第七章 塔设备
化工设计概论第七章-设备的工艺设计与选型
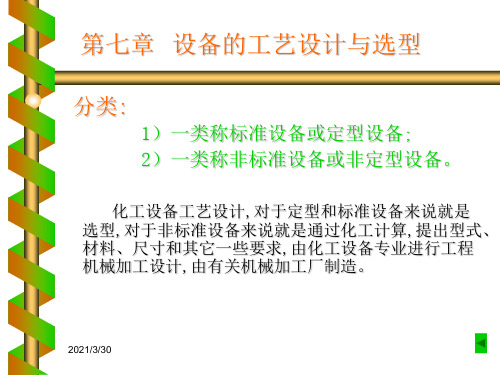
2021/3/30
51
设计与选用方法:
(1)汇总设计数据、分析设计任务根据工艺衡算和工艺物 料的要求、特性,获得物料流量、温度、压力和化学性 质、物性参数,取得有关设备的负荷、流程中的地位与 流程中其他设备的关系等数据。
• 折流板的间距不小于圆通内直径的五分之 一,且不小于50mm,最大间距不大于圆筒 内直径。
• 间距过小,不便于制造及检修,阻力增大。 过大,对传热不利。可参考表7-4。
2021/3/30
40
1.换热器设计的一般原则
• (1)基本要求 ➢ 满足工艺操作条件 ➢ 能长期运转 ➢ 安全可靠 ➢ 不泄漏 ➢ 维修清洗方便 ➢ 满足工艺要求的传热面积 ➢ 尽量有较高的传热效率 ➢ 流体阻力尽量小 ➢ 满足工艺布置的安装尺寸等要求
第七章 设备的工艺设计与选型
分类:
1)一类称标准设备或定型设备; 来自)一类称非标准设备或非定型设备。
化工设备工艺设计,对于定型和标准设备来说就是 选型,对于非标准设备来说就是通过化工计算,提出型式、 材料、尺寸和其它一些要求,由化工设备专业进行工程 机械加工设计,由有关机械加工厂制造。
2021/3/30
标准换热器型式:固定管板式,浮头式,U形管式和填料函式。 标准换热器型号的表示方法:
×××DN-P1/P2-A-LN/d-Nt/Ns Ⅰ(或Ⅱ)
×××——由三个字母组成,第一个字母表示前端管箱形式;第二个字母 代表管壳形式;第三个字母代表后端结构形式,参见图例(图7.10)。
DN——公称直径(mm)对重沸器用分数表示,分子为管箱内直径,分母为圆 筒内直径。
轴的功率。流体从泵获得的实际功率为
泵的有效功率Ne,由泵的流量和扬程求得
有效功率与轴功率的比值为离心泵的效率
7-垂直运输设备的选用和布置

第七章垂直运输设备的选用和布置一、垂直运输设备的选择结构施工阶段我们拟投入4台塔吊,装修、机电施工阶段我们拟投入6台施工井架。
二、塔吊施工方案1、塔吊的选型结构施工阶段设置4台塔吊:1# ST60/15 臂长60米2# ST60/15 臂长60米3# ST60/15 臂长60米4# ST60/15 臂长60米塔吊的平面定位如下图所示:结构施工阶段塔吊布置2、塔吊设置原则1)覆盖建筑物以及现场物料堆放场地和载物车辆装卸货物场所2)满足工期和垂直运输任务的需要3)满足塔吊安装条件和塔基开挖条件4)满足塔吊拆除条件5)距建筑物外皮间距不小于4米3、塔吊起重性能表ST60/15起重性能表半径倍率最大吊重及位置15 25 30 40 45 50 55 6060Ⅱ吊重5T20.2M 5 4.43 3.57 2.53 2.18 1.91 1.68 1.50Ⅳ吊重10T11.75M 7.41 3.83 2.93 1.88 1.54 1.26 1.04 0.854、塔吊安装准备1)塔吊及其附属配件的准备;2)具有上岗证的安装人员;3)塔吊专用电箱。
为了满足塔吊正常工作,塔吊必须配用专用电箱,根据塔吊的定位对塔机电箱合理布置,塔吊专用电箱距塔吊中心不得大于5米;4)平整场地,便于塔吊部件的摆放和汽车吊的入场选位;5)准备标号为C35以上的混凝土和钢筋;2-7-316)对塔吊基础块区域进行地质分析,如须加固须报方案经监理批准备案;7)对架空输电线或通讯线架设防护设置。
5、塔吊安装塔吊的安装我们采用55吨汽车吊进行安装。
塔吊安装过渡节。
注意塔机的顶升方向。
安装标准节。
安装顶升套架,包括走道平台、扁担梁、油缸。
安装回转装置.先在地面上安装好引进大梁,然后吊装。
吊装回转装置吊装平衡臂安装平衡臂,汽车吊整体吊装。
安装司机室、塔顶。
吊装塔顶连接塔机用电线路,并缓慢回转平衡臂。
整体安装起重臂按规范安装平衡重。
调试验收,合格后投入使用。
第七章 塔设备

(a) 自身梁式
(b)槽式
图7-23 自身梁式与槽式塔盘示意图
在直径较大的板式塔中,如果仍用整块式塔盘,则由于刚度的要求,塔盘板的 厚度势必增加,而且在制造、安装与检修等方面很不方便。因此,当塔径在 800~900mm以上时,由于人能进入塔内,故都采用分块式塔盘(图7-22),此 时塔身为一焊制整体圆筒,不分塔节,而塔盘板被分成数块,通过人孔送进塔内,
填料塔塔体安装垂直度偏差不得超过塔高的2/1000,且不大于30mm。 (3)塔盘板长度偏差不得超过±0.4mm,宽度偏差不得超过:±0.2 mm。 (4)塔盘板需要维持一定的水平度,否则将影响气、液的均匀分布。
第一节 塔设备概述
第一节 塔设备概述
(5) 为了保证塔盘的水平度,支持圈的表面水平度亦有一定的要求。在300mm弦长 的表面上,局部不平度不超过1mm,总的不平度的允许偏差与塔盘相同(即表7-2的 f值),相邻两支撑全间距的偏不超过±20mm. (6) 溢流堰顶的水平度对塔盘板的操作及效率均有影响,故堰顶的水平度不超过 堰宽的1/1000,且不大于3mm。 (7) 降液管安装后,其下端与受液盘距离的偏差为±3mm。 (8) 栅板应平整,安装后的不平度不超过2mm。对最底层的栅板没有不平度要求。 (9) 液体分布装置安装时,水平偏差不超过3mm,标高偏差不超过±3mm,其中心 线与塔中心线偏差不超过3mm。 (10)塔体在同一断面上的最大直径与最小直径之差e,应符合下述规定:受内压塔, e≤1%DN(DN 为塔内径),且e不大于25mm;对受外压塔,e≤0.5%DN,且e不大于 25mm。 (11) 裙座(支座)螺栓孔中心圆直径偏差小于±3mm,任意两孔间距偏差小于±3mm。
吨催化裂化装置中占48.9%,年产30万吨乙烯装置中占25~28.3%。
塔类设备安全技术规程范本(2篇)
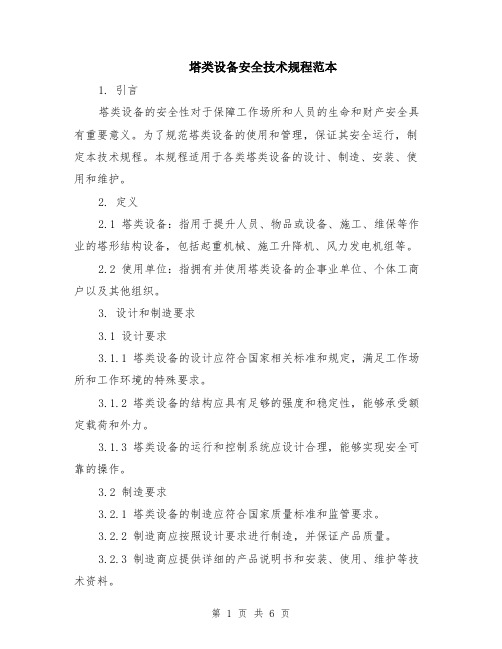
塔类设备安全技术规程范本1. 引言塔类设备的安全性对于保障工作场所和人员的生命和财产安全具有重要意义。
为了规范塔类设备的使用和管理,保证其安全运行,制定本技术规程。
本规程适用于各类塔类设备的设计、制造、安装、使用和维护。
2. 定义2.1 塔类设备:指用于提升人员、物品或设备、施工、维保等作业的塔形结构设备,包括起重机械、施工升降机、风力发电机组等。
2.2 使用单位:指拥有并使用塔类设备的企事业单位、个体工商户以及其他组织。
3. 设计和制造要求3.1 设计要求3.1.1 塔类设备的设计应符合国家相关标准和规定,满足工作场所和工作环境的特殊要求。
3.1.2 塔类设备的结构应具有足够的强度和稳定性,能够承受额定载荷和外力。
3.1.3 塔类设备的运行和控制系统应设计合理,能够实现安全可靠的操作。
3.2 制造要求3.2.1 塔类设备的制造应符合国家质量标准和监管要求。
3.2.2 制造商应按照设计要求进行制造,并保证产品质量。
3.2.3 制造商应提供详细的产品说明书和安装、使用、维护等技术资料。
4. 安装和调试要求4.1 安装要求4.1.1 塔类设备的安装应由具备相应资质和经验的专业施工人员进行。
4.1.2 安装前,应仔细检查设备零部件的完好性和可靠性。
4.1.3 安装应遵循设备制造商的技术规范和要求,确保设备的水平度和垂直度符合要求。
4.2 调试要求4.2.1 安装完成后,应进行严格的设备调试,确保其运行正常。
4.2.2 调试应包括机械传动系统、电气控制系统、保护装置等方面的检查和测试。
4.2.3 调试完成后,应对设备进行全面检查,确保设备各项指标符合要求。
5. 使用和维护要求5.1 使用要求5.1.1 使用单位应按照设备制造商的说明书和规定进行使用,严禁超负荷使用或改变设备的结构和性能。
5.1.2 操作人员应经过专业培训,熟悉设备的性能和操作方法,且持证上岗。
5.1.3 在设备运行期间,应及时清理设备表面的杂物和积尘,确保设备正常运行。
塔设备配件设备安全操作规定

塔设备配件设备安全操作规定为了保障塔设备配件设备的正常运行及安全操作,制定以下安全操作规定。
1. 设备安装1.1 在安装塔设备配件设备时,必须保证该设备所在的基础都已符合设计要求,支架坚固可靠,力学性能满足要求。
1.2 进行设备安装时,必须按照设备的安装要求,正确安装接头、牵引螺栓等连接件。
操作人员应该熟悉设备的机械结构、安装规定和关键构件,按照文档中给出的图纸或者操作步骤进行操作。
1.3 安装完毕后,对设备进行检查,严格按照设备使用说明进行测试和调试。
检查无误后,方可进行运转。
2. 设备维护2.1 设备维护工作按照设备的维护要求进行,在设备停止运转后,对设备进行彻底检查并进行清洁维护。
如发现异常情况,应立即报告上级进行处理。
2.2 定期对塔设备配件设备进行维护,如替换轮子、维护电子控制设备等。
维护周期应按照设备的使用寿命、技术状态和生产要求制定计划。
2.3 在维护设备时,应保证设备处于停止状态,严禁在运行的设备上进行维护操作,切断电源或者在电路扼流器中设置合适的开关,确保无法起动,才可进行安全维护操作。
3. 设备运行3.1 在设备运行前,应将设备处于正常状态,检查设备是否有异响,是否处于正常润滑状态,掌握设备的运行规律和性能。
3.2 在设备运行过程中,应该严格按照设备的使用要求进行操作,保持设备稳定运行状态,如发现有异响、有烟尘或者其他异常情况,应立即停机检修,排除异常,保证设备正常运行。
4. 设备保养4.1 定期进行设备保养,根据设备的使用情况及要求制定计划。
设备保养应由具有相关技术资格证书的人员进行,遵循设备的保养规范进行操作。
4.2 设备保养应注意保证设备的稳定运行,如清洁设备、润滑设备、检查设备易损件等。
设备保养记录应详细记录,记录包括设备名称、工作时间、维护标准及效果等内容。
5. 设备报废5.1 设备报废指设备达到了使用年限或者损坏到不能修复的程度,无法维持设备运行的需要而进行报废处理。
塔设备基础知识

塔设备基础知识简介塔设备是指用于通信、广播、航空等领域的设备,通常安装在高塔上。
塔设备的安装和维护涉及到多个方面的知识和技术,在本文档中,我们将介绍塔设备的基础知识,帮助读者对塔设备有一定的了解。
塔设备的种类在通信和广播领域,常见的塔设备主要包括以下几种:1.天线:用于发送和接收无线信号的装置,包括接收天线和发射天线。
2.主设备:包括基站设备、调制解调器等,用于处理和转发信号。
3.电源设备:提供塔设备所需的电力。
4.传输设备:用于传输信号的设备,包括光纤、电缆等。
5.监控设备:用于监控塔设备的运行状态,包括摄像头、传感器等。
塔设备的安装塔设备的安装需要遵循一定的规范和标准,以确保设备的安全和正常运行。
以下是一些常见的安装步骤:1.塔基建设:在塔设备安装之前,首先需要建设塔基。
塔基的建设包括土方开挖、混凝土浇筑等工作。
2.铁塔安装:安装好塔基后,可以进行铁塔的组装和安装。
3.天线安装:在铁塔上安装适当数量和类型的天线,以满足通信或广播需求。
4.主设备安装:将主设备安装在铁塔上,并进行连接和调试。
5.电源设备安装:安装适当的电源设备,并进行连接和测试。
6.传输设备安装:安装传输设备,如光纤、电缆等,并进行连接和测试。
7.监控设备安装:安装监控设备,如摄像头、传感器等,以提供对塔设备的监控和管理。
塔设备的维护为确保塔设备的正常运行,定期的维护是必不可少的。
以下是一些常见的维护步骤:1.定期巡检:定期巡检塔设备,检查设备是否存在松动、腐蚀等问题。
2.清洁保养:定期清洁设备表面的灰尘和污垢,并定期更换易损件。
3.设备检修:对设备进行定期检修,如更换老化的零部件、重新校准设备等。
4.通风与降温:确保塔设备具有良好的通风和降温措施,避免设备过热。
5.防雷与接地:对塔设备进行防雷和接地处理,确保设备的稳定性和安全性。
6.应急维护:在突发情况下,及时进行应急维护,确保塔设备的正常运行。
塔设备的安全塔设备的安全性是至关重要的,保障设备的正常运行和工作人员的安全。
塔类设备安全技术规程范本(二篇)

塔类设备安全技术规程范本【引言】塔类设备具有高高度、高负荷、高风险等特点,对于塔类设备的安全管理至关重要。
为了确保塔类设备的运营安全,制定本技术规程范本,明确塔类设备安全管理的各个环节和要求,以提高塔类设备的安全性和可靠性。
【一、总则】1. 根据国家相关法律法规,制定塔类设备安全管理技术规程,旨在规范塔类设备的安全管理,确保设备运营过程中的人员安全和设备可靠性。
2. 本规程适用于所有的塔类设备,包括但不限于通信塔、电视塔、天线塔等。
3. 塔类设备的产权单位和使用单位应当严格遵守本规程的要求,并承担相应的安全管理责任。
4. 本规程应当与相关国家标准、行业标准和塔类设备产品标准相配合,相互协调。
【二、安全责任】1. 塔类设备的产权单位应当设立安全管理部门,负责塔类设备的安全管理工作,并委托专职人员负责具体的安全管理事务。
2. 塔类设备的产权单位应当制定安全责任制度,明确安全管理部门和相关人员的职责,确保安全管理工作的有效开展。
3. 塔类设备的使用单位应当派遣专职人员负责设备的日常安全管理,并定期开展安全培训,提高人员的安全意识和操作技能。
4. 塔类设备的使用单位应当建立安全档案,包括设备的使用情况、维护记录、事故记录等,并做好备份工作,以备查阅和分析。
【三、设计与施工】1. 塔类设备的设计应符合国家相关标准和规范的要求,具有足够的强度和稳定性。
2. 塔类设备的施工应委托具备相应资质的单位进行,并按照设计要求进行施工工艺和质量管理。
3. 塔类设备的施工现场应划定相应的安全区域,并做好安全隐患排查。
4. 塔类设备的材料和设备选择应符合国家相关标准和行业标准,不得使用假冒伪劣产品。
5. 塔类设备的施工单位应对施工现场的人员进行安全教育和培训,确保工人的安全意识和操作技能。
【四、设备维护】1. 塔类设备的日常维护工作应委托专业的维护单位进行,确保设备的正常运行和安全可靠。
2. 塔类设备的维护人员应持有相应的岗位资格证书,具备一定的技术水平和工作经验。
脱硫塔 管理制度

脱硫塔管理制度第一章总则第一条为了规范脱硫塔的管理,提高脱硫效率,保障生产安全和环境保护,制定本管理制度。
第二条本管理制度适用于公司运营的所有脱硫塔设备,包括湿法脱硫塔和干法脱硫塔等。
第三条公司应当加强对脱硫塔设备的维护保养和管理,确保设备正常运行,提高脱硫效率,减少对环境的污染。
第四条公司要求脱硫塔操作人员必须具备相关的技术培训和操作证书,严格按照操作规程进行操作。
第五条公司领导要高度重视脱硫塔管理工作,加强对设备运行和维护的监督检查,确保设备安全运行。
第二章脱硫塔管理机构第六条公司应当设立脱硫塔管理机构,按照职责分工明确各部门的责任,保障脱硫塔设备的正常运行。
第七条脱硫塔管理机构应当由技术部门、生产部门和安全保卫部门等共同组成,建立健全的管理体系。
第八条技术部门负责脱硫塔设备的维护保养和技术改进工作,负责编制相关技术文件和操作规程。
第九条生产部门负责脱硫塔设备的生产运行工作,定期检查设备情况,制定生产计划和排产计划。
第十条安全保卫部门负责脱硫塔设备的安全管理工作,确保设备运行不发生事故,及时处理安全隐患。
第十一条公司领导应当加强对脱硫塔管理机构的指导和监督,确保各部门间的协作配合,促进工作效率。
第三章脱硫塔设备维护保养第十二条脱硫塔设备的维护保养工作是保证设备正常运行的重要环节,必须定期进行检查和清洁。
第十三条脱硫塔设备的日常维护保养工作由技术部门负责,包括清洁脱硫塔内部各部位和更换易损件等。
第十四条脱硫塔设备的定期检修由专业人员进行,包括清洗反应罐、更换填料、检修阀门等。
第十五条脱硫塔设备的维护保养工作必须做到有计划、有组织、有记录,确保设备的安全运行和延长使用寿命。
第十六条脱硫塔设备的维护保养工作有特殊要求时,必须由专业人员进行操作,严格按照操作规程进行。
第四章脱硫塔设备操作管理第十七条脱硫塔设备操作人员必须具备相关的技术培训和操作证书,严格按照操作规程进行操作。
第十八条脱硫塔设备的操作人员必须着装整洁,戴好安全帽和防护眼镜,确保安全生产。
【输电杆塔设计培训】07、第七章 铁塔结构
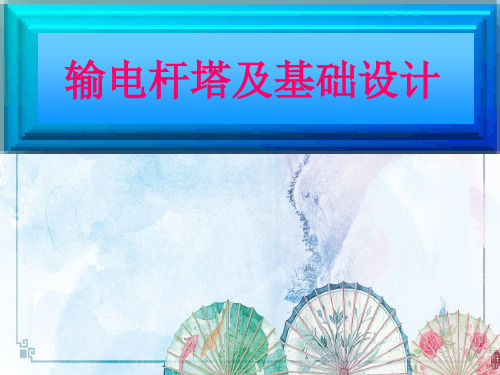
坡度小:与上相反 2、斜材、辅助材:保证铁塔主柱的几何不变 性,和杆件的稳定性及减少构件的长细比 斜材的布置有:单斜材、叉型(双)斜材和K型
斜材。 3、横隔材:用于铁塔分段 4、节点:
斜材与主材的连接或斜材与辅助材连接的 连结处称为节点,各杆件纵向中心线的交点称为 节点中心,相邻两节间的杆件部分称为节间。两 节点中心间的距离称节间长度
4、猫头型铁塔多用于导线要求三角形布置的强 度较高的杆塔。
5、地基承载能力较差及基础施工条件较差的地 区一般采用根开较大或者宽基铁塔。
输电杆塔及基础设计
第七章 铁塔的型式及结构布置
铁塔优缺点:
优点:强度高、重量轻、制造简单等优点,
缺点:维护费用高和造价高等缺点,因此受
一定限制。
第一节 铁塔的分类
一、按根开分
根开b与高度h之比,分为宽基与窄基铁塔
宽基型铁塔
耐张型1/4~l/5
∑P
直线型1/6~1/8;
优点:宽基型铁塔由于底座宽,因此 h
对主材、斜材和基础的作用力
较小(如图N=∑Ph/b)
b
N
N
缺点:但主材间相隔太宽,使斜材与辅助材的布 置复杂。
窄基型铁塔。 1/12~1/14 (b/h) 。
优缺点与宽基相反 选用原则: 宽基铁塔:宽基铁塔相对可以减轻塔身荷载和基 础受力,这对基础土方开挖量大且运输不方便的山 区,地耐力较差的地区较适用。 窄基塔塔:窄基塔塔与宽基铁塔相比,结构较简 单,重量较轻,对线路通过人口稠密的狭窄地段, 窄基铁塔尤为适宜。窄基铁塔为整体基础,需混凝土用量较大。
(2)按头部型式分 单回路: 上字型、猫头型、“干”字型(如图)
特点:导线呈三角形排列 酒杯型、门型(如图)
水塔设备日常管理制度

水塔设备日常管理制度第一章总则第一条为了规范水塔设备的日常管理工作,确保水塔设备的正常运行和安全使用,制定本制度。
第二条水塔设备日常管理制度适用于水塔设备的日常检查、维护、保养和管理工作。
第三条水塔设备的管理依据相关国家标准和规定执行。
第四条水塔设备的使用单位应建立相应的设备档案,记录设备的基本信息、检修记录、维护记录等。
第五条水塔设备管理人员应具备相应的专业技术能力和管理经验,经过相关培训后方可上岗。
第二章检查和维护第六条水塔设备的日常检查工作应定期进行,检查内容包括设备的完好性、运行状况、安全防护等。
第七条水塔设备的维护工作应定期进行,主要包括设备清洁、润滑、紧固以及易损件的更换等。
第八条水塔设备的检查和维护应由专业人员负责,确保检查和维护的质量。
第九条水塔设备出现故障时,应及时进行维修,维修过程中应做好安全防护措施,确保维修人员的安全。
第十条水塔设备的定期检查、维护和维修工作需制定详细的计划和方案,由设备管理人员负责执行。
第三章安全管理第十一条水塔设备的管理单位应建立健全的安全管理制度,规范设备的使用和维护。
第十二条水塔设备管理人员应加强对设备操作人员的培训和教育,提高其安全意识和应变能力。
第十三条水塔设备使用过程中应做好防火、防爆等安全预防工作,确保设备的安全运行。
第十四条水塔设备管理人员应定期进行安全检查,发现安全隐患及时整改,确保设备的安全使用。
第四章应急管理第十五条水塔设备管理单位应建立应急预案,明确应急处理流程和责任人。
第十六条水塔设备管理人员应参加应急演练,提高处理突发事件的应变能力。
第十七条水塔设备发生故障或事故时,应立即启动应急预案,组织相关人员进行应急处置。
第十八条水塔设备管理人员应做好事故记录和报告,及时总结经验教训,改进管理工作。
第五章监督检查第十九条监督部门应加强对水塔设备管理工作的监督检查,确保管理工作的规范性和有效性。
第二十条监督部门有权对水塔设备的使用单位进行抽查检查,发现问题应及时整改。
塔设备基础知识课件(原创)

Байду номын сангаас4、溢流堰及进口堰
溢流堰有保持塔盘板上一定液层 高度和促使液流均匀分布的作用。 采用平型受液盘时,为使上层塔 板流入的液体能在塔盘上均匀分 布,并为了减小入口液流的冲力, 常在液体进口处设置进口堰
二、填料塔
(一)填料
填料是填料塔的核心内 件,它为气-液两相 充分接触进行传热传 质提供了表面积。可 分为散装填料和规整 填料两大类。
a.塔体 塔体即塔设备的外壳,常见的塔 体由等直径、等厚度的圆筒及上下封头 组成。塔设备通常安装在室外,因而塔 体除了承受一定的操作压力(内压或外 压)、温度外,还要考虑风载荷、地震 载荷、偏心载荷。此外还要满足在试压、 运输及吊装时的强度、刚度及稳定性要 求
b.支座 塔体支座是塔体与基础的连接结构。因为塔设 备较高、重量较大,为保证其足够的强度及刚度,通 常采用裙式支座。
优点 : ① 由于没有降液管,所以结构简单,加工容易、安装维
修方便,投资少; ② 因节省了降液管所占的塔截面(一般约为塔盘截面的
15%~30%),允许通过更多的蒸气量,因此生产能力比 泡罩塔大20%~100%; ③ 因为塔盘上开孔率大,栅缝或筛孔处的压力降较小, 比泡罩塔低40%~80%,可用于真空蒸馏。 其缺点是: ① 塔板效率比较低,比一般板式塔低30%~60%,但因 这种塔盘的开孔率大,气速低,形成的泡沫层高度较低, 雾沫夹带量小,所以可以降低塔板的间距,在同样分离 条件下,塔总高与泡罩塔基本相同; ② 操作弹性较小,能保持较好的分离效率时,塔板负荷 的上下限之比约为2.5~3.0。
(3)浮动舌形塔 浮动舌形塔是20世纪60年代研制的一种定向喷
射型塔板。它的处理能力大,压降小,舌片 可以浮动。因此,塔盘的雾沫夹带及漏液均 较小,操作弹性显著增加,板效率也较高, 但其舌片容易损坏。
化工安全教育(第七章 机械伤害的预防)
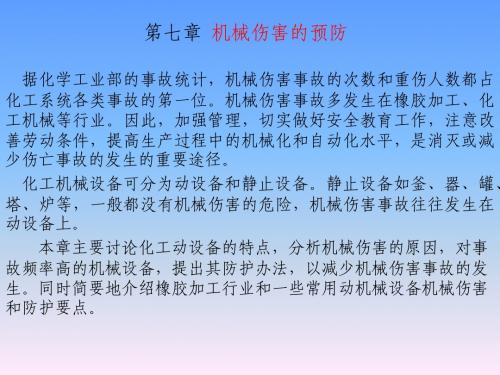
3.对安全防护装臵、栅栏和防护罩的要求 (1)使操作者触及不到运转中的零部件。 (2)当操作者接近运动中零部件时,动机械设备应能立即自动停车 。 (3)安全防护装臵应便于检查、调节和维修。 (4)安装牢固、维修完毕及时复原。 4.动设备的安全环境要求 (1)动设备的操作岗位,应设防滑、防坠落的安全平台和栏杆。 (2) 动设备的操作岗位在 2m以上时,应配臵安全可靠的操作平台 、梯子和栏杆。 (3)动设备的操作岗位必须有良好的照明和通风。 (4)噪声大的动机械设备,应设隔音设施,或给职工提供耳塞等防 护用品。
(5)机器电气安全联锁装臵如有失灵现象,必须及时停车检 修。 (6)机器设备不得超负荷运转。 (7)转动部件上不要放臵物件,以免开车时物件飞出,发生 打击事故。 (8)正确使用和穿戴个体劳动保护用品。劳保用品是保护职 工安全和健康的必需品,必须正确穿戴衣、帽、鞋、防毒面 具、手套等防护品。防护用品要根据实际工况条件选择,如 机床岗位的工人不准戴手套操作,但要戴防护眼镜;接触酸 、碱的岗位要穿防护衣,同时要佩戴防护眼镜,有的还需要 佩戴防护于套;有长发的女工,必须戴工作帽操作。
三、操作环境不良
操作人员如在照明不好、通风不良、排尘排毒欠佳的 环境下工作,就可能出现误操作的行为。
第三节 防止机械伤害事故的安全措施
防止机械伤害事故的发生,必须从安全管理工作入手, 防止出现人的不安全行为和消除动机械的不安全状态。 同时还应在工程技术方面解决动机械设备的安全防护 和安全保险等同题。
一、严格安全管理,健全动机械设备的安全管理 制度,防止人的不安全行为
1.根据各种不同类型的机械设备,按其特点制订安全操作 规程,其内容如下。 (1)动机械设备的工作原理、结构和各项技术性能指标。 (2)主要零部件的规格、材料及使用条件。 (3)安全操作方法和开停车时应注意的安全事项。 (4)各类事故的处理方法。 (5)该机械设备的重要防护部位和危险区域范围。 (6)做好保养和定期维修。 健全各项机械设备的安全操作规程,同时还应严格执 行,这样才能保障安全生产,减少和消灭机械伤害事 故的发生。
塔设备配件设备安全操作规程

塔设备配件设备安全操作规程1. 前言本规程旨在为使用塔设备配件设备的工作人员提供相关的安全操作指南,减少工作中的安全隐患,保障人员的生命财产安全。
2. 塔设备配件设备的分类塔设备配件设备主要分为以下几类:1.吊装设备:主要用于吊装、安装塔设备及其配件。
2.电动工具:主要用于加工、修理塔设备及其配件。
3.支架、建筑工具:主要用于搭建塔设备及其配件的支架、建筑工作。
3. 塔设备配件设备的安全操作规程在使用塔设备配件设备时,应注意以下安全操作规程:3.1 工作前的检查在工作前,应对设备及其配件进行以下检查:•检查吊装、支架、建筑工具的结构是否完整,严禁使用存在破损、变形、断裂的工具。
•检查电动工具的电源是否接通正确、是否有异常声音,严禁使用存在电缆断裂、机身磨损、锈蚀、电器故障等情况的电动工具。
•检查安全装置是否完好,是否安装可靠。
3.2 设备安装、吊装操作规程•设备安装、吊装前,应制定详细的操作计划,根据操作要求设置相关的支架、悬挂点等设备,保证吊装、安装平稳、安全。
•在设备吊装时,应保证吊具的坚实、牢固,吊钩固定在设备吊装点上,严禁吊装时半空中操作。
•吊装过程中,应严格控制吊装速度,避免过快或过慢的操作,以免造成设备的损坏或坠落。
3.3 电动工具操作规程•在使用电动工具时,应先了解其性能、特点,事先进行试机、试切等操作,确保设备能正常运转。
•操作时应遵守规范的操作程序,避免过度力量操作,以免造成人身伤害或设备损坏。
•电动工具的电源线应放在安全地方,以免造成人员交织、电线插座短路等情况,避免出现火灾等事故。
3.4 建筑工具操作规程•建筑工具操作人员应熟练掌握操作技巧,只有具备一定的专业技能才能进行操作。
•在工作中,应避免从高处坠落、接触到锋利的建筑用具等危险操作,建议在不安全的操作位置设立警告标志。
•在使用开裆锤、电钻等工具时,应戴好防护镜、口罩等设备,防止出现眼、口腔等危害。
4. 安全注意事项•使用塔设备配件设备的工作人员,应熟练操作相关设备,了解相应安全操作规程,并按规程操作。
塔式起重机使用、装、拆管理规定(3篇)

塔式起重机使用、装、拆管理规定第一章总则第一条为规范塔式起重机的使用、装、拆工作,保障施工安全,制定本管理规定。
第二条本规定适用于各类塔式起重机的使用、装、拆工作。
第三条塔式起重机的使用、装、拆工作应遵守国家和地方的有关法律法规、标准和规范。
第四条塔式起重机的使用、装、拆工作由具有相应资质的专业人员负责,并经过培训合格。
第五条塔式起重机的使用、装、拆工作应有明确的责任分工和工作流程。
第二章使用管理第六条选择塔式起重机时,应根据工地实际情况确定合适的起重机型号、技术参数,并确保满足国家和地方的安全要求。
第七条塔式起重机的使用前应进行全面检查,确保各项安全设备完好,机械部件灵活可靠。
第八条塔式起重机的使用过程中,操作人员应按照操作规程进行操作,并及时报告设备异常情况。
第九条塔式起重机在运行过程中,不得超负荷作业,不得进行非法改装、拼装或局部加固。
第十条塔式起重机使用完毕后,应及时停止运行并进行检查,确保设备安全退场。
第三章装配管理第十一条塔式起重机的装配工作应由具有相应资质的专业人员负责,并按照施工方案进行操作。
第十二条塔式起重机的各部组装前,应检查各部件的完整性和可靠性,并依次进行组装。
第十三条塔式起重机的各部组装完毕后,应进行调试和试车,确保设备运行正常。
第十四条塔式起重机的装配过程中,应根据实际情况设置适当的防护措施,确保工作环境安全。
第十五条塔式起重机装配完毕后,应进行验收,由专业人员进行确认,并签署相应文件。
第四章拆卸管理第十六条塔式起重机的拆卸工作应由具有相应资质的专业人员负责,并按照施工方案进行操作。
第十七条塔式起重机的拆卸前,应进行设备检查,包括安全设备和机械部件的检查,并确保各部件的可拆卸性。
第十八条塔式起重机的拆卸过程中,应根据实际情况设置适当的防护措施,确保工作环境安全。
第十九条塔式起重机拆卸完毕后,应进行验收,由专业人员进行确认,并签署相应文件。
第五章安全管理第二十条塔式起重机使用、装、拆工作中,应遵循“安全第一、预防为主”的原则,重视施工过程中的安全风险。
塔类设备安全技术规程范文
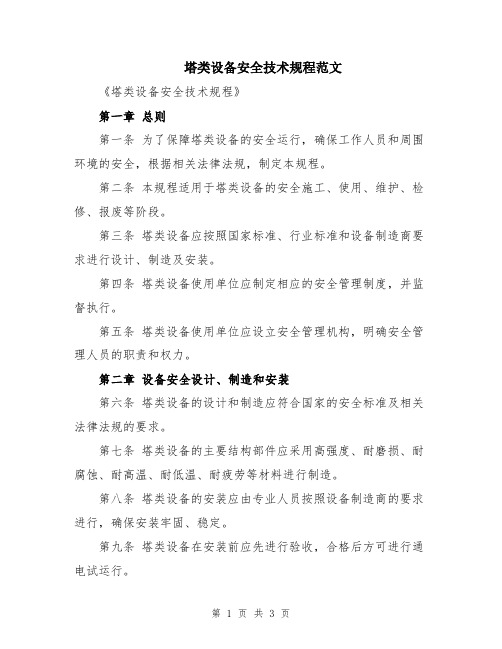
塔类设备安全技术规程范文《塔类设备安全技术规程》第一章总则第一条为了保障塔类设备的安全运行,确保工作人员和周围环境的安全,根据相关法律法规,制定本规程。
第二条本规程适用于塔类设备的安全施工、使用、维护、检修、报废等阶段。
第三条塔类设备应按照国家标准、行业标准和设备制造商要求进行设计、制造及安装。
第四条塔类设备使用单位应制定相应的安全管理制度,并监督执行。
第五条塔类设备使用单位应设立安全管理机构,明确安全管理人员的职责和权力。
第二章设备安全设计、制造和安装第六条塔类设备的设计和制造应符合国家的安全标准及相关法律法规的要求。
第七条塔类设备的主要结构部件应采用高强度、耐磨损、耐腐蚀、耐高温、耐低温、耐疲劳等材料进行制造。
第八条塔类设备的安装应由专业人员按照设备制造商的要求进行,确保安装牢固、稳定。
第九条塔类设备在安装前应先进行验收,合格后方可进行通电试运行。
第三章设备使用管理第十条塔类设备使用单位应指定专人负责设备的日常管理和维护工作。
第十一条设备使用人员应经过相关的培训,掌握操作技能和紧急故障处理能力。
第十二条塔类设备使用单位应制定相应的操作规程,明确设备使用的步骤和注意事项。
第十三条塔类设备的使用过程中,应严格按照设备的使用说明进行操作,不得随意变动参数。
第四章设备维护与检修第十四条塔类设备使用单位应制定设备的定期检查和维护计划,并按时进行维护和检修工作。
第十五条塔类设备的维护和检修工作应由专业人员进行,不得由无相关技术知识的人员擅自进行。
第十六条塔类设备的检修过程中应严格遵守相关的操作规程,确保安全。
第五章设备报废与淘汰第十七条塔类设备达到使用寿命或存在严重安全隐患时,应及时停止使用并报废。
第十八条塔类设备的报废处理应有相关的程序和计划,确保设备的安全处理。
第十九条塔类设备报废后,应妥善存放或交由合法机构进行处理。
第六章安全教育与培训第二十条塔类设备使用单位应定期组织安全教育和培训,提升人员的安全意识和技能。
塔式起重机基础知识
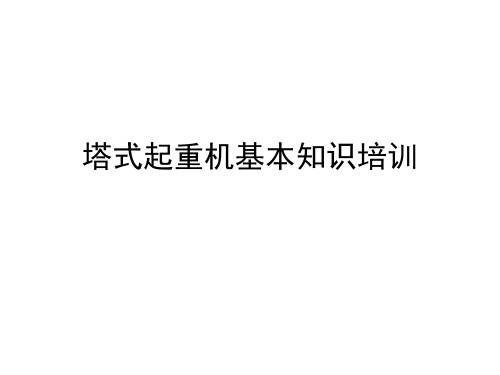
第一章 塔式起重机的分类与标识
1、分类 按回转支承位置分 上回转塔机 下回转塔机 按变幅方式分主要有 小车变幅式 动臂变幅式 按安装方式分 快速安装式(下回转式) 非快速安装式(上回转式) 按底架固定情况分 固定式 轨行式 升高方式分 固定高度 自升式(附着式、内爬式)
自升附着式塔机
塔机安装在建筑物一侧,底 座固定在专门的基础上或将行走 台车固定在轨道上,随着塔身的 自行加节升高,每间隔一定高度 用专用杆件将塔身与建筑物连接, 依附在建筑物上。 附着式塔机是我国目前应用 最广泛的一种安装形式,塔机由 其他起重设备安装至基本高度后, 即可由自身的顶升机构,随建筑 物升高将塔身逐节接高,附着和 顶升过程可利用施工间隙进行, 对工程进度影响不大,且建筑物 仅承受由塔机附着杆件所传递的 水平载荷,一般无需特别加固。 施工结束后,塔机的拆卸可按安 装逆程序进行,不需另设拆卸设 备
3、满足塔吊基础设置的要求 设置在基坑外的塔吊基础,应尽量避开室外总体管线密集区域;设置于基坑 基础结构内的塔吊基础,应避免与地下室墙、柱、梁、后浇带体系相碰。并设置 于防水处理较方便的位置。
4、满足塔吊附着的位置和尺寸要求 建筑物的附着点可选为框架柱、结构主梁及剪力墙、丁字墙、L形墙等位置,
并尽可能对称布置以利附着及结构的合理受力。经验数据为:塔身中点至两个附
着支座连线的垂直距离为5~8m,附着杆与附着支座连线的夹角为45~70°。 5、满足结构施工设备及设施的空间位置要求 在塔吊定位时注意避免塔身尤其是塔吊顶部爬升架平台不可与外墙脚手架相 交错(特别注意要避开外挑造型);塔吊平面定位还应考虑施工电梯位置的要求 (可考虑塔吊与施工电梯分立建筑物两侧;必须设于同一侧时应尽量错开设置)。 6、满足塔吊拆除的要求 塔吊在安、拆过程中,塔吊前臂必须与爬升架标准节引进装置口的朝向一致。 若塔吊前臂方向存在新建建筑物的主体或其它障碍物,将导致塔身无法拆除。塔 吊布置应尽量使塔吊能拆至地面。
化工过程设备设计教学课件:第七章塔设备7.1-7.2塔设备的作用与分类及填料塔与板式塔简介
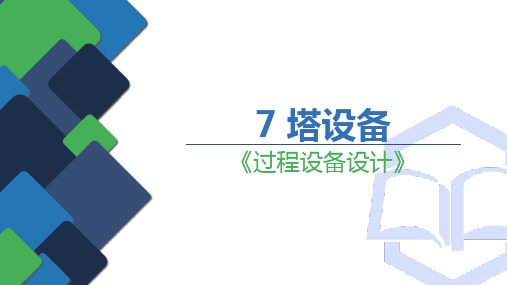
《过程设备设计》
目录
7.1 塔设备的作用与分类 7.2 填料塔与板式塔简介 7.3 塔设备的选型 7.4 塔设备的设计 7.5 塔设备的振动
1
塔设备的作用与分类
石化装置中的塔林
7.1 塔设备的作用与分类
(1)塔设备作用 重要的单元操作设备。 实现气(汽)—液相或液—液相之间的充分接触,从而达到 相际间进行传质及传热的目的。 石油化工、煤化工、医药、食品等行业有广泛应用。 例如,在炼油和煤化工中,塔设备投资占所有工艺设备总投 资的34.85%;在30万吨乙烯装置中,塔设备所占的质量比 例高达25.3%。
谢谢观赏
《过程设备设计》
气体通过每层板上液层时,形成气泡与液沫,泡沫可为两相
接触提供足够大的相际接触面,有利于相间传质。
板式塔
板式塔结构简图
返回
板式塔
返回
7.2 填料塔与板式塔简介
(2)塔设备的结构 无论是填料塔还是板式塔,除了各种内件之外, 均由塔体、支座、人孔或手孔、除沫器、接管、 吊柱及扶梯、操作平台等组成。
甲醇酒精回收塔
(2)塔设备分类
按操作 压力
加压塔 常压塔 减压塔
按内件 结构
填料塔 板式塔
按单元 操作
精馏塔 吸收塔 萃取塔 干燥塔
最常用的分类方法
12
填料塔与板式塔简介
7.2 填料塔与板式塔简介
(1)填料塔
简图1 简图2
填料塔为连续(或称微分)接触式的气液传质设备。 在圆筒形的塔体内部,分段装有若干段填料,填料堆积于支撑装置上。 液体由塔顶入口管进入分布器,均匀喷淋在填料表面上并在重力作用下向 下流动,气体在压强差的推动下,由支承板下方气体入口管进入塔内,通 过填料间的空隙由塔的顶部排出。 填料塔内气液两相呈逆流流动,气体和液体在填料表面上进行传质和传热, 两相的组成沿塔高连续变化。
精选塔设备的附件与振动
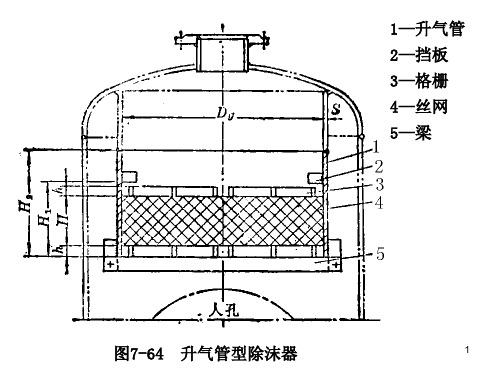
⒋ 临界风速
共振—当旋涡脱落的频率与塔的任一振型的固有频率一致时, 会引起塔的剧烈振动临界风速—塔共振时风速. 若取Sr =0.2,则由(7-49) 式可求得临界风速。
(7-49)
二、塔设备的自振周期(固有周期)
固有周期计算方法
塔设备的力学模型: 简化成底端固定、顶端自由、质量沿高度 连续分布的悬臂梁,图7-71塔视为具有多个自由度体系,则它具有多个固有频率。基本频率—固有频率中最低的频率振型—振动后的变形曲线,图7-72
三、吊柱
图7-70
目的—(室外无框架整体塔设备)为了安装、拆卸内件, 更换或补充填料。位置— 塔顶。吊柱中心线与人孔中心线间有合适夹角, 便于操作。见图7-70。材料—吊柱管用20无缝钢管,其它部件用Q235-A和 Q235-A·F。吊柱与塔连接的衬板应与塔体材料相同尺寸—主要结构尺寸参数已制定系列标准
⒊结构: ⑴裙座的组成: 图7-68, 裙座筒体、基础环、地脚螺栓座、人孔、 排气孔、排液孔、引出管通道、保温支承圈等 ⑵裙座与塔体的焊接型式:
对接:图7-69(a), a.焊缝受压, 焊缝受力好 b.但焊缝位于端盖折边处, 对端盖受力不利 c.且不利于和塔体组对时的对中搭接:图7-69(b), (c) a.焊缝受剪, 焊缝受力不好 b.但焊缝位于端盖直边处, 改善了端盖受力情况 c.且安装较方便
旋涡特性与雷诺数的关系
a.当Re<5—不发生边界层分离现象→无旋涡产生b.当 5≤Re<40—塔体背后出现一对稳定的旋涡c.当40≤Re<150—出现卡曼涡街, 塔体背风面交替产 生旋转方向相反的旋涡, 图7-84d.当300≤Re<3×105—亚临界区, 旋涡以一确定的 频率周期性地脱落e.当3×105≤Re<3.5×106—过渡期, 无涡街出现, 尾流 变窄,无规律且都变成紊流f.当Re≥3.5×106—超临界区, 卡曼涡街又重新出现
- 1、下载文档前请自行甄别文档内容的完整性,平台不提供额外的编辑、内容补充、找答案等附加服务。
- 2、"仅部分预览"的文档,不可在线预览部分如存在完整性等问题,可反馈申请退款(可完整预览的文档不适用该条件!)。
- 3、如文档侵犯您的权益,请联系客服反馈,我们会尽快为您处理(人工客服工作时间:9:00-18:30)。
(b)
(a)
(c)
(a)弓形降液管 (b)带溢流堰的圆形降液管 (c) 兼作溢流堰的圆形降液管图
图7-15 降液管的基本类型
第二节 板式塔
图7-13 单溢流分块式塔盘支撑结构
1-通道板;2-矩形板;3-弓形板;4-支撑圈; 5-筋板;6-受液盘;7-支撑板;8-固定降液板; 9-可调堰板;10-可拆降液板;11-联接板
第一节 塔设备概述
塔设备在 化工生产 中的应用
化工生产中常见的可在塔设备中完成的单元操作有:精馏、吸收、解 吸和萃取等。此外,工业气体的冷却与回收、气体的湿法精制和干燥中 也多使用塔设备,另外,在兼有气液两相传质和传热的增湿、减湿等生 产装置塔设备也有广泛的应用。 据有关资料报道,塔设备的投资费用及钢材耗量仅次于换热设备, 参看表7-1。据统计,在化工和石油化工生产装置中,塔设备的投资费用 占全部工艺设备总投资的25.39%,在炼油和煤化生产装置中占34.85%; 其所消耗的钢材重量在各类工艺设备中所占比例也是比较高的,如年产 250万吨常减压蒸馏装置中,塔设备耗用钢材重量占45.5%,年产120万
图7-6 筛板结构及气液接触情况
第二节 板式塔
(3)穿流 板塔气体 通道
穿流板塔与筛板塔相比,其结构 特点是不设降液管。气体和液体同
栅板支撑圈
时经由板上孔道逆流通过,在塔盘上 形成泡沫进行传质与传热。常用的塔 板结构有筛孔板和栅板两种。穿流式 栅板及支承情况如图7-7所示。
穿流板塔结构简单,制造、加工、
图7-5 圆形泡罩
第二节 板式塔
(2)筛板 塔气体通 道
筛板塔的塔盘为一钻有许多孔的圆形平板。 筛板分为筛孔区、无孔区、溢流区、降液管 区等几个部分。筛孔直径一般为3~8mm, 通常按正三角形布置,孔间距与孔径的比值 为3~4。随着研究的深入,近年来,发展了 大孔径(20~25mm)和导向筛板等多种形式 的筛板塔。
填料塔塔体安装垂直度偏差不得超过塔高的2/1000,且不大于30mm。 (3)塔盘板长度偏差不得超过±0.4mm,宽度偏差不得超过:±0.2 mm。 (4)塔盘板需要维持一定的水平度,否则将影响气、液的均匀分布。
第一节 塔设备概述
第一节 塔设备概述
(5) 为了保证塔盘的水平度,支持圈的表面水平度亦有一定的要求。在300mm弦长 的表面上,局部不平度不超过1mm,总的不平度的允许偏差与塔盘相同(即表7-2的 f值),相邻两支撑全间距的偏不超过±20mm. (6) 溢流堰顶的水平度对塔盘板的操作及效率均有影响,故堰顶的水平度不超过 堰宽的1/1000,且不大于3mm。 (7) 降液管安装后,其下端与受液盘距离的偏差为±3mm。 (8) 栅板应平整,安装后的不平度不超过2mm。对最底层的栅板没有不平度要求。 (9) 液体分布装置安装时,水平偏差不超过3mm,标高偏差不超过±3mm,其中心 线与塔中心线偏差不超过3mm。 (10)塔体在同一断面上的最大直径与最小直径之差e,应符合下述规定:受内压塔, e≤1%DN(DN 为塔内径),且e不大于25mm;对受外压塔,e≤0.5%DN,且e不大于 25mm。 (11) 裙座(支座)螺栓孔中心圆直径偏差小于±3mm,任意两孔间距偏差小于±3mm。
2.塔设备的技术要求 塔设备制造、安装质量对设备能否达到预期的操作性能有很大影响, 必须注意技术要求。 (1)塔体弯曲度应小于1/1000塔高。塔总高20m以下,塔体弯曲度不得 超过20mm,当塔高>20m,塔体弯曲度不得超过30mm。
(2)板式塔塔体安装垂直度偏差应小于1/1000塔高,且不大于15mm;
装到焊在塔内壁的塔盘固定件(一般为支持圈)上。塔盘板的分块,应结构简单,
图7-7 穿流式栅板
维修简便,塔截面利用率高,生产能 力大,塔盘开孔率大,压降小。但塔 板效力较低,操作弹性小。
第二节 板式塔
(4)浮阀 塔气体通 道
(a) F型浮阀结构
(b)F1型(v-1型)浮阀 (c) v-4 型浮阀
(d) v-6型
(e) 十字架形浮阀
(f) v-o型
(g) A形浮阀
(h) 十字型浮阀 (i)条形浮阀
图7-14 双溢流分块式塔盘支撑结构
1-塔盘板;2-支持板;3-筋板;4-压板;5-支 座;6-主梁;7-两侧降液板;8-可调降液板; 9-中心降液板;10-支撑圈
第二节 板式塔
(a) (b) 1- 受液盘; 2- 降液管; 1- 塔壁筋板 3-塔盘板;4-
第二节 板式塔
整块式塔盘塔的塔体由若干塔节组成,塔节与 塔节之间由用法兰连接。每个塔节中安装若干块 层层叠置起来的塔盘。塔盘与塔盘之间用管子支 承,并保持需要的间距。在这类结构中,由于塔 盘和塔壁有间隙,故对每一层塔盘须用填料来密
图7-21 塔盘的密封形式
封(图7-21)。
第二节 板式塔
图7-22 分块式塔盘示意图
图7-8 浮 阀
图7-9 工作时的阀片
第二节 板式塔
(5)舌形 塔气体通 道
(b)
(c)
20°
(a)
(d)
图7-10 舌形塔盘及舌孔形状
舌形塔属于喷射形塔。 20世纪60年代开始应用。 与开有圆形孔的筛板不 同,舌形塔板的气体通 道是按一定排列方式冲 出的舌片孔(见图7-10)。 舌孔有三面切口和拱形 切口两种,如图7-10(b) 和图7-10(c)所示。常用 的三面切口舌片的开启 度一般为20°,如图710(d)所示。
第二节 板式塔
(6)浮动舌 形塔气体 通道
图7-11 浮动舌片结构
(6)浮动舌形塔 浮动舌形塔盘是在塔板孔内装设 了可以浮动的舌片(见图7-11)。 浮动舌片 既保留了舌形塔倾斜喷射的结构 特点,又具有浮阀操作弹性好的 优点。 浮动舌形塔具有处理量大、压降 小、雾沫夹带少、操作弹性大稳 定性好、 塔板效率高等优点。缺点是在操 作过程中浮舌易磨损。
第二节 板式塔
板式塔的结构形式多种多样,各种塔盘结构都具有各自的特点,且都有各自 适宜的生产条件和范围,在具体选择塔盘结构时应根据工艺要求选择。表7-3对 几种常用塔形的性能进行了比较,供使用时参考。
第二节 板式塔
2. 溢流装置 板式塔内部的溢流装置包括降液管、受液盘、溢流堰等部件。 (1)降液管 降液管是液体自上层塔板流至下层塔板 的通道,也是气(汽)体与液体分离的部位。 为此,降液管中必须有足够的空间,让液体 有所需的停留时间。此外,为保证气液两相 在塔板上形成足够的相际传质表面,塔板上 须保持一定深度的液层,为此,在塔板流体 的出口端设置溢流堰。塔板上液层高度在很 大程度上由堰高决定。溢流装置有单溢流分 块式塔盘(图7-13)和双溢流分块式塔盘 (图7-14)。对于大型塔板,为保证液流均 布,一般采用双溢流分块式塔盘结构,还在 塔板的进口端设置进口堰。
第二节 板式塔
(7)导向筛 板塔气体 通道
图7-12 导向筛板与鼓泡促进器
导向筛板塔是在普通筛板塔的基础上改进而成。它的结构特点是:在塔盘上开有一定数量的 导向孔,通过导向孔的气流与液流方向一致,对液流有一定的推动作用,有利于减少液面梯度; 在塔板的液体入孔处增设了鼓泡促进结构,有利于液体刚流入塔板就可以生产鼓泡,形成良好 的气液接触条件,以提高塔板利用率,减薄液层,减小压降。与普通筛板塔相比,塔板效率可 提高13%左右,压降可下降15%左右。
(a) 自身梁式
(b)槽式
图7-23 自身梁式与槽式塔盘示意图
在直径较大的板式塔中,如果仍用整块式塔盘,则由于刚度的要求,塔盘板的 厚度势必增加,而且在制造、安装与检修等方面很不方便。因此,当塔径在 800~900mm以上时,由于人能进入塔内,故都采用分块式塔盘(图7-22),此 时塔身为一焊制整体圆筒,不分塔节,而塔盘板被分成数块,通过人孔送进塔内,
第二节 板式塔
在塔或塔段的最底层塔盘降液管末 端应设液封盘,以保证降液管出口处 的液封。用于弓形降液管的液封盘如 图7-17(a)所示。用于圆形降液管的液
(a) 图7-17 液封盘 (b)
封盘如图7-17(b)所示。液封盘上开设
有泪孔,以供停工时排液。
1-支撑圈;2-液封盘 1-圆形降液管;2-筋板; 3-泪孔;4-降液板 3-液封盘
《化工设备操作与维护》
第七章 塔设备
第七章 塔设备
目 录
1 2 3
塔设备概述 板式塔 填料塔
第一节 塔设备概述
一、塔设备在化工生产中的应用
在炼油、化工及轻工等工业生产中,气、液两相直接接触进行
传质传热的过程是很多的,如精馏、吸收、解吸、萃取等。这些过 程都是在一定的压力、温度、流量等工艺条件下,在一定的设备 内完成的。由于其过程中两种介质主要发生的是质的交换,所以 也将实现这些过程的设备叫传质设备;从外形上看这些设备都是 竖直安装的圆筒形容器,且长径比较大,形如“塔”,故习惯上称其 为塔设备。
图7-16 受液盘的基本类型
(2)受液盘 为了保证降液管出口处的液封,在塔盘 上一般都设置有受液盘。受液盘的结构形 式对塔的侧线取出、降液管的液封、液体 流出塔盘的均匀性都有影响。受液盘有平 形和凹形两种。平形受液盘有可拆和焊接 两种结构,图7-16(a)为一种可拆式平形受 液盘。平形受液盘因可避免形成死角而适 应易聚合的物料。当液体通过降液管与受 液盘时,如果压降过大或采用倾斜式降液 管,则应采用凹形受液盘,见图7-16(b)。 凹形受液盘的深度一般大于50mm,而小 于塔板间距的1/3。
图7-2 填料塔基本结构
第一节 塔设备概述
三、塔设备的工艺要求和技术要求
1.塔设备的工艺要求
(1) 生产能力大。 (2) 分离效率高。 (3) 操作稳定、弹性大。 (4) 压降小。 (5) 结构简单、材料耗用量小、制造和安装容易。 (6) 耐腐蚀和不易堵塞,操作、调节和检修方便。
第一节 塔设备概述
第一节 塔设备概述
四、塔设备的发展