电子束蒸发与磁控溅射镀铝的性能分析研究导电薄膜
真空薄膜的制备及其光学性能研究

真空薄膜的制备及其光学性能研究随着科技的发展,真空薄膜技术被广泛应用于许多领域,如电子、光学、汽车、通信等。
真空薄膜的制备和性能研究是当前研究的热点之一。
本文将介绍真空薄膜的制备方法和光学性能研究的相关内容。
一、真空薄膜制备方法真空薄膜制备的方法多样,其中最常用的方法有热蒸发、磁控溅射、电子束蒸发和离子束蒸发。
1. 热蒸发法热蒸发法是将固体材料加热到高温状态,使其蒸发并沉积在基底上形成薄膜的方法。
这是最基本的制备方法之一。
该方法适用于固体材料的制备,如氧化物、氟化物、金属和合金等。
但是该方法存在一些缺点,例如膜厚不均匀、易形成颗粒状结构和凝固速度慢等。
2. 磁控溅射法磁控溅射法是将材料靶放在真空腔室中,通过放电将靶表面的原子或离子击出到基板上生成薄膜的方法。
它具有膜厚均匀、成膜速度快和成膜选择性强等优点,适用于制备金属、混合材料和非晶体等。
3. 电子束蒸发法电子束蒸发法是将材料放在陶瓷棒中,通过高功率电子束将材料加热至蒸发点,沉积在基板上形成薄膜的方法。
该方法具有较高的成膜速度和高成膜率,适用于制备铝、铬、铜和钨等材料。
4. 离子束蒸发法离子束蒸发法是利用高能离子束直接蒸发材料,并在基底上形成薄膜的方法。
该方法通过使用高能离子束,在原材料上的束缚能变化,导致部分原子发生蒸发现象,最终在基板上形成薄膜。
该方法具有较高的成膜速度、薄膜致密度高以及合适的流行面取向等特点,适用于制备氮化物、碳化物、氧化物、砷化镓和硅等化合物。
二、真空薄膜光学性能研究真空薄膜具有良好的光学性能,对于不同领域的研究,往往需要对真空薄膜进行光学性能研究。
包括以下几个方面:1. 光学薄膜的反射率光学薄膜的反射率的研究是真空薄膜中较为重要的研究内容。
通过对光学反射薄膜的研究,可以研究光学元件的工作方式和性能,也可以研究薄膜材料的光学性能。
常用的反射率测试方法有求解测量法和显微光学反射法等。
2. 光学薄膜的透过率透过率是指光线经过薄膜后能够透过并到达反面的能量占入射光能量的比例。
磁控溅射制备ITO薄膜光电性能的研究
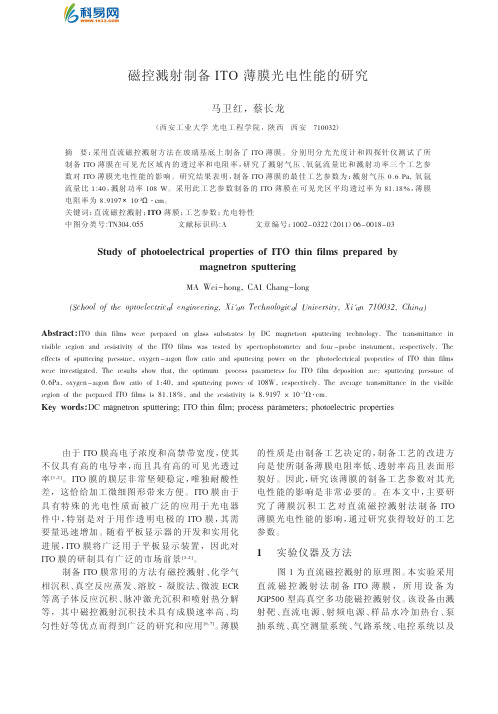
磁控溅射制备ITO薄膜光电性能的研究马卫红,蔡长龙(西安工业大学光电工程学院,陕西西安710032)摘要:采用直流磁控溅射方法在玻璃基底上制备了ITO薄膜。
分别用分光光度计和四探针仪测试了所制备ITO薄膜在可见光区域内的透过率和电阻率,研究了溅射气压、氧氩流量比和溅射功率三个工艺参数对ITO薄膜光电性能的影响。
研究结果表明,制备ITO薄膜的最佳工艺参数为:溅射气压0.6Pa,氧氩流量比1:40,溅射功率108W。
采用此工艺参数制备的ITO薄膜在可见光区平均透过率为81.18%,薄膜电阻率为8.9197×10-3Ω·cm。
关键词:直流磁控溅射;ITO薄膜;工艺参数;光电特性中图分类号:TN304.055文献标识码:A文章编号:1002-0322(2011)06-0018-03Study of photoelectrical properties of ITO thin films prepared bymagnetron sputteringMA Wei-hong,CAI Chang-long(School of the optoelectrical engineering,Xi'an Technological University,Xi'an710032,China)Abstract:ITO thin films were prepared on glass substrates by DC magnetron sputtering technology.The transmittance in visible region and resistivity of the ITO films was tested by spectrophotometer and four-probe instrument,respectively.The effects of sputtering pressure,oxygen-argon flow ratio and sputtering power on the photoelectrical properties of ITO thin films were investigated.The results show that,the optimum process parameters for ITO film deposition are:sputtering pressure of 0.6Pa,oxygen-argon flow ratio of1:40,and sputtering power of108W,respectively.The average transmittance in the visible region of the prepared ITO films is81.18%,and the resistivity is8.9197×10-3Ω·cm.Key words:DC magnetron sputtering;ITO thin film;process parameters;photoelectric properties由于ITO膜高电子浓度和高禁带宽度,使其不仅具有高的电导率,而且具有高的可见光透过率[1,2]。
磁控溅射对薄膜附着力的影响_概述及解释说明

磁控溅射对薄膜附着力的影响概述及解释说明1. 引言1.1 概述随着科学技术的不断发展,薄膜材料的制备和应用在各个领域中起到了至关重要的作用。
而通过磁控溅射技术来制备薄膜已经成为一种常见且有效的方法。
然而,薄膜的附着力是影响其性能和稳定性的关键因素之一。
因此,深入研究磁控溅射对薄膜附着力的影响机理以及优化策略具有重要意义。
1.2 文章结构本文将围绕磁控溅射技术对薄膜附着力的影响进行系统论述,并结合实验验证和数据分析,解释结果差异的原因。
具体而言,本文分为五个主要部分:引言、磁控溅射技术概述、影响薄膜附着力的因素分析、实验验证与数据分析以及结论与展望。
1.3 目的本文旨在全面阐明磁控溅射技术对于薄膜附着力方面所产生的影响,并深入探讨影响因素的机理。
通过实验验证和数据分析,我们将尽力揭示磁控溅射下薄膜附着力变化的规律,并提出优化策略。
最终,期望为相关领域的科研工作者提供有益的参考和指导,推动薄膜制备技术在更广泛的应用中发挥更大的作用。
2. 磁控溅射技术概述:2.1 原理介绍:磁控溅射技术是一种常用的物理气相沉积技术,主要用于制备薄膜材料。
其原理是在真空条件下,通过施加外加磁场和高能粒子轰击靶材表面,使得靶材中的原子或分子离开靶面并沉积在衬底上形成薄膜。
利用这种方法可以制备出均匀、致密且具有优异性能的薄膜。
2.2 工艺参数与薄膜附着力关系研究:磁控溅射工艺的参数对最终薄膜的质量和性能有很大影响。
诸如气体种类、压力、功率、溅射时间等参数都会影响到溅射过程中产生的离子束特性以及靶材表面和溅射沉积层之间的相互作用。
在进行磁控溅射时,合适选择和调节这些工艺参数可以优化沉积层的结构和性能,并且提高薄膜附着力。
2.3 典型应用领域:磁控溅射技术在许多领域有广泛应用。
其中包括但不限于光电子器件、集成电路、光学薄膜、传感器和太阳能电池等。
这种技术可以制备具有高透明性、低反射率、优异导电性以及耐腐蚀性的材料,满足不同领域对薄膜材料的需求。
反应rf磁控溅射法制备氧化铝薄膜及其介电损耗
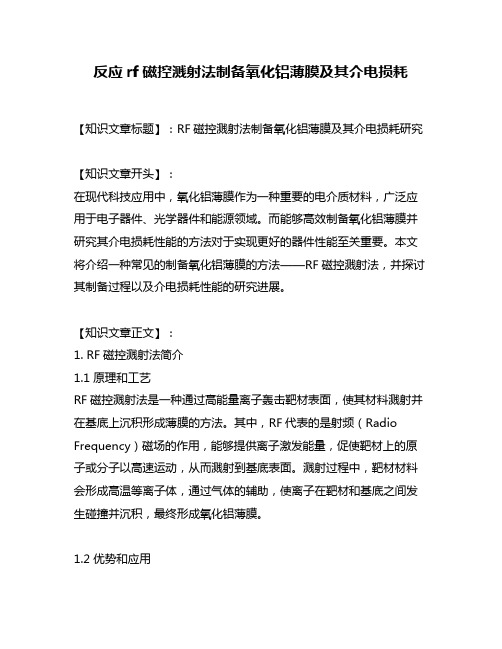
反应rf磁控溅射法制备氧化铝薄膜及其介电损耗【知识文章标题】:RF磁控溅射法制备氧化铝薄膜及其介电损耗研究【知识文章开头】:在现代科技应用中,氧化铝薄膜作为一种重要的电介质材料,广泛应用于电子器件、光学器件和能源领域。
而能够高效制备氧化铝薄膜并研究其介电损耗性能的方法对于实现更好的器件性能至关重要。
本文将介绍一种常见的制备氧化铝薄膜的方法——RF磁控溅射法,并探讨其制备过程以及介电损耗性能的研究进展。
【知识文章正文】:1. RF磁控溅射法简介1.1 原理和工艺RF磁控溅射法是一种通过高能量离子轰击靶材表面,使其材料溅射并在基底上沉积形成薄膜的方法。
其中,RF代表的是射频(Radio Frequency)磁场的作用,能够提供离子激发能量,促使靶材上的原子或分子以高速运动,从而溅射到基底表面。
溅射过程中,靶材材料会形成高温等离子体,通过气体的辅助,使离子在靶材和基底之间发生碰撞并沉积,最终形成氧化铝薄膜。
1.2 优势和应用RF磁控溅射法具有溅射速率高、薄膜致密性好、薄膜成分均匀等优点。
它也被广泛应用于氧化铝薄膜的制备,如集成电路、微电子器件、光纤器件、光学镀膜和电池等领域。
其高效的制备方法和优良的薄膜性能使得研究人员对其进行了广泛的研究。
2. 氧化铝薄膜制备与表征2.1 制备方法RF磁控溅射法制备氧化铝薄膜的关键步骤包括靶材选择、氧气流量控制、溅射功率调节以及工艺优化等。
靶材的选择对于薄膜性能至关重要,常见的靶材有纯氧化铝、铝合金等。
氧气流量的控制可以影响薄膜的氧化程度和致密性,适当的氧气流量可以提高薄膜的氧化性能。
溅射功率的调节决定了靶材离子轰击能量和溅射速率,适宜的溅射功率可以得到均匀致密的薄膜。
工艺优化则包括溅射时间、基底温度和气压等参数的选择,通过调节这些参数可以实现不同性质氧化铝薄膜的制备。
2.2 表征方法为了评估氧化铝薄膜的性能,研究人员通常采用多种表征技术进行分析。
一种常见的性能评估方法是X射线衍射(XRD)分析,可以确定薄膜的结晶性以及晶体结构。
试谈磁控溅射镀膜技术的研究及发展趋势
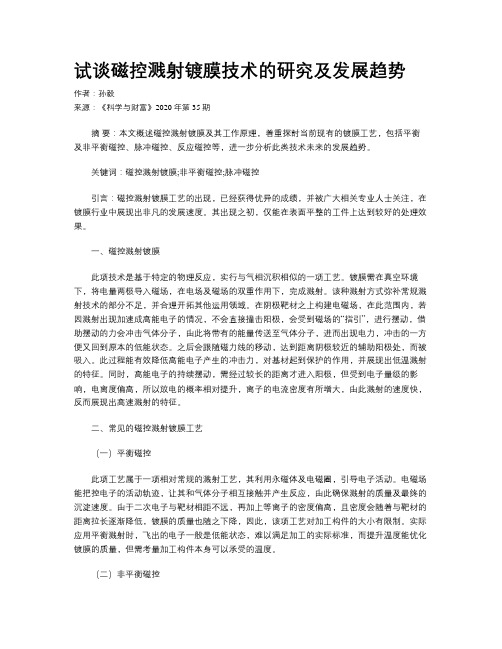
试谈磁控溅射镀膜技术的研究及发展趋势作者:孙毅来源:《科学与财富》2020年第35期摘要:本文概述磁控溅射镀膜及其工作原理,着重探討当前现有的镀膜工艺,包括平衡及非平衡磁控、脉冲磁控、反应磁控等,进一步分析此类技术未来的发展趋势。
关键词:磁控溅射镀膜;非平衡磁控;脉冲磁控引言:磁控溅射镀膜工艺的出现,已经获得优异的成绩,并被广大相关专业人士关注,在镀膜行业中展现出非凡的发展速度。
其出现之初,仅能在表面平整的工件上达到较好的处理效果。
一、磁控溅射镀膜此项技术是基于特定的物理反应,实行与气相沉积相似的一项工艺。
镀膜需在真空环境下,将电量两极导入磁场,在电场及磁场的双重作用下,完成溅射。
该种溅射方式弥补常规溅射技术的部分不足,并合理开拓其他运用领域。
在阴极靶材之上构建电磁场,在此范围内,若因溅射出现加速成高能电子的情况,不会直接撞击阳极,会受到磁场的“指引”,进行摆动,借助摆动的力会冲击气体分子,由此将带有的能量传送至气体分子,进而出现电力,冲击的一方便又回到原本的低能状态。
之后会跟随磁力线的移动,达到距离阴极较近的辅助阳极处,而被吸入。
此过程能有效降低高能电子产生的冲击力,对基材起到保护的作用,并展现出低温溅射的特征。
同时,高能电子的持续摆动,需经过较长的距离才进入阳极,但受到电子量级的影响,电离度偏高,所以放电的概率相对提升,离子的电流密度有所增大,由此溅射的速度快,反而展现出高速溅射的特征。
二、常见的磁控溅射镀膜工艺(一)平衡磁控此项工艺属于一项相对常规的溅射工艺,其利用永磁体及电磁圈,引导电子活动。
电磁场能把控电子的活动轨迹,让其和气体分子相互接触并产生反应,由此确保溅射的质量及最终的沉淀速度。
由于二次电子与靶材相距不远,再加上等离子的密度偏高,且密度会随着与靶材的距离拉长逐渐降低,镀膜的质量也随之下降,因此,该项工艺对加工构件的大小有限制。
实际应用平衡溅射时,飞出的电子一般是低能状态,难以满足加工的实际标准,而提升温度能优化镀膜的质量,但需考量加工构件本身可以承受的温度。
反应rf磁控溅射法制备氧化铝薄膜及其介电损耗

一、介绍:rf磁控溅射法制备氧化铝薄膜及其介电损耗在材料研究领域,氧化铝薄膜的制备及其介电性能一直是一个备受关注的课题。
而rf磁控溅射法作为一种常用的制备方法,对于氧化铝薄膜的制备具有重要意义。
介电性能作为一种重要的材料性能指标,也对氧化铝薄膜的应用具有重要影响。
二、rf磁控溅射法制备氧化铝薄膜的步骤1. 材料准备:首先需要准备高纯度的氧化铝靶材和基底材料。
2. 溅射工艺:通过rf电源和磁场的作用,将氧化铝靶材表面的原子溅射到基底材料上,形成氧化铝薄膜。
3. 处理工艺:对溅射薄膜进行退火、晶化等处理,以提高薄膜的结晶度和致密性。
三、rf磁控溅射法制备氧化铝薄膜的特点1. 高纯度:使用高纯度的氧化铝靶材和精密的溅射工艺,可以得到高纯度、低缺陷的氧化铝薄膜。
2. 薄膜致密性好:由于溅射工艺的特性,制备出的氧化铝薄膜致密性好,具有良好的机械性能和耐腐蚀性。
3. 薄膜厚度可控:通过调节溅射工艺的参数,可以实现对氧化铝薄膜的厚度精确控制。
四、rf磁控溅射法制备氧化铝薄膜的介电损耗在实际应用中,氧化铝薄膜的介电损耗是一个重要的性能指标。
rf磁控溅射法制备的氧化铝薄膜,由于其致密性好、结晶度高等特点,具有较低的介电损耗。
通过控制溅射工艺参数和薄膜后处理工艺,还可以进一步降低氧化铝薄膜的介电损耗,提高其在电子器件、光学器件等领域的应用性能。
五、结论rf磁控溅射法制备的氧化铝薄膜具有高纯度、致密性好、厚度可控等特点,在介电损耗方面表现出良好的性能。
在实际应用中具有广阔的应用前景。
随着材料制备技术的不断进步,相信rf磁控溅射法制备的氧化铝薄膜将在电子、光学等领域发挥重要作用。
个人观点我认为,rf磁控溅射法制备的氧化铝薄膜在介电损耗方面具有潜力,但在实际应用中还需要进一步研究和优化,以满足不同领域的需求。
希望未来能够有更多的研究投入到这一领域,推动氧化铝薄膜技术的发展,为电子、光学器件等领域的发展贡献更多的可能性。
在撰写本文的过程中,我对rf磁控溅射法制备氧化铝薄膜及其介电损耗有了更深入的理解。
薄膜磁控溅射实验报告(3篇)
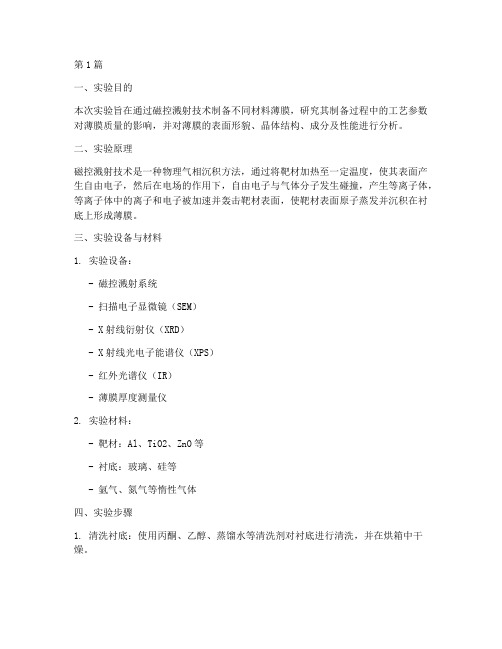
第1篇一、实验目的本次实验旨在通过磁控溅射技术制备不同材料薄膜,研究其制备过程中的工艺参数对薄膜质量的影响,并对薄膜的表面形貌、晶体结构、成分及性能进行分析。
二、实验原理磁控溅射技术是一种物理气相沉积方法,通过将靶材加热至一定温度,使其表面产生自由电子,然后在电场的作用下,自由电子与气体分子发生碰撞,产生等离子体,等离子体中的离子和电子被加速并轰击靶材表面,使靶材表面原子蒸发并沉积在衬底上形成薄膜。
三、实验设备与材料1. 实验设备:- 磁控溅射系统- 扫描电子显微镜(SEM)- X射线衍射仪(XRD)- X射线光电子能谱仪(XPS)- 红外光谱仪(IR)- 薄膜厚度测量仪2. 实验材料:- 靶材:Al、TiO2、ZnO等- 衬底:玻璃、硅等- 氩气、氮气等惰性气体四、实验步骤1. 清洗衬底:使用丙酮、乙醇、蒸馏水等清洗剂对衬底进行清洗,并在烘箱中干燥。
2. 装置准备:将靶材安装在磁控溅射系统上,设置靶材与衬底的距离、溅射气压、溅射时间等参数。
3. 磁控溅射:启动磁控溅射系统,进行溅射实验,制备薄膜。
4. 薄膜性能测试:使用SEM、XRD、XPS、IR等设备对薄膜的表面形貌、晶体结构、成分及性能进行分析。
五、实验结果与分析1. 薄膜表面形貌:SEM结果表明,Al、TiO2、ZnO等薄膜表面均匀,无明显缺陷。
2. 晶体结构:XRD分析表明,薄膜具有良好的晶体结构,晶粒尺寸较小。
3. 成分分析:XPS结果表明,薄膜中各元素含量符合预期。
4. 薄膜性能:- 硬度:Al、TiO2、ZnO等薄膜的硬度较高,具有良好的耐磨性能。
- 导电性:Al薄膜具有良好的导电性,适用于电子器件。
- 介电性能:TiO2、ZnO等薄膜具有良好的介电性能,适用于电容器等器件。
六、实验讨论1. 溅射气压对薄膜质量的影响:溅射气压越高,薄膜密度越大,晶粒尺寸越小,但溅射气压过高会导致薄膜表面出现缺陷。
2. 溅射时间对薄膜质量的影响:溅射时间越长,薄膜厚度越大,但溅射时间过长会导致薄膜内部应力增大,影响薄膜性能。
电子束蒸发与磁控溅射镀铝的性能分析研究

电子束蒸发与磁控溅射镀铝的性能分析研究随着科学技术的不断发展,半导体器件的种类不断增多。
原始点接触晶体管、合金晶体管、合金扩散晶体管、台面晶体管、硅平面晶体管、TTL集成电路和N沟硅栅平面MOS集成电路等,其制造工艺及工艺之间的各道工序也有所差别。
在硅平面晶体管工艺过程中,电极材料的制备技术是一项关键工艺,典型的制备技术主要有两类:一类是电子束蒸发镀膜技术,另一类是磁控溅射镀膜方法。
长期以来,在生产实践中由于电了束蒸发与磁控溅射这两种方法制备晶体管微电极各具优势,而且各自采用的设备和工艺不同,因而其产品质量孰优孰次一直存在争论。
本文就这一问题展开研究,详细分析了常用电极材料Al通过这两种方法制备成薄膜电极的膜厚控制、附着力、致密性、电导率和折射率等重要性能指标,测试结果分析表明磁控溅射铝膜的综合性能优于电子束蒸发。
1实验设备及优化工艺参数1.1电子束蒸发设备及优化工艺参数选用CHA-600型电子束蒸发台。
它主要由真空镀膜室、真空系统和真空测量仪器的一部分构成。
真空镀膜室主要由钟罩、球面行星转动基片架、基片烘烤装置、磁偏转电子枪、蒸发档板及加热装置等构件所组成;真空系统主要由机械泵的冷凝泵组成,选用冷凝泵可以更容易地抽到高真空状态,避免了油扩散泵返油而产生污染真空室的现象;用离子规来测量真空度。
坩埚选用石墨坩埚,避免了坩埚与Al反应生成化合物而污染Al膜,坩埚的位置处在行星架的球心位置,从而保证成膜厚度的均匀性。
蒸镀过程中膜厚的测量选用石英晶体膜厚监控仪。
电子束蒸发镀Al的典型工艺参数为:真空度:2.6×10-4Pa;蒸发速率:20—25A/s;基片温度:120°C;蒸距:45cm;蒸发时间:25min;电子枪电压:9Kv;电子枪电流:0.2A。
1.2溅射设备及优化工艺参数选用ILC-1012MARKⅡ1012溅射装置;操作简单,并能保证产品质量的均一性。
此溅射台主要由片盒卸室SL,片盒交换室TL,清洗室CL和溅射成膜室SP组成。
磁控溅射镀膜实验报告..doc

磁控溅射镀膜实验报告..doc
本次实验的目的是磁控溅射镀膜技术在材料科学中的应用,通过对磁控溅射镀膜过程的研究,探究其原理,并对所得到的薄膜进行分析。
一、实验步骤
1.将不同材料的基片放入溅射室中。
2.通过高频电源将气体放入溅射室中。
3.通过磁控电源产生磁场,使气体被激发。
4.激发后的气体离子在磁场作用下,被加速与基片的表面相撞,形成薄膜。
5.取出薄膜进行表面形貌、成分和结构的分析。
二、实验结果
本次实验我们选取了铜、铁和碳三种材料进行磁控溅射镀膜实验,得到了三组薄膜。
通过扫描电镜、X射线衍射仪、场发射扫描电子显微镜等手段对其进行了分析。
1.铜薄膜:表面均匀光滑,没有明显的颗粒,厚度在几十纳米。
2.铁薄膜:表面呈现网状结构,均匀分布的圆形颗粒,颗粒直径约为100纳米,厚度在50纳米左右。
3.碳薄膜:表面比较光滑,无明显纹路和颗粒,但是颜色比较暗,黑色。
通过X射线衍射实验,铜和铁薄膜的晶体结构比较完善,而碳薄膜由于其非晶结构,无法通过X射线衍射仪观察到其晶体形态。
另外,通过场发射扫描电子显微镜对样品进行表面成分分析,我们发现铜薄膜表面主要是铜元素,铁薄膜表面主要是铁元素,碳薄膜表面主要是碳元素。
三、经验总结
1.磁控溅射镀膜技术是一种高端的材料制备方法,具有良好的制备效果和广泛的应用前景。
2.制备薄膜的品质取决于材料本身的质量和处理工艺。
3.通过对薄膜的表面形貌、成分和结构的分析,可以更好的了解样品的特性和有效性。
4.在实验中,操作人员需要熟悉实验设备的操作规程,正确使用实验设备并遵守实验安全规范。
磁控溅射法制备ITO膜的研究
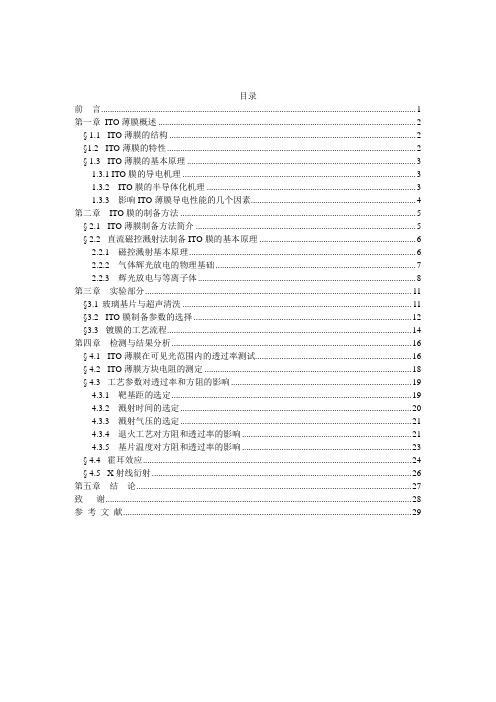
目录前言 (1)第一章ITO薄膜概述 (2)§1.1ITO薄膜的结构 (2)§1.2ITO薄膜的特性 (2)§1.3ITO薄膜的基本原理 (3)1.3.1 ITO膜的导电机理 (3)1.3.2 ITO膜的半导体化机理 (3)1.3.3 影响ITO薄膜导电性能的几个因素 (4)第二章ITO膜的制备方法 (5)§2.1ITO薄膜制备方法简介 (5)§2.2直流磁控溅射法制备ITO膜的基本原理 (6)2.2.1 磁控溅射基本原理 (6)2.2.2 气体辉光放电的物理基础 (7)2.2.3 辉光放电与等离子体 (8)第三章实验部分 (11)§3.1玻璃基片与超声清洗 (11)§3.2ITO膜制备参数的选择 (12)§3.3镀膜的工艺流程 (14)第四章检测与结果分析 (16)§4.1ITO薄膜在可见光范围内的透过率测试 (16)§4.2ITO薄膜方块电阻的测定 (18)§4.3工艺参数对透过率和方阻的影响 (19)4.3.1 靶基距的选定 (19)4.3.2 溅射时间的选定 (20)4.3.3 溅射气压的选定 (21)4.3.4 退火工艺对方阻和透过率的影响 (21)4.3.5 基片温度对方阻和透过率的影响 (23)§4.4霍耳效应 (24)§4.5X射线衍射 (26)第五章结论 (27)致谢 (28)参考文献 (29)磁控溅射法制备ITO膜的研究 1 磁控溅射法制备ITO膜的研究前言19世纪末,透明导电薄膜材料的研究刚刚起步,当时是在光电导的材料上获得很薄的金属薄膜。
经历一段很长时间后的第二次世界大战期间,关于透明导电材料的研究才进入一个新的时期,于是开发了由宽禁带的n型简并半导体SnO2材料,主要应用于飞机的除冰窗户玻璃。
在1950年,第二种透明半导体氧化物In2O3首次被制成,特别是在In2O3里掺入锡以后,使这种材料(掺锡氧化铟,即Indium Tin Oxide,简称ITO)在透明导电薄膜方面得到了普遍的应用,锡掺杂的氧化铟(ITO)透明导电膜是一种重要的光电信息材料,优良的光电特性使其在太阳电池、液晶显示器、热反射镜等领域得到广泛的应用。
磁控溅射制备al2o3薄膜及耐蚀性能研究

[]
对薄膜致 密 度 有 显 著 影 响。 H.
Kaka
t
i等 人 8 应 用 射
DOI:
10.
3969/
.
s
sn.
1001
9731.
2020.
02.
035
ji
基于此,采 用 直 流 磁 控 溅 射 镀 膜 技 术 在 不 同 溅 射
功率下(
60,
90,
液相沉积法 等 [3,4]。不 同 的 制 备 方 法 沉 积 的 薄 膜 在 致
密程度、膜基结 合 力 和 耐 腐 蚀 性 能 方 面 有 着 很 大 的 差
异,可制备出表面光滑、膜层致密和耐腐蚀性能优异的
Al2O3 薄膜一直 是 研 究 重 点,而 磁 控 溅 射 法 由 于 溅 射
速率高和 基 材 升 温 低 的 特 点 成 为 高 效 高 质 量 Al2O3
薄膜的常用制备方法。
[ ,]
O.
Zywi
t
zk
i5 6 利 用 脉 冲 反 应 双 极 磁 控 溅 射 在 不
锈钢基体制备 Al2O3 薄 膜,发 现 基 底 温 度 升 高 所 沉 积
的 Al2O3 薄 膜 晶 态 成 分 随 之 不 断 增 加。 K.
Ko
sk
i等
人 [7]采用直流磁控溅射技术在不同基底上 制 备 Al2O3
(
60,
90,
120,
150 和180 W)沉积 Al2O3 薄膜。采用 X 射线衍射仪(
XRD)和扫描电子显微镜(
SEM)对薄膜晶体结
构和表面形貌进行分析表征,使用 电 化 学 工 作 站 考 察 Al2O3 薄 膜 的 耐 蚀 性 能。 结 果 表 明:所 制 备 的 Al2O3 薄 膜
电子束蒸发与磁控溅射制备AI/PI复合薄膜的性能研究

薄膜的蒸镀 。磁控溅射主要是利用辉 光放 电将 A r
收 稿 日期 :20 — 3 2 080— 5
基金项 目:国防基础科研 项 目( 0 2 0 1 3 ) B 9 0 6 3 7 ,济南市科技攻关项 目(6 0 2 0 51 ) 作者简介:余凤斌 ,男 ,1 8 9 2年生 ,硕士 ,山东天诺 光电材料有限公 司研发部 ,山东 济南 2 0 0 ,电话 :0 5— 3 84 1 511 1 86 1 12
样 也 严重 影 响 A 膜 的 电学 性 能 。根据 工 艺参 数 , l 所 制 备 的一 批试 样 经测 试 ,溅 射 A 薄 膜 的平 均 厚 l 度 是 0 1 ± .0 m,蒸 发镀 A 薄 膜 的平 均 厚 度 . 8 0 1m 0 0 l 是 00 8 003m .1 ± . m,由此可 见溅射 铝膜 的厚 度均 匀 0
维普资讯
22 溅射镀膜及 工艺参数 -
采用 自制 的溅射设 备 ,该设 备主要 由溅 射室 和卷绕室组成 ,所 有操作过程都是 在这两个室 中
完 成 的 ,避免 了空气 和杂 质 的污染 ,能 够 获得 高质 量 的膜层 。磁控溅 射镀 A 的典型工 艺参数 为 :本底 l
也一 直存 在争议 。本实验针对这一问题进行研究 ,
分 别 采 用 电子束 蒸 发镀 膜 及磁 控 溅 射镀 膜 两种 方 法 在 P 膜 基 材 上制 备 了 A 反射 膜 材 料 ,分 别 记 为 样 I 1 品 1、样 品 2,并 对 其 表 面 形 貌 、膜 厚 、附 着 力 、 反 射率 、电导 率等 重要 性 能指标 进行 表 征 。
磁控溅射法制备薄膜材料综述

磁控溅射法制备薄膜材料综述材料化学张召举摘要薄膜材料的厚度是从纳米级到微米级,具有尺寸效应,在国防、通讯、航空、航天、电子工业等领域有着广泛应用,其有多种制造方法,目前使用较多的是溅射法,其中磁控溅射的应用较为广泛。
本文主要介绍了磁控溅射法的原理、特点,以及制备过程中基片温度、溅射功率、溅射气压和溅射时间等工艺条件对所制备薄膜性能的影响。
关键字磁控溅射;原理;工艺条件;影响正文薄膜是指尺度在某个一维方向远远小于其他二维方向,厚度可从纳米级到微米级的材料,由于薄膜的尺度效应,它表现出与块体材料不同的物理性质,有广泛应用。
薄膜的制备大致可分为物理方法和化学方法两大类。
物理方法主要包括各种不同加热方式的蒸发,溅射法等,化学方法则包括各种化学气相沉积(CVD)、溶胶-凝胶法(sol-gel)等。
溅射沉积法由于速率快、均一性好、与基片附着力强、比较容易控制化学剂量比及膜厚等优点,成为制备薄膜的重要手段。
溅射法根据激发溅射离子和沉积薄膜方式的不同又分直流溅射、离子溅射、射频溅射和磁控溅射,目前多用后两种。
本文主要介绍磁控溅射制备薄膜材料的原理及影响因素。
磁控溅射是70年代迅速发展起来的新型溅射技术,目前已在工业生产中实际应用。
这是由于磁控溅射的镀膜速率与二极溅射相比提高了一个数量级。
具有高速、低温、低损伤等优点。
高速是指沉积速率快;低温和低损伤是指基片的温升低、对膜层的损伤小。
1974年Chapin发明了适用于工业应用的平面磁控溅射靶,对进人生产领域起了推动作用。
磁控溅射基本原理磁控溅射是20世纪70年代迅速发展起来的一种高速溅射技术。
对许多材料,利用磁控溅射的方式溅射速率达到了电子术蒸发的水平,而且在溅射金属时还可避免二次电子轰击而使基板保持冷态,这对使用怕受温度影响的材料作为薄膜沉积的基板具有重要意义。
磁控溅射是在磁场控制下的产生辉光放电,在溅射室内加上与电场垂直的正交磁场,以磁场来改变电子的运动方向,电子的运动被限制在一定空间内,增加了同工作气体分子的碰撞几率,提高了电子的电离效率。
强磁场对真空蒸发薄膜生长的影响研究
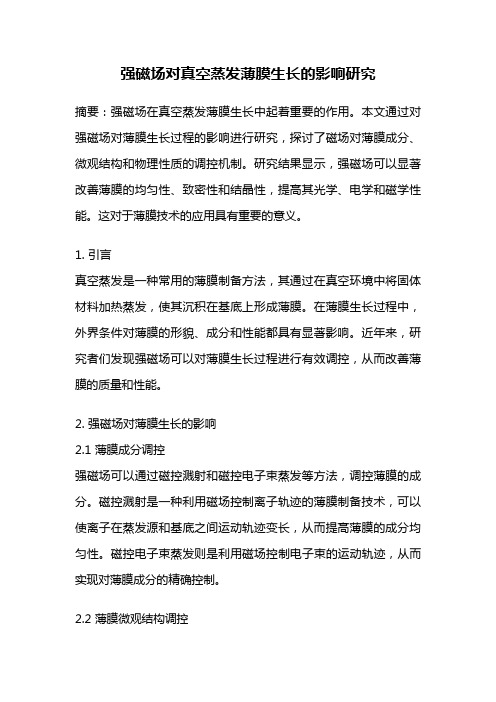
强磁场对真空蒸发薄膜生长的影响研究摘要:强磁场在真空蒸发薄膜生长中起着重要的作用。
本文通过对强磁场对薄膜生长过程的影响进行研究,探讨了磁场对薄膜成分、微观结构和物理性质的调控机制。
研究结果显示,强磁场可以显著改善薄膜的均匀性、致密性和结晶性,提高其光学、电学和磁学性能。
这对于薄膜技术的应用具有重要的意义。
1. 引言真空蒸发是一种常用的薄膜制备方法,其通过在真空环境中将固体材料加热蒸发,使其沉积在基底上形成薄膜。
在薄膜生长过程中,外界条件对薄膜的形貌、成分和性能都具有显著影响。
近年来,研究者们发现强磁场可以对薄膜生长过程进行有效调控,从而改善薄膜的质量和性能。
2. 强磁场对薄膜生长的影响2.1 薄膜成分调控强磁场可以通过磁控溅射和磁控电子束蒸发等方法,调控薄膜的成分。
磁控溅射是一种利用磁场控制离子轨迹的薄膜制备技术,可以使离子在蒸发源和基底之间运动轨迹变长,从而提高薄膜的成分均匀性。
磁控电子束蒸发则是利用磁场控制电子束的运动轨迹,从而实现对薄膜成分的精确控制。
2.2 薄膜微观结构调控强磁场可以改变薄膜的微观结构,提高其致密性和结晶性。
磁场可以对蒸发源中的原子或分子进行定向控制,使其以更高的能量和速度沉积在基底上,从而形成致密的薄膜结构。
同时,磁场还可以通过改变蒸发源中的原子或分子的振动状态,促进晶体的生长,提高薄膜的结晶度。
2.3 薄膜物理性质调控强磁场对薄膜的物理性质也具有显著影响。
研究发现,强磁场可以改变薄膜的光学、电学和磁学性能。
磁场可以改变薄膜中的电子结构,从而调控其光学吸收、折射和透射等性质。
同时,磁场还可以调控薄膜中的电子输运行为,改变其电导率和载流子浓度。
此外,磁场还可以改变薄膜中的磁性行为,如调控磁畴结构、磁矩取向等。
3. 强磁场调控薄膜生长的机制强磁场调控薄膜生长的机制主要包括离子轨迹控制、原子或分子能量调控和晶体生长控制等方面。
磁场可以通过对离子轨迹的控制,实现薄膜成分的均匀沉积。
磁控溅射法制备薄膜材料实验报告
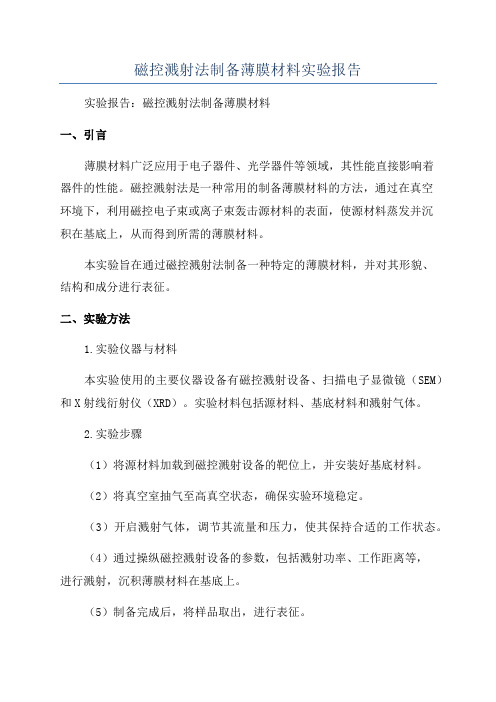
磁控溅射法制备薄膜材料实验报告实验报告:磁控溅射法制备薄膜材料一、引言薄膜材料广泛应用于电子器件、光学器件等领域,其性能直接影响着器件的性能。
磁控溅射法是一种常用的制备薄膜材料的方法,通过在真空环境下,利用磁控电子束或离子束轰击源材料的表面,使源材料蒸发并沉积在基底上,从而得到所需的薄膜材料。
本实验旨在通过磁控溅射法制备一种特定的薄膜材料,并对其形貌、结构和成分进行表征。
二、实验方法1.实验仪器与材料本实验使用的主要仪器设备有磁控溅射设备、扫描电子显微镜(SEM)和X射线衍射仪(XRD)。
实验材料包括源材料、基底材料和溅射气体。
2.实验步骤(1)将源材料加载到磁控溅射设备的靶位上,并安装好基底材料。
(2)将真空室抽气至高真空状态,确保实验环境稳定。
(3)开启溅射气体,调节其流量和压力,使其保持合适的工作状态。
(4)通过操纵磁控溅射设备的参数,包括溅射功率、工作距离等,进行溅射,沉积薄膜材料在基底上。
(5)制备完成后,将样品取出,进行表征。
三、实验结果与分析通过SEM观察,薄膜材料的表面形貌均匀,没有明显的颗粒和裂纹,呈现出光滑的特点。
通过透射电子显微镜(TEM)的观察,薄膜材料的厚度约为100 nm,呈现出均匀的结构。
通过XRD分析,薄膜材料的晶体结构为立方晶系,晶面取向较好。
通过对XRD图谱的解析,还可以得到薄膜材料的晶格常数、晶粒大小等信息。
通过能谱仪的分析,可以确定薄膜材料的成分。
实验结果显示,制备的薄膜材料主要由目标材料的原子组成,没有掺杂物的存在。
四、讨论与改进通过磁控溅射法制备的薄膜材料,表面形貌均匀且结构良好,符合预期需求。
但是,在实验过程中,我们发现了一些问题,如薄膜材料的制备速率较慢、材料的含气量较高等。
为了解决这些问题,我们可以在实验过程中进行参数的优化,如调节溅射功率、溅射时间等,以提高制备速率;同时可以加入适量的氩气来降低材料的含气量。
此外,在薄膜材料的表征上,我们只是使用了SEM、XRD和能谱仪等仪器进行了一些基本的表征,对于材料的电学、光学等特性并没有进行深入的研究。
电子束蒸发镀膜
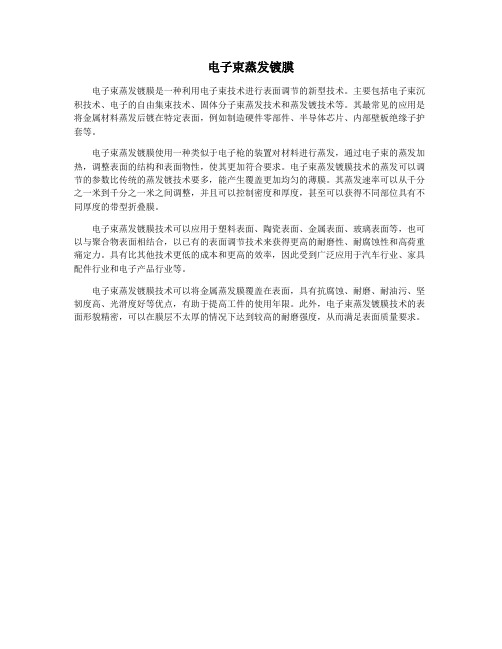
电子束蒸发镀膜
电子束蒸发镀膜是一种利用电子束技术进行表面调节的新型技术。
主要包括电子束沉积技术、电子的自由集束技术、固体分子束蒸发技术和蒸发镀技术等。
其最常见的应用是将金属材料蒸发后镀在特定表面,例如制造硬件零部件、半导体芯片、内部壁板绝缘子护套等。
电子束蒸发镀膜使用一种类似于电子枪的装置对材料进行蒸发,通过电子束的蒸发加热,调整表面的结构和表面物性,使其更加符合要求。
电子束蒸发镀膜技术的蒸发可以调节的参数比传统的蒸发镀技术要多,能产生覆盖更加均匀的薄膜。
其蒸发速率可以从千分之一米到千分之一米之间调整,并且可以控制密度和厚度,甚至可以获得不同部位具有不同厚度的带型折叠膜。
电子束蒸发镀膜技术可以应用于塑料表面、陶瓷表面、金属表面、玻璃表面等,也可以与聚合物表面相结合,以已有的表面调节技术来获得更高的耐磨性、耐腐蚀性和高荷重痛定力。
具有比其他技术更低的成本和更高的效率,因此受到广泛应用于汽车行业、家具配件行业和电子产品行业等。
电子束蒸发镀膜技术可以将金属蒸发膜覆盖在表面,具有抗腐蚀、耐磨、耐油污、坚韧度高、光滑度好等优点,有助于提高工件的使用年限。
此外,电子束蒸发镀膜技术的表面形貌精密,可以在膜层不太厚的情况下达到较高的耐磨强度,从而满足表面质量要求。
磁控溅射法制备ITO膜的研究

磁控溅射法制备ITO膜的研究ITO膜是一种透明导电薄膜,具有良好的电导率和光透过性。
它在太阳能电池、液晶显示、触摸屏等领域有着广泛的应用。
本文将研究磁控溅射法制备ITO膜的工艺过程、影响因素和优化方法。
磁控溅射法是一种常用的薄膜制备方法,它利用磁场控制离子在目标表面的沉积,通过高能粒子轰击和扩散,形成均匀致密的薄膜。
在ITO膜的制备中,通常使用靶材为含有ITO的铟锡合金,沉积气体为氩气或氩气与氧气的混合物。
研究表明,ITO膜的制备工艺参数对薄膜的电学和光学性能有着重要影响。
其中,沉积速率是一个关键参数,它与工艺中的离子能量、靶材的离子通量和沉积时间有关。
较高的沉积速率可以提高生产效率,但可能导致薄膜内部应力增大和晶体结构退化。
另外,氧气流量也是一个重要参数,它可以调节薄膜的电学性能。
适量的氧气流量可以形成ITO膜中的氧化物相,提高膜的导电性能。
然而,过高或过低的氧气流量都会导致薄膜电学性能下降。
此外,靶材的成分和纯度也对ITO膜的性能有着显著影响。
铟锡合金中铟的含量和靶材的纯度对薄膜的导电性能和透过率有着直接影响。
近年来,一些研究还表明,掺杂其他金属元素或添加改性剂可以提高ITO膜的导电性能和稳定性。
在优化磁控溅射法制备ITO膜的工艺中,需要综合考虑薄膜的电学、光学和力学性能。
适当的沉积速率、氧气流量和靶材成分可以获得具有较低电阻率和较高透过率的ITO膜。
此外,精密控制膜的厚度和表面形貌也是提高膜性能的重要因素。
总之,磁控溅射法是一种常用的ITO膜制备方法,通过调节工艺参数和优化靶材成分可以获得良好的薄膜性能。
进一步研究磁控溅射法制备ITO膜的工艺过程和优化方法,将有助于实现ITO膜的高效制备和应用。
实验4磁控溅射法制备薄膜材料资料讲解
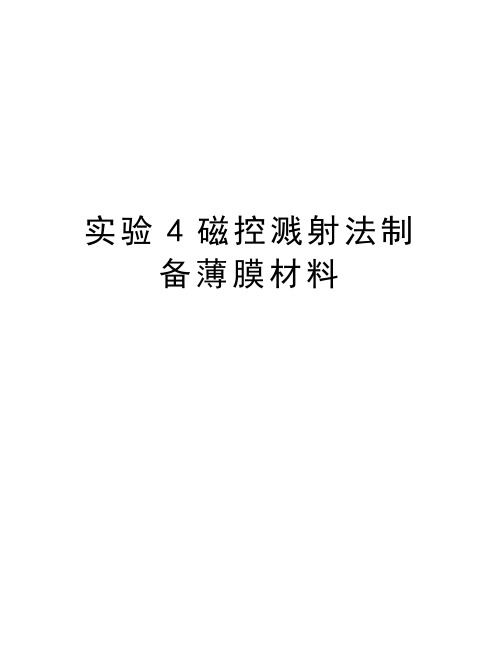
实验4磁控溅射法制备薄膜材料实验4 磁控溅射法制备薄膜材料一、实验目的1. 掌握真空的获得2. 掌握磁控溅射法的基本原理与使用方法3. 掌握利用磁控溅射法制备薄膜材料的方法二、实验原理磁控溅射属于辉光放电范畴,利用阴极溅射原理进行镀膜。
膜层粒子来源于辉光放电中,氩离子对阴极靶材产生的阴极溅射作用。
氩离子将靶材原子溅射下来后,沉积到元件表面形成所需膜层。
磁控原理就是采用正交电磁场的特殊分布控制电场中的电子运动轨迹,使得电子在正交电磁场中变成了摆线运动,因而大大增加了与气体分子碰撞的几率。
用高能粒子(大多数是由电场加速的气体正离子)撞击固体表面(靶),使固体原子(分子)从表面射出的现象称为溅射。
1. 辉光放电:辉光放电是在稀薄气体中,两个电极之间加上电压时产生的一种气体放电现象。
溅射镀膜基于荷能离子轰击靶材时的溅射效应,而整个溅射过程都是建立在辉光放电的基础之上的,即溅射离子都来源于气体放电。
不同的溅射技术所采用的辉光放电方式有所不同,直流二极溅射利用的是直流辉光放电,磁控溅射是利用环状磁场控制下的辉光放电。
如图1(a)所示为一个直流气体放电体系,在阴阳两极之间由电动势为的直流电源提供电压和电流,并以电阻作为限流电阻。
在电路中,各参数之间应满足下述关系:V=E-IR使真空容器中Ar气的压力保持一定,并逐渐提高两个电极之间的电压。
在开始时,电极之间几乎没有电流通过,因为这时气体原子大多仍处于中性状态,只有极少量的电离粒子在电场的作用下做定向运动,形成极为微弱的电流,即图(b)中曲线的开始阶段所示的那样。
图1 直流气体放电随着电压逐渐地升高,电离粒子的运动速度也随之加快,即电流随电压上升而增加。
当这部分电离粒子的速度达到饱和时,电流不再随电压升高而增加。
此时,电流达到了一个饱和值(对应于图曲线的第一个垂直段)。
当电压继续升高时,离子与阴极之间以及电子与气体分子之间的碰撞变得重要起来。
在碰撞趋于频繁的同时,外电路转移给电子与离子的能量也在逐渐增加。
蒸发镀铝 和磁控溅射镀铝
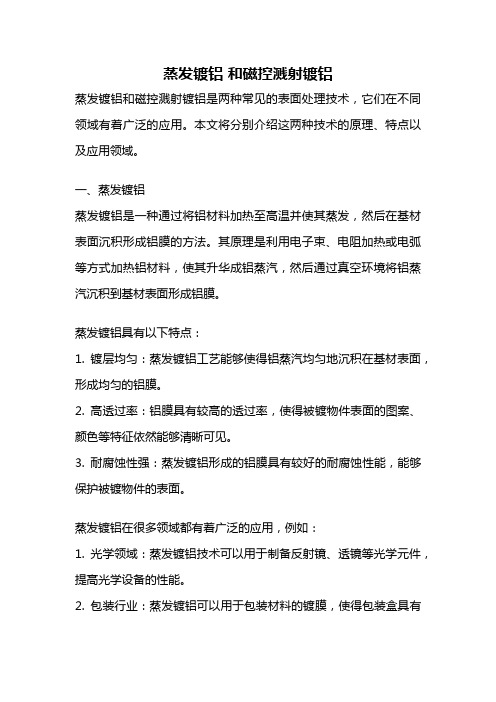
蒸发镀铝和磁控溅射镀铝蒸发镀铝和磁控溅射镀铝是两种常见的表面处理技术,它们在不同领域有着广泛的应用。
本文将分别介绍这两种技术的原理、特点以及应用领域。
一、蒸发镀铝蒸发镀铝是一种通过将铝材料加热至高温并使其蒸发,然后在基材表面沉积形成铝膜的方法。
其原理是利用电子束、电阻加热或电弧等方式加热铝材料,使其升华成铝蒸汽,然后通过真空环境将铝蒸汽沉积到基材表面形成铝膜。
蒸发镀铝具有以下特点:1. 镀层均匀:蒸发镀铝工艺能够使得铝蒸汽均匀地沉积在基材表面,形成均匀的铝膜。
2. 高透过率:铝膜具有较高的透过率,使得被镀物件表面的图案、颜色等特征依然能够清晰可见。
3. 耐腐蚀性强:蒸发镀铝形成的铝膜具有较好的耐腐蚀性能,能够保护被镀物件的表面。
蒸发镀铝在很多领域都有着广泛的应用,例如:1. 光学领域:蒸发镀铝技术可以用于制备反射镜、透镜等光学元件,提高光学设备的性能。
2. 包装行业:蒸发镀铝可以用于包装材料的镀膜,使得包装盒具有更好的防潮、防氧化等性能。
3. 电子行业:蒸发镀铝可以制备导电铝膜,用于电子元件的制造,提高电子设备的性能和稳定性。
二、磁控溅射镀铝磁控溅射镀铝是一种利用磁场和离子轰击的方法,在真空环境下将铝材料溅射到基材表面形成铝膜。
其原理是通过施加磁场,使得铝材料形成磁控等离子体,并通过离子轰击将铝离子溅射到基材表面。
磁控溅射镀铝具有以下特点:1. 镀层致密:磁控溅射镀铝工艺能够在基材表面形成致密的铝膜,具有较好的附着力和硬度。
2. 控制性强:磁控溅射镀铝可以通过调节磁场、离子轰击能量等参数,实现对镀层厚度、结构等性质的精确控制。
3. 涂层均匀:磁控溅射镀铝可以在大面积基材上均匀地形成铝膜,适用于大规模生产。
磁控溅射镀铝在各个领域也有着广泛的应用,例如:1. 玻璃行业:磁控溅射镀铝可以用于玻璃制品的镀膜,改善玻璃的光学性能和防热性能。
2. 汽车行业:磁控溅射镀铝可以用于汽车零部件的表面处理,提高其耐腐蚀性和装饰性。
- 1、下载文档前请自行甄别文档内容的完整性,平台不提供额外的编辑、内容补充、找答案等附加服务。
- 2、"仅部分预览"的文档,不可在线预览部分如存在完整性等问题,可反馈申请退款(可完整预览的文档不适用该条件!)。
- 3、如文档侵犯您的权益,请联系客服反馈,我们会尽快为您处理(人工客服工作时间:9:00-18:30)。
F= bγ (4)
根据测量所得的F便可计算出附着能γ=F/b。如果要直接计算单位长度的附着力f,根据定义并采用上述方法(θ=0°)进行剥离可得f=γ。可见,附着力的大小和附着能γ的数据相同,由于Al膜的附着能γ较高,所以其附着力较大。实验测得的数据是:溅射Al膜的平均附着力25N,电子束蒸发Al膜的平均附着力为9.8N。这些数据和理论分析结论一致。
测定附着力所采用的方法是测量Al膜从基片上剥离时所需要的力或者能量,我们采用剥离水法来测定附着力。
设薄膜单位面积的附着能为γ,则宽度为b,长度为a的薄膜的总附着能
E=abγ (1)
用于剥离该薄膜的力F所作的功
Wp=Fa(1-sin(θ)) (2)
从而整个结构的反射率为
RM=|(n0- YM)/(n0+YM)|2={[(n0- YM(1))]2+[ YM(1)]2}/{[(n0+ YM(1))]2+[ YM(1)]2} (6)
但其描述和计算过程过于复杂,故可以有下面的描述和计算代替。
当光束垂直入射到单层薄膜有面时,反射率
Al膜的电阻率与Al块材的非常接近。电阻率随结晶粒径的减小而增加。由于电子束蒸发Al膜的结晶粒径明显小于溅射,所以溅射的电阻率小于电子束蒸发,其电导率较高。
2.5折射率
折射率一般可以反映薄膜的致密程度,随致密程度的增加而增加,而我们所制备的电极引线Al膜要求致密性好,这就可能通过测试折射率的大小来定性地判断Al膜的致密性。而折射率可以通过反射率间接地换算得到。
电子束蒸发与磁控溅射镀铝的性能分析研究导电薄膜
随着科学技术的不断发展,半导体器件的种类不断增多。原始点接触晶体管、合金晶体管、合金扩散晶体管、台面晶体管、硅平面晶体管、TTL集成电路和N沟硅栅平面MOS集成电路等,其制造工艺及工艺之间的各道工序也有所差别。在硅平面晶体管工艺过程中,电极材料的制备技术是一项关键工艺,典型的制备技术主要有两类:一类是电子束蒸发镀膜技术,另一类是磁控溅射镀膜方法。长期以来,在生产实践中由于电了束蒸发与磁控溅射这两种方法制备晶体管微电极各具优势,而且各自采用的设备和工艺不同,因而其产品质量孰优孰次一直存在争论。本文就这一问题展开研究,详细分析了常用电极材料Al通过这两种方法制备成薄膜电极的膜厚控制、附着力、致密性、电导率和折射率等重要性能指标,测试结果分析表明磁控溅射铝膜的综合性能优于电子束蒸发。
由于电子束蒸发的基片温度Ts=120°C,蒸发速率20—25A/s,蒸汽Al原子的能量为0.1—0.3eV,而溅射的基片温度Ts=120°C,溅射速率8000A/min(133.3A/s)或10000A/min(166.7A/s),溅射阈为13eV,溅射Al原子的能量比电子束蒸发的Al原了能量高1—2个数量级,所以电子束蒸发的Al原子碰到基片,很快失去能量,且迁移率很小,故原子在表面上重新排列较困难,即沉积的地方就是定位的地方成原子之间的空隙较大,有面粗糙度很大;溅射的基片温度较高,Al原子能量也较高,在而基片表面的原子迁移率增大,使得薄膜表面横向动能较大,易于连结殂成光滑的表面,稳定性较高,晶粒较大,原子间距较小,因而形成的薄膜表面粗糙芳减小。
2.3致密性
考虑Al膜的致密性就相当于考虑Al膜的晶粒的大小,密度以及能达到均匀化的程度,因为它也直接影响Al膜的其它性能,进而影响半导体哗啦的性能。
气相沉积的多晶Al膜的晶粒尺寸随着沉积过程中吸附原子或原子团在基片表面迁移率的增加而增加。由此可以看出Al膜的晶粒尺寸的大小将取决环于基片温度、沉积速度、气相原子在平行基片方面的速度分量、基片表面光洁度和化学活性等因素。
1.2溅射设备及优化工艺参数
选用ILC-1012MARK Ⅱ 1012溅射装置;操作简单,并能保证产品质量的均一性。此溅射台主要由片盒卸室SL,片盒交换室TL,清洗室CL和溅射成膜室SP组成。所有溅射过程都是在这四个室中完成的,避免了空气和杂质的污染,能够获得高质量的膜层。磁控溅射镀Al的典型工艺参数为:本底真空度1.3 ×10-4Pa以下;溅射速率:8000A/min或者10000A/min 基片温度:200°C;靶-基距:5cm;阴极电压:420V(在300—600V之间);电流:13A;溅射真空度:0.13—1.3Pa;溅射角:5—8°;溅射时间:2min/片,具体时间视片数而定。
为了更进一步地观测膜厚及表面形貌,样品放入环境扫描电子显微镜philipsXL30-ESEM中进行观测,并根据视频打印机输出的SEM图片可以看出,电子束蒸发的膜厚分散度较大,即均匀性较差。
2.2附着力
附着力反映了Al膜与基片之间的相互作用力,也是保证器件经久耐用的重要因素。溅射原子能量比蒸发原子能量高1—2个数量级。高能量的溅射原子沉积在基片上进行的能量转换比蒸发原子高得多,产生较高的热能,部分高能量的溅射原子产生不同程度的注入现象,在基片上形成一层溅射原子与基片原了相互溶合的伪扩散层,而且,在成膜过程中基片始终在等离子区中被清洗和激活,清除了附着力不强的溅射原子,净化且激活基片表面,增强了溅射原子与基片的附着力,因而溅射Al膜与基片的附着力较高。
如果是静态剥离并忽略薄膜弯曲时所产生的弹性能,则F所作的功近似等于薄膜的总附着能,即Wp=E,于是
Байду номын сангаас
F=bγ/(1-sin(θ)) (3)
(3)式中F随着θ角的变化而变化,不能真正反映薄膜的附着性能。当所加剥离力与薄膜垂直,即θ=0°时,则式简化为
采用电子束蒸发,行星机构在沉积薄膜时均匀转动,各个基片在沉积Al膜时的几率均等;行星机构的聚焦点在坩埚蒸发源处,各个基片在一定真空度下沉积速率几乎相等。采用磁控溅射镀膜方法,由于沉积电流和靶电压可以控制,也即是溅射功率可以调节并控制,因此膜厚的可控性和重复性较好,并且可在较大表面上获得厚度均匀的膜层。
此外,溅射还可以解决电子束蒸发带来的三个问题:
①台阶覆盖度。一般器件的图形尺寸为2--3μm或更小,要求在1μm左右高的台阶部位尽量能镀覆膜厚均匀的金属镀层。采用电子束蒸发和行星回旋式基片架机构组成的装置,难以得到十分理想的覆盖度。
②合金膜的成分控制。随着圆形的微细化,为确保可靠性并提高成品率采用Al-Si、Al-Cu、Al-Si-Cu等Al合金膜代替纯金属Al膜。如果采用电子束蒸发来制取合金膜,由于组分蒸气压不同会引起分解,很难控制合金膜使其达到所要求的成分。
n2-----------Si片的折射率(约为3.5)
只要准确测出垂直入射的反射率RM就可以求出Al膜的反射率NM。通过日本岛津生产的UV3101型分光光度计测得的在不同波长范围内的反射率可知,在可见光400—760nm范围内,Al膜的反射率11#样品为RM=0.82,8#样品为RM=0.83,通过(7)、(8)式计算,得出Al薄膜的反射率NM:8#样品为NM=0.702, 11#样品为NM=0.688。虽然,溅射Al膜的折射率大于电子束蒸发的Al膜,溅射Al膜的致密性比电子束蒸发好。
金属膜的特性一般用折射率NM=n-ik来表征,设金属膜厚度为dM,折射率为NM=n-ik,位相厚度为δM=2πNM dM/λ,若考虑垂直入射,金属膜与Si基底的组合导纳为
YM=((ngcos(δM)+iNMsin(δM))/( cos(δM)+i sin(δM) ng/ NM)= YM(1)+ iYM(2) (5)
通过环境扫描电子显微镜philips XL30-ESEM观测,并分析两种Al膜的晶粒大小及表面形貌的SEM照片也能验证这一结论,电子束蒸发的平均粒径为266.8nm,溅射的平均粒径为1.528μm,虽然电子束蒸发Al膜的粒径明显小于溅射的Al薄膜,但是电子束蒸发的Al原子最终不得靠得很近,当中存在很多间隙,而且溅射的Al原子相互靠得很紧,从侧面观测,溅射的Al膜平滑而且色泽光亮,说明溅射Al膜的致密较好。
RM=(n0 n2-NM2)/(n0 n2+NM2) (7)
则NM={[(1-RM)/(1+ RM)] n0 n2}1/2 (8)
式中 RM-----------反射率
n0------------空气的反射率
NM---------------Al膜的折射率
1 实验设备及优化工艺参数
1.1电子束蒸发设备及优化工艺参数
选用CHA-600型电子束蒸发台。它主要由真空镀膜室、真空系统和真空测量仪器的一部分构成。真空镀膜室主要由钟罩、球面行星转动基片架、基片烘烤装置、磁偏转电子枪、蒸发档板及加热装置等构件所组成;真空系统主要由机械泵的冷凝泵组成,选用冷凝泵可以更容易地抽到高真空状态,避免了油扩散泵返油而产生污染真空室的现象;用离子规来测量真空度。坩埚选用石墨坩埚,避免了坩埚与Al反应生成化合物而污染Al膜,坩埚的位置处在行星架的球心位置,从而保证成膜厚度的均匀性。蒸镀过程中膜厚的测量选用石英晶体膜厚监控仪。电子束蒸发镀Al的典型工艺参数为:真空度:2.6 ×10-4Pa;蒸发速率:20—25 A/s;基片温度:120°C;蒸距:45cm;蒸发时间:25min;电子枪电压:9Kv;电子枪电流:0.2A。
溅射的晶粒较大还有一个好处,减小了晶界面积,从而减少电迁移短路通道的数目,有利于增强Al膜的抗电迁移能力,延长Al膜的平均寿命。但晶粒尺寸不可太大,否则影响Al膜细线条图形的光刻质量。同时,溅射的Al膜晶粒虽大,但可以通过的后面的热处理使之细化并使性能更加优越。
2.4电导率
金属与半导体接触并非一定能够形成一个纯电阻性接触。如果接触电阻太大,即电阻率低,则外加的信号电压就会有相当大的一部分降落在接触电阻上,造成不必要的电压降和功率损耗,所以要想获得低阻的欧姆接触,膜层的电阻率应尽量小,电导率应尽量高。
3 结论
电子束蒸发和磁控溅射制Al膜是半导体器件电极制备生产中常用的两种方法,通过理论与实验分析,并对样品进行了膜厚、附着力、致密性,电导率、折射率等指标的综合测试,实验表明:电子束蒸发制得的Al薄膜厚度的可控性和重复性较差及分散度较大;Al薄膜与Si基片的附着力较小;Al薄膜的晶粒虽小,但很疏松,导致其致密性较差;Al膜的电导率、折射率较块状Al材小得多。而磁控溅射制得的Al膜的性能指标则比电子束蒸发的指标优越。实践证明,磁控溅射方法制备的Al薄膜的综合性能优于电子束蒸发,所以在生产实践中绝大多数采用磁控溅射沉积半导体电极材料,这也是半导体行业中薄膜行业的发展方向。