铸铁件通用检验标准
铸件质量检查标准

一、目的:为了确保外协标准铸件、成品铸件质量符合工艺、技术要求,为了满足产品特性,结合相关文件特制定本标准。
二、适用范围:本办法适用于我公司产品外协、采购、装配过程中、全部铸件质量检查标准。
三、检查标准:3.1、铸件结构要符合设计要求或加工工艺要求。
无特殊要求时按铸件通用标准执行。
通用标准等级分为:交货验收技术条件标准;铸件质量分等通则(合格品、一等品、优等品)材质、检验方法;工艺和材料规格等一般性规则。
3.2、铸件成品检验。
铸件成品检验包括:相关技术条件的检验、表面质量检验、几何尺寸检验等项内容。
①相关技术条件的检验。
包括铸件化学成分、机械性能等检验内容。
机械性能检验和金相及化学成分检验等技术条件的检验,均必须按相关国家标准执行检验(此处略)。
②表面质量检验。
机械加工生产一线人员在工艺过程中对铸造毛坯的检查主要是对其外观铸造缺陷(如有无沙眼、沙孔、疏松、有无浇不足、铸造裂纹等)的检验;以及毛坯加工余量是否满足加工要求的检验。
表3-1铸件外观质量检验项目(GB6060.1—1985)表3-2 铸件表面粗糙度(R a 值μm)(GB6414—1986)③铸件成品几何尺寸检验。
主要一种是采用划线法检查毛坯的加工余量是否足够。
另一种方法是:用毛坯的参考基准面(也称工艺基准面)作为毛坯的检验基准面的相对测量法(需要测量相对基准面的尺寸及进行简单换算)。
表3-3 铸件尺寸公差数值(mm)(GB6414—1986)注:铸件基本尺寸≤10mm 时,其公差等级提高3 级;大于10mm 至等于15mm 时,其公差等级提高2级;大于16mm 至25mm 时,其公差等级提高1 级。
附表:铸件质量检验与缺陷处理实用技术。
铸件质量检验标准

铸件质量检验标准铸件是一种常见的生产工艺,广泛用于各个行业和领域。
铸件质量的好坏直接影响产品的性能和可靠性,因此进行铸件质量检验至关重要。
本文将介绍铸件质量检验的标准和方法。
一、铸件质量检验的重要性铸件质量检验的目的是确保铸件的尺寸精度、表面质量和机械性能达到设计要求。
一方面,铸件的尺寸精度和表面质量直接影响产品的装配和使用;另一方面,对于承受重载或高温等极端工况的铸件来说,其机械性能的好坏关系到产品的安全可靠性。
二、铸件质量检验的标准铸件质量检验的标准包括国家标准、行业标准和企业自身标准。
国家标准是根据相关法律法规制定的,具有强制性,是衡量铸件质量的重要依据。
行业标准是在国家标准的基础上,由行业协会或行业组织制定的,作为行业内铸件质量的参考指南。
企业自身标准是企业根据生产情况和需求制定的,用于规范和管理内部质量控制。
在铸件质量检验中,常用的国家标准有《铸造铁件技术条件》、《铸铝合金件技术条件》等,而行业标准包括《汽车铝合金压铸铸件技术规范》、《船用铸铁件技术条件》等。
企业自身标准则根据企业具体的生产工艺和要求制定,例如《XX公司铸件质量检验标准》。
三、铸件质量检验的方法铸件质量检验的方法主要包括外观检查、尺寸检测和性能测试。
1. 外观检查外观检查是铸件质量检验中最简单直观的方法。
通过肉眼观察铸件的外观,检查是否有裂纹、砂眼、气孔、夹渣等缺陷。
外观检查可以用目视检查或借助放大镜进行观察。
2. 尺寸检测尺寸检测是铸件质量检验中最常见的方法。
主要是测量铸件的外形尺寸、孔径尺寸和壁厚尺寸等。
常用的尺寸测量工具有游标卡尺、内径卡尺、外径卡尺、深度尺等。
尺寸检测可以帮助判断铸件是否满足设计要求。
3. 性能测试性能测试是铸件质量检验中最关键的方法,主要包括力学性能测试、化学成分分析和金相组织分析。
力学性能测试主要是测试铸件的拉伸、弯曲、冲击等力学性能。
化学成分分析可以确定铸件的材料成分是否符合要求。
金相组织分析可以观察铸件的金相组织结构,评估其机械性能。
铸件外观检验规范标准

铸件外观检验规范一、范围本规范适用于本厂产品的精铸件、砂型铸件的外观检验。
本规范规定了精铸件、砂型铸件的外观检验要求和详尽查收准则。
二、铸件外观弊端名称及分类种类序号名称特征1气孔2缩孔孔3缩松眼4渣眼5砂眼6铁豆裂7热裂8冷裂纹9温裂10粘砂表面11结疤缺12夹砂在铸件内部、表面或近于表面处有大小不等的圆滑孔眼。
形状有圆的、长的及不规则的、有单个的,也有齐聚成片的。
颜色为白色或带一层暗色,有时覆有一层氧化皮。
在铸件厚断面内部,两交界面的内部及厚断面和厚断面交接处的内部或表面,形状不规则,孔内粗糙不平,晶粒粗大。
在铸件内部细小而不连结的缩孔,齐聚在一处或多处,晶粒粗大,各晶粒间存在很小的孔眼,水压试验时渗水。
在铸件内部或表面形状不规则的孔眼。
孔眼不圆滑,里面全部或部分充塞着渣。
在铸件内部或表面有充塞着型砂的孔眼。
在铸件内部或表面有包含金属小珠的孔眼,常发生在铸铁件上。
在铸件上有穿透或不穿透的裂纹(主若是波折形的),开裂处金属表皮氧化。
在铸件上有穿透或不穿透的裂纹(主若是直的),开裂处金属表皮未氧化。
在铸件上有穿透或不穿透的裂纹。
开裂处金属表皮氧化。
由于气割、焊接或热办理不当所引起。
在铸件表面上、全部或部分覆盖着金属(或金属氧化物)与砂(或涂料)的混杂物(或化合物),或一层烧结的型砂,致使铸件表面粗糙。
在铸件表面上,有金属夹杂或包含型砂或渣的片状或瘤状物。
在铸件表面上,有一层金属瘤状或片状物。
在金属瘤片和铸件之间夹有一层型砂。
陷13冷隔形14多肉在铸件上有一种未圆满交融的缝隙或洼坑,其交接边缘是圆滑的。
铸件上有形状不规则的毛刺、披缝或凸出部分。
状15浇不足缺16变形由于金属液未圆满充满型腔而产生的铸件缺肉。
由缩短应力引起的铸件外形和尺寸与图样不符。
陷17料口毛刺由打磨料口时产生的毛刺。
三、检验要求铸件不得有明显孔眼(气孔、缩孔、缩松、渣眼、砂眼、铁豆),裂纹(热裂、冷裂、温裂),表面弊端(粘砂、结疤、夹砂、冷隔),形状弊端(多肉、浇不足、变形、料口毛刺)等严重影响产品的外观和强度弊端。
铸件的检验项目...
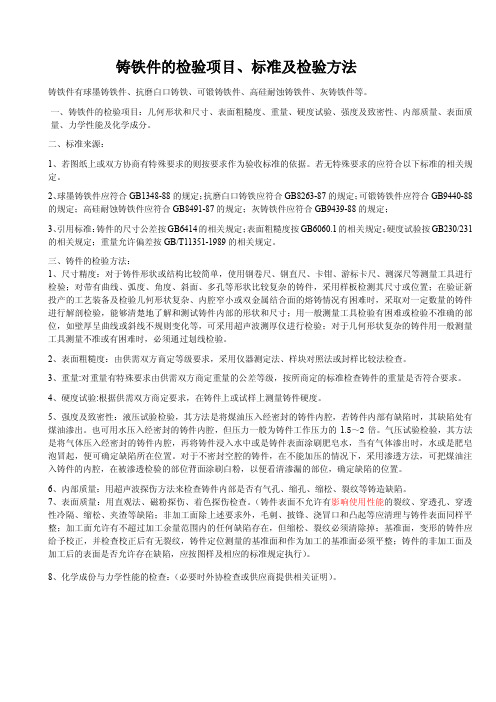
铸铁件的检验项目、标准及检验方法铸铁件有球墨铸铁件、抗磨白口铸铁、可锻铸铁件、高硅耐蚀铸铁件、灰铸铁件等。
一、铸铁件的检验项目:几何形状和尺寸、表面粗糙度、重量、硬度试验、强度及致密性、内部质量、表面质量、力学性能及化学成分。
二、标准来源:1、若图纸上或双方协商有特殊要求的则按要求作为验收标准的依据。
若无特殊要求的应符合以下标准的相关规定。
2、球墨铸铁件应符合GB1348-88的规定;抗磨白口铸铁应符合GB8263-87的规定;可锻铸铁件应符合GB9440-88的规定;高硅耐蚀铸铁件应符合GB8491-87的规定;灰铸铁件应符合GB9439-88的规定;3、引用标准:铸件的尺寸公差按GB6414的相关规定;表面粗糙度按GB6060.1的相关规定;硬度试验按GB230/231的相关规定;重量允许偏差按GB/T11351-1989的相关规定。
三、铸件的检验方法:1、尺寸精度:对于铸件形状或结构比较简单,使用钢卷尺、钢直尺、卡钳、游标卡尺、测深尺等测量工具进行检验;对带有曲线、弧度、角度、斜面、多孔等形状比较复杂的铸件,采用样板检测其尺寸或位置;在验证新投产的工艺装备及检验几何形状复杂、内腔窄小或双金属结合面的熔铸情况有困难时,采取对一定数量的铸件进行解剖检验,能够清楚地了解和测试铸件内部的形状和尺寸;用一般测量工具检验有困难或检验不准确的部位,如壁厚呈曲线或斜线不规则变化等,可采用超声波测厚仪进行检验;对于几何形状复杂的铸件用一般测量工具测量不准或有困难时,必须通过划线检验。
2、表面粗糙度:由供需双方商定等级要求,采用仪器测定法、样块对照法或封样比较法检查。
3、重量:对重量有特殊要求由供需双方商定重量的公差等级,按所商定的标准检查铸件的重量是否符合要求。
4、硬度试验:根据供需双方商定要求,在铸件上或试样上测量铸件硬度。
5、强度及致密性:液压试验检验,其方法是将煤油压入经密封的铸件内腔,若铸件内部有缺陷时,其缺陷处有煤油渗出。
铸件质量检验标准

铸件质量检验标准铸件质量检验标准铸件质量检验标准铸件质量检验标准铸件质量检验标准⼀、⽬的:为了确保外协⽑坯铸件、采购⽑坯铸件、标准铸件、成品铸件质量符合⼯艺、技术要求,为了满⾜产品特性,结合相关⽂件特制定本标准。
⼆、适⽤范围:本标准适⽤于我公司产品外协、采购、⽣产、装配过程中,全部铸件质量检验标准。
三、检验标准:3.1 铸件结构要符合设计要求或加⼯⼯艺要求。
⽆特殊要求时按铸件通⽤标准执⾏。
通⽤标准等级分为:交货验收技术条件标准;铸件质量分等通则(合格品、⼀等品、优等品)材质、检验⽅法;⼯艺和材料规格等⼀般性规则。
3.2 铸件成品检验。
铸件成品检验包括:铸件的内部质量检验和外观质量检验。
铸件内部质量检验包括:化学成分、机械性能等。
铸件外观质量检验包括:表⾯质量、粗糙度、铸件尺⼨、重量等。
3.2.1 铸件内部质量检验①化学成分:表1牌号标准化学成分C Si Mn Cr P S Ni Cu MoWCAASTMA2160.25 0.60 0.70 0.50 0.04 0.045 0.50 0.30 0.20WCBASTMA2160.30 0.60 1.00 0.50 0.04 0.045 0.50 0.30 0.20WCCASTMA2160.25 0.60 1.20 0.50 0.04 0.045 0.50 0.30 0.20LCBASTMA3520.30 0.6 1.00 0.5 0.04 0.045 0.05 0.3 0.20LC1ASTMA3520.25 0.6 0.5~0.8 — 0.04 0.045 — — 0.45~0.65 LC2ASTMA3520.25 0.6 0.5~0.8 — 0.04 0.045 2~3 — —LC3ASTMA3520.15 0.6 0.5~0.8 — 0.04 0.045 3~4 — —WC6ASTMA217M0.05~0.201.50.04 0.045 0.5 0.5 0.45~0.65WC9ASTMA217M0.05~0.180.600.4~0.72.0~2.750.04 0.045 0.5 0.5 0.90~1.20C5ASTMA217M0.20 0.750.4~0.74.0~6.50.04 0.045 0.5 0.5 0.45~0.65CF3ASTMA3510.03 2.0 1.5 17~21 0.04 0.04 8~12 0.5CF8ASTMA3510.08 2.0 1.5 18~21 0.04 0.04 8~11 0.5CF3MASTMA3510.03 1.5 1.5 17~21 0.04 0.04 9~13 2~3CF8MASTMA3510.08 1.5 1.5 18~21 0.04 0.04 9~12 2~3CG3MASTMA3510.03 1.0 2.0 18~20 0.035 0.03 11~15 3~4CG8MASTMA3510.08 1.0 2.0 18~20 0.035 0.03 11~15 3~4②机械性能表2牌号标准⼒学性能σb(MPa) σs(MPa) δ(%) ψ(%)WCA ASTM A216 415~585 205 24 35WCB ASTM A216 485~655 250 22 35WCC ASTM A216 485~655 275 22 35 LCB ASTM A352 450~620 240 24 35 LC1 ASTM A352 450~620 240 24 35LC2 ASTM A352 485~655 275 24 35LC3 ASTM A352 485~655 275 24 35WC6 ASTM A217M 485~655 275 20 35CF3M ASTM A351 485 205 30CF8M ASTM A351 485 205 30CG3M ASTM A351 480 177 40CG8M ASTM A351 520 205 403.2.2 铸件外观质量检验①表⾯质量检验。
资料│球铁铸件验收标准

资料│球铁铸件验收标准一、引用标准GB9441-88 球墨铸铁金相检验GB6060.1-85 表面粗糙度比较样块铸造表面 GB321-81 硬度试验二、技术要求三、机械性能机械性能为铸态毛坯本体试块测试值。
1、金相组织按GB9441-88《球墨铸铁金相检验》2、石墨铸件毛坯本体的球化率在60%以上,球化级别80%为1-3级,最差部位不低于5级,球径为5-7级。
3、基体(参考)铸件本体的基础组织为:铁素体80%以上,碳化物含量小于2%。
4、几何形状与尺寸铸件应符合相应的毛坯图尺寸规定。
铸件错型≤0.5mm,砂芯歪斜量≤0.8mm。
5、表面质量①铸件毛坯表面应无粘砂、氧化皮等缺陷,铸件毛坯表面的浇冒口、出气孔、多肉、飞边、毛刺等清除干净。
②铸件毛坯不允许有裂纹、缩孔、疏松、冷隔等影响使用性能的铸造缺陷。
③铸造毛坯非加工表面粗糙度R a≤100粗糙度评定按GB6060.1-85的规定进行。
④铸造毛坯不允许有锈蚀。
⑤铸件外表气孔和渣孔加工部位:直径≤Φ3mm,最大深度≤1.5mm,Φ2mm以上气孔数量每侧面不多于4个,Φ2mm以下气孔数量每侧面不多于7个。
非加工部位:直径≤Φ2mm,最大深度≤1.5mm,Φ2mm以上气孔数量不多于2个,Φ2mm以下气孔数量不多于5个。
6、铸件上的缺陷不允许修补。
7、批次的标识铸件毛坯必须在其本体的表面铸出永久性炉次标志即炉号。
炉号用六位组成。
第一位表示年号,取年号尾数,第二、三位表示月号,第四、五位为H号,第六位为流水号(当一炉铁水分作多包球化浇注时)× ×× ×× ×年号尾数月号日号流水号四、检验方法1、在提供最处样件时,铸件必须经解剖检测,X射线检测或Y射线检测无缩孔、缩松、裂纹等缺陷;在正常生产时,为确保质量稳定,要定期进行上述方式检测。
并且抽1‰铸件进行解剖检测。
生产设备改变、材料改变、更换模具、更改工艺或更换操作者时,铸件必须经以上解剖与检测。
铸铁件检验规程
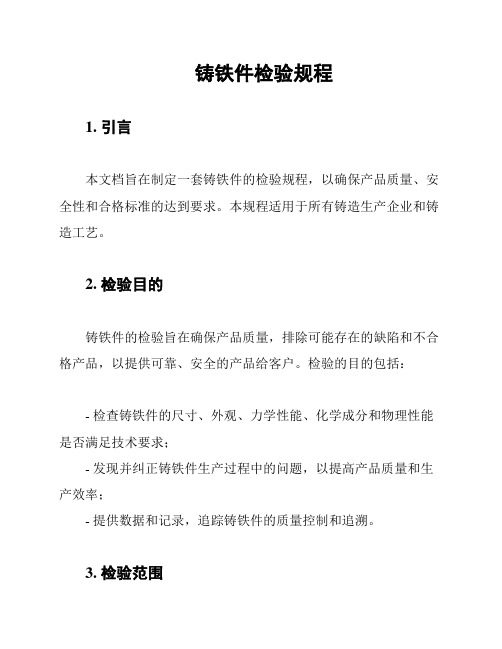
铸铁件检验规程1. 引言本文档旨在制定一套铸铁件的检验规程,以确保产品质量、安全性和合格标准的达到要求。
本规程适用于所有铸造生产企业和铸造工艺。
2. 检验目的铸铁件的检验旨在确保产品质量,排除可能存在的缺陷和不合格产品,以提供可靠、安全的产品给客户。
检验的目的包括:- 检查铸铁件的尺寸、外观、力学性能、化学成分和物理性能是否满足技术要求;- 发现并纠正铸铁件生产过程中的问题,以提高产品质量和生产效率;- 提供数据和记录,追踪铸铁件的质量控制和追溯。
3. 检验范围本检验规程适用于所有铸铁件的生产过程,包括原材料检验、工艺检验和成品检验。
检验内容包括但不限于以下方面:- 质量管理:包括铸造过程控制、温度控制、材料配比、熔炼过程控制等;- 外观检查:包括表面质量、外形尺寸、表面光洁度等;- 尺寸检验:包括尺寸精度、平行度、垂直度等;- 力学性能检验:包括强度、硬度、抗拉性能等;- 化学成分检验:包括成分分析、含碳量、含硅量等;- 物理性能检验:包括热处理性能、热膨胀系数等。
4. 检验方法本规程采用以下检验方法来进行铸铁件的检验:- 目视检查:通过肉眼观察,对铸铁件的外观质量进行检查;- 量具检测:使用合适的量具进行尺寸测量,确保尺寸的准确性;- 超声波检测:利用超声波技术对铸铁件进行探伤检测,发现内部缺陷;- 化学分析:使用化学分析仪器对铸铁件的化学成分进行检验;- 力学性能测试:通过拉伸试验机等仪器进行力学性能的测试。
5. 检验记录和报告每次铸铁件的检验都应有相应的检验记录和报告。
检验记录应包含以下内容:- 产品信息:包括产品名称、编号、规格等;- 检验项:包括检验内容、检验方法、检验数据等;- 检验结果:包括合格、不合格等;- 接收/拒收判定:根据检验结果,确定铸铁件是否符合要求;- 签名和日期:对检验人员进行记录。
检验报告应根据需要,提供检验结果的详细信息,记录每次检验的结果和趋势,以便于质量控制和问题追溯。
铸件外观质量检验规范
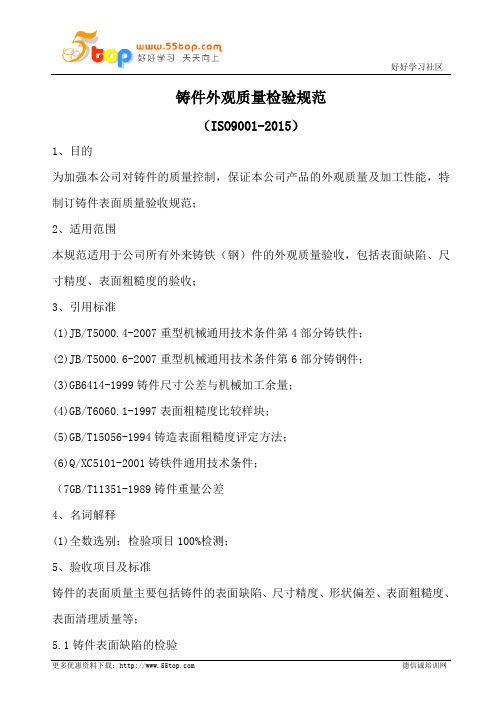
铸件外观质量检验规范(ISO9001-2015)1、目的为加强本公司对铸件的质量控制,保证本公司产品的外观质量及加工性能,特制订铸件表面质量验收规范;2、适用范围本规范适用于公司所有外来铸铁(钢)件的外观质量验收,包括表面缺陷、尺寸精度、表面粗糙度的验收;3、引用标准(1)JB/T5000.4-2007重型机械通用技术条件第4部分铸铁件;(2)JB/T5000.6-2007重型机械通用技术条件第6部分铸钢件;(3)GB6414-1999铸件尺寸公差与机械加工余量;(4)GB/T6060.1-1997表面粗糙度比较样块;(5)GB/T15056-1994铸造表面粗糙度评定方法;(6)Q/XC5101-2001铸铁件通用技术条件;(7GB/T11351-1989铸件重量公差4、名词解释(1)全数选别:检验项目100%检测;5、验收项目及标准铸件的表面质量主要包括铸件的表面缺陷、尺寸精度、形状偏差、表面粗糙度、表面清理质量等;5.1铸件表面缺陷的检验5.1.1表面缺陷检验的一般要求(1)铸件非加工表面上的浇冒口必须清理得与铸件表面同样平整,加工面上的浇冒口残留量应符合技术要求,若无要求,则按表8执行;(2)在铸件上不允许有裂纹、通孔、穿透性的冷隔和穿透性的缩松、夹渣等机械加工不能去除的缺陷;(3)铸件非加工表面的毛刺、披缝、型砂、砂芯等应清理干净;(4)铸件一般待加工表面,允许有不超过加工余量范围内的任何缺陷存在;重要加工面允许有不超过加工余量2/3的缺陷存在,但裂纹缺陷应予清除;加工后的表面允许存在直径*长度*深度小于等于2*2*2的非连片孔洞的铸造缺陷;(5)作为加工基准面(孔)和测量基准的铸件表面,平整度小于等于2.0毫米、粗糙度Ra50以内;(6)铸件表面气孔、砂眼、夹渣面积不大,但比较分散或者有连片麻点的表面不予接收;(7)除技术要求特别注明的铸件外,对于表面有气孔、缩孔、砂眼等缺陷的铸钢件允许补焊,但铸铁件未经允许不得焊补(铸铁件实行一案一判的原则)但补焊面积不允许超过铸件面积的10%,焊接质量应符合JB/T5000.7-2007标准要求,补焊后必须退火、机械性能达到图纸要求,且不得有渗漏及影响外观的缺陷;5.1.2铸件外观质量等级缺陷项目等级A B C飞边不允许飞边高度≤1.5毫米允许不易于伤手的飞边毛刺不允许允许不易于伤手的毛刺允许不易伤手的毛刺孔眼气孔 100cm 2面积内允许直径不大于φ2mm 深度不超过壁厚1/4的孔眼2个,两处距离>60mm ;整个铸件不超过4个100cm 2面积内允许直径不大于φ3mm 深度不超过壁厚1/3的孔眼2处,两处距离>60mm ;整个铸件不超过8个不致于影响强度,其余不做要求 针孔 渣眼 缩孔 不致于影响强度裂纹 不允许 不允许不允许 冷隔 沟槽 夹砂结疤 不允许 100cm 2面积内允许面积不超过8cm 2的缺陷2处;整个铸件不超过4处不致于影响强度 皱皮 不允许 不明显引人注意缩陷不允许不允许 不允许缺肉1、一般零部件采用B 级精度,在检查过程中,如有一个或多个项目超出B 级精度要求的零部件均判定为不合格;2、影响到零部件安全、性能的部位,外观质量采用A 级精度,如果有一个或多个项目超出规定级精度要求的零部件均判定为不合格;5.2铸件尺寸的检验 5.2.1铸件毛坯尺寸公差铸件尺寸公差应按毛坯图或技术条件规定的尺寸公差等级执行,当技术文件未规定尺寸公差时,则应以GB6414为依据,并按照下表选定公差值(粗线框内为推荐使用公差等级);毛坯铸件基本尺寸(mm )尺寸公差等级CT12CT13 CT14 CT15 CT16 ≤10~16 4.4 --- --- --- --- >16~25 4.6 6 8 10 12 >25~40 5.0 7 9 11 14 >40~63 5.6 8 10 12 16 >63~100 6 9 11 14 18 >100~160 7 10 12 16 20 >160~250 8 11 14 18 22 >250~400912162025>400~630 10 14 18 22 28 >630~1000 11 16 20 25 32 >1000~1600 13 18 23 29 37 >1600~2500 15 21 26 33 42 >25004000 17 24 30 38 49 >4000~6300 20 28 35 44 56 >6300~100002332405064注:1、毛坯铸件基本尺寸是指机械加工前毛坯铸件的尺寸,包括加工余量和起模斜度; 2、毛坯基本尺寸按铸件最大尺寸选取,该铸件较小尺寸公差等级与最大尺寸公差等级相同;3、壁厚采用低一级的公差等级;4、公差带应对称于毛坯铸件基本尺寸配置,例:基本尺寸30mm ,CT13公差值为±7mm ;如有特殊要求非对称式配置时,应在技术要求中单独列出公差范围;5.2.2铸件分型面处最大错型值应不得超过表2所示公差值,当需进一步限制错型量时,应从表中选取;公差等级CT 错型值(mm )11~13 1.5 14~162.55.2.3铸件加工余量应符合表的规定,有特殊要求的表面应在技术要求中单独标注加工余量;最大轮廓尺寸加工余量一个面顶面加量≤30 4 2>30~50 5 >50~180 6 >180~315 7 >315~500 8 >500~800 103>800~1250 12 >1250~1600 144>1600~250016>2500~3150 18>3150~4000 205>4000~6300 25>6300~10000 30 7注:1、属于该铸件的较小尺寸的加工余量与最大轮廓尺寸的加工余量相同;2、此表加工余量仅指一个面的加工余量,对于柱面和两面加工的铸件,铸件轮廓尺寸应为最终机械加工后成品尺寸与两倍加工余量之和;5.3表面粗糙度检测表面粗糙度总体检测原则依据图纸要求,当图纸无要求是执行国标GB/T15056;5.3.1一般情况下,表面粗糙度要求Ra50,铸件难以清理的部位,局部允许Ra100,待加工表面允许降低1级;5.3.2.使用面积法作为验收依据面积法常用的比较样块评定铸件表面粗糙度;方法如下:(1)铸造表面粗糙度比较样块应符合GB6060.1-1997标准;(2)按照国标BWZ001-88评定铸件表面粗糙度的等级;(3)铸件的浇道、冒口、修补的残余表面及铸造表面缺陷(如粘砂、结疤等)不列为被检表面;(4)以铸造表面粗糙度比较样块为对照标准,对被检铸件的铸造表面用视觉或触觉的方法进行对比;(5)用样块对比时,应选用适于铸造合金材料和工艺方法的样块进行对比;(6)被检的铸造表面必须清理干净,样块表面和被检表面均不得有锈蚀处;(7)用样块对比时,砂型铸造表面被检点数应符合表的规定;特种铸造表面被检点数应按表8的规定加倍;被检点应平均分布,每点的被检面积不得小于与之对比面的面积;被检铸造表面面积(cm2)<200 200~1000 100~10000 >10000被检点数(个) 不少于2 每200cm2不少于1 每1000cm2不少于1不少于40 (8)当被检铸造表面的粗糙度介于比较样块两级参数值之间者,所确定的被检铸造表面的粗糙度等级为粗的一级;(9)对被检铸造表面,以其80%的表面所达到的最粗表面粗糙度等级,为该铸造表面粗糙度等级;5.3.3铸件表面清理检测5.3.1铸件几何形状必须完整,非加工面上的清理损伤不应大于该处的尺寸偏差,加工面上的损伤不应大于该处加工余量的1/2;5.3.2允许铸件表面有少量的局部低凹或打磨痕迹,在直径不大于8mm,并能保证铸件规定的最小的壁厚;5.3.3为去除铸造缺陷而打磨后的铸件表面粗糙度应与一般铸件表面粗糙度基本一致;5.3.4除特殊情况外,铸件表面允许残留的浇冒口、毛刺,多肉残余量应按表8的要求进行;类别非加工面凸出高度(mm)加工面凸出高度(mm) 外表面非外表面浇冒口残余量-0.5~0.5 <2 <2~4毛刺残余量0 <2 <1~2多肉残余量<1 <2 <25.3.5铸件表面须经过防锈处理,保证在铸件进入面加工时不得有任何的锈蚀;5.3.6铸件表面如有油漆要求的,必须按有关涂装规定执行;5.4铸件重量检测5.4.1对于没有特殊要求的铸件,重量偏差可以不作为验收依据;如果技术条件有要求,供需双方协商后,铸件的重量偏差也应作为验收依据,一般应符合表的规定;公称重量(Kg) ≤200>200~500>500~1000>1000~5000>5000~10000>10000~30000>30000~50000>50000铸件重量上偏差(%)8 7.5 7 6.5 6 5.5 5 4.5。
铸件检验标准
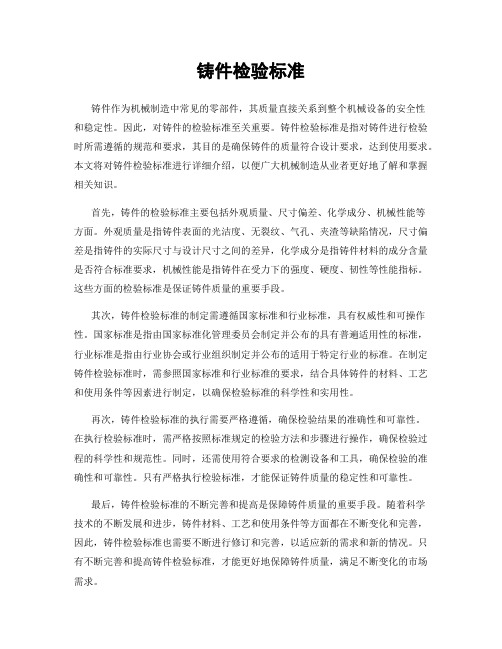
铸件检验标准铸件作为机械制造中常见的零部件,其质量直接关系到整个机械设备的安全性和稳定性。
因此,对铸件的检验标准至关重要。
铸件检验标准是指对铸件进行检验时所需遵循的规范和要求,其目的是确保铸件的质量符合设计要求,达到使用要求。
本文将对铸件检验标准进行详细介绍,以便广大机械制造从业者更好地了解和掌握相关知识。
首先,铸件的检验标准主要包括外观质量、尺寸偏差、化学成分、机械性能等方面。
外观质量是指铸件表面的光洁度、无裂纹、气孔、夹渣等缺陷情况,尺寸偏差是指铸件的实际尺寸与设计尺寸之间的差异,化学成分是指铸件材料的成分含量是否符合标准要求,机械性能是指铸件在受力下的强度、硬度、韧性等性能指标。
这些方面的检验标准是保证铸件质量的重要手段。
其次,铸件检验标准的制定需遵循国家标准和行业标准,具有权威性和可操作性。
国家标准是指由国家标准化管理委员会制定并公布的具有普遍适用性的标准,行业标准是指由行业协会或行业组织制定并公布的适用于特定行业的标准。
在制定铸件检验标准时,需参照国家标准和行业标准的要求,结合具体铸件的材料、工艺和使用条件等因素进行制定,以确保检验标准的科学性和实用性。
再次,铸件检验标准的执行需要严格遵循,确保检验结果的准确性和可靠性。
在执行检验标准时,需严格按照标准规定的检验方法和步骤进行操作,确保检验过程的科学性和规范性。
同时,还需使用符合要求的检测设备和工具,确保检验的准确性和可靠性。
只有严格执行检验标准,才能保证铸件质量的稳定性和可靠性。
最后,铸件检验标准的不断完善和提高是保障铸件质量的重要手段。
随着科学技术的不断发展和进步,铸件材料、工艺和使用条件等方面都在不断变化和完善,因此,铸件检验标准也需要不断进行修订和完善,以适应新的需求和新的情况。
只有不断完善和提高铸件检验标准,才能更好地保障铸件质量,满足不断变化的市场需求。
综上所述,铸件检验标准是保证铸件质量的重要保障,其制定、执行和不断完善都具有重要意义。
Q2024J04铸铁件、碳钢铸件检验规范
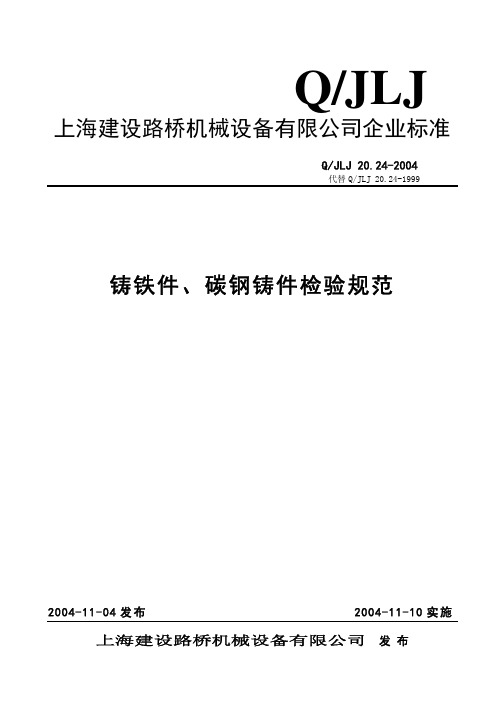
Q/JLJ 上海建设路桥机械设备有限公司企业标准Q/JLJ 20.24-2004代替Q/JLJ 20.24-1999铸铁件、碳钢铸件检验规范2004-11-04发布2004-11-10实施上海建设路桥机械设备有限公司发 布前 言本标准根据国家现有的铸件通用标准及本公司相关的技术文件而制定,指导检验人员用于铸件质量检验。
本标准对Q/JLJ 20.24-1993第3.1和3.3条款进行了修改,补充了相应的理化试验内容,作为进货检验和试验工作指导性文件。
本标准的格式按照GB/T 1.1-2000《标准化工作导则 第1部分:标准的结构和编写规则》进行编辑性修改,具体内容与Q/JLJ 20.24-1999完全一致。
本标准由公司标准化委员会提出;本标准由总工程师室归口;本标准主要起草人:张兰;本标准审核人:陈志兴;本标准标准化审查人:王定华;本标准由公司总工程师李本仁审定;本标准由公司总经理张庆伟批准。
本标准所代替标准的历次发布情况为:——Q/JLJ 20.24-1993、Q/JLJ 20.24-1999。
I铸铁件、碳钢铸件检验规范1 范围本规范规定了质量检查项目和检验频次等事项。
本规范适用于本公司外协铸铁件、碳钢铸件的检验。
不适用高锰钢件及高铬铸铁件。
2 规范性引用文件下列文件中的条款通过本标准的引用而成为本标准的条款。
凡是注日期的引用文件,其随后所有的修改单(不包括勘误的内容)或修订版均不适用于本标准,然而,鼓励根据本标准达成协议的各方研究是否可使用这些文件的最新版本。
凡是不注日期的引用文件,其最新版本适用于本标准。
GB/T 1348 球墨铸铁件GB/T 6414 铸件尺寸公差GB/T 9439 灰铸铁件GB/T 9441 球墨铸铁金相GB/T 11352 一般工程用铸造碳钢件3 质量检查项目3.1 铸件进厂应含有下列内容的质量证明书a ) 铸造厂名;b ) 炉批号;c ) 材质牌号;d ) 机械性能;e ) 化学成分(铸钢件);f ) 浇注随炉试样(重要铸件);3.2 几何形状和尺寸检查按图纸规定的尺寸检查,毛坯中未注公差的尺寸按 GB/T 6414 检验。
铸件检验标准
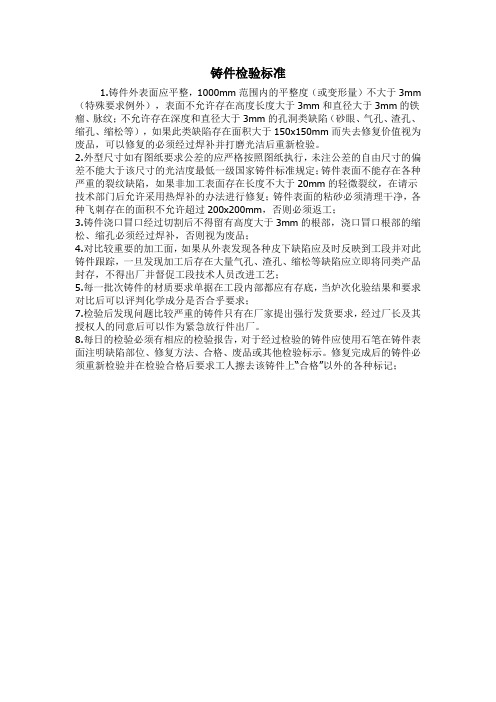
铸件检验标准
1.铸件外表面应平整,1000mm范围内的平整度(或变形量)不大于3mm (特殊要求例外),表面不允许存在高度长度大于3mm和直径大于3mm的铁瘤、脉纹;不允许存在深度和直径大于3mm的孔洞类缺陷(砂眼、气孔、渣孔、缩孔、缩松等),如果此类缺陷存在面积大于150x150mm而失去修复价值视为废品,可以修复的必须经过焊补并打磨光洁后重新检验。
2.外型尺寸如有图纸要求公差的应严格按照图纸执行,未注公差的自由尺寸的偏差不能大于该尺寸的光洁度最低一级国家铸件标准规定;铸件表面不能存在各种严重的裂纹缺陷,如果非加工表面存在长度不大于20mm的轻微裂纹,在请示技术部门后允许采用热焊补的办法进行修复;铸件表面的粘砂必须清理干净,各种飞刺存在的面积不允许超过200x200mm,否则必须返工;
3.铸件浇口冒口经过切割后不得留有高度大于3mm的根部,浇口冒口根部的缩松、缩孔必须经过焊补,否则视为废品;
4.对比较重要的加工面,如果从外表发现各种皮下缺陷应及时反映到工段并对此铸件跟踪,一旦发现加工后存在大量气孔、渣孔、缩松等缺陷应立即将同类产品封存,不得出厂并督促工段技术人员改进工艺;
5.每一批次铸件的材质要求单据在工段内部都应有存底,当炉次化验结果和要求对比后可以评判化学成分是否合乎要求;
7.检验后发现问题比较严重的铸件只有在厂家提出强行发货要求,经过厂长及其授权人的同意后可以作为紧急放行件出厂。
8.每日的检验必须有相应的检验报告,对于经过检验的铸件应使用石笔在铸件表面注明缺陷部位、修复方法、合格、废品或其他检验标示。
修复完成后的铸件必须重新检验并在检验合格后要求工人擦去该铸件上“合格”以外的各种标记;。
金属铸件来料通用检验标准
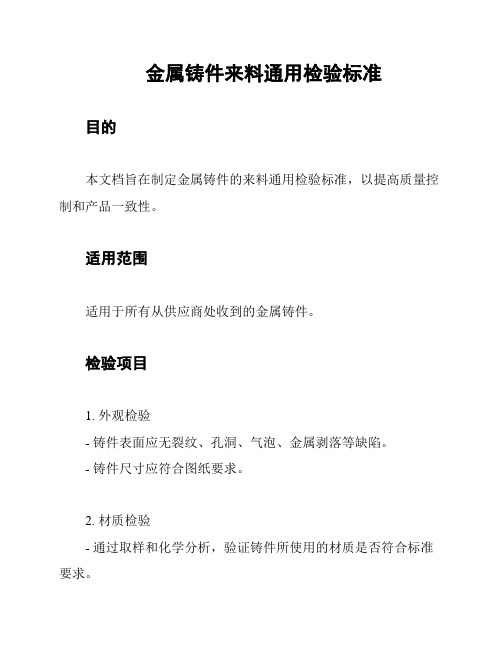
金属铸件来料通用检验标准目的本文档旨在制定金属铸件的来料通用检验标准,以提高质量控制和产品一致性。
适用范围适用于所有从供应商处收到的金属铸件。
检验项目1. 外观检验- 铸件表面应无裂纹、孔洞、气泡、金属剥落等缺陷。
- 铸件尺寸应符合图纸要求。
2. 材质检验- 通过取样和化学分析,验证铸件所使用的材质是否符合标准要求。
3. 硬度检验- 使用硬度测量仪器对铸件进行硬度测试,确保硬度符合要求范围。
4. 渗透检验- 对铸件表面施加渗透剂,观察其渗透情况,检测是否存在裂纹和其他缺陷。
5. 尺寸检验- 根据图纸要求,测量铸件的尺寸,确保尺寸精度和一致性。
检验方法1. 外观检验- 目视检查铸件表面是否满足要求。
2. 材质检验- 从铸件中取样,并使用化学分析方法进行材质验证。
3. 硬度检验- 使用硬度测量仪器对铸件的不同位置进行硬度测试。
4. 渗透检验- 将渗透剂施加到铸件表面,并进行适当的处理后,观察其渗透情况。
5. 尺寸检验- 使用测量工具,如游标卡尺、千分尺等,对铸件进行尺寸测量。
报告与记录1. 检验结果应详细记录,并以报告形式提交给相关部门。
2. 报告中应包含检验项目、检验方法、检验结果以及任何不合格项的处理措施。
不合格品处理1. 如果铸件未通过某项检验项目,则应将其标记为不合格品,并采取适当的措施进行处理。
2. 不合格品应按照公司的不合格控制程序进行处理,包括退货、返工或报废等。
复检1. 如有需要,可以对不合格品进行复检,以确保其问题已得到解决。
变更控制1. 如有必要对此检验标准进行更改,应按照变更控制程序执行,并及时通知相关人员。
附录本文档附有相关的图纸和仪器操作说明,供参考使用。
以上为金属铸件来料通用检验标准的主要内容,以确保金属铸件质量符合要求,提供一致性的产品。
铸铁件检验规程
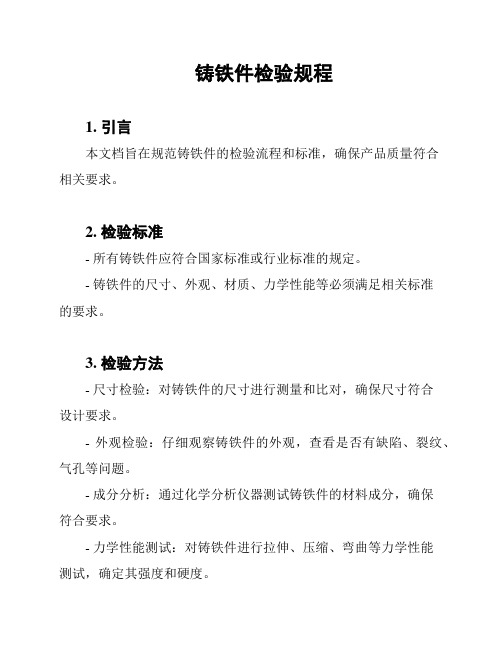
铸铁件检验规程1. 引言本文档旨在规范铸铁件的检验流程和标准,确保产品质量符合相关要求。
2. 检验标准- 所有铸铁件应符合国家标准或行业标准的规定。
- 铸铁件的尺寸、外观、材质、力学性能等必须满足相关标准的要求。
3. 检验方法- 尺寸检验:对铸铁件的尺寸进行测量和比对,确保尺寸符合设计要求。
- 外观检验:仔细观察铸铁件的外观,查看是否有缺陷、裂纹、气孔等问题。
- 成分分析:通过化学分析仪器测试铸铁件的材料成分,确保符合要求。
- 力学性能测试:对铸铁件进行拉伸、压缩、弯曲等力学性能测试,确定其强度和硬度。
- 非破坏性检测:采用超声波、磁粉、射线等非破坏性检测方法,发现内部缺陷和隐蔽问题。
4. 检验流程1. 准备工作:准备检验仪器、标准样品等必要设备和材料。
2. 尺寸检验:按照标准要求对铸铁件的尺寸进行检测。
3. 外观检验:用肉眼观察铸铁件的外观,发现任何缺陷或异常。
4. 成分分析:采集铸铁件样品进行化学分析,确认材料成分。
5. 力学性能测试:根据标准要求进行力学性能测试。
6. 非破坏性检测:根据需要进行相应的非破坏性检测。
7. 结果评定:根据检测结果,评定铸铁件是否合格。
8. 记录和报告:将检验结果记录并制作报告,保存备查。
5. 检验记录与报告- 检验过程中的数据、观察结果和评定意见应当记录并保存。
- 不合格的铸铁件应当注明问题所在,并提出修复或退货的建议。
- 检验报告应当详细描述被检铸铁件的信息、检验结果及评定意见。
6. 检验责任- 检验工作由经过培训和合格考核的专业人员负责。
- 检验人员应遵守相关规程、标准和操作要求,严格把控检验质量。
7. 术语及定义- 根据《铸铁件检验术语及定义》(可参考国家标准或行业标准)规定进行术语和定义的理解和解释。
8. 附录- 相关国家标准或行业标准的引用。
- 检验仪器与设备的清单。
---以上为《铸铁件检验规程》的内容概要,该规程旨在确保铸铁件的质量符合要求,同时规范了检验流程和标准。
铸件检验标准

铸件检验标准1.铸件质量检测仪:用于检测合金性能、组织、表面状态等铸件质量的仪器。
2.铸件公称重量检验:根据铸件图计算或根据供需双方认定合格的标准样品铸件的称重结果订出的铸件重量。
包括铸件机械加工余量及其他工艺余量。
3.铸件重量公差检验:用占铸件公称重量的百分比表示的铸件实际重量与公称重量之差的最大允许值。
与铸件尺寸公差对应的分为16个等级,以MT1-MT16表示。
4.铸件重量偏:铸件重量与公称重量之间的正偏差或负偏差。
5.铸件尺寸公差:铸件各部分尺寸允许的极限偏差。
6.铸件尺寸稳定性:铸件在使用和存放过程中保持原来尺寸不变的性能。
7.铸件机械加工余量:为保证铸件加工面尺寸和零件精度,在铸件工艺设计时预先增加而在机械加工时切去的金属层厚度。
8.铸造表面粗糙度:铸造表面上由微小间距和峰谷组成的微观几何特征。
铸造工段铸件质量检验标准根据目前的生产情况,在初期对我单位的铸件检验制定了以下检验标准,随着以后生产和技术的进一步完善对此标准将逐步细化:1. *铸件外表面应平整,1000mm范围内的平整度(或变形量)不大于3mm(特殊要求例外),表面不允许存在高度长度大于3mm和直径大于3mm的铁瘤、脉纹;*不允许存在深度和直径大于3mm的孔洞类缺陷(砂眼、气孔、渣孔、缩孔、缩松等),如果此类缺陷存在面积大于150x150mm而失去修复价值视为废品,可以修复的必须经过焊补并打磨光洁后重新检验;*外型尺寸如有图纸要求公差的应严格按照图纸执行,未注公差的自由尺寸的偏差不能大于该尺寸的光洁度最低一级国家铸件标准规定;*铸件表面不能存在各种严重的裂纹缺陷,如果非加工表面存在长度不大于20mm的轻微裂纹,在请示技术部门后允许采用热焊补的办法进行修复;*铸件表面的粘砂必须清理干净,各种飞刺存在的面积不允许超过200x200mm,否则必须返工;2. *铸件水口冒口经过切割后不得留有高度大于2mm的根部,水口冒口根部的缩松、缩孔必须经过焊补,否则视为废品;*对比较重要的加工面,如果从外表发现各种皮下缺陷应及时反映到工段并对此铸件跟踪,一旦发现加工后存在大量气孔、渣孔、缩松等缺陷应立即将同类产品封存不得出厂并督促工段技术人员改进工艺;3. *每一批次铸件的材质要求单据在质监部门都应有存底,当炉次化验结果和要求对比后可以评判化学成分是否合乎要求;4. *对于用户在加工后发现的各种内在质量缺陷应及时核对并确定生产日期,作为考核数据重新对检验报告进行更改并及时建议工段技术人员改进工艺;5. *检验后发现问题比较严重的铸件只有在厂家提出强行发货要求,经过总经理及其授权人的书面同意后可以作为紧急放行件出厂。
铸件质量检验标准
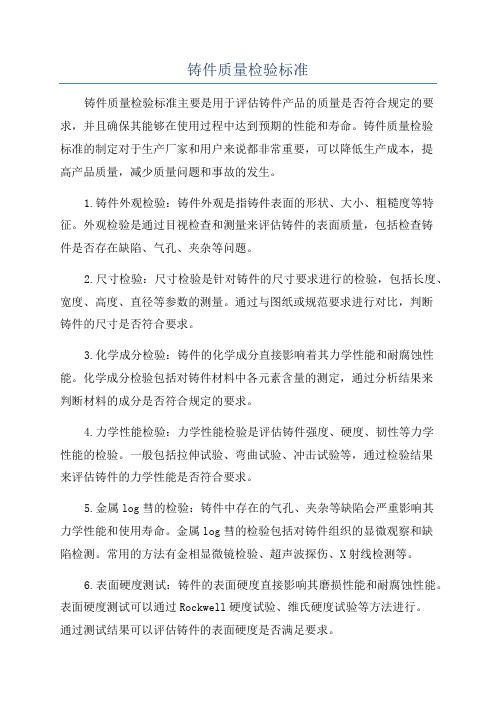
铸件质量检验标准铸件质量检验标准主要是用于评估铸件产品的质量是否符合规定的要求,并且确保其能够在使用过程中达到预期的性能和寿命。
铸件质量检验标准的制定对于生产厂家和用户来说都非常重要,可以降低生产成本,提高产品质量,减少质量问题和事故的发生。
1.铸件外观检验:铸件外观是指铸件表面的形状、大小、粗糙度等特征。
外观检验是通过目视检查和测量来评估铸件的表面质量,包括检查铸件是否存在缺陷、气孔、夹杂等问题。
2.尺寸检验:尺寸检验是针对铸件的尺寸要求进行的检验,包括长度、宽度、高度、直径等参数的测量。
通过与图纸或规范要求进行对比,判断铸件的尺寸是否符合要求。
3.化学成分检验:铸件的化学成分直接影响着其力学性能和耐腐蚀性能。
化学成分检验包括对铸件材料中各元素含量的测定,通过分析结果来判断材料的成分是否符合规定的要求。
4.力学性能检验:力学性能检验是评估铸件强度、硬度、韧性等力学性能的检验。
一般包括拉伸试验、弯曲试验、冲击试验等,通过检验结果来评估铸件的力学性能是否符合要求。
5.金属log彗的检验:铸件中存在的气孔、夹杂等缺陷会严重影响其力学性能和使用寿命。
金属log彗的检验包括对铸件组织的显微观察和缺陷检测。
常用的方法有金相显微镜检验、超声波探伤、X射线检测等。
6.表面硬度测试:铸件的表面硬度直接影响其磨损性能和耐腐蚀性能。
表面硬度测试可以通过Rockwell硬度试验、维氏硬度试验等方法进行。
通过测试结果可以评估铸件的表面硬度是否满足要求。
7.耐蚀性测试:铸件在使用过程中可能会接触到各种介质,耐蚀性是评价铸件耐久性能的重要指标。
耐蚀性测试可以通过浸泡试验、盐雾试验等方法进行,通过测试结果来评估铸件的耐腐蚀性能是否符合要求。
8.热处理性能检验:铸件由于制造过程中会经历冷却和加热等工艺过程,热处理性能对于铸件的组织结构和力学性能有很大影响。
热处理性能检验包括热处理工艺参数的测定和热处理后的铸件组织结构的观察与检测。
铸铁件通用检验标准

铸铁件通用检验标准1目的:规范公司对铸铁件的检查验收。
2适用范围:适用于铸铁件。
※本标准就是铸件的通用型标准,铸件存有特殊要求时,参看有关铸件分类环评标准。
3环评标准:3.1铸铁件材质检验标准:3.1.1球墨铸铁件材质检验标准:球墨铸件材质环评标准应当合乎gb1348或en1563:1997球墨铸铁的标准,以机械性能(抗拉强度、延伸率)、球化率和渗碳体含量为环评依据,硬度、其它金二者非政府及化学成份作为参照。
3.1.1.1球墨铸铁牌号及机械性能(单铸试块)见下表:机械性能球铁牌号抗拉强度,σqt400-18qt400-15qt450-10qt450-12qt500-7qt600-3qt700-2qt550-6b屈服强度,σ0.2延伸率,硬度(hb)δ(%)≥18≥15≥10≥12≥7≥3≥2≥6130-180130-180160-210160-210170-270190-270225-305187-255(mpa)(mpa)≥400≥400≥450≥450≥500≥600≥700≥550≥250≥250≥310≥310≥320≥370≥420≥3793.1.1.2球墨铸铁常规金二者非政府球铁牌号qt400-18qt400-15qt450-10球化率≥80%≥80%≥80%基体组织铁素体f≥80%铁素体f≥75%铁素体f≥75%渗碳体≤3%≤3%≤3%qt450-12qt500-7qt600-3qt700-2qt550-6≥80%≥80%≥80%≥80%≥80%铁素体f≥75%铁素体f+珠光体p珠光体p+铁素体f珠光体p珠光体p+铁素体f≤3%≤3%≤3%≤3%≤3%3.1.1.3球墨铸铁化学成份球铁牌号qt400-18qt400-15qt450-10qt450-12qt500-7qt600-3qt700-2qt550-6化学成份c,%3.4-3.93.4-3.93.4-3.93.4-3.93.4-3.93.2-3.73.2-3.73.4-3.9si,%mn,%p,%2.6-3.12.6-3.12.6-3.12.6-3.12.6-3.02.4-2.82.3-2.62.6-3.0≤0.2≤0.2≤0.3≤0.3≤0.450.4-0.50.5-0.70.1-0.4s,%mg,%re,%cu,%0.2-0.40.2-0.4≤0.07≤0.030.025-0.060.02-0.04≤0.07≤0.030.025-0.060.02-0.04≤0.07≤0.030.025-0.060.02-0.04≤0.07≤0.030.025-0.060.02-0.04≤0.07≤0.030.025-0.060.02-0.04≤0.07≤0.030.025-0.060.02-0.04≤0.07≤0.030.025-0.060.02-0.04≤0.06≤0.030.025-0.060.02-0.043.1.2灰铸铁件材质检验标准:灰铸件材质环评标准应当合乎gb9439或en1561:1997灰铸铁件的标准,以机械性能(抗拉强度)和硬度为环评依据,金二者非政府及化学成份作为参照。
铸件检验标准
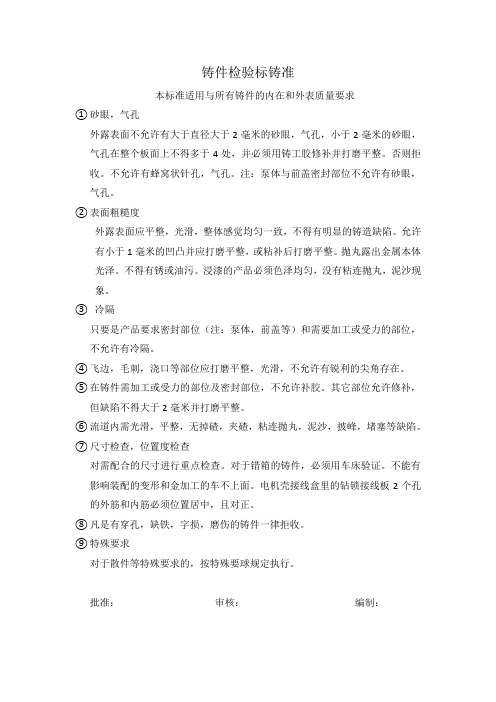
铸件检验标铸准
本标准适用与所有铸件的内在和外表质量要求
①砂眼,气孔
外露表面不允许有大于直径大于2毫米的砂眼,气孔,小于2毫米的砂眼,气孔在整个板面上不得多于4处,并必须用铸工胶修补并打磨平整。
否则拒收。
不允许有蜂窝状针孔,气孔。
注:泵体与前盖密封部位不允许有砂眼,气孔。
②表面粗糙度
外露表面应平整,光滑,整体感觉均匀一致,不得有明显的铸造缺陷。
允许有小于1毫米的凹凸并应打磨平整,或粘补后打磨平整。
抛丸露出金属本体光泽。
不得有锈或油污。
浸漆的产品必须色泽均匀,没有粘连抛丸,泥沙现象。
③冷隔
只要是产品要求密封部位(注:泵体,前盖等)和需要加工或受力的部位,不允许有冷隔。
④飞边,毛刺,浇口等部位应打磨平整,光滑,不允许有锐利的尖角存在。
⑤在铸件需加工或受力的部位及密封部位,不允许补胶。
其它部位允许修补,
但缺陷不得大于2毫米并打磨平整。
⑥流道内需光滑,平整,无掉碴,夹碴,粘连抛丸,泥沙,披峰,堵塞等缺陷。
⑦尺寸检查,位置度检查
对需配合的尺寸进行重点检查。
对于错箱的铸件,必须用车床验证。
不能有影响装配的变形和金加工的车不上面。
电机壳接线盒里的钻锁接线板2个孔的外筋和内筋必须位置居中,且对正。
⑧凡是有穿孔,缺铁,字损,磨伤的铸件一律拒收。
⑨特殊要求
对于散件等特殊要求的,按特殊要球规定执行。
批准:审核:编制:。
铸件外观检验标准
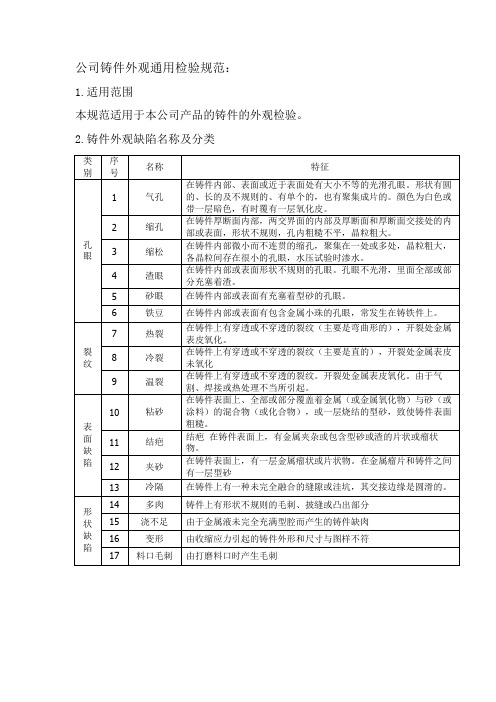
公司铸件外观通用检验规范:
1.适用范围
本规范适用于本公司产品的铸件的外观检验。
2.铸件外观缺陷名称及分类
3.检验要求
3.1铸件不得有明显孔眼(气孔、缩孔、缩松、渣眼、砂眼、铁豆)3.2单个气孔或夹杂的最大尺寸不大于3mm,且不超过壁厚的1/3,
在安装边上不超过壁厚的1/4,在10cm×10cm面积上的数量不多于
3个,边距不小于30mm。
3.3尺寸小于0.5mm的单个气孔或夹杂不计。
气孔或夹杂距铸件边
缘和内孔边缘的距离不小于夹杂或气孔最大尺寸的2倍。
3.4裂纹(热裂、冷裂、温裂),表面缺陷(粘砂、结疤、夹砂、
冷隔),形状缺陷(多肉、浇不足、变形、料口毛刺)等严重影响
产品的外观和强度缺陷。
- 1、下载文档前请自行甄别文档内容的完整性,平台不提供额外的编辑、内容补充、找答案等附加服务。
- 2、"仅部分预览"的文档,不可在线预览部分如存在完整性等问题,可反馈申请退款(可完整预览的文档不适用该条件!)。
- 3、如文档侵犯您的权益,请联系客服反馈,我们会尽快为您处理(人工客服工作时间:9:00-18:30)。
1目的:
规范公司对铸铁件的检查验收。
2适用范围: 适用于铸铁件。
※本标准是铸件的通用标准,铸件有特殊要求时,参见相关铸件分类验收标准。
3 验收标准:
3.1铸铁件材质检验标准:
3.1.1球墨铸铁件材质检验标准:
球墨铸件材质验收标准应符合GB1348或EN1563:1997球墨铸铁的标准,以机械性能(抗拉强度、延伸率)、球化率和渗碳体含量为验收依据,硬度、其它金相组织及化学成份做为参考。
3.1.1.1球墨铸铁牌号及机械性能(单铸试块)见下表:
3.1.1.2 球墨铸铁常规金相组织
3.1.1.3球墨铸铁化学成份
3.1.2灰铸铁件材质检验标准:
灰铸件材质验收标准应符合GB9439或EN 1561:1997灰铸铁件的标准,以机械性能(抗拉强度)和硬度为验收依据,金相组织及化学成份做为参考。
3.1.2.1灰铸铁牌号及机械性能(单铸试块)见下表:
HT250 250-350 190-240
3. 1.2.2 灰铸铁常规金相组织
3.1.2.3灰铸铁化学成份
3.1.3 材质检验取样规范
3.1.3.1机械性能检查:机械性能测试的试棒,每班次每种牌号至少浇一组,有新产品时增加一组,每组浇三根,若铸件进行退火处理,必须连同试棒(试块)一同进行热处理(若是渗碳体超标需热处理的件,按热处理后铸件本体的金相组织来验收)。
机械性能试验:二根用于生产厂测试性能(第一根合格则该批次合格,余下试棒留存(留有生产日期、包次标识),在工厂存放,存放期三年;若第一根试棒不合格,测试剩余二根,若第二根不合格则该批次产品全部报废;若第二根合格,应加试第三根,合格则判定该炉产品合格,若第三根不合格则该批次产品全部报废)。
材质检测报告存根(原始记录)保留11年。
常规灰铸铁试棒见下图:
常规球墨铸铁试棒见下图:
其余
其余
ASTM536标准(美标)试棒见下图
3.1.3.2金相组织检查:球铁铸件从每包铁水的最后一型附铸金相试块或铸件本体进行检验,依次往前直到合格(或本包铁水所浇铸件检验完)为止。
附铸试块应能代表本体。
试块不好,破件进行检验。
对于灰铸铁件每炉铁水至少分析一件附铸试块或本体废件。
若金相有问题,加倍抽查。
金相本体试块应按天分类以月为单位保存,保持期6个月。
检验报告保留11年。
3.1.3.3化学成份检查:每天必须分析每炉铁水(炉前)及至少两炉铸件(炉后)的化学成分。
炉前主要化验碳、硅和硫;炉后碳、硅、锰、硫、磷、稀土、镁(灰铸铁件无稀土、镁两元素)全部化验。
每天第一炉熔清后必须检测C、Si、Mn、
S,之后C、Si每炉化验检测。
化学成分记录要求齐全,归档存放保留11年。
3.2 铸件尺寸精度
3.2.1 铸件尺寸符合图纸要求,未注尺寸公差采用CT9公差,具体数值见下表:
3.3铸件外观质量
3.3.1铸字、标识:铸件上所要求的铸字、标识必须完整、清晰、正确,符合图纸要求。
3.3.2错箱值:铸件最大错箱值不超过0.8mm。
3.3.3浇冒口、飞边残留高度:铸件上浇冒口、披缝等要清理干净,最大残留高度不超过0.5mm。
3.3.4表面粗糙度:铸件表面应光滑、平整,表面有粘砂、氧化皮、锈蚀等应清理干净,表面粗糙度应小于Ra25。
3.3.5铸件表面缺陷
3.3.5.1生产交货的铸件表面质量应进行100%目测检验。
铸件上不允许存在影响性能的缺陷(裂纹、冷隔、浇不足、缩孔等)存在。
3.3.5.2铸件非加工面允许不大于2×2mm深1.5mm的单个孔洞存在,并且每12.5×12.5mm面积范围内的孔数,不多于3处存在,相邻缺陷间隔在10mm以上。
但不允许在铸件壁厚的对应面出现,不允许成片的孔眼类缺陷。
3.3.5.3铸件加工面允许存在加工时可以去除的缺陷,一般控制在加工量的2/3。
3.3.5.4铸件非加工表面每棱边上的磕碰砸伤不得多于2处,并且每处面积不得大于2×2mm。
3.3.5.5铸件非加工面上缺陷如果超出3.3.5.2的规定(但缺陷深度不允许超过铸件壁厚的二分之一),且不在铸件的关键部位(密封面、受力部位、应力点等)周围直径30毫米范围内时,经过允许可以通过焊补或胶补的方法进行修补。
4. 铸件表面防护处理
4.1铸件表面的锈蚀、粘砂、氧化皮等应通过抛丸处理干净。
4.2对有防腐处理要求的铸件,按指定的要求(喷涂、防锈油或防锈漆)进行表面处理,表面处理后颜色应一致且符合要求。
涂层均匀表面光滑,没有磕碰、划伤、流挂、堆集和气泡等明显缺陷。
表面洁净,无污物粘连。
待确认铸件表面涂层完全干透之后,方可进行装箱工序操作,防止涂层粘连的质量问题发生。
5.铸件包装及装箱
5.1铸件包装时表面应干净、整洁。
5.2 铸件装箱时,应在包装箱内放防潮塑料袋,铸件摆放整齐、放置牢靠、数量准确,装箱后及时将防潮塑料袋扎口密封以防生锈。
5.3 装箱后的铸件,箱内必须附带产品合格证、并填写产品库存卡:必须标明装箱产品的名称、产品图号、模型号、箱编号XXXXX-YYYY-ZZ(年月日(年一位数)-日期码-当日装箱序号)、数量等所需标签贴在包装箱外测,并准确无误。
5.4 铸件包装箱采用多层胶合板,外测必须用至少三道钢制打包带固定牢靠。
6.引用标准
GB1348 球墨铸铁件牌号 GB9439 灰铸铁件牌号
GB6414 铸件尺寸公差 GB9441 球墨铸铁金相检验
GB7216 灰铸铁金相检验 EN1563:1997
EN1561:1997。