如何解决不锈钢螺纹车削问题
车削螺纹时常见故障及解决方法

车削螺纹时常见故障及解决方法螺纹车削是机械加工中的一项重要工艺,常用于制作螺栓、螺母等产品。
在车削螺纹过程中,有时会遇到一些常见的故障,如螺纹断裂、螺纹毛刺等问题。
本文将针对这些常见故障,给出相应的解决方法。
一、螺纹断裂螺纹断裂是车削螺纹中最常见的故障之一,主要原因有以下几点:1. 切削量过大。
车削螺纹时,如果一次性切削量过大,容易导致螺纹切削力过大,从而造成螺纹断裂。
2. 车削速度过高。
车削速度过高,会使螺纹材料在车削过程中产生过热现象,从而影响螺纹强度,导致断裂。
3. 切削刃磨损严重。
切削刃磨损严重会导致螺纹车削时切削力不均匀,从而容易引起断裂。
解决方法:1. 合理控制切削量。
在车削螺纹时,应根据工件的材料和尺寸,选择合适的切削量,避免一次性过大的切削力。
2. 控制切削速度。
根据螺纹材料的硬度和热处理情况,选择合适的切削速度,避免过高的车削速度造成螺纹断裂。
3. 及时更换刀具。
定期检查和更换切削刃,保证切削刃的锐利度,避免因刀具磨损产生过大的切削力。
二、螺纹毛刺螺纹毛刺是车削螺纹常见的表面缺陷之一,主要原因有以下几点:1. 加工精度不高。
车削螺纹时,如果刀具偏斜、工件夹紧不稳定等,容易导致精度不高,从而产生毛刺。
2. 切削液不合适。
切削液在车削螺纹时起到冷却、润滑的作用,选用不合适的切削液容易造成毛刺。
3. 刀具磨损严重。
刀具磨损严重会导致切削力不均匀,从而产生毛刺。
解决方法:1. 提高加工精度。
在车削螺纹前,检查刀具和夹持装置,确保工艺参数设置正确,以提高加工精度。
2. 合理选择切削液。
根据螺纹材料的特性和切削条件,选择合适的切削液,保证切削液的冷却和润滑效果,减少毛刺。
3. 及时更换刀具。
定期检查和更换刀具,保证刀具的切削锋利度,减少切削力不均匀引起的毛刺问题。
三、螺纹尺寸不准确螺纹尺寸不准确是车削螺纹常见的质量问题之一,主要原因有以下几点:1. 刀具磨损不均匀。
刀具磨损不均匀会导致切削力不均匀,从而影响螺纹尺寸的精度。
2023年车削螺纹时常见故障及解决方法

2023年车削螺纹时常见故障及解决方法在2023年,车削螺纹是机械加工中常见的操作之一。
尽管现在的机床和螺纹刀具更加先进和精密,但在操作过程中仍然可能出现各种故障。
在本文中,我们将讨论一些常见的车削螺纹故障,并提供相应的解决方法。
1. 切削过浅或过深切削过浅或过深是车削螺纹中常见的问题之一。
切削过浅会导致螺纹无法完全形成,从而影响螺栓或螺母的连接。
切削过深则会导致零件材料受损或刀具磨损更快。
解决方法:- 调整切削速度和进给速度,确保切削深度适当。
- 检查并更换磨损严重的刀具,确保刀具质量良好。
- 根据不同的螺纹规格,选择适当的刀具。
2. 切屑缠绕刀具或零件切屑缠绕刀具或零件会导致切削不顺畅,从而影响螺纹的质量。
特别是当切屑无法被顺利排出时,切削过程可能会中断。
解决方法:- 使用适当的冷却液或切削液,促进切削过程中切屑的排出。
- 调整切削速度和进给速度,确保切削过程平稳。
- 定期清理切削区域,防止切屑积聚。
3. 螺纹表面质量差螺纹表面质量差可能是由于切削条件不当或刀具磨损导致的。
螺纹表面质量差不仅影响零件的功能,还可能影响到螺纹的密封性能或装配质量。
解决方法:- 检查并更换磨损严重的刀具,确保刀具质量良好。
- 调整切削速度和进给速度,确保切削条件适当。
- 使用合适的冷却液或切削液,促进切削过程中的润滑和冷却。
4. 刀具断裂或磨损快刀具断裂或磨损严重会导致切削效果不佳,或者需要频繁更换刀具,从而影响生产效率。
解决方法:- 使用高质量的刀具,确保刀具的强度和耐磨性。
- 调整切削速度和进给速度,避免刀具过载。
- 定期检查刀具,及时更换磨损严重的刀具。
5. 螺纹偏斜或失真螺纹偏斜或失真可能是由于切削速度不均匀、材料变形或刀具错误等原因导致的。
螺纹偏斜或失真会影响螺纹的装配和连接质量。
解决方法:- 调整切削速度和进给速度,确保切削过程均匀。
- 使用合适的冷却液或切削液,减轻材料变形的影响。
- 检查并更换刀具,确保刀具质量良好。
不锈钢的车削技巧

不锈钢的车削技巧主要包括以下几个方面:1.刀具选择:选择适合不锈钢车削的刀具非常重要。
通常,选择具有较高耐热性、耐磨性和与不锈钢亲和作用小的刀具材料,如高碳、高钒或钼系的高速钢。
此外,刀具的几何形状和角度也需要根据具体加工要求进行选择。
2.切削用量选择:切削用量包括切削速度、进给量和切削深度。
对于不锈钢的车削,切削速度通常较低,一般为普通碳钢切削速度的40%~60%。
进给量和切削深度也需要根据具体情况进行选择,以避免刀具过度磨损和工件表面质量下降。
3.冷却液选择:使用合适的冷却液可以有效降低切削温度,减少刀具磨损和提高工件表面质量。
对于不锈钢的车削,通常选择具有较好冷却和润滑性能的冷却液。
4.操作技巧:在车削不锈钢时,需要注意以下几点操作技巧:首先,保持刀具的锋利,及时更换磨损的刀具;其次,避免使用过大的切削用量,以减少刀具的受力;最后,注意工件的装夹方式和切削力的方向,以避免工件变形或振动。
此外,还需要注意以下几点:1.由于不锈钢的塑性大、韧性高,车削时容易产生积屑瘤和鳞刺,这不仅影响工件的表面粗糙度,还会使刀具的磨损加快。
因此,需要选择合适的刀具材料和几何角度,以及合理的切削用量来避免这些问题的产生。
2.不锈钢的导热性差,导致切削热无法及时散出,使刀具的刃口温度升高,加剧刀具磨损。
为了降低切削温度,可以采用浇注冷却液的方法。
3.在车削过程中,应随时注意观察切削情况,如发现异常现象(如振动、噪声、温度升高等),应及时采取措施进行调整。
4.对于不同种类和规格的不锈钢材料,其车削性能也会有所不同。
因此,在实际加工前,最好先进行一些试验性切削,以确定最佳的切削参数和工艺方案。
总之,掌握不锈钢的车削技巧需要综合考虑多个因素,包括刀具选择、切削用量、冷却液和操作技巧等。
通过合理的选择和调整这些参数,可以提高加工效率、降低生产成本并获得高质量的工件。
螺纹车削的方法及技巧【详解】

螺纹车削的方法内容来源网络,由“深圳机械展(11万㎡,1100多家展商,超10万观众)”收集整理!更多cnc加工中心、车铣磨钻床、线切割、数控刀具工具、工业机器人、非标自动化、数字化无人工厂、精密测量、3D打印、激光切割、钣金冲压折弯、精密零件加工等展示,就在深圳机械展.一、螺纹车削的概念工螺纹车削是指螺纹加工过程,具体是指工件旋转一转,车刀沿工件轴线移动一个导程,刀刃的运动轨迹就形成了工件的螺纹表面的螺纹加工过程。
二、螺纹分类螺纹的种类很多,按用途可分为连接螺纹和传动螺纹;按牙形可分为三角螺纹、方形螺纹、锯形螺纹、圆形螺纹;按螺旋方向可分为右旋螺纹和左旋螺纹;按螺旋线数分为单线螺纹和多线螺纹。
按母体形状可分为圆柱螺纹和圆锥螺纹。
三、螺纹车削原理螺纹的加工方法很多,其中用车削的方法加工螺纹是常用的加工方法。
无论车削哪一种螺纹,车床主轴和刀具之间必须保持严格的运动关系:主轴每转一圈(即工件转一圈),刀具应均匀地移动一个导程的距离。
工件的转动和车刀的移动都是通过主轴的带动来实现的,从而保证了工件和刀具之间严格的运动关系。
四、螺纹车削的主要方法1、径向进刀法如图2-42a所示,车削螺纹时,车刀左右两侧刀刃都参加切削,由中滑板横向进给,通过多次行程,直到把螺纹车好。
径向进刀法适用螺距P<3mm的三角螺纹车削,也适用于P≥3mm三角螺纹的精车。
2、轴向进刀法(左右进刀法)车削较大螺距的螺纹时,为减小车刀两个刀刃同时切削所产生的扎刀现象,可使车刀只用一侧刀刃进行切削。
车削过程中,除了做横向进给外,同时还利用小滑板把车刀向左或向右做微量进给,使车刀只有一侧刀刃进行切削,通过多次行程,直至把螺纹车好。
这种加工方法适用于P≥3mm螺纹的精车等。
3、斜向进刀法如图2-42c所示,车削螺纹时,除中滑板横向进给外,只把小滑板向一个方向做微量进给。
这种方法只适用于粗车。
4、改进型斜向进刀法如图2-42d所示,这种车削方法是两侧刀刃都有切削任务,其中一个刀刃承担主要切削任务,这样可以避免斜向进刀不切削一侧刀刃磨损大和工件表面粗糙度大的问题。
螺纹车削加工原理及常见问题解决办法(1.02)
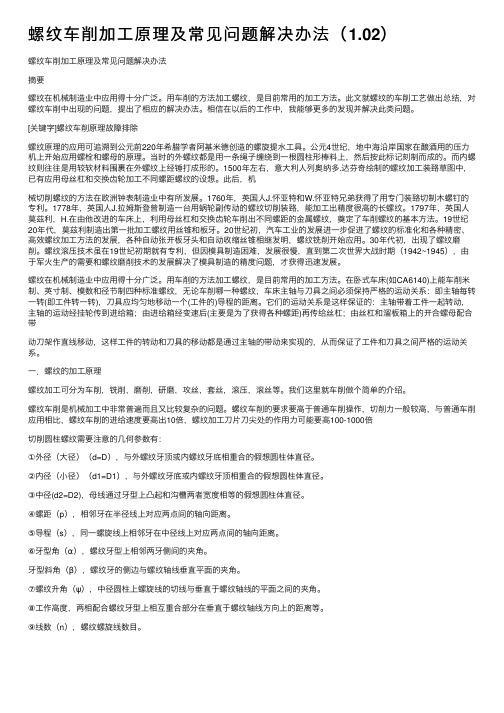
螺纹车削加⼯原理及常见问题解决办法(1.02)螺纹车削加⼯原理及常见问题解决办法摘要螺纹在机械制造业中应⽤得⼗分⼴泛。
⽤车削的⽅法加⼯螺纹,是⽬前常⽤的加⼯⽅法。
此⽂就螺纹的车削⼯艺做出总结,对螺纹车削中出现的问题,提出了相应的解决办法。
相信在以后的⼯作中,我能够更多的发现并解决此类问题。
[关键字]螺纹车削原理故障排除螺纹原理的应⽤可追溯到公元前220年希腊学者阿基⽶德创造的螺旋提⽔⼯具。
公元4世纪,地中海沿岸国家在酿酒⽤的压⼒机上开始应⽤螺栓和螺母的原理。
当时的外螺纹都是⽤⼀条绳⼦缠绕到⼀根圆柱形棒料上,然后按此标记刻制⽽成的。
⽽内螺纹则往往是⽤较软材料围裹在外螺纹上经锤打成形的。
1500年左右,意⼤利⼈列奥纳多.达芬奇绘制的螺纹加⼯装臵草图中,已有应⽤母丝杠和交换齿轮加⼯不同螺距螺纹的设想。
此后,机械切削螺纹的⽅法在欧洲钟表制造业中有所发展。
1760年,英国⼈J.怀亚特和W.怀亚特兄弟获得了⽤专门装臵切制⽊螺钉的专利。
1778年,英国⼈J.拉姆斯登曾制造⼀台⽤蜗轮副传动的螺纹切削装臵,能加⼯出精度很⾼的长螺纹。
1797年,英国⼈莫兹利,H.在由他改进的车床上,利⽤母丝杠和交换齿轮车削出不同螺距的⾦属螺纹,奠定了车削螺纹的基本⽅法。
19世纪20年代,莫兹利制造出第⼀批加⼯螺纹⽤丝锥和板⽛。
20世纪初,汽车⼯业的发展进⼀步促进了螺纹的标准化和各种精密、⾼效螺纹加⼯⽅法的发展,各种⾃动张开板⽛头和⾃动收缩丝锥相继发明,螺纹铣削开始应⽤。
30年代初,出现了螺纹磨削。
螺纹滚压技术虽在19世纪初期就有专利,但因模具制造困难,发展很慢,直到第⼆次世界⼤战时期(1942~1945),由于军⽕⽣产的需要和螺纹磨削技术的发展解决了模具制造的精度问题,才获得迅速发展。
螺纹在机械制造业中应⽤得⼗分⼴泛。
⽤车削的⽅法加⼯螺纹,是⽬前常⽤的加⼯⽅法。
在卧式车床(如CA6140)上能车削⽶制、英⼨制、模数和径节制四种标准螺纹,⽆论车削哪⼀种螺纹,车床主轴与⼑具之间必须保持严格的运动关系:即主轴每转⼀转(即⼯件转⼀转),⼑具应均匀地移动⼀个(⼯件的)导程的距离。
关于数控车床螺纹车削的加工工艺常见问题分析及解决办法探讨

关于数控车床螺纹车削的加工工艺常见问题分析及解决办法探讨数控车床螺纹车削作为数控加工的一种常见工艺,广泛应用于机械制造、航空航天、汽车制造等领域。
在实际生产中,常常会出现一些问题,影响加工效率和产品质量。
本文将对数控车床螺纹车削的加工工艺常见问题进行分析,并提出解决办法,以期能够帮助广大生产人员更好地掌握这一工艺,提高加工效率和产品质量。
一、加工工艺常见问题分析1. 螺纹精度不高在数控车床螺纹车削过程中,螺纹精度不高是一个常见问题。
这会直接影响到螺纹的配合质量和使用性能,严重影响产品质量。
2. 刀具磨损严重刀具磨损严重是另一个常见问题,这会导致刀具寿命缩短,加工效率低下,甚至造成加工质量不稳定。
3. 加工过程中出现振动在数控车床螺纹车削过程中,振动是一个常见问题,严重影响加工质量,甚至可能导致加工失效。
4. 加工余量不足加工余量不足是因为工艺参数设置不合理,导致产品尺寸不稳定,甚至无法满足要求。
5. 加工表面粗糙度不合格表面粗糙度不合格是另一个常见问题,这直接影响到产品的外观和使用性能。
二、解决办法探讨要解决螺纹精度不高的问题,首先要选择合适的加工参数,保证切削速度和进给速度适当。
要选择合适的刀具,并严格控制刀具的安装和刀具槽道的精度。
要加强对数控车床的维护保养,确保设备的精度和稳定性。
刀具磨损严重的问题可以通过选择合适的刀具材料和刀具类型来解决。
加强刀具的冷却和润滑,合理选择刀具的切削速度和进给速度,延长刀具的使用寿命。
加工余量不足的问题主要是由工艺参数设置不合理导致,因此要优化加工参数设置,保证加工余量符合要求。
要对数控车床进行定期检查和维护,确保各个参数的准确性和稳定性。
表面粗糙度不合格的问题可以通过选择合适的切削参数来解决,包括切削速度、进给速度和切削深度。
要确保刀具和工件的质量,严格控制刀具的磨损情况,确保加工表面的光洁度。
数控车床螺纹车削的加工工艺常见问题是可以通过合理的解决办法来避免的。
不锈钢螺纹车削
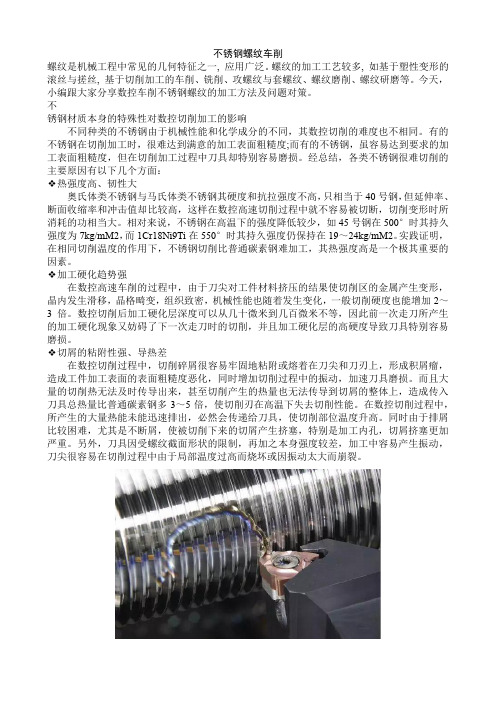
不锈钢螺纹车削螺纹是机械工程中常见的几何特征之一, 应用广泛。
螺纹的加工工艺较多, 如基于塑性变形的滚丝与搓丝, 基于切削加工的车削、铣削、攻螺纹与套螺纹、螺纹磨削、螺纹研磨等。
今天,小编跟大家分享数控车削不锈钢螺纹的加工方法及问题对策。
不锈钢材质本身的特殊性对数控切削加工的影响不同种类的不锈钢由于机械性能和化学成分的不同,其数控切削的难度也不相同。
有的不锈钢在切削加工时,很难达到满意的加工表面粗糙度;而有的不锈钢,虽容易达到要求的加工表面粗糙度,但在切削加工过程中刀具却特别容易磨损。
经总结,各类不锈钢很难切削的主要原因有以下几个方面:❖热强度高、韧性大奥氏体类不锈钢与马氏体类不锈钢其硬度和抗拉强度不高,只相当于40号钢,但延伸率、断面收缩率和冲击值却比较高,这样在数控高速切削过程中就不容易被切断,切削变形时所消耗的功相当大。
相对来说,不锈钢在高温下的强度降低较少,如45号钢在500°时其持久强度为7kg/mM2,而1Cr18Ni9Ti在550°时其持久强度仍保持在19~24kg/mM2。
实践证明,在相同切削温度的作用下,不锈钢切削比普通碳素钢难加工,其热强度高是一个极其重要的因素。
❖加工硬化趋势强在数控高速车削的过程中,由于刀尖对工件材料挤压的结果使切削区的金属产生变形,晶内发生滑移,晶格畸变,组织致密,机械性能也随着发生变化,一般切削硬度也能增加2~3倍。
数控切削后加工硬化层深度可以从几十微米到几百微米不等,因此前一次走刀所产生的加工硬化现象又妨碍了下一次走刀时的切削,并且加工硬化层的高硬度导致刀具特别容易磨损。
❖切屑的粘附性强、导热差在数控切削过程中,切削碎屑很容易牢固地粘附或熔着在刀尖和刀刃上,形成积屑瘤,造成工件加工表面的表面粗糙度恶化,同时增加切削过程中的振动,加速刀具磨损。
而且大量的切削热无法及时传导出来,甚至切削产生的热量也无法传导到切屑的整体上,造成传入刀具总热量比普通碳素钢多3~5倍,使切削刃在高温下失去切削性能。
关于数控车床螺纹车削的加工工艺常见问题分析及解决办法探讨

关于数控车床螺纹车削的加工工艺常见问题分析及解决办法探讨数控车床螺纹车削是机械加工中常见的一种工艺,常常用于制造螺纹连接件、螺纹轴等零部件。
在实际的加工过程中,经常会遇到一些常见的问题,这些问题不仅影响了生产效率,还可能导致产品质量不达标。
探讨数控车床螺纹车削的加工工艺常见问题及解决办法对于提高加工质量和效率具有重要意义。
一、加工过程中的常见问题分析及解决办法1、螺纹质量不达标螺纹质量不达标是数控车床螺纹车削中常见的问题之一。
造成这一问题的原因是多方面的,比如刀具磨损严重、切削参数设置不当、机床振动过大等。
针对这些问题,可以采取以下一些解决办法。
(1)定期更换刀具,确保刀具的切削性能;(2)合理设置切削参数,包括进给速度、主轴转速等,保证切削质量;(3)对机床进行定期维护,减小机床振动,改善加工质量。
2、芯部和头部连接不紧密螺纹加工中,芯部和头部连接不紧密会导致产品的质量问题。
这一问题可能是由于机床的刚性不够、夹具安装不稳等原因导致的。
对于这一问题,可以采取以下措施加以解决。
(1)提高机床的刚性,加强机床的支撑和固定;(2)优化夹具的设计和安装方式,确保夹具的稳定性;(3)增加刚性支撑,减小加工振动,保证连接的紧密性。
3、螺纹表面粗糙二、如何提高数控车床螺纹车削的加工效率除了解决加工过程中的常见问题外,提高数控车床螺纹车削的加工效率也是非常重要的。
以下是一些提高加工效率的方法。
1、优化切削参数合理设置切削参数,比如切削速度、进给速度、切削深度等,是提高加工效率的关键。
通过优化切削参数,可以达到快速而稳定的加工效果。
2、提高刀具和设备的使用寿命通过定期更换刀具、科学维护设备等方法,可以保证刀具和设备的良好状态,提高使用寿命,减少因刀具和设备磨损导致的停机次数,从而提高加工效率。
3、精心设计夹具和工装合理设计夹具和工装,确保工件的固定和稳定,可以有效地提高加工效率。
夹具和工装的设计应该考虑到工件的特性和加工过程的需要,从而提高加工效率。
浅谈螺纹车削原理及常见问题的解决办法

浅谈螺纹车削原理及常见问题的解决办法作者:李建军来源:《职业·下旬》2014年第08期摘要:用车削的方法加工螺纹,是常用的加工方法和车工的基本技能之一。
但是,在螺纹加工中,初学者往往因为操作不当,无法正确加工出所需要的螺纹。
本文对螺纹车削中出现的问题,提出了相应的解决办法。
关键词:螺纹车削原理故障解决办法一、螺纹的加工原理螺纹的加工方法很多,其中用车削的方法加工螺纹是目前常用的加工方法。
无论车削哪一种螺纹,车床主轴与刀具之间必须保持严格的运动关系:主轴每转一圈(即工件转一圈),刀具应均匀地移动一个导程的距离。
工件的转动和车刀的移动都是通过主轴的带动来实现的,从而保证了工件和刀具之间严格的运动关系。
二、常见故障原因及解决办法螺纹车削是机械加工中非常普遍而且又比较复杂的问题。
螺纹车削的要求要高于其他普通车削操作,车削时所产生的切削力一般较大。
车削螺纹时,由于螺纹升角的影响,引起切削平面和基面位置的变化,从而使车刀工作时的前角和后角与刃磨的前角和后角的数值不同,影响正常车削。
在车削螺纹时,若有一个环节出现问题,就会产生意想不到的后果,影响正常加工,这时应及时加以解决。
下面,笔者就对车削螺纹时最常见的故障谈谈自己的见解和解决办法。
1.啃刀和打刀(1)故障原因之一:车刀安装得过高。
车刀装夹过高,在切削时,由于工件与车刀之间产生的主切削力的作用,螺纹车刀刀尖受到工件压力而向下移动,从而使车刀被压到工件的最大外圆处,使本来车削不深的车刀越来越进入工件深处,从而车削深度变深,使工件与车刀之间的车削力进一步增大,造成啃刀或打刀现象。
解决方法:应及时调整车刀高度,使其刀尖与工件的轴线等高(可利用尾座顶尖对刀)。
(2)故障原因之二:工件装夹强度不够。
在车削螺纹时,工件与车刀主要产生的车削力是背向力(即切深抗力),与工件的直径方向一致,此时工件随时受到一个向外的力,这个力使工件随时有向外弯曲的趋势。
这样造成工件在车削时一边车削浅,一边车削深。
车削螺纹时常见故障及解决方法

车削螺纹时常见故障及解决方法在机械加工中,车削螺纹是一项基本技能。
然而,在操作过程中经常会发生一些故障,例如螺纹深度不够、刀具磨损过快等,这些问题会影响到加工效率和产品质量。
本文将介绍几种常见的车削螺纹故障及其解决方法。
1. 螺纹深度不够螺纹深度不够是一个常见而难以发现的问题,经常在现场加工中出现。
它通常是由于刀具高度不够或车削深度过浅引起的。
以下是解决该问题的方法:•提高刀具高度:可以通过增加支撑刀杆高度或调整刀具上的螺纹垫片来解决。
•增加车削深度:可以通过增加刀具与工件的接触时间或增加刀具超前量来解决。
2. 刀具磨损过快刀具磨损过快通常是由于切削速度太高或切削深度过大引起的。
如果您遇到这种问题,请参考以下建议:•降低切削速度:将切削线速降低到合适的范围内,通常介于5~20 m/min。
•降低切削深度:通过减少车削深度来降低切削负荷。
•更换高质量的刀具:选择具有高刚性和切削耐受性的刀具,可以显著提高刀具的使用寿命。
3. 螺纹折断或错位螺纹折断或错位通常是由于不当的刀具选择、不均匀的切削、机床闲置时间过长和工件内部缺陷引起的。
为了防止发生这种情况,请使用以下技巧:•选择合适的工具:使用专业用于螺纹车削的刀具,确保刀具的角度和尺寸正确。
•均匀切削:确保刀具与工件之间的接触均匀,并避免在工件周边产生太多的压力。
•机床保养:确保机床在加工前和加工后进行适当的保养,防止闲置过长,影响机床的性能。
4. 边角毛刺边角毛刺通常是由于刀尖磨损、粗糙的工件表面和不规则的车刀线轮廓等原因引起的。
如果您的工件出现边角毛刺,可以尝试以下措施:•更换刀具:将刀具钝化或磨损过度的刀具更换为新的刀具。
•改进车床设置:通过改变车床的速度、进给和角度等参数来改善车削表面的粗糙度。
•维护工件表面:对工件表面进行抛光、喷砂或磨削等操作,以改善表面质量。
5. 超出公差范围对于车削螺纹来说,公差范围非常重要。
如果您的工件超出了规定的公差范围,则可能会导致部件的不适合和效率低下。
车削螺纹时常见故障及解决方法范本

车削螺纹时常见故障及解决方法范本在车削螺纹的过程中,常会遇到一些常见的故障,比如螺纹断裂、螺纹质量不合格、刀具磨损严重等。
下面是一些常见的故障及解决方法范本:一、螺纹断裂:故障原因:螺纹材料硬度过高,切割力过大,导致螺纹断裂。
解决方法:使用更适合的刀具材料,减小切削力,合理调整车削参数。
如果螺纹断裂发生在材料较薄的部位,可以采用退刀或退刀速度减小的方法解决。
二、螺纹质量不合格:故障原因:刀具磨损严重,切削液不足,车削参数不合理等。
解决方法:及时更换磨损严重的刀具,调整切削液供给量,合理选择车削参数。
注意刀具的冷却和润滑,以保证螺纹的质量。
三、刀具磨损严重:故障原因:切削条件不合理,切削液不足,刀具质量不佳等。
解决方法:调整切削条件,增加切削液的供给量,更换质量较好的刀具。
合理选择刀具材料和刀具形状,可以延长刀具的使用寿命。
四、刀具断裂:故障原因:刀具材料问题,切削参数不合理,刀具过热等。
解决方法:选择更合适的刀具材料,调整切削参数。
注意刀具的冷却和润滑,以避免刀具过热断裂的问题。
五、螺纹内外径不一致:故障原因:车床的进给不稳定,刀具磨损不均匀,切削液不足等。
解决方法:调整车床的进给机构,保持稳定的进给量。
及时更换磨损严重的刀具,增加切削液的供给量。
六、螺纹表面粗糙:故障原因:刀具磨损严重,车削参数不合理,切削液不足等。
解决方法:更换磨损严重的刀具,调整合理的车削参数。
增加切削液的供给量,以保证螺纹表面的质量。
总之,对于车削螺纹过程中的常见故障,应根据具体情况进行分析,并采取相应的解决方法。
只有不断总结经验,提高技术水平,才能有效地解决故障,提高车削螺纹的质量和效率。
普通车床螺纹车削常见故障及解决方法(三篇)

普通车床螺纹车削常见故障及解决方法1. 放松刀夹:在车削过程中,如果刀夹没有固定好,会导致刀具松动或者偏位,从而造成螺纹不良。
解决方法是检查刀夹固定螺母是否紧固,如果松动则重新固定。
2. 刀具磨损:长时间使用刀具会磨损,导致刀尖变钝,从而无法进行正常的车削。
解决方法是更换刀具,保持刀具的锐利度。
3. 机床不稳定:如果机床本身存在不稳定的问题,例如床身变形、主轴不平衡等,会导致螺纹加工时产生偏差。
解决方法是定期检测和调整机床,确保其稳定性。
4. 刀具与工件匹配不良:在螺纹车削过程中,刀具与工件的匹配也非常重要。
如果选用的刀具尺寸不合适,就会导致螺纹加工结果不理想。
解决方法是选择合适尺寸的刀具,确保刀具与工件的配合良好。
5. 刀具进给速度不恰当:刀具进给速度过快或者过慢都会影响螺纹加工的质量。
解决方法是根据不同的工件材料和螺纹规格,调整刀具的进给速度,确保加工的质量。
6. 冷却液不适用:在螺纹车削过程中,适当使用冷却液可以降低温度,减少摩擦,提高切削润滑效果,从而改善加工质量。
如果使用的冷却液性质不合适,也会影响螺纹加工结果。
解决方法是选择合适的冷却液,根据加工工件的要求进行选择。
7. 机床刚度不足:机床刚度不足会导致在螺纹车削过程中产生振动和共振,造成螺纹不良。
解决方法是增加机床的刚度,例如加强机床床身的结构,增加加工时的稳定性。
8. 机床零件磨损:长时间使用机床,有些零部件会磨损,例如导轨、导向轨等,会导致加工误差。
解决方法是定期检查和更换机床零部件,保证机床的准确性和稳定性。
总之,普通车床螺纹车削常见故障的解决方法就是:确保刀具的固定和锐利度,稳定机床的结构和性能,选择合适尺寸和质量的刀具,调整进给速度和冷却液的使用,定期检查和维护机床零部件,确保加工质量和效果。
普通车床螺纹车削常见故障及解决方法(二)车床螺纹车削是机械加工中常见的一种加工方式,常用于制作螺纹零件。
然而,在车削过程中,可能会遇到一些常见的故障。
2024年车削螺纹时常见故障及解决方法(三篇)

2024年车削螺纹时常见故障及解决方法螺纹是在圆柱工件表面上,沿着螺旋线所形成的,具有相同剖面的连续凸起和沟槽。
在机械制造业中,带螺纹的零件应用得十分广泛。
用车削的方法加工螺纹,是目前常用的加工方法。
在卧式车床(如CA6140)上能车削米制、英寸制、模数和径节制四种标准螺纹,无论车削哪一种螺纹,车床主轴与刀具之间必须保持严格的运动关系:即主轴每转一转(即工件转一转),刀具应均匀地移动一个(工件的)导程的距离。
它们的运动关系是这样保证的:主轴带着工件一起转动,主轴的运动经挂轮传到进给箱;由进给箱经变速后(主要是为了获得各种螺距)再传给丝杠;由丝杠和溜板箱上的开合螺母配合带动刀架作直线移动,这样工件的转动和刀具的移动都是通过主轴的带动来实现的,从而保证了工件和刀具之间严格的运动关系。
在实际车削螺纹时,由于各种原因,造成由主轴到刀具之间的运动,在某一环节出现问题,引起车削螺纹时产生故障,影响正常生产,这时应及时加以解决。
车削螺纹时常见故障及解决方法如下:一、啃刀故障分析及解决方法:原因是车刀安装得过高或过低,工件装夹不牢或车刀磨损过大。
1.车刀安装得过高或过低过高,则吃刀到一定深度时,车刀的后刀面顶住工件,增大摩擦力,甚至把工件顶弯,造成啃刀现象;过低,则切屑不易排出,车刀径向力的方向是工件中心,加上横进丝杠与螺母间隙过大,致使吃刀深度不断自动趋向加深,从而把工件抬起,出现啃刀。
此时,应及时调整车刀高度,使其刀尖与工件的轴线等高(可利用尾座顶尖对刀)。
在粗车和半精车时,刀尖位置比工件的中心高出1%D左右(D表示被加工工件直径)。
2.工件装夹不牢工件本身的刚性不能承受车削时的切削力,因而产生过大的挠度,改变了车刀与工件的中心高度(工件被抬高了),形成切削深度突增,出现啃刀,此时应把工件装夹牢固,可使用尾座顶尖等,以增加工件刚性。
3.车刀磨损过大引起切削力增大,顶弯工件,出现啃刀。
此时应对车刀加以修磨。
二、乱扣故障分析及解决方法:原因是当丝杠转一转时,工件未转过整数转而造成的。
普通车床螺纹车削常见故障及解决方法

普通车床螺纹车削常见故障及解决方法普通车床螺纹车削是车床加工中的一项重要工艺,常见故障及解决方法如下:一、螺纹卡刀1. 故障表现:车削时,切削力过大,导致刀具与工件之间出现卡住现象。
2. 解决方法:检查刀具是否磨损或损坏,及时更换;调整加工参数,降低切削力;检查刀具与工件是否正常对中。
二、螺纹起皮1. 故障表现:车削螺纹后,螺纹表面出现起皮现象。
2. 解决方法:检查刀具的刀片角度和尺寸是否正确;调整进给量和主轴转速的匹配关系;适当增加切削液的使用量,降低切削温度。
三、螺纹跳动1. 故障表现:螺纹车削时,螺纹线跳动或不规则。
2. 解决方法:检查刀具的夹紧是否牢固;调整车床的主轴转速和进给量,使其匹配合理;检查工件的圆度和平行度,保证其质量。
四、螺纹偏斜1. 故障表现:螺纹车削后,螺纹线偏斜或不垂直于工件轴线。
2. 解决方法:调整刀具的夹角和切削液的喷射方向;检查车床的床身和导轨是否磨损,及时进行维护和更换;检查工件夹持装置是否牢固。
五、螺纹粗糙1. 故障表现:螺纹车削后,螺纹表面粗糙度较大。
2. 解决方法:检查刀具的刀片尺寸和刀片刃磨状况,及时更换磨损刀片;调整切削液的使用量和喷射方式;适当增加进给量,提高切削速度。
六、螺纹断裂1. 故障表现:车削螺纹时,螺纹线段突然断裂。
2. 解决方法:检查刀具是否磨损或脆化,及时更换;提高加工刚度,减少振动,避免过大的切削力;检查工件材料的硬度和强度,避免选择低质材料。
综上所述,螺纹车削常见故障及解决方法主要集中在刀具选择和切削参数的合理搭配、工件和刀具的装夹和对中、车床的维护保养等方面。
只有做好这些方面的工作,才能确保螺纹车削的质量和效率。
螺纹车削的常见问题及解决方法

螺纹车削的常见问题及解决方法针对公司叶轮及轴在车削螺纹时常出现的问题,提出解决方法,从而最大限度地保证螺纹加工的质量。
标签:螺纹;常见问题;加工工艺;解决方法我公司目前大多数叶轮、轴均使用螺纹进行连接,起传递动力的作用,目前公司叶轮与轴的连接大多为梯形螺纹,有单线螺纹,即由一条螺旋线形成的螺纹叫单线(单头)螺纹;也有多线螺纹,即由两条或者两条以上的轴向等距分布的螺旋线所形成的螺纹叫多线(多头)螺纹。
螺纹的螺旋线沿轴向等距分布,单线螺纹每旋转一周,移动一倍的螺距;多线螺纹每旋转一周时,能移动几倍的螺距,它广泛的应用于快速机构中,但其牙型深,切削层面积大,加工过程中更容易出现“乱扣”、“扎刀”现象,除此之外,操作者的技术水平不同,常出现中径不正确等问题,针对上述的问题,结合实际工作中的经验,谈谈解决上述问题的办法。
1.螺纹加工过程中常见的问题1.1加工过程中出现乱扣、扎刀的现象在加工螺纹时,刀具到退刀槽的中间需退刀时,采用打开开合螺母,将床鞍摇至起始位置,主轴带动丝杠旋转一圈时,被加工的工件未旋转整数圈或者丝杠的轴向间隙过大,在车削过程中产生轴向的窜动,那么,再次闭合开合螺母时,就会发生车刀刀尖不在前一刀所车出的螺旋槽内,容易出现乱扣。
车床中滑板、小滑板的间隙没有调整适当;安装刀具时刀杆伸出过长或刀杆刚性不足;刀尖低于工件中心;工件的刚性不足;车刀的前角过大,造成径向切削力把车刀拉向工件造成扎刀,操作方法不当致使车刀同时受力。
1.2螺纹中径不正确在车削过程中,车刀切削量过大,刻度盘不准或间隙过大,未能及时发现;加工螺纹前的圆柱面车削时同轴度误差较大,导致车削螺纹时吃刀不均匀,螺纹量规旋到中间旋不进去。
1.3螺纹的表面质量不高車刀刃磨的角度不合理,不光洁;采用的切削参数与工件不匹配;刀具的刚性不足产生较大的震动。
车削螺纹时产生的故障有很多,造成缺陷的原因也很多,从上述的分析可看出,有设备的原因,也有刀具和人员的原因。
车削螺纹常见故障及其解决方法如何减小金属材料的热处理变形
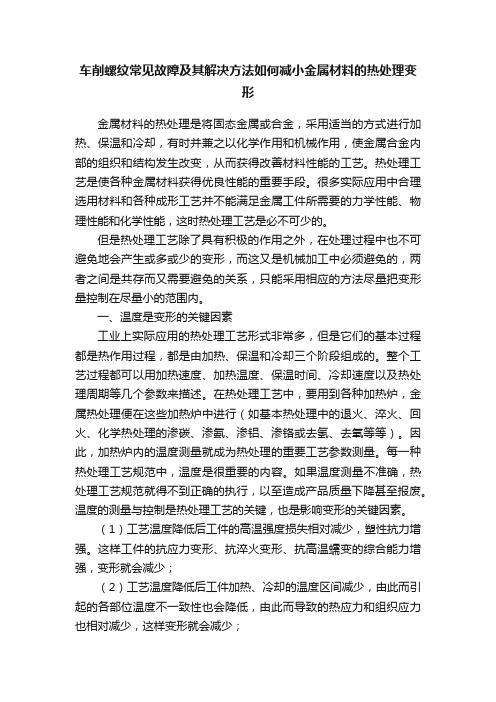
车削螺纹常见故障及其解决方法如何减小金属材料的热处理变形金属材料的热处理是将固态金属或合金,采用适当的方式进行加热、保温和冷却,有时并兼之以化学作用和机械作用,使金属合金内部的组织和结构发生改变,从而获得改善材料性能的工艺。
热处理工艺是使各种金属材料获得优良性能的重要手段。
很多实际应用中合理选用材料和各种成形工艺并不能满足金属工件所需要的力学性能、物理性能和化学性能,这时热处理工艺是必不可少的。
但是热处理工艺除了具有积极的作用之外,在处理过程中也不可避免地会产生或多或少的变形,而这又是机械加工中必须避免的,两者之间是共存而又需要避免的关系,只能采用相应的方法尽量把变形量控制在尽量小的范围内。
一、温度是变形的关键因素工业上实际应用的热处理工艺形式非常多,但是它们的基本过程都是热作用过程,都是由加热、保温和冷却三个阶段组成的。
整个工艺过程都可以用加热速度、加热温度、保温时间、冷却速度以及热处理周期等几个参数来描述。
在热处理工艺中,要用到各种加热炉,金属热处理便在这些加热炉中进行(如基本热处理中的退火、淬火、回火、化学热处理的渗碳、渗氨、渗铝、渗铬或去氢、去氧等等)。
因此,加热炉内的温度测量就成为热处理的重要工艺参数测量。
每一种热处理工艺规范中,温度是很重要的内容。
如果温度测量不准确,热处理工艺规范就得不到正确的执行,以至造成产品质量下降甚至报废。
温度的测量与控制是热处理工艺的关键,也是影响变形的关键因素。
(1)工艺温度降低后工件的高温强度损失相对减少,塑性抗力增强。
这样工件的抗应力变形、抗淬火变形、抗高温蠕变的综合能力增强,变形就会减少;(2)工艺温度降低后工件加热、冷却的温度区间减少,由此而引起的各部位温度不一致性也会降低,由此而导致的热应力和组织应力也相对减少,这样变形就会减少;(3)如果工艺温降低、且热处理工艺时间缩短,则工件的高温蠕变时间减少,变形也会减少。
减小热处理变形需要合理的热处理工艺。
普通车床螺纹车削常见故障及解决方法

普通车床螺纹车削常见故障及解决方法螺纹车削是机械加工中非常重要的一项工艺,通常在各种零部件的制造过程中都需要进行螺纹车削。
然而,在螺纹车削过程中,常常会出现一些故障,如刀具磨损、精度偏差、刀具掉刃等。
本文将针对普通车床螺纹车削中的常见故障进行分析,并提供相应的解决方法。
一、刀具磨损刀具磨损是螺纹车削最常见的故障之一,主要表现为刀尖磨损、后角磨损以及侧刃磨损。
刀具磨损会导致工件表面粗糙度增大、尺寸偏差增加等问题。
解决方法:1.定期检查刀具的磨损情况,及时更换磨损严重的刀具。
2.选择合适的刀具材料,提高刀具的耐磨性能。
3.加强刀具的润滑,减少磨损。
4.使用合适的切削参数,减少刀具的磨损。
二、精度偏差精度偏差是指螺纹车削过程中工件的实际尺寸与设计尺寸之间的差异。
精度偏差可能来自于车床本身的误差,也可能是由于操作不当或刀具磨损造成的。
解决方法:1.定期检查车床的准直度,及时调整车床的各个零部件,确保车床的准确度。
2.合理选择刀具,根据工件的要求选择适当的切削速度和进给速度,减小精度偏差。
3.加强操作人员的技术培训,提高操作人员的技能水平。
三、刀具掉刃刀具掉刃是螺纹车削中的一个严重故障,会导致螺纹质量不合格,同时也对安全造成威胁。
解决方法:1.选择优质的刀具,确保刀具的质量。
2.加强刀具的紧固力,定期检查刀具是否松动。
3.根据切削工况合理选择刀具的进给速度和切削深度。
4.在进给过程中避免突然变速,防止刀具发生震动。
5.定期检查刀具的磨损情况,及时更换磨损严重的刀具。
四、切削液问题切削液在螺纹车削过程中起到冷却、润滑、清洁的作用,然而切削液的质量差或使用不当会引起一系列问题,如工件表面粗糙度增大、刀具磨损加快等。
解决方法:1.选择合适的切削液,根据加工材料的不同,选择适当的切削液种类。
2.合理调节切削液的浓度和温度。
3.加强对切削液的管理,定期更换切削液。
4.根据切削工况,调整切削液的喷射方式和位置。
总结起来,普通车床螺纹车削中常见的故障包括刀具磨损、精度偏差、刀具掉刃以及切削液问题。
螺纹车削加工方式、进刀方式、螺纹加工常见问题及解决方法
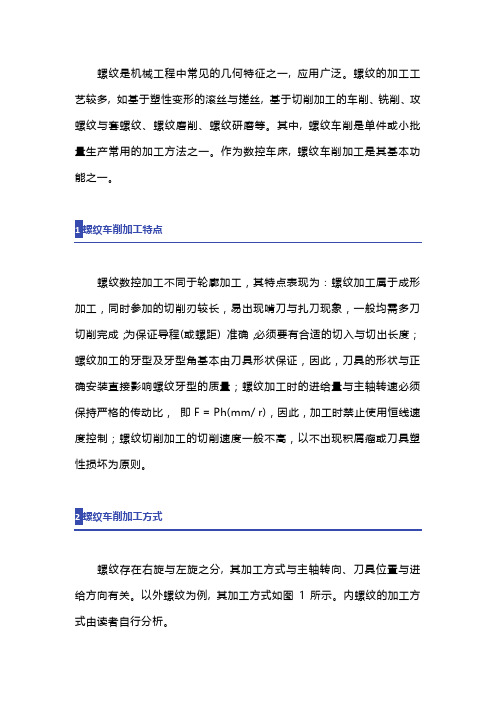
螺纹是机械工程中常见的几何特征之一, 应用广泛。
螺纹的加工工艺较多, 如基于塑性变形的滚丝与搓丝, 基于切削加工的车削、铣削、攻螺纹与套螺纹、螺纹磨削、螺纹研磨等。
其中, 螺纹车削是单件或小批量生产常用的加工方法之一。
作为数控车床, 螺纹车削加工是其基本功能之一。
1螺纹车削加工特点螺纹数控加工不同于轮廓加工,其特点表现为:螺纹加工属于成形加工,同时参加的切削刃较长,易出现啃刀与扎刀现象,一般均需多刀切削完成;为保证导程(或螺距) 准确,必须要有合适的切入与切出长度;螺纹加工的牙型及牙型角基本由刀具形状保证,因此,刀具的形状与正确安装直接影响螺纹牙型的质量;螺纹加工时的进给量与主轴转速必须保持严格的传动比,即F = Ph(mm/ r),因此,加工时禁止使用恒线速度控制;螺纹切削加工的切削速度一般不高,以不出现积屑瘤或刀具塑性损坏为原则。
2螺纹车削加工方式螺纹存在右旋与左旋之分, 其加工方式与主轴转向、刀具位置与进给方向有关。
以外螺纹为例, 其加工方式如图1所示。
内螺纹的加工方式由读者自行分析。
图1 外螺纹加工方式a)、d) 右旋螺纹b)、c) 左旋螺纹图1a 所示为常见的右旋螺纹加工方式, 主轴正转、前置正装或后置反装刀具、从右至左进给。
若进给方向反向, 则为左旋螺纹加工, 如图1b 所示。
图1c 所示为左旋螺纹加工, 主轴反转、前置反装或后置正装刀具、从右至左进给。
若进给方向反向, 则为右旋螺纹加工, 如图1d 所示。
3螺纹车削进刀方式(1) 进刀方式螺纹加工必须多刀切削, 其进刀方式有以下几种, 如图2所示。
图2 进刀方式a) 径向进刀b) 侧向进刀c) 改进式侧向进刀d) 左右侧交替进刀1) 径向进刀(图2a) 是基础的进给方式, 编程简单, 左、右切削刃后刀面磨损均匀, 牙型与刀头的吻合度高; 但切屑控制困难, 可能产生振动, 刀尖处负荷大且温度高。
适合于小螺距(导程) 螺纹的加工以及螺纹的精加工。
针对不锈钢零件的车削加工

针对不锈钢零件的车削加工随着企业的快速发展,对加工材料的多样化需求不断增加,像高温合金、不锈钢以及钛合金等难加工的材料被广泛的应用于各行各业当中。
在对这些材料加工的过程中,一定要分析出不同材料中存在的加工差异性。
本文针对不锈钢零件精密深孔数控车加工的方法进行了探讨,不锈钢作为一种难加工的材料,在建筑、电力、航空、航天、船舶等行业有着广泛的应用。
在实际的加工过程中易硬化、易产生积屑瘤等特性,而且导热性较差,所以针对这种现象对不锈钢零件的加工工艺方法进行了探讨,通过使用数控车加工可以更加精准的加工不锈钢零件,提高了工作效率。
标签:不锈钢;零件;车削加工一、不锈钢零件车削加工难点分析由于零件结构的特殊构成,在内腔车削时只能采用螺纹胎具的定位方式进行装夹,工作断面与轴向定位面的距离由于工件加工的特殊要求,重心不规则,所以在装夹系统中就很容易失衡。
同时也就增加了刀具的装夹的难度。
同时对于尺寸精度、同轴度、垂直度都有很高的要求,如果在加工的过程中出现一点误差,都可能会对零件的实用性能造成严重的影响。
所以对于不锈钢精密深孔的数控车加工要对刀具的选择、切削参数以及工艺路线的设置等都要有严格的要求,这些因素都会影响到该零件加工之后是否合格。
二、不锈钢具有的切削特点不锈钢的切削加工性比中碳钢差得多,在切削过程中有如下几方面特点:1.加工硬化严重:在不锈钢中,以奥氏体和奥氏体+铁素体不锈钢的加工硬化现象最为突出。
因为不锈钢的塑性大,塑性变形时品格歪扭,强化系数很大;且奥氏体不够稳定,在切削应力的作用下,部分奥氏体会转变为马氏体;再加上化合物杂质在切削热的作用下,易于分解呈弥散分布,使切削加工时产生硬化层。
前一次进给或前一道工序所产生的加工硬化现象严重影响后续工序的顺利进行。
2.切削力大:不锈钢在切削过程中塑性变形大,尤其是奥氏体不锈钢,使切削力增加。
同时,不锈钢的加工硬化严重,热强度高,进一步增大了切削抗力,切屑的卷曲折断也比较困难。
- 1、下载文档前请自行甄别文档内容的完整性,平台不提供额外的编辑、内容补充、找答案等附加服务。
- 2、"仅部分预览"的文档,不可在线预览部分如存在完整性等问题,可反馈申请退款(可完整预览的文档不适用该条件!)。
- 3、如文档侵犯您的权益,请联系客服反馈,我们会尽快为您处理(人工客服工作时间:9:00-18:30)。
如何解决不锈钢螺纹车削问题螺纹是机械工程中常见的几何特征之一, 应用广泛。
螺纹的加工工艺较多, 如基于塑性变形的滚丝与搓丝, 基于切削加工的车削、铣削、攻螺纹与套螺纹、螺纹磨削、螺纹研磨等。
不同种类的不锈钢由于机械性能和化学成分的不同,其数控切削的难度也不相同。
有的不锈钢在切削加工时,很难达到满意的加工表面粗糙度;而有的不锈钢,虽容易达到要求的加工表面粗糙度,但在切削加工过程中刀具却特别容易磨损。
经总结,各类不锈钢很难切削的主要原因有以下几个方面:1 热强度高、韧性大奥氏体类不锈钢与马氏体类不锈钢其硬度和抗拉强度不高,只相当于40号钢,但延伸率、断面收缩率和冲击值却比较高,这样在数控高速切削过程中就不容易被切断,切削变形时所消耗的功相当大。
相对来说,不锈钢在高温下的强度降低较少,如45号钢在500°时其持久强度为7kg/mm2,而1Cr18Ni9Ti在550°时其持久强度仍保持在19——24kg/mm2。
实践证明,在相同切削温度的作用下,不锈钢切削比普通碳素钢难加工,其热强度高是一个极其重要的因素。
2 加工硬化趋势强在数控高速车削的过程中,由于刀尖对工件材料挤压的结果使切削区的金属产生变形,晶内发生滑移,晶格畸变,组织致密,机械性能也随着发生变化,一般切削硬度也能增加2——3倍。
数控切削后加工硬化层深度可以从几十微米到几百微米不等,因此前一次走刀所产生的加工硬化现象又妨碍了下一次走刀时的切削,并且加工硬化层的高硬度导致刀具特别容易磨损。
3 切屑的粘附性强、导热差在数控切削过程中,切削碎屑很容易牢固地粘附或熔着在刀尖和刀刃上,形成积屑瘤,造成工件加工表面的表面粗糙度恶化,同时增加切削过程中的振动,加速刀具磨损。
而且大量的切削热无法及时传导出来,甚至切削产生的热量也无法传导到切屑的整体上,造成传入刀具总热量比普通碳素钢多3——5倍,使切削刃在高温下失去切削性能。
在数控切削过程中,所产生的大量热能未能迅速排出,必然会传递给刀具,使切削部位温度升高。
同时由于排屑比较困难,尤其是不断屑,使被切削下来的切屑产生挤塞,特别是加工内孔,切屑挤塞更加严重。
另外,刀具因受螺纹截面形状的限制,再加之本身强度较差,加工中容易产生振动,刀尖很容易在切削过程中由于局部温度过高而烧坏或因振动太大而崩裂。
4 螺纹粗糙度差的原因及对策数控切削后螺纹表面粗糙度太差,鱼鳞斑状波纹及啃刀现象是不锈钢螺纹车削中最常遇到的现象,产生这些现象的原因有:(1)螺纹车刀两侧刃后角太小,两侧刃与后面的螺纹表面相摩擦使加工表面恶化,加工时必须考虑螺纹旋转角对两侧刃实际后角的影响。
螺纹车刀的前角太小,刃口不够锋利,切屑不能顺利地被切断,而是部分地被挤压或撕裂下来,必定造成螺纹表面非常粗糙。
当前角太大时,刀刃强度削弱且容易磨损、崩裂、扎刀,更容易引起振动而使螺纹表面产生波纹。
因此,应根据不锈钢的不同材质选择适当的前角。
车削耐浓硫酸用不锈钢螺纹时,应比车削2Cr13不锈钢螺纹采用较小的前角,车刀两侧切削刃上应带有很窄的刃带以避免刃口迅速被磨损。
切削2Cr13、1Cr17、4Cr13时,切削刃应尽可能锋利,否则就不容易达到所需的良好的表面粗糙度。
螺纹刀刀片磨钝,实际上的前角、后角由大变小,切屑在形成过程中挤压严重,使切削过程中切削力增加振动加剧,加工表面恶化严重。
因此,车削不锈钢螺纹时,必须随时保持刀刃的锋利,及时更换刀头。
螺纹车刀固定不牢、刀头伸出过长、刀杆刚性不够,或者是机床精度差、主轴松动、刀架部分松动等因素都会引起振动,使螺纹表面产生波纹。
因此,在操作时必须注意操作机床、刀具及工件,使系统有足够的刚性。
安装车刀时,除了保证安装牢固、不能有任何松动以外,车刀刀尖应略高于工件中心0.2——0.5mm,绝不能低于中心,以免扎刀。
车削螺纹时应避免采用直进法,由于左右两侧的切屑接触长度长,容易产生振动,使刀尖承受的负荷加大,引起振动和增加排屑时的阻力,把加工表面划伤。
因此,对于不锈钢螺纹的加工最好选用交叉式车削螺纹的方法。
这种方法采用交替侧向进给,尤其对于大螺距螺纹、粘性材料的切削,是解决振动问题的最有效措施。
由于左右交叉使用切削刃,故磨损均匀,还能延长刀具的使用寿命。
数控切削螺纹的过程中切削用量的匹配程度直接影响加工的效率。
切削量过小将会使刀具加剧磨损,过大则将使刀具产生崩碎,因此进刀数和每刀进给量会对车削螺纹产生决定性的影响。
为了获得最佳刀具寿命,工件直径不应大于螺纹大径0.14mm,应当避免少于0.05mm的每刀进给量。
加工的总切削量应设定在0.1mm左右,第一次的切深应是刀尖半径(R)的150——200(百分号),最大不能超过0.5mm,对于奥氏体不锈钢应避免少于0.08mm 的每刀进给量,内螺纹用刀尖半径小的普通刃刀片,随着刀深的缩小切削次数可能相应地增加。
5 数控加工螺纹尺寸不稳定的原因及对策螺纹加工后,用螺纹环规测量外螺纹“通端”进不去或者出现前后松紧不一致以及“止端”部分通过等现象。
产生这些弊病的原因:螺纹牙形不对。
即使螺纹中径已经达到规定尺寸,螺纹环规、塞规仍可能拧不动。
螺纹倒牙。
用螺纹量规测量时,往往会出现受方向性限制的现象,也就是从一端拧过较紧,而从另一端拧过较松,甚至出现“通端”通不过而“止端”反而通过的现象。
内螺纹底径车的太小,或外螺纹底径过大,也会使得螺纹规拧不进去,这是由于车刀磨损变钝,切削过程中有挤压现象,使螺纹的外径或内径挤压出毛刺的结果。
车削直径较小的内螺纹时,因车刀刀杆受尺寸的限制刚性较差,车削过程中容易产生“让刀”,以至四部尺寸较大造成局部超差。
车削细长螺杆时,由于工件的刚性较差,车削过程中产生变形,造成螺纹上的尺寸误差。
车削薄壁工件的内、外螺纹时,工件因受力和切削温度的影响,产生局部变形,也会产生螺纹的局部超差。
因此,要解决“螺纹量规进不去”的问题,必须针对上述原因采取相应的措施,主要是从正确安装及工件装卡合适等方面着手。
6 冷却润滑液在数控切削螺纹中的微妙作用合理地使用润滑液能改善切削条件达到事半功倍的效果。
在数控切削不锈钢螺纹时应注意:要了解冷却润滑液的特殊要求由于不锈钢的韧性大、切削不易被分离,故要求冷却液要有较高的冷却性能,以带走大量的热量。
由于粘性大、熔着性大,在切削螺纹过程中容易产生积屑瘤,故应使冷却液具有较高的润滑性能。
要求冷却液有较好的渗透性,可在切削中渗入到金属区的微细隙线中,使切屑容易断离。
还要有一定的洗涤功能。
7 推荐几种合适的冷却液硫化油具有较好的冷却性能和润滑机能,按照配制方法的不同可分为直接和间接两种。
直接流化油的配方为:矿物油98(百分号),硫2(百分号)。
间接硫化油配方为:矿物油78(百分号)——80(百分号),黑机油、植物油18(百分号)——20(百分号),硫1.7(百分号)。
F43号机油适合于作不锈钢切削的冷却润滑液,对车不锈钢螺纹效果最佳。
其配方为:5号高速机油83.5(百分号),石油磺酸钙4(百分号),石油磷酸钡4(百分号),氧化石油脂钡皂4(百分号),二烷硫代磷酸锌4(百分号),二硫化0.5(百分号)。
植物油如豆油,在车削螺纹时有利于得到较好的螺纹表面粗糙度和延长刀具的使用寿命。
刀具涂层技术知识及金刚石、氮化碳、立方氮化硼CBN刀具涂层技术的研究一、刀具涂层通过化学或物理的方法在刀具表面形成某种薄膜,使切削刀具获得优良的综合切削性能,从而满足高速切削加工的要求;自20世纪70年代初硬质涂层刀具问世以来,化学气相沉积(CVD)技术和物理气相沉积(PVD)技术相继得到发展,为刀具性能的提高开创了历史的新篇章。
涂层刀具与未涂层刀具相比,具有显着的优越性:它可大幅度提高切削刀具寿命;有效地提高切削加工效率;提高加工精度并明显提高被加工工件的表面质量;有效地减少刀具材料的消耗,降低加工成本;减少冷却液的使用,降低成本,利于环境保护。
二、刀具涂层的特点:1,采用涂层技术可在不降低刀具强度的条件下,大幅度地提高刀具表面硬度,目前所能达到的硬度已接近100GPa;2.随着涂层技术的飞速发展,薄膜的化学稳定性及高温抗氧化性更加突出,从而使高速切削加工成为可能。
3.润滑薄膜具有良好的固相润滑性能,可有效地改善加工质量,也适合于干式切削加工;4.涂层技术作为刀具制造的最终工序,对刀具精度几乎没有影响,并可进行重复涂层工艺。
三、常用的涂层1,氮化钛涂层:氮化钛(TiN)是一种通用型PVD涂层,可以提高刀具硬度并具有较高的氧化温度。
该涂层用于高速钢切削刀具或成形工具可获得很不错的加工效果。
2,氮化铬涂层:CrN涂层良好的抗粘结性使其在容易产生积屑瘤的加工中成为首选涂层。
涂覆了这种几乎无形的涂层后,高速钢刀具或硬质合金刀具和成形工具的加工性能将会大大改善。
3,金刚石涂层CVD金刚石涂层可为非铁金属材料加工刀具提供最佳性能,是加工石墨、金属基复合材料(MMC)、高硅铝合金及许多其它高磨蚀材料的理想涂层(注意:纯金刚石涂层刀具不能用于加工钢件,因为加工钢件时会产生大量切削热,并导致发生化学反应,使涂层与刀具之间的粘附层遭到破坏)。
4,氮碳化钛涂层:氮碳化钛(TiCN)涂层中添加的碳元素可提高刀具硬度并获得更好的表面润滑性,是高速钢刀具的理想涂层。
5,氮铝钛或氮钛铝涂层(TiAlN/AlTiN):TiAlN/AlTiN涂层中形成的氧化铝层可以有效提高刀具的高温加工寿命。
主要用于干式或半干式切削加工的硬质合金刀具可选用该涂层。
根据涂层中所含铝和钛的比例不同,AlTiN涂层可提供比TiAlN涂层更高的表面硬度,因此它是高速加工领域又一个可行的涂层选择。
四、涂层技术及刀具涂层知识1,氮碳化钛(TiCN)涂层比氮化钛(TiN)涂层具有更高的硬度。
由于增加了含碳量,使TiCN涂层的硬度提高了33%,其硬度变化范围约为Hv3000——4000(取决于制造商)。
2,CVD金刚石涂层:表面硬度高达Hv9000的CVD金刚石涂层在刀具上的应用已较为成熟,与PVD涂层刀具相比,CVD金刚石涂层刀具的寿命提高了10——20倍。
金刚石涂层刀具的高硬度,使得切削速度可比未涂层的刀具提高2——3倍,使CVD金刚氧化温度是指涂层开始分解时的温度值。
氧化温度值越高,对在高温条件下的切削加工越有利。
虽然TiAlN涂层的常温硬度也许低于TiCN涂层,但事实证明它在高温加工中要比TiCN有效得多。
TiAlN 涂层在高温下仍能保持其硬度的原因在于可在刀具与切屑之间形成数控微信号cncdar一层氧化铝,氧化铝层可将热量从刀具传入工件或切屑。
与高速钢刀具相比,硬质合金刀具的切削速度通常更高,这就使TiAlN成为硬质合金刀具的首选涂层,硬质合金钻头和立铣刀通常采用这种PVD TiAlN 涂层石涂层刀具成为有色金属和非金属材料切削加工的不错选择。