清洁验证及风险管理
清洁验证风险评估报告

清洁验证风险评估报告1. 引言清洁验证是指对清洁产品或服务进行验证以确保其符合预定的质量标准和卫生要求的过程。
随着清洁行业的不断发展和消费者对产品质量和安全性的关注增加,清洁验证的重要性也日益凸显。
本报告旨在对清洁验证过程中的风险进行评估,以便制定相应的管理措施和风险缓解计划。
2. 风险识别在进行清洁验证时,可能存在以下风险: - 不完整的清洁验证流程:如果验证流程不完整或不合理,可能无法全面评估清洁产品或服务的质量和卫生状况。
- 数据不准确或不可靠:如果采集的数据不准确或数据源不可靠,可能导致评估结果的失真。
- 人为误操作:人为误操作可能导致数据收集的错误或遗漏,影响验证结果的准确性。
- 潜在的质量问题:某些清洁产品或服务可能存在潜在的质量问题,可能对验证流程和结果产生不利影响。
3. 风险评估方法为了评估清洁验证过程中的风险,我们采用了以下方法: - 信息收集:收集与清洁验证相关的文献、行业标准和相关法规,了解清洁验证的要求和最佳实践。
- 风险识别:通过头脑风暴和经验分享,识别可能存在的风险。
- 风险分析:对已识别的风险进行定性和定量分析,确定其潜在影响和发生概率。
- 风险评估:根据风险的影响和发生概率,对风险进行评估,确定其优先级和严重程度。
4. 风险评估结果根据我们的风险评估,我们得出以下结果: 1. 不完整的清洁验证流程是最高优先级的风险,因为它可能导致整个验证过程的失效。
2. 数据不准确或不可靠是次高优先级的风险,因为它可能导致评估结果的失真。
3. 人为误操作是次高优先级的风险,因为它可能导致数据收集和处理的错误。
4. 潜在的质量问题是低优先级的风险,因为它可能对验证结果产生一定的影响,但不会完全失效。
5. 风险缓解计划针对上述风险,我们提出了以下风险缓解计划: 1. 完善清洁验证流程:制定详细的验证流程和标准操作程序,确保清洁验证的全面性和一致性。
2. 数据验证和审核:建立数据验证和审核机制,确保采集到的数据准确可靠,同时进行数据核查和验证。
设备清洁验证方案

腐蚀设备
某些清洁剂可能对设备材 料产生腐蚀作用,缩短设 备使用寿命。
健康风险
清洁剂的气味或成分可能 对人体健康产生不良影响 ,如刺激呼吸道或皮肤。
微生物的风险
微生物污染
清洁不彻底可能导致微生物在设备表 面或内部滋生,进而影响产品质量和 安全性。
数据记录和分析
数据记录
在验证过程中,应详细记录设备的清洁度数据, 包括但不限于设备表面清洁度、微生物数量等。
数据分析
对收集到的数据进行分析,以评估设备的清洁效 果和清洁方案的实施情况。
数据报告
根据分析结果,编写清洁验证报告,总结验证结 果和改进建议,并及时向相关部门和人员报告。
05
验证结果评估
合格标准
员工健康
微生物滋生环境可能对操作员工的健 康构成威胁,如引起呼吸道或皮肤不 适。
交叉污染
已清洁的设备如未妥善存放或未及时 使用,可能导致不同批次产品间的交 叉污染。
安全风险控制措施
选择合适的清洁剂
根据设备材质和清洁需求,选择低残留、无 腐蚀性的清洁剂。
设备维护和检查
定期对设备进行维护和检查,及时发现并处 理潜在的腐蚀或微生物污染问题。
清洁人员的培训和资质
对清洁人员进行专业培训,确保他们 了解设备结构和材质,掌握正确的清 洁方法和技巧。
确保清洁人员具备相应的资质和证书 ,能够胜任设备清洁工作。
03
验证方法
目视检查
总结词
直接观察设备表面和内部情况,判断清洁效果。
详细描述
通过目视检查,可以直观地观察设备表面是否残留污渍、杂质等,以及设备内 部是否清洁。目视检查通常用于初步判断设备清洁程度,但可能受到光线、观 察角度等因素的影响。
清洁验证要求

•
当日常监测中发现异常结果时;
參定期再验证:每个。对日常清洁程序监测结果的回顾可以作为周期性再验证。与在位清洁系统
相比,手工清洁方法应采取更高频率的再评估。
•
结果计算
生产设备主要包含2种材质—
不锈钢和塑料(共5个主要部件),在设备的不锈钢
(Minimum Single Dose, M SD )与后一产品的最大日服用量(Maximum Daily Dose,MDD)
根据下列公式计算。如后一产品为Y,前一产品为X,则:
_ MSP (X) x 1000000
MDD (Y) xSF
MACO
[mg/kg]最大允许携带量
MSD ( X ) [活性成分mg]
潜在的微生物污染等因素,对于一些特殊的产品,还应考査降解产物。
对于没有与药物成分接触的设备(如加工辅料用的流化床或包衣片所使用的包装设
备),清洁验证可以不必对活性成分进行考察,但必须考虑清洁剂残留及微生物污染等
因素。
清洁验证中需对下列放置时间进行考察,进而确定常规生产中设备的放置时间:
•
设备最后一次使用与清洁之间的最大时间间隔(“待清洁放置时间”);
剂量的1/1000。
辅料
通常针对辅料的清洁限度使用目测标准即可(见上文)
可接受的微生物限度
企业制定清洁验证的微生物限度时可以考虑产品、剂型、清洁方法的特点以及环境级
别等因素。如果没有其他特殊考虑因素,建议根据生产区域的洁净级别选用中国GMP
A
质量管理体系
(2010版)附录1中的表面微生物限度(表3-30)。
材质表面选择一个取样点,塑料表面选择2个取样点,通过擦拭法取样测试。
清洗验证标准管理程序

1.目的PURPOSE1.1.提供指导方针,以规范清洁验证需要进行的活动及程序。
2.范围SCOPE2.1.适用于本公司在GMP生产过程中,所有存在潜在污染风险阶段的清洗验证。
3.职责RESPONSIBILITY3.1.QA:质量保证负责验证文件的制定,负责组织清洁验证活动。
3.2.QC:负责审核验证文件,检验方法的验证,以及验证过程中的取样与分析。
3.3.PD:负责审核验证文件,并对清洗工艺及相关的提供技术支持。
3.4.Quality VP:质量副总负责所有确认和验证文件的批准。
4.术语DEFINITION4.1.Cleaning清洗清洗可定义为除去产品或非产品污染,包括除去表面的残留以有效地降低总污染和与下一个产品的交叉污染。
清洗可使用清洗剂,如表面活性剂或消毒剂。
清洗的目的是除去产品和非产品污染物料,以有效地降低微生物的滋生、总污染和与下一种物料潜在的交叉污染。
5.PROCEDURE程序5.1.Cleaning Validation Project Plan (VPP) 清洗验证项目计划5.1.1.工厂的生产设施/公用系统/设备都要制定一个清洗验证项目计划以规定验证的范围和进度。
5.1.2.成立清洗验证项目组,项目组一般由QA、QC、生产、设备人员组成。
清洗验证项目组负责清洗验证项目计划的建立。
5.1.3.清洗验证计划至少3年修订一次,或者根据需要随时修订。
清洗验证项目小组负责验证清洗验证项目计划的更新。
5.2.清洁验证的一般要求5.2.1.清洁程序通常应当进行验证,以证明清洁程序的有效性和重现性。
一般来说,清洁验证应当针对污染及物料易夹带给原料药质量带来最大风险的状况及步骤。
5.2.2.对于专用生产线或设备(指用于同一品种的生产),要求至少作连续3次的清洁验证。
对于专用生产线或一台非专用设备(指用于多品种生产),每种产品都必须做验证,且要求至少作3次的清洁验证。
5.2.3.设备使用完后应及时清洗,若使用放置一段时间才清洗,应对清洗效果进行评估或验证。
清洁验证风险评估
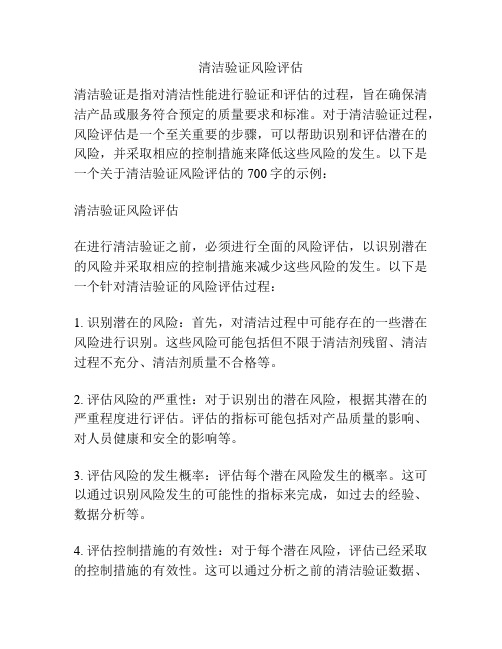
清洁验证风险评估清洁验证是指对清洁性能进行验证和评估的过程,旨在确保清洁产品或服务符合预定的质量要求和标准。
对于清洁验证过程,风险评估是一个至关重要的步骤,可以帮助识别和评估潜在的风险,并采取相应的控制措施来降低这些风险的发生。
以下是一个关于清洁验证风险评估的700字的示例:清洁验证风险评估在进行清洁验证之前,必须进行全面的风险评估,以识别潜在的风险并采取相应的控制措施来减少这些风险的发生。
以下是一个针对清洁验证的风险评估过程:1. 识别潜在的风险:首先,对清洁过程中可能存在的一些潜在风险进行识别。
这些风险可能包括但不限于清洁剂残留、清洁过程不充分、清洁剂质量不合格等。
2. 评估风险的严重性:对于识别出的潜在风险,根据其潜在的严重程度进行评估。
评估的指标可能包括对产品质量的影响、对人员健康和安全的影响等。
3. 评估风险的发生概率:评估每个潜在风险发生的概率。
这可以通过识别风险发生的可能性的指标来完成,如过去的经验、数据分析等。
4. 评估控制措施的有效性:对于每个潜在风险,评估已经采取的控制措施的有效性。
这可以通过分析之前的清洁验证数据、评估清洁过程中采取的控制措施等来完成。
5. 制定风险管理策略:在评估完风险的严重性和发生概率后,根据结果制定相应的风险管理策略。
这可能包括加强清洁过程的监控、引入更有效的清洁剂、优化清洁工艺等。
6. 决定风险控制的优先级:根据风险评估结果,在所有识别出的潜在风险中确定风险控制的优先级。
对于高风险的风险,应优先采取控制措施来降低其风险水平。
7. 实施和监控控制措施:根据制定的风险管理策略,实施和监控相应的控制措施。
这可能包括建立清洁过程的监控程序、进行定期的清洁验证等。
通过进行清洁验证风险评估,可以帮助组织识别和评估潜在的风险,并采取措施来降低这些风险。
这有助于确保清洁产品或服务的质量和可靠性,同时也提升了组织对风险的管理能力和决策的准确性。
醇沉罐清洁验证风险评估

醇沉罐清洁再验证风险评估目录1、目的 (3)2、概述 (3)2.1设备介绍 (3)2.2设备主要生产品种 (3)2.3设备清洁验证现状 (3)2.4清洁再验证的设备共线情况介绍 (3)3、评估范围 (3)4、评估依据 (3)4.1法规指南 (3)4.2内部文件 (3)5、风险评估小组成员 (4)6、评估风险过程 (4)6.1风险因素标准的评定 (4)6.2 醇沉罐清洁后潜在风险 (6)7、风险分析 (7)7.1 醇沉罐清洁后风险项 (7)7.2共线情况说明 (7)7.3最难清洁产品及取样点的选择 (7)7.4化学残留计算方法选择 (10)7.5基于日治疗剂量的1/1000计算标准 (12)7.6基于一般浓度限度(10ppm) (13)7.7基于毒性数据的计算标准 (14)7.8表面残留物限度分析 (15)7.9风险分析结论 (15)8、评估结论 (15)1、目的本报告是对醇沉罐生产的安全性进行风险管理的报告,报告对醇沉罐生产过程中可能产生混淆、污染和交叉污染的风险要素进行分析判定,对于每种风险可能产生损害的严重度和危害的发生概率进行估计,在某一风险水平不可接受时,提出降低风险预见的控制措施,以期将剩余风险降低到可以接受的水平。
2、概述2.1设备介绍醇沉罐工作原理:设备适用于中药水煎液浓缩后浓缩液进行冷冻灌温乙醇沉淀。
设备是由附夹套的椭圆封头。
锥形底的圆筒体,内安装三叶式搅拌以及微调旋出液管等组装而成,中药水煎浓缩采用加入乙醇配成一定醇度的液体,然后常温,低温冷冻沉降进行液固分离,以提高中药提取液的纯度及澄明度。
设备选用不锈钢制造,配有高压水自动喷淋清洗系统,夹套中可通低温冷却水。
2.2设备主要生产品种[XXXXXX]。
2.3设备清洁验证现状根据《清洁验证管理规程》[XXXXXX][XXXXXX]的规定,“产品组份或产品批量改变,致使有更难清洁的产品或可接受限度改变”需要进行再验证,上次清洁验证完成时间为2023年4月完成,本次抗病毒口服液批量发生变更,需要进行再验证。
清洁验证方案

清洁验证方案___风险评估,确定了最差情况的产品。
4.2根据风险评估结果,制定了相应的清洁验证方案,以保证生产设备的清洁可靠性和稳定性。
5.验证方法:5.1清洁剂、消毒剂的配制和使用应符合相关规定。
5.2清洁验证应按照验证方案的要求进行,包括物理外观、检测化学残留和微生物残留等方面的检测。
5.3验证周期应根据生产设备的使用情况和产品的特性确定,一般为每批次生产结束后进行清洁验证。
6.验证结果:6.1经过3次清洁验证,所有设备的物理外观、检测化学残留和微生物残留均低于设定残留限度要求,验证结论为可靠性高、稳定性好。
6.2根据验证结果,进一步完善了生产设备的清洁管理制度,确保产品质量的稳定和可靠性。
7.验证结论:本次清洁验证方案的实施,验证结果表明清洁方法的可靠性和稳定性较高,符合GMP要求,为保障产品质量提供了有力的保证。
同时,也为今后类似的验证工作提供了经验和参考。
洁净程序风险评估提出了处理质量风险的措施,具体细节见《验证总计划》。
由于上一产品对下一产品的污染不是均匀分布在整个设备的接触面上,因此选择设备的最差区域,这些区域在清洁难度和残留水平方面代表对清洁规程的最大挑战。
因此,在确定清洁验证的活性成分的取样计划之前,必须先进行风险分析,具体细节见《验证总计划》。
验证内容包括清洁验证前的检查和确认项目。
其中,确认验证涉及人员按规定进行了培训,具体见附件;确认验证涉及文件现行批准的规程、管理和操作文件,指令清楚、明确,不易引起误操作;确认空调净化系统、纯化水系统、压缩空气系统等均经过验证且能正常运行;各操作间温湿度、压差及环境经检查符合GMP要求。
清洁条件包括人员净化、工艺用水(纯化水)和设备环境。
人员净化应按照《人员进入洁净区净化操作规程》进行。
工艺用水(纯化水)应按照《中华人民共和国药典》2015年版二部及《纯化水内控质量标准》检验,并符合规定。
设备环境应为D级。
清洗操作方法为:设备能拆卸部分拆卸完毕后,用饮用水冲洗或用刷子涮洗至无明显残留物,再用饮用水擦拭设备内外表面,用纯化水擦拭两遍,最后用75%乙醇或3%双氧水消毒。
新建厂房车间清洁验证风险评估报告
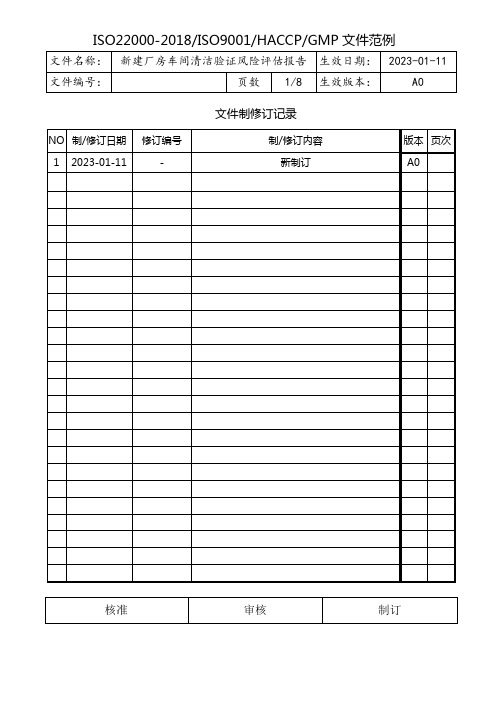
文件制修订记录2010版GMP第七章“确认与验证”的第一百四十三条规定:“清洁方法应经过验证,证实其清洁的效果,以有效防止污染和交叉污染。
清洁验证应综合考虑设备使用情况、所使用的清洁剂和消毒剂、取样方法和位置以及相应的取样回收率、残留物的性质和限度、残留物检验方法的灵敏度等因素。
”本报告的目的,就是运用风险管理的工具,全面评估公司新车间的清洁验证,通过质量风险管理方法评估后确定清洁验证中的风险及相应CAPA措施,以确保经过清洁验证证明的清洁方法具有有效性,能够保证不会产生污染与交叉污染。
二 .范围评估包括生产系统需要清洁所涉及的工艺设备及管道、物料、控制系统、关键设施、环境控制和人员操作。
据此,范围主要是:•生产系统需要清洁的所有工艺设备及管道。
•物料:包括活性成分、中间体、试剂、辅料、清洁剂等。
•清洁操作时相关的控制系统、关键设施、环境控制:其它辅助设备、公用工程系统(如空调、制水、压缩空气、纯蒸汽系统)等。
•该岗位操作人员的规范操作及培训。
三 .评估方法进行风险评估所用的方法遵循因果关系图(鱼骨图)以及FMEA技术(失效模式与影响分析),其中FMEA技术包括以下几点。
•风险确认:可能影响产品质量、产量、工艺操作或数据完整性的风险。
•风险判定:包括评估先前确认风险的后果,其基础建立在严重程度、可能性及可探测性上。
•判定标准:根据医药生产的特点和便于确切的评定等级,本次评估将严重程度、发生的可能性和可探测性的评定等级均分为十级。
严重程度的评定等级表(S)严重程度(S)的评定等级表发生的可能性的评定等级表(P)发生的可能性的评定等级表(P)可探测性的评定等级表(D)可探测性的评定等级表(D)以便采取可能的预防措施.RPN = Severity(严重程度)×Possibility(发生的可能性)×Detection(可探测性) 风险优先数量等级判定四.通过因果关系图(鱼骨图)找出影响清洁验证效果的因素1、清洁验证的要求:目测标准、活性成分残留量、清洁剂残留量、微生物污染水平。
清洁验证方案

清洁验证方案在现代生活中,清洁已经成为了人们日常生活中必不可少的一部分。
清洁工作的关键在于检验清洁是否彻底,针对清洁的验证成为了必要的步骤。
清洁验证的重要性清洁验证是确保清洁工作完成的一种方式,可以验证清洁工作是否彻底,并且验证结果可以及时发现清洁中存在的问题和隐患。
在某些场合中,如医院、实验室、卫生间等需要进行更加细致的清洁操作,在这些场合下,清洁验证尤为重要。
清洁验证方案的制定制定一个清洁验证方案是对清洁工作进行有效管理的一种方式。
首先,应该确认清洁验证的目的、确定什么情况下需要进行清洁验证,其次,在制定清洁验证方案时,应该考虑使用何种验证方法,验证方法应该与清洁操作相吻合。
最后,清洁验证方案的制定需要考虑在验证过程中存在的风险,制定相应的应急措施和解决方案。
清洁验证方案的执行清洁验证方案的执行是确保验证结果准确可靠的关键步骤。
在执行清洁验证方案过程中,应该按照验证方案的要求,对清洁进行逐一检查,确保每一项任务已经完成。
如果发现清洁存在问题,应该及时调整验证方案并重新执行。
清洁验证的常用方法以下为清洁验证的常用方法。
检查检查是验证清洁的一种方法,通常会使用一些检查工具,如灯光和镜子等。
这些工具可以帮助查找隐藏的污垢和污染物,并且通过对比前后清洁结果,可以判断清洁工作是否完成。
功能测试在一些场合下,如实验室和医院,应该进行功能测试来验证清洁是否彻底。
对于设备、仪器等进行相应的功能测试,以确保彻底清除污物和污染物。
抽样检验抽样检验是对清洁进行更严格的验证方式,通常在对卫生间、实验室等进行清洁后,进行抽样检验以确保清洁的彻底度。
抽样检验是一种依赖于概率和随机性的验证方法,可以保证随机选择的样本能够反映整个样本的情况,从而降低误差。
清洁验证的常见问题清洁验证中存在一些常见的问题,这些问题通常表现为验证方式的不当或验证方法的错误使用等,以下列举一些常见问题:验证方案不严谨清洁验证方案的不严谨会导致验证结果的不可靠和验证过程的失败。
中药共线生产的风险评估和清洁验证
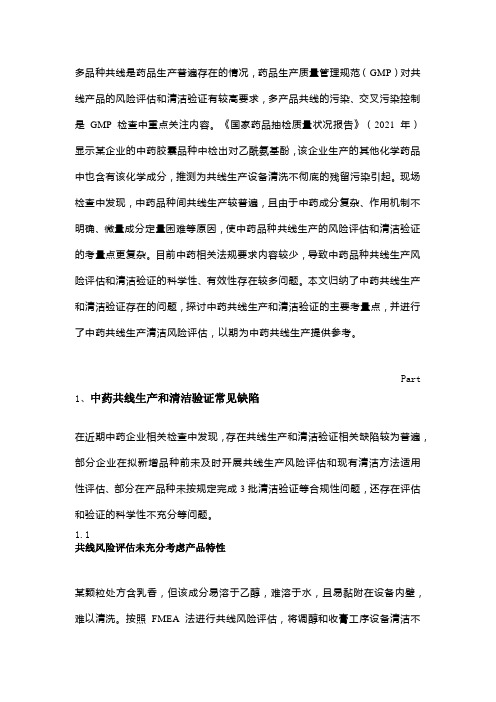
多品种共线是药品生产普遍存在的情况,药品生产质量管理规范(GMP)对共线产品的风险评估和清洁验证有较高要求,多产品共线的污染、交叉污染控制是GMP 检查中重点关注内容。
《国家药品抽检质量状况报告》(2021 年)显示某企业的中药胶囊品种中检出对乙酰氨基酚,该企业生产的其他化学药品中也含有该化学成分,推测为共线生产设备清洗不彻底的残留污染引起。
现场检查中发现,中药品种间共线生产较普遍,且由于中药成分复杂、作用机制不明确、微量成分定量困难等原因,使中药品种共线生产的风险评估和清洁验证的考量点更复杂。
目前中药相关法规要求内容较少,导致中药品种共线生产风险评估和清洁验证的科学性、有效性存在较多问题。
本文归纳了中药共线生产和清洁验证存在的问题,探讨中药共线生产和清洁验证的主要考量点,并进行了中药共线生产清洁风险评估,以期为中药共线生产提供参考。
Part 1、中药共线生产和清洁验证常见缺陷在近期中药企业相关检查中发现,存在共线生产和清洁验证相关缺陷较为普遍,部分企业在拟新增品种前未及时开展共线生产风险评估和现有清洁方法适用性评估、部分在产品种未按规定完成3批清洁验证等合规性问题,还存在评估和验证的科学性不充分等问题。
1.1共线风险评估未充分考虑产品特性某颗粒处方含乳香,但该成分易溶于乙醇,难溶于水,且易黏附在设备内壁,难以清洗。
按照FMEA 法进行共线风险评估,将调醇和收膏工序设备清洁不彻底的风险评估为中风险。
实际上,因乳香的溶解特性和物理特性,这两个工序的设备表面均易黏附乳香,存在较大的共线风险隐患。
清洁方案中若只使用水进行清洗,采用该品种指标性成分迷迭香酸(水易溶)进行清洁验证评价,则没有考虑到乳香不同工艺状态下的存在形式和黏附性,在共线生产时可能将乳香成分引入其他品种。
使用乙醇或NaOH 溶液清洗,则基本可解除污染风险。
1.2清洁验证含量测定方法学验证细节导致失败某颗粒开展清洁验证方法学确认,采用迷迭香酸作为检测指标。
(完整版)设备清洁验证管理规程
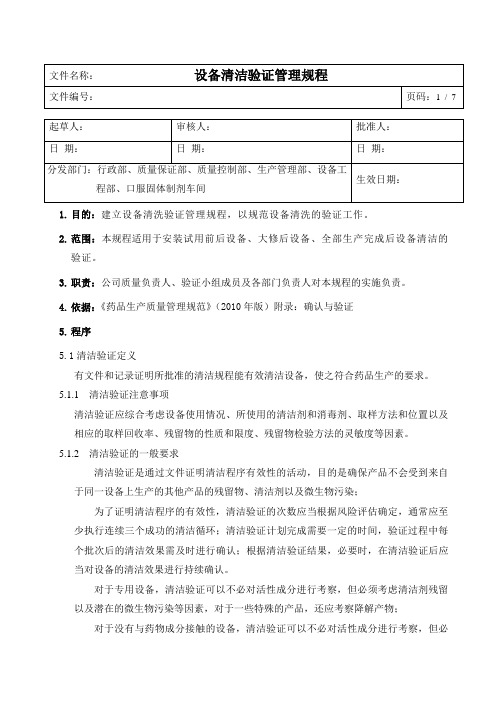
1.目的:建立设备清洗验证管理规程,以规范设备清洗的验证工作。
2.范围:本规程适用于安装试用前后设备、大修后设备、全部生产完成后设备清洁的验证。
3.职责:公司质量负责人、验证小组成员及各部门负责人对本规程的实施负责。
4.依据:《药品生产质量管理规范》(2010年版)附录:确认与验证5.程序5.1清洁验证定义有文件和记录证明所批准的清洁规程能有效清洁设备,使之符合药品生产的要求。
5.1.1清洁验证注意事项清洁验证应综合考虑设备使用情况、所使用的清洁剂和消毒剂、取样方法和位置以及相应的取样回收率、残留物的性质和限度、残留物检验方法的灵敏度等因素。
5.1.2清洁验证的一般要求清洁验证是通过文件证明清洁程序有效性的活动,目的是确保产品不会受到来自于同一设备上生产的其他产品的残留物、清洁剂以及微生物污染;为了证明清洁程序的有效性,清洁验证的次数应当根据风险评估确定,通常应至少执行连续三个成功的清洁循环;清洁验证计划完成需要一定的时间,验证过程中每个批次后的清洁效果需及时进行确认;根据清洁验证结果,必要时,在清洁验证后应当对设备的清洁效果进行持续确认。
对于专用设备,清洁验证可以不必对活性成分进行考察,但必须考虑清洁剂残留以及潜在的微生物污染等因素,对于一些特殊的产品,还应考察降解产物;对于没有与药物成分接触的设备,清洁验证可以不必对活性成分进行考察,但必文件编号:页码:2 / 7须考虑清洁剂残留及微生物污染等因素;清洁验证中需对下列放置时间进行考察,进而确定常规生产中设备的放置时间:①设备最后一次使用与清洁之间的最大时间间隔(“待清洁放置时间”)②设备清洁后至下次使用的最大时间间隔(“清洁后放置时间”)③当采用阶段性生产组织方式时,应当综合考虑阶段性生产的最长时间和最大批次数量,以作为清洁验证的评价依据(最长连续生产周期)5.2清洁验证流程清洁验证前提条件①清洁规程已经批准,包括关键清洁程序的参数范围②完成风险评估(包括关键操作、设备、物料包括活性成分、试剂、辅料、清洁剂以及其他可能影响到清洁效果的参数);③分析方法经过验证;④取样方法及取样回收率已经验证和批准;⑤验证方案已经批准,其中包括接受标准5.3 清洁验证设备5.3.1制粒、整粒、提升转料、干燥设备5.3.2混料设备5.3.3压片设备、包衣设备5.3.4 直接接触药品的内包装设备5.3.5直接接触药品的容器5.3.6其他与产品直接接触的设备5.4清洁验证的步骤5.4.1产品分组在对设备进行清洁验证前,首先应依据该设备用来生产的产品进行分组。
清洁验证管理规程

生产车间、设备部、研发部等其他可提供技术支持的部门组成。
QA:是清洁验证的组织者,主要负责起草清洁验证方案,组织验证过程的实施,以及验证过程出现的偏差处理和变更控制,并负责验证数据的汇总和完成清洁验证报告;QC:负责提供清洁验证中标的物分析方法验证工作,以及不同材质设备取样回收率试验,完成清洁验证的检测工作等;生产技术部:提供清洁验证的技术支持,负责提供生产工艺、审核清洁规程,协助QA完成清洁验证方案、审核清洁验证报告等;设备部:提供清洁验证的技术支持,负责提供设备基本信息,协助QA完成清洁验证方案、审核清洁验证报告等;生产车间:提供设备、容器具等难清洁点,按照批准的清洁规程进行清洁,协助质量部门完成清洁验证;研发部等其他可提供技术支持的部门:提供相应技术支持,协助完成清洁验证。
4清洁验证前准备清洁验证前应汇总一些资料,以便进行充分的风险评估。
4.1产品列表,包括该产品的批量、活性成分及其性状、在清洁剂中的溶解性、日治疗剂量及毒理数据;4.2设备列表,包括设备材质、接触物料的内表面积及共用情况等;4.3清洁SOP,包括详细的清洁方法(手工清洁、自动清洁或者半自动清洁)、清洁剂以及设备的难清洁点。
5风险评估风险评估贯穿于清洁验证的整个周期,清洁验证小组应通过充分的风险评估来确定清洁验证的范围和程度,依此来制定详细的验证策略。
5.1设备的评估药品生产过程中用到各种各样的设备,但并非所有的设备均需要清洁验证,即使该设备需要确清洁验证,但也应通过评估选取那些部位进行清洁验证。
一般情况下清洁验证只对于直接接触产品的设备进行清洁验证。
同时设备的评估还用考虑设备是否专用、设备的材质、设备的构造、设备的功能等方面,例如同一个产品有几条生产线,每条生产线的设备是平行的,那么可以选取一条生产线的生产设备进行清洁验证。
5.1.1根据设备的使用情况不同,分为专用设备和非专用设备,专用设备仅用于生产一个产品,或单一产品线(如同一种API的不同规格)。
(风险管理)欧盟清洁验证方案(带风险分析)
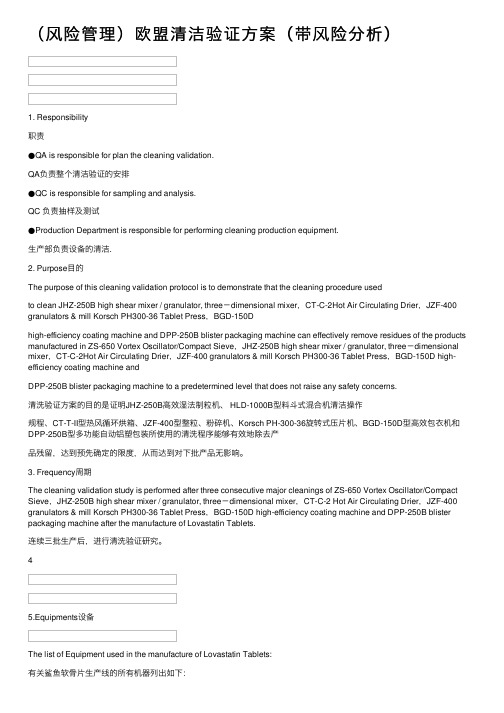
(风险管理)欧盟清洁验证⽅案(带风险分析)1. Responsibility职责●QA is responsible for plan the cleaning validation.QA负责整个清洁验证的安排●QC is responsible for sampling and analysis.QC 负责抽样及测试●Production Department is responsible for performing cleaning production equipment.⽣产部负责设备的清洁.2. Purpose⽬的The purpose of this cleaning validation protocol is to demonstrate that the cleaning procedure usedto clean JHZ-250B high shear mixer / granulator, three-dimensional mixer,CT-C-2Hot Air Circulating Drier,JZF-400 granulators & mill Korsch PH300-36 Tablet Press,BGD-150Dhigh-efficiency coating machine and DPP-250B blister packaging machine can effectively remove residues of the products manufactured in ZS-650 Vortex Oscillator/Compact Sieve,JHZ-250B high shear mixer / granulator, three-dimensional mixer,CT-C-2Hot Air Circulating Drier,JZF-400 granulators & mill Korsch PH300-36 Tablet Press,BGD-150D high-efficiency coating machine andDPP-250B blister packaging machine to a predetermined level that does not raise any safety concerns.清洗验证⽅案的⽬的是证明JHZ-250B⾼效湿法制粒机、 HLD-1000B型料⽃式混合机清洁操作规程、CT-T-II型热风循环烘箱、JZF-400型整粒、粉碎机、Korsch PH-300-36旋转式压⽚机、BGD-150D型⾼效包⾐机和DPP-250B型多功能⾃动铝塑包装所使⽤的清洗程序能够有效地除去产品残留,达到预先确定的限度,从⽽达到对下批产品⽆影响。
阶段性生产或间歇式生产背景下清洁验证的管理要求

阶段性生产或间歇式生产背景下清洁验证的管理要求分析了生产结束到设备清洁的时间间隔的界定与确认,设备清洁结束到下一轮生产启动设备投入生产的时间间隔的界定与确认,设备清洁状态维持等清洁要素在清洁验证中的有效性,并依托微生物限度指标对密闭性设备、开放类设备分别进行清洁的持续受控状态研究,为实现药品生产全生命周期的药品生产设备设施的持续受控提供了清晰的管理思路,有效控制并降低清洁管理方面的药品质量风险,为设备的持续验证状态管理提供有力的验证数据支持,为持续稳定的生产出符合预定用途和注册要求的药品提供清洁保障。
一、药品生产的清洁验证及其管理要求药品 GMP 规范的宗旨是预防污染、交叉污染、混淆与差错等风险,为了能够满足这一法规要求,需要制定详细的专用清洁规程,并通过清洁验证来确认清洁规程的有效性。
谭克辉的论文《对药物配制罐和灌装机清洁消毒验证的探讨》提供了清洁规程的主要内容[1]。
药品 GMP 规范通则对清洁验证的具体要求[2],如: 清洁验证应当综合考虑设备使用情况、所使用的清洁剂和消毒剂、取样方法和位置以及相应的取样回收率、残留物的性质和限度、残留物检验方法的灵敏度等因素。
已经有很多专家和论文专著对清洁验证的方法和测试项目开展了讨论,讨论的焦点是产品生产结束后的药物残留控制及清洁效果的确认,关注清洁验证中间隔时间管理的比较少,然而也正是清洁之后的维持清洁状态的间隔时间管理衔接了药品生产设备的持续受控状态管理,提供了药品生产设备设施的全程受控管理的重要数据信息。
本文就阶段性生产组织方式中非灭菌用的生产设备的清洁验证及清洁状态的维护开展相关探索,为药品生产的间歇期间持续受控状态的管理提供有益的思路。
《确认与验证》附录要求清洁验证对潜在的微生物污染进行评价,考虑设备使用后至清洁前的间隔时间以及设备清洁后的保存时限。
阶段性生产组织方式还应考虑阶段性生产的最长时间和最大批次数量。
根据这一要求,阶段性生产组织方式( 或者药品间歇式生产) 的清洁验证的主要考察点就需要包含设备清洁后的存放状态及清洁后至再生产启动后投入使用前的时间间隔的确认。
清洁验证及其风险管理
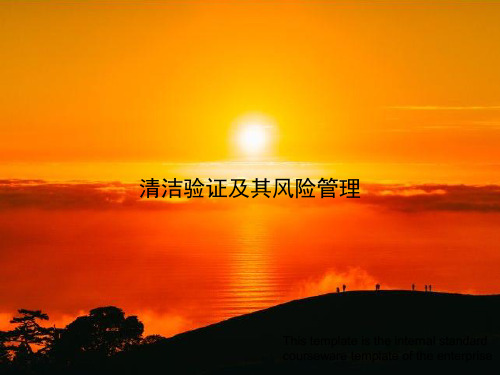
制定SOP是清洁验证的先决条件; 通常参照设备的说明书制定详细的规程,规定每一台设备的清洁程序,保证每个操作人员都能以可重复的方式对其清洗,并获得相同的清洁效果。 清洁规程的要点: 系统的拆卸; 预清洁; 清洁剂、浓度、溶液量,水质量;
清洁规程的要点(续):
时间、温度和频次、流速、压力; 消毒(消毒剂浓度、消毒方法、消毒剂用量); 装配:按说明书、示意图要求装配; 干燥:明确干燥的方式和参速; 检查:符合预定的标准。
0.5
0.3048
2.728
1.0
0.1615
5.910
1.5
0.1067
8.637
2.0
0.08230
11.820
通常,对于盲管和垂直管路为了清洁干净要求管道中水的流速要大于湍流所需要的流速1.52米/秒 (5英尺/秒)。
因为: 有效的冲洗垂直管道; 排出垂直管道中的空气; 完全润湿管路
0.1615米/秒
棉签取样方法的验证(续):
⑧将擦拭棉签分别放入棉签管中,加入预定溶剂5ml,超声; ⑨ 用经验证的检验方法检验,计算回收率和回收率的RSD。 下图为棉签插试取样方法:
第一步
第二步
淋洗液取样方法的验证:
通常淋洗法限度检查不需做回收率验证;定量检查应做回收率验证,可以利用淋洗溶剂冲洗已知量(在限度附近)的分析物确定回收率,回收率通常应不低于95%。 淋洗的取样方法为根据淋洗水流经设备的线路,选择淋洗线路相对最下游的一个或几个排水口为取样口。分别按照微生物检验样品和化学检验样品的取样规程收集清洁程序最后一步淋洗即将结束时的水样。 淋洗法样品可对冲洗液直接检测也可对冲洗液做稀释后检测;无论直接检测还是稀释检测都应在接到样品后首先将样品同空白溶剂做视觉检查,确定是否有颜色差异和异物存在;如果有上述现象发生,可直接判定样品不合格。
基于科学和风险的清洁工艺开发与验证系列——概述篇

基于科学和风险的清洁工艺开发与验证系列——概述篇展开全文前言清洁活动,例如清洁生产用工艺设备以防止可能出现的交叉污染是GMP的一个基本方面。
监管组织一直要求对清洁工艺进行验证,并将其视为确保控制产品交叉污染以确保患者安全和产品质量的一项重要活动。
美国材料与试验协会ASTM(American Society for Testing Materials)于2018年11月发布了针对清洁开发与验证的标准指南ASTM E3106-18,意在指导清洁工艺开发阶段与清洁验证的过程,并对要点内容提供指导。
ASTM E3106-18清洁验证指南在生命周期的清洁开发与验证过程中基于三个方面进行考虑:•基于科学的方法应贯穿于清洁工艺开发和验证的整个过程。
•质量风险管理应贯穿于清洁工艺开发和验证的整个过程。
•适当的统计学分析应贯穿于清洁工艺开发和验证的整个过程。
综述一基于科学的方法传统的清洁验证包括一个批准的方案,预定确认的可接受标准以及连续三次的清洁验证过程执行,企业很少进行基于风险的适当次数的清洁程序评估并确认是否满足验收标准,以证明清洁程序有效。
而随着行业不断的发展和技术进步,更为科学的方法逐步应用到清洁工艺当中,例如:1. 质量源于设计QbD(Quality by Design)•选择一个合适的清洁工艺•识别清洁工艺过程的控制策略•通过先验知识、试验和风险评估等方法,识别可能对清洁关键质量属性(CQA)产生影响的材料的物料属性和清洁工艺参数•确定关联物料属性和清洁工艺参数与清洁CQA的功能关系•充分理解的清洁工艺,结合质量风险管理,建立适当的控制策略,例如,包括设计空间和/或实时放行的建议2. 过程分析技术PAT(Process Analytical Technology)•PAT的一个期望目标是设计和开发易于理解的清洁工艺,从而始终确保清洁工艺结束时达到预期的清洁效果。
这种清洁工艺在设计上符合质量与合规的原则,并可以在提高效率的同时减少对质量和管理方面的风险。
- 1、下载文档前请自行甄别文档内容的完整性,平台不提供额外的编辑、内容补充、找答案等附加服务。
- 2、"仅部分预览"的文档,不可在线预览部分如存在完整性等问题,可反馈申请退款(可完整预览的文档不适用该条件!)。
- 3、如文档侵犯您的权益,请联系客服反馈,我们会尽快为您处理(人工客服工作时间:9:00-18:30)。
10版GMP的要求(WHO GMP):第七章 确认与验证第一百四十三条清洁方法应经过验证,证实其清洁的效果,以有效防止污染和交叉污染。
清洁验证应综合考虑设备使用情况、所使用的清洁剂和消毒剂、取样方法和位置以及相应的取样回收率、残留物的性质和限度、残留物检验方法的灵敏度等因素。
10版GMP的要求(WHO GMP):第五章 设 备第二节 设计和安装 第七十四条 生产设备不得对药品质量产生任何不利影响。
与药品直接接触的生产设备表面应当平整、光洁、易清洗或消毒、耐腐蚀,不得与药品发生化学反应、吸附药品或向药品中释放物质。
10版GMP的要求(WHO GMP):第四节 使用和清洁第八十四条 应当按照详细规定的操作规程清洁生产设备。
生产设备清洁的操作规程应当规定具体而完整的清洁方法、清洁用设备或工具、清洁剂的名称和配制方法、去除前一批次标识的方法、保护已清洁设备在使用前免受污染的方法、已清洁设备最长的保存时限、使用前检查设备清洁状况的方法,使操作者能以可重现的、有效的方式对各类设备进行清洁。
10版GMP的要求(WHO GMP):如需拆装设备,还应当规定设备拆装的顺序和方法;如需对设备消毒或灭菌,还应当规定消毒或灭菌的具体方法、消毒剂的名称和配制方法。
必要时,还应当规定设备生产结束至清洁前所允许的最长间隔时限。
第八十五条 已清洁的生产设备应当在清洁、干燥的条件下存放。
10版GMP的要求(WHO GMP):第九章 生产管理第二节 防止生产过程中的污染和交叉污染 第一百九十七条 生产过程中应当尽可能采取措施,防止污染和交叉污染,如:(六)采用经过验证或已知有效的清洁和去污染操作规程进行设备清洁;必要时,应当对与物料直接接触的设备表面的残留物进行检测;36. 为确认清洁规程的效力,应进行清洁验证。
应根据所涉及的物料,合理的确认产品残留、清洁剂和微生物污染的限度标准。
这个限度标准应该是可以达到的,能够证实的。
37. 应使用经验证、检出灵敏度高的检验方法来检测残留或污染物。
每种分析方法或仪器的检测灵敏度应足以检测出设定合格限度水平的残留或污染物。
38. 通常只有接触产品设备表面的清洁规程需要验证。
某些场合下,还应考虑不直接接触产品的部分。
应验证设备使用与清洁的间隔时间,以及已清洁设备可保留的时间,并通过验证确定清洁的间隔时间和清洁方法。
39. 对于相似产品和相似工艺而言,可从相似产品及工艺中,选择一个具有代表性产品和工艺进行清洁验证。
可采用“最差条件”的方法进行单独的验证试验,在验证中应考虑关键因素。
40. 为证明方法是经过验证的,通常应在3个连续批上使用该清洁规程,并检验合格。
41. 清洁验证不应采用“不断测试,直至清洁”的方式。
42. 如果实际产品是有毒物质或有害物质,在清洁验证中,可以例外地采用物化特性相似的无毒无害物质来模拟。
FDA的要求:在FDA的cGMP 211.67章节中规定了设备清洗验证的要求。
�建立书面标准操作程序(SOP),其中必须详细规定设备各部件的清洗过程。
�必须建立书面的清洗方法验证通则。
�清洗方法验证通则应规定执行验证的负责人、批准验证工作的负责人、验证标准(合格标准)、再验证的时间。
�对各生产系统或各设备部件进行清洗验证之前,应制定专一特定的书面验证计划,其中应规定取样规程、分析方法(包括分析方法的灵敏度)。
�消胆胺召回事件:即1988年从市场上撤回了消胆胺成品制剂,原因是规程不当。
生产该制剂的原料药受到了农业杀虫剂生产中少量中间体和降解物质的污染。
造成交叉污染的主要原因使用了回收溶媒。
而回收溶媒受到了污染,原因是对溶媒桶的重复使用缺少监控。
贮存杀虫剂产生的回收溶媒桶又重复地用于贮存该药品生产中的回收溶媒。
而工厂没有对这些溶媒桶进行有效的监控,没有对其中的溶媒进行有效的检验,也没有对桶的清洗规程进行验证。
被杀虫剂污染的部份化学原料药运到了另一地点的第二家工厂生产制剂,使该工厂的流化床干燥器中物料袋受到了杀虫剂的污染,料造成各批产品受到污染,而该工厂根本就没有生产杀虫剂。
FDA历来的检查重点:��要求清洗设备的主要目的还是防止污染或混料。
由于设备清洗维护不当或防尘管理不当,FDA 检查官曾十分注意检查卫生状况。
过去FDA 总是更注意检查青霉素类与非青霉素类药物之间的交叉污染、药品与甾类物质或激素之间的交叉污染问题。
在过去二十年间,因实际或潜在的青霉素交叉污染问题已从市场上撤回了大量的药品。
�有一位幼儿教师,怀抱着一名2小时前注射过青霉素钠的婴儿,孩子的一泡尿撒在了幼儿教师的手臂上,1分钟后该名幼儿教师呼吸困难、面色苍白、心慌气短,不一会就呈现昏迷状态,经医生诊断为青霉素过敏。
�FDA加强对进口原料供应商的检查:�1992年,FDA 对一家海外原料药生产厂发出了进口警告,该工厂使用同一设备生产强力甾体类物质和非甾体类物质。
该工厂是多品种原料药生产厂。
FDA 认为交叉污染的可能性很大,对公众的健康造成了严重威胁。
该工厂仅在FDA 检查时开始清洗验证工作,FDA 在检查时认为该清洗验证不当。
理由之一是:工厂仅寻找没有前一种物质存在的证据。
但是用TLC 法检验洗涤水之后,找到了设备中还残留了前一产品生产过程中的副反应物质和降解物质的证据。
通常清洁方法分为:�手工清洁(Manual Cleaning)�在线清洁(Cleaning In Place)在线清洁的特点:1. 设备、容器、管道能够自动进行清洗;2. 对容器采用喷林法清洁,对管道采用压力法清洁;3. 极少的手工操作,重复性高。
1. 清洗剂(水、有机溶剂或表面活性剂)采用扩散或对流的方法到达“脏物”表面;2. 清洗剂通“脏物”反应;3. 反应产物采用扩散或对流的方法离开设备。
因为:1.有效的冲洗垂直管道;2.排出垂直管道中的空气;3.完全润湿管路0.1615米/秒 1.52米/秒通常要求在容器内壁达到湍流的雷诺系数为大于2,000.核黄素(维生素B2)覆盖测试检查法:�把核黄素均匀涂布在设备内表面;�干燥;�按照预定的SOP启动CIP进行清洗;�干燥;�采用黑光灯检查;�合格标准:无核黄素残留,在黑光灯检查下无荧光。
2.5为了有效和可重复的清洗通常要求管路系统中的分叉口或交接口的L/D<2.0仪器形分叉口阀门形分叉口1. 清洁剂应能有效溶解残留物,不腐蚀设备,且本身易被清除。
2. 人用药品注册技术要求国际标准协调会(ICH)在“残留溶剂指南”中将溶剂分为3个级别,对其使用和残留限度有明确的要求。
3. 随着环境保护标准的提高,还应要求清洁剂对环境尽量无害或可被无害化处理。
4.满足以上要求的前提下应尽量廉价。
选择标准:�根据这些标准,对于水溶性残留物,水是首选的清洁剂。
不同批号的清洁剂应当有足够的质量稳定性。
因此不宜采用一般家用清洁剂,因其成分复杂、质量波动较大且供应商不公布详细组份。
使用这类清洁剂后,还会引起新的问题,即如何证明清洁剂的残留达到了标准?�因此,应尽量选择组份简单、成分确切的清洁剂。
根据残留物和设备的性质,企业还可自行配制成分简单效果确切的清洁剂,如一定浓度的酸、碱溶液等。
企业应有足够灵敏的方法检测清洁剂的残留情况,并有能力回收或对废液进行无害化处理。
制定SOP是清洁验证的先决条件;通常参照设备的说明书制定详细的规程,规定每一台设备的清洁程序,保证每个操作人员都能以可重复的方式对其清洗,并获得相同的清洁效果。
清洁规程的要点:�系统的拆卸;�预清洁;�清洁剂、浓度、溶液量,水质量;�时间、温度和频次、流速、压力;�消毒(消毒剂浓度、消毒方法、消毒剂用量);�装配:按说明书、示意图要求装配;�干燥:明确干燥的方式和参速;�检查:符合预定的标准。
1. 湍流的清洁速率大大大于层流的清洁速率;2. 盲管和垂直管道中的清洁液的速率要大于湍流所需的速率,通常要求大于1.52米/秒 (5英尺/秒);3. 在设备设计时需要考虑盲管的清洁问题,通常要求L/D<2.0;4. 喷林球的覆盖率检查;5. CIP清洗中避免设备底部的积水;6. 有效、可靠和反复的清洁要求湍流。
通常清洁分析方法验证包括取样方法验证和检验方法验证。
棉签取样方法的验证:取样过程需经过验证,通过回收率试验验证取样过程的回收率和重现性。
通常取样回收率和检验方法回收率结合进行,总回收率一般(企业可以根据实际情况确定)不低于70%,多次取样回收率的相对标准偏差应不大于20%。
棉签取样过程的验证实际上是对取样棉签、溶剂的选择、取样人员操作、残留物转移到取样棉签、样品溶出(萃取)过程的全面考察。
验证方法如下:①准备一块与设备表面材质相同的板材,如平整光洁的316L不锈钢板;②在钢板上划出100mm×100mm 的区域;③将5倍限度量的待检测物溶液,定量装入校验的微量注射器;④将其溶液尽量均匀地涂布在100mm×100mm 的区域内;⑤自然干燥或用电吹风温和地吹干不锈钢板;⑥用选定的擦拭溶剂润湿擦拭棉签,按下图所示进行擦拭取样;⑦重复以上规程3次;⑧将擦拭棉签分别放入棉签管中,加入预定溶剂5ml,超声;⑨用经验证的检验方法检验,计算回收率和回收率的RSD。
下图为棉签插试取样方法:第一步第二步通常淋洗法限度检查不需做回收率验证;定量检查应做回收率验证,可以利用淋洗溶剂冲洗已知量(在限度附近)的分析物确定回收率,回收率通常应不低于95%。
淋洗的取样方法为根据淋洗水流经设备的线路,选择淋洗线路相对最下游的一个或几个排水口为取样口。
分别按照微生物检验样品和化学检验样品的取样规程收集清洁程序最后一步淋洗即将结束时的水样。
淋洗法样品可对冲洗液直接检测也可对冲洗液做稀释后检测;无论直接检测还是稀释检测都应在接到样品后首先将样品同空白溶剂做视觉检查,确定是否有颜色差异和异物存在;如果有上述现象发生,可直接判定样品不合格。
通常设备的取样清洁验证中如何确定合适取样方法和取样点是验证方案的关键内容之一,必须由合适的理由来确认取样点,此取样点应能够代表设备的“最脏点”。
(1)取样方法的确认方法分为棉签直接表面擦拭、淋洗液冲洗和安慰剂取样。
擦拭取样的优点是能对最难清洁部位直接取样,通过考察有代表性的最难清洁部位的残留物水平评价整套生产设备的清洁状况。
通过选择适当的擦拭溶剂、擦拭工具和擦拭方法,可将清洗过程中未溶解的,已“干结”在设备表面或溶解度很小的物质擦拭下来。
检验的结果能直接反映出各取样点的清洁状况。
擦拭取样的缺点是很多情况下须拆卸设备后方能接触到取样部位,对取样工具、溶剂、取样人员的操作等都有一定的要求,总的来说比较复杂。
淋洗取样法为大面积取样方法,其优点是取样面大,对不便拆卸或不宜经常拆卸的设备也能取样。
因此其适用于擦拭取样不易接触到的表面,尤其适用于设备表面平坦、管道多且长的的生产设备。