储罐工厂预制和现场组焊技术方案
储罐施工方案
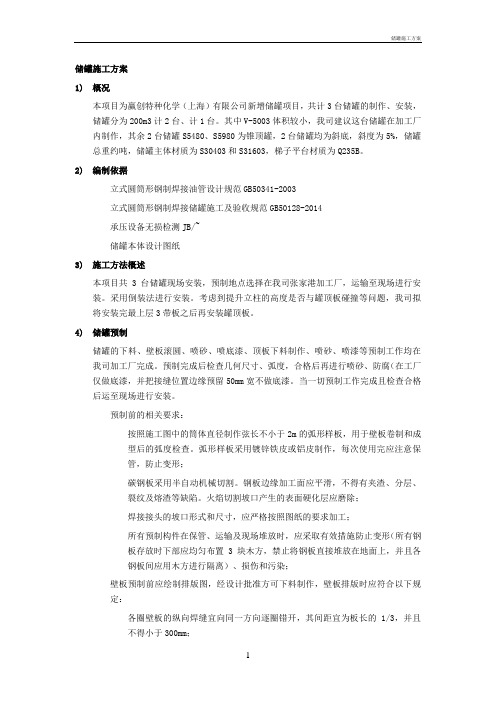
储罐施工方案1) 概况本项目为赢创特种化学(上海)有限公司新增储罐项目,共计3台储罐的制作、安装,储罐分为200m3计2台、计1台。
其中V-5003体积较小,我司建议这台储罐在加工厂内制作,其余2台储罐S5480、S5980为锥顶罐,2台储罐均为斜底,斜度为5%,储罐总重约吨,储罐主体材质为S30403和S31603,梯子平台材质为Q235B。
2) 编制依据立式圆筒形钢制焊接油管设计规范GB50341-2003立式圆筒形钢制焊接储罐施工及验收规范GB50128-2014承压设备无损检测JB/~储罐本体设计图纸3) 施工方法概述本项目共3台储罐现场安装,预制地点选择在我司张家港加工厂,运输至现场进行安装。
采用倒装法进行安装。
考虑到提升立柱的高度是否与罐顶板碰撞等问题,我司拟将安装完最上层3带板之后再安装罐顶板。
4) 储罐预制储罐的下料、壁板滚圆、喷砂、喷底漆、顶板下料制作、喷砂、喷漆等预制工作均在我司加工厂完成。
预制完成后检查几何尺寸、弧度,合格后再进行喷砂、防腐(在工厂仅做底漆,并把接缝位置边缘预留50mm宽不做底漆。
当一切预制工作完成且检查合格后运至现场进行安装。
预制前的相关要求:按照施工图中的筒体直径制作弦长不小于2m的弧形样板,用于壁板卷制和成型后的弧度检查。
弧形样板采用镀锌铁皮或铝皮制作,每次使用完应注意保管,防止变形;碳钢板采用半自动机械切割。
钢板边缘加工面应平滑,不得有夹渣、分层、裂纹及熔渣等缺陷。
火焰切割坡口产生的表面硬化层应磨除;焊接接头的坡口形式和尺寸,应严格按照图纸的要求加工;所有预制构件在保管、运输及现场堆放时,应采取有效措施防止变形(所有钢板存放时下部应均匀布置3块木方,禁止将钢板直接堆放在地面上,并且各钢板间应用木方进行隔离)、损伤和污染;壁板预制前应绘制排版图,经设计批准方可下料制作,壁板排版时应符合以下规定:各圈壁板的纵向焊缝宜向同一方向逐圈错开,其间距宜为板长的1/3,并且不得小于300mm;任意壁板宽带不得小于1000mm;底圈壁板的纵向焊缝与罐底边缘板对接焊缝之间的距离,不得小于300mm;开孔接管或补强板外缘与罐壁纵焊缝之间的距离,不应小于150mm;与罐壁环焊缝的距离不得小于壁板厚度的倍,且不应小于75mm;包边角钢对接接头与壁板纵向焊缝之间的距离不得小于200mm;壁板上连接件的垫板周边焊缝与壁板纵焊缝或接管补强圈的边缘角焊缝之间的距离,不应小于150 mm,与罐壁环缝之间的距离不应小于75 mm,如不可避免与罐壁焊缝交叉时,被覆盖焊缝应磨平并进行射线或超声波检测,垫板角焊缝在罐壁对接焊缝两侧边缘最少20 mm不焊;壁板下料尺寸允许偏差应符合下表:测量部位允许偏差mm宽度AC、BD、EF±1长度AB、CD±对角线之差∣AD—BC∣≤2直线度AC、BD≤1 AB、CD≤2Figure 1图1壁板下料采用半自动切割和机械切割,严格控制切割精度,使满足规范规定标准,其纵、环缝坡口加工应符合设计图纸要求,确保组对和焊接质量;壁板卷制壁板滚圆前,在滚床上放入压头板将壁板两端进行预弯曲;将卷好的壁板放置在专用胎具上,胎具采用[14a制作。
(建筑工程管理)球罐现场组焊施工方案(安装公司审核版

眉山市奥新能源技术有限公司8万吨/年丙烯工程球罐现场组焊施工方案编制单位:眉山奥新能源项目部编制人:审核人:批准人:编制日期: 年月日中建安装工程有限公司眉山奥新8万吨/年丙烯项目球罐现场组焊施工方案印号:(盖章受控)版本:第一版发布日期:年月日目录第一章编制依据 (1)1.1 眉山奥新能源技术有限公司8万吨/年丙烯工程装置平面布置图和球罐单体图 (1)1.2 本工程所采用的施工规范 (1)1.3 编制原则 (1)第二章分部分项工程概况 (2)第三章主要施工方法及技术要求 (3)3.1 主要施工程序 (3)3.2主要施工方法及技术要求 (5)3.3球罐焊接 (22)3.4热处理前的无损检测 (27)3.5球罐热处理 (28)3.6平台、喷淋装置的制作与安装 (33)3.7水压试验 (33)3.8水压试验后的无损检测 (35)3.9气密性试验 (35)3.10涂漆施工 (36)3.11验收 (38)第四章技术复核内容及方法 (38)第五章劳动力组织 (39)5.1 劳动力投入计划 (39)5.2 劳动力供应保障措施 (40)第六章材料、设备等供应计划 (41)6.1 主要施工机具一览表 (41)中建安装工程有限公司眉山奥新8万吨/年丙烯项目球罐现场组焊施工方案6.2计量检测器具一览表 (46)6.3施工机械保障措施 (47)第七章工期安排及保证措施 (48)7.1确保工期的施工准备措施 (48)7.2确保工期的技术措施 (48)7.3确保工期的计划管理措施 (49)第八章质量标准及保证措施 (53)8.1 质量控制点设置 (53)8.2质量管理措施 (54)8.3 质量通病的控制 (55)8.4 成品保护 (56)第九章安全防护措施 (57)9.1组织管理措施 (57)9.2球罐吊装安全措施 (58)9.3脚手架安全技术措施 (59)9.4现场高处作业的安全措施 (60)9.5施工用电管理措施 (61)9.6防火防爆炸安全管理 (63)中建安装工程有限公司眉山奥新8万吨/年丙烯项目球罐现场组焊施工方案9.7预热安全措施 (64)9.8焊接安全措施 (64)9.9气刨安全措施 (65)9.10打磨安全措施 (66)9.11无损探伤安全措施 (66)9.12耐压强度试验安全措施 (67)9.13气密性试验安全措施 (67)9.14油漆防腐安全措施 (68)9.15有限空间作业 (68)第十章节能减排及绿色施工 (69)10.1 节能措施 (69)10.2 节材与材料资源利用措施 (70)10.3 环境保护措施 (70)10.4 节水与水资源利用 (71)10.5 节地与土地资源保护 (71)中建安装工程有限公司眉山奥新8万吨/年丙烯项目球罐现场组焊施工方案中建安装工程有限公司眉山奥新8万吨/年丙烯项目球罐现场组焊施工方案第一章编制依据1.1 眉山奥新能源技术有限公司8万吨/年丙烯工程装置平面布置图和球罐单体图1.2 本工程所采用的施工规范1.2.1《固定式压力容器安全技术监察规程》 TSG R0004-20091.2.2《钢制球形储罐》 GB12337-2010;1.2.3《压力容器》 GB150—2011;1.2.4《球形储罐施工及验收规范》GB50094-2010;1.2.5《锅炉和压力容器用钢板》 GB713-2008;1.2.6《施工现场临时用电安全技术规范》JGJ46-2005;1.2.7《承压设备无损检测》 JB/T4730-20051.2.8《压力容器涂敷与运输包装》JB/T4711-20031.2.9《建筑施工扣件式钢管脚手架安全技术规范》JGJ130-20111.2.10《石油化工建设工程施工安全技术规范》GB50484-20081.2.11《建筑施工高处作业安全技术规范》JGJ80-911.3 编制原则1.3.1认真贯彻国家工程建设的法律、法规、规程、方针和政策。
储罐施工方案
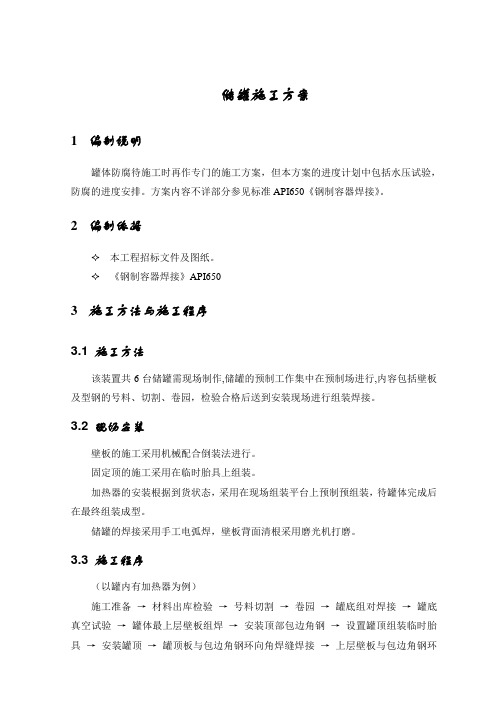
储罐施工方案1编制说明罐体防腐待施工时再作专门的施工方案,但本方案的进度计划中包括水压试验,防腐的进度安排。
方案内容不详部分参见标准API650《钢制容器焊接》。
2编制依据✧本工程招标文件及图纸。
✧《钢制容器焊接》API6503施工方法与施工程序3.1 施工方法该装置共6台储罐需现场制作,储罐的预制工作集中在预制场进行,内容包括壁板及型钢的号料、切割、卷园,检验合格后送到安装现场进行组装焊接。
3.2 现场安装壁板的施工采用机械配合倒装法进行。
固定顶的施工采用在临时胎具上组装。
加热器的安装根据到货状态,采用在现场组装平台上预制预组装,待罐体完成后在最终组装成型。
储罐的焊接采用手工电弧焊,壁板背面清根采用磨光机打磨。
3.3 施工程序(以罐内有加热器为例)施工准备→材料出库检验→号料切割→卷园→罐底组对焊接→罐底真空试验→罐体最上层壁板组焊→安装顶部包边角钢→设置罐顶组装临时胎具→安装罐顶→罐顶板与包边角钢环向角焊缝焊接→上层壁板与包边角钢环向角焊缝焊接→临时支架拆除→组装焊接壁板直至最下层壁板→最下层壁板与罐底角缝先内后外焊接→储罐梯子平台预制安装→罐内加热器安装试压→检查验收4施工质量要求及保证措施本工程的质量重点是焊接及焊接变形的控制。
4.1 材料验收储罐制作所用材料的附件,应具有质量合格证明书。
建造储罐所用钢板应逐张进行外观检查,表面质量应符合现行相应钢板标准的规定。
储罐所用焊接材料应具有质量合格证明书。
4.2 预制钢板切割及坡口加工应符合下列规定:1)钢板的切割采用半自动火焰切割加工,弧形边缘加工手工火焰切割加工。
2)钢板焊接接头的坡口形式采用V型坡口,V型坡口加工用角向磨光机进行。
3)所有预制件在保管、运输及现场堆放时素材下垫置道木且要垫平,弧形预制件应放在胎具上,防止变形、损伤、锈蚀。
4.2.1壁板预制壁板预制应根据材料实际尺寸绘制排版图,并符合下列规定:1)各圈壁板的纵向焊缝宜向同一方向逐圈错开板长的1/3,最小距离500mm以上。
大型储罐制作安装施工方案

新能能源甲醇中间罐区储罐制作安装施工方案编制:审核:批准:新能能源工程项目部2007年11月20日目录1、工程概况.................................... 错误!未定义书签。
工程简介..................................... 错误!未定义书签。
2、编制说明及编制依据.......................... 错误!未定义书签。
编制说明..................................... 错误!未定义书签。
编制依据..................................... 错误!未定义书签。
3、施工准备..................................... 错误!未定义书签。
施工现场准备................................. 错误!未定义书签。
施工技术准备................................. 错误!未定义书签。
基础验收..................................... 错误!未定义书签。
材料验收.................................... 错误!未定义书签。
施工顺序..................................... 错误!未定义书签。
4、储罐的预制................................... 错误!未定义书签。
预制技术要求................................. 错误!未定义书签。
底板的预制................................... 错误!未定义书签。
壁板的预制................................... 错误!未定义书签。
固定顶顶板预制............................... 错误!未定义书签。
储油罐制作施工方案
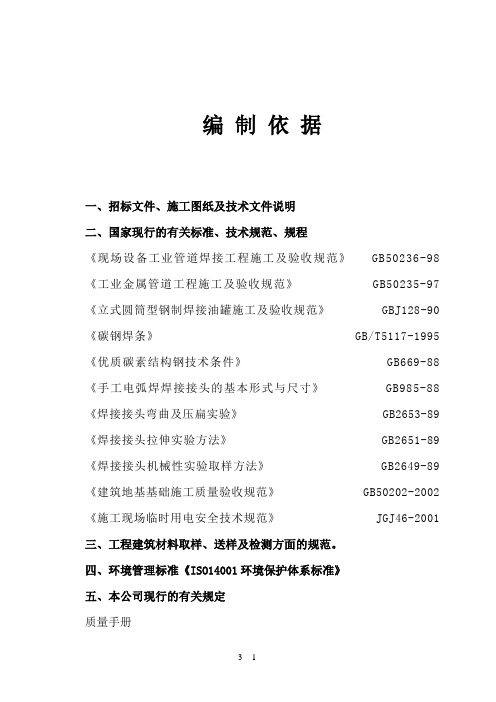
编制依据一、招标文件、施工图纸及技术文件说明二、国家现行的有关标准、技术规范、规程《现场设备工业管道焊接工程施工及验收规范》 GB50236-98 《工业金属管道工程施工及验收规范》 GB50235-97 《立式圆筒型钢制焊接油罐施工及验收规范》 GBJ128-90 《碳钢焊条》 GB/T5117-1995 《优质碳素结构钢技术条件》 GB669-88 《手工电弧焊焊接接头的基本形式与尺寸》 GB985-88 《焊接接头弯曲及压扁实验》 GB2653-89 《焊接接头拉伸实验方法》 GB2651-89 《焊接接头机械性实验取样方法》 GB2649-89 《建筑地基基础施工质量验收规范》 GB50202-2002 《施工现场临时用电安全技术规范》 JGJ46-2001三、工程建筑材料取样、送样及检测方面的规范。
四、环境管理标准《ISO14001环境保护体系标准》五、本公司现行的有关规定质量手册质量体系控制程序文件工程施工操作规范相应的工艺文件第三章施工方案一、施工原则:根据本工程的特点及工期要求,确定原则如下:1、合同签定后立即组织有关施工人员到安装现场进行施工暂设的准备,同时进行原材料的采购工作,并进行二次复验工作。
2、施工设备及工机具、施工人员的组织和运送,力争在最短的时间进入施工现场,投入施工中。
二、施工程序:施工准备→材料采购及复验→预制加工→罐底基础验收→罐底板基础放线→罐底板铺设→罐底焊接→罐底真空试漏→安装第一圈壁板→罐顶角钢圈安装→罐顶临时支撑架安装→罐顶板安装→罐顶板焊接→群桅抱杆安装→第二圈壁板安装→第一次罐体提升→第一圈壁板与第二圈壁板组对、焊接→第三、四……及最底圈壁板安装、焊接→底圈壁板与罐底板角焊缝焊接→罐体附件安装(含加热器)→充水试验→平台、梯子安装→罐体除锈、涂漆(内部涂食用油漆、外部涂防锈漆)→交工验收。
三、施工方法及技术措施本工程采用倒装法施工,即油罐顶自上向下施工。
储罐施工组织方案

1.编制说明该工程由乌鲁木齐石化总厂**设计,我公司承担其中27台储罐的施工任务.为保证优质、快速、顺利地完成施工任务.特编制此技术措施以指导施工操作.2.编制依据**中油化工**储罐建设工程合同乌鲁木齐石化总厂**设计的储罐工程施工图中国石油天然气第一建设公司质量管理手册及程序文件《现场设备、工业管道焊接工程施工及验收规范》 GB50236-98《立式圆筒形钢制焊接油罐施工及验收规范》 GBJ128-90《石油化工立式圆筒形钢制焊接储罐设计规范》 SH3046—923.工程概况3.1工程简介**中油化工**精细化工厂储运建设工程,共有储罐36台,其中6台10000m3钢制拱顶柴油贮罐、9台10000m3钢制内浮顶原油贮罐、4台5000m3钢制内浮顶汽油贮罐,4台3000 m3钢制拱顶沥青贮罐、4台200 m3零位罐由我公司承建,贮罐主体钢板材质为16MnR、08KP和Q235-A.该工程位于**乌鲁木齐市头屯河区王家沟工业园区.工程开工日期为2003年5月1日,计划竣工日期为2003年9月31日.3.2工程实物量工程实物量表4施工技术方案4.1 储罐总体施工技术方案根据本工程施工的特点,所有储罐均采用电动倒链倒装法施工.焊接全部采用手工电弧焊焊接.4.2 施工程序施工准备→罐底、罐顶、罐壁预制→罐底板防腐→基础验收→罐底铺设→弓形边缘板外缘300mm及中幅板焊接→罐底无损检测、真空试漏→顶圈罐壁板组焊→包边角钢组焊→设置中心伞架→顶板安装焊接→罐顶劳动保护及罐顶附件安装→背杠、窗口处倒装立柱及电动倒链安装→上数第二圈壁板安装、纵缝焊接→顶圈壁板提升→组对、焊接顶圈与第二圈壁板环缝→组对、焊接上数第三圈壁板→提升第二圈壁板→组对、焊接第二、三圈壁板之间的环缝→组对、焊接第四圈壁板→……→组对、焊接底圈壁板→倒装吊具拆除→组焊大角缝→组焊收缩缝→底圈罐壁开孔、配件、附件安装→封孔→充水试验、沉降观测→放水清扫→防腐、保温→竣工验收.说明:立柱数量计算公式, N=<罐总重量-罐底板重量-最下层罐壁板重量+罐顶平台及附件重量>×动载风载系数/10动载风载系数取值为1.25,电动倒链型号选用10t级.所以单台10000m3柴油罐设置电动倒链20个,单台10000m3原油罐设置电动倒链22个,单台5000m3汽油罐设置电动倒链16个,单台3000m3沥青罐设置电动倒链10个. 4.3 施工准备材料准备及验收本工程由业主提供主要材料,工程中所用材料的质量合格与否是决定工程质量好坏的关键,也是交工验收的主要内容之一.所以,材料验收是施工生产不可缺少的一个重要步骤.材料验收及管理主要包括以下几项内容:A资料检查储罐所选用的材料〕钢板、钢管及其它型钢〔、附件、设备等应具有相应的质量合格证明书.当无质量证明书或对质量证明书有疑问时,应进行复验,合格后方可使用.B外观检查对油罐所用的钢板,严格按照技术文件GB6654标准规定的相应要求进行验收,逐张进行外观检查,其表面质量、表面锈蚀减薄量,划痕深度等应符合下表规定:钢板厚度允许偏差C焊接材料验收焊接材料应具有质量证明书,焊条质量证明书应包括熔敷金属的化学成分和机械性能,低氢型焊条还应包括熔敷金属的扩散氢含量.技术准备A认真做好设计交底和图纸会审工作;B熟悉图纸和资料,编制切实可行的施工方案;C 将各台罐的罐顶排版下料图、罐壁排版图、罐底排版图、吊装立柱、伞架图、胎具图等根据施工图纸和规范要求计算、出图装订成册随施工方案下发给各施工队;D详细向施工班组进行技术交底.现场准备A修通道路,平整施工现场,选定材料、构件存放场地;B接通水源、电源,按平面布置图放置焊接电焊机房及工具、休息室;4.4储罐预制在施工生产中,对罐体的许多构件和材料安装前必须进行预制加工,如罐底边缘板成型、罐壁板坡口及圆弧度加工以及各种弧型构件〕加强圈、包边角钢等〔.有些构件为了成型规范、减少高空作业、提高工效、保证工程质量也需要在专用平台上进行预制加工,如排水管、劳动平台等.在预制、组装及检验过程中所使用的样板应符合以下规定:汽油罐、沥青罐、零位罐的弧形样板的弦长不得小于 1.5m,柴油罐、原油罐的弧形样板的弦长不得小于2m,直线样板的长度不得小于1m,测量焊缝角变形的弧形样板弦长不得小于1m.罐底边缘板的预制切割采用手工或半自动火焰切割,罐壁板的预制切割采用半自动切割机.罐顶板和罐底边缘板的圆弧板,可采用气焊切割加工,罐顶板直线段采用半自动切割机切割.钢板边缘加工面应平滑,不得有夹渣、分层、裂纹及熔渣等缺陷,火焰切割坡口产生的表面硬化层应磨除.壁板焊接接头的坡口的型式及尺寸应符合设计图纸要求.所有预制构件在保管、运输及现场堆放时应采取有效措施防止变形、损伤和锈蚀.底板预制按罐底排板图,确定每张板的几何尺寸,切割加工后的每张底板都应做好标识,并复检几何尺寸、做好自检记录.预制弓形边缘板及不规则板,钢板切割采用半自动切割机切割和手工切割相结合的切割方法.预制好的罐底板应做好标识,然后进行防腐.A 罐底板的预制主要工序为:准备工作→材料验收→划线→复验→切割→打磨→下一道工序.B 底板预制应符合以下规定:弓型边缘板允许偏差 弓型边缘板测量部位罐顶预制 储罐罐顶的预制严格按罐顶排版图进行分块预制.顶板加强筋应进行成型加工,加强筋应用成型样板检查,间隙需小于2㎜;加强筋与顶板组焊时,应采取防变形措施. 加强筋的拼接采用对接接头时,加垫板,且必须完全焊透,采用搭接时,其FC DB A搭接长度不得小于加强筋宽度的2倍.顶板预制成型后,用弧型样板检查,其间隙需小于10㎜.壁板预制A 罐壁板的预制工序为:准备工作→材料验收→钢板划线→复验→切割→坡口打磨→滚板成型→检查、记录→准备安装组对.B 罐壁板预制要严格按照图纸要求,采用半自动切割机进行坡口加工,壁板几何尺寸要严格按罐壁排板确定.同时要做好预制检查记录.壁板尺寸的允许偏差符合下表:壁板尺寸测量部位壁板卷制后,应立置在平台上用样板检查,垂直方向上用直线样板检查,其间隙不得大于1mm,水平方向上用弧形样板检查,其间隙不得大于4mm.壁板滚圆时,吊车配合要注意下滚床时防止外力引起不可回塑性变形.滚制后,应立置在平台上检查,合格后,再放在准备好的成型胎具上.构件、附件预制严格按施工图纸和规范的要求,按方便安装施工,尽可能减少安装工作量,DC F A E B尤其是高空作业工作量的原则,最大限度的加深预制.A量油管等预制成型后必须保证水平放置的直线度不超过规范要求,量油管上的钻孔要用锉刀把开孔内壁的毛刺全部剔除,并保证内壁光滑,以防止量油装置安装后不能正常使用.B抗风圈预制时要采取防焊接变形措施,成型后弧形曲率和翘曲变形不应超过构件长度的0.1%,且不大于4mm.C加强圈、包边角钢的预制曲率同设计曲率,弧形加工预制产生的直段要采取预弯或者火焰加热纠正,以保证构件整体成型,翘曲变形也必须控制在设计规范要求范围内.D盘梯、通气阀、排水管、通气管、人孔需要预制的以及其它有关附件按有关设计文件、规范进行预制焊接.4.5储罐组装组装前应组织相关人员进行基础验收,合格后方可进行储罐组装.储罐组装时,将构件的坡口和搭接部位的泥砂、铁锈、水及油污等清理干净.拆除组装用的工卡具时,不得损伤母材.钢板表面的焊疤应打磨平滑.如果母材有损伤,应按有关要求进行修补.罐底组装基础验收合格后,在基础上确定罐的具体方位,划出"十"字中心线,作为罐底铺设的基准线.依据罐底排板图,在基础上划出各底板的位置线,然后开始罐底铺设.A、罐底组装要求:底板铺设前其下表面应涂刷防腐涂料,每块底板边缘50mm内不刷;中幅板搭接宽度允许偏差为±5mm;搭接接头三层钢板重叠部分,将上层底板切角,切角长度为搭接长度的2度为搭接长度的2/3,在上层底板铺设前应先焊接上层底板覆盖的角焊缝.B 、底板铺设边缘板铺设后,再进行中幅板的铺设.中幅板铺设时,先铺设中间条板,再向两侧铺设中幅板,铺设时必须在条板上划出中心线,保证其与基础中心线相重合,整板采用铺设一张,就位固定一张的方法.具体工序:施工准备→罐底放线→罐底边缘板垫板铺设→罐底边缘板组对→中间走廊板铺设→大板铺设→两侧走廊板铺设点焊→小板排列→大角缝组对→收缩缝及剩余罐底焊缝组对.C 、罐底放线:以基础中心和四个方位标记为基准,画十字中心线,并确定基准线做出永久标记.划出底板外圆周线,考虑焊接收缩量,底板外圆直径应比设计直径放大80mm.基础划线时还应考虑基础坡度差,划线半径 R= r 2+h 2+c 2R-实际划线半径 r-设计图纸所标之半径h-半径r 处的坡度差 c-收缩量D 、边缘板铺设边缘板采用对接形式,在后一块边缘板铺设前,要在前一块边缘板坡口处点焊垫板,边缘板之间不点焊,只用临时卡具固定.坡口型式,根据收缩系数及施工便利,选用外大内小的外坡口型式,外侧间隙e1为6-7mm,内侧间隙e2为8—12mm. 边缘板铺设时,按270°180°→270°的方位进行定位铺设,,必须保证组对间隙内大搭接量外小的特点,边铺设边用组合卡具固定.图如图所示:E 铺设中心定位板〕中心的一块底板〔,并在该板上画出底板中心点和中心线,打上样冲眼作出明显标记,铺设顺序如下:中幅板铺设时按设计规定尺寸制作组对挡板,以方便组对时控制搭接量. 中幅板边组对边点焊,点焊时两底板要紧贴,间隙控制在1mm 以下;点焊方式采用隔200mm 焊50mm 的方法,点焊时一定要注意:搭接丁字缝处覆盖角焊缝要先焊接完成后再铺上层板.铺中幅板时要随时检查板的位置与排版图相符合,铺板时要保证与基础踏实接触.小板的下料尺寸,要根据计算尺寸或现场量取尺寸的径向方向放大150mm 确定.小板与边缘板组对时,小板应沿径向方向预留100mm 余量,铺板调整后用组合龙门板将小板压紧固定,余量等收缩缝焊接时再切割.如下图所示:,切角长度按搭接长度的2倍确定,切角后用大锤锤击角接处,直至搭接角处板与板间缝隙达到焊接要求,切角示意图如下图所示:罐顶安装小板固定结构示意图8-12mm先按胎具图预制好罐顶胎具,见下页图.然后立第一层壁板,安装好包边角钢<包边角钢与罐壁焊缝暂不焊接>,此时可进行顶板组装.组装过程中焊工始终配合铆工点焊顶板的搭接缝,焊接前焊工应检验所点的焊缝是否符合要求,检查合格后,即可根据罐顶焊缝数配备焊工,使之均布在整个罐顶上,采用分段退焊法由中心往外施焊.罐顶板施焊完毕后,焊工可进行包边角钢与罐顶板,包边角钢与罐顶板搭接焊缝的焊接,焊工均布四周采用分端退焊法向同一方向施焊.上数第二圈至底圈壁板安装每圈壁板应备有调整板,除顶圈留一块外,其余各圈留两块调整板,对称分布,调整板每块留300mm 余量,调整板在封口时切割.在储罐内部距罐壁500mm 左右的同心圆上均布电动倒链,电动倒链固定在倒装立柱上.倒装立柱用φ273×6钢管制成,高4m<考虑到重复利用>,立柱上端吊耳、底座及筋板均用δ=20mm 钢板制作而成.倒装立柱应对称均布,距罐壁的距离应以电动倒链与起吊吊耳基本在一条铅垂线上为佳.立柱安装必须保证垂直,如与罐底接触有间隙,可垫薄钢板找平,并焊接牢固.为防止立柱失稳,在立柱3/4高度位置安装两根斜撑,斜撑用L75×7角钢制作.斜撑之间的夹角及斜撑与罐底的夹角均以45℃为宜.对称的两根立柱之间用钢丝绳拉紧.在每圈罐壁下端用背杠加固,背杠用[20槽钢滚弧制成.用龙门卡具将背杠与罐壁固定在一起.在电动倒链下方的背杠上焊接起吊吊耳,电动倒链通过控制装置提升起吊吊耳,将力传到背杠及罐壁上,达到提升罐壁的目的,电动倒链可同步提升,也可单独提升.电动倒链提升示意图见下图:吊具准备完毕后,围上数第二圈壁板,组对点焊纵缝,封口处分别用两个钢索罐壁电动倒链3t 手拉倒链拉紧,然后开始焊接纵缝.纵缝外侧焊完后,即可开始提升顶圈罐壁.提升时将封口处倒链适当松开,以免起升困难或将第二圈壁板带起.提升前先将电动倒链吊钩挂在起吊吊耳上,并使之拉紧.安排一人检查,使拉紧程度均匀.同时检查背杠是否顶紧,龙门卡具是否焊牢,倒装立柱斜撑是否安全可靠.一切准备就绪后,开始提升.提升时电动倒链应由专人集中控制,同步运行.提升过程中应密切注意提升是否平稳正常.发现异常情况,应立即停止提升,查明原因,消除隐患后重新开始提升.提升到约600mm 左右高度时,暂停.检查电动倒链是否同步运行,提升高度是否一致,受力是否均衡,背杠有无变形,倒装立柱有无异常等.如无问题,可继续提升.如果电动倒链不同步,则对个别倒链单独控制调整,直至受力状态,提升高度一致后,再集中控制,同时进行提升.重复上述操作,直至提升到所需高度.提升示意图如下页图:提升到位后,拉紧封口倒链,测量周长、切割余量,组对点焊封口处纵缝,然后开始组对顶圈与第二圈壁板的环缝.环缝组对时,可个别升降电动倒链,以调整环缝组对间隙.环缝组对点焊完毕后,应先焊封口处纵缝外侧焊缝,然后焊接环缝外侧焊缝.外口焊完后,里口清根,检查合格后,焊接里口焊缝.里外口均焊完毕,自然冷却到环境温度后,撤下背杠,用电动倒链将背杠放下,重新安装到第二圈板下口,并顶紧固定好.然后安装其余倒装立柱,每根立柱挂10t 电动倒链,立柱的加固与上述相同,对应的两根立柱间用钢丝绳拉紧.在第二圈壁板外侧安装第三圈板,围板且组对点焊完毕后,焊接纵缝,纵缝焊好后,同提升顶圈壁板一样,重复上述检查,提升第二圈壁板,组对第三圈封口纵缝,然后组对第二圈与第三圈之间的环缝.组对好后焊接,焊完后回落背杠,安装到立柱拉紧钢电动倒链斜拉杆 立柱罐地板吊耳背杠 挡板 壁板 垫板第三圈壁板下口,重复上述过程,直到罐壁全部安装完毕.底圈壁板组对焊接时在进出口处留一块封口调节板暂不上,由此将罐内倒装吊具、背杠等所有手段用设备、材料全部运出罐外,随后开罐壁人孔,安装最后一块壁板,然后组对焊接大角缝,组对焊接收缩缝.A罐壁组装检查:①底圈壁板相邻两板上口水平的偏差不大于2mm,在整个圆周上任意两点水平偏差不应大于6mm.壁板的铅垂允许偏差不大于3mm,组焊后,在底圈罐壁1m高处,内表面任意点半径允许偏差±19mm.②壁板组装时,应保证内表面平齐,错边量应符合以下规定:纵向焊缝错边量:板厚δ≤10mm 允许错边≤1mmδ>10mm 允许错边≤1.5mm环向焊缝错边量:上圈板厚<8mm 允许错边≤1.5mm上圈板厚≥8mm 允许错边2/10δ且≤3mm③组焊后焊缝的角变形用1m长的弧形样板检查,应符合下表规定:罐壁焊缝的角变形表④组焊后,罐壁的局部凹凸变形应平缓,不得有突然起伏,且应符合下表规定:罐壁的局部凹凸变形控制表⑤罐体的开孔接管,应符合以下要求:开孔接管的中心位置偏差,不得大于10mm,接管外伸长度的允许偏差,应为±5mm;开孔补强板的曲率,应与罐体曲率一致;开孔接管法兰的密封面应平整,不得有焊瘤和划痕,法兰的密封面应与接管的轴线垂直,倾斜不应大于法兰外径的1%,且不得大于3mm,法兰的螺栓孔应跨中安装.顶圈壁板及包边角钢安罐底焊接完毕,且无损检测、真空试漏合格后,按照排板图安装顶圈壁板.顶圈壁板安装后必须保证壁板垂直度、椭圆度和上口水平度.壁板垂直度、椭圆度和上口水平度调整好后,将壁板临时固定,在壁板纵缝上安装三块防变形圆弧板,以防焊接变形,焊接可先焊外侧纵缝,里口清根,再焊内侧纵缝.顶圈壁板安装完后安装包边角钢,其拼接缝和壁板纵缝应错开200mm以上.附件安装工序流程:准备工作→罐壁防水孔→人孔安装→加强圈、抗风圈安装→盘梯安装→包边角钢安装→量油管、液位测量管安装→劳动保护结构安装→交工验收.①加强圈在罐壁组装过程中安装,采取分段预制吊装.②包边角钢的对接焊缝与罐壁的纵缝应错开200mm以上.③罐壁和罐顶开孔接管及补强圈焊接时,在罐壁开孔背面打上圆弧板,防止罐壁及罐顶焊接后变形.④油管、液位测量管安装时,必须保证其垂直度偏差≤±5mm.4.6储罐检查与验收储罐的检查和验收按GBJ128-90《立式圆筒形钢制焊接油罐施工及验收规范》及设计要求进行.焊缝的外观检查外观检查前应将熔渣、飞溅清理干净.焊缝的表面质量,应符合以下规定:焊缝的表面及热影响区,不得有裂纹、气孔、夹渣和弧坑等缺陷;对接焊缝的咬边深度,不得大于0.5mm;咬边的连续长度,不得大于100mm;焊缝两侧咬边的总长度,不得超过该焊缝长度的10%;底圈壁板与边缘板的T形接头,罐内角焊缝靠罐底一侧的边缘,应平滑过渡,咬边应打磨圆滑;罐壁纵向对接焊缝不得有低于母材表面的凹陷.罐壁环向对接焊缝和罐底对接焊缝低于母材表面的凹陷深度,不得大于0.5mm.凹陷的连续长度不得大于100mm;凹陷的总长度,不得大于该焊缝总长度的10%.对接焊缝的余高〕mm〔焊缝检查及严密性试验从事油罐焊缝无损探伤人员,必须具有国家有关部门颁发的并与其工作相适应的**书.罐底的所有焊缝应采用真空箱法进行严密性试验,试验负压值不得低于53Kpa,无渗漏为合格;开孔的补强板焊完后,由信号孔通入100—200Kpa的压缩空气,检查焊缝严密性,无渗漏为合格.罐体几何形状和尺寸检查①罐壁组装焊接后,几何形状和尺寸应符合以下规定:罐壁高度的允许偏差不应大于70mm;罐壁铅垂的允许偏差不大于50mm..②罐壁局部凹凸及底圈壁板内表面半径允许偏差应符合有关规定.③罐壁上的工卡具焊迹应清除干净,焊疤应打磨平滑.④罐底焊接后,其局部凹凸变形的深度不应大于变形长度的2%,且不应大于50mm.充水试验储罐的充水试验、罐壁强度及严密性试验、固定顶的严密性、强度和稳定性试验应严格按照每台储罐的技术要求进行.罐体无损检测合格及所有配件、附件安装完毕,充水试验前,应进行联合检查,检查合格后,封闭人孔等所有开孔,开始充水,进行充水试验.充水过程中,设置专人进行监控,发现异常情况应及时处理,处理合格后方可继续上水.充水试验结束后,罐体内的水应按业主要求和排放位置及时排放.①油罐在充水试验中,要检查以下内容:罐底严密性;罐壁强度及严密性;固定顶的严密性、强度和稳定性;基础的沉降观测.②充水试验前,应符合以下规定:充水试验前,所有附件及其它与罐体焊接的构件,应全部完工;充水试验前,所有与严密性试验有关的焊缝,均不得涂刷油漆;充水试验应采用洁净水,水温不应低于5℃;充水高度为设计最高液位下1m处.充水试验中应加强基础沉降观测.在充水试验中,如基础发生不允许的沉降,应停止充水,待处理后,方可继续进行试验;充水和放水过程中,不得使基础浸水.③罐底的严密性,对罐底焊缝进行真空试漏并在充水试验过程中罐底无渗漏为合格,若发现渗漏,应按规定补焊.④罐壁的强度及严密性试验,应以充水到试验要求高度并保持48h后,罐壁无渗漏、无异常变形为合格.发现渗漏时应放水,使液面比渗漏处低300mm 左右,并应按规定进行焊接修补.⑤罐顶严密性及强度试验应在设计最高液位下1m时进行缓慢充水升压,在罐内空间达到试验正压后,以罐顶无渗漏为合格,试验后立即恢复常压,使罐顶与大气相通.⑥罐顶稳定性试验应在水位达到罐顶边梁后进行放水,在罐内空间达到试验负压〕1500Pa〔后,以罐顶无异常变形为全格, 试验后立即恢复常压,使罐顶与大气相通.基础的沉降观测①储罐在充水试验时要进行沉降观测,做法为:在罐壁均布12个观测点用φ14〕L=200mm〔的钢筋钩焊于距罐底板200mm高处.②观测要求沉降观测应在基础施工完毕,罐体充水前、充水过程中、充水稳压阶段、放水过程中进行.测量精度为Ⅱ级水准.由专人定期测量,按规定做记录.观测点要严加保护,以防磨损或撞坏.③储罐基础沉降观测方法储罐充水时,可快速充水到罐高的1/2进行沉降观测,并与充水前观测到的数据进行对照,计算出实际的不均匀沉降量.当未超过允许的不均匀沉降量时,可继续充水到罐高的3/4,再进行观测,当仍未超过允许的不均匀沉降量,可继续充水到最高操作液位,分别在充水后和保持48h后进行观测,当沉降量无明显变化,即可放水;当沉降量有明显变化,应保持最高操作液位,进行每天的定期观测,直至沉降稳定为止.4.7 储罐焊接方案由于油罐储存介质为易燃品,对储罐焊缝质量要求较高,这就要求我们要从各个环节来保证焊接质量,包括拍片合格率和焊缝外观成型,同时要控制焊接变形,减少返工.本工程储罐材质为08KP和Q235-A,焊接方法罐壁、罐底用手工焊全部选用手工焊的焊接方法.焊前准备①储罐施工前,需按照4708—92《钢制压力容器焊接工艺评定》和GBJ128-90《立式圆筒形钢制焊接油罐施工及验收规范》的规定进行焊接工艺评定.②所有参与油罐焊接的电焊工必须持证上岗.③油罐施工前,应根据焊接工艺评定报告等制定油罐焊接工艺.④焊接材料应设专人负责保管,使用前按规定烘干,烘干后的焊条,应保存在100—150℃恒温箱中,随用随取,现场使用时,应备有性能良好的保温筒.⑤焊材选用所有储罐焊材选用见施工图要求.焊接要求①定位焊及工卡具的焊接,应由合格焊工担任,焊接工艺应与正式焊接相同.引弧和熄弧都应在坡口内侧,每段定位焊缝的长度不宜小于50mm.②焊接前应检查组装质量,清除坡口面及坡口两侧20mm范围内的泥沙、铁锈、水分和油污,并应充分干燥.。
储罐制作方案

5000m3油罐、2500m3油罐、1000m3油罐本体制作安装工程施工方案文件编号:编制人:时间:审核人:时间:批准人:时间:二0一一年七月目录一工程概况 (1)二施工准备 (1)三施工方法和施工程序 (4)四健康、环保、安全 (22)一、工程概况1.工程特点5000m3油罐本体制作安装工程是由投资建设的工程项目。
储油罐制作、安装工程20000m3油罐有2台,罐顶为球形拱顶油罐,采用钢网壳,其储存介质为柴油,设计压力为常压,常温。
油罐施工按GBJ128-90《立式圆筒形钢制焊接油罐施工及验收规范》进行制造、试验和验收。
2.主要实物工作量及工期要求油罐描述如下:2×5000m³罐底板外径:Φ23830mm2×5000m³罐内径:23700mm2×5000m³罐壁高度:12530mm2×5000m³罐顶高度:15117 mm2500m³罐底板外径:Φ16130mm2500m³罐内径:16000mm2500m³罐壁高度:12600mm2500m³罐顶高度:14347 mm1000m³罐底板外径:Φ13620mm1000m³罐内径:13500mm1000m³罐壁高度:10650mm1000m³罐顶高度:12254 mm二、施工准备工程开工前必须作好充分的施工准备,这样才能保证工程施工的顺利实施和实现过程总工期目标。
1 技术准备1.1根据施工图和设计有关文件,编制施工方案并报送监理审批。
1.2 收集以下国家或行业的施工及验收规范《立式圆筒形钢制焊接油罐施工及验收规范》 GBJ128-90《现场设备、工业管道焊接工程施工及验收规范》GB50236 – 98《中低压化工设备施工及验收规范》 HGJ201 - 83《石油化工施工安全实施规程》 SHJ3505 – 99《钢制焊接常压容器》 JB/T 4735-1997《石油化工安装工程质量检验评定标准》 SHJ514-90《工程建设交工技术文件规定》 SH3503-93《钢融化焊对接接头射线照和质量分级》 GB3323-87《焊接接头的基本形式与尺寸》 GB985-88《石油化工工程焊接工艺平定标准》 SHJ509-881.3 施工前有关人员应熟悉施工图纸及有关技术文件、法规,通过图纸会审,明确储运建设工程相关专业配合要求。
不锈钢储罐施工方案
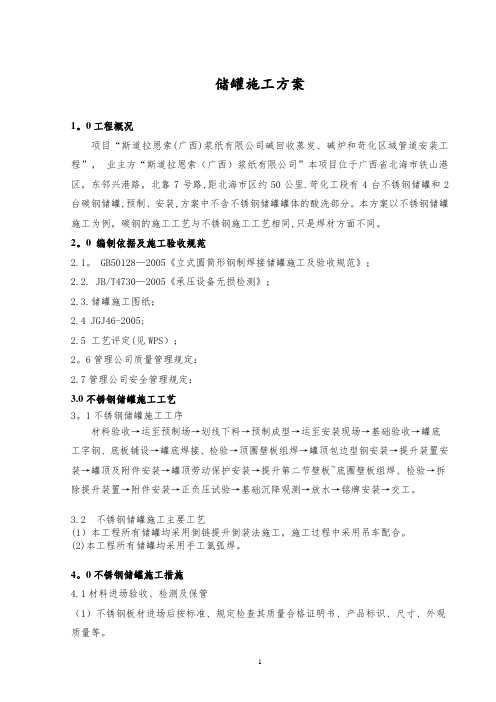
储罐施工方案1。
0工程概况项目“斯道拉恩索(广西)浆纸有限公司碱回收蒸发、碱炉和苛化区域管道安装工程”,业主方“斯道拉恩索(广西)浆纸有限公司”本项目位于广西省北海市铁山港区,东邻兴港路,北靠7号路,距北海市区约50公里.苛化工段有4台不锈钢储罐和2台碳钢储罐,预制、安装,方案中不含不锈钢储罐罐体的酸洗部分。
本方案以不锈钢储罐施工为例,碳钢的施工工艺与不锈钢施工工艺相同,只是焊材方面不同。
2。
0 编制依据及施工验收规范2.1。
GB50128—2005《立式圆筒形钢制焊接储罐施工及验收规范》;2.2. JB/T4730—2005《承压设备无损检测》;2.3.储罐施工图纸;2.4 JGJ46-2005;2.5 工艺评定(见WPS);2。
6管理公司质量管理规定:2.7管理公司安全管理规定:3.0不锈钢储罐施工工艺3。
1不锈钢储罐施工工序材料验收→运至预制场→划线下料→预制成型→运至安装现场→基础验收→罐底工字钢、底板铺设→罐底焊接、检验→顶圈壁板组焊→罐顶包边型钢安装→提升装置安装→罐顶及附件安装→罐顶劳动保护安装→提升第二节壁板~底圈壁板组焊、检验→拆除提升装置→附件安装→正负压试验→基础沉降观测→放水→铭牌安装→交工。
3.2 不锈钢储罐施工主要工艺(1)本工程所有储罐均采用倒链提升倒装法施工,施工过程中采用吊车配合。
(2)本工程所有储罐均采用手工氩弧焊。
4。
0不锈钢储罐施工措施4.1材料进场验收、检测及保管(1)不锈钢板材进场后按标准、规定检查其质量合格证明书、产品标识、尺寸、外观质量等。
(2)对不锈钢板材做PMI,比例为同一炉批号、同一生产批号、同一规格做一点检测. (3)不锈钢材料运至预制工厂,按BAYER规定做好产品标识,即在304L材料两角部做100MM*10MM的蓝色彩条;材料下料后对主要部分做好标识移植。
特别是V913—BA005罐,必须在板材上标明炉批号,以便追溯。
(4)不锈钢材料在预制工厂或安装现场都与碳钢施工区域隔离,视实际情况如有必要则采用彩条布覆盖.(5)不同不锈钢材料分开摆放,并挂牌.4.2 不锈钢储罐下料预制(1)储罐下料预制在场外工厂进行。
大型储罐工厂制作施工工法
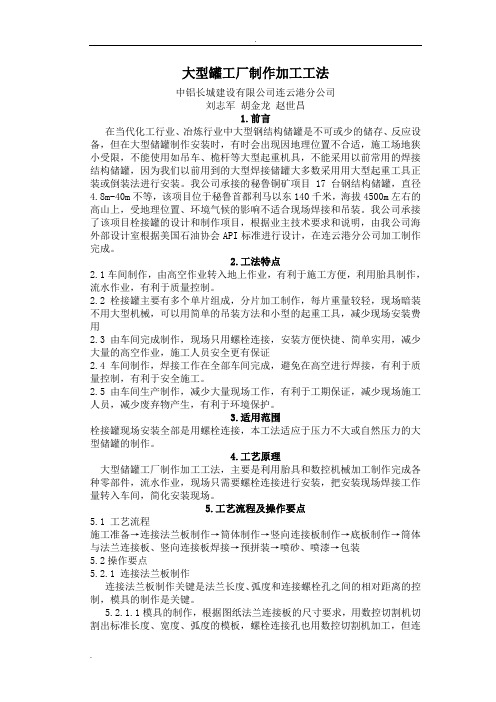
大型罐工厂制作加工工法中铝长城建设有限公司连云港分公司刘志军胡金龙赵世昌1.前言在当代化工行业、冶炼行业中大型钢结构储罐是不可或少的储存、反应设备,但在大型储罐制作安装时,有时会出现因地理位置不合适,施工场地狭小受限,不能使用如吊车、桅杆等大型起重机具,不能采用以前常用的焊接结构储罐,因为我们以前用到的大型焊接储罐大多数采用用大型起重工具正装或倒装法进行安装。
我公司承接的秘鲁铜矿项目17台钢结构储罐,直径4.8m-40m不等,该项目位于秘鲁首都利马以东140千米,海拔4500m左右的高山上,受地理位置、环境气候的影响不适合现场焊接和吊装。
我公司承接了该项目栓接罐的设计和制作项目,根据业主技术要求和说明,由我公司海外部设计室根据美国石油协会API标准进行设计,在连云港分公司加工制作完成。
2.工法特点2.1车间制作,由高空作业转入地上作业,有利于施工方便,利用胎具制作,流水作业,有利于质量控制。
2.2栓接罐主要有多个单片组成,分片加工制作,每片重量较轻,现场暗装不用大型机械,可以用简单的吊装方法和小型的起重工具,减少现场安装费用2.3由车间完成制作,现场只用螺栓连接,安装方便快捷、简单实用,减少大量的高空作业,施工人员安全更有保证2.4 车间制作,焊接工作在全部车间完成,避免在高空进行焊接,有利于质量控制,有利于安全施工。
2.5由车间生产制作,减少大量现场工作,有利于工期保证,减少现场施工人员,减少废弃物产生,有利于环境保护。
3.适用范围栓接罐现场安装全部是用螺栓连接,本工法适应于压力不大或自然压力的大型储罐的制作。
4.工艺原理大型储罐工厂制作加工工法,主要是利用胎具和数控机械加工制作完成各种零部件,流水作业,现场只需要螺栓连接进行安装,把安装现场焊接工作量转入车间,简化安装现场。
5.工艺流程及操作要点5.1 工艺流程施工准备→连接法兰板制作→筒体制作→竖向连接板制作→底板制作→筒体与法兰连接板、竖向连接板焊接→预拼装→喷砂、喷漆→包装5.2操作要点5.2.1 连接法兰板制作连接法兰板制作关键是法兰长度、弧度和连接螺栓孔之间的相对距离的控制,模具的制作是关键。
现场储罐施工方案

现场储罐施⼯⽅案现场制作储罐T06001~T06016施⼯⽅案项⽬:3000吨/年⾼纯硅项⽬设计单位:北京蓝图⼯程设计有限公司南京分公司买⽅:江苏康博新材料科技有限公司编制:杜明艳审核:李传新批准:李世明恒远国际⼯程集团有限公司2011年3⽉现场制作储罐T06001~T06016施⼯⽅案1 制作⽅案1.1设备位号及尺⼨如下:T06001~T06014,Φ6000*13270T06015~T06016,Φ3500*98001.2制作⽅案:1.2.1 T06001~T06014,由于设备直径Φ6000,因运输条件的限制,不能在制造⼚制造成整台,因此采取在制造⼚分节预制,然后到现场组装的施⼯⽅案。
由于在制造⼚内制造、起吊的⽅便性,编制⽅案时,应考虑最⼤限度地将⼯作量放在制造⼚内,只要在运输允许的情况下,尽量减少现场的⼯作量。
因此,我们对当时投技术标时的制作⽅案进⾏了以下修改。
当时投技术标时的⽅案为:“筒节制作⽅案:⼚内预制,每节筒节沿圆周⽅向分2块,在⼚内成形为圆弧,然后运输⾄现场,在现场将2个半圆焊接成整圆。
”在制造前,我公司对从制造⼚到买⽅⼯地的道路、涵桥进⾏了察看,可以采取分段运输出⼚的⽅案,因此将制作、运输⽅案改为:从上到下分成4段运输,将设备的直径作为运输的宽度。
1.2.2 T06015~T06016,在⼚内全部制造完成(包括压⼒试验、油漆),整体运输到现场,在现场进⾏清洗和充氮。
2 T06001~T06014在⼚内的分段制作1.1每台分成4段,见下图(图中管⼝按T06001~T06009/T06014所画,T06010~T06013管⼝有所不同):图1 第4段图2 第3段图3 第2段图4 第1段2.2每⼀段在⼚内的制造完成程度2.2.1第1段在⼚内的制造完成程度:(1)封头上焊缝已完成探伤;(2)裙座与下封头组对完成,为了防⽌裙座与封头焊接时产⽣的焊接变形对封头形状的影响,裙座与封头在⼚内只进⾏点焊,在第1段与第2段组焊后再进⾏焊接;(3)N1管⼝已与封头组焊,并完成探伤;(4)为了地脚螺栓座与地脚螺栓⽅位的⼀致性,螺栓座现场焊接,环板上的螺栓槽可以现场修正;(5)内外表⾯进⾏喷丸除锈,外表⾯涂底漆1道(按技术附件),待焊坡⼝处40mmm范围不涂。
大型储罐施工方案

大型储罐施工方案 Prepared on 22 November 2020§1 施工方案§总体施工方案1、液压提升倒装自动焊工艺a、本工程二台20000m3内浮顶罐采用液压提升倒装自动焊工艺进行施工,施工工艺流程图如后图所示。
b、罐底板、罐壁板在本部生产基地进行深度工厂化预制,利用进口的龙门自动切割机,切割下料和坡口加工一次成型。
c、油罐纵缝和环缝外口采用CO2气体保护自动焊,内口采用CO2气体保护半自动焊;油罐底板采用埋弧焊+碎丝焊。
2、液压提升倒装自动焊施工工艺流程图§油罐预制方案1、罐底预制a、罐底预制主要是弓形边缘板和中幅板的切割。
罐底中幅板、边缘板采用净料预制技术,用龙门自动切割机切割钢板的直边和坡口,罐底边缘板弧线采用半自动火焰切割机切割。
b、罐底板预程序如下:c、底板预制前应绘制排板图,并应符合下列规定●罐底的排板直径,宜按设计直径放大%%;●边缘板沿罐底半径方向的最小尺寸,不得小于700mm;●弓形边缘板的对接接头,宜采用不等间隙,外侧间隙宜为6-7mm;内侧间隙宜为8-12mm;●中幅板的宽度不得小于1000mm,长度不得小于2000mm;●底板任意相邻焊逢之间的距离不得小于200mm。
d、中幅板的尺寸允许偏差应符合下表的规定e、弓形边缘板尺寸允许偏差:2、壁板预制a、壁板预制主要为板料检验、切割下料和滚圆三个过程,进行工厂化施工,壁板预制工艺流程如下:b、壁板预制前,根据设计要求、施工规范及钢板实际到货规格绘制排板图,报设计及监理单位批准,并应符合下列要求:●底圈壁板纵缝,宜向同一方向逐圈错开,其间距不得小于500mm;●底圈壁板纵向焊缝与罐底边缘板的对接缝之间的间距不得小于200mm;●罐壁开孔接管或开孔接管补强板外缘与罐壁纵向焊缝之间的距离,不得小于200 mm;与环向焊缝之间的距离,不得小于100 mm;●包边槽钢对接接头与罐板纵向焊缝之间的距离不得小于200mm;●壁板宽度为1800mm,长度不得小于6000mm。
3000立方和2000立方储罐施工方案

目录1.工程概况及编制依据工程概述本方案适用于宁夏石嘴山惠农油库贮罐区8台3000m3内浮顶油罐、4台2000m3内浮顶油罐的现场预制、组装。
编制依据GB50128-2005《立式圆筒形钢制焊接油罐施工及验收规范》。
SH/T3530-2001《石油化工立式圆筒形钢制储罐施工工艺标准》。
GB50236-98《现场设备、工业管道焊接施工及验收规范》。
JB4708-2000《钢制压力容器焊接工艺评定》。
JB/T4709-2000《钢制压力容器焊接规程》。
JB4730-2005《压力容器无损检测》。
施工图纸。
2.施工准备施工技术准备(1)对施工图进行三级会审,并做详细记录,施工方案经业主批准且进行详细安全技术交底,施工记录表格齐全。
(2)工程所用材料,均要有合格的质量证明书。
若对材质合格证明书或货物有疑问时须进行复验,无合格证的材料不得使用。
检查材料的表面质量,表面应无严重锈蚀、损伤及表面裂纹、分层、重皮等缺陷。
(3)做好基础检查验收工作,基础应符合设计和规范要求,并结合土建交工资料进行检查和验收,做好检查验收记录。
基础验收合格并经业主同意方可进行罐底的施工。
(4)预制加工前要根据图纸、材料规格及施工规范的要求绘制贮罐排版图。
所有切割成型的专用钢板和罐顶支撑构件,在包装起运前按制造图注上标记。
施工机具准备按施工机具计划配备施工机械,并保证机具性能完好,机械运转记录随时填写。
施工现场准备施工场地应设置:材料、半成品存放场地;加工场地、办公设施等。
场地应平整,道路应畅通,临时用水、用电线路应按要求敷设。
3.材料的采购、验收、保管3.1材料的采购应根据储罐的排版图合理采购材料,既要考虑到缩短施工时间,节约施工材料,节省人力资源,又要考虑到施工的难易程度和施工质量控制。
材料供应厂家应是国家级大型企业、全国知名企业。
3.2材料入场后应按照相关的国家规范进行验收。
尤其是钢板的验收必须严格按照GB/709-2006进行验收,钢板的外形几何尺寸、不平整度、钢板的外观、厚薄、短面的变形情况、锈蚀情况进行检查。
10000立方米柴油贮罐制作安装方案1

第二带板
15282
14
盘梯及平台
2370
15
圈平台
1700
16
胀圈[32
3600
17
总计
185764
2、参数选择
1起吊最大重量P=K.G=1.2×186t=223.2t。式中K为吊装安全系数,取K=1.2。G为提升总重量。
2导链数量及能力选择
设置28个吊装柱。56个5t导链
则:56×5t=280t>223.2t。
3、罐壁组对方法
倒装吊装工具准备就绪后,开始按罐壁排板图组装。先组对第十一带壁板,在壁板下口处安装胀圈并把胀圈联接处用30吨千斤顶胀紧,检查罐壁板与弧形样板的间隙是否符合技术要求,当各种技术项目全部合格后,开始焊接,当顶层壁板全部焊完后,安装组对边环梁及罐顶平台及盘梯。盘梯应按每带罐壁的高度分段安装。围第十带板,焊接第十带板立缝(留一道活口)。按施工图纸检查无误后,提升第十一带板,提升到第十带板上口平齐时,利用角形铁和卡板将上下两壁板固定,使上带壁板与下带壁板达到要求的组对间隙。开始组对环缝,并测量其周长,最后处理各组对预留口主缝。并在该节壁板下口有立缝处点焊弧形板,以保证罐壁焊接后的圆度。上述工作完成后,进行各项技术检查,合格后焊接,焊完后打掉立缝处弧形板,松胀圈下落到第十带板,围第九层带板,组对胀圈,焊接罐壁卡板等工作,依次类推,直到罐体全部安装完毕。
(2)罐底板的组对焊接方法
焊接时应先焊边缘板外侧向内300mm的对接焊缝,焊工必须均布在罐底边缘板外侧整个圆周上同时对称施焊,隔一条焊缝焊一条,最后留下对称两条焊缝先不焊,待调节好因对接焊缝收缩造成的总体变形后再由两名焊工对称施焊,同时,也可进行中幅板之间的搭接焊缝的焊接,边缘板剩余的对接缝待罐底板与罐壁板之间的大角焊缝焊完后且与中幅板之间的环向搭接焊缝焊前进行施焊。罐底板与中幅板之间的环向搭接焊缝在第一带壁板组装完毕后且与罐体的大角焊缝焊完后再进行焊接。
不锈钢储罐施工方案

储罐施工方案1.0工程概况项目“斯道拉恩索(广西)浆纸有限公司碱回收蒸发、碱炉和苛化区域管道安装工程”,业主方“斯道拉恩索(广西)浆纸有限公司”本项目位于广西省北海市铁山港区,东邻兴港路,北靠7号路,距北海市区约50公里。
苛化工段有4台不锈钢储罐和2台碳钢储罐,预制、安装,方案中不含不锈钢储罐罐体的酸洗部分。
本方案以不锈钢储罐施工为例,碳钢的施工工艺与不锈钢施工工艺相同,只是焊材方面不同。
2.0 编制依据及施工验收规范2.1. GB50128-2005《立式圆筒形钢制焊接储罐施工及验收规范》;2.2. JB/T4730-2005《承压设备无损检测》;2.3.储罐施工图纸;2.4 JGJ46-2005;2.5 工艺评定(见WPS);2.6管理公司质量管理规定:2.7管理公司安全管理规定:3.0不锈钢储罐施工工艺3.1不锈钢储罐施工工序材料验收→运至预制场→划线下料→预制成型→运至安装现场→基础验收→罐底工字钢、底板铺设→罐底焊接、检验→顶圈壁板组焊→罐顶包边型钢安装→提升装置安装→罐顶及附件安装→罐顶劳动保护安装→提升第二节壁板~底圈壁板组焊、检验→拆除提升装置→附件安装→正负压试验→基础沉降观测→放水→铭牌安装→交工。
3.2 不锈钢储罐施工主要工艺(1)本工程所有储罐均采用倒链提升倒装法施工,施工过程中采用吊车配合。
(2)本工程所有储罐均采用手工氩弧焊。
4.0不锈钢储罐施工措施4.1材料进场验收、检测及保管(1)不锈钢板材进场后按标准、规定检查其质量合格证明书、产品标识、尺寸、外观质量等。
(2)对不锈钢板材做PMI,比例为同一炉批号、同一生产批号、同一规格做一点检测。
(3)不锈钢材料运至预制工厂,按BAYER规定做好产品标识,即在304L材料两角部做100MM*10MM的蓝色彩条;材料下料后对主要部分做好标识移植。
特别是V913-BA005罐,必须在板材上标明炉批号,以便追溯。
(4)不锈钢材料在预制工厂或安装现场都与碳钢施工区域隔离,视实际情况如有必要则采用彩条布覆盖。
储罐焊接方案
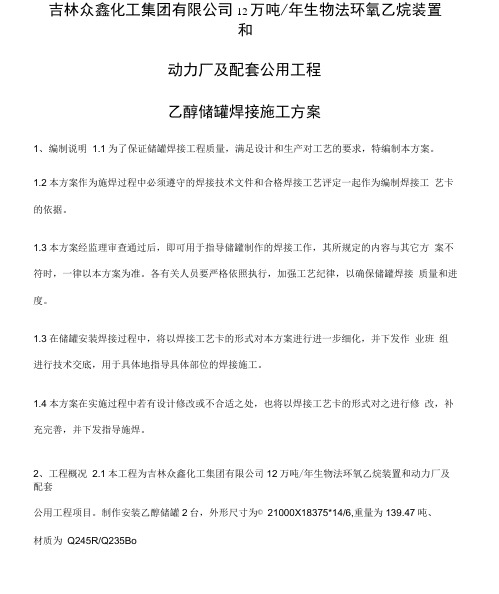
吉林众鑫化工集团有限公司12万吨/年生物法环氧乙烷装置和动力厂及配套公用工程乙醇储罐焊接施工方案1、编制说明1.1为了保证储罐焊接工程质量,满足设计和生产对工艺的要求,特编制本方案。
1.2本方案作为施焊过程中必须遵守的焊接技术文件和合格焊接工艺评定一起作为编制焊接工艺卡的依据。
1.3本方案经监理审查通过后,即可用于指导储罐制作的焊接工作,其所规定的内容与其它方案不符时,一律以本方案为准。
各有关人员要严格依照执行,加强工艺纪律,以确保储罐焊接质量和进度。
1.3在储罐安装焊接过程中,将以焊接工艺卡的形式对本方案进行进一步细化,并下发作业班组进行技术交底,用于具体地指导具体部位的焊接施工。
1.4本方案在实施过程中若有设计修改或不合适之处,也将以焊接工艺卡的形式对之进行修改,补充完善,并下发指导施焊。
2、工程概况2.1本工程为吉林众鑫化工集团有限公司12万吨/年生物法环氧乙烷装置和动力厂及配套公用工程项目。
制作安装乙醇储罐2台,外形尺寸为© 21000X18375*14/6,重量为139.47吨、材质为Q245R/Q235Bo2.2设计参数一览表3.3设计板厚及材质材质:Q245R/Q235B3、编制依据3.1 •设计院设计蓝图。
3.2相关规范《立式圆筒形钢制焊接油罐设计规范》GB50341-2003《立式圆筒形钢制焊接储罐施工及验收规范》GB50128-2005《压力容器焊接规程》JB/T47019-2011《承压设备无损检测》JB/T4730-2005《焊接工艺评定规程》DL/T 868-20043.3企业工艺标准的名称及编号:《施工技术通用管理标准》Q/JH222 • 21100.01-2013《施工质量通用管理标准》Q/JH223 • 21500.01-2013《质量、环境、职业安全健康综合管理手册》Q/JH223 - 20001.2007接材料进行复验,复验合格后方可使用(2) 电焊条的存放,应符合下列规定:4、施工方法4.1施工顺序材料验收4.2焊工要求:人员、机具、焊评准备焊丁•:从事储觥焊擠的悍匸凹持冇按《锅炉庠力容器心; 魏If 扌牛考试试板接头形比 施焊的储罐一敕。
油罐施工方案

2.储罐施工方案2。
1施工方法主体安装采用内脚手架正装法,并实施两台罐交叉作业.2.1。
1采用预制场集中预制,用平板车运至安装场地进行组装、焊接。
2.1.2浮顶施工采用临时支架法,便于大角缝、龟甲缝、中央排水管等浮顶附件同时施工。
2。
1.3浮梯采用罐内整体预制方法,在浮顶完工时整体预制,主体完工后整体吊装.2。
1.4加强圈、抗风圈与壁板连接的施工,采用罐壁外行走小车进行作业.2。
1。
5主体完工后立即安装所有配件及附属工程,准备进行上水试验。
2。
1.6在上水试验过程中,开始进行密封、挡雨装置的安装。
2。
3施工技术措施2.3.1材料验收严格按照GBJ128-90第二章材料验收进行。
2。
3。
2基础验收依据GBJ128-90第二节的规定进行验收,各项尺寸必须满足规定要求,同时确定油罐安装方位,并在罐基础上做出临时性标记.2。
3.3预制部分2.3.3.1底板中幅板预制2.3。
3.1.1画线根据安装技术人员提供的尺寸及坡口形式进行画线。
2.3。
3.1.2切割用数控龙门火焰切割机切割板材。
2。
3.3。
1。
3坡口打磨及修补用角向磨光机去除坡口氧化皮,坡口表面凹凸度应小于0.5mm,对于深度大于0.5mm的凹坑,应开长度大于50mm的槽进行补焊、打磨.补焊用焊条应符合工艺评定的要求。
2.3.3。
1。
4底板底面防腐。
2。
3。
3.2底板边缘板预制2。
3.3.2.2切割将半自动氧乙炔切割机放在与边缘板外缘弧相当的弧形轨道上,切割外缘弧边。
其它直线段用直轨道。
先切割直边,然后切割坡口,坡口一次成型。
2.3。
3.2.3按照中幅板要求进行坡口打磨及修补。
2。
3。
3。
2。
4底板底面防腐.2.3.3.3壁板预制2.3。
3。
3。
1画线:根据安装技术人员提供的尺寸及坡口形式,用与安装单位相同的钢尺,分别画切割线及测量线.2。
3。
3。
3.3切割用数控龙门火焰切割机切割板材。
首先按划线位置切割板料,然后再切割坡口,坡口一次成型。
2.3.3。
7.大型储罐制安施工方案

5.1。
2。
5大型储罐制作安装施工方案1.工程概况:芳烃装置有2台8500 m3、2台5000 m3、3台3000 m3、1台592 m3和一台407m3内浮顶罐制安,罐的主体材质Q235B,其储罐安装工程量及规格、技术参数如下表1所示:表12.1.《立式圆筒形钢制焊接油罐施工及验收规范》GB50128-052。
2.《钢制压力容器焊接工艺评定》JB4708—20002。
3.《钢制压力容器焊接规程》JB/T4709-20002.4.《现场设备、工业管道焊接工程施工及验收标准》GB50236-982。
5.《立式圆筒形钢制储罐施工工艺标准》SH/T3530—20012.5.C7芳烃联合装置施工程合同及设计资料3.施工方法及施工工艺程序:3.1.施工方法:5000m3以上(含5000m3)采用液压顶升倒装法安装罐,即先将储罐底板铺设在基础上并用卡具打紧,然后在底板上放出罐壁基准线,依据罐壁基准线组装第一带板并焊接,然后组焊储罐顶板,再在第一带板外侧围第二带板并留一活口,焊接后利用液压千斤顶提升装置将第一带板及顶盖整体提升到与第二带板高度一致,先焊完第二带纵缝找正焊接一、二带板环缝,再在第二带板外侧围第三带板并留一活口,依次提升直到储罐组装完毕.解吸剂罐(T-601、T—602)二甲苯产品检查罐(T-603)采用电动提升倒装法,(在罐壁周边布置多个倒链,倒链由电动驱动装置提供动力),即先将储罐底板铺设在基础上并用卡具打紧,然后在底板上放出罐壁基准线,依据罐壁基准线组装第一带板并焊接,然后组焊储罐顶板,再在第一带板外侧围第二带板并留一活口,焊接后利用到链提升装置将第一带板及顶盖整体提升到与第二带板高度一致,选用参数相同的电动机加配套涡轮涡杆驱动倒链向上提升罐壁,收紧活口,先焊完第二带纵缝找正焊接一、二带板环缝,再在第二带板外侧围第三带板并留一活口,依次提升直到储罐组装完毕。
溶剂罐(T—801)、湿溶剂罐(T—802)采用倒链手动提升倒装法,(在罐壁周边布置多个倒链),即先将储罐底板铺设在基础上并用卡具打紧,然后在底板上放出罐壁基准线,依据罐壁基准线组装第一带板并焊接,然后组焊储罐顶板,再在第一带板外侧围第二带板并留一活口,焊接后利用到链提升装置将第一带板及顶盖整体提升到与第二带板高度一致,用倒链收紧活口,先焊完第二带纵缝找正焊接一、二带板环缝,再在第二带板外侧围第三带板并留一活口,依次提升直到储罐组装完毕.采用液压顶升和倒链提升安装贮罐方法分别如图1-1、图1-2所示:图1-1、液压顶升系统示意图图1-2、倒链(电机驱动)提升装置3.2.施工工艺程序贮罐倒装法施工程序图4.施工技术措施:4.1.施工准备4。
- 1、下载文档前请自行甄别文档内容的完整性,平台不提供额外的编辑、内容补充、找答案等附加服务。
- 2、"仅部分预览"的文档,不可在线预览部分如存在完整性等问题,可反馈申请退款(可完整预览的文档不适用该条件!)。
- 3、如文档侵犯您的权益,请联系客服反馈,我们会尽快为您处理(人工客服工作时间:9:00-18:30)。
☐特殊☐重大☑一般储罐工厂预制和现场组焊技术方案编制:X校审:X批准:XX厂X年X月X日目录1.工程概况 (2)1.1 工程简介 (2)1.2 编制依据 (2)1.3 球罐技术参数 (2)2.预制深度 (3)3.加工工艺及措施 (3)3.1 材料准备 (3)3.2 材料复验 (4)3.3 下料 (4)3.4 球壳板的压制 (5)3.5 球壳板几何尺寸及成形后无损检查 (7)3.6 人孔、接管的组对、焊接 (9)3.7 支柱制作 (10)3.8 支柱与球壳板的组装 (10)3.9 极带板预组装 (11)4.焊接 (12)4.1 焊接施工方法及焊机和附属器具。
(12)4.2 焊工 (12)4.3 焊接工艺 (12)4.4 焊接环境 (12)4.5 焊接预、后热及层间温度控制 (13)4.6 焊材管理 (13)4.7 焊接实施 (14)4.8 焊缝打磨 (15)4.9 焊缝返修及修补 (16)4.10 产品焊接试板 (16)4.11 焊接记录 (16)4.12 焊接检验 (17)5 包装运输 (18)6 措施用料 (18)1.工程概况1.1工程简介本工程为X联合装置(罐区部分),共三台储罐。
其中一台1000m3粗丙烯储罐,两台400m3液化气储罐。
由X设计院设计。
1.2编制依据①GB150-1998《钢制压力容器》②GB12337-98《钢制球形储罐》③GBJ94-86《球形储罐施工及验收规范》④《压力容器安全技术监察规程》1.3球罐技术参数1000m3粗丙烯储罐设计参数表1400m3液化气储罐设计参数2.预制深度①上、下极中板上所有接管、人孔均焊接完毕出厂。
②赤道带与支柱组焊为一体,其余球壳板均净料出厂。
③球罐整体喷砂、油漆、防火层及消防喷淋我厂不负责施工。
3.加工工艺及措施制造工序见球罐制造工艺流程图3.1材料准备3.1.1球罐用钢材应附有质量证明书,并按施工图纸的要求对钢板进行验收。
3.1.2球壳用16MnR钢板应在正火状态使用,要求对钢板进行100%UT检验,按JB4730-94 II级合格。
3.1.3本球罐所用锻件应符合JB4726-94《压力容器用碳钢和低合金钢锻件》III级标准,并应进行正火加回火热处理。
3.1.4球壳的对接焊缝及与球壳直接焊接的焊缝,采用的低氢型焊条应具有质量证明书,质量证明书应包括熔敷金属的化学成分、力学性能、扩散氢含量等。
3.2材料复验3.2.1球壳用钢板必须按炉批号进行复验,复验内容为材料的力学性能、弯曲性能及化学成分。
并每批取两张钢板进行夏比(V型缺口)低温冲击试验。
实验温度-20℃,取样方向为横向,三个试样冲击功的平均值指标为Akv≥34J3.2.2焊接采用的低氢型焊条,按批号进行扩散氢含量复验。
扩散氢实验方法按GB/T3965的规定进行,烘干后的实际扩散氢含量应≤6ml/100g。
3.2.35锻件复验应按JB4726-94《压力容器用碳素钢和低合金钢锻件》的标准进行硬度、化学成分和力学性能复验。
3.3下料3.3.1下料前应核对钢板规格与材质,确认材料已按要求进行复验,并进行外观检查,要求钢材表面良好,无明显压痕、划伤和严重的麻点等缺陷,腐蚀严重的钢板应更换。
3.3.2按排版图要求放样下毛料,周边留有20~40mm余量,每块球壳板不得拼接。
3.3.3切割采用氧气-乙炔气精密切割,作好标记移植,除净毛刺、熔渣。
3.4球壳板的压制3.4.1使用1000t和2000t油压机进行球壳板的压制,胎具的选择与球壳曲率相符。
3.4.2压制采用冷点压成型工艺,球壳点压成型按照S形压延加工顺序路线,逐渐且反复的向球壳板胚料施加点压力,使达到所需的曲率要求。
3.4.3在压制过程中应采用十字样板进行检查,当球壳板弦长大于或等于2000mm时,样板的弦长不得小于2000mm,当球壳板弦长小于2000mm,样板的弦长不得小于球壳板的弦长。
样板与球壳板的间隙不得大于3mm,见图一所示。
样板制作完毕后必须由质检人员确认方能使用。
3.4.4在压制过程中,需考虑压制回弹量,以保证曲率的精度。
3.4.5钢板表面应保持清洁,及时去除氧化皮等杂物,并随时检查钢板表面,防止产生裂纹、折痕等缺陷。
3.4.6吊装使用专用卡具,以防止吊装过程中产生变形。
3.4.7净料及坡口加工3.4.7.1净料样板的制作及使用①净料样板根据排板图绘制出球壳尺寸,在压制成形曲率合格的球壳板上实样制作,选用1.5~2mm厚,宽80~100mm的扁钢做筋条,组焊成网格状,并根据球壳板大小确定长度及宽度方向的筋条数。
筋条用机械方法加工,并除去加工毛刺。
组焊后将使用侧的焊缝打磨至与母材平齐。
样板与球壳板贴附的接触面积,按扁钢条长度计算,不能小于90%。
样板制成后,须经质量检验人员检查合格并打上确认钢印后,方可使用。
②划线时,将样板与球壳板贴附后,用6~8个卡兰将样板固定在球壳板上,使之全面接触且不能移位。
按样板在球壳板上画出中心线、周边标准线、切割线,并用样冲和铅油标记。
每一环带切割后的首件必须进行检查确认,以验证准确性,保证球壳板几何尺寸达到要求,否则需修整样板直至合格方可使用。
样板使用后,须妥善存放,防止变形,影响精度。
3.4.7.2净料及坡口加工①采用自动或半自动切割机、双嘴割炬在专用切割胎具上同时进行切割(除局部处理外不许使用手工切割)。
先加工纵向坡口,后加工环向坡口。
球壳板下净料后须经质检员进行检验确定,以保证球壳板的制造几何尺寸准确。
切割后的球壳板应具有互换性。
②坡口质量a.坡口表面应平滑,表面粗糙度 25um。
b.熔渣与氧化皮应用砂轮机清除干净.坡口表面不得存在裂纹和分层等缺陷。
若有缺陷时,应修磨或补焊,焊补时应将缺陷清除干净,并经渗透探伤确认无缺陷后方可补焊。
补焊工艺与球罐焊接工艺相同,补焊部位应修磨,使其保持设计坡口的形状及尺寸。
c.坡口角度允差±2.5o,钝边±2mm。
每条焊缝坡口至少检查10点。
3.5球壳板几何尺寸及成形后无损检查3.5.1外观检查:目测确认钢板表面及端面是否存在重皮、分层、夹渣、裂纹等有害缺陷。
对于目视检查怀疑存在的缺陷,采用磁粉或渗透探伤方法进行复检。
3.5.2球壳板曲率检查:采用3.4.3条制作的样板按图一所示进行球壳板曲率检查要求任意部位的间隙E≤3mm。
检查样板使用前,应经检验人员确认合格。
3.5.3几何尺寸的检查(见图二)①长度方向弦长允差A±2.5mm;②宽度方向弦长允差B±2mm;③对角线允许偏差C±3mm;④两条对角线应在同一平面上。
用两直线对角测量时,两直线的垂直距离偏差不得大于5mm。
⑤球壳板的最小厚度不得小于47.75mm(400m3球壳板的最小厚度不得小于29.75mm)。
图二3.5.4成形后无损检验①球壳板周边100mm范围内进行100%UT检验,按JB4730-94 II级合格。
②成形后的球壳板应进行UT抽查。
UT抽检数量不得少于球壳板总数的20%,且每带不少于两块,上、下极板不少于一块,检查结果按JB4730-94 II级为合格。
③成形后的球壳板应进行内、外表面MT抽查。
抽检数量不得少于两块(其中一块极板,一块与支柱连接的球壳板)检查结果按JB4730-94 II级为合格。
上述②③条抽查若发现超标缺陷应加倍抽查,若仍有超标缺陷则应100%抽查。
3.6人孔、接管的组对、焊接3.6.1按图纸要求划线,确定无误后开出极中板上各孔并加工坡口,坡口形式按图纸或排版图要求,切割后用砂轮机打磨氧化层及熔渣。
3.6.2开孔球壳板周边100mm范围内及开孔中心一倍开孔直径范围外用弦长不小于1000mm的样板检查极板曲率,最大间隙不得大于3mm。
3.6.3组焊人孔和各接管执行本措施第4条,人孔补强件与壳体进行无间隙组对,组对错边量 1.5mm。
3.6.4嵌入式接管与球壳的对接焊缝和球壳自身的对接焊缝焊后立即进行后热消氢处理(400m3球罐嵌入式接管与球壳的对接焊缝焊后立即进行后热消氢处理)。
3.6.5带有人孔、接管的上、下极带板的尺寸检查见表33.7支柱制作3.7.1支柱采用无缝管制作下料顺序为:下料→切割→外观及尺寸检查。
3.7.2支柱采用钢板卷制,制造顺序为:下料→切割→滚制→纵缝组对→焊接→RT→环缝组对→焊接→RT→外观及尺寸检查。
3.7.3支柱的尺寸检验见表4 表43.8支柱与球壳板的组装3.8.1支柱安装时,用千斤顶等工具将赤道板按要求的曲率加以固定并检测合格后,将支柱放在适当位置并定位,如图三所示。
3.8.2支柱焊接见焊缝表及焊接部分的要求3.8.3尺寸检验见图四和表5表53.9极带板预组装3.9.1组装准备首先对组装胎面找平,其基准面水平误差≤1mm。
在经检验的钢平台上,标出基础中心和中心线,所用的各种样板应经质检人员检查合格后方可使用。
拉杆、加紧丝、螺栓等的选用,应具有足够的强度。
3.9.2组装要求组装时利用工卡具调整对接焊缝的间隙错边量及角变形,不允许强力组对,组对间隙3±1mm,对口错边量≤2mm,组对角变形<7mm,应选用弦长不小于1米的样板检查,每500mm长测量一点。
组装时板号顺序按排版图编号,不得互换,极带板整体预组装。
4.焊接4.1焊接施工方法及焊机和附属器具。
1)球罐附件焊接采用手工电弧焊,并执行其焊缝表。
2)球罐施焊焊机必须完好,并配备计量合格且在有效期内的电流表、电压表。
所有附属机具应完好无损,满足焊接要求。
4.2焊工焊工必须由具有一定施焊经验、焊接成绩稳定并具有“锅炉压力容器焊工考试规则”(劳动部)所规定的相应位置资格且在有效期限内。
4.3焊接工艺根据母材特点、设计图纸要求进行施焊,焊接工艺见焊缝表。
4.4焊接环境当在室外环境施焊时,若出现下列任一情况,且无有效防护措施时,禁止施焊。
a.雨天、雾天或雪天;b.风速超过8m/s;c.环境温度在0℃以下;d.相对湿度在90%以上。
4.5焊接预、后热及层间温度控制1)焊接预、后热及层间温度控制按表6进行:表6①预、后热采用液化气加热。
②预、后热必须均匀,预热宽度应为焊缝中心两侧3倍板厚范围内且≥100mm,测温时距焊缝中心线50mm处对称测量,每条焊缝测温点不少于三对,定位焊及补焊预后热范围应为距补焊中心半径150mm范围内,4.6焊材管理1)焊材必须按“压力容器质量保证手册”规定进行检验、复验,其要求如下:外观检验:焊材外观完整、无破损、受潮、锈蚀。
材质证核对:进行扩散氢含量须 6ml/100g。
2)焊材必须贮存于认定合格的焊材贮存室。
焊材贮存室应满足以下要求:①温度不得低于0℃;②相对湿度不得大于60%;③支架高度及距墙面距离不得小于250mm。
3)焊材烘干①球罐所用焊条使用前必须按表7要求烘干并做相应记录。