汽车轻量化设计理念
现代汽车设计理念和技术创新研究

现代汽车设计理念和技术创新研究一、引言随着人们生活水平和经济水平的提高,汽车已经成为人们生活中必不可少的交通工具之一。
而作为汽车的制造者,汽车设计理念和技术创新水平的提高也变得尤为重要。
本文将主要探讨现代汽车设计理念和技术创新研究的相关问题。
二、国内外汽车设计理念的发展汽车设计理念包括整车造型、车辆空气动力学、座椅舒适性等方面。
在国内和国外,汽车设计理念的发展历程各不相同。
1、国外汽车设计理念的发展早在20世纪初,汽车造型设计已经呈现出不同的风格。
20世纪50年代,欧洲车型逐渐被美国车型所取代。
但是在20世纪70年代以后,欧洲的汽车设计理念又重新占据了主导地位。
现代汽车设计理念的发展也是基于传统车型的改良和突破。
2、国内汽车设计理念的发展中国的汽车设计起步较晚,到20世纪60、70年代才有了国产汽车的设计制造。
但是由于产业链不完善,技术人才不足等因素,中国的汽车设计在形态等方面还比较单一,整车造型上相对较为保守。
三、现代汽车技术创新研究1、动力总成技术在国内,汽车生产厂家越来越注重动力总成技术的研究和开发,力求提高汽车动力性能、降低油耗和排放等。
2、智能化汽车控制技术智能化汽车控制技术是指通过计算机、网络通信等多种技术手段将汽车智能化,使汽车能够实现无人驾驶、智能导航、远程诊断等功能。
3、汽车轻量化技术轻量化技术是指通过优化材料、减少汽车质量等方式降低车辆重量,从而提高汽车的燃油效率和行车性能。
四、结论如今,人们的生活离不开汽车,汽车成为重要的工具。
而在汽车制造业中,汽车设计理念和技术创新研究已成为行业内不可缺少的一部分。
随着中国汽车工业本土创新能力的提高,相信中国汽车在未来的发展中也会和国际汽车同步发展。
汽车车身轻量化设计原理

四、白车身轻量化系数简介
标杆车型
Audi A2
Mini 2003 轿车
Volvo S60
VW Fox
BMW New X5 SUV
VW Touareg
扭转刚度 (N·m/deg)
11900
公司现有车型 XX
24500
XX
ห้องสมุดไป่ตู้轿车
20000
XX
17941
XX
27000
XX
SUV
36900
XX
扭转刚度 (N·m/deg)
9153 8866 10618 9829 15102 17000
德系车的扭转刚度相对较高,基本达到15000 N.m /deg以上, 高刚度车身可提升整车的安全性和操稳性,是未来的发展趋势。
2020-5-26
10
四、白车身轻量化系数简介
汽车轻量化设计应包括质量减轻和功能的完善和改进,为表征白车 身轻量化的效果,宝马汽车公司提出了轻量化系数的概念,该系数L可用下 式表示为:
2020-5-26
5
二、整车重量管理流程及理念
AudiA4在实现整车性能和功能时造成重量大幅提高,通过整车重 量管理采取轻量化技术设计有效平衡性能与重量之间的矛盾对立关系; 即保证性能又达成重量目标,甚至减轻整车重量,进一步提高经济性.
6
三、车身轻量化开发实施思路
建立机制
设定目标
技术预研
车身轻量化方案制定
增加 130kg
4
二、整车重量管理流程及理念
整车重量管理的理念及原则即保证整车性能,实现功能的前提下达 成整车重量目标
不采用高强钢 重量发展趋势
采用了高强钢后 重量发展趋势
电动汽车的轻量化设计理念

电动汽车的轻量化设计理念随着环保意识的不断增强和技术的不断进步,电动汽车逐渐成为人们追逐的热门选择。
然而,电动汽车的重量成为了制约其发展的一个重要问题。
为了解决这一问题,轻量化设计理念逐渐被引入到电动汽车的制造过程中。
本文将就电动汽车的轻量化设计理念进行探讨。
1. 轻量化设计的重要性电动汽车的轻量化设计很重要,原因有三。
首先,减轻汽车重量可以降低车辆动力消耗,提高续航里程,延长电池寿命。
其次,减少重量可以降低车辆的制动距离,提高行驶安全性。
最后,轻量化设计可以减少对资源的消耗,降低环境负担。
2. 材料选择在轻量化设计中,材料选择显得尤为重要。
传统汽车中常用的钢材在电动汽车中体现不出优势,因此需要选择更轻、更强度高的材料。
目前,常用的轻量化材料包括铝合金、碳纤维增强塑料(CFRP)和镁合金等。
这些材料具有良好的强度和刚度,使汽车在减少重量的同时,仍然能够保持结构的稳定性。
3. 结构优化在电动汽车的设计中,结构也需要进行优化,以实现轻量化目标。
通过使用高强度材料,可以在保持结构强度的前提下减少材料的使用量,降低整车重量。
此外,合理设计的支撑结构和准确的荷载分配也能进一步降低车身重量。
4. 部件优化电动汽车的部件也需要进行优化设计,以减少重量。
例如,在电池方面,可以采用高能量密度的锂离子电池,以减少电池组的重量。
在电动机方面,可以采用高效、轻量的电动机,以提高整体效率和减少重量。
各个部件的优化设计可以在整体上减轻汽车重量,提升续航里程。
5. 制造工艺在电动汽车的制造过程中,采用先进的制造工艺也能够实现轻量化设计的目标。
例如,采用铝合金车身可以通过冲压、铆接和粘接等工艺技术实现。
此外,采用先进的连接技术和焊接技术也能提高车身的整体刚度和强度。
6. 应用案例举例来说,特斯拉公司在电动汽车的轻量化设计方面做出了很大的努力。
他们使用了大量的铝合金材料,使得整车重量明显减轻。
此外,他们还将碳纤维材料应用于车身部件中,进一步降低了车身重量,提升了车辆的性能和续航里程。
阐述汽车结构的轻量化设计方法

阐述汽车结构的轻量化设计方法1 汽车结构轻量化设计的提出目前,国内外汽车技术的发展主要有以下三个方面的趋势:一是轻量化;二是环保;三是安全。
现在,人们已经渐渐认识到,想要让汽车工业长久发展下去,就要走可持续发展之路。
可持续发展之路一个很明显的要求就是要节约资源,减少消耗。
针对汽车工业,为了达到这样的要求,就必须采取提高发动机的效率、改善传动机构或者降低车身重量等方法。
其中降低车体重量的一个重要方法就是汽车结构的轻量化设计,其可以显著减轻汽车的重量。
在现实生活中,无论是普通的柴油汽油汽车、电驱动汽车还是燃气驱动汽车,车身机构轻量化都有极为重要的意义。
汽车行业一直在追求舒适、安全、快速,而为了达到这一目标,汽车轻量化是最佳途径之一。
2 汽车材料的轻量化2.1 高强度钢在汽车结构轻量化设计中的应用在汽车结构中,使用最多的材料就是钢。
因此,利用高强度钢来减少汽车结构中钢的使用,对于汽车结构的轻量化设计有重要意义。
一般来说,钢的强化途径主要有以下五种:一是加碳强化。
由于钢中含碳的百分比不同其刚度也不同,因此想要得到高强度钢就需要控制钢中碳的含量。
为此,必须适当增加钢中珠光体的含量,降低铁素体的含量;二是合金强化,在钢中添加合金元素可以大大增加钢的强度,而且不同的合金元素能够使钢所具有的性能也不同,能够大大扩大钢的适用范围;三是固溶强化,即在钢中添加磷、硅或者锰等元素来加强钢的强度的方法;四是热处理强化。
一般来说,钢在经过一定顺序的冷热交替处理之后,其金相组织的结构会发生变化,从而使钢的强度增加。
另外,热处理还可以使钢内碳等元素的含量发生变化,从而可以使钢内部形成一层一层地具有不同性质的结构;五是应力强化,钢在受到一定限度内的拉力之后,其屈服强度可能会提高。
因为钢在受到一定限度内的应力后表面会存在残余应力,这种应力可以抵消钢在今后使用中受到的弯曲应力、扭转应力等。
高强度钢主要是用于制造汽车的外壳和结构件,其优点是经济性好、强度较大;但是其缺点也比较明显,就是耐腐蚀性差。
车身零部件轻量化设计与优化
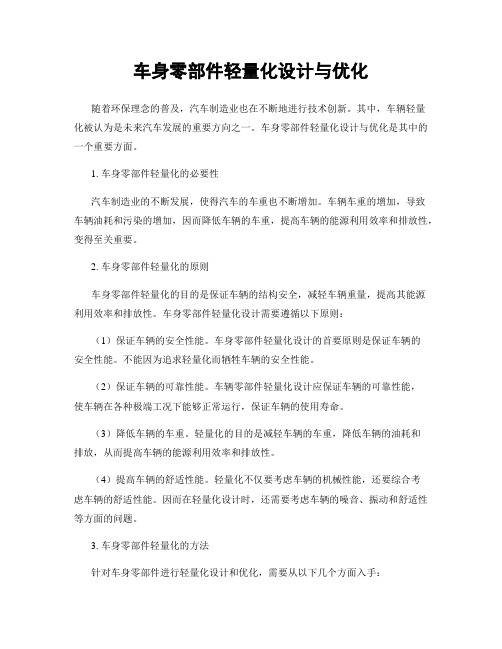
车身零部件轻量化设计与优化随着环保理念的普及,汽车制造业也在不断地进行技术创新。
其中,车辆轻量化被认为是未来汽车发展的重要方向之一。
车身零部件轻量化设计与优化是其中的一个重要方面。
1. 车身零部件轻量化的必要性汽车制造业的不断发展,使得汽车的车重也不断增加。
车辆车重的增加,导致车辆油耗和污染的增加,因而降低车辆的车重,提高车辆的能源利用效率和排放性,变得至关重要。
2. 车身零部件轻量化的原则车身零部件轻量化的目的是保证车辆的结构安全,减轻车辆重量,提高其能源利用效率和排放性。
车身零部件轻量化设计需要遵循以下原则:(1)保证车辆的安全性能。
车身零部件轻量化设计的首要原则是保证车辆的安全性能。
不能因为追求轻量化而牺牲车辆的安全性能。
(2)保证车辆的可靠性能。
车辆零部件轻量化设计应保证车辆的可靠性能,使车辆在各种极端工况下能够正常运行,保证车辆的使用寿命。
(3)降低车辆的车重。
轻量化的目的是减轻车辆的车重,降低车辆的油耗和排放,从而提高车辆的能源利用效率和排放性。
(4)提高车辆的舒适性能。
轻量化不仅要考虑车辆的机械性能,还要综合考虑车辆的舒适性能。
因而在轻量化设计时,还需要考虑车辆的噪音、振动和舒适性等方面的问题。
3. 车身零部件轻量化的方法针对车身零部件进行轻量化设计和优化,需要从以下几个方面入手:(1)材料的优化选择。
轻量化首先就是要选用质量轻、强度高、刚度高的材料。
例如,高强度钢、铝合金、碳纤维等材料都是选择较为理想的材料。
(2)结构的优化设计。
车身零部件的结构优化设计,可以通过改进结构形式和减小件数来降低整车的重量。
如采用先进的焊接技术可以降低车身焊点数量。
(3)工艺的改进。
工艺的改进可以降低车身零部件的重量,例如采用先进的烤漆技术,可以更好的控制反光,减少涂层厚度,降低零部件重量。
4. 结语车身零部件轻量化设计与优化是未来车辆轻量化的一个重要方面。
实现车身零部件的轻量化设计,不仅能够降低车辆的油耗和污染,还能够提高车辆的能源利用效率和排放性,从而推动汽车制造业的可持续发展。
、选取汽车任意零部件进行轻量化设计,写明设计思路,及前后对比

、选取汽车任意零部件进行轻量化设计,写明设计思路,及前后对比设计思路:选取汽车任意零部件进行轻量化设计,首先需要确定目标零部件,并分析其功能和使用要求。
然后可以采取以下几个方面的设计思路进行轻量化:1. 优选材料:选择高强度、高刚度的材料,如高强度钢材、铝合金等,以减少零部件的重量。
同时还要考虑材料的成本和可加工性,确保设计的可行性。
2. 结构优化:通过结构的优化设计,减少材料的使用量,同时保持零部件的强度和刚度。
可以采用加强筋、薄壁结构、孔洞等手段来实现结构重量的减轻。
3. 制造工艺优化:在设计时考虑零部件的制造工艺,尽量减少工序和操作,减少材料的浪费。
采用先进的制造工艺,如模锻、压铸、复合材料制造等,可以提高零部件的性能和轻量化效果。
4. 材料组合优化:在一些特殊情况下,可以采用不同材料的组合来进行设计,如复合材料结构、材料层叠等,以实现更轻量化的设计效果。
前后对比:轻量化设计后的零部件相较于原有设计,具有以下优势:1. 减重效果显著:通过优选材料、结构优化和制造工艺优化等手段,能够有效地减轻零部件的重量,降低整车的总重,提高汽车的燃油经济性和动力性能。
2. 强度和刚度满足要求:尽管轻量化设计减少了材料的使用量,但通过结构优化和合理的材料选择,仍保持了零部件的足够强度和刚度,保证了汽车的安全性和可靠性。
3. 节约材料和能源:轻量化设计减少了材料的使用量,节约了原材料资源,并在整个产品生命周期中减少了能源消耗,具有显著的环境保护效益。
4. 提升可持续性:轻量化设计符合现代社会对于可持续发展的要求,降低了环境影响和生产成本,提高了产品的竞争力和可持续性。
综上所述,轻量化设计对汽车任意零部件具有明显的优势,在实际应用中可以发挥重要的作用。
新能源车辆车身结构轻量化设计研究

新能源车辆车身结构轻量化设计研究随着环保理念的日益普及,新能源车辆已经成为了市场上瞩目的领域。
然而,对于新能源车辆而言,车身结构轻量化的问题是其制造以及续航能力的重要因素。
在本文中,我们将探讨如何通过轻量化设计来提高新能源车辆的性能和实现可持续发展。
一、轻量化设计的概念和意义轻量化设计即是通过减少汽车的重量来提高其性能表现的设计方案。
轻量化设计可以分为两种,一种是材料轻量化,另一种是结构轻量化。
材料轻量化是通过采用新材料、优化材料厚度或者减少材料的使用量来减轻汽车的重量。
而结构轻量化是通过优化汽车的构造设计、减少结构件的数量来减轻汽车的重量。
轻量化设计对于新能源汽车而言至关重要。
因为新能源汽车的基础是电力,而电池的质量和容量决定了其续航能力。
所以,在保证其稳定性和安全性的前提下,轻量化设计可以有效地提高新能源汽车的续航能力,增强其市场竞争力。
二、新能源汽车轻量化设计的研究现状目前,新能源汽车轻量化设计的研究主要集中在车身结构和材料方面。
其中,一些新型的材料,例如碳纤维复合材料、铝合金材料等已经被广泛应用于新能源汽车的制造中。
这些新材料能够实现优异的性能表现和轻质化的效果,带来了良好的市场反响。
另一方面,新能源汽车的车身结构设计也在不断优化中。
例如应用优化设计原理和计算机模拟技术,可以优化车身结构,降低重量。
通过减少车身壳体中的不必要的支撑和加固结构,使得车身结构更加稳固、安全,并且减轻了车身自重。
三、新能源汽车轻量化设计的前景和发展趋势从行业发展的角度来看,新能源汽车的未来发展必将趋势于轻量化。
因为随着人们的环保意识不断加强,节能与低碳成为了社会发展的主旋律。
同时,轻量化设计将成为新能源汽车更为普遍的发展趋势,也是制造商实现可持续发展的重要途径。
在实际生产中,新能源汽车制造商也在不断地进行创新与改进,在材料和结构方面寻求技术的突破。
例如,压铸成形、全铝车身、高强钢材料等均成为了新能源汽车轻量化设计的重要发展方向。
汽车车身结构的轻量化设计
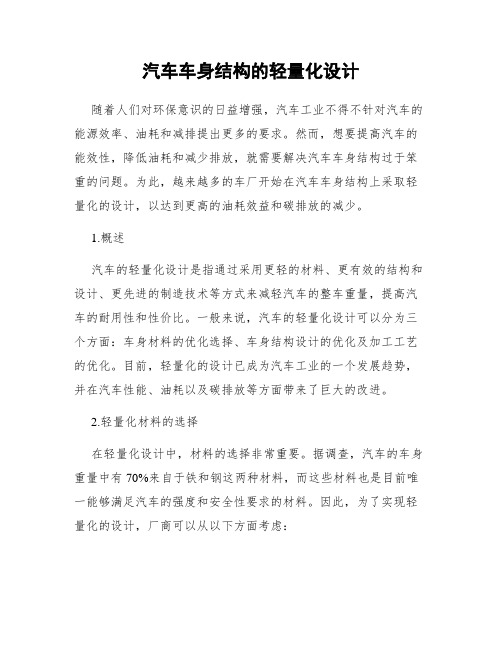
汽车车身结构的轻量化设计随着人们对环保意识的日益增强,汽车工业不得不针对汽车的能源效率、油耗和减排提出更多的要求。
然而,想要提高汽车的能效性,降低油耗和减少排放,就需要解决汽车车身结构过于笨重的问题。
为此,越来越多的车厂开始在汽车车身结构上采取轻量化的设计,以达到更高的油耗效益和碳排放的减少。
1.概述汽车的轻量化设计是指通过采用更轻的材料、更有效的结构和设计、更先进的制造技术等方式来减轻汽车的整车重量,提高汽车的耐用性和性价比。
一般来说,汽车的轻量化设计可以分为三个方面:车身材料的优化选择、车身结构设计的优化及加工工艺的优化。
目前,轻量化的设计已成为汽车工业的一个发展趋势,并在汽车性能、油耗以及碳排放等方面带来了巨大的改进。
2.轻量化材料的选择在轻量化设计中,材料的选择非常重要。
据调查,汽车的车身重量中有70%来自于铁和钢这两种材料,而这些材料也是目前唯一能够满足汽车的强度和安全性要求的材料。
因此,为了实现轻量化的设计,厂商可以从以下方面考虑:(1)铝合金:相比于铁和钢,铝合金密度更低,具有一定的强度和硬度,耐腐蚀性能良好,成本较高,但是可以提高车辆燃油效率及减少碳排放。
(2)碳纤维:碳纤维是当今车身轻量化的理想材料,密度仅仅只有铁和钢的1/5,而且具有很高的强度和拉伸强度。
但是碳纤维容易受潮湿及高温影响,而且成本非常高,所以在实际应用中用的较少。
(3)镁合金:镁合金是一种相对轻质的金属材料,密度比铝合金更轻,力学性能也很好,而且还具有良好的热传导和电导率。
不过,镁合金的腐蚀性也比较强,制造成本较高,所以仅在部分车型上应用。
3.车身结构设计的优化除了材料的选择,车身结构的优化设计也是轻量化设计的重要方面。
通常,车厂可以采取以下设计措施:(1)钢材件结构优化:对车身的各个零件加以精简或是部分区域的厚度减薄,将车身零件的功能和强度保持不变,同时将车身重量降低,否则加强,可以使用HSS及UHSS材料。
如何进行汽车轻量化设计
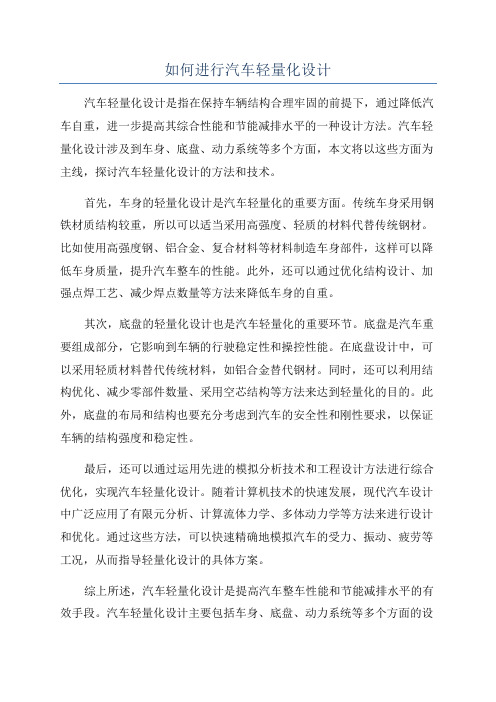
如何进行汽车轻量化设计汽车轻量化设计是指在保持车辆结构合理牢固的前提下,通过降低汽车自重,进一步提高其综合性能和节能减排水平的一种设计方法。
汽车轻量化设计涉及到车身、底盘、动力系统等多个方面,本文将以这些方面为主线,探讨汽车轻量化设计的方法和技术。
首先,车身的轻量化设计是汽车轻量化的重要方面。
传统车身采用钢铁材质结构较重,所以可以适当采用高强度、轻质的材料代替传统钢材。
比如使用高强度钢、铝合金、复合材料等材料制造车身部件,这样可以降低车身质量,提升汽车整车的性能。
此外,还可以通过优化结构设计、加强点焊工艺、减少焊点数量等方法来降低车身的自重。
其次,底盘的轻量化设计也是汽车轻量化的重要环节。
底盘是汽车重要组成部分,它影响到车辆的行驶稳定性和操控性能。
在底盘设计中,可以采用轻质材料替代传统材料,如铝合金替代钢材。
同时,还可以利用结构优化、减少零部件数量、采用空芯结构等方法来达到轻量化的目的。
此外,底盘的布局和结构也要充分考虑到汽车的安全性和刚性要求,以保证车辆的结构强度和稳定性。
最后,还可以通过运用先进的模拟分析技术和工程设计方法进行综合优化,实现汽车轻量化设计。
随着计算机技术的快速发展,现代汽车设计中广泛应用了有限元分析、计算流体力学、多体动力学等方法来进行设计和优化。
通过这些方法,可以快速精确地模拟汽车的受力、振动、疲劳等工况,从而指导轻量化设计的具体方案。
综上所述,汽车轻量化设计是提高汽车整车性能和节能减排水平的有效手段。
汽车轻量化设计主要包括车身、底盘、动力系统等多个方面的设计和优化。
通过采用高强度、轻质的材料、优化结构设计、减少焊点数量、优化动力系统等方法,可以实现汽车的轻量化设计。
此外,运用先进的模拟分析技术和工程设计方法,可以指导设计和优化过程,为汽车轻量化设计提供有效的支持。
汽车轻量化设计可以降低车辆重量,提高燃油经济性和安全性能,对于推动汽车技术进步和未来可持续发展有着重要意义。
汽车车身设计及制造工艺新技术分析
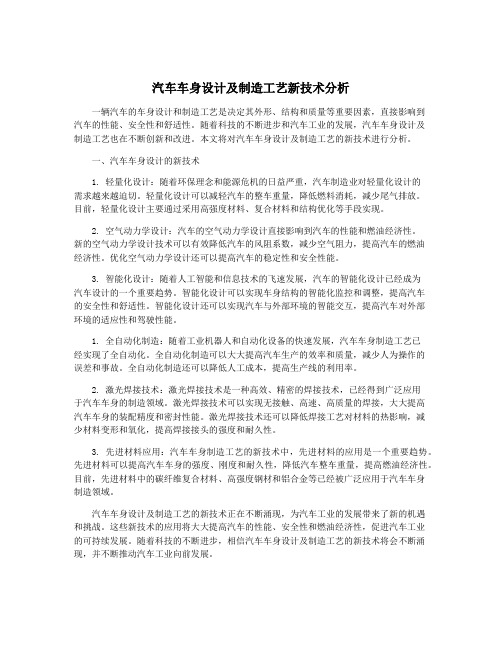
汽车车身设计及制造工艺新技术分析一辆汽车的车身设计和制造工艺是决定其外形、结构和质量等重要因素,直接影响到汽车的性能、安全性和舒适性。
随着科技的不断进步和汽车工业的发展,汽车车身设计及制造工艺也在不断创新和改进。
本文将对汽车车身设计及制造工艺的新技术进行分析。
一、汽车车身设计的新技术1. 轻量化设计:随着环保理念和能源危机的日益严重,汽车制造业对轻量化设计的需求越来越迫切。
轻量化设计可以减轻汽车的整车重量,降低燃料消耗,减少尾气排放。
目前,轻量化设计主要通过采用高强度材料、复合材料和结构优化等手段实现。
2. 空气动力学设计:汽车的空气动力学设计直接影响到汽车的性能和燃油经济性。
新的空气动力学设计技术可以有效降低汽车的风阻系数,减少空气阻力,提高汽车的燃油经济性。
优化空气动力学设计还可以提高汽车的稳定性和安全性能。
3. 智能化设计:随着人工智能和信息技术的飞速发展,汽车的智能化设计已经成为汽车设计的一个重要趋势。
智能化设计可以实现车身结构的智能化监控和调整,提高汽车的安全性和舒适性。
智能化设计还可以实现汽车与外部环境的智能交互,提高汽车对外部环境的适应性和驾驶性能。
1. 全自动化制造:随着工业机器人和自动化设备的快速发展,汽车车身制造工艺已经实现了全自动化。
全自动化制造可以大大提高汽车生产的效率和质量,减少人为操作的误差和事故。
全自动化制造还可以降低人工成本,提高生产线的利用率。
2. 激光焊接技术:激光焊接技术是一种高效、精密的焊接技术,已经得到广泛应用于汽车车身的制造领域。
激光焊接技术可以实现无接触、高速、高质量的焊接,大大提高汽车车身的装配精度和密封性能。
激光焊接技术还可以降低焊接工艺对材料的热影响,减少材料变形和氧化,提高焊接接头的强度和耐久性。
3. 先进材料应用:汽车车身制造工艺的新技术中,先进材料的应用是一个重要趋势。
先进材料可以提高汽车车身的强度、刚度和耐久性,降低汽车整车重量,提高燃油经济性。
汽车轻量化技术方案及应用实例

汽车轻量化技术方案及应用实例一、汽车轻量化分析轻量化技术应用给汽车带来的最大优点就是油耗的降低,并且汽车轻量化对于环保,节能,减排,可持续发展也发挥着重大效用。
一般情况下,汽车车身的重量约占总重量的30%,没有承载人或物的情况下,大概70%的油耗是因为汽车自身的质量,由此可得到结论,车身的轻量化会减少油耗,提高整车的燃料经济性。
目前轻量化技术的主要思路是:在兼顾产品性能和成本的前提下,采用轻质材料、新成型工艺并配合结构上的优化,尽可能地降低汽车产品自身重量,以达到减重、降耗、环保、安全的综合指标。
二、新材料技术1、金属材料。
(1)高强度钢。
高强钢具有强度高、质量轻、成本低等特点,而普通钢是通过减薄零件来减轻质量的,它是汽车轻量化中保证碰撞安全的最主要材料,可以说高强钢的用量直接决定了汽车轻量化的水平。
另一方面,它与轻质合金、非金属材料和复合材料相比,制造成型过程相对容易,具有经济性好的优势。
(2)铝合金的密度小(2.7g/cm3左右),仅为钢的1/3,具有良好的工艺性、防腐性、减振性、可焊性以及易回收等特点,是一种非常优良的轻量化材料。
典型的铝合金零件一次减重(传统结构件铝替钢后的减重)效果可达30%~40%,二次减重(车身重量减轻后,制动系统与悬架等零部件因负载降低而设计的减重)则可进一步提高到50%,用作结构材料替换钢铁能够带来非常显著的减重效果。
(3)镁合金。
镁的密度仅为铝的2/3,是所有结构材料中最轻的金属,具有比强度和比刚度高、容易成型加工、抗震性好等优点。
采用镁合金制造汽车零件能在应用铝合金的基础上再减轻15%〜20%,轻量化效果十分可观,但成本偏高于铝合金和钢。
2、非金属材料。
(1)塑料是重要的非金属轻量化材料,具有比重小、成本低、易于加工、耐蚀性好等特点,在汽车行业中的应用前景被看好。
(2)树脂基复合材料根据增强体和基体材料不同分为多种类型增强基复合材料,如玻璃纤维增强复合材料、碳纤维增强复合材料、生物纤维增强复合材料等。
汽车轻量化设计

汽车轻量化设计随着人们对燃料经济性和环境保护的需求不断增加,汽车轻量化设计日益成为了汽车制造业的关注焦点。
汽车轻量化设计旨在减少汽车的整体重量,从而降低能源消耗和尾气排放,并提高燃油经济性。
本文将探讨汽车轻量化设计的重要性,以及一些常见的轻量化解决方案。
1. 汽车轻量化设计的重要性汽车作为交通工具的重要组成部分,其整体质量对燃料经济性和性能起着决定性的影响。
较轻的汽车质量意味着更少的能源消耗和更低的尾气排放,同时还可以提高汽车的加速性能和操控性。
因此,汽车轻量化设计对于提高汽车的可持续性和竞争力至关重要。
2. 轻量化设计解决方案2.1 材料选择使用轻量化材料是实现汽车轻量化的一种关键方法。
例如,大量采用高强度钢材、镁合金、铝合金和碳纤维复合材料等可以有效减轻汽车自重。
这些材料可以在同时保持足够强度和刚度的情况下降低重量。
此外,新兴的材料科技,如3D打印技术和纳米材料,也为轻量化设计提供了更多可能性。
2.2 结构优化在设计汽车的整体结构时,可以通过优化结构设计,提高构件的性能并减少材料的使用量。
例如,应用先进的梁柱结构和蜂窝结构原理,可以实现更好的受力传递和分散,从而减少结构重量。
此外,采用模块化设计和共享平台等方法,可以减少冗余部件和材料的使用,进一步提高轻量化效果。
2.3 部件优化汽车的各个部件也是轻量化的关键对象。
通过技术改良和材料升级,可以降低部件的自重,从而减少整车的总重量。
例如,采用轻量化的发动机和传动系统,可以减少动力总成的质量,并提高燃油经济性。
此外,减少车身外饰件的使用和改进座椅、底盘等组件的设计,也可以有效降低汽车的整体重量。
3. 轻量化设计的挑战与前景尽管汽车轻量化设计带来了许多好处,但也存在一些挑战。
首先,轻量化设计需要在保证车辆安全性的前提下实现。
其次,新材料和结构设计可能带来额外的成本,对汽车制造厂商产生压力。
此外,材料回收和再利用也是一个重要的问题,以减少对有限资源的过度依赖。
新能源汽车车身轻量化设计理念探究

NEW ENERGY AUTOMOBILE | 新能源汽车新能源汽车车身轻量化设计理念探究刘锋江苏省盐城技师学院 江苏省盐城市 224000摘 要: 随着汽车行业的不断发展,人们对汽车行业也提出了新的要求?如何在保证质量的前提下做到节能减排成为了汽车领域里的新挑战。
很快,新能源汽车诞生,通过采用更为科学的能源与燃油系统,极大程度上降低了对环境的污染,被更多的人民群众所关注。
新能源汽车的车身设计与传统的汽车相比差别极大,因此设计过程中,需要高度重视车身的轻量化设计。
本文通过对新能源汽车车身轻量化的设计理念深入探究,提升大家对汽车车身轻量化设计的进一步了解。
关键词:新能源汽车 车身轻量化 设计理念1 引言随着人们的环保意识不断增强,日常的衣食住行方面愈发注重使用环保节能的产品。
同时,我国提倡绿色发展,为顺应时代潮流,汽车行业也是进行了很大的改革,对环保节能的理念更为重视。
我们都知道,世界各个国家的常规能源都是有限的,因此资源形势问题变得愈发严峻,新能源兼具环境保护和降低耗能的特性使得它成为汽车行业的重点发展方向。
可以说,新能源汽车的投入与推广,将大幅度推动汽车行业的能源结构转型。
但是与此相对的,新能源汽车在发展过程中也遇到了很多的难题和障碍,汽车车身的轻量化设计就是问题之一,能否有效解决这一难题,将对我国汽车行业的持续发展影响深远。
2 新能源汽车的车身轻量化设计理念从何而来早在上世纪50年代,欧洲等发达国家的汽车生产商就开始了针对汽车车身轻量化方面的研究,并取得了很大的成果。
例如,我们都知道的特斯拉电动汽车,其整体车身95%以上采用的都是铝材,铝材由于密度较小,具有很强的防腐蚀性和高寿命,即使恶劣的环境也能很好的适应,因此大大提升了汽车的整体续航能力。
我国对新能源汽车的研究虽然晚了一步,但是我们国内的汽车生产商也在努力将新能源汽车推入国内市场。
众所周知,新能源汽车在环境保护、节约资源方面有很大的优势,可以说是我国汽车行业能源结构转型的重要基石,有极其重要的战略意义和商业价值。
新能源汽车的设计理念和功能特点分析

新能源汽车的设计理念和功能特点分析
新能源汽车作为未来出行的主力军,具有很多独特的设计理念和功能特点。
以下为相关参考内容:
设计理念:
1. 环保:新能源汽车是以电、氢等新型能源为驱动力,相比传统燃油车,有着更小的环境污染和更低的能源消耗。
2. 轻量化:新能源汽车在车身材料和结构上进行了优化,以减少车重,提高能源利用率。
3. 智能化:新能源汽车加入了各种智能化技术,例如自动泊车、语音识别、人机交互等,提高用户体验。
功能特点:
1. 续航里程:新能源汽车相对于传统燃油车,最大的优势是续航里程更长,这些汽车在单次充电或氢气注入下可行驶更远的距离。
2. 能源回收:新能源汽车能够通过制动能量回收系统,将制动过程中的能量转换成电能或氢气能量,实现能源的再利用。
3. 智能充电:新能源汽车配备了智能充电系统,可以通过手机APP或智能家居连接,实现多种充电方式,方便用户进行充电。
4. 安全性:新能源汽车在安全性方面有所提升,例如采用了高强度车身材料、智能安全气囊等多种安全措施。
同时,电动车在车祸时没有燃油爆炸的风险,也能避免尾气污染。
以上是设定理念和功能特点的基本内容,当然在具体的车型和品牌中还有很多细节上的不同。
汽车十大革命设计理念

汽车十大革命设计理念
1. 绿色出行:为了应对环境污染和资源短缺,汽车设计应以绿色出行为目标,采用清洁能源和节能技术,减少尾气排放和燃料消耗。
2. 智能互联:随着信息技术的发展,汽车设计应积极采用智能互联技术,实现车辆与车辆、车辆与基础设施、车辆与用户之间的实时互联,提升安全性、便利性和舒适性。
3. 自动驾驶:自动驾驶技术是汽车设计的最前沿领域,目标是实现完全无人驾驶,提高行驶安全性和效率,减少人为操作错误和交通事故。
4. 空间优化:为了提升乘坐舒适性和储物空间利用率,汽车设计应以空间优化为首要考虑因素,包括座椅设计、储物功能布局等方面的创新。
5. 材料轻量化:为了降低车辆重量,提高燃油经济性、车辆性能和减少碳排放,汽车设计应采用轻量化材料,如高强度钢、铝合金和碳纤维复合材料等。
6. 独特外观:为了在市场竞争中脱颖而出,汽车设计应注重独特的外观造型,体现科技感、个性化和品牌特色,吸引消费者的注意力。
7. 车内舒适性:为了提升乘客的舒适感和乘坐体验,汽车设计应注重座椅设计、空调系统、噪音控制等方面的创新,提供温
馨、舒适的车内环境。
8. 安全性能:汽车设计应重视车辆的安全性能,包括主动安全和被动安全,采用先进的制动系统、防抱死系统、稳定控制系统等,减少交通事故的发生和损伤。
9. 可维修性:为了降低维修成本和提高车辆的可靠性,汽车设计应注重易维修、易保养的特点,如模块化设计、可更换部件等。
10. 可持续发展:汽车设计应符合可持续发展原则,包括资源节约、环境保护、社会责任等方面的考虑,促进汽车产业的健康发展。
汽车车身结构的轻量化设计与优化

汽车车身结构的轻量化设计与优化随着环保意识的增强和能源问题的突出,汽车工业正朝着轻量化的方向发展。
车身结构作为汽车的重要组成部分,其轻量化设计与优化具有重要意义。
本文将讨论汽车车身结构轻量化设计与优化的相关问题,并提出一些有效的方法和技术。
一、轻量化设计的必要性现今社会对环境负担越来越大,对于汽车行业而言,减少汽车自身的重量能够降低燃油消耗,并减少对环境的污染。
此外,轻量化还能提高汽车的操控性能、减少噪音和振动等,提升乘坐舒适度和安全性。
二、轻量化设计的原则1. 材料选择:在轻量化设计中,材料的选择至关重要。
高强度、高刚度、低密度的材料是首选,如高强度钢、铝合金等。
此外,也可以考虑使用轻质复合材料。
2. 结构优化:通过结构优化,可以在保持强度和刚度的前提下减少材料的使用量。
合理的结构设计和形状优化能够减少应力集中和振动问题,提高车身的整体性能。
3. 制造工艺:选择合适的制造工艺也是轻量化设计的一项重要考虑因素。
采用先进的制造方法可以降低车身的自重,并提高生产效率。
三、轻量化设计的方法与技术1. 拓扑优化:通过拓扑优化技术,可以确定出最佳的结构布局,以减少材料使用量并保持足够的强度。
拓扑优化能够帮助工程师发现车身结构中不必要的部分,从而实现轻量化设计。
2. 材料优化:根据汽车的工作环境和功能要求,针对每个部位选择最合适的材料。
通过优化材料的选择,可以达到轻量化设计的目标,同时保证车身的性能和安全性。
3. 多材料结构设计:通过将不同材料进行组合,并充分发挥各自的优势,可以实现汽车车身结构的轻量化。
例如,将铝合金与钢材进行结合,既减轻了总重量,又提高了刚度和强度。
四、轻量化设计的挑战与前景在轻量化设计过程中,还存在着一些挑战。
例如,新材料的研发和生产成本较高,制造工艺的改进和调整需要时间和经费投入。
然而,随着科技的不断进步和相关政策的支持,汽车的轻量化设计将会取得更大的突破和进展。
从长远来看,汽车车身结构的轻量化设计与优化将成为未来汽车工业的一个重要发展方向。
汽车轻量化
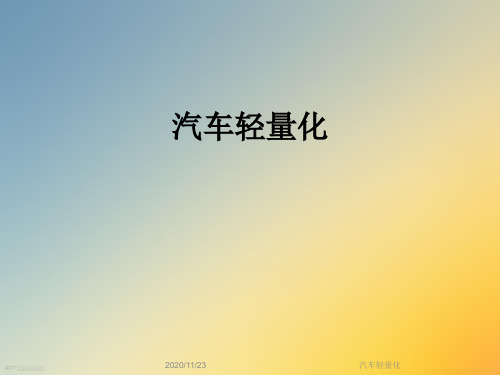
(2)改善性能
•( 2)改善性能:汽车轻量化,有利于改善汽车的行驶、 转向、加速、制动等运动性能和排气性能等多方面的 性能。其中,发动机的轻量化还可改善前轮荷重分担 率,进而改善汽车的操纵稳定性,还可为降低噪声、 振动、实现大功率化创造条件。同时还有利于减轻部 件振动和降低噪声,提高舒适性能,对于某些承载件, 其承载的重量减轻,有利于降低元件疲劳,提高耐久 性。例如一辆重量1543 kg的汽车,若车重减轻25% , 可使该车加速到60 km/h的时间从原来的10 秒减少到8 秒。
美国的新一代汽车合作项目(PNGV)
欧盟超轻车身联合研发项目(ER Collaborative R&D Project SuperLIGHT-CAR)
美国汽车材料合作项目U.S. Automotive Materials Partnership (USAMP)
新型钢车身项目New Steel Body(NBS)
亨利·福特Model T 型汽车 福特Prodigy、Jaguar new XJ 法拉利360等赛车 DaimlerChrysler Prowler 大众 3L Lupo、奥迪A2、A8 本田混合动力轿车 Insight、 NSX 均采用铝制车身
PPT文档演模板
汽车轻量化
典型的镁合金汽 车零件
PPT文档演模板
碳纤维增强聚合物基复合材料。适于制造车身和底盘零部件 减重幅度通常可达50~65% 欧盟最近采用树脂传递模塑成型(RTM)工艺成功地试制出某轿车碳纤维底板 零件的数量由28个减少到8个,重量较钢约减轻50%,而白车身的性能达到
了原钢车身水平材料 美国除低成本碳纤维制备技术开发外,还在进行碳纤维增强树脂的开发,探
索碳纤维增强塑料零部件的大规模制造工艺
基于ANSYS的汽车结构轻量化设计概要

基于ANSYS的汽车结构轻量化设计概要汽车结构轻量化设计是为了降低汽车总重量以提高燃油经济性和减少碳排放。
在设计过程中,ANSYS是一种广泛应用的工程仿真软件,可以帮助工程师进行计算分析和优化设计,以实现汽车结构轻量化的目标。
在汽车结构轻量化设计中,首先需要确定车身结构的材料选择。
传统汽车结构主要采用钢材,然而,钢材具有较高的密度,因此重量相对较大。
利用ANSYS软件,可以进行材料力学性能分析,评估不同材料的强度、刚度和耐久性等特性。
比如,在车身骨架的设计中,可以引入轻质材料如铝合金和碳纤维复合材料,通过材料对比和力学分析,选择最适合的材料,以实现轻量化目标。
其次,采用优化设计方法可以在结构设计过程中找到最优解。
通过ANSYS软件中的有限元分析功能,可以对汽车结构进行力学仿真,模拟不同载荷条件下的应力和变形。
在轻量化设计中,最常用的优化方法是拓扑优化和参数化设计。
拓扑优化是指通过改变结构的外形和材料分布,以实现最佳性能。
参数化设计是指在提供一组设计变量的基础上,通过优化算法寻找最佳设计。
这些优化方法可以帮助工程师调整结构的几何形状、材料厚度和材料分布,以减少结构重量而不影响其强度和刚度。
此外,采用多学科优化方法可以综合考虑多个设计约束和目标。
汽车结构轻量化设计需要考虑多个因素,如强度、刚度、安全性、NVH(噪音、振动和刚度)和制造成本等。
在ANSYS中,可以集成多种分析模块,如结构力学、热力学、流体力学和声学分析,以实现多学科优化。
通过综合考虑不同学科之间的相互影响,可以找到一套最优的设计方案,既满足轻量化要求,又满足其他设计约束。
最后,仿真验证是轻量化设计的关键一步。
通过将设计方案导入ANSYS软件,进行结构力学仿真,可以验证设计的效果。
这些仿真结果可以帮助工程师评估设计的可行性,并进行修改和优化。
例如,可以检查结构的强度是否满足要求,是否存在热应力和振动问题等。
通过不断优化设计方案,并进行仿真验证,可以得到最终的轻量化结构设计方案。
新能源汽车底盘轻量化设计方向
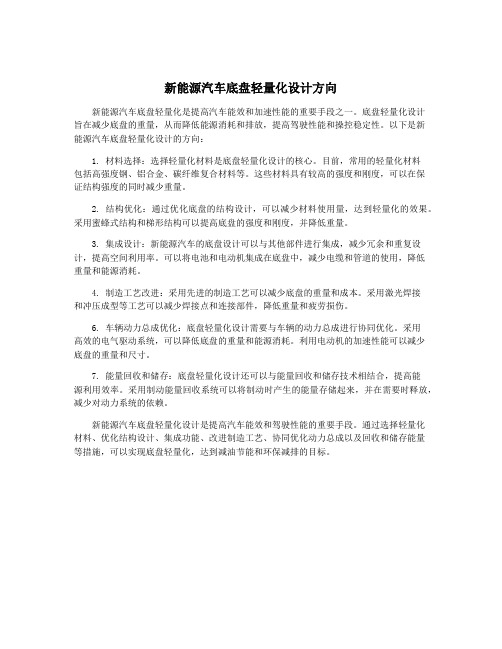
新能源汽车底盘轻量化设计方向新能源汽车底盘轻量化是提高汽车能效和加速性能的重要手段之一。
底盘轻量化设计旨在减少底盘的重量,从而降低能源消耗和排放,提高驾驶性能和操控稳定性。
以下是新能源汽车底盘轻量化设计的方向:1. 材料选择:选择轻量化材料是底盘轻量化设计的核心。
目前,常用的轻量化材料包括高强度钢、铝合金、碳纤维复合材料等。
这些材料具有较高的强度和刚度,可以在保证结构强度的同时减少重量。
2. 结构优化:通过优化底盘的结构设计,可以减少材料使用量,达到轻量化的效果。
采用蜜蜂式结构和梯形结构可以提高底盘的强度和刚度,并降低重量。
3. 集成设计:新能源汽车的底盘设计可以与其他部件进行集成,减少冗余和重复设计,提高空间利用率。
可以将电池和电动机集成在底盘中,减少电缆和管道的使用,降低重量和能源消耗。
4. 制造工艺改进:采用先进的制造工艺可以减少底盘的重量和成本。
采用激光焊接和冲压成型等工艺可以减少焊接点和连接部件,降低重量和疲劳损伤。
6. 车辆动力总成优化:底盘轻量化设计需要与车辆的动力总成进行协同优化。
采用高效的电气驱动系统,可以降低底盘的重量和能源消耗。
利用电动机的加速性能可以减少底盘的重量和尺寸。
7. 能量回收和储存:底盘轻量化设计还可以与能量回收和储存技术相结合,提高能源利用效率。
采用制动能量回收系统可以将制动时产生的能量存储起来,并在需要时释放,减少对动力系统的依赖。
新能源汽车底盘轻量化设计是提高汽车能效和驾驶性能的重要手段。
通过选择轻量化材料、优化结构设计、集成功能、改进制造工艺、协同优化动力总成以及回收和储存能量等措施,可以实现底盘轻量化,达到减油节能和环保减排的目标。
- 1、下载文档前请自行甄别文档内容的完整性,平台不提供额外的编辑、内容补充、找答案等附加服务。
- 2、"仅部分预览"的文档,不可在线预览部分如存在完整性等问题,可反馈申请退款(可完整预览的文档不适用该条件!)。
- 3、如文档侵犯您的权益,请联系客服反馈,我们会尽快为您处理(人工客服工作时间:9:00-18:30)。
i_二=!
轮罩
莎j
曩柔
字
M*
图4
2
2洼续变截面薄板技术TRB(Tailor
及整个车身的承载情况,在轧制之前选定有利丁
后续加工的板料型面。利JIICAD/CAM/CAE较 件,这种优化设计可以通过DFM/DFA(而向制造
Rolting Blanksl…
正是由于TWB突然变截面的缺点,德国亚 琛J二业大学的金届成型研究所(IMF)从1990q÷ 开始研制秉性轧制连续变截而技术。柔性轧制
Blank.
到起冲爪以{{}高材料利H{率
。l传统^焊1
Z帕产舳相比激光拼f#扳址显著的优“足减少
2010年海南省机械I。程学亡
........................。.,.............................................!!业
取得了一系列的成果,裁焊的每一块板在需要 的地方都具有专门设计的厚度,而不是使铵块扳 具有最厚区域的厚度。圈4是所示TRB在车身
车工业界近期的研究热点之一。
铝作为汽车材料有许多优点,如在满足相 同力学性能的条件下,比钢减少质量60%,且易
于回收、在碰撞过程中比钢多吸收50%的能
实现汽车的轻量化常采用两种途径:一是 结构设计优化,二是应用新型材料。前者经过 几十年的不断研究开发,日趋完善,空间已相对
狭窄。后者随着科学技术的发展和新材料的不 断涌现,为汽车轻量化开辟了广阔的发展空
2010年海南省机械工程学会
Ⅱ一109
从表5的分析结果中可以看出仅从连接点
的刚度来考虑的话,仅类焊点是完全可以取 消。但如果是作为一个完整的可行性分析却还
线性的接触情况,完善了企业的分析方式;最 后在工程方案的确定上进行了计算筛选。
要参考很多的别的工况,以及对整个白车身的 弯曲、扭转和模态的影响,综合考虑才能做下
technology development,lightweight automotive structural lightweighting design ideas.And the application
materials,technology application process to solve problems and developing direction. Key words:weight lightening;lightweighting materials;hot press forming;austenite;martensite.
铝材在汽车上的应用 铸造件
底盘系统 动力系统
横梁、上下控制臂、转向器壳、制动钳、车轮、等 发动机气缸体、气缸盖、活塞、进气歧管、水泵壳、油泵壳、滤清器底 座、正时齿轮罩盖、发动机支架、变速器壳等
其他
离合器踏板、制动踏板、转向盘、转向节等 铝材件
车身系统 热交换器系 其他系统
发动机盖板、车门、行李箱盖、地板、车身骨架及覆盖件 散热器、机油散热器、中冷器、空调冷凝器和蒸发器等 冲压车轮、座椅、保险杠、车厢地板及装饰件等
曼惫主
,啤.∥-一'☆÷
圈
矗墼■Biblioteka 崮1肯结拘材料中最轻的金属
钒轻33%
比钢铁轻75c/:
比
1 1
3塑料殛非金属复合材料
:是亡比强垭高于舒{台金和钠,比
轴科度j£复合材料是”类重要的m金属 车Ⅲ轻质材料.它木仅可减轻零部什约40c±的 质姑
刚度接近舒{台金和训,能够承受定的负茼,
具肯高度^々抗冲击rt
二是En有良好的铸造
罐以搜|{住等举部什.降12所示
\夕/\
世界范围内的35家王曼钢铁企业合作完成 了‘超轻钢喷汽车车身’(U12;AB
Light Stccl Auto Ulh'a
r零什数量_l材料消耗降低r整车重量简化 r装配T艺冈怖得到了越来越J泛的啦用, TWRfl{JT.L流稚女1l罔3昕示
Body)课题研究表明,车身
量、无需防锈处理等。随着铝合金化技术的发 展和技术进步,铝中添加镁、铬、硅等合金元素
获得高强度铝合金材料,为汽车配件的轻量化、
间。轻量化材料对汽车工业的可持续发展具有 重要意义,它不仅关系到车辆的节能、减排、安 全、成本等诸多方面,而且汽车轻量化材料的
表l
高质量化、低成本化提供了可靠依据。铝材在
汽车应用主要表现在表1所示:
结论。 6.结语 通过对某款家用轿车B连接点的刚度分 析。尝试了新的焊点模拟方式带来的便捷并也 对网格尺寸的大小进行了验证,提高了对网格
7.参考文献
[1]美国A1tair从司上海办事处。上海:宣
传资料:2007
[2】周中坚,卢耀祖。机械与汽车结构的
有限元分析。上海:同济大学出版社,1997
作者简介:第一作者:张羽翼、男、汉
问题的认识;第一次在连接点分析中考虑了非
族、湖南泪罗、1982年4月、工程师、学士
汽车轻量化设计理念
王洪印
(一汽海马汽车有限公司海口570216) 摘要:文章主要从以下三方面介绍汽车轻量化技术的应用及发展,包括轻量化材料的应用及发 展,汽车轻量化工艺技术发展,汽车结构轻量化设计思路。以及材料应用、技术运用过程当中需要
1.汽车轻量化材料应用 目前,全球中型轿车平均质量约为
1200~1400
kg,汽车发达国家力争在2015年将
中型轿车整车质量减轻到1000 kg以下,新环保
材料(材料本身具有环保性和可回收性)将扮 演愈来愈重要的角色。与减轻汽车自身质量相
对应,汽车轻量化材料用量逐年增加。新材料 的应用是实现汽车轻量化的主要途径之一。目 前,可用来减轻汽车自重的材料有两大类:一 类是高强度材料,如高强度钢和高强度不锈
利用率由柏%增加到65%。
H1扳料之问的拼接处存在着厚度的突 变这对于模具的设计和制造是一个不小的难
题。 目附.由拼焊板生产的汽车零部件主要有 前后车fJ内板、前后纵粱、伽围、底板、车f J
内侧的A、H、c立柱、轮罩、尾门内扳等.世
界知名汽车制造商奔驰、宝r5、通用等相继在
车身中采用了激光拼焊板技术。国内外一些研 究机构对拼焊板成型相关技术进行了研究,并
PVC
%
聚J氡酯
PUR
热闶性 复合村料
尼龙
聚乙烯 阼
2】
嘲外汽车的内饰什L罐奉实现翅料化如 今龌料“汽年中的Ji用范耐正在由内转件向外
装件车身结壮J什扩展.今后的审苣发展山… 足扦发结构件外装件用的增强翊料复合材
服强度为210—550 MPan々制定望为高强度钢 fHSS).脯日K强度为550 Mn的俐定义为超l岛强 度钢{IIHSS)衙先进离强度钢l^Hs‘)的屈服强
2010{F海南省#l馈『判学会
锅合金的加I难度比钢材岛,成彤性还有 待继续改善除此以外,成奉控制是未来汽车 进一步应片j*{厶金的重蚓旰究睬题。
1 1
2镁及镁台金
镁的密度仪由骨{的2,3,采门】镁制造汽车
零件的轻^}化敞果吏胜于锅,岜。r在铝减审基 础上再碱轻I s%一20% 一是E的质^}轻是所
腰介十HSS和I HSS之问的强度范阿高蝇度钢 f}有良好的低温切性、成形性和焊接阵汽车
料、高性能树脂材抖,并对材料的可同收性子
“高度关沣。从品种L看聚烯烃材料冈密度
片{钢逐步向高强度化方向发展,当_l【9板厚度分别
减少005
mm
小性能较好日成奉低.近来有把汽车内饰和
外装材料统到聚烯烽材料的趋磐因此其用 虽会有较足的增K预汁难丙烯和聚氯己烯今 后分别可侏持8%和4rh的年j口K半.策己烯的 增鹾势文也比较强劲
钢板的90%使用现已大量生产的高强度钢板 (包括高强腰、超高强度和夹崖减重钮板),
可以在不增力¨成本的前提下实现I‘身降重 25%(眦4门轿车为参照),日静态a【转刚度 提高80%,静态弯曲刚度提高52Ⅸ.第午身 结柑模舒提高58%当然+高强度钢板在车身 l’的宴惭、mHj进束达到如此高的水平。欧洲超 轻J“钠制车体的世¨中高强度牲相钢所占比
钢;另一类是轻质材料,如铝合金、镁合金、 钛合金、塑料及复合材料等。 1.1轻质材料【11 1.1.1铝及铝合金
均有改善。从安全性考虑,碰撞时陨性小,制
动距离减小。另外发生碰撞时,塑性材料对人 的冲击小得多,所以更加安全。汽车轻量化技 术是有效降低油耗、减少排放和提升安全性的
重要技术措施之一。因此,汽车轻量化成为汽
也质量已逃220 kg.【}】总用柑1]!J246%垃J△国 家々-H{蛔料现已占犟料0消耗量的7%一11%. 预“不久将达到10%一11%日前车Hj塑料居
川的原料资源。镁台金材料在^车上得到r广
泛的应州,涉驶剑的符种汽下零部件如H1所
爪
日“7位的*种与所F,比例大体见表2,
表2 聚圳希
PP
汽车-l,常用的颦料比例 聚氯乙烯
例超过S0%,还采用r约4%的机托强度达到
1200MPa和1 520MPa的超高强度马瞳体钠
卿一唧一国
2汽车轻量化工艺技术发展 21激光拼焊板技术(TailorWelded TWB) 作为汽车轻错化前要技术之一已在汽车 制造领域t'}Nt泛的咒沣和J“H{;敫光拼焊板 是将儿块小同材质、jJf}=同曙度不同涂层的铡 材nq£戍一块牲体概以满足零部件xt剌料性能 自0小问坚求也一U以把棚Id材质的等厚利料焊接
是电动汽车及混合动力新型能源汽车;二是汽
应用对世界能源、自然资源和环境具有深刻的
影响,它已成为汽车材料技术发展的主导方向。
车轻量化。无论是电动驱动还是汽油、柴油驱 动的汽车,减轻汽车本身重量是提高汽车的燃 油经济性、节约能耗、减少污染的重要措施之 一。以不影响汽车的安全性、抗振性以及舒适 性为前提,同时又能保证成本具有竞争力。一般 汽车零部件质量每减轻1%则可节油1%;运动 件质量每减轻1%贝WJ可节油2%。试验表明,汽 车质量每减轻10%,油耗下降6%~8%,排放 下降4%。另外,从驾驶方面来讲,汽车轻量 化后加速性提高,稳定性和噪声、振动方面也