张力减径的工艺原理及主要问题
热轧(微)张力减径钢管的主要缺陷和消除方法

热轧(微)张力减径钢管的主要缺陷和消除方法
- 热轧(微)张力减径钢管的主要缺陷及消除方法
1、缺点:表面缺陷(毛发状缺陷、裂纹、气孔)
消除方法:提高表面洁净度,加强质量检验,严格控制张力差、减
径钢管精度及表面质量;定期作业前对减径钢管进行卷筒表面填充磨光,减少毛发样缺陷,并且要充分控制卷筒表面填充过程中的处理温度、进料收缩率及剩余应力等。
2、缺点:表面弯角不均匀以及错位等
消除方法:应采用实心轴或带有凹槽的轴,并要有足够的轴面硬度,以防止表面错位;减径钢管的低减径层使用放大器,以减少弯角不均
匀情况,还需要弯曲过程定期维护润滑,增强设备操作稳定性。
3、缺点:减径钢管叞边区减径精度较差
消除方法:提高减径工艺技术,提高减径钢管质量,如拉伸减径阶段,应采用刚性夹头、均匀减径以及调整减径速度等;同时,要及时
对减径钢管进行彻底维护,它才能确保拉伸减径的精度。
4、缺点:减径钢管的精度较差
消除方法:在减径钢管的生产过程中,应配备严格的检测,如采用液压系统定时监测拉伸减径的精度;同时进行原料批次检测,以保持安全性。
同时,要加强钢管表面处理,打磨质量,防止表面老化,提高减径钢管的使用性能和精度。
张力减径的工艺特点

张力减径的工艺特点为了提高轧管机组的生产率和产量,在轧管机后配备了张力减径机。
这样,轧管机只需轧出1种或2种、最多3种外径的荒管,通过张力减径就可生产出多种不同直径和壁厚的成品钢管,使轧管机轧制的钢管单一化,从而减少了管坯和芯棒规格数量。
如宝钢无缝钢管厂的Φ140mm连轧管机组用两种直径,不同壁厚的70个规格的荒管,张力减径后就生产出成品管460个规格。
张力轧制减径中,钢管中间部分的壁厚受到张力作用而被拉薄,头尾两端的壁厚由于受不到张力或受到的张力不同,出现增厚或由厚到薄的过夜壁厚。
因而必须切去钢管两端增厚和过渡壁厚部分的管端。
因此,张力减径机只能配置在能轧制长荒管的轧管机组中,以减少切头损失率。
但是张力减径机如果采用限制管端增厚的电控技术,管端增厚的长度可以减少约1/3。
三辊张力减径机传动有内、外传动两种方式,采用内传动结构居多。
内传动的张力减径机,每个机架内设置有两对圆锥齿轮,简化了机座的结构,但在一定程度上影响了机架间距的缩小。
外传动式是双位机座,机架间距小,承载轧制力大,管端增厚长度也减少。
最大减径率和最大减壁率是张力减径机的两个主要参数。
在最大减径率及其允许的最大减壁率的条件下,用最薄壁的荒管生产出壁厚最薄的钢管,一般称为该台张力减径机的极限规格。
张力减径机组的总对数减径量可达90%,单架对数减径量最髙达12%〜17%。
为提高减径管质量,单架对数减径量常被限制在7%〜9%范围内。
主要机架的单架对数减径量一般为6%〜12%。
张力减径机的进出口速度由生产能力决定。
目前张力减径机的出口速度可达18m/s,进口速度大多在1〜3m/s。
张力减径机的张力系数z的最大允许值一般在0.5〜0.84之间波动,轧制温度高时取下限。
张力减径机的动力学和运动学的分析

张力减径机的动力学和运动学分析文章主要对三辊式张力减径机进行分析,主要分析张力减径机的动力学和运动学原理,通过对张力减径机的速度分析、转速分析和速度控制来分析张力减径机运动学特征,通过对张力减径机受力分析、张力减径机轧制压力和轧制扭矩动态特性分析。
张力减径机是现代化的生产机组,它的功能和优越性使其在大型无缝钢管生产中不可或缺。
随着我国钢管工业的发展张力减径机组正被广泛运用。
对三辊式张力减径机进行分析,该机组是90年代研制的,具有许多独特的优点。
以下分析张力减径机的运动学和动力学原理。
1.张力减径机的运动特性1.1.运动学特征在张力减径的过程中,要求各个机架的延伸系数和轧辊圆周协调一致,同时,决定连续轧机运行的基本条件要求通过每个机架的第二股金属流相等。
在所有的机架都充满金属而C不等于0的情况下,对于每对轧辊在任意瞬间都遵守秒流量、相等的原则,这种相等可通过轧辊和金属之间的滑移达到。
因此当C不等于0时,减径机任何一个机架中的变形条件发生变化,都会影响其余机架中的变形条件,但由于连轧过程本身存在着相适应,自相调整的过程,因此,即使在这种相互作用的复杂关系中,还原过程仍然可以在任何时刻保持第二个流相等。
但是当差别较大时,必然会造成严重的拉钢和推钢,轻者不能获得所需的钢管尺寸,重者连轧过程不能建立,甚至出现事故,因此较为准确的计算各机架转速是很重要的。
1.2.张力减径机的速度控制当轧管转速确定后,必须采用适当的方法进行测定以控制轧辊的速度。
无论拉伸减径机是单独驱动还是整体驱动,速度必须控制在一定水平内,以确保正确的张力。
2.张力减径机的动态分析2.1.张力减径过程中的外力分析张力减径实际上是无芯棒连轧。
符合圆孔型中轧管时的外作用力关系。
按力学原理,轧制工具对金属施加的外力主要是正压力(垂直于工具表面)以及相对运动而产生的摩擦力(垂直于正压力)。
考虑每个零件沿孔槽宽度的应力条件要复杂得多,不过还是两个力——正压力和摩擦力。
钢管张力减径工艺特点及设备选型

由不可调机架发展到成品机架用可调机架,增加了产品的生产灵活性,并且对产品的尺寸精度有了更好的控制。定径机+张力减径机的工艺布置对提高延伸机组的生产能力,简化其生产管理具有积极的作用。张力减径研究理论则是由按均匀变形的传统方法发展为利用计算机把张力减径按非均匀变形来计算的现代方法。
张力减径机专利自1932年出现后,由于其特有的工艺,在连轧管机组及其他方式生产无缝管的机组后,都广泛安设了张力减径机。张力减径机成为了三步轧管法(穿孔、延伸、精轧)中不可或缺的设备。针对机组不同的工艺要求,对张力减径机机型的选择就显得尤为重要。本文将介绍张力减径工艺的特点、各类张力减径机的特征及设备选型。
张力减径另一个特点是生产灵活,变更成品钢管的规格,其设备、电控方面所需的变动很少,生产调整时间较短。
张力减径的缺点及解决方法
在张力减径过程中,由于荒管的两端不承受张力或承受张力较小,并且减径量很大,所以此部分的增壁很多,内孔的形状更不规则,因此在张力减径后要将钢管的两端切去相当长的一段,增加了切头尾损失,降低了钢管成材率。目前张力减径机组可配有切头控制系统(CEC)、平均壁厚控制(WTCA)、局部壁厚控制(WTCL)、管长控制来提高钢管成材率。
按传动系统分类介绍
◇单独传动系统(直流单独传动)
代表机组:宝钢140机组后的28机架张力减径机(可生产300多种规格)。
张力减径机每个机架有直流主电机,各自配有独立的直流调压供电装置,功率和调速范围大。其优点有:从工艺角度来看,单独传动系统对张力的调节最好,对成品钢管规格最大化是最有利的,对实现诸多过程控制提高钢管成材率及产品质量是最有利的;轧辊调速灵活、快速,调速精度很高,机组生产组织灵活;轧机传动结构被大大简化,使传动的可靠性提高;轧辊转速能迅速可靠改变,对实现切头尾损失控制(CEC)变得容易。
张力减径机理论资料

计算管端增厚的方法很多,我认为德国 Meer 厂和考克斯公司的的方法是较为
实用的计算方法。
德国 Meer 厂计算方法介绍如下。
1》 已 知
机 架 间 距 (m): A
毛管 外 径(mm):D0、毛管壁厚(mm):S0;
钢管 外 径(mm):D 、钢管壁厚(mm):S
2》 计 算
1) 延 伸 系 数
µ= S0*(D0- S0)/[ S*(D- S)]
3
△ D= (D0- D)/D0 Zm— — 所 有 机 架 中 钢 管 总 的 平 均 张 力 系 数
3、 减 径 的 几 个 工 艺 问 题
3、1 管端增厚
1) 产生管端增厚的机理和特征
在 钢 管 头 部 出 了 第 一 机 架 但 还 没 有 进 入 第 二 机 架 时 ,这 一 段 钢 管 就 没 有 张 力 的
2) 毛 管 壁 厚 系 数
ν 0= S0/D0
3) 钢 管 壁 厚 系 数
ν = S/D
4) 平 均 壁 厚 系 数
ν m=[(ν0+ν)/2+(S0+S)/(D0+D)]/2
4
5) 减 径 率
ρ = 1- D/D0
6) 轴 向 对 数 变 形
Φ e= LN(µ)
7) 切 向 对 数 变 形
Φ t= LN((D- S)/(D0- S0))
δ i= 1- (1- ρ i)ε ε = [2Zi(ν i-1- 1)+ (1- ν i-1)]/[Zi(1- ν i-1)- (2- ν i-1)] δ i— — 第 机 架 中 钢 管 的 相 对 减 壁 量
δ i= (Si-1- Si)/Si-1 ρ i— — 第 机 架 中 钢 管 的 相 对 减 径 量
卷绕系统中的张力递减控制
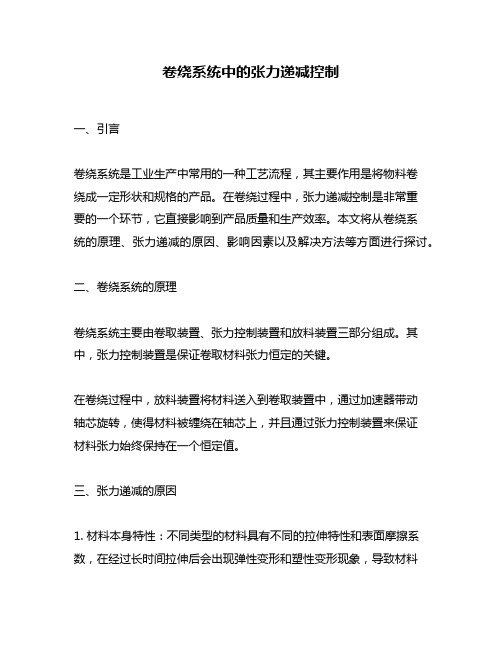
卷绕系统中的张力递减控制一、引言卷绕系统是工业生产中常用的一种工艺流程,其主要作用是将物料卷绕成一定形状和规格的产品。
在卷绕过程中,张力递减控制是非常重要的一个环节,它直接影响到产品质量和生产效率。
本文将从卷绕系统的原理、张力递减的原因、影响因素以及解决方法等方面进行探讨。
二、卷绕系统的原理卷绕系统主要由卷取装置、张力控制装置和放料装置三部分组成。
其中,张力控制装置是保证卷取材料张力恒定的关键。
在卷绕过程中,放料装置将材料送入到卷取装置中,通过加速器带动轴芯旋转,使得材料被缠绕在轴芯上,并且通过张力控制装置来保证材料张力始终保持在一个恒定值。
三、张力递减的原因1. 材料本身特性:不同类型的材料具有不同的拉伸特性和表面摩擦系数,在经过长时间拉伸后会出现弹性变形和塑性变形现象,导致材料表面摩擦系数变化,从而引起张力递减。
2. 张力控制装置的不稳定性:张力控制装置在长时间运行后可能会出现故障或者误差,导致材料张力递减。
3. 卷取装置的设计和状态:卷取装置的设计和状态会影响材料在卷取过程中的张力分布情况,如果设计不合理或者状态不良好,就会导致张力递减。
四、影响因素1. 材料类型:不同类型的材料具有不同的拉伸特性和表面摩擦系数,会对张力递减产生影响。
2. 卷绕速度:卷绕速度越快,材料受到的拉伸程度就越大,容易出现弹性变形和塑性变形现象,从而引起张力递减。
3. 卷取轴芯直径:卷取轴芯直径越大,材料受到的压缩程度就越小,在卷绕过程中容易出现松弛现象,从而引起张力递减。
4. 环境温度和湿度:环境温度和湿度会对材料表面摩擦系数产生影响,从而影响张力递减。
五、解决方法1. 优化卷取装置的设计和状态:通过改变卷取轴芯的直径、改进加速器的结构等方式来优化卷取装置的设计和状态,从而减少张力递减。
2. 优化张力控制装置:通过使用高精度传感器、控制算法等技术手段来提高张力控制装置的稳定性和精度,从而减少张力递减。
3. 控制卷绕速度:通过降低卷绕速度来减少材料受到的拉伸程度,从而减少张力递减。
张减机工艺

1.AR和AO都属于A系列孔型,实行一套减径率分配方 案,这两套孔型的平均减径率都为5.74%,即对应各机 架孔型的平均外径相同。 2.AO采用正宽展轧制,AR采用的是负宽展轧制。 AR 比AO的圆度要好(主要指工作机架部分),AR的 工作机架所选择的椭圆系数在1.02左右,变化小于0.01。 而AO孔型的工作机架的椭圆系数在1.07左右。 3.A0主要用来轧制簿壁管(δ/D<0.125),采用较大的 椭圆系数主要是为增大孔型底部接触轧辊的长度,使 底部金属有较大张力减壁来消减前一机架轧制时壁厚 增厚量,来维持管壁的横向均匀度。
工艺流程 工艺设备及数据 可调机架 质量检查 张减工艺 孔型介绍
1 工艺说明 1总述 张减的过程是一个空心体连轧的过程,除了起定径的作用外,还要求有较大的减径率, 除此之外,张力减径还要求通过各机架间建立张力来实现减壁的目的。因而其工作 机架数较多,一般为12~24架,多至28架,我厂二套选用的是24架,最大总减率可 达72.6﹪。 1. 2工艺过程 荒管在再加热炉加热至920°~1050°后出炉,在出炉辊道出口进行表面测温后,首先 经20Mpa的高压水除鳞装置去除荒管在再加热过程中表面产生的氧化铁皮,然后在 张力减径机中轧制成Φ48~168mm外径的钢管,轧后最大管长达80m。本车间选用 的24架张减机,最大出口设度为7m/s,张减机配有Sms-Meer的CARTA控制系统,采 用该系统可以有效地进行钢管的头尾增厚端的控制,平均壁厚控制及局部壁厚控制。 荒管出张减机后通过冷床的辊道上进行壁厚、温度、外径、长度的连续测量。测量 的结果可用于轧制过程中的闭环控制。 钢管出张减机后,输送到冷床入口辊道处,然后横移到步进式冷床上冷却。
1.张减机的前部工序-轧管机轧制某种薄壁管很难,易产 生轧卡和外表面划伤。 2.用户要求较苛刻,如要求光管的壁厚只能有上偏差,或 只能有下偏偏差。 3.原产品大纲中,单机架减径率大而出现内折叠。 4.生产市场上畅销而原产品中没有的规格时
张力减径的工艺原理及主要问题

包头钢铁职业技术学院学生毕业论文论文题目:张力减径的工艺原理及主要问题专业:冶金班级:冶金一班学生:李咏光指导教师:魏宁日期: 2010年3月31日目录摘要 (1)关键词 (1)引言 (1)1 张力减径机技术的发展 (1)2 张力减径机的作用 (1)2.1张力减径机的形式 (2)3 钢管定径、减径的工艺原理 (3)3.1 张力减径的优点、缺点 (3)3.2三辊定径、减径机减径与二辊定径减径机相比 (4)3.3张力径机的孔型 (5)3.4张力减径机与微张力减径机的不同 (8)3.5 管材热扩径方法 (8)4张力减径时管端偏厚的原因 (10)4.1影响张力减径机管端增厚的因素 (10)4.2影响管内多边形的因素 (11)结语 (11)参考文献 (12)张力减径机的工艺原理及主要问题摘要:简介了三辊定径机定径和减径的作用及形式,提出了定减径机工作时常出现的问题,进行了三辊定减径机和两辊定减径机的比较。
关键词:定减径机;壁厚;斜轧;张力引言:在无缝钢管生产的三大机组——穿孔机组、轧管机组、定减径机组中,人们一直十分关注轧管机的研究,先后开发出自动轧管机组、顶管机组、新型顶管机组(CPE)、三辊轧管机组、连轧管机组(包括浮动芯棒MM、限动芯棒MPM和半浮动芯棒连轧管机组等)、AccuRoll轧管机组、改进型三辊轧管机组。
但对于穿孔机组,仅在20世纪80年代初才提出菌式穿孔机。
而定减径机一直使用二辊式和三辊式,直到20世纪90年代初才提出三辊可调式定径机技术。
新型三辊可调式定径机技术是为满足现代钢管生产高效、优质、低耗的要求而开发的,它的开发成功也为无缝钢管的生产注入新的活力。
1张力减径机技术的发展张减工艺主要特点是边连续多机架二辊或三辊无芯棒纵轧,采用适当的孔型系使毛管外径减缩,通过机架系列中轧辊速比的调节获得预定的壁厚变化。
20世纪40年代无缝管机组被美国和西欧所用,这时的张减机都是二辊式,到了20世纪50年代,西德曼乃斯曼公司成功地奕用了三辊式张力减径机,从而代替了二辊式。
焊管史话之二十电阻焊管的张力减径工艺C_L)

工艺可 以 生产更 宽 的材 质 范 围,具有 明显 的品种 灵活 性 。
( 4 )焊 缝 质 量 优 于 C B W 工艺 。
( 5 ) 由于加 热 轧制 的 原 因 ,表 面质量 和尺 寸精度 低 于 电 阻焊 管 。但 因加 热 温度 仅 为 9 5 0 ~ 9 8 0 o C,
1 E RW + S R 工 艺 组 成 和 布 置
E R W+ S R 工艺 的基 本过 程是 :首先 生产 出单一 直径 的焊接母 管 :采 用加 热 炉或感 应加 热的 方式把 母 管加 热 到热轧 温度 ,一般 为 9 5 0 ~ 9 8 0 ;进入 热 张 力减径 ( 一般 为 三辊 结构 ) 轧 制 出成 品 直径 管 ;飞
普遍 。
( 2 )在 焊 管机组 和加 热 炉 间设置 一 个较 长的缓 冲 台架 ,焊 管通过 该 台架连 续进 入加 热炉和 张 力减
径机 这是德 国人 开始采 用 的工 艺
( 3 )在 焊 管机 组 和加 热 炉 间仅 有 1 0 1 T I 左 右 的距 离,焊 管连 续进 入加 热 炉 和 张力 减 径机 。 这 或 两个 规格 的 电 阻焊母 管 ,通 过 张 力减 径 即 可 生产 出较 宽直径 范 围的钢
管。该 工 艺最 大的特 点是提 高 了电 阻焊 管 的生产 效率 ,能 实现水煤 气管 、方矩 形 建筑 用管和 一般 结构 管的 高效 大批 量 生产 ,生产效 率与 当时的连 续对接焊 管 ( C B W) 工 艺相 当,而投 资相 对较低 。 由此可 见 , 该 工 艺起 源的 宗 旨是提 高 电阻焊 管的 生产 效率 ,而 非提 高焊 管 的质量 ,对标或 竞 争工 艺是 当时的 对接 焊管 工 艺。
张力减径中产品缺陷及预防

张力减径中产品缺陷及预防作者:武建兵来源:《科技创新与生产力》 2016年第4期武建兵(太原通泽重工有限公司,山西太原 030032)摘要:通过分析张力减径中产品青线形成、外径超差、管端增厚、鹅头弯、内六方等缺陷产生的原因,提出了预防或消除缺陷的相应措施。
关键词:减径机;青线;管端增厚;鹅头弯;内六方中图分类号:TG335 文献标志码:A DOI:10.3969/j.issn.1674-9146.2016.04.114收稿日期:2015-11-30;修回日期:2016-03-02作者简介:武建兵(1979-),男,山西平遥人,硕士,工程师,主要从事无缝钢管生产设备设计及生产工艺研究,E-mail:147362164@。
张力减径轧制作为无缝钢管生产的最后一道热轧工序,对产品质量的控制起着决定性作用。
无缝钢管的张力减径是一种不带芯棒的连续轧制过程,在轧制过程中,轧件受到轧辊的径向压力作用使外径、壁厚发生变化,轴向受到轧辊摩擦力作用,使壁厚发生改变,同时受到切向应力及以温度变化等各种因素作用。
由于其轧制过程的复杂性,因此容易引起许多种产品缺陷,其主要缺陷有青线、外径超差、内六方、管端增厚、鹅头弯等。
其中一些缺陷可以采用一定的措施消除,而另一些缺陷则可以加以控制或改善。
为此,笔者从理论与实践两方面就常见缺陷形成原因及预防措施做了简要分析。
1 青线形成原因及预防青线是指钢管表面沿长度方向有一条突起的直线。
青线产生的主要原因有:孔型设计时椭圆度过小、宽展量不合理,使钢管在轧制时金属过充满后被挤入辊缝,形成青线;轧辊沿轴向窜动,由于固定轧辊轴向移动的螺栓(或圆螺母)松动,使得轧辊可以沿轴向移动,造成辊面在辊缝处形成台阶,在钢管轧制时,形成青线。
为了预防青线出现,应根据生产现场情况,分析产生青线的原因。
首先检验每个机架轧辊是否在轴向窜动,如果有个别轧辊轴向窜动,则应维修轧辊机架,消除轧辊机架的窜动因素,随后重新修正孔型尺寸,进行轧制,最后检验产品是否合格。
张力减径机的动力学和运动学的分析
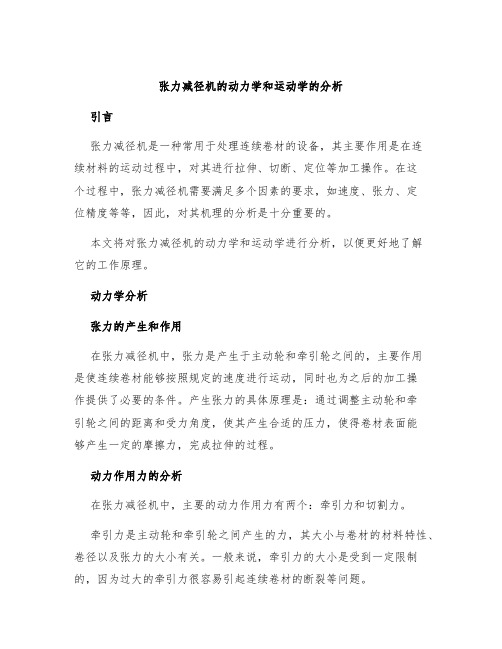
张力减径机的动力学和运动学的分析引言张力减径机是一种常用于处理连续卷材的设备,其主要作用是在连续材料的运动过程中,对其进行拉伸、切断、定位等加工操作。
在这个过程中,张力减径机需要满足多个因素的要求,如速度、张力、定位精度等等,因此,对其机理的分析是十分重要的。
本文将对张力减径机的动力学和运动学进行分析,以便更好地了解它的工作原理。
动力学分析张力的产生和作用在张力减径机中,张力是产生于主动轮和牵引轮之间的,主要作用是使连续卷材能够按照规定的速度进行运动,同时也为之后的加工操作提供了必要的条件。
产生张力的具体原理是:通过调整主动轮和牵引轮之间的距离和受力角度,使其产生合适的压力,使得卷材表面能够产生一定的摩擦力,完成拉伸的过程。
动力作用力的分析在张力减径机中,主要的动力作用力有两个:牵引力和切割力。
牵引力是主动轮和牵引轮之间产生的力,其大小与卷材的材料特性、卷径以及张力的大小有关。
一般来说,牵引力的大小是受到一定限制的,因为过大的牵引力很容易引起连续卷材的断裂等问题。
切割力则是在完成张力放松和定位后对连续卷材进行切割的力,其大小取决于切割刀具的选择和切割方式。
运动状态的分析张力减径机的运动状态主要分为两类:平动和旋动。
平动是指卷材在张力减径机中的直线运动,其速度和方向可以通过控制主动轮和牵引轮的转速和角度来控制。
旋动是指卷材在放松张力和定位后完成切断操作时所进行的旋转运动。
在进行旋转操作时,需要确保主动轮和牵引轮的运动速度和位置的精度,并保持对卷材的限位等操作。
运动学分析定位精度的分析卷材的定位是张力减径机中一项非常重要的任务。
其通过采用不同的装置和传感器对卷材的位置进行监测来完成。
在进行定位操作时,需要严格控制主动轮和牵引轮的运动状态以及切割刀具的位置和速度等参量,以达到精准的定位效果。
运动的控制和优化尽管张力减径机的主要功能是完成张力、切割和定位操作,但其运动过程中也需要实时监测和调整主动轮和牵引轮的运动状态以及切割刀具的参数等相关因素。
电阻焊张力减径钢管的力学模型研究
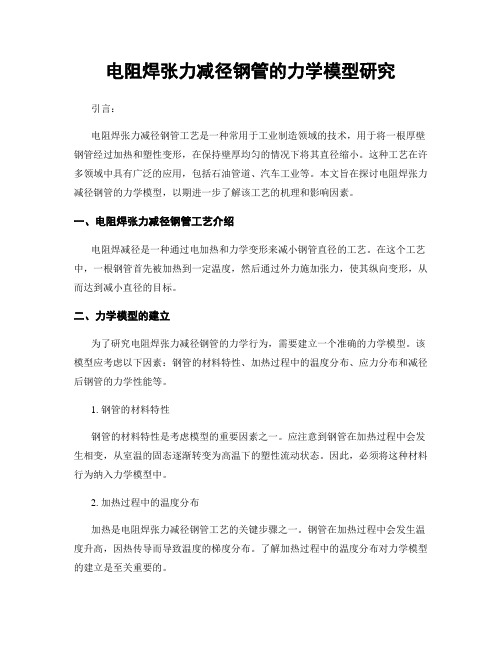
电阻焊张力减径钢管的力学模型研究引言:电阻焊张力减径钢管工艺是一种常用于工业制造领域的技术,用于将一根厚壁钢管经过加热和塑性变形,在保持壁厚均匀的情况下将其直径缩小。
这种工艺在许多领域中具有广泛的应用,包括石油管道、汽车工业等。
本文旨在探讨电阻焊张力减径钢管的力学模型,以期进一步了解该工艺的机理和影响因素。
一、电阻焊张力减径钢管工艺介绍电阻焊减径是一种通过电加热和力学变形来减小钢管直径的工艺。
在这个工艺中,一根钢管首先被加热到一定温度,然后通过外力施加张力,使其纵向变形,从而达到减小直径的目标。
二、力学模型的建立为了研究电阻焊张力减径钢管的力学行为,需要建立一个准确的力学模型。
该模型应考虑以下因素:钢管的材料特性、加热过程中的温度分布、应力分布和减径后钢管的力学性能等。
1. 钢管的材料特性钢管的材料特性是考虑模型的重要因素之一。
应注意到钢管在加热过程中会发生相变,从室温的固态逐渐转变为高温下的塑性流动状态。
因此,必须将这种材料行为纳入力学模型中。
2. 加热过程中的温度分布加热是电阻焊张力减径钢管工艺的关键步骤之一。
钢管在加热过程中会发生温度升高,因热传导而导致温度的梯度分布。
了解加热过程中的温度分布对力学模型的建立是至关重要的。
3. 应力分布在电阻焊减径过程中,外力施加在钢管上,使钢管产生纵向应力。
这些应力分布是在钢管减径的过程中非常关键的。
通过建立钢管应力分布的模型,可以进一步分析减径过程中材料的变形和应力集中情况。
4. 减径后钢管的力学性能在完成电阻焊减径后,钢管会发生直径、壁厚和材料性能的变化。
因此,在力学模型中必须考虑这些因素。
三、实验验证和计算模拟建立理论力学模型后,我们可以通过实验验证和计算模拟来验证模型的准确性。
1. 实验验证通过采集电阻焊张力减径钢管的温度和应力数据,可以比较实验结果和模型预测值,从而验证模型的准确性。
实验还可以评估不同参数对减径过程的影响。
2. 计算模拟在进行计算模拟之前,必须将电阻焊减径钢管的力学模型转化为数值模型。
卷绕系统中的张力递减控制
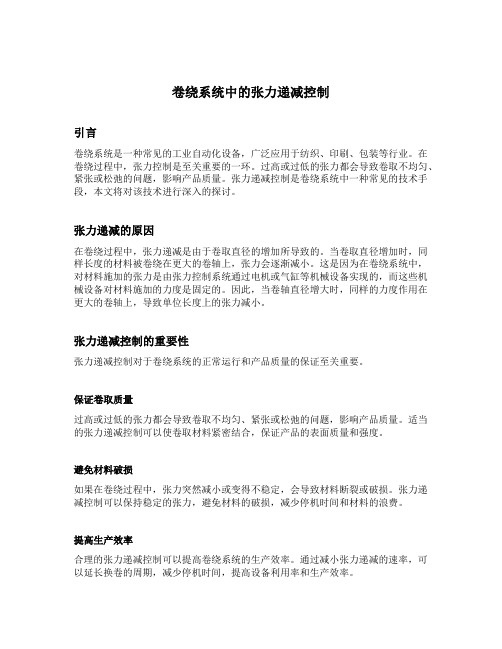
卷绕系统中的张力递减控制引言卷绕系统是一种常见的工业自动化设备,广泛应用于纺织、印刷、包装等行业。
在卷绕过程中,张力控制是至关重要的一环。
过高或过低的张力都会导致卷取不均匀、紧张或松弛的问题,影响产品质量。
张力递减控制是卷绕系统中一种常见的技术手段,本文将对该技术进行深入的探讨。
张力递减的原因在卷绕过程中,张力递减是由于卷取直径的增加所导致的。
当卷取直径增加时,同样长度的材料被卷绕在更大的卷轴上,张力会逐渐减小。
这是因为在卷绕系统中,对材料施加的张力是由张力控制系统通过电机或气缸等机械设备实现的,而这些机械设备对材料施加的力度是固定的。
因此,当卷轴直径增大时,同样的力度作用在更大的卷轴上,导致单位长度上的张力减小。
张力递减控制的重要性张力递减控制对于卷绕系统的正常运行和产品质量的保证至关重要。
保证卷取质量过高或过低的张力都会导致卷取不均匀、紧张或松弛的问题,影响产品质量。
适当的张力递减控制可以使卷取材料紧密结合,保证产品的表面质量和强度。
避免材料破损如果在卷绕过程中,张力突然减小或变得不稳定,会导致材料断裂或破损。
张力递减控制可以保持稳定的张力,避免材料的破损,减少停机时间和材料的浪费。
提高生产效率合理的张力递减控制可以提高卷绕系统的生产效率。
通过减小张力递减的速率,可以延长换卷的周期,减少停机时间,提高设备利用率和生产效率。
张力递减控制的方法张力递减控制是通过控制卷取直径和调整张力控制系统来实现的。
以下是一些常用的方法:传感器测量利用张力传感器测量卷取过程中的张力,并实时反馈给张力控制系统。
通过对测量数据的分析和处理,可以控制张力的递减速率,保持稳定的张力。
PID控制PID控制器是一种常用的控制器类型,通过对测量误差的比例、积分和微分进行加权和调节,实现对张力的控制。
在张力递减控制中,可以根据卷取直径的变化,动态调整PID控制器的参数,使得张力能够随着卷取直径的增加适当地递减。
卷取直径的测量和预测卷取直径的测量和预测是实现张力递减控制的关键。
钢管张力减速机的减径理论及工艺参数-未成稿

钢管张力减径机的减径理论及工艺参数太原重型机器有限公司技术中心轧钢所汤智辉前言张力钢管减径是钢管生产中的一项重大的发展,世界各国都十分重视。
张力减径机已经愈来愈广地得到应用。
用一般不带张力的减径机来生产小直径钢管,已经有很多年的历史了。
但是,由于减径出来的钢管壁厚增加、横向壁厚不均比较严重,减径管的质量不能令人满意;同时由于减径量较小,需要比较多的机架,因此,这种减径机应用范围多半局限在生产轧管机组不能或不容易直接生产的小直径钢管。
在一般减径机上,单架减径理只有3~5%,而在张力减径机上,单架减径量可以达到12~14%。
张力减径时,在减小直径的同时可以使钢管壁厚减薄或者保持不变,减径过程稳定并且钢管的横向壁厚不均也比较小。
因此,张力减径就成了生产薄壁小直径钢管的有效方法。
此外,由于张力减径时的变形量大,所需要的机架数目可以显著减少,因而使减径管的规格范围日益扩大。
这样,减径机就不仅用来生产小直径钢管,同时也用来生产较大规格的钢管。
在这种情况下,前面的轧管机组就可以只生产少数几种生产北最高、最便于生产的规格,通过张力减径机得到各种尺寸的成品管,从而大大提高了机组的生产能力,简化了生产。
目前,只要是在无缝钢管生产中,不论在连续生产还是单根钢管生产中,也不论在轧钢机还是在挤压机后,都广泛安设了张力减径机。
因此,可以说:张力减径机已经成为钢管生产中应用最广泛的设备之一。
张减理论一、 管材的壁厚变化与延伸在张力减径时过程中,管材的壁厚减薄与延伸,既发生在减径机的各机架上,也同样发生在减径机各机架之间。
㈠ 在机架上的变形当管材在机架上受压时,直径和壁厚都发生变化。
如果说直径的变化完全决 定于孔型的尺寸,那么壁厚的改变则同其它一些因素(张力、壁厚与直径之比等)有关。
现以管材在变形区的一个单元体为例,对其应力状态进行分析。
径向应力 σr 、切向应力σq 、轴向应力σx 在管材断面和在变形区的分布都是不均匀的。
这可以从管材出入口断面的应力不相等,和内外表面的应力不相等可以看出。
无缝钢管张力减径过程中内六方的成因分析及解决办法
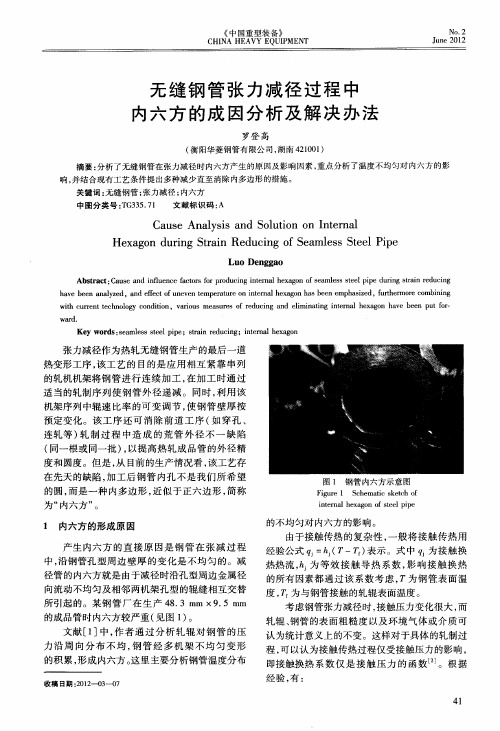
及 传 动上 的方便 , 邻 机架上 下倒 置摆 放 , 相 这相 当 于将 轧辊 每 次 旋 转 6 。 正 是 这 种 布 置 使 钢 管 的 0, 壁 厚变 化趋 势 叠 加 。如 果 采 用 不 同角 度 布 置 , 最
机 架叠 加后 , 管 金 属 在 沿 轧辊 孔 型 方 向流 动 不 钢 均 匀 。钢管 在 减 径 过程 中 , 薄 的部 位 在 不 断 减 减
2 解 决措 施
薄 , 厚 的部 位 在不 断增 厚 。如果 钢 管 此 时 能 产 增
生 一定 角度 的旋 转 , 则增 厚 和减 薄趋 势不会 叠 加 , 这 样金 属在 沿 轧 辊孔 型方 向 的流 动 趋 于 均 匀 , 内 六 方 问题将 得 到根本 上 的解决 。
中, 沿钢 管孔 型 周 边 壁 厚 的 变 化是 不 均 匀 的。减
的不 均 匀对 内六 方 的影 响。
由于接触传热的复杂性 , 一般将接触传热用
经验 公式 q =h( ) 示 。式 中 g 为 接触 换 iT— 表 i
热热 流 ,; 等 效 接 触 导 热 系数 , 响 接 触 换 热 h为 影
41
No. 2
J n 0l u e2 2
《 中国重型装备》 C N E V Q IME T HIA H A Y E U P N
单机架 轧 制后
第 二机架 轧制 后
图 2 沿 16周长 的 q 分布 图 / ;
F g r q it b t n ao g 1 6 p rmee iue2 Jdsr u i ln / e i tr i o
wih c re e hn l g o diin, v ro s t u r ntt c o o y c n to a iu me s r s o e u i g a d e i ia i ne a h x g n a e e n p fr a u e f r d c n n lm n tng i tr l e a o h v b e uto — n
张减资料

给常州减径机讲稿2004年10月17日1、前言1、1张力减径机与微张力减径机的区别总的来,张减与微张减在设备和变形原理上是完全一样的,只是在实际运用时,根据不同的条件和要求,选择的工艺参数(张力系数)不同而已。
张力减径一般机架数≥16,工艺上最大的特点是减壁减径,一般单架最大减径率>6.0%,总减径率可达到80%以上。
但同时它的切头损失非常大(最大的切头长度可超过2米)。
微张力减径的机架数≤14,过去单架最大减径率不超过3.5%、总减径率小于35%。
由于张力系数≤0.5,只能实现等壁或减壁减径,因此切头损失比张减大大减少——大多情况下,切头长度大多可控制在300MM以内。
同时,只要措施得当,中、厚壁管的“内六方”可控制在较好水平。
因此微张力减径机比较适用于荒管长度≤15米的热轧无缝钢管机组和中、厚壁管生产。
1、2介绍主要内容介绍的主要内容是减径的变形理论、几个工艺问题和生产工艺的编制、轧机调整。
2、变形理论(微张减工艺的基础)2、1基本变形理论——钢管张力减径变形的基本方程式2、1、1 推导所用的符号和定义S ——钢管壁厚D ——钢管外径F ——钢管横断面积F=πS(D-S)ν——钢管壁厚系数ν=S/DDm——钢管平均直径1Dm=D-Sζr ——径向应力ζ e ——轴向应力ζt ——切向应力Φr ——径向对数变形Φr=l nS/S0Φe ——轴向对数变形Φe=l nL/L0=ln F0/F=lnµΦt ——切向对数变形Φt=l n(D-S)/(D0-S0)2、1、2 基本出发点1)三向的应力—应变关系——圣维南塑性应力应变理论(ζr-ζm):(ζe-ζm):(ζt-ζm)=Φr:Φe:Φt 式中:ζm为平均应力ζm=(ζr+ζe+ζt)/32)屈服条件——最大切应力理论ηma x=(ζ1-ζ3)/2=Kf/2在钢管减径条件下,即为:ζe-ζt=K fKf为材料的变形抗力,主要与材料的屈服极限ζs、变形温度、变形速度以及加工硬化等有关。
张力减径过程管端增厚机理与控制策略研究

张力减径过程管端增厚机理与控制策略研究无缝钢管在国民经济发展的诸多行业中都起着重要的作用,而张力减径机组作为热轧无缝钢管的最后一道热变形工序,直接影响成品管的尺寸精度和力学性能。
各国钢管企业都通过这一环节扩大钢管产品规格、提高产品质量、降低生产成本。
因此进行张力减径过程基本工艺理论、管端增厚机理及控制的有限元模拟研究,深入了解张力减径过程金属变形特点、掌握关键工艺参数对管端增厚的影响规律,对进一步优化工艺参数、减少切除损失、节约能源和资源具有重要的理论意义和实用价值。
基于MSC.Marc建立无缝钢管张力减径过程三维热力耦合有限元模型,并利用实际生产数据验证有限元模型的可靠性和准确性,进一步分析张力减径过程管端增厚机理,并通过改变初始温度、摩擦系数、减径量、张力系数研究轧制过程中张力和轧后头尾端切损量的变化规律。
利用有限元方法对原有管端增厚控制CEC技术进行研究分析,根据其工作原理对现有三级CEC控制策略进行改进,并开发新型管端控制技术,以达到管端切损量降低20%-50%的国际先进水平。
基于张力减径过程基本理论,采用VB软件编制张力减径工艺程序,以计算、输出指定钢管系列的关键工艺参数,并可实现无缝钢管新品种工艺参数的准确计算,方便无缝钢管行业者。
电阻焊张力减径钢管的切削性能研究
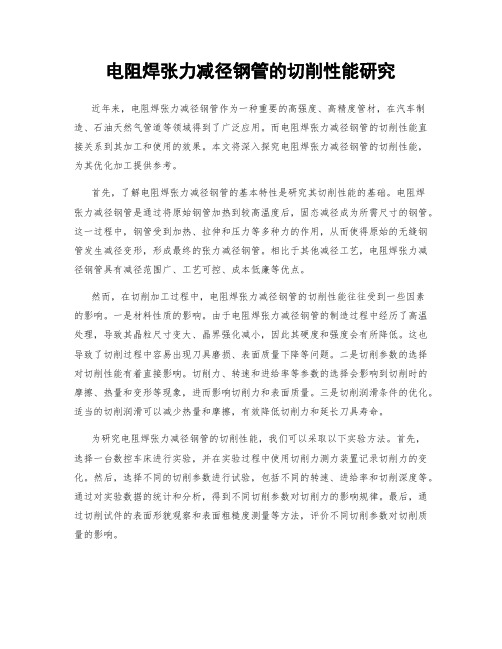
电阻焊张力减径钢管的切削性能研究近年来,电阻焊张力减径钢管作为一种重要的高强度、高精度管材,在汽车制造、石油天然气管道等领域得到了广泛应用。
而电阻焊张力减径钢管的切削性能直接关系到其加工和使用的效果。
本文将深入探究电阻焊张力减径钢管的切削性能,为其优化加工提供参考。
首先,了解电阻焊张力减径钢管的基本特性是研究其切削性能的基础。
电阻焊张力减径钢管是通过将原始钢管加热到较高温度后,固态减径成为所需尺寸的钢管。
这一过程中,钢管受到加热、拉伸和压力等多种力的作用,从而使得原始的无缝钢管发生减径变形,形成最终的张力减径钢管。
相比于其他减径工艺,电阻焊张力减径钢管具有减径范围广、工艺可控、成本低廉等优点。
然而,在切削加工过程中,电阻焊张力减径钢管的切削性能往往受到一些因素的影响。
一是材料性质的影响。
由于电阻焊张力减径钢管的制造过程中经历了高温处理,导致其晶粒尺寸变大、晶界强化减小,因此其硬度和强度会有所降低。
这也导致了切削过程中容易出现刀具磨损、表面质量下降等问题。
二是切削参数的选择对切削性能有着直接影响。
切削力、转速和进给率等参数的选择会影响到切削时的摩擦、热量和变形等现象,进而影响切削力和表面质量。
三是切削润滑条件的优化。
适当的切削润滑可以减少热量和摩擦,有效降低切削力和延长刀具寿命。
为研究电阻焊张力减径钢管的切削性能,我们可以采取以下实验方法。
首先,选择一台数控车床进行实验,并在实验过程中使用切削力测力装置记录切削力的变化。
然后,选择不同的切削参数进行试验,包括不同的转速、进给率和切削深度等。
通过对实验数据的统计和分析,得到不同切削参数对切削力的影响规律。
最后,通过切削试件的表面形貌观察和表面粗糙度测量等方法,评价不同切削参数对切削质量的影响。
在实验进行过程中,我们需要注意以下几点。
首先,要选择合适的切削润滑剂,并在不同实验条件下加以比较。
其次,在实验过程中要及时记录切削力的变化,并进行数据的准确统计。
- 1、下载文档前请自行甄别文档内容的完整性,平台不提供额外的编辑、内容补充、找答案等附加服务。
- 2、"仅部分预览"的文档,不可在线预览部分如存在完整性等问题,可反馈申请退款(可完整预览的文档不适用该条件!)。
- 3、如文档侵犯您的权益,请联系客服反馈,我们会尽快为您处理(人工客服工作时间:9:00-18:30)。
δ1=1/2δ,δ2=δ3……δn-2=δ δn-1=1/2δ,δn=0 对于任一机架相对压下量为
δ1=Di-1-Di/Di-1×100% Di=Ai+Bi/2 式中 Di、Di-1——为孔型平均直径; Ai——孔型高度; Bi——孔型宽度; 根据相对压下量公式可写出: Di=Di-1((1-δi)
当 i=1 时,Di-1 为来料外径,即为斜轧延伸以后的外径 Dp,则 Di-1=Dp 利用此式和前述所确定的平均压下量,可写出一系列等式:
D1=Dp(1-1/2δ)≈Dp(1-δ)0.5 D2=D1(1-δ)≈Dp(1-δ)1.5 ………………
Dn-1=Dn-2(1-1/2δ)δ=Dp(1-δ)n-2.5 Dn=Dn-1=Dp(1-δ)n-2 由此可得到相对压下量
(4)张力减径的延伸系数为 6--9,可以生产长达 165m 的钢管。 张力减径的缺点: 张力减径的缺点是张力减径轧制中,钢管中间部分的管壁受到张力作用而 减壁,头尾两端的管壁由于受不到张力或受到的张力由小变大, 出现增厚段, 这增厚部分超过公差,需切掉,增加了头尾的损失,所以要求一般进入张力 减径机的管子来料长度要足够长,在经济上才合理。管理计算机和过程控制 机的投入使用,使张力减径机管端增厚控制 CEC 得以实现,这样能在更大程 度上满足工艺的要求,为张力减径生产的高产、优质、低消耗开阔了更加广 阔的前景。在广泛应用的连轧管机后面配置一台张力减径机作为成型机组, 即可满足连轧管机的产量要求,又可解决产品规格的要求,这样用一种或两 种连轧毛管即可生产出几百种不同规格的热轧管。这标志着钢管生产的最新 发展方向,使无缝钢管生产实现大 型化、高速化和连续化。张力减径机已经 在几乎各类轧管机组和中小型焊管机组上得到广泛的应用。 3.2:三辊定径、减径机减径与二辊定径减径机相比 (1)机架间距;三辊式定径减径机机架间距比二辊式定径、减径机间距 小,但机械结构复杂。 (2)单机架变形量;与二辊定径、减径机相比,三辊式定径、减径机每 个轧辊轧制变形量小,管端增厚长度小、切头切尾量少、金属损耗少。 (3)钢管质量:三辊式比二棍式定径 、减径机轧辊孔型周边的速度差小, 从而减少轧辊与钢管的相对滑动,轧辊较小。沿周向每个轧辊型与钢管接触 弧长较小,这使周向上所受的变形力比较均匀,金属变形时的流动趋于均匀, 从而可以减少横向壁厚的不均匀程度。三辊式定径、减径机与二辊式定径、
管,直径偏差较小,椭圆度较小,直度较好,表面光洁。定径机工作机架数 目较少,一般为 3--12 架总减径率约为 3%到 7%,增加定径机架数可扩大产品 规格,给生产带来方便,新设计车间定径机架数一般都较多。
直径小于 60mm 的钢管,很难由轧管机轧成,而需要经过减径工序。静静 除具有定径相同的作用外,还要求有较大的减径率,以实现大管料生产小口 径钢管的目的,也可用来生产异型管。减径机的机架数一般较多,一般为 5 到 24 架。减径机有两种形式:
张力减径机的工艺原理及主要问题
摘要:简介了三辊定径机定径和减径的作用及形式,提出了定减径机工 作时常出现的问题,进行了三辊定减径机和两辊定减径机的比较。
关键词:定减径机;壁厚;斜轧;张力 引言: 在无缝钢管生产的三大机组——穿孔机组、轧管机组、定减径机组 中,人们一直十分关注轧管机的研究,先后开发出自动轧管机组、顶管机组、 新型顶管机组(CPE)、三辊轧管机组、连轧管机组(包括浮动芯棒 MM、限动 芯棒 MPM 和半浮动芯棒连轧管机组等)、AccuRoll 轧管机组、改进型三辊轧管 机组。但对于穿孔机组,仅在 20 世纪 80 年代初才提出菌式穿孔机。而定减 径机一直使用二辊式和三辊式,直到 20 世纪 90 年代初才提出三辊可调式定 径机技术。新型三辊可调式定径机技术是为满足现代钢管生产高效、优质、 低耗的要求而开发的,它的开发成功也为无缝钢管的生产注入新的活力。 1 张力减径机技术的发展 张减工艺主要特点是边连续多机架二辊或三辊无芯棒纵轧,采用适当的孔 型系使毛管外径减缩,通过机架系列中轧辊速比的调节获得预定的壁厚变化。 20 世纪 40 年代无缝管机组被美国和西欧所用,这时的张减机都是二辊式, 到了 20 世纪 50 年代,西德曼乃斯曼公司成功地奕用了三辊式张力减径机, 从而代替了二辊式。 2 张力减径机的作用 定径的目的是在较小的总减径率和小的单机减径率条件下,将钢管轧成一定 要求的尺寸精度和真圆度,并进一步提高钢管外表面质量。经过定径后的钢
减径机相比,生产的钢管外径圆度较好。 (4)机架布置:三辊式定径、减径机轧辊交叉 60°,使轧机结构简化,
便于布置。 (5)张力的建立:三辊式定径、减径机轧辊数目多,则轧制时对钢管的
曳入性能较好,可在较短的咬入钢管长度上建立足够的张力。 (6)可调整性:二辊式定径、减径机容易实现在线孔型尺寸的调整,以
(1)一般微张力减径机,作用就是减缩管径,生产机组不能轧制或加工 起来很不经济的规格;
(2)张力减径机,作用不但减缩管径的外径,而且可以减小钢管的壁厚, 既减径又减壁,使机组产品进一步扩大;并可适当加大来料的重量,提高减 径率轧制更长的产品。
2.1 张力减径机的形式 定径机的形式很多,按辊数可分为二辊、三辊、四辊式定径机;按轧制方 式分为纵轧定径机和斜轧定径机。斜轧定径机一般多配在三辊斜轧管机组中。 斜轧回转定径机的构造与二辊或三辊斜轧穿孔机相似,只是辊型不同。与纵 轧定径相比,斜轧定径的钢管外径精度高,椭圆度小,更换规格品种方便, 不需要换辊,只要调整轧辊间距即可;缺点是生产率低。 减径机的形式很多,按辊数可分为二辊、三辊、四辊式减径机。按机架 张力大小可分为两种形式: (1)微张力减径机,减径过程中壁厚增加,横截面上的壁厚均匀性恶化, 所以总减径率限制在 40%到 50%;
满足标准、规范对外径偏差的要求,而三辊式定径、减径机一般不能实现在 线孔型尺寸的调整。现在广泛采的是三辊式径、减径机。
3.3:张力径机的孔型 在张减孔型设计时,主要考虑的因素是不要产生容易出现的几种轧制缺 陷,即内多边形,壁厚不均,外表面纵向轧痕及外表面折叠,根据经验,一 般认为轧制缺陷支下面趋势有关随着壁厚/直径比(s/d),总减径率 P∑孔型椭 圆度 a 的增大,内多边形的趋势增加,随着单架减径 P∑的增大壁厚不均也增 大,轧制薄壁管金属容易挤入辊缝形成纵向轧痕,由此人们得出结论:薄壁 管应在椭圆孔型中轧制,厚壁管应在圆孔型中轧制(在 s/d,9%~12%时,必 须用圆孔)所谓椭圆孔型系指 ai-bi-1>0,而圆孔型系指 ai-bi-1<0。 孔型的几何参数有: A—孔型高度; B—孔型宽度; C—孔型顶部圆弧半径 按下式计算:R=A2+B2/4A E—偏心距,按下式计算:E=B2-A2/4A
包头钢铁职业技术学院学生毕业论文 论文题目: 张力减径的工艺原理及主要问题
专 业: 班 级: 学 生: 指导教师: 日 期:
冶金 冶金一班 李咏光 魏宁 2010 年 3 月 31 日
目录
摘要 ……………………………………………………………… 1 关键词 …………………………………………………………… 1 引言 ……………………………………………………………… 1 1 张力减径机技术的发展 …………………………………… 1 2 张力减径机的作用 ………………………………………… 1 2.1 张力减径机的形式 ………………………………………… 2 3 钢管定径、减径的工艺原理………………………………… 3 3.1 张力减径的优点、缺点 …………………………………… 3 3.2 三辊定径、减径机减径与二辊定径减径机相比…………… 4 3.3 张力径机的孔型……………………………………………… 5 3.4 张力减径机与微张力减径机的不同 ……………………… 8 3.5 管材热扩径方法 …………………………………………… 8 4 张力减径时管端偏厚的原因 ………………………………… 10 4.1 影响张力减径机管端增厚的因素 ………………………… 10 4.2 影响管内多边形的因素 …………………………………… 11 结语 ……………………………………………………………… 11 参考文献 ……………………………………………………………12
量:
………… Dn-2=Dn-3(1-δ) Dn-1=Dn-2(1-1/2δ) Dn=Dn-1
3.4:张力减径机与微张力减径机的不同 张力与微张在设备和变形原理上是完全一样的,只是在实际运用时,根据 不同的条件和要求,选择的工艺参数(张力系数)不同而已。 张力减径一般 机架数多,工艺上最大的特点是减壁减径,一般单机最大减径率大于 6.0%, 总减径率可达到 80%以上。但同时它的切头损失也非常大,因此张力减径机适 合于荒管长度 20m 以上的热轧无缝钢管机组。 微张力减径的机架数相对小,过去单机最大减径率不超过 3.5%,总减径 率小于 35%。由于张力系数不大于 0.5,只能实现等壁活减壁减劲,因此切头 损失比张力减径大大减少。同时,只要措施得当,中、厚壁管的“内六方” 可控制在较好水平。因此微张力减径机比较适用于荒管长度 不大于 15m 的热 轧无缝钢管机组。 3.5 :管材热扩径方法 随着工业技术尤其是石油与化学工业的发展,大直径无缝钢管需求量逐年 增加,尽管大型周期式轧管机组与顶管机组可以生产一部分大直径,但其设 备庞大,一次性投资高,且生产大直径薄壁管在技术上还有一定困难。管材 热径方法主要有以下几种: (1)斜轧热扩径在斜轧扩管机上进行。斜轧扩管机有两个装在箱型机架
公式:
式中 Dp——来料外径(即延伸轧制后的毛管外径); Dn——成品管热状态下的平均外径,可用下式求出: Dn=(1+a)D0=(1.013~1.017)D0 式中 a 金属热膨胀系数;
t 轧制温度;
D0 常温下成品钢管的外径。
孔型尺寸的计算方法: 1、计算平均相对压下 2、计算各架平均直径
D1=Dp(1-1/2δ) D2=D1(1-δ) D3=D2(1-δ)