YFSJ-GC-002-ER50-6E焊接用钢盘条操作规程
钢结构焊接操作规程

钢结构焊接操作规程XGJZ-QOE-03-07-20041.0 适用范围1.1本规程适用于建筑安装工程现场钢结构手工电弧焊接等操作。
1.2本规程参照《钢结构焊接及验收规程》JGJ 81-91等标准编制而成。
2.0施工准备.2.1材料及主要机具:2.1.2电焊条:⑴电弧焊所用焊条的型号与母材的匹配应符合设计要求。
⑵电弧焊所用焊条,基性能应现场国家标准《碳素焊条》GB700或《低合金钢焊条》GB1591的规定,应有产品合格证书。
⑶设计对焊条无要求时,焊接Q235钢时宜选用E43系列碳钢结构焊条;焊接16M n 钢时选择E50系列低合金结构钢焊条。
2.2作业条件:2.2.1熟悉图纸,做好焊接工艺技术交底。
2.2.2进行工艺能力评定:焊工上岗证有效期、焊机能力、焊接材料、焊接环境、工艺参数。
2.2.3现场供电应符合焊接用电要求。
2.2.4操作人员要求⑴电焊工应经过政府主管部门组织的专门培训,并通过考试,取得相应的上岗证书者。
并在有限期内,上岗证书的有限期为3年。
⑵如果是分包工程,首先应对承包单位的专业施工资质进行审核,选择具有相应资质的承包商,其次应对电焊操作人员进行上岗资格的审核。
2.2.5施工环境的要求⑴焊接工程应在结构尺寸核对无误的情况下进行。
⑵在负温度下焊接对焊接设备应采取防寒措施,-200C以下时不宜焊接,在风速超过7.9m/s时应采取挡风措施;雨雪天不宜在室外现场焊接。
⑶焊接前应清理焊接现场区域内的可燃可爆物质,并配备充足的消防灭火器材,应设置安全照明并保持通风。
办理明火作业申请,并得到相关人员的批准。
2.2.6焊条的焙烘⑴焊条在使用前要检查其是否受潮。
鉴定焊条是否受潮的方法是:------将若干焊条在手掌上滚动,焊条相互磨擦时发出清脆的金属声,则焊条药皮干燥可用,若发出低低的沙沙声,则表明焊药已受潮不能使用;------焊芯上有锈痕,则表明焊药已受潮不能使用;------焊接时焊药皮成块脱落,产生大量水蒸汽等,都表明焊药已受潮不能使用。
焊接用ER50—6盘条的研制

14Pa: MPa,
平均抗拉强度527 ilPa,最小伸长率360,40,平均伸
%辆村}4生产t0』训IJ
2
2
2
l靴逝^Ll地度 3结论
(1)F350
1:艺1’o r艺3所牛产的m祭金棚自l织如削l 所示。曲种上艺金剌组织均为F岬,l艺1 0 1.岂3 所生产盘条的^^牲度分别为0级、9 5级.L艺3生 产的盘条晶粒巫细小.组织蜓均匀。 对工艺l与工艺3对比可知.辊逆入口速度降 低时.F,RSO-6盘条抗拉强度略有F降,但从其金 相组织可见,工艺3比工艺l所生产的盘条金相组 0}均匀,说明辊道^口速度降低可使ER50—6盘条 得到均匀细小的铁索体和极少最的珠光体纽织. 从而获得良好的拉拔性能。
【4]储继钉.卅希海,何#凯.锋梆接¨J钠&条,h.HE仕
”后的蹙化及埘蜱材}r啦的影响…W接.2004
¨)36—4l
0Ⅱr样照.拉拔上艺为
[5】I熏群.耿继烈.彝^m.*^∞m火l=艺的ER?OS一6 蜱熊川盘枭的日制【Jj#饲技术2007(5):30—32 【6】£勇.张嚣萍ER705-6盘采{i拔断裂鲧因分昕【J】盒 WM8.2009.35(6):55—58 [7】崔林甫.万圃辑.杨晓奇.辱焊接朋lm删葩sl^线材的 生产U】盒H制%.2009.35“)35—37 (收捣日期卸Ilq3—30) 作者蔼介 辛■l蛔0年生.宣目1月铁蜒埘有毗谢任2iU第一拣轧 J_轧钢助月I柱Ⅻ. 超自义1965年qt.离鳍I翱师.安Ⅲ钢铁艇团有戳贵仟 *目帮“炼nr“rK。 i克i]978年‘E.安Ⅲ制铁蝇例订戳☆任。司第一炼轧 r'炼钢1程师。 岳囊tl 1983年±.蜜刚制铁啦1月fIm贯ft公t4技术中心
ER50-6盘条拉拔开裂原因分析

国标 0 6 010 0 11 1 0 1 0≤0 2 ≤0 3 ≤O ≤02 . . ~. . ~. . . 0 38 54 8 . 5 . 5 . , 《0 0 0 3 2
22 非金属 夹杂 物 _
对 ab 、 两组试样 的非金属夹杂物进行评级 , 结 果见表 2 。可见两组试样的非金属夹杂物类型 、 级别
袁 长 波
( 青岛钢铁控股集 团有 限公 司 , 山东 青岛 264 ) 603 摘 要: 低合金焊接用钢盘条在挖拔 过程中有时出现劈裂现象 , 为找 出其原 因 , 每一道次 的钢丝 取样 进行金相分析 , 对 发现
Hale Waihona Puke 劈裂 钢丝对应 的盘条和半成 品钢 丝中都存在严重的横 向珠光体带状 偏析 ,且盘条 的横 向带状偏析 与连铸坯 的内部裂纹 有 很好 的对应关系 , 盘条 中存在 的严 重横向带状偏 析是造成钢丝劈 裂的主要原因。 关键词 :R 06盘条 ; E 5— 拉拔 ; 开裂 ; 偏析带 ; 带状组织 中图分类号 :G 4. T 12 3 3 文献标识码 : A 文章编号: 0 -6020 )104—2 1 442 (060 —0 20 0 -
及在钢丝 中的分布都比较正常,且夹杂物经球化变 性处理效果较好( 见图 1。因此 , ) 可以判断 a 批盘条 制成 的钢丝出现劈裂 , 与非金属夹杂物无直接关系。
●- ●o c> ●0 ●0 ●o ●<> ● 0 ●・ ●< > ●<> ●< > ●0 争 ● <> ●< > ●< >● o ●0 ●0 ●o ●o ●o ●o ●
E 5 — 等 )由于其拔丝性能好 , R06 , 成分稳定 , 深受用 户欢迎。 20 年 6 但 00 月份生产的某批号 E 5— 盘 R 06 条, 经焊丝厂拉拔到 1 m . m后 , 的直接劈裂 , 0 有 有 的经简单扭转后开裂。 焊丝生产工艺为 : 盘条经机械 剥 壳 、酸 洗 、 中 和 ,经 5 m + . m_ . m_ 5 r ÷ 5 0 a 42 _ 3 m ÷ 2 mm ÷ 23 m 后 ,进 水 . mm ÷ . m_ . _ . 4 8 m 箱。再经 9 道减径拉成 1 m . m钢丝 , 0 然后酸洗 、 水 洗、 化学镀铜、 定径抛光制成成品钢丝 , 最后绕盘 、 包 装。 钢丝经水箱拉拔后开始发现有劈裂现象, 镀铜后 的焊丝放置数天后表面出现锈蚀。
ER50-6热轧盘条异常显微组织分析

ER50-6热轧盘条异常显微组织分析温国栋;王忠伟;花凌冬【摘要】ER50-6热轧盘条在进行交货检验时发现,盘条中存在混晶、心部马氏体以及白亮带异常显微组织.结合生产工艺分析认为:吐丝温度高是导致盘条产生混晶和心部马氏体的主要原因;末端电磁搅拌强度大引起连铸坯白亮带,偏析遗传导致盘条亦出现白亮带.通过优化控冷工艺和末端电磁搅拌参数,消除了盘条的异常显微组织,合格交货.【期刊名称】《天津冶金》【年(卷),期】2018(000)002【总页数】3页(P57-59)【关键词】混晶;马氏体;白亮带;吐丝温度;末端电磁搅拌【作者】温国栋;王忠伟;花凌冬【作者单位】天津荣程联合钢铁集团有限公司,天津300352;天津荣程联合钢铁集团有限公司,天津300352;天津荣程联合钢铁集团有限公司,天津300352【正文语种】中文0 引言ER50-6(即 GB/T3429中 H11Mn2SiA)系焊接用钢热轧盘条,用于制造气体保护焊丝。
气体保护焊丝的主要生产工序包括拉丝、镀铜和精绕等。
原料盘条通过机械剥壳+电解酸洗的方式去除氧化铁皮,经表面硼化后再进行粗拉以及精拉。
由于拉丝工序无中间热处理过程,所以要求ER50-6热轧盘条必须具有合适的力学性能以及均匀的显微组织,以保证稳定的拉拔生产与良好的焊丝质量。
某公司以转炉→LF→Φ250 mm连铸圆坯→高线工艺流程生产的Φ5.5 mm ER50-6热轧盘条,在进行交货检验时,发现强度偏低,并且存在异常显微组织,无法满足交货要求。
本文针对以上不合格问题进行了分析探讨和工艺优化,有效改善了ER50-6热轧盘条的质量。
1 检验情况ER50-6热轧盘条力学性能要求屈服强度ReL:350~430 MPa,抗拉强度 Rm:470~550 MPa,断面收缩率Z≥70.0%,显微组织要求为均匀的铁素体+珠光体。
某炉强度偏低盘条的初验和复验数据如表1所示。
由表可知,盘条屈服强度尤其偏低,同时对应的抗拉强度和断面收缩率亦存在偏低规律。
钢筋焊接操作规程

钢筋的焊接因受电压、焊条、焊接人员等因素的影响,其质量不稳定,且其属于隐蔽工程,抽检频率有限,故事先的质量控制显得尤为重要,在本项目中,钢筋焊接被列为特殊过程。
为规范施工,提高焊接质量,特制定本作业指导书。
1.人员要求焊工属于特殊工种,按照《安全技术操作规程》和专业性要求,所有用于工程的钢构件,焊接必须由有资格的焊工制作,即焊工必须有合格的上岗证。
2.电压、电流要求2.1受力构件焊接时,输入电焊机的电压要满足额定电压要求,且电压要稳定。
电焊机输出电流必须稳定,且满足各种规格的钢筋焊接要求,以防止电流过高时,烧伤钢筋;电流过低,熔点不足。
2.2搭铁应置于焊逢下或钢筋的末端,以防烧伤主筋。
3.焊条3.1电弧帮条焊及搭接焊所用焊条应满足下表要求:表1编号钢筋类型符合中国标准GB/T5117-1995、GB/T5118-1995的焊条1 Ι级钢 T4212 Ⅱ级钢 T502、T5063.2焊条必须存放在干燥、通风的地方。
禁止使用受潮焊条。
4.焊接环境4.1氧、电焊工的工作环境必须满足《安全技术操作规程》第十二章第二节的要求。
详见《安全技术操作规程》。
4.2环境温度低于5℃时,钢筋在焊接前应预热。
焊接好的钢筋不能淬水,应由其自然冷却。
4.3第一次打底后,应敲除焊渣,待其冷却后,再焊第二批。
5.焊接接头5.1当采用闪光对焊焊接热轧钢筋时:5.1.1为保证对焊质量,钢筋的焊接端应在垂直于钢筋的轴线方向切平,两焊接端面彼此平行。
焊渣必须清除。
5.1.2在构件任一搭接段内,闪光对焊接头的钢筋面积,在受拉区不应超过钢筋总面积的50%。
搭接区段长度内是指30d(d为钢筋直径)长度内但不得小于50cm。
5.2当采用电弧焊焊接热轧钢筋时:5.2.1焊缝长度、宽度、厚度应按图示或按表2取用,参见下图。
在构件任一搭接区段内,电弧焊接头应符合5.1.2条规定;对于两个不同构件的连接,例如钻孔桩与立柱的连接、两预制构件的连接,如采取保证质量措施,且经工程师同意,可以不受上述限制。
钢结构焊接操作规程
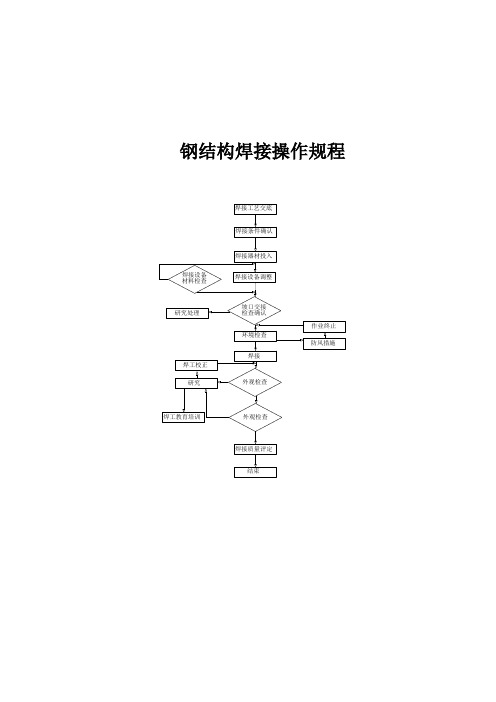
钢结构焊接操作规程焊接工艺交底焊接器材投入焊接条件确认焊接设备调整焊接设备材料检查坡口交接检查确认环境检查焊接作业终止防风措施研究处理焊工校正研究焊接质量评定焊工教育培训结束外观检查外观检查钢结构焊接操作规定1焊接设备应具有参数稳定,调节灵活,满足焊接工艺要求和安全可靠的性能。
2焊工应经过考试并取得合格证,持双证方可从事钢结构工程焊接。
3焊条,焊丝在被使用前,必须按产品说明书及有关工艺文件规定进行烘干。
4低氢焊条烘干温度为350-380℃,保温1.5-2h,烘干应缓冷放置于110-120℃的保温箱中存放,待用,使用时应置于保温筒中,随用随取,烘干后的低氢焊条在大气中放置时间超过4h后应重新烘干,焊条重复烘干次数不宜超过2次,受潮焊条不应使用,并建立焊条烘焙发放领用记录.5酸性焊条烘干温度为100-150℃,保温1-2h,烘后在50℃温度的保温箱中存放。
6彻底清除待焊处表面的水,氧化皮,绣,油污。
7焊接完成后,应由焊工自检合格。
(二)1施焊前,焊工应检查焊接部位的组装和表面清理质量。
如不符合要求,应修磨合格后方能施焊,坡口组装间隙超过允许偏差规定时,可在坡口单侧或两侧堆焊,修磨使其符合要求,但当坡口组装间隙超过较薄板厚度2倍或大于20mm时,可应用堆焊方法增加构件长度或减小组装间隙,焊接接头组装的允许偏差见表3.3.1。
2对接接头,T型接头,角接接头,十字接头等对焊接缝及组合焊接缝应在焊缝的两端设置引弧和引出板,其材料和坡口形式应与焊件相同,引弧和引出的焊缝长度不小于20mm,焊接完毕后应采用气割切除,并修磨平整,不得用锤击落。
3角焊缝转角处宜连续绕角施焊,起落弧点距焊缝端部宜大于10mm。
4定位焊工应有焊工合格证,定位焊所用焊接材料应与焊材质匹配。
焊缝厚度不宜超过设计焊缝厚度的2/3,且不大于8mm,焊缝长度不宜小于40mm,间距宜为500-600mm,定位焊应在焊道内,定位焊缝质量要求同正式焊缝。
ER50-6-盘条的组织与性能分析

ER50-6-盘条的组织与性能分析轧三ER50-6 盘条的组织与性能分析·1·轧三ER50-6 盘条的组织与性能分析任翠华(天津冶金集团轧三金属材料科技有限公司,天津301606)摘要本文简要介绍了天津冶金集团轧三ER50-6 热轧盘条的试轧生产情况,并通过抽样试验,对盘条的主要化学成分、显微组织和力学性能等进行了分析。
确定了盘条的质量能达到标准要求,拉拔性能和焊接性能满足客户要求,表明了盘条的成分控制及轧制工艺设计合理可行。
关键词ER50-6 盘条化学成分显微组织力学性能Analysis of Microstrucrure and Properties of ER50-6Wire Rod for Zhasan CompanyRen Cuihua(Tianjin Metal Materials and Technology Co., Ltd., Tianjin, 301606)Abstract This paper briefly introduces the trial production of ER50-6 hot-rolled wire rod for the Tianjin Metal Materials and Technology Co. Ltd. Through the sampling test, it analyses the main chemical composition, microstructure andproperties of wire rod.The results show that, the quality of wire rod can meet the standard requirements. And the drawing and welding properties can meet customer requirements too.So the conclusion can be drawn that the components in control and the design of wire rod rolling process is reasonable and feasible.Key words ER50-6, wire rod, chemical composition, microstructure, mechanics properties1 前言ER50-6 是碳钢氩弧焊丝,具有优良的塑性、韧性和抗裂性能,尤其低温冲击韧性较高。
金属焊割作业操作规程范本(2篇)
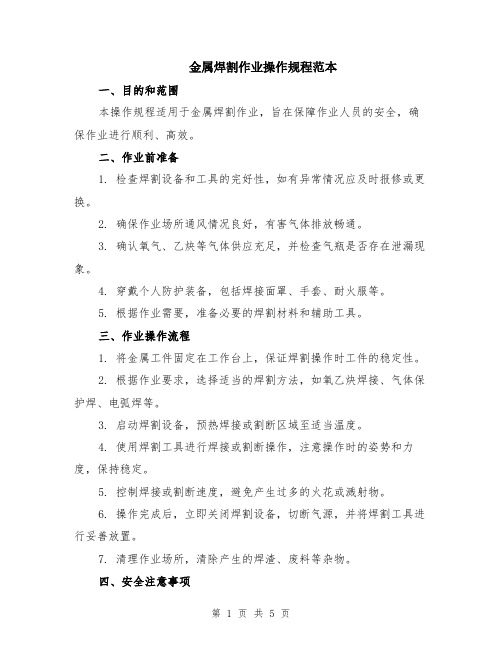
金属焊割作业操作规程范本一、目的和范围本操作规程适用于金属焊割作业,旨在保障作业人员的安全,确保作业进行顺利、高效。
二、作业前准备1. 检查焊割设备和工具的完好性,如有异常情况应及时报修或更换。
2. 确保作业场所通风情况良好,有害气体排放畅通。
3. 确认氧气、乙炔等气体供应充足,并检查气瓶是否存在泄漏现象。
4. 穿戴个人防护装备,包括焊接面罩、手套、耐火服等。
5. 根据作业需要,准备必要的焊割材料和辅助工具。
三、作业操作流程1. 将金属工件固定在工作台上,保证焊割操作时工件的稳定性。
2. 根据作业要求,选择适当的焊割方法,如氧乙炔焊接、气体保护焊、电弧焊等。
3. 启动焊割设备,预热焊接或割断区域至适当温度。
4. 使用焊割工具进行焊接或割断操作,注意操作时的姿势和力度,保持稳定。
5. 控制焊接或割断速度,避免产生过多的火花或溅射物。
6. 操作完成后,立即关闭焊割设备,切断气源,并将焊割工具进行妥善放置。
7. 清理作业场所,清除产生的焊渣、废料等杂物。
四、安全注意事项1. 严禁在易燃物质附近进行焊割作业,并保持作业区域的整洁。
2. 在高温操作区域工作时,禁止穿戴易燃、易熔的服装。
3. 作业人员必须熟悉并遵守相关的安全操作规程,如禁止焊割时戴手表、戒指等物品。
4. 切勿将焊割设备连接错误气源,确保乙炔气瓶的使用和存储符合标准规定。
5. 在使用焊割设备时,注意接地保护,避免触电事故的发生。
6. 当出现设备异常或气体泄漏等状况时,应立即停止作业并及时报修。
7. 焊接或割断完成后,应等待工件冷却后再进行后续操作。
五、事故处理措施1. 发现明火或火花飞溅时,应立即采取措施扑灭,并通知相关人员。
2. 在焊割作业中出现严重的事故或人员受伤时,应立即停止作业,将受伤人员送往医院救治,并及时通知上级主管部门。
3. 对于设备损坏或气体泄漏等情况,应及时报修处理,避免产生二次事故。
六、作业记录每次进行金属焊割作业时,作业人员应填写相应的作业记录,包括作业时间、作业人员、作业内容等,并交由主管部门进行存档。
焊接操作规程

焊接操作规程1. 引言本文档旨在规范焊接操作,确保焊接工作的安全性和质量。
任何从事焊接工作的人员都应遵守本规程。
2. 工作准备在进行焊接操作之前,务必进行以下工作准备:- 根据作业环境和焊接材料选择合适的焊接方法、焊接电流和焊接材料。
- 检查焊接设备是否完好并进行必要的维护。
- 确保焊接操作区域周围的安全,并清除可能引起火灾的杂物。
- 确保焊接操作区域有足够的通风,并佩戴个人防护装备,如焊接面罩、手套和防护服。
3. 焊接操作步骤以下是焊接操作的基本步骤:1. 将焊接设备接通电源,确保工作区域的电气安全。
2. 清理焊接材料和焊接接头,确保表面干净、平整且没有油脂、尘土等污染物。
3. 进行合适的预热或预处理,根据具体焊接规范操作。
4. 调整焊接设备的焊接电流和电压至适宜的水平。
5. 开始焊接操作,保持焊接枪或焊接电极与焊接材料的接触,并保持一定的焊接速度和角度。
6. 在焊接过程中,注意焊接温度、电流和电压的变化,根据需要及时调整。
7. 完成焊接后,关闭焊接设备,待其冷却后进行维护和清洁。
4. 安全注意事项在进行焊接操作时,必须注意以下安全事项:- 严禁在没有有效安全措施的情况下进行焊接操作。
- 焊接操作人员必须穿戴个人防护装备,避免焊接光线和火花对眼睛、皮肤和呼吸系统的伤害。
- 焊接操作区域必须保持通风良好,以避免因焊接过程中产生的有害气体和烟尘对操作人员的危害。
- 在焊接操作期间,严禁使用易燃和易爆物品,以及使用可能引起火灾的设备。
- 焊接设备必须经过合适的维护和检修,以确保其安全性和正常运行。
5. 质量控制为确保焊接质量和连接的强度,应进行以下质量控制措施:- 检查焊接材料的质量和规格是否符合要求。
- 对焊接接头进行适当的准备和预处理,确保其表面干净和无缺陷。
- 控制焊接电流、电压和焊接速度,以确保焊接质量稳定。
- 定期对焊接接头进行无损检测和力学性能测试。
6. 结论本文档为焊接操作规程,对焊接工作的安全和质量进行了规范。
ER50—6焊接用热轧盘条的研制
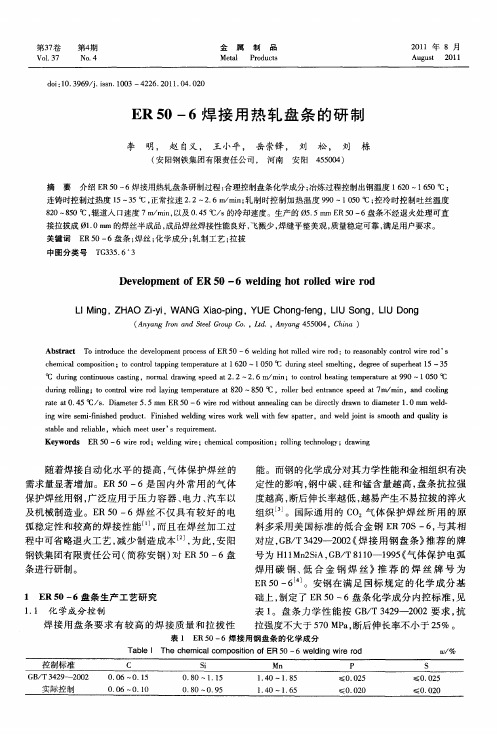
Vo _ I37
第4 期
No 4 .
金
属
制
品
2 1 年 8 月 01
Au u t g s 2 1 01
Mea tl
P o ucs r d t
d i1 . 9 9 j i n 10 o :0 3 6 /.s . 0 3—4 2 . 0 .4 0 0 s 2 6 2 1 0 .2 1
艺 流 程 : 0 10 t复 吹 转 炉 冶 炼 一 L 炉 精 炼 一 F 10l 0m 5 m x1 m六 机六 流方 坯连铸 一 轧制 。 n 5
根据 E 0— R5 6钢 的 C T曲线 可知 , 素体 转变 C 铁 温度 为 7 0o 当冷速 小于 2 5%/ 时 , 会得 到贝 9 C, . s 不
随着焊接 自动化 水 平 的提 高 , 体保 护焊 丝 的 气
能 。而 钢 的化学 成分对 其力学性 能 和金 相组织 有决 定 性 的影 响 , 中碳 、 和锰 含 量越 高 , 条抗 拉 强 钢 硅 盘
需求量显 著增 加 。E 0—6是 国 内外 常用 的 气 体 R5
保 护焊丝用 钢 , 泛 应用 于 压力 容 器 、 广 电力 、 车 以 汽 及 机械制造 业 。E 0— R 5 6焊 丝 不仅 具 有 较 好 的 电 弧稳 定性 和较 高 的焊 接性 能 , 而且 在 焊丝 加 工过 程 中可省 略退 火工 艺 , 减少 制 造成 本 j为 此 , 阳 , 安 钢铁 集团有 限责任公 司 ( 简称 安钢 ) E 0—6盘 对 R5 条进行 研制 。
sa l d r la e,whc e e sr q ie n . tb e a eibl n ih me tusr’ e u r me t
电焊工技术操作规程
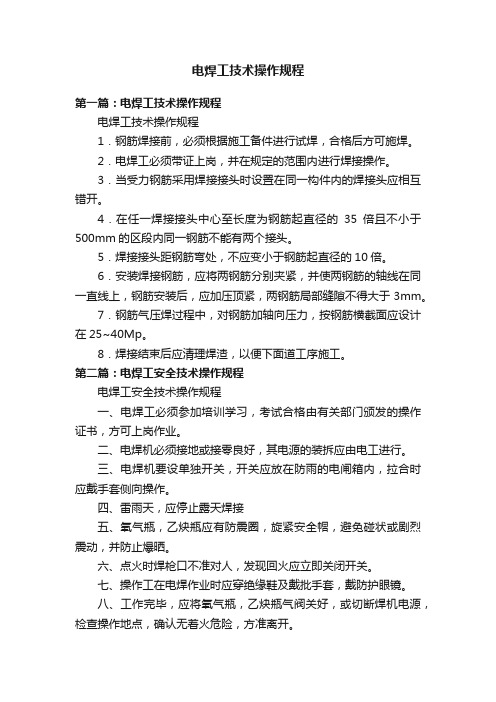
电焊工技术操作规程第一篇:电焊工技术操作规程电焊工技术操作规程1.钢筋焊接前,必须根据施工备件进行试焊,合格后方可施焊。
2.电焊工必须带证上岗,并在规定的范围内进行焊接操作。
3.当受力钢筋采用焊接接头时设置在同一构件内的焊接头应相互错开。
4.在任一焊接接头中心至长度为钢筋起直径的35倍且不小于500mm的区段内同一钢筋不能有两个接头。
5.焊接接头距钢筋弯处,不应变小于钢筋起直径的10倍。
6.安装焊接钢筋,应将两钢筋分别夹紧,并使两钢筋的轴线在同一直线上,钢筋安装后,应加压顶紧,两钢筋局部缝隙不得大于3mm。
7.钢筋气压焊过程中,对钢筋加轴向压力,按钢筋横截面应设计在25~40Mp。
8.焊接结束后应清理焊渣,以便下面道工序施工。
第二篇:电焊工安全技术操作规程电焊工安全技术操作规程一、电焊工必须参加培训学习,考试合格由有关部门颁发的操作证书,方可上岗作业。
二、电焊机必须接地或接零良好,其电源的装拆应由电工进行。
三、电焊机要设单独开关,开关应放在防雨的电闸箱内,拉合时应戴手套侧向操作。
四、雷雨天,应停止露天焊接五、氧气瓶,乙炔瓶应有防震圈,旋紧安全帽,避免碰状或剧烈震动,并防止爆晒。
六、点火时焊枪口不准对人,发现回火应立即关闭开关。
七、操作工在电焊作业时应穿绝缘鞋及戴批手套,戴防护眼镜。
八、工作完毕,应将氧气瓶,乙炔瓶气阀关好,或切断焊机电源,检查操作地点,确认无着火危险,方准离开。
第三篇:9电焊工安全技术操作规程新建广深港铁路客运专线广深段综合工程ZH-2标段电焊工安全技术操作规程中铁十七局集团广深港铁路客运专线ZH-2标项目经理部一分部 2006年11月1日电焊工安全技术操作规程1.电焊机外壳,必须接零接地良好,其电源的拆装应由电工进行。
现场使用的电焊机应设有可防雨、防潮、防晒的机棚,并备有消防器材。
2.电焊机要设单独的开关,开关应放在防雨的闸箱内,拉合时应戴手套侧向操作。
3.焊钳与把线必须绝缘良好,连接牢固,更换焊条应戴手套,在潮湿地点工作,应站在绝缘胶板或木板上。
钢筋焊接机操作规程

钢筋焊接机操作规程目的本操作规程的目的是确保钢筋焊接机的安全操作,并提供操作人员所需的指导,以保障工作效率和质量。
适用范围本操作规程适用于所有使用钢筋焊接机的工作场所和操作人员。
安全要求操作人员在操作钢筋焊接机时应严格遵守以下安全要求:1. 确保钢筋焊接机的工作环境清洁、通风良好,并远离易燃物和可燃气体。
2. 使用钢筋焊接机前,应进行必要的检查和维护,确保设备的正常工作。
3. 操作人员应穿戴好安全防护装备,如手套、护目镜和防护服。
4. 操作人员应接受必要的培训,熟悉钢筋焊接机的操作方法和安全注意事项。
5. 钢筋焊接机在使用中应保持稳定,避免晃动和碰撞。
6. 操作人员应避免将手部或其他身体部位靠近焊接电极或熔化的钢筋。
7. 在操作过程中,操作人员应时刻注意周围的工作人员和环境,确保安全。
操作步骤以下为钢筋焊接机的基本操作步骤:1. 开机准备:- 检查钢筋焊接机的电源线和接地线是否正常连接。
- 打开电源开关,并进行必要的预热。
- 检查焊接电极是否正常,如有损坏应及时更换。
2. 调整焊接参数:- 根据焊接材料和厚度,调整电流和焊接时间。
- 确保焊接参数与要求相符。
3. 开始焊接:- 将焊接电极对准焊接位置,并稳定握紧。
- 按下启动按钮,开始进行焊接。
- 在焊接过程中保持稳定的焊接速度和力度,保证焊接质量。
4. 完成焊接:- 焊接完成后,松开焊接电极,并断开电源。
- 检查焊接质量,如有不良情况应及时整改。
维护和保养为确保钢筋焊接机的正常工作和延长其使用寿命,应进行定期的维护和保养:1. 定期清洁机器表面和内部杂物,保持通风良好。
2. 检查电源和接地线的连接是否松动或损坏,及时进行修复或更换。
3. 定期检查焊接电极和电缆是否正常,如有需要,及时更换。
4. 根据使用情况,定期注油或润滑机器运动部件。
总结以上是钢筋焊接机的操作规程,操作人员在操作钢筋焊接机时应严格遵守安全要求,并按照操作步骤进行操作。
维护和保养工作也不能忽视,以确保钢筋焊接机的正常工作和使用寿命。
钢筋对焊机操作规程
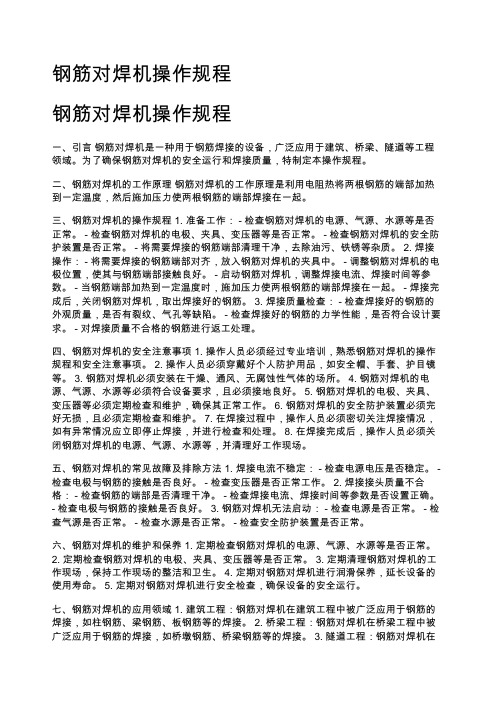
钢筋对焊机操作规程钢筋对焊机操作规程一、引言 钢筋对焊机是一种用于钢筋焊接的设备,广泛应用于建筑、桥梁、隧道等工程领域。
为了确保钢筋对焊机的安全运行和焊接质量,特制定本操作规程。
二、钢筋对焊机的工作原理 钢筋对焊机的工作原理是利用电阻热将两根钢筋的端部加热到一定温度,然后施加压力使两根钢筋的端部焊接在一起。
三、钢筋对焊机的操作规程 1. 准备工作: - 检查钢筋对焊机的电源、气源、水源等是否正常。
- 检查钢筋对焊机的电极、夹具、变压器等是否正常。
- 检查钢筋对焊机的安全防护装置是否正常。
- 将需要焊接的钢筋端部清理干净,去除油污、铁锈等杂质。
2. 焊接操作: - 将需要焊接的钢筋端部对齐,放入钢筋对焊机的夹具中。
- 调整钢筋对焊机的电极位置,使其与钢筋端部接触良好。
- 启动钢筋对焊机,调整焊接电流、焊接时间等参数。
- 当钢筋端部加热到一定温度时,施加压力使两根钢筋的端部焊接在一起。
- 焊接完成后,关闭钢筋对焊机,取出焊接好的钢筋。
3. 焊接质量检查: - 检查焊接好的钢筋的外观质量,是否有裂纹、气孔等缺陷。
- 检查焊接好的钢筋的力学性能,是否符合设计要求。
- 对焊接质量不合格的钢筋进行返工处理。
四、钢筋对焊机的安全注意事项 1. 操作人员必须经过专业培训,熟悉钢筋对焊机的操作规程和安全注意事项。
2. 操作人员必须穿戴好个人防护用品,如安全帽、手套、护目镜等。
3. 钢筋对焊机必须安装在干燥、通风、无腐蚀性气体的场所。
4. 钢筋对焊机的电源、气源、水源等必须符合设备要求,且必须接地良好。
5. 钢筋对焊机的电极、夹具、变压器等必须定期检查和维护,确保其正常工作。
6. 钢筋对焊机的安全防护装置必须完好无损,且必须定期检查和维护。
7. 在焊接过程中,操作人员必须密切关注焊接情况,如有异常情况应立即停止焊接,并进行检查和处理。
8. 在焊接完成后,操作人员必须关闭钢筋对焊机的电源、气源、水源等,并清理好工作现场。
钢筋对焊机安全操作规程
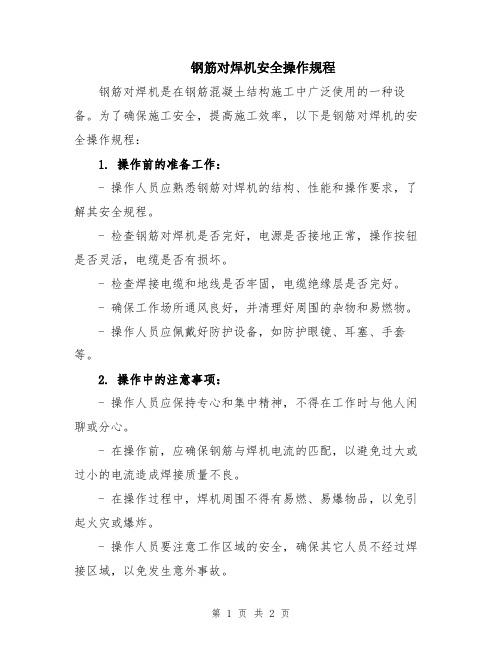
钢筋对焊机安全操作规程钢筋对焊机是在钢筋混凝土结构施工中广泛使用的一种设备。
为了确保施工安全,提高施工效率,以下是钢筋对焊机的安全操作规程:1. 操作前的准备工作:- 操作人员应熟悉钢筋对焊机的结构、性能和操作要求,了解其安全规程。
- 检查钢筋对焊机是否完好,电源是否接地正常,操作按钮是否灵活,电缆是否有损坏。
- 检查焊接电缆和地线是否牢固,电缆绝缘层是否完好。
- 确保工作场所通风良好,并清理好周围的杂物和易燃物。
- 操作人员应佩戴好防护设备,如防护眼镜、耳塞、手套等。
2. 操作中的注意事项:- 操作人员应保持专心和集中精神,不得在工作时与他人闲聊或分心。
- 在操作前,应确保钢筋与焊机电流的匹配,以避免过大或过小的电流造成焊接质量不良。
- 在操作过程中,焊机周围不得有易燃、易爆物品,以免引起火灾或爆炸。
- 操作人员要注意工作区域的安全,确保其它人员不经过焊接区域,以免发生意外事故。
- 在操作钢筋对焊机时,不得同时进行其他手工作业,以免分心导致事故发生。
- 操作人员应定期检查焊接电缆和焊枪,确保其绝缘性能良好,防止漏电和触电事故。
- 当操作完成或暂时停止操作时,应将钢筋对焊机断电,并撤离施工现场。
3. 紧急情况处理:- 若发生钢筋对焊机漏电、触电、冒烟等异常情况,应立即切断电源,并报告相关人员处理。
- 若发生火灾或爆炸等紧急情况,应迅速撤离现场,并报警求助,切勿随意靠近或扑灭火源。
- 若操作人员发生意外伤害,应立即停止操作,寻求及时的医疗救治,并报告相关人员处理。
总之,对钢筋对焊机的安全操作规程是确保施工安全的重要保障措施。
操作人员应熟悉钢筋对焊机的操作方法和安全要求,严格按照规程操作,做到专心、细致、谨慎,以确保施工安全和焊接质量。
ER50-G焊丝用盘条粗拉拔断裂原因分析
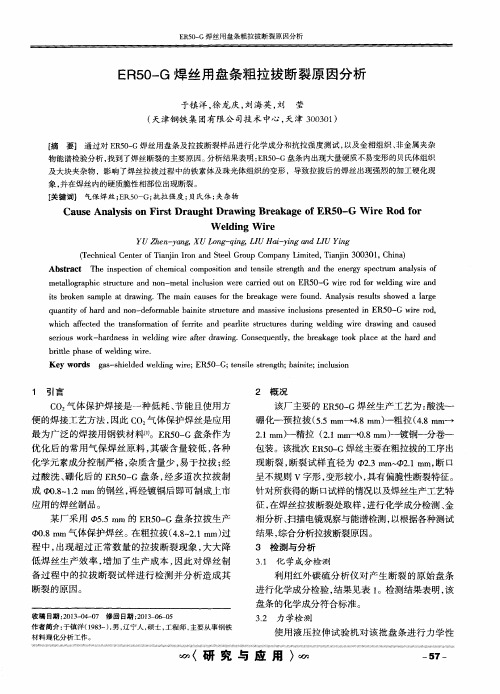
i t s b r o k e n s a mp l e a t d r a wi n g ., I ’ h e ma i n c a u s e s f o r t h e b r e a k a g e we r e f o u n d.An a l y s i s r e s u l t s s h o we d a l a r g e q u a n t i t y o f h a r d a n d n o n- d e f o r ma b l e b a i n i t e s t r u c t u r e a nd ma s s i v e i n c l u s i o n s p r e s e n t e d i n ER5 0 一G wi r e r o d ,
YU Z h e n - y a n g , XU L o n g- q i n g , LI U Ha i - y i n ga ndLI U Yi n g
( T e c h n i c a l C e n t e r o f T i a n j i n I r o n a n d S t e e l G r o u p C o m p a n y L i m i t e d , T i a n j i n 3 0 0 3 0 1 , C h i n a )
Ab s t r a c t Th e i n s p e c t i o n o f c h e mi c a l c o mp o s i t i o n a n d t e n s i l e s t r e ng t h a n d t h e e ne r g y s p e c t r u m a n a l y s i s o f
me t a l l o g r a p h i c s t uc r t u r e a n d n o n - me t a l i n c l us i o n we r e c a r r i e d o u t O i l ER5 0 - G wi r e r o d f o r we l d i n g wi r e a n d
ER50-6焊丝钢开发生产实践

ER50-6焊丝钢开发生产实践孙衍国;刘吉志【摘要】广富集团采用单渣快速脱磷,出钢[P]≤0.010%,终点碳0.035%~0.05%;LF 精炼控制渣系和氧含量;连铸全程保护浇注、塞棒自动控制以及结晶器电磁搅拌;控轧控冷,成功开发生产了ER50-6焊丝用钢.产品检验表明,钢的化学成分均匀、稳定,氧含量(15~35)×10-6,铸坯组织致密,中心疏松≤1.0级,热轧盘条抗拉强度500~550 MPa,断后伸长率≥25%.%Adopting single slag fast dephosphorization for tapping[P]≤0.010%and 0.035%-0.05%aim carbon content in converter operation, controlling refining slag system and the oxygen content in LF, using full protection pouring, stopper automatic control and mould electromagnetic stirring in casting and control rolling and control cooling in rolling, Guangfu Group developed and produced ER50-6 welding wire steel. The Product inspection showed that the chemical composition is stable and uniform. The oxygen content in the steel is (15-35)×10-6. Casting billet microstructure compacts;The central porosity is≤1.0 grade. The tensile strength of the hot rolled wire rod is 500-550 MPa and the elongation is≥25%.【期刊名称】《山东冶金》【年(卷),期】2015(037)003【总页数】2页(P13-14)【关键词】ER50-6焊丝钢;产品开发;终点碳;精炼渣【作者】孙衍国;刘吉志【作者单位】山东广富集团有限公司技术中心,山东滨州256217;山东广富集团有限公司技术中心,山东滨州256217【正文语种】中文【中图分类】TF762为应对严峻的钢铁形势,山东广富集团有限公司(简称广富集团)通过扩大产业链来提高市场竞争力。
ER50-6热轧盘条质量控制与轧制工艺研究

t mp r tr sf m 8 0℃ t 0 e e au e i r 6 o o9 0℃ ,w r a i g tmp r t r sf m 0 ℃ t 2 i ly n e e e a u ei o 8 0 r o 8 0℃ ,c oi g s e d atrr l n . 5 o l p e e ol g i 0 5 n f i s  ̄ s t , 5 ̄ s ie o a h p s i e s a e s o l e c n r l d srcl n r l n r c s ,g o v n u d r n C/ O 0 8 C/ ,sz fe c a s bl t h p h u d b o t l t t i ol g p o e s r o e a d g i e a e i l oe i y i
u l y ter l gpo s i dut , t to i prt ei f m 9 5℃ t 90℃ , ns oig i euig q a t, h ln r essajs d s r rl gtm ea r o 5 i oi c e a ln e u sr o7 i h l f i rln (s er c ) z d n
Ab ta t T e q ai fE S — ie rd frw l i gi n y e rte p r o e t a R 0—6 wi o rw l ig c n s r c h u l y o R 0—6 w r o e dn sa a z d f u p s h t S — r r d f ed n a t o l o h E e o b rwn t i mee . ed a d a tr 8 mm n s e rd c i o t n e l g n i we r g i n r li r w n .T ef c a ee o 0 i f ih d p o u t t u n ai ,a d d e ai o ma d a i g h a t h tt r w h a n n s n t h ae n b i u ee t s c so e lp.wu s a d s a n wi o u fc s rq ie . Mir s u t r S fri n i l r o o v o s d f cs u h a v r a lt n c ri r rd s r e i e ur d e a c o t cu e i e r e a d l t r t te p al e,v l mefa t n o ri so e 0% ,tn i t n t sb l w 5 0 MP .Ai n t h a tr f c ig d a i g e rt i ou r ci ff r ei v r o e t 8 e sl sr gh i eo 6 a e e mi g a ef co saf t rw n t e n
钢筋焊接操作规程
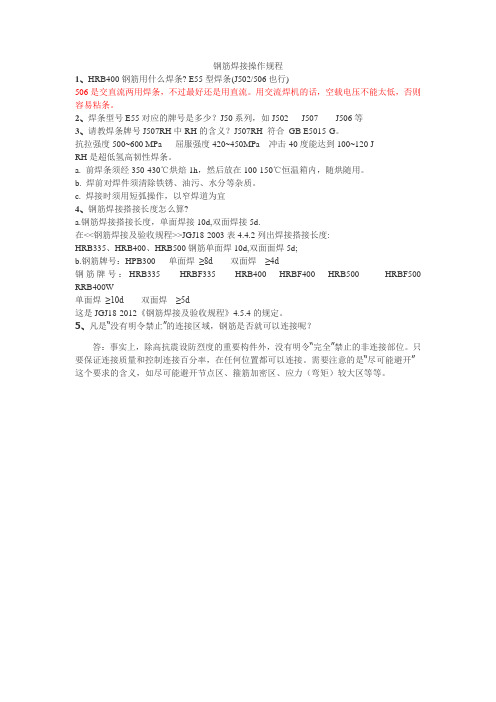
钢筋焊接操作规程1、HRB400钢筋用什么焊条? E55型焊条(J502/506也行)506是交直流两用焊条,不过最好还是用直流。
用交流焊机的话,空载电压不能太低,否则容易粘条。
2、焊条型号E55对应的牌号是多少?J50系列,如J502 J507 J506等3、请教焊条牌号J507RH中RH的含义?J507RH 符合GB E5015-G。
抗拉强度500~600 MPa 屈服强度420~450MPa 冲击-40度能达到100~120 JRH是超低氢高韧性焊条。
a. 前焊条须经350-430℃烘焙1h,然后放在100-150℃恒温箱内,随烘随用。
b. 焊前对焊件须清除铁锈、油污、水分等杂质。
c. 焊接时须用短弧操作,以窄焊道为宜4、钢筋焊接搭接长度怎么算?a.钢筋焊接搭接长度,单面焊接10d,双面焊接5d.在<<钢筋焊接及验收规程>>JGJ18-2003表4.4.2列出焊接搭接长度:HRB335、HRB400、HRB500钢筋单面焊10d,双面面焊5d;b.钢筋牌号:HPB300 单面焊≥8d 双面焊≥4d钢筋牌号:HRB335 HRBF335 HRB400 HRBF400 HRB500 HRBF500RRB400W单面焊≥10d 双面焊≥5d这是JGJ18-2012《钢筋焊接及验收规程》4.5.4的规定。
5、凡是“没有明令禁止”的连接区域,钢筋是否就可以连接呢?答:事实上,除高抗震设防烈度的重要构件外,没有明令“完全”禁止的非连接部位。
只要保证连接质量和控制连接百分率,在任何位置都可以连接。
需要注意的是“尽可能避开”这个要求的含义,如尽可能避开节点区、箍筋加密区、应力(弯矩)较大区等等。
- 1、下载文档前请自行甄别文档内容的完整性,平台不提供额外的编辑、内容补充、找答案等附加服务。
- 2、"仅部分预览"的文档,不可在线预览部分如存在完整性等问题,可反馈申请退款(可完整预览的文档不适用该条件!)。
- 3、如文档侵犯您的权益,请联系客服反馈,我们会尽快为您处理(人工客服工作时间:9:00-18:30)。
YF/SJ-GC-002 ER50-6E焊丝用钢盘条技术操作规程1.工艺路线低硫铁水→120吨转炉→LF炉→8机8流连铸→高线轧制2.技术要求2.1标准执行GB/T 3429-2002标准2.2注:钢中残余元素Cr、Ni、Cu、Mo、Pb、Sn均≤0.040%,Al≤0.005%, As≤0.010%。
2.3力学性能抗拉强度:510≤Rm≤540MPa;A≥28%。
2.4表面质量盘条表面不得有裂纹、折叠、结疤、耳子、分层及夹杂。
2.5夹杂物控制B类≤2级,C类≤2.5级;Be类≤1.5级,Ce类≤2级3.质量考核对于不符合本技术规程标准要求的钢坯、钢材,均纳入一次合格率考核。
4.附件附件1、2、3分别为炼钢工艺操作要点、轧钢工艺操作要点、检验项目及取样数量要求。
附件1ER50-6E炼钢工艺操作要点1、冶炼工艺流程高炉铁水→鱼雷罐车→铁水包→120T转炉→LF炉外精炼→连铸机2、化学成份控制要求注:①严格按内控成分控制。
Cu、Ni≤0.10%,Cr≤0.15%,Ca≤0.0012%,Al T ≤0.005%;②转炉须保证精炼的进站的成份。
3、工艺条件3.1 原材料条件3.1.1 铁水:Si ≥0.20% ,P≤0.125%,温度≥1300℃。
3.1.2 废钢:采用干燥、块度合适(单重≯50kg)、优质废钢,不得含有有色金属。
3.1.3高硅硅锰:Si≥27%;Mn≥60%;P≤0.10%;S≤0.025%;C≤0.15%;水份≤0.5%,粒度:10mm~70mm;低铝硅铁:74%≤Si≤80%,P≤0.035%,S≤0.02%,Al≤0.5%,粒度10-50mm。
3.1.4造渣料等原料应干燥,不得潮湿;严禁使用污泥球、返渣。
3.1.5 氧枪、烟罩漏水时,不得冶炼该钢种。
负责人:炉长3.2 钢包条件3.2.1 使用镁碳钢包,要求底吹通畅,包沿清理干净,严禁使用新包、喷补包和带包底的钢包出钢,钢包正常周转2-3炉(温度要求≥900℃)。
3.2.2 使用铬质引流沙,保证大包自开率≥98%。
3.2.3 所用原材料要求尽量减少Al2O3和TiO2含量。
4 转炉工艺:4.2 装入制度:160±1t(150+10),负责人:兑铁工。
4.3 供氧制度:4.3.1 使用五孔(140)氧枪冶炼,采用分阶段恒压变枪操作;4.3.2工作氧压控制在0.75-0.90Mpa,全程供氧时间15-18分钟;4.3.3 冶炼终点前要采取低枪位操作,终点压枪>30秒;4.3.4底吹模式:底吹全程吹氩气,气量180-260Nm3/h。
4.4 造渣制度4.4.1保证终点脱磷效果,加强吹炼过程操作,过程化渣适量使用萤石,确保全程化渣,【P】≤0.015%,【S】≤0.020%,终渣碱度控制在2.8-3.5,终渣MgO控制在8-10%;4.4.2全部渣料在终点前3分钟加完,补吹时严禁加入矿石/烧结矿。
全程渣子化好、化透,全程禁止加入铁矾土、污泥球、返渣;遇下雨天矿石或烧结矿潮湿,使用烧结料仓中的烧结矿;4.4.3使用萤石调整渣粘度,终渣不透不允许放钢。
4.5 出钢操作:4.5.1 冶炼前,必须将挡渣车调整到合适状态,进行准确的定位,确保挡渣锥投放到位;4.5.2 出钢口良好,不出现散流现象;出钢时间≥4.5min。
4.5.3出钢前打开氩气,并对钢包吹氩搅拌15秒钟,出钢过程中全程吹氩,视钢水翻滚情况调整氩气压力。
4.5.4 采用挡渣塞、挡渣锥挡渣方式,分别挡住转炉一次渣和二次渣;严禁出钢过程下渣。
4.5.5 出钢前检查挡渣塞情况,挡渣锥投放时间,当炉内钢水出到3/4-4/5时,将挡渣锥投到出钢口上方挡渣出钢。
4.6 脱氧合金化:4.6.1 所有入炉合金必须烘烤4.6.2放钢前先加入0.5-1kg/t低铝硅铁进行预脱氧;放钢1/4时开始加入低铝硅铁、高硅硅锰(严禁出完钢后加合金)进行合金化,放钢碳≤0.04%时,加入0.5kg/t硅钡铝脱氧剂。
4.6.3在加完合金之后加入顶渣,顶渣料配比:先加700kg钢帘线精炼渣(2#预熔渣),随后加入500kg石灰(次序不可颠倒)。
4.8 冶炼周期:≤50分钟。
5 精炼工艺:5.1工艺流程进站测温定氧通电调整温度、成份合格后定氧后开钢包车加覆盖剂软吹测温上钢注:浇次前5炉要求进出站定氧,并对成品样化验钢中钙、铝、砷含量。
注:除连铸更换套管及中包开6个流以下时,由连铸机机长要平台温度,其他情况由精炼车间控制中包温度。
5.4 4进站后,开氩气搅拌同时定氧,继续加热钢水至1560℃以上,加入石灰300Kg、预熔渣100Kg(根据蘸渣情况,决定是否补加石灰)继续加热至1580-1590℃,[O]控制在30PPm以下。
5.5 当钢渣变为流动性较好的液态渣时,加入硅铁粉、碳化钙等脱氧剂进行脱氧(严禁使用碳粉脱氧),过程炉长用探渣棒看渣子是否为白渣,直到达到白渣为止,白渣保持时间≥10min。
5.6 形成均匀白渣后,停止通电,测温取钢样、渣样。
根据成分分析结果,加入高硅硅锰、低铝硅铁、普通硅锰微调成分。
5.7 根据渣碱度情况(碱度控制在1.5-2.0)加入硅石砂。
5.8 精炼过程中炉盖盖严,送电脱硫时适当将除尘阀关闭,尽力防止增氮。
加料时钢水裸露直径不得大于300mm。
5.9 连浇炉次软吹时间>15分钟,浇次第一炉及转炉补炉第一炉软吹时间>25分钟,氩气压力控制以钢包液面蠕动为准,整个软吹过程不得吹破渣层,软吹开始后,必须勤检查,防止氩气压力波动造成停吹。
5.10 出站时加入中包预熔覆盖剂、碳化稻壳;覆盖剂加入量确保覆盖住包面,加覆盖剂禁止向氩气流上扔。
5.11 精炼周期:连浇炉次≤50分钟,需调整节奏时,提前向调度说明,连铸降低拉速,保证软吹时间。
5.12 每炉取精炼炉渣化验,需调整节奏时,提前向调度说明,连铸降低拉速,保证软吹时间。
6 连铸6.1工艺参数6.1.1 液相线温度为1515℃6.1.2 结晶器水:1800L/min。
6.1.3 二冷水:采用1#水表。
6.1.4 振动模式采用“5模式”。
6.1.5 结晶器电磁搅拌参数:I=280A、f=5Hz。
6.1.6 结晶器保护渣采用自动加;型号为:ST-SP/BT1;保护渣必须烘烤。
注:中间包温度低于1530℃,连铸须催促下一包钢水,准备转包浇下一炉,以免钢水结流事故发生。
6.1.8 开浇前要通水检查喷水情况,保证喷嘴喷水正常无堵塞,喷淋架保持对中。
6.2 工艺要求6.2.1精炼第一炉开始软吹时,连铸机进行关火试棒,中包闭火至大包开浇不得大于5分钟。
6.2.2大包到中包采用套管保护浇注,大包长水口必须加密封圈,并且要求大包长水口采用吹氩气保护(保证不大翻,但一定要给够,减少带入的空气量)。
(浇注时,插入钢液的套管周围渣面上应有较多的气泡冒出或火花溅起。
)以便减少从接缝处抽入钢水的空气量。
6.2.3中包到结晶器采用浸入式水口保护浇注。
浸入式水口与中包滑块的接缝应密闭,防止浇注时抽入空气。
浸入式水口要垂直对中,插入钢水深度控制在100-140mm。
每次退下的浸入式水口,要检查其渣线的深度。
6.2.4中包换套管时尽可能在坯子接头位置。
操作时必须两人配合,先把烘烤好的套管准备好,一人摘下原套管,另一人马上换上新的,减少裸浇时间。
换套管甩坯必须单独管理发放,ERP上必须有产出,以便最后做统一处理;其他特殊情况甩坯,如液面大幅波动或无电搅的钢坯,直接甩出不必点产出。
6.2.5第一包钢水开浇达到10吨后,加干燥后的无碳低硅覆盖剂、碳化稻壳(碳化稻壳须加在无碳低硅覆盖剂之上)。
当长水口在液面之上时,严禁向大包注流区加入覆盖剂。
6.2.6中间包每班及时排渣,中包渣厚不允许超50mm。
6.2.7当中包内钢水达12-13吨时开始测温,钢水重量大于16吨时中包开浇,开浇采用塞棒手动模式开浇,起步拉速控制在1.3~1.5m/min,全流开浇后中包按满包控制。
6.2.8开浇顺序:2流、7流,1流、8流,3流、6流,4流、5流;6.2.9 连铸坯切头、尾坯长度大于4.5米。
6.2.10 连铸坯标识:符合内控标准成分的钢坯按照《钢坯、钢材管理规定》在每夹钢坯两侧的两根钢坯的一个端面及一个侧面涂上“E”,并在钢坯侧面描写相应的钢种炉号。
6.2.11在钢包转包的过程中,中包内的钢水不得少于30吨,禁止大包下渣。
6.2.12、火切工随时检查、及时调整火焰切割机及割嘴的工作状态,确保铸坯切割断面平整,连铸坯端面长度加切割渣厚度<162mm。
6.2.13、主控人员应与出坯人员及时通报每炉的钢水量及大包停浇时间,以便按炉分坯数量准确。
6.2.14、铸坯质量应按行业标准(YB/T2011----2014连续铸钢方坯和矩形坯)进行控制和检验。
6.2.15 中包停浇:停最后两个流之前,必须保证中包钢水重量在14-15吨。
暂留的钢坯涂上白漆。
附件2ER50-6E轧钢高线工艺操作要点1.加热部分1.1钢坯的检查对钢坯表面质量的检查严格执行YB/T2011-2014标准,剔除表面缺陷的钢坯。
严格执行按炉送钢制度。
2.轧钢部分2.1轧制温度2.2水箱控制2.3风冷辊道控制2.3.2保温罩保温罩全部关闭。
2.4力学性能钢材力学性能按按510≤Rm≤540MPa、A≧28%控制。
2.5表面质量盘条表面不得有裂纹、折叠、结疤、耳子、分层及夹杂。
2.6盘条外形、尺寸逐盘使用相应精度的量具测量,盘条表面质量逐盘用目视检查盘条外形尺寸按C级精度控制(允许偏差±0.15,不圆度≤0.24),按B级精度判定允许(偏差±0.25,不圆度≤0.40),重量及允许偏差严格执行GB/T14981-2009的规定。
3.收集部分3.1关于产品的验收、打包、标志严格执行GB/T2101-2008标准。
3.2包装质量控制:盘条头、尾、耳子要修剪干净,具体圈数现场根据实际情况灵活掌握,轧制过程中产生的圈形大、多头乱丝、耳子等表面质量不符合要求的钢材,负责挑出单独存放。
3.3码垛时按照整炉码垛,由南向北依次码垛。
3.4打印标牌执行标准为:GB/T 3429-2002,牌号:ER50-6E。
3.5标牌颜色:粉红无许可标牌。
附件3ER50-6E检验项目及取样数量要求。