金属力学性能习题答案
材料力学性能-第2版课后习题答案

第一章 单向静拉伸力学性能1、 解释下列名词。
2.滞弹性:金属材料在弹性范围内快速加载或卸载后,随时间延长产生附加弹性应变的现象称为滞弹性,也就是应变落后于应力的现象。
3.循环韧性:金属材料在交变载荷下吸收不可逆变形功的能力称为循环韧性。
4.包申格效应:金属材料经过预先加载产生少量塑性变形,卸载后再同向加载,规定残余伸长应力增加;反向加载,规定残余伸长应力降低的现象。
11.韧脆转变:具有一定韧性的金属材料当低于某一温度点时,冲击吸收功明显下降,断裂方式由原来的韧性断裂变为脆性断裂,这种现象称为韧脆转变2、 说明下列力学性能指标的意义。
答:E 弹性模量 G 切变模量 r σ规定残余伸长应力 2.0σ屈服强度 gt δ金属材料拉伸时最大应力下的总伸长率 n 应变硬化指数 【P15】3、 金属的弹性模量主要取决于什么因素?为什么说它是一个对组织不敏感的力学性能指标?答:主要决定于原子本性和晶格类型。
合金化、热处理、冷塑性变形等能够改变金属材料的组织形态和晶粒大小,但是不改变金属原子的本性和晶格类型。
组织虽然改变了,原子的本性和晶格类型未发生改变,故弹性模量对组织不敏感。
【P4】4、 现有45、40Cr 、35 CrMo 钢和灰铸铁几种材料,你选择哪种材料作为机床起身,为什么?选灰铸铁,因为其含碳量搞,有良好的吸震减震作用,并且机床床身一般结构简单,对精度要求不高,使用灰铸铁可降低成本,提高生产效率。
5、 试述韧性断裂与脆性断裂的区别。
为什么脆性断裂最危险?【P21】答:韧性断裂是金属材料断裂前产生明显的宏观塑性变形的断裂,这种断裂有一个缓慢的撕裂过程,在裂纹扩展过程中不断地消耗能量;而脆性断裂是突然发生的断裂,断裂前基本上不发生塑性变形,没有明显征兆,因而危害性很大。
6、 何谓拉伸断口三要素?影响宏观拉伸断口性态的因素有哪些?答:宏观断口呈杯锥形,由纤维区、放射区和剪切唇三个区域组成,即所谓的断口特征三要素。
汽车材料习题集及答案

汽车材料习题集及答案目录第一章金属材料的力学性能--------------------------------(3)第二章钢铁材料----------------------------------------------------------------(4)第三章有色金属及其合金---------------------------------(8)第四章非金属材料-------------------------------------------------------------(9)第五章汽车零件的选材------------------------------------------------------(11)第六章汽车燃料---------------------------------------------------------------(11)第七章车用润滑油及特种液------------------------------------------------(13)第八章汽车轮胎---------------------------------------------------------------(15)第九章汽车美容材料---------------------------------------------------------(16)习题答案------------------------------------------------------------------------(16)第一章金属材料的力学性能一、名词解释1.金属的使用性能:1.指金属材料在正常使用条件下所具备的性能。
它包括力学、物理、化学三方面的性能2.金属的工艺性能:指机械零件在制造加工过程中,金属材料所具备的性能。
它包括铸造、压力加工、焊接、切削、热处理等加工过程中的性能。
工程材料习题册-打印-答案

第一章 金属的性能一、填空(将正确答案填在横线上。
下同)1、金属材料的性能一般分为两类。
一类是使用性能,它包括物理性能、化学性能和力学性能等。
另一类是工艺性能,它包括铸造性能、锻造性能、焊接性能和切削加工性能等。
2、大小不变或变化很慢的载荷称为静载荷,在短时间内以较高速度作用于零件上的载荷称为冲击载荷,大小和方向随时间发生周期变化的载荷称为交变载荷。
3、变形一般分为弹性变形和塑性变形两种。
不能随载荷的去除而消失的变形称为塑性变形。
4、强度是指金属材料在静载荷作用下,抵抗塑性变形或断裂的能力。
5、强度的常用衡量指标有抗拉强度和屈服强度,分别用符号σb 和σs 表示。
6、如果零件工作时所受的应力低于材料的σb 或σ0.2,则不会产生过量的塑性变形。
7、有一钢试样其截面积为100mm 2,已知钢试样的M P a S 314=σM P ab 530=σ 。
拉伸试验时,当受到拉力为—————— 试样出现屈服现象,当受到拉力为—————— 时,试样出现缩颈。
8、断裂前金属材料产生永久变形的能力称为塑性。
金属材料的延伸率和断面收缩率的数值越大,表示材料的塑性越好。
9、一拉伸试样的原标距长度为50mm,直径为10mm 拉断后试样的标距长度为79mm ,缩颈处的最小直径为4.9 mm ,此材料的伸长率为—————,断面收缩率为——————。
10.金属材料抵抗冲击载荷作用而不破坏能力。
称为冲击韧性。
11.填出下列力学性能指标的符号:屈服点σs ,抗拉强度σb ,洛氏硬度C 标尺HRC ,伸长率δ,断面收缩率ψ,冲击韧度αk ,疲劳极限σ-1。
二、判断(正确打√,错误打×。
下同)1、弹性变形能随载荷的去除而消失。
(√ )2、所有金属材料在拉伸试验时都会出现显著的屈服现象。
(× )3、材料的屈服点越低,则允许的工作应力越高。
(× )4、洛氏硬度值无单位。
(√ )5、做布氏硬度试验时,当试验条件相同时,其压痕直径越小,材料的硬度越低。
金属工艺学各章节习题、测试题(含答案)

第一部分章节习题第一章金属的力学性能一、填空题1、金属工艺学是研究工程上常用材料性能和___________的一门综合性的技术基础课。
2、金属材料的性能可分为两大类:一类叫_____________,反映材料在使用过程中表现出来的特性,另一类叫__________,反映材料在加工过程中表现出来的特性。
3、金属在力作用下所显示与弹性和非弹性反应相关或涉及力—应变关系的性能,叫做金属________。
4、金属抵抗永久变形和断裂的能力称为强度,常用的强度判断依据是__________、___________等。
5、断裂前金属发生不可逆永久变形的能力成为塑性,常用的塑性判断依据是________和_________。
6、常用的硬度表示方法有__________、___________和维氏硬度。
二、单项选择题7、下列不是金属力学性能的是()A、强度B、硬度C、韧性D、压力加工性能8、根据拉伸实验过程中拉伸实验力和伸长量关系,画出的力——伸长曲线(拉伸图)可以确定出金属的()A、强度和硬度B、强度和塑性C、强度和韧性D、塑性和韧性9、试样拉断前所承受的最大标称拉应力为()A、抗压强度B、屈服强度C、疲劳强度D、抗拉强度10、拉伸实验中,试样所受的力为()A、冲击B、多次冲击C、交变载荷D、静态力11、属于材料物理性能的是()A、强度B、硬度C、热膨胀性D、耐腐蚀性12、常用的塑性判断依据是()A、断后伸长率和断面收缩率B、塑性和韧性C、断面收缩率和塑性D、断后伸长率和塑性13、工程上所用的材料,一般要求其屈强比()A、越大越好B、越小越好C、大些,但不可过大D、小些,但不可过小14、工程上一般规定,塑性材料的δ为()A、≥1%B、≥5%C、≥10%D、≥15%15、适于测试硬质合金、表面淬火刚及薄片金属的硬度的测试方法是()A、布氏硬度B、洛氏硬度C、维氏硬度D、以上方法都可以16、不宜用于成品与表面薄层硬度测试方法()A、布氏硬度B、洛氏硬度C、维氏硬度D、以上方法都不宜17、用金刚石圆锥体作为压头可以用来测试()A、布氏硬度B、洛氏硬度C、维氏硬度D、以上都可以18、金属的韧性通常随加载速度提高、温度降低、应力集中程度加剧而()A、变好B、变差C、无影响D、难以判断19、判断韧性的依据是()A、强度和塑性B、冲击韧度和塑性C、冲击韧度和多冲抗力D、冲击韧度和强度20、金属疲劳的判断依据是()A、强度B、塑性C、抗拉强度D、疲劳强度21、材料的冲击韧度越大,其韧性就()A、越好B、越差C、无影响D、难以确定三、简答题22、什么叫金属的力学性能?常用的金属力学性能有哪些?23、什么是疲劳断裂?如何提高零件的疲劳强度?四、计算题24、测定某种钢的力学性能时,已知试棒的直径是10mm,其标距长度是直径的五倍,Fb=33.81KN,Fs=20.68KN,拉断后的标距长度是65mm。
付华-材料性能学-部分习题答案1
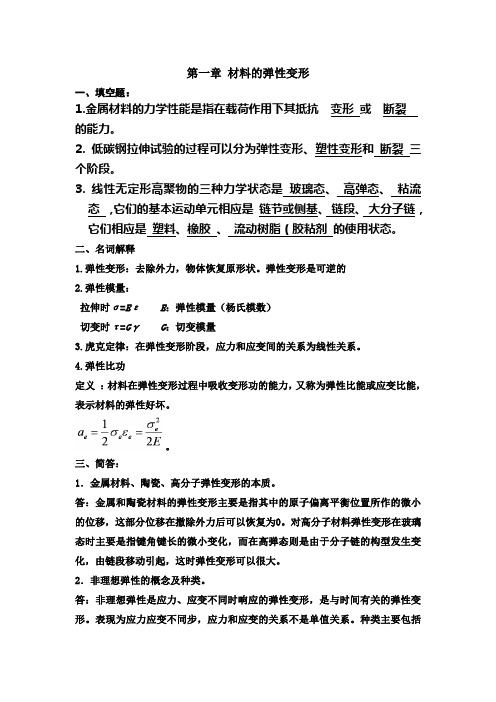
第一章材料的弹性变形一、填空题:1.金属材料的力学性能是指在载荷作用下其抵抗变形或断裂的能力。
2. 低碳钢拉伸试验的过程可以分为弹性变形、塑性变形和断裂三个阶段。
3. 线性无定形高聚物的三种力学状态是玻璃态、高弹态、粘流态,它们的基本运动单元相应是链节或侧基、链段、大分子链,它们相应是塑料、橡胶、流动树脂(胶粘剂的使用状态。
二、名词解释1.弹性变形:去除外力,物体恢复原形状。
弹性变形是可逆的2.弹性模量:拉伸时σ=EεE:弹性模量(杨氏模数)切变时τ=GγG:切变模量3.虎克定律:在弹性变形阶段,应力和应变间的关系为线性关系。
4.弹性比功定义:材料在弹性变形过程中吸收变形功的能力,又称为弹性比能或应变比能,表示材料的弹性好坏。
三、简答:1.金属材料、陶瓷、高分子弹性变形的本质。
答:金属和陶瓷材料的弹性变形主要是指其中的原子偏离平衡位置所作的微小的位移,这部分位移在撤除外力后可以恢复为0。
对高分子材料弹性变形在玻璃态时主要是指键角键长的微小变化,而在高弹态则是由于分子链的构型发生变化,由链段移动引起,这时弹性变形可以很大。
2.非理想弹性的概念及种类。
答:非理想弹性是应力、应变不同时响应的弹性变形,是与时间有关的弹性变形。
表现为应力应变不同步,应力和应变的关系不是单值关系。
种类主要包括滞弹性,粘弹性,伪弹性和包申格效应。
3.什么是高分子材料强度和模数的时-温等效原理?答:高分子材料的强度和模数强烈的依赖于温度和加载速率。
加载速率一定时,随温度的升高,高分子材料的会从玻璃态到高弹态再到粘流态变化,其强度和模数降低;而在温度一定时,玻璃态的高聚物又会随着加载速率的降低,加载时间的加长,同样出现从玻璃态到高弹态再到粘流态的变化,其强度和模数降低。
时间和温度对材料的强度和模数起着相同作用称为时=温等效原理。
四、计算题:气孔率对陶瓷弹性模量的影响用下式表示:E=E0 (1—1.9P+0.9P2)E0为无气孔时的弹性模量;P为气孔率,适用于P≤50 %。
金属材料与热处理教材习题答案

《金属材料与热处理》教材习题答案作者:陈志毅绪论1.金属材料与热处理是一门怎样的课程?答:金属材料与热处理这门课程的内容主要包括金属材料的基本知识、金属的性能、金属学基础知识和热处理的基本知识等。
2.什么是从属与从属材料?答:所谓金属是指由单一元素构成的具有特殊的光泽、延展性、导电性、导热性的物质。
如金、银、铜、铁、锰、锌、铝等。
而合金是指由一种金属元素与其它金属元素或非金属元素通过熔炼或其它方法合成的具有金属特性的材料,所以金属材料是金属及其合金的总称,即指金属元素或以金属元素为主构成的,并具有金属特性的物质。
3.怎样才能学好金属材料与热处理这门课程?答:金属材料与热处理是一门从生产实践中发展起来,又直接为生产服务的专业基础课,具有很强的实践性,因此在学习时应结合生产实际,弄清楚重要的概念和基本理论,按照材料的成分和热处理决定其组织,组织决定其性能,性能又决定其用途这一内在关系进行学习和记忆;认真完成作业和实验等教学环节,就完全可以学好这门课程的。
第一章金属的结构与结晶1.什么是晶体和非晶体?它们在性能上有什么不同?想一想,除了金属,你在生活中还见过哪些晶体?答:原子呈有序、有规则排列的物质称为晶体;而原子呈无序、无规则堆积状态的物质称为非晶体。
晶体一般具有规则的几何形状、有一定的熔点,性能呈各向异性;而非晶体一般没有规则的几何形状和一定的熔点,性能呈各向同性。
生活中常见的食盐、冰糖、明矾等都有是典型的晶体。
2.什么是晶格和晶胞?金属中主要有哪三种晶格类型?它们的晶胞各有何特点?答:假想的能反映原子排列规律的空间格架,称为晶格。
晶格是由许多形状、大小相同的小几何单元重复堆积而成的。
我们把其中能够完整地反映晶体晶格特征的最小几何单元称为晶胞。
金属中主要有体心立方晶格、面心立方晶格和密排六方晶格等三种晶格类型,体心立方晶格的晶胞是一个立方体,原子位于立方体的八个顶点和立方体的中心;面心立方晶格的晶胞也是一个立方体,原子位于立方体的八个顶点和立方体六个面的中心;密排六方晶格的晶胞是一个正六棱柱,原子除排列于柱体的每个顶点和上、下两个底面的中心外,正六棱柱的中心还有三个原子。
机械工程材料_习题集答案

作业01 力学性能 参考答案一、下列情况分别是因为哪一个力学性能指标达不到要求?1. 紧固螺栓使用后发生塑性变形。
( 屈服强度 )2. 齿轮正常负荷条件下工作中发生断裂。
( 疲劳强度 )3. 汽车紧急刹车时,发动机曲轴发生断裂。
( 冲击韧度 )4. 不锈钢圆板冲压加工成圆柱杯的过程中发生裂纹。
( 塑性 )5. 齿轮工作在寿命期内发生严重磨损。
( 硬度 )二、下列现象与哪一个力学性能有关?1. 铜比低碳钢容易被锯割。
( 硬度 )2. 锯条易被折断,而铁丝不易折断。
( 塑性 )p151-4 甲、乙、丙、丁四种材料的硬度分别为45HRC 、90HRB 、800HV 、240HBS ,试比较这四种材料硬度的高低。
答: 45HRC →HV : 90HRB →HB : 183901307300HRB 1307300HB ≈-=-=所以,800HV >45HRC >240HBS >90HRB作业02a 金属结构与结晶 参考答案一、判断题( × )1. 凡是由液体凝固成固体的过程都是结晶过程。
( × )2. 室温下,金属晶粒越细,则强度越高、塑性越低。
二、选择题( b )1. 金属结晶时,冷却速度越快,其实际结晶温度将:a. 越高b. 越低c. 越接近理论结晶温度( b )2. 为细化晶粒,可采用:a. 快速浇注b. 加变质剂c. 以砂型代金属型(c )3. 晶体中的位错属于:a. 体缺陷b. 面缺陷c. 线缺陷d. 点缺陷三、填空题1. 晶体与非晶体结构上的最根本的区别是,晶体内原子排列是:(有规则、周期性的)。
2. γ-Fe的一个晶胞原子数=(4 )。
3. α-Fe、Al、Cu、Ni、V、Mg、Zn各属何种晶体结构:体心立方:(α-Fe、V );面心立方:(Al、Cu、Ni );密排六方:(Mg、Zn )4. 实际金属晶体中存在:(点、线、面)三种缺陷,引起晶格(畸变)。
5. 结晶过程是靠两个密切联系的基本过程来实现的,它们是:(形核)和(晶核长大)。
工程材料课后习题答案

《工程材料及机械制造基础》习题参考答案第一章材料的种类与性能(P7)1、金属材料的使用性能包括哪些?力学性能、物理性能、化学性能等。
2、什么是金属的力学性能?它包括那些主要力学指标?金属材料的力学性能:金属材料在外力作用下所表现出来的与弹性和非弹性反应相关或涉及力与应变关系的性能。
主要包括:弹性、塑性、强度、硬度、冲击韧性等。
3、一根直径10mm的钢棒,在拉伸断裂时直径变为8.5mm,此钢的抗拉强度为450Mpa,问此棒能承受的最大载荷为多少?断面收缩率是多少?F=35325N ψ=27.75%4、简述洛氏硬度的测试原理。
以压头压入金属材料的压痕深度来表征材料的硬度。
5、什么是蠕变和应力松弛?蠕变:金属在长时间恒温、恒应力作用下,发生缓慢塑性变形的现象。
应力松弛:承受弹性变形的零件,在工作过程中总变形量不变,但随时间的延长,工作应力逐渐衰减的现象。
6、金属腐蚀的方式主要有哪几种?金属防腐的方法有哪些?主要有化学腐蚀和电化学腐蚀。
防腐方法:1)改变金属的化学成分;2)通过覆盖法将金属同腐蚀介质隔离;3)改善腐蚀环境;4)阴极保护法。
第二章材料的组织结构(P26)1、简述金属三种典型结构的特点。
体心立方晶格:晶格属于立方晶系,在晶胞的中心和每个顶角各有一个原子。
每个体心立方晶格的原子数为:2个。
塑性较好。
面心立方晶格:晶格属于立方晶系,在晶胞的8个顶角和6个面的中心各有一个原子。
每个面心立方晶格的原子数为:4个。
塑性优于体心立方晶格的金属。
密排六方晶格:晶格属于六方棱柱体,在六棱柱晶胞的12个项角上各有一个原子,两个端面的中心各有一个原子,晶胞内部有三个原子。
每个密排六方晶胞原子数为:6个,较脆2、金属的实际晶体中存在哪些晶体缺陷?它们对性能有什么影响?存在点缺陷、线缺陷和面缺陷。
使金属抵抗塑性变形的能力提高,从而使金属强度、硬度提高,但防腐蚀能力下降。
3、合金元素在金属中存在的形式有哪几种?各具备什么特性?存在的形式有固溶体和金属化合物两种。
金属材料与热处理(第七版)习题册 答案
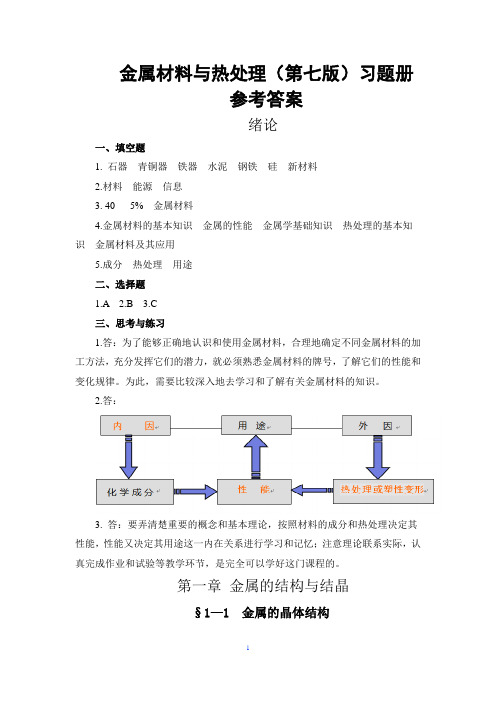
金属材料与热处理(第七版)习题册参考答案绪论一、填空题1. 石器青铜器铁器水泥钢铁硅新材料2.材料能源信息3. 40 5% 金属材料4.金属材料的基本知识金属的性能金属学基础知识热处理的基本知识金属材料及其应用5.成分热处理用途二、选择题1.A2.B3.C三、思考与练习1.答:为了能够正确地认识和使用金属材料,合理地确定不同金属材料的加工方法,充分发挥它们的潜力,就必须熟悉金属材料的牌号,了解它们的性能和变化规律。
为此,需要比较深入地去学习和了解有关金属材料的知识。
2.答:3. 答:要弄清楚重要的概念和基本理论,按照材料的成分和热处理决定其性能,性能又决定其用途这一内在关系进行学习和记忆;注意理论联系实际,认真完成作业和试验等教学环节,是完全可以学好这门课程的。
第一章金属的结构与结晶§1—1 金属的晶体结构1.非晶体晶体晶体2.体心立方面心立方密排六方体心立方面心立方密排六方3.晶体缺陷点缺陷线缺陷面缺陷二、判断题1.√ 2.√ 3.×4.×三、选择题1.A 2.C 3.C四、名词解释1.答:晶格是假想的反映原子排列规律的空间格架;晶胞是能够完整地反映晶体晶格特征的最小几何单元。
2.答:只由一个晶粒组成的晶体称为单晶体;由很多大小、外形和晶格排列方向均不相同的晶粒所组成的晶体称为多晶体。
五、思考与练习答:三种常见的金属晶格的晶胞名称分别为:(体心立方晶格)(面心立方晶格)(密排六方晶格)§1—2 纯金属的结晶一、填空题1.液体状态固体状态2.过冷度3.冷却速度冷却速度低4.形核长大5.强度硬度塑性二、判断题1.×2.×3.×4.√ 5.√6.√1.CBA 2.B 3.A 4.A四、名词解释1.答:结晶指金属从高温液体状态冷却凝固为原子有序排列的固体状态的过程。
在结晶的过程中放出的热量称为结晶潜热。
2.答:在固态下,金属随温度的改变由一种晶格转变为另一种晶格的现象称为金属的同素异构转变。
工程材料基础知识 课后习题答案

第一章工程材料根底知识参考答案1.金属材料的力学性能指标有哪些?各用什么符号表示?它们的物理意义是什么?答:常用的力学性能包括:强度、塑性、硬度、冲击韧性、疲劳强度等。
强度是指金属材料在静荷作用下抵抗破坏〔过量塑性变形或断裂〕的性能。
强度常用材料单位面积所能承受载荷的最大能力〔即应力σ,单位为Mpa〕表示。
塑性是指金属材料在载荷作用下,产生塑性变形〔永久变形〕而不被破坏的能力。
金属塑性常用伸长率δ和断面收缩率ψ来表示:硬度是指材料抵抗局部变形,特别是塑性变形、压痕或划痕的能力,是衡量材料软硬程度的指标,是一个综合的物理量。
常用的硬度指标有布氏硬度〔HBS、HBW〕、洛氏硬度〔HRA、HRB、HRC等〕和维氏硬度〔HV〕。
以很大速度作用于机件上的载荷称为冲击载荷,金属在冲击载荷作用下抵抗破坏的能力叫做冲击韧性。
冲击韧性的常用指标为冲击韧度,用符号αk表示。
疲劳强度是指金属材料在无限屡次交变载荷作用下而不破坏的最大应力称为疲劳强度或疲劳极限。
疲劳强度用σ–1表示,单位为MPa。
2.对某零件有力学性能要求时,一般可在其设计图上提出硬度技术要求而不是强度或塑性要求,这是为什么?答:这是由它们的定义、性质和测量方法决定的。
硬度是一个表征材料性能的综合性指标,表示材料外表局部区域内抵抗变形和破坏的能力,同时硬度的测量操作简单,不破坏零件,而强度和塑性的测量操作复杂且破坏零件,所以实际生产中,在零件设计图或工艺卡上一般提出硬度技术要求而不提强度或塑性值。
3.比拟布氏、洛氏、维氏硬度的测量原理及应用范围。
答:〔1〕布氏硬度测量原理:采用直径为D的球形压头,以相应的试验力F压入材料的外表,经规定保持时间后卸除试验力,用读数显微镜测量剩余压痕平均直径d,用球冠形压痕单位外表积上所受的压力表示硬度值。
实际测量可通过测出d值后查表获得硬度值。
布氏硬度测量范围:用于原材料与半成品硬度测量,可用于测量铸铁;非铁金属〔有色金属〕、硬度较低的钢〔如退火、正火、调质处理的钢〕〔2〕洛氏硬度测量原理:用金刚石圆锥或淬火钢球压头,在试验压力F 的作用下,将压头压入材料外表,保持规定时间后,去除主试验力,保持初始试验力,用剩余压痕深度增量计算硬度值,实际测量时,可通过试验机的表盘直接读出洛氏硬度的数值。
第2章习题与答案

思考题1.为什么说力学性能是机械零件设计时首先要考虑的性能?解:所谓力学性能是指金属在力或能的作用下,材料所表现出来的性能。
力学性能包括强度、塑性、硬度、冲击韧性及疲劳强度等,机械零件在加工过程或使用过程中,都要受到不同形式外力的作用,而力学性能反映了金属材料在各种外力作用下抵抗变形或破坏的某些能力,是选用金属材料的重要依据,因此是机械零件设计时首先要考虑的性能。
2.塑性和强度都是金属材料的一种能力。
金属材料的塑性对零件制造有什么特殊意义?金属材料的强度对零件使用有什么特殊意义?解:金属材料的断后伸长率(A)和断面收缩率(Z)数值越大,表示材料的塑性越好。
塑性好的金属可以发生大量塑性变形而不破坏,易于通过塑性变形加工成复杂形状的零件。
当零件工作时所受的应力,低于材料的屈服强度或规定残余延伸强度,则不会产生过量的塑性变形。
材料的屈服强度或规定残余延伸强度越高,允许的工作应力也越高,则零件的截面尺寸及自身质量就可以减小。
零件在工作中所承受的应力,不允许超过抗拉强度,否则会产生断裂。
R m也是机械零件设计和选材的重要依据。
3.通过拉伸试验绘制的力—伸长曲线表达了金属材料在静拉伸力作用下的强度行为、塑性行为等。
请就力-伸长曲线思考下列问题:(1)哪一段曲线表达了材料的弹性变形能力和抗弹性变形能力(刚度)?(2)哪一段曲线表达了材料的塑性变形能力和抗塑性变形能力?(3)哪一段曲线表达了材料的塑性变形后强度得到提高的能力(形变强化能力)?解:(1)op——弹性变形阶段(2)p点后的水平或锯齿状线段——屈服阶段(3)屈服后至m点——强化阶段4.强度判据R e L、R m、R r0.2都是机械零件选材和设计的依据,应用场合有何不同?解:R e L——有明显屈服现象的金属材料。
R r0.2——无明显屈服现象的金属材料。
R m——承受的最大应力,零件在工作中所承受的应力,不允许超过R m,否则会产生断裂。
5.抗拉强度与硬度之间有没有一定的关系?为什么?解:有。
结构设计原理 第一章 材料的力学性能 习题及答案

第一章材料的力学性能一、填空题1、钢筋混凝土及预应力混凝土中所用的钢筋可分为两类:有明显屈服点的钢筋和无明显屈服点的钢筋,通常分别称它们为____________和。
2、对无明显屈服点的钢筋,通常取相当于残余应变为时的应力作为假定的屈服点,即。
3、碳素钢可分为、和。
随着含碳量的增加,钢筋的强度、塑性。
在低碳钢中加入少量锰、硅、钛、铬等合金元素,变成为。
4、钢筋混凝土结构对钢筋性能的要求主要是、、、。
5、钢筋和混凝土是不同的材料,两者能够共同工作是因为、、6、光面钢筋的粘结力由、、三个部分组成。
7、钢筋在混凝土中应有足够的锚固长度,钢筋的强度越、直径越、混凝土强度越,则钢筋的锚固长度就越长。
8、混凝土的极限压应变包括和两部分。
部分越大,表明变形能力越,越好。
9、混凝土的延性随强度等级的提高而。
同一强度等级的混凝土,随着加荷速度的减小,延性有所,最大压应力值随加荷速度的减小而。
10、钢筋混凝土轴心受压构件,混凝土收缩,则混凝土的应力,钢筋的应力。
11、混凝土轴心受拉构件,混凝土徐变,则混凝土的应力,钢筋的应力。
12、混凝土轴心受拉构件,混凝土收缩,则混凝土的应力,钢筋的应力。
二、判断题1、混凝土强度等级是由一组立方体试块抗压后的平均强度确定的。
2、采用边长为100mm的非标准立方体试块做抗压试验时,其换算系数是0.95。
3、混凝土双向受压时强度比其单向受压时强度降低。
4、线性徐变是指徐变与荷载持续时间之间为线性关系。
5、对无明显屈服点的钢筋,设计时其强度标准值取值依据是条件屈服强度。
6、强度与应力的概念完全一样。
7、含碳量越高的钢筋,屈服台阶越短、伸长率越小、塑性性能越差。
8、钢筋应力应变曲线下降段的应力是此阶段拉力除以实际颈缩的断面积。
9、有明显流幅钢筋的屈服强度是以屈服下限为依据的。
10、钢筋极限应变值与屈服点所对应的应变值之差反映了钢筋的延性。
11、钢筋的弹性模量与钢筋级别、品种无关。
12、钢筋的弹性模量指的是应力应变曲线上任何一点切线倾角的正切。
金属材料及热处理 工程材料 试题答案

机械工程材料习题金属材料及热处理工程材料试题答案复习思考题11.写出下列力学性能符号所代表的力学性能指标的名称和含义。
、akvψ、δ5 、δb 、σ0.2 、σs 、σe、σ500 1×103、KIc、HRC、HVσ700 2/1×105、σ600 1×10-5、σ-1、σ、、HBS、E。
2.低碳钢试样在受到静拉力作用直至拉断时经过怎样的变形过程?b。
σ0.2、σ3.某金属材料的拉伸试样l0=100mm,d0=10mm。
拉伸到产生0.2%塑性变形时作用力(载荷)F0.2=6.5×103N;Fb=8.5×103N。
拉断后标距长为ll=120mm,断口处最小直径为dl=6.4mm,试求该材料的4.钢的刚度为20.7×104MPa,铝的刚度为6.9×104MPa。
问直径为2.5mm,长12cm的钢丝在承受450N的拉力作用时产生的弹性变形量(Δl)是多少?若是将钢丝改成同样长度的铝丝,在承受作用力不变、产生的弹性变形量(Δl)也不变的情况下,铝丝的直径应是多少?5.某钢棒需承受14000N的轴向拉力,加上安全系数允许承受的最大应力为140MPa。
问钢棒最小直径应是多少?若钢棒长度为60mm、E=210000MPa,则钢棒的弹性变形量(Δl)是多少? 6.试比较布氏、洛氏、维氏硬度的特点,指出各自最适用的范围。
下列几种工件的硬度适宜哪种硬度法测量:淬硬的钢件、灰铸铁毛坯件、硬质合金刀片、渗氮处理后的钢件表面渗氮层的硬度。
7.若工件刚度太低易出现什么问题?若是刚度可以而弹性极限太低易出现什么问题? 8.指出下列硬度值表示方法上的错误。
12HRC~15HRC、800HBS、58HRC~62HRC、550N /mm2HBW、70HRC~75HRC、200N/mm2HBS。
5≥26%。
现对进厂的一批Q235钢材采用d0=10mm的标准短试样进行拉伸试验,测得的试验数据是Fs=20KN,断后标距长lk=65mm。
工程材料习题集参考答案(第一章)

习题集部分参考答案吴超华老师提供1工程材料的分类与性能思考题1.写出下列力学性能符号所代表的力学性能指标的名称和含义。
答:σe: 弹性极限,试样发生最大弹性变形时对应的应力值。
σs: 屈服强度(屈服点),试样拉伸中载荷达到S点后,发生屈服现象,S点对应的应力值称为屈服强度。
σ0.2: 试验产生0.2%的残余塑性变形时对应的屈服强度σb: 抗拉强度,试样在断裂前所能承受的最大应力。
σ-1: 疲劳强度,材料经无数次交变载荷作用而不致引起断裂的最大应力值。
δ: 伸长率,试样拉断后的标距伸长量与原始标距之比。
φ: 收缩率,试样拉断处横截面积的收缩量与原始横截面积之比。
α冲击韧性,材料在冲击载荷作用下抵抗破坏的能力。
KV:HRC: 洛氏硬度,在洛氏硬度计上,将顶角为1200的金刚石圆锥体或直径为1.588mm的淬硬钢球压头在一定载荷F的作用下压入被测材料的表面,然后根据压痕的深度来测量所得的硬度值。
HV: 维氏硬度,将顶角为1360的正四棱锥金刚石压头以一定的载荷压入试样表面并保持一定的时间后卸除试验力,所使用的载荷与试样表面上形成的压痕的面积之比。
HBS: 布氏硬度,用一直径为D的标准钢球,以一定压力P将球在被测金属表面上经T 秒后,撤去压力,由于塑性变形,在材料表面形成一个凹印,用这个凹印的球形面积去除压力P,由所得值表示材料硬度。
2.低碳钢试验在受到静拉力作用直至拉断时经过怎样的变形过程?答:先是弹性变形阶段(Oe段);然后是屈服阶段(es段);再是强化阶段(sb段);最后是缩颈阶段(bk段)。
如图1所示。
3.3. 通常把工程材料分为哪几类?各举二个例子。
答:工程材料一般分为金属材料、非金属材料和复合材料。
金属材料如汽车发动机的缸体、连杆、活塞和气门等。
非金属材料如各种塑料(公交车上的塑料座椅、汽车驾驶台的塑料面板和各种塑料玩具等)、橡胶(汽车轮胎、密封条等)、陶瓷(花瓶、唐三彩、瓷碗等)。
复合材料如碳纤维、玻璃钢和风力机叶片等。
材料力学性能学练习习题及答案

答:高分子材料的强度和模数强烈的依赖于温度和加载速率。加载速率一定时, 随温度的升高,高分子材料的会从玻璃态到高弹态再到粘流态变化,其强度和 模数降低;而在温度一定时,玻璃态的高聚物又会随着加载速率的降低,加载 时间的加长,同样出现从玻璃态到高弹态再到粘流态的变化,其强度和模数降 低。时间和温度对材料的强度和模数起着相同作用称为时=温等效原理。 四、计算题:
cos cos
( 1) [001]方向与[111]滑移方向的夹角 λ:
cos
12 12 12
2 2 2 12 12 12 2 2 2
0 1 0 1 1 1 1 1 111 3
[001]方向与 (110) 面法线方向夹角 υ:
0 1 0 1 1 1 1 1 111 3
cos cos 70
1 1 28.6MPa 2 3
在 (111)面上的 [101] 方向的分切应力应为 28.6Mpa。 [001]方向与 [110] 滑移方向的夹角 λ:
cos
12 12 12
1.金属单晶体的塑性变形方式。 答滑移和孪生 2.什么是滑移系?产生晶面滑移的条件是什么?写出面心立方金属在室温下所 有可能的滑移系。 答:滑移系是一个滑移面和该面上一个滑移方向的组合。产生晶面滑移 的条件是在这个面上的滑移方向的分切应力大于其临界分切应力。 3.试述Zn、 α -Fe、Cu等几种金属塑性不同的原因。 答:Zn、α -Fe、Cu这三种晶体的晶体结构分别是密排六方、体心立方和面心立 方结构。 密排六方结构的滑移系少,塑性变形困难,所以 Zn的塑性差。 面心立方结构滑移系多,滑移系容易开动,所以对面心立方结构的金属Cu塑性 好。 体心立方结构虽然滑移系多,但滑移面密排程度低于 fcc,滑移方向个数少,较 难开动,所以塑性低于面心立方结构材料,但优于密排六方结构晶体,所以α -Fe的塑性较 Cu差,优于Zn。 4.孪晶和滑移的变形机制有何不同? 答:主要的不同1)晶体位向在滑移前后不改变,而在孪生前后晶体位向改变, 形成镜面对称关系。2)滑移的变形量为滑移方向原子间距的整数倍,而孪生过 程中的位移量为孪生方向的原子间距的分数倍。3)滑移是全位错运动的结果而 孪生是分位错运动的结果。 5.什么是应变硬化?有何实际意义? 答:随着应变量的增加,让材料继续变形需要更大的应力,这种现象称为应变 硬化。随变形量的增加,材料的强度、硬度升高而塑性、韧性下降的
金属材料的力学性能练习题与答案

金属材料的力学性能练习题与答案1.下列关于韧性的说法,不正确的是A.韧性是金属材料在断裂前吸收变形能量的能力B.金属材料韧性的大小通常采用吸收能量 K 指标来衡量C.冲床的冲头要求具有足够的强度、塑形、硬度外,还要有足够的韧性D.韧性好的材料塑性一般不好(正确答案)2.下列零件可用布氏硬度HBW来测定硬度值的是()A.淬火轴B.硬质合金刀片C.铸铁底座(正确答案)D.渗碳淬火齿轮3.低碳钢拉伸实验时,首先经历的阶段是()A.弹性变形阶段(正确答案)B.屈服阶段C.强化阶段D.缩颈阶段4.拉伸试验中,拉伸试样拉断前所能承受的最大标称应力是()A.屈服强度B.抗拉强度(正确答案)C.抗压强度D.弯曲强度5.压入法测定成品或半成品的零件硬度,应采用的测定方法是()A.维氏硬度B.洛氏硬度(正确答案)C.布氏硬度D.莫氏硬度6.某金属的耐磨性好,说明该金属的哪项力学性能较好()A.强度B.塑性C.硬度(正确答案)D.韧性7.压入法检验成品或半成品的零件硬度,应采用的测定方法是()A.维氏硬度B.洛氏硬度(正确答案)C.布氏硬度D.莫氏硬度8.低碳钢棒料拉伸试验过程中,最大拉伸力出现在()A.弹性变形阶段B.屈服阶段C.变形强化阶段(正确答案)D.缩颈与断裂阶段9.下列符号中,用来表示塑性力学性能指标的是()A.RLB.KC.Z(正确答案)D.Rm10.按照国家规定,从2013年起,小汽车行使60万公里后会引导报废,这主要是考虑材料的()A.强度B.疲劳强度(正确答案)C.硬度D.韧性11.金属材料在交变载荷作用下,经受无限多次循环而不断裂的能力称为()A.疲劳强度(正确答案)B.硬度C.强度D.塑性12.用拉伸试验测定材料的强度时,试样承受的载荷是()A.交变载荷B.静载荷(正确答案)C.冲击载荷D.动载荷13.反映金属材料塑性的两个指标一般是指()A.屈服点和比例极限B.弹性极限和屈服点C.强度极限和断口收缩率D.伸长率和断面收缩率(正确答案)14表示塑性力学性能指标的符号是()A.RmB.HRC.KD.Z(正确答案)15.关于金属材料强度指标说法正确的是()A.强度是金属材料在静载荷作用下,抵抗变形和破坏的能力(正确答案) B.强度是金属材料在静载荷作用下产生永久变形的能力C.强度是金属材料抵抗其它更硬物体压入其表面的能力D.强度是金属材料抵抗冲击载荷而不破坏的能力16.下列不属于金属材料工艺性能指标的是()A.热膨胀性(正确答案)B.锻造性C.铸造性D.焊接性17.金属材料抵抗比它更硬的物体压入其表面的能力是()A.强度B.韧性C.塑性D.硬度(正确答案)18.金属材料在静载荷作用下抵抗变形和破坏的能力是()A.强度(正确答案)B.硬度C.塑性D.韧性19.Rm表示试样________所承受的最大拉应力。
- 1、下载文档前请自行甄别文档内容的完整性,平台不提供额外的编辑、内容补充、找答案等附加服务。
- 2、"仅部分预览"的文档,不可在线预览部分如存在完整性等问题,可反馈申请退款(可完整预览的文档不适用该条件!)。
- 3、如文档侵犯您的权益,请联系客服反馈,我们会尽快为您处理(人工客服工作时间:9:00-18:30)。
第一单元3.【提示】可从取样和加工两个方面分别加以阐述。
8.高碳钢力-伸长曲线上没有屈服阶段,而且在产生少量均匀塑性变形后就突然断裂。
10.实质上都表示材料对微量塑性变形的抗力,区别是:①各性能指标的物理意义不同,②对残余塑性变形量的要求不同,R p要求的残余延伸率最小,③测试方式的区别,有的是了加载时测量的,而有的是卸载时测量的。
11.弹性极限为精密弹簧以及不允许产生任何微量塑性变形等零件的失效抗力指标。
屈服强度是工程技术上重要的力学性能指标之一,也是大多数机械零件或工程构件选材和设计的依据。
抗拉强度脆性材料设计和选材的主要指标。
19. R eL=400MPa,R m=600MPa,A=24%,Z=47%。
这批钢材合格。
第二单元3.选择灰铸铁,因为灰铸铁具有良好的消振性和抗压强度。
4.(1)能明显地显示脆性或低塑性材料的塑性,适合评定铸铁、硬质合金、工具钢等材料的抗弯强度和塑性。
(2)试样表面应力最大、中心为零,可以较灵敏地反映材料的表面缺陷情况。
(3)对试样的要求比拉伸时宽松,操作简单。
7.进行缺口试样轴向静拉伸试验,测定NSR。
低碳钢对缺口不敏感。
高碳钢对缺口比较敏感,表面缺口处成应力集中,因材料不存在屈服,当缺口附近最大应力值达到材料的抗拉强度时,便产生断裂。
铸铁虽也属脆性材料,但由于其内部组织中有夹渣、气孔及石墨存在,其内部组织的不均匀性已远大于外部应力集中的影响,而工件表面截面形状的改变反而不会对构件承载能力造成明显的影响,所以对缺口不敏感。
8. 【提示】缺口强化。
10. (1) 渗碳层的硬度分布—HRC或HV;(2) 淬火钢—HRC;(3) 灰铸铁—HBW;(4) 鉴别钢中的隐晶马氏体与残余奥氏体—显微维氏硬度;(5) 仪表小黄铜齿轮—HRB;(6) 龙门刨床导轨—HS或HL;(7) 渗氮层—HV或HK;(8) 高速钢刀具—HRC;(9) 退火态低碳钢—HBW;(10)硬质合金—HRA或HV。
11. 低碳钢——单向拉伸、布氏硬度;灰铸铁——单向压缩、布氏硬度;高碳工具钢——弯曲或扭转试验,洛氏硬度。
第三单元3.开缺口——Q345、60Si2Mn、40Cr、20CrMnTi、HPb59-1。
不开缺口——Cr12MoV 、HT200。
5. 因为冲击吸收能量K 值不仅决定于材料本身,同时还随试样缺口的形状和尺寸、加工精度和试验温度等因素在很大范围内变化。
同时,摆锤冲击试验时所消耗的能量不是全部用于试样变形和断裂,故冲击吸收能量K 值并不能正确代表材料所吸收的冲击能量。
在冲击载荷下的机器零件很少是受大能量一次冲击而破坏,这时强度较高而冲击韧性较低的材料寿命较长。
因此在一次冲断条件下确定的冲击吸收能量K 值只能作为设计和选材的参考性指标。
6.(1)试样的取样位置与加工精度;(2)试验机的工作状况;(3)试样放置的准确性;(4)试验温度;(5)安全。
7. 焊接结构的刚性大,整体性强,如结构中存在应力集中区,往往诱发裂纹,一旦裂9. 【提示】可在坐标纸上描点绘制曲线图,也可采用office 办公软件中的Excel 制作曲线图。
随温度降低,钢的冲击吸收能量下降,存在明显的冷脆现象。
在-25℃~-50℃下降最快,此温度区间为韧脆转变温度。
第四单元 3. 韧性断裂的特征是断裂前发生明显的宏观塑性变形,脆性断裂的特征是断裂前基本上不发生明显的塑性变形,脆断时承受的工作应力很低,一般低于材料的屈服强度,没有明显征兆,因而危害性很大。
4. 断裂前基本不发生塑性变形,断面收缩率Z <5%,无明显前兆; 断口与正应力垂直。
断口平齐光亮,常呈放射状或结晶状;人字纹花样的放射方向与裂纹扩展方向平行。
断面放射状条纹汇聚于一个中心,这个中心区域就是裂纹源。
无缺口的板状矩形拉伸试样,人字形花样中“人”字的尖端指向裂纹源。
5. 应力腐蚀、氢脆、回火脆性、淬火裂纹、磨削裂纹等大都属于沿晶断裂。
沿晶断裂的断口形貌特征是冰糖状花样。
7. 解理断裂是以极快速率沿一定晶体学平面产生的穿晶断裂,解理面一般是指低指数晶面或表面能量低的晶面。
大部分解理断裂属于脆性断裂,其断口形貌特征为河流花样。
8. 韧窝大而深——材料基体塑性高,第二相粒子少。
韧窝大而浅——材料基体塑性低,第二相粒子少。
韧窝小而深——材料基体塑性高,第二相粒子多。
韧窝小而浅——材料基体塑性低,第二相粒子多。
9. K I 表示裂纹尖端附近应力场的强弱程度,故称为应力场强度因子,K I 越大,则应力场各应力分量也越大。
K 判据的意义: K 判据是工程设计中防止低应力脆断的重要依据,它将材料断裂韧度与零构件的工作应力及裂纹尺寸的关系定量地联系起来了,因此可以直接用于设计计算。
K 判据可以应用在以下三个方面:① 确定裂纹失稳扩展时的临界尺寸,为探伤质量验收提供理论依据;② 确定零构件的最大承载能力;③ 确定零构件的安全性或为选择材料提供理论依据。
13. 5.159101014.39003=⨯⨯⨯==-a K I πσMPa·m 1/2>115MPa·m 1/2 该件不安全。
14. 先确定屈服强度R eL :[σ]= R eL /n →R eL =[σ]×n =900×1.4=1260 MPa选 R eL =1300 MPa 。
再计算K I ,然后确定K IC :32.7110214.39003=⨯⨯⨯==-a K I πσ MPa·m 1/2 (注意:题中给出的条件是a = 2mm ,直接代入公式即可,不要再除以2)根据K I < K IC ,选择K IC =75 MPa·m 1/2综上,应选择R eL =1300 MPa 、K IC =75 MPa·m 1/2的材料。
第五单元3. (1)疲劳是低应力循环延时断裂,即具有寿命的断裂。
(2)疲劳是脆性断裂,疲劳的应力水平比屈服强度低,在断裂前不会发生塑性变形及有形变预兆。
(3)疲劳对表面缺陷(缺口、裂纹及组织缺陷)十分敏感。
(4))疲劳断口特征非常明显,能清楚地显示出裂纹的发生、发展和最后断裂三个组成部分。
4. 疲劳断裂的宏观断口一般由疲劳裂纹产生区(裂纹源)、裂纹扩展区和最后断裂区三个区域组成。
裂纹源一般在机件表面的薄弱区,常与缺口、裂纹、刀痕、蚀坑等缺陷相连,由于应力集中会引发疲劳裂纹。
从断口形貌看,疲劳源区的光亮度最大。
裂纹扩展区比较光滑并分布有贝纹线(或海滩花样)。
最后断裂区比裂纹扩展区粗糙,同静载的裂纹件的断口一样,对于塑性材料,断口为纤维状,暗灰色,而对脆性材料则是结晶状。
6.可以。
7.高周疲劳交变应力水平较低,往往低于材料的屈服强度,产生的只是弹性变形,塑性变形很小,高周疲劳寿命则决定于应力幅。
低周疲劳交变应力水平较高,往往接近或超过材料的屈服强度,因而是在塑性应变循环下引起的疲劳断裂,低周疲劳寿命决定于塑性应变幅。
8.改进工件结构设计,减小应力集中。
提高零件表面加工质量,并应尽量减少表面缺陷和表面加工损伤。
进行表面强化处理。
提高材料冶金质量,细化晶粒,进行合理的热处理等。
火和化学热处理等。
9. (1)可用Excel作图。
(2)从图上可知,N=5 × 107强度为150MPa。
(3)从图上可知,应力幅值为250时的疲劳寿命为6×105次循环。
第六单元3.判断方法:征进行判断。
(1(2以是穿晶断裂,也可以是晶间断裂。
如果是穿晶断裂,其断口是解理或准解理的,其裂纹有似人字形或羽毛状的标记。
5. (1)实验室中识别氢脆与应力腐蚀的办法是,当施加一小的阳极电流,如使开裂加速,则为应力腐蚀;而当施加一小阴极电流,使开裂加速者则为氢脆。
(2) 氢脆断口上一般没有腐蚀产物或者其量极微,主裂纹没有分枝。
(3)大多数的氢脆断裂(氢化物的氢脆除外),都表现出对温度和形变速率有强烈的依赖关系。
8.应力腐蚀断裂。
对螺栓进行防腐处理或进行电化学保护。
第七单元2.摩擦是原因,磨损是结果。
磨损过程(略)。
4.参考表7-1。
5.参考表7-1。
6.磨损试验特点:影响因素多,需要试样数量多,试验时间长,试验结果数值分散,重现性差。
第八单元3.(1)随温度升高,强度降低而塑性增加。
(2)在高温下载荷持续时间对力学性能产生影响,在同样温度下,强度随着载荷保持时间的增长而降低。
(3)高温应力松弛。
(4)温度升高时晶粒强度和晶界强度都要下降且晶界强度下降较快,在等温强度T E以上工作时,金属的断裂便由常见的穿晶断裂过渡到沿晶断裂。
4. 金属的蠕变变形主要通过位错滑移、原子扩散等机理进行,一是位错滑移蠕变,二是扩散蠕变。
与温度、应力和时间的变化有关。
5.使用温度高于等强温度时,粗晶粒钢有较高的蠕变极限和持久强度极限,但晶粒太大会降低高温下的塑性与韧性,对于耐热钢及合金来说,随合金成分及工作条件不同有一最佳晶粒度范围。
如晶粒度不均匀,会显著降低其高温性能,这是由于在大小晶粒交界处易产生应力集中形成裂纹。
8.产生了应力松驰。
9. 【提示】阻止刃型位错的攀移,控制晶界的滑动,以及阻止空位的形成与运动,从而阻止其扩散。
具体方法可从合金的化学成分、冶炼工艺、热处理工艺和晶粒度等方面出发进行论述。
MPa10.(1)【提示】根据题目所给数据,在应力-时间双对数坐标图上描点,再将试验数据点回归成直线,即持久强度曲线。
也可采用Excel作图。
600℃和810℃持久强度曲线如下图所示。
(2)810℃,经受2000h的持久强度极限为97 MPa。
(3)用外推法求600℃,20000h的持久强度,约为295 MPa,见下图中虚线段圆点处。
设安全系数n=3,其许用应力为:295/3≈98 MPa第九单元1. (1) 试验过程与材料的加工或使用条件相似。
(2)试验结果的评定是以受力后表面变形情况来考核材料的优劣。
因此,试验结果能反映出材料的塑性、韧性及部分质量问题。
(3) 试样加工容易。
工程中常用的金属工艺试验包括金属弯曲试验、杯突试验、顶锻试验,金属线材扭转试验、反复弯曲试验和金属管试验等。
2. 对直径或多边形横截面内切圆直径不大于50mm的材料,试样横截面与原材料相同。
直径或多边形内切圆直径大于50 mm的材料,应将其加工成横截面内切圆直径不小于25mm 的试样,并保留一侧原表面。
对于板材,当原材料的宽度不大于20mm时,试样宽度为原材料的宽度;当材料宽度大于20 mm,厚度小于3mm的板材,试样宽度为(20±5)mm;厚度不小于3 mm的板材,试样宽度在20 ~50 mm之间。
当板材其厚度不大于25 mm时,试样厚度应为原材料厚度;材料厚度大于25mm时,试样厚度可以机加工减薄至25 mm,并保留一侧原表面。