(橡胶)汽车工业橡胶制品发展趋势
橡胶制品行业分析报告

橡胶制品行业分析报告1000字橡胶制品行业是一个广阔的领域,涉及到医疗、建筑、汽车、玩具、运动和其他领域。
该行业的主要特点是适用性广泛,市场需求量大,创新速度快,竞争激烈。
这篇报告旨在分析该行业的现状、发展趋势和面临的挑战。
一、橡胶制品行业现状1.市场规模橡胶制品市场规模庞大,随着全球经济的发展和人民生活水平的提高,需求量不断增加。
据统计,全球橡胶制品市场规模已经超过3000亿美元,而中国橡胶制品市场规模已经超过4500亿人民币。
2.行业结构橡胶制品行业结构复杂,市场竞争激烈。
目前,全球橡胶制品行业龙头企业主要集中在美国、欧洲和日本,中国的橡胶制品行业处于崛起期,虽然在国内市场占有率较高,但在国际市场竞争力还有待提高。
3.技术水平橡胶制品行业的技术水平不断提高,创新速度快。
随着先进制造技术的不断出现,橡胶制品的生产效率和质量得到了明显提高,对于行业的发展起到了积极作用。
4.环保问题橡胶制品生产过程中产生的废气、废水和废弃物处理问题已经引起社会的广泛关注,并且有一些国家和地区已经制定了严格的环保法规,这对于行业的健康发展和企业的可持续发展产生了一定压力。
二、橡胶制品行业发展趋势1.高端产品市场逐渐扩大随着消费者的需求不断提高,橡胶制品向高端市场转型已成为发展趋势。
市场需求量大的高端产品包括工业橡胶制品、医疗用橡胶制品、太阳能橡胶制品、汽车橡胶制品等。
2.大力发展绿色环保橡胶制品在环保成为全球热点话题的当下,越来越多的企业开始注重绿色环保橡胶制品的研发和生产。
这种产品具有无毒、无害、可回收等优点。
3.生产自动化程度提高橡胶制品生产过程中,自动化程度越高,生产效率越高,细节处理越精细。
随着先进制造技术的不断出现,企业应积极引进更先进的生产设备,提高企业的生产自动化程度。
三、橡胶制品行业面临的挑战1.原材料价格波动风险橡胶制品生产的原材料主要是橡胶和化工原料,原材料价格波动波动将对企业生产造成直接的影响。
2024年橡胶市场需求分析
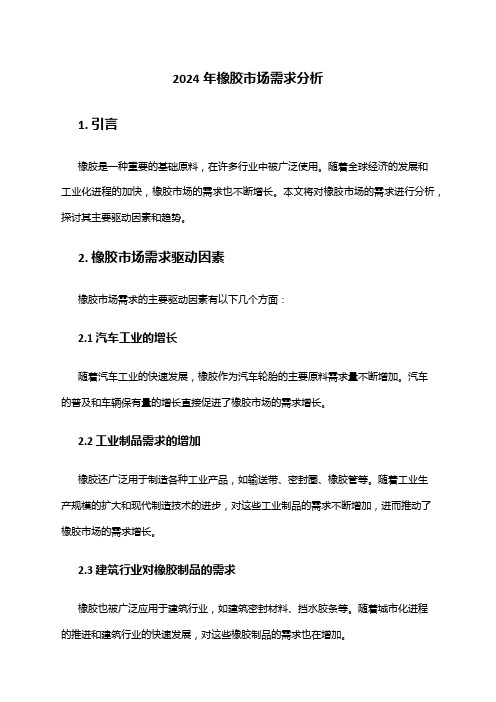
2024年橡胶市场需求分析1. 引言橡胶是一种重要的基础原料,在许多行业中被广泛使用。
随着全球经济的发展和工业化进程的加快,橡胶市场的需求也不断增长。
本文将对橡胶市场的需求进行分析,探讨其主要驱动因素和趋势。
2. 橡胶市场需求驱动因素橡胶市场需求的主要驱动因素有以下几个方面:2.1 汽车工业的增长随着汽车工业的快速发展,橡胶作为汽车轮胎的主要原料需求量不断增加。
汽车的普及和车辆保有量的增长直接促进了橡胶市场的需求增长。
2.2 工业制品需求的增加橡胶还广泛用于制造各种工业产品,如输送带、密封圈、橡胶管等。
随着工业生产规模的扩大和现代制造技术的进步,对这些工业制品的需求不断增加,进而推动了橡胶市场的需求增长。
2.3 建筑行业对橡胶制品的需求橡胶也被广泛应用于建筑行业,如建筑密封材料、挡水胶条等。
随着城市化进程的推进和建筑行业的快速发展,对这些橡胶制品的需求也在增加。
3. 橡胶市场需求趋势除了上述驱动因素,橡胶市场的需求还受到一些趋势的影响,这些趋势有以下几个方面:3.1 环保意识提升随着全球环保意识的提高,对可持续发展和环保材料的需求也在增加。
橡胶市场也面临着对环保橡胶产品的需求增长的压力。
3.2 新兴市场需求增长新兴市场的经济发展迅猛,这些市场对橡胶产品的需求也在不断增加。
例如,中国和印度等新兴市场国家对橡胶的需求量持续增长,成为全球橡胶市场需求增长的重要推动力。
3.3 替代品的竞争随着科技的发展,橡胶替代品的研发和生产不断进行,这对橡胶市场的需求产生了一定冲击。
特别是一些新材料的出现,如塑料、聚氨酯等,正在逐渐替代部分橡胶产品。
4. 总结综上所述,橡胶市场的需求受到多个因素的驱动。
随着汽车工业的增长、工业制品需求的增加和建筑行业对橡胶制品的需求增加,橡胶市场的需求持续增长。
与此同时,环保意识提升、新兴市场需求增长和替代品的竞争等趋势也对橡胶市场需求产生影响。
这些因素和趋势共同塑造了橡胶市场的需求格局,对橡胶行业的发展产生着重要的影响。
橡胶制品行业的先进制造技术与装备
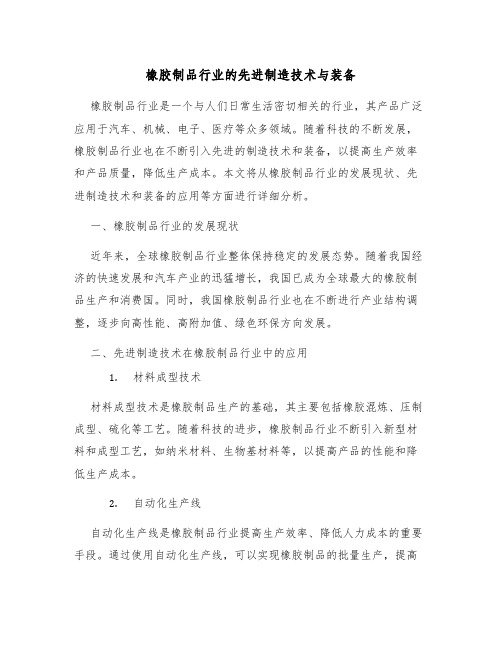
橡胶制品行业的先进制造技术与装备橡胶制品行业是一个与人们日常生活密切相关的行业,其产品广泛应用于汽车、机械、电子、医疗等众多领域。
随着科技的不断发展,橡胶制品行业也在不断引入先进的制造技术和装备,以提高生产效率和产品质量,降低生产成本。
本文将从橡胶制品行业的发展现状、先进制造技术和装备的应用等方面进行详细分析。
一、橡胶制品行业的发展现状近年来,全球橡胶制品行业整体保持稳定的发展态势。
随着我国经济的快速发展和汽车产业的迅猛增长,我国已成为全球最大的橡胶制品生产和消费国。
同时,我国橡胶制品行业也在不断进行产业结构调整,逐步向高性能、高附加值、绿色环保方向发展。
二、先进制造技术在橡胶制品行业中的应用1.材料成型技术材料成型技术是橡胶制品生产的基础,其主要包括橡胶混炼、压制成型、硫化等工艺。
随着科技的进步,橡胶制品行业不断引入新型材料和成型工艺,如纳米材料、生物基材料等,以提高产品的性能和降低生产成本。
2.自动化生产线自动化生产线是橡胶制品行业提高生产效率、降低人力成本的重要手段。
通过使用自动化生产线,可以实现橡胶制品的批量生产,提高产品质量稳定性,降低生产事故率。
目前,国内许多橡胶制品企业都已实现了自动化生产,部分企业已开始向智能化生产线转型。
3.信息化管理技术信息化管理技术在橡胶制品行业的应用,可以提高企业管理效率,缩短产品研发周期,加快市场响应速度。
通过使用企业资源计划(ERP)、产品生命周期管理(PLM)等信息化管理系统,可以实现企业生产、销售、研发等环节的协同管理,提高企业的核心竞争力。
4.检测与测试技术检测与测试技术是保证橡胶制品质量的关键环节。
先进的检测与测试技术可以实时监控生产过程中的各项指标,确保产品质量符合国家标准。
目前,橡胶制品行业已广泛应用光学、电子、超声波等检测技术与设备,实现了对产品质量和生产过程的全面监控。
三、先进装备在橡胶制品行业中的应用1.高性能橡胶混炼设备高性能橡胶混炼设备可以提高橡胶材料的性能,降低生产成本。
2024年橡胶制品业市场发展现状

2024年橡胶制品业市场发展现状引言橡胶制品业是一个重要的制造业领域,其产品广泛应用于汽车制造、建筑行业、医疗器械等各个领域。
本文将探讨橡胶制品业的市场发展现状,并分析其面临的挑战和机遇。
市场规模橡胶制品业市场在过去几年一直保持稳定增长。
据统计数据显示,2019年全球橡胶制品市场规模达到3000亿美元,预计到2025年将达到5000亿美元。
亚太地区是橡胶制品的主要消费地区,其市场占据了全球的大部分份额。
市场驱动因素市场发展的主要驱动因素包括以下几点:1. 工业化进程加速随着全球工业化进程的加速推进,各行业对橡胶制品的需求也在不断增长。
汽车工业作为橡胶制品的主要消费领域之一,随着汽车产量的不断增加,对橡胶制品的需求也在增长。
2. 基础设施建设投资增加随着各国基础设施建设投资的增加,对橡胶制品的需求也在增加。
例如,建筑行业对橡胶密封制品的需求增加,促使橡胶制品业市场快速发展。
3. 医疗行业的发展随着医疗行业的发展,对橡胶制品的需求也在增加。
医疗器械如手术手套、导尿管等均采用橡胶制品,市场需求量大。
市场竞争态势橡胶制品业市场竞争激烈,企业之间的竞争主要体现在以下几个方面:1. 产品质量和技术创新企业需要通过提高产品质量和不断进行技术创新来提高竞争力。
高品质的产品和先进的制造技术可以帮助企业在市场上脱颖而出。
2. 成本控制成本控制是企业保持竞争力的一个重要方面。
橡胶制品业需面对原材料价格波动、能源价格上升等挑战,企业需要通过提高生产效率、降低成本来应对竞争。
3. 品牌建设品牌的建设是企业在市场上取得竞争优势的重要手段之一。
企业需要通过品牌建设来提升产品形象和企业声誉,吸引更多的客户。
持续发展挑战橡胶制品业市场面临以下几个持续发展的挑战:1. 环境保护压力由于橡胶制品制造过程中会产生大量的废水、废气和固体废弃物,因此橡胶制品业受到环境保护压力的影响。
企业需要加强环保治理,提高生产工艺的节能环保性。
2. 原材料供应不稳定橡胶制品的主要原材料是天然橡胶和合成橡胶,而天然橡胶的价格受到天气、疾病和政策等因素的影响,导致供应不稳定。
2024年合成橡胶制造市场需求分析

合成橡胶制造市场需求分析引言合成橡胶是一种重要的工业原料,广泛应用于汽车轮胎、橡胶制品、建筑密封材料等领域。
随着全球经济的快速发展和工业化进程的加速,对合成橡胶的需求也呈现出稳定增长的趋势。
本文将对合成橡胶制造市场的需求进行分析,并提出未来的发展趋势和关键问题。
市场需求概述合成橡胶制造市场的需求主要由以下几个方面驱动:1.汽车工业的发展:汽车工业是合成橡胶的最大需求行业之一,随着全球汽车市场的扩大和新能源车推广,对合成橡胶的需求将进一步增加。
2.建筑行业的增长:合成橡胶在建筑密封材料等方面有广泛应用,随着城市化进程的推进和城市建设的不断扩大,对合成橡胶的需求也将持续增长。
3.橡胶制品市场的需求:橡胶制品广泛应用于家电、电子、医疗器械等领域,随着这些领域的发展和对高品质橡胶制品的需求增加,对合成橡胶的需求也将相应增长。
市场需求分析市场需求分析是了解市场需求的重要方法,可以从多个角度进行分析:1. 地理区域需求合成橡胶的市场需求在地理上存在一定的差异。
发达国家市场需求相对饱和,增长缓慢;发展中国家市场需求快速增长,成为合成橡胶的主要消费者之一。
2. 产品需求细分在合成橡胶市场,需求可以根据不同产品进行细分,例如丁苯橡胶、丁腈橡胶、丁二烯橡胶等。
不同产品在不同行业的需求量和需求变化趋势存在一定差异。
3. 技术需求随着科技的进步和创新,市场对合成橡胶的技术要求也在不断提高。
例如,对合成橡胶的强度、耐磨性、耐高温性等性能要求越来越高,对环保型合成橡胶的需求也在增加。
4. 价格需求价格是市场需求的重要影响因素之一。
合成橡胶市场上的价格波动会对需求产生一定的影响。
价格的稳定和合理性是满足市场需求的重要条件之一。
未来发展趋势和关键问题在合成橡胶制造市场,未来的发展和关键问题包括以下几个方面:1.市场竞争加剧:随着合成橡胶市场的不断扩大和竞争的加剧,企业间的竞争将更加激烈。
提高产品质量、加强研发创新、降低生产成本等将成为企业获取市场份额的关键。
2024年乙烯-醋酸乙烯酯橡胶市场发展现状
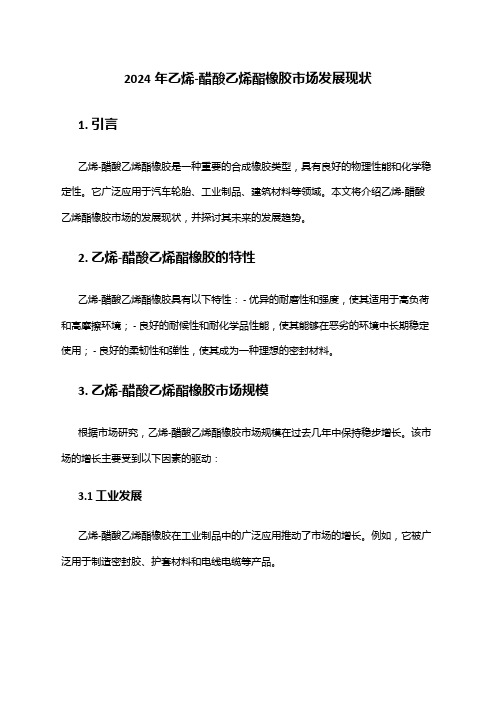
2024年乙烯-醋酸乙烯酯橡胶市场发展现状1. 引言乙烯-醋酸乙烯酯橡胶是一种重要的合成橡胶类型,具有良好的物理性能和化学稳定性。
它广泛应用于汽车轮胎、工业制品、建筑材料等领域。
本文将介绍乙烯-醋酸乙烯酯橡胶市场的发展现状,并探讨其未来的发展趋势。
2. 乙烯-醋酸乙烯酯橡胶的特性乙烯-醋酸乙烯酯橡胶具有以下特性: - 优异的耐磨性和强度,使其适用于高负荷和高摩擦环境; - 良好的耐候性和耐化学品性能,使其能够在恶劣的环境中长期稳定使用; - 良好的柔韧性和弹性,使其成为一种理想的密封材料。
3. 乙烯-醋酸乙烯酯橡胶市场规模根据市场研究,乙烯-醋酸乙烯酯橡胶市场规模在过去几年中保持稳步增长。
该市场的增长主要受到以下因素的驱动:3.1 工业发展乙烯-醋酸乙烯酯橡胶在工业制品中的广泛应用推动了市场的增长。
例如,它被广泛用于制造密封胶、护套材料和电线电缆等产品。
3.2 汽车工业乙烯-醋酸乙烯酯橡胶在汽车工业中的应用也是市场增长的重要驱动因素。
随着汽车产量的增加,对轮胎和密封件等橡胶制品的需求也在增加。
3.3 建筑行业乙烯-醋酸乙烯酯橡胶在建筑行业中的应用也呈现增长趋势。
它被广泛用于建筑密封、隔音材料和防水材料等方面,由于建筑行业的快速发展,对该橡胶的需求也在不断增加。
4. 市场竞争格局乙烯-醋酸乙烯酯橡胶市场存在着激烈的竞争。
主要的市场参与者包括橡胶生产商、制造商和分销商。
在这个竞争激烈的环境中,竞争者通过提高产品质量、降低成本和加强客户关系等手段来争夺市场份额。
5. 市场发展趋势乙烯-醋酸乙烯酯橡胶市场在未来预计将继续保持增长,并且将出现以下几个发展趋势:5.1 技术创新乙烯-醋酸乙烯酯橡胶市场将会面临技术创新的挑战和机遇。
新的制造技术和材料研发将使得产品更具竞争力,并且可以进一步提高其性能和降低成本。
5.2 环境可持续性在全球环境可持续性的要求下,乙烯-醋酸乙烯酯橡胶市场也将朝着更环保的方向发展。
对于原材料和生产过程的可持续性要求将逐渐增加,同时对于再生橡胶的需求也将增加。
橡胶制品行业的技术创新与发展

橡胶制品行业的技术创新与发展随着科技的进步和工业的发展,橡胶制品行业在我国经济中占据着重要的地位。
橡胶制品以其独特的弹性和密封性能,广泛应用于汽车、机械、建筑、医疗等众多领域。
本文将探讨橡胶制品行业在技术创新和产业发展方面的现状和未来趋势。
技术创新在橡胶制品行业,技术创新一直是推动产业发展的重要动力。
在原材料方面,合成橡胶的出现和发展,极大地丰富了橡胶制品的种类和性能。
同时,新型橡胶材料的研发,如导电橡胶、磁性橡胶等,为橡胶制品行业带来了新的应用领域。
在生产工艺方面,橡胶制品行业经历了从手工制作到机械自动化,再到智能化生产的过程。
自动化生产线和智能工厂的应用,提高了生产效率,降低了生产成本,同时也保证了产品质量的稳定性。
在产品设计方面,计算机辅助设计和制造技术的应用,使得橡胶制品的设计更加灵活和高效。
通过仿真技术,可以预测橡胶制品在实际应用中的性能,从而优化设计,提高产品的可靠性和使用寿命。
产业发展橡胶制品行业的技术创新,推动了产业的快速发展。
随着市场需求的增长,橡胶制品行业不断壮大,产业规模不断扩大。
同时,橡胶制品行业的竞争也日益激烈,企业需要不断创新,提高产品的性能和质量,以满足市场的需求。
在产业升级方面,橡胶制品行业正朝着高性能、高功能、绿色环保的方向发展。
新型橡胶材料和先进生产工艺的应用,使得橡胶制品在性能和应用领域上有了新的突破。
同时,环保型橡胶制品的研发和生产,也在一定程度上缓解了环境压力,提高了企业的社会责任形象。
在未来,橡胶制品行业将继续保持创新发展的态势。
新技术、新材料、新工艺的不断涌现,将为橡胶制品行业带来新的机遇和挑战。
我们可以期待,橡胶制品行业将在技术创新和产业发展的道路上,继续前进,为人类社会的进步做出更大的贡献。
以上内容为橡胶制品行业技术创新与发展的概述,接下来将深入探讨橡胶制品行业在各个领域的具体应用和发展前景。
橡胶制品在各领域的应用橡胶制品因其独特的性能,在各个领域都有着广泛的应用。
2024年橡胶和塑料制品市场发展现状

2024年橡胶和塑料制品市场发展现状简介橡胶和塑料制品市场一直是全球化工行业的重要组成部分,其在各个行业中都扮演着重要角色。
本文将介绍橡胶和塑料制品市场的发展现状,包括行业概述、市场规模、主要产品以及发展趋势等内容。
行业概述橡胶和塑料制品行业在过去几十年中经历了快速发展。
橡胶主要来源于天然橡胶和合成橡胶,而塑料则是通过化学合成过程获得的。
这两种材料具有重要的物理特性和化学特性,使其成为各种行业中广泛使用的材料。
橡胶和塑料制品应用领域广泛,包括汽车、电子电器、建筑、食品包装等。
汽车工业是橡胶和塑料制品的主要消费领域之一,橡胶和塑料制品在汽车中广泛应用于轮胎、密封件、管道等部件。
随着汽车工业的发展,对橡胶和塑料制品的需求也在增长。
市场规模橡胶和塑料制品市场规模庞大。
2019年,全球橡胶产量超过3100万吨,全球塑料产量超过3亿吨。
亚洲地区是全球橡胶和塑料制品市场的主要生产和消费地区,尤其以中国和印度为代表。
随着全球人口的增长以及新兴国家工业化进程的加快,橡胶和塑料制品市场仍然保持着稳定的增长。
同时,科技的发展也推动了橡胶和塑料制品的需求增加,例如高性能橡胶和塑料的应用,如高温耐磨材料和电子器件封装材料。
主要产品橡胶和塑料制品的主要产品包括橡胶制品和塑料制品。
橡胶制品包括轮胎、密封件、胶管、胶带等,而塑料制品包括塑料薄膜、塑料容器、塑料管道等。
轮胎是橡胶制品的主要应用领域之一。
全球轮胎市场规模巨大,特别是在汽车工业的快速发展下,轮胎需求持续增加。
此外,轮胎的技术升级和改进也推动了橡胶制品市场的发展。
塑料制品的应用也非常广泛。
食品包装领域是塑料制品的重要应用领域之一,各种各样的塑料容器和包装薄膜广泛使用于食品包装。
此外,塑料制品还应用于电子电器、建筑材料、医疗器械等行业。
发展趋势橡胶和塑料制品市场在未来仍将保持稳定增长。
随着全球经济的发展和人口的增加,对橡胶和塑料制品的需求将持续增加。
此外,环保和可持续发展的理念也对橡胶和塑料制品行业提出了新的要求。
橡胶工业发展现状

橡胶工业发展现状1. 引言橡胶是一种重要的工业原料,广泛应用于汽车、轮胎、橡胶制品等领域。
随着全球经济的发展和人们对生活质量的要求提高,橡胶工业也逐渐成为各国关注的焦点。
本文将探讨当前全球橡胶工业的发展现状,分析其面临的挑战和机遇。
2. 全球橡胶产量与消费情况2.1 全球橡胶产量全球橡胶产量主要集中在东南亚地区,其中泰国、印度尼西亚和马来西亚是最大的生产国家。
根据国际橡胶研究组织(IRSG)的数据,2019年全球天然橡胶产量约为1396万吨。
2.2 全球橡胶消费全球橡胶消费市场呈现稳步增长趋势。
中国是全球最大的橡胶消费国家,其次是印度和美国。
据IRSG数据,2019年全球天然橡胶消费量约为1383万吨。
3. 橡胶工业的主要产品3.1 天然橡胶天然橡胶是橡胶工业的重要原料,广泛用于轮胎制造、橡胶制品等领域。
目前,全球天然橡胶产量约占总产量的70%以上。
3.2 合成橡胶合成橡胶是通过化学合成方法生产的人工橡胶,具有优良的物理性能和化学稳定性。
合成橡胶种类繁多,应用广泛,包括丁苯橡胶、丁腈橡胶、丁酸橡胶等。
4. 橡胶工业发展面临的挑战4.1 原材料供应不稳定全球天然橡胶产量主要依赖于东南亚地区,而该地区常年受到气候因素和疾病等影响,导致原材料供应不稳定。
此外,天然橡胶价格波动较大,对企业经营带来一定压力。
4.2 环境保护压力增大橡胶加工过程中会产生大量废水、废气和固体废弃物,对环境造成一定的污染。
随着全球环境保护意识的提高,各国对橡胶工业的环境要求也越来越高,企业需要加大环保投入,提升生产工艺和设备。
4.3 技术创新压力增加橡胶工业是一个高技术含量的行业,需要不断进行技术创新才能适应市场需求。
随着新材料、新工艺的不断涌现,传统橡胶制造技术面临更新换代的挑战。
5. 橡胶工业发展的机遇5.1 新能源汽车需求增加随着全球对环境问题的关注和节能减排政策的推动,新能源汽车市场快速发展。
新能源汽车中轮胎所需橡胶量较传统汽车更多,这为橡胶工业带来了巨大机遇。
橡胶制品在汽车领域的应用前景研究

橡胶制品在汽车领域的应用前景研究发布时间:2021-04-14T14:09:58.890Z 来源:《中国科技信息》2021年4月作者:贺红文[导读] 橡胶是汽车构件中的重要原材料之一,在汽车用非金属材料中有着重要地位,是其他材料难以替代的。
每辆汽车有数百个胶件,总重达几十千克,约占整车自重的3%-6%。
其中轮胎约占橡胶件总重的70%。
可见,轮胎是汽车的主要橡胶件。
此外,还有各种汽车用橡胶配件如胶管、胶带、密封件、减振等约300多件,随着新能源汽车的推广与发展,橡胶制品在汽车领域的应用也更加广泛。
身份证号:4304261986110****6 贺红文摘要:橡胶是汽车构件中的重要原材料之一,在汽车用非金属材料中有着重要地位,是其他材料难以替代的。
每辆汽车有数百个胶件,总重达几十千克,约占整车自重的3%-6%。
其中轮胎约占橡胶件总重的70%。
可见,轮胎是汽车的主要橡胶件。
此外,还有各种汽车用橡胶配件如胶管、胶带、密封件、减振等约300多件,随着新能源汽车的推广与发展,橡胶制品在汽车领域的应用也更加广泛。
也就是说,经济的发展将促使汽车的产销量持续增长,所需要的橡胶制品量也会随之增多,可见研究橡胶制品在汽车领域的应用前景极具现实意义。
关键词:橡胶制品汽车领域应用前景引言:汽车橡胶制品涉及到密封,传动,装饰,减振,行走等重要部件,是为汽车行业配套的重要部件,其产品质量和性能直接关系到汽车的安全,节能和环保三个方面。
我国汽车工业广阔的发展前景和快速发展形势,对车用橡胶制品和原材料提出了更高的要求,也促进和带动了橡胶制品行业和相关材料的发展,并为汽车用橡胶制品发展带来了机遇和良好市场前景。
1、橡胶的构成橡胶的构成主要包含两部分:一是生橡胶,二是配合剂。
生橡胶作为橡胶工业的主原料,根据其来源可以分为天然橡胶与合成橡胶两种。
前者主要是从热带橡胶树上采集而来的胶乳,经过一系列加工处理后形成的一种高弹性材料。
经过加工处理后的天然橡胶一般为片状固体,单体是异戊二烯。
汽车工业的发展为橡胶制品产业注入生机

1 0万 k 以上 ,其耐 热性 也提 高到 1 0 以上 。 m 2%
另一个 显 著 的变 化 是热 塑性 弹性体 取代 橡胶 ,在
20 . . 08 6 NO
肖艳.汽车工业 的发展为橡胶制品产业注入生机
3 3
汽 车上 的用 量迅 速增 长 ,其在 汽车 上用 量 已 占汽
技术 转让 作为 该项 目的主 要研 发 目的 。横滨 、 东
带 、减 振 橡 胶 制 品 、 车 用胶 管 、胶 粘 剂 、 密封 胶 和 门 窗密 封 条 的 市 场 动 态 和 发展 前景 。 关键 词 :汽 车 工业 ;橡 胶 制 品 ;市 场 动 态
1 车用橡 胶制 品 的发展趋 势 汽 车工 业是 国 民经济 支柱 产 业 ,其特 点 是技 术推 动性 大 ,生 产关 联度 高 ,应 用覆 盖面 广 和生 产 总值 高 。汽车 工业 的 发展 可 以带动 国民经 济许 多 部 门的发 展 ,但 同时 也需 要许 多相 关行 业 与之 配 合 ,橡胶 工业 就 是其 中之 一 。汽 车工 业 的快速 发 展对 橡胶 制 品业 带来 了 良好发 展机 遇 ,许 多汽
新 水平 ,为 引进 车 型配 件 国产 化作 出了贡 献 ,但
%。 由此 可见 ,汽 车橡 胶 制 品在汽 车 工业 中 , 占 有重 要地 位 。 国 内汽 车用 橡胶 制 品生 产企 业仍 处 于 小规模 、低 水 平 的阶段 ,而 同时 , 国外 大 型生 产企 业看 好我 国汽车 发展 市场 ,纷纷 在 国 内投 资 建厂 。今 后 国 内企业 参 与 的竞争 将会 更加 激 烈 , 因此 要 加快 汽车 用橡 胶 制 品设计 、 开发 与生 产 ,
上胶 料制 品用 量 为 2 3 g 占整 车 质量 的 2 %, 4k, 1 奥 迪轿 车 上胶 料制 品用 量 3 1 g 占整车 质量 的 0k ,
橡胶制品小型化、轻量化技术趋势
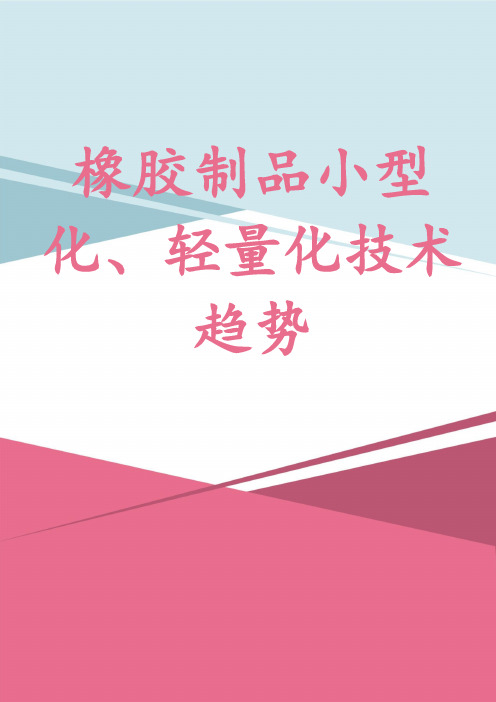
橡胶制品小型化、轻量化技术趋势橡胶制品作为现代工业不可或缺的一部分,广泛应用于汽车、航空航天、电子产品、医疗设备、建筑及日常消费品等领域。
随着科技的进步和可持续发展的需求日益增长,橡胶制品的小型化、轻量化技术趋势成为行业创新的关键方向。
以下将从六个方面探讨这一趋势的内涵、驱动力、技术路径及未来展望。
一、市场需求的多样化与个性化在消费电子、可穿戴设备、智能家居等新兴领域,小型化、轻量化的橡胶制品能够更好地匹配精密组件,满足产品设计的紧凑性和便携性需求。
例如,智能手机、无线耳机、智能手表中的密封圈、减震垫片等,要求橡胶件具有超薄、高弹、耐久的特性。
同时,个性化定制服务的兴起也促使橡胶制造业探索更灵活高效的生产方式,以快速响应市场多变的需求。
二、材料与工艺的创新橡胶材料科学的进展是实现小型化、轻量化的核心。
新型橡胶复合材料,如热塑性弹性体(TPE)、硅橡胶、氟橡胶等,因具备优异的物理性能和加工性,成为替代传统橡胶的理想选择。
这些材料不仅密度低、强度高,而且可通过改性进一步提升特定性能,如耐高温、耐化学品腐蚀等。
此外,精密注塑、微成型、3D 打印等先进制造工艺的应用,使得橡胶制品能够达到更精细的尺寸精度和复杂形状,同时减少材料浪费,实现轻量化。
三、结构设计的优化设计层面的革新同样重要,通过有限元分析、仿真技术等现代设计工具,可以在虚拟环境中对橡胶部件进行优化设计,确保在减重的同时不牺牲功能性。
结构上的创新,如蜂窝结构、空心设计、梯度密度材料布局等,能够在保持原有性能指标的前提下显著降低重量。
此外,集成化设计策略,即将多个功能集成到单一部件中,也能减少零件数量,实现小型化。
四、环保与可持续性考量在全球范围内对环境保护意识的提升下,橡胶制品的回收利用和生物基材料的研发成为新的研究热点。
小型化、轻量化不仅有助于减少原材料消耗和废物产生,还便于回收处理。
生物基橡胶,如来自植物的天然橡胶、生物工程合成橡胶,以及可降解橡胶材料,为实现绿色生产提供了新途径。
谈橡胶制品在汽车的使用与发展

对于四点支承型式;减少 由发动机振动引起 的结 构 噪声 , 并 减小 声 波 ; 防止 由发 动机 振动 引 起 的 人体的不舒服及疲劳;防止部件的疲劳、损坏或 误操 作 ,诸 如散 热器 、继 电器 、仪表 等 等 。总 的 来说,橡胶减振块具有三大功能:支承、限位 、 隔振 。橡 胶 减振块 的结构 形式 通 常为复 合 型 、剪
Ab tr c s a t: T e o u o c r s es h v l me f a ai an h d o t g o h f h c r d ol d wn he r wt o t e a wi h t e t h
ru be p od ct i u t t p mo e t r pi d ve op e o au o bi e b r r u s nd s ry o ro t he a d e l m nt f t mo l
谈 橡胶 制品在 汽 车的使 用 与发展
谈橡胶制 品在汽车 的使 用与发展
朱 则 刚
湖 北十堰 东风汽 车公 司 4 2 0 401
摘 要 :汽 车产销 及保 有 量 的增 长促 进 了车 用橡 胶制 品业 的 高速 发展 ,汽车 工业一 直是 橡 胶
制 品的主要市场。尤其橡胶密封制品是汽车用橡胶制品中不可缺少的重要组成部 分,是 汽 车 中不 可替 代的一 类特殊 零件 ,分别起 着 密封 、减振 、 隔音 、制 动等作 用 ,对 汽车正
硫化过程,缩短硫化时间的作用,常用的有氧化 锌 、氧 化 铝 、氧 化 镁 以及 醛 胺 类 有机 化 合物 等 ;
橡胶制品市场的市场规模预测与趋势分析

市场规模增长因素
经济增长:全球经济 持续增长,带动橡胶
制品市场需求增加
政策支持:政府出台相 关政策,鼓励橡胶制品
行业发展
技术进步:新技术和 新材料的应用,推动
橡胶制品市场发展
市场需求:汽车、建 筑、医疗等领域对橡 胶制品的需求持续增
长
市场规模预测未来趋势
橡胶制品市场需 求持续增长
技术创新推动产 品升级换代
汽车、建筑等行业对橡胶 制品的需求增加
环保、节能等趋势对橡胶 制品市场产生影响
技术创新和研发能力对市 场需求变化的影响
市场竞争格局变化
市场竞争加剧:新进入者增多,市场份额争夺激烈 技术进步:新技术、新产品不断涌现,推动市场发展 消费升级:消费者对高品质、高性能产品的需求增加 环保政策:环保法规的实施,影响市场格局和竞争态势
感谢您耐心观看
名度和美誉度
国际化战略:企业将拓展 国际市场,提高国际竞争
力
行业政策对市场的影响
政策支持:政府出台相关政策,支持橡胶制品行业发展 环保要求:政府对橡胶制品行业的环保要求越来越严格 技术创新:政府鼓励橡胶制品行业进行技术创新,提高产品质量和性能 市场准入:政府对橡胶制品市场的准入条件进行限制,提高市场门槛
人造橡胶的价格走势和影响 因素
人造橡胶的定义和分类
人造橡胶在橡胶制品市场中 的应用和前景
其他原材料市场分析
橡胶制品的原 材料主要包括 天然橡胶、合 成橡胶和再生 橡胶
天然橡胶市场: 全球天然橡胶 产量和消费量 逐年增长,价 格波动较大
合成橡胶市场: 全球合成橡胶 产量和消费量 逐年增长,价 格相对稳定
橡胶制品市场的市场规模 预测与趋势分析
汇报人:
橡胶制品在新能源汽车中的应用新趋势
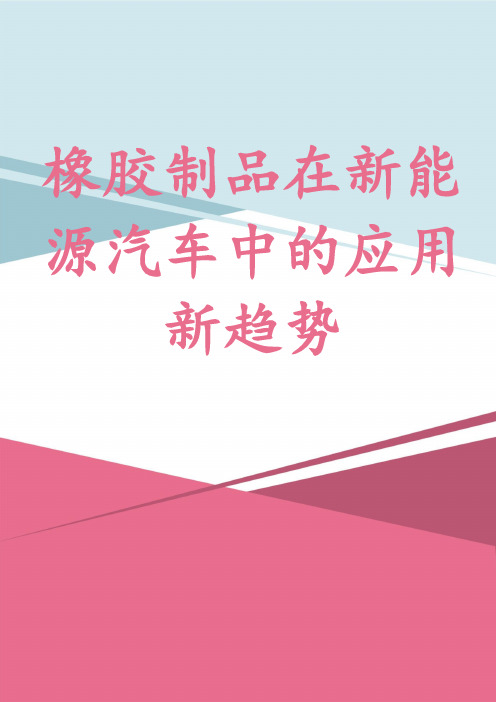
橡胶制品在新能源汽车中的应用新趋势橡胶制品作为汽车产业不可或缺的组成部分,在新能源汽车的快速发展中扮演着至关重要的角色。
随着电动汽车技术的不断进步和市场渗透率的显著增长,橡胶制品的应用也迎来了全新的挑战与机遇。
以下是橡胶制品在新能源汽车中应用的六大新趋势:一、适应电气化需求的绝缘与防护材料新能源汽车的核心在于电力驱动系统,这要求橡胶制品不仅要保持传统汽车中对机械部件的保护与密封功能,还需具备优异的电绝缘性能,以防止漏电和短路风险。
因此,开发高耐电压、低介电损耗的特种橡胶材料,用于电池包密封、高压电缆护套、电机绝缘垫片等领域,成为了行业发展的重点。
这些材料需要经过特殊配方设计,以确保在极端温度、振动及化学腐蚀条件下仍能维持稳定可靠的绝缘性能。
二、轻量化与环保材料的创新应用新能源汽车为了提高续航能力,对车辆整体减重有着迫切需求。
传统的橡胶部件往往密度较大,而通过采用轻质填料改性、纳米复合材料等技术,可以有效减轻橡胶制品的重量,同时不牺牲其原有的物理机械性能。
此外,随着环保法规的日益严格,生物基橡胶、可回收橡胶等环保材料的研发与应用也成为新的趋势,旨在减少化石资源依赖,降低碳足迹。
三、动态性能的提升与智能化集成新能源汽车的驱动方式与传统燃油车不同,对橡胶部件的动态响应和耐久性提出了更高要求。
例如,电动车的瞬间扭矩输出大,对轮胎的抓地力、耐磨性以及减震系统的要求更为苛刻。
因此,开发具有低滚阻、高耐磨、高抓地力特性的轮胎成为必然趋势。
同时,随着车辆智能化程度的提升,集成传感器的智能橡胶部件开始出现,如能够监测轮胎压力、温度甚至路面状况的智能轮胎,为车辆的主动安全和预测性维护提供了可能。
四、热管理系统的优化新能源汽车的热管理系统是保证电池组高效运作的关键。
橡胶制品在这里的应用主要体现在冷却系统的管路密封、热交换器的密封圈以及电池包内外的隔热材料等方面。
这些部件需具有良好的耐高温、耐介质腐蚀性,同时保持良好的密封性能,以确保电池在适宜的温度范围内工作,延长使用寿命并提高安全性。
2024年工业橡胶制品市场分析报告
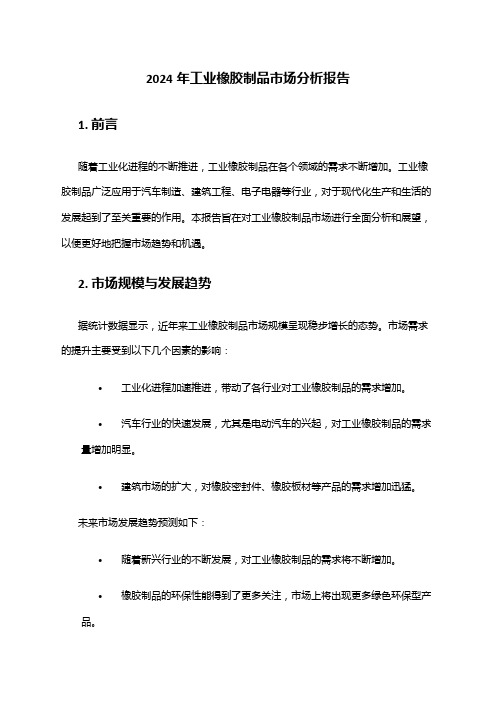
2024年工业橡胶制品市场分析报告1. 前言随着工业化进程的不断推进,工业橡胶制品在各个领域的需求不断增加。
工业橡胶制品广泛应用于汽车制造、建筑工程、电子电器等行业,对于现代化生产和生活的发展起到了至关重要的作用。
本报告旨在对工业橡胶制品市场进行全面分析和展望,以便更好地把握市场趋势和机遇。
2. 市场规模与发展趋势据统计数据显示,近年来工业橡胶制品市场规模呈现稳步增长的态势。
市场需求的提升主要受到以下几个因素的影响:•工业化进程加速推进,带动了各行业对工业橡胶制品的需求增加。
•汽车行业的快速发展,尤其是电动汽车的兴起,对工业橡胶制品的需求量增加明显。
•建筑市场的扩大,对橡胶密封件、橡胶板材等产品的需求增加迅猛。
未来市场发展趋势预测如下:•随着新兴行业的不断发展,对工业橡胶制品的需求将不断增加。
•橡胶制品的环保性能得到了更多关注,市场上将出现更多绿色环保型产品。
•自动化设备的广泛应用推动了工业橡胶制品的多样化和个性化需求。
3. 市场竞争状况工业橡胶制品市场竞争激烈,主要表现在以下几个方面:•市场主要参与者众多且实力强大,产品品质和技术优势成为竞争关键。
•价格战常见,低价竞争现象严重,导致行业整体利润率较低。
•品牌竞争激烈,知名品牌在市场占有率方面占据优势。
市场竞争分析还需要深入挖掘行业现状、产业生态和未来趋势,以预测市场规模的增长潜力和市场份额的分配。
4. 市场机遇与挑战工业橡胶制品市场存在一系列机遇和挑战,需要企业积极应对:•市场机遇:–新兴产业的兴起,带来了对橡胶制品的新需求。
–消费升级,消费者对产品质量和性能要求提高,对品质优异的橡胶制品有较高需求。
–供应链升级,提出更高的合格率、交付率等要求,对于质量合格的工业橡胶制品的需求增加。
•市场挑战:–市场竞争激烈,产品同质化现象突出,企业需要通过技术创新和品质提升来区别竞争。
–原材料价格上涨,增加了生产成本,对企业盈利能力产生一定影响。
–环保要求不断提高,对工业橡胶制品的生产工艺和原材料选择提出了更高的要求。
橡胶制品的市场需求与消费行为
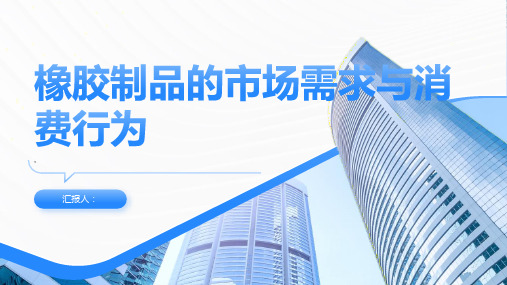
汽车行业:轮 胎、密封件、
减震器等
建筑行业:防水 材料、隔音材料、
保温材料等
医疗行业:医用 手套、医用管材、
医用垫片等
日用品行业:橡 胶鞋、橡胶手套、
橡胶玩具等
电子行业:电 缆、电线、电
子元件等
工业行业:橡胶 输送带、橡胶辊、
橡胶密封件等
橡胶制品广泛 应用于汽车、 建筑、医疗等
橡胶制品的种类:了解各种橡胶制品的用途和特点 质量认知:关注橡胶制品的质量和耐用性 价格认知:考虑橡胶制品的价格和性价比 品牌认知:关注橡胶制品的品牌和口碑
价格因素:消费 者对橡胶制品的 价格敏感度较高, 价格是影响购买 意愿的重要因素
品质因素:消费 者对橡胶制品的 品质要求较高, 高品质的产品更 容易获得消费者 的青睐
环保要求提高:随着环保 意识的提高,对橡胶制品 的环保要求也将提高,环 保型橡胶制品将更受欢迎。
智能化发展:随着科技的 发展,智能化橡胶制品将 逐渐普及,提高生产效率
和产品质量。
汇报人:
行业
全球橡胶制品 市场需求持续 增长,预计到 2025年将达到 2.5万亿美元
发展中国家橡 胶制品市场需 求增长迅速, 尤其是中国、
印度等国家
环保型橡胶制 品市场需求增 加,如可降解 橡胶、环保轮
胎等
市场规模:中国橡胶制品 市场规模庞大,增长迅速
消费需求:中国橡胶制品 消费需求多样化,包括耐 热、耐寒、耐腐蚀、耐磨、
耐老化等性能要求
消费群体:中国橡胶制 品消费群体广泛,包括 工业、农业、建筑、汽
车、医疗等领域
发展趋势:中国橡胶制 品市场需求将持续增长, 高端化、个性化、绿色
化将成为发展趋势
橡胶制品市场需 求将持续增长
- 1、下载文档前请自行甄别文档内容的完整性,平台不提供额外的编辑、内容补充、找答案等附加服务。
- 2、"仅部分预览"的文档,不可在线预览部分如存在完整性等问题,可反馈申请退款(可完整预览的文档不适用该条件!)。
- 3、如文档侵犯您的权益,请联系客服反馈,我们会尽快为您处理(人工客服工作时间:9:00-18:30)。
①生胶原料:同步带的生胶从60年代起,一直使用CR,现在仍广泛用于一般产业用途。从80年代起,开始采用CSM和HN BR,现在HNBR成为主流。最新动向是 HN BR和异丁烯酸锌(ZD-MA)的复合材料(略写为ZSC),断裂强度50MPa以上,耐磨耗性亦佳,可望用作同步带生胶原料。另外,HNBR与NBR相比, 存在着耐寒性差的问题。对此,国外正在开发改进HNBR耐寒性好的新品种,这种HNBR从氢化前的 NBR 聚合起就控制分子中的顺序,并通过氢化来抑制耐寒性下降。
④散热器胶管。散热器胶管是发动机气缸和散热器之间流通冷却水的软连接件。由于散热器用水中加有防锈液、防冻液等,所以必须用耐液体性、耐气体性强的材料。这类胶管在国外是以EPDM胶料为主,也有的采用短纤维复合的EPDM胶料。进入 90年代,使用温度要求150℃,同时对胶料变形要求也很严格,因此EPDM 用作水箱管内外层胶时,需要采用过氧化物体系硫化。就软管结构而言,采用芳纶纤维编织层(圆织层),可获得耐温与耐压的平衡。
②V带用生胶主要使用氯丁橡胶,底胶中掺用短纤维。
CR品种主要使用耐龟裂性、动态生热低及粘合性佳的硫黄改性型橡胶。在要求耐热性能高的特殊用途中,也有采用氢化丁腈橡胶(HNBR)的。 据耐热试验, 在 120℃气体介质中,HNBR V带耐久性是CR V带的4倍。
③V带骨架材料主要用聚酯纤维, 在需要高负荷传动和耐冲击性的高速皮带及农机用V带则使用芳纶纤维。V带外包布采用尼龙包布。
2.同步带
同步带是一种工作面带有齿状结构的传动带,它集齿轮、链条和带传动的优点为一体,具有传动效率高、传动比准确、噪音小、节能、维修方便等优点。60年代后期,采用玻璃纤维线绳为骨架材料并广泛应用于汽车之后,同步带得以迅速发展; 80年代则有大幅度发展。目前欧洲80%轿车、美国40%轿车均采用同步带传动。我国引进和合资生产的轿车除广州标致外,均采用同步带传动。目前全国汽车同步带生产能力约400万条,2000年需求量预计700万条,2010年预测为1500万2000万条。但由于国产原材料不配套,引进技术消化吸收还有一定差距,加上其它因素,目前为主机厂认可和配套的汽车同步带甚少,大部分仍靠进口。我国应用和生产同步带时间较晚,80年代下半期有青岛、上海、无锡等先后从德国引进了同步带生产线,宁波则从美国引进了生产线。但由于CR、玻纤线绳和尼龙包布等国产材料尚不过关,线绳与包布仍需进口。汽车同步带发展动向是:
1.汽车V带
汽车V带原称风扇带,是V带一个重要种类,用于将汽车或拖拉机发动机的动力传递到冷却风扇。空压机、发电机和液压泵等辅助机械,随着汽车工业的发展和汽车保有量的增加,对汽车V带的需求量也在不断增多。预计2000年需求量为6000 万条,2010年为1.3~1.7亿条,近些年来,通过引进消化吸收国外先进技术与设备,汽车V带产品结构与质量均有很大提高。骨架材料已基本淘汰棉纤维, 由人造丝、玻璃纤维线绳向聚酯线绳发展。有的已采用切边式结构,产品已达到或接近国际水平,基本上达到了为引进车型配套要求。但从总体水平来看,我国V 带与国外产品相比,仍有较大差距,日本三星公司切边V带寿命可达到18万公里, 国内产品一般不到10万公里。国外汽车V带发展动向除要求耐苛刻条件和使用寿命长之外, 又把噪音低作为其重要特征。为此,V带的结构和原材料方面都发生了重要变化。
②骨架材料:同步带骨架材料主要使用玻璃纤维。玻璃纤维在啮合传动中拉伸小且有适度的线膨胀系数,因此通过各种改进,现已使用高强度型玻璃纤维。部分使用强力更高、耐弯曲性好的芳纶。芳纶由于线膨胀系数为负,与皮带轮的材质正相反,温度引起的尺寸变化比玻纤大,为了吸收张力变动,通常是与自动张力装置组合使用。同步带包布主要用经RFL处理的尼龙包布。最近也开始用芳纶包布。
①高功能的充液体的发动机垫和轴套:这种新结构产品是以橡胶弹性体做流体密封膜,受震动时,橡胶弹簧发生变形,即流体室发生变形,使室内流体通过通路流入另一流体室:通过流体支撑隔膜,也即支撑框架而起到缓冲作用,这种液体减震垫中封入的流体是防冻液(避免天冷冻结)。一般是用乙二醇与丙二醇的混合液。目前日本己有8家橡胶公司开发生产了这种新型减震制品。并发表有专利。 美国固特异公司生产的这种减震垫已经装用于多种车型汽车上,据称一台车用3个这种垫: 2个用于发动机下,1个用在传动系统。这种复合结构的充以液体的发动机垫和轴套的研制成功是80年代国外减震橡胶制品开发的重要成果,目前还开发出采用电子自动控制的新一代充液减震垫,被称为高技术橡胶产品。
③减震材料开发:在国外,汽车是减震制品的主要市场。为满足汽车工业对减震制品的需要,从减震材料开发来看,主要是适应汽车长寿命和可靠性的需要,提高制品的耐久性,甚至要求减震制品能伴随汽车同时报废。今后主要是提高胶料耐热性,即从目前100℃提高到150℃,而在将来则要求提供超耐热材料(300℃以上)和开发可变弹簧常数橡胶。国外采用树脂及热塑弹性体制作减震制品也在发展之中,这是因为树脂价格低廉、重量轻,经改性的塑料减震材料其性能不亚于橡胶,所以各国汽车上使用塑料减震件日益增多。但塑料还不能完全取代橡胶,因为橡胶某些性能还是塑料所不能比拟的。因此,国外也有发展橡塑复合材料制造减震制品的动向。
汽车工业是国民经济支柱产业,其特点是技术推动性大,生产关联度高,应用覆盖面广和生产总值高。汽车工业的发展可以带动国民经济许多部门的发展,但同时也需要许多相关行业与之配合,橡胶工业就是其中之一。据调查,一辆汽车需要橡胶配件400~500个,重约40公斤,占车重4%~5%。汽车橡胶制品产值约占汽车部件总产值的6%。由此可见,汽车橡胶制品在汽车工业中,占有重要地位。
⑤热塑弹性体(TPE)管材。由于产业废弃物产生的环境问题, 对废弃物再利用的呼声日益高涨,而硫化胶管不能再利用,因此,采用树脂或TPE 做胶管材料的趋向增强。还有报道,日本丰田合成公司已开发成功用EPDM再生胶制造汽车胶管,包括加热和冷却胶管。
4.减震制品
汽车用减震橡胶制品主要有橡胶弹簧、橡胶空气弹簧、发动机悬挂减震器、橡胶锥体减震器、塞子形橡胶减震件和各种防震胶垫等,分别用于发动机和传动操作系统、前后悬挂系统、车体及排气系统等,其结构主要是橡胶与金属板的复合制品,也有纯胶件。从国外发展趋势看,汽车用减震件一直呈增长趋势。70年代后半期,由于汽车高级化,为提高乘坐舒适性,减震橡胶无论是用量还是质量均有发展,每辆汽车已有50~60个点使用减震橡胶件。进入80年代以后,汽车的安全性、舒适性与便利性成为用户关心的主要问题。尽管汽车产量增长不多,但减震橡胶用量仍呈增长势头。汽车减震橡胶产品开发动向是:
②扭转减震器:主要用于缓和曲轴的扭转运动,以前多用于卡车和公共汽车等大型发动机,而近年来轿车也倾向于要求发动机大功率、轻型化和低噪音,也更多地应用扭转减震器。扭转减震器的使用条件,除发动机室内空气温度、发动机辐射热之外,橡胶本身发热也大,因此生胶多用耐热性良好的CR、NBR、SBR和NR,从减震效果和耐热性考虑,正在开发耐热减震性好的EPDM、VA-MAC(乙基- 丙烯酸共聚弹性体)作为新型减震橡胶材料。这些聚合物不仅耐热性良好,而且高温下仍保持较高阻尼特性。扭转减震器在品种结构开发上也取得一些成果:从功能看,有扭曲减震器、挠曲减震器、轴向减震器以及附有其它功能的多功能减震器;从形状上看,除套筒、圆盘式以外,还有弹性衬套、球面衬套;从减震块数量上看,为提高减震效果,采用多个减震块复合;为降低成本,除硫化粘合型以外,还有橡胶压人型、两个减震块同时硫化粘合型等。
②动力转向营。这类胶管接触介质是矿物油,要求耐热性好和管接头部位牢固,没有泄漏。国外汽车动力转向系统最近发展趋势是采用高压泵,以及实现泵的小型化和高出力化,对胶管则要求提高耐热性与耐久性,内层胶要有很好耐油性,耐温则要求达到150℃以上。此种胶管以往内外层胶为NBR/ CR,现在向HNBR、CSM、CPE、 ACM转换。为提高耐热性,也有用氟胶的, 但由于氟胶与油中某些添加剂起反应而劣化,因而应用不够普及。液压转向管的新结构是用HNBR为内层胶,尼龙66为补强层,外层用CSM。这种软管的使用寿命,在140℃条件下,比没有改进的提高2 倍以上。
③汽车同步带今后开发方向:为与引擎变化(小型化、高负荷、耐环境性优异)相适应,同步带要进一步推进高性能化,高功能化,不断降低成本。今后主要是控制芯线的线膨胀系数,控制齿面部分摩擦力和硬度,以及控制高模量高衰减应力的分散,材质将转向能再生利用,无废弃物的方向。
3.胶管
在汽车上要装配多种多样胶管,如刹车管、燃料管、加热器管、散热器管、空调管、水箱管(异型管)等,以完成动力传动及燃料、水、气等的输送。每辆车大约需用70m胶管。由于在汽车中使用,条件苛刻,性能要求高,组装要方便, 所以其品种规格不断增多,质量也不断改进。近些近来,国内胶管企业通过引进技术与自己开发,研制生产了一批适应汽车要求的不同类型胶管,如空调管、液压刹车管、水箱胶管、树脂管等。目前国内液压制动软管生产能力为2亿标米,2000 年国内需求量预测为1.3亿标米,2010年为2.6亿~3.0亿标米。 但在产品结构使用性能以及原材料方面,与国外相比仍有不少需要改进之处。目前我国汽车胶管的生产仍处于发展阶段,配套能力与市场需求相差甚远,还不能生产为中高档轿车配套的各类胶管,即使是桑塔纳这样的车型,国内仍只能配套低能级胶管,象防抱死制动系统、空调系统、转向系统等胶管还要依靠进口。据报道,国内最大的胶管企业上海橡胶制品有限公司正进行汽车胶管的三期工程,明年完成后,可实现整车配套,届时我国汽车胶管整体水平可达到国外90年代水平。国外汽车胶管发展动向是:
下面就汽车甩橡胶制品现状及发展动向作一一简要介绍。
一、汽车用橡胶制品的开发
汽车用橡胶制品包括传动带(V带、同步带)、各种胶管、 密封制品(油封、密封胶条)、减震橡胶制品及安全气袋等几大类,近些年来,我国广大橡胶企业和科研单位在开发汽车用橡胶新产品,提高产品性能等方面做出了很大努力,特别是通过引进国外先进技术与设备,以及合资、合作等关系,使汽车用各种橡胶制品质量提高到了新水平,为引进车型配件国产化作出了贡献,从带体结构来看,切割V带在国外己普遍采用。