车门亮条设计规范
汽车车门线束的布置原则与作法

汽车车门线束的布置原则与作法汽车车门线束是指连接车门内部各个零部件的电缆集合体。
车门线束的布置对于整个汽车的安全性、稳定性等方面都有着重要的影响。
因此,良好的车门线束布置必不可少。
一、车门线束的布置原则1.保证线束的安全性车门线束的布置应当避免出现割裂、磨损、摩擦、异物进入等情况。
线束应根据车门的开合动作和施加的力量合理地布置,防止在打开或关闭车门时,线束被卡住或直接受到挤压,从而造成故障。
2.保证线束的可靠性车门线束的布置应当避免线束产生过大的张力,以减少线束在运动中的摇晃和振动,从而确保线束状态的稳定性。
同时,车门线束应尽量降低线束的长度,在连接处采取适当的保护措施,减少连接处的断电风险。
3.保证线束的易维护性车门线束的布置应当方便维修和更换。
所以,布置应尽量简单,能够直观地看到线束的布局和各个零部件的连接情况。
二、车门线束的作法1.布局设计车门线束的布局应该合理,采用尽量短的长度,并且依据车门开合、关闭的动作规律,避免将线束放置在易磨损的位置。
同时,线束应该使用特定的材料进行保护,确保其避免与车门内部其他部件摩擦,避免损坏。
2.固定方式车门线束的固定方式应该符合车门的科学道理。
在每个固定部位,使用专用的固定装置固定线束,以确保线束的安全和稳定。
3.瞪眼长度车门线束的长度要保持一定的瞪眼长度,以避免线垢太长在车门打开和关闭时磨损和缠绕的情况。
4.缆线材料车门线束的材料应选用耐磨、耐高温、耐腐蚀等特殊材料,以确保线束的性能更加可靠。
5.线束保护车门线束的保护系统应该采取可靠的措施,以确保线束的完整性。
使用专业的保护装置,对于线束起到良好的保护作用,同时,要避免使用铁线、尼龙带等易于损坏线束的保护装置。
综上所述,车门线束的布置原则和作法对于整个汽车的安全性和可靠性有着重要的影响。
因此,厂家需要十分重视线束的布置,并严格按照相关的标准进行操作,从而确保线束的质量和使用效果。
同时,应定期检查和维修车门线束,以保护其正常运行。
118_车门密封条设计指南

车门密封条1概述汽车车门属于经常活动的部件,车门一般要设计专门的密封条进行密封;由于此类密封对耐久及弹性都有较高的要求,因此车门密封条一般都需要用橡胶材料制成。
2范围本规范规定了车门密封条安装在车门飯金上的设计要求。
本规范适用于公司设计的轿车及衍生车车门密封条的设计。
设计时参照本规范。
3引用性文件车门密封条的设计法规要求:如表格1表格14目的轿车密封性设计是针对车身室内居住环境改善,提高车身防腐蚀性要求进行的。
主要包括防止尘、沙、雨、污染气体进入车内;防止振动、噪音、热量侵入车内;防止腐蚀介质侵蚀车身板件。
5车门密封条设计要求5.1车门密封条的功能及外观要求满足密封要求:使密封条有足够的压缩量与接触面积,保证密封条在公差范围内具有良好的密封效果;满足工艺要求:密封条断面及接角的设计应该利于工艺生产,且易于产品一致性的控制;满足外观要求:密封条的设计外观应该具有良好的外观效果,且外观质量一致性容易控制;满足装配要求:满足插拔力要求,既能易于装配,又能保证不易脱落;满足开关门力矩要求:整个车门的开关门力矩保持在25kgf左右;满足成本要求:密封条断面、接角及材料的选用在满足功能前提下需降低生产成本,既要考虑材料的成本,又要考虑生产时间及人力资源成本;满足标准要求:满足气味性、耐久性、耐候性等标准要求。
6设计流程图7设计步骤7.1车门上段截面线考虑要点:由于车门飯金在腰线以上无固定点,由于密封条的反作用力,车门上段有向外的轻微变形, 且在车辆高速行驶的过程中,由于车门内外气压不一样,车门飯金受到内外空气的合力方向向 外,因此车门钗金应该比侧围外表面低大约1〜3mm;各种压缩量应该合理,且在门上段保持一致;车门密封条为第一道密封,起到主要密封作 用,一般建议压缩量为6-8mm o飯金的走向要考虑拔模方向,飯金要容易成型,车门密封条固定于车门内板上,密封面需 与车门运动方向垂直,车门锁鱼嘴处由于布責空间问题,可能会导致此处钗金难以成型,设计 时需综合考虑后进行设计;车门外飯与流水槽的焊接面之间的夹角应该保持平顺过渡,以保证流水槽能够容易成型; 呢嘈与门洞条之间的银金露出部分要保持均匀,以利于外观质量。
汽车车门窗框设计规范
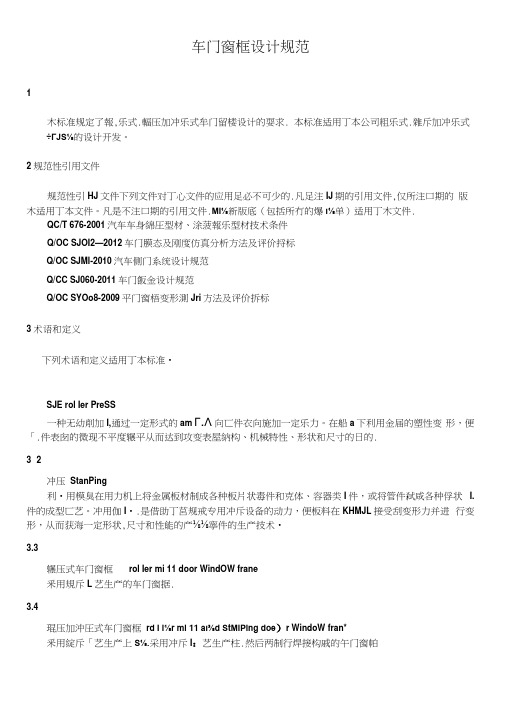
车门窗框设计规范1木标准规定了報,乐式.輻压加冲乐式牟门留楼设计的耍求. 本标准适用丁本公司粗乐式.雜斥加冲乐式÷ΓJS⅛的设计开发。
2规范性引用文件规范性引HJ文件下列文件对丁心文件的应用足必不可少的.凡足注IJ期的引用文件,仅所注口期的版木适用丁本文件。
凡是不注口期的引用文件.Mi⅛新版底(包括所冇的爆ι⅛单)适用丁木文件.QC/T 676-2001汽车车身綿圧型材、涂菠報乐型材技术条件Q/OC SJOI2—2012车门膜态及刚度仿真分析方法及评价捋标Q/OC SJMl-2010汽车侧门系统设计规范Q/CC SJ060-2011车门飯金设计规范Q/OC SYOo8-2009平门窗梧变形測Jri方法及评价拆标3术语和定义下列术语和定义适用丁本标准•SJE rol Ier PreSS一种无幼削加I,通过一定形式的am Γ.Λ向匸件衣向施加一定乐力。
在船a下利用金届的塑性变形,便「.件表囱的微现不平度辗平从而达到攻变表屋納构、机械特性、形状和尺寸的日的.3 2冲压StanPing利•用模臭在用力机上将金属板材制成各种板片状毒件和克体、容器类I件,或将管件弑咸各种俘状I.件的成型匸艺。
冲用伽I•.是借助丁莒规戒专用冲斥设备的动力,便板料在KHMJL接受刮变形力并进行变形,从而获海一定形状,尺寸和性能的产⅛⅛寧件的生产技术•3.3辗压式车门窗框rol Ier mi 11 door WindOW frane釆用規斥L艺生产的车门窗据.3.4琨压加沖圧式车门窗框rd I l⅛r mi 11 aι⅜d StMlPing doe)r WindoW fran*釆用綻斥「艺生产上S⅛.采用冲斥I:艺生产柱.然后两制行焊接构戚的午门窗帕41总布養设计要求4.1.1引丫及规范玻璃的升降.提供視觉区域及保持空勺1流連,4 12辐乐式乍门谢框具冇宽度较雀外形芙观的优点;辐压加冲压式Sfiffi利丁外怖件的安辕对丁提升牟身堆体品质提供较大空何.4.2材斡设计要求4 2 1宙惟相关嗥部件选材,见表Ia表1选材材质料厚农面处埋后视锁安芨桓DCXH/1O1/BLJ50P1 1.4/1 Z FB| 上虫阪DCoI 1.8FBL 期柜连戏板DCoI15EB/FD4. 2 2基丁防密的翌求.后视儀安装板可以采用相对应的镀锌板DC5W+2. DC521H2或具他材质。
机动车用不锈钢光亮饰条标准规定

汽车用不锈钢光亮饰条标准标准修订记录目录前言 (2)1、范围 (3)2、规范性引用文件 (3)3、组成 (3)4、要求 (3)5、试验方法 (5)6、检验规则 (6)7、标志、包装、运输和储存 (7)前言本标准自发布之日起实施。
本标准由研究院提出。
本标准由研究院归口。
本标准起草单位:究院车身部本标准主要起草人:陈俊慧本标准为首次发布。
汽车不锈钢光亮装饰条技术条件1.范围本标准规定了汽车不锈钢光亮装饰条总成的组成、要求、试验方法、检验规则、标志、包装、运输与贮存。
本标准适用于基体为不锈钢材料的装饰条总成(以下简称装饰亮条)。
2.规范性引用文件下列文件对于本文件的应用是必不可少的。
凡是注日期的引用文件,仅注日期的版本适用于本文件。
凡是不注日期的引用文件,其最新版本(包括所有的修改单)适用于本文件。
JIS-G4305-2005 冷轧不锈钢钢板和钢带GB/T 2828.1-2003 计数抽样检验程序GB/T 10125-1997 人造气氛腐蚀试验盐雾试验GB 1031 表面粗糙度参数及其数值GB 11566 轿车外部凸起物QC/T 17-1992 汽车零部件耐侯性试验一般规则3.组成3.1 装饰亮条的组成主要有以下3类:A类:a)光亮条(滚压) b)端盖 c) 3M胶带B类:a)光亮条(复押) b)端盖 c) 3M胶带C类:a)光亮条(滚压) b)端盖注塑 c) 铆钉4.要求4.1 一般要求4.1.1 窗框亮条应符合本标准的要求,并应按照经规定程序批准的图样及设计文件制造。
4.1.2 窗框饰条装配完成后应静置,时间应不小于1天。
4.2 装车要求4.2.1 装饰亮条装车后应符合GB 11566的规定。
4.3 外观要求4.3.1 装饰亮条金属外观面a)无可见划伤、粒点、压痕、裂纹;无明显的扭曲变形及表面磨损;不得有任何影响装配的缺陷。
b)表面不允许有直径0.3mm以上的疵点和直径0.8mm以上的压痕,对于未超出此限值的疵点和压痕在10 cm2内所允许的点数不得超过2点,且任意压痕和疵点间的距离不得小于20cm;c)表面不允许存在长1mm宽0.005mm以上划痕。
汽车车门钣金设计规范模板

XXXX公司企业规范编号:xxxx 汽车车门钣金设计规范模板XXXX发布车门钣金设计规范1.范围本规范规定了车门钣金的术语、一般汽车车门钣金的设计规则以及设计方法。
本规范适用于各种轿车,其它车型可参考执行。
2.车门基本简介2.1车门钣金概述1.作为外覆盖件,起装饰作用,保证装配后外观效果,需保证翼子板、侧围、前后门之间的间隙平度满足要求;2.有效保证车门密封性,避免出现漏水、风噪,导致顾客抱怨;3.为开启件,需满足开启及关闭的易操作性;4.车辆在行驶过程中保证车门始终处于关闭状态;5.保证车门很容易的装配到车身骨架上;6.为车身附件安装(外开把手、后视镜、外水切、昵嘈、内水切、门护板、门锁、扬声器、防水膜、升降器等安装)提供必要安装点及型面;7.保证升降系统的正常运行;8.保证行车门在行驶过程中不出现振动;不产生噪音;9.车门售后可更换及可维修性;10.具有承受一定作用力的刚度及强度2.2车门结构类型实用文档车门是车身的重要组成部分。
根据车型不同,车门结构形式一般有旋开式车门如图2.1所示、滑动门以及外摆式车门等,还有一些轿车上使用了上下车极方便的鸥翼式车门。
目前轿车车门使用最多的是旋开式车门,应用较多的轿车车门结构全尺寸内外板结构(整体式)、滚压窗框结构(分体式)以及半开放式车门结构(混合式),其结构具有各自不同的特点。
图2.1 旋开式车门2.2.1整体式----即车门面板与门框部分一体成形。
由全尺寸的冲压外板、全尺寸的冲压内板和嵌在内外板间的窗框导轨组成,导轨为U 字形滚压成型件,焊接在内板上,最后外板与内板总成通过包边方式闭合起来,这种车门板金结构在许多早期的车型被普遍采用。
优点:具有较好的完整性,整个车门的刚度较好,一体冲压出来的门板尺寸精度较高,并且加工工序较少、工艺简单。
缺点:窗框外边框通常较宽大,窗框的可装饰性不强,对造型有限制,不太符合现在造型的要求,而且全尺寸的门板需要较大的冲压模具,对冲压模的要求也比较高,整套模具的成本很高,由于窗框是一体冲压而成,废料面积较大,材料利用率较低。
亮饰条设计指南
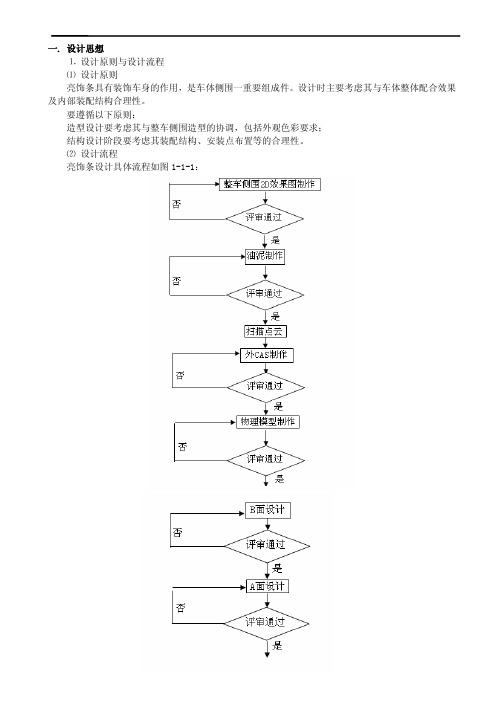
一.设计思想⒈设计原则与设计流程⑴设计原则亮饰条具有装饰车身的作用,是车体侧围一重要组成件。
设计时主要考虑其与车体整体配合效果及内部装配结构合理性。
要遵循以下原则:造型设计要考虑其与整车侧围造型的协调,包括外观色彩要求;结构设计阶段要考虑其装配结构、安装点布置等的合理性。
⑵设计流程亮饰条设计具体流程如图1-1-1:图1-1-1亮饰条设计流程2.环境条件、材料、热处理及加工要求亮饰条骨架材料多为SUS430,挤出基体材料多为PVC,耐热性80℃,耐寒性要符合-40℃。
表面有镀铬的亮条。
装配卡扣材料为POM。
3.设计基本限制因素设计主要受整车侧围造型因素的限制,设计中务必要确保与车体配合良好。
4.零部件装配设计亮饰条装配结构的设计通常是卡扣与车体卡接固定的结构,卡扣布置一定要合理。
5.零部件试验要求⑴耐碱性试验将不锈钢浸入0.1N NaOH中5分钟,取出用布擦拭后放入80℃烘箱中30分钟,取出观察,试验要求:表面无明显变化。
⑵耐酸性试验将不锈钢浸入0.1N H2SO4中5分钟,取出用布擦拭后放入80℃烘箱中30分钟,取出观察,试验要求:表面无明显变化。
⑶CASS试验按ASTMB368,16小时,试验要求:不锈钢表面上不存在腐蚀区域。
⑷耐清洁剂性试验用清洁剂浸湿绒棉布,擦拭产品表面,再清洗,晾干,试验要求:外观清洁完好,无明显变化。
⑸耐寒性试验在-40±2℃条件下24小时,试验要求:表面不允许有皱纹及波浪的改变,不允许破裂或剥离。
⑹高温高湿性试验在标准实验室环境下(80±2℃,相对湿度95~100%)暴露7天,试验要求:外观不允许裂纹、破裂、变白、剥离和溶胀,表面不允许发粘、变色和软化、硬化。
二.零部件设计1.设计步骤及设计计算⑴造型设计阶段:该阶段主要要考虑亮饰条与整车侧围造型的协调一致,包括外表面色彩处理、周边配合间隙、面差等要符合外观设计要求;⑵结构设计阶段:该阶段主要是在油泥造型基础上对各部位的结构进行详细设计。
车门内饰板设计规范

编号代替密级商密×级▲汽车工程研究院设计技术规范车门内饰板设计规范2005-01-22制订 2005-11-22发布前言汽车的自主开发是中国汽车业健康发展的必经之路。
在汽车自主开发设计中,内外饰设计占有及其重要的位置,特别是车门内饰板设计。
在此,特编写此规范——《车门内饰板设计规范》,希望对坚持走自主开发之路的新生力量的快速成长能起到一定帮助,也希望对各位设计人员能有一定帮助。
本规范尚有许多不足之处,需要我们在实际操作中进一步完善和补充,希望大家能给予指正。
本规范由汽车工程研究院车身所负责起草;本规范由汽车工程研究院项目处进行管理和解释;本规范主要起草人员:编制:校核:审定:批准:本规范的版本记录和版本号变动及修订记录车门内饰板设计规范一、适用范围本规范规定了轿车车门内饰板在开发设计过程中应遵守一些要求和标准,规定了车门内饰板开发的一般过程、材料的选择、车门内饰板的分块、结构等。
本规范适用于M1、N1类车辆。
二、专业术语三维坐标系:指汽车制造厂在最初设计阶段确定的由三个正交的基准平面组成的系统。
三个基准平面如下:X基准平面——垂直于Y基准平面的铅垂面,通常规定通过左右前轮中心;Y基准平面——汽车纵向对称平面;Z基准平面——垂直于Y和X基准平面的水平面。
R点:汽车制造厂规定的基准点,该点具有及车辆结构相关的固定的坐标,对应于驾驶员座位在正常的最低及最后位置时的躯干和大腿旋转点(H点)的理论位置,或各座位在车辆制造厂规定的使用位置时的H点理论位置。
三、车门内饰板总成的组成车门内饰板总成通用组成件见表一,根据造形的不同、所开发车的档次不同和所选用的生产工艺的不同等,车门内饰板总成组成会有所不同,车门内饰板总成各部件间主要是采用焊接、螺钉或者卡接结构连接成整体。
表一:下图是以本公司前车门内饰板总成为例介绍门的组成:车门锁止按钮套圈车门内开手柄总成六、车门内饰板总成各部件设计要求 :1、吸能块设计要求此件根据法规要求而设计(法规需要),多采用热熔胶及门板本粘接,一般情况下为、发泡,发泡倍数协商;以下是其设计及周边配合要求: 编号 内 容 基准值 备注① 及车窗玻璃的间隙 10 ② 及车门内板表面的间隙 5 ③ 及车门内板孔的间隙 10 ④及车门内饰的间隙2门内饰杂物盒(包含扬声器孔盖) 车门内拉手(包含车门控制开关)门内饰板主体(包含扶手)门内饰板上部装饰板杂物盒盖板2、内开扳手框的设计要求内开扳手框,是一个覆盖于门板上、套在内开扳手的装饰件,多采用材料加工;它在门板总成上的位置随内开扳手而确定,一般采用螺钉联接及卡挂在内开扳手座上两种方式固定(均需要设计相的卡挂结构及门板本体固定),下表是其设计的边界要求:⑨编号内容基准值备注①扣手度<685最大限度760②从开始的位置>480最小限度420③及竖立把手开始位置120~1402④内开扳手框周围及对手件的间隙(前后方向)⑤内开扳手框周围及对手件的3搭接量(前后方向)⑥内开扳手框周围及对手件的1间隙(上下方向)3、摇窗机手柄设计要求摇窗机手柄总长度一般设计为120左右,多数情况下借用参考车件,需配合升降玻璃扭矩校核;下表是其设计的边界要求:⑦及座椅垫的距离参照图B手柄臂背面及门板距7⑧离0.3手柄臂背面及门板平⑨行度要求4、电动控制钮的布置设计要求编号内容基准值备注625~715①电动控制钮前端布置及人体模型肩部转点要求②从把手开始的距离>140③从把手开始的角度<18°④前后倾斜角0~10°前面提升至10°⑤左右倾斜角0~5°扶手表面⑥及内饰表面的距离≥255、肘靠的设计要求⑴肘靠也叫扶手,分独立加工和及门板本体一体加工两种方式,独立加工件分纯注塑、覆表皮或面料(低压注塑或包覆)、塘塑、聚胺脂发泡等类型;及门板一体成型多采用压制和低压注塑两种成型方式,这两种均需要覆面料或表皮,同时需在肘靠处表皮下增加泡沫垫或成型软垫。
全车密封条技术要求

全车胶条技术和质量要求一、技术要求1密封条应按经规定程序批准的图样及技术文件制造,并应符合本标准的规定。
2密封条工作温度为 -40 ℃~80 ℃。
3材料要求3.1 密封条用材料类别应符合表1的规定。
表1 密封条用材料类别4、橡胶密封条胶料性能按此标准执行5、外观质量按照以下要求执行6、未注公差尺寸的极限偏差6.1密实胶密封条尺寸公差6.1.1密实胶密封条截面尺寸公差密实胶密封条截面尺寸公差按此表进行,其中装配尺寸公差按E2级,非装配尺寸公差按E3级规定;密实胶密封条截面尺寸公差(单位:mm)6.1.2密实胶密封条长度尺寸公差实心橡胶密封条长度尺寸公差按此表进行,其中接角、接头产品按L1级。
密实胶密封条长度公差(单位:mm)6.2海绵橡胶密封条尺寸公差6.2.1海绵橡胶密封条截面尺寸公差,安装尺寸按G1执行,非安装尺寸依照G3执行。
海绵橡胶截面尺寸公差(单位:mm)6.2.3海绵橡胶接角的长度公差。
)6.3海绵类密封条的尼龙扣钉孔距偏差按±1.5mm,排气孔距偏差按±10mm。
6.4密封条冲孔、冲槽、端头冲切尺寸偏差按GB/T 3672.1表7中EC2级的规定。
7、成品性能要求7.1橡胶密封条成品性能8. 供方提供的产品需要满足法律、法规要求。
a) 禁限用有害物质:标准符合Q/CC JT098-2008《汽车产品中有毒有害物质的限量要求》中关于铅、镉、汞、六价铬、PBB、PBDE的限值要求。
汽车产品中有毒有害物质的详细检测方法依照IEC 62321、DIN3314执行。
试验周期为:“不定期抽检”。
b)针对内饰非金属件气味散发性应符合Q/CC JT001-2009《汽车内饰材料气味散发性试验方法和限值》中4级要求。
9、出厂检验9.1外观质量、成品长度检验:出厂前按GB/T2828.1-2003正常检查一次,抽样方案取AQL为1.5和一般检验水平Ⅱ随机抽样进行检验。
如检验不合格,退回生产部门逐根检查。
Q ZTB 05 024-2015 汽车密封条技术规范
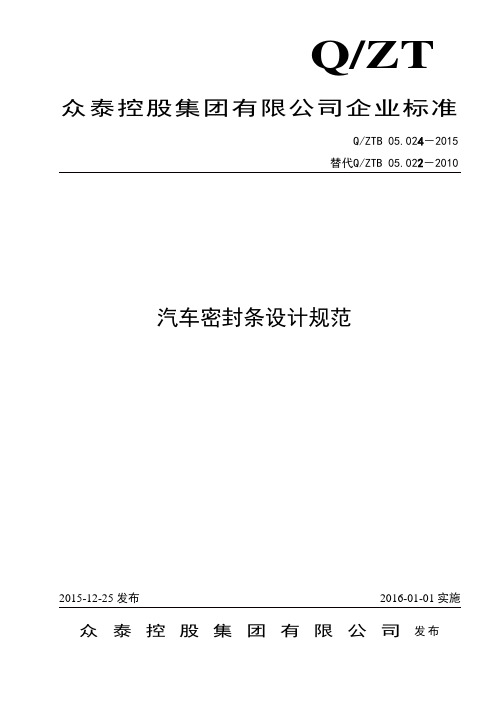
Q/ZT 众泰控股集团有限公司企业标准Q/ZTB 05.024-2015替代Q/ZTB 05.022-2010 汽车密封条设计规范众泰控股集团有限公司发布前言本标准以《Q/ZTB 05.022-2010》为主,与其相比,主要技术变化点如下:——增加密封条与门护板间隙的要求(见4.3.1);——门洞密封条压缩量范围重新定义(见4.3.1);——新增欧美系密封条、导槽设计的注意事项(见4.3.2.1);——新增引擎盖密封条断面、钣金设计的要求(见4.3.5);——其它变化、新增。
本标准由众泰汽车工程研究院提出。
本标准由众泰汽车工程研究院车型管理科归口管理。
本标准由众泰汽车工程研究院车身科负责起草。
本标准主要起草人:李玉玺。
本标准为首次修订。
汽车密封条设计规范1范围本标准规定了汽车用密封条的设计规范要求。
本标准适用于新开发的M1类车辆。
2规范性引用文件QZTB 05.073-2015 整体式车门结构密封系统设计规范QZTB 05.053-2014 汽车用TPV材料玻璃呢槽技术条件QZTB 05.058-2014 汽车密封条用TPV材料性能要求QZTB 05.070-2015 汽车用密封条插入力拔出力试验规范3术语与定义下列术语和定义适用于文件。
密封系统密封系统最基本的目的是保证车体的密封,阻止车外的尘、沙、雨,雪及噪音进入车内。
4密封系统分类对于汽车的密封,一般分为三大类。
对于密封系统的规范,本文只针对第三类进行描述。
4.1车身本体的密封即车身骨架焊接总成时的钣金接触缝隙等的密封,一般采用密封胶进行密封;另外在钣金进行总成时或车身附件进行安装时所留的诸多工具过孔以及线束过孔,通常需要增加专门的堵盖进行密封;4.2装配后非活动部件与车身钣金的密封如前风窗、后风窗、车门三角窗、侧围固定玻璃等,一般车门上的三角窗玻璃考虑到需要拆卸,因此采用注塑胶条进行密封与固定,其它在车身上的固定玻璃多采用密封胶进行密封与紧固:车门护板、内外三角块及后视镜等塑料件的安装卡扣,在设计上也要有一定的密封功能;4.3活动部件的密封如前、后车门、行李箱、车门玻璃等经常活动部件的密封,一般要设计专门的密封条进行密封;由于此类密封件对耐久和弹性都有较高的要求,因此一般都需要用橡胶材料或TPE材料制成。
车门亮条设计规范

车门亮条设计规范车门亮条设计规范车门亮条设计规范1范围本标准介绍了林汽车车门亮条的材料,制造工艺,种类,设讣要求。
本标准适用于林汽车车门亮条设il ?要求?2规范应用文件规范性引用文件下列文件对于本文件的应用是必不可少的。
凡是注日期的引用文件,仅注日期的版凡是不注日期的引用文件,英最新版本(包括所有的修改单)适用于本文件。
3术语与定义车门窗框上表而不锈钢或铝合金部分,主要起装饰作用,下文简称亮条。
一种常温下具有橡胶的物理特性,高温下又具有可注塑加工特征的材料。
是指将车门亮条固定在车门窗框飯金上的卡扣,用于亮条的定位。
4技术要求 4.1车门亮条结构 4.1.1车门亮条结构分类车门亮条结构一般分为金属亮条结构及包覆式亮条结构两种,车门亮条的结构一般可划分:亮条本体、端头、3M 胶带,如图1所示。
4.1.2车门亮条组成亮条本体为车门亮条的主要组成部分,不锈钢馄压+拉弯成型或铝合金挤出+拉弯成型工艺,用来卡接在车门窗框上。
4.1.3车门亮条端头结构本适用于本文件3 GB/T 10125 人造气杲腐蚀试验盐雾试验 GB/T 1084 未注公差尺寸GB/T 3512 硫化橡胶或热塑性橡胶热空气加速老化和耐热试验QC/T15-1992汽车塑料制品通用试验方法3. 1 车门亮条本体3.2 热塑性弹性体TPV3.3 定位卡扣全亮面结构亮条断面包覆亮面断面端头采用注塑成型或二次注塑成型?用来将车门亮条紧固在车门窗框上,端头与亮条采用卡接或粘接方式连接在一起。
4.2车门亮条的设计4.2.1车门亮条本体的结构设计、断面及公差分配车门亮条厚度一般为0. 4mm或0. 5mm, 3M胶带厚度一般为0. 6am或0. 8mm。
亮条断而卡接韶位断面开口公差为+ 0. 2mm,断而线轮劇公差为±0?5Dmh而轮廓度公差为±l?0mm,苴他要求见图2所示。
图2车门亮条断面的主要公差尺寸4.2.2端头与车门窗框的配合结构亮条端头与窗框直接采用卡扣卡接或自攻丝?进行装配、锁紧,如图3所示。
提示灯条设计标准规范是什么
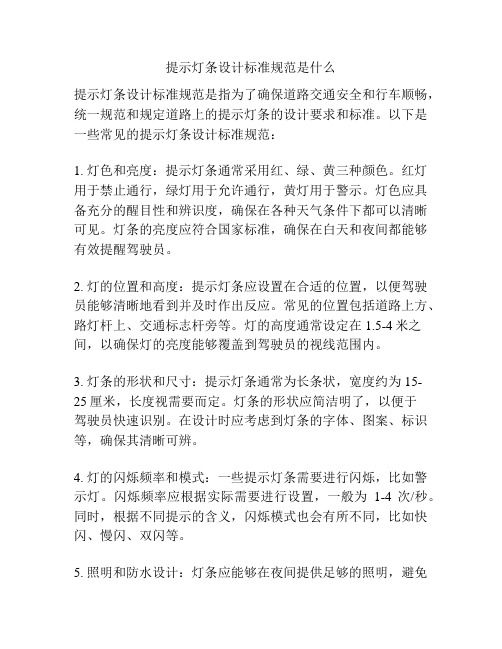
提示灯条设计标准规范是什么提示灯条设计标准规范是指为了确保道路交通安全和行车顺畅,统一规范和规定道路上的提示灯条的设计要求和标准。
以下是一些常见的提示灯条设计标准规范:1. 灯色和亮度:提示灯条通常采用红、绿、黄三种颜色。
红灯用于禁止通行,绿灯用于允许通行,黄灯用于警示。
灯色应具备充分的醒目性和辨识度,确保在各种天气条件下都可以清晰可见。
灯条的亮度应符合国家标准,确保在白天和夜间都能够有效提醒驾驶员。
2. 灯的位置和高度:提示灯条应设置在合适的位置,以便驾驶员能够清晰地看到并及时作出反应。
常见的位置包括道路上方、路灯杆上、交通标志杆旁等。
灯的高度通常设定在1.5-4米之间,以确保灯的亮度能够覆盖到驾驶员的视线范围内。
3. 灯条的形状和尺寸:提示灯条通常为长条状,宽度约为15-25厘米,长度视需要而定。
灯条的形状应简洁明了,以便于驾驶员快速识别。
在设计时应考虑到灯条的字体、图案、标识等,确保其清晰可辨。
4. 灯的闪烁频率和模式:一些提示灯条需要进行闪烁,比如警示灯。
闪烁频率应根据实际需要进行设置,一般为1-4次/秒。
同时,根据不同提示的含义,闪烁模式也会有所不同,比如快闪、慢闪、双闪等。
5. 照明和防水设计:灯条应能够在夜间提供足够的照明,避免造成视觉盲区。
此外,灯条应具备防水功能,以确保在恶劣的天气条件下仍然能正常工作,不影响提示效果。
6. 维护和保养:为了确保提示灯条的正常运行和使用寿命,应定期进行维护和保养。
包括灯泡的更换、电路系统的检修、灯体的清洁等,以确保灯条的正常工作和提醒功能。
总之,提示灯条设计标准规范是为了保障道路交通安全和行车顺畅,统一规范和规定道路上的提示灯条的设计要求和标准。
这些规范包括灯色和亮度、灯的位置和高度、灯条的形状和尺寸、灯的闪烁频率和模式、照明和防水设计以及维护和保养等方面的要求。
只有符合这些规范,才能确保提示灯条的有效性和可靠性。
车门亮条设计规范
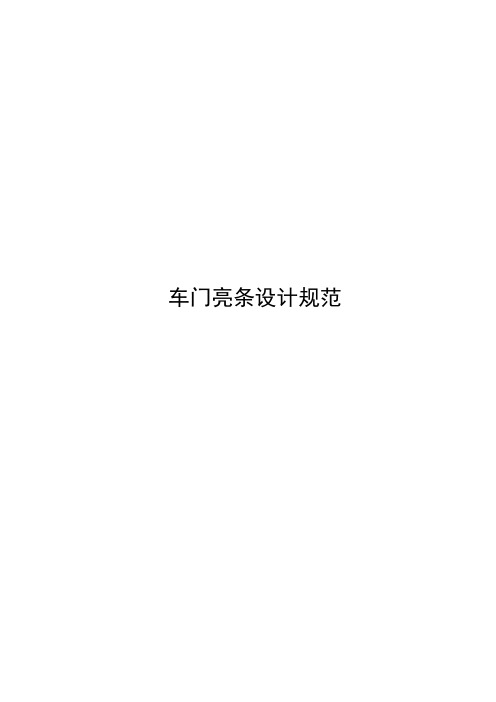
车门亮条设计规范车门亮条设计规范1 范围本标准介绍了**汽车车门亮条的材料,制造工艺,种类,设计要求。
本标准适用于**汽车车门亮条设计要求。
2 规范应用文件规范性引用文件下列文件对于本文件的应用是必不可少的。
凡是注日期的引用文件,仅注日期的版本适用于本文件。
凡是不注日期的引用文件,其最新版本(包括所有的修改单)适用于本文件。
GB/T 10125 人造气氛腐蚀试验盐雾试验GB/T 1084 未注公差尺寸GB/T 3512 硫化橡胶或热塑性橡胶热空气加速老化和耐热试验QC/T15-1992 汽车塑料制品通用试验方法3 术语与定义3.1 车门亮条本体车门窗框上表面不锈钢或铝合金部分,主要起装饰作用,下文简称亮条。
3.2 热塑性弹性体TPV一种常温下具有橡胶的物理特性,高温下又具有可注塑加工特征的材料。
3.3 定位卡扣是指将车门亮条固定在车门窗框钣金上的卡扣,用于亮条的定位。
4 技术要求4.1 车门亮条结构4.1.1 车门亮条结构分类车门亮条结构一般分为金属亮条结构及包覆式亮条结构两种,车门亮条的结构一般可划分:亮条本体、端头、3M胶带,如图1所示。
全亮面结构亮条断面包覆亮面断面4.1.2 车门亮条组成亮条本体为车门亮条的主要组成部分,不锈钢辊压+拉弯成型或铝合金挤出+拉弯成型工艺,用来卡接在车门窗框上。
4.1.3 车门亮条端头结构端头采用注塑成型或二次注塑成型,用来将车门亮条紧固在车门窗框上,端头与亮条采用卡接或粘接方式连接在一起。
4.2 车门亮条的设计4.2.1 车门亮条本体的结构设计、断面及公差分配车门亮条厚度一般为0.4mm或0.5mm,3M胶带厚度一般为0.6mm或0.8mm。
亮条断面卡接部位断面开口公差为±0.2mm,断面线轮廓公差为±0.5mm,面轮廓度公差为±1.0mm,其他要求见图2所示。
图2 车门亮条断面的主要公差尺寸4.2.2 端头与车门窗框的配合结构亮条端头与窗框直接采用卡扣卡接或自攻丝进行装配、锁紧,如图3所示。
汽车亮饰条技术条件
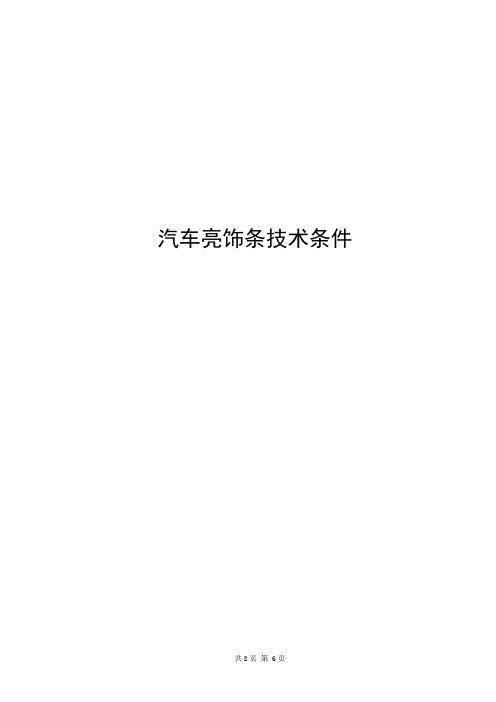
汽车亮饰条技术条件汽车亮饰条技术条件1 范围本标准规定了PVC复合装饰亮条(简称产品)的质量要求、技术要求和试验方法、检验规则、标志、包装、运输及存储。
本标准适用于以软质PVC和不锈钢钢带复合的亮面密封条产品。
2 规范性引用文件下列文件中的条款通过本标准的引用而成为本标准的条款。
凡是注日期的引用文件,其随后所有的修改单(不包括勘误的内容)或修订版本均不使用本标准。
凡是不注日期的引用文件,其最新版本适用于本标准。
GB /T 1040.2-2006 塑料拉伸性能的测定第2部份:模塑和挤塑塑料的试验条件GB/T 2411 -2008 塑料和硬橡胶使用硬度计测定压痕硬度(邵氏硬度)GB /T 2828.1-2012 计数抽样检验程序第1部分:按接收质量限(AQL)检索的逐批检验抽样计划(idtISO 2859一1:1999)GB /T 2917.1-2002 以氯乙烯均聚物和共聚物为主的共混物及制品在高温时放出氯化氢和任何其他酸性产物的测定刚果红法GB /T 3672.1-2002 橡胶制品的公差第1部分:尺寸公差(ISO3 302- 1 :1996,ID T)GB /T 5470-2008 塑料冲击法脆化温度的测定JIS G 4305-2005 冷轧不锈钢带GB /T 7141-2008 塑料热老化试验方法GB /T 7762-2003 硫化橡胶或热塑性橡胶耐臭氧龟裂静态拉伸试验GB/T 16422.2-1999 塑料实验室光源暴露试验方法第2部分:氙弧灯QC /T 643-2000 车辆用密封条的污染性试验方法GB/T 8410 汽车内饰材料的燃烧特性JIS D 0205 汽车部件的耐候性试验通则GB/T 10125 人造气氛腐蚀试验盐雾试验3 技术要求3.1 一般要求产品应符合本标准的要求,并应按照经规定程序批准的图样及设计文件制造。
3.2 特殊要求应符合供需双方协商确定的封样件或样板要求。
3.3 规格尺寸3.3.1 产品断面形状及尺寸应符合其十倍放大倍率的控制图公差范围之内,如无明确要求的可按GB/T 3672.1-2002执行。
车门设计方法和规范
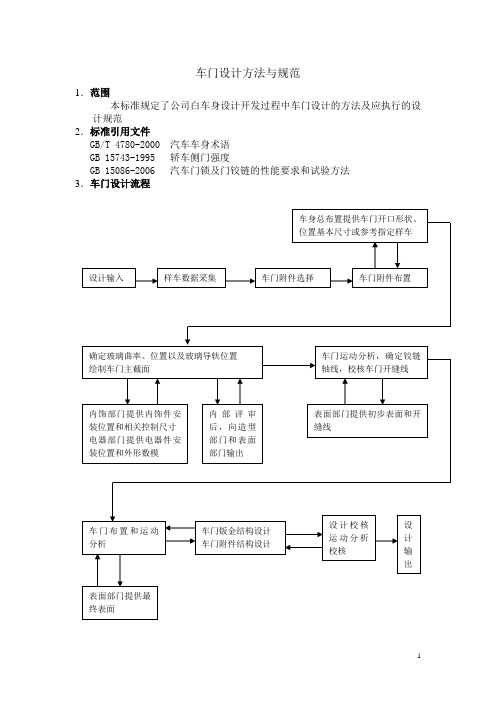
车门设计方法与规范1.范围本标准规定了公司白车身设计开发过程中车门设计的方法及应执行的设计规范2.标准引用文件GB/T 4780-2000 汽车车身术语GB 15743-1995 轿车侧门强度GB 15086-2006 汽车门锁及门铰链的性能要求和试验方法3.车门设计流程3.设计输入A.设计任务书、项目要求、计划及客户要求B.车身总布置方案中与车门有关的控制尺寸C.参考样车、样件、点云、参考资料及客户对车门附件的选用要求D.车门附件的样件、数模、图纸、性能参数;密封条和挡水条断面图E.内饰部门提供内饰件安装位置和相关控制尺寸F.电器部门提供电器件安装位置和外轮廓数模G.数字表面4.设计结构的熟悉及数据的采集A.样车拆解之前应观察样车车门结构,注意车门与侧围及内饰的密封及配合关系;外后视镜与车门的连接关系。
B.样车拆解之前应采集以下数据:车门开度及档位、铰链轴线的坐标位置、门缝尺寸及面差、玻璃与门外板面差、门内饰与侧围内饰配合尺寸、门与侧围密封面的配合尺寸、内外把手和车门的配合尺寸、缓冲块处门内板与侧围外板距离。
C.拆下门内饰板后应采集以下数据:玻璃上止点位置、玻璃下止点位置、玻璃行程、玻璃与门内板、外板、防撞梁、锁体之间的最小距离、玻璃升降器的设计位置等。
5.车门开口线的确定A.车门开口大小、形状和位置的基本尺寸由车身总布置确定,开口线的初步形状由造型部门根据车身总布置确定的基本尺寸按造型风格确定,也可以根据客户要求按样车逆向确定。
B.车门结构设计人员应及时对初步的开口线进行分析,校核其是否能满足铰链布置要求和车门运动间隙要求,做到及时发现问题、及时反馈问题。
C.门缝间隙应根据制造企业的生产水平确定,一般为4mm~5mm,车门下边间隙通常比车门其余周边间隙大1mm左右。
D.车门开口线最终由数字表面部门确定。
6.确定玻璃曲面A.玻璃曲面的曲率半径和倾斜度由车身总布置和造型风格确定;也可以按要求根据样车逆向确定。
- 1、下载文档前请自行甄别文档内容的完整性,平台不提供额外的编辑、内容补充、找答案等附加服务。
- 2、"仅部分预览"的文档,不可在线预览部分如存在完整性等问题,可反馈申请退款(可完整预览的文档不适用该条件!)。
- 3、如文档侵犯您的权益,请联系客服反馈,我们会尽快为您处理(人工客服工作时间:9:00-18:30)。
车门亮条设计规范
车门亮条设计规范
1范围
本标准介绍了林汽车车门亮条的材料,制造工艺,种类,设讣要求。
本标准适用于林汽车车门亮条设il •要求•
2规范应用文件
规范性引用文件下列文件对于本文件的应用是必不可少的。
凡是注日期的引用文件,仅注日期的版 凡是不注日期的引用文件,英最新版本(包括所有的修改单)适用于本文件。
3术语与定义
车门窗框上表而不锈钢或铝合金部分,主要起装饰作用,下文简称亮条。
一种常温下具有橡胶的物理特性,高温下又具有可注塑加工特征的材料。
是指将车门亮条固定在车门窗框飯金上的卡扣,用于亮条的定位。
4技术要求 4.1车门亮条结构 4.1.1车门亮条结构分类
车门亮条结构一般分为金属亮条结构及包覆式亮条结构两种,车门亮条的结构一般可划分:亮条本 体、端头、3M 胶带,如图1所示。
4.1.2车门亮条组成
亮条本体为车门亮条的主要组成部分,不锈钢馄压+拉弯成型或铝合金挤出+拉弯成型工艺,用来卡 接在车门窗框上。
4.1.3车门亮条端头结构
本适用于本文件3 GB/T 10125 人造气杲腐蚀试验盐雾试验 GB/T 1084 未注公差尺寸
GB/T 3512 硫化橡胶或热塑性橡胶热空气加速老化和耐热试验 QC/T15-1992
汽车塑料制品通用试验方法
3. 1 车门亮条本体
3.2 热塑性弹性体TPV
3.3 定位卡扣
全亮面结构亮条断面 包覆亮面断面
端头采用注塑成型或二次注塑成型•用来将车门亮条紧固在车门窗框上,端头与亮条采用卡接或粘接方式连接在一起。
4.2车门亮条的设计4.2.1车门亮条本体的结构设计、断面及公差分配
车门亮条厚度一般为0. 4mm或0. 5mm, 3M胶带厚度一般为0. 6am或0. 8mm。
亮条断而卡接韶位断面开口公差为+ 0. 2mm,断而线轮劇公差为±0・5Dmh而轮廓度公差为±l・0mm,
苴他要求见图2所示。
图2车门亮条断面的主要公差尺寸
4.2.2端头与车门窗框的配合结构
亮条端头与窗框直接采用卡扣卡接或自攻丝•进行装配、锁紧,如图3所示。
为保证车门亮条安装后平顺,亮条端头与窗框内板中间预留a 5咂间隙。
图3车门亮条端头与车门窗框的配合方式
4.2.3车门亮条的安装配合公差
根据车门亮条断而结构不同,分别对车门亮条与窗框配合间隙进行规范,如图4、图5所示。
图4全亮面结构亮条
说明:
A —亮条断面公^±0. 2mm.弯曲后为(-0. 3,0.2)(弯曲R 大于800mm ):弯曲后(-0. 5,0.3)(弯
曲R 大于35Oomit 小于500ram):
B 一设计间陳为0. lmm-0. 2mm :
C 一设计间隙为0. 2mra-0・3mm (对门框精度较好的情况八 设计间隙0. 4眄0・5mm (对门框精度较差 的情
况):
D —设计间陳a Smm-L 0mm (间隙越小,装配越困难)°
螺钉 银金
扳金
密封条 绒布条 绒布条
亮条端头 条本体
、
V
说明:
A—亮条断面公差±0・2mDb弯曲后为(-0. 3,0.3)(弯曲R大于800mm):弯曲后(-0.6,0.3)(弯曲R大于350nmb小于oOOram):
B"设计间陳为0. 1mm:
C一设计间隙为0. 2mm (对门框精度较好的情况):设计间隙0・4mm (对门框精度较差的情况):
D~设计间隙a 8mm-L 0mm (间隙越小,装配越困难)°
车门亮条的安装方式均为从B处进行安装,C处进行卡接。
5 性能要求
5.1 一般要求
车门亮条总成应按规定程序批准的数据、图纸及技术文件制造,如有其它特殊要求,由供需双方协
5.2外观质量
车门亮条表而外观质量应符合表6的要求。
表6外观要求
序号部位外观要求
1整体成品窗框亮条形状保持a好,不N冇影响便用的变形
2町视商(装饰而)制品表面应光滑、平整、无裂纹、变形、鼓泡、飞边、毛刺、波纹、疵点、刀痕等缺陷。
3非可视而(即裝®:后看不见的金属部位)允许冇不形响使川功能的轻微缺陷
5.3规格尺寸
5. 3. 1安装尺寸及外形按提供的图纸及三维数模为准。
5.3.2产品的长度尺寸及公差应符合产品图样的有关规定,未注线性尺寸公差按GB/T 1084-2000中粗
糙等级执行。
5.4材料性能5.4.1概述
车门亮条通常由不锈钢或铝合金材料、与橡胶材料(TPV〉、端头、卡扣或金属卡子等组成。
5.4.2 TPV材料性能
TPV材料性能应符合表7中相关规;
表
的材料要求
端头、卡扣和金属卡子要求安装、卡接牢固,不脱落,端头、卡扣材料通常采用POM. PP等,金属
优质惮簧钢(C67S) O材料性能应符合衬相应的材料性能要求。
5.4.4亮条材料性能5. 4. 4. 1不锈钢材料性能
不锈钢材料通常采用牌号为SUS430,厚度为0.5mm。
表而加工类型采用冷轧、光亮退火(BA)表而加工处理,苴材料性能应符合相关要求(特姝要求需供需双方商定在协议及图纸中注明)O
5. 4. 4. 2铝合金材料性能(哑光)
铝合金材料(哑光)通常采用牌号6060,材料性能应符合表8的要求。
铝合金材料性能(高光)
铝合金材料(高亮)通常采用牌号6401,材料性能符合表9的要求。
成品试验性能
5. 5. 1尺寸稳定性
尺寸符合设il •图纸要求。
5.5.2热空气老化性能
无变形、裂纹、粉化、颜色变化、尺寸变化及其他不良后果。
5.5.3耐盐雾性
试验后产品表而应无裂纹、起泡、锈蚀、白点等不良现象。
5.5.4耐溶剂性
试验后产品无溶胀、变色、发粘等现象,色牢度等级不小于4级。
5. 5. 5耐温度循环性
试验后产品表而无变形、龟裂、表而褪色、喷霜、粘结、气泡等。
5.5.6铝合金氧化膜耐碱性
试验后抛光棉和工业用擦亮剂或镁氧化物擦干水分,表而没有裂纹、腐蚀点及可见的浸渍线。
5.5.7铝合金氧化膜耐温度性
试验后无抛光线线、裂纹或英他检査可视的表面裂纹。
5.5.8污染性
成品件在供货状态无不良气味3
6成品试验方法
6.1尺寸稳定性试验6.1.1断面形状
若非特別说明,采用放大投影的方法进行断而形状的测量。
自由状态是指挤出断而在未受任何外力下的形状,安装状态是指挤出断而安装到和飯金形状一致的检具上后的形状。
6.1.2长度尺寸
产品必须使用具有相应精度的量具或检具进行测量。
6.2 热空气老化试验
根据GB/T 3512的规定进行气候交变试验。
试样按要求放置结束后,在(23土2)°C环境温度下调节2h
后, 再进行相应的性能试验。
6.3 中性盐雾试验
按GB/T 10125-2012的规世进行试验:盐雾喷射时间240小时.腐蚀液成分:浓度50g/L+5g/L, PH 值6. 5-7.
2.温度35±2匸。
6.4耐溶剂性试验
按GC/T 15-1992中的5. 5. 3. 2的规崔进行试验,擦賦溶液选用车窗晴洗液(45号或35号)。
6.5耐温度循环试验
按GC/T 15-1992的规企进行试验,温度循环顺序为:(90±2)°CX3h, (23 + 2)°CX0. 5h. (-40 + 2)•CX2h. (23 + 2) rxO.Sh,为一次循环,试样经5次循环。
6.6铝合金氧化膜耐碱性试验
把零件浸入18-20 D 由2 g/lXa3Pai 200 mg/l CI-: pH = 12.5+2组成的无铝混合试验液中(PH
值用NaOH和H3P04调整)。
把零件约10cm的阳极氧化表而浸入到试验液中,浸背^约10 min,然后用蒸馅
水洗净,并自然吹"然后进行评价。
6.7铝合金氧化膜耐温度性试验
在+100° C进行1 h试验,氧化层没有肉眼可见的裂纹。