铝合金电阻点焊和缝焊工艺
铝合金焊接方法
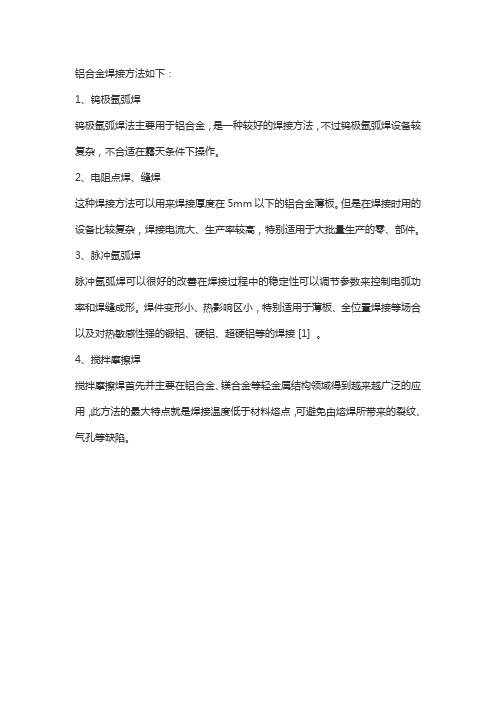
铝合金焊接方法如下:
1、钨极氩弧焊
钨极氩弧焊法主要用于铝合金,是一种较好的焊接方法,不过钨极氩弧焊设备较复杂,不合适在露天条件下操作。
2、电阻点焊、缝焊
这种焊接方法可以用来焊接厚度在5mm以下的铝合金薄板。
但是在焊接时用的设备比较复杂,焊接电流大、生产率较高,特别适用于大批量生产的零、部件。
3、脉冲氩弧焊
脉冲氩弧焊可以很好的改善在焊接过程中的稳定性可以调节参数来控制电弧功率和焊缝成形。
焊件变形小、热影响区小,特别适用于薄板、全位置焊接等场合以及对热敏感性强的锻铝、硬铝、超硬铝等的焊接 [1] 。
4、搅拌摩擦焊
搅拌摩擦焊首先并主要在铝合金、镁合金等轻金属结构领域得到越来越广泛的应用,此方法的最大特点就是焊接温度低于材料熔点,可避免由熔焊所带来的裂纹、气孔等缺陷。
铝合金的焊接方法
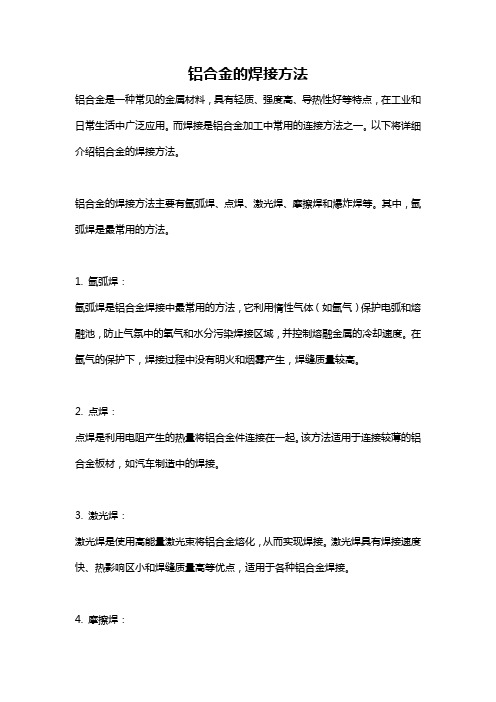
铝合金的焊接方法铝合金是一种常见的金属材料,具有轻质、强度高、导热性好等特点,在工业和日常生活中广泛应用。
而焊接是铝合金加工中常用的连接方法之一。
以下将详细介绍铝合金的焊接方法。
铝合金的焊接方法主要有氩弧焊、点焊、激光焊、摩擦焊和爆炸焊等。
其中,氩弧焊是最常用的方法。
1. 氩弧焊:氩弧焊是铝合金焊接中最常用的方法,它利用惰性气体(如氩气)保护电弧和熔融池,防止气氛中的氧气和水分污染焊接区域,并控制熔融金属的冷却速度。
在氩气的保护下,焊接过程中没有明火和烟雾产生,焊缝质量较高。
2. 点焊:点焊是利用电阻产生的热量将铝合金件连接在一起。
该方法适用于连接较薄的铝合金板材,如汽车制造中的焊接。
3. 激光焊:激光焊是使用高能量激光束将铝合金熔化,从而实现焊接。
激光焊具有焊接速度快、热影响区小和焊缝质量高等优点,适用于各种铝合金焊接。
4. 摩擦焊:摩擦焊是通过在接触面上施加压力和产生热量,将铝合金摩擦热熔融并加以压实。
该方法适用于焊接铝合金和其他金属之间的连接。
5. 爆炸焊:爆炸焊是利用爆炸产生的高温和高压将两个铝合金件连接在一起。
该方法适用于焊接较大尺寸的铝合金构件。
除了上述常见的焊接方法外,还有一些特殊的焊接方法,如熔覆焊、滚焊和冷焊等。
在进行铝合金焊接时,需要注意以下几点:1. 选择合适的焊接材料和焊接工艺,根据焊接材料的种类、厚度和焊接强度要求等因素确定焊接方法。
2. 预处理焊缝,包括去除焊接区域的氧化皮、油污和杂质,以保证焊接质量。
3. 选择合适的焊接电流和焊接速度,以避免产生焊接缺陷,如焊接裂纹和气孔等。
4. 控制焊接区域的温度,避免过热和过冷引起的焊接缺陷。
5. 使用适当的焊接保护措施,如惰性气体保护和冷却液冷却,以确保焊接质量。
总结起来,铝合金的焊接方法有多种,每种方法都适用于不同的焊接需求。
在选择和使用焊接方法时,需要考虑材料的性质、焊接强度要求和工艺条件等因素。
正确选择和使用焊接方法,可以保证焊接质量,提高铝合金制品的性能和使用寿命。
电阻焊接原理与电阻点焊过程四个阶段

电阻焊接原理与电阻点焊过程四个阶段
电阻焊虽然具有劳动条件好,不需另加焊接材料,操作简便,易实现机械化等优点;但也受到耗电量大、电极棒更换、被焊材料导电性能、适用的接头形式、以及可焊工件厚度(或断面尺寸)等因素的限制。
在动力电池的成组工艺中,电阻焊作为一种比较成熟的工艺,被在一些场合应用,比如单体与母排的焊接,电池极耳与并联导电条的连接等等。
由于设备简单,成本较低,在电池行业发展早期,应用比较多。
虽然近年有逐步被更先进的激光焊接和超声焊接替代的趋势……不管怎样,整理一份资料,了解一下这位成型工艺界的前辈。
电阻焊虽然具有劳动条件好,不需另加焊接材料,操作简便,易实现机械化等优点;但也受到耗电量大、电极棒更换、被焊材料导电性能、适用的接头形式、以及可焊工件厚度(或断面尺寸)等因素的限制。
电阻焊接原理
电阻焊(resistance welding)是把工件置于一定的电极力夹紧间,然后利用接电流通过件所析出的电阻热使被材料熔化,待冷却后形成可靠点的接方法。
电阻焊基本形式如下图所示,将即将接的材料 3 夹紧于两电极2 之间,在施加一定的接压力后,接变压器 1 在接区释放较大的电流,并持续一定的时间,直到件的接触面间出现了真实的接触点后,再继续加大接电流让熔核持续地生长,此时接材料接触位置的原子不断被激活后形成熔化核心4。
最后接变压器停止通电,被融化件材料遇冷凝固为点。
利用电流流经工件接触面及邻近区域产生的电阻热效应将其加热到熔化或塑性状态,使之形成金属结合的一种方法。
电阻焊方法主要有四种,即点、缝、凸、对。
电阻焊点的热源是电流通过接区产生的电阻热。
电阻焊点时,电流通过件产生的热量可由下式确定:
Q=I Rt。
电阻点焊操作流程与注意事项

电阻点焊操作流程与注意事项1、电阻点焊机焊接方法——点焊点焊是将焊件装配成搭接接头,并压紧在两柱状电极之间,利用电阻热熔化母材金属,形成焊点的电阻焊方法。
点焊主要用于薄板焊接。
点焊的工艺过程:(1)预压,保证工件接触良好。
(2)通电,使焊接处形成熔核及塑性环。
(3)断电锻压,使熔核在压力继续作用下冷却结晶,形成组织致密、无缩孔、裂纹的焊点。
2、电阻点焊机焊接方法——缝焊(1)缝焊的过程与点焊相似,只是以旋转的圆盘状滚轮电极代替柱状电极,将焊件装配成搭接或对接接头,并置于两滚轮电极之间,滚轮加压焊件并转动,连续或断续送电,形成一条连续焊缝的电阻焊方法。
(2)缝焊主要用于焊接焊缝较为规则、要求密封的结构,板厚一般在3mm以下3、电阻点焊机焊接方法——对焊对焊是使焊件沿整个接触面焊合的电阻焊方法。
4、电阻点焊机焊接方法——凸焊凸焊(projection welding ),是在一工件的贴合面上预先加工出一个或多个突起点,使其与另一工件表面接触并通电加热,然后压塌,使这些接触点形成焊点的电阻焊方法。
凸焊是点焊的一种变形,主要用于焊接低碳钢和低合金钢的冲压件。
板件凸焊最适宜的厚度为0.5~4mm,小于0.25mm时宜采用点焊。
随着汽车工业发展,高生产率的凸焊在汽车零部件制造中获得大量应用。
凸焊在线材、管材等连接上也获得普遍应用。
)在使用点焊机作业过程中的注意事项:1、在作业时,应检查气路及水流量检测开关,确保气路、水冷系统畅通。
气体应保持干燥。
排水温度不得超过40℃,排水量可根据气温调节。
2、严禁在引燃电路中加大熔断器。
3、当控制箱长期停用时,每月应通电加热30min.更换闸流管时应邓热30min。
正常工作的控制箱的预热时间不得小于5min。
4、中频点焊机焊接操作及配合人员必须按规定穿戴劳动防护用品。
5、现场使用的中频点焊机,应设有防雨、防潮、防晒的机棚,并应装设相应的消防器材。
6、当清除焊件焊渣时,应戴防护眼镜,头部应避开敲击焊渣飞溅方向。
电阻点焊原理及工艺

b)单块板中
c)点焊时
i一电流线 j一电流密度 jc一平均电流密度
2)边缘效应与绕流现象
边缘效应:在点焊过程中,当电流流过焊件时, 电流将从板的中部向边缘扩展,使整个焊件的 电流场呈双鼓形。
原因:焊件的横截面积远大于焊件与电极间的 横截面积 。
绕流效应:由于焊接区温度不均匀,促使电 流线从中间向四周扩散的现象。
这种配合是以 焊接过程中不产生 喷溅为主要特征, 这是目前国外几种 常用规范(RWMA、
MIL spec、BWMA 等)的制定依据。根 据这一原则制定的I、 F关系曲线称喷溅 临界曲线。
点焊时的分流
点焊分流的影响因素
焊点距的影响:连续点焊时,点距愈小,板 材愈厚,分流愈大;如果所焊材料是导电性 良好的轻合金,分流将更严重,为此必须加 大点距。
3)焊件内部电阻的近似计算
2RW
K1 K2 T
2 d0
2
4
K1 边缘效应引起电流场扩展的系数;
K2 绕流现象引起电流场扩展的系数;
T 焊接区金属的电阻率;
单个焊件的厚度;
d0 电极与焊件接触面直径。
1.0
0.8
K1
0.6 0.4
0.2
01 2 3 4 5 6
d0
K1 0.82 ~ 0.84
第二章 电阻点焊工艺
第一节 点焊过程分析 一、焊接循环 1。定义:在电阻焊接过程中,完成一个焊点或 焊缝所需要的全部过程或全部阶段 2。点焊的基本焊接循环
F,I
加压 通电焊接 维持 休止 加压
3。复杂的点焊焊接循环
F,I
Fu
Fp
Fw
I1
I2
I3
二、点焊接头形成过程
铝合金通用焊接工艺规程

铝合金通用焊接工艺规程1使用范围及目的范围:本规范是适用于地铁铝合金部件焊接全过程的通用工艺要求。
目的:与焊接相关的作业人员按标准规范作业,同时也使焊接过程检查更具可操作性。
2焊前准备的要求2.1在焊接作业前首先必须根据图纸检查来料或可见的重要尺寸、形位公差和焊接质量,来料不合格不能进行焊接作业。
2.2在焊接作业前,必须将残留在产品表面和型腔内的灰尘、飞溅、毛刺、切削液、铝屑及其它杂物清理干净。
2.3用棉布将来料或工件上的灰尘和脏物擦干净,如果工件上有油污,使用清洗液清理干净。
2.4使用风动不锈钢丝轮将焊缝区域内的氧化膜打磨干净,以打磨处呈白亮色为标准,打磨区域为焊缝两侧至少25mm 以上。
2.5焊前确认待焊焊缝区域无打磨时断掉的钢丝等杂物。
2.6钢焊和铝焊的打磨、清理工具禁止混用。
2.7原则上工件打磨后在48小时内没有进行焊接,酸洗部件在72小时内没有进行焊接,则焊前必须重新打磨焊接区域。
2.8为保证焊丝的质量,焊丝原则上用完后再到焊丝房领用,对于晚班需换焊丝的,能够在当天白班下班前领用,制止现场长工夫(24小时以上)存放焊丝。
2.9在焊接功课前,必须检查焊接装备和工装处于正常工作状态。
焊前应检查焊机喷嘴的实际气流量(允差为+3L/min),自动焊焊丝在8圈以下,手工焊焊丝在5圈以上,不然需要调换气体或焊丝;检查导电嘴是否拧紧,喷嘴是否需要清算。
导电嘴不克不及只简单的采用手动拧紧,必须采用尖嘴钳拧紧。
检查工装状态是否完好,若工装有损坏,应立刻告诉工装管理员进行核查,并组织维修,制止在工装异常状态下进行焊接操作。
2.10焊接前必须检查环境的温度和湿度。
功课区要求温度在5℃以上,MIG焊湿度小于65%,TIG焊湿度小于70%。
环境不符合要求,不克不及进行焊接功课。
2.11焊接过程中不允许有穿堂风。
因此,在焊接作业前必须关闭台位附近的通道门。
当焊接过程中,如果有人打开台位相近处的大门,则要立即停止施焊。
铝合金的点焊
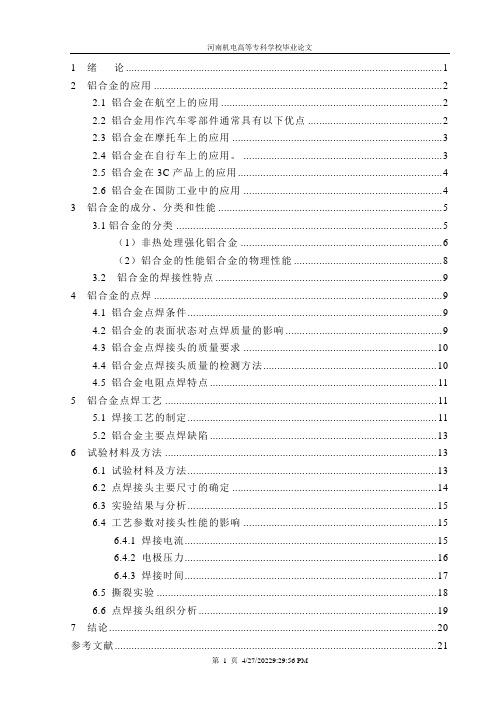
1 绪论 (1)2 铝合金的应用 (2)2.1 铝合金在航空上的应用 (2)2.2 铝合金用作汽车零部件通常具有以下优点 (2)2.3 铝合金在摩托车上的应用 (3)2.4 铝合金在自行车上的应用。
(3)2.5 铝合金在3C产品上的应用 (4)2.6 铝合金在国防工业中的应用 (4)3 铝合金的成分、分类和性能 (5)3.1铝合金的分类 (5)(1)非热处理强化铝合金 (6)(2)铝合金的性能铝合金的物理性能 (8)3.2铝合金的焊接性特点 (9)4 铝合金的点焊 (9)4.1 铝合金点焊条件 (9)4.2 铝合金的表面状态对点焊质量的影响 (9)4.3 铝合金点焊接头的质量要求 (10)4.4 铝合金点焊接头质量的检测方法 (10)4.5 铝合金电阻点焊特点 (11)5 铝合金点焊工艺 (11)5.1 焊接工艺的制定 (11)5.2 铝合金主要点焊缺陷 (13)6 试验材料及方法 (13)6.1 试验材料及方法 (13)6.2 点焊接头主要尺寸的确定 (14)6.3 实验结果与分析 (15)6.4 工艺参数对接头性能的影响 (15)6.4.1 焊接电流 (15)6.4.2 电极压力 (16)6.4.3 焊接时间 (17)6.5 撕裂实验 (18)6.6 点焊接头组织分析 (19)7 结论 (20)参考文献 (21)1 绪论随着现代工业的发展,对工业材料的要求越来越向着质量轻﹑强度高、易加工的方向发展。
由于铝及铝合金材料具有一系列的优良特性,已广泛应用于国民经济的各个领域,成为发展国民经济与提高人民物质生活和文化生活水平的重要基础材料。
近二十年来,我国的铝加工业发展十分迅速,其产量已从1980年不到30万吨,发展到2005年的583.7万吨。
同时,出现了许多的新材料、新技术、新工艺及新设备。
我国已经成为名副其实的铝业大国。
铝和铝合金具有优异的物理性能和力学性能,其密度低、比强度高、热导率高、电导率高,耐蚀能力强,已广泛应用于机械、电力、化工、轻工、航空、航天、铁道、舰船、车辆等工业内的焊接结构产品上,例如飞机、飞船、火箭、导弹、高速铁道机车和车辆、鱼雷和鱼雷快艇、轻型汽车、自行车和赛车、大小化工容器、空调器、热交换器、雷达天线、微波器件等,都采用了铝和铝合金材料,制成各种熔焊、电阻焊、钎焊结构。
电阻焊的基本原理
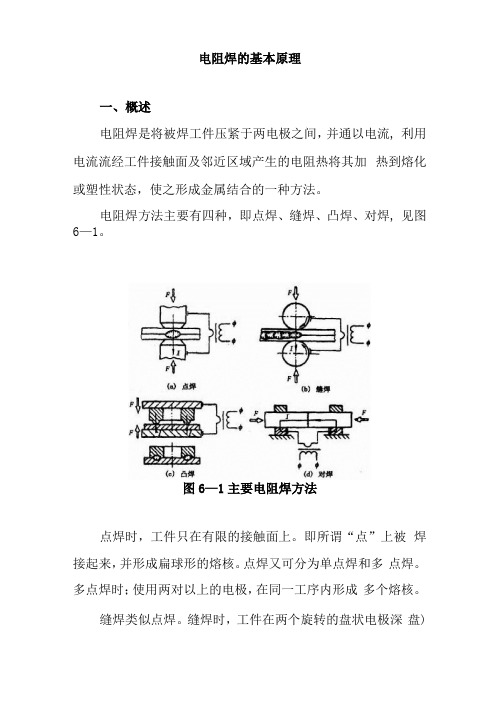
电阻焊的基本原理一、概述电阻焊是将被焊工件压紧于两电极之间,并通以电流, 利用电流流经工件接触面及邻近区域产生的电阻热将其加热到熔化或塑性状态,使之形成金属结合的一种方法。
电阻焊方法主要有四种,即点焊、缝焊、凸焊、对焊, 见图6—1。
图6—1主要电阻焊方法点焊时,工件只在有限的接触面上。
即所谓“点”上被焊接起来,并形成扁球形的熔核。
点焊又可分为单点焊和多点焊。
多点焊时;使用两对以上的电极,在同一工序内形成多个熔核。
缝焊类似点焊。
缝焊时,工件在两个旋转的盘状电极深盘)间通过后,形成一条焊点前后搭接的连续焊缝。
凸焊是点焊的一种变型。
在一个工件上有预制的凸点,凸焊时,一次可在接头处形成一个或多个熔核。
对焊时,两工件端面相接触,经过电阻加热和加压后沿整个接触面被焊接起来。
电阻焊有下列优点:(1)熔核形成时,始终被塑性环包围,熔化金属与空气隔绝,冶金过程简单。
(2)加热时间短,热量集中,故热影响区小,变形与应力也小,通常在焊后不必安排校正和热处理工序。
(3)不需要焊丝、焊条等填充金属,以及氧、乙快、氩等焊接材料,焊接成本低。
(4)操作简单,易于实现机械化和自动化,改善了劳动条件。
(5)生产率高,且无噪声及有害气体,在大批量生产中,可以和其他制造工序一起编到组装线上。
但闪光对焊因有火花喷溅,需要隔离。
电阻焊缺点:(1)目前还缺乏可靠的无损检测方法,焊接质量只能靠工艺试样和工件的破坏性试验来检查,以及靠各种监控技术来保证。
(2)点、缝焊的搭接接头不仅增加了构件的重量,且因在两板间熔核周围形成夹角,致使接头的抗拉强度和疲劳强度均较低。
(3)设备功率大,机械化、自动化程度较高,使设备成本较高、维修较困难,并且常用的大功率单相交流焊机不利于电网的正常运行。
随着航空航天、电子、汽车、家用电器等工业的发展,电阻焊越来受到社会的重视,同时,对电阻焊的质量也提出了更高的要求。
可喜的是,我国微电子技术的发展和大功率可控硅、整流器的开发,给电阻焊技术的提高提供了条件。
铝合金焊接性能及焊接接头性能

铝合金焊接性能及焊接接头性能摘要:在新科学技术的影响下,高速动车组也在进行全面提升发展,高速动车的车体结构的材料也进行更新换代,传统的钢材质的车体结构已经开始逐渐被铝合金材质的车体进行淘汰,铝合金材质的车体结构比钢材质的车体更加轻盈,采用新材料能够使高速动车组的车体实现轻量化,但同时还能保障高速动车的行程安全,新材料就需要新的焊接技术,基于此对铝合金焊接技术和性能以及焊接接头的性能成为本文探究的内容。
关键词:铝合金焊接;焊接技术;性能分析引言:随着矿产资源开采和冶炼技术的进步,铝合金材质的使用量和使用范围也得到很大的提升,关乎我们生活的方方面面,比如:铝合金材质的阳台门窗门框、自行车的铝合金车架和铝合金材质的高速动车组车体。
铝合金材料也需要进行切割和焊接,才能达到使用要求,铝合金的焊接不同于传统铁质材料的焊接,铝合金焊接技术需要面对很多新的焊接问题,针对不同的焊件需要运用不同的焊接技术,不同的焊接技术焊接出来的产品具有不同的焊接性能。
一、铝合金材料的特点铝合金材料有很多有优良的性能,大体可以归结为以下几点:第一点:铝合金材质很多都具有质地轻盈而且材质较软。
这是因为同等体积铝的重量大约是同等体积钢重量的三分之一。
第二点:铝合金材料也具有很好的强度。
虽然,低碳钢的抗拉强度是纯铝的五倍。
但纯铝经过合金化强化以及热处理强化后形成的铝合金,其强度能达到刚才所具有的强度值。
第三点:主要是因为铝合金材料与空气后在其表面会形成一层致密的化学性质稳定的三氧化二铝薄膜,若是对铝合金材料进行氧化铝膜处理法,就能使其具有全面防止腐蚀的特点。
第四点:因为铝材具有良好的柔软和可塑性,铝合金材料具有良好的加工性。
比如:高速动车的车体就是运用型材具有良好挤压性的特点,而且这种材质进行二次加工和进行弯曲化加工时也都比较容易实现。
第五点:铝合金材料易于循环利用。
冶炼时纯铝的熔点比钢材低很多,所以废弃的铝材料更易于实现回收和再利用。
电阻点焊方法和工艺

电阻点焊方法和工艺点焊方法和工艺一、点焊方法:点焊通常分为双面点焊和单面点焊两大类。
双面点焊时,电极由工件的两侧向焊接处馈电。
典型的面点焊方式如图11-5所示。
图中a是最常用的方式,这时工件的两侧均有电极压痕。
图中b表示用大焊接面积的导电板做下电极,这样可以消除或减轻下面工件的压痕。
常用于装饰性面板的点焊。
图中c为同时焊接两个或多个点焊的双面点焊,使用一个变压器而将各电极并联,这时,所有电流通路的阻抗必须基本相等,而且每一焊接部位的表面状态、材料厚度、电极压力都需相同,才能保证通过各个焊点的电流基本一致。
图中d为采用多个变压器的双面多点点焊,这样可以避免c的不足。
单面点焊时,电极从工件的同一侧送入焊接位置。
典型的单面点焊方法如图11-6所示。
图中a为单面单点点焊。
不形成焊点的焊条采用大直径、大接触面,以降低电流密度。
图中B为单面双点点焊,无分流。
此时,所有焊接电流流过焊接区域。
在图C中,有一个单面双点点焊,流过上部工件的电流没有通过焊接区域形成气流。
为了为焊接电流提供低电阻路径,在工件下方垫一块铜垫板。
图中D显示,当两个焊接点之间的距离L较大时,例如,在焊接骨架构件和复合板时,为了避免因加热不当导致复合板翘曲,降低两电极之间的电阻,采用了特殊的铜桥a,它与电极同时压在工件上。
在大量生产中,单面多点点焊获得广泛应用。
这时可采用由一个变压器供电,各对电极轮流压住工的型式(图11-7a),也可采用各对电极均由单独的变压器供电,全部电极同时压住工件的型式(图11-7b).后一型式具有较多优点,应用也较广泛。
其优点有:各变压器可以安置得离所联电极最近,因而。
其功率及尺寸能显著减小;各个焊点的工艺参数可以单独调节;全部焊点可以同时焊接、生产率高;全部电极同时压住工件,可减少变形;多台变压器同时通电,能保证三相负荷平衡。
二、点焊工艺参数选择通常,电极端面的形状和尺寸根据工件的材料和厚度以及材料的焊接条件表确定。
铝基复合材料焊接
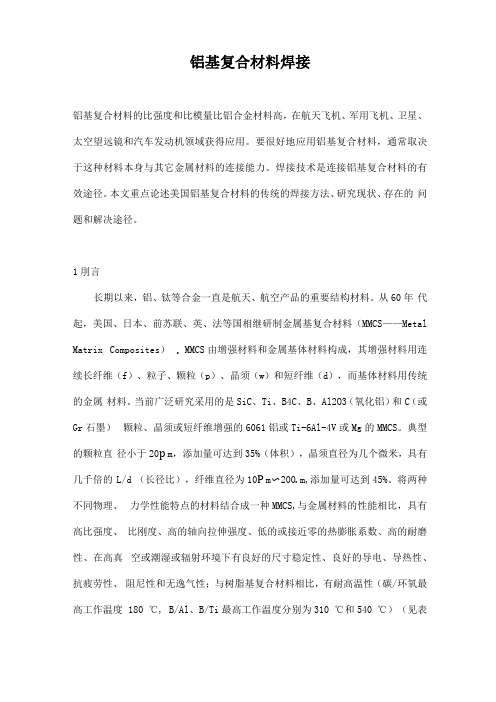
铝基复合材料焊接铝基复合材料的比强度和比模量比铝合金材料高,在航天飞机、军用飞机、卫星、太空望远镜和汽车发动机领域获得应用。
要很好地应用铝基复合材料,通常取决于这种材料本身与其它金属材料的连接能力。
焊接技术是连接铝基复合材料的有效途径。
本文重点论述美国铝基复合材料的传统的焊接方法、研究现状、存在的问题和解决途径。
1刖言长期以来,铝、钛等合金一直是航天、航空产品的重要结构材料。
从60年代起,美国、日本、前苏联、英、法等国相继研制金属基复合材料(MMCS——Metal Matrix Composites)o MMCS由增强材料和金属基体材料构成,其增强材料用连续长纤维(f)、粒子、颗粒(p)、晶须(w)和短纤维(d),而基体材料用传统的金属材料。
当前广泛研究采用的是SiC、Ti、B4C、B、Al2O3(氧化铝)和C(或Gr石墨)颗粒、晶须或短纤维增强的6061铝或Ti-6Al-4V或Mg的MMCS。
典型的颗粒直径小于20p m,添加量可达到35%(体积),晶须直径为几个微米,具有几千倍的L/d (长径比),纤维直径为10P m〜200. m,添加量可达到45%。
将两种不同物理、力学性能特点的材料结合成一种MMCS,与金属材料的性能相比,具有高比强度、比刚度、高的轴向拉伸强度、低的或接近零的热膨胀系数、高的耐磨性、在高真空或潮湿或辐射环境下有良好的尺寸稳定性、良好的导电、导热性、抗疲劳性、阻尼性和无逸气性;与树脂基复合材料相比,有耐高温性(碳/环氧最高工作温度180 ℃, B/Al、B/Ti最高工作温度分别为310 ℃和540 ℃)(见表1)。
MMCS不但可以制成板材、面板、管材和型材,还可以用面板和型材扩散焊连接成为波纹焊接结构。
这种波纹结构可承受510 MPa的的轴向应力,是锻造同样波纹金属结构的1.4倍。
为满足航天工业的发展需要,美国60年代研制出以连续B纤维增强的铝基复合材料,70年代用于航天飞机的主隔框、翼肋构架支柱和管子上。
铝合金电阻点焊所存在的主要问题
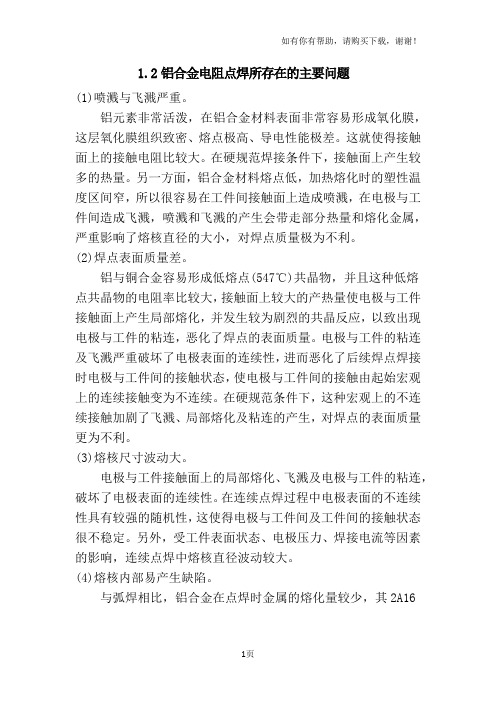
1.2铝合金电阻点焊所存在的主要问题(1)喷溅与飞溅严重。
铝元素非常活泼,在铝合金材料表面非常容易形成氧化膜,这层氧化膜组织致密、熔点极高、导电性能极差。
这就使得接触面上的接触电阻比较大。
在硬规范焊接条件下,接触面上产生较多的热量。
另一方面,铝合金材料熔点低,加热熔化时的塑性温度区间窄,所以很容易在工件间接触面上造成喷溅,在电极与工件间造成飞溅,喷溅和飞溅的产生会带走部分热量和熔化金属,严重影响了熔核直径的大小,对焊点质量极为不利。
(2)焊点表面质量差。
铝与铜合金容易形成低熔点(547℃)共晶物,并且这种低熔点共晶物的电阻率比较大,接触面上较大的产热量使电极与工件接触面上产生局部熔化,并发生较为剧烈的共晶反应,以致出现电极与工件的粘连,恶化了焊点的表面质量。
电极与工件的粘连及飞溅严重破坏了电极表面的连续性,进而恶化了后续焊点焊接时电极与工件间的接触状态,使电极与工件间的接触由起始宏观上的连续接触变为不连续。
在硬规范条件下,这种宏观上的不连续接触加剧了飞溅、局部熔化及粘连的产生,对焊点的表面质量更为不利。
(3)熔核尺寸波动大。
电极与工件接触面上的局部熔化、飞溅及电极与工件的粘连,破坏了电极表面的连续性。
在连续点焊过程中电极表面的不连续性具有较强的随机性,这使得电极与工件间及工件间的接触状态很不稳定。
另外,受工件表面状态、电极压力、焊接电流等因素的影响,连续点焊中熔核直径波动较大。
(4)熔核内部易产生缺陷。
与弧焊相比,铝合金在点焊时金属的熔化量较少,其2A16铝合金电阻点焊焊点表面缺陷分析与工艺优化导热系数又比较大,所以熔核的冷却速度非常快。
另外,铝合金是非导磁材料,液态熔核区的流动速度非常小,熔核在凝固时极易形成缩孔、缩松和气孔。
虽然这些缺陷对接头强度影响不大,但对接头的疲劳性能却有显著影响。
(5)结合线伸入。
结合线伸入是点焊和缝焊某些高温合金和铝合金时特有的缺陷,是指结合面伸入到熔核中的部分。
对于铝合金,主要是工件表面有强氧化物,焊接过程中通电时间短暂,导致结合面熔合不完整。
铝及铝合金焊接要点解析

铝及铝合金焊接要点解析铝(Aluminium)是一种金属元素,元素符号为Al,原子序数为13。
其单质是一种银白色轻金属,有延展性。
商品常制成棒状、片状、箔状、粉状、带状和丝状。
在潮湿空气中能形成一层防止金属腐蚀的氧化膜。
铝粉在空气中加热能猛烈燃烧,并发出眩目的白色火焰。
易溶于稀硫酸、硝酸、盐酸、氢氧化钠和氢氧化钾溶液,难溶于水。
相对密度2.70。
熔点660℃。
沸点2327℃。
铝元素在地壳中的含量仅次于氧和硅,居第三位,是地壳中含量最丰富的金属元素。
航空、建筑、汽车三大重要工业的发展,要求材料特性具有铝及其合金的独特性质,这就大大有利于这种新金属铝的生产和应用。
应用极为广泛。
工业纯铝具有铝的一般特点,密度小,导电、导热性能好,抗腐蚀性能好,塑性加工性能好,可加工成板、带、箔和挤压制品等,可进行气焊、氩弧焊、点焊。
工业纯铝不能热处理强化,可通过冷变形提高强度,惟一的热处理形式是退火,再结晶开始温度与杂质含量和变形度有关,一般在200℃左右。
退火板材的σb=80~100MPa,σ0.2=30~50MPa,ζ=35%~40%,HB=25~30。
经60%~80%冷变形,虽然能提高到150~180MPa,但ζ值却下降到1%~1.5%。
增加铁、硅杂质含量能提高强度,但降低塑性、导电性和抗蚀性。
铝合金焊接是指铝合金材料的焊接过程。
铝合金强度高和质量轻。
主要焊接工艺为手工TIG焊(非熔化极惰性气体保护焊)、自动TIG焊和MIG焊(熔化极惰性气体保护焊),其母材、焊丝、保护气体、焊接设备。
铝及铝合金在现代工程技术所用的各种材料中占有举足轻重的地位,它在世界年产量仅次于钢铁而居第二位,在有色金属中则居第一位。
如果说铝合金最初是在航空工业中崭露头角的话,那么近几十年来,除航空工业外,在航天、汽车、船舶、桥梁、机械制造、电纯铝的熔点低(660℃),熔化时颜色不变,难以观察到熔池,焊接时容易塌陷和烧穿;热导率是低碳钢的三倍,散热快,焊接时不易熔化;线膨胀系数是低碳钢的二倍,焊接时易变形;在空气中易氧化成致密的高熔点氧化膜Al2O3(熔点2050℃),难熔且不导电,焊接时易造成未熔合、夹渣并使焊接过程不稳定。
铝合金的点焊工艺..

图中2b表示用大接触面积的导电板做下电极,这样可以消除或减轻下面工 作的压痕,常用于装饰性面板的点焊。
图2c为,同时焊接两个或多个焊点的双面点焊,使用一个变压器而将各 电极并联。这时,所有电流通路的阻抗必须基本相等,而且每一焊接部 位的表面状态,材料厚度、电极压力都必须相同,才能保证通过各个焊 点的电流基本一致。
铝合金焊接工艺
学性能,使其在焊接过程中有以下 几大特点: 1.1 极强的氧化能力 铝合金与氧的亲和力很大,在空气中极易与氧化合在其表面生成致密 的、厚度约为0.1µm的氧化膜(Al2O3) ,其熔点极高(约2050℃)、密度大 (3.95~4.10kg/m³ ),属于难熔物质,焊接时会阻碍金属之间的良好结合,导 致未焊透“焊缝夹渣”不熔合现象,且由于氧化膜吸附大量水分,容易使 焊缝产生气孔 。 1.2 高的热导率和导电性 铝合金具有较大的导热系数和比热容,比热容比钢约大2倍,导热性约大3 倍。因此焊接时为保证良好熔合,必须采用能量集中、功率大的热源,有时 需采用预热等工艺措施。经验表明:相同焊接速度下,焊接铝合金的热输入 量要比焊接钢材大2~3 倍。
2.1 清洗 清洗是表面准备的第一步,可以使用工业溶液去除材料表面上的油类、 污物或标记。无论是点焊、缝焊或凸焊,在焊前必须进行工件表面清理,以 保证接头质量稳定。铝合金表面进行除油处理时,可以利用稀释剂、汽油、 石油醚、三氯乙烯和全氯乙烯等有机溶剂将其浸泡清洗,或用浸有这些溶剂 的清洁布擦洗。
2.2 氧化膜的清除 材料表面上的氧化膜不能用上述有机溶剂清除,必须用机械或化学的 方法进行清除。
a)搭接接头b)折边接头e-点距b-边距
表1 接头的最小搭接量(单位:mm)
表2 焊点的最小点距
(单位:mm)
4 铝合金的电阻点焊原理
铝合金焊接方法

铝合金焊接方法铝合金是一种常见的金属材料,因其轻质、耐腐蚀和导热性能好而被广泛应用于航空航天、汽车制造和建筑等领域。
然而,铝合金的焊接工艺相对复杂,需要特殊的方法和技术来保证焊接质量。
本文将介绍几种常见的铝合金焊接方法,帮助读者了解如何正确地进行铝合金焊接。
首先,我们来介绍氩弧焊。
氩弧焊是一种常用的铝合金焊接方法,它利用惰性气体氩气作为保护气体,防止氧气和水蒸气对熔化池的侵蚀。
在氩弧焊中,焊接电流较小,焊接速度较快,可以获得较好的焊接质量。
然而,氩弧焊需要较高的焊接技术要求,操作人员需要具备一定的经验和技能。
其次,激光焊接是另一种常见的铝合金焊接方法。
激光焊接利用高能激光束对铝合金进行熔化和连接,具有焊接速度快、热影响区小、变形小等优点。
然而,激光焊接设备成本较高,操作复杂,需要专业的操作人员进行操作,因此在实际应用中较少见。
除了氩弧焊和激光焊接,摩擦搅拌焊也是一种常用的铝合金焊接方法。
摩擦搅拌焊是一种固态焊接方法,利用高速旋转的摩擦搅拌头对铝合金进行搅拌和连接,不需要额外的焊接材料,可以获得较好的焊接质量。
摩擦搅拌焊适用于各种铝合金材料的焊接,尤其适用于铝合金板材的连接。
最后,我们介绍电阻点焊。
电阻点焊是一种适用于薄板铝合金的焊接方法,它利用电流通过两个金属板产生热量,使其瞬间熔化并连接在一起。
电阻点焊操作简单,成本低,适用于大批量生产。
然而,电阻点焊对板材厚度和形状有一定要求,不适用于较厚的铝合金板材。
综上所述,铝合金焊接方法有多种选择,每种方法都有其适用的场景和特点。
在实际应用中,需要根据具体的焊接要求和条件选择合适的焊接方法,保证焊接质量和效率。
希望本文的介绍能够帮助读者更好地理解铝合金焊接方法,为实际生产和工程应用提供参考。
合金条焊接方法
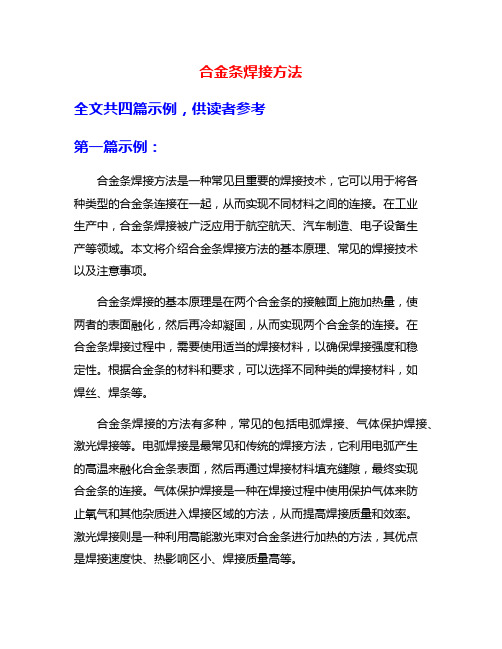
合金条焊接方法全文共四篇示例,供读者参考第一篇示例:合金条焊接方法是一种常见且重要的焊接技术,它可以用于将各种类型的合金条连接在一起,从而实现不同材料之间的连接。
在工业生产中,合金条焊接被广泛应用于航空航天、汽车制造、电子设备生产等领域。
本文将介绍合金条焊接方法的基本原理、常见的焊接技术以及注意事项。
合金条焊接的基本原理是在两个合金条的接触面上施加热量,使两者的表面融化,然后再冷却凝固,从而实现两个合金条的连接。
在合金条焊接过程中,需要使用适当的焊接材料,以确保焊接强度和稳定性。
根据合金条的材料和要求,可以选择不同种类的焊接材料,如焊丝、焊条等。
合金条焊接的方法有多种,常见的包括电弧焊接、气体保护焊接、激光焊接等。
电弧焊接是最常见和传统的焊接方法,它利用电弧产生的高温来融化合金条表面,然后再通过焊接材料填充缝隙,最终实现合金条的连接。
气体保护焊接是一种在焊接过程中使用保护气体来防止氧气和其他杂质进入焊接区域的方法,从而提高焊接质量和效率。
激光焊接则是一种利用高能激光束对合金条进行加热的方法,其优点是焊接速度快、热影响区小、焊接质量高等。
在进行合金条焊接时,需要注意以下几点。
选择适当的焊接材料和焊接方法,确保焊接质量和稳定性。
要掌握好焊接温度和时间,避免出现焊接质量不稳定的问题。
还需要注意保护环境和人员安全,避免因焊接造成的安全事故。
合金条焊接是一种重要的焊接技术,它在工业生产中具有广泛的应用前景。
通过掌握合金条焊接的基本原理、常见的焊接技术和注意事项,可以提高焊接质量和效率,为实现各种合金条的连接提供有力的支持。
希望本文的介绍对您有所帮助,谢谢阅读!第二篇示例:合金条焊接是一种常见的金属加工方法,用于将金属合金条通过焊接的方式连接成一体。
合金条焊接方法可以应用于多种场合,如机械制造、建筑工程、航空航天等领域。
通过合金条焊接,可以实现金属材料之间的牢固连接,提高产品的强度和耐久性。
合金条焊接方法有多种,常见的包括电弧焊接、气体保护焊接、电阻焊接等。
- 1、下载文档前请自行甄别文档内容的完整性,平台不提供额外的编辑、内容补充、找答案等附加服务。
- 2、"仅部分预览"的文档,不可在线预览部分如存在完整性等问题,可反馈申请退款(可完整预览的文档不适用该条件!)。
- 3、如文档侵犯您的权益,请联系客服反馈,我们会尽快为您处理(人工客服工作时间:9:00-18:30)。
中华人民共和国航空工业部部标准HB/Z 77-84铝合金电阻点焊和缝焊工艺1 总则1.1 本标准适用于LF2、LF3、LF6、LF21、LY12、LY16、LC4、LC9变形铝合金电阻点焊及LF2、LF3、LF6、LF21变形铝合金电阻缝焊工艺。
1.2 焊工应有焊接航空产品的焊接操作证书。
2 设备2.1 焊机:点焊机、缝焊机。
2.1.1 焊接铝合金一般选用直流脉冲式、电容储能式、次级整流式等类型的焊机,缝焊机建议选用步进式的。
2.1.2 焊机最好具有三种加压方式:不变的压力、附加锻压力、附加予压和锻压力。
2.1.3 焊机电极臂应有足够的刚性,当施加最大额定压力时,臂长不大于500㎜,弹性挠度应不超过1.5㎜,臂长不大于1200㎜,挠度应不超过2㎜。
2.1.4 焊机在规定气压范围和额定焊接速度下工作时,电极压力的波动应不超过+8%。
上电极下降时应平稳无冲击现象。
2.1.5 焊机工作时,电源电压应在额定值的+5%范围内。
管道压缩空气压力应不低于5kg/cm2,室温应不低于15℃。
2.1.6 焊机的次级回路电阻,直流脉冲焊机应不大于60μΩ,交流焊机应不大于100μΩ,单个活动连结处电阻不大于20μΩ,单个固定结合处电阻不大于2μΩ。
焊机的次级回路电阻至少三个月测量一次,并记入设备档案中。
2.1.7 焊机应定期检修,活动导电部分应定期更换石墨润滑剂。
2.1.8 焊机应配备必要的专用工具。
2.1.9 焊机在安装、改装、大修或改变动力线路之后,由工厂主管部门组织进行鉴定,鉴定合格后才允许投入生产使用。
焊机鉴定内容如下:a.按附录A《焊机鉴定表》规定内容测量焊机的参数。
b.选用生产中常用的一种材料,取最薄和最厚的两种相同厚度的组合进行工艺稳定性试验,试验内容列于表1,试验结果应符合表1及HB5276--84《铝合金电阻点焊和缝焊质量检验》的规定。
在全部试验项目中有一项不合格,则应调整焊机重新试验,直到全部试验项目合格为止。
鉴定试验结果应记入焊机鉴定表中(附录A)。
c.焊机鉴定试验应按生产需要在该焊机上焊接的最高等级接头的要求进行。
2.2 电极和滚盘2.2.1 电极和滚盘可以采用镉青铜或其它铜合金,其导电率应不低于80%IACS(国际标准退火铜)。
布氏硬度不小于110kgf/mm2。
当电极压力不大于600kgf时,可选用布氏硬度不小于80 kgf/mm2的冷拉钢。
2.2.2 电极和滚盘应按不同材料分别打上印记,并不在损伤其工作面的条件下存放。
航空工业部1983-05-30发布1984-07-01实施表1 焊机鉴定焊接试验检验项目注:Pt为一组试样搞剪强度的平均值图1 点焊接头抗剪试样mm图2 缝焊接头拉伸试样2.2.3 电极和滚盘的推荐尺寸列于表2。
2.2.4 电极应采用内部流动水冷却,其冷却面与工作表面之间的距离应不大于15mm,不小于4mm。
表2 mm2.2.5 电极与电极座为锥形面配合,配合精度为4~6级。
电极压力不大于1500kgf或电极直径不大于35mm时,锥度建议采用1:10。
电极压力大于1500kgf时,锥度可选用1:5。
2.2.6 电极和滚盘工作面应在车床上精加工,工作面上不应有碰伤、划伤和其它缺陷。
2.2.7 电极和滚盘工作面尺寸应经常用样板检查,当球面半径变化超过规定尺寸15%时,应更换或按样本修正。
2.2.8 上下电极不允许相互直接接触,停止工作时,应在电极间垫上不致损伤其工作表面的垫片。
3 焊接工艺3.1 一般要求3.1.1 铝合金点焊和缝焊接头一般应为同牌号金相组合。
点焊接头组合层数,一、二级接头应为2层,一般不超过3层。
缝焊接头应为2层。
接头组合板材厚度比一般大于2,三级接头应不大于3。
3.1.2 焊件应有良好的开敞性。
板形件的宽度或筒形件的长度应小于焊机机臂有效伸出长度的两倍。
简形件直径一般不小于400mm。
3.1.3 承受动载荷的接头建议采用双排焊缝。
3.1.4大型或复杂的点焊件,建议在焊缝的两端以及在焊缝上每隔400~500mm铆一个铆钉。
3.1.5 点焊接头的搭接尺寸,焊点位置及分布尺寸列于表表3 mm注:○1接头组合超过2层时,表中尺寸须增加15%~20%。
○2搭接量指平面部分,不包括园角半径。
3.1.6 零件焊接以前,表面不允许人工氧化或涂干燥底漆及其它涂层。
3.1.7 焊件需用多种连接方法时,应首先进行点焊和缝焊,然后再熔焊或铆接。
3.1.8 涂胶点焊零件按工厂编制的专用说明书施焊。
3.1.9 焊件生产中的焊接质量检验按HB5276—84表2的规定。
点焊试样按本标准图1和图4。
缝焊试样按图2、图3和图5。
图4图53.2 焊前准备3.2.1 零件焊接处和试样表面不允许有氧化膜、油污及其它污物。
点焊工艺试样长150~200mm,宽30mm。
缝焊工艺试样长200~300mm,宽30mm。
试样可预先制备储存。
3.2.2 铝合金焊前表面准备可采用工厂制定的化学清洗方法或机械方法清理。
3.2.3 工艺试样的材料应与零件同牌号、同规格、同热处理状态,并一起清洗,其搭接接触电阻应不大于120μΩ。
用测定试样电阻值验证零件的清洗质量,测量方法按HB/Z5128-79《铝合金酸洗工艺》进行。
3.2.4 化学清洗后的零件和试样,在搬运和存放过程中必须防尘和防油污,搬运零件必须戴洁净的手套。
3.2.5 零件化学清洗后至焊接完毕的时间应不超过72小时。
当超过72小时时,如能用选定的焊接规范参数焊出合格的焊缝。
则允许继续焊接,否则必须重新化学清洗。
重新化学清洗后的零件必须在24小时内装配并焊接完毕。
3.2.6 零件在机械清理后必须立即装配和定位焊,并应在24小时内焊接完毕。
3.3 焊接规范参数选定3.3.1在选定的焊机上,根据焊件的材料、厚度、组合要求,用工艺试样按HB5276-84规定的内容,并参照本标准附录B推荐的焊接规范参数,通过试验选定焊件的具体焊接规范参数,试验时应先进行撕破试验。
3.3.2 在选定焊接规范参数,以及对焊接规范参数进行验证时,所用试样的材料牌号、厚度、热处理状态和表面状态应与焊件的相同。
3.3.3 缝焊筒形零件时,外滚盘的直径一般要比内滚盘的大。
3.3.4 全部试验数据应记录保存,选定的焊接规范参数应编入焊件的工艺规程或生产专用记录档案中。
3.3.5低倍检验用的试样经磨光后腐蚀,腐蚀方法可参考表43.4 零件的定位焊3.4.1 凡互换性差并且装配中需修合的大型复杂零件,应按型架或装配孔进行予装配,予装配好的零件检验后,拆开并成套进行表面清洗。
3.4.2 零件的最终装配,可采用工艺螺栓、定位销或工艺铆钉,装配时不允许有再修合,并保持零件洁净。
3.4.3 焊接夹具宜采用非磁性材料制造。
3.4.4 点焊件的装配间隙应不大于1mm,局部间隙大于1mm时,如用手力可以压合,则允许存在。
缝焊件的局部装配间隙应不大于0.3mm。
3.4.5 零件经检验后进行定位焊。
定位焊点的位置、分布和顺序应符合图纸和工艺规程的规定。
3.4.6 定位焊应保证结构的刚性。
尽量防止变形。
定位焊一般先焊曲径半径小或装配间隙较大的部位。
大型零件可以从中间向两端定位。
定位焊点的间距一般为150~200mm。
定位焊后的间隙,防锈铝合金应不大于0.3mm,硬铝合金不大于0.5mm。
3.4.7 点焊件定位焊的焊接规范参数和焊点质量要求与正式点焊的相同。
缝焊前的定位焊点,其熔核直径应为缝焊熔核宽度的70%~80%,焊点应在焊缝的中心在线。
3.4.8 零件的定位焊后,经检验合格,方允许焊接。
3.5 零件的焊接3.5.1 每批焊件的首件用已选定的焊接规范参数焊接并检验合格后,方可焊接成批零件。
3.5.2 开始焊接前应检查焊机,上下电极轴心应在同一垂在线,上电极的行程(上电极端面至焊件上表面的距离)调至5~6mm为宜。
施加电极压力时,上下电极在零件上滑移应不超过0.5mm。
焊机冷却水系统应正常,在各连接处和电极配合处无渗漏水现象。
3.5.3 在焊接过程中应注意:焊机上的气压和电源电压在正常工作范围;电极头工作面保持清洁、形状正确、无过热现象;一般焊接10~50个焊点打磨一次。
3.5.4 焊接时应防止焊件其余部份与焊接回路中的机件相接触,以免电击烧伤焊件,一般可采用绝缘材料隔开以防止接触。
3.5.5 不封闭的长焊缝应从中间向两端焊接。
曲面变化的焊件可先点焊曲率半径小的部位。
3.5.6 当型材缘边宽度较小或要求焊件表面压痕平滑时,建议在型材或要求平滑的一面采用平面电极。
3.5.7 焊接较大厚度比的零件时,与厚板接触的电极球面半径应比与薄板接触的大,焊接规范参数可按薄板的参数适当增大。
3.5.8 焊件图纸规定的点距小于表3所列数据时,可先用间隔点焊,焊接其余焊点应适当增大焊接电流或延长通电时间,具体参数应通过试验确定。
3.5.9 缝焊气密焊缝时,整个焊接过程应尽可能不中断,如已中断,接头处焊缝应重迭15~25mm。
3.5.10 铝合金缝焊时应采用外部水冷却。
3.5.11 为了减小焊件变形必须注意:避免应力装配;装配间隙应符合要求;选择焊接规范参数时尽量选用小的电极压力;焊接过程防止焊件过热;焊接表面保持与电极垂直;正确选择焊接顺序和方向;尺寸长刚性小的焊件应采用夹具或在托架上施焊。
3.5.12 焊件焊后局部变形,允许用木质或橡皮鎯头或加静载荷进行校正。
校正后的焊件必须仔细检验。
3.5.13 焊接过程中发现焊接缺陷,应停止焊接,找出原因并予以排除。
须改变焊接规范参数时,单个参数变化不超过选定的值10%,多个参数变化应不超过50%,当超过上述规定时,应按3.3.1款要求重新选定焊接规范参数。
3.5.14 零件焊接完毕后应在图纸规定位置打上焊工印记。
3.6 零件焊接缺陷的修补3.6.1 零件焊接缺陷的修补应符合HB5276-84的规定。
3.6.2 点焊补焊可在原焊点之间焊上新的焊点,或在原焊点上重新点焊。
重新点焊时须适当加大焊接电流或延长通电时间。
3.6.3 缝焊补焊可在原焊缝上重新缝焊、连续点焊或采用氩弧焊。
3.6.4 在不影响零件装配和使用的条件下,允许采用铆钉修补缺陷焊点,质量应符合铆接的规定。
3.6.5 修补焊件应由经验丰富的焊工担任。
4 技术安全4.1 焊工必须严格遵守工厂有关技术安全规程。
4.2 焊机机壳必须良好接地,接地螺钉直径不小于8mm 。
4.3 焊机工作场地应有木制或橡皮绝缘垫板。
4.4 焊工工作时,应穿工作服和绝缘鞋、戴工作帽、手套和眼镜。
电极用外部水冷时,应穿防水围裙和绝缘胶靴。
附录A 在Excel 窗体中附 录 B推荐的焊接规范参数(补充件)表B1 LF2、LF21铝合金在直流脉冲缝焊机上的焊接规范参数注:焊机型号FJ-400-1表B2 LF3、LF6铝合金在直流脉冲缝焊机上的焊接规范参数注:焊机型号FJ-400-1表B3 LY12CZ 铝合金在直流脉冲点焊机上的焊接规范参数注:焊机型号DJ-300-1表B4 LY12CZ铝合金在电容储能点焊机上的焊接规范参数注:焊机型号DRN-3 (自制)附加说明本标准由航空工业部六二一研究所提出本标准由航空工业部一七二厂、六二一所、和三二零厂起草。