钢铁渗铝及渗铝钢的性能
渗铝工艺的工艺特点
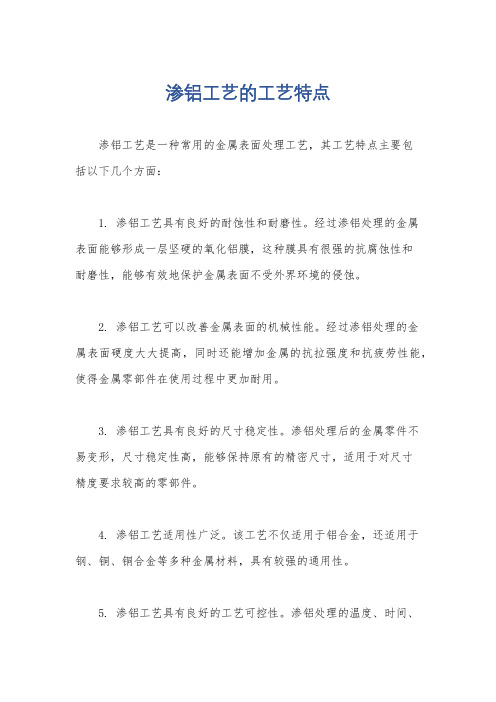
渗铝工艺的工艺特点
渗铝工艺是一种常用的金属表面处理工艺,其工艺特点主要包
括以下几个方面:
1. 渗铝工艺具有良好的耐蚀性和耐磨性。
经过渗铝处理的金属
表面能够形成一层坚硬的氧化铝膜,这种膜具有很强的抗腐蚀性和
耐磨性,能够有效地保护金属表面不受外界环境的侵蚀。
2. 渗铝工艺可以改善金属表面的机械性能。
经过渗铝处理的金
属表面硬度大大提高,同时还能增加金属的抗拉强度和抗疲劳性能,使得金属零部件在使用过程中更加耐用。
3. 渗铝工艺具有良好的尺寸稳定性。
渗铝处理后的金属零件不
易变形,尺寸稳定性高,能够保持原有的精密尺寸,适用于对尺寸
精度要求较高的零部件。
4. 渗铝工艺适用性广泛。
该工艺不仅适用于铝合金,还适用于钢、铜、铜合金等多种金属材料,具有较强的通用性。
5. 渗铝工艺具有良好的工艺可控性。
渗铝处理的温度、时间、
气氛等工艺参数可以进行精确控制,能够根据具体的材料和要求进
行调整,以满足不同工件的处理需求。
总的来说,渗铝工艺具有耐蚀性好、耐磨性强、机械性能优异、尺寸稳定、适用性广泛和工艺可控等特点,因此在航空航天、汽车
制造、机械加工等领域得到广泛应用。
钢中常见元素对钢的各种性能影响

1、 SiSi的熔点1410℃,是缩小γ相区、形成γ相圈的元素,在α铁和γ铁中的溶解度分别为18.5%及2.15%。
Si是钢中常见元素之一,Si和氧的亲和力仅次于铝和钛,而强于Mn、Cr、V。
所以在炼钢中为常用的还原剂和脱氧剂。
为保证质量,除沸腾钢的半镇静钢外,Si在钢中含量应不小于0.10%,作为合金元素一般不低于0.4%Si在钢中不形成碳化物,而是以固溶体的形态存在于铁素体或奥氏体中。
Si固溶于铁素体和奥氏体中可起到提高它们的硬度和强度的作用,在常见元素中仅次于P,而较Mn、Ni、Cr、W、Mo、V等为强。
但Si量超过3%,将显著降低钢的塑性、韧性和延展性。
低Si含量对钢的抗腐蚀性能有显著增强作用。
Si含量为15~20%的Si铁是很好的耐酸材料,对不同温度和浓度的硫酸、硝酸都很稳定。
但在盐酸和王水的作用下稳定性很小,在HF酸中则不稳定。
高Si铸铁之所以抗腐蚀,是由于当开始腐蚀时,在其表面形成致密的SiO2薄层,阻碍着酸的进一步向内侵蚀。
含Si的钢在氧化气氛中加热时,表面也形成SiO2薄层,从而提高钢在高温时的抗氧化性。
在Cr、Cr-Al、Cr-Ni、Cr-W等钢中加Si,都将提高它们的高温抗氧化性能。
各种奥氏体不锈钢中加入约2%的Si,可以增强它们的高温不起皮性。
Mn钢加Si也可以提高它的抗氧化性。
但Si含量高时,钢的表面脱碳倾向加剧。
Si提高钢中固熔体的硬度和强度,从而提高钢的屈服强度和抗拉强度。
在普通低合金钢中,Si还可以增强钢在自然条件下的耐腐蚀性,特别时增高局部腐蚀的抗力。
Si含量较高时,对焊接性不利,并易导致冷脆,还降低钢的被切削性;对中高碳钢回火时易产生石墨化。
2、 MnMn的熔点1244℃,扩大γ相区,形成无限固熔体。
Mn与硫形成MnS,是良好的脱氧剂和脱硫剂,可防止因硫而导致的热脆现象,从而改善钢的热加工性能。
在工业用钢中一般都含有一定数量的Mn。
Mn与Fe形成固溶体,提高钢中铁素体和奥氏体的硬度和强度;同时又是碳化物的形成元素,进入渗碳体中取代一部分铁原子。
固体粉末包埋扩散渗铝技术简介-渗铝车间

渗铝最新技术——固体粉末包埋扩散渗铝技术第一部分固体粉末包埋扩散渗铝技术简介1、固体粉末包埋扩散渗铝技术在我国的发展固体粉末包埋扩散渗铝技术早在40年代就已出现,50年代由原苏联传入我国,由于该项技术工艺复杂,渗铝成本较高,我国仅在军工等行业有少量应用。
美国、日本等国家从60年代末期开始研究将固体粉包埋扩散渗铝材料用于石化行业的受压元件,以解决加工高硫原油的设备腐蚀问题和材料高温氧化问题。
采用固体粉末包埋扩散渗铝技术加工的渗铝材料除具备渗铝钢的抗高温氧化和耐腐蚀等特性以外,还具有良好的再加工性和焊接性能。
这就为渗铝材料的应用拓宽了道路。
我国于90年代初开始研究将用固体粉末包埋技术加工的渗铝材料批量用于石化设备内构件,经过十多年的研究和实验。
固体粉末包埋扩散渗铝技术水平有了很大的提高。
应用范围也从设备内构件填料向热交换器管束、工艺管道和加热炉管方向发展。
2、固体粉末包埋扩散渗铝的概念固体粉末包埋扩散渗铝工艺是将被渗工件和固体粉末渗铝剂,按一定要求装入一个特制的箱体内密闭,放进加热炉内,按一定的要求加热、恒温,在加热过程中渗铝剂内发生一系列的化学反应、使渗剂中的铝原子活化、从而将铝原子渗透(扩散)到钢表层基体内,在钢表层基体内形成一层铁铝合金的过程。
(见下图)1—加热炉2—渗剂3—渗箱4—工件5—端盖和排气装置3、渗层的组织与铝含量的关系。
根据铁铝合金状态图,随着渗层中铝含量的增加、在渗层中依次出现铝在α铁中的固熔体、Fe3Al、FeAl 、FeAl2和少量的Fe2Al5及FeAl3等。
渗层组织及铝含量有以下对应关系。
(1)渗层表面主要成份是FeAl2和少量的Fe2Al5及Fe2Al5 ,这层的铝含量在45%(wt)左右(2)第二层主要成份是Al4C3相,灰色棒状。
(3)第三层主要成份是FeAl ,这层铝含量32%(wt)左右。
(4)第四层主要成份是Fe3Al ,这层铝含量在14%以下。
(5)第五层Al在α铁中的固熔体,铝含量在10%(wt)以下。
钢的表面热处理

热处理工艺的应用
热处理技术条件是指对零件采用的热处理方法以及所应达到的
性能要求的技术性的文件。具体应根据零件性能要求,在零件 图样上标出,内容包括最终热处理方法(如调质、淬火、回火、 渗碳等)以及应达到的力学性能判据等,作为热处理生产及检 验时的依据。力学性能通常只标出硬度值,且有一定误差范围, 如弹簧淬火回火硬度45~50HRC。
表4-7 加热方式及代号
加热 方式
可控气 氛(气
体)Leabharlann 真 空盐浴 (液 体)
感 应
火 激 电子 等离 固体 液态 电接 焰 光 束 子体 装箱 床 触
代号
01
0 2
03
04 05 06 07 08 09 10 11
表4-8 退火工艺及代号
退火 工艺
代号
去应 力退
火
St
均匀 化退
火
H
再结 晶退
火
R
石墨 化退
• 不仅改变了钢表面的组织,而且表面层的化学成分也发生了 变化,因而能更有效地改变零件表层的性能。
• 根据渗入元素分类:渗碳、渗氮、碳氮共渗、渗硼、渗金属 等。
• 化学热处理的基本过程
分解
吸收
扩散
(1)钢的渗碳及其应用
• 渗碳——将钢件置于渗碳介质中加热并保温,使碳原子渗 入工件表层的化学热处理工艺。
热处理工艺分类及代号热处理工艺分类及代号工艺总称总称代号工艺类型类型代号工艺名称名称代号整体热处理表面热处理化学热处理表47加热方式及代号加热方式可控气固体装箱液态代号01030405060708091011表48退火工艺及代号退火工艺脱氢退火退火等温退火完全退火不完代号st表49淬火冷却介质和冷却方法及代号冷却介热处理工序位置安排11预先热处理工序位置退火正火调质预先热处理工序位置退火正火调质安排在毛坯生产之后切削加工之前或粗加工之后半精加安排在毛坯生产之后切削加工之前或粗加工之后半精加工之前
固体渗铝技术介绍

固体粉末包埋渗铝概念渗铝是金属材料表面化学热处理的一种方法,是把钢制工件或介质加热到一定温度使铝原子渗入并扩散到钢材基体内的过程。
根据不同的使用要求、渗铝可在碳钢、低合金钢及高铬镍合金钢基体上进行。
这些材料经过渗铝后,在其表面形成一层具有特殊性能的铁—铝合金层,从而提高材料的抗高温氧化性能和耐腐蚀性能。
渗铝的方法有多种,一般按处理过程的介质状态,操作方法及加热手段可分为:固体粉末包埋扩散渗铝;液体热浸扩散渗铝;气体渗铝;涂刷和喷涂渗铝;静电喷涂渗铝;电泳沉积渗铝;熔融盐电解渗铝;中频高频料浆快速感应渗铝等多种方法。
其中应用最多的是固体粉末包埋扩散渗铝和液体热浸扩散渗铝两种方法。
凡钢材需要弯曲焊接等再加工的一般均采用固体粉末包埋扩散渗铝方法。
渗铝钢的性能1、机械性能总体上说,渗铝钢的机械性能取决于母材的机械性能,但在钢材表面进行渗铝后,虽然渗层很薄,但渗层的机械性能同母材的机械性能相差很大,对其基体材料的机械性能或多或少都会产生一些影响。
材料表面经过渗铝后,在表面形成一层铁—铝合金层,这层合金层硬度非常高,并且很脆。
但是由于渗层厚度有限,对于结构件来说,不会对使用性能产生什么影响,但是对于受压元件来说,就不得不考虑渗层对机械性能的影响,为了尽可能减少渗层对机械性能的影响程度,从两个方面加以控制,第一是调整渗剂配方,使渗层硬度降低,改善渗铝层的机械性能;第二是控制渗层厚度,在满足需要的前提下尽可能减小渗铝层的厚度,渗层薄对机械性能自然影响就小。
定性上说渗铝对母材机械性能影响大小决定于渗厚度与母材厚度的比值,对于渗后做承压部件或受力部件的管材单面渗铝层厚与母材厚度的比值不宜超过0.07、且不大于0.20mm,对于双面渗铝的管材或型钢,渗铝双面厚度之和与母材厚度的比值不宜超过0.12,且每面渗层不超过0.20mm。
对于薄壁管材和轻型型钢、渗铝层对机械性能影响大一些,对于厚壁管和普通型钢渗铝层对整体机械性能影响很小。
渗铝工艺的工艺特点
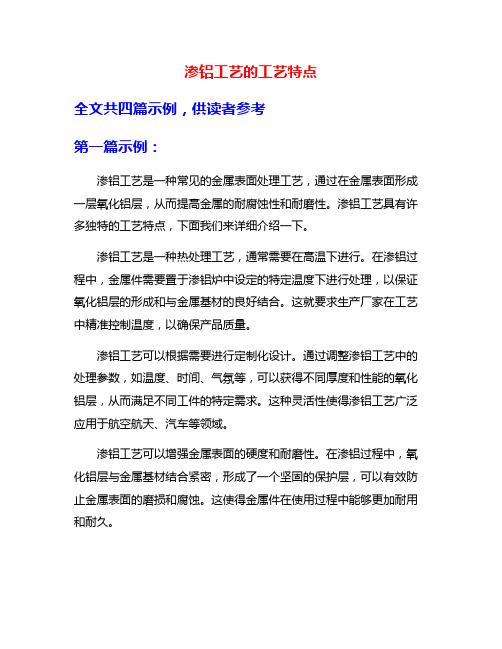
渗铝工艺的工艺特点全文共四篇示例,供读者参考第一篇示例:渗铝工艺是一种常见的金属表面处理工艺,通过在金属表面形成一层氧化铝层,从而提高金属的耐腐蚀性和耐磨性。
渗铝工艺具有许多独特的工艺特点,下面我们来详细介绍一下。
渗铝工艺是一种热处理工艺,通常需要在高温下进行。
在渗铝过程中,金属件需要置于渗铝炉中设定的特定温度下进行处理,以保证氧化铝层的形成和与金属基材的良好结合。
这就要求生产厂家在工艺中精准控制温度,以确保产品质量。
渗铝工艺可以根据需要进行定制化设计。
通过调整渗铝工艺中的处理参数,如温度、时间、气氛等,可以获得不同厚度和性能的氧化铝层,从而满足不同工件的特定需求。
这种灵活性使得渗铝工艺广泛应用于航空航天、汽车等领域。
渗铝工艺可以增强金属表面的硬度和耐磨性。
在渗铝过程中,氧化铝层与金属基材结合紧密,形成了一个坚固的保护层,可以有效防止金属表面的磨损和腐蚀。
这使得金属件在使用过程中能够更加耐用和耐久。
渗铝工艺还具有良好的兼容性。
渗铝工艺可以与其他金属处理工艺相结合,如阳极氧化、热喷涂等,从而获得更好的性能表现。
这种多元化的处理方式可以进一步提高金属件的耐用性和使用寿命。
渗铝工艺具有独特的工艺特点,包括高温处理、定制化设计、增强硬度和耐磨性以及良好的兼容性。
这些特点使得渗铝工艺成为一种广泛应用于金属表面处理的重要工艺,为提高金属件的性能和品质提供了有效的技术手段。
希望我所写的文章可以符合您的要求,谢谢!第二篇示例:渗铝工艺是一种重要的金属加工工艺,主要用于生产高强度、高硬度的铝合金零件。
该工艺通过在铝合金表面渗入一层其他金属元素,从而提高其表面硬度和抗磨损性能。
渗铝工艺具有许多独特的工艺特点,下面将详细介绍。
一、渗铝工艺的原理渗铝工艺是一种将其他金属元素渗入铝合金表面的工艺。
在渗铝过程中,将含有渗入金属元素的混合物覆盖在铝合金表面,然后通过高温处理使金属元素渗入铝合金内部,与铝原子形成新的合金相,从而提高铝合金的硬度和强度。
渗铝钢管的焊接工艺方法
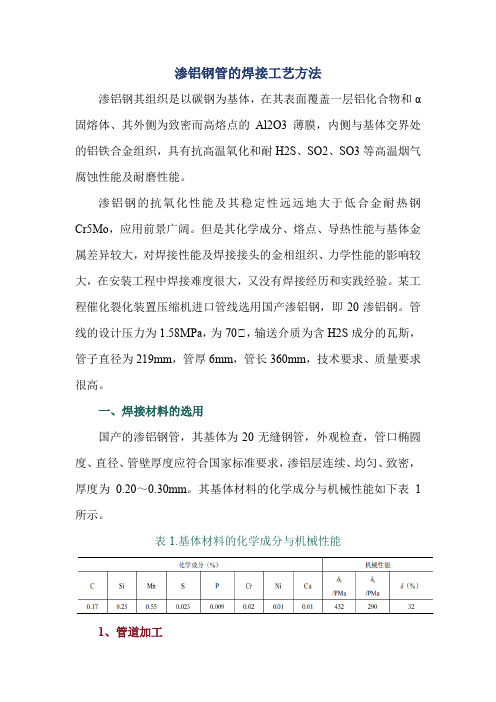
渗铝钢管的焊接工艺方法渗铝钢其组织是以碳钢为基体,在其表面覆盖一层铝化合物和α固熔体、其外侧为致密而高熔点的Al2O3薄膜,内侧与基体交界处的铝铁合金组织,具有抗高温氧化和耐H2S、SO2、SO3等高温烟气腐蚀性能及耐磨性能。
渗铝钢的抗氧化性能及其稳定性远远地大于低合金耐热钢Cr5Mo,应用前景广阔。
但是其化学成分、熔点、导热性能与基体金属差异较大,对焊接性能及焊接接头的金相组织、力学性能的影响较大,在安装工程中焊接难度很大,又没有焊接经历和实践经验。
某工程催化裂化装置压缩机进口管线选用国产渗铝钢,即20渗铝钢。
管线的设计压力为1.58MPa,为70℃,输送介质为含H2S成分的瓦斯,管子直径为219mm,管厚6mm,管长360mm,技术要求、质量要求很高。
一、焊接材料的选用国产的渗铝钢管,其基体为20无缝钢管,外观检查,管口椭圆度、直径、管壁厚度应符合国家标准要求,渗铝层连续、均匀、致密,厚度为0.20~0.30mm。
其基体材料的化学成分与机械性能如下表1所示。
表1.基体材料的化学成分与机械性能1、管道加工20渗铝钢管的内、外表面均由厚度为0.15mm以上的铝镀层和厚度为0.05mm以上的扩散层所组成,铝镀层的外表面上一层致密的Al2O3薄膜,其熔点高达2050℃;扩散层是在铝、铁金属交界处经过高温扩散全部转变为铝铁合金的合金层,它的熔点和硬度都非常高。
在管道预制加工时,要考虑保证焊接工艺要求的焊接接头形式,又要避免因加工而使坡口处管子内、外壁的渗铝层遭到破坏。
因此,必须在施焊前对管件进行预处理。
(1)坡口渗铝层清理碳钢管道在渗铝前已经加工了坡口,在渗铝时,坡口处无法进行保护,与管子的内、外壁同时形成约0.3mm厚的渗铝层,如不进行彻底清除,会直接影响焊接质量,一般采用机械方法予以清除。
由于渗铝层的硬度较高,用角向磨光机清除效率低,又不易保证接头的几何尺寸;用坡口机车削则必须使用硬质合金刀具(YG8),并选用合理的刃磨角度,以便提高其耐磨性能和耐冲击性能。
GCr15钢表面粉末包埋渗铝工艺研究
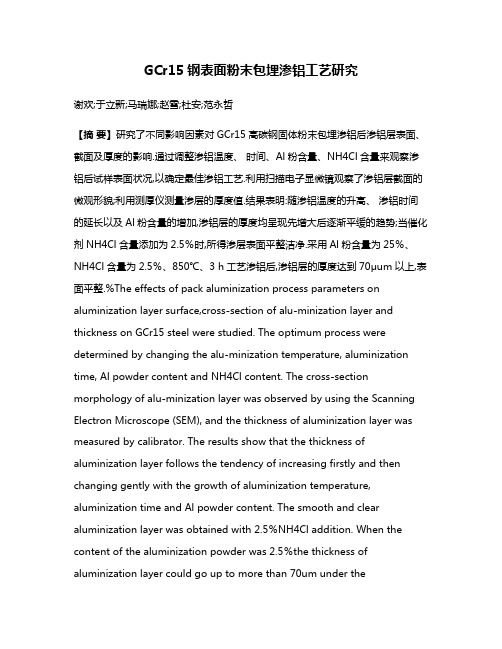
GCr15钢表面粉末包埋渗铝工艺研究谢欢;于立新;马瑞娜;赵雪;杜安;范永哲【摘要】研究了不同影响因素对GCr15高碳钢固体粉末包埋渗铝后渗铝层表面、截面及厚度的影响.通过调整渗铝温度、时间、Al粉含量、NH4Cl含量来观察渗铝后试样表面状况,以确定最佳渗铝工艺.利用扫描电子显微镜观察了渗铝层截面的微观形貌;利用测厚仪测量渗层的厚度值.结果表明:随渗铝温度的升高、渗铝时间的延长以及Al粉含量的增加,渗铝层的厚度均呈现先增大后逐渐平缓的趋势;当催化剂NH4Cl含量添加为2.5%时,所得渗层表面平整洁净.采用Al粉含量为25%、NH4Cl含量为2.5%、850℃、3 h工艺渗铝后,渗铝层的厚度达到70μum以上,表面平整.%The effects of pack aluminization process parameters on aluminization layer surface,cross-section of alu-minization layer and thickness on GCr15 steel were studied. The optimum process were determined by changing the alu-minization temperature, aluminization time, Al powder content and NH4Cl content. The cross-section morphology of alu-minization layer was observed by using the Scanning Electron Microscope (SEM), and the thickness of aluminization layer was measured by calibrator. The results show that the thickness of aluminization layer follows the tendency of increasing firstly and then changing gently with the growth of aluminization temperature, aluminization time and Al powder content. The smooth and clear aluminization layer was obtained with 2.5%NH4Cl addition. When the content of the aluminization powder was 2.5%the thickness of aluminization layer could go up to more than 70um under thealuminization technology of 25%Al content, 2.5%NH4Cl content, at850 ℃for 3 h aluminization condition, and the surface of the aluminization layer was smooth and clear.【期刊名称】《河北工业大学学报》【年(卷),期】2017(046)006【总页数】7页(P53-59)【关键词】GCr15钢;Fe-Al金属间化合物;渗铝层;固体粉末包埋渗铝【作者】谢欢;于立新;马瑞娜;赵雪;杜安;范永哲【作者单位】河北工业大学材料科学与工程学院, 天津 300130;天津市力拓钢制品有限公司, 天津 300381;河北工业大学材料科学与工程学院, 天津 300130;河北工业大学材料科学与工程学院, 天津 300130;河北工业大学材料科学与工程学院, 天津 300130;河北工业大学材料科学与工程学院, 天津 300130【正文语种】中文【中图分类】TG178腐蚀、磨损和断裂是导致材料失效的3种最主要形式,其中每年由于摩擦导致的磨损失效都在上千亿美元,约占设备损坏的70%~80%[1-2].GCr15钢是一种在工程上广泛应用的高碳、高铬轴承钢,经过淬火、回火热处理后具有良好的耐疲劳磨损性能[3-4].但随着工程设备的大型化、重载荷化的发展,轴承钢需要适应大载荷长时间的工况条件,因此提高钢材的耐疲劳磨损性能既增加了零部件的服役寿命,又节约了生产耗能成本.利用固体粉末包埋渗铝的方法,在试样表面生成Fe-Al金属间化合物层以提高渗铝钢的耐磨性能和抗氧化能力.1911年Van Aller[5]首次公开固体粉末渗铝法以来,渗铝工艺有了不断的发展.Levin等[6]通过调整渗剂中Fe、Al的比例,在渗层中可以得到不同配比的Fe-Al金属间化合物.Zhan等[7]通过球磨撞击碾磨的方式进行助渗,从而降低了渗铝的温度和渗铝的时间.但以往的研究与应用往往针对中低碳钢、不锈钢、镍基高温合金等结构材料,对高碳钢表面的渗铝却鲜见报道[8].通过调整在GCr15高碳钢渗铝温度和渗铝时间,以获得最佳的渗铝工艺.1 试验内容试验材料为GCr15轴承钢,化学成分见表1.试验所用的试样尺寸均为10mm×10 mm×5 m m,用400至2000号水磨砂纸磨平表面,在无水乙醇中用90 Hz超声波震荡清洗试样30 min,冷风吹干备用.表1 GCr15钢的成分Tab.1 Composition of GCr5 steel%ω(C)ω(Si)ω(Mn)ω(Cr)ω(Cu)ω(P)ω(Fe)0.95~1.05 0.15~0.35 0.25~0.45 1.40~1.65 ≤0.25 ≤0.025 Bal将预处理后的试样置于粉末渗剂中,渗铝温度为650、700、750、800、850、900、950℃;渗铝时间为1 h、2 h、3 h、4 h、5 h;渗铝剂中铝粉所占比例为10%、15%、20%、25%、30%、35%;渗铝剂中HN4Cl所占比例为0、0.5%、1.0%、1.5%、2.0%、2.5%.渗铝结束后,待炉温冷却至室温,利用无水乙醇在超声波中震荡清洗试样后,进行镶样、磨样、抛光、腐蚀,并利用扫描电子显微镜观察渗铝后的截面形貌,用测厚仪测量渗铝层厚度值.2 结果及分析2.1 固体粉末包埋渗铝保温温度渗铝层的形成过程主要是渗铝剂中的活性 [Al]原子向钢基体进行扩散,及基体中的铁原子向外扩散反应形成Fe-Al金属间化合物的过程,随着温度的升高,原子的扩散速度逐渐增强,若要保证化学热处理过程的顺利进行,获得一定厚度的渗铝层,就必须保证具有足够高的温度提供渗铝所需要的反应扩散能量,因此温度是影响原子扩散速度的主要因素.表2是渗铝时间为3 h条件下在不同渗铝温度渗铝后试样表面宏观状况.由表可以看出,当渗铝时间为650℃时,由于未达到铝粉的熔融温度,无渗铝反应发生,故表面无渗铝层出现;当渗铝温度低于700℃时,由于渗铝温度过低,活性Al原子的移动速率较弱,试样表面无法出现完整的渗铝层;当渗铝温度为750℃时,渗铝层完整连续且平整,但渗层表面颜色呈黑色;当渗铝温度为800~850℃时,渗剂中Al原子的活性较高,故渗铝层表面呈灰黑色且平整;当渗铝温度高于900℃时,由于渗铝温度过高,一方面渗铝剂容易粘结,附着在表面造成结块现象,降低渗铝钢的性能;另一方面,活性铝原子的生成速率提高,大量来不及反应的活性铝原子在钢表面聚集,渗铝层表面出现粘结现象,边缘增厚,渗铝层表面遭到破坏,性能降低.图1分别为不同温度渗铝试样的渗铝层的扫描截面形貌图.图1a)试样为750℃条件下渗铝层的扫描截面形貌图,渗铝层虽薄但分层明显,渗层致密且无孔洞出现,图1b)试样为800℃条件下渗铝层的扫描截面形貌图,图中渗层厚度有所增加,有分层现象,但渗层边界处有大量微小孔洞出现,图1c)试样为850℃条件下渗铝层扫描截面形貌图,图中渗层厚度增加,渗层分层明显且连续致密呈冶金结合,无孔洞出现,图1d)试样为900℃条件下渗铝层扫描截面形貌图,图中试样增厚明显,与表面铝粉的粘结有关,渗层中基本不存在孔洞,渗层致密但分层不明显.渗层图1b)中孔洞的出现是由于在渗铝过程中,Fe原子的原子半径大于Al原子的原子半径,且Fe原子的扩散速率大于Al原子的扩散速率,故随扩散的进行,会有孔洞出现.继续升高反应温度,原子的扩散速率增大,Fe-Al合金形成速率上升,故渗层中孔洞逐渐消失.表2 渗铝温度对表面宏观状况的影响Tab.2 The effect of surface macroscopic condition with aluminization temperature试样编号渗铝温度/℃ 表面状况1 650 表面着有黑斑,无渗铝层2 700 表面呈黑色,略漏钢基体金属光泽3 750表面呈黑色、平整4 800 表面呈灰黑色、平整5 850 表面呈灰黑色、平整6 900 表面呈灰黑色、略有粘结现象7 950 表面呈灰黑色、粘结现象严重图1 不同渗铝温度处理试样的SEM照片Fig.1 SEM photographs of aluminization layers with different aluminization temperature渗铝层的增厚过程符合Fick定律式中:ρ为扩散物质的质量浓度;t为扩散时间;D为扩散系数;x为扩散距离;dρ/dx为浓度梯度.其中扩散系数D为式中:R为气体常数,其值为8.314 J/(mo l·K);Q为每摩尔原子的激活能;T为热力学温度.由公式可以判断出,在一定的渗铝温度范围内,随着温度的升高,渗铝层的厚度在逐渐增大,超过某一增长速度临界的时候,渗层的增长会变得缓慢.图2为渗层厚度与渗铝温度的曲线关系图,从图中可以看出,CGr15钢随固体粉末包埋渗铝温度的升高,渗铝层的厚度逐渐增大,当温度变化范围在700~900℃时,渗铝层的厚度随着渗铝温度的升高增大趋势明显.当温度变化范围在超过900℃时,随渗铝温度的升高,渗铝层的厚度增长趋势逐渐减小.在一定的渗铝温度范围之内,随温度的升高,原子的热扩散激活能随之增大,增强了原子的扩散移动能力,渗铝层的厚度随之增大,渗铝层的表面质量随之变好.渗铝温度过高,熔融的铝粉容易产生粘结现象,一方面导致活性铝原子生成困难,所以没有充足的铝源为渗铝提供保证,另一方面导致大量熔融铝原子在渗铝试样表面粘结,导致渗铝试样的质量降低.2.2 固体粉末包埋渗铝保温时间表3是渗铝温度为850℃条件下不同渗铝时间渗铝后试样表面的宏观状况.当渗铝时间小于3 h时,所得渗铝层表面平整,当渗铝时间大于4 h时,表面出现粘结现象,渗铝层表面质量下降.这是由于随着渗铝时间的延长,渗铝剂中反应物质消耗殆尽,作为填充剂的Al2O3经长时间的高温加热,容易产生粘结,附着在试样表面;渗铝反应催化剂HN4Cl随着长时间渗铝的进行,会有一部分从粘土的裂缝孔隙逸出挥发,导致活性铝原子的生成反应停止,渗铝剂中所剩余的Al粉熔融粘结,附着在试样表面.图3分别为不同时间下渗铝试样的渗层截面形貌.图3a)试样为渗铝1 h条件下渗铝层的扫描截面形貌图,渗层较薄且无明显分层现象,渗层致密无孔洞,图3b)试样为渗铝2 h条件下渗铝层的扫描截面形貌图,图中渗层厚度增加,出现分层现象,渗层致密无孔洞出现,图3c)试样为渗铝3 h条件下渗铝层扫描截面形貌图,图中渗层厚度增加明显,渗层分层明显且连续致密呈冶金结合,无孔洞出现,图3d)试样为渗铝4 h条件下渗铝层扫描截面形貌图,图中试样无明显增厚现象且最外层遭破坏严重.图2 渗层厚度与渗铝温度的曲线关系图Fig.2 The changing of aluminization layer thickness with aluminization temperature表3 渗铝时间对表面宏观状况的影响Tab.3 The effect of surface macroscopic condition with aluminization time试样编号渗铝时间/h 表面状况1 1表面呈灰黑色、平整2 2表面呈灰黑色、平整3 3表面呈灰黑色、平整4 4表面呈灰黑色、略有粘结5表面呈灰黑色、略有粘结6 6表面呈灰黑色、粘结严重5 7 7表面呈灰黑色、粘结严重图3 不同渗铝时间处理试样的SEM照片Fig.3 SEM photographs ofaluminization layers with different aluminization timeAl原子向基体内部扩散,所形成的Fe-Al合金渗层的增厚过程符合Fick第二定律式(3)的误差解为进一步求得误差解为式中:x为平均扩散距离;t为扩散时间;D为扩散系数.由此式可以看出,当温度一定时,扩散时间与渗层厚度呈近似上升趋势的半抛物线关系.图4为渗铝层的厚度随保温时间的变化曲线图,从图中可以看出,当保温时间控制在0~3 h时,随渗铝保温时间的增加,渗铝层的厚度呈近乎直线型增长趋势,当保温时间超过3 h以后,虽然渗铝层厚度随保温时间的增加仍保持增加趋势,但单位时间渗铝层厚度增加的速率明显降低.渗铝时间对渗铝反应的影响相对较小,在一定的时间变化范围内,随时间的延长渗铝层的厚度在逐渐增厚.但当渗铝时间延长到一定时间时,由于在粉末包埋渗铝过程中,作为催渗剂的NH4Cl发生分解产生的气体会从渗灌的水泥密封处逸出,从而导致渗灌内的催化活性铝原子的Cl-的浓度降;其次高温下软化态的铝粉粘滞性性增强,参加反应的有效铝粉含量降低,从而即使延长渗铝反应时间,也在一定程度上降低了渗铝涂层的增加速率.当Cl-的浓度减少到一定的范围内时,即使继续增长渗铝反应时间,没有Cl-继续提供反应,渗铝反应无法进行;另一方面,随着渗铝层厚度的生长增大,已经形成的高铝相Fe-Al合金层会对新扩散进入的活性铝原子产生阻碍作用,故虽保温时间增长,但还是会导致渗铝层的增厚速率降低,长期高温条件下会使钢件的组织造成破坏,渗铝剂粘结严重会使取件变得困难,对生产造成一定的能源浪费.2.3 Al粉含量的影响表4是渗铝温度为850℃,渗铝时间为3 h,渗铝剂中Al粉含量不同时渗铝试样表面的宏观状况.由表可以看出,固体粉末包埋渗铝的过程中,当渗铝剂中的Al粉的含量低于25%时,渗铝层表面干净整洁;当渗铝剂中Al粉含量超过30%时,在高温渗铝的过程中,由于大量的铝粉反应快速生成活性铝原子,其生成活性铝原子的速度远远高于与钢基体中的Fe发生反应的速度,故大量的铝原子变会在试样表面造成聚集,阻碍正常的渗铝层形成过程,从而造成渗件边缘增厚严重,表面凹凸不平颗粒感严重和渗剂粘结等现象.图5为渗层厚度与渗铝剂铝粉含量的曲线关系图.Al原子作为固体粉末渗铝反应中的直接供铝剂,其含量直接决定了所产生的活性铝原子的数量.从图中可以看出,GCr15钢随固体粉末包埋渗铝剂中铝粉含量的升高,渗铝层的厚度逐渐增大,当铝粉含量变化范围在10%~25%时,渗铝层的厚度随着渗铝剂中铝粉含量的增高增大趋势明显.但当温度变化范围超过25%时,随渗铝温度的升高,渗铝层的厚度增长趋势逐渐减小.这是由于当渗铝剂配方中Al原子的含量达到一定范围时,随Al 原子含量的增加,渗层厚度的增加量逐渐减缓,这是由于当生成的活性 [Al]原子达到一定量时,一方面当供铝剂含量过多时,铝原子的利用率会下降,另一方面制约活性 [Al]扩散的主要因素为渗铝温度和渗铝保温时间,活性 [Al]原子的含量对渗铝层厚度的变化就不再是主要影响因素,因此增大渗剂中Al原子含量并无法使渗铝层的厚度显著增长.故准确控制渗剂配方中的铝含量,对渗层质量的好坏起到至关重要的影响.图4 渗层厚度与渗铝时间的曲线关系图Fig.4 The changing of aluminization layer thickness with aluminization time表4 Al粉含量对表面宏观状况的影响Tab.4 The effect of surface macroscopic condition with Al content试样编号 Al粉含量/% 表面状况1 10 表面呈灰黑色,渗层表面干净平整2 15 表面呈灰黑色,渗层表面干净平整3 20 表面呈灰黑色,渗层表面干净平整4 25 表面呈银灰色,试样表面平整干净5 30 表面呈灰黑色,试样边缘略微有增厚现象,试样表面有粘结现象6 35 表面呈灰黑色,试样表面有颗粒感,边缘增厚严重,表面有严重粘结现象2.4 催化剂NH4Cl含量的影响表5是渗铝温度为850℃,渗铝时间为3 h,铝粉含量为25%,不同NH4Cl含量下渗铝试样表面的宏观状况.当渗铝配方中不添加NH4Cl时,基本无渗铝反应发生;当NH4Cl含量添加为0.5%时,渗铝层表面开始有渗铝层出现;当渗铝剂中NH4Cl的含量增加到1.0%~1.5%时,渗铝层表面出现轻微的粘结现象,这是由于渗剂中NH4Cl的含量过少,无法为渗铝反应提供充足的催化剂,导致反应末期大量的铝粉熔融粘结在试样表面.当渗剂配方中NH4Cl的含量超过2.5%时,渗铝表面出现严重的粘结现象,试样表面平整度下降,颗粒感增强.这是由于NH4Cl在340℃开始发生NH4Cl→NH3↑+HCl↑分解反应,随着NH4Cl在渗剂配方中所占比重的增大,NH4Cl所产生的气体含量也随之提高,当NH4Cl分解所产生NH3和HCl气体的含量增加到一定程度时,将会从渗灌封口处的空隙中逸出,导致渗灌内活化剂气相的浓度有所降低,当渗灌内外的气相达到平衡以后,将会有大量的O2从渗灌封口的空隙中进入内部与渗铝剂中的Al发生反应生成氧化物,所形成的氧化物会以黑色的氧化皮的形式粘附在试样的表面,所以在渗铝剂配方中催化剂NH4Cl的含量所占比重不应太高.综合考虑,当渗铝剂配方中铝粉含量为25%,催化剂NH4Cl的含量为25%,在850℃高温条件下渗铝3 h后,所得渗件的渗铝层干净且平整,厚度值满足要求.图5 渗铝层厚度与铝粉含量的曲线关系图Fig.5 The changing of aluminiation layer thickness with Al content表5 NH4Cl含量对表面宏观状况的影响Tab.5 The effect of surfacemacroscopic condition with NH4Cl content试样编号 NH4Cl含量表面状况1 0表面呈金属光泽,无渗上痕迹2 0.5 表面略着灰黑色,且明显有漏渗金属光泽区3 1.0 表面呈灰黑色,有轻微粘结现象4 1.5 表面呈灰黑色,有轻微粘结现象52.0 表面呈灰黑色,表面平整6 2.5 表面呈灰黑色,颗粒感严重,粘结现象严重73.0 表面呈灰黑色,颗粒感严重,粘结现象严重3 结论1)当渗铝保温温度变化范围在700~900℃时,渗铝层的厚度随着渗铝温度的升高增大趋势明显;当渗铝温度超过900℃时,随渗铝温度的升高,渗铝层的厚度增长趋势逐渐减小,且渗铝层表面质量下降.2)当渗铝保温时间控制在0~3 h时,随渗铝保温时间的增加,渗铝层的厚度呈近乎直线型增长趋势,当保温时间超过3 h以后,虽然渗铝层厚度随保温时间的增加仍保持增长趋势,但单位时间渗铝层厚度增加的速率明显降低,且渗铝层表面出现粘结现象.3)当渗铝剂配方中Al粉的含量为10%~25%时,随Al粉含量的增加,渗铝层厚度增长迅速;当Al粉所占比例超过30%后,随Al粉含量的增长,渗铝层厚度增长缓慢,且表面粘结严重.4)当渗铝剂配方中所添加的NH4Cl的含量为2.5%时,所得渗层为灰黑色,平整且洁净.5)渗铝保温温度为850℃,渗铝时间为3 h条件下所得渗铝层的厚度达到70 μm 以上,所得试样表面平整.参考文献:[1] 屈晓斌.材料的磨损失效及其预防研究现状与发展趋势[J].摩擦学学报,1999,19(2):187-189.[2]Zhan Zhaolin,Liu Zhong.Microstructure and high-temperaturecorrosion behaviors of aluminide coatings by low-temperature pack aluminizing process[J].Applied Surface Science,2010,256(12):3874-3875.[3] 弓自洁,曹必刚.GCr15轴承钢的热处理发展动向[J].金属热处理,1992(9):3-6.[4] 孔永华,李东方.国内外轴承钢钢领组织与性能的比较[J].纺织器材,2011,38(2):70-72.[5] 黄志荣,徐宏.加速固体粉末渗铝的两段法新工艺[J].金属热处理,2003,4(13):39-41.[6]Levin L,Ginzburg A.Controlled formation of surface layers by pack aluminization[J].Surface and Coatings Technology,1998,106(2-3):209-213.[7] Zhan Zhao-lin,He Ye-dong.Low-temperature processing of Fe-Al intermetallic coatings assisted by ball milling[J].Science Direct,2006,14:76-77.[8] 李凌峰,沈嘉年.不锈钢表面粉末包埋渗铝过程及渗铝层表征[J].腐蚀科学与防护技术,2004,16(2):80-82.。
第八章_热渗镀
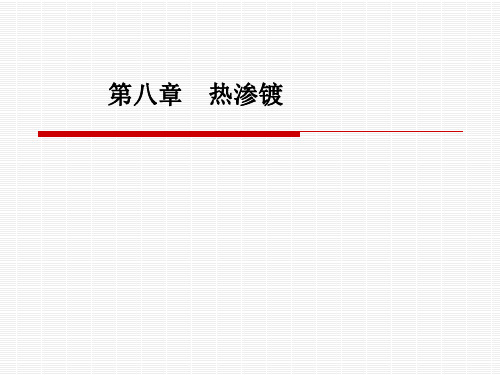
1.热浸铝 把预处理过的工件浸人熔融的铝浴中保温一定时间取出, 使其表面渗入一层铝。
2.渗铝层的性能: 渗铝层具有特殊的抗氧化性和耐腐蚀性
① 抗氧化性能
渗铝后的钢与原来未渗铝的钢相比,使用温度可提高200℃。
渗铝层要具有高的抗氧化能力,其含铝量必须高于12%,最好是 32~33%。 ② 耐腐蚀性 渗铝是目前提高钢材耐硫化物腐蚀最有效的手段之一。在大气条件
第八章
热渗镀
8-1 热渗镀概述
用加热扩散的方法把一种或几种元素渗入基体金属的表面,
得到一扩散合金层,称为热渗镀。
该技术的突出特点是表面强化层的形成主要依靠加热扩散 的作用,因而不存在结合力不足的问题。 热渗镀过程: 加热 + 扩散 渗入基体 合金层
热渗镀方法分类详见下图:
液渗法
① 热浸法
下,渗铝钢比热镀锌钢具有更好的耐蚀性。渗铝钢的腐蚀量仅是热
镀锌钢的1/10~1/5。
3.渗镀铝的应用 渗镀铝主要用于提高机件的耐热耐腐蚀寿命,可用于炉 内构件、烟道、汽车消音器、汽车进排气零部件、高温石 油化工用换热器、加热管、热风管、加热炉排风扇、空气 预热器和热处理用设备,以及一切与H2S,SO2,CO2, H2CO3,HNO3,液N2,水煤气接触的设备。
将工件直接浸入某一液态金属中,经较短时间即形成合
金镀层。
热浸渗优点是设备简单,操作容易,因而被广泛采用。 这种方法多用于钢铁制品的镀锌、镀铝、镀锡等。
② 熔烧法 把渗镀金属或合金粉末加粘结剂后制成料浆,均匀涂敷
于工件表面上,干燥后在惰性气体或真空环境中以稍高
于料浆熔点的温度加热烧结,通过液固界面扩散而形成 合金层。 该法能获得成分和厚度都很均匀的渗层,同时具有热传 递性好、渗速快等特点。
渗铝

渗铝使一种或多种金属原子渗入金属工件表层内的化学热处理工艺。
将金属工件放在含有渗入金属元素的渗剂中,加热到一定温度,保持适当时间后,渗剂热分解所产生的渗入金属元素的活性原子便被吸附到工件表面,并扩散进入工件表层,从而改变工件表层的化学成分、组织和性能。
与渗非金属相比,金属元素的原子半径大,不易渗入,渗层浅,一般须在较高温度下进行扩散。
金属元素渗入以后形成的化合物或钝化膜,具有较高的抗高温氧化能力和抗腐蚀能力,能分别适应不同的环境介质。
渗金属的方法主要有固体法(如粉末包装法、膏剂涂渗法等)、液体法(如熔盐浸渍法、熔盐电解法、热浸法等)和气体法。
金属元素可单独渗入,也可几种共渗,还可与其他工艺(如电镀、喷涂等)配合进行复合渗。
生产上应用较多的渗金属工艺有:渗铝、渗铬、渗锌、铬铝共渗、铬铝硅共渗、钴(镍、铁)铬铝钒共渗、镀钽后的铬铝共渗、镀铂(钴)渗铝、渗层夹嵌陶瓷、铝-稀土共渗等。
渗铝钢铁和镍基、钴基等合金渗铝后,能提高抗高温氧化能力,提高在硫化氢、含硫和氧化钒的高温燃气介质中的抗腐蚀能力。
为了改善铜合金和钛合金的表面性能,有时也采用渗铝工艺。
渗铝的方法很多。
冶金工业中主要采用热浸、静电喷涂或电泳沉积后再进行热扩散的方法,大量生产渗铝钢板、钢管、钢丝等。
静电喷涂或电泳沉积后,必须经过压延或小变形量轧制,使附着的铝层密实后再进行扩散退火。
热浸铝可用纯铝浴,但更普遍的是在铝浴中加入少量锌、钼、锰、硅,温度一般维持在670℃左右,时间是10~25分。
机械工业中应用最广的是粉末装箱法,渗剂主要由铝铁合金(或纯铝、氧化铝)填料和氯化铵催化剂组成。
渗铝主要用于化工、冶金、建筑部门使用的管道、容器,能节约大量不锈钢和耐热钢。
在机械制造部门,渗铝的应用范围也不断扩大。
低碳钢工件渗铝后可在780℃下长期工作。
在900~980℃环境中,渗铝件的寿命比未渗铝件显著提高。
18-8型不锈钢和铬不锈钢渗铝后,在594℃硫化氢气氛中,抗腐蚀能力比未渗铝的大大增加。
渗铝

渗铝aluminize;alumetize常用的渗镀品种之一,欲渗入的元素为铝。
被渗镀的材料可以是碳钢、不锈钢、镍基合金和钴基合金等。
渗铝的方法有固体粉末渗铝、热浸渗铝、料浆渗铝、气体渗铝、喷镀渗铝、快速电加热渗铝等多种。
渗铝工艺已在炼油、冶金、化工等方面得到广泛应用。
渗铝层有良好的抗高温氧化性,耐大气、海水、工业循环水、耐高温硫化物腐蚀和防止钢材的应力腐蚀破裂等优良性能。
渗铝钢在石油化工装备中的应用石油化工装备,有些需在中、高温(400-800℃)、强、腐蚀介质(如H2S、SO3、S02、CO2、NH3、有机酸等)和硬质颗粒(催化剂)的冲刷磨损条件下工作。
要求材料具备较好的耐腐、耐蚀和抗氧化性,能满足这些要求的,几乎全是价昂的高档材料。
但应用普通碳钢渗铝,可基本满足上述要求,是一种价廉物美的材料,因而得到了广泛的应用。
渗铝钢是对碳钢母材经过渗铝工艺处理,形成0.1-0.3mm的渗铝表层。
渗铝层具有耐磨、耐蚀和抗氧化性能,可满足特殊需求,但碳钢母材本身的性能不变或有所提高。
一、机械性能钢材渗铝一般在1000℃左右的奥氏体区域进行,由于渗铝后的冷却速度不同,母材可能出现各种不同的相变组织(如马氏体、索代体等)。
合金钢容易产生相变,引起机械性能的变化,因此合金钢渗铝目前很少应用。
低碳钢(C小于等于0.25%)渗铝后,不发生相变,只有晶粒大小的变化;只要正确地控制渗铝处理后冷却速度,可以细化晶粒,提高强度和韧性,所以应用最为广泛。
以20号碳钢为例,渗铝后在空气中冷却晶粒细化,由原来的5-6级上升至7-8级,强度和韧性都有所提高;渗铝后在炉中冷却,晶粒会粗化至4-5级,机械性能有所下降,但仍符合GB699-65要求,不影响使用。
二、抗氧化性能同一钢种,渗铝后比不渗铝的抗氧化性能有较大幅度的提高。
如20号碳钢的使用温度为500℃,渗铝后可提高至800℃;20碳钢渗铝后900℃保温10h,抗氧化能力提高153倍。
材料—常见元素对金属材料性能的影响

常见元素对金属材料性能的影响1. 碳(1)含碳量的增加,使得碳素钢的强度和硬度增加,而塑性、韧性和焊接性能下降。
(2)一般情况下,当含碳量大于0.25%时,碳钢可焊性开始变差,故压力管道中一般采用含碳量小于0.25%的碳钢。
含碳量的增加,其球化和石墨化的倾向增加。
(3)作为高温下耐热用的高合金钢,含碳量应大于或等于0.04%,但此时奥氏体不锈钢的抗晶间腐蚀性能下降。
2.硅(1)硅固溶于铁素体和奥氏体中可起到提高它们的硬度和强度的作用。
(2)含硅量若超过3%时,将显著地降低钢的塑性、韧性、延展性和可焊性,并易导致冷脆,中、高碳钢回火时易产生石墨化。
(3)各种奥氏体不锈钢中加入约2%的硅,可以增强它们的高温不起皮性。
在铬、铬铝、铬镍、铬钨等钢中加入硅,都将提高它们的高温杭氧化性能。
但含硅量太高时,材料的表面脱碳倾向增加。
(4)低含硅量对钢的耐腐蚀性能影响小大,只有当含硅量达到一定值时,它对钢的耐腐性能才有显著的增强作用。
含硅量为l5%~20%的的硅铸铁是很好的耐酸材料,对不同温度和浓度的硫酸、硝酸都很稳定,但在盐酸和王水的作用下稳定性很小,在氢氟酸中则不稳定。
高硅铸铁之所以耐腐蚀,是由于当开始腐蚀时,在其表面形成致密的SiO2薄层,阻碍了酸的进一步向内侵蚀。
3.硫、氧在碳素钢中的作用硫和氧作为杂质元素常以非金属化合物(如FeS、FeO)形式存在于碳素钢中,形成非金属杂质,从而导致材料性能劣化,尤其是硫的存在引起材料的热脆。
六和磷是钢中要控制的元素,并以其含量的多少来评定碳素钢的优劣。
(由于FeS可与铁形成共晶,并沿晶界分布),Fe-FeS共晶物的熔点为985℃,当在1000~1200℃温度下,对材料进行压力加工时,由于它已经熔化而导致晶粒开裂,使材料呈现脆性。
这种现象称为热脆。
)4.磷、砷、锑在碳素钢中的作用(1)磷、砷、锑作为杂质元素,它们对提高碳素钢的抗拉强度有一定的作用,但同时又都增加钢的脆性,尤其是低温脆性。
渗铝与渗锌区别
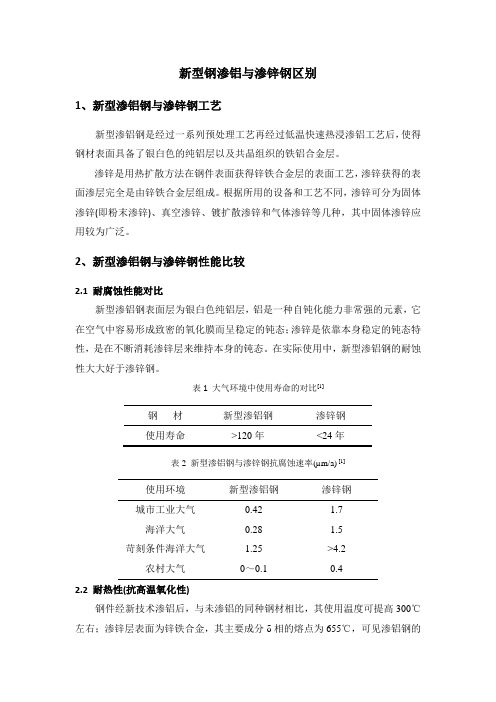
新型钢渗铝与渗锌钢区别1、新型渗铝钢与渗锌钢工艺新型渗铝钢是经过一系列预处理工艺再经过低温快速热浸渗铝工艺后,使得钢材表面具备了银白色的纯铝层以及共晶组织的铁铝合金层。
渗锌是用热扩散方法在钢件表面获得锌铁合金层的表面工艺,渗锌获得的表面渗层完全是由锌铁合金层组成。
根据所用的设备和工艺不同,渗锌可分为固体渗锌(即粉末渗锌)、真空渗锌、镀扩散渗锌和气体渗锌等几种,其中固体渗锌应用较为广泛。
2、新型渗铝钢与渗锌钢性能比较2.1 耐腐蚀性能对比新型渗铝钢表面层为银白色纯铝层,铝是一种自钝化能力非常强的元素,它在空气中容易形成致密的氧化膜而呈稳定的钝态;渗锌是依靠本身稳定的钝态特性,是在不断消耗渗锌层来维持本身的钝态。
在实际使用中,新型渗铝钢的耐蚀性大大好于渗锌钢。
表1 大气环境中使用寿命的对比[1]钢材新型渗铝钢渗锌钢使用寿命>120年<24年表2 新型渗铝钢与渗锌钢抗腐蚀速率(µm/a) [1]使用环境新型渗铝钢渗锌钢城市工业大气0.42 1.7海洋大气0.28 1.5苛刻条件海洋大气 1.25 >4.2农村大气0~0.1 0.42.2 耐热性(抗高温氧化性)钢件经新技术渗铝后,与未渗铝的同种钢材相比,其使用温度可提高300℃左右;渗锌层表面为锌铁合金,其主要成分δ相的熔点为655℃,可见渗铝钢的耐热性和抗高温氧化性远远优于渗锌钢。
表3 新型渗铝钢与渗锌钢的耐热性能[1]钢材新型渗铝钢渗锌钢最高使用温度800~1000℃<500℃2.3 表面硬度及耐磨性能新型渗铝钢表面生成的氧化铝层和铁铝合金层,均有很高的硬度值;渗锌层的主要组织为δ(FeZn7)相,与铁铝合金相比,硬度相对较低。
材料的耐磨性与其硬度值有正比关系,所以渗铝钢具有较高的硬度和耐磨性能。
经本公司低温快速热浸渗铝技术处理渗铝钢,其渗层大约20µm,不仅对钢材机械强度没有影响,而且母材的抗热冲击稳定性和疲劳强度均提高了10%以上。
35CrMo钢固体粉末渗铝及渗铝层性能研究

中 图 分 类 号 :TQ 5 . 6 0 0 9
文 献 标 志 码 :A
S u y o l m i ii g La e ir sr c u e n r o m a eo 5 M o S e l t d n A u n z n y r M c o t u t r sa d Pe f r nc f3 Cr te
E 3 Re d G H.R fie ain A Prcin l n a frMe h nc 2 e er r t : a t a Ma u l o c a i g o o s ( n d E .L n o : p i c n e 1 8 . 2 d e ) M3 o d n Ap l d S i c , 1 e e 9
通截 面上 的静压 基本 均匀 。出翅 片 管束后 进风 机之 前 的静压 不均匀 , 近管束 宽度 中部 的风速 较 高 , 靠 静
压较 低 。
参考文献 :
[] 张祉 佑 , 秉 三 .低 温 技 术 原 理 与装 置 [ .北 京 : 械 工 业 出 1 石 M] 机
版 社 ,9 7 18.
+ “+ 一+ “+ “+ ” + ”- -”+ 4 一+ ” + 一 + 一+ 一+ “+ “+ “ — 一
3 C Mo钢进 行 渗 铝 , 通过 试 验 验 证 固体粉 末 法 5r 并
渗 铝 后 的 3 C M o钢 的性 能 。 5r
一
+
“ +
一 +
“+
”— “— “-- - 4 ・卜 ”— ”- “—卜 ”—卜 一— ”- 一 卜 卜 4 - -・— 卜 - 卜 卜 —+
表 面 形 成 铝 铁 合 金 的 钢 , 文 采 用 固 体 粉 末 法 对 本
包埋时间对N80套管钢表面渗铝层组织和性能的影响

图 4为 不 同包 埋 时 间所 得 N 0套 管 钢 试 样 的 8
gaeO T ( at [ ] Sel ie20 ,6 6 :-. rd C G pr I) J .t p ,0 7 3 ( ) 1 eP 6
电化学极化 曲线. 与未渗铝 N 0套管钢试样相 比, S 经 2h 4h 6h 、 和 包埋渗铝处理后 的渗铝 N 0 8 套管 钢试样的阳极强化区均出现了明显 的 Tf 区 , a l 这就 e 说明渗铝 N 0套 管钢的 阳极溶解 反应完全受 活化 8
层 致 密度 的提 高作 用较厚 度 增加 更 为显 著 ; 长 包埋 时间 可以显 著提 高渗铝层 的硬 度 , 延 但过 长的 包
埋 时 间会 同时造 成基 体硬 度 严 重地 下 降 ; 包埋 时 间对 腐蚀 性 能 的影 响作 用不 明显 .
关键 词 : 8 管钢 ; 铝层 ; N 0套 渗 包埋 时 间 ; 显微 组 织 ; 耐蚀 性能 中 图分 类号 :B 3 T 32 文献 标 识码 : A
工艺处理. 同包埋时间下所得渗层的物相组成、 不 微观形貌、 显微硬度和电化学性能不 同. 测试结果 表 明: 渗铝时间为 2h时Байду номын сангаас 所得渗铝层厚度为 10I 渗铝 时间延长到 4h 6h , 5 m, . L 和 后 渗铝层厚度增 大到 30I 渗铝时间为 2h 4h时所得 N 0套管钢的渗铝层主要 由 F A 金 属间化合物组成 , 0 m; . L 、 8 el 当 渗 铝时间为6h时, 渗铝层 中开始 出现 了高铝 F l相; eA 不同时间包埋渗铝处理后的 N 0 管钢试 8套 样表 面硬度高于基体 , 自腐蚀 电流密度显著下降. 由此得 出结论 : 高铝相铁铝化合物随 包埋时间的 延长开始出现 ; 渗铝层厚度随包埋时间的延长有所增加 , 当包埋 时间超过 4h后 , 包埋 时间对渗铝
渗铝及其在工业上的应用

熔融盐腐蚀
渗铝钢和渗铝高温合金具有非常好的耐腐蚀能力,可以抵抗包括氯酸盐、硝酸盐、亚硝酸盐和碳酸盐 的腐蚀。
渗铝碳钢锅经过多年使用证明,其抗腐蚀能力比不锈钢好。
其他可以应用渗铝涂层的领域
工业领域 水泥 硫酸
我们通常为除硫设备的冷凝器和热交换器做渗铝涂层。
中国科学院金属研究所表面工程研究部
地址:沈阳市沈河区文化路 72 号
联系方式 hjyu11s@
氧化
相对于奥氏体不锈钢而言,渗铝的碳钢和高温合金具有更为优良的耐高温氧化性能。在 1000°C (1850°F)以上的工作寿命不低于不锈钢。
渗铝涂层可以形成一层致密的氧化铝阻挡层,可以阻止碳扩散到基体当中,从而防止了金属粉化现象 的发生,延长金属使用寿命。我们的扩散涂层可以抵抗上万小时的金属粉化腐蚀。
用来抵抗金属粉化现象的渗铝部件有热交换器、管道、金属管套和其他紧固件等。
结焦
结焦现象存在于很广的温度范围内。在某些温度范围内抗结焦剂和其他冶金方案无法完全解决表面结 焦,而渗铝和渗铬涂层可以提供长达数年的防护,防止结焦的发生。最常见的应用是在乙烯蒸汽裂解 管表面渗铝化物涂层防止结焦。
渗铝的尺寸限制
我们现在的尺寸限制为 1.7 米长,直径 0.7 米的圆 ASTM B875 - 96 涂覆涂层,并可根据客户需要订制。
中国科学院金属研究所表面工程研究部
地址:沈阳市沈河区文化路 72 号
联系方式 hjyu11s@
渗碳
渗碳,例如催化重整装置,结焦会导致碳扩散到合金当中,并且形成稳定的金属碳化物,这些金属碳 化物主要集中在晶界当中,降低合金的性能。渗铝可以有效的利用表面形成的氧化铝膜来防止碳的进 一步渗透。
渗铝钢焊接工艺及焊接接头性能研究
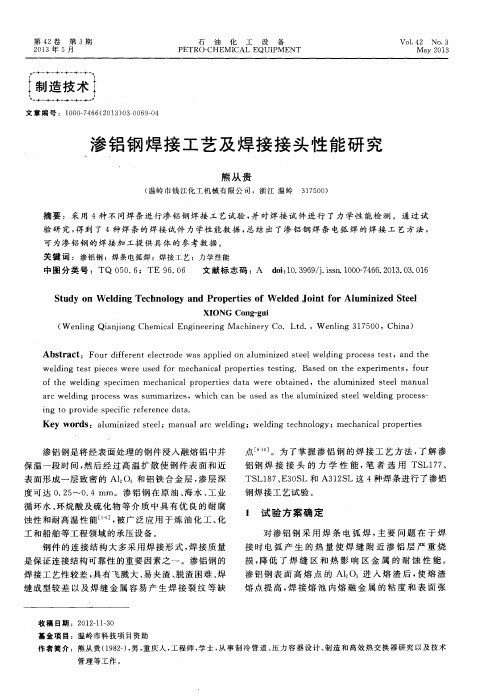
Ke y wo r d s: a l u mi n i z e d s t e e l ;m a n u a l a r c we l d i n g;we l d i n g t e c h n o l o g y;me c h a n i c a l p r o p e r t i e s
S t u d y o n We l di n g Te c h n o l o g y a n d Pr o p e r t i e s o f We l de d J o i n t f o r Al u mi n i z e d S t e e l
we l d i n g t e s t p i e c e s we r e u s e d f o r me c h a ni c a l p r op e r t i e s t e s t i ng . Ba s e d on t he e x pe r i me nt s ,f o ur o f t he we l di ng s pe c i me n me c ha ni c a l p r o pe r t i e s da t a we r e o bt a i ne d, t he a l umi n i z e d s t e e l ma nu a l a r c we l di ng pr o c e s s wa s s umma r i z e s,whi c h c a n h e us e d a s t he a l u mi n i z e d s t e e l we l d i ng p r oc e s s — i ng t o p r o v i de s pe c i f i c r e f e r e nc e da t a .
渗铝工艺的工艺特点

渗铝工艺的工艺特点渗铝工艺是一种将铝元素渗透到其他材料表面的工艺,也称为铝渗透工艺。
它通过在高温和高压的环境中,将铝元素与被渗透材料的表面发生化学反应,从而形成一层致密、耐蚀、耐磨的铝合金层。
该工艺具有以下特点:1. 高渗透性:渗铝工艺能够在短时间内实现铝元素的高渗透率,使得被渗透材料的表面快速形成均匀的铝合金层。
这种高渗透性能使渗铝工艺在工业生产中得到广泛应用。
2. 耐腐蚀性:渗铝工艺形成的铝合金层具有良好的耐腐蚀性能。
铝合金层能够有效地防止被渗透材料的表面受到氧化、腐蚀等外界环境的侵蚀,从而延长了被渗透材料的使用寿命。
3. 耐磨性:渗铝工艺形成的铝合金层具有优异的耐磨性能。
铝合金层能够有效地防止被渗透材料的表面受到摩擦、磨损等力量的破坏,从而提高了被渗透材料的耐磨性能。
4. 良好的附着力:渗铝工艺能够使铝元素与被渗透材料的表面发生化学反应,从而形成一层牢固的铝合金层。
这种牢固的附着力使得铝合金层与被渗透材料的结合更加紧密,不易剥离。
5. 适用范围广:渗铝工艺可以应用于各种不同的材料,包括金属材料和非金属材料。
无论是钢铁、铜、合金、陶瓷等材料,都可以通过渗铝工艺来提高其表面的性能。
6. 工艺简单:相比于其他表面处理工艺,渗铝工艺具有工艺简单的特点。
渗铝工艺只需要将被渗透材料与含有铝元素的渗透剂一起置于高温高压的环境中进行反应即可,不需要复杂的设备和操作。
总的来说,渗铝工艺具有高渗透性、耐腐蚀性、耐磨性、良好的附着力、适用范围广和工艺简单等特点。
这些特点使得渗铝工艺成为一种常用的表面处理工艺,被广泛应用于航空航天、汽车制造、机械制造等领域,提高了材料的使用寿命和性能。
热浸渗铝球墨铸铁合金层组织的演变规律

热浸渗铝球墨铸铁合金层组织的演变规律陈江;赵君文;黄兴民;程乾;韩靖;张鲲;戴光泽【摘要】为了探索热浸渗铝球墨铸铁合金层的组织演变规律以及基体中 Ni 含量对渗铝合金层组织的影响,利用激光共聚焦显微镜(LCM)、场发射扫描电子显微镜(FESEM)以及能谱仪(EDS)对不同渗铝时间制备的球墨铸铁渗铝试样以及不同 Ni 含量的球墨铸铁渗铝试样的合金层组织进行观察和定量分析。
结果表明:在本实验条件下,热浸渗铝球墨铸铁合金层组织由厚度较大的“舌状”Fe2Al5和厚度很小的 FeAl3组成,合金层和表面纯铝层中存在石墨球分布;在0~15 min内,渗铝试样合金层经过短暂的过渡阶段后随渗铝时间的延长按抛物线规律扩散生长,15 min后合金层厚度达65µm以上;基体Ni含量由0增加至1.5%(质量分数)后,合金层厚度由88µm减小至49µm,合金层与基体的“舌状”界面程度变小。
此外,对热浸渗铝球墨铸铁合金层组织演变机理进行了探讨。
%To study the microstructure evolution of intermetallic layer of hot dip aluminized ductile cast iron and the effect of Ni content on the microstructure of the intermetallic layer, laser confocal microscope (LCM), field emission scanning electron microscope (FESEM) and Xray energy dispersive spectrometer (EDS) were used to carry out the microstructure observation and quantitative analysis of the intermetallic layer of hot dip aluminized ductile cast iron with different hotdip times as well as specimens with different Ni contents. The results show that the intermetallic layer consists of a“tongueshape”Fe2Al5 layer and a FeAl3 layer of which the thickness is much thinner than that of the former. At the same time, graphite spheroids disperse in the outer Al topcoat and the inner FeAl intermetalliclayer;within 0−15 min, the growth r ate of the intermetallic layer approximately obeys the parabolic rate law after a short transition phase, and the layer is thicker than 65 µm after 15 min. Furthermore, the thickness of the intermetallic layer decreases from 88 to 49 µm with the increase of Ni content from 0 to 1.5%(mass fraction), andthe“tongueshape”interface between the substrate and Fe2Al5 phase becomes smooth. In addition, the microstructure evolution of intermetallic layer of hot dip aluminized ductile cast iron was also discussed.【期刊名称】《中国有色金属学报》【年(卷),期】2013(000)005【总页数】7页(P1248-1254)【关键词】球墨铸铁;热浸渗铝;组织演变;Ni含量【作者】陈江;赵君文;黄兴民;程乾;韩靖;张鲲;戴光泽【作者单位】西南交通大学材料科学与工程学院,成都 610031;西南交通大学材料科学与工程学院,成都 610031;西南交通大学材料科学与工程学院,成都610031;西南交通大学材料科学与工程学院,成都 610031;西南交通大学材料科学与工程学院,成都 610031;西南交通大学材料科学与工程学院,成都 610031;西南交通大学材料科学与工程学院,成都 610031【正文语种】中文【中图分类】TG174.443钢铁材料经热浸渗铝后在试样表面形成保护层,能显著提高其抗高温氧化及抗热腐蚀性能等[1-3]。