叶轮叶片加工
hyperMILL在叶轮和叶片加工中的应用
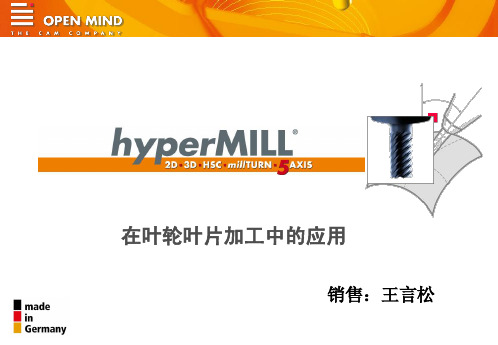
OPEN MIND Technologies Italia Srl Rho/ Milano, Ancona, Padova © 2011 by OPEN MIND Technologies Asia Pacific. All rights reserved.
hyperMILL® 用户
12
© 2011 by OPEN MIND Technologies Asia Pacific. All rights reserved.
5轴叶轮点加工
使用刀具点位接触对叶片
精加工
自动产生螺旋刀路,无中
间进退刀
可自定义加工深度 自动干涉检测并避免避让 可加工任意曲面
24
© 2011 by OPEN MIND Technologies Asia Pacific. All rights reserved.
5轴叶轮侧刃加工
使用刀具侧刃对叶片精加工 自动计算刀具贴合位置及轴
向
球头刀,圆鼻刀皆可使用 可加工自由曲面
25
© 2011 by OPEN MIND Technologies Asia Pacific. All rights reserved.
5轴叶轮进排气缘加工
精加工叶片进排气缘 与两侧光滑连接 可保持顺铣 自动干涉检测并避免避让
位置和轴向
支持残留模型进行多次开粗 自动干涉检测并避免避让 支持球头刀,圆鼻刀等 提供多种加工策略 支持4+1轴加工
19
© 2011 by OPEN MIND Technologies Asia Pacific. All rights reserved.
径向分层
5轴叶轮粗加工
两叶片之间去除大余量 自动在叶片间计算最优
数控加工工艺及设备PPT课件:整体叶轮五轴加工中心加工工艺编制及程序生成

表2-4-4 整体叶轮数控加工合理的装夹方案
装夹序号
装夹方法
定位基准
使用夹具
表2-4-12 学生任务6参考答案:整体叶轮五轴加工中心加工合理的装夹方案
在五轴加工中心数控回转盘上安装专用夹具 夹紧工件,工件以底部外圆柱面+底面为定位基 准,底部中心M10螺纹锁紧。
装夹序号 1
装夹方法 底部中心 M10 螺纹锁紧
序号 1 2 3 4 5 6 7 8 9 10
表面名称
使用刀具名称 刀尖圆弧半径 刀具半径
表2-4-11学生任务5参考答案:整体叶轮数控加工选用的刀具及
参数
序号
加工内容
使用刀具名称
刀角半径 刀具半径
五轴加工用包络毛坯的粗加工
400R C32-32-160
1
(三轴数控加工)
(Ф 32 立铣刀杆)
0.8
D8R4 (Ф 8 球铣刀)
4
4
精加工叶片
D8R4
7
(此工序可完成 9 个叶精片加的工侧叶面片和前缘面的精加工)
(Ф 8 球铣刀)
4
4
(特别说明:此工序可完成 9 个叶片的侧面和前
D6R3
8
叶轮叶根圆角清根 缘面的精加工)
(Ф 6 球铣刀)
3
3
学生任务6:填写表2-4-4 整体叶轮数控加工合理的装 夹方案
表面加工刀路生成 CAVITY_方MI式LL ZLEVEL_PROFILE
ZLEVEL_PROFILE MULTI_BLADE_ROUG H HUB_FINISH BLADE_FINISH BLADE_FINISH BLEND_FINISH
学生任务4:填写整体叶轮加工 选来自的设备及主要规格和技术参数表2-4-1 整体叶轮需加工部位及表面
风力发电机组叶轮叶片的改进设计
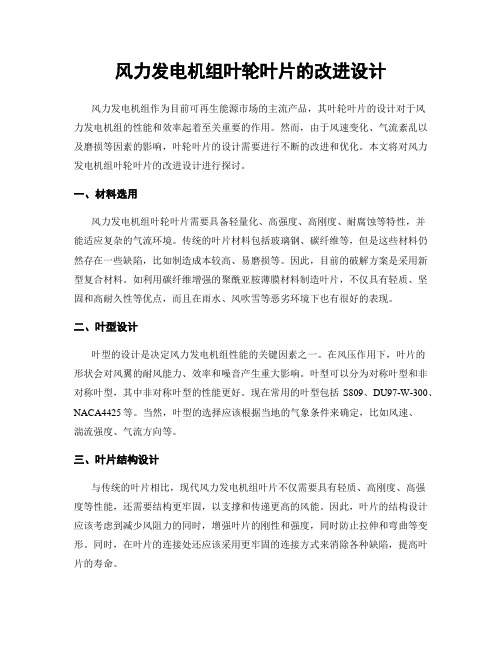
风力发电机组叶轮叶片的改进设计风力发电机组作为目前可再生能源市场的主流产品,其叶轮叶片的设计对于风力发电机组的性能和效率起着至关重要的作用。
然而,由于风速变化、气流紊乱以及磨损等因素的影响,叶轮叶片的设计需要进行不断的改进和优化。
本文将对风力发电机组叶轮叶片的改进设计进行探讨。
一、材料选用风力发电机组叶轮叶片需要具备轻量化、高强度、高刚度、耐腐蚀等特性,并能适应复杂的气流环境。
传统的叶片材料包括玻璃钢、碳纤维等,但是这些材料仍然存在一些缺陷,比如制造成本较高、易磨损等。
因此,目前的破解方案是采用新型复合材料。
如利用碳纤维增强的聚酰亚胺薄膜材料制造叶片,不仅具有轻质、坚固和高耐久性等优点,而且在雨水、风吹雪等恶劣环境下也有很好的表现。
二、叶型设计叶型的设计是决定风力发电机组性能的关键因素之一。
在风压作用下,叶片的形状会对风翼的耐风能力、效率和噪音产生重大影响。
叶型可以分为对称叶型和非对称叶型,其中非对称叶型的性能更好。
现在常用的叶型包括S809、DU97-W-300、NACA4425等。
当然,叶型的选择应该根据当地的气象条件来确定,比如风速、湍流强度、气流方向等。
三、叶片结构设计与传统的叶片相比,现代风力发电机组叶片不仅需要具有轻质、高刚度、高强度等性能,还需要结构更牢固,以支撑和传递更高的风能。
因此,叶片的结构设计应该考虑到减少风阻力的同时,增强叶片的刚性和强度,同时防止拉伸和弯曲等变形。
同时,在叶片的连接处还应该采用更牢固的连接方式来消除各种缺陷,提高叶片的寿命。
四、尾流影响多台风力发电机组并网构成风场,在这种情况下会产生大量的尾流,给设备的耐久性和维护带来很大的挑战。
在叶轮叶片的设计中应该充分考虑尾流的影响,通过优化叶片的结构和尺寸,减少尾流对叶片的影响,从而提高设备的可靠性和稳定性。
五、结论综上所述,每一次机组的重新设计和改进都是在当时的技术状态下取得的最佳结果,希望借助技术的不断发展,让风力发电机组叶轮叶片设计更加优化。
叶轮轴数控加工技术及叶片加工误差分析
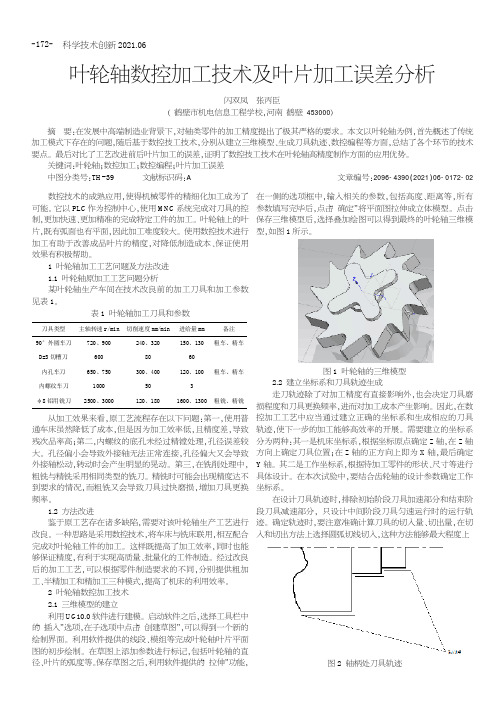
科学技术创新2021.06叶轮轴数控加工技术及叶片加工误差分析闪双凤张丙臣(鹤壁市机电信息工程学校,河南鹤壁453000)数控技术的成熟应用,使得机械零件的精细化加工成为了可能。
它以PLC 作为控制中心,使用M N C 系统完成对刀具的控制,更加快速、更加精准的完成特定工件的加工。
叶轮轴上的叶片,既有弧面也有平面,因此加工难度较大。
使用数控技术进行加工有助于改善成品叶片的精度,对降低制造成本、保证使用效果有积极帮助。
1叶轮轴加工工艺问题及方法改进1.1叶轮轴原加工工艺问题分析某叶轮轴生产车间在技术改良前的加工刀具和加工参数见表1。
表1叶轮轴加工刀具和参数从加工效果来看,原工艺流程存在以下问题:第一,使用普通车床虽然降低了成本,但是因为加工效率低,且精度差,导致残次品率高;第二,内螺纹的底孔未经过精镗处理,孔径误差较大。
孔径偏小会导致外接轴无法正常连接,孔径偏大又会导致外接轴松动,转动时会产生明显的晃动。
第三,在铣削处理中,粗铣与精铣采用相同类型的铣刀。
精铣时可能会出现精度达不到要求的情况,而粗铣又会导致刀具过快磨损,增加刀具更换频率。
1.2方法改进鉴于原工艺存在诸多缺陷,需要对该叶轮轴生产工艺进行改良。
一种思路是采用数控技术,将车床与铣床联用,相互配合完成对叶轮轴工件的加工。
这样既提高了加工效率,同时也能够保证精度,有利于实现高质量、批量化的工件制造。
经过改良后的加工工艺,可以根据零件制造要求的不同,分别提供粗加工、半精加工和精加工三种模式,提高了机床的利用效率。
2叶轮轴数控加工技术2.1三维模型的建立利用U G 10.0软件进行建模。
启动软件之后,选择工具栏中的“插入”选项,在子选项中点击“创建草图”,可以得到一个新的绘制界面。
利用软件提供的线段、模组等完成叶轮轴叶片平面图的初步绘制。
在草图上添加参数进行标记,包括叶轮轴的直径、叶片的弧度等。
保存草图之后,利用软件提供的“拉伸”功能,在一侧的选项框中,输入相关的参数,包括高度、距离等,所有参数填写完毕后,点击“确定”将平面图拉伸成立体模型。
叶轮建模及数控加工仿真
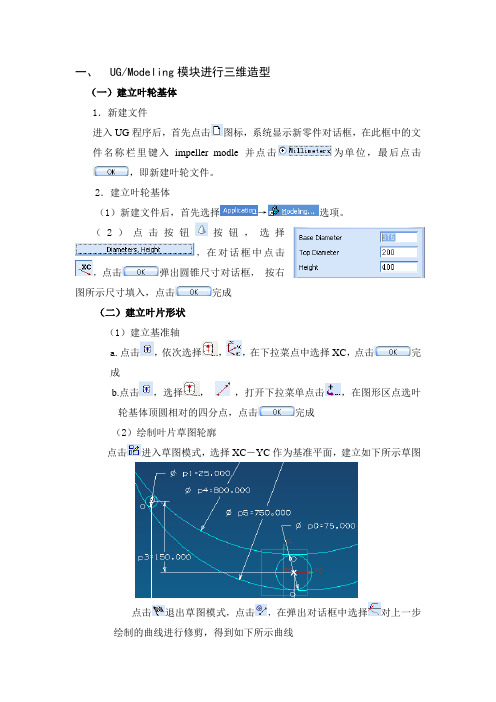
一、UG/Modeling模块进行三维造型(一)建立叶轮基体1.新建文件进入UG程序后,首先点击图标,系统显示新零件对话框,在此框中的文件名称栏里键入impeller_modle并点击为单位,最后点击,即新建叶轮文件。
2.建立叶轮基体(1)新建文件后,首先选择→选项。
(2)点击按钮按钮,选择,在对话框中点击,点击弹出圆锥尺寸对话框,按右图所示尺寸填入,点击完成(二)建立叶片形状(1)建立基准轴a.点击,依次选择,,在下拉菜点中选择XC,点击完成b.点击,选择,,打开下拉菜单点击,在图形区点选叶轮基体顶圆相对的四分点,点击完成(2)绘制叶片草图轮廓点击进入草图模式,选择XC-YC作为基准平面,建立如下所示草图点击退出草图模式,点击,在弹出对话框中选择对上一步绘制的曲线进行修剪,得到如下所示曲线(3)拉伸叶片点击,选择,用鼠标分别选取上图中曲线的四根线段,点击弹出对话框,选择,在弹出对话框中点击沿Z轴方向拉伸,点击,在对话框的end distance栏中填入300,点击,选择,点击完成叶片拉伸操作。
(4)修剪叶片a.建立修剪用曲面点击,以(420,0,260),(-10,0,300)为坐标绘制直线,点击,鼠标选取图形区中刚绘制的直线,点击,选择,在弹出对话框中点击,两次点击,确保基点坐标为零,start angle和end angle 分别填入-50和50。
点击完成b.用曲面修剪叶片点击,在图形区点选叶片,点击,在图形区点选上一步完成的曲面,选择完成修剪叶片操作。
(5)建立圆阵列点击,选择,在界面图形区中点击上一步完成的叶片,点击,阵列数为5,转角72°。
(6)建立倒圆角特征a.在叶片底部建立12.5倒圆角点击,在default radius处填入12.5,用鼠标分别选取图形区中叶片和叶轮基体的交界线,点击完成。
b.建立叶片顶部变半径倒圆角点击,在前打勾,在图形区分别点选下图所示三点,每点的圆角半径值为1:31.25;2:12.5;3:1.5625,点击完成c.建立叶轮基体倒角点击,选择,在图形区点选叶轮基体的顶圆和底圆,点击,在offset处填入6.25,点击完成(三)建立叶轮基体键槽等其他特征a.建立孔特征1.点击,选择,在弹出对话框中点击,点击,尺寸如右图,点击,基点坐标为(0,0,0),点击,选择,在图形区点选叶轮基体,点击完成。
基于UG NX6.0的整体叶轮数控加工仿真校验与后置处理

基于UG NX6.0的整体叶轮数控加工仿真校验与后置处理4.4.1 整体叶轮数控加工路径规划叶轮整体数控铣削加工是指轮廓与叶片在同一毛坯上铣削加工成形。
其加工过程大致包括以下几个主要工序:1.粗加工叶轮流道曲面;2.粗加工叶片曲面;3.叶片精加工;加工。
下面对其路径规划方法分别讨论。
1)创建整体叶轮数控加工父级组。
打开已经建构的整体叶轮三维CAD文件,进入UG加工界面,选择“mill_muti-axis(多轴铣削)”CAM加工配置模板,先后创建程序组、几何组、刀具组和方法组,为下面的加工仿真做准备,具体如下:a.创建程序组。
程序组是用于组织各加工操作和排列各操作在程序中的次序。
由于在单个叶片的多轴加工程序编制后,要使用旋转复制功能生成其余叶片的加工程序,因此这里先采用UG 缺省的程序组,待全部叶片加工程序完成后再统一修改、管理。
b.创建几何组。
在“导航器”中选择“几何视图”功能,进入几何视图工作界面,设置叶轮的圆柱圆心点为加工坐标系位置(双击MCS_MILL 在CSYS 状态下单击点对话框将捕捉类型设置为“圆弧中心/椭圆中心/球心”并将加工坐标系移至到圆心点),如图4.11所示;在铣削几何体中选择已经车削完成的回转体作为毛坯几何体,如图4.12所示c.创建刀具组根据前面已经确定的刀具类型和相关刀具参数,利用“创建刀具”功能,分别创建粗、精加工刀具,并且从内定库中检索刀具夹持器,创建刀具夹持器,本文中选取了库代号为“HLD001_00041”的刀具夹持器。
由于上一节中对刀具选择已作了比较详细的论述,这里不再重复,且此步的操作比较简单。
e.创建方法组由于叶片及流道曲面加工采用了表面积驱动方法,不便设置统一的加工余量、几何体的内外公差、切削步距和进行速度等参数,先选用内定的“METHOD ”加工方法,可根据需要再设置上述加工参数。
2)粗加工叶轮流道曲面通过可变轮廓铣程序控制驱动方法和刀具轴,根据叶轮流道曲面的加工要求创建多轴联动粗加工程序。
UG自动编程的叶轮加工(五轴联动加工中心)毕业设计
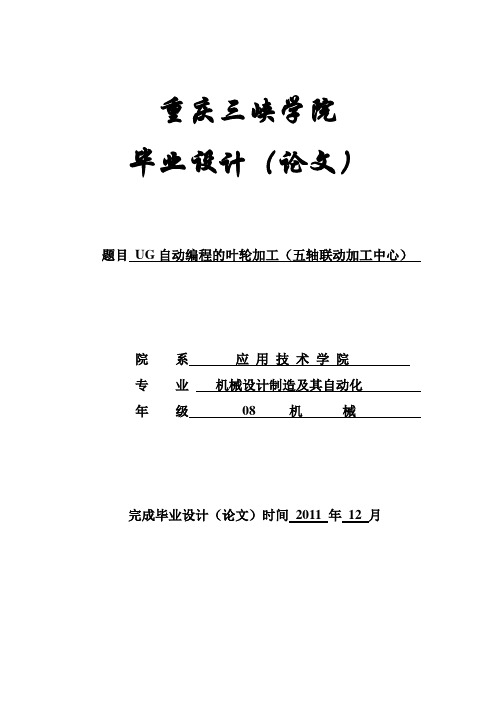
重庆三峡学院毕业设计(论文)题目UG自动编程的叶轮加工(五轴联动加工中心)院系应用技术学院专业机械设计制造及其自动化年级08 机械完成毕业设计(论文)时间2011 年12 月目录摘要第一章:绪论1.1:五轴联动简介1.2:五轴联动加工中心的特点1.3:五轴联动加工中心的分析1.4:五轴联动加工中心的应用领域第二章:FANUC系统编程方法2.1 FANUC系统概述2.2 FANUC系统编程指令第三章:叶轮轴加工的工艺分析3.1概述3.2零件三维模型与零件图3.3叶轮轴的加工工艺分析第四章:叶轮轴加工的UG自动编程4.1 建立零件的UG三维模型4.2 叶轮轴加工的UG自动编程4.3 叶轮轴加工的UG程序后处理第五章:总结致谢语参考文献基于UG自动编程的数控铣削加工牟松重庆三峡学院应用技术学院机械设计制造及其自动化08机械重庆万州 404000摘要五轴联动数控机床是一种科技含量高、精密度高专门用于加工复杂曲面的机床,这种机床系统对一个国家的航空、航天、军事、科研、精密器械、高精医疗设备等等行业有着举足轻重的影响力。
目前,五轴联动数控机床系统是解决叶轮、叶片、船用螺旋桨、重型发电机转子、汽轮机转子、大型柴油机曲轴等等加工的唯一手段。
关键字五轴联动加工中心UG 自动编程第一章:绪论1.1:五轴联动简介所谓五轴加工这里是指在一台机床上至少有五个坐标轴(三个直线坐标和两个旋转坐标),而且可在计算机数控(CNC)系统的控制下同时协调运动进行加工。
1:对于五轴立式加工来说,必须要有C轴,即旋转工作台,然后再加上一个轴,要么是A轴要么是B轴。
2:主轴头旋转类型,立式结构的两个回转轴A,C轴。
该机床将A,C回转轴设置在主轴上。
铣头绕Z轴旋转360度形成C轴,绕X轴旋转±90度形成A轴。
这样的结构形式工作台上无旋转轴。
3:工作台旋转类型,工作台绕X轴旋转,工作台绕Z轴旋转,主轴无需摆动。
4:工作台绕Z轴旋转,主轴头绕Y轴摆动称B轴。
叶轮打磨工具、打磨工艺方法及注意要点培训
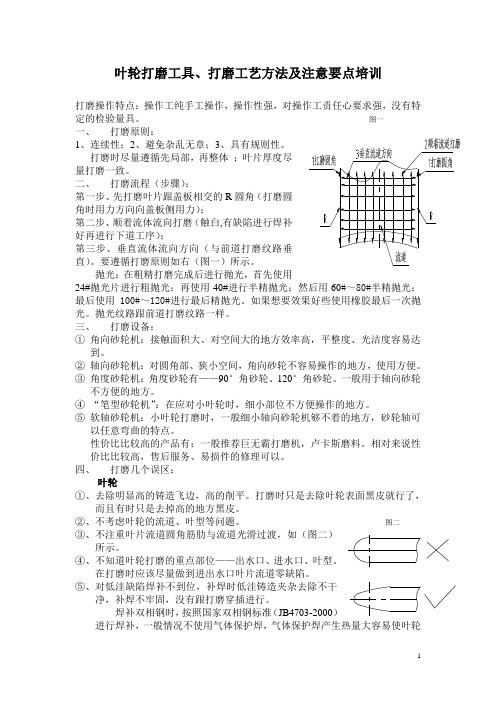
叶轮打磨工具、打磨工艺方法及注意要点培训打磨操作特点:操作工纯手工操作,操作性强,对操作工责任心要求强,没有特定的检验量具。
图一一、打磨原则:1、连续性;2、避免杂乱无章;3、具有规则性。
打磨时尽量遵循先局部,再整体;叶片厚度尽量打磨一致。
二、打磨流程(步骤):第一步、先打磨叶片跟盖板相交的R圆角(打磨圆角时用力方向向盖板侧用力);第二步、顺着流体流向打磨(触白,有缺陷进行焊补好再进行下道工序);第三步、垂直流体流向方向(与前道打磨纹路垂直)。
要遵循打磨原则如右(图一)所示。
抛光:在粗精打磨完成后进行抛光,首先使用24#抛光片进行粗抛光;再使用40#进行半精抛光;然后用60#~80#半精抛光;最后使用100#~120#进行最后精抛光。
如果想要效果好些使用橡胶最后一次抛光。
抛光纹路跟前道打磨纹路一样。
三、打磨设备:①角向砂轮机:接触面积大、对空间大的地方效率高,平整度、光洁度容易达到。
②轴向砂轮机:对圆角部、狭小空间,角向砂轮不容易操作的地方,使用方便。
③角度砂轮机:角度砂轮有——90°角砂轮、120°角砂轮。
一般用于轴向砂轮不方便的地方。
④“笔型砂轮机”:在应对小叶轮时,细小部位不方便操作的地方。
⑤软轴砂轮机:小叶轮打磨时,一般细小轴向砂轮机够不着的地方,砂轮轴可以任意弯曲的特点。
性价比比较高的产品有:一般推荐巨无霸打磨机,卢卡斯磨料。
相对来说性价比比较高,售后服务、易损件的修理可以。
四、打磨几个误区:叶轮①、去除明显高的铸造飞边,高的削平。
打磨时只是去除叶轮表面黑皮就行了,而且有时只是去掉高的地方黑皮。
②、不考虑叶轮的流道、叶型等问题。
图二③、不注重叶片流道圆角筋肋与流道光滑过渡,如(图二)所示。
④、不知道叶轮打磨的重点部位——出水口、进水口、叶型。
在打磨时应该尽量做到进出水口叶片流道零缺陷。
⑤、对低洼缺陷焊补不到位,补焊时低洼铸造夹杂去除不干净,补焊不牢固,没有跟打磨穿插进行。
五轴叶轮加工步骤

五轴叶轮加工一、实体造型(附件:叶轮.Z3):二、叶轮粗加工:1、叶轮实体制作完成后,在空白处点击右键选择进入CAM加工。
2、添加坯料---配料分两部分,a为整体柸料,用于整体加工。
b为局部柸料,用于局部测试用。
a、整体柸料制作及添加过程;点击退出,再点击新建对象。
文件名输入“毛坯”---确定。
⑴只添加与实体轴向、颈项相等的圆柱体即可。
⑵改变圆柱面属性,使其变为半透明状,便于测试时观察。
属性---面---调节透明度---用鼠标框选坯料实体---确定。
b、局部柸料制作及添加过程;点击退出,再点击选择复制叶轮文件,在用粘贴新对象。
用右键点击新建对象选择“重命名”重新设置文件名称。
双击进入编辑。
⑴先导入叶轮实体,再做一个大于叶片间距的立方体;⑵选择修剪实体对坯料进行修剪。
⑶再选择修剪实体对坯料进行修剪。
⑷选择修剪实体对坯料圆边进行修剪。
⑸利用直纹面选择图中黄色线段生成修剪曲面。
⑹选择修剪实体通过修剪面修剪柸料。
⑺用删除剩余残面。
⑻点击再选择隐藏实体。
⑼利用直纹面选择图中黄色线段生成修剪曲面。
⑽点击显示所有实体。
⑾选择分割实体。
⑿选择删除切割下来的实体。
⒀先选择中的“造型”选项,在选择合并图中两部分。
⒁再用删除叶轮实体,只剩下局部毛坯。
⒂局部毛坯属性,使其变为半透明状,便于测试时观察。
属性内选择面---调节透明度---用鼠标框选坯料实体---确定⒃选择面偏移来拉伸实体。
(偏移-1)自此坯料全部制作完成。
3、点击退出后,双击进入“加工方案”。
4、右键点击选择“插入”。
把之前制作好的两个柸料导入进来。
5、右键点击选择再选择,实体将转变成毛坯。
6、局部坯料转变过程同上。
7、点击选择---快速铣削---粗加工工序---二维偏移粗加工。
8、确定加工工序后选择刀具,并设置刀具参数。
如果新建工艺可以直接点击此处来设置刀具参数,如果已有刀具可以点击此处,在“刀具列表”内选择已有刀具。
如果要是添加新刀具用右键点击选择“管理”就可以添加新刀具。
离心风机叶轮制作工艺流程

离心风机叶轮制作工艺流程英文回答:Centrifugal fan impeller manufacturing process involves several steps to ensure the production of high-quality impellers. The process can be divided into the following stages:1. Design and Engineering: The first step in manufacturing a centrifugal fan impeller is designing and engineering the impeller. This involves determining the impeller size, shape, and blade angle based on the specific requirements of the fan system. Computer-aided design (CAD) software is often used in this stage to create a detailed design.2. Material Selection: Once the impeller design is finalized, the next step is to select the appropriate material for manufacturing the impeller. Common materials used for impeller manufacturing include aluminum, steel,and plastic. The material selection is based on factorssuch as cost, strength, and corrosion resistance.3. Pattern Making: In this stage, a pattern of the impeller is created using wood, metal, or plastic. The pattern is an exact replica of the final impeller and is used to create the mold for casting or forging the impeller.4. Casting or Forging: The pattern is used to create a mold, which is then used for casting or forging the impeller. Casting involves pouring molten metal into the mold and allowing it to solidify. Forging, on the other hand, involves shaping the metal by applying pressure and heat. Both casting and forging methods can be used to manufacture impellers, depending on the material and design requirements.5. Machining: After the impeller is cast or forged, it undergoes machining to achieve the final shape and dimensions. Machining processes such as turning, milling, and drilling are used to remove excess material and create the desired shape. This stage requires precision andaccuracy to ensure the impeller meets the design specifications.6. Balancing: Balancing is a critical step in impeller manufacturing to ensure smooth operation and minimize vibrations. The impeller is balanced by removing material from specific areas or adding weights to achieve the desired balance. Dynamic balancing machines are used to measure and correct any imbalance in the impeller.7. Surface Treatment: The final step in the manufacturing process is surface treatment. This involves applying coatings or finishes to protect the impeller from corrosion and improve its appearance. Common surface treatments for impellers include painting, powder coating, or anodizing.中文回答:离心风机叶轮的制作工艺流程包括以下几个步骤,以确保生产出高质量的叶轮:1. 设计与工程,制作离心风机叶轮的第一步是设计和工程化叶轮。
推进器底座及叶轮加工

推进器底座及叶轮加工刘艳申【摘要】随着数控技术的发展,高速切削与五轴加工设备运用日益普及.针对推进器底座及叶轮的编程与加工问题,以一种简化的螺旋桨推进器模型为载体,重点介绍利用UG NX9完成推进器复杂的底座和叶轮的自动编程,并利用DMU80 mono Block五轴镗铣加工中心对刀具轨迹进行验证.【期刊名称】《精密制造与自动化》【年(卷),期】2016(000)002【总页数】4页(P55-58)【关键词】推进器;叶轮;五轴【作者】刘艳申【作者单位】陕西工业职业技术学院陕西咸阳 712000【正文语种】中文推进器(助推器)一般用来提供动力,提高速度,它是通过旋转叶片或喷气(水)来产生推力。
推进器在船舶、航空等领域应用广泛,主要是提供船艇的动力。
推动器的种类繁多,有螺旋桨推进器、电动船用推进器、航空推进器、喷水推进器等。
每一种都有它特殊的用途及特点,但推进器的加工需要采用多轴联动加工设备才能完成。
UG NX是集CAD/CAM/CAE于一体的三维参数化设计软件[1],可以借助于UG NX的计算机辅助制造功能完成推进器底座及叶轮的自动编程。
图1和图2所示为推进器底座及叶轮结构,加工中需要进行二次装夹,同时根据要求配做简单工装,利用底座上表面和叶轮下表面的四个螺钉孔、两个销孔进行定位装夹。
零件加工所用毛坯均为各个特征的包容圆柱体,所有圆角及叶轮根部均为R4,利用CAXA加工时需要利用R4球头刀来完成。
工装为可以和推进器底座顶面的四个螺钉孔和叶轮底面上两个销孔所对应的一个圆柱形结构(高度可做到50mm左右),通过一面两销孔定位方式完成定位。
在圆柱形工装上必须做一个定位面,以保证工件在进行二次定位装夹时上下特征之间的对应关系。
1.2.1 推进器底座工序安排针对推进器底座结构可以按照下列工序进行加工:顶部圆槽加工→顶部孔加工→顶部锥面加工→锥面上槽加工及孔加工→底面槽加工(需掉头,用辅助工装定位)→底部孔加工→外圆槽加工→侧面特征加工→侧面孔加工。
叶轮叶片的制作工艺流程

叶轮叶片的制作工艺流程英文回答:Impeller Blade Manufacturing Process.The impeller blade is a critical component of a centrifugal pump, responsible for converting the rotational energy of the impeller into kinetic energy to move the fluid. The manufacturing process of impeller blades involves several key steps to ensure their precision, efficiency, and durability.1. Design and Engineering:The first step is to design and engineer theimpeller blade based on the pump's specifications, such as flow rate, pressure head, and efficiency requirements.Advanced computational fluid dynamics (CFD) simulations are often used to optimize the blade geometryfor optimal flow dynamics.2. Pattern Making:Once the design is finalized, a pattern is created to accurately represent the shape of the impeller blade.The pattern can be made from wood, plastic, or metal and is used to create the mold for blade casting.3. Mold Making:Using the pattern, a mold is created in two halves. The mold is typically made of sand, plaster, or a combination of materials.The mold is designed to allow molten metal to be poured into it and form the impeller blade.4. Casting:Molten metal, typically a corrosion-resistant alloysuch as stainless steel, is poured into the mold.The metal solidifies in the mold, forming the impeller blade.After solidification, the mold is broken away to release the blade.5. Heat Treatment:The casted impeller blade undergoes heat treatment processes to improve its strength and hardness.This typically involves heating and cooling the blade under controlled conditions.6. Machining:The blade is then machined to achieve precise dimensions and surface finish.CNC (Computer Numerical Control) machines are oftenused for this process, ensuring accuracy and repeatability.7. Finishing:After machining, the blade is finished to remove any burrs or imperfections.This may involve grinding, polishing, or shot blasting.The blade may also undergo a corrosion-resistant coating process.8. Balancing:The impeller blade is balanced to ensure smooth operation without vibrations.Balancing involves adjusting the blade's mass distribution to minimize any imbalances.9. Inspection and Testing:The finished impeller blade undergoes thorough inspection and testing to verify its dimensions, quality, and performance.Non-destructive testing (NDT) methods, such as ultrasonic testing or dye penetrant testing, are often used for this purpose.中文回答:叶轮叶片的制作工艺流程。
点铣法和侧铣法
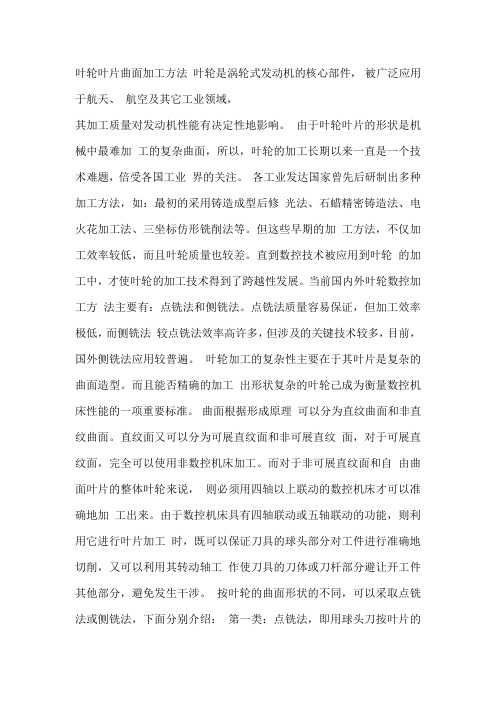
叶轮叶片曲面加工方法叶轮是涡轮式发动机的核心部件,被广泛应用于航天、航空及其它工业领域,其加工质量对发动机性能有决定性地影响。
由于叶轮叶片的形状是机械中最难加工的复杂曲面,所以,叶轮的加工长期以来一直是一个技术难题,倍受各国工业界的关注。
各工业发达国家曾先后研制出多种加工方法,如:最初的采用铸造成型后修光法、石蜡精密铸造法、电火花加工法、三坐标仿形铣削法等。
但这些早期的加工方法,不仅加工效率较低,而且叶轮质量也较差。
直到数控技术被应用到叶轮的加工中,才使叶轮的加工技术得到了跨越性发展。
当前国内外叶轮数控加工方法主要有:点铣法和侧铣法。
点铣法质量容易保证,但加工效率极低,而侧铣法较点铣法效率高许多,但涉及的关键技术较多,目前,国外侧铣法应用较普遍。
叶轮加工的复杂性主要在于其叶片是复杂的曲面造型。
而且能否精确的加工出形状复杂的叶轮己成为衡量数控机床性能的一项重要标准。
曲面根据形成原理可以分为直纹曲面和非直纹曲面。
直纹面又可以分为可展直纹面和非可展直纹面,对于可展直纹面,完全可以使用非数控机床加工。
而对于非可展直纹面和自由曲面叶片的整体叶轮来说,则必须用四轴以上联动的数控机床才可以准确地加工出来。
由于数控机床具有四轴联动或五轴联动的功能,则利用它进行叶片加工时,既可以保证刀具的球头部分对工件进行准确地切削,又可以利用其转动轴工作使刀具的刀体或刀杆部分避让开工件其他部分,避免发生干涉。
按叶轮的曲面形状的不同,可以采取点铣法或侧铣法,下面分别介绍:第一类:点铣法,即用球头刀按叶片的流线方向逐行走刀(加工一个叶片一般需50~200 次走刀),逐渐加工出叶片曲面。
这种方法在自由曲面型叶片上普遍采用,在一小部分直母线型叶片上也采用。
我国航天用的转子、风扇都采用这种点铣法。
以航天部某机器厂加工某型号叶轮为例,叶轮材料为TC6 钛合金。
其加工方法即是在四轴联动的机床上利用圆柱球头铣刀进行点铣加工。
即从叶片顶部开始,沿叶片的流线方向,用球头刀的刀头部分对其进行切削,当其走刀行程加工完一侧的一条流线后,经过退刀及进刀后,刀具即向轮毂方向移动0.3mm,进行下一次切削,直到叶片的一面加工完毕,再对另一面进行切削。
- 1、下载文档前请自行甄别文档内容的完整性,平台不提供额外的编辑、内容补充、找答案等附加服务。
- 2、"仅部分预览"的文档,不可在线预览部分如存在完整性等问题,可反馈申请退款(可完整预览的文档不适用该条件!)。
- 3、如文档侵犯您的权益,请联系客服反馈,我们会尽快为您处理(人工客服工作时间:9:00-18:30)。
多叶片复杂曲面零件的设计与五轴模拟加工1.1 加工任务整体叶轮的零件视图如图1所示图1 叶轮零件针对本零件,本例中将进行叶轮底部圆弧面的加工。
此工件的毛坯为圆棒料,材料牌号为钛合金TC4.采用专用的夹具将其底面固定安装在机床C轴上。
本例中我们将完成叶轮圆弧底面的精加工。
1.2 加工工艺方案通常情况下,在大部分制造场合,单片叶轮的叶片多采用锻造方式做成毛坯,整体式叶轮类零件的毛坯多采用铸造的方式形成,然后采用3~5轴数控机床进行半精加工或精加工,特殊情况下可能还采用人工抛光的方法,形成最后的精加工。
本例中,我们就介绍整体式叶轮在5轴数控机床上的精加工工作。
(1)刀具选择:R4的球头棒铣刀(或选用锥度球头铣刀)(2)加工坐标原点的设置:工件零点取在叶轮圆弧底面大圆140的圆心点上。
(3)加工设备:五轴联动数控机床。
1.3 编程操作(设置零件加工程序)在UG NX4软件系统中对此零件进行编程的操作步骤如下:1.建立刀具路径文件夹(1)单击菜单栏中的“文件”→“打开”命令,从UG NX4文件浏览器窗口选择“train11.prt”文件并单击“确定”按钮将其打开,如图2所示。
图2 在UG NX4 中进入造型文件的NX加工界面(2)选择加工环境1)单击(起始)图标,单击“加工”命令,弹出“加工环境”对话框。
如图3所示。
2)在“CAM进程配置”列表框中选择“mill→multi→axis”,结果如图4所示。
图3“加工环境”对话框图4选择多轴铣加工配制3)在“CAM设置”列表框中选择“mill→multi→axis”,单击“初始化”按钮,进入加工过程的创建界面,弹出如图5所示的“加工创建”工具栏。
2. 创建加工方法(1)单击“加工创建”工具栏中的(创建方法)工具,弹出“创建方法”对话框,如图11→6所示。
图5“加工创建”工具栏图 6“创建方法”对话框(2)在“类型”下拉列表框中选择“mill→multi→axis”(3)在“父级组”下拉列表框中选择“MILL→FINISH”。
(4)单击“确定”按钮,弹出“MILL→METHOD(铣削方法)”对话框,如图7所示(5)单击“确定”按钮,系统又回到图5所示的“加工创建”工具栏。
3. 创建几何体(1)单击“加工创建”工具栏中的(创建几何体)工具,弹出“创建集合体”对话框,如图8所示。
图7“铣削方法”对话框图8“创建几何体”对话框(2)在“类型”下拉列表框中选择“mill→multi→axis(多轴铣)”选’项。
(3)在“父级组”的下拉列表框中选择为“WORKPIECE”,在“名称”文本框输入为“bott→surf”,如图9所示。
(4)单击“确定”按钮,弹出如图10所示的“MCO(机床坐标系)”对话框图9选择“多轴铣”图10“MCS(机床坐标系)”对话框(5)单击如图10所示的(构造)按钮,弹出如图11所示的“CSYS构造器(构造机床坐标系)”对话框。
保持DX,DY,DZ均为0,单击“确定”按钮。
(6)同样单击如图11所示的(RCS构造)按钮,完成RCS坐标系的设置。
(7)单击“确定”按钮,系统又回到图5所示的“加工创建”工具栏。
4. 创建刀具(1)单击“加工创建”工具栏中的(创建刀具)工具,弹出“创建刀具”对话框。
(2)在图中我们可以看到,“类型”下拉列表框显示仍为“mill→multi→axis(多轴铣)”只需要选择“子类型”选项中的工具,进行“子类型”的设定即可。
(3)单击“子类型”选项栏中的(球头切)按钮。
(4)在“名称”文本框中输入“ball_mill_6”,如图12所示。
(5)再单击“确定”按钮,弹出“Milling Toll→Ball Mill ( 球头铣刀)”对话框,如图13所示。
图11 “CSYS构造器”对话框图12 “创建刀具”对话框图13 “球头铣刀对话框(6)设置“球直径”为6mm、“长度”为60mm、“刃口长度”为30mm、“刃数”为2、“刀具号”为1,“半径补偿寄存器”为1.(7)单击“确定”按钮,系统又返回到如图5所示的“加工创建”工具栏。
5. 创建程序(1)单击如图5所示的工具栏中的(创建)工具,单击“创建程序”对话框,如图14所示。
(2)此时在“父级组”文本框中显示的是“NC_PROGRAM”,代表“NC_PROGRAM”是我们要创建的程序组的父节点组,。
(3)在“名称”文本框内输入“yelun1”,单击“确定”按钮,则创建了第一个程序名。
(4)重复以上步骤,用同样的方法,仍然用创建“NC_PROGRAM作为父节点组”,创建程序名“yelun2”。
(5)单击“确定”按钮,系统又回到图5所示的“加工创建”工具栏。
(6)单击(操作导航器)按钮,在操作导航器中就可以看到我们新建的两个程序名,如图15所示。
图14 “创建程序”对话框图15操作导航器的程序次序表说明:“YELUN1”和“YELUN2”作为程序父节点组,就可以分别包含其他的程序次序表。
6. 创建操作(1)单击资源管理条中的(操作导航器)按钮,在出现的程序次序目录中单击“YELUN1”目录。
(2)右击,在系统弹出的快捷菜单中一次单击“插入”→“操作”命令,弹出“创建操作”对话框,如图16所示。
(3)在“使用方法”下拉列表框中选择“MILL_METHEND”。
(4)单击“确定”按钮,弹出“VARIABLE_CONTOUR(可变轴轮廓)”对话框,如图17所示。
图16 “创建操作”对话框图17 “可变轴轮廓”对话框(5)在如图17所示的“几何体”选项栏中,单击(检查几何体)按钮,再单击“选择”按钮,弹出如图18所示的“检查几何体”对话框。
(6)在“过滤方式”下拉列表框中选择“面”,再单击“全选”按钮。
这时模型中所有的曲面改变了颜色,表示已被选择上了,如图19所示。
(7)在“操作模式”下拉列表框中,将“附加”选项更改为“编辑”选项,这时的对话框变换为如图20所示的形式。
图18 “检查几何体”对话框图19 “检查几何体”对话框(8)在如图20所示的对话框中,单击“移除”按钮,在工作上选择圆弧型叶轮底面,再单击“确定”按钮,系统回到图17所示的对话框。
(9)单击“几何体”选项栏中的(部件)按钮,用上述同样的方法选择所有的曲面为工作几何体,完成后系统回到图17所示对话框。
(10)在如图17所示的“驱动方式”下拉列表框中选择“曲面区域”,系统提示“驱动方式改变”,单击“确定”按钮,弹出“曲面驱动方式”对话框,如图21所示。
(11)单击“驱动几何体”选项栏中的“选择”按钮,系统弹出如图22所示的“驱动几何体”对话框。
选择叶轮圆弧底面,然后单击“确定”按钮,系统回到“曲面驱动方式”对话框。
(12)单击“材料反向”按钮,如果显示的加工材料的方向箭头指向了叶轮内部,则可再次“材料反向”按钮进行改换。
(13)单击“切削方向”按钮,如果系统显示的切削方向不满足我们的要求,则可根据出现的箭头提示,用光标重新选择我们想要的切削方向。
这里我们用光标选择径向向内的箭头作为切削方向。
(14)在“切削步长”下拉列表框中选择“公差”,变换后的界面的内外公差设定保持不变。
图20 “检查几何体”对话框对话框 图21 “曲面驱动方式”对话框(15)在“步进”下拉列表框中选择“残余波峰高度”,设置“残余波峰高峰”为0.005。
(16)在“When GOUGE DRIVE(过切驱动时)”下拉列表框中选择“退刀”。
(17)在“刀轴”下拉列表框中选择“垂直于驱动”。
(18)在“投影矢量”下拉列表框中选择“指定矢量”。
(19)弹出如图23所示的“矢量构造器”对话框,依次选择坐标为选择“0,0,→1”。
(20)依次单击“确定”→“确定”按钮,系统回到如图17所示的对话框。
(21)单击“切削”按钮,弹出“切削参数”对话框,如图24所示。
(22)单击“Clearances ”选项卡,在“When Gouge Drive (当干涉时)”下拉列表框中,设置“检查安全距离”为0.1mm,单击“确定”按钮,系统又回到如图17所示的对话框。
(23)单击“非切削的”按钮,弹出“非切削移动”对话框,定义刀具非切削时的移动方式,如图25所示。
图22 “驱动几何体”对话框图23 “矢量构造器”对话框图24 “切削参数”对话框(24)在“进刀状态”下拉列表中选择“手工”方式,点选“距离”单选钮,在文本框中输入50mm。
(25)单击“确定”按钮,系统又回到如图17所示的对话框。
(26)单击“进给率”按钮,弹出“进给和速度”对话框,如图26(a)所示。
(27)设置“表面速度”为300smm,“每齿进给”为0.06mm,“主轴速度”为15000rpm。
(28)单击“进给”选项卡,进给选项卡页如图26(b)所示。
(29)设置“快速”为5000mmpm“逼近”为1500mmpm,“进刀”为200mmpm,“第一刀切削”为200mmpm,“步进”为300mmpm,“剪切”为300mmpm,“退刀”为1500mmpm,图25 “非切削移动”对话框图26 “进给和速度”对话框(30)单击“确定”按钮,系统又回到如图17所示的对话框。
(31)在如图17所示的对话框中,单击(生成)按钮,则可以生成加工程序。
(32)最后单击“确定”按钮,接受刀具路径。
(33)单击“加工操作”工具栏中的“重新显示刀具路径”工具,再单击“确定”按钮。
刷新显示生成轨迹如图27所示图27 生成加工刀具轨迹2.1 切削模拟(1)在UG NX4软件系统中,单击(确认刀轨)工具,系统弹出如图28所示的“可视化刀轨轨迹”对话框。
图28“可视化刀轨轨迹”对话框图29 加工局部模拟(2)选择“回放”选项卡,单击(播放)按钮。
局部模拟如图29所示2.2 后置处理(1)NC加工过程的最后一个步骤为post processing(后处理),输出所需的加工程序代码(G→M Coes).单击“加工操作”工具栏中的(后处理)工具,系统弹出“后处理”对话框(2)在“可用机床”列表框中选择“MILL→5→AXLS”,或单击“浏览”按钮选择其他的或自己设定的后处理器文件(Post Processer)(3)在“输出文件名”文本框中键入自己想要的文件名,如“TRAIN71”。
(4)在“单位”下拉列表框中选择“公制/部件”选项。
(5)单击“确定”按钮,则系统完成后处理工作。
如图30所示。
图30 后处理生成G代码。