数控技术论文中英文摘要
数控话题英语作文

数控话题英语作文As a major topic in the field of manufacturing, numerical control (NC) technology has played a criticalrole in modern industry. It has greatly improved the efficiency and accuracy of production processes, and has become an indispensable tool in the manufacturing industry. In this essay, I will discuss the significance of numerical control technology, its development and application, andits future prospects.First and foremost, numerical control technology has significantly improved the efficiency and precision of manufacturing processes. By using computer-aided design (CAD) and computer-aided manufacturing (CAM) systems, manufacturers are able to program machines to perform complex tasks with a high degree of accuracy. This has led to a reduction in production time and costs, as well as an increase in the quality of manufactured products. In addition, numerical control technology has enabled the automation of many manufacturing processes, leading to increased productivity and reduced labor costs.Furthermore, the development of numerical control technology has had a profound impact on various industries, including aerospace, automotive, and electronics. In the aerospace industry, for example, numerical control technology has enabled the production of complex and lightweight parts for aircraft and spacecraft. In the automotive industry, it has facilitated the mass production of vehicles with consistent quality and precision. In the electronics industry, numerical control technology has been used to manufacture intricate components for electronic devices. Overall, numerical control technology has revolutionized the way products are designed and manufactured, and has contributed to the advancement of various industries.Looking ahead, the future of numerical control technology is promising. With the rapid advancement of computer technology and the Internet of Things (IoT), numerical control systems are becoming more intelligent and interconnected. This has led to the development of smart factories, where machines and processes are connected and can communicate with each other in real time. This level of connectivity and intelligence will further improve theefficiency and flexibility of manufacturing processes, and will enable the production of highly customized and personalized products. Additionally, the integration of artificial intelligence and machine learning into numerical control systems will further enhance their capabilities, allowing for autonomous decision making and adaptive manufacturing processes.In conclusion, numerical control technology has greatly impacted the manufacturing industry, leading to increased productivity, efficiency, and precision. Its development and application have transformed various industries and have paved the way for the future of manufacturing. With the continuous advancement of technology, numerical control systems will continue to play a crucial role in the evolution of manufacturing processes and the production of high-quality products.数控技术作为制造业的重要话题,在现代工业中发挥着至关重要的作用。
数控技术专业英文介绍范文
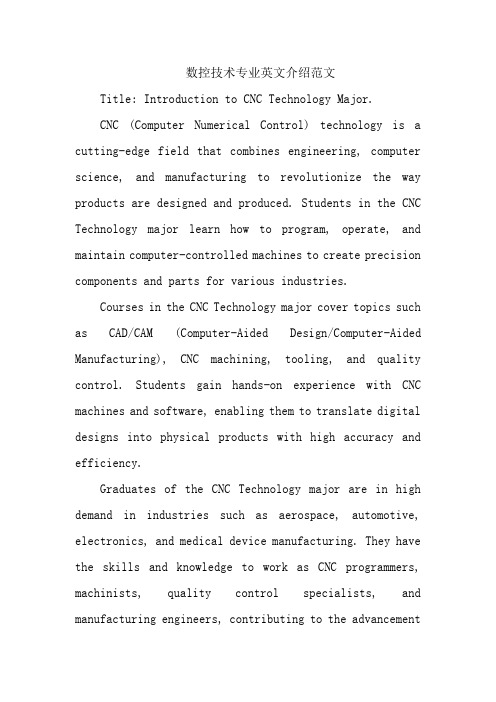
数控技术专业英文介绍范文Title: Introduction to CNC Technology Major.CNC (Computer Numerical Control) technology is a cutting-edge field that combines engineering, computer science, and manufacturing to revolutionize the way products are designed and produced. Students in the CNC Technology major learn how to program, operate, and maintain computer-controlled machines to create precision components and parts for various industries.Courses in the CNC Technology major cover topics such as CAD/CAM (Computer-Aided Design/Computer-Aided Manufacturing), CNC machining, tooling, and quality control. Students gain hands-on experience with CNC machines and software, enabling them to translate digital designs into physical products with high accuracy and efficiency.Graduates of the CNC Technology major are in high demand in industries such as aerospace, automotive, electronics, and medical device manufacturing. They have the skills and knowledge to work as CNC programmers, machinists, quality control specialists, and manufacturing engineers, contributing to the advancementof technology and innovation in manufacturing processes.By studying CNC Technology, students not only acquire technical skills but also develop problem-solving abilities, critical thinking, and attention to detail. This major prepares individuals for exciting and rewarding careers in the fast-paced world of advanced manufacturing.标题:数控技术专业介绍。
有关数控的英文作文

有关数控的英文作文1. CNC technology has revolutionized the manufacturing industry, allowing for precise and efficient production of complex parts and components.2. The use of computer-controlled machines has significantly reduced the need for manual labor in the production process, leading to increased productivity and cost savings for manufacturers.3. CNC machines are capable of performing a wide range of tasks, from cutting and drilling to milling and shaping, with high levels of accuracy and consistency.4. The programming of CNC machines requires specialized skills and knowledge, as operators must understand the machine's capabilities and limitations in order to create effective programs.5. One of the key advantages of CNC technology is itsability to produce identical parts with minimal variation, ensuring that products meet strict quality standards.6. The flexibility of CNC machines allows for rapid reconfiguration and retooling, making it easier for manufacturers to adapt to changing production requirements and market demands.7. As CNC technology continues to advance, the potential for automation and integration with other manufacturing processes is becoming increasingly feasible, leading to even greater levels of efficiency and productivity.。
数控专业的英语作文带翻译

English is the primary language for scientific and technological information exchange. By improving your English writing skills, you can access the latest technological developments, research findings, and industry trends, which will enhance your professional knowledge and expertise in numerical control.
Numerical Control Major English Writing with Translation
With the rapid development of manufacturing industry, the demand for numerical control professionals with proficient English skills is increasing. As a numerical control major student, it is essential to master professional English writing, which will benefit your future career development. In this article, we will discuss the importance of English writing for numerical control majors and provide useful tips and examples to improve English writing skills in this field.
数控技术外文文献翻译

数控技术外文文献翻译(含:英文原文及中文译文)英文原文The development trend of numerical control technology AbstractThe current trends in the development of numerical control technology and equipment in the world and the status quo of the development and industrialization of CNC equipment technology in China are briefly introduced. On this basis, we discuss the development of CNC technology and equipment in China under the new environment of China's accession to the WTO and further opening to the outside world. The importance of improving the level of China's manufacturing informatization and international competitiveness, and put forward some views on the development of China's CNC technology and equipment from both strategic and strategic aspects.The technological level and degree of modernization of the equipment industry determine the level of the entire national economy and the degree of modernization. Numerical control technology and equipment are the development of emerging high-tech industries and cutting-edge industries (such as information technology and its industries, biotechnology and its industries, aviation, aerospace, etc.) (Defense Industry Industry) enabling technology and basic equipment. Marx oncesaid that “the difference between various economic times is no t what is produced but how it is produced and what labor data it is used to produce”. Manufacturing technology and equipment are the most basic production materials for human production activities, and numerical control technology is the core technology of today's advanced manufacturing technologies and equipment. In the manufacturing industry of the world today, CNC technology is widely used to improve manufacturing capabilities and levels, and to improve the adaptability and competitiveness of dynamic markets. In addition, various industrialized countries in the world have also listed numerical control technology and numerical control equipment as strategic materials of the country. They not only take significant measures to develop their own numerical control technologies and their industries, but also have the key technology and equipment of “high-precision” numerical control. Our country adopts a policy of blockade and restriction. In short, the vigorous development of advanced manufacturing technologies centered on numerical control technology has become an important way for all developed countries in the world to accelerate economic development and improve their overall national strength and national status.Numerical control technology is a technology that uses digital information to control mechanical movement and work process. Numerical control equipment is a mechatronic product formed by thepenetration of new technologies represented by numerical control technology into traditional manufacturing industries and emerging manufacturing industries, namely, so-called digital equipment. Its technical scope covers many fields: (1) machinery manufacturing technology; (2) information processing, processing, and transmission technology; (3) automatic control technology; (4) servo drive technology;(5) sensor technology; (6) software Technology and so on. Keywords: CNC technology, machinery manufacturing, information processing, sensors1 Development Trends of Numerical Control TechnologyThe application of numerical control technology has not only brought about revolutionary changes in the traditional manufacturing industry, but also made manufacturing a symbol of industrialization. With the continuous development of numerical control technology and the expansion of application fields, he has made important contributions to the national economy and people's livelihood (IT, automotive The development of light industry, light industry, medical care, etc. is playing an increasingly important role, because the digitalization of the equipment required by these industries is a major trend of modern development. From the current trend of numerical control technology and its equipment development in the world, its main research hotspots are the following aspects [1~4].1.1 New trends in high-speed, high-precision processing technology and equipmentEfficiency and quality are the mainstays of advanced manufacturing technology. High-speed, high-precision machining technology can greatly improve efficiency, improve product quality and grade, shorten production cycle and increase market competitiveness. To this end, the Japanese Advanced Technology Research Institute will list it as one of the five major modern manufacturing technologies. The International Association of Production Engineers (CIRP) has identified it as one of the central research directions for the 21st century.In the passenger car industry, the production cycle of 300,000 vehicles per year is 40 seconds per vehicle, and multi-species processing is one of the key issues that must be addressed for car equipment. In the aviation and aerospace industries, the parts processed by them are mostly thin-walled. With thin ribs, the rigidity is poor, and the material is aluminum or aluminum alloy. These ribs and walls can be processed only when the high cutting speed and cutting force are small. Recently, the method of “hollowing out” large-size aluminum alloy billets has been used to manufacture large parts such as wings and fuselage to replace multiple parts and assembled by numerous rivets, screws, and other coupling methods to obtain strength, stiffness, and reliability of components. improve. All of these require high-speed, high-precision andhigh-flexibility for processing equipment.From the standpoint of EMO2001, the feed rate of high-speed machining centers can reach 80m/min, or even higher, and the airspeed can reach around 100m/min. At present, many automobile plants in the world, including China's Shanghai General Motors Corporation, have adopted a part of the production line consisting of a high-speed machining center to replace the combined machine tools. The HyperMach machine tool feed rate of CINCINNATI, USA is up to 60m/min, the speed is 100m/min, the acceleration is 2g, and the spindle speed has reached 60,000r/min. It takes only 30 minutes to machine a thin-walled aircraft part, and the same part takes 3h for general high-speed milling and 8h for normal milling; the spindle speed and acceleration of the twin-spindle lathe of DMG, Germany, reach 12*!000r/mm respectively. And 1g.In terms of machining accuracy, in the past 10 years, the machining accuracy of ordinary CNC machine tools has increased from 10μm to 5μm, precision machining centers have increased from 3~5μm to 1~1.5μm, and ultra-precision machining precision has begun to enter the nanometer level. (0.01μm).In terms of reliability, the MTBF value of foreign numerical control devices has reached more than 6000 hours, and the MTBF value of the servo system has reached more than 30,000 hours, showing very highreliability.In order to achieve high-speed, high-precision machining, the supporting functional components such as electric spindles and linear motors have been rapidly developed and the application fields have been further expanded.1.2 Rapid development of 5-axis simultaneous machining and compound machiningThe use of 5-axis simultaneous machining of 3D surface parts allows cutting with the best geometry of the tool, resulting in not only a high degree of finish, but also a significant increase in efficiency. It is generally considered that the efficiency of a 5-axis machine tool can be equal to 2 3-axis linkage machines. Especially when using ultra-hard material milling tools such as cubic boron nitride for high-speed milling of hardened steel parts, 5-axis simultaneous machining can be compared with 3-axis linkage. Processing to play a higher efficiency. In the past, due to the complexity of the 5-axis linkage CNC system and the host machine structure, the price was several times higher than that of the 3-axis linkage CNC machine tool, and the programming technology was more difficult, which restricted the development of 5-axis linkage machine tools.At present, due to the emergence of electric spindles, the structure of the composite spindle head that realizes 5-axis simultaneous machining isgreatly simplified, its manufacturing difficulty and cost are greatly reduced, and the price gap of the numerical control system is reduced. As a result, the development of composite spindle head type 5-axis linkage machine tools and compound machine tools (including 5-sided machine tools) has been promoted.At the EMO2001 exhibition, the new 5-axis machine tool of Nippon Machine Tool Co., Ltd. adopts a compound spindle head, which can realize the processing of four vertical planes and processing at any angle, so that 5-sided machining and 5-axis machining can be realized on the same machine tool. It can realize the processing of inclined surface and inverted cone. Germany DMG company exhibited DMUV oution series machining center, which can be processed in five-face machining and five-axis linkage in a single clamping. It can be directly or indirectly controlled by CNC system control or CAD/CAM.1.3 Intelligentization, openness, and networking have become major trends in the development of modern digital control systemsThe 21st century CNC equipment will be a certain intelligent system. The intelligent content is included in all aspects of the CNC system: in order to pursue the processing efficiency and processing quality in the intelligent, such as the process of adaptive control, process parameters automatically Generated; To improve the driving performance and the use of convenient connection intelligent, such as feed-forward control,adaptive calculation of motor parameters, automatic identification load automatic selection model, self-tuning, etc.; simplify the programming, simplify the operation of intelligent, such as smart The automatic programming, intelligent man-machine interface, etc.; as well as the contents of intelligent diagnosis, intelligent monitoring, convenient system diagnosis and maintenance.In order to solve the problems of traditional CNC system closure and industrial application of CNC application software. At present, many countries have conducted research on open numerical control systems such as NGC of the United States, OSACA of the European Community, OSEC of Japan, and ONC of China. The openness of numerical control systems has become the future of CNC systems. The so-called open CNC system is the development of CNC system can be in a unified operating platform, for machine tool manufacturers and end users, by changing, adding or cutting structure objects (CNC function), to form a series, and can be convenient to the user's special The application and technology are integrated into the control system to quickly realize open numerical control systems of different varieties and different grades to form brand-name products with distinctive personality. At present, the architecture specification, communication specification, configuration specification, operation platform, numerical control system function library and numerical control system function software development toolof open CNC system are the core of current research.Networked CNC equipment is a new bright spot in the international well-known machine tool exposition in the past two years. The networking of CNC equipment will greatly satisfy the requirements of information integration for production lines, manufacturing systems, and manufacturing companies. It is also the basic unit for realizing new manufacturing models such as agile manufacturing, virtual enterprise, and global manufacturing. Some famous domestic and foreign CNC machine tools and numerical control system manufacturing companies have introduced relevant new concepts and prototypes in the past two years. For example, at the EMO 2001 exhibition, the “Cyber Production Center” exhibited by Japan's Mazak company Mazak Production Control Center (CPC); Okuma Machine Too l Company, Japan exhibited “ITplaza” (Information Technology Plaza, IT Plaza); Open Manufacturing Environment (Open Manufacturing Environment, OME), exhibited by Siemens, Germany Etc., reflecting the trend of the development of CNC machine tools to the direction of the network.1.4 Emphasizing the Establishment of New Technology Standards and Specifications1.4.1 About Design and Development of CNC SystemsAs mentioned above, the open CNC system has better versatility, flexibility, adaptability, and expandability. The United States, theEuropean Community, and Japan have implemented strategic development plans one after another, and have conducted the open architecture system specification (OMAC). , OSACA, OSEC) research and development, the world's three largest economies in the short term carried out almost the same set of scientific plans and norms, indicating that the arrival of a new revolution in digital technology. In 2000, China began to conduct research and development of the regulatory framework for China's ONC numerical control system.1.4.2 About CNC StandardsCNC standards are a trend in the development of manufacturing informatization. The information exchange in the 50 years since the birth of CNC technology was based on the ISO 6983 standard. That is how the G and M codes describe how to process. The essential feature is the processing-oriented process. Obviously, he has been unable to meet the high speed of modern CNC technology. The need for development. For this purpose, a new CNC system standard ISO14649 (STEP-NC) is being researched and developed internationally. Its purpose is to provide a uniform data model that can describe the entire life cycle of a product without relying on a neutral mechanism of a specific system. , in order to achieve the entire manufacturing process, and even the standardization of product information in various industrial fields. The emergence of STEP-NC may be a revolution in CNC technology. It will have aprofound impact on the development of CNC technology and even the entire manufacturing industry. First, STEP-NC proposes a brand-new manufacturing concept. In the traditional manufacturing concept, NC machining programs are concentrated on a single computer. Under the new standard, NC programs can be distributed on the Internet. This is the direction of open and networked CNC technology. Secondly, STEP-NC CNC system can also greatly reduce the processing drawings (about 75%), processing program preparation time (about 35%) and processing time (about 50%).At present, European and American countries attach great importance to the research of STEP-NC, and Europe has initiated STEP-NC's IMS plan ( Participation in this program comes from 20 CAD/CAM/CAPP/CNC users, vendors and academic institutions in Europe and Japan. STEPTools of the United States is the developer of global manufacturing data exchange software. He has developed a SuperModel for the information exchange of CNC machine tools. Its goal is to describe all machining processes with a unified specification. This new data exchange format has now been validated on prototype prototypes equipped with SIEMENS, FIDIA and European OSACA-NC numerical control systems.2 Basic Estimates of China's CNC Technology and Its Industrial DevelopmentCNC technology in China started in 1958. The development process in the past 50 years can be roughly divided into three stages: the first stage from 1958 to 1979, which is the closed development stage. At this stage, the development of numerical control technology is relatively slow due to the limitations of foreign technology and China's basic conditions. The second stage is the introduction of technology during the “sixth and fifth” periods of the country, the “seventh five-year plan” period, and the “eighth five-year plan period,”and it will be digested and absorbed to initially establish the stage of the national production system. At this stage, due to the reform and opening up and the country’s attention, as well as the improvement of the research and development environment an d the international environment, China’s CNC technology has made great progress in research, development, and localization of products. The third stage is the implementation of industrialization research in the later period of the "Eighth Five-Year Plan" and the "Ninth Five-Year Plan" period of the country, entering the stage of market competition. At this stage, the industrialization of domestically-manufactured CNC equipment has achieved its essenceSexual progress. At the end of the “Ninth Five-Year Plan” period, the domestic market share of domestic CNC machine tools reached 50%, and the number of domestically-manufactured numerical control systems (pervasive models) also reached 10%.Looking at the development process of CNC technology in China in the past 50 years, especially after four five-year plans, the overall results are as follows:a. It lays the foundation for the development of CNC technology and basically masters modern CNC technology. China has now basically mastered the basic technologies from numerical control systems, servo drives, numerical control mainframes, special planes and their accessories. Most of these technologies already have the basis for commercial development. Some technologies have been commercialized and industrialized.b. Initially formed a CNC industrial base. Based on the research results and the commercialization of some technologies, we have established numerical control system production plants such as Huazhong Numerical Control and Aerospace Numerical Control which have mass production capabilities. Lanzhou Electric Machinery Factory, Huazhong Numerical Control and a number of servo systems and servo motor manufacturers, as well as a number of CNC machine manufacturers such as Beijing No. 1 Machine Tool Plant and Jinan No. 1 Machine Tool Plant. These production plants have basically formed China's CNC industrial base.c. Established a basic team of CNC research, development and management talents.Although significant progress has been made in the research, development, and industrialization of numerical control technology, we must also soberly realize that the research and development of high-end numerical control technologies in China, especially the status quo of the technological level of industrialization and the actual needs of China There is a big gap. Although our country's development speed is very fast in the vertical direction, the horizontal ratio (compared with foreign countries) not only has a gap in the level of technology, but also has a gap in the development speed in certain aspects, that is, the gap in the technological level of some highly sophisticated numerical control equipment has expanded. From the international point of view, the estimated level of China's numerical control technology and industrialization is roughly as follows:a. On the technical level, it will be about 10 to 15 years behind the advanced level in foreign countries, and it will be even bigger in terms of sophisticated technology.b. At the industrialization level, the market share is low, the variety coverage is small, and scale production has not yet been established; the specialized production level of functional components and the complete set capacity are low; the appearance quality is relatively poor; the reliability is not high, and the degree of commercialization is insufficient; The domestic CNC system has not established its own brand effect, andthe user's confidence is insufficient.c. On the ability of sustainable development, the research and development and engineering capabilities of pre-competitive numerical control technology are weak; the application of numerical control technology is not strong; the research and formulation of related standard specifications is lagging behind.The main reasons for analyzing the above gaps are as follows:a. Awareness. Insufficient understanding of the arduous, complex and long-term characteristics of the domestic CNC industry process; Insufficient estimates of market irregularities, foreign blockades, killings, and systems; and insufficient analysis of the application level and capabilities of CNC technology in China.b. Systematic aspects. From the point of view of technology, attention has been paid to the issue of CNC industrialization. It has been a time to consider the issue of CNC industrialization from the perspectives of system and industry chain; there is no complete supporting system of high-quality supporting systems, perfect training, and service networks. .c. Mechanisms. Bad mechanisms have led to brain drain, which in turn has restricted technological and technological route innovations and product innovations, and has constrained the effective implementation of planning. It is often planned to be ideal and difficult to implement.d. Technical aspects. Enterprises have little ability to independentlyinnovate in technology, and the engineering ability of core technologies is not strong. The standard of machine tools is backward, the level is low, and the new standard of CNC system is not enough.3 Strategic Thinking on the Development of CNC Technology and Industrialization in China3.1 Strategic ConsiderationsChina is a manufacturing country, and we must try to accept the transfer of the front-end rather than the back-end in the industrial transfer of the world. That is to master the advanced manufacturing core technologies, otherwise, in the new round of international industrial restructuring, China's manufacturing industry will further “empty core”. At the expense of resources, the environment, and the market, we may obtain only the international "processing centers" and "assembly centers" in the world's new economic structure, rather than the status of manufacturing centers that master core technologies. This will seriously affect our country. The development of modern manufacturing.We should pay attention to numerical control technology and industrial issues from the perspective of national security strategy. First of all, we must look at social security because manufacturing industry is the industry with the largest number of employed people in China. Manufacturing industry development can not only improve the people’s living standards, but also ease the country’s The pressure of employmentguarantees social stability. Secondly, from the perspective of national defense security, Western developed countries classify high-precision numerical control products as national strategic materials and implement embargoes and restrictions on China. The “Toshiba Incident” and the “Cox Report” "This is the best illustration.3.2 Development StrategyFrom the perspective of China’s basic national conditions, taking the country’s strategic needs and the market demand of the national economy as the guide, and aiming at improving the comprehensive competitiveness and industrialization le vel of China’s manufacturing equipment industry, we can use systematic methods to choose to dominate the early 21st century in China. The key technologies for the development and upgrade of the manufacturing equipment industry and supporting technologies and supporting technologies for supporting industrialization development are the contents of research and development and the leap-forward development of the manufacturing equipment industry. Emphasizing the market demand as the orientation, that is, taking CNC terminal products as the mainstay, and driving the CNC industry with complete machines (such as large-scale CNC lathes, milling machines, high-speed, high-precision and high-performance CNC machine tools, typical digital machines, key equipment of key industries, etc.). development of. The focus is on the reliability and production scale of CNC systems andrelated functional components (digital servos and motors, high-speed spindle systems and accessories for new equipment, etc.). Without scale, there will be no high-reliability products; without scale, there will be no cheap and competitive products; of course, CNC equipment without scale in China will be difficult to come to the fore. In the research and development of high-precision equipment, we must emphasize the close integration of production, learning, research, and end-users, and aim at “doing, using, and selling off” as a goal, and implement national research on the will of the country to solve the urgent need of the country. . Before the competition, CNC technology emphasizes innovation, emphasizes research and development of technologies and products with independent intellectual property rights, and lays a foundation for the sustainable development of China's CNC industry, equipment manufacturing industry, and even the entire manufacturing industry.中文译文数控技术的发展趋势摘要本文简要介绍了当今世界数控技术及装备发展的趋势及我国数控装备技术发展和产业化的现状, 在此基础上讨论了在我国加入WTO 和对外开放进一步深化的新环境下, 发展我国数控技术及装备、提高我国制造业信息化水平和国际竞争能力的重要性, 并从战略和策略两个层面提出了发展我国数控技术及装备的几点看法。
关于数控技术的英语作文

关于数控技术的英语作文英文回答:Computer Numerical Control (CNC) Technology.Computer numerical control (CNC) technology is a method of automated machining that uses a computer to control the movement of a machine tool. This allows for precise and repeatable movements, which are essential for many manufacturing processes.CNC machines are used in a wide variety of industries, including aerospace, automotive, and medical. They are capable of producing complex parts with tight tolerances. CNC machines can also be used to automate repetitive tasks, which can save time and money.There are two main types of CNC machines:Open-loop CNC machines use a computer to generate thecommands that control the machine tool. However, the computer does not receive any feedback from the machine tool, so it cannot correct for errors.Closed-loop CNC machines use a computer to generate the commands that control the machine tool, and they also receive feedback from the machine tool. This allows the computer to correct for errors, which results in greater accuracy and precision.CNC machines are a powerful tool that can be used to produce complex parts with tight tolerances. They are also capable of automating repetitive tasks, which can save time and money.中文回答:数控技术。
数控技术专业英文介绍范文

数控技术专业英文介绍范文English: The CNC technology major is designed to train students in the principles and practical skills of computer numerical control (CNC) machining. Students will learn how to use computer programs to control and operate machines such as lathes, milling machines, and grinders to produce precision parts and components. They will also study topics such as machining strategies, tooling selection, blueprint reading, and quality control. In addition to hands-on experience in CNC programming and machine operation, students will also receive training in CAD/CAM software, CNC equipment maintenance, and troubleshooting techniques. Graduates of this program will be well-equipped to pursue careers in industries such as aerospace, automotive, medical device manufacturing, and more, where precision machining is essential for producing high-quality products.中文翻译: 数控技术专业旨在培养学生掌握计算机数控(CNC)加工的原理和实践技能。
数控论文带英文版

数控论文带英文版第一篇:数控论文带英文版Development and maintenance of CNC1946 On the birth of the world's first electronic computer, which indicates that human beings created to enhance and replace the mental part of the tool.It is human in the agricultural, industrial society created a tool that is enhanced compared to manual qualitative leap, he entered the information society for human foundation.Half a century, and the core of computer-driven information technology, both through the TV, modern communications, improve the quality of human life, but also improve productivity fast forward, creating a history of human civilization, the production history of the era.The rapid development of information technology led directly to the arrival of the knowledge economy.In 1952, computer technology applied to the machine.Born in the United States first CNC machine puters and control technology in the application of machinery equipment manufacturing industry within the century's most significant technological advances.Since then, the conventional machine produced a qualitative change.Nearly half a century, has undergone two phases of CNC machine tools and the development of six generations.(1)Numerical control(NC)phase(1952-1970 years) early computing speed is low, which was affected scientific computing and data processing is not large, can not meet the requirements of real-time control machine tools.People have used digital logic circuits, “ride” into a dedicated computer as numerical control machine tool system, known as the hardware connection NC(HARD WIREDNC), referred to as NC(NC).With thedevelopment of components, at this stage after three generations, that in 1952 the first generationthe transistor;1965, the third generationpresent)In 1970, GM has a small computer and into mass production there.Its operation faster than the fifties and sixties have increased significantly, more than a special “ride” into a dedicated computer, low cost, high reliability.So it came as a CNC porting the core components, entered a computer numerical control(CNC)stage.By 1971, INTEL Corporation in the United States the world's first computer of the two core componentsthe microprocessor;1990, the sixth generationBASED).CNC system nearly five decades gone through two stages six generation of development, but development to the fifth generation only after a fundamental solution to the reliability is low, the price is extremely expensive, extremely convenient application is very critical issue.Thus, even in industrialized countries, large-scale numerical control system has been applied and popularity in the late seventies early eighties after the thing, that is numerical control technology after nearly three decades of development before wider application to.Abroad has been renamed as early as the computer numerical control(ie CNC), while China is still often called numerical control(NC).So we talk about everyday, “NC” in essence is that “computer numerical control” of C machine tool numerical control system is the core component, therefore, the maintenance of CNC machine tool numerical control system is mainly to maintain.After a NC system for a longer period of use, performance of electronic components to aging or damaged, and some mechanical parts especially, to try to extend the lifetime of components and parts wear cycle, to prevent all kinds of failures, particularly fatal accidents theoccurrence of the numerical control system must be routine maintenance.T o sum up, pay attention to the following aspects.1 NC system maintenance formulate rulesRegulations according to the characteristics of various components to determine their maintenance regulations.Expressly provided, such as what areas need cleaning every day(such as CNC system input / output unit-optical reading machines for cleaning, inspection is well-oiled machine structural parts, etc.), which parts should be regularly checked or replaced(such as brush DC servo motors and commutator should be checked once a month).(2)As less as possible open CNC ark and high voltage ark of the doorBecause in machining workshop in the air of general contain oil mist, dust and even metal powder.Once they fall within the NC system or electrical components on printed circuit, easily lead to decreased insulation resistance between components, and even lead to damage to components and printed circuits.Some users in the summer to make long-term work overload CNC system, CNC cabinet door open to heat, which is not desirable kind of approach will eventually lead to accelerated damage to the CNC system.The correct way is to reduce the numerical control system of the external ambient temperature.Therefore, there should be a strict requirement, unless the necessary adjustments and repairs, just open the doors is not allowed, but not allowed to open doors when in use.Regular cleaning the ark of the numerical control heat ventilation systemShould every day to check on the numerical control system each cooling fan is functioning properly, should inspect working environment condition, every half an year or quarterly review of a duct filter whether jam phenomenon.If excessive dust build-upInternet filter, the need for timely clean-up, otherwise it will cause the temperature inside the high numerical control system(generally not exceed 55 ℃), resulting in overheating or NC alarm system does not work reliably.4 CNC systems are often used to monitor voltage produced by FANUC CNC system, allowing the grid voltage rating of 85% to 110% of range fluctuations.If you exceed this range, it will cause the system not working properly, or even cause damage to electronic components within the NC system.5 periodic replacement of memory battery FANUC CNC production company within the system memory in two ways:(1)No batteries to keep the magnetic bubble memory.(2)the need to maintain the CMOS RAM with battery device is not powered on CNC system in order to maintain the contents of the storage period, with internal rechargeable battery to maintain the circuit, in the NC system is powered by the +5 V power supply through a diode to the CMOS RAM power, and can charge the rechargeable battery;cut off power when the numerical control system is replaced by a battery to maintain the information in CMOS RAM, under normal circumstances, even if the battery has not yet expired, the battery should be replaced once a year, in order to ensure that the system can work properly.In addition, we must note that the battery replacement should be carried out under the NC system power C long-term maintenance when not in numerical order to improve system utilization and reduce the numerical control system failure, CNC machine tools should be used at full capacity, and not long idle, for some reason, resulting in long idle CNC system, in order to numerical control system to avoid damage, please note the following two points:(1)should always power to the CNC system, especially in high humidity environment of therainy season and even more so, lock the machine does not move in the case(that is, the servo motor does not turn time), let dry run CNC e of electrical components to disperse their heat moisture within the NC system, to ensure stable and reliable performance of electronic devices, proved in the air humidity areas, power is to reduce the failure rate is often an effective measure.(2)CNC machine tool feed servo drives using DC and DC servo spindle drive, brush should be removed from the DC motor, so as not due to chemical corrosion, the commutator surface corrosion, resulting in change to the performance deterioration, and even entire motor damage.At present, the field of sheet metal stamping, CNC punching machine / CNC turret punch press with its fast, high precision machining, mold versatile, flexible products, etc., are widely er in choosing a quality mold, its use and maintenance of the level of direct impact to the workpiece machining quality and mold life.Mold control equipment is also an important part of operating costs.First,ensure the best mold clearanceMould clearance is to point to the punch into the next model, the sum of the clearance between the sides.It and thickness, material and the stamping process and suitable mould clearance, can guarantee good punching quality, reduce burr and collapse and keep the sheet metal level off, effectively prevent take material, prolong die life.Through the examination of stamping waste, we can determine whether appropriate mould clearance.If too much clearance waste will be rough rolling fractures and smaller light face.The greater the clearance, fractures and light the viewpoint of the formation of surface and the more they can form punching edge and fracture, appear even a thin rim bumps.Conversely, if the clearance is too small, waste will besmall Angle fractures and larger light face.When slot, step blunt, cutting local stamping, lateral force will make the punch deflection and cause unilateral gap is too small, sometimes edge migration will scratch lower die, causing the lower die quickly wear.Mould to best clearance stamping, waste of fractures and bright surface with the same Angle, and overlap each other, so that can make the cutting force minimum, punching the burr was very small.Second, timely grinding can effectively extend the life of the mold if too large of a workpiece or stamping burrs generated when abnormal noise may die passivation.Check the punch and the die, when its blade edges have a radius of approximately 0.10mm wear arc, it is necessary sharpening of.Practice has shown that frequent small amounts of sharpening rather than waiting until non-grinding mill can not be again when, not only to maintain good quality of the workpiece, reducing the blanking force, but die life can be extended more than doubled.In addition to knowing when to die grinding, the grinding master the correct method is especially important.Mold grinding procedure is as follows:1)grinding, it will punch a vertical grip on the surface grinder's magnetic chuck or fixture within the V-groove, each grinding capacity of 0.03 ~ 0.05mm, repeat until the punch grinding sharp, the maximum amount of grinding is generally 0.1 ~ 0.3mm.2)the use of sintered aluminum oxide grinding wheel, the hardness D ~ J, grit sizes 46 to 60, preferably for high-speed steel grinding wheel.3)When the grinding force or mold near the wheel, add coolant to prevent overheating and cracking the mold or annealing, should be required in accordance with the manufacturer of high quality multi-purpose coolant.4)The amount of feed wheel down 0.03 ~ 0.08 mm, lateral feed rate0.13 ~ 0.25 mm, lateral feed rate 2.5 ~ 3.8m/min.5)After grinding, oil stone polished edge, remove the burr, and grind the radius of 0.03 ~ 0.05 mm round, to prevent edge cracking.6)punch to the magnetic treatment and sprayed with oil to prevent rust.Third, the elimination and reduction of adhesive material way because when the pressure and heat stamping, sheet metal fine particles will bond to the surface of the punch, resulting in poor quality punching.Removal of binder used fine whetstone grinding, sanding should be directed to the direction of movement with the same punch, so the light will avoid the generation of further binder.Do not use gauze and other coarse grinding, to avoid the punch surface is more rough and more prone to sticky material.Reasonable die clearance, good stamping process, and the necessary lubrication sheet, will reduce the production of sticky material.Prevent overheating, the general lubrication of the way, this will reduce the friction.If you can not waste lubricating or rebound occurs, may take the following approach: alternate punch than the same size turns punching,Can make its repeated in before use have long cooling time.Overheating will use all die.Through the programming control changing mould, the interrupt their long time of repetition of work, or reduce its pressing frequency.Four, blunt is when the deformation of sheet metal porous to prevent measuresIf in a rush on board a porous, due to the accumulation of shear stress plank cannot maintain level.Every time punching, around the hole material will down deformation, causing the surface appears on the sheet metal tensile stress, and under the surface have compressive stress.For a small amount of punching, and its effect is not obvious, but when punching quantity is increased, the pull, compressive stress somewhere inaccumulation, until materials.Eliminate such deformation of a method is: to every one KongChong cut, and then returns to the rest of the punching holes.So although also can produce stress, but easing in the same direction order stamping of stress at accumulation, also can make the two groups before and after the stress of offset each other holes, so as to prevent the deformation of sheet metal.Five, try to avoid cutting through the narrow strip materialWhen the used for cutting width of less than in the process of sheet metal sheet thickness, lateral force for and make the punch to bending deformation, make side of the gap is too small or wear is intensified, serious scratch when the mould, make fluctuation mode and damage.Suggestions don't step blunt width of less than 2.5 times the thickness of the narrow a sheet metal sheet.Cutting through the narrow strip material, sheet metal tend to turn into the mode of open, and not be completely cut off, and even wedge dies profile.If can't avoid the above situation, the proposed use output slabs supported the role of the punch fully guided mold.Six, the punch surface hardening and the applicable scopeAlthough heat treatment and surface coating can improve the punch surface properties, but is not the solution to the problems and prolong die life is pressing the general method.Generally speaking, the coating surface hardness and improve the punch that side lubricity improved, but in large tonnage, hard materials stamping, these advantages in about 1000 times after stamping and disappeared.According to the following circumstance can use surface hardening the punch: Blunt soft or sticky materials(such as aluminum);Blunt thin non-abrasive materials(such as glass epoxypieces);Blunt thin hard material(such as stainless steel);Frequent point blunt;Abnormal lubrication.Surface hardening usually adopts of titanium coating and seepage nitrogen, method, its surface hardening layer thickness for 12 ~ 60 μ m molecular structure, it is a part of the matrix punch, and not only is the coating.Surface hardening of the mould can press usually way further.Through the surface hardening will lower mould in the stainless steel plate wear behavior, but can not prolong its service life, and the appropriate and timely lubrication, according to procedures, burrs, is the effective way.Seven, CNC turret punch die a neutral is bad for the overhaulIf a punch mould to neutral is bad, cause mould fast passivation, workpiece machining quality is poor, can the following maintenance: Check the level of the machine tool, when necessary to adjust;Check and lubrication of model hole on the wheel and the direction key, if there is damage timely repair;Clean the next mould seat, so as to lower die accurate installation, check and its key or the keyway wear and, when necessary, to change;Use the special mandrel calibration mould location, such as a deviation adjust in time.The contents of the situation is usually concerned, in view of the press and the concrete types die specifications are different, the user should combine the actual to know and summarizing the experience, and displays the best use of the mould performance.数控的发展及设备维护浅谈1946年诞生了世界上第一台电子计算机,这表明人类创造了可增强和部分代替脑力劳动的工具。
(数控加工)机械类数控外文翻译外文文献英文文献数控
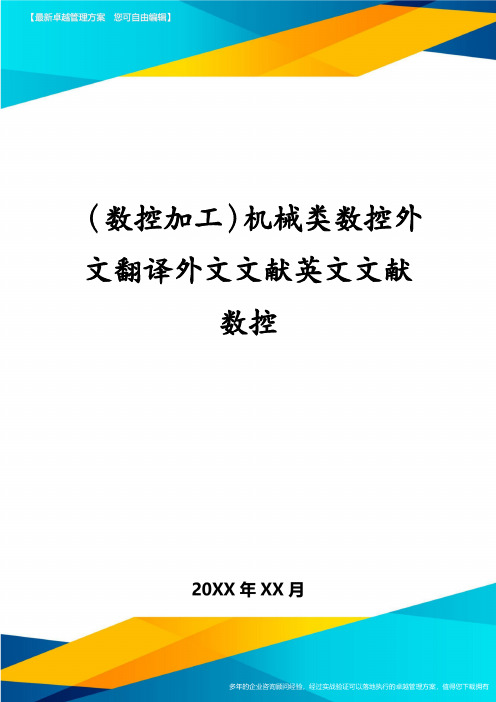
(数控加工)机械类数控外文翻译外文文献英文文献数控NumericalControlOneofthemostfundamentalconceptsintheareaofadvancedmanufacturingte chnologiesisnumericalcontrol(NC).PriortotheadventofNC,allmachinetools weremanualoperatedandcontrolled.Amongthemanylimitationsassociatedwith manualcontrolmachinetools,perhapsnoneismoreprominentthanthelimitation ofoperatorskills.Withmanualcontrol,thequalityoftheproductisdirectlyre latedtoandlimitedtotheskillsoftheoperator.Numericalcontrolrepresentst hefirstmajorstepawayfromhumancontrolofmachinetools.Numericalcontrolmeansthecontrolofmachinetoolsandothermanufacturin gsystemsthoughtheuseofprerecorded,writtensymbolicinstructions.Rathert hanoperatingamachinetool,anNCtechnicianwritesaprogramthatissuesoperat ionalinstructionstothemachinetool,Foramachinetooltobenumericallycontr olled,itmustbeinterfacedwithadeviceforacceptinganddecodingthep2ogramm edinstructions,knownasareader.Numericalcontrolwasdevelopedtoovercomethelimitationofhumanoperato r,andithasdoneso.Numericalcontrolmachinesaremoreaccuratethanmanuallyo peratedmachines,theycanproducepartsmoreuniformly,theyarefaster,andthe long-runtoolingcostsarelower.ThedevelopmentofNCledtothedevelopmentofs everalotherinnovationsinmanufacturingtechnology:1.Electricaldischargemachining.sercutting.3.Electronbeamwelding.Numericalcontrolhasalsomademachinetoolsmoreversatilethantheirmanuallyoperatedpredecessors.AnNCmachinetoolcanautomaticallyproduceawidev arietyofpar4s,eachinvolvinganassortmentofundertaketheproductionofprod uctsthatwouldnothavebeenfeasiblefromaneconomicperspectiveusingmanuall ycontrolledmachinetoolsandprocesses.Likesomanyadvancedtechnologies,NCwasborninthelaboratoriesoftheMas sachusettsInstituteofTechnology.TheconceptofNCwasdevelopedintheearly1 950swithfundingprovidedbytheU.SAirForce.Initsearlieststages,NCmachine swereabletomakestraightcutsefficientlyandeffectively.However,curvedpathswereaproblembecausethemachinetoolhadtobeprogra mmedtoundertakeaseriesofhorizontalandverticalstepstoproduceacurve.The shorteristhestraightlinesmakingupthestep,thesmootheris4hecurve.Eachli nesegmentinthestepshadtobecalculated.Thisproblemledtothedevelopmentin1959oftheAutomaticallyProgrammedT ools(APT)languageforNCthatusesstatementssimilartoEnglishlanguagetodef inethepartgeometry,describethecuttingtoolconfiguration,andspecifythen ecessarymotions.ThedevelopmentoftheAPTlanguagewasamajorstepforwardint hefurtherdevelopmentofNCtechnology.TheoriginalNCsystemwerevastlydiffe rentfromthoseusedpunchedpaper,whichwaslatertoreplacedbymagneticplasti ctape.Atapereaderwasusedtointerprettheinstructionswrittenonthetapefor themachine.Together,all/fthisrepresentedgiantstepforwardinthecontrolo fmachinetools.However,therewereanumberofproblemswithNCatthispointinit sdevelopment.Amajorproblemwasthefragilityofthepunchedpapertapemedium.Itwascomm onforthepapercontainingtheprogrammedinstructionstobreakortearduringam achiningprocess,Thisproblemwasexacerbatedbythefactthateachsuccessivet imeapartwasproducedonamachinetool,thepapertapecarryingtheprogrammedin structionshadtorerunthoughtthereader.Ifitwasnecessarytoproduce100copi esofagivenpart,itwasalsonecessarytorunthepapertapethoughtthereader100 separatetimes.Fragilepapertapessimplycouldnotwithstandtherigorsofshop floorenvironmentandthiskindofrepeateduse.Thisledtothedevelopmentofaspecialmagnetictape.Whereasthepapertape carriedtheprogrammedinstructionsasaseriesofholespunchedinthetape,theT hismostimportantofthesewasthatitwasdifficultorimpossibletochangethein structionsenteredonthetape.Tomakeeventhemostminoradjustmentsinaprogra mofinstructions,itwasnecessarytointerruptmachiningoperationsandmakean ewtape.Itwasalsostillnecessarytorunthetapethoughtthereaderasmanytimes astherewerepartstobeproduced.Fortunately,computertechnologybecomearea lityandsoonsolvedtheproblemsofNC,associatedwithpunchedpaperandplastic tape.Thedevelopmentofaconceptknownasnumericalcontrol(DNC)solvethepaper andplastictapeproblemsassociatedwithnumericalcontrolbysimplyeliminati ngtapeasthemediumforcarryingtheprogrammedinstructions.Indirectnumeric alcontrol,machinetoolsaretied,viaadatatransmissionlink,toahostcompute randfedtothemachinetoolasneededviathedatatransmissionlinkage.Directnumericalcontrolrepresentedamajorstepforwardoverpunchedtapeandplasticta pe.However,itissubjecttothesamelimitationasalltechnologiesthatdependo nahostcomputer.Whenthehostcomputergoesdown,themachinetoolsalsoexperie ncedowntime.Thisproblemledtothedevelopmentofcomputernumericalcontrol.Thedevelopmentofthemicroprocessorallowedforthedevelopmentofprogra mmablelogiccontrollers(PLC)andmicrocomputers.Thesetwotechnologiesallo wedforthedevelopmentofcomputernumericalcontrol(CNC).WithCNC,eachmachi netoolhasaPLCoramicrocomputerthatservesthesamepurpose.Thisallowsprogr Csolvedtheproblems associateddowntimeofthehostcomputer,butitintroducedanotherproblemknow nasdatamanagement.Thesameprogrammightbeloadedontendifferentmicrocompu terswithnocommunicationamongthem.Thisproblemisintheprocessofbeingsolv edbylocalareanetworksthatconnectDigitalSignalProcessorsTherearenumeroussituationswhereanalogsignalstobeprocessedinmanywa ys,likefilteringandspectralanalysis,Designinganaloghardwaretoperformt hesefunctionsispossiblebuthasbecomelessandpractical,duetoincreasedper formancerequirements,flexibilityneeds,andtheneedtocutdownondevelopmen t/testingtime.Itisinotherwordsdifficultpmdesignanaloghardwareanalysis ofsignals.Theactofsamplingansignalintothehatarespecialisedforembeddedsignal processingoperations,andsuchaprocessoriscalledaDSP,whichstandsforDigi talSignalProcessor.TodaytherearehundredsofDSPfamiliesfromasmanymanufacturers,eachonedesignedforaparticularprice/performance/usagegroup.Man yofthelargestmanufacturers,likeTexasInstrumentsandMotorola,offerboths pecialisedDSP’sforcertainfieldslikemotor-controlormodems,andgeneralh igh-performanceDSP’sthatcanperformbroadrangesofprocessingtasks.Devel opmentkitsan`softwarearealsoavailable,andtherearecompaniesmakingsoftw aredevelopmenttoolsforDSP’sthatallowstheprogrammertoimplementcomplex processingalgorithmsusingsimple“drag‘n’drop”methodologies.DSP’smoreorlessfallintotwocategoriesdependingontheunderlyingarch itecture-fixed-pointandfloating-point.Thefixed-pointdevicesgenerallyo perateon16-bitwords,whilethefloating-pointdevicesoperateon32-40bitsfl oating-pointwords.Needlesstosay,thefixed-pointdevicesaregenerallychea per.Anotherimportantarchitecturaldifferenceisthatfixed-pointprocessor stendtohaveanaccumulatorarchitecture,withonlyone“generalpurpose”reg ister,makingthemquitetrickytoprogramandmoreimportantly,makingC-compil ersinherentlyinefficient.Floating-pointDSP’sbehavemorelikecommongene ral-purposeCPU’s,withregister-files.TherearethousandsofdifferentDSP’sonthemarket,anditisdifficulttas kfindingthemostsuitableDSPforaproject.Thebestwayisprobablytosetupacon straintandwishlist,andtrytocomparetheprocessorsfromthebiggestmanufact urersagainstit.The“bigfour”manufacturersofDSPs:TexasInstruments,Motorola,AT&Ta ndAnalogDevices.Digital-to-analogconversionInthecaseofMPEG-Audiodecoding,digitalcompresseddataisfedintotheDS Pwhichperformsthedecoding,thenthedecodedsampleshavetobeconvertedbacki ntotheanalogdomain,andtheresultingsignalfedanamplifierorsimilaraudioe quipment.Thisdigitaltoanalogconversion(DCA)isperformedbyacircuitwitht hesamename&DifferentDCA’sprovidedifferentperformanceandquality,asmea suredbyTHD(Totalharmonicdistortion),numberofbits,linearity,speed,filt ercharacteristicsandotherthings.TheTMS320familyDQPofTexasInstrumentsTheTLS320familyconsistsoffixed-point,floating-point,multiprocesso rdigitalsignalprocessors(D[Ps),andfoxed-pointDSPcontrollers.TMS320DSP haveanarchitecturedesignedspecificallyforreal-timesignalprocessing.Th e’F/C240isanumberofthe’C2000DSPplatform,andisoptimizedforcontrolapp lications.The’C24xseriesofDSPcontrollerscombinesthisreal-timeprocess ingcapabilitywithcontrollerperipheralstocreateanidealsolutionforcontr olsystemapplications.ThefollowingcharacteristicsmaketheTMS320familyth erightchoiceforawiderangeofprocessingapplications:---Veryflexibleinstructionset---Inherentoperationalflexibility---High-speedperformance---Innovativeparallelarchitecture---CosteffectivenessDeviceswithinagenerationoftheTMS320familyhavethesameCPUstructure butdifferenton-chipmemoryandperipheralconfigurations.Spin-offdevicesu senewcombinationsofOn-chipmemoryandperipheralstosatisfyawiderangeofne edsintheworldwideelectronicsmarket.Byintegratingmemoryandperipheralso ntoasinglechip,TMS320devicesreducesystemcostsandsavecircuitboardspace .The16-bit,fixed-pointDSPcoreofthe‘C24xdevicesprovidesanalogdesi gnersadigitalsolutionthatdoesnotsacrificetheprecisionandperformanceof theirsystemperformancecanbeenhancedthroughtheuseofadvancedcontrolalgo rithmsfortechniquessuchasadaptivecontrol,Kalmanfiltering,andstatecont rol.The‘C24xDSPcontrollerofferreliabilityandprogrammability.Analogco ntrolsystems,ontheotherhand,arehardwiredsolutionsandcanexperienceperf ormancedegradationduetoaging,componenttolerance,anddrift.Thehigh-speedcentralprocessingunit(CPU)allowsthedigitaldesignert oprocessalgorithmsinrealtimeratherthanapproximateresultswithlook-upta bles.TheinstructionsetoftheseDSPcontrollers,whichincorporatesbothsign alprocessinginstructionsandgeneral-purposecontrolfunctions,coupledwit htheextensivedevelopmenttimeandprovidesthesameeaseofuseastraditional8 -and16-bitmicrocontrollers.Theinstructionsetalsoallowsyoutoretainyour softwareinvestmentwhenmovingfromothergeneral-purpose‘C2xxgeneration, sourcecodecompatiblewiththe’C2xgeneration,andupwardlysourcecodecompa tiblewiththe‘C5xgenerationofDSPsfromTexasInstruments.The‘C24xarchitectureisalsowell-suitedforprocessingcontrolsignal s.Itusesa16-bitwordlengthalongwith32-bitregistersforstoringintermedia teresults,andhastwohardwareshiftersavailabletoscalenumbersindependent lyoftheCPU.Thiscombinationminimizesquantizationandtruncationerrors,an dincreasesp2ocessingpowerforadditionalfunctions.Suchfunctionsmightinc ludeanotchfilterthatcouldcancelmechanicalresonancesinasystemoranestim ationtechniquethatcouldeliminatestatesensorsinasystem.The‘C24xDSPcontrollerstakeadvantageofansetofperipheralfunctions thatallowTexasInstrumentstoquicklyconfigurevariousseriesmembersfordif ferentprice/performancepointsorforapplicationoptimization.Thislibraryofbothdigitalandmixed-signalperipheralsincludes:---Timers---Serialcommunicationsports(SCI,SPI)---Analog-to-digitalconverters(ADC)---Eventmanager---Systemprotection,suchaslow-voltageandwatchdogtimerTheDSPcontrollerperipherallibraryiscontinuallygrowingandchanging tosuittheoftomorrow’sembeddedcontrolmarketplace.TheTMS320F/C240isthefirststandarddeviceintroducedinthe‘24xserie sofDSPcontrollers.Itsetsthestandardforasingle-chipdigitalmotorcontrol ler.The‘240canexecute20MIPS.Almostallinstructionsareexecutedinasimpl ecycleof50ns.Thishighperformanceallowsreal-timeexecutionofverycomple8controlalgorithms,suchasadaptivecontrolandKalmanfilters.Veryhighsampl ingratescanalsobeusedtominimizeloopdelays.The‘240hasthearchitecturalfeaturesnecessaryforhigh-speedsignalp rocessinganddigitalcontrolfunctions,andithastheperipheralsneededtopro videasingle-chipsolutionformotorcontrolapplications.The‘240ismanufac turedusingsubmicronCMOStechnology,achievingalogpowerdissipationrating.A lsoincludedareseveralpower-downmodesforfurtherpowersavings.Someapplic ationsthatbenefitfromtheadvancedprocessingpowerofthe‘240include: ---Industrialmotordrives---Powerinvertersandcontrollers---Automotivesystems,suchaselectronicpowersteering,antilockbrake s,andclimatecontrol---ApplianceandHVACblower/compressormotorcontrols---Printers,copiers,andotherofficeproducts---Tapedrives,magneticopticaldrives,andothermassstorageproducts---RoboticandCNCmillingmachinesTofunctionasasystemmanager,aDSPmusthaverobuston-chipI/Oandotherp eripherals.Theeventmanagerofthe‘240isunlikeanyotheravailableonaDSP.T hisapplication-optimizedperipheralunit,coupledwiththehighperformanceD SPcore,enablestheuseofadvancedcontroltechniquesforhigh-precisionandhi gh-efficiencyfullvariable-speedcontrolofallmotortypes.Includeintheeve ntmanagerarespecialpulse-widthmodulation(PWM)generationfunctions,suchasaprogrammabledead-bandfunctionandaspacevectorPWMstatemachinefor3-ph asemotorsthatprovidesstate-of-the-artmaximumefficiencyintheswitchingo fpowertransistors.Thereindependentupdowntimers,eachwithit’sowncompareregister,sup portthegenerationofasymmetric(noncentered)aswellassymmetric(centered) PWMwaveforms.Open-LoopandClosed-LoopControlOpen-loopControlSystemsThewordautomaticimpliesthatthereisacertainamountofsophistication inthecontrolsystem.Byautomatic,itgenerallymeansThatthesystemisusually capableofadaptingtoavarietyofoperatingconditionsandisabletorespondtoa classofinputssatisfactorily.However,notanytypeofcontrolsystemhastheau ually,theautomaticfeatureisachievedbyfeed.gthefeedbackstructure,itiscalledanopen-loopsystem,whichisthesimp lestandmosteconomicaltypeofcontrolsystem.inaccuracyliesinthefactthato nemaynotknowtheexactcharacteristicsofthefurther,whichhasadefinitebear ingontheindoortemperature.Thisalcopointstoanimportantdisadvantageofth eperformanceofanopen-loopcontrolsystem,inthatthesystemisnotcapableofa daptingtovariationsinenvironmentalconitionsortoexternaldisturbances.I nthecaseofthefurnacecontrol,perhapsanexperiencedpersoncanprovidecontr olforacertaindesiredtemperatureinthehouse;butidthedoorsorwindowsareop enedorclosedintermittentlyduringtheoperatingperiod,thefinaltemperatureinsidethehousewillnotbeaccuratelyregulatedbytheopen-loopcontrol.Anelectricwashingmachineisanothertypicalexampleofanopen-loopsyst em,becausetheamountofwashtimeisentirelydeterminedbythejudgmentandesti mationofthehumanoperator.Atrueautomaticelectricwashingmachineshouldha vethemeansofcheckingthecleanlinessoftheclothescontinuouslyandturnitse dtoffwhenthedesireddegisedofcleanlinessisreached.Closed-LoopControlSystemsWhatismissingintheopen-loopcontrolsystemformoreaccurateandmoread aptablecontrolisalinkorfeedbackfromtheoutputtotheinputofthesystem.Ino rdertoobtainmoreaccuratebontrol,thecontrolledsignalc(t)mustbefedbacka ndcomparedwiththereferenceinput,andanactuatingsignalproportionaltothe differenceoftheoutputandtheinputmustbesentthroughthesystemtocorrectth eerror.Asystemwithoneormorefeedbackpat(slikethatjustdescribediscalled aclosed-loopsystem.humanbeingareprobablythemostcomplexandsophisticate dfeedbackcontrolsysteminexistence.Ahumanbeingmaybeconsideredtobeacont rolsystemwithmanyinputsandoutputs,capableofcarryingouthighlycomplexop erations.Toillustratethehumanbeingasafeedbackcontrolsystem,letusconsidert hattheobjectiveistoreachforanobjectonaperformthetask.Theeyesserveasas ensingdevicewhichfeedsbackcontinuouslythepositionofthehand.Thedistanc ebetweenthehandandtheobjectistheerror,whichiseventuallybroughttozeroa sthehandreachertheobject.Thisisatypicalexampleofclosed-loopcontrol.However,ifoneistoldtoreachfortheobjectandthenisblindolded,onecanonlyrea chtowardtheobjectbyestimatingitsexactposition.ItisAsantherillustrativ eexampleofaclosed-loopcontrolsystem,showstheblockdiagramoftherudderco ntrolsystemofThebasicalementsandtheblocadiagramofaclosed-loopcontrols ystemareshowninfig.Ingeneral,theconfigurationofafeedbackcontrolsystem maynotbeconstrainedtothatoffig&.Incomplexsystemstheremaybemultitudeof feedbackloopsandelementblocks.数控在先进制造技术领域最根本的观念之壹是数控(NC)。
数控基础英文作文

数控基础英文作文1. CNC machining is a revolutionary technology that has completely transformed the manufacturing industry. It allows for precise and efficient production of complex parts and components. The use of computer-controlled machines eliminates the need for manual labor and significantly reduces human error.2. The beauty of CNC machining lies in its versatility. It can be used to create a wide range of products, from simple objects like screws and bolts to intricate and delicate pieces of jewelry. The ability to program the machines to follow specific instructions ensures consistent and accurate results every time.3. One of the key advantages of CNC machining is its speed. Traditional manufacturing methods can be time-consuming and labor-intensive, but with CNC machines, production times are greatly reduced. This not only increases productivity but also allows for fasterturnaround times, meeting the demands of a fast-paced market.4. Another benefit of CNC machining is its cost-effectiveness. While the initial investment in CNC machines may be higher than traditional machines, the long-term savings are significant. The elimination of manual labor reduces labor costs, and the precision of the machines reduces material waste. This results in higher efficiency and lower production costs.5. CNC machining also offers unparalleled precision and accuracy. The machines can achieve tolerances as small as a few micrometers, ensuring that each part is identical and meets the required specifications. This level of precision is crucial in industries such as aerospace and medical, where even the slightest deviation can have serious consequences.6. In addition to its precision, CNC machining also allows for complex and intricate designs that would be impossible to achieve with traditional methods. The abilityto program the machines to create intricate patterns and shapes opens up a world of possibilities in terms of design and creativity.7. The use of CNC machining has also contributed to the reduction of waste and environmental impact. The precision of the machines minimizes material waste, and the use of computer simulations and virtual testing reduces the need for physical prototypes. This not only saves resources but also reduces the carbon footprint of the manufacturing process.8. The future of CNC machining looks promising, with advancements in technology leading to even more efficient and precise machines. The integration of artificial intelligence and machine learning will further enhance the capabilities of CNC machines, allowing for more complex and intelligent manufacturing processes.9. In conclusion, CNC machining has revolutionized the manufacturing industry with its precision, speed, versatility, and cost-effectiveness. It has opened up newpossibilities in design and creativity and has contributed to the reduction of waste and environmental impact. As technology continues to advance, the future of CNC machining looks bright, promising even greater efficiency and innovation.。
数控技术类外文文献翻译、中英文翻译、外文翻译

外文原文:NC Technology1、Research current situation of NC lathe in our timesResearch and development process to such various kinds of new technologies as numerical control lathe , machining center , FMS , CIMS ,etc. of countries all over the world, linked to with the international economic situation closely. The machine tool industry has international economy to mutually promote and develop, enter 21 alert eras of World Affairs, the function that people's knowledge plays is more outstanding, and the machine tool industry is regarded as the foundation of the manufacturing industry of the machine, its key position and strategic meaning are more obvious. Within 1991-1994 years, the economic recession of the world, expensive FMS, CIMS lowers the temperature, among 1995-2000 years, the international economy increases at a low speed, according to requisition for NC lathe and the world four major international lathes exhibition in order to boost productivity of users of various fields of present world market (EMO , IMTS , JIMTOF , China CIMT of Japan of U.S.A. of Europe), have the analysis of the exhibit, there are the following several points mainly in the technical research of NC lathe in our times:(1)、Pay more attention to new technology and innovationWorldwide , are launching the new craft , new material , new structure , new unit , research and development of the new component in a more cost-effective manner, developmental research of for instance new cutter material , the new electric main shaft of main shaft structure , high speed , high-speed straight line electrical machinery ,etc.. Regard innovating in improvement of the processing technology as the foundation, for process ultra and hard difficult to cut material and special composite and complicated part , irregular curved surface ,etc. research and develop new lathe variety constantly.(2)、Improve the precision and research of machine toolingIn order to improve the machining accuracy of the machining center, are improving rigidity of the lathe, reduction vibration constantly, dispel hotly and out of shape, reduce the noise , improve the precision of localization of NC lathe, repeat precision, working dependability , stability , precision keeping, world a lot of country carry on lathe hot error , lathe sport and load out of shape software of error compensate technical research, take precision compensate, software compensate measure improve , some may make this kind of error dispel 60% already. And is developing retrofit constantly, nanometer is being processed.(3)、Improve the research of the machine tooling productivityWorld NC lathe, machining center and corresponding some development of main shaft, electrical machinery of straight line, measuring system, NC system of high speed, under the prerequisite of boosting productivity.(4)、What a lot of countries have already begun to the numerical control system melt intelligently, openly, study networkedlyA、Intelligent research of the numerical control systemMainly showing in the following aspects: It is intelligent in order to pursue the efficiency of processing and process quality, the self-adaptation to the processing course is controlled, the craft parameter produces research automatically; Join the convenient one in order to improve the performance of urging and use intelligently, to the feedback control, adaptive operation , discerning automatically load selects models automatically, since carries on research whole definitely ,etc. of the electrical machinery parameter; There are such research of the respect as intelligent automatic programming , intelligent man-machine interface , intelligence diagnosing , intelligent monitoring ,etc..B、The numerical control system melts and studies openMainly showing in the following aspects: The development of the numerical control system is on unified operation platform, face the lathe producer and support finally, through changing, increasing or cutting out the structure target(numerical control target ), form the seriation, and can use users specially conveniently and the technical know-how is integrated in the control system, realize the open numerical control system of different variety, different grade fast, form leading brand products with distinct distinction. System structure norm of the open numerical control system at present, norm, disposing the norm, operation platform, numerical control systematic function storehouse and numerical control systematic function software developing instrument, etc. are the core of present research to pass through.C、Meeting the manufacture system of the production line , demand for the information integration of the manufacturing company networkedly greatly of numerical control equipment, it is a basic unit of realizing the new manufacture mode too.2、Classification of the machining center(1)Process according to main shaft space position when it classifies to be as follows, horizontal and vertical machining center.Horizontal machining center, refer to the machining center that the axis level of the main shaft is set up. Horizontal machining center for 3-5 sport coordinate axis, acommon one three rectilinear motion coordinate axis and one turn the coordinate axis of sports round (turn the working bench round), it can one is it is it finish other 4 Taxi processing besides installing surfaces and top surfaces to insert to install in work piece, most suitable for processing the case body work piece. Compared with strength type machining center it, the structure is complicated, the floor space is large, quality is large, the price is high.Vertical machining center, the axis of the main shaft of the vertical machining center, in order to set up vertically, its structure is mostly the regular post type, the working bench is suitable for processing parts for the slippery one of cross, have 3 rectilinear motion coordinate axis generally, can find a room for one horizontal numerical control revolving stage (the 4th axle) of axle process the spiral part at working bench. The vertical machining center is of simple structure, the floor space is small, the price is low, after allocating various kinds of enclosures, can carry on the processing of most work pieces.Large-scale gantry machining center, the main shafts are mostly set up vertically, is especially used in the large-scale or with complicated form work piece , is it spend the many coordinate gantry machining center to need like aviation , aerospace industry , some processing of part of large-scale steam turbine.Five machining centers, this kind of machining center has function of the vertical and horizontal machining center, one is it after inserting, can finish all five Taxi processing besides installing the surface to install in work piece, the processing way can make form of work piece error lowest, save 2 times install and insert working, thus improve production efficiency, reduce the process cost.(2)Classify by craft useIs it mill machining center to bore, is it mill for vertical door frame machining center, horizontal door frame mill the machining center and Longmen door frame mill the machining center to divide into. Processing technology its rely mainly on the fact that the door frame is milled, used in case body, shell and various kinds of complicated part special curve and large processes , curved surface of outline process, suitable for many varieties to produce in batches small.Complex machining center, point five times and compound and process mainly, the main shaft head can be turned round automatically, stand, lie and process, after the main shaft is turned round automatically, realize knowing that varies in the horizontal and vertical direction.(3)Classify by special functionSingle working bench, a pair of working bench machining center;Single axle, dual axle, three axle can change machining center, main shaft of case;Transfer vertically to the tower machining center and transfer;One hundred sheets of storehouses adds the main shaft and changes one one hundred sheets of machining centers;One hundred sheets of storehouses connects and writes hands to add the main shaft and change one hundred sheets of machining centers;One hundred sheets of storehouses adds the manipulator and adds one pair of main shafts to transfer to the tower machining center.3、Development trend of the current numerical control latheAt present, the advanced manufacturing technology in the world is rising constantly, such application of technology as ultrafast cutting , ultraprecision processing ,etc., the rapid development of the flexible manufacturing system and integrated system of the computer one is constant and ripe, have put forward higher demand to the process technology of numerical control. Nowadays the numerical control lathe is being developed in several following directions.(1). The speed and precision at a high speed , high accuracy are two important indexes of the numerical control lathe, it concerns directly that processes efficiency and product quality. At present, numerical control system adopt-figure number, frequency high processor, in order to raise basic operation speed of system. Meanwhile, adopt the super large-scale integrated circuit and many microprocessors structure, in order to improve systematic data processing ability, namely improve and insert the speed and precision of mending operation. Adopt the straight line motor and urge the straight line of the lathe working bench to be servo to enter to the way directly, it is quite superior that its responds the characteristic at a high speed and dynamically. Adopt feedforward control technology, make it lag behind error reduce greatly, thus improve the machining accuracy cut in corner not to track.For meet ultrafast demand that process, numerical control lathe adopt main shaft motor and lathe structure form that main shaft unite two into one, realize frequency conversion motor and lathe main shaft integrate , bearing , main shaft of electrical machinery adopt magnetism float the bearing , liquid sound pigeonhole such forms as the bearing or the ceramic rolling bearing ,etc.. At present, ceramic cutter and diamond coating cutter have already begun to get application.(2). Multi-functional to is it change all kinds of machining centers of organization (a of capacity of storehouse can up to 100 of the above ) automatically tofurnished with, can realize milling paring , boring and pares , bores such many kinds of processes as paring , turning , reaming , reaming , attacking whorl ,etc. to process at the same time on the same lathe , modern numerical control lathe adopt many main shaft , polyhedron cut also , carry on different cutting of way process to one different position of part at the same time. The numerical control system has because adopted many CPU structure and cuts off the control method in grades, can work out part processing and procedure at the same time on a lathe, realize so-called "the front desk processes, the backstage supporter is an editor ". In order to meet the needs of integrating the systematic one in flexible manufacturing system and computer, numerical control system have remote serial interface , can network , realize data communication , numerical control of lathe, can control many numerical control lathes directly too.(3). Intelligent modern numerical control lathe introduce the adaptive control technology, according to cutting the change of the condition, automatic working parameter, make the processing course can keep the best working state , thus get the higher machining accuracy and roughness of smaller surface , can improve the service life of the cutter and production efficiency of the equipment at the same time . Diagnose by oneself, repair the function by oneself, among the whole working state, the system is diagnosed, checked by oneself to CNC system and various kinds of equipment linking to each other with it at any time. While breaking down, adopt the measure of shutting down etc. immediately, carry on the fault alarm, brief on position, reason to break down, etc.. Can also make trouble module person who take off automatically, put through reserve module ,so as to ensure nobody demand of working environment. For realize high trouble diagnose that requires, its development trend adopts the artificial intelligence expert to diagnose the system.(4).Numerical control programming automation with the development of application technology of the computer, CAD/CAM figure interactive automatic programming has already get more application at present, it is a new trend of the technical development of numerical control. It utilize part that CAD draw process pattern , is it calculate the trailing punishing to go on by cutter orbit data of computer and then, thus produce NC part and process the procedure automatically, in order to realize the integration of CAD and CAM. With the development of CIMS technology , the full-automatic programming way in which CAD/CAPP/CAM integrates has appeared again at present, it, and CAD/CAM systematic programming great differencetheir programming necessary processing technology parameter needn't by artificial to participate in most, get from CAPP database in system directly.(5). The dependability of the dependability maximization numerical control lathe has been the major indicator that users cared about most all the time. The numerical control system will adopt the circuit chip of higher integrated level, will utilize the extensive or super large-scale special-purpose and composite integrated circuit, in order to reduce the quantity of the components and parts, to improve dependability. Through the function software of the hardware, in order to meet various kinds of demands for controlling the function, adopt the module, standardization, universalization and seriation of the structure lathe noumenon of the hardware at the same time, make not only improve the production lot of the hardware but also easy to is it produce to organize and quality check on. Still through operating and starting many kinds of diagnostic programs of diagnosing, diagnosing, diagnosing off-line online etc. automatically, realize that diagnoses and reports to the police the trouble to hardware, software and various kinds of outside equipment in the system. Utilize the warning suggestion, fix a breakdown in time; Utilize fault-tolerant technology, adopt and design the important part " redundantly ", in order to realize the trouble resumes by oneself; Utilize various kinds of test, control technology, excess of stroke, knife damages, interfering, cutting out, etc. at the time of various kinds of accidents as production, carry on corresponding protection automatically.(6). Control system miniaturization systematic miniaturization of numerical control benefit and combine the machine, electric device for an organic whole. Adopt the super large-scale integrated component , multi-layer printed circuit board mainly at present, adopt the three-dimensional installation method , make the electronic devices and components must use the high density to install, narrow systematic occupying the space on a larger scale. And utilize the new-type slim display of colored liquid crystal to substitute the traditional cathode ray tube, will make the operating system of numerical control miniaturize further. So can install it on the machine tool conveniently, benefit the operation of the numerical control lathe correctly even more.本文出自:Shigley J E. Mechanical Engineering Design. New York: McGraw-Hill, 1998译文:数控技术1、当前世界NC机床的研究现状世界各国对数控机床、加工中心以至FMS、CIMS等各种新技术的研究与发展进程,是与世界经济形势紧密相连的。
数控专业的介绍作文英文

数控专业的介绍作文英文英文:As a CNC major, I have learned a lot about the world of computer numerical control. CNC technology is a vital partof modern manufacturing, allowing for precise and efficient production of parts and products. In my studies, I have gained a deep understanding of the principles andtechniques involved in CNC machining, including programming, tool selection, and machine operation.One of the most important aspects of CNC machining is programming. This involves writing code that tells the machine how to move and operate. It requires a high levelof technical skill and attention to detail, as even a small mistake in the code can result in a faulty product. However, with practice and experience, programming becomes easierand more intuitive.Another key skill in CNC machining is tool selection.Different tools are used for different tasks, and it is important to choose the right tool for the job in order to achieve the desired result. This requires knowledge of the properties of different materials and the capabilities of different tools.Finally, machine operation is a crucial part of CNC machining. This involves setting up the machine, loading the program, and monitoring the process to ensure that everything is running smoothly. It requires a keen eye for detail and the ability to troubleshoot problems quickly and effectively.Overall, I have found studying CNC technology to be both challenging and rewarding. It has given me a deep appreciation for the precision and complexity of modern manufacturing, as well as the skills and knowledge necessary to succeed in this field.中文:作为一名数控专业的学生,我学到了很多关于计算机数控技术的知识。
机械设计制造及其自动化(数控技术)英语论文

Numerical control technology and equiping development trend andcountermeasureNumerical control technology is the technology controlled to mechanical movement and working course with digital information, integrated products of electromechanics that the numerical control equipment is the new technology represented by numerical control technology forms to the manufacture industry of the tradition and infiltration of the new developing manufacturing industry, namely the so-called digitization is equipped, its technological range covers a lot of fields: (1)Mechanical manufacturing technology; (2)Information processing , processing , transmission technology; (3)Automatic control technology; (4)Servo drive technology; (5)Technology of the sensor ; (6)Software engineering ,etc..1 Development trend of a numerical control technologyThe application of numerical control technology has not only brought the revolutionary change to manufacturing industry of the tradition, make the manufacturing industry become the industrialized symbol , and with the constant development of numerical control technology and enlargement of the application, the development of some important trades (IT , automobile , light industry , medical treatment ,etc. ) to the national economy and the peoples livelihood of his plays a more and more important role, because the digitization that these trades needed to equip has already been the main trend of modern development. Numerical control technology in the world at present and equiping the development trend to see, there is the following several respect [1- ] in its main research focus .1.1 A high-speed , high finish machining technology and new trend equippedThe efficiency , quality are subjavanufacturing technology. High-speed , high finish machining technology can raise the efficiency greatly , improve the quality and grade of the products, shorten production cycle and improve the market competitive power. Japan carries the technological research association first to classify it as one of the 5 great modern manufacturing technologies for this, learn (CIRP ) to confirm it as the centre in the 21st century and study one of the directions in international production engineering.In the field of car industry, produce one second when beat such as production of 300,000 / vehicle per year, and many variety process it is car that equip key problem that must be solved one of; In the fields of aviation and aerospace industry,spare parts of its processing are mostly the thin wall and thin muscle, rigidity is very bad, the material is aluminium or aluminium alloy, only in a situation that cut the speed and cut strength very small high, could process these muscles , walls . Adopt large-scale whole aluminium alloy method that blank " pay empty " make the wing recently, such large-scale parts as the fuselage ,etc. come to substitute a lot of parts to assemble through numerous rivet , screw and other connection way, make the intensity , rigidity and dependability of the component improved. All these, to processing and equiping the demand which has proposed high-speed , high precise and high flexibility. According to EMO2001 exhibition situation, high-speed machining center is it give speed can reach 80m/min is even high , air transport competent speed can up to 100m/min to be about to enter.A lot of automobile factories in the world at present, including Shanghai General Motors Corporation of our country, have already adopted and substituted and made the lathe up with the production line part that the high-speed machining center makes up . HyperMach lathe of U.S.A. CINCINNATI Company enters to nearly biggest 60m/min of speed, it is 100m/min to be fast, the acceleration reaches 2g, the rotational speed of the main shaft has already reached 60 000r/min. Processing a thin wall of plane parts, spend 30min only, and same part general at a high speed milling machine process and take 3h, the ordinary milling machine is being processed to need 8h; The speed and acceleration of main shaft of dual main shaft lathes of Germany DMG Company are up to 12* separately! 000r/mm and 1g. In machining accuracy, the past 10 years, ordinary progression accuse of machining accuracy of lathe bring 5¦Ìm up to from 10¦Ìm already, accurate grades of machining center from 3- 5¦Ìm, rise to 1- 1.5¦Ìm, and ultraprecision machining accuracy is it enter nanometer grade to begin already (0.01¦Ìm). In dependability, MTBF value of the foreign numerical control device has already reached above 6 000h, MTBF value of the servo system reaches above 30000h, demonstrate very high dependability . In order to realize high-speed , high finish machining, if the part of function related to it is electric main shaft , straight line electrical machinery get fast development, the application is expanded further.1.2 Link and process and compound to process the fast development of the lathe in 5 axesAdopt 5 axles to link the processing of the three-dimensional curved surface part, can cut with the best geometry form of the cutter , not only highly polished, but also efficiency improves by a large margin . It is generally acknowledged , the efficiency of an 5 axle gear beds can equal 2 3 axle gear beds , is it wait for to use the cubic nitrogen boron the milling cutter of ultra hard material is milled and pared at a high speed while quenching the hard steel part, 5 axles link and process 3 constant axles to link and process and give play to higher benefit. Because such reasons as complicated that 5 axles link the numerical control system , host computer structure that but go over, it is several times higher that its price links the numerical control lathe than 3 axles , in addition the technological degree of difficulty of programming is relatively great, have restricted the development of5 axle gear beds. At present because of electric appearance of main shaft, is it realize 5 axle complex main shaft hair structure processed to link greatly simplify to make, it makes degree of difficulty and reducing by a large margin of the cost, the price disparity of the numerical control system shrinks . So promoted 5 axle gear beds of head 无效 of complex main shaft and compound to process the development of the lathe (process the lathe including 5 ). At EMO2001 exhibition, new Japanese 5 of worker machine process lathe adopt complex main shaft hair, can realize the processing of 4 vertical planes and processing of the wanton angle , make 5 times process and 5 axles are processed and can be realized on the same lathe, can also realize the inclined plane and pour the processing of the hole of awls . Germany DMG Company exhibits the DMUVoution series machining center, but put and insert and put processing and 5 axles 5 times to link and process in once, can be controlled by CNC system or CAD/CAM is controlled directly or indirectly.1.3 Become the main trend of systematic development of contemporary numerical control intelligently , openly , networkedlilyThe numerical control equipment in the 21st century will be sure the intelligent system, the intelligent content includes all respects in the numerical control system: It is intelligent in order to pursue the efficiency of processing and process quality, control such as the self-adaptation of the processing course, the craft parameter is produced automatically; Join the convenient one in order to improve the performance of urging and use intelligently, if feedforward control , adaptive operation , electrical machinery of parameter , discern load select models , since exactly makes etc. automatically automatically; The ones that simplified programming , simplified operating aspect are intelligent, for instance intelligent automatic programming , intelligent man-machine interface ,etc.; There are content of intelligence diagnose , intelligent monitoring , diagnosis convenient to be systematic and maintaining ,etc..Produce the existing problem for the industrialization of solving the traditional numerical control system sealing and numerical control application software. A lot of countries carry on research to the open numerical control system at present, such as NGC of U.S.A. (The Next Generation Work-Station/Machine Control), OSACA of European Community (Open System Architecture for Control within Automation Systems), OSEC (Open System Environment for Controller ) of Japan, ONC (Open Numerical Control System ) of China ,etc.. The numerical control system melts to become the future way of the numerical control system open.The so-called open numerical control system is the development of the numerical control system can be on unified operation platform, face the lathe producer and end user, through changing, increasing or cutting out the structure target(numerical control function), form the seriation, and can use users specially conveniently and the technical know-how is integrated in the control system, realize the open numerical control system of different variety , different grade fast, form leading brand products with distinct distinction.System structure norm of the open numerical control system at present, communication norm , disposing norm , operation platform , numerical control systematic function storehouse and numerical control systematic function software developing implement ,etc. are the core of present research. The networked numerical control equipment is a new light spot of the fair of the internationally famous lathe in the past two years. Meeting production line , manufacture system , demand for the information integration of manufacturing company networkedly greatly of numerical control equipment, realize new manufacture mode such as quick make , fictitious enterprise , basic Entrance that the whole world make too.Some domestic and international famous numerical control lathes and systematic manufacturing companies of numerical control have all introduced relevant new concepts and prototypes of a machine in the past two years, if in EMO2001 exhibition, " CyberProduction Center " that the company exhibits of mountain rugged campstool gram in Japan (Mazak ) (intellectual central production control unit, abbreviated as CPC); The lathe company of Japanese big Wei (Okuma ) exhibits " IT plaza " (the information technology square , is abbreviated as IT square ); Open Manufacturing Environment that the company exhibits of German Siemens (Siemens ) (open the manufacturing environment, abbreviated as OME),etc., have reflected numerical control machine tooling to the development trend of networked direction.1.4 Pay attention to the new technical standard , normal setting-up1.4.1 Design the norm of developing about the numerical control systemAs noted previously, there are better commonability , flexibility , adaptability , expanding in the open numerical control system, such countries as U.S.A. , European Community and Japan ,etc. implement the strategic development plan one after another , carry on the research and formulation of the systematic norm (OMAC , OSACA , OSEC ) of numerical control of the open system structure, 3 biggest economies in the world have carried on the formulation that nearly the same science planned and standardized in a short time, have indicated a new arrival of period of change of numerical control technology. Our country started the research and formulation of standardizing the frame of ONC numerical control system of China too in 2000.1.4.2 About the numerical control standardThe numerical control standard is a kind of trend of information-based development of manufacturing industry. Information exchange among 50 years after numerical control technology was born was all because of ISO6983 standard, namely adopt G, M code describes how processes, its essential characteristic faces the processing course, obviously, he cant meet high-speed development of modern numerical control technologys needs more and more already. For this reason, studying and making a kind of new CNC system standard ISO14649 (STEP-NC) in the world, its purpose is to offer a kind of neutral mechanism not depending on the concrete system , can describe the unified data model in cycle of whole life of the products , thusrealize the whole manufacture process, standardization of and even each industrial field product information.The appearance of STEP-NC may be a revolution of the technological field of the numerical control, on the development and even the whole manufacturing industry of numerical control technology , will exert a far-reaching influence. First of all, STEP-NC puts forward a kind of brand-new manufacture idea , in the traditional manufacture idea, NC processes the procedures to all concentrate on individual computer. Under the new standard, NC procedure can be dispersed on Internet, this is exactly a direction of open , networked development of numerical control technology. Secondly, STEP-NC numerical control system can also reduce and process the drawing (about 75% ) , process the procedure to work out the time (about 35% ) and process the time (about 50% ) greatly . At present, American-European countries pay much attention to the research of STEP-NC, Europe initiates IMS plan (1999.1.1- 2001.12.3 ) of STEP-NC. 20 CAD/CAM/CAPP/CNC users , manufacturers and academic organizations from Europe and Japan participated in this plan. STEP Tools Company of U.S.A. is a developer of the data interchange software of manufacturing industry in the global range, he has already developed the super model (Super Model ) which accuses of information exchange of machine tooling by counting, its goal is to describe all processing courses with the unified norm. Such new data interchange form has already been verified in allocating the SIEMENS , FIDIA and European OSACA-NC numerical control at present.2 pairs of basic estimations of technology and industry development of numerical control of our countryThe technology of numerical control of our country started in 1958, the development course in the past 50 years can roughly be divided into 3 stages:The first stage is from 1958 to 1979, namely closed developing stage. In this stages, because technology of foreign countries blockade and basic restriction of terms of our country, the development of numerical control technology is comparatively slow.The second stage is during " Sixth Five-Year Plan Period " , " the Seventh Five-Year Plan Period " of the country in second stage and earlier stage in " the Eighth Five-Year Plan Period ", namely introduce technology, digest and assimilate, the stage of establishing the system of production domesticization arisesing tentatively. At this stage , because of reform and opening-up and national attention , and study the improvement of the development environment and international environment, research , development and all making considerable progress in production domesticization of the products of the technology of numerical control of our country.The third stage is during the " Ninth Five-Year Plan Period " on the later stage in " the Eighth Five-Year Plan Period " of the country, namely implement the research of industrialization, enter market competition stage. At this stage , madesubstantive progress in industrialization of the domestic numerical control equipment of our country. In latter stage for " the Ninth Five-Year Plan ", the domestic occupation rate of market of the domestic numerical control lathe is up to 50%, it is up to 10% too to mix the domestic numerical control system (popular ).Make a general survey of the development course in the past 50 years of technology of numerical control of our country, especially through tackling key problems of 4 Five-Year Plans, all in all has made following achievements.a.Have establish the foundation of the technical development of numerical control, has mastered modern numerical control technology basically. Our country has already, the numerical control host computer , basic technology of special plane and fittings grasped and driven from the numerical control system and servoly basically now, among them most technology have already possessed and commercialized the foundation developed , some technology has already, industrialization commercialized.b.Have formed the industrial base of numerical control tentatively. In tackling key problems the foundation that the achievement and some technology commercialize , set up the systematic factories of numerical control with production capacity in batches such as numerical control in Central China , numerical control of the spaceflight etc.. Electrical machinery plant of Lanzhou, such factory and the first machine tool plant of Beijing , the first machine tool plant of Jinan ,etc. several numerical control host computer factories of a batch of servo systems and servo electrical machineries as the numerical control in Central China,etc.. These factories have formed the numerical control industrial base of our country basically.c.Have set up a numerical control research, development , managerial talents basic team . Though has made considerable progress in research and development and industrialization of numerical control technology, but we will realize soberly, the research and development of the technology of advanced numerical control of our country, especially there is greater disparity in current situation and current demand of our country of engineering level in industrialization. Though very fast from watching the development of our country vertically, have disparity horizontally more than (compare foreign countries with ) not merely engineering level, there is disparity too in development speed in some aspects, namely the engineering level disparity between some high-grade , precision and advanced numerical control equipment has the tendency to expand .Watch from world , estimate roughly as follows about the engineering level of numerical control of our country and industrialization level.a.On the engineering level, in probably backward 10- 1 years with the advanced level in foreign countries, it is bigger in high-quality precision and sophisticated technology.b.On the industrialization level, the occupation rate of market is low, the variety coverage rate is little, have not formed the large-scale production yet; The specialized level of production of function part and ability of forming a complete set are relatively low; Appearance quality is relatively poor; Dependability is not high, the commercialized degree is insufficient; Ones own brand effect that the domestic numerical control system has not been set up yet, users have insufficient confidence.c.On the ability of sustainable development, research and development of numerical control technology , project ability are relatively weak to the competition; It is not strong that the technological application of numerical control expands dynamics;Research , formulation that relevant standards are normal lag behind. It is analysed that the main reason for having above-mentioned disparity has the following several respect.a.Realize the respect. Know to industrys process arduousness , complexity and long-term characteristic of domestic numerical control insufficiently; It is difficult to underestimate to add strangling , system ,etc. to the unstandard , foreign blockade of the market; It is not enough to analyse to the technological application level and ability of numerical control of our country.b.System. Pay close attention to numerical control industrialization many in the issue , consider numerical control industrialization little in the issue synthetically in terms of the systematic one , industry chain in terms of technology; Have not set up related system , perfect training , service network of intact high quality ,etc. and supported the system.c.Mechanism. It causes the brain drain, restraining technology and technological route from innovating again , products innovation that the bad machine is made, and has restricted the effective implementation of planning , has often planned the ideal , implement the difficulty.d.Technology. The autonomous innovation in technology of enterprises is indifferent, the project of key technology is indifferent. The standard of the lathe lags behind, the level is relatively low, it is not enough for new standard of the numerical control system to study.3 pairs of strategic thinking of technology and industrialized development of numerical control of our country 3.1 Strategic considerationOur country make big country, industry is it is it accept front instead of transformation of back end to try ones best to want in shifting in world, namely should master and make key technology advancedly, otherwise in a new round ofinternational industrial structure adjustment, the manufacturing industry of our country will step forward and " leave the core spaces ". We regard resource , environment , market as the cost, it is only an international " machining center " in the new economic pattern of the world to exchange the possibility got and " assemble the centre ", but not master the position of the manufacturing center of key technology , will so influence the development process of the modern manufacturing industry of our country seriously. We should stand in the height of national security strategy paying attention to numerical control technology and industrys question , at first seen from social safety, because manufacturing industry whether our country obtain employment most populous trade, the development of manufacturing industry not only can improve the peoples living standard but also can alleviate the pressure of employment of our country , ensure the stability of the society; Secondly seen from national defence security, the western developed country has classified all the high-grade , precision and advanced numerical control products as the strategic materials of the country, realizing the embargo and restriction to our country, " Toshiba incident " and " Cox Report " is the best illustration.3.2 Development tacticsProceed from the angles of the fundamental realities of the country of our country, regard the strategic demand of the country and market demand of national economy as the direction, regard improving our country and making the comprehensive competitive power of equiping industry and industrialization level as the goal, use the systematic method , be able to choose to make key technology upgraded in development of equiping industry and support technology supporting the development of industrialization in our country in initial stage of 21st century in leading factor, the ability to supply the necessary technology realizes making the jumping development of the equiping industry as the content of research and development.Emphasize market demand is a direction, namely take terminal products of numerical control as the core, with the complete machine (Such as the numerical control lathe having a large capacity and a wide range, milling machine , high speed high precise high-performance numerical control lathe , digitized machinery of model , key industry key equipment ,etc.) drive the development of the numerical control industry. Solve the numerical control system and relevant functions part especially The dependability that (digitized servo system and electrical machinery , high speed electric main shaft system and new-style enclosure that equip ,etc. ) and production scale question. There are no products that scale will not have high dependability ; Will not have cheap and products rich in the competitiveness without scale ; Certainly, it is difficult to have day holding up ones head finally that there is no scale Chinese numerical control equipment.In equiping researching and developing high-grade , precision and advancedly , should emphasize the production, learning and research and close combination of the end user, regard " drawing, using, selling " as the goal, tackle key problemsaccording to the national will, in order to solve the needing badly of the country. Numerical control technology, emphasized innovation, put emphasis on researching and developing the technology and products with independent intellectual property right before the competition, establish the foundation for the industry of numerical control of our country , sustainable development of equipment manufacture and even the whole manufacturing industry.List of references:[1]China machine tool industrial association Development department of the trade. CIMT2001 tour [J ]. The manufacturing technology in the world and equiping the market, 2001 (3): 18-20.[2]The roof beam trains a king to declare , the distribution is helped. New tendency [J ] of the technical development of the lathe . The manufacturing technology in the world and equiping the market, 2001 (3): 21-28.[3]China machine tool industrial association Systematic branch of numerical control. CIMT2001 tour [J ]. The manufacturing technology in the world and equiping the market, 2001 (5): 13-17.[4]Yang XueTong, Li DongRu, He WenLi ,etc.? Numerical control lathe technical development strategic research [M ] from now to century. Beijing: State Bureau of Machinery Industries, 2000.。
机械类数控外文翻译外文文献英文文献数控
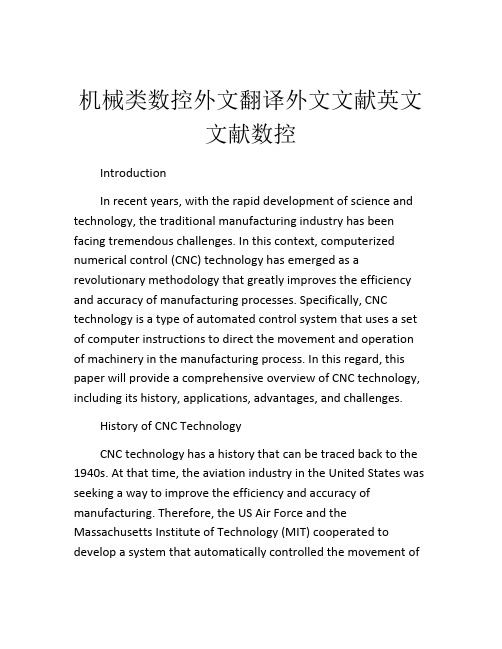
机械类数控外文翻译外文文献英文文献数控IntroductionIn recent years, with the rapid development of science and technology, the traditional manufacturing industry has been facing tremendous challenges. In this context, computerized numerical control (CNC) technology has emerged as a revolutionary methodology that greatly improves the efficiency and accuracy of manufacturing processes. Specifically, CNC technology is a type of automated control system that uses a set of computer instructions to direct the movement and operation of machinery in the manufacturing process. In this regard, this paper will provide a comprehensive overview of CNC technology, including its history, applications, advantages, and challenges.History of CNC TechnologyCNC technology has a history that can be traced back to the 1940s. At that time, the aviation industry in the United States was seeking a way to improve the efficiency and accuracy of manufacturing. Therefore, the US Air Force and the Massachusetts Institute of Technology (MIT) cooperated to develop a system that automatically controlled the movement ofaircraft components during the manufacturing process. This system was called the numerical control (NC) system.In the mid-1950s, John Parsons, a researcher at the Massachusetts Institute of Technology, invented the first NC machine tool. The machine used punched tape to control the movement of the cutting tool. During the 1960s, digital computer technology became more advanced, which paved the way for the development of CNC machines. By 1970, CNC machines had become a mature and widely used technology in the manufacturing industry.Applications of CNC TechnologyCNC technology has a wide range of applications in the manufacturing industry. For example, CNC machines can be used to produce a variety of products, including automobile parts, aircraft components, medical equipment, and consumer goods. CNC technology is also used in many other industries, such as woodworking, metalworking, plastics, and textiles.CNC technology has revolutionized the manufacturing industry by improving the quality, precision, and consistency of products. In addition, CNC machines can work faster and often require less manual labor than traditional manufacturing methods. CNC technology also allows manufacturers to produce complex shapes and designs that would be difficult or impossible to produce using traditional manufacturing methods.Advantages of CNC TechnologyThere are several advantages of using CNC technology in manufacturing. First, CNC machines can produce parts with very high precision and accuracy, which is crucial in industries such as aerospace and medical equipment manufacturing. CNC machines can also work 24/7, which means that manufacturers can produce parts at any time of day or night without having to worry about workers becoming tired.Second, CNC machines are highly flexible and can be programmed to produce a wide range of products. This means that manufacturers can quickly switch between different products without having to buy new machines or invest in expensive retooling. This flexibility also allows manufacturers to respond quickly to changes in market demand.Third, CNC machines can greatly reduce the amount of waste generated during the manufacturing process. This is because CNC machines can accurately measure and cut materials, minimizing the amount of scrap that is created. In addition, CNC machines can be programmed to optimize the use of materials, further reducing waste.Challenges of CNC TechnologyDespite its many advantages, CNC technology also presents several challenges. First, CNC machines can be expensive to purchase and maintain, which can be a barrier for smallmanufacturers. In addition, CNC machines require skilled operators who can program and operate the machines. This means that manufacturers must invest in training their workers, which can also be costly.Second, CNC machines can sometimes be less efficient than traditional manufacturing methods for small production runs. This is because CNC machines require a certain amount of time to set up and program, which can be inefficient for small production runs. In addition, CNC machines require a certain amount of precision, which means that they may not be suitable for certain types of products, such as handmade crafts.Finally, CNC machines also present some ethical challenges. For example, some argue that CNC machines could lead to job loss in the manufacturing industry, as the machines can perform tasks that were previously done by workers. In addition, CNC machines could lead to a reduction in the quality of products, as manufacturers may be more focused on speed and efficiency rather than quality.ConclusionCNC technology has revolutionized the manufacturing industry by improving the quality, precision, and consistency of products. CNC machines are highly flexible and can be programmed to produce a wide range of products. In addition, CNC machines can greatly reduce the amount of waste generated during the manufacturing process. However, CNC technology alsopresents several challenges, including high cost, the need for skilled operators, efficiency issues for small production runs, and ethical concerns. Overall, CNC technology is a powerful tool for manufacturers, but it is important for manufacturers to carefully consider the costs and benefits of using this technology.。
数控技术 外文翻译 外文文献 英文文献

外文翻译NUMERICAL CONTROLNumerical control(N/C)is a form of programmable automation in which the processing equipment is controlled by means of numbers,letters,and other symbols.The numbers,letters,and symbols are coded in an appropriate format to define a program of instructions for a particular work part or job.When the job changes,the program of instructions is changed.The capability to change the program is what makes N/C suitable for low-and medium-volume production.It is much easier to write programs th an to make major alterations of the processing equipment.There are two basic types of numerically controlled machine tools:point—to—point and continuous—path(also called contouring).Point—to—point machines use unsynchronized motors,with the result that the position of the machining head Can be assured only upon completion of a movement,or while only one motor is running.Machines of this type are principally used for straight—line cuts or for drilling or boring.The N/C system consists of the following comp onents:data input,the tape reader with the control unit,feedback devices,and the metal—cutting machine tool or other type of N/C equipment.Data input,also called “man—to—control link”,may be provided to the machine tool manually,or entirely by automatic means.Manual methods when used as the sole source of input data are restricted to a relatively small number of inputs.Examples of manually operated devices are keyboard dials,pushbuttons,switches,or thumbwheel selectors.These are located on a console near t he machine.Dials ale analog devices usually connected to a syn-chro-type resolver or potentiometer.In most cases,pushbuttons,switches,and other similar types of selectors aye digital input devices.Manual input requires that the operator set the controls fo r each operation.It is a slow and tediousprocess and is seldom justified except in elementary machining applications or in special cases.In practically all cases,information is automatically supplied to the control unit and the machine tool by cards,punched tapes,or by magnetic tape.Eight—channel punched paper tape is the most commonly used form of data input for conventional N/C systems.The coded instructions on the tape consist of sections of punched holes called blocks.Each block represents a machine function,a machining operation,or a combination of the two.The entire N/C program on a tape is made up of an accumulation of these successive data blocks.Programs resulting in long tapes all wound on reels like motion-picture film.Programs on relatively short tapes may be continuously repeated by joining the two ends of the tape to form a loop.Once installed,the tape is used again and again without further handling.In this case,the operator simply loads and unloads the parts.Punched tapes ale prepared on typ e writers with special tape—punching attachments or in tape punching units connected directly to a computer system.Tape production is rarelyerror-free.Errors may be initially caused by the part programmer,in card punching or compilation,or as a result of physical damage to the tape during handling,etc.Several trial runs are often necessary to remove all errors and produce an acceptable working tape.While the data on the tape is fed automatically,the actual programming steps ale done manually.Before the coded tape may be prepared,the programmer,often working with a planner or a process engineer, must select the appropriate N/C machine tool,determine the kind of material to be machined,calculate the speeds and feeds,and decide upon the type of tooling needed. The dimensions on the part print are closely examined to determine a suitable zero reference point from which to start the program.A program manuscript is then written which gives coded numerical instructions describing the sequence ofoperations that the machine tool is required to follow to cut the part to the drawing specifications.The control unit receives and stores all coded data until a complete block of information has been accumulated.It then interprets the coded instruction and directs the machine tool through the required motions.The function of the control unit may be better understood by comparing it to the action of a dial telephone,where,as each digit is dialed,it is stored.When the entire number has been dialed,the equipment becomes activated and the call is completed.Silicon photo diodes,located in the tape reader head on the control unit,detect light as it passes through the holes in the moving tape.The light beams are converted to electrical energy,which is amplified to further strengthen the signal.The signals are then sent to registers in the control unit, where actuation signals are relayed to the machine tool drives.Some photoelectric devices are capable of reading at rates up to 1000 characters per second.High reading rates are necessary to maintain continuous machine—tool motion;otherwise dwell marks may be generated by the cutter on the part during contouring operations.The reading device must be capable of reading data blocks at a rate faster than the control system can process the data.A feedback device is a safeguard used on some N/C installations to constantly compensate for errors between the commanded position and the actual location of the moving slides of the machine tool.An N /C machine equipped with this kind of a direct feedback checking device has what is known as a closed-loop system.Positioning control is accomplished by a sensor which,during the actual operation,records the position of the slides and relays this information back to the control unit.Signals thus received ale compared to input signals on the tape,and any discrepancy between them is automatically rectified.In an alternative system,called an open—loop system,the machine is positioned solely by stepping motor drives in response to commands by a controllers.There are three basic types of NC motions, as follows: Point-to-point or Positional Control In point-to-point control the machine tool elements (tools, table, etc.) are moved to programmed locations and the machining operations performed after the motion s are completed. The path or speed of movement between locations is unimportant; only the coordinates of the end points of the motions are accurately controlled. This type of control is suitable for drill presses and some boring machines, where drilling, t apping, or boring operations must be performed at various locations on the work piece. Straight-Line or Linear Control Straight-Line control systems are able to move the cutting tool parallel to one of the major axes of the machine tool at a controlled rate suitable for machining. It is normally only possible to move in one direction at a time, so angular cuts on the work piece are not possible, consequently, for milling machines, only rectangular configurations can be machined or for lathes only surfaces parall el or perpendicular to the spindle axis can be machined. This type of controlled motion is often referred to as linear control or a half-axis of control. Machines with this form of control are also capable ofpoint-to-point control.Continuous Path or Contouring Control In continuous path control the motions of two or more of the machine axes are controlled simultaneously, so that the position and velocity of the can be tool are changed continuously. In this way curves and surfaces can be machined at a controlled feed rate. It is the function of the interpolator in the controller to determine the increments of the individual controlled axes of the machines necessary to produce the desired motion. This type of control is referred to as continuous control or a full axis of control.Some terminology concerning controlled motions for NC machines has been introduced. For example, some machines are referred to asfour-or five-or even six-axis machines. For a vertical milling machine three axes of control are fairly obvious, these being the usual X, Y, Z coordinate directions. A fourth or fifth axis of control would imply some form of rotary table to index the work piece or possibly to provide angular motion of the work head. Thus, in NC terminology an axis of control is any controlled motion of the machine elements (spindles, tables, etc). A further complication is use of the term half-axis of control; for example, many milling machines are referred to as 2.5-axis machine. This means that continuous control is possib le for two motions (axes) and only linear control is possible for the third axis. Applied to vertical milling machines, 2.5axis control means contouring in the X, Y plane and linear motion only in the Z direction. With these machines three-dimensional objects have to be machined with water lines around the surface at different heights. With an alternative terminology the same machine could be called a 2CL machine (C for continuous, L for linear control). Thus, a milling machine with continuous control in th e X, Y, Z directions could be termed be a three-axis machine or a 3c machine, Similarly, lathes are usually two axis or 2C machines. The degree of work precision depends almost entirely upon the accuracy of the lead screw and the rigidity of the machine st ructure.With this system.there is no self-correcting action or feedback of information to the control unit.In the event of an unexpected malfunction,the control unit continues to put out pulses of electrical current.If,for example,the table on a N/C milling machine were suddenly to become overloaded,no response would be sent back to the controller.Because stepping motors are not sensitive to load variations,many N/C systems are designed to permit the motors to stall when the resisting torque exceeds the motor torque.Other systems are in use,however,which in spite of the possibility of damage to the machine structure or to the mechanical system,ale designed with special high—torque steppingmotors.In this case,the motors have sufficient capacity to “overpower” the system in the event of almost any contingency.The original N/C used the closed—loop system.Of the two systems,closed and open loop,closed loop is more accurate and,as a consequence,is generally more expensive.Initially,open—loop systems were used almost entirely for light-duty applications because of inherent power limitations previously associated with conventional electric stepping motors.Recent advances in the development of electro hydraulic stepping motors have led to increasingly heavier machin e load applications.数控技术数控是可编程自动化技术的一种形式,通过数字、字母和其他符号来控制加工设备。
数控技术 外文翻译 外文文献 英文文献 数控技术的发展与维修

Development and maintenance of CNC technology Numerical control technology and equipment is the development of new high-tech industry and cutting-edge enabling technology, industry and the most basic equipment. The world information industry, biological industry, aviation, aerospace and other defense industry widely used numerical techniques to improve manufacturing capacity and level, to improve the adaptability of the market and competitiveness. Industrial countries and CNC numerical control technology and equipment will also be listed as countries of strategic materials, not only to develop their own numerical control technology and industry, and in "sophisticated" technology and equipment, numerical control key aspects of the policy of closures and restrictions. Therefore, efforts to develop advanced numerical control technology as the core manufacturing technology has become the world's developed countries to accelerate economic development, enhance the comprehensive national strength and an important way to statehood.Part I: the development of CNC machine tools trends in individual1. High speed, high accuracy, high reliabilityHigh speed: To improve the speed and increase feed spindle speed.High precision: the precision from micron to sub-micron level, and even the nano-level (high reliability: the reliability of numerical control system generally higher than the reliability of numerical control equipment more than an order of magnitude, but not the higher the better reliability because the goods by the cost performance constraints.2. CompositeComposite function CNC machine tool development, its core is in a single machine to complete the turning, milling, drilling, tapping, reaming and reaming and other operating procedures, thereby increasing the efficiency and precision machine tools to improve production flexibility.3. IntelligentIntelligent content included in all aspects of the numerical control system: the pursuit of processing efficiency and processing quality of intelligence; to improve the performance and the use of convenient connections and other aspects of intelligence; simplify programming, simplifying operational intelligence; also like the intelligent automatic programming, intelligent man-machine interface, as well as intelligent diagnostics, intelligent monitoring and other aspects, to facilitate system diagnostics and maintenance.4. Flexible, integratedThe world of CNC machine tools to the development trend of flexible automation systems are: from the point (CNC single, composite machining centers and CNC machine tools), line (FMC, FMS, FTL, FML) to the surface (Section workshop independent manufacturing island FA) , body (CIMS, distributed network integrated manufacturing system) direction, the other to focus on applied and economic direction. Flexible automation technology is the industry to adapt to dynamic market demands and quickly update the primary means of product is the main trend of national manufacturing industry is the basis for the field of advanced manufacturing technology.Second, personalization is the adaptability of the market trendsToday's market, gradually formed the pattern of international cooperation, the products becoming more competitive, efficient and accurate processing of the escalating demand means, the user's individual requirements become increasingly strong, professional, specialization, more and more high-tech machine tools by the users of all ages.Third, the open architecture trend isThe core of a new generation of CNC system development is open. Open software platform and hardware platforms are open systems, modular, hierarchical structure, and through out the form to provide a unified application interface.CNC system to address the closure of the traditional CNC applications and industrial production problems. At present, many countries of open CNC system, CNC system has become an open numerical control system of the future of the road. The open numerical control system architecture specification, communication specifications, configuration specifications, operating platform, function libraries and CNC numerical control system software development tools, system function is the core of the current study. Network numerical control equipment is nearly two years of a new focus. NC network equipment will greatly satisfy the production lines, manufacturing systems, manufacturing information integration needs of enterprises, but also achieve new manufacturing model, such as agile manufacturing, virtual enterprises, global manufacturing the base unit. Some well-known at home and abroad, and CNC CNC machine tools manufacturing company inPart II: Machine MaintenanceCNC machine tools is electronic technology, measurement technology, automation technology, semiconductor technology, computer technology and electrical technology, and integrated set of automation equipment, high precision, high efficiency and high flexibility. CNC machine tools is a process control equipment and asked him in real-time control of the accuracy of every moment of work, any part of the fault and failure, so that the machine will shut down, resulting in production stoppages, which seriously affected and restricted the production efficiency . CNC machine tools in many industries to work the device is critical, if not after a failure in its maintenance and troubleshooting time, it will cause greater economic losses. Therefore, the principle that complex numerical control system, structure, maintenance of sophisticated equipment is necessary. CNC machine tools to enhance fault diagnosis and maintenance of power, can improve the reliability of CNC machine tools, CNC machine tools is conducive to the promotion and use.CNC machine tools is a mechanical, electrical, hydraulic, gas combination of complex equipment, though the reasons for failure vary, but the failure occurred, the general idea of the steps are the same. Fails,Spindle start below to stop immediately after the fault diagnosis of CNC machine tools as an example the general process.First, the fault-site investigation. The survey content includes 1, 2 types of failure, the failure frequency of 3, 4, external conditions, the operating conditions 5, 6, machine conditions, the functioning of 7, wiring between machine tools and systems 8, CNC equipment visual inspection. After an investigation, such failure is spindle class failure, only once, outside of all normal, the operator of a boot to reflect this situation.Second, the fault information collation, analysis. For some simple fault, because not alot of time, the method can be used form of logical reasoning, analysis, identification and troubleshooting. After a failed on-site investigation for several reasons we suspect that the system output pulse ①②drive is not enough time to move the state line to control the spindle components ③④damage to the spindle motor short-circuit, causing the spindle thermal relay protection ⑤ not with self-control loop lock circuits, and the parameter is set to pulse signal output, so that the spindle can not operate normally. Identify possible reasons to rule out one by one.Third, conduct fault diagnosis and troubleshooting.Diagnosis usually follows the following principles: 1, after the first outside inside. Reliable line of modern CNC system increasingly high failure rate of CNC system itself less and less, and most are non-occurrence of failure causes the system itself. The CNC machine is a mechanical, hydraulic, electrical as one of the tools, the occurrence of the fault will be reflected by these three comprehensive, maintenance personnel should be from outside to inside one by one investigation to avoid arbitrary unsealed, demolition, otherwise expand the malfunction, so that the loss of precision machine tools, slow performance, outside the system detected the fault is due to open one by one, hydraulic components, pneumatic components, electrical actuators, mechanical devices caused problems. 2, the first after the electrical machinery. In general, the mechanical failure easier to find, and numerical control system and electrical fault diagnosis more difficult, before the troubleshooting to rule out mechanical failure of the first 3, after the first static dynamic. Power off the machine first, quiescent state, through understanding, observation, testing, analysis, confirm the power failure will not result in expansion of the incident only after the power to the machine, run the state, the dynamic of observation, inspection and testing, to find fault. While after the devastating power failure, you must first rule out the danger, before electricity. 4, after the first simple and complex. When multiple failures are intertwined, and sometimes impossible to start with, we should first solve the problem easily, then solve the difficult problem, often a simple problem to solve, the difficulty of the problem may also become easier.CNC machine tools in the fault detection process, should make full use of numerical control system self-diagnostic features to be judged, but also flexibility in the use of some common troubleshooting methods. Troubleshooting common methods are:1. Routine examination methodRoutine examination method is mainly of hands, eyes, ears, nose and other organs of the fault occurrence of various light, sound, smell and abnormal observations and careful look at every system, follow the "first post outside of" the principle of fault diagnosis by looking, listening, smelling, asking, mold and so on, from outside to inside one by one check, the fault can often be narrowed down to a module or a printed circuit board. This requires maintenance personnel have a wealth of practical experience, to the wider multidisciplinary and comprehensive knowledge of the ability to judge.2. Self-diagnostic function methodModern CNC system has yet to achieve a high degree of intelligence. But already has a strong self-diagnostic function. CNC ready to monitor the hardware and software is working. Once the abnormal, immediately displayed on the CRT alarm or fault LEDs indicate the approximate cause. Using self-diagnosis function, but also shows the interface signals between the system and the host state, in order to determine the fault occurred in themechanical part or parts of NC system, and indicate the approximate fault location. This method is currently the most effective maintenance methods.3. Functional program testing methodSo-called functional program testing method is commonly used in the numerical control system functions and special features, such as linear positioning, circular interpolation, helical cut, fixed cycle, such as the user macro programming by hand or automatic programming methods, the preparation of test procedures into a functional program , into the numerical control system, and then start the CNC system to make it run, to check the im time the first boot of CNC whether a programming error or operational error or machine4. Spare parts substitutionSpare parts replacement method is a simple method to determine the scene is one of the most commonly used. The so-called spare substitution is generally the cause of failure in the analysis of the case, maintenance personnel can use the alternate PCB, templates, integrated circuit chip or replace the questionable parts of components, which narrowed the fault to a printed circuit board or chip level. It is actually in the verification analysis is correct. However, before switching the standby board should carefully check the spare board is intact, and should check the status of reserve board should be fully consistent with the original board the state. This includes checking with the board selection switch, set the location and the short rod potentiometer position. In short, we must strictly in accordance with the system's operation, maintenance requirements manual operation.In determining the replacement of a part to, should carefully check the relevant connected to electrical lines and other related, confirming that no failure up to the new replacement to prevent failures caused by external damage to replace the parts up.5. Transfer ActThe so-called transfer method is to have the same numerical control system features two printed circuit boards, templates, integrated circuit chips or components to exchange, observed failure phenomena be transferred. In this way, the system can quickly determine the fault position. This method is actually a kind of spare parts substitution. Therefore, the considerations described in the same spare parts substitution.6. Parameter check methodKnown parameters can directly affect the numerical performance of CNC machine tools. Parameters are usually stored in the magnetic bubble memory, or stored in batteries to be maintained by the CMOS RAM, once the battery is low or because of outside interference and other factors, some parameters will be lost or change in chaos, so that the machine does not work. At this point, through the proofreading, correction parameters, will be able to troubleshoot. When the machine idle for a long time to work again for no reason that there is no normal or failure without warning, it should be based on fault characteristics, inspection and proof-reading the relevant parameters.After a long run of CNC machine tools, wear and tear due to its mechanical drive components, electrical component performance changes and other reasons, also need to adjust the parameters of its. Some machine tool failure is often not timely because the parameters change due to some not meet. Of course, these failures are the fault of the areas are soft.7. Measurement of Comparative LawCNC system in the design of printed circuit board manufacturing plant, in order to adjust, repair facilities, in the printed circuit board designed a number of test terminals. Users can also use normal printed circuit board terminals comparing the measured and the difference between the printed circuit board failure. These terminals can detect the voltage and waveform measurements, analyze the causes of failure and failure location. Even on a normal printed circuit board can sometimes artificially create "fault", such as broken connection or short circuit, unplug the components, in order to determine the real cause of failure. Therefore, maintenance personnel should be in the usual accumulation of key parts of the printed circuit board or failure-prone parts of the right in the normal waveform and voltage values. Because the CNC system manufacturer often does not provide the information in this regard.8. Percussion methodWhen the CNC system failures showed Ruoyouruowu, often used method for detecting the fault struck the site lies. This is because the numerical control system is composed by the multi-block printed circuit boards, each board has a lot of solder joints, plates or between modules and is connected through the connectors and cables. Therefore, any cold solder joint or bad, may cause a malfunction. When the tap with the insulation and poor contact with Weld doubt at fault must be repeated reproduction.9. Local heating methodAfter a long running CNC system components are to be aging, performance will deteriorate. When they are not fully damaged, failures will become from time to time. Then heat can be used such as a hair dryer or electric iron is suspected to local heating components, accelerating the aging so thoroughly exposed fault components. Of course, using this method, be sure to pay attention to components of the temperature parameters, do not roast the original device is a good or bad.10. Principle of analysisThe composition according to principles of numerical control system can be analyzed from various points of logical levels and logical parameters (such as voltage or waveform) and then with a multimeter, logic pen, only the oscilloscope or logic analyzer to measure, analyze and compare, and thus failure positioning. Using this method, which requires maintenance personnel to be on the whole system or the principle of each circuit have a clear, deep understanding.Based on the above principles and methods, we may be itemized on the check it and eliminate the causes.The first possible failure for the system output pulse time is not enough, we adjust the M-code system, start the spindle output time, found the problem still exists, and then find the next possible cause may be in the drive to move the state, refer to the manual drive , set parameters start the spindle, the problem still exists we suspected spindle motor short-circuit, resulting in thermal relay protection. Then find the cause of the short, so that the spindle thermal relay reset the start and found that the normal operation of the spindle, the problem solved.Fourth, do a lessons learned and recorded. After troubleshooting, repair work can not be considered complete, still need technical and management aspects of the underlying causes of failure have to take appropriate measures to prevent failures from happening again. Underfield conditions when necessary use of mature technologies to transform and improve the equipment. Finally, the failure of the maintenance of the phenomenon, cause analysis, resolution process, the replacement of components, legacy, etc. to make a record.数控技术的发展与维修数控技术及装备是发展新兴高新技术产业和尖端工业的使能技术和最基本的装备。
数控专业毕业论文及英译中文

数控技术一,我国数控系统的发展史1.我国从1958年起,由一批科研院所,高等学校和少数机床厂起步进行数控系统的研制和开发。
由于受到当时国产电子元器件水平低,部门经济等的制约,未能取得较大的发展。
2.在改革开放后,我国数控技术才逐步取得实质性的发展。
经过“六五"(81----85 年)的引进国外技术,“七五” (86——90 年)的消化吸收和“八五” (91~一-95年)国家组织的科技攻关,才使得我国的数控技术有了质的飞跃,当时通过国家攻关验收和鉴定的产品包括北京珠峰公司的中华I型,华中数控公司的华中I型和沈阳高档数控国家工程研究中心的蓝天I 型,以及其他通过“国家机床质量监督测试中心”测试合格的国产数控系统如南京四开公司的产品。
3.我国数控机床制造业在80年代曾有过高速发展的阶段,许多机床厂从传统产品实现向数控化产品的转型。
但总的来说,技术水平不高,质量不佳,所以在90年代初期面临国家经济由计划性经济向市场经济转移调整,经历了几年最困难的萧条时期,那时生产能力降到50%库存超过4个月。
从1 9 9 5年“九五” 以后国家从扩大内需启动机床市场,加强限制进口数控设备的审批,投资重点支持关键数控系统、设备、技术攻关,对数控设备生产起到了很大的促进作用,尤其是在1 9 9 9年以后,国家向国防工业及关键民用工业部门投入大量技改资金,使数控设备制造市场一派繁荣。
三,数控车的工艺与工装削阅读:133数控车床加工的工艺与普通车床的加工工艺类似,但由于数控车床是一次装夹,连续自动加工完成所有车削工序,因而应注意以下几个方面。
1.合理选择切削用量对于高效率的金属切削加工来说,被加工材料、切削工具、切削条件是三大要素。
这些决定着加工时间、刀具寿命和加工质量。
经济有效的加工方式必然是合理的选择了切削条件。
切削条件的三要素:切削速度、进给量和切深直接引起刀具的损伤。
伴随着切削速度的提高,刀尖温度会上升,会产生机械的、化学的、热的磨损。
数控技术在机械制造中的有效应用外文文献翻译、中英文翻译、外文翻译

本科生毕业设计 (论文)
外文翻译
原文标题The Effective Use in the Process of Numerical
Technology in Mechanical Manufacturing
译文标题数控技术在机械制造中的有效应用
作者所在系别机电工程学院
作者所在专业车辆工程
作者所在班级B13142
作者姓名郝立新
作者学号201322375
指导教师姓名赵秋芳
指导教师职称副教授
完成时间2017 年 2 月
北华航天工业学院教务处制
注:1. 指导教师对译文进行评阅时应注意以下几个方面:①翻译的外文文献与毕业设计(论文)的主题是否高度相关,并作为外文参考文献列入毕业设计(论文)的参考文献;②翻译的外文文献字数是否达到规定数量(3 000字以上);③译文语言是否准确、通顺、具有参考价值。
2. 外文原文应以附件的方式置于译文之后。
- 1、下载文档前请自行甄别文档内容的完整性,平台不提供额外的编辑、内容补充、找答案等附加服务。
- 2、"仅部分预览"的文档,不可在线预览部分如存在完整性等问题,可反馈申请退款(可完整预览的文档不适用该条件!)。
- 3、如文档侵犯您的权益,请联系客服反馈,我们会尽快为您处理(人工客服工作时间:9:00-18:30)。
摘要
Abstract
数控技术是用数字信息对机械运动和工作过程进行控制的技术, 是现代化工业生产中的一门发展十分迅速的高新技术。
数控装备是以数控技术为代表的新技术, 应用于传统制造产业和新型制造业形成的机电一体化产业, 即所谓的数字化装备。
本文简要分析了数控机床高速化、高精度化、可靠性、工艺复合性和多轴化等发展趋势,并提出了我国数控机床发展中存在的一些问题。
Numerical control technology is the technology controlled to mechanical movement and work process with digital information. I t’s a very rapidly developing technology in modern industrial production. Numerical control equipment is the new technology represented by numerical control technology forms to the manufacture industry of the tradition and infiltration of the new developing manufacturing industry, namely the so-called digital equipment. This paper analyzes the development trend of numerical control machine tools of high-speed, high-accuracy, reliability, process complex and multi-axis, and presents some of the problems existing in the development of China’s numerical control machine tools.
关键词:精度材料市场竞争力
Keywords: accuracy material market competitive
I。