锅炉引风机叶轮现场动平衡调试的技术应用
现场动平衡技术在风机检修中的应用

现场动平衡技术在风机检修中的应用摘要:现场动平衡技术是解决风机振动、保障风机连续稳定运行的好方法。
现场动平衡技术是对旋转机械进行振动测量和平衡校正的一种方法。
在振动测量和平衡校正时,旋转机械的转速、安装条件、支承条件和负载情况等与其工作状态相同或接近。
关键词:现场动平衡技术;风机检修;应用;该项技术在检修风机是的工作原理是:首先,需要采用安放试探质量来改变风机中转子的质量分布情况, 然后对其中轴承振动的大小以及相位变化进行全面测量,最后在采用试探质量来了解需要校正的位置, 然后通过动平衡技术来对风机设备进行维修。
一、现场动平衡故障的识别旋转机械在运行时发生故障的原因有很多, 安装不当以及人为破坏因素等都会使其发生运行故障。
但排除人为因素之外,75%的故障起因都是由转子不平衡而引起。
下面就转子不平衡因素对旋转机械运行的影响作详细介绍。
一般来说, 在校检某一设备的性能与质量时, 首要工作都是对设备进行故障判断, 识别出故障类型。
因此, 相关维修人员在进行风机检修时,要先检查风机设备的运行故障,依次排查转动设备的轴弯曲、部件松动以及轴裂缝等机械故障。
如果排查的结果显示为无,那么该设备可使用现场动平衡技术进行最后的性能校验, 如果排查结果为有, 则不可以。
事实上, 风机校验时, 只有在转子保持不平衡状态时才可利用动平衡技术对其进行校验, 并获得最佳的校验结果。
这是因为,当转子保持不平衡状态时,它将产生一个均匀的旋转力,但始终作用在径向方向。
因此,轴和支承轴承趋向于以某一圆周轨道运动。
然而由于轴承的垂直方向比水平方向刚性强.所以通常振动响应是一定程度的椭圆轨迹。
二、现场动平衡技术在风机检修中的应用1.相位及相位测量。
相位是相对于基准位置的量,是简谐振动的三要素之一。
从广义上讲,相位是指两个事件之间的时间差。
在旋转机械的振动测量中,相位是指键相脉冲与振动正峰值之间的时间差。
由基频振动的相位和转子的机械滞后角可以确定不平衡的角度。
论动平衡技术在风机检修中的应用分析

论动平衡技术在风机检修中的应用分析摘要:现场动平衡技术是解决风机振动问题,保证风机连续稳定运行的有效手段,是测量和校正旋转机械振动的一种方法。
旋转机械的转速、安装条件、支承条件和负载条件与其工作条件相同或接近。
关键词:现场动平衡技术;风机维护;实施;该技术对风机的工作原理是:首先调整风机中的试验质量,改变风机的质量分布,然后测量好轴承的振动和相位变化,最后利用试验质量了解需要修正的位置,然后对风机设备进行改进。
通过技术实现动态平衡。
一、现场动平衡破坏的确定旋转机器的故障有几个原因。
无缺陷安装和人为损坏因素导致运行故障,除人为因素外,转子不平衡造成75%的误差,下面详细介绍转子不平衡因素对与旋转机械相关的旋转机械运行的影响。
因此,在对风机进行维修时,有关维修人员应先检查风机故障,然后检查是否有轴弯曲、部件松脱、旋转故障等机械故障。
如果失效结果表明没有,设备可以使用现场动平衡技术来验证最终性能。
如果故障结果是肯定的,则不能这样做,动平衡技术只能在转子失去平衡的情况下对风机进行标定,才能达到最好的效果,这是因为转子失去平衡时,会产生均匀的旋转力,但它总是在径向工作,因此,竖井和营地往往在一个圆形轨道上移动,但由于垂直方向的刚性,振动响应通常有些椭圆。
二、风机维护现场动平衡的应用1.相位和相位测量。
相位是与参考位置成比例的量,这是在元件的三次简谐振动的e上,广义上,相位是指两个事件之间的时间差,在测量旋转机械的振动时,相位是指键相脉冲和正振动峰值之间的时间差。
实际中最重要的是测量基频振动相位,为了测量一个事实,必须在转子轴上使用反射带,并且必须提供一个传感器(称为键相器)来接收参考信号。
当反射带通过键相器时,它通过键相发出脉冲信号。
将脉冲与1倍谐波信号第一正峰值之间的时间间隔定义为反射带通过关键相位时的相位,将周期时间分成360等分,称为360-o,相位单位表示为公式o。
自键相脉冲到第一个正峰值开始的时间已经过了1/8旋转周期。
风机现场动平衡技术在烧结厂的应用.论文doc
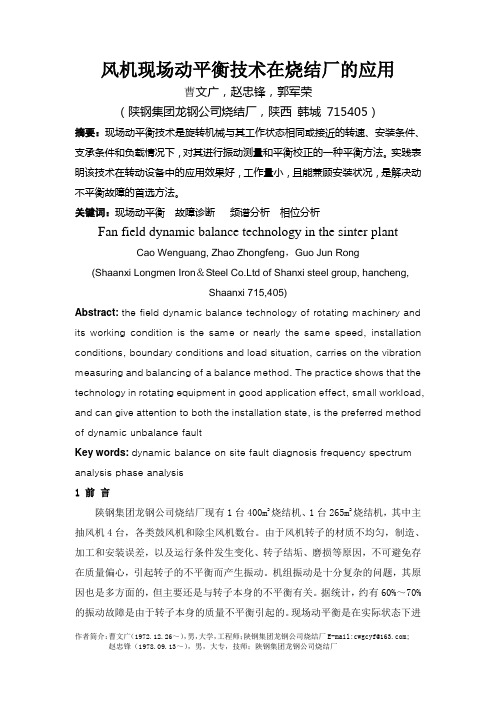
风机现场动平衡技术在烧结厂的应用曹文广,赵忠锋,郭军荣(陕钢集团龙钢公司烧结厂,陕西韩城 715405)摘要:现场动平衡技术是旋转机械与其工作状态相同或接近的转速、安装条件、支承条件和负载情况下,对其进行振动测量和平衡校正的一种平衡方法。
实践表明该技术在转动设备中的应用效果好,工作量小,且能兼顾安装状况,是解决动不平衡故障的首选方法。
关键词:现场动平衡故障诊断频谱分析相位分析Fan field dynamic balance technology in the sinter plantCao Wenguang, Zhao Zhongfeng,Guo Jun Rong (Shaanxi Longmen Iron&Steel Co.Ltd of Shanxi steel group, hancheng,Shaanxi 715,405)Abstract:the field dynamic balance technology of rotating machinery and its working condition is the same or nearly the same speed, installation conditions, boundary conditions and load situation, carries on the vibration measuring and balancing of a balance method. The practice shows that the technology in rotating equipment in good application effect, small workload, and can give attention to both the installation state, is the preferred method of dynamic unbalance faultKey words:dynamic balance on site fault diagnosis frequency spectrum analysis phase analysis1 前言陕钢集团龙钢公司烧结厂现有1台400m2烧结机、1台265m2烧结机,其中主抽风机4台,各类鼓风机和除尘风机数台。
动平衡仪在转炉一次除尘风机中的应用
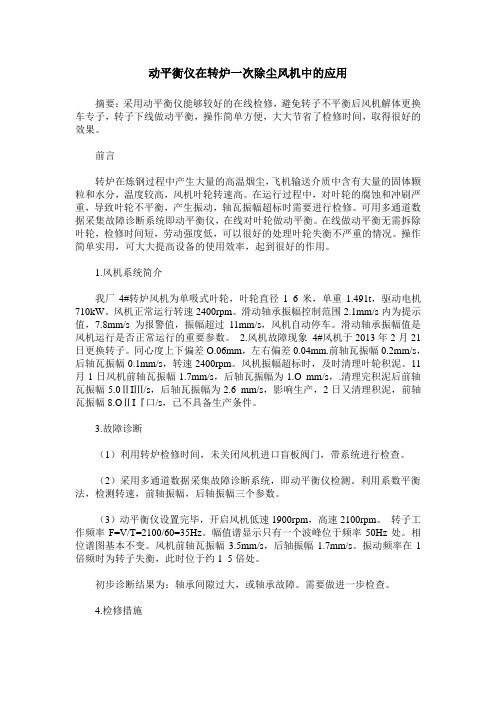
动平衡仪在转炉一次除尘风机中的应用摘要:采用动平衡仪能够较好的在线检修,避免转子不平衡后风机解体更换车专子,转子下线做动平衡,操作简单方便,大大节省了检修时间,取得很好的效果。
前言转炉在炼钢过程中产生大量的高温烟尘,飞机输送介质中含有大量的固体颗粒和水分,温度较高,风机叶轮转速高。
在运行过程中,对叶轮的腐蚀和冲刷严重,导致叶轮不平衡,产生振动,轴瓦振幅超标时需要进行检修。
可用多通道数据采集故障诊断系统即动平衡仪,在线对叶轮做动平衡。
在线做动平衡无需拆除叶轮,检修时间短,劳动强度低,可以很好的处理叶轮失衡不严重的情况。
操作简单实用,可大大提高设备的使用效率,起到很好的作用。
1.风机系统简介我厂4#转炉风机为单吸式叶轮,叶轮直径1_6米,单重1.491t,驱动电机710kW。
风机正常运行转速2400rpm。
滑动轴承振幅控制范围2.1mm/s内为提示值,7.8mm/s为报警值,振幅超过11mm/s,风机自动停车。
滑动轴承振幅值是风机运行是否正常运行的重要参数。
2.风机故障现象4#风机于2013年2月21日更换转子。
同心度上下偏差O.06mm,左右偏差0.04mm.前轴瓦振幅0.2mm/s,后轴瓦振幅0.1mm/s,转速2400rpm。
风机振幅超标时,及时清理叶轮积泥。
11月1日风机前轴瓦振幅1.7mm/s,后轴瓦振幅为1.O mm/s,.清理完积泥后前轴瓦振幅5.0ⅡIⅢ/s,后轴瓦振幅为2.6 mm/s,影响生产,2日又清理积泥,前轴瓦振幅8.OⅡI『口/s,已不具备生产条件。
3.故障诊断(1)利用转炉检修时间,未关闭风机进口盲板阀门,带系统进行检查。
(2)采用多通道数据采集故障诊断系统,即动平衡仪检测。
利用系数平衡法,检测转速,前轴振幅,后轴振幅三个参数。
(3)动平衡仪设置完毕,开启风机低速1900rpm,高速2100rpm。
转子工作频率F=V/T=2100/60=35Hz。
幅值谱显示只有一个波峰位于频率50Hz处。
如何应用动平衡仪作现场高速动平衡处理风机振动超限问题

如何应用动平衡仪作现场高速动平衡处理风机振动超限问题来源:亚泰光电风机轴承大幅振动会引起安装基础破坏、风机损坏事故。
五阳热电厂曾发生过一起引风机振动大造成风机损坏报废事故,造成锅炉停运。
该厂采用先进的YBD现场动平衡仪快速、有效地对引风机作高速动平衡,取得了成功,并在实际应用中不断完善、创新。
风机在线振动监测与报警系统的设计方案为:在引风机轴承座上安装水平与垂直方向上的振动探头,探头输出的振动信号接入YBD现场动平衡仪中,使运行人员能在线连续监视引风机振动状况,再将监视仪报警输出触点信号分别接入微机闪光报警仪与电铃回路中,实现了光字牌与电铃发声报警功能,将该系统安装并调试好后投入使用。
应用风机在线监测系统后减少了运行人员工作量,提高了引风机监控质量。
当风机振动超出限制范围后,报警功能可提醒运行人员作出正确判断,及时处理故障,保证了引风机与锅炉的正常安全运行。
当风机振动超限停运后,用动平衡仪对引风机作动平衡试验,找出其不平衡点,经过计算后进行配重,可降低引风机振动值到正常范围内,快速有效地解决了引风机振动超限问题,消除了安全隐患,延长了风机运行周期。
此项试验成功后,将其推广至锅炉一、二次风机,也获得了成功。
1 风机振动在线连续监测与报警系统的应用用现场动平衡仪在水平与垂直两个方向上监视轴承的径向振动。
经验表明,风机轴承座振动幅度最大,在风机叶轮侧轴承座的水平方向与电机侧轴承座的垂直方向上安装速度传感器,速度传感器输出电压正比于振动速度值,输出电压进入振动监测仪,经放大后驱动表头,显示振动速度值,供运行人员监视。
现场动平衡仪具有报警(报警1)与危险(报警2)输出功能,当风机振动幅值超过所设定的报警或危险值时,通过报警比较器(或危险比较器)驱动报警(或危险)继电器工作,将报警继电器的一组常开触点接入微机闪光报警仪光字牌报警回路,危险继电器的一组常开触点接入电铃报警回路,实现了风机振动超限的声光报警,提醒运行人员在风机振动超限时迅速作出正确判断与操作。
循环流化床锅炉引风机的现场动平衡
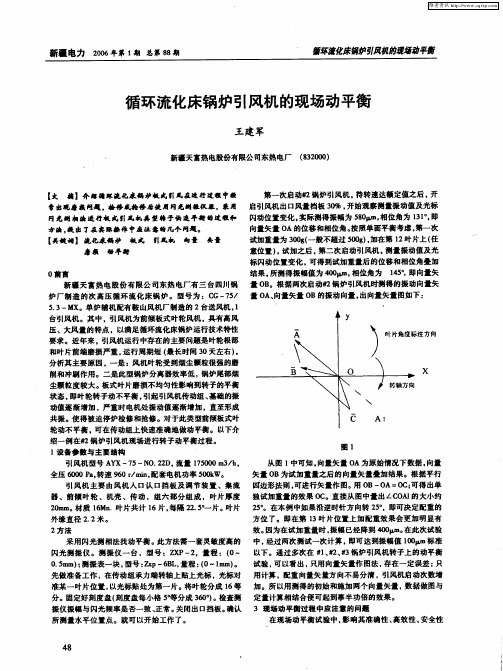
0前 育
结果 。 所测得振幅值为 4 0 ̄ 。 0 1a 相位角为 15, 4  ̄ 即向量矢
B I 2锅炉弓风机时测得 的振动 向量矢 I 新疆天 富热 电股份有限公 司东热 电厂 有三 台四川 锅 量 O 。根据两次启动| _ A、 B的振动 向量 。 出向量矢量 图如下 : 炉 厂制造 的次 高压 循环流 化床锅 炉 。型 号为 :C G一7 / 量 O 向量矢量 O 5 5 3一V . lX。单炉辅机配有鞍山风机厂制造 的 2台送 风机 。 l 1 台弓风机 。其 中。引风机为前倾板式叶轮风机 。具有高风 I
闪光测振仪 。测 振仪一 台 ,型号 :Z P一 。量程 :( — X 2 0 以下。通过多次在 嚣 、2 嚣 1 嚣 、 3锅炉 引风机转子上 的动平衡 05 m) 测振表一块 , .m ; 型号 :x Zp一6 L 量程 : 0一l m) B, ( m 。
先做 准备工作 ,在传动组承力端转轴上贴上光标 ,光标对 用计算 ,配重 向量矢量方向不易分清 ,弓风机启动次数增 I 准某一叶片位置 , 以光标贴处为第一片。将叶轮分成 1 等 加 。所以用测得 的初始和施加两个 向量矢量 , 6 数据做图与
48
维普资讯
新疆 电力
20 年第1 总第 8 期 06 期 8
输 电线路的合成绝缘子 防风闪问题
张
新疆 电力设计院
鹏
( 乌鲁木齐 8 0 0 ) 30 2
【 文
. 0 操作过电压 14 m, . 5 工频电压 冀 】 分析脊 电残球发 生风 闪l 的多种原 因,介囊 了残 2 0 V, 2 k 雷电过 电压 19 m。
维普资讯
大连锅炉风机叶轮动平衡

大连锅炉风机叶轮动平衡的重要性及其应用在工业生产中,锅炉风机作为关键设备之一,其性能和稳定性对于整个生产流程具有至关重要的作用。
而在锅炉风机的运行过程中,叶轮作为核心部件,其动平衡性能的好坏直接影响到风机的运行效率和稳定性。
特别是在大连这样的工业城市,锅炉风机的运行对于各个行业的生产都起着至关重要的作用。
因此,本文将重点探讨大连锅炉风机叶轮动平衡的重要性、实现方法以及实际应用。
一、大连锅炉风机叶轮动平衡的重要性锅炉风机叶轮在运行过程中,如果动平衡性能不佳,会导致叶轮产生振动,进而影响到整个风机的运行。
这种振动不仅会产生噪音,还会加速叶轮的磨损,降低风机的使用寿命。
更为严重的是,长期的振动还可能导致叶轮出现裂纹或断裂,从而引发安全事故。
因此,确保大连锅炉风机叶轮的动平衡性能,对于保障风机的稳定运行、提高生产效率以及确保生产安全都具有重要意义。
二、大连锅炉风机叶轮动平衡的实现方法要实现大连锅炉风机叶轮的动平衡,首先需要对叶轮进行精确的测量,确定其不平衡量和不平衡位置。
然后,根据测量结果,对叶轮进行配重或去重处理,使其达到动平衡的要求。
在配重或去重过程中,需要选择合适的配重材料或去重方法,确保处理后的叶轮能够满足动平衡的要求,并且不会对叶轮的性能产生不良影响。
三、大连锅炉风机叶轮动平衡的实际应用在实际应用中,大连的许多工业企业都对锅炉风机叶轮的动平衡给予了高度重视。
他们不仅定期对叶轮进行动平衡检测和处理,还在风机的设计和制造过程中,注重提高叶轮的动平衡性能。
例如,一些企业采用了先进的叶轮设计理念和制造工艺,使叶轮在制造过程中就具有较好的动平衡性能。
此外,他们还通过优化风机的结构和运行参数,降低叶轮在运行过程中产生振动的可能性,从而进一步提高了风机的运行稳定性和使用寿命。
四、大连锅炉风机叶轮动平衡的未来展望随着科技的不断发展,大连锅炉风机叶轮动平衡技术也将不断进步。
未来,我们可以期待更加精确的测量方法和更高效的配重或去重技术的出现,使叶轮的动平衡性能得到进一步提升。
三点法找动平衡在大型风机上的应用

作 图直接找 出不平衡 位置的轻 点。在操作过程 中, 要 坚持理论联 系实际 , 尊 重客观规律 , 使之在 大型风机上更好地应用。
关键词 : 三 点 法动 平 衡 ; 试加重量 ; 平衡 点 ; C A D作 图 ; 应用
现场动平衡技术在生产中的应用

引风机 组为例加 以论述 ( 为现场动 平衡校验测试简 2 现场动平衡校验 图1 . 2
图)。
2 . 停 机状态 下在联 轴器轮 毂处 贴鉴相 片 ,标 出相 .1 2
位 角 。在3 测 点水 平方 向放置加 速度传 感器 。从观 察 群 孔 中沿风机 旋转方 向,在 叶轮筋 板上做 标记 ,即统 计 出总叶片数为1片( ) 2 图4 。 2 . 启 动风机 ,待转速 平稳 后 ,测量 初始振 动值及 .2 2
维普资讯
T ech n ca
E xc ange h
测 6 试
现场动平衡技术在生产中的应用
旭 李建辉/ 天津大学
1 概述
6 lm) 0a ( 该机 组 的测点位 置布置简 图见 图1。通过振动 )
现 场动平衡 技术是旋转机 械在 工作状态下 ,对其 测试及 频谱 分析发 现 :( 水平振 动大 于垂直振 动 ,振 1 )
= 3 。) 2 5 ,处 即位 置8 和位 置9 中间 。开机 后3} 点处振 j f j 测
动值为3 m, 残余不 平衡质量和相位 分别 为一0 g 2 1 . 和 7
23 校验后结果: .
嘲6
现场动平衡校验结果见表 1 和图5 。
32 频谱分析 .
转子 不平衡状 态 的现6 lm和8 。( 9 即位置4 。 )
DP1 o 5 o
223 停 机 ,打 开观 察孔 ,将 9 g 重块 点焊 在 位置 .. 4试 4 ̄ 叶轮 前盘棱 缘处) (l J ,盖好观 察孔 。开机 ,待 转速平
图1
21 振 动控制及故障诊断 .
衡校验 效果好 ,工作 量小 ,且能兼顾 安装状 况 ,是解
量 ,轴 承 故障亦可 排除 。经相位 分析发现 :垂直 和水 平方 向相位 相差9 。。结论 为叶轮 磨损 不匀造 成的不 0 平衡 故障。
影响系数法在引风机现场动平衡中的分析与应用

影响系数法在引风机现场动平衡中的分析与应用摘要:本文旨在深入探讨影响系数法在引风机现场动平衡中的分析与应用。
本文概述了对影响系数进行前期预测的原理和方法,并通过实例说明了影响系数法在引风机现场动平衡中的应用及优势。
研究表明,采用影响系数法分析引风机现场动平衡问题,可以从多个方面解决动平衡问题,大大提高工作效率、节省时间和成本。
关键词:影响系数法;引风机;现场动平衡正文:引风机的现场动平衡是一项极其重要的任务,它必须保证引风机的运转稳定性和振动是否超出预定的范围,例如Vibration Severity指标(VS)。
因此,需要对引风机现场动平衡进行及时有效的分析和处理,以确保引风机的稳定性和可靠性。
影响系数法是对引风机现场动平衡中常用的一种分析方法,它可以有效预测并分析引风机振动,从而更好地控制引风机现场动平衡。
首先,影响系数通过测量现场的动平衡条件来计算,然后根据实际动平衡情况,通过调整影响系数来优化实际的动平衡条件,并且可以估算出预期的振动水平。
本文从理论和实践的角度深入探讨了影响系数法在引风机现场动平衡中的分析与应用。
实例说明,影响系数法可以有效解决现场动平衡问题,同时可以大大提高工作效率、节省时间和成本。
综上所述,本文介绍了影响系数法在引风机现场动平衡中的应用,并指出了其优势和局限性,为引风机运行安全提供可靠的技术保障。
影响系数法也可以用于现场动平衡的优化,以改善当前系统的性能。
首先,通过计算动平衡条件下的影响系数,可以快速准确的判断系统的动平衡状态。
同时,可以通过改变影响系数来达到优化系统的目的,从而有效抑制振动噪声。
此外,影响系数法还可以用于风扇的在线检测和诊断,它可以实时监测风扇的运行状况,从而定位和解决存在的动平衡问题。
另外,通过影响系数法,可以准确掌握风扇轴承状态,从而实现及时更换轴承和轴承维护,保持风扇的正常运转状态。
总之,影响系数法是一种高效的引风机现场动平衡分析与应用方法,它可以从多种方面解决动平衡问题,有助于风扇的快速、准确的动平衡,大大提高工作效率、节省时间和成本,确保风扇的可靠运行。
风机现场动平衡仪的使用技术

风机现场动平衡仪的使用技术
风机现场动平衡仪的使用技术包括以下几个方面:
1. 选择合适的仪器:在使用风机现场动平衡仪之前,需要根据实际情况选择合适的仪器。
通常应选择精度高、稳定性好的仪器,以确保测试的准确性和可靠性。
2. 安装仪器:将仪器正确地安装在要测试的风机上,一般需要将仪器的传感器与风机的旋转轴对应位置相连接,并确保连接牢固。
3. 连接电源:将仪器连接到电源,启动仪器,检查仪器的状态是否正常,并校准仪器的零点。
一般情况下,仪器会有相应的使用说明书,可以根据说明书进行连接和校准。
4. 进行测试:按照仪器的要求进行测试,一般包括两个步骤:静态平衡测试和动态平衡测试。
- 静态平衡测试:启动风机,观察仪器显示的振动情况。
根据振动大小和位置,判断风机是否存在不平衡。
- 动态平衡测试:根据静态平衡测试的结果,在风机上进行相应的校正,以达到平衡状态。
可通过增加或减少平衡铁块的方法,或者调整风机的刀片角度等方式来进行校正。
5. 验证测试:在调整完风机的平衡后,再次进行测试,以验证平衡效果。
如果风机振动明显减少,且在允许范围内,则说明
平衡调整成功。
6. 记录和分析数据:在测试过程中,应及时记录测试数据,并进行分析。
可以通过数据分析来确定不平衡的原因,并采取相应的措施进行改善。
以上是风机现场动平衡仪的使用技术的一般步骤,具体的操作方法和注意事项还需要根据具体的仪器和实际情况进行调整。
分析风机检修中现场动平衡技术的应用

分析风机检修中现场动平衡技术的应用摘要:运动中的转子出现不平衡现象是必然的,特别是一些高速运转的机械振动,都是因为转子的不平衡,这也将影响机械的正常运转。
因此,解决转子不平衡问题是消除机械振动的一项重要措施。
过去采用转子离机平衡,利用专门的机器进行平衡校对,但是这样的操作方法需要对机械进行拆装,在加大施工难度的同时也可能会影响被检测器械的精度。
而目前应用较广的现场动平衡技术便可以很好的避免这些难题。
本文针对风机检修中现场动平衡技术的应用进行简要分析。
关键词:风机;检修;现场动平衡技术;应用风机的使用在石化行业生产中占据着重要的地位,一旦风机出现问题,将对生产有重大的影响,更严重影响车间工人的人身安全,所以一旦振动问题应该引起重视。
导致风机的振动故障,包括不平衡,宽松,接触地面,如旋转失速、不平衡振动的主要原因。
我们风机失衡的原因分析,总结了现场动态平衡的常用方法,并介绍了其操作。
另外我们总结了现场动平衡和经验,和常见的问题,希望能给现场动平衡技术的实现提供一定的指导和帮助。
1风机不平衡原因风机和电动机组成的转子系统,由于风扇在使用过程中,粘泥掉落,一定程度上是由于叶轮叶片的磨损,叶轮和轴转子装配很容易出现不均匀点,质量和质心偏移量的超标问题。
此时整个转子系统扭转旋转轴,质量的不均匀分布产生离心力。
对转子的不平衡离心力影响轴承产生剧烈振动,加速轴承磨损,降低轴承的使用寿命,增加功率损耗,影响机械精度和相邻的正常功能,产生大量噪音,增加了操作员的负担,严重时会造成设备事故。
2风机现场动平衡方法方法动态平衡方法包括动态平衡机平衡,整个动态平衡方法和在线动平衡方法。
平衡法的动态平衡机把需要校正转子动平衡机,这就需要特殊的动平衡机。
动平衡机操作条件和实际生产情况产生区别。
对于较大的转子、拆装、运输是很困难的。
在线动平衡结构是复杂的,平衡模块控制精度要求高、价格低等优点。
考虑动态平衡的效率和可行性和大型风扇转子的结构特点,整个动态平衡是最简单、实用,可实现高速动平衡,满足的需求平衡。
风机叶轮现场动平衡服务具体操作步骤
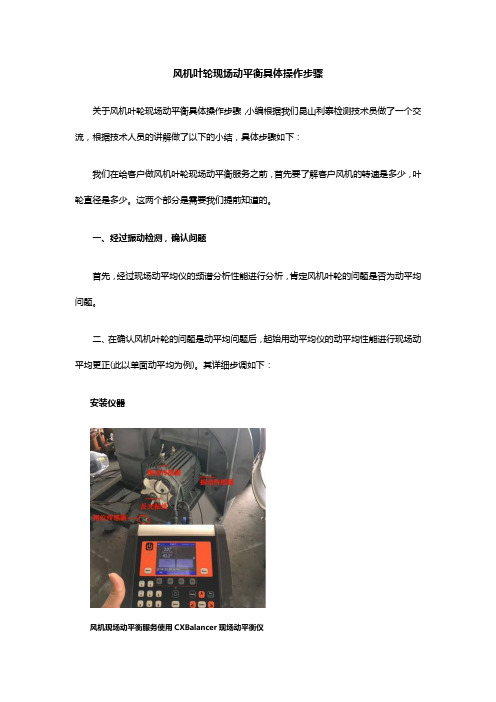
风机叶轮现场动平衡具体操作步骤关于风机叶轮现场动平衡具体操作步骤,小编根据我们昆山利泰检测技术员做了一个交流,根据技术人员的讲解做了以下的小结,具体步骤如下:我们在给客户做风机叶轮现场动平衡服务之前,首先要了解客户风机的转速是多少,叶轮直径是多少。
这两个部分是需要我们提前知道的。
一、经过振动检测,确认问题首先,经过现场动平均仪的频谱分析性能进行分析,肯定风机叶轮的问题是否为动平均问题。
二、在确认风机叶轮的问题是动平均问题后,起始用动平均仪的动平均性能进行现场动平均更正(此以单面动平均为例)。
其详细步调如下:安装仪器风机现场动平衡服务使用CXBalancer现场动平衡仪在风机设备停机的形态下,在转动部位上贴上一小块反光贴纸(约为1cm2);将振动传感器吸在电机轴承部位,相位计传感器架于磁性座之上,使其激光打到反光贴纸上。
安装表示图如下:三、进行动平均更正确认仪器安装好之后,开启风机,在风机抵达正常工作转速之后,进入动平均仪的动平均性能界面,点击试运转性能后,按肯定键起始进行丈量风机叶轮的初始振动值和相位。
待数据安稳后进行保存并使风机停机。
四、安装试重螺丝肯定叶轮停止以后,在叶轮上任意位置经过打孔锁螺丝或许焊接的方法加一个称好分量的试重(根据风机叶轮分量选择合适分量的试重);并将分量输入到动平均仪中;从头开启风机并进行二次丈量振动及相位;待保存后,动平均仪上能够自动计算出其应加配重的角度和分量。
试加分量的角度不妨由相位和滞后角肯定:五、安配备重螺丝先使风机处于停机形态,先取下试重,而后根据CXBalancer动平均仪上计算的后果,以安装试重螺丝的位置为0度,转动目标的反目标角度来安装称好的配重螺丝。
六、检查更正后果再次开启风机,丈量安配备重后的振动值和角度,根据ISO-1940动平均准则进行对比,看是否符合准则,若符合,则这次动平均完毕,若不符合准则,则根据动平均仪二次的计算后果反复“安配备重螺丝”这一步调,直到符合准则为止。
现场动平衡技术在风机检修中的运用

现场动平衡技术在风机检修中的运用发表时间:2018-08-06T15:29:49.463Z 来源:《电力设备》2018年第12期作者:吕伟周[导读] 摘要:在风电场中拥有数量较多的风机设备,其在运行中最常见的故障就是振动故障,且容易引发其他类型的故障。
(国华瑞丰(荣成)风力发电有限公司山东省威海市 264300)摘要:在风电场中拥有数量较多的风机设备,其在运行中最常见的故障就是振动故障,且容易引发其他类型的故障。
对于由于转子不平衡原因而引起的振动问题,文章提出了采用现场动平衡技术进行振动故障检修的方法,并对现场动平衡故障识别,以及应用现场动平衡技术进行风机振动故障检修的具体策略进行分析,以实际案例介绍此技术在风机检修中的应用情况,以供参考。
关键词:现场动平衡技术;风机;检修1引言近年来随着全球经济的快速发展,全球资源紧缺和环境恶化问题不断加剧,各国在不断进行能源结构调整以及加大对清洁型能源的开发和利用之外,也提出了节能减排的各项措施来应对以上问题。
我们地域辽阔,具有丰富的风能,近年来我国也加大了对风能的开发力度,风电场的装机容量和建设规模不断增加。
风机是企业中的常用设备,有的企业中各类风机多达上百台,少的也有几十台。
在设备运行时因叶轮不平衡而引起的风机振动时有发生,由此带来的风机检修必将在很大程度上影响生产系统的连续稳定运行。
在风电场发电机组的运行中,存在数量较多的风机设备,且在风电场中具有重要的作用。
但是风机在长时间的运行过程中极易出现振动故障,而且由于在长时间运行中出现磨损或结垢而导致风机运行失衡,对整个发电系统的正常运行造成不良影响。
在目前的风电场风机运行中,最常用的风机振动故障检修方法就是现场动平衡技术,此技术不仅能够对风机的故障进行快速检测,而且能够实现现场校正,大大提高了风机运行的稳定性,为确保风电场发电系统的运行效率起到重要作用。
2现场动平衡技术概述现场动平衡技术是基于风机故障解决而开发出的专门的应用型技术,其主要作用就是对类似风机类型的旋转类机械设备进行振动测量和平衡校正,从而对风机类设备的振动故障以及不平衡的问题进行有效解决,确保风机类设备的连续运行。
大型风机三点动平衡找轻点的探索与应用

重块焊接点的角度
转θ,如图1)。
3 三点法动平衡找叶轮轻点现状
贵冶需要在现场完成动平衡的大型风机遍布全厂各个车间。
目前主要使用焊接配重方式,即在叶轮较轻一侧焊接等重
将卸扣横销用相同型号全丝螺杆代替,从有丝扣一端旋进,将叶轮卡在U型环中间,压紧后旋紧螺杆,将卸扣固定在叶片上,卸扣及等同于配重块。
效果分析
用卸扣代替焊接配重找轻点,拆卸方便、快捷,不会对叶轮造成损伤,通用性强,市场上卸扣易于购买且价格便宜,重量易控制。
目前已广泛应用于我厂大型风机现场动平衡上,实用效果得到了各车间一致肯定。
现场动平衡技术在生产中的应用
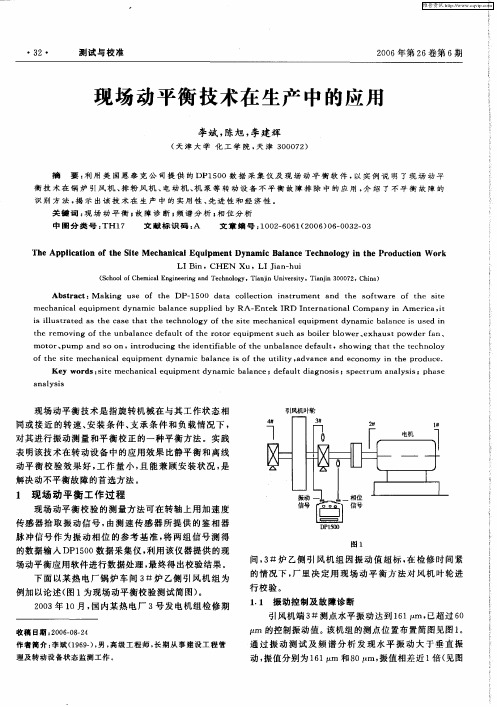
现 场动 平衡 技 术 是 指旋 转机 械 在 与其 工 作状 态 相 同或 接 近 的转 速 、 安装 条 件 、 承 条 件 和 负 载情 况 下 , 支 对 其进 行 振动 测 量 和平 衡校 正 的 一种 平衡 方 法 。实 践 表 明该 技 术在 转 动设 备 中的应 用效 果 比静 平衡 和离 线 动 平 衡 校 验 效 果 好 , 作 量 小 , 能 兼 顾 安 装状 况 , 工 且 是 解 决动不 平衡 故 障的首 选方 法 。
m e ha c l e i m e t d na i al nc u le y RA — c ni a qu p n y m c b a e s pp i d b Ent k I e RD nt r a i a m p ny i m e i a.t I e n ton lCo a n A r c i
i lus r t d a he c s h t t e h l gy o he s t e h ni a q pm e na i a a e i e n s il t a e s t a e t a he t c no o f t ie m c a c le ui ntdy m c b l nc s us d i t e ov n f t nb l nc e a l f t e r or e i m e t s c s b l r b o e 、 xh us ow d r f n、 he r m i g o he u a a e d f u t o h ot qu p n u h a oi l w r e a t p e e a moo 、 t r pum p a d s n,i r du i g t d nt fa e o he u al nc e a t n o o nt o c n he i e ii bl f t nb a e d f ul ,s o i ha h e hn oy h w ng t t t e t c ol
影响系数法在引风机现场动平衡中的分析与应用

燃 料 在锅 炉 内燃烧 , 生 高温 高压蒸 汽 , 产 蒸汽 在 汽轮机 内膨胀 做功 , 动汽 轮机 旋转 , 轮机再 带 动 推 汽 发 电机 发 电 。上 述 过程 首先 锅炉 将燃 料 的化学 能 转
化 为蒸 汽 的热能 , 后汽 轮机 将热 能转 化 为机 械能 , 然
其 中影 响 系数法 是 一 种 运算 方 法 简 单 , 理 意 义 明 物
= —
引风机 工作 时 , 子 的转 动 存 在 由不平 衡 质量 转 产 生 的离 心力 , 该力 引起 转 子 的振 动 , 并通 过支 撑 转 子 的轴 承 向外传 递 , 得 整 个 引 风 机 在 工作 过程 中 使
产 生振 动 。当振 动 值 在 规定 的 范 围 内 时 , 会 影 响 不 风机 的 正常工 作 ; 当不 平 衡 离 心 力增 大 到一 定 限值 后 , 子会 产 生很 大 的振 动 。 这 时振 动 不 仅 会 影 响 转 引风机 的正常 工作 , 而且 还 会 引发如 轴 承磨损 、 子 转 断裂 、 叶轮 甩 出等 一 系列严 重后 果 , 电厂 的安全 生 给
I B
—
—
l f l
Ⅱ
动平衡方法将其残余不平衡质量减少 , 以使其残余
振 动小 于规 定 的值 。
图 1 双 面 动 平 衡 的测 点 与配 重 面
2 在 I— I面上 加试 重 , 同一 平衡 转 速 ) 在
l 理论分析
目前 , 已研 究 出多 种 进 行 转 子 动 平 衡 的 方 法 。
至平 衡转 速 , 出轴 承 的初 始基 频水 平振 动 。 测 2 在 平 衡 面 上 加 试 重 , 同 一 平 衡 转 速 ) 在 下 , 得轴 承 的一次 基频 水平 振 动 。 测 3 计 算试 重 对测 点 的影 响系数 )
大型引风机叶轮的动平衡问题及对策

大型引风机叶轮的动平衡问题及对策大型引风机叶轮的动平衡问题及对策一、叶轮产生不平衡问题的主要原因叶轮在使用中产生不平衡的原因可简要分为两种:叶轮的磨损与叶轮的结垢。
造成这两种情况与引风机前接的除尘装置有关,干法除尘装置引起叶轮不平衡的原因以磨损为主,而湿法除尘装置影响叶轮不平衡的原因以结垢为主。
现分述如下。
1.叶轮的磨损干式除尘装置虽然可以除掉烟气中绝大部分大颗粒的粉尘,但少量大颗粒和许多微小的粉尘颗粒随同高温、高速的烟气一起通过引风机,使叶片遭受连续不断地冲刷。
长此以往,在叶片出口处形成刀刃状磨损。
由于这种磨损是不规则的,因此造成了叶轮的不平衡。
此外,叶轮表面在高温下很容易氧化,生成厚厚的氧化皮。
这些氧化皮与叶轮表面的结合力并不是均匀的,某些氧化皮受振动或离心力的作用会自动脱落,这也是造成叶轮不平衡的一个原因。
2.叶轮的结垢经湿法除尘装置(文丘里水膜除尘器)净化过的烟气湿度很大,未除净的粉尘颗粒虽然很小,但粘度很大。
当它们通过引风机时,在气体涡流的作用下会被吸附在叶片非工作面上,特别在非工作面的进口处与出口处形成比较严重的粉尘结垢,并且逐渐增厚。
当部分灰垢在离心力和振动的共同作用下脱落时,叶轮的平衡遭到破坏,整个引风机都会产生振动。
二、解决叶轮不平衡的对策1.解决叶轮磨损的方法对干式除尘引起的叶轮磨损,除提高除尘器的除尘效果之外,最有效的方法是提高叶轮的抗磨损能力。
目前,这方面比较成熟的方法是热喷涂技术,即用特殊的手段将耐磨、耐高温的金属或陶瓷等材料变成高温、高速的粒子流,喷涂到叶轮的叶片表面,形成一层比叶轮本身材料耐磨、耐高温和抗氧化性能高得多的超强外衣。
这样不仅可减轻磨损造成叶轮动平衡的破坏,还可减轻氧化层产生造成的不平衡问题。
选用引风机时,干式除尘应优先选用经过热喷涂处理的叶轮。
使用中未经过热喷涂处理的叶轮,在设备维修时,可考虑对叶轮进行热喷涂处理。
虽然这样会增加叶轮的制造或维修费用,但却提高叶轮的使用寿命l~2倍,延长了引风机的大修周期。
锅炉引风机叶轮的静平衡就地校正
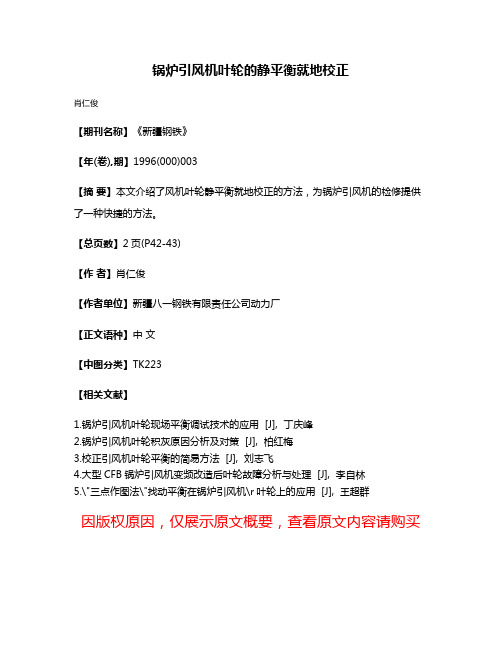
锅炉引风机叶轮的静平衡就地校正
肖仁俊
【期刊名称】《新疆钢铁》
【年(卷),期】1996(000)003
【摘要】本文介绍了风机叶轮静平衡就地校正的方法,为锅炉引风机的检修提供了一种快捷的方法。
【总页数】2页(P42-43)
【作者】肖仁俊
【作者单位】新疆八一钢铁有限责任公司动力厂
【正文语种】中文
【中图分类】TK223
【相关文献】
1.锅炉引风机叶轮现场平衡调试技术的应用 [J], 丁庆峰
2.锅炉引风机叶轮积灰原因分析及对策 [J], 柏红梅
3.校正引风机叶轮平衡的简易方法 [J], 刘志飞
4.大型CFB锅炉引风机变频改造后叶轮故障分析与处理 [J], 李自林
5.\"三点作图法\"找动平衡在锅炉引风机\r叶轮上的应用 [J], 王超群
因版权原因,仅展示原文概要,查看原文内容请购买。
- 1、下载文档前请自行甄别文档内容的完整性,平台不提供额外的编辑、内容补充、找答案等附加服务。
- 2、"仅部分预览"的文档,不可在线预览部分如存在完整性等问题,可反馈申请退款(可完整预览的文档不适用该条件!)。
- 3、如文档侵犯您的权益,请联系客服反馈,我们会尽快为您处理(人工客服工作时间:9:00-18:30)。
锅炉引风机叶轮现场动平衡调试的技术应用
锅炉引风机由于长期处于高温及高尘的工作环境,容易导致叶轮在运转过程中变形,从而使得引风机工作中产生振动从而轴承的疲劳,严重影响设备的正常运行,因此在平时引风机检修过程中要对叶片进行平衡校正处理,本文根据个人在工作中的经验简单介绍锅炉引风机叶轮现场平衡调试的方法,供各位同仁交流。
标签:锅炉引风机;动平衡调试;三点法
1 引风机产生不平衡的原因分析
1.1 风机叶轮磨损及氧化
锅炉引风机的工作环境中会伴随着大量颗粒粉尘,粉尘颗粒伴随着高速流动和高温的气体通过引风机的叶轮,从而使得引风机叶轮在工作中不断的冲刷,长期如此在叶轮的工作面处形成刀刃状的磨损,就会产生常见的叶片有薄厚不均匀,造成风机叶轮的不平衡。
另外,由于高温潮湿的环境会加速风机叶轮的氧化,氧化是不均匀分布,导致叶轮不平衡。
1.2 风机叶轮上产生污垢
由于锅炉引风机工作环境潮湿而伴随这大量的粉尘,而且经过高温气体的作用,很容易使粉尘被吸附在叶轮的非工作面上,长期积累会在非工作面上形成比较严重的粉尘结垢,并且是逐渐的增厚。
随着叶轮的得转动,部分尘垢会因离心力和振动脱漏,导致叶轮平衡不稳定,影响风机平衡。
2 锅炉引风机叶轮现场动平衡调试的方法
在实际的维护工作中,锅炉引风机叶轮平衡调试中常见的方法为三点作图法,因其操作简单,外界影响因素小,因此在实际工作中显得更加有效,成功率高。
下面就简单介绍下三点作图法的具体操作过程:
2.1 三点作图法现场动平衡调试步骤
2.1.1 确定初始最大振幅A0
在风机轴承水平方向上用测振表测得最大初始振幅A0
2.1.2 将刚性转子分为三等分,别且标记为A、B、C。
(如下图1所示)
2.1.3确定风机叶轮动平衡试加配重块质量G。
G=(150*ll*G1)/(r1*n/300)2)
G-试加重量(g);G1-转子重量(Kg);11-原始振幅(mm);r1-试加重量安装半径(mm);n-转子转速(r/min)
注:在加配重时焊条重量也应计算在内。
2.1.4 分别将试加配重块依次加于A、B、C点上,然后依次启动风机到工作速率,并在风机轴承水平方向上同一处,用测振表分别测得A、B、C处最大初始振幅A1、A2、A3。
注:分别在A、B、C上加上试重铁块,并且必须将上一次的加重铁块取掉。
2.1.5 做比例圆,向量图。
①以A 为圆心,以A1为半径画圆;②以B 为圆心,以A2为半径画圆;
③以C 为圆心,以A3为半径画圆;④圆A1和圆A2交于a,圆A1和圆A3交于b,圆A2和圆A3交于c(见图2);⑤连接a、b、c 三点,并作△abc 的外接圆(见图3),其圆心为O1;⑥连接OO1,测得OB与OO1的夹角为W0。
2.1.6 平衡质量和平衡位置的确定。
平衡质量m=Gl1/OO1
平衡位置确定:在叶轮上,由B点向C点移动W0
2.1.7 加完加配重块快以后,用测振表测试,是否符合标准。
3 实例分析
西安化工厂35吨/h链条锅炉为本厂最大的一台出力锅炉,担负着全厂的生产及生活用汽。
该台锅炉的引风机与电机采用弹性联轴器连接,输送介质为烟气,型号为Y4-73离心式风机,机号NO20,传动方式D,主要由叶轮、机壳、进口、调节门及联轴器组成。
其中,叶轮是产生风压和传递能量的主要做功部件。
引风机机壳采用普通钢板祖对焊接制作而成,叶轮重量826Kg,风机控制参数:转速730r/min,流量为160800m3/h,全压2039Pa,电机功率132Kw。
叶轮直径2300mm。
在引風机叶轮边缘(距边缘3cm)均匀地钻三个φ12孔,编A、B、C做好标记,(用M10螺栓固定配重块)。
启动风机后,用测振仪器在靠近风机端轴承箱上下箱连接处、联轴器靠近轴承箱端、电机靠近联轴器端、电机远离联轴器端分别选四个点并编成1#、2#、
3#、4#做好标记,分别测试振幅,测得的四个点振幅分别为0.12mm、0.11mm、0.105mm、0.09mm,选取靠近风机端的轴承箱上下箱连接处测得的风机振幅(为0.12mm),按经验公式计算后需试加配重为218g。
实际制作配重块时要考虑减去紧固螺栓的重量。
将配重块按叶轮边缘加工好的三个φ12孔按已编好的A、B、C,分三次固定在叶轮边,每固定一次,安装好机壳,启动风机后测试一次风机振幅,只在靠近叶轮端轴承箱上盖处测试并记录。
三次测试后,分别测得风机振幅为0.18mm、0.17mm、0.19mm。
对所测得的三次振幅以轴心处为原点按振幅大小画出矢量图,计算合成矢量,矢量合成采用平面坐标法计算,结果为001=0.0173mm。
平衡质量m=Gl1/001=218×0.12/0.0173=151.66(g)
合成矢量的指向端即为产生叶轮转动不平衡的最重点,需要在合成矢量反向端加配重块(配重块重心距边缘3cm),采用焊接方法加固,配重块重量要减去所加焊条重量,配重块焊后重量与试加配重相同。
加好配重重量,安装好机壳,然后再次启动风机,在靠近叶轮端轴承箱上盖处、联轴器靠近轴承箱端、电机靠近联轴器端、电机远离联轴器端分别选四个点在进行测试,对应已编好的标记1#、2#、3#、4#测得振幅分别为,试验结果表明风机振动缺陷基本得以消除。
表1 动平衡前后振幅值对比表(单位:mm)
4 注意事项
在实际应用中,三点作图法做动平衡的方法相对于动平衡仪、画线法、两点法等方法,更容易理解,做法简单,且可有效地降低风机振动值,消除设备故障,较为实用;虽然在都能完成动平衡的情况下,三点作图法的精度不如动平衡仪,但是在转速低于1500r/min 的风机动平衡应用上精度已经足够了。
三点作图法在排粉风机动平衡中能成功应用,可举一反三,在其它风机发生叶轮动不平衡引起振动大时也同样可以使用这种方法来消除振动故障。
三点作图法找动平衡时,须注意以下事项:①按叶轮编号时不得将次序打乱,且编号不应被抹掉,最好是逆着风机转向编号,编号可写在不容易磨损的叶轮后盘表面上,以防试运后被煤粉冲刷掉;②用焊条贴焊平衡配重块时,应该焊在磨损不严重的叶轮后盘表面上,以防止平衡块在磨损后造成振动加大;③试加重块后分别测得的3次振动值,都必须是在同一轴承座的同一方向上,并要求数据是最大振动时的稳定值;④做动平衡时,应尽量防止受周围振动的影响,可采用紧固地脚螺栓等方法;⑤因每次试运都须拆、装蜗壳人孔,为了节省时间,试运时蜗壳人孔只需上紧四个角的螺栓即可,不需安装石棉绳,以便拆卸;⑥由于风机叶轮不平衡一般是表现在轴承的水平方向上的振动,所以通常只需测出轴承的水平方向上的振动幅值便可做动平衡。
5 结束语
西安化工厂35吨/h链条锅炉为本厂最大的一台出力锅炉,担负着全厂的生产及生活用汽。
在本厂生产停车大检修过程中,作为一名设备技术人员,初次遇到了需要现场进行大流量风机叶轮平衡调试的问题,通过个人思考以及借助经验公式,成功完成了叶轮动平衡试验,感悟颇深。
个人认为,就工厂锅炉大直径离心式风机的维护检修而言,值得推广应用。
参考文献
[1]乔文生,孙晓波. 利用现场动平衡技术提高企业设备维修效率[J].风机技术,2002(2).
[2]韦善杰. 三点作图法现场做风机叶轮的动平衡方法[J].轻工科技,2012.。