热处理变形
热处理变形的原因

热处理变形的原因在实际生产中,热处理变形给后续工序,特别是机械加工增加了很多困难,影响了生产效率,因变形过大而导致报废,增加了成本。
变形是热处理比较难以解决的问题,要完全不变形是不可能的,一般是把变形量控制在一定范围内。
一、热处理变形产生的原因钢在热处理的加热、冷却过程中可能会产生变形,甚至开裂,其原因是由于淬火应力的存在。
淬火应力分为热应力和组织应力两种。
由于热应力和组织应力作用,使热处理后零件产生不同残留应力,可能引起变形。
当应力大于材料的屈服强度时变形就会产生,因此,淬火变形还与钢的屈服强度有关,材料塑性变形抗力越大,其变形程度越小。
1.热应力在加热和冷却时由于零件表里有温差存在造成热胀冷缩的不一致而产生热应力。
零件由高温冷却时表面散热快,温度低于心部,因此表面比心部有更大的体积收缩倾向,但受心部阻碍而使表面受拉应力,而心部则受压应力。
表里温差增大应力也增大。
2.组织应力组织应力是因为奥氏体与其转变产物的比容不同,零件的表面和心部或零件各部分之间的组织转变时间不同而产生的。
由于奥氏体比容最小,淬火冷却时必然发生体积增加。
淬火时表面先开始马氏体转变,体积增大,心部仍为奥氏体体积不变。
由于心部阻碍表面体积增大,表面产生压应力,心部产生拉应力。
二、减少和控制热处理变形的方法1.合理选材和提高硬度要求对于形状复杂,截面尺寸相差较大而又要求变形较小的零件,应选择淬透性较好的材料,以便使用较缓和的淬火冷却介质淬火。
对于薄板状精密零件,应选用双向轧制板材,使零件纤维方向对称。
对零件的硬度要求,在满足使用要求前提下,尽量选择下限硬度。
2.正确设计零件零件外形应尽量简单、均匀、结构对称,以免因冷却不均匀,使变形开裂倾向增大。
尽量避免截面尺寸突然变化,减少沟槽和薄边,不要有尖锐棱角。
避免较深的不通孔。
长形零件避免截面呈横梯形。
3.合理安排生产路线,协调冷热加工与热处理的关系对于形状复杂、精度要求高的零件,应在粗、精加工之间进行预先处理,如消除应力、退火等。
钢件热处理容易变形的温度

钢件热处理容易变形的温度全文共四篇示例,供读者参考第一篇示例:钢件热处理是钢材加工中的一种重要工艺,通过加热和冷却来改变钢件的组织结构和性能。
热处理可以使钢件获得理想的硬度、强度和耐磨性,提高其使用性能和寿命。
在进行热处理过程中,钢件很容易发生变形,这给工艺控制和产品质量带来一定的困扰。
钢件热处理容易变形的主要原因有以下几点:1. 温度变化大:钢件在进行热处理时,需要进行高温加热和快速冷却。
由于钢材的热膨胀系数比较大,加热后钢件表面和内部温度会出现较大的差异,导致钢件形变。
2. 冷却速度不均匀:钢件在热处理过程中,冷却速度是影响钢件性能的重要因素之一。
如果冷却速度不均匀,会导致钢件产生内部应力,从而引起变形。
3. 热处理工艺不当:热处理工艺的参数设置不合理,比如加热温度、保温时间、冷却速度等方面没有进行有效控制,会导致钢件变形。
4. 初始应力存在:钢件在进行热处理之前,可能存在一定的残余应力,这些应力在热处理过程中会被释放出来,导致钢件变形。
钢件热处理容易变形的问题严重影响了产品的质量和生产效率,为了有效解决这一问题,可以采取以下措施:2. 合理设计工装:在热处理过程中,采用合理的工装设计,使钢件受力均匀,避免局部受力过大导致变形。
3. 预热处理:对于特殊形状或要求严格的钢件,可以在热处理前进行预热处理,降低残余应力,减少变形的可能性。
4. 热处理后回火处理:在热处理后进行回火处理,可以减少钢件内部应力,提高稳定性,减少变形。
通过以上措施的采取,可以有效降低钢件热处理过程中的变形问题,提高产品的质量和工艺稳定性,为钢件加工行业的发展提供有力支撑。
第二篇示例:钢件热处理是一种常见的工艺,可以通过加热和冷却钢件来改变其物理和化学性质。
在进行热处理过程中,钢件往往会出现变形的现象,这给生产制造过程带来了一定的困扰。
其中一个重要的原因就是温度控制不当。
钢件在热处理过程中容易发生变形的主要原因之一就是温度过高或者温度变化过快。
金属材料热处理变形的影响因素和控制策略

金属材料热处理变形的影响因素和控制策略
金属材料热处理变形是指在金属材料进行热处理过程中,由于温度、压力和力学应力的作用,导致材料发生形变。
热处理变形是金属加工中不可忽视的问题,对材料的性能和工艺性能有着重要影响。
本文将从影响因素和控制策略两个方面进行讨论。
影响金属材料热处理变形的因素有以下几个方面:
1. 温度:温度是影响金属材料热处理变形的重要因素。
在高温下,金属材料的塑性增强,易于发生变形。
但是温度过高会导致材料的晶粒长大,使材料的性能下降。
在热处理过程中需要控制好温度的选择,避免过高或过低的温度对材料的不良影响。
2. 压力:压力是热处理过程中的控制参数之一,对材料的变形起到重要作用。
适宜的压力可以加快变形过程,改善材料的性能。
但是过大的压力可能会导致材料的破裂和损坏,因此需要根据材料的性质和工艺要求确定合适的压力。
3. 力学应力:在热处理过程中,材料在受到外力作用下容易发生塑性变形。
力学应力的大小和方向对材料的变形有决定性影响。
不同形状和尺寸的材料在受力时会产生不同的应力分布,因此需要合理设计热处理装置和选择适当的应力状态,以控制材料的变形。
4. 热处理时间:热处理时间是影响金属材料热处理变形的另一个重要因素。
时间过长可能会导致材料的晶粒长大和析出相的生成,使材料的性能下降。
在热处理过程中需要精确控制热处理时间,避免时间过长对材料的不良影响。
金属材料热处理变形的影响因素和控制策略是一个复杂的问题。
需要综合考虑材料的性质、工艺要求和设备情况等因素,通过合理的策略和控制手段,实现对金属材料热处理变形的控制和优化。
薄壁件热处理变形
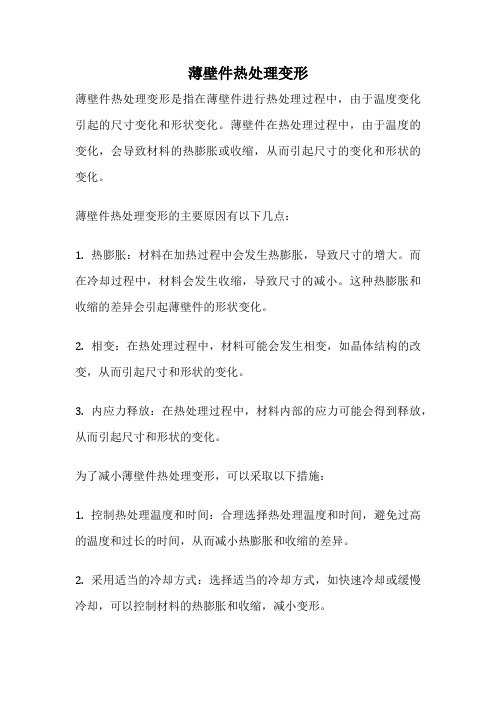
薄壁件热处理变形
薄壁件热处理变形是指在薄壁件进行热处理过程中,由于温度变化引起的尺寸变化和形状变化。
薄壁件在热处理过程中,由于温度的变化,会导致材料的热膨胀或收缩,从而引起尺寸的变化和形状的变化。
薄壁件热处理变形的主要原因有以下几点:
1. 热膨胀:材料在加热过程中会发生热膨胀,导致尺寸的增大。
而在冷却过程中,材料会发生收缩,导致尺寸的减小。
这种热膨胀和收缩的差异会引起薄壁件的形状变化。
2. 相变:在热处理过程中,材料可能会发生相变,如晶体结构的改变,从而引起尺寸和形状的变化。
3. 内应力释放:在热处理过程中,材料内部的应力可能会得到释放,从而引起尺寸和形状的变化。
为了减小薄壁件热处理变形,可以采取以下措施:
1. 控制热处理温度和时间:合理选择热处理温度和时间,避免过高的温度和过长的时间,从而减小热膨胀和收缩的差异。
2. 采用适当的冷却方式:选择适当的冷却方式,如快速冷却或缓慢冷却,可以控制材料的热膨胀和收缩,减小变形。
3. 采用适当的工艺参数:调整热处理的工艺参数,如加热速度、冷却速度等,可以减小薄壁件的变形。
4. 采用适当的夹具和支撑:在热处理过程中,使用适当的夹具和支撑,可以控制薄壁件的形状变化,减小变形。
薄壁件热处理变形是一个复杂的问题,需要综合考虑材料的性质、热处理工艺参数等因素,采取合适的措施来减小变形。
9个影响热处理变形的因素

9个影响热处理变形的因素一、变形的原因钢的变形主要原因是钢中存在内应力或者外部施加的应力。
内应力是因温度分布不均匀或者相变所致,残余应力也是原因之一。
外应力引起的变形主要是由于工件自重而造成的“塌陷”,在特殊情况下也应考虑碰撞被加热的工件,或者夹持工具夹持所引起的凹陷等。
变形包括弹性变形和塑性变形两种。
尺寸变化主要是基于组织转变,故表现出同样的膨胀和收缩,但当工件上有孔穴或者复杂形状工件,则将导致附加的变形。
如果淬火形成大量马氏体则发生膨胀,如果产生大量残余奥氏体则相应的要收缩。
此外,回火时一般发生收缩,而出现二次硬化现象的合金钢则发生膨胀,如果进行深冷处理,则由于残余奥氏体的马氏体化而进一步膨胀,这些组织的比容都随着含碳量的增加而增大,故含碳量增加也使尺寸变化量增大。
二、淬火变形的主要发生时段1.加热过程:工件在加热过程中,由于内应力逐渐释放而产生变形。
2.保温过程:以自重塌陷变形为主,即塌陷弯曲。
3.冷却过程:由于不均匀冷却和组织转变而至变形。
三、加热与变形当加热大型工件时,存在残余应力或者加热不均匀,均可产生变形。
残余应力主要来源于加工过程。
当存在这些应力时,由于随着温度的升高,钢的屈服强度逐渐下降,即使加热很均匀,很轻微的应力也会导致变形。
一般,工件的外缘部位残余应力较高,当温度的上升从外部开始进行时,外缘部位变形较大,残余应力引起的变形包括弹性变形和塑性变形两种。
加热时产生的热应力和想变应力都是导致变形的原因。
加热速度越快、工件尺寸越大、截面变化越大,则加热变形越大。
热应力取决于温度的不均匀分布程度和温度梯度,它们都是导致热膨胀发生差异的原因。
如果热应力高于材料的高温屈服点,则引起塑性变形,这种塑性变形就表现为“变形”。
相变应力主要源于相变的不等时性,即材料一部分发生相变,而其它部分还未发生相变时产生的。
加热时材料的组织转变成奥氏体发生体积收缩时可出现塑性变形。
如果材料的各部分同时发生相同的组织转变,则不产生应力。
浅析金属材料热处理过程变形及开裂问题
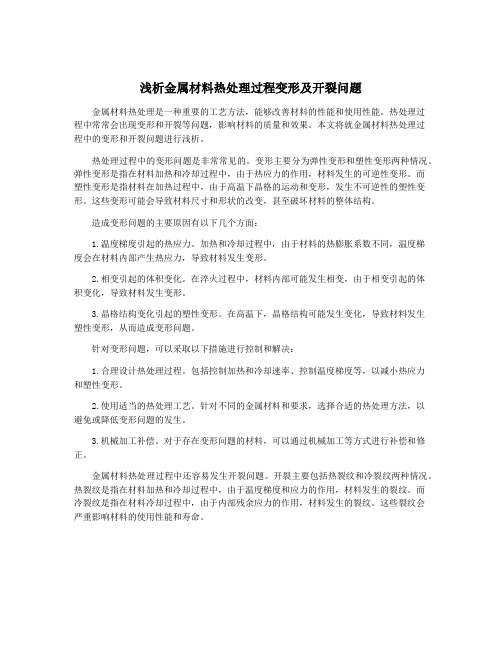
浅析金属材料热处理过程变形及开裂问题金属材料热处理是一种重要的工艺方法,能够改善材料的性能和使用性能。
热处理过程中常常会出现变形和开裂等问题,影响材料的质量和效果。
本文将就金属材料热处理过程中的变形和开裂问题进行浅析。
热处理过程中的变形问题是非常常见的。
变形主要分为弹性变形和塑性变形两种情况。
弹性变形是指在材料加热和冷却过程中,由于热应力的作用,材料发生的可逆性变形。
而塑性变形是指材料在加热过程中,由于高温下晶格的运动和变形,发生不可逆性的塑性变形。
这些变形可能会导致材料尺寸和形状的改变,甚至破坏材料的整体结构。
造成变形问题的主要原因有以下几个方面:1.温度梯度引起的热应力。
加热和冷却过程中,由于材料的热膨胀系数不同,温度梯度会在材料内部产生热应力,导致材料发生变形。
2.相变引起的体积变化。
在淬火过程中,材料内部可能发生相变,由于相变引起的体积变化,导致材料发生变形。
3.晶格结构变化引起的塑性变形。
在高温下,晶格结构可能发生变化,导致材料发生塑性变形,从而造成变形问题。
针对变形问题,可以采取以下措施进行控制和解决:1.合理设计热处理过程。
包括控制加热和冷却速率、控制温度梯度等,以减小热应力和塑性变形。
2.使用适当的热处理工艺。
针对不同的金属材料和要求,选择合适的热处理方法,以避免或降低变形问题的发生。
3.机械加工补偿。
对于存在变形问题的材料,可以通过机械加工等方式进行补偿和修正。
金属材料热处理过程中还容易发生开裂问题。
开裂主要包括热裂纹和冷裂纹两种情况。
热裂纹是指在材料加热和冷却过程中,由于温度梯度和应力的作用,材料发生的裂纹。
而冷裂纹是指在材料冷却过程中,由于内部残余应力的作用,材料发生的裂纹。
这些裂纹会严重影响材料的使用性能和寿命。
热处理中的材料变形与应力释放
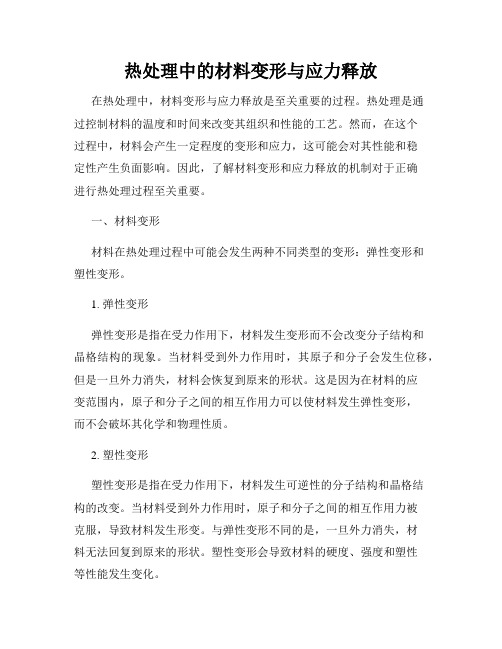
热处理中的材料变形与应力释放在热处理中,材料变形与应力释放是至关重要的过程。
热处理是通过控制材料的温度和时间来改变其组织和性能的工艺。
然而,在这个过程中,材料会产生一定程度的变形和应力,这可能会对其性能和稳定性产生负面影响。
因此,了解材料变形和应力释放的机制对于正确进行热处理过程至关重要。
一、材料变形材料在热处理过程中可能会发生两种不同类型的变形:弹性变形和塑性变形。
1. 弹性变形弹性变形是指在受力作用下,材料发生变形而不会改变分子结构和晶格结构的现象。
当材料受到外力作用时,其原子和分子会发生位移,但是一旦外力消失,材料会恢复到原来的形状。
这是因为在材料的应变范围内,原子和分子之间的相互作用力可以使材料发生弹性变形,而不会破坏其化学和物理性质。
2. 塑性变形塑性变形是指在受力作用下,材料发生可逆性的分子结构和晶格结构的改变。
当材料受到外力作用时,原子和分子之间的相互作用力被克服,导致材料发生形变。
与弹性变形不同的是,一旦外力消失,材料无法回复到原来的形状。
塑性变形会导致材料的硬度、强度和塑性等性能发生变化。
二、应力释放热处理过程中,材料会在高温下处理一段时间,这个过程会导致材料内部产生一定的应力。
要避免这些应力对材料性能造成不利影响,需要进行应力释放。
1. 冷却过程中的应力释放在热处理过程中,材料在高温处理后需要进行冷却。
在冷却过程中,由于材料的不均匀收缩,内部会产生应力。
为了释放这些应力,通常采取缓慢冷却的方法,使材料逐渐恢复到平衡状态。
这样可以减少材料的内部应力,提高其稳定性和可靠性。
2. 后热处理过程中的应力释放有一些材料,在经过热处理后还需要进行后热处理过程,以进一步调整其组织和性能。
在这个过程中,同样需要考虑到应力的释放。
通过适当的热处理工艺和参数设置,可以使材料内部的应力得到有效释放,从而提高材料的性能。
总结:在热处理过程中,材料变形与应力释放是不可避免的。
了解材料的变形类型和应力释放机制,可以帮助工程师和技术人员选择合适的热处理工艺和参数,以达到预期的材料性能和稳定性。
浅析金属材料热处理过程变形及开裂问题

浅析金属材料热处理过程变形及开裂问题热处理是金属材料加工过程中重要的一环,通过加热和冷却的过程,可以改善金属材料的物理和机械性能。
然而,在热处理过程中,金属材料经常会出现变形和开裂的问题,这对后续加工和使用都会产生负面影响。
本文将从变形和开裂两方面对金属材料热处理过程中的问题进行分析。
一、变形问题金属材料热处理过程中最常见的问题就是变形。
因为热处理过程中,金属材料发生了高温变形,如果不加以控制就容易导致材料失去原本的形状和尺寸,并成为废品。
热处理过程中的变形主要有两种类型:弹性变形和塑性变形1、弹性变形弹性变形是在热处理过程中最普遍的变形形式。
在热处理过程中,金属材料会受到热膨胀和冷缩的影响,这种变形是可逆的。
也就是在完成热处理后,金属材料可以回弹到原来的形状和尺寸。
塑性变形是非常复杂的变形过程。
当金属材料在热处理过程中受到热作用时,材料的原子开始流动,从而导致材料的微观结构发生变化。
如果这种变化超过材料的变形极限,就会导致塑性变形。
这种变形是不可逆的,并且金属材料的形状和尺寸将永久改变。
二、开裂问题除了变形问题,金属材料在热处理过程中还可能会出现开裂的问题。
开裂是金属材料加热和冷却过程中的一个严重问题,如果不能及时地修复,就会损坏整个工件。
那么金属材料在热处理过程中容易出现开裂的情况,因为存在以下几种原因:1、应力过大在热处理过程中,金属材料的表面和内部会产生应力。
如果这种应力超过了材料的强度极限,就会导致开裂。
所以需要在热处理过程中进行应力放松,避免材料过度应力。
2、温度过高金属材料在热处理过程中需要加热到一定的温度才能达到理想的效果,但是过高的温度会导致材料的热膨胀过大,从而超过了其极限。
此时也会发生开裂的情况。
3、冷却速率过快热处理过程中的冷却过程同样需要进行控制,过快的冷却速率可能导致金属材料内部产生应力过大,从而导致开裂发生。
总之,要避免金属材料在热处理过程中发生变形或者开裂的问题,需要在控制好加热、保温、冷却的温度和速率等因素的基础上,也要对金属材料的材质、形状、尺寸等方面进行综合分析和把握,以确保热处理过程的成功进行。
热处理变形的原因
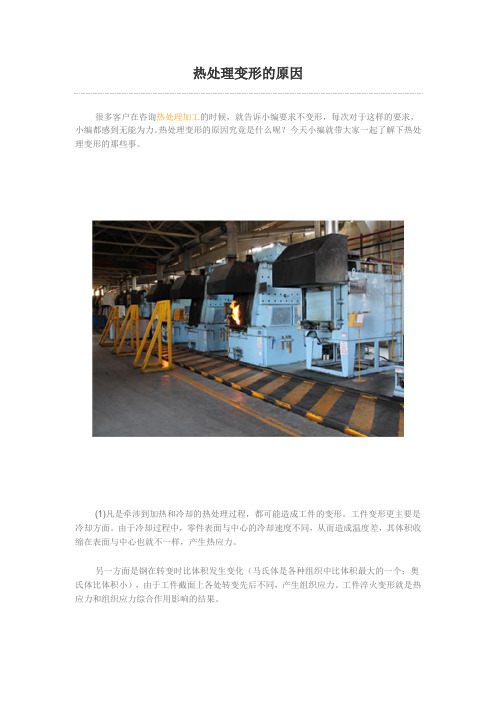
很多客户在咨询热处理加工的时候,就告诉小编要求不变形,每次对于这样的要求,小编都感到无能为力。
热处理变形的原因究竟是什么呢?今天小编就带大家一起了解下热处理变形的那些事。
(1)凡是牵涉到加热和冷却的热处理过程,都可能造成工件的变形。
工件变形更主要是冷却方面。
由于冷却过程中,零件表面与中心的冷却速度不同,从而造成温度差,其体积收缩在表面与中心也就不一样,产生热应力。
另一方面是钢在转变时比体积发生变化(马氏体是各种组织中比体积最大的一个;奥氏体比体积小),由于工件截面上各处转变先后不同,产生组织应力。
工件淬火变形就是热应力和组织应力综合作用影响的结果。
(2)工件的结构形状、原材料质量、热处理前的加工状态、工件的自重以及工件在炉中加热和冷却时的支承或夹持不当,冷却投入方向、方法和冷却时在冷却中的动作不当等也能引起变形。
加热温度高,冷却速快,故淬火变形最为严重。
(3)工件热处理后的不稳定组织和不稳定的应力状态,在常温和零下温度长时间放置或使用过程中,逐渐发生转变而趋于稳定,也会伴随引起工件的变形,这种变形称为时效变形。
时效变形虽然不大,但是对于精密零件和标准量具也不许的。
实际生产中必须予以防止。
(4)热处理过程中产生的内应力有
热应力和相变应力,它们的形成原因和作用是不同的。
这种应力在热处理过程中对变形影响是主要的原因。
钢件热处理变形的原因总结

钢件热处理变形的原因总结
引起热处理变形的因素颇多,总括起来,基本上有三点:
1、固态相变时,各相质量体积的变化必然引起体积的变化,造成零件的胀与缩的尺寸变化;
2、热应力,包括急热热应力和急冷热应力,当它们超过零件在该温度下所具有的屈服极限时,将使零件产生塑性变形,造成零件的形状变化,即歪扭,或称为畸变;
3、组织应力也会引起形状的改变,即畸变。
一般说,淬火工件的变形总是由于以上的两种或三种因素综合作用的结果,但究竟哪一个因素对变形的影响较大,则需要具体情况作具体的分析。
总的来说,体积变化是由相变时比容的改变而引起的。
马氏体的质量体积比钢的其他组成相的质量体积要大,热处理时钢由其他组成相转化为马氏体时,必然引起体积的增加。
而奥氏体的质量体积要比钢的其他组织质量体积要小,在热处理时由其他组成相转变为奥氏体时,则引起体积的减小。
关于形状的变化,歪扭或称为畸变,主要是由于内应力或者外加应力作用的结果。
在加热、冷却过程中,因工件各个部位的温度有差别,相变在时间上有先后,有时发生的组织转变也不一致,而造成内应力。
这种内应力一旦超过了该温度下材料的屈服极限,就产生塑性变形,引起形状的改变。
此外工件内的冷加工残余应力在加热过程中的松弛,以及由于加热时受到较大的外加应力也会引起形状的变化。
在热处理时可能引起体积变化和形状变化的原因见下表。
表中“体积变化原因” 一栏未列入钢因热胀冷缩现象而产生的体积变化,钢由淬火加热温度到零下温度进行冷处理,均随温度的变化而有相应的体积变化,因热胀冷缩而引起的体积变化不均匀乃是热应力产生的原因,而且对变形有相当的影响。
热处理可能引起体积变化和形状变化的原因。
热处理变形的原因
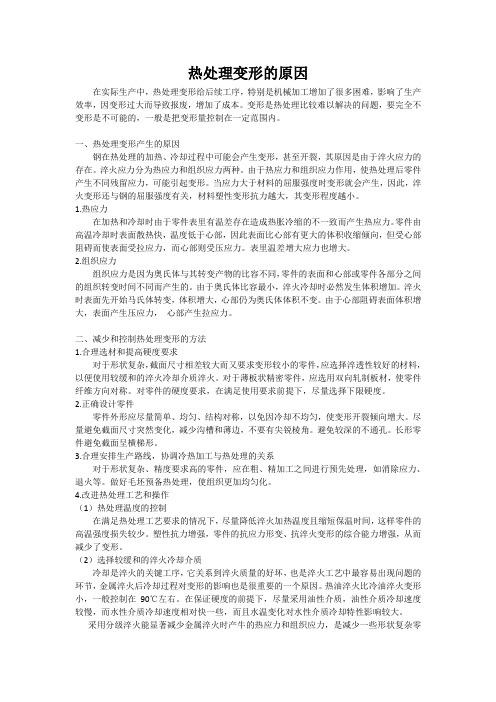
热处理变形的原因在实际生产中,热处理变形给后续工序,特别是机械加工增加了很多困难,影响了生产效率,因变形过大而导致报废,增加了成本。
变形是热处理比较难以解决的问题,要完全不变形是不可能的,一般是把变形量控制在一定范围内。
一、热处理变形产生的原因钢在热处理的加热、冷却过程中可能会产生变形,甚至开裂,其原因是由于淬火应力的存在。
淬火应力分为热应力和组织应力两种。
由于热应力和组织应力作用,使热处理后零件产生不同残留应力,可能引起变形。
当应力大于材料的屈服强度时变形就会产生,因此,淬火变形还与钢的屈服强度有关,材料塑性变形抗力越大,其变形程度越小。
1.热应力在加热和冷却时由于零件表里有温差存在造成热胀冷缩的不一致而产生热应力。
零件由高温冷却时表面散热快,温度低于心部,因此表面比心部有更大的体积收缩倾向,但受心部阻碍而使表面受拉应力,而心部则受压应力。
表里温差增大应力也增大。
2.组织应力组织应力是因为奥氏体与其转变产物的比容不同,零件的表面和心部或零件各部分之间的组织转变时间不同而产生的。
由于奥氏体比容最小,淬火冷却时必然发生体积增加。
淬火时表面先开始马氏体转变,体积增大,心部仍为奥氏体体积不变。
由于心部阻碍表面体积增大,表面产生压应力,心部产生拉应力。
二、减少和控制热处理变形的方法1.合理选材和提高硬度要求对于形状复杂,截面尺寸相差较大而又要求变形较小的零件,应选择淬透性较好的材料,以便使用较缓和的淬火冷却介质淬火。
对于薄板状精密零件,应选用双向轧制板材,使零件纤维方向对称。
对零件的硬度要求,在满足使用要求前提下,尽量选择下限硬度。
2.正确设计零件零件外形应尽量简单、均匀、结构对称,以免因冷却不均匀,使变形开裂倾向增大。
尽量避免截面尺寸突然变化,减少沟槽和薄边,不要有尖锐棱角。
避免较深的不通孔。
长形零件避免截面呈横梯形。
3.合理安排生产路线,协调冷热加工与热处理的关系对于形状复杂、精度要求高的零件,应在粗、精加工之间进行预先处理,如消除应力、退火等。
浅析金属材料热处理过程变形及开裂问题

浅析金属材料热处理过程变形及开裂问题金属材料热处理是一种常见的工艺,通过热处理可以改善金属的组织结构和力学性能,提高其硬度、强度、耐磨性等。
在热处理过程中,金属材料可能会发生变形和开裂等问题,影响热处理效果和制品质量。
本文将就金属材料热处理过程中的变形及开裂问题进行浅析。
1.1 变形的原因金属在加热和冷却过程中,会发生体积膨胀和收缩,由于材料的弹性变形和塑性变形,会导致材料发生变形。
在加热过程中,金属材料的晶粒会发生重新组织,晶粒的尺寸和形状发生变化,从而引起材料产生变形。
在冷却过程中,由于温度梯度和残余应力的存在,也会使得金属材料产生变形。
1.2 变形的表现金属材料热处理过程中的变形主要表现为尺寸变化和形状变化。
尺寸变化包括线膨胀、面膨胀和体积膨胀,形状变化包括挠曲、弯曲、翘曲等。
这些变形会影响工件的精度和质量,甚至导致工件无法使用。
1.3 变形的影响金属材料热处理过程中的变形会影响工件的尺寸精度和形状精度,降低工件的加工精度和装配精度,甚至影响工件的功能和使用寿命。
研究金属材料热处理过程中的变形问题,并寻求有效的控制措施,对于提高金属材料热处理质量具有重要意义。
2.1 开裂的原因金属材料在热处理过程中容易发生开裂,其主要原因包括内应力和组织缺陷。
在热处理过程中,由于金属材料的非均匀加热和冷却,会导致材料产生内应力,当内应力超过材料的承受能力时,就会引起裂纹的产生。
金属材料在制备过程中可能存在组织缺陷,如夹杂物、气孔等,这些缺陷也会成为裂纹的萌生点,易引发开裂。
2.2 开裂的表现金属材料热处理过程中裂纹的表现有很多种,主要包括表面开裂、内部裂纹、轧制裂纹等。
这些裂纹会降低金属材料的强度和韧性,影响其使用性能,甚至导致工件的失效。
3.1 完善工艺流程在金属材料热处理过程中,应根据材料的属性和工件的结构特点,合理设计和优化热处理工艺流程。
包括加热温度、保温时间、冷却速度等参数的选择,以及预热、均热、保温、淬火等工艺控制的改进,以减小工件的内应力和组织缺陷,降低变形和开裂的风险。
热处理变形基础知识
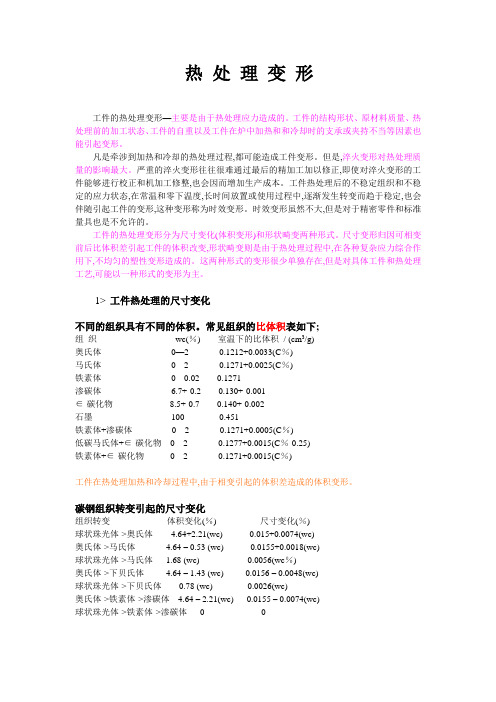
热处理变形工件的热处理变形—主要是由于热处理应力造成的。
工件的结构形状、原材料质量、热处理前的加工状态、工件的自重以及工件在炉中加热和和冷却时的支承或夹持不当等因素也能引起变形。
凡是牵涉到加热和冷却的热处理过程,都可能造成工件变形。
但是,淬火变形对热处理质量的影响最大。
严重的淬火变形往往很难通过最后的精加工加以修正,即使对淬火变形的工件能够进行校正和机加工修整,也会因而增加生产成本。
工件热处理后的不稳定组织和不稳定的应力状态,在常温和零下温度,长时间放置或使用过程中,逐渐发生转变而趋于稳定,也会伴随引起工件的变形,这种变形称为时效变形。
时效变形虽然不大,但是对于精密零件和标准量具也是不允许的。
工件的热处理变形分为尺寸变化(体积变形)和形状畸变两种形式。
尺寸变形归因可相变前后比体积差引起工件的体积改变,形状畸变则是由于热处理过程中,在各种复杂应力综合作用下,不均匀的塑性变形造成的。
这两种形式的变形很少单独存在,但是对具体工件和热处理工艺,可能以一种形式的变形为主。
1>工件热处理的尺寸变化不同的组织具有不同的体积。
常见组织的比体积表如下;组织wc(%) 室温下的比体积/ (cm3/g)奥氏体0—2 0.1212+0.0033(C%)马氏体0---2 0.1271+0.0025(C%)铁素体0---0.02 0.1271渗碳体 6.7+-0.2 0.130+-0.001∈-碳化物8.5+-0.7 0.140+-0.002石墨100 0.451铁素体+渗碳体0---2 0.1271+0.0005(C%)低碳马氏体+∈-碳化物0---2 0.1277+0.0015(C%-0.25)铁素体+∈-碳化物0---2 0.1271+0.0015(C%)工件在热处理加热和冷却过程中,由于相变引起的体积差造成的体积变形。
碳钢组织转变引起的尺寸变化组织转变体积变化(%) 尺寸变化(%)球状珠光体->奥氏体- 4.64+2.21(wc) - 0.015+0.0074(wc)奥氏体->马氏体 4.64 – 0.53 (wc) - 0.0155+0.0018(wc)球状珠光体->马氏体 1.68 (wc) 0.0056(wc%)奥氏体->下贝氏体 4.64 – 1.43 (wc) 0.0156 – 0.0048(wc)球状珠光体->下贝氏体0.78 (wc) 0.0026(wc)奥氏体->铁素体->渗碳体 4.64 – 2.21(wc) 0.0155 – 0.0074(wc)球状珠光体->铁素体->渗碳体0 02>工件热处理的形状畸变工件热处理的形状畸变有多种原因。
零件热处理变形

零件热处理变形一、引言零件热处理是一种重要的材料加工技术,它能够改善材料的性能和延长使用寿命。
然而,在零件热处理过程中,由于温度和应力的影响,零件可能会发生变形。
这种变形会对零件的尺寸和形状造成影响,从而影响其功能和性能。
因此,了解零件热处理变形的原因和控制方法对于保证零件质量和稳定性具有重要意义。
二、零件热处理变形原因1.温度梯度引起的变形在热处理过程中,由于加热和冷却速度不同,导致不同部位温度存在梯度差异。
这种温度梯度会引起材料内部应力分布不均匀,从而导致变形。
2.相变引起的变形在一些特殊的材料中,在热处理过程中会发生相变现象。
相变时产生的体积变化会导致材料产生应力分布不均匀,从而导致变形。
3.机械加工残余应力引起的变形在机械加工过程中,由于切削和加工等原因,零件内部会产生残余应力。
在进行热处理时,残余应力会被释放,从而导致变形。
4.材料的热膨胀引起的变形在热处理过程中,由于材料温度升高,导致材料发生热膨胀。
这种膨胀会导致材料产生应力分布不均匀,从而导致变形。
三、零件热处理变形控制方法1.优化加热和冷却方式在进行零件热处理时,可以通过优化加热和冷却方式来减少温度梯度的影响。
例如,在加热过程中采用均匀加热方式,在冷却过程中采用缓慢冷却方式等。
2.控制相变过程在进行特殊材料的热处理时,需要控制相变过程来减少变形。
例如,在进行淬火处理时可以采用间歇淬火或油淬等方式来控制相变速率。
3.预处理机械加工残余应力在进行零件热处理前,可以通过预处理机械加工残余应力来减少变形。
例如,在机械加工后进行热处理前可以进行退火处理来释放残余应力。
4.控制材料的热膨胀在进行零件热处理时,可以通过控制材料的热膨胀来减少变形。
例如,在加热过程中可以采用局部加热或多次加热等方式来控制材料的膨胀。
四、结论零件热处理变形是一个复杂的问题,其产生原因和控制方法需要综合考虑。
在实际应用中,需要根据具体情况选择合适的控制方法来减少变形。
7个减小热处理变形的方法

7个减小热处理变形的方法热处理是通过加热和冷却金属材料来改变其性质的过程。
在进行热处理过程中,材料会发生变形,这是由于温度和应力的变化引起的。
为了减小热处理过程中的变形,可以采取以下7种方法:1.加工前热处理:在材料进行初次加工之前,可以进行热处理以减小后续加工过程中的变形。
这样可以通过改变材料的晶体结构和分布来改变其屈服强度和塑性,从而减小变形。
2.采用复合材料:复合材料由两种或多种不同的材料组成,其中一个材料具有较高的强度和刚性,而另一个材料具有较高的韧性和延展性。
通过使用复合材料,可以在一定程度上减小热处理过程中的变形。
3.控制变形工艺参数:在进行热处理过程中,可以通过控制加热温度、冷却速率和时间等参数来减小变形。
例如,降低加热温度和冷却速率可以减少变形量。
4.施加局部应力:在进行热处理过程中,可以在材料上施加一定的局部应力来减小整体的变形。
这可以通过冷却或加热过程中施加压力实现,从而使材料变形更加均匀。
这种方法可以大大降低材料的变形量。
5.使用支撑装置:在进行热处理过程中,可以使用支撑装置或夹具来固定材料,以减小变形。
这些支撑装置可以帮助保持材料的形状和尺寸,从而降低变形。
6.采用适当的冷却介质:在进行热处理过程中,选择适当的冷却介质可以减小变形。
不同的冷却介质具有不同的冷却速率,可以根据需要选择合适的冷却介质,以减小变形。
7.进行后续时效处理:在进行热处理后,可以进行后续的时效处理以减小变形。
时效处理是通过在一定时间内将材料保持在一定的温度下,使其继续发生晶体结构和性质的变化。
这样可以通过改变材料的结构和性质来减小变形。
热处理变形产生的原因及控制方法
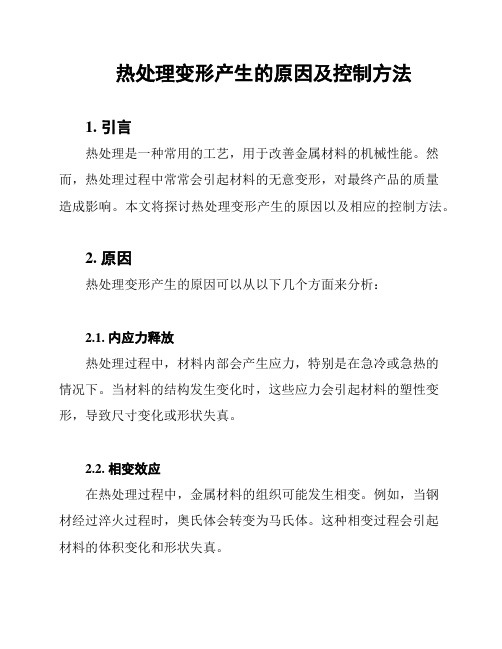
热处理变形产生的原因及控制方法1. 引言热处理是一种常用的工艺,用于改善金属材料的机械性能。
然而,热处理过程中常常会引起材料的无意变形,对最终产品的质量造成影响。
本文将探讨热处理变形产生的原因以及相应的控制方法。
2. 原因热处理变形产生的原因可以从以下几个方面来分析:2.1. 内应力释放热处理过程中,材料内部会产生应力,特别是在急冷或急热的情况下。
当材料的结构发生变化时,这些应力会引起材料的塑性变形,导致尺寸变化或形状失真。
2.2. 相变效应在热处理过程中,金属材料的组织可能发生相变。
例如,当钢材经过淬火过程时,奥氏体会转变为马氏体。
这种相变过程会引起材料的体积变化和形状失真。
2.3. 不均匀加热或冷却如果热处理过程中加热或冷却不均匀,材料的局部温度会存在差异。
这种温度差异会导致材料的非均匀膨胀或收缩,从而引起变形。
3. 控制方法为了减少热处理产生的变形,可以采取以下控制方法:3.1. 控制加热和冷却速率合理控制加热和冷却速率,避免过快或过慢,可以减少材料的变形。
在进行急冷或急热处理时,可以采取预先控制的温度梯度,以缓解内应力的释放。
3.2. 优化工艺参数通过调整热处理过程中的工艺参数,如温度、时间和冷却介质等,可以最大限度地减少材料的变形。
合理选择工艺参数,可以提高材料的均匀性和稳定性。
3.3. 采用合适的支撑结构对于形状复杂的工件,可以采用合适的支撑结构来减少变形。
支撑结构可以提供一定的约束,防止材料发生不受控制的变形。
4. 结论热处理变形是热处理过程中常见的问题,但通过合理的控制方法可以有效减少其影响。
合理控制加热和冷却速率、优化工艺参数以及采用合适的支撑结构都是减少热处理变形的有效途径。
这些控制方法可以提高最终产品的质量和性能。
---以上是关于热处理变形产生的原因及控制方法的内容。
请基于以上内容,进一步完善和添加具体细节,使文档达到800字以上的要求。
热处理变形校正方法

热处理变形校正方法在金属加工行业中,热处理是一个至关重要的环节,它能够改善材料的性能,为产品提供必要的强度和硬度。
然而,热处理过程中往往伴随着变形的问题,这给产品质量带来了挑战。
本文将详细介绍热处理变形校正的方法,帮助读者更好地理解和应对这一工艺难题。
一、热处理变形的原因热处理变形主要是由于材料在加热和冷却过程中,内部应力重新分布所导致的。
当材料暴露在高温环境下,其晶体结构会发生改变,冷却后,这些改变会导致尺寸变化和形状变形。
二、热处理变形校正方法1.预防措施:- 选择合适的材料:不同材料的热处理变形程度不同,选择变形较小的材料是预防变形的有效手段。
- 优化热处理工艺:通过调整加热速度、保温时间、冷却速度等参数,降低热处理变形的风险。
2.变形校正方法:- 机械校正:通过机械力对变形部位进行校正,如锤击、拉伸等,但这种方法仅适用于轻微变形。
- 热校正:利用材料在高温下的塑性变形,对变形部位进行加热至适当温度后进行校正。
这种方法对操作技术要求较高,需防止过度加热导致新的变形。
- 液体校正:将变形部位浸入高温液体中,利用液体的压力和温度对变形进行校正。
此方法适用于复杂形状的零件。
3.数控加工校正:- 采用数控加工技术,根据变形量对零件进行精确加工,以消除变形影响。
这种方法适用于高精度要求的零件。
4.表面处理:- 对变形部位进行表面处理,如喷漆、氧化等,以掩盖或补偿变形。
三、总结热处理变形是金属加工中不可避免的问题,但通过合理的预防措施和校正方法,可以最大限度地降低变形对产品质量的影响。
在实际操作中,应根据具体情况选择合适的校正方法,确保产品达到预期的性能和质量要求。
各种热处理工艺造成变形的原因总结

各种热处理工艺造成变形的原因总结引言:热处理工艺是一种常见的金属加工方法,它通过对金属材料进行加热和冷却来改变其结构和性能。
然而,热处理过程中往往会导致材料发生变形,这对于一些精密零件的加工和制造带来一定的困扰。
本文将从各种热处理工艺的角度,总结造成变形的原因,并探讨相应的解决方法。
一、淬火过程中的变形原因淬火是一种通过快速冷却来使金属材料达到高强度和硬度的热处理工艺。
然而,淬火过程中常常会出现变形现象。
造成淬火变形的主要原因有以下几点:1. 冷却速度不均匀:淬火过程中,材料表面和内部的冷却速度不一致,导致应力不均匀分布,从而引起变形。
2. 材料内部组织不均匀:金属材料内部的组织不均匀,如晶粒尺寸、相含量等差异,会导致淬火时的收缩和变形不一致。
3. 冷却介质选择不当:不同的冷却介质对材料的冷却速度有不同的影响,选择不当可能导致应力集中和变形。
解决方法:针对淬火过程中的变形问题,可以采取以下措施:1. 控制冷却速度:通过优化冷却介质的选择和控制冷却速度,使材料表面和内部的冷却速度尽可能一致,减少应力的不均匀分布。
2. 优化材料组织:通过调整材料的化学成分和热处理工艺,使材料内部的组织更加均匀,减少淬火时的收缩和变形差异。
3. 采用适当的淬火工艺:根据材料的特性和要求,选择适当的淬火工艺,控制冷却速度和温度,减少变形的发生。
二、退火过程中的变形原因退火是一种通过加热和缓慢冷却来改善材料的性能和结构的热处理工艺。
然而,退火过程中同样存在变形的问题。
造成退火变形的主要原因有以下几点:1. 温度不均匀:退火过程中,材料的温度分布不均匀,导致应力分布不均匀,从而引起变形。
2. 冷却速度过快:退火结束后,如果冷却速度过快,会导致材料内部的残余应力无法得到充分释放,从而引起变形。
3. 材料内部缺陷:金属材料内部存在各种缺陷,如气孔、夹杂物等,这些缺陷在退火过程中会扩散和移动,导致变形的发生。
解决方法:针对退火过程中的变形问题,可以采取以下措施:1. 控制温度均匀性:通过合理设计加热设备和工艺参数,确保材料的温度分布均匀,减少应力的不均匀分布。
- 1、下载文档前请自行甄别文档内容的完整性,平台不提供额外的编辑、内容补充、找答案等附加服务。
- 2、"仅部分预览"的文档,不可在线预览部分如存在完整性等问题,可反馈申请退款(可完整预览的文档不适用该条件!)。
- 3、如文档侵犯您的权益,请联系客服反馈,我们会尽快为您处理(人工客服工作时间:9:00-18:30)。
热处理变形:一:钢的内应力及应力变形:1.热应力:冷却初期表面为拉应力,心部为压应力.冷却最终则是表面为压应力,心部为拉应力.组织应力:冷却初期表面为压应力,心部为拉应力.冷却最终则是表面为拉应力,心部为压应力. 附加应力:因表面和心部组织结构的不均匀性及钢件内部的弹塑性变形不一致形成的内应力. 局部淬火或表面淬火:表层呈现压应力,中心呈现拉应力.渗碳件淬火:冷却初期表面为拉应力,心部为压应力.冷却最终则是表面为压应力,心部为拉应力.(最大的压应力不在渗碳层的最外层,而存在于渗碳层表面以里约50-60%的深度处,此处碳浓度低于0.5%).2.影响钢的内应力的因素:1)钢的化学成分的影响:在全淬透的情况下,试样表层和中心显现压应力,中间层显现拉应力,故表层的应力分布以热应力为主,而内部则以组织应力主.随着含碳量的增加,热应力减弱,组织应力逐渐增强,因此表层的压应力减小,中间层的拉应力略有下降,心部的压应力则增大,且中间层的拉应力最大值随含碳量的增加而移向表层.因切向应力较大,故对高碳钢极易产生纵向裂纹.在未淬透的情况下,钢件表层为压应力,心部为拉应力.淬透性愈小,表层压应力愈大.Ms点温度较高的钢,热应力作用较强烈,残余拉应力最大值移向中心,表层显现压应力.2)淬火工艺的影响:淬火加热温度愈高,产生的淬火应力愈大,但径向应力变化较小,切向和轴向应力变化较大.加热温度高,还易于造成钢的过热,即组织粗大化而导致脆性增大,易引起开裂.a:水淬钢全部淬透时,其应力分布为表面和心部呈压应力,中间区域呈拉应力,即属于热应力和组织应力重叠型的分布规律.当中心未淬透时,表面被淬火部分受压应力,中心受拉应力作用. b:油中全淬透时,表层具有拉应力,心部为压应力,即属于单一的组织应力分布规律.未淬透时,表层具有压应力,心间为拉应力,但应力变化较缓和.c:在穿透淬火时,水淬钢的最大拉应力值显现在钢件表面附近,油淬钢的拉应力显现在钢的表面.这种表面附近的拉应力是形成淬火裂纹的主要危险.这时切向应力大于轴向应力,易形成纵向裂纹.3)钢件尺寸大小和形状的影响:内孔直径很小的圆套筒的淬火应力是内孔的表面和外表面具有压应力,中间层为拉应力.内孔直径稍大时,随壁厚的减小热应力的影响急剧减小,从而其残余应力的分布是内表面和外表面具有拉应力,中间层具有压应力.在淬火效果差时,内表面产生的拉应力将很大,故内径小的高碳钢套筒内壁易产生淬火裂纹.内径进一步增大,壁厚进一步减小时,组织应力的影响增强,热应力分布减弱,则总的淬火应力趋于降低.4)钢件表面脱碳的影响:脱碳使得钢伯的脱碳层具有拉应力.脱碳层浓度不同,其应力分布也有差别:随脱碳层浓度的增加,表面的切向应力由压应力转变为拉应力.轴向应力则随脱碳层浓度的增加,开始为拉应力而后转为压应力.3.钢的内应力的分解:1)径向应力:2)轴向应力:3)切向应力:3.钢件表面淬火时的残余应力:1)高频淬火后钢的内应力:2)火焰淬火后钢的内应力:表面具有压应力,中心具有拉应力.4.化学热处理后钢件内的残余应力:1)渗碳淬火后钢的内应力:2)氮化钢的内应力:2.热应力塑性变形的作用结果是使轴类零件的长度收缩,直径变粗;使饼形零件直径收缩,厚度增加;使环形零件的内孔和外径收缩,厚度增加.在生产中主要表现为零件的尺寸收缩.如50#,T10A钢,φ20×200试样加热至720-740℃水淬一次,长度方向的收缩变形量约0.4mm.因淬火时形成的马氏体比容比奥氏体的大,硬度高,塑性条件差,故钢淬火冷至马氏体转变区的应力变形主要以拉伸应力变形为主.组织应力使杆状零件长度伸长,直径减缩;使圆饼形零件直径胀大,厚度减少.3.杆状零件,一般应力作用的主导主向都是轴向.圆饼形零件主导应力主向都是径向.简单的立方体零件应力最集中的部位是八条棱角边.应力变形取决于主导应力方向应力作用类型和大小.4.淬火体积变形的大小还与下列因素有关:1).淬火前后的组织比容差别:2).提高淬火加热温度时,奥氏体中合金元素的溶解量增加,使淬火后马氏体比容增大,但同时引起残余奥氏体量增加.在常规淬火范围内,对低合金工具钢,多数是以提高淬火加热温度使马氏体比容增大引起体积变形增加的效应为主,而对高碳高铬钢则不同3).零件全淬透时体积变形量最大,淬硬层愈浅,体积变形量愈小.4).凡使残余奥氏体量增加的各种方法如分级等温淬火,等温级冷等都可使体积变形量减少.5).除在回火时促使残余奥氏体转变的情况外,其它回火形式都使体积尺寸收缩.淬火冷却激烈的碳素钢零件内应力塑性变形大.采用分级等温淬火的高合金钢内应力变形小.碳和合金含量高,淬透性好的高合金钢比容变形表现比较明显.只有淬火后能控制残余奥氏体量和马氏体温表合金浓度并能运用分级等温淬火的钢种比容变形和内应力变形都较小.二:钢件的热处理裂纹:1.纵向裂纹:由工件表面裂向心部的深度较大的裂纹.它往往发生在完全淬透的工件上.是由切向应力引起的.2.横向裂纹和弧形裂纹:往往性生于大锻件的热处理时.断口特点是垂直于轴向方向,断口中心附近有破坏的起点,以此为中心向四周有放射的断裂扩张痕迹.横向断裂属于热应力引起.弧形裂纹往往发生在未淬透的或经过渗碳淬火的工件上,主要产生于工件的内部,工在尖锐棱角及孔洞附近,即易于造成应力集中处.3.表面裂纹:4.剥离裂纹:5.影响淬火裂纹的因素:1)钢的化学成分对淬火裂纹敏感性的影响:2)原材料缺陷对淬火时形成裂纹的影响:3)钢件结构特点对形成裂纹的影响:4)淬火前原始组织和应力状态对裂纹的影响:5)加热因素对形成裂纹的影响:6)冷却因素对形成裂纹的影响:6.防止淬火裂纹的措施:1)改善钢件结构,合理选择钢材和确定技术条件:2)妥善安排冷热加工工序和正确应用预先热处理:3)正确选择加热介质,加热时间和保温时间:4)合理选用冷却介质和冷却方法:5)其它方法:7.钢件的表面淬火裂纹形成及防止措施:8.钢件化学热处理裂纹的形成及防止措施:二:碳素钢1.中碳钢:含碳较低的钢,水冷淬火沿主导应力方向有较小的胀大变形率,随含碳量的增加变形率增大,至含碳量达0.45-0.5%时,胀大变形率出现峰值,增至0.45-0.52%. 之后随含碳量增加,胀大变形率又渐渐减小. 当含碳量增至1.0%时,变形率接近零(饼形试样开始出现负值,杆状试样仍有微量胀大).含碳量大于 1.2%时,变形为负值,即表现为主导应力方向上的改缩.同时相对应方向产生少量的相应变形,含碳高的T10, T12钢的非主导应力方向的胀大变形量大于中碳钢.2.分析:不论在退火状态或淬火状态,钢的比容均随含碳量的增加而增大,淬火前后的比容变化差,也是随含碳量的增加而增大,而马氏体比容较小的中碳钢40,50在水冷淬透下表现为最大的组织应力特征,而马氏体比容较大的T10, T12却表现为很小的组织变形特征或者是热应力特征,其原因应从淬火冷却过程中热应力和组织应力的作用过去过程和产生塑性变形的条件来分析:1)M S点温度的高低,直接关系零件冷却时两种应力作用的大小,塑性变形方向和变形量的多少.其值低时热应力作用区增大,M S接近室温时冷却过程全部处于热应力作用下,变形特征将全部表现为热应力型变形特征.2)M S温度较高的钢在马氏体转变时的冷却速度较快,M S温度低的钢在马氏体转变区的冷却速度慢.如5%食盐水在相当于中碳钢转变温度300-500℃时的冷却速度为1600℃/ S,而在相当T10A马氏体转变点180-200℃时的冷却速度降低至350℃/S.3)M S温度的变化,改变了马氏体转变时相邻区域奥氏体的塑性状态,从而影响了塑性变形阻力的大小.4)低碳钢在主导应力方向的胀大变形小于中碳钢,是由于低碳钢具有较低的奥氏体稳定性.即使是截面很小的试样在水中淬火也难得到纯马氏体组织.另一方面,由于转变产物为低碳马氏体,比容较小,因比容变化差而产生的组织应力和应力塑性变形也较小.3.影响中碳钢及中碳合金钢淬火变形的因素:中碳钢及中碳合金钢用水淬火的变形主要表现为主导应力方向的胀大,属于组织应力变形的特征.如圆饼,圆环以及扁方零件,水淬变形主要表现为内孔,外径或长宽,孔距方向的胀大,对筒形零件表现为内孔,外径和高度的胀大.1)零件的截面尺寸:A:淬透零件:中碳钢水淬的最大尺寸≤15mm,40Mn,45Mn2V,40Cr约为30-50mm.淬透尺寸范围之内最大变形率是0.45-0.55%.随截面尺寸增大,淬火冷却时温差大,相变的不等时性明显,组织应力增大,应力作用时机的可塑性条件较好,组织应力变形量增大.B:淬不透零件:当中碳钢截面尺寸为20-25mm时,胀大变形率减小至约0.3%.截面尺寸增加至30-35mm时,水淬胀大变形率减小一对该钢最大变形率的1/2左右,即0.25%左右.中碳钢45,50能淬透截面尺寸约是12-15mm,钢的最大胀大变形率的截面也正好是这个尺寸.中碳低合金钢水淬时最大胀大变形率可保持到较大的截面尺寸.对40Cr可保持至60-80mm.2)淬火加热温度:中碳钢的胀大变形率,是随淬火加热温度的提高而增加的.3)淬火冷却方式:A:淬火介质:可低温硝盐中淬火,可明显地减小胀大变形(淬透性差的中碳钢大部分在高温区即开始转变为索氏体等比容变化较小的相结构).采用150-180℃的碱浴淬火时,也能减小胀大变形,但不如硝盐淬的效果好,其变形率一般是0.15-0.25%,但比采用硝盐时的硬度较高.淬透性较高的低合金钢在采用低温硝盐淬火时也能获得较小的胀大变形,但比淬透性差的中碳钢胀大变形量大,一般为0.1-0.15%.除硝盐外,其它各类水溶性介质防胀大变形效果均不显著.B:水冷方式:截面厚度均匀的套管,大多数先入水一端的胀大变形量要大于另一端.为防止这一变形,可在先入水前局部预冷先入水一端,或将套筒放在环形铁板上淬火.中碳高合金钢采用油或低温硝盐淬火冷却时,其胀大变形率比其它钢号稳定,一般胀大变形率为0.12-0.14%. 4.回火对变形的影响:零件尺寸均随回火温度的提高而使收缩变形量增加.大多数钢号当回火后获得HRC35-40的硬度时,其尺寸收缩量大约是淬火后变形量的1/2.5.淬火胀大变形的控制:有较大灵活性.而高碳工具钢一旦出现淬火收缩则很难恢复.1):调整淬火前加工余量.截面尺寸小于20mm的中碳钢套筒按零件尺寸的0.4%,截面尺寸20~50mm的零件按0.2-0.3%.零件尺寸小的中碳合金钢零件可地考虑调整量,零件尺寸大于300mm时可按减小0.1-0.15%来调整.(要注意批时大小和要求的硬度高低)2)淬火前进先进行收缩处理.3)用较低的淬火加热温度加热4)用高频局部加热淬火5)淬火前进行渗碳处理6)选择胀大变形小的淬火介质淬火.7)适当缩短水冷时间并配合等温冷却,即水淬硝盐等温冷却.8)淬火前进行防止胀大的覆盖保护措施,如包铁皮,石棉.9)合理调整回火温度10)淬火前在粗加工后进行调质处理,使钢的原始组织比容增大等.三碳素工具钢:T8A,T10A,T12A钢制零件和模具,除截面尺寸很小的套管,薄板细轴等小零件水淬后出现胀大变形外(主要是比容变形),大部分中小截面(大于10mm而小于50mm)的模具,量规等的淬火变形主要都表现为主导应力方向上的尺寸收缩.含碳量高的T12A收缩变形量最大1.淬火加热温度对T10A,T12A钢变形的影响:1): 淬火加热温度对截面较小的T10A,T12A钢试样,无论加热温度的高低各个方向上的淬火变形均倾向于胀大,但随加热温度的升高,主导应力方向上的胀大变形率明显减小,甚至会出现收缩,而相应方向的胀大变形率明显增加.2)截面尺寸在12-25mm的所有试样在相同的热处理条件下,在主导应力方向上的塑性收缩变形率比小截面和大截面试样都大,而且收缩变形率受淬火加热温度的影响更为明显,淬火加热温度从770℃升高至830-840℃时,收缩变形率将近增加一倍.3)所有T10A,T12A试样,淬火后的变形率都是随加热温度的升学高难度,主导应力方向的收缩变形率增加.如果低温淬火时的最终变形为胀大,则随淬火温度的升高,胀大变压器形逐渐减小或变为收缩变形(但有一定限度)4)对大截面的过共析钢零件的淬火变形也是随淬火加热温度的提高使收缩变形率增加5)T10A,T12A不同温度下水淬变形的实质:截面很小的零件热应力作用很小,最终淬火后变形大部是因比容变化而引起的比容变形.同时提高淬火加热温度,钢的马氏体转变温度降低,使热应力作用增大,组织应力减小,故主导应力方向上热应力收缩变形增加或胀大变形减小.对T10A,T12A钢,截面厚度为12-20mm的零件,当提高淬火加热温度时,零件的淬透程度必然改变,从只能表面淬硬至整个截面全部淬透,而接近淬透的最大临界截面尺寸比易淬透的小截面和淬不透的大截面零件受淬火加热温度的影响较为敏感,热应力收缩变形也最大.大截面零件=心部或靠近淬硬层处会较早地发生奥氏体向索氏体或贝氏体转变,抵制了热应力塑性收缩变形的作用,故截面尺寸增大至25mm以上,淬火加热温度对变形的影响高越小. 当淬火加热温度升高至A CM点时,淬火温度对Ms点的影响逐渐消失,故对变形的影响也逐渐减小.2.淬火加热温度对T8A钢变形的影响:T'8A与T10A,T12A同属水淬时易收缩变形的刚号,但收缩变形量不如T10A,T12A明显.其不同之处是T8A随淬火加热温度的提高而使胀大变形增加或收缩变形减小,或随淬火温度的提高,变形由收缩转各胀大.1)截面厚度不大下20mm小截面零件,在常规热处理工艺范围内,淬火后的变形基本为稍量的胀大变形,淬火温度愈高胀大变形愈大.2)截面尺寸在25mm附近的零件,较低温度加热时,变形趋向于少量收缩,随淬火温度的提高,淬火变形转向胀大,并随淬火温度的提出高胀大量增加.3))截面尺寸大于30mm的零件,淬火温度愈低收缩变形量愈大,只有当淬火温度提高警惕至接近或超过常规淬火温度上限810-820℃时,才开始出现胀大变形.4)从控制T8A变形出发,对每一具体零件的淬火温度应根据截面厚度作适当调整.5)T8A与T10A,T12A变形规律不同的实质是:T8A为共析钢,没有自由碳化物存在,提高淬火温度基本上不改变奥氏体的碳浓度,故对Ms点的影响不明显,热应力不会增加.而淬火温度提高却使淬透性增加,使心部硬度增加,强化了组织应力的作用.3.硝盐淬火时的变形:中碳钢的胀大变形可用收缩处理方法使其尺寸收缩,但对T10A,T12A的收缩变形却没有有效的方法挽救.然而,T10A,T12A钢用硝盐(KNO3 53%+NaNO2 40%+NaNO3 7%另加0.5%水)淬火时,却很少出现收缩变形,常表现出少量的胀大变形,且胀大变形量随淬火温度的而增加.当采用810-830℃加热,且截面尺寸较小,能在低温硝盐中使模口边缘淬至高硬度的模具,在硝盐中停留1-2min后转油中淬火,则在主导应力方向均表现为0.02-0.03%的胀大变形1)采用硝盐分级淬火并使零件表面和棱角淬至高硬度时,则棱角部分都是翘起的,而零件平面部分多数都表现为凹陷,这与用水淬火易收缩变形的零件表面状况正好相反,后者是棱角下塌而中间平面鼓起.两种淬火方式出现不同表面形态特征,实质是两种不同淬火冷却方式,导致零件在冷却时沿截面的各个区域组织转变先后次序发生了改变,从而改变了冷却过程中的应力作用状况和应力塑性变形方向2)水淬碳工钢在能淬透情况下,总是零件的表面或棱角首先转变为马氏体,而在用硝盐分级淬火焊,零件表面和棱角在高温共能躲过S曲线鼻部的产部分淬硬区,总是在零件从硝盐中取出后空冷或油冷时才大量转变为马氏体,但不能淬硬的过渡区和心部在表面发生转变之前在温度400-600℃时即转变为索氏体和贝氏体,在过渡区和心部相变完成比容增大的基础上,表面棱角的马氏体转变体积增大,就造成零件尺寸的少量胀大和棱角翘凸.淬火加热温度愈高,胀大变形量也随之增大.3)硝盐分级淬火时,冷却较慢,产生的热应力和热应力塑性变形都较小,故零件不易产生收缩变形.4.回火对变形的影响:回火时在淬火收缩变形的基础上继续收缩,回火温度愈高收缩变形量愈大.在240-280回火时,收缩变形率一般为0.06%左右(各种钢差别不大).5.防止变形的方法:1)淬火前弄清材料,掌握零件特征并采取措施2)选择好加热方式,防止加热快的部位出现热挤压塑性变形,采取预先热处理措施;掌握也预热和加热速度,选择好淬火加热温度.对T8A钢,厚度<15mm者加热温度宜用770-790℃;截面厚度在20-30mm者用800-820℃;厚度在30-50mm者用820-830℃,均水淬.对于硝盐和碱浴淬火电厂,一般宜用810-820℃.3)冷却方法:厚度小于30mm的冲孔较大的冲模尽可能采用硝盐.水淬时时间不宜过长(一般按每3-4mm冷却1秒),水冷后可直接转入低温硝盐继续冷却对防止裂纹和减小变形十分有利.4)回火工艺的选择5)保证一次处理合格.因每次淬火回火,特别是高温回火和正火均造成主导应力方向的收缩.6)调整淬火前加工余量.6.调质处理的影响:淬火前获得较大比容相结构的调质处理,虽能减小淬火时体积变形量,但会增大T10A,T12A 在主导应力方向的收缩变形量,淬火时在主导应力方向易产生胀大变形的中碳钢或中碳合金钢,以及比容变形和组织应力塑性胀大变形为主的钢,采用粗加工后的调质工艺对防止最终淬火时的胀大变形有一定效果. 四:过共析低合金工具钢:这类钢淬火加热后奥氏体的稳定性都较碳素钢高,热处理规范的调整,能改变奥氏体的稳定性,淬火后马氏体的比容,残留奥氏体的数量和淬硬层深度,这些因素的变化直接关系到零件淬火过程的应力作用状况及淬火后应力塑性变形和比容变形的大小.1.淬火加热温度的影响: 合金工具钢淬火温度升高时,出现胀大变形并逐渐增加.对9SiCr,CrWMn, CrMn三种钢的试验表明:1)钢在冷却过程中组织应力占主导地位,只是冷却减缓后应力作用强度减弱,故在主导应力方向产生胀大变形.变形是应力变形和比容变形的总和.2)提高淬火加热温度,主导应力方向的胀大变形增加.特别超过常用温度(三种钢分别为840;820;850)以后,胀大变形率急剧增加,由0.03-0.06%增至0.08-0.18%3)提高淬火加热温度,使马氏体比容增大,残余奥氏体量相对增加,这两个因素中,马氏体比容的增加起着主要作用.2.常用淬火冷却方法的特点:1)油冷淬火:对能基本淬透的零件,一般表现为主导应力方向的胀大变形,其中包括相当分量的比容变形.当出现淬不硬或淬不透时,则不发生胀大变形或胀大变形量很小.将油加热到80-100可作分级淬火介质(汽缸油可用到150-200),但局限性很小,故油冷不是理想方法.2)硝盐转油冷却:是一种单纯地为提高淬硬能力和淬透性的冷却方式.在马氏体转变区温差大.其胀大变形率最大:9SiCr可达0.12-0.18%, CrWMn可达0.1-0.14%, CrMn可达0.08-0.18% 3)在马氏体转变点上方分级淬火:可用来处理精度要求不很严格,硬度要求较高,又易产生弯曲变形的对称形状零件.但对不对称零件和精度要求很高的零件本工艺得不到理想结果.4)在马氏体转变区内等温淬火:对精度要求较高,硬度在HRC62以上的零件和不易淬硬的低淬透性钢的大截面零件,以及为防止胀大变形而选用较低淬火温度时,采用本工艺较合适.5)在马氏体转变点上方停留一定时间的不完全贝氏体等温淬火:用调整等温时间的方法,可控制残余奥氏体量和零件的尺寸变形.这种淬火方法适用于精度要求高,但硬度要求稍低(如HRC54-60)的零件6)贝氏体完全等温淬火:能保证相变的等时均匀进行,减小应力,对预防不对称零件的畸形变形有明显的效果.但不适于处理硬度要求大于HRC60的零件.7)先在冷却快的低温硝盐中冷却,再转入温度较高的硝盐中进行贝氏体等温转变:先入低温硝盐时,会有少量马氏体产生,其马氏体的生成会加速以后贝氏体的转变速度和转变量.8)贝氏体区或马氏体区等温后级慢冷却(常是和硝盐一起冷却):可减小等温后冷却的不均匀相变和热收缩,并使残余奥氏体量增加.适用于防止形状不对称零件的畸变和高精度零件的尺寸胀大变形.3.贝氏体等温淬火的变形:贝氏体区等温时间短时(CrWMn 5-15min; 9SiCr 5-10 min),其胀大变形量比等温时间较长的或完全贝氏体等温转变的胀大变形量小.这主要是残余奥氏体量的确良多少引起的比容变形量不同的结果.同时,等温温度较高时,等温不同时间淬火后的变形量差别较大,等温温度愈接近Ms点,等温时间对变形的影响的所减弱.需注意的是:等温淬火后若不及时回火,在室温下一定时间后将会出现尺寸的继续胀大(残余奥氏体转变的结果)4.马氏体转变区等温淬火的变形:低合金过共析钢在Ms点下方温度等温淬火,如等温时间较短,对零件的胀大变形影响较小.若将等温时间延长至45min以上,或等温后与硝盐一起缓冷,对防止胀大变形有一定效果对硬度要求高于HRC60的高精度零件,推荐如下工艺:1)选较低的加热温度:CrMn 830-840℃; CrWMn 790-810℃; 9SiCr 830-840℃; GCr15830-850℃2)淬入冷却速度快的低温硝盐中(120-140℃),等温50-60分钟,空冷或随硝盐一起缓冷.3)用不高于200℃的温度回火.5.回火时的变形:回火温度不高于200℃时,使零件尺寸收缩,收缩率多数在0.02-0.03%范围内,淬火温度较高时收缩较大,这属于单纯的比容变形. 回火温度高于200时变形逐渐转变为胀大,温度升高至260-300℃,随钢号不同分别出现胀大变形的最大值:对CrMn ,GCr15 这一峰值温度是250-280℃; 对9SiCr 则是280-320℃; 对CrWMn 则是270-290℃. 高于上述温度继续回火时,所有钢号的变形又转向尺寸收缩6:预防变形的工艺选择:1)淬火温度不宜取高2)须注意零件的胀大变形量按零件的尺寸大小按比例增加3)对低淬透性的较大截面零件,应首先设法增加淬火冷却速度,采用冷却较快的硝盐为主要手段,而将提高淬火加热温度,提高奥氏体的合金浓度和稳定性放在次要地位.4)为防止不均匀的冷却与相变形成应力变形,同时防止淬不硬,应先在冷却较快的低温硝盐中冷却,再转和主温度较高的硝盐中冷却.。