《精密与超精密加工技术》知识点总结
机械实习总结之精密和超精密加工技术学习总结心得

《精密和超精密加工技术》学习总结0.引言随着现代高科技的先进制造技术的发展,超精密加工技术应运而生,在现代高科技尖端产品的生产和开发中超精密加工技术是必不可少的关键技术,一个国家超精密加工技术的先进程度,直接影响着一个国家的制造业水平,是先进制造技术基础和关键,不管是在军事领域还是日常生活中,超精密加工技术都有着极其广阔的发展空间,对于任何一个国家的发展而言,发展超精密加工技术都是势在必行的[1]。
1.超精密切削超精密切削技术是在上世纪60年代发展起来的技术,在国防和尖端技术的发展中扮演着极其重要的角色,超精密切削技术主要是指金刚石超精密切削技术,其中包括金刚石超精密车削技术和金刚石超精密铣削, 使用的刀具是天然单晶金刚石刀具,其切削刃可磨得非常锋利[2]。
超精密切削技术是超精密加工技术的重要分支,是最早发展的超精密加工技术,在多个领域中均有运用到该项技术。
金刚石超精密加工的切削深度一般在微米量级,可加工出微米及亚微米级的形状精度及纳米级表面粗糙度的精密工件,在符合条件的机床和环境条件下,表面粗糙度Ra0.02-0.005Mm,精度<0.01Mm。
不同的背吃刀量、不同的进给量和不同的切削速度对加工表面粗糙度都有着不同程度的影响。
通过用两把几何角度相同的金刚石车刀,当在不同的背吃刀量下加工工件,可发现切削刃锋锐度对加工表面粗糙度影响最为明显;在不同的进给量下,锋锐的金刚石车刀加工表面粗糙度较小,二者差别明显;而在不同的切削速度下,两把车刀切出的加工表面粗糙度差别不大,可知切削速度对加工表面粗糙度影响不大。
金刚石刀具根据其切削刃的形状可以分为圆弧刃和直线刃,其中圆弧刃可用于加工各种形状的工件,尤其适用于加工复杂曲面的工件;而直线刃主要用于加工平面、柱面以及锥面等简单规则形状的工件, 就切削阻力而言,直线切削刃比圆弧切削刃的切削阻力要小,在尺寸精度和表面粗糙度方面更易于控制,并且制造容易、研磨方便, 直线切削刃在高品质、高精度加工方面有着不可替代的优势,当然,直线切削刃也有其不足之处,直线切削刃比较难安装调整。
第一章 精密和超精密加工技术概述 管文编著
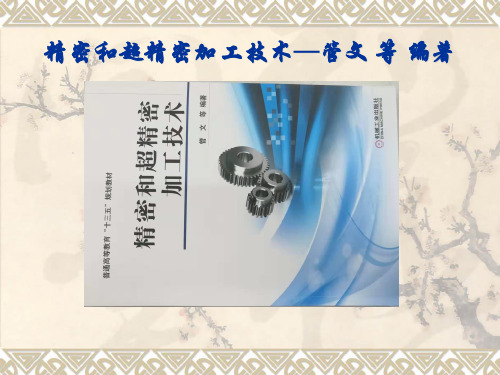
1.3 精密和超精密加工技术发展趋势
一、超精密加工技术基础理论和实验还需进一步发展
所谓超精密加工技术基础理论,是指在了解并掌握超精密 加工过程的基本规律和现象的描述后才能驾驭这一过程,取得 预期结果。例如上世纪 90 年代初,日本学者用金刚石车刀在 LLNL的DTM3上加工出最薄的连续切屑的照片,当时认为达到 了1nm的切削厚度,已成为世界最高水平,并至今无人突破 (见图1-4)。那么超精密切削极限尺度是多少、材料此时是 如何去除的,此外超精密加工工艺系统在力、热、电、磁、气 等多物理量/场复杂耦合下的作用机理是什么、此时系统的动态 特性、动态精度及稳定性如何保证等都需要得到新理论的支持。
1.2 精密超精密加工技术的作用
发动机喷嘴零件(如旋流槽、微小孔等特征)的精密 加工与检测技术、发动机叶片型面及进排气边的精密加工 与检测技术、整体叶盘的精密加工与检测技术等发展为航 空发动机零部件的加工与检测提供了可靠保证,促进了航 空发动机性能的提升。图1-3为发动机零部件专用五轴非 接触扫描精密测量机。
1.3 精密超精密加工技术发展趋势
三、微纳结构功能表面的超精密加工技术
微结构功能表面具有特定的拓扑形状,结构尺寸一般为 10~100μm ,面形精度小于 0.1μm,其表面微结构具有纹 理结构规则、高深宽比、几何特性确定等特点,如凹槽阵列、 微透镜阵列、金字塔阵列结构等,这些表面微结构使得元件 具有某些特定的功能,可以传递材料的物理、化学性能等, 如粘附性、摩擦性、润滑性、耐磨损性,或者具备特定的光 学性能等。在航空、航天飞行器宏观表面加工出微纳结构, 形成的功能性表面不仅可以减小飞行器的风阻、摩阻,减小 摩擦,还可以避免结冰层形成,提高空气动力学和热力学功 能,从而达到增速、增程、降噪等目的,同时表面特定的微 结构特征还能起到隐身功能,增强突防能力。
精密和超精密加工技术

1、通常将加工精度在0.1-1um、加工表面粗糙度R在0.02-0.1um之间的加工方法称为精密加工。
而将加工精度高于0.1um、加工表面粗糙度R小于0.01um的加工方法称为超精密加工。
2、提高加工精度的原因:提高制造精度后可提高产品的性能和质量,提高其稳定性和可靠性;促进产品的小型化;增强零件的互换性,提高装配生产率,并促进自动化装配。
3、精密和超精密加工目前包含三个领域:超精密切削;精密和超精密磨削研磨‘精密特种加工。
4、金刚石刀具的超精密切削加工技术,主要应用于两个方面:单件的大型超精密零件的切削加工和大量生产的中小型零件的超精密切削加工技术。
5、金刚石刀具有两个比较重要的问题:晶面的选择;切削刃钝圆半径。
6、超稳定环境条件主要是指恒温、防振、超净和恒湿五个方面的条件。
7、我国应开展超精密加工技术基础的研究,其主要内容包括以下四个方面:1)超精密切削、磨削的基本理论和工艺。
2)超精密设备的关键技术、精度、动特性和热稳定性。
3)超精密加工的精度检测、在线检测和误差补偿。
4)超精密加工的环境条件。
5)超精密加工的材料。
8、超精密切削实际选择的切削速度,经常是根据所使用的超精密机床的动特性和切削系统的动特性选取,即选择振动最小的转速。
9、超精密切削实际能达到的最小切削厚度和金刚石刀具的锋锐度、使用的超精密机床的性能状态、切削时的环境等都直接有关。
10、为实现超精密切削,刀具应具有如下性能:1)极高的硬度、极高的耐磨性和极高的弹性模量,以保证刀具有很长的寿命和很高的尺寸耐用度。
2)切削刃钝圆能磨得极其锋锐,切削刃钝圆半径r值极小,能实现超薄切削厚度。
3)切削刃无缺陷,切削时刃形将复印在加工表面上,能得到超光滑的镜面。
4)和工件材料的抗粘结性好、化学亲和性小、摩擦因素低,能得到极好的加工表面完整性。
11、SPDT——金刚石刀具切削和超精密切削。
12、晶体受到定向的机械力作用时,可以沿平行于某个平面平整地劈开的现象称为解理现象。
先进制造技术-3精密与超精密加工技术
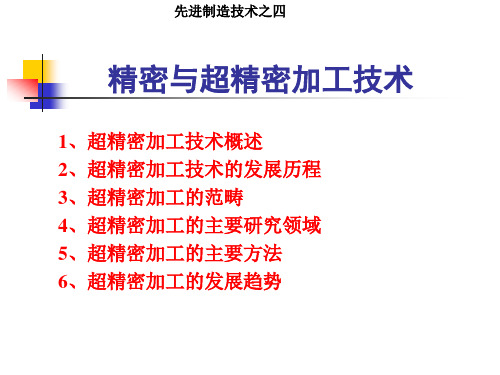
先进制造技术之四
精密与超精密加工技术
天然金刚石的加工多采用研磨加工方法, 天然金刚石的加工多采用研磨加工方法,通 常采用空气轴承研磨机,由于振动小, 常采用空气轴承研磨机,由于振动小,可达到很 低的粗糙度和极小的刃口半径。 低的粗糙度和极小的刃口半径。
先进制造技术之四
精密与超精密加工技术
1)刀尖的磨损 ) 在切削距离到达100km以前,后刀面磨损急剧上 以前, 在切削距离到达 以前 以后磨损逐渐减慢。 升,以后磨损逐渐减慢。 注:由于积屑瘤的原因,一般将研磨好的锋利刀 由于积屑瘤的原因, 尖有意加工成理想的稳定的磨损状态。 尖有意加工成理想的稳定的磨损状态。 2)切削速度和振动 ) 提高切削速度有利于获得良好的加工表面, 提高切削速度有利于获得良好的加工表面,但注意 以不产生振动为准则。 以不产生振动为准则。
6、1 金刚石刀具镜面切削 、
(1)金刚石刀头的特性 金刚石刀头的特性 (2)金刚石刀头的制造 金刚石刀头的制造 (3)刀头的使用特性 刀头的使用特性 (4)刀头的形状 刀头的形状
先进制造技术之四
精密与超精密加工技术
1) 金刚石的颜色和硬度选用
黄色金刚石:韧性较好,硬度较高, 黄色金刚石:韧性较好,硬度较高,一般用于 金属材料和硬度较低的材料的加工 茶色金刚石:韧性差,硬度最高, 茶色金刚石:韧性差,硬度最高,一般用于难 切削材料的镜面加工中。 切削材料的镜面加工中。 2)热传导率 ) 金刚石的热传导率是矿物中最大的, 金刚石的热传导率是矿物中最大的,切削加工 中发热量非常小。 中发热量非常小。
空气静压导轨
先进制造技术之四
精密与超精密加工技术
摩擦驱动原理图
先进制造技术之四
精密与超精密加工技术
第5章 精密、超精密加工技术

• 和表面粗糙度的检验,而且要测量加工设备 的精度和基础零部件的精度。 • 高精度的尺寸和几何形状可采用分辨率为 0.1~0.01µ m,的电子测微计、分辨率为 0.01~0.001µ m的电感测微仪或电容测微仪来 测量。圆度还可以用精度为0.01µ m的圆度仪 来测量。
加工设备必须具有高精度的主轴系统、进给 系统(包括微位移装臵),现在的超精密车 床,其主轴回转精度可达0.02µ m,导轨直线 度可达1000000:0.025,定位精度可达 0.013µ m,进给分辨率可达0.005µ m。其回转 零件应进行精密的动平衡。
• 2)高刚度
• 包括静刚度和动刚度,不仅要注意零件本身
• 精密和超精密磨料加工是利用细粒度的磨粒 和微粉主要对黑色金属、硬脆材料等进行加 工,按具体地加工方法分为精密和超精密磨 削,加工精度可达5~0.5µ m,表面粗糙度 Ra0.05~0.008µ m);精密和超精密研磨(加 工精度可达10~0.1µ m,表面粗糙度 Ra0.01~0.008µ m);
合金等刀具进行精密和超精密切削,这些刀
具材料的切削效果不如金刚石,但能加工黑
色金属。对黑色金属等硬脆材料的精密加工
和超精密加工,一般多采用磨削、研磨、抛
光等方法。
• 精密和超精密磨削时,通常采用粒度240#~W7
或更细的白刚玉或铬刚玉磨料和树脂结合剂
制成的紧密组织砂轮,经金刚石精细修整后
• 进行加工。
• 出现了精密电火花加工、精密电解加工、精
密超声波加工、分子束加工、电子束加工、
离子束加工、原子束加工、激光加工、微波
加工、等离子体加工、光刻、电铸及变形加
工等。
• 4.复合加工
• 复合加工是将几种加工方法叠合在一起,发 挥各种加工方法的长处,达到高质量(加工
精密和超精密加工复习整理资料

精密和超精密加⼯复习整理资料1.精密和超精密加⼯⽬前包含的三个领域:超精密切削、精密和超精密磨削研磨和精密特种加⼯2.超精密加⼯中超稳定的加⼯环境条件主要指(恒温)、(恒湿)、(防振)和(超净)四个⽅⾯的条件。
3.电⽕花型腔加⼯的⼯艺⽅法有:(单电极平动法)、(多电极更换法)、(分解电极法)、简单电极数控创成法等。
4.超精密加⼯机床的总体布局形式主要有以下⼏种:(T形布局)、(⼗字形布局)、(R-θ布局)、(⽴式结构布局)等。
5.实现超精密加⼯的技术⽀撑条件主要包括:(超精密加⼯机理与⼯艺⽅法)、(超精密加⼯机床设备)、(超精密加⼯⼯具)、(精密测量和误差补偿)、⾼质量的⼯件材料、超稳定的加⼯环境条件等。
6.激光加⼯设备主要包括电源、(激光器)、(光学系统)、(机械系统)、控制系统、冷却系统等部分。
7.精密和超精密加⼯机床主轴轴承的常⽤形式有(液体静压轴承)和(空⽓静压轴承)。
8.⾦刚⽯晶体的激光定向原理是利⽤⾦刚⽯在不同结晶⽅向上(因晶体结构不同⽽对激光反射形成不同的衍射图像)进⾏的。
9.电⽕花加⼯蚀除⾦属材料的微观物理过程可分为(介质电离击穿)、(介质热分解、电极材料熔化、⽓化)、(蚀除物抛出)和(间隙介质消电离)四个阶段。
10.超精密加⼯机床的关键部件主要有:(精密主轴部件)、(导轨部件)和(进给驱动系统)等。
11.三束加⼯是指电⼦束、离⼦束和激光束。
12.所谓空⽓洁净度是指空⽓中含尘埃量多少的程度。
13.⼯业⽣产中常见的噪声主要有空⽓动⼒噪声、机械噪声和电磁噪声。
14.纳⽶级加⼯精度包含:纳⽶级尺⼨精度、纳⽶级⼏何形状精度、纳⽶级表⾯质量。
15.超精密切削时积屑瘤的⽣成规律:1)在低速切削时,h0值⽐较稳定;在中速时值不稳定。
2)在进给量f很⼩时,h0较⼤3)在背吃⼑量a p<25um时,h0变化不⼤;在a p>25um时,h0将随a p的值增⼤⽽增⼤。
16.超精密切削时积屑瘤对切削过程的影响:积屑瘤⾼时切削⼒⼤,积屑瘤⼩时切削⼒⼩。
精密与超精密加工技术
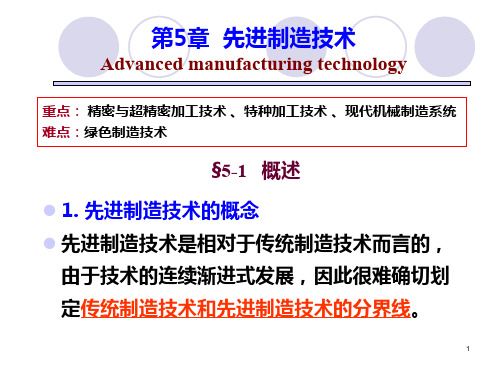
就目前的发展来说,先进制造技术可以定义为:
制造业不断吸收机械、电子、信息(计算机与通讯、 控制理论、人工智能等)、能源及现代系统管理等方面
的成果,并将其综合应用于产品设计、制造、检测、管 理、销售、使用、服务乃至回收的制造全过程,以实现
优质、高效、低耗、清洁、灵活生产,提高对动态多 变的产品市场的适应能力和竞争能力的制造技术的总 称。
7
5.2.2 金刚石刀具超精密切削 1. 金刚石刀具超精密切削机理 金刚石刀具超精密切削是微细切削,切深一般小于晶格的尺寸,切削
就在晶格内进行。这时,切削力一定要超过晶体内部非常大的原子、 分子结合力,刀刃上所承受的剪切应力也急速地增加并变得非常大, 产生很大的热量,导致刀刃切削处的温度极高,因此要求刀具材料不 但具有高温强度和高温硬度(10000HV)性能,而且本身质地细密, 经过精细研磨,切削刃钝圆半径可达0.02~0.002 µm,表面粗糙度可以 很低,能够进行Ra 0.05~0.008 µm的镜面切削,达到比较理想的效果。 金刚石刀具超精密切削是在高速、小切深、小进给量下,以及高应力 和高温度下进行。由于切屑极薄,切速高,不会波及工件内层,因此 塑性变形小,同样可以获得高精度、低表面粗糙度的加工表面。
撑面、反射镜等需要高精度的场合,可 以达到表面粗糙度0.01µm。在可加工材 料上,包括塑性材料、有色金属、有机 玻璃、各种塑料制品、脆性材料,如硅、 锗、红外光学晶体。 金刚石超精密切削的一个典型代表是由 美国国防部高等研究计划局(DARPA) 投资,LLL实验室和空军Wright航空研 究所等单位合作研制的LODTM-大型光 学金刚石车床。该机床可以加工直径 1635 mm×500 mm,重1360 kg的大型 反射镜,如图5-1所示。
超精密加工复习要点

超精密加工第一章1. 什么是精密加工和超精密加工技术?答:精密加工:是指在一定时期,加工精度和表面质量达到较高程度的精密加工技术(加工工艺)。
具体地说,是指加工精度在1~0.1μm,粗糙度在Ra0.1μm以下(一般Ra0.02~0.1μm)的加工方法。
超精密加工:是指在一定时期,加工精度和表面质量达到最高程度的精密加工技术(加工工艺)。
具体地说,是指加工精度在0.1~0.01μm,粗糙度小于Ra0.01μm(Ra0.01~Ra0.001μm)的加工方法。
研究它有何重要意义?答:1). 机械工业是国民经济发展的基础,为其他行业提供技术装备;而技术装备的水平和质量影响各行业生产技术的水平。
2). 国家要振兴机械装备制造业,先进制造技术是振兴机械装备制造业的重要组成部分。
3). 精密和超精密加工技术又是先进制造技术中最具有实质性的重要组成部分,是先进制造技术的基础和关键。
2. 精密加工和超精密加工包括哪些内容?答:1). 精密、超精密切削和磨削加工。
2). 精密和超精密特种加工,包括: a.电物理加工;b.电化学加工;c.物理加工;d.化学加工;e.复合加工。
3. 金刚石刀具超精密切削的切削速度应如何选择?答:根据所使用的超精密机床和切削系统的动特性选取,即选择振动最小的转速(切削速度)。
因为在该速度时,表面粗糙度最小,加工质量最高。
小批量加工可选低切削速度(低主轴转速);大批量加工选高切削速度(高主轴转速)以提高生产率。
4. 单晶金刚石有哪几个主要晶面?晶面选择对切削变形和加工表面质量的影响如何?答:单晶金刚石有(100)、(110)和(111)三个主要晶面。
对切削变形的影响:晶面不同的刀具,切削变形不同,(100)晶面的车刀切削变形小。
对加工表面质量的影响:相同切削条件,锋锐度基本相同,不同晶面的加工表面粗糙度相差不多。
(100) 晶面车刀切出的表面层残余应力小于(110)晶面车刀切出的表面层残余应力。
精密和超精密加工技术(第三章)

精密加工技术- 精密加工技术-LYD
3.1 加工设备的精化
1.蜕化性加工(母性加工)原则: 1.蜕化性加工(母性加工)原则: 蜕化性加工
精度 1um 滚齿机分度误差 加工母机(机床) 加工母机(机床)
2um
工件
齿轮的分度误差= 齿轮的分度误差=机 床分度误差+ 床分度误差+刀具误 工件安装偏心+ 差+工件安装偏心+ 其它随机误差
•
创造性加工—— 创造性加工 工 工件 件
蜕化法
间 接 法
加工 的机床 精化 —— 的加工精 加工 精 件 • 创造性加工—— 创造性加工
工件
直接法
精化
的机床
工 精 件 精 加工
精 的机床 化 加工 ——
创造性加工原则
精密加工技术- 精密加工技术-LYD
3.1 加工设备的精化
获得高精度零件的两种加工途径: 获得高精度零件的两种加工途径:
2.影响最小切削深度的因素 2.影响最小切பைடு நூலகம்深度的因素
1. 刀具刃口半径ρ 2. 工艺系统的刚性
精密加工技术- 精密加工技术-LYD
3.2 微量切除原理
3.常用切削刀具的 3.常用切削刀具的 ρ
刀具材料 碳素工具钢 高速钢 硬质合金 陶瓷刀具 天然金刚石刀具 玻璃刀具 可以刃磨到的
ρ (um)
使用时的
花岗岩的吸振能力、稳定性和热胀系数均优于钢铁材料, 花岗岩的吸振能力、稳定性和热胀系数均优于钢铁材料,高/ 超精密机床的床身、导轨等基础部件多采用此石材制作。 超精密机床的床身、导轨等基础部件多采用此石材制作。
瑞士( 公司)制造的人造花岗岩,性能比天然花岗岩还好。 瑞士(Stude公司)制造的人造花岗岩,性能比天然花岗岩还好。
精密与超精密加工技术
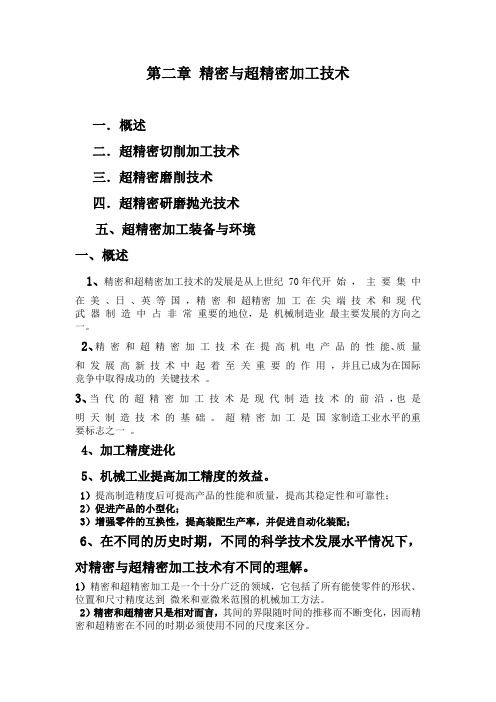
第二章精密与超精密加工技术一.概述二.超精密切削加工技术三.超精密磨削技术四.超精密研磨抛光技术五、超精密加工装备与环境一、概述1、精密和超精密加工技术的发展是从上世纪 70年代开始,主要集中在美、日、英等国,精密和超精密加工在尖端技术和现代武器制造中占非常重要的地位,是机械制造业最主要发展的方向之一。
2、精密和超精密加工技术在提高机电产品的性能、质量和发展高新技术中起着至关重要的作用,并且已成为在国际竞争中取得成功的关键技术。
3、当代的超精密加工技术是现代制造技术的前沿,也是明天制造技术的基础。
超精密加工是国家制造工业水平的重要标志之一。
4、加工精度进化5、机械工业提高加工精度的效益。
1)提高制造精度后可提高产品的性能和质量,提高其稳定性和可靠性;2)促进产品的小型化;3)增强零件的互换性,提高装配生产率,并促进自动化装配;6、在不同的历史时期,不同的科学技术发展水平情况下,对精密与超精密加工技术有不同的理解。
1)精密和超精密加工是一个十分广泛的领域,它包括了所有能使零件的形状、位置和尺寸精度达到微米和亚微米范围的机械加工方法。
2)精密和超精密只是相对而言,其间的界限随时间的推移而不断变化,因而精密和超精密在不同的时期必须使用不同的尺度来区分。
3)1983年日本的 Taniguchi教授在考查了许多超精密加工实例的基础上对超精密加工的现状进行完整的综述,并对其发展趋势进行了预测。
7、超精密加工技术的现状1)超精密加工技术是一门综合性的系统工程,它的发展综合地利用了机床、工具、计量、环境技术、微电子技术、计算机技术、数控技术等的进步。
2)精密加工和超精密加工已从单一的技术方法发展为制造系统工程,简称精密工程。
它以人、技术、组织为基础,涉及超微量去除、结合、变形加工技术,高稳定性和高净化的加工环境,检测与误差补偿,工况监测与质量控制,被加工材料等。
二、超精密切削加工技术超精密切削技术是60年代发展起来的新技术,它在国防和尖端技术的发展中起着重要的作用;超精密切削是使用精密的单晶天然金刚石刀具加工有色金属和非金属;超精密切削可代替研磨等很费工的精加工工序,不仅节省工时,还提高加工精度和表面质量。
精密和超精密加工技术
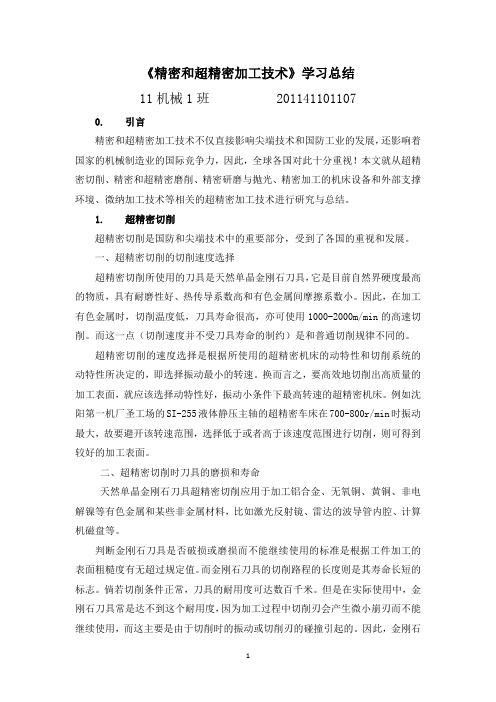
《精密和超精密加工技术》学习总结11机械1班 2011411011070. 引言精密和超精密加工技术不仅直接影响尖端技术和国防工业的发展,还影响着国家的机械制造业的国际竞争力,因此,全球各国对此十分重视!本文就从超精密切削、精密和超精密磨削、精密研磨与抛光、精密加工的机床设备和外部支撑环境、微纳加工技术等相关的超精密加工技术进行研究与总结。
1. 超精密切削超精密切削是国防和尖端技术中的重要部分,受到了各国的重视和发展。
一、超精密切削的切削速度选择超精密切削所使用的刀具是天然单晶金刚石刀具,它是目前自然界硬度最高的物质,具有耐磨性好、热传导系数高和有色金属间摩擦系数小。
因此,在加工有色金属时,切削温度低,刀具寿命很高,亦可使用1000-2000m/min的高速切削。
而这一点(切削速度并不受刀具寿命的制约)是和普通切削规律不同的。
超精密切削的速度选择是根据所使用的超精密机床的动特性和切削系统的动特性所决定的,即选择振动最小的转速。
换而言之,要高效地切削出高质量的加工表面,就应该选择动特性好,振动小条件下最高转速的超精密机床。
例如沈阳第一机厂圣工场的SI-255液体静压主轴的超精密车床在700-800r/min时振动最大,故要避开该转速范围,选择低于或者高于该速度范围进行切削,则可得到较好的加工表面。
二、超精密切削时刀具的磨损和寿命天然单晶金刚石刀具超精密切削应用于加工铝合金、无氧铜、黄铜、非电解镍等有色金属和某些非金属材料,比如激光反射镜、雷达的波导管内腔、计算机磁盘等。
判断金刚石刀具是否破损或磨损而不能继续使用的标准是根据工件加工的表面粗糙度有无超过规定值。
而金刚石刀具的切削路程的长度则是其寿命长短的标志。
倘若切削条件正常,刀具的耐用度可达数百千米。
但是在实际使用中,金刚石刀具常是达不到这个耐用度,因为加工过程中切削刃会产生微小崩刃而不能继续使用,而这主要是由于切削时的振动或切削刃的碰撞引起的。
因此,金刚石刀具只能使用在机床主轴转动非常平稳的高精度机床上,而刀具的维护对机床的要求亦是如此。
04精密与超精密加工技术

微量进给装置二
压电陶瓷式微进给装置
1—刀夹 2—机座 3—压电陶瓷 4—后垫块 5—电感测头 6—弹性支承
五、精密加工环境
超精密加工必须在超稳定的环境下进 行。 超稳定环境:恒温、超净和防振。
六、超精密加工精度的在线检测及计量测试
对加工误差进行在线检测,实时建模与 动态分析预报,再根据预报数据对误差 源进行补偿,从而消除或减少加工误差。
1、去除加工(分离加工)
从工件上去除一部分材料。
超精密切削加工形面示例 (图为各种镜面切削加工的形面)
2、结合加工
利用物理和化学方法,将不同材料结合在一起。 利用物理和化学方法,将不同材料结合在一起。按结合的 机理、方法、强弱等,分为附着、注入和连接三种。 机理、方法、强弱等,分为附着、注入和连接三种。
3、变形加工(流动加工)
利用力、热、分子运动等手段,使工件 产生变形,改变其尺寸、形状和性能。
3.3.2 超精密切削加工
超精密切削对刀具的要求 • 极高的硬度、极高的耐用度和极高的弹性模量,保证 刀具寿命和尺寸耐用度; • 刃口能磨得极其锋锐,刃口半径ρ值极小,能实现超 薄的切削厚度; • 刀刃无缺陷,避免刃形复印在加工表面; • 抗粘结性好、化学亲和性小、摩擦系数低、能得到极 好的加工表面完整性。
3、精密与超精密加工的应用与进展
美国是研究最早的国家,处于世界领先地位,以 民品应用为主要对象 英国的克兰菲尔德精密工程研究所有较高声誉 日本起步较晚,发展最快,以发展国防尖端技术 为主要目标。 我国在70年代末期有长足进步,80年代中期出现 了具有世界水平的超精密机床和部件
二、 超精密加工方法
六、超精密加工精度的在线检测及计量测试
大距离的测量仪器:双频激光干涉仪 小距离的测量仪器:电容式、电感式测微仪、 光纤测微仪 更小测量范围的测量仪器:扫描隧道显微 镜 、扫描电子显微镜、原子力显微镜
精密和超精密加工技术_期末复习资料
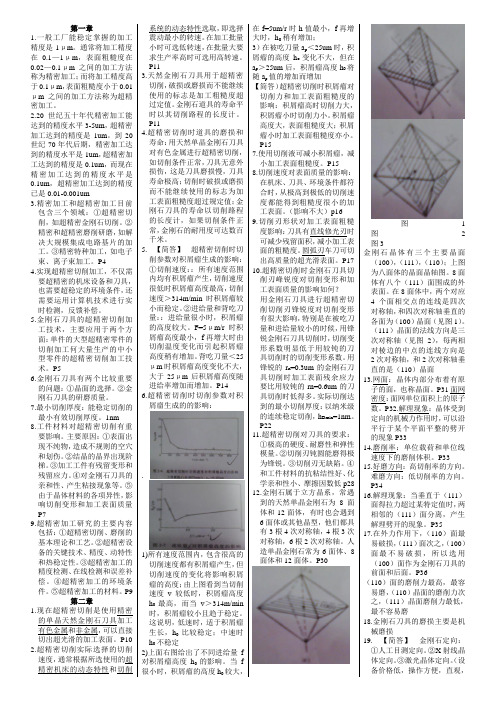
第一章1.一般工厂能稳定掌握的加工精度是1μm。
通常将加工精度在0.1—1μm,表面粗糙度在0.02—0.1μm之间的加工方法称为精密加工;而将加工精度高于0.1μm,表面粗糙度小于0.01μm之间的加工方法称为超精密加工。
2.20世纪五十年代精密加工能达到的精度水平3-5um,超精密加工达到的精度是1um。
到20世纪70年代后期,精密加工达到的精度水平是1um,超精密加工达到的精度是0.1um,而现在精密加工达到的精度水平是0.1um,超精密加工达到的精度已是0.01-0.001um3.精密加工和超精密加工目前包含三个领域:①超精密切削,如超精密金刚石切削。
②精密和超精密磨削研磨,如解决大规模集成电路基片的加工。
③精密特种加工,如电子束、离子束加工。
P44.实现超精密切削加工,不仅需要超精密的机床设备和刀具,也需要超稳定的环境条件,还需要运用计算机技术进行实时检测,反馈补偿。
5.金刚石刀具的超精密切削加工技术,主要应用于两个方面:单件的大型超精密零件的切削加工何大量生产的中小型零件的超精密切削加工技术。
P56.金刚石刀具有两个比较重要的问题:①晶面的选择。
②金刚石刀具的研磨质量。
7.最小切削厚度:能稳定切削的最小有效切削厚度。
1nm8.工件材料对超精密切削有重要影响。
主要原因:①表面出现不纯物,造成不规则的空穴和划伤。
②结晶的晶界出现阶梯。
③加工工件有残留变形和残留应力。
④对金刚石刀具的亲和性、产生粘接现象等。
⑤由于晶体材料的各项异性,影响切削变形和加工表面质量P79.超精密加工研究的主要内容包括:①超精密切削、磨削的基本理论和工艺。
②超精密设备的关键技术、精度、动特性和热稳定性。
③超精密加工的精度检测、在线检测和误差补偿。
④超精密加工的环境条件。
⑤超精密加工的材料。
P9第二章1.现在超精密切削是使用精密的单晶天然金刚石刀具加工有色金属和非金属,可以直接切出超光滑的加工表面。
P102.超精密切削实际选择的切削速度,通常根据所选使用的超精密机床的动态特性和切削系统的动态特性选取,即选择震动最小的转速。
精密与超精密加工技术

刀具种类:金刚石刀具; 超精密磨削砂轮
金刚石刀具
1、金刚石刀头的特性: 颜色:有红色和绿色等多种颜色,其硬
度随颜色而不同; 硬度:显微硬度值比其他物质高许多; 热传导率:在矿物中最大。
金刚石刀具
2、金刚石刀头的制造: 成形:采用研磨加工方法; 研磨方法:用空气轴承的研磨机; 特殊刀头的形状
第三章 先进制造工艺技术
第一节 精密与超精密加工技术
一、 精密与超精密加工技术概述
1、精密加工与超精密加工定义
精密加工是指加工精度在0.1~lμm之间, 表面粗糙度Ra在0.lμm以下(称微米加工)
超精密加工的加工精度在0.lμm以下,表面 粗糙度在0.02μm以下(称为亚微米加工)
2、精密加工与超精密加工的特点
光纤测微仪 更小测量范围的测量仪器:扫描隧道显微
镜 、扫描电子显微镜、原子力显微镜
激光干涉仪
SPA-400 多功能扫描探针显微镜
回顾
一、 精密与超精密加工技术概述 二、 超精密加工方法 三、 超精密加工刀具 四、 超精密加工设备 五、 精密加工环境 六、 超精密加工精度的在线检测及计量测试
五、精密加工环境
超精密加工必须在超稳定的环境下进 行。
超稳定环境:恒温、超净和防振。
六、超精密加工精度的在线检测及计量测试
对加工误差进行在线检测,实时建模与 动态分析预报,再根据预报数据对误差 源进行补偿,从而消除或减少加工误差。
六、超精密加工精度的在线检测及计量测试
大距离的测量仪器:双频激光干涉仪 小距离的测量仪器:电容式、电感式测微仪、
超精密磨削砂轮
超精密磨削质量控制方面的首要因素: 砂轮磨料:应与工件材料选配适当; 磨料粒度:具备形成微刃的粒度; 砂轮硬度:硬度中软。
第3讲 精密与超精密加工技术
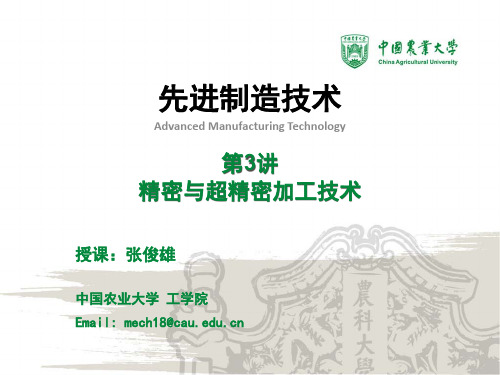
6
先进制造技术
第3讲 精密与超精密加工技术
单晶金刚石飞铣加工的激光系统用KDP 晶体 (长宽420mm,厚10mm,粗糙度2nm rms)
LODTM 加工的美国宇航局用的抛物面镜, 最终形状误差150nm
7
先进制造技术
第3讲 精密与超精密加工技术
世界发达国家均予以高度重视。启动的研究计划包括 :
27
先进制造技术
第3讲 精密与超精密加工技术
(1)超精密加工刀具
超精密加工要求刀具能均匀地去除不大于工件加工精度且 厚度极薄的金属层或非金属层。 超精密切削中的加工刀具,一般指天然单晶金刚石刀具。 超精密切削中必须保证金刚石刀具的刀面与刃口质量。 超精密磨削的加工刀具砂轮的磨料品级与力度均匀性在加 工中十分重要。
◆ 与高新技术产品紧密结合
精密与超精密加工设备造价高,难成系列。常常针对某一特定产品设 计(如加工直径3m 射电天文望远镜的超精密车床,加工尺寸小于1mm 微型零件的激光加工设备)。
◆ 与自动化技术联系紧密
广泛采用计算机控制、适应控制、再线检测与误差补偿技术,以减小 人的因素影响,保证加工质量。
◆ 加工与检测一体化
第3讲 精密与超精密加工技术
加工设备 102 加工误差(μm) 101 精密加工 100 10-1 超精密加工 10-2 10-3 1900 1920 1940 1960 1980 2000
车床,铣床
测量仪器
卡尺 百分尺 比较仪 气动测微仪 光学比较仪 光学磁尺 电子比较仪 激光测长仪 圆度仪轮廓仪 激光高精度 测长仪 扫描电镜 电子线分析仪
10
先进制造技术
第3讲 精密与超精密加工技术
精密与超精密加工的地位
精密和超精密加工复习整理资料
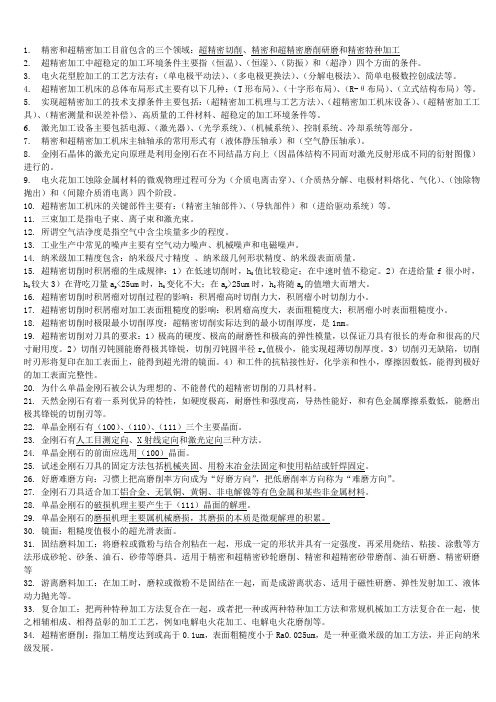
1.精密和超精密加工目前包含的三个领域:超精密切削、精密和超精密磨削研磨和精密特种加工2.超精密加工中超稳定的加工环境条件主要指(恒温)、(恒湿)、(防振)和(超净)四个方面的条件。
3.电火花型腔加工的工艺方法有:(单电极平动法)、(多电极更换法)、(分解电极法)、简单电极数控创成法等。
4.超精密加工机床的总体布局形式主要有以下几种:(T形布局)、(十字形布局)、(R-θ布局)、(立式结构布局)等。
5.实现超精密加工的技术支撑条件主要包括:(超精密加工机理与工艺方法)、(超精密加工机床设备)、(超精密加工工具)、(精密测量和误差补偿)、高质量的工件材料、超稳定的加工环境条件等。
6.激光加工设备主要包括电源、(激光器)、(光学系统)、(机械系统)、控制系统、冷却系统等部分。
7.精密和超精密加工机床主轴轴承的常用形式有(液体静压轴承)和(空气静压轴承)。
8.金刚石晶体的激光定向原理是利用金刚石在不同结晶方向上(因晶体结构不同而对激光反射形成不同的衍射图像)进行的。
9.电火花加工蚀除金属材料的微观物理过程可分为(介质电离击穿)、(介质热分解、电极材料熔化、气化)、(蚀除物抛出)和(间隙介质消电离)四个阶段。
10.超精密加工机床的关键部件主要有:(精密主轴部件)、(导轨部件)和(进给驱动系统)等。
11.三束加工是指电子束、离子束和激光束。
12.所谓空气洁净度是指空气中含尘埃量多少的程度。
13.工业生产中常见的噪声主要有空气动力噪声、机械噪声和电磁噪声。
14.纳米级加工精度包含:纳米级尺寸精度、纳米级几何形状精度、纳米级表面质量。
15.超精密切削时积屑瘤的生成规律:1)在低速切削时,h0值比较稳定;在中速时值不稳定。
2)在进给量f很小时,h0较大3)在背吃刀量a p<25um时,h0变化不大;在a p>25um时,h0将随a p的值增大而增大。
16.超精密切削时积屑瘤对切削过程的影响:积屑瘤高时切削力大,积屑瘤小时切削力小。
- 1、下载文档前请自行甄别文档内容的完整性,平台不提供额外的编辑、内容补充、找答案等附加服务。
- 2、"仅部分预览"的文档,不可在线预览部分如存在完整性等问题,可反馈申请退款(可完整预览的文档不适用该条件!)。
- 3、如文档侵犯您的权益,请联系客服反馈,我们会尽快为您处理(人工客服工作时间:9:00-18:30)。
《精密与超精密加工技术》知识点总结1.加工的定义:改变原材料、毛坯或半成品的形状、尺寸及表面状态,使之符合规定要求的各种工作的统称。
规定要求:加工精度和表面质量。
2.加工精度:是指零件在加工以后的几何参数(尺寸、形状、位置)与图纸规定的理想零件的几何参数相符合的程度。
符合程度越高,加工精度则越高。
3.表面质量:指已加工表面粗糙度、残余应力及加工硬化。
4.精密加工定义:是指在一定时期,加工精度和表面质量达到较高程度的加工技术(工艺)。
5.超精密加工:是指在一定时期,加工精度和表面质量达到最高程度的加工技术(工艺)。
6.加工的划分普通加工(一般加工)、精密加工和超精密加工。
普通加工:加工精度在1μm 以上(粗加工IT13~IT9、半精加工IT8~IT7、精加工IT6~IT5),粗糙度Ra0.1-0.8μm。
加工方法:车、铣、刨、磨等。
适用于:普通机械(汽车、拖拉机、机床)制造等。
精密加工:加工精度在1~0.1μm ,粗糙度Ra0.1μm 以下(一般Ra0.1~0.01μm )的加工方法。
加工方法:车削、磨削、研磨及特种加工。
适用于:精密机床、精密测量仪器等中的关键零件的制造。
超精密加工:加工精度在0.1~0.01μm ,粗糙度小于Ra0.01μm(Ra0.01~Ra0.001μm)的加工方法。
加工方法:金刚石刀具超精密切削、超精密磨削、超精密特种加工。
适用于:精密元件的制造、计量标准元件、集成电路等的制造。
7.精密加工影响因素8.切削、磨削加工:精密切削和磨削、超精密切削与磨削。
9.特种加工:是指一些利用热、声、光、电、磁、原子、化学等能源的物理的,化学的非传统加工方法。
10.精密加工和超精密加工的发展趋势:向高精度方向发展、向大型化,微型化方向发展、向加工检测一体化发展、研究新型超精密加工方法的机理、新材料的研究。
11.精密加工和超精密加工的特点:形成了系统工程它是一门多学科的综合高级技术;它与特种加工关系密切传统加工方法与非传统加工方法相结合;加工检测一体化在线检测并进行实时控制、误差补偿;与自动化技术联系密切依靠自动化技术来保证;与产品需求联系紧密加工质量要求高、技术难度大、投资大、必须与具体产品需求相结合。
12.金刚石刀具是超精密切削中的重要关键。
金刚石刀具有两个比较重要的问题:一是晶面的选择,因为金刚石晶体各向异性;二是研磨质量,也就是刃口半径,因为影响变形和最小切削厚度。
13.检测技术是超精密切削中一个极为重要的问题。
超精密加工要求测量精度比加工精度高一个数量级。
14.超精密加工必须在超稳定的加工环境条件下进行:恒温条件、防振条件。
恒温:20℃±(1~0.02)℃恒湿:35﹪~45﹪空气净化、防振等。
15.金刚石分类:天然金刚石和人造金刚石两大类(碳的同素异形体)。
16.金刚石晶体的三种晶面晶体——原子具有规则排列的物体。
晶体中各种方位上的原子面叫晶面。
晶体中各种方位上的原子列叫晶向。
金刚石晶格中有三种重要晶面,(100),(110),(111)。
17.金刚石晶体具有强烈的各向异性不同晶面,不同方向性能有明显差别;金刚石刀具的晶面选择直接影响切削变形和加工表面质量;金刚石晶体和铝合金、紫铜间的摩擦系数在0.06~0.13之间,而且随金刚石晶面不同和摩擦方向不同而变化。
18.金刚石刀具的晶面选择直接影响切削变形和加工表面质量。
19.金刚石刀具的特点:硬度极高、耐热性差不宜超过800℃、强度低自脆性大,对振动敏感,只能微量切削、与铁有强的化学亲和力不宜加工黑色金属,适宜有色金属,非金属、超精密切削使用天然单晶金刚石刀具:切削刃可磨得极锋利,硬度极高(是硬度最高的物质),耐磨性好,热传导系数高,摩擦系数低。
20.刀具耐用度T:新刃磨的刀具从开始切削直到磨损量达到磨钝标准为止的切削时间。
21.随着V增大,切削温度也增大,刀具磨损加快,所以刀具耐用度是选择切削速度的重要依据。
22.动特性包括抗振性和动态稳定性;抗振性是抵抗强迫振动的能力;动态稳定性是预防自激振动的能力。
23.金刚石刀具对有色金属进行超精密切削:多数属于正常磨损情况—刀具磨损甚慢,耐用度极高,原因:机械磨损。
有时出现剧烈磨损情况—磨损形式为层状微小剥落,沿(111)面解理造成。
24.解理现象:晶体受到定向的机械力作用,可以沿平行于某个平面平整地劈开,即晶体沿一定晶面(解理面)破裂的现象。
25.切削钢和镍的磨损形式:沿切削方向产生磨损沟槽,由于金刚石和铁镍发生化学反应和物理亲和所致。
26.金刚石刀具的耐用度,通常以其切削路径的长度计算。
刀具破损或磨损而不能继续使用的标志为加工表面粗糙度超过规定值。
金刚石刀具磨损甚微,耐用度极高,正常可达数百公里。
同一刀具可以加工很多零件,零件的尺寸一致,基本不受刀具磨损的影响。
刀具达不到高耐用度的原因主要是振动使切削刃产生微小崩刃。
27.积屑瘤:来自切屑和工件上的金属冷焊(粘结)并层积在前刀面上形成硬度很高的楔块,能代替切削刃及前刀面进行切削工作。
28.积屑瘤在切削过程中的作用:1)保护刀具2)增大前角3)增大切削厚度4)增大已加工表面粗糙度29.所有切削速度范围内都产生积屑瘤,但切削速度变化将影响积屑瘤的高度。
30.超精密切削时切削速度对积屑瘤生成的影响: 切削速度较低时,积屑瘤高度大。
说明低速时,切削温度较低,适合积屑瘤生长; 当切削速度> 314 m/min 时,积屑瘤较小且趋于稳定; 在切削速度相同条件下,刀刃的微观缺陷直接影响积屑瘤高度。
如完整刃的积屑瘤高度为 5 μm,而微小崩刃的刀刃积屑瘤高度为18 μm。
31.超精密切削时积屑瘤对切削力的影响: 积屑瘤高度大时,切削力大;积屑瘤小时,切削力小;原因:(积屑瘤代替刀具切削)(1)鼻形积屑瘤前端的圆弧半径R(2~3m)比刀具刃口钝圆半径ρ(0.2~0.3m)大得多,导致切削力大。
(2)积屑瘤与切屑和工件间的摩擦系数和摩擦力较金刚石与切屑和工件的摩擦系数及摩擦力大。
(3)积屑瘤产生的切削厚度大于原切削厚度,使切削力增大。
32.超精密切削时积屑瘤对表面粗糙度的影响:积屑瘤高度大,表面粗糙度差;积屑瘤小时,表面粗糙度好。
33.切削液的主要作用之一—润滑→减小摩擦和变形。
超精密切削,使用切削液,减小切削中的摩擦,可减小积屑瘤,减小Rz。
这时,切削速度的改变对Rz 无影响,这一点不同于普通切削。
加工黄铜时,切削液作用不明显,因为它是脆性材料,变形和摩擦力小。
34. 切削速度对加工表面粗糙度的影响:使用切削液时,在机床、刀具、环境条件都符合时,从极低到很高的切削速度,都能够得到粗糙度极小(Ra<0.01m)的加工表面。
这个结论具有实际意义,超精密切削常用于车端面,切速是变化的,但表面粗糙度则要求不变。
使用切削液时,切削速度对表面粗糙度的影响甚微。
使用切削液时,切削速度对铝合金加工表面粗糙度的影响甚微,微小的变化主要是受机床动特性的影响。
35. 进给量和修光刃对加工表面粗糙度的影响:普通切削f 是影响Ra 的主要因素;超精密切削采用很小的f,而且刀具要有修光刃。
36.超精密切削的金刚石刀具通常做成直线修光刃或圆弧修光刃直线修光刃—制造容易,国内用得较多,修光刃长度常取0.05~0.20mm;圆弧修光刃—易于对刀,圆弧半径R=2-5mm,制造较复杂。
(f较小)37.修光刃长度对Ra 的影响:修光刃的长度过长,对减小Ra效果不大。
(常取0.05~0.20mm);要精确对刀,使修光刃和进给方向一致,使用对刀显微镜。
38.精密切削背吃刀量对Ra的影响1)当ρ较大时:结论:ap 减小,使Ra 增大。
原因:ρ较大。
ap 减小,使切削困难,变质层大,Ra↑。
2)2)当ρ< 0.05~0.1m,最小ap< 0.1m,可得到Ra < 0.02m,表面变质层极小。
在刀具刃口半径足够小时(ρ<0.05~0.1m),ap 对Ra 影响甚小。
39.识图:背吃刀量对加工表面残余应力的影响。
ap减小,表面残余应力减小;减小到一定值后增大;临界点与刀具锋锐度有关。
40.刀刃锋锐度:反映刀具切削刃的锋利程度,大小用刃口半径ρ(或rn)表示。
刃口半径ρ(或rn)愈小,表示刀刃愈锋利。
41.识图:刀刃锋锐度对加工表面粗糙度的影响。
两把车刀几何形状完全相同,仅锋锐度有差别,ρ1=0.6μm,ρ2=0.3μm。
结论:刀刃锋锐度对加工表面粗糙度有明显影响。
ρ增大,Rmax 增大。
两把刀具在不同背吃刀量ap 时的加工表面粗糙度两把刀具在不同进给量ƒ时的加工表面粗糙度结论:刀刃锋锐度对加工表面粗糙度有明显影响。
ρ增大,Rmax 增大。
42.刀刃锋锐度对切削变形和切削力的影响。
ρ↓,变形系数ξ↓,Fz↓。
ap 很小时,ρ值的很小变化将使ξ,Fz 产生很大变化。
(ap 很小时,要求ρ值小)43.刀刃锋锐度对切削表面层的冷作硬化和组织位错的影响。
ρ不同时,加工表面变质层的冷硬和显微硬度有明显差别。
ρ↑,ξ↑,位错密度增大。
(ρ↑,挤压和摩擦作用更强)即使刃口较锋利的情况下,也存在着加工硬化。
要求变质层小时,ρ↓。
44.刀刃锋锐度对加工表面残留应力的影响。
ρ增大,残余应力增大。
a p=1 μm为临界值,此时继续减小a p,残余应力增大。
45.超精密切削实际达到的最小切削厚度:研究结果证明,使用极锋锐的刀具和机床条件最佳的情况下,金刚石刀具的超精密切削,可以实现切削厚度为纳米级(1nm)的连续稳定切削。
46.金刚石各晶面特性:1) (100)晶面的摩擦系数曲线有4个波峰和波谷;(110)晶面的摩擦系数曲线有2个波峰和波谷;(111)晶面的摩擦系数曲线有3个波峰和波谷;2) 以摩擦系数的坡谷比较,(100)晶面最低,(111)次之,(110)晶面最高。
3) 同一晶面值的变化比较,(100)晶面最大,(110)次之,(111)晶面最小。
金刚石切削有色金属。
摩擦曲线比较波谷,越小越好(100)晶面最好。
47.金刚石晶面不同对切削变形的影响。
(100)晶面车刀切削时的切削变形< (110)晶面车刀的切削变形。
原因:(100)晶面μ小。
结论:晶面不同的刀具,切削变形不同,(100)晶面的车刀切削变形小。
48. 金刚石刀具晶面不同对加工表面质量的影响。
1.加工表面粗糙度(100)和(110)晶面车刀加工紫铜,相同切削条件,加工表面粗糙度相差不多。
2.加工表面残余应力(100)晶面车刀< (110)晶面车刀,特别是切向残余应力。
原因:(100)晶面车刀的μ小,→ξ↓,后刀面与加工表面摩擦↓,→残余应力↓。
这对要求残余应力小,要求长期尺寸稳定性高的精密零件的加工非常适合。
49.金刚石刀具晶面不同对刀具磨损的影响。