连铸板坯表面纵裂纹控制

连铸板坯表面纵裂纹控制
一、连铸板坯表面纵裂纹的产生因素
1、造坯温度:过低的造坯温度会导致板坯表面纵裂纹的出现,应在钢
水熔化温度的基础上提高造坯温度;
2、造坯件间距:连铸板坯的冷却过程会产生很强的内应力,如果水冷
却造坯件间距过大,冷却之后会出现拉伸变形,从而产生纵裂纹;
3、连铸熔口处处理不当:当积熔渣正常时,若造坯件分离不平衡,也
会使连铸熔口处出现倾斜度,且不平衡的张力会造成热锻段产生纵裂纹;
4、水冷却喷口结构:水冷却温度不均匀,会在板坯表面形成表面纵裂纹,应采取合理的水冷却喷口结构布置,保证冷却水均匀性;
二、连铸板坯表面纵裂纹的控制措施
1、温度控制:在连铸造坯过程中,采用温度控制措施,确保钢水熔化
温度跨度不要在半钩温度以内,另外,为了减轻连铸板坯表面拉伸应
力也有助于减少纵裂纹;
2、造坯件间距控制:对于比较薄的连铸板坯,如低碳钢、低合金钢等,尤其需要多加注意造坯件间距的控制,相应地采用一定的补偿措施;
3、熔口处理控制:在熔口结构上有要求,要保证熔口垂直度,以保证
熔口平整,以及减少裂纹的出现;
4、水冷却喷口结构控制:采取合理的水冷却喷口结构,尽量取均衡的
喷口布置,以保证冷却的均匀性;。
连铸坯表面裂纹形成及防止

1.前言
铸坯裂纹是影响连铸机产量和铸坯 质量的主要缺陷。据统计铸坯各类缺 陷中的50%为裂纹。铸坯出现裂纹, 重者会导致漏钢和废品,轻者需进行 精整。
2 铸坯表面纵裂纹
2.1 板坯表面纵裂纹特征 表面纵裂纹可能发生在板坯宽面中心区域或宽面到
棱边的任一位置产生。图2-1为板坯宽面中心区域的 纵 裂 纹 和 纵 裂 纹 的 显 微 形 貌 。 以 250×1200mm (C=0.08%)板坯为例: 细小纵裂纹:宽度1-2mm,深度3-4mm,长100mm左
5.结论
(1)连铸坯产生裂纹主要决定于: 钢成分对裂纹敏感性、 浇注工艺条件、连铸机设备状况。
(2)带液芯连铸坯在连铸机内运行过程中受外力作用是 坯壳产生裂纹的外因,钢的高温力学行为是产生裂纹 的内因,而设备、工艺因素是产生裂纹的条件。
(3)根据所浇钢种,对连铸机设备的调整应符合钢凝固收 缩规律,使其坯壳不受变形为原则,对工艺参数的优化, 使其得到合理的铸坯凝固结构。这样使连铸坯不产 生裂纹或控制裂纹不足以造成废品的所允许的范围 内。
图3-4 矫直温度与横裂纹关系
3 铸坯表面横裂纹
3.4 防止横裂纹措施
(1) 采用高频率,小振幅结晶器振动 为防止横裂纹,就要减浅振痕,则必须降低,要
降低,则必须采用高频率 (100~400min-1),小振幅 (±5mm)的结晶器振动机构。 (2) 合适的二次冷却水量
根据钢种不同,二冷配水量分布应使铸坯表面 温度分布均匀,应尽量减少铸坯表面和边部温度差。 采用动态二冷配水模型。
匀性强,振痕深,表面易产生凹陷 或横裂纹;生产实践表明,C= 0.15~0.18%或0.15~0.20%时, 振痕浅了,铸坯边部横裂减少; 降低钢中[N],防止氮化物沉淀; (2) 结晶器振动特点 振痕深度增加,横裂纹增加(图31); 振动频率f增加,振痕变浅,横裂纹 减少(图3-2);
连铸坯表面裂纹形成及防止

如比值太小,说明侧面铜板热流过低, 凝固坯壳厚度较薄,钢水静压力作用 使侧面鼓胀,加大了宽面坯壳变形, 在薄弱处产生微裂纹。
如比值过大,说明侧边热流过高,侧 边凝固坯壳生长过厚,当宽面鼓胀时, 侧边不能随之收缩而导致宽面坯壳薄 弱处应力集中产生微细裂纹。
侧面热流与宽面热流比值与裂纹关系
2 铸坯表面纵裂纹
矫直温度与横裂纹关系
3 铸坯表面横裂纹
3.4 防止横裂纹措施 (1) 采用高频率,小振幅结晶器振动 负滑脱时间tN与拉速v成正比,与频率和振幅f成反比。为防止横 裂纹,就要减浅振痕,则必须降低,要降低,则必须采用高频率 (100~400min-1),小振幅(±5mm)的结晶器振动机构。 (2) 合适的二次冷却水量 根据钢种不同,二冷配水量分布应使铸坯表面温度分布均匀, 应尽量减少铸坯表面和边部温度差。采用动态二冷配水模型。 (3) 合适保护渣性 保护渣用量和粘度,既要满足减浅振痕,又要防止坯壳粘结。最 少为 0.3kg/m2。
铸坯表面裂纹类型
1-横向角部裂纹 2-纵向角部裂纹 3-横裂纹 5-星形裂纹 4-宽面纵向裂纹 6-深振痕
连铸板坯角部横裂产生的原因及应对措施

铸坯角部横裂产生的原因及应对措施板坯可以在表面上观察到纵向裂纹,在尾部观察到中线裂纹。
要了解板坯中的角裂纹及孔隙,必须用沿板坯边部进行火焰切割处理,切割出50mm宽,2~3mm深的槽。
在检查板坯的裂纹时,在高强低合金钢(HSLA)、包晶钢、中碳钢中发现了角部横裂,但是在低碳铝镇静钢中却很少发现裂纹。
包晶钢含有Nb,因此,角裂的百分比极高。
虽然在板坯的疏松边发现了角部横裂,但板坯中的大多数裂纹出现在板坯的固定边。
几乎板坯中所有的角部横裂纹与振动痕迹方向一致。
在出厂前,必须对板坯中的角裂纹和针孔进行处理。
处理板坯中出现的裂纹将增加产品成本,降低生产能力,耽误产品出厂日期。
经过火焰切割后的板坯样品送到米塔尔研究实验室进行分析,以便确定其中角部横裂纹的发生原因。
为减少角部横裂纹,米塔尔公司LazaroCardenas(MSLC)的操作人员、维修人员、技术人员组成了一支精干的团队,以降低板坯角部横裂纹的发生。
裂纹起因当铸流表面遭受到热力应变、机械力应变或相变时,若该应变量超过了铸件材料的最大应变值,板坯就会发生横裂。
在下列条件下板坯可能产生裂纹:(1)铸流表面温度下降至低延展区以下,拉伸应变导致铸件产生裂纹。
(2)结晶器上热收缩应变引起板坯内部热断裂,产生裂纹。
(3)结晶器上或结晶器附近所施加的外力引起表面热拉裂。
产品的延展性低是出现裂纹的主要原因。
影响板坯横裂的因素还包括化学作用。
减小温差,降低震动是避免板坯裂隙发生的主要措施。
角部裂分析对板坯切削样本(削痕深度2~3mm)进行化学成分分析的结果如表1。
在这种钢中发现了严重的角部裂纹,主要原因是该种钢的Nb、V和C含量高,特别是C对包晶钢非常敏感。
理论上讲,Nb(C,N)在1090℃开始析出,当温度下降,析出量快速增长,当温度降低到900℃时主要析出物为V(C,N),温度进一步下降到800℃时,晶间继续析出。
众所周知,在温度降低过程中,Nb基及V基析出物沿奥氏体晶粒边界析出。
连铸板坯裂纹的可能原因

连铸板坯裂纹的可能原因连铸板坯裂纹是指在连铸过程中板坯表面或内部出现的裂纹现象。
连铸板坯是制造板材的重要中间产品,其质量直接关系到最终产品的质量。
因此,了解连铸板坯裂纹的可能原因对于提高板材质量具有重要意义。
连铸板坯裂纹的可能原因主要包括以下几个方面:1. 温度控制不当:温度是连铸过程中最重要的控制参数之一。
如果连铸板坯的冷却速度过快或过慢,都会导致板坯表面或内部的温度梯度过大,从而引起裂纹的产生。
此外,连铸机的冷却水温度和流量的不稳定也会对板坯的温度分布产生影响,进而导致裂纹的形成。
2. 铸造过程中的应力:连铸板坯在冷却过程中由于温度变化而产生应力,如果应力超过了材料的承受能力,就会引起裂纹。
铸造过程中的应力主要包括热应力、冷却应力和收缩应力。
热应力是由于连铸板坯的非均匀冷却引起的,冷却应力是由于冷却水的不均匀冷却引起的,而收缩应力是由于连铸板坯的收缩引起的。
3. 材料质量问题:连铸板坯的质量直接关系到裂纹的产生。
如果原料中存在夹杂物、气孔或其他缺陷,都会在连铸过程中发展为裂纹。
此外,连铸板坯的化学成分和物理性能也会对裂纹的形成起到重要影响。
4. 连铸工艺参数调整不当:连铸过程中的各项工艺参数对于连铸板坯的质量具有重要影响。
如果连铸机的浇注速度、结晶器的冷却强度、结晶器的振动频率等参数调整不当,都会导致连铸板坯出现裂纹。
为了避免连铸板坯裂纹的产生,可以采取以下措施:1. 合理控制连铸过程中的温度,保证板坯的均匀冷却。
2. 优化连铸工艺参数,确保连铸板坯的质量稳定。
3. 加强原料检验,确保原料的质量达标。
4. 定期检查和维护连铸机设备,确保设备的正常运行。
5. 引入先进的控制技术,如自动化控制系统和智能监测设备,提高连铸过程的稳定性和可控性。
连铸板坯裂纹的产生是由多种因素共同作用的结果。
通过合理控制连铸过程中的温度、调整工艺参数、优化原料质量以及加强设备维护,可以有效地避免连铸板坯裂纹的产生,提高板材的质量。
连铸板坯三角区裂纹的成因及对策
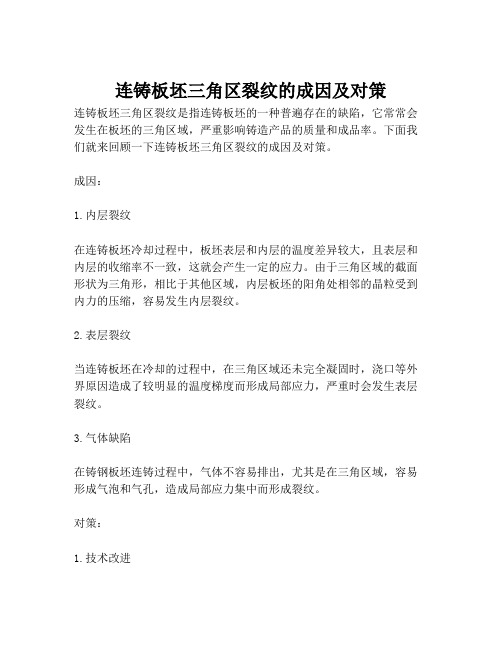
连铸板坯三角区裂纹的成因及对策连铸板坯三角区裂纹是指连铸板坯的一种普遍存在的缺陷,它常常会发生在板坯的三角区域,严重影响铸造产品的质量和成品率。
下面我们就来回顾一下连铸板坯三角区裂纹的成因及对策。
成因:1.内层裂纹在连铸板坯冷却过程中,板坯表层和内层的温度差异较大,且表层和内层的收缩率不一致,这就会产生一定的应力。
由于三角区域的截面形状为三角形,相比于其他区域,内层板坯的阳角处相邻的晶粒受到内力的压缩,容易发生内层裂纹。
2.表层裂纹当连铸板坯在冷却的过程中,在三角区域还未完全凝固时,浇口等外界原因造成了较明显的温度梯度而形成局部应力,严重时会发生表层裂纹。
3.气体缺陷在铸钢板坯连铸过程中,气体不容易排出,尤其是在三角区域,容易形成气泡和气孔,造成局部应力集中而形成裂纹。
对策:1.技术改进对于连铸板坯三角区裂纹的发生,可以先从技术的角度入手,采取改进措施,降低板坯的质量,减少三角区裂纹的发生。
例如:优化冷却过程,改善铸坯结构,以及适当的添加合金等。
2.材料改进连铸板坯三角区裂纹的发生与材料有一定的关系,因此在材料方面也可以采取一些措施,降低三角区裂纹的发生率。
例如,使用具有更好强度和韧性的材料,加入细小的晶粒改进剂等。
3.操作规范操作规范和操作技能的提高也是降低连铸板坯三角区裂纹发生率的关键。
对于操作者,需要按照正确的操作流程进行操作,严格掌握生产技术规范,避免因操作失误而导致的铸造缺陷。
总结:综上所述,连铸板坯三角区裂纹是铸造中一个比较复杂的问题,其造成的缺陷不仅影响产品质量,也影响生产效率。
因此,我们需要重视连铸板坯三角区裂纹缺陷的控制,采取一系列的改善措施,从技术,材料和操作规范等角度去降低三角区裂纹的发生率。
连铸表面裂纹产生的原因和改进的技术措施

姓名:陈守汪班级: 冶094班学号:099014214 2018年5月14日连铸表面裂纹产生地原因和改进地技术措施摘要:连铸坯表面裂纹地产生主要取决于:钢成分对裂纹敏感性、浇铸工艺条件及连铸机设备状况•带液芯地连铸坯在连铸机内运行过程中受到外力作用是坯壳产生裂纹地外因,钢地高温力学行为是产生裂纹地内因,而设备和工艺因素是产生裂纹地条件•根据所浇钢种,对连铸机设备地调整应符合钢水凝固收缩规律,以坯壳不发生变形为原则.优化工艺参数,使其处于能够保证连铸坯不产生裂纹或不足以造成废品地允许范围内,得到合理地铸坯凝固结构.b5E2RGbCAP关键词:铸坯表面纵裂纹、铸坯表面横裂纹主要内容:铸坯裂纹是影响连铸机产量和铸坯质量地主要缺陷.据统计,铸坯各类缺陷中有50汹裂纹缺陷.铸坯出现裂纹,轻者需进行精整,重者会导致漏钢和废品,既影响连铸坯生产率,又影响产品质量,增加生产成本. plEanqFDPw1铸坯表面纵裂纹1. 1 板坯表面纵裂纹特征表面纵裂纹可能在板坯宽面中心区域或宽面到棱边地任一位置产生.综合分析表明,纵裂纹有以下特征:(1>产生纵裂纹地表面常伴有凹陷(depression>, 纵裂纹地严重性与表面凹陷相对应.(2>裂纹沿树枝晶干方向扩展.(3>裂纹内发现有硅、钙、铝等元素地夹杂物.(4>在裂纹周围发现有P, S, Mn地偏析.(5>裂纹边缘出现一定地脱碳层,说明裂纹是在高温下形成扩展地.1.2 表面纵裂纹产生地原因板坯表面纵裂纹在连铸机内产生原因如下(1>板坯横断面低倍检验表明,纵裂纹起源于激冷层薄弱处(约2〜3mm> .(2>结晶器地模拟实验表明,纵裂纹起源于结晶器弯月面区(几十毫M到150mm>周边坯壳厚度薄弱处.这说明纵裂纹起源于结晶器地弯月面区初生凝固壳厚度地不均匀性. DXDiTa9E3d坯壳受下列所述力地作用:( 1> 板坯凝固壳四周温度不均匀而产生地收缩力。
连铸坯横裂产生的原因

连铸坯横裂产生的缘由横裂纹是位于铸坯内弧外表振痕的波谷处,通常是隐蔽看不见的。
经酸洗检查指出,裂纹深度可达 7mm,宽度 0.2mm。
裂纹位于铁素体网状区,而网状区正好是初生奥氏体晶界。
且晶界上有细小质点(如 A1N)的沉淀。
尤其是 C—Mn—Nb(V)钢,对裂纹敏感性更强。
横裂产生的缘由:1)振痕太深是横裂纹的发源地。
2)钢中 A1、Nb 含量增加,促使质点(A1N)在晶界沉淀,诱发横裂纹。
3)铸坯在脆性温度 900~700~C 矫直。
4)二次冷却太强。
防止横裂发生的措施:结晶器承受高频率(200~400 次/分)小振辐(2~4mm)是削减振痕深度的有效办法。
2)二次冷却区承受平稳的弱冷却,使矫直时铸坯外表温度大于900℃。
3)结晶器液面稳定,承受良好润滑性能、粘度较低的保护渣。
4)用火焰清理外表裂纹。
1.连铸坯外表纵裂产生的缘由及其防止方法有哪些?连铸坯外表纵裂纹,会影响轧制产品质量。
如长300mm、深2.5mm 的纵裂纹在轧制板材上留下 1125mm 分层缺陷。
纵裂纹严峻时会造成拉漏和废品。
争论指出:纵裂纹发源于结晶器弯月面初生坯壳厚度的不均匀性。
作用于坯壳拉应力超过钢的允许强度,在坯壳薄弱处产生应力集中导致断裂,出结晶器后在二次冷却区扩展。
纵裂产生的缘由可归纳为:1)水口与结晶器不对中而产生偏流冲刷凝固壳。
2)保护渣熔化性能不良、液渣层过厚或过薄导致渣膜厚薄不均,使局部凝固壳过薄。
液渣层<10mm,纵裂纹明显增加。
3)结晶器液面波动。
液面波动>10 ㎜,纵裂发生几率 30%。
4)钢中 S+P 含量。
钢中S>0.02%,P>0.017%,钢的高温强度和塑性明显降低,发生纵裂趋向增大。
5)钢中 C 在0.12~0.17%,发生纵裂倾向增加。
防止纵裂发生的措施是:1)水口与结晶器要对中。
2)结晶器液面波动稳定在±10mm。
3) 适宜的浸入式水口插入深度。
4)适宜的结晶器锥度。
连铸坯表面裂纹形成及防止汇总

图2-4 拉速对纵Biblioteka 纹的影响2 铸坯表面纵裂纹
(3) 保护渣 液渣层厚度<10mm,纵裂纹增加(图2-5)。
图2-5 液渣层厚度对纵裂纹的影响
2 铸坯表面纵裂纹
(4) 结晶器液面波动 液面波动<±5mm,纵裂纹最少(图2-6);
图2-6 结晶器液面波动对纵裂纹的影响
2W (T1 T2 ) W
3 铸坯表面横裂纹
3.2横裂纹产生原因 (1) 横裂纹产生于结晶器初始坯壳形成振痕的 波谷处,振痕越深,则横裂纹越严重,在波谷 处,由于: -奥氏体晶界析出沉淀物,产生晶间断裂 -沿振痕波谷S、P元素呈正偏析,降低了钢高 温强度。 这样,振痕波谷处,奥氏体晶界脆性增大,为裂 纹产生提供了条件。
这些力的的综合作用在坯壳上,当张应力超过钢的高温允许的 强度,则就在坯壳薄弱处萌生裂纹,出结晶器后在二冷区继续扩展。
2 铸坯表面纵裂纹
在结晶器弯月面区坯壳厚度生长不均匀的主要原 因是: (1)包晶相变(L+δ→γ)收缩特征,气隙过早形成, 导致坯壳生长不均匀。 (2)工艺因素影响结晶的坯壳生长不均匀。 显然要防止产生纵裂纹,就是要使结晶的弯月面初 生坯壳厚度均匀,避免坯壳产生应力梯度。要做到这点, 对于包晶相变的收缩特征是由Fe-C相图决定的,人为 无法改变,而重要的是准确控制影响结晶的初生坯壳生 长的工艺因素,来防止产生纵裂纹。
图3-1 振痕深度与横裂纹产生几率的关系
3 铸坯表面横裂纹
图3-2 振动频率与振痕深度的关系
3 铸坯表面横裂纹
图3-3 结晶器液面波动与角裂发生率的关系
(3) 结晶器液面波动 结晶器液面波动增加,横裂纹加重(图3-3)。
3 铸坯表面横裂纹
连铸板坯表面纵裂事故分析及预防措施.doc

YJ0712-连铸板坯表面纵裂事故分析及预防措施案例简要说明:依据国家职业标准和冶金技术专业教学要求,归纳提炼出所包含的知识和技能点,弱化与教学目标无关的内容,使之与课程学习目标、学习内容一致,成为一个承载了教学目标所要求知识和技能的教学案例。
本案例是连续铸钢产品质量缺陷案例,体现了铸坯质量特征、表面纵裂产生的原因、预防措施等知识点和岗位技能,与本专业连续铸钢课程连铸坯质量缺陷单元的教学目标相对应。
连铸板坯表面纵裂事故分析及预防措施1 背景介绍某炼钢厂连铸车间,采用超薄热带生产线,FTSC连铸板坯连铸机,机型直弧形,二冷气水雾化喷嘴,铸机基本半径5m,工作拉速2.8-5.2m/min,生产铸坯厚度87mm,结晶器液面控制方式Cs137射源控制。
主要生产薄板坯。
2 主要内容2.1事故经过2012年5月,FTSC工艺连铸薄板坯出现了大量的表面纵裂。
特别是浇注的ss400钢的裂纹率明显超高,占有缺陷铸坯的60~70%。
其主要发生在距中心四分之一宽度附近,距离中心300~400mm的区域。
当时,取样反馈的情况滞后于铸机生产,发现裂纹缺陷时已经造成至少两炉钢的裂纹质量缺陷。
因缺少铸坯离线检测的中间环节,这种铸坯纵裂纹对轧钢工序影响较大,最终导致质量异议事件2.2事故原因分析连铸板坯的裂纹表面纵裂由于在结晶器内凝固壳的生长不均匀,导致在特定部位拉伸应力的集中而产生。
对于薄板坯连铸来说,由于工艺的特殊性,其原因更为复杂多样。
(见图1)图1:铸坯表面纵裂(1)四孔水口通钢量大,对坯壳冲刷严重,使得在水口射流下方距中心260~430的区域坯壳减薄,导致结晶器出口处坯壳厚度比平均坯壳厚度减薄20%。
(2)钢水射流冲刷作用反映到坯壳表面温度上使得在距中心260~400的区域形成高温区,并随着拉速的增加而被加强,在结晶器出口处铸坯表面横向温度差达到1000C,高温、坯壳薄所造成的应力集中是产生铸坯纵裂纹的一个根源。
(3)结晶器漏斗区宽度为800mm,自由锥度设计较小,漏斗区内坯壳的收缩需要靠挤压窄面进行补充,但过大的局部锥度构成了形成纵裂纹的潜在因素。
连铸坯表面纵裂产生原因及控制

连铸坯表面纵裂产生的原因及控制一、表面纵裂的危害1、铸坯表面纵裂纹影响轧制产品质量,长300mm、深2.5mm的表面纵裂纹在轧制板材上留下1125mm分层缺陷,纵裂纹严重时会造成拉漏和废品。
2、表面纵裂经修磨后,由于修磨处铸坯厚度小于其他部位,造成轧制时压缩比偏小,板的表面质量和钢质性能不连续,降低板材的等级和钢材的收得率。
二、铸坯表面纵裂纹形成的机理:铸坯的表面纵裂纹产生于结晶器,由于热流分布不均匀,造成坯壳厚度不均匀,在坯壳薄的地方产生应力集中;结晶器壁与坯表面间的摩擦力使坯壳承受较大的负荷,在牵引坯壳向下运动时产生纵向应力,这种应力与从结晶器窄面,到宽面中心线的距离呈直线增加,最大处在板坯的中间,而钢水静压力随着坯壳往下移动呈直线增加,静压力使得坯壳往外鼓,表面裂纹得到进一步扩大。
三、钢坯表面纵裂纹形成的原因及分析:1、保护渣性能的影响,保护渣的黏度过大或过小,都会使渣膜在坯壳与结晶器壁之间,厚薄不均匀,从而影响结晶器的热流分布,导致坯壳凝固不均匀,从而影响结晶器的热流分布,导致坯凝固不均匀,保护渣的融化速率应与其消耗量平衡,熔化速度和熔点均对保护渣渣层的性能有直接关系,熔化过快或过慢均会影响渣膜的厚度及其均匀性,从而影响结晶器的热流分布。
2、结晶器内钢水行为的影响,钢水在结晶器内的流动状态,对结晶器内钢水卷渣、保护渣对夹杂物的捕捉,铸坯裂纹的形成均有一定关系。
当浸入式水口侧孔直径和角度或是水口的浸入深度和对中程度改变时,钢水流场随之改变,钢水对坯壳的冲刷程度也改变,流场不合理也会造成保护渣的铺展性不良,结晶器液面液渣层厚薄不均匀,使流入气隙的渣厚薄不均,造成热流分布不均匀,坯壳凝固不均,而出现表面纵裂纹。
当下水口外径过大时,结晶器内钢水在口区的内外弧处会出现钢水流动“死区”,造成结晶器液面“搭桥”现象,影响保护渣的熔化性,增加了铸坯中部的摩擦应力。
3、钢水过热度的影响,增加钢水过热度,保护渣熔化速度快,液渣层过厚在空隙内流失过快造成结晶器内热流分布不均匀,坯壳凝固不均匀,表面纵裂纹趋势增大。
- 1、下载文档前请自行甄别文档内容的完整性,平台不提供额外的编辑、内容补充、找答案等附加服务。
- 2、"仅部分预览"的文档,不可在线预览部分如存在完整性等问题,可反馈申请退款(可完整预览的文档不适用该条件!)。
- 3、如文档侵犯您的权益,请联系客服反馈,我们会尽快为您处理(人工客服工作时间:9:00-18:30)。
连铸板坯表面裂纹形成原因及控制措施
作者:郭金山, 马凤川, Guo Jinshan, Ma Fengchuan
作者单位:郭金山,Guo Jinshan(唐钢第一钢轧厂,唐山,063009), 马凤川,Ma Fengchuan(河北理工大学研究生学院,063009)
刊名:
天津冶金
英文刊名:TIANJIN METALLURGY
年,卷(期):2009(2)
被引用次数:1次
1.赵建伟HP295连铸坯表面无缺陷率的提高[期刊论文]-冶金标准化与质量 2003(5)
2.王雅贞;张岩连续铸钢工艺及设备 2007
3.蔡廷书控制连铸坯夹杂物工艺技术的进步 1997(12)
4.蔡开科连铸坯洁净度控制 1994(05)
1.杨海林.陈耀辉1 900 mm连铸板坯表面横裂纹成因的分析[期刊论文]-特殊钢2003,24(3)
2.许晞.吴国庆.岑永权.Xu Xi.Wu Guoqing.Cen Yongquan浦钢连铸大板坯表面横裂成因及对策分析[期刊论文]-上海金属2000,22(1)
3.朱国森.王新华.栗伟.王万军连铸板坯表面横裂纹研究[会议论文]-2002
4.吴薇化学成分对连铸板坯横裂纹形成的影响[期刊论文]-上海金属2004,26(1)
5.汤曙光.焦兴利.刘启龙连铸板坯表面纵裂纹的成因及防止措施[期刊论文]-炼钢2002,18(6)
6.巨建涛.张朝晖.折媛.王海江.杨建洲.张志华.JU Jian-tao.ZHANG Zhao-hui.SHE Yuan.WANG Hai-jiang.YANG Jian-zhou.ZHANG Zhi-hua板坯表面纵裂的成因分析及控制措施[期刊论文]-铸造技术2007,28(8)
7.赵树斌.岳尔斌.王志道.刘爱强.刘新民.刘永龙.吕建会连铸板坯表面温度分布及冷却的试验研究[期刊论文]-钢铁2002,37(2)
8.马富昌连铸板坯表面裂纹产生的原因分析[会议论文]-2009
9.江学德板坯表面纵裂纹的成因与控制[期刊论文]-连铸2003(6)
10.朱正海.李峰.Zhu Zhenghai.Li Feng连铸板坯表面纵裂纹及影响因素[期刊论文]-冶金丛刊2008(1)
1.戴秀东304不锈钢连铸坯表面裂纹原因分析及改善措施[期刊论文]-山西冶金 2010(4)
本文链接:/Periodical_tjyj200902005.aspx。