真空压力浸渍炉技术方案
真空浸渍设备的工艺技术及对应设备的改进

真空浸渍设备的工艺技术及对应设备的改进摘要:真空浸渍就是将设备真空化后融入浸渍液,然后将设备缝隙浸入浸渍液,让设备彻底浸渍。
解决了产品的绝缘性,同时做到了防水和防止透气的问题。
相关的产业包括一些电缆电力设备和开关设备等。
本文通过真空浸渍的设备的改进,技术的改进和具体环节的改进三方面,同时在相关的弊端和解决方案上来阐述真空浸渍的改进方法。
并且笔者通过自己的个人经验,对新的绝缘材料的发展和材料的调试方面进行讲解,相对的问题进行分析,提出相应的建议和反馈。
关键词:真空浸渍;设备;工艺;改进引言真空浸渍法是为了创造真空环境和解决漏水透气的问题,广泛地应用到电力、金属铸件等方面,同时它还是主要的电热和传导的工艺手段。
将真空浸渍的方法提高,提高密闭性,同时改善真空浸渍的技术和工艺,可以大大地提高工艺水平和工艺精准性,减少事故的发生和相关的安全隐患,同时在新型的绝缘材料上提出自己的建议,为日后的工艺创造制造了良好的条件,同时造福生产和生活。
一、真空浸渍工艺操作的弊端(一)返油真空浸渍设备的返油是因为真空罐和真空泵的配合气压差造成的,油随着气体压差被带到了别的区域,所以造成了设备的损害和使用寿命的折损。
因为真空泵是一个活门的排气装置,与外界断开,而耐油橡胶活门具有一定的弹性,可以保持它的相对通透性,但是由于真空泵内气场压力过大,或者是使用操作不当带来的过大压差,都会造成大量的真空油渍被带入进别的区域,油渍的进入会减少内部的油量,并且让局部温度过高,产生局部积油。
这样甚至会带来腐蚀,因为机器内长久以来存在的杂质会与油脂发生反应,会使设备加速老化,同时带来安全隐患。
油脂在过高的温度下还会发生一些其他的问题,例如是油质的变质和一些油脂甚至会与氧气发生反应,产生新的物质,这样带来的安全隐患就更为严重。
油脂在这种情况下的逐渐堆积,会让机器运转速度变慢,而局部的变慢就会产生运转的弧度,甚至是事故,同时油脂的部分积累带来机器局部过重的问题[1]。
真空压力浸漆工艺流程
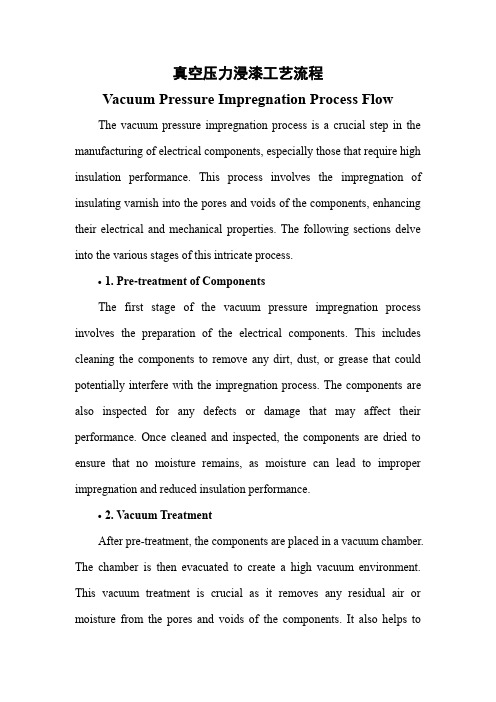
真空压力浸漆工艺流程Vacuum Pressure Impregnation Process FlowThe vacuum pressure impregnation process is a crucial step in the manufacturing of electrical components, especially those that require high insulation performance. This process involves the impregnation of insulating varnish into the pores and voids of the components, enhancing their electrical and mechanical properties. The following sections delve into the various stages of this intricate process.•1. Pre-treatment of ComponentsThe first stage of the vacuum pressure impregnation process involves the preparation of the electrical components. This includes cleaning the components to remove any dirt, dust, or grease that could potentially interfere with the impregnation process. The components are also inspected for any defects or damage that may affect their performance. Once cleaned and inspected, the components are dried to ensure that no moisture remains, as moisture can lead to improper impregnation and reduced insulation performance.•2. Vacuum TreatmentAfter pre-treatment, the components are placed in a vacuum chamber. The chamber is then evacuated to create a high vacuum environment. This vacuum treatment is crucial as it removes any residual air or moisture from the pores and voids of the components. It also helps toexpand the pores, making it easier for the varnish to penetrate and fill them during the impregnation process.•3. Varnish ImpregnationOnce the vacuum chamber has reached the desired vacuum level, the insulating varnish is introduced into the chamber. The varnish is carefully chosen based on the specific requirements of the components, such as their operating temperature, electrical performance, and environmental conditions. The varnish is then drawn into the pores and voids of the components by the vacuum pressure. This process ensures that the varnish penetrates deeply into the components, providing optimal insulation.•4. Pressure ApplicationAfter the varnish has been impregnated into the components, pressure is applied to the chamber. This pressure helps to force the varnish deeper into the pores and voids, ensuring complete impregnation. The pressure is maintained for a specific duration to allow the varnish to fully saturate the components. This step is crucial in achieving uniform and thorough impregnation, which is essential for optimal insulation performance.•5. Post-treatment and DryingOnce the pressure application is complete, the components are removed from the vacuum chamber and undergo post-treatment. Thismay include additional cleaning to remove any excess varnish or residue. The components are then dried to ensure that the varnish is fully cured and hardened. This drying process is typically done in a controlled environment to prevent any damage to the components or adverse effects on the curing process.•6. Quality Control and InspectionAfter the drying process, the components undergo strict quality control and inspection. This involves checking for any defects or imperfections in the impregnation, such as incomplete filling of pores or the presence of air bubbles. The electrical properties of the components are also tested to ensure they meet the required standards. Only components that pass this rigorous quality control are deemed suitable for further use in the manufacturing process.In conclusion, the vacuum pressure impregnation process is a meticulous and crucial step in the production of high-performance electrical components. It involves multiple stages, each designed to ensure optimal impregnation and insulation performance. From pre-treatment to post-treatment, each step contributes to the overall quality and reliability of the final product. By following this comprehensive process, manufacturers can produce electrical components that meet the highest standards of performance and safety.。
木材防腐真空 压力浸渍 灌使用设备操作规程
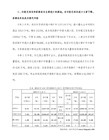
木材防腐真空压力浸渍灌使用设备操作规程木材防腐真空压力浸渍灌使用设备操作规程木材防腐真空压力浸渍灌使用设备操作规程一、我公司生产的木材防腐(真空浸渍灌)其工艺流程如下:1、先将阻烯药剂粉和水溶解均可,并把药剂装入储药灌内,用压力泵注入木材防腐真空浸渍灌内(若在重复使用药剂时,会计师达不到正常值的情况下增加补充阻燃料)。
2、按产品规格取材mdash;选材并四面刨光mdash;脱脂干燥mdash;装入料车mdash;开启罐门mdash;推动移车台与罐内接轨mdash;将料车推至罐内mdash;关闭罐门mdash;真空作业mdash;吸液mdash;加压mdash;频压mdash;卸压mdash;回液mdash;后真空mdash;卸压mdash;开启罐门mdash;(待压力卸完后)mdash;出料mdash;检验。
二、操作顺序:配置阻燃液rarr;真空rarr;浸渍rarr;加压rarr;真空干燥三、使用方法:1、满细胞法:满细胞法又叫全吸收法,字是一种使防腐、阻燃剂充满木材细胞的防腐工艺方法。
通常适用于水溶性防腐、阻燃剂,用该种方法处理木材可以是木材保留最大数量的防腐阻燃剂。
2、高低频压法:用不断重复的常压和压力周期对木材进行防腐阻燃处理的工艺方法叫高低频压发,用这种工艺法处理木材便难浸注的木材和浸材得到比满细胞法更优良的防腐阻燃效果。
通常情况下,木材的浸注深度会更深。
这是一种木材防腐阻燃效果较好的防腐阻燃工艺,推荐使用。
四、注意事项:1、阻燃液的配置浓度一定要在要求范围内,根据木材的种类和工艺要求称是阻燃剂量和计量准确水的添加量。
2、在工作之前,一定要检查各电器是否完好,各处阀门、压力表、真空表、液位计、各类泵是否正常,损害的进行更换。
3、在加热、加压过程中,要逐步加温、加压,并要注意压力变化,不得超过罐内所规定的工作压力。
产品在防腐、阻燃、染色时在常温下进行木材处理,不需要锅炉加热。
4、若用户需要把产品脱脂时需加装我公司生产的0.5T-0.4Mpa锅炉进行脱脂和烘干。
真空油浸工艺操作规程

真空油浸工艺操作规程本规程规定了真空油浸的工艺参数要求和操作顺序,适用于真空高压浸渍工艺的操作。
1、工艺参数及控制1.1预热窑的温度:自窑头至窑尾的温度依次为T1=50~100℃,T2=150~200℃,T3=250±30℃。
温度调节由引风机W1和排烟机W2的控制闸板来控制。
1.2导热油的温度:进油温度T4=280±20℃,回油温度T5为参考温度。
进油温度过高时可以用高位热油罐中的热油加入循环或打开全部热油循环系统,也可采用降低加热炉内温度的方法进行控制。
1.3罐体温度:浸渍罐内温度T6=180±20℃,当温度过高时可关闭该循环。
熔化罐内温度T7熔化沥青时为220±20℃,非熔化沥青过程为180±20℃,该温度可由关闭该罐三个热油循环来实现。
1.4浸渍最高压力:依浸渍制品要求,可设定范围为0.5~1.5MPa,靠电接点压力表B1设定相应压力来控制。
1.5回油压力:0.5MPa,由电接点压力表B2控制,设定为0.5MPa。
1.6真空度:100Pa,由真空数量仪显示。
1.7保压时间:依浸渍制品要求为0.5~4h。
1.8保真空时间:依浸渍制品要求为5~10分钟。
2、操作规程2.1预热系统:指加热炉、预热窑系统。
2.1.1点窑顺序:预热窑内推入待浸渍制品→打开热油泵使导热油在系统内循环→开引风机W1→开排烟机W2→点火。
2.1.2顶车:当窑尾为空位,并将摆渡车停于窑车位时,分别打开窑头及窑尾窑门,将制品顶入窑内,关闭前后窑门。
2.2导热油系统导热油系统共有七个循环,其中R代表进油,V代表回油。
七个循环分别为:2.2.1 R—V 主循环系统,加热炉与导热油分配器之间的循环。
2.2.2 R1—V1 浸渍罐导热油夹套内的循环。
2.2.3 R2—V2输油管道的导热油循环。
2.2.4 R3—V3回油管道的导热油循环。
2.2.5 R4—V4熔化罐内盘管的导热油循环。
真空浸漆或真空压力浸漆
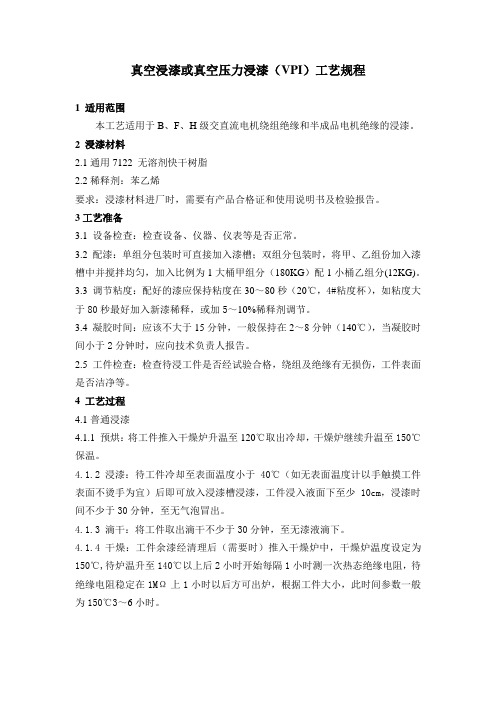
真空浸漆或真空压力浸漆(VPI)工艺规程1 适用范围本工艺适用于B、F、H级交直流电机绕组绝缘和半成品电机绝缘的浸漆。
2 浸漆材料2.1通用7122 无溶剂快干树脂2.2稀释剂:苯乙烯要求:浸漆材料进厂时,需要有产品合格证和使用说明书及检验报告。
3工艺准备3.1 设备检查:检查设备、仪器、仪表等是否正常。
3.2 配漆:单组分包装时可直接加入漆槽;双组分包装时,将甲、乙组份加入漆槽中并搅拌均匀,加入比例为1大桶甲组分(180KG)配1小桶乙组分(12KG)。
3.3 调节粘度:配好的漆应保持粘度在30~80秒(20℃,4#粘度杯),如粘度大于80秒最好加入新漆稀释,或加5~10%稀释剂调节。
3.4 凝胶时间:应该不大于15分钟,一般保持在2~8分钟(140℃),当凝胶时间小于2分钟时,应向技术负责人报告。
2.5 工件检查:检查待浸工件是否经试验合格,绕组及绝缘有无损伤,工件表面是否洁净等。
4 工艺过程4.1普通浸漆4.1.1 预烘:将工件推入干燥炉升温至120℃取出冷却,干燥炉继续升温至150℃保温。
4.1.2 浸漆:待工件冷却至表面温度小于40℃(如无表面温度计以手触摸工件表面不烫手为宜)后即可放入浸漆槽浸漆,工件浸入液面下至少10cm,浸漆时间不少于30分钟,至无气泡冒出。
4.1.3 滴干:将工件取出滴干不少于30分钟,至无漆液滴下。
4.1.4 干燥:工件余漆经清理后(需要时)推入干燥炉中,干燥炉温度设定为150℃,待炉温升至140℃以上后2小时开始每隔1小时测一次热态绝缘电阻,待绝缘电阻稳定在1MΩ上1小时以后方可出炉,根据工件大小,此时间参数一般为150℃3~6小时。
5.2 VPI浸漆工艺5.2.1预烘:将工件推入干燥炉升温至100℃~130℃,保温2~4小时,取出冷却至50℃以下进罐。
注意工件浸入液面下至少10cm。
5.2.2真空去湿5.2.2.1手动扳开(1)号压缩空气阀,在工控机上开(30)号密封圈充气阀,进行工件真空去湿。
沈阳电机厂真空压力浸渍设备操作说明书

沈阳电机厂真空压力浸渍设备操作说明书1、浸漆前准备:合上控制柜总电源,开启小空压机。
看绝缘漆是否达到浸漆所需温度,如温度低于浸漆温度则将漆加热至浸漆温度,开启罐对应的循环水阀,开启加热水泵,开启加热器对罐进行加热,直至达到工艺所需温度。
如果温度高于浸漆温度,则将漆温降至浸漆温度,开启对应的循环水泵,开启冷水泵,再启动制冷机,开始对漆进行降温,直至达到浸漆所需温度。
加热或制冷时应开启对应贮罐的搅拌电机。
需要停止加热或制冷时先关闭对应的加热器或制冷机,然后在关闭对应的热水泵或冷水泵,再关闭循环水阀。
2、罐盖操作:开启浸罐安全手阀,确定浸罐内的压力为零压,开启液压站,再开启浸罐旋松,到位后旋松自动停止,将旋松旋钮复位,开启浸罐开盖旋钮,到位后自动停止,将开盖旋钮复位,关闭液压站,吊装工件。
工件吊装完毕后,开启液压站,再开启浸罐合盖操作,待罐盖合到位后自动停止,将其复位,开启浸罐旋紧将罐盖旋紧,到位后自动停止,将旋紧按钮复位,关闭液压站,关闭安全手阀,准备浸漆。
3、抽真空操作:开启对应罐的真空阀,开启3#制冷机水泵,开启3#制冷机,开启真空机组对其进行抽真空操作,到达工艺要求的真空度后关闭罐的抽空阀,延时10秒或等到抽空阀门完全关闭后关闭真空机组,延时一段时间后关闭3#制冷机水泵,关闭3#制冷机。
进入到保真空阶段。
4、输漆操作:保真空时间到达后开启对应浸罐的积液器阀门,再开启贮罐的输漆阀,靠罐体内的压差将绝缘漆压入到浸罐内,达到要求液位后关闭贮罐输漆阀,关闭积液器阀,完成输漆。
5、加压操作:输漆结束后开启对应浸罐的加压阀对浸罐进行加压,到达工艺要求的压力后自动停止,将浸罐加压旋钮开关复位。
进入到保压阶段。
6、一次泄压操作:保压结束后,开启对应浸罐的一次泄压阀对浸罐进行泄压操作,到达一次泄压设定压力后自动停止,将一次泄压阀复位。
7、回漆操作:开启对应浸罐的积液器阀门,开启对应贮罐的回漆阀进行回漆,待漆全部回到贮罐后将回漆阀关闭,将积液器阀关闭。
真空压力浸漆罐说明书
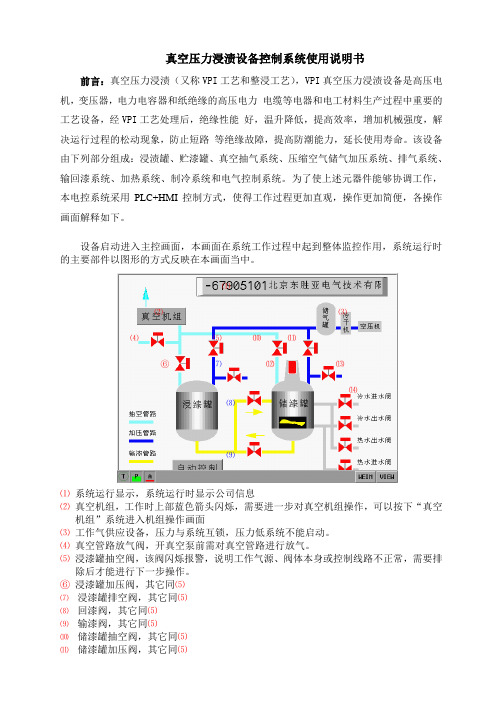
真空压力浸渍设备控制系统使用说明书前言:真空压力浸渍(又称VPI工艺和整浸工艺),VPI真空压力浸渍设备是高压电机,变压器,电力电容器和纸绝缘的高压电力电缆等电器和电工材料生产过程中重要的工艺设备,经VPI工艺处理后,绝缘性能好,温升降低,提高效率,增加机械强度,解决运行过程的松动现象,防止短路等绝缘故障,提高防潮能力,延长使用寿命。
该设备由下列部分组成:浸渍罐、贮漆罐、真空抽气系统、压缩空气储气加压系统、排气系统、输回漆系统、加热系统、制冷系统和电气控制系统。
为了使上述元器件能够协调工作,本电控系统采用PLC+HMI控制方式,使得工作过程更加直观,操作更加简便,各操作画面解释如下。
设备启动进入主控画面,本画面在系统工作过程中起到整体监控作用,系统运行时的主要部件以图形的方式反映在本画面当中。
⑴⑵⑶⑷⑸⑽⑾⑥⑺⑿⒀⒁⑻⑼⑴系统运行显示,系统运行时显示公司信息⑵真空机组,工作时上部蓝色箭头闪烁,需要进一步对真空机组操作,可以按下“真空机组”系统进入机组操作画面⑶工作气供应设备,压力与系统互锁,压力低系统不能启动。
⑷真空管路放气阀,开真空泵前需对真空管路进行放气。
⑸浸漆罐抽空阀,该阀闪烁报警,说明工作气源、阀体本身或控制线路不正常,需要排除后才能进行下一步操作。
⑥浸漆罐加压阀,其它同⑸⑺浸漆罐排空阀,其它同⑸⑻回漆阀,其它同⑸⑼输漆阀,其它同⑸⑽储漆罐抽空阀,其它同⑸⑾储漆罐加压阀,其它同⑸⑿储漆罐搅拌器,指示块闪烁说明主回路有问题⒀储漆罐排空阀,其它同⑸⒁设备连接的外围加热或制冷用的水路及控制阀门点击屏幕右下角的“VIEW”菜单栏中选择“浸漆罐”屏幕弹出如下控制画面,⑵⑴⑶⑷⑸⑥⑦⑴浸漆罐抽空阀,输漆前或正在输漆时打开该气动阀门,使工作用漆快速从储漆罐流向浸漆罐,若在规定时间内该阀状态没有切换完毕,则该阀闪烁报警,说明工作气源、阀体本身或控制线路不正常,需要排除后才能进行下一步操作。
⑵浸漆罐加压阀,回漆时打开该气动阀门,使工作用漆快速从浸漆罐流回储漆罐,其它同⑴⑶浸漆罐排空阀,回漆结束后打开该气动阀门,其它同⑴⑷罐体内部漆料液位,正常显示黄色,超限时显示红色⑸罐体内部压力大小,正常显示蓝色,超限时显示红色⑥罐体内部漆料液位和工作气压数值⑺浸漆保压时间设定,下面显示剩余时间单位分钟点击屏幕右下角的“VIEW”菜单栏中选择“储漆罐”屏幕弹出如下控制画面,⑴⑵⑶⑷⑸⑥⑦⑧⑨⑴储漆罐搅拌器,加热罐内漆料时开启搅拌器,使之升温均匀,为输漆做好前期准备工作,指示块闪烁说明主回路有问题⑵储漆罐加压阀,输漆时打开该气动阀门,使工作用漆快速从储漆罐流向浸漆罐,若在规定时间内该阀状态没有切换完毕,则该阀闪烁报警,说明工作气源、阀体本身或控制线路不正常,需要排除后才能进行下一步操作。
真空压力浸渍工艺

真空压力浸渍工艺嘿,朋友们!今天咱来聊聊真空压力浸渍工艺,这可真是个有意思的玩意儿!你想想看啊,这真空压力浸渍就好比是给材料做了一场特别的“美容护理”。
就像咱人要保养皮肤一样,让它变得更好更耐用。
在这个工艺里呀,真空就像是一个神奇的魔法,把那些讨厌的气泡啊啥的都给吸走了。
这可太重要啦!要是材料里有好多气泡,那质量能好吗?肯定不行呀!然后呢,压力又来啦,就像是给材料来了个“紧紧的拥抱”,让那些浸渍的东西能更好地渗进去,和材料融为一体。
咱平时用的好多东西可都离不开这真空压力浸渍工艺呢!比如说一些电器设备里的绝缘材料,要是没有经过好好的浸渍处理,那万一漏电啥的可咋办呀,多吓人!还有些机械零件,经过这工艺处理后,那可就更耐磨更耐用啦,能为咱服务更长时间呢!你说这工艺神奇不神奇?它就像是一个幕后英雄,虽然咱平时不太注意到它,但它却在默默地为我们的生活提供保障呢!再打个比方,这真空压力浸渍工艺就像是给材料盖房子,真空把地基打得牢牢的,没有空洞和杂质,然后压力把建筑材料紧紧地堆砌在一起,让房子坚固又可靠。
而且呀,这个工艺要求还挺高呢!操作人员得特别细心,就像个细心的大厨一样,要掌握好各种调料的比例,稍有差错可能就达不到理想的效果啦。
这可真不是随便谁都能做好的哟!咱生活中的好多好东西可都是因为有了这个工艺才变得更好用、更可靠呢!你说咱是不是得好好感谢发明这个工艺的人呀?反问咱自己,要是没有它,咱的生活会变成啥样呢?所以啊,真空压力浸渍工艺可真是个了不起的东西!它虽然不那么起眼,但却在背后默默地发挥着巨大的作用。
咱可得好好珍惜这些经过它处理的好东西,也得尊重那些从事这项工作的人呢!这就是咱今天要说的真空压力浸渍工艺,你了解了吗?原创不易,请尊重原创,谢谢!。
非包封干式变压器(OVDT)真空压力浸渍(VPI)工艺及其发展
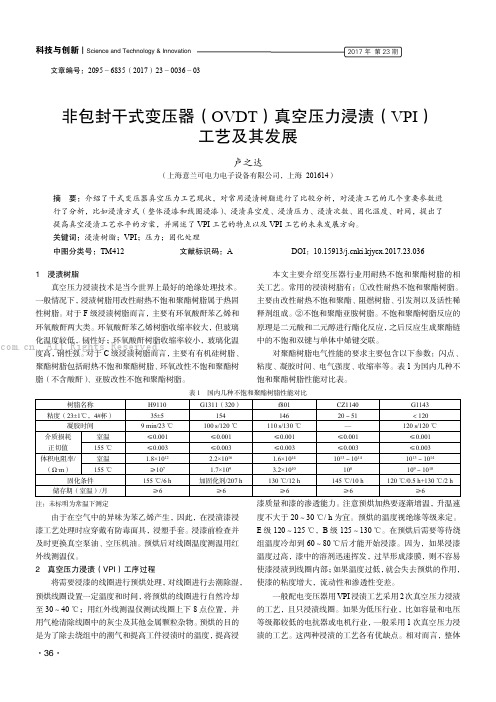
科技与创新┃Science and Technology&Innovation ·36·2017年第23期文章编号:2095-6835(2017)23-0036-03非包封干式变压器(OVDT)真空压力浸渍(VPI)工艺及其发展卢之达(上海意兰可电力电子设备有限公司,上海201614)摘要:介绍了干式变压器真空压力工艺现状,对常用浸渍树脂进行了比较分析,对浸渍工艺的几个重要参数进行了分析,比如浸渍方式(整体浸漆和线圈浸漆)、浸渍真空度、浸渍压力、浸渍次数、固化温度、时间,提出了提高真空浸渍工艺水平的方案,并阐述了VPI工艺的特点以及VPI工艺的未来发展方向。
关键词:浸渍树脂;VPI;压力;固化处理中图分类号:TM412文献标识码:A DOI:10.15913/ki.kjycx.2017.23.0361浸渍树脂真空压力浸渍技术是当今世界上最好的绝缘处理技术。
一般情况下,浸渍树脂用改性耐热不饱和聚酯树脂属于热固性树脂。
对于F级浸渍树脂而言,主要有环氧酸酐苯乙烯和环氧酸酐两大类。
环氧酸酐苯乙烯树脂收缩率较大,但玻璃化温度较低,韧性好;环氧酸酐树脂收缩率较小,玻璃化温度高,钢性强。
对于C级浸渍树脂而言,主要有有机硅树脂、聚酯树脂包括耐热不饱和聚酯树脂、环氧改性不饱和聚酯树脂(不含酸酐)、亚胺改性不饱和聚酯树脂。
本文主要介绍变压器行业用耐热不饱和聚酯树脂的相关工艺。
常用的浸渍树脂有:①改性耐热不饱和聚酯树脂。
主要由改性耐热不饱和聚酯、阻燃树脂、引发剂以及活性稀释剂组成。
②不饱和聚酯亚胺树脂。
不饱和聚酯树脂反应的原理是二元酸和二元醇进行酯化反应,之后反应生成聚酯链中的不饱和双键与单体中烯键交联。
对聚酯树脂电气性能的要求主要包含以下参数:闪点、粘度、凝胶时间、电气强度、收缩率等。
表1为国内几种不饱和聚酯树脂性能对比表。
表1国内几种不饱和聚酯树脂性能对比树脂名称H9110G1311(320)f801CZ1140G1143粘度(23±1℃,4#杯)35±515414620~51<120凝胶时间9min/23℃100s/120℃110s/130℃—120s/120℃介质损耗正切值室温≤0.001≤0.001≤0.001≤0.001≤0.001 155℃≤0.003≤0.003≤0.003≤0.003≤0.003体积电阻率/(Ω·m)室温 1.8×1012 2.2×1016 1.6×10141013~10141013~1014 155℃≥107 1.7×109 3.2×1010108109~1010固化条件155℃/6h加固化剂/207h130℃/12h145℃/10h120℃/0.5h+130℃/2h 储存期(室温)/月≥6≥6≥6≥6≥6注:未标明为常温下测定由于在空气中的异味为苯乙烯产生,因此,在浸渍漆浸漆工艺处理时应穿戴有防毒面具,浸塑手套。
真空浸渍设备的工艺技术及对应设备的改进

浸 渍 过程抽 真 空 系统配 置对 比见 图 2 。
电子元 器件 注油 加压 ( 各个浸 渍管 液压 加压 )
0
浸 渍腔体 内 排 气并下 料
各个浸 渍管 内 泄液 压并下 料
( a ) 传 统浸渍 抽 真空 系统
( b) 改 进后浸 渍抽 真空 系统
图1 改 进 后 的 浸 渍 过 程 与 传 统 浸渍 过 程 对 比
关 键词 : 真 空 ;真 空浸渍 ;浸 渍设 备
中图 分类号 : T B 7 9 文献 标识 码 : A
真空 浸渍设 备是 用 于在 电子 元器 件生 产 中的关 键设备 , 主要 是 对 电 子 元 器 件 进 行 浸 绝 缘 油 、 浸 树
2 . 1 抽真 空过 程 的技 术改 进 抽真 空过 程是 浸 渍 过 程 真 空 的 基 础 过程 , 是将 电子 元气 件 中的水 分 和空 气 排 出 , 为 注 油 加 压 浸 渍
脂、 浸 变压 器油 等 操 作 。传 统 的浸 渍设 备 主要 包 括 抽 真 空处 理 、 加热 、 注油 加压 等三 部分 过程 。现 在原
有过 程 中采用 了新 的处 理技 术 : 1 )抽 真 空处 理 中采
进行 基础 准备 。抽 真 空效果 的好 坏 直接 决定 了电子
元气 件 浸渍 生产 的 品 质 和 良品率 , 抽 真 空 的速 率 也 直接 决定 了浸渍 生产 的效 率 。现采 用 了分 子泵组 进
图 2 浸 渍 过 程 抽 真 空 系 统 配 置 对 比图
2 真空浸渍过程 中具体对应环节 的技术改进
2 . 2 加热 方式 的 改进
ห้องสมุดไป่ตู้
传 统 的真 空浸 渍设 备是 采用 了 真空压 力罐 外加
真空压力浸渍设备加热系统提升

真空压力浸渍设备加热系统提升浅析[摘要]真空压力浸渍(vpi)是当前机车牵引电机绝缘处理的先进工艺技术,随着绝缘处理新材料、新工艺的发展,对真空压力浸渍设备提出了新的要求。
本文主要介绍真空压力浸渍设备加热系统改造提升后,对绝缘漆的改善以及对产品质量提升所取得的效果。
[关键词]真空压力浸漆 vpi设备加热系统改造中图分类号:th 文献标识码:a 文章编号:1009-914x(2013)08-185-01一、引言为提高电力机车牵引电机的可靠性和安全性,对牵引电机的核心工艺技术绝缘处理提出新的要求。
绝缘处理是通过真空压力浸渍(vpi)设备来实现的,为满足工艺要求,获得良好的浸渍效果,要求绝缘漆在浸渍时流动性好,浸透能力强;在浸渍完成后要求低温保存,以延长绝缘漆的使用寿命为实现上述功能,要求真空压力浸渍(vpi)设备具有良好的加热系统,现在就设备的加热系统提升进行如下浅析。
二、加热系统设计方案加热系统是vpi设备中的重要部分,主要由加热器、水箱、管道泵、电接点压力表、温度传感器、液位传感器、电接点温度表以及控制系统组成。
1.电加热器的设计1)电加热器的设计要求加热方式:380v/50hz电加热方式,工作方式为连续工作制。
2)加热功率计算i.初始加热所需要的功率计算:功率=(c1m1△t + c2m2△t)÷ 864/h式中:c1、c2、c3分别为介质(水)、容器(钢)的比热(kcal/kg℃),c1=1kcal/kg℃,c2=0.12kcal/kg℃m1、m2、分别为介质、容器的质量(kg)△t为所需温度和初始温度之差(℃)h为初始温度加热到设定温度所需要的时间(h)p最终温度下容器的热散量(kw)ii.初始加热所需要的功率:水在60℃时的表面损失3500w/m2保温层损失(在60℃时)32w/m2容器的面积:1.8m2保温层的面积:14.4m2容器内水的加热:c1m1△t = 1×(1.2×1.5×1.5×1000)×(60-15)= 121500 kcal iii. 容器自身加热:c2m2△t= 0.12×1.2×1.5×2×1000×(60-15)= 19440 kcal平均水表面热损失:1.8m2 × 3500w/m2 × 3h × 1/2 ×864/1000 = 8164.8kcal平均保温层热损失:14.4m2 × 32w/m2 × 3h × 1/2 × 864/1000= 1194.4 kcal(考虑20%的富裕量)初始加热需要的能量:(121500 + 19440 + 8164.8+ 1194.4)×1.2= 180359 kcal/kg℃工作时需要的功率p=(c1m1△t + c2m2△t)÷ 864/h=180359÷864÷3=69.58kw考虑其他热损失选择功率为72kw。
真空(压力)连续浸渍绝缘工艺技术要求(续)
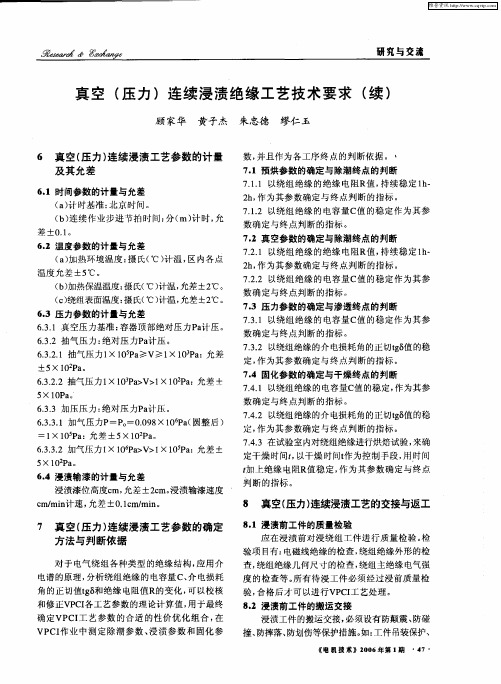
() 2 清洁浸渍罐 口和门盖动密 剂 。
() 3 排净浸渍罐 内的残余漆液 。
( ) 理浸 渍 T 艺 的现 场 和通 道 。 4清
漆罐浸渍漆的储备、 工件堆放场地的清洁、 吊装搬 运、 通道的畅通等等 。 应在设备的工艺状态完备情 况下, 对工件进行V C 工艺处理 。 PI 84浸渍中工件的工艺返工 . 为 了保证浸漆质量 良好, 必须注意在漆 尚未 完全浸没绕组工件时不可降低真空度 , 如果 由于 某种原因使得在漆还未浸没绕组工件以前就 已破 坏了真空度, 那么浸渍过程应该从头开始。 85浸溃后设备的工艺维护 . 为 了保证 下 次 浸渍 工 艺 质量 , 对浸 渍 后 设备 的工艺状态应进行如下维护 工作 :
6332 加气压 力 i OP > ... ×loaV>i 0P :允差 ± ×15a
5× 1 Pa。 02
64 浸溃输漆的计量与允差 . 浸渍漆位高度c 允差±2m。 m, c 浸渍输漆速度
c mi 计速 , m/ n 允差 ±0 1m/ n .c mi 。
8 真 空( 压力) 连续浸渍工艺的交接与返工
8 1漫渍前工件的质量检验 .
应 在 浸 渍 前对 浸 绕 组 工件 进 行 质 量 检验 。 检 验 项 目有 : 电磁线 绝缘 的检 查 , 绕组 绝 缘外形 的检
7 真空( 压力) 连续浸渍工艺参数的确定 方法与判 断依据
对于电气绕组各种类型的绝缘结构 , 应用介 电谱 的原理 , 分析绕组绝缘 的电容量c 介 电损耗 、 角的正切值t ̄I g I 绝缘 电阻值R 的变化 , 可以校核 和修正V C 各工艺参数 的理论计算值, PI 用于最终
- 1、下载文档前请自行甄别文档内容的完整性,平台不提供额外的编辑、内容补充、找答案等附加服务。
- 2、"仅部分预览"的文档,不可在线预览部分如存在完整性等问题,可反馈申请退款(可完整预览的文档不适用该条件!)。
- 3、如文档侵犯您的权益,请联系客服反馈,我们会尽快为您处理(人工客服工作时间:9:00-18:30)。
真空压力浸渍炉技术方案单位:技术部编制:刘可启审核:罗俊2013年1月目录1设备用途 (1)2现有设备优缺点及解决方案 (1)3设备主要技术参数 (2)4设备主要组成及原理 (2)4.1主机 (3)4.2气体系统 (3)4.3 真空系统 (3)4.4 冷却系统 (3)4.5 液压驱动系统 (3)4.6 电气系统 (3)4.7电加热系统 (4)4.8 平台 (4)5设备主要工作流程 (4)6设计开发可行性分析 (4)6.1 设计资质的获取 (4)6.2 制造资质的获取 (5)7设计开发流程及时间节点 (8)8设计开发人员分工 (8)9问题的解决 (9)真空压力浸渍炉技术方案1设备用途真空压力浸渍炉是为了适应纤维增强和颗粒增强复合材料的生产而研制的一种专用设备,用于金属基复合材料的研究和生产。
现我公司主要利用其进行铝基碳化硅基板的试验和制备。
2现有设备优缺点及解决方案经过一段时间的跟踪和现场了解,以及与操作者交谈,发现现有设备基本满足铝基碳化硅基板的试验和制备要求,但产能不足,有如下优缺点:2.1优点:结构紧凑、操作方便、安全可靠、工艺参数可调并数字显示。
2.2 缺点:2.2.1坩埚偏小,盛装铝容量受限,生产率不高,产能低;2.2.2送气装置为气瓶,压力下降快。
2.2.3所配增压气泵效率低,达不到铝碳化硅产品工艺要求,目前已改造用来灌装集中余气。
2.2.4 保养维护较困难,必须要全部拆开才能进行。
2.2.5 取料时炉壁余温高,有烫伤危险,可否设计坩埚自动升顶。
2.2.6 热电偶无法直接检测其温度是否准确,必须拆开后检测。
2.2.7加压气体为液氮,导致加压时冷却速度太快,导致铝液过早凝固,影响产品性能。
2.3解决方案针对上述优缺点,我们经过内部讨论和研究,认为我们新设计的真空压力浸渍炉一定要紧紧围绕铝碳化硅基板制备的工艺要求进行设计,发扬和继承现有设备的优点,解决现有设备存在的不足和缺点,方能比现有设备的性能有所提高,更适应铝碳化硅基板的生产。
经过分析讨论,有如下解决方案:2.3.1 加大容器容积以解决坩埚太小的问题;2.3.2 送气装置管路上加装集中式阀门和压力表,集中供气;2.3.3 采用大功率增压泵的提高增压效率;2.3.4 在供气管路上设计加热装置,为气体加热,降低冷却速度,延长铝液凝固时间。
2.3.5 其余缺点暂无有效的解决方案,留待后续改进。
3设备主要技术参数根据上述指导思想,我们确定了真空压力浸渍炉需要达到的主要技术参数,并与现有设备对比如下:表1 主要技术参数对比表序号主要技术参数现有设备新设计1 最高工作压力(MPa)12 122 熔化室最高工作温度(℃)1000 10003 浸渍室最高工作温度(℃)1000 10004 熔化室尺寸(mm)φ250×300 φ400×3005 浸渍室尺寸(mm)φ250×400 φ400×4006 极限真空度(Pa)≤10 ≤107 工作介质纯度(氮气、氩气)≥99.999% ≥99.999%8 控温精度(℃)±5 ±59 升温时间(h)≤2 ≤210 加料方式上装料上装料11 整机重量(吨) 5.5 1012 冷却水流量(m3/h)8.5 1013 整机安装面积(m2)25 40供电电源:AC380V,50HZ,三相五线制,~240KW;4设备主要组成及原理设备主要由主机、气体系统、真空系统、水冷系统、液压驱动系统、电气系统、电加热系统、平台等组成。
主机示意图如下:图1 设备主机示意图4.1主机主机是设备的主体,由缸体、上下塞组件、上下卡套、缸盖操纵器、升降气缸、上下隔热屏、上下发热体、热电偶、炉座等组成。
上下塞与芯筒之间由卡套连接,承受轴向载荷。
4.2气体系统气体系统作用是向缸体内提供气体;实现向缸体内运气、洗炉、加压、保压等功能。
气体系统由高压、低压两部分组成。
高压为工作介质部分,由气瓶、气动阀件、安全阀、高压管路、压力传感器、隔膜式压缩机等组成,用于压力浸渍。
高压部分设有压力数字显示、压力指针显示两种方式和超压报警、超压自动卸压及爆破阀超压爆破卸压功能,以实现压力的自动控制和设备的安全保护。
低压为控制气路部分,有气源、减压阀、电磁阀组、气缸等组成,用于实现自动卸荷、坩锅升降等功能。
4.3 真空系统真空系统由真空泵、罗茨泵、真空管路、真空阀、真空特规管等组成。
真空系统的作用是在加热前或加热过程中对加热炉进行抽真空,以实现炉内清洗和真空熔化、真空冶炼等目的。
4.4 冷却系统冷却系统由进水阀、流量监控器、温度传感器、连接水管、水箱组成,用于对缸体、上塞、下塞、电极、汽缸、隔膜式压缩机等部位进行冷却。
电加热前冷却水总流量必须在规定范围内,否则设备将报警并不能正常工作。
冷却水压应在0.2~0.4Mpa范围内。
冷却水从总进水口进入,经总进水阀、流量监控器、连接管路,进入各冷却部位后,再经出水阀、出水管汇入水箱内排出。
在冷却部位的出水口端装有温度传感器用于监测出水口的水温。
当总进水流量不足或各重要部位的冷却水温度超过上限(40℃)时,设备自动声光报警;温度超过极限(45℃)时设备自动声光报警并自动停止炉内电加热。
4.5 液压驱动系统液压驱动系统由液压站和管路等组成。
液压站的主要功能是实现上塞的自动提升、转位、下降等辅助动作设置的。
4.6 电气系统电气系统采用西门子S7系列可编程控制器(简称PLC)实现温度、压力的过程控制和逻辑控制,OP77B操作员面板实现温度、压力、报警等过程显示和温度-时间曲线的参数设定。
4.6.1 电气系统组成电气系统由以下几部分组成:电源柜、控制柜、分线盒、外部传感器。
电源柜主要是电源控制部分、各电机主控元件的装配柜。
控制柜主要装有PLC控制系统、按钮、旋钮、指示灯、OP77B操作员面板、记录仪、真空计及加热系统主控元件。
分线盒作用是连接执行元件和外部传感器元件。
主要有液压站分线盒、真空系统分线盒和热电偶分线盒三个分线盒。
外部传感器分别安装在不同的部件上,用来测试设备工作情况和准确位置。
主要有如下三种传感器:A.热电偶:检测设备炉内温度的传感器。
B.压力传感器:是缸内压力显示、控制的主要元件。
C.行程开关:检测机械动作形成是否到位的元件,发讯须及时正确。
4.7电加热系统电加热系统由两台变压器、安全围栏、铜排和电缆等组成,主要功能是向主机的上下室的发热体输入大功率电流。
4.8 平台操作平台,为操作者提供方便的操作空间。
5设备主要工作流程根据铝碳化硅基板制备工艺,目前设备主要工作流程如下:开机检查(水、电、气)--------拔出卡销、旋转卡套松开--------上塞提升、插入卡销----------洗炉--------抽真空----------加热--------停热---------------取上、中隔热垫-------(坩埚上升)------装铝--------(坩埚下降)--------放中隔热垫------放模具------放上隔热垫--------绝缘检查--------上塞下降-------旋转卡套锁紧-坩埚上升------加压-------保压------卸压------出炉------停机(关气、电、水)设备需要具备的保护功能如下:超压保护,冷却水温度、流量保护,炉温保护,行程保护,控制气源压力保护,短路保护,失电保护。
6设计开发可行性分析真空压力浸渍炉属高温压力容器,其设计、制造均需具备相关资质,需向国家质量监督检验检疫总局申请《中华人民共和国特种设备设计许可证》和《中华人民共和国特种设备制造许可证》,根据相关法律法规要求,真空压力浸渍炉属于第二类压力容器,必须要取得C级压力容器设计许可证和A2级压力容器制造许可证。
6.1 设计资质的获取6.1.1 C级压力容器设计许可证的办理需向国家质检总局递交申请。
6.1.2 C级设计单位必须具备以下条件(仅列不满足项):6.1.2.1有健全的质量保证体系和程序性文件及其设计技术规定;6.1.2.2有与设计范围相适应的法规、安全技术规范、标准;6.1.2.3 C级压力容器设计单位专职设计人员总数一般不少于10名,设计审批人员不少于2名。
6.1.2.4相应审批、审核人员必须经压力容器设计审批人员专业考核合格并取得相关证书。
6.2 制造资质的获取6.2.1 A2级压力容器制造许可证的办理需向国家质检总局递交申请。
6.2.2 A2制造单位必须具备以下条件(仅列不满足项):6.2.2.1 有与所制造产品相适应的耐压试验和气密试验专用场地;6.2.2.2 有满足检验与试验设备和器材存放要求的专用场所,制造单位自行进行无损检测的,应当具有与所制造产品相适应的检测场所、射线底片冲洗与评定专用场所;6.2.2.3制造单位应当有满足压力容器产品制造各方面的人员,并且与其签订劳动合同,经过专门的岗位培训与考核。
6.2.2.4制造单位应当有满足压力容器产品制造要求的具备相关专业知识、有一定工作经历和能力的下列质量保证体系责任人员:(一)质量保证工程师;(二)设计、工艺及标准化责任人;(三)材料和热处理责任人;(四)焊接责任人;(五)无损检测和理化检验责任人;(六)产品检验责任人;(七)设备和计量责任人。
质量保证工程师应当有从事压力容器制造检验或者质量管理五年以上的工作经历,其他责任人应当有从事所负责专业三年以上的工作经历,并且至少具有表2所列理工科相关专业的学历或者技术职称,A1、A3和C级制造单位的质量保证工程师、设计和焊接责任人应当同时具有本科及以上学历和工程师及以上的技术职称,无损检测责任人还应当满足至少具有RT和UT中级人员各3人•项,无损检测责任人员具有RT或者UT中级资格的要求。
根据压力容器产品生产的需要,一个责任人岗位可以由两个及以上的人员担任,但应当明确每个人的职责;必要时,一个人员也可以兼任两个责任人岗位。
各责任人应当熟悉任职岗位的工作任务和要求,经过专门的培训与考核,能够履行岗位职责,工作表现和结果符合有关法规标准和制造单位质量体系文件规定的要求。
表2 质量保证体系责任人员学历与技术职称6.2.2.5制造单位应当具有满足压力容器产品制造需要的理工科大专以上学历或者助理工程师以上职称或者高级技师的专业技术人员。
各级别制造单位技术人员与从事压力容器制造的职工比例和数量应当满足表3的要求。
表3 专业技术人员比例与数量6.2.2.6各级别制造单位中,制造焊接压力容器的制造单位,应当具有满足制造需要的,并且具备相应资格条件的持证焊工。
焊工人数和持证项目应当满足以下要求:A1级、A2级、A3级和C级许可制造单位,具有不少于10名持证焊工,并且具备至少4项合格项目;6.2.3 A2级压力容器制造单位,应当具有额定能力不小于30mm的卷板机和起重能力不小于20t的起重机。