高炉炼铁资料12.1高炉强化冶炼
高炉强化冶炼资料重点

是:燃烧产物煤气量增加;喷吹煤粉气
“高”指入炉矿石含 铁品位要高,焦炭、 烧结矿和球团矿强度 要高,烧结矿的碱度 要高。
王瑞祥
高炉炼铁知识9
6.2 精料
入炉矿含铁品位提高1%,炼铁燃料比降低 2%,产量提高3%,渣量减少30kg/t,允许 多喷煤15 kg/t。
原燃料转鼓强度要高。大高炉对原燃料 的质量要求是高于中小高炉。如宝钢要求 焦炭M40为大于88%,M10为小于6.5%,。
2020年10月28日星期三
王瑞祥
高炉炼铁知识2
6、高炉强化冶炼
在高炉冶炼的诸多矛盾中,炉料和煤气
的相向运动是主要的矛盾,炉料和煤气
的相向运动的存在和发展,影响着其他
矛盾的存在和发展,因此,处理好料和
煤气的矛盾,也就是要调整好料和风的
关系。实践证明,通过改善料柱透气性,
改善煤气流分布,从而降低料柱压差,
保证炉况顺行,是使此矛盾相统一的关
键。由此,普遍采用的高炉强化冶炼的
主要措施有:精料、高风温、富氧鼓风、
喷吹燃料、低硅生铁冶炼以及高寿命炉
衬等。 2020年10月28日星期三
王瑞祥
高炉炼铁知识3
6.1 提高冶炼强度
√
2020年10月28日星期三
王瑞祥
高炉炼铁知识4
6.1 提高冶炼强度
2020年10月28日星期三
王瑞祥
高炉炼铁知识26
6.5 喷吹燃料
2020年10月28日星期三
王瑞祥
高炉炼铁知识27
6.5 喷吹燃料
2020年10月28日星期三
王瑞祥
高炉炼铁知识28
6.5 喷吹燃料
2020年10月28日星期三
王瑞祥
高炉炼铁
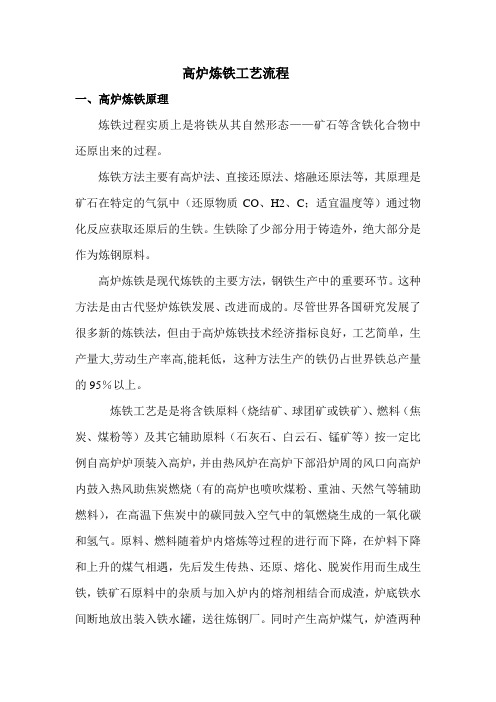
高炉炼铁工艺流程一、高炉炼铁原理炼铁过程实质上是将铁从其自然形态——矿石等含铁化合物中还原出来的过程。
炼铁方法主要有高炉法、直接还原法、熔融还原法等,其原理是矿石在特定的气氛中(还原物质CO、H2、C;适宜温度等)通过物化反应获取还原后的生铁。
生铁除了少部分用于铸造外,绝大部分是作为炼钢原料。
高炉炼铁是现代炼铁的主要方法,钢铁生产中的重要环节。
这种方法是由古代竖炉炼铁发展、改进而成的。
尽管世界各国研究发展了很多新的炼铁法,但由于高炉炼铁技术经济指标良好,工艺简单,生产量大,劳动生产率高,能耗低,这种方法生产的铁仍占世界铁总产量的95%以上。
炼铁工艺是是将含铁原料(烧结矿、球团矿或铁矿)、燃料(焦炭、煤粉等)及其它辅助原料(石灰石、白云石、锰矿等)按一定比例自高炉炉顶装入高炉,并由热风炉在高炉下部沿炉周的风口向高炉内鼓入热风助焦炭燃烧(有的高炉也喷吹煤粉、重油、天然气等辅助燃料),在高温下焦炭中的碳同鼓入空气中的氧燃烧生成的一氧化碳和氢气。
原料、燃料随着炉内熔炼等过程的进行而下降,在炉料下降和上升的煤气相遇,先后发生传热、还原、熔化、脱炭作用而生成生铁,铁矿石原料中的杂质与加入炉内的熔剂相结合而成渣,炉底铁水间断地放出装入铁水罐,送往炼钢厂。
同时产生高炉煤气,炉渣两种副产品,高炉渣铁主要矿石中不还原的杂质和石灰石等熔剂结合生成,自渣口排出后,经水淬处理后全部作为水泥生产原料;产生的煤气从炉顶导出,经除尘后,作为热风炉、加热炉、焦炉、锅炉等的燃料。
二、高炉冶炼主要工艺设备简介高护炼铁设备组成有:①高炉本体;②供料设备;③送风设备;④喷吹设备;⑤煤气处理设备;⑥渣铁处理设备。
通常,辅助系统的建设投资是高炉本体的4~5倍。
生产中,各个系统互相配合、互相制约,形成一个连续的、大规模的高温生产过程。
高炉开炉之后,整个系统必须日以继夜地连续生产,除了计划检修和特殊事故暂时休风外,一般要到一代寿命终了时才停炉。
高炉强化冶炼详解
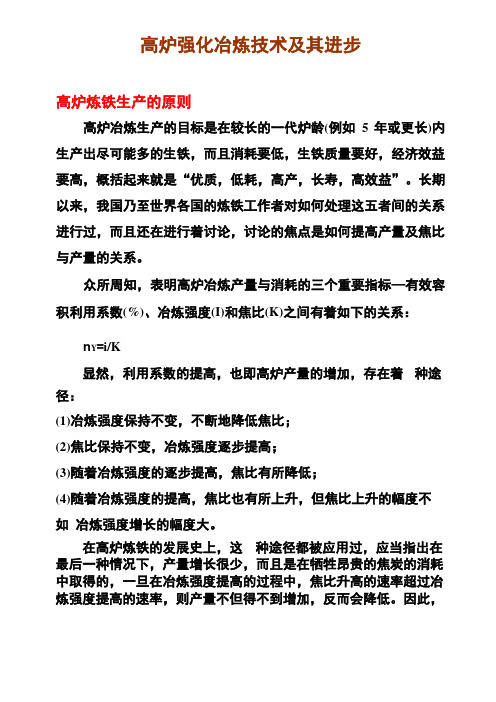
高炉强化冶炼技术及其进步高炉炼铁生产的原则高炉冶炼生产的目标是在较长的一代炉龄(例如5年或更长)内生产出尽可能多的生铁,而且消耗要低,生铁质量要好,经济效益要高,概括起来就是“优质,低耗,高产,长寿,高效益”。
长期以来,我国乃至世界各国的炼铁工作者对如何处理这五者间的关系进行过,而且还在进行着讨论,讨论的焦点是如何提高产量及焦比与产量的关系。
众所周知,表明高炉冶炼产量与消耗的三个重要指标—有效容积利用系数(%)、冶炼强度(I)和焦比(K)之间有着如下的关系:n Y=i/K显然,利用系数的提高,也即高炉产量的增加,存在着种途径:(1)冶炼强度保持不变,不断地降低焦比;(2)焦比保持不变,冶炼强度逐步提高;(3)随着冶炼强度的逐步提高,焦比有所降低;(4)随着冶炼强度的提高,焦比也有所上升,但焦比上升的幅度不如冶炼强度增长的幅度大。
在高炉炼铁的发展史上,这种途径都被应用过,应当指出在最后一种情况下,产量增长很少,而且是在牺牲昂贵的焦炭的消耗中取得的,一旦在冶炼强度提高的过程中,焦比升高的速率超过冶炼强度提高的速率,则产量不但得不到增加,反而会降低。
因此,冶炼强度对焦比的影响,成为高炉冶炼增产的关键。
在高炉冶炼的技术发展过程中,人们通过研究总结出冶炼强度与焦比的关系如图1所示。
图1冶炼强度与产量(I)和焦比(K)的关系美国资料,b 一原西德资料,一前苏联资料在一定的冶炼条件下,存在着一个与最低焦比相对应的最适宜的冶炼强度I适。
当冶炼强度低于或高于I适时,焦比将升高,而产量稍迟后,开始逐渐降低。
这种规律反映了高炉内煤气和炉料两流股间的复杂传热、传质现象。
在冶炼强度很低时,风量及相应产生的煤气量均小,流速低,动压头很小,造成煤气沿炉子截面分布极不均匀,表现为边缘气流过分发展,煤气与矿石不能很好地接触,结果煤气的热能和化学能不能得到充分利用,炉顶煤气中CO,含量低,温度高,而进入高温区的炉料因还原不充分,直接还原发展,消耗了大量宝贵的高温热量,因此焦比很高。
高炉强化冶炼
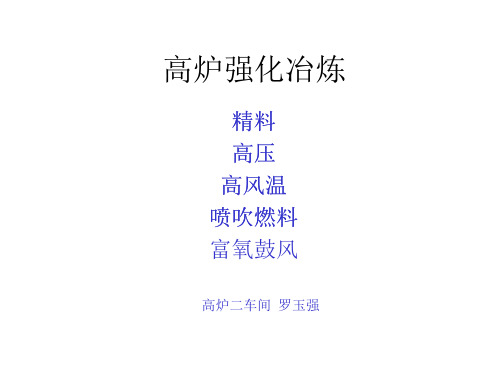
3.提高风温还可加快风口前焦炭的燃烧速度,提高T理,热 量更集中干炉缸,使高温区域下移,中温区域扩大,有利间 接还原发展,直接还原度rd降低。 4.风温的改变也是调剂炉况的重要手段之一。
高炉接受高风温的条件 凡是能降低炉缸燃烧温度和改善料柱透气性的措施,都 有利高炉接受高风温。 1.改善原燃料条件精料是高炉接受高风温的基本条件。只 有原料强度好,粒度组成均匀、粉未少,才能在高温条件下 保持顺行。 2.喷吹的燃料在风口前燃烧时分解、吸热,使理论燃烧温 度降低,高炉容易接受高风温。为了维持风口燃烧区域具有 足够的温度,需要提高风温进行补偿。 3.加湿鼓风时.因水分解吸热要降低理论燃烧温度,相应提 高风温进行热补偿。 4.搞好上下部调剂。保证高炉顺行的情况下才可提高风温。
• • • • • • • • •
(2)高还原性:低FeO、多气孔低温固结型烧结矿 FeO↓1%——K↓1.5%——产量↑1.5% (3)焦炭固定碳含量高:CS = 100 – A – V A↓——焦炭热值↑——渣量↓ (4)熔剂CaO含量高:CaO有效 = CaO – R×SiO2 (5)高强度:冷态强度——转鼓指数 热态强度——烧结矿低温还原粉化RDI 球团矿还原膨胀RSI 焦炭反应性↓ C + CO2 = CO
• (3) 煤气停留时间延长 • 提高炉顶压力,煤气在炉内停留时间延长,有利于还原反 应进行,也有利于焦比降低。 • (4) 有利稳定顺行 • 提高炉顶压力,由于压头损失降低,流速减慢,作用于炉 料的浮力也相应降低,炉料比较容易下降,因而有利于炉 况稳定顺行。 • (5) 除尘器瓦斯灰量减少 • 炉顶压力由常压转为0.08MPa时,炉尘量降了20%~50%, 现代高炉炉顶压力提高到 0.15 ~ 0.25MPa ,炉尘量常低于 10/kg/t。
高炉强化冶炼

→煤气热能、化学能利用不充分
→焦比升高
I> I适时:煤气流速过大
中心过吹或管道行程
△P↑
炉况恶化→焦比↑
适宜冶炼强度和焦比的关系
I适是随冶炼条件的改善不断增大的
1
2
冶炼条件改善
3
焦
比
4
5
适宜的 冶炼强度
各类因素之间关系的分析
1) 产量和消耗之间的关系 2) 效益与产量、消耗之间的关系 3) 产量与高炉寿命、效益之间的关系 4) 产量与质量之间的关系
还原、软化熔融等。
散料堆中的粒度分布情况
炉料性质对布料的影响(A)
炉料的粒度
(不同粒度的混合料)
大块炉料易于滚落到堆角 由于堆角处料层薄,相对透气性好;
小块炉料则多集中在堆尖 由于堆尖处料层厚,相对透气性差。
高炉炉顶装料设备
料车- - 钟式
P·W- -无钟式
影响炉顶装料状况的因素
固定因素 a、布料设备参数 1、布料器形式 2、炉喉高度和直径 3、大钟与炉喉间隙 4、大钟倾角及速度 5、无钟炉顶参数 b、炉料特性
(一般:下部调剂的反应较快)
6.2 高炉操作制度
高炉四大操作制度
装料制度 送风制度 造渣制度 热制度
3) 造渣制度
★ 控制炉渣各种理化性能的总称
包括
熔化温度、粘度、炉渣成分、 熔化滴落区间、 脱硫性、排碱 性、表面性能等
控制造渣过程和终渣性能
6.2 高炉操作制度
高炉四大操作制度
装料制度 送风制度 造渣制度 热制度
高炉炼铁生产的原则
各类因素之间关系的分析
1) 产量和消耗之间的关系 2) 效益与产量、消耗之间的关系 3) 产量与高炉寿命、效益之间的关系 4) 产量与质量之间的关系
高炉炼铁

3.用固体C还原
高炉冶炼特点
1.高炉冶炼是在炉料与煤气流的逆向运动 过程中完成各种复杂的化学反应和物理变 化,反应气氛是还原性气氛; 2.高炉是一个密闭容器,除了装料、出铁、 出渣以及煤气以外,操作人员都无法直接 观察到反应过程的状况,只能凭借仪器间 接观察; 3.高炉生产过程是连续的,大规模的高温 生产过程,机械化和自动化水平较高。
燃料燃烧反应 铁矿石还原反应(铁氧化物) 非铁元素还原(Si,Mn,等) 造渣过程 生铁生成
A、燃烧反应
放热 燃烧 产生高温还原气体CO 在高炉下部形成空间, 保证炉料持续下降 直接还原(参与化学还原) 溶入生铁(铁水中含有一定量C)
焦炭 (主要燃料)
燃料的燃烧是高炉的热能和化学能的发源 地,决定了炉内煤气流,温度和热量的初始 分布,对高炉生产起着至关重要的作用!
1.钢筋混凝土 2.耐火砖 3.冷却壁 4.水冷管
5.炉壳
冷却设备
支梁式水箱 A—铸管式 B—隔板式
扁水箱 (铸钢)
炉腹、炉腰、炉身下部:冷却壁
炉缸和炉底周围:光板式冷却壁(紫铜冷却壁)
风口:冷却套
1.风口 2.风口二套 3.风口大套 4.直吹管 5.弯管 6.固 定弯管 7.围管 8.短管 9.带有窥视孔的弯管 10.拉杆 11.炉壳
B、还原反应
铁氧化物的还原
1.铁氧化物的还原条件 还原反应通式: MeO+B=Me+BO B:还原剂 Me:某种金属 要使反应能够进行,则: Me O B
还原剂B与O的化学亲和力 > Me与O的化学亲和力 在高炉冶炼过程中,满足条件的还原剂是CO和C,还 有少量的H2也参与还原
二.铁氧化物的还原顺序
焦炭在风口发生燃烧反应: C+O2 =CO2 +33356kJ/kg + C+CO2 =2CO -13794kJ/kg 2C+O2 =2CO +9781kJ/kg
高炉炼铁工艺介绍

高炉炼铁工艺介绍1. 简介高炉炼铁是一种重要的冶金工艺,用于将铁矿石转化为生铁的过程。
它是钢铁工业的核心环节之一,用于生产各种钢材。
2. 高炉炼铁的基本原理高炉炼铁的基本原理是将铁矿石与焦炭等还原剂混合后,在高温下进行还原反应,将铁矿石中的氧化铁还原为金属铁。
同时,炉内的温度和化学反应条件还可以使一部分其他有害物质被除去。
3. 高炉炼铁的工艺流程3.1 高炉炉缸高炉炉缸是高炉的主要部分,通常由炉壳、炉缸和炉缸衬板组成。
炉缸衬板由耐火材料制成,以承受高温和化学侵蚀。
3.2 上料系统上料系统的主要作用是将矿石、焦炭、燃料及其他辅助材料送入高炉。
通常,这些原料需要经过破碎、筛分、称重等处理。
3.3 炉冰炉冰是指在高炉顶部装置的冷却设备,用于冷却进入高炉的热气体。
这样可以减少热能的损失,并为高炉提供所需的煤气流动动力。
3.4 高炉通气系统高炉通气系统主要包括风机和风口。
高炉顶部的风机通过送风管将空气送入高炉,从而维持高炉的氧气供应。
风口是位于炉缸底部的通气装置,用于引入煤气和空气,同时也是控制和调节高炉燃烧的关键。
3.5 高炉冷却系统高炉冷却系统主要用于冷却高炉的各个部位,包括炉缸、炉壁和炉顶。
这些部位会受到高温的侵蚀,而冷却系统可以降低温度,延长高炉使用寿命。
3.6 出铁系统出铁系统用于从高炉底部将生铁和渣铁分离出来。
通常通过出铁口将液态金属铁和渣铁分别引出,然后进一步处理。
3.7 气体处理系统高炉产生的煤气会通过气体处理系统进行处理。
其中一种常见的处理方法是将煤气用作燃料,同时采用高炉煤气洗涤的方式除去其中的尘埃和硫化物等有害物质。
4. 高炉炼铁的优缺点4.1 优点•高炉炼铁工艺稳定,适合大规模生产。
•可以利用多种铁矿石和煤炭,适应不同的原料条件。
•高炉炼铁可以同时除去一部分有害物质,对环境保护有一定的效果。
4.2 缺点•高炉炼铁能耗较高,对资源消耗较大。
•高炉炼铁产生的煤气和废渣需要进一步处理,处理过程中会产生一定的环境污染物。
高炉强化冶炼的手段
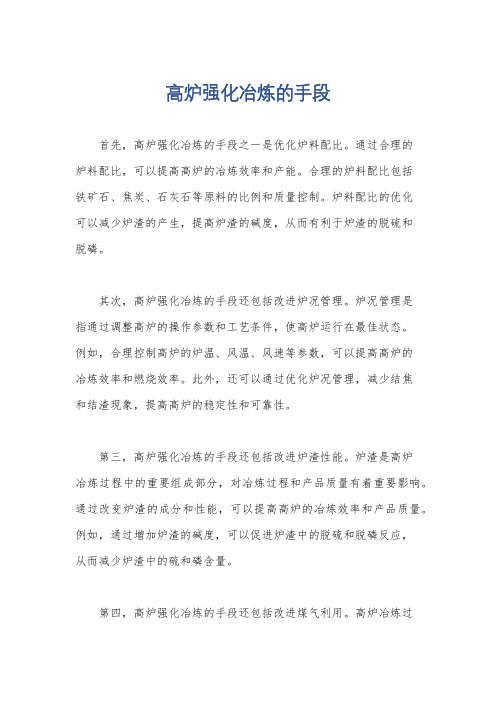
高炉强化冶炼的手段首先,高炉强化冶炼的手段之一是优化炉料配比。
通过合理的炉料配比,可以提高高炉的冶炼效率和产能。
合理的炉料配比包括铁矿石、焦炭、石灰石等原料的比例和质量控制。
炉料配比的优化可以减少炉渣的产生,提高炉渣的碱度,从而有利于炉渣的脱硫和脱磷。
其次,高炉强化冶炼的手段还包括改进炉况管理。
炉况管理是指通过调整高炉的操作参数和工艺条件,使高炉运行在最佳状态。
例如,合理控制高炉的炉温、风温、风速等参数,可以提高高炉的冶炼效率和燃烧效率。
此外,还可以通过优化炉况管理,减少结焦和结渣现象,提高高炉的稳定性和可靠性。
第三,高炉强化冶炼的手段还包括改进炉渣性能。
炉渣是高炉冶炼过程中的重要组成部分,对冶炼过程和产品质量有着重要影响。
通过改变炉渣的成分和性能,可以提高高炉的冶炼效率和产品质量。
例如,通过增加炉渣的碱度,可以促进炉渣中的脱硫和脱磷反应,从而减少炉渣中的硫和磷含量。
第四,高炉强化冶炼的手段还包括改进煤气利用。
高炉冶炼过程中产生的煤气含有可利用的热能和化学能。
通过改进煤气的利用方式,可以提高高炉的能源利用效率。
例如,可以采用煤气发电、煤气热解等技术,将煤气中的能源转化为电能或其他形式的能源,提高能源利用效率。
最后,高炉强化冶炼的手段还包括改进炉外工艺。
炉外工艺是指高炉冶炼过程中与高炉相配套的其他工艺环节。
通过改进炉外工艺,可以提高高炉的冶炼效率和产品质量。
例如,可以改进铁矿石的预处理工艺,提高铁矿石的还原性能;可以改进炼铁工艺,提高铁水的质量和纯度。
综上所述,高炉强化冶炼的手段包括优化炉料配比、改进炉况管理、改进炉渣性能、改进煤气利用和改进炉外工艺等多个方面。
这些手段可以提高高炉的冶炼效率和产品质量,实现高炉的强化冶炼。
高炉炼铁

高炉炼铁高炉gaolu liantie高炉炼铁blast furnace ironmaking现代炼铁的主要方法,钢铁生产中的重要环节。
这种方法是由古代竖炉炼铁发展、改进而成的。
尽管世界各国研究发展了很多新的炼铁法,但由于高炉炼铁技术经济指标良好,工艺简单,生产量大,劳动生产率高,能耗低,这种方法生产的铁仍占世界铁总产量的95%以上。
高炉生产时从炉顶装入铁矿石、焦炭、造渣用熔剂(石灰石),从位于炉子下部沿炉周的风口吹入经预热的空气。
在高温下焦炭(有的高炉也喷吹煤粉、重油、天然气等辅助燃料)中的碳同鼓入空气中的氧燃烧生成的一氧化碳和氢气,在炉内上升过程中除去铁矿石中的氧,从而还原得到铁。
炼出的铁水从铁口放出。
铁矿石中不还原的杂质和石灰石等熔剂结合生成炉渣,从渣口排出。
产生的煤气从炉顶导出,经除尘后,作为热风炉、加热炉、焦炉、锅炉等的燃料。
简史和近况早期高炉使用木炭或煤作燃料,18世纪改用焦炭,19世纪中叶改冷风为热风(见冶金史)。
20世纪初高炉使用煤气内燃机式和蒸汽涡轮式鼓风机后,高炉炼铁得到迅速发展。
20世纪初美国的大型高炉日产生铁量达450吨,焦比1000公斤/吨生铁左右。
70年代初,日本建成4197米高炉,日产生铁超过1万吨,燃料比低于500公斤/吨生铁。
中国在清朝末年开始发展现代钢铁工业。
1890年开始筹建汉阳铁厂,1号高炉(248米,日产铁100吨)于1894年5月投产。
1908年组成包括大冶铁矿和萍乡煤矿的汉冶萍公司。
1980年,中国高炉总容积约8万米,其中1000米以上的26座。
1980年全国产铁3802万吨,居世界第四位。
[主要产铁国家产量和技术经济指标]70年代末全世界2000米以上高炉已超过120座,其中日本占1/3,中国有四座。
全世界4000米以上高炉已超过20座,其中日本15座,中国有1座在建设中。
50年代以来,中国钢铁工业发展较快,高炉炼铁技术也有很大发展,主要表现在:①综合采用精料、上下部调剂、高压炉顶、高风温、富氧鼓风、喷吹辅助燃料(煤粉和重油等)等强化冶炼和节约能耗新技术,特别在喷吹煤粉上有独到之处。
高炉冶炼的基本过程

03
CHAPTER
高炉冶炼过程
炉料装填与送风
炉料装填
将焦炭、矿石、熔剂等原料按照一定比例装入高炉炉膛内,形成炉料柱。
送风
通过鼓风机将空气送入高炉风口,与炉料中的焦炭发生反应,产生热量和还原气。
燃烧过程与还原反应
要点一
燃烧过程
空气中的氧气与焦炭反应,产生高温和还原气(一氧化碳 和氢气)。
要点二
还原反应
鼓风温度
根据高炉内温度和生铁成分要求,调 整鼓风温度,以控制高炉内的热量平 衡和化学反应。
鼓风湿度
合理控制鼓风湿度,有助于调节高炉 内气氛和减少焦炭消耗。
炉渣碱度
通过调整炉渣碱度,可以优化生铁成 分和降低有害杂质,提高生铁质量。
高炉内温度与压力的控制
温度控制
通过调节鼓风温度和焦炭比例等参数,控制高炉内温度在适宜范围内,以保证化学反应 顺利进行和降低能耗。
压力控制
维持高炉内压力稳定,防止外界空气进入炉内,保证高炉安全运行和生铁质量的稳定。
高炉内气氛的控制
CO浓度控制
通过调节鼓风流量和焦炭比例等参数,控制 高炉内CO浓度在适宜范围内,以促进化学 反应的进行和提高生铁产量。
O2浓度控制
合理控制高炉内O2浓度,有助于调节高炉 内气氛和减少焦炭消耗,提高生铁质量。
原料准备
铁矿石的选取与处理
铁矿石的选取
根据高炉冶炼的要求,选择品位高、 成分稳定、含有害杂质少的铁矿石。 常见的铁矿石有赤铁矿、磁铁矿和褐 铁矿等。
铁矿石的处理
将铁矿石破碎、筛分和磨细,以减小 颗粒度,提高其反应活性。同时,根 据需要加入适量的熔剂,以调整炉渣 的成分和性质。
焦炭的选取与处理
焦炭的选取
高炉强化冶炼
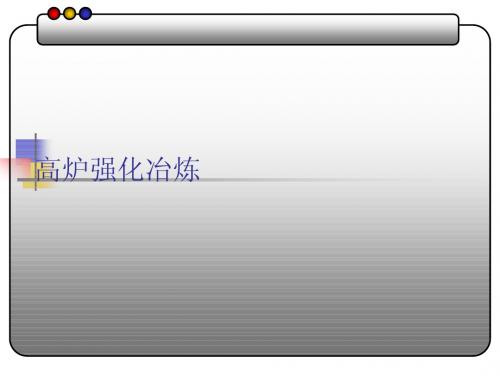
高炉强化冶炼
3、提高热风温度 、
提高热风温度是降低焦比和强化高炉冶炼的重要措施。 采用喷吹技术之后,使用高风温更为迫切。高风温能为提高 喷吹量和喷吹效率创造条件。据统计,风温在950~1350℃ 之间,每提高100 ℃可降低焦比8~20kg ,增加产量2~3%。 当前我国大高炉平均风温在1050~1100 ℃ ,先进高炉可 达1200 ℃,国外高炉风温水平达1300~1350 ℃,日本高炉 1200 1300 1350 的燃料比,1955~1979年间降低了 253kg/t,其中提高风温 的因素占31%。据资料,风温由1000℃提高到1250 ℃ ,焦 比降低22. 5kg/t,增产12.5%。 目前采用高风温已经不是高炉能否接受的问题,而是如何 能提供更高的风温。
“稳” 是指各种原料的化学成分稳定、波 高炉强化冶炼 动小。这是稳定炉况、实现自动控制的先 决条件。
“熟” 是指高炉全部装入烧结矿和球团矿, 熟料率达到100%,尽量不加石灰石入炉。 “小、匀、净” 是对原料的粒度而言。 综上所述,精料对矿石来说,关键是要使
高炉强化冶炼
2、高压操作
提高炉顶煤气压力的操作称为高压操作, 是相对于常压操作而言的。一般常压高 炉炉顶压力(表压)低于30kPa,凡炉顶压 力超过此值者,均为高压操作。它是通 过安装在高炉煤气除尘系统管道上的高 压调节阀组,改变煤气通道截面积,使 其比常压时为小,从而提高炉顶煤气压 力的。由于炉顶压力提高,高炉内部各
高炉强化冶炼
高压操作使炉尘吹出量显著减少, 单位矿石消耗降低,实际焦炭负荷得到 保证,批料出铁量增加,铁的回收率提 高,焦比应有所降低。实践证明,实行 高压操作,不断提高炉顶压力水平,是 强化高炉冶炼,增产节能的一条重要途 径。根据国内外经验,1000m3级高炉, 炉顶压力应达到120kPa左右;2000m3级 高炉,应达到150kPa以上; 3000m3级 高炉,应达到200kPa左右;4000m3级以
高炉炼铁基本原理及工艺

2、焦比 : K=Q(昼夜焦碳用量)/P(现主要核算综合 焦比)
3、冶炼强度: I=Q/Vu (反应焦碳的燃烧能力)
4、透气性指数: K 5、炉腹煤气指数:
PB2 PT2
X
V 1.7 BG
BG
4VBG
D2
4、休风率:计划外的检修时间占规定作业时间的百
分比(≤2%)
5、生铁成本:原料占80%±
6、一代炉龄:高炉点火开炉→停炉大修历经时间
48.2
30~40
25
P,S↓熔烧
后易还原
精品课件
5
各类铁矿石图
磁铁矿
褐铁矿
赤铁矿
精品课件
菱铁矿
6
烧结矿及烧结球团
烧结矿
精品课件
烧结球团
7
⑴品位:含铁量,理论上品位↑1%,焦
比↓2%,产量↑ 3%
⑵脉石成分:SiO2、Al2O3↓越好(须重
视Al2O3 ),MgO ↑越好
⑶有害杂质:S、P、Cu、Pb、Zn、As
(5)炉缸区:渣铁分层存在,焦碳浸泡其中 主要反应: 渣铁间脱S,Si、Mn等元素氧化还原
精品课件
15
2.铁的间接还原与直接还原
(1)间接还原:用CO、H2为还原剂还原铁的氧化物,产物CO2、 H2O的还原反应。 特点:放热反应 反应可逆
(2)直接还原:用C作为还原剂,最终气体产物为CO的还原反应。 特点:强吸热反应 反应不可逆
精品课件
26
Thank you!
精品课件
27
1000 ℃间还) →MnO→(1200 ℃直接还原)→Mn
②Mn还原的特点:间接还原放热大,使炉顶温度↑ 直接还原吸热大,使焦比↑
③控制Mn还原的手段:提高炉缸温度,但会使Mn的挥发损失↑ 提高炉渣R 生铁中保持一定[Si]
高炉炼铁工艺及强化操作

高炉炼铁工艺及强化操作高炉炼铁是指利用高炉将铁矿石还原成铁的工艺。
下面将介绍高炉炼铁的工艺流程和强化操作。
首先是炉料准备。
炉料是指进入高炉的原料,主要包括铁矿石、燃料和熔剂。
铁矿石是炼铁的主要原料,有各种类型,如富含铁的赤铁矿、磁铁矿等。
燃料主要是焦炭,用于提供炉内的热量。
熔剂主要是石灰石,用于与铁矿石中的杂质产生反应,形成易于熔融的铁渣。
然后是炉顶喂料。
炉顶喂料是将炉料逐层从高炉顶部加入,以保持炉内的物料平衡。
铁矿石、焦炭和石灰石按照一定比例加入到高炉顶部,同时还需要加入一定量的还原剂、燃料和助熔剂。
炉料从高炉顶部逐层往下加入,以确保炉内的物料层结构稳定。
然后是高炉操作。
高炉操作是指控制高炉正常运行的一系列操作。
首先是通风。
高炉顶部设有风管,通过风管送入燃料燃烧所需的氧气,维持炉内的高温。
其次是给料。
在正常运行过程中,需要不断地给炉料补料,保持高炉内的物料平衡。
还有是温度和压力的控制。
高炉内的温度和压力需要进行实时监测,以保持高炉内部的平衡状态。
接下来是铁渣处理。
高炉炼铁过程中,铁矿石中的杂质会与熔剂反应形成铁渣。
铁渣是高炉炼铁的副产物,需要进行处理。
铁渣处理主要包括根据铁渣的性质进行分选和利用。
铁渣中的铁石可以回收利用,用于生产水泥等建筑材料。
而其他杂质则需要通过石灰石的熔融和化学反应,形成不溶于炉渣的物质,进一步净化炉渣。
最后是产品收得。
通过高炉炼铁,最终产生的产品是生铁。
生铁是铁矿石还原后的产物,含有较高的碳含量和一些杂质。
生铁需要进行进一步的加工和处理,使其达到市场上的要求。
加工过程中,可以采用转炉炼钢或电炉炼钢技术,将生铁中的杂质进一步去除,得到优质的钢铁产品。
为了提高高炉炼铁的效率和质量,还有一些强化操作可以应用。
比如,在炉料准备过程中,可以根据铁矿石的性质进行选矿和破碎处理,以提高炉内的还原反应速率。
另外,可以在炉顶喂料过程中,适当控制喂料速度和炉料的层次,以保持高炉内的平衡状态。
高炉强化冶炼1
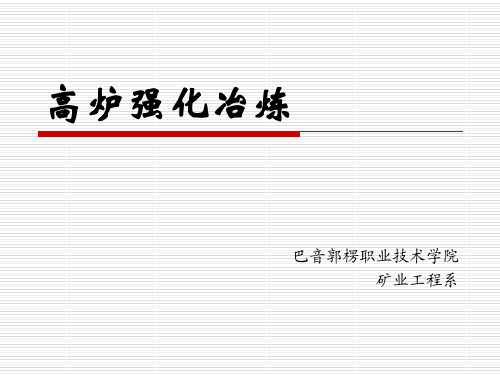
高风温与降低焦比的关系
高风温降低焦比的原因 (1)风温带入的物理热,减少了作为发热 剂所消耗的焦炭,因而可使焦比降低。 (2)风温提高后焦比降低,使单位生铁生 成的煤气量减少,炉顶煤气温度降低,煤气 带走的热量减少,因而可使焦比进一步降低。 (3)提高风温后,因焦比降低煤气量减少, 高温区下移,中温区扩大、增加间接还原, 减少直接还原,有利于焦比降低。
我国高炉炼铁在近几年来取得了很大的进步, 冶炼强度在中小型高炉上超过了1.5 t/(m3d),大高炉上也达到了 1.1t/(m3d)以上,利用系数相应达到 3.5 t/(m3d)以上和2.3 t/(m3d)以 上,燃料比降到530 kg/t和500 kg/t左 右。这是由于采取了所谓强化高炉冶炼技术 的结果。这些技术包括精料技术、高风温技 术、高压操作技术、喷吹燃料技术、富氧大 喷煤技术、先进的计算机控制技术等。
鼓风含氧按下式计算: 鼓风含氧=大气中含氧+富氧率 式中,鼓风含氧的单位为%;大气中含氧一 般取21%;富氧率按下式计算: 富氧率=富氧量/(风量+富氧量) 式中,富氧率的单位为%;富氧量的单位为 m3/min;风量的单位为m3/min,或以 吨铁所用的风量和吨铁耗的氧气量为单位计 算。
高风温与降பைடு நூலகம்焦比的关系
高风温降低焦比的原因 (4)由于风温提高焦比降低,产量相应提 高,单位生铁热损失减少。 (5)风温升高,炉缸温度升高,炉缸热量 收入增多,可以加大喷吹燃料数量,更有利 于降低焦比。
高风温与降低焦比的关系
高风温降低焦比的效果 风温水平不同,提高风温的节焦效果也不相 同。风温愈低,降低焦比的效果愈明显,相 反,风温水平愈高,增加相同的风温所节约 的焦炭减少。 对于焦比高、风温偏低的高炉,提高风温后 其效果更大。风温水平已经较高 (1200℃~1300 ℃)时,再提高风温的作 用减小。
高炉炼铁的所有知识点总结

高炉炼铁的所有知识点总结一、高炉炼铁的工艺过程高炉炼铁的主要工艺过程包括铁矿石的预处理、还原反应、炼铁反应和产物的分离和收集等步骤。
1. 预处理铁矿石通常是氧化铁矿石,例如赤铁矿、磁铁矿、褐铁矿等。
在高炉炼铁之前,需要对铁矿石进行预处理,主要包括破碎、煅烧和粉碎等步骤。
首先,铁矿石需要经过破碎设备进行破碎,将其破碎成较小的颗粒。
然后,将破碎后的铁矿石进行煅烧,通常是在煤气或焦炉中进行,将氧化铁矿石还原成较高的还原度。
最后,将煅烧后的铁矿石进行粉碎,使其达到适当的颗粒度,以便于高炉内的还原反应。
2. 还原反应高炉炼铁的核心工艺是还原反应。
在高炉内,煅烧后的铁矿石与焦炭共同投入高炉,并通过热炭气、空气和热风等途径,使焦炭在高炉内发生燃烧,产生大量的一氧化碳和二氧化碳等气体。
这些气体与煅烧后的铁矿石发生还原反应,使氧化铁矿石还原成金属铁。
还原反应的主要化学反应式为Fe2O3 + 3CO = 2Fe + 3CO2。
在此过程中,还将生成一些硅、锰等元素的还原物金属。
3. 炼铁反应在还原反应之后,得到的金属铁流向高炉底部,与炉渣和热铁水的反应产生炼铁反应。
炼铁反应的目的是提高生铁的品质,并去除炉渣中的杂质。
在炼铁反应中,金属铁与炉渣中的碱金属、碳酸盐等发生反应,使炉渣脱碱和夺碳,并将少量的氧、碳等被夹杂在金属铁中的杂质除去。
4. 产物的分离和收集最后,通过高炉的底部出口,生铁和炉渣被分离出来。
生铁被收集起来,经过冷却、成型和质量检验等步骤,最终被用于钢铁冶炼。
炉渣则被收集起来,并用于建筑材料、道路铺设等领域。
以上就是高炉炼铁的工艺过程,我们可以看到,高炉炼铁的工艺过程是一个复杂的化学反应过程,需要严格控制反应条件和工艺参数,以确保生铁的品质和产量。
二、高炉炼铁的原料高炉炼铁的主要原料包括铁矿石、焦炭和石灰石等。
1. 铁矿石铁矿石是高炉炼铁的主要原料,通常是氧化铁矿石。
常见的铁矿石有赤铁矿、磁铁矿、褐铁矿等。
高炉冶炼技术详解

汇报人:可编辑 2024-01-06
目录
CONTENTS
• 高炉冶炼技术概述 • 高炉冶炼工艺流程 • 高炉冶炼设备与操作 • 高炉冶炼技术优化与改进 • 高炉冶炼技术应用与案例分析
01
CHAPTER
高炉冶炼技术概述
高炉冶炼的定义与原理
定义
高炉冶炼是一种将铁矿石、焦炭 和熔剂在高炉内高温条件下还原 成生铁的冶金过程。
高炉冶炼技术的现状与趋势
现状
高炉仍是钢铁生产的主要方式,但面 临环保、能源消耗等方面的挑战。
趋势
高炉节能减排、低碳化、智能化等技 术的发展,以及新型熔融还原技术的 探索和应用。
02
CHAPTER
高炉冶炼工艺流程
原料准备
原料准备
高炉冶炼的原料主要包括铁矿 石、熔剂和燃料。在准备原料 时,需要确保其质量和供应的
高炉冶炼技术在有色金属行业的应用
有色金属行业也是高炉冶炼技术的应用领域之一,通过高炉冶炼可以提取铜、镍、钴等有色金属。
在有色金属行业中,高炉冶炼技术需要针对不同金属的特性进行工艺调整,以实现金属的高效提取和 分离。
高炉冶炼技术应用案例分析
某钢铁企业采用高炉冶炼技术,通过优化工艺参数和原料配比,实现了高效、低耗的生产目标,提高了产品质量和市场竞争 力。
供料系统
供料系统是高炉冶炼的重要环节之一 ,主要负责将原料按照一定的比例和 顺序加入高炉。
供料系统通常包括原料储存、原料输 送、原料称重和原料加入等设备,这 些设备需要精确控制原料的配比和加 入量,以保证高炉冶炼的顺利进行。
送风系统
送风系统是高炉冶炼的关键环节之一,主要负责向高炉内送 入空气或氧气。
03
CHAPTER
炼铁原理与工艺13(强化冶炼)

13.1高炉高压操作
高压操作的条件是: (1)鼓风机要有满足高压操作的压力,保证 在高压操作下能向高炉供应足够的风量。 (2)高炉及整个炉顶煤气系统和送风系统必 须保证可靠的密封及足够的强度,以满足高 压操作的要求。
13.1高炉高压操作
高压高炉的特点是: (1)强化冶炼进程,提高产量。增加0.1kg/cm2约 提高产量3%. (2)在一定程度上可降低焦炭消耗。减少了气化反应。 (3)降低炉尘吹出量。减少管道。有利于炉况顺行。 (4)可以回收能量。采用炉顶余压发电,顶压越高发 电量越多。 (5)高压以后,对硅的还原不利(抑制了硅还原反 应),而强化了渗碳过程,所以高压有利于低硅生 铁的冶炼。
13.1高炉高压操作
高压高炉的操作特点 : (1)常压转高压操作的条件 (2)高压操作时需加重边沿 (3)高压操作高炉炉内压差变化 (4)高压高炉处理悬料的特点
13.1高炉高压操作
高压操作注意事项 (1)高、常压转换会引起煤气流分布的变化, 所以转换操作应缓慢进行,以免损坏设备和 引起炉况不顺。 (2)转高压后一般会导致边缘气流发展,要 视情况相应调整装料制度与送风制度。 (3)处理悬料,首先要改常压,然后放风坐 料。严禁在高压下强迫放风坐料。
13.6高炉检测技术和计算机控制的认知
1. 高炉检测新技术 ① 激光测料面技术 ② 高炉料面红外摄像技术 ③ 光导纤维检测技术:用光导纤维观测仪观察高炉 内矿石、焦炭反应情况,渣、铁形成过程及炉衬 破损情况等。 ④ 料层测定磁力仪 ⑤ 用来测试矿石层与焦炭层的厚度及其界面移动情 况。 ⑥ 同位素测定炉料下行速度
13.高炉强化冶炼
高炉高压操作 高风温操作 富氧操作
13.高炉强化冶炼 提高高炉利用系数的途径分析
高炉炼铁概述课件

高炉炼铁作为工业生产的重要环节,必须遵守国家和地方的 环保法规,严格控制污染物排放,确保生产过程中的环保合 规性。
环保措施
为满足环保要求,高炉炼铁企业应采取一系列环保措施,如 安装除尘、脱硫、脱硝等环保设施,对生产过程中的废气、 废水、废渣进行治理和回收利用,降低对环境的影响。
高炉炼铁节能减排技术
02
高炉炼铁原料
铁矿石的种类与选择
赤铁矿(Hematite)
赤铁矿是高炉炼铁最常用的铁矿石,具有 较高的铁含量和相对较低的杂质元素。
磁铁矿(Magnetite)
磁铁矿是一种具有磁性的铁矿石,其含铁 量较高,但杂质元素也相对较高。
褐铁矿(Limonite)
褐铁矿是一种含水较多的铁矿石,含铁量 较低,但杂质元素较少。
排渣设备
高炉出铁时,控制出铁口开启和关闭 的设备。
将高炉渣排出的设备,如冲渣机、排 渣机等。
渣铁处理设备
对高炉渣铁进行处理的设备,如渣罐、 铁罐等。
04
高炉炼铁操作与控制
高炉开炉与停炉操作
准备阶段
检查高炉及其周围设备,确保安 全无隐患;准备充足的原料和燃 料;对高炉进行预热。
启动阶段
点燃焦炭,开始加热高炉;控制 加热速度,确保高炉均匀受热; 逐步增加焦炭和铁矿石的投入量。
萤石(Fluorite)
萤石是一种具有较低熔点的矿物,在高炉炼铁中主要用作助 熔剂,帮助降低渣的熔点,提高流动性。
其他辅助原料
碎焦
碎焦是焦炭在运输和装卸过程中产生的碎料,可以作为高炉炼铁的辅助原料,提供热量和还原剂。
煤粉
煤粉可以作为高炉炼铁的辅助燃料,提供热量和还原剂,同时也可以替代部分焦炭。
膨润土
高炉炼铁概述课件
高炉炼铁工艺及强化操作共111页文档

高炉炼铁工艺及强化操作
谢谢你的阅读
❖ 知识就是财富 ❖ 丰富你的人生
71、既然我已经踏上这条道路,那么,任何东西都不应妨碍我沿着这条路走下去。——康德 72、家庭成为快乐的种子在外也不致成为障碍物但在旅行之际却是夜间的伴侣。——西塞罗 73、坚持意志伟大的事业需要始终不渝的精神。——伏尔泰 74、路漫漫其修道远,吾将上下而求索。——屈原 75、内外相应,言行相称。——韩非
- 1、下载文档前请自行甄别文档内容的完整性,平台不提供额外的编辑、内容补充、找答案等附加服务。
- 2、"仅部分预览"的文档,不可在线预览部分如存在完整性等问题,可反馈申请退款(可完整预览的文档不适用该条件!)。
- 3、如文档侵犯您的权益,请联系客服反馈,我们会尽快为您处理(人工客服工作时间:9:00-18:30)。
[课堂小结]
1、高炉强化冶炼的基本途径和方针; 2、高炉强化冶炼的主要措施;
产量
x
量
焦
比
I适
I
对一个实际高炉而言 存在与最低焦比相适宜的冶炼强度I适
12.1.4高强度冶炼的操作特点和技术措施
1.操作特点 (1)扩大料批 (2)增加倒装比例。 (3)适当提高料线。 (4)扩大风口直径或缩短风口伸入炉内的长度。
2.技术措施
·采用新技术
文
文
·设计合理炉型
文
文
字
字
字
字
文
文
文
文
字
·改善原料
字
字
字
·及时放好渣铁
实践证明,通过改善料柱透气性,改善煤气流分布,从而降低料柱 压差△P,保证炉况顺行,是达到高炉强化冶炼的的关键。
高炉强化冶炼主要措施有:精料、高压操作、高风温、富氧鼓风、 喷吹燃料、低硅生铁冶炼以及高寿命炉衬等。这些措施的使用大大强 化了高炉冶炼,促进了炼铁生产工艺的进步。
5
为了使高炉产量↑有4种途径: ηv = I / K
☆ I不变,K↓ ☆ K不变,I↑ ☆ 随I↑,K有所↓ ☆ 随I↑,K有所↑(一般不采用)
6
2)产量与高炉寿命、效益之间的关系
产量↑↑,意味着冶炼强度 I ↑↑ 高炉设备的寿命↓ → 修理费用↑ → 效益↓
故提高一代高炉寿命是很重要的
提高高炉寿命的对策
高炉炼铁技术
项目12 ---- 高炉强化冶炼
任务12.1高炉强化冶炼的基本途径
[学习任务]
•分析高炉强 化冶炼的基本 途径及影响因 素
•分析提高冶 炼强度对高炉 冶炼进程的影 响
•高强度冶炼 的操作特点和 技术措施
12.1.1高炉强化冶炼的基本途径
高炉强化冶炼 定义:
在保证高炉的顺行基础上,使高炉在单位时间内能鼓入 更多的风量(氧量),提高冶炼强度,以便获得高的利用 系数和低的焦比。
• (2)增加下料速度。下料速度加快,单位时间 内燃烧的焦炭增多。
• (3)加大燃烧强度。燃烧强度是指每小时每平 方米炉缸截面积燃烧的焦炭量。
12.1.3提高冶炼强度对高炉冶炼进程的影响
I适是随冶炼条件的改善不断增大的
1
焦
2 3
冶炼条件改善
比
4
5
适宜的 冶炼强度
冶炼强度和焦比之间的关系
焦比
Ima 产
1、采用高质量炉衬(碳砖、碳化硅砖等) 2、改进高炉冷却设备和采取先进的冷却技术 3、采用钒钛炉渣护炉技术 4、提高高炉的操作水平
3、产量与质量之间的关系
铁水质量的主要指标 • 铁水含硫 • 铁水温度
I过高时,炉料停留时间↓
脱硫反应能力↓ 加热不充分
[S] ↑ T铁↓
9
12.1.2提高冶炼强度
• (1)增加入炉风量。增加高炉每分钟鼓入的风 量,高炉燃烧焦炭越多,即冶炼强度越高。
目的:提高产量,即提高高炉利用系数。
• 提要:高炉利用系数 I K
• √1、高炉强化冶炼两种途径: 1)提高冶炼强度, 2)降低焦比。
• √ 2、强化冶炼的基本方针:高产、优质、低耗、长寿、安 全与环保
各类因素之间关系的分析
1、 产量和消耗之间的关系 2、 产量与高炉寿命、效益之间的关系 3、产量与质量之间的关系