机械类外文翻译译文轴和齿轮的设计及应用
机械零件齿轮中英文对照外文翻译文献

(文档含英文原文和中文翻译)中英文资料对照外文翻译Machine Parts (I)GearsGears are direct contact bodies, operating in pairs, that transmit motion and force from one rotating shaft to another or from a shaft to a slide (rack), by means of successively engaging projections called teeth.Tooth profiles. The contacting surfaces of gear teeth must be aligned in such a way that the drive is positive; i.e., the load transmitted must not depend on frictional contact. As shown in the treatment of direct contact bodies, this requires that thecommon normal to the surfaces not to pass through the pivotal axis of either the driver or the follower.As it is known as direct contact bodies, cycloidal and involute profiles profiles provide both a positive drive and a uniform velocity ratio;i.e., conjugate action.Basic relations. The smaller of a gear pair is called the pinion and the larger is the gear. When the pinion is on the driving shaft the pair is called the pinion and the larger is the gear. When the pinion is on the driving shaft the pair acts as a speed reducer; When the gear drives, the pair is a speed incrreaser. Gears are more frequently used to reduce speed than to increase it.If a gear having N teeth rotates at n revolutions per minute, the product N*n has the dimension “teeth per minute”. This product must be the same for both members of a mating pair if each tooth acquires a partner from the mating gear as it passes through the region of tooth engagement.For conjugate gears of all types, the gear ratio and the speed ratio are both given by the ratio of the number of teeth on the gear to the number of teeth on the pinion. If a gear has 100 teeth and a mating pinion has 20, the ratio is 100/20=5. Thus the pinion rotates five times as fast as the gear, regardless of the gear. Their point of tangency is called the pitch point, and since it lies on the line of centers, it is the only point at which the profiles have pure roling contact. Gears on nonparallel, non-intersecting shafts also have pitch circles, but the rolling-pitch –circle concept is not valid.Gear types are determined largely by the disposition of the shafts; in addition, certain types are better suited than others for large speed changes. This means that if a specific disposition of the shafts is required, the type of gear will more or less be fixed. On the other hand, if a required speed change demands a certain type, the shaft positions will also be fixed.Spur gears and helical gears. A gear having tooth elements that are straight and parallel to its axis is known as a spur gear. A spur pair can be used to connect parallel shafts only.If an involute spur pinion were made of rubber and twisted uniformly so that the ends rotated about the axis relative to one another, the elements of the teeth, initially straight and parallel to the axis, would become helices. The pinion then in effect would become a helical gear.Worm and bevel gears. In order to achieve line contact and improve the load carrying capacity of the crossed axis helical gears, the gear can be made to curvepartially around the pinion, in somewhat the same way that a nut envelops a screw. The result would be a cylindrical worm and gear. Worms are also made in the shape of an hourglass, instead of cylindrical, so that they partially envelop the gear. This results in a further increase in load-carrying capacity.Worm gears provide the simplest means of obtaining large ratios in a single pair. They are usually less efficient than parallel-shaft gears, however, because of an additional sliding movement along the teeth.V-beltThe rayon and rubber V-belt are widely used for power transmission. Such belts are made in two series: the standard V-belt and the high capacity V-belt. The belts can be used with short center distances and are made endless so that difficulty with splicing devices is avoided.First, cost is low, and power output may be increased by operating several belts side by side. All belts in the drive should stretch at the same rate in order to keep the load equally divided among them. When one of the belts breaks, the group must usually be replaced. The drive may be inclined at any angle with tight side either top or bottom. Since belts can operate on relatively small pulleys, large reductions of speed in a single drive are possible.Second,the included angle for the belt groove is usually from 34°to 38°.The wedging action of the belt in the groove gives a large increase in the tractive force developed by the belt.Third,pulley may be made of cast iron, sheet steel, or die-cast metal. Sufficient clearance must be provided at the bottom of the groove to prevent the belt from bottoming as it becomes narrower from wear. Sometimes the larger pulley is not grooved when it is possible to develop the required tractive force by running on the inner surface of the belt. The cost of cutting the grooves is thereby eliminated. Pulleys are on the market that permit an adjustment in the width of the groove. The effective pitch diameter of the pulley is thus varied, and moderate changes in the speed ratio can be secured.Chain DrivesThe first chain-driven or “safety” bicycle appeared in 1874, and chains were used for driving the rear wheels on early automobiles. Today, as the result of modern design and production methods, chain drives that are much superior to their prototypes are available, and these have contributed greatly to thedevelopment of efficient agricultural machinery, well-drilling equipment, and mining and construction machinery. Since about 1930 chain drives have become increasingly popular, especially for power saws, motorcycle, and escalators etc.There are at least six types of power-transmission chains; three of these will be covered in this article, namely the roller chain, the inverted tooth, or silent chain, and the bead chain. The essential elements in a roller-chain drive are a chain with side plates, pins, bushings (sleeves), and rollers, and two or more sprocket wheels with teeth that look like gear teeth. Roller chains are assembled from pin links and roller links. A pin link consists of two side plates connected by two pins inserted into holes in the side plates. The pins fit tightly into the holes, forming what is known as a press fit. A roller link consists of two side plates connected by two press-fitted bushings, on which two hardened steel rollers are free to rotate. When assembled, the pins are a free fit in the bushings and rotate slightly, relative to the bushings when the chain goes on and leaves a sprocket.Standard roller chains are available in single strands or in multiple strands, In the latter type, two or more chains are joined by common pins that keep the rollers in the separate strands in proper alignment. The speed ratio for a single drive should be limited to about 10∶1; the preferred shaft center distance is from 30 to 35 times the distance between the rollers and chain speeds greater than about 2500 feet (800 meters) per minute are not recommended. Where several parallel shafts are to be driven without slip from a single shaft, roller chains are particularly well suited.An inverted tooth, or silent chain is essentially an assemblage of gear racks, each with two teeth, pivotally connected to form a closed chain with the teeth on the inside, and meshing with conjugate teeth on the sprocket wheels. The links are pin-connected flat steel plates usually having straight-sided teeth with an included angle of 60 degrees. As many links are necessary to transmit the power and are connected side by side. Compared with roller-chain drives, silent-chain drives are quieter, operate successfully at higher speeds, and can transmit more load for the same width. Some automobiles have silent-chain camshaft drives.Bead chains provide an inexpensive and versatile means for connecting parallel or nonparallel shafts when the speed and power transmitted are low. The sprocket wheels contain hemispherical or conical recesses into which the beads fit. The chains look like key chains and are available in plain carbon and stainless steel and also in the form of solid plastic beads molded on a cord. Bead chains are used oncomputers, air conditioners, television tuners, and Venetian blinds. The sprockets may be steel, die-cast zinc or aluminum, or molded nylon.Machine Parts (II)FastenerFasteners are devices which permit one part to be joined to a second part and, hence, they are involved in almost all designs.There are three main classifications of fasteners, which are described as follows:(1) Removable. This type permits the parts to be readily disconnected without damaging the fastener. An example is the ordinary nut-and-bolt fastener.(2) Semi permanent. For this type, the parts can be disconnected, but some damage usually occurs to the fastener. One such example is a cotter pin.(3) Permanent. When this type of fastener is used, it is intended that the parts will never be disassembled. Examples are riveted joints and welded joints.The importance of fasteners can be realized when referring to any complex product. In the case of the automobile, there are literally thousands of parts which are fastened together to produce the total product. The failure or loosening of a single fastener could result in a simple nuisance such as a door rattle or in a serious situation such as a wheel coming off. Such possibilities must be taken into account in the selection of the type of fastener for the specific application.Nuts, bolts, and screws are undoubtedly the most common means of joining materials. Since they are so widely used, it is essential that these fasteners attain maximum effectiveness at the lowest possible cost. Bolts are, in reality, carefully engineered products with a practically infinite use over a wide range of services.An ordinary nut loosens when the forces of vibration overcome those of friction. In a nut and lock washer combination, the lock washer supplies an independent locking feature preventing the nut from loosening. The lock washer is useful only when the bolt might loosen because of a relative change between the length of the bolt and the parts assembled by it. This change in the length of the bolt can be caused by a number of factors-creep in the bolt, loss of resilience, difference in thermal expansion between the bolt and the bolted members, or wear. In the above static cases, the expanding lock washer holds the nut under axial load and keeps the assembly tight. When relative changes are caused by vibration forces, the lock washer is not nearly as effective.Rivets are permanent fasteners. They depend on deformation of their structure for their holding action. Rivets are usually stronger than the thread-type fastener and are more economical on a first-cost basis. Rivets are driven either hot or cold,depending upon the mechanical properties of the rivet material. Aluminum rivets, for instance, are cold-driven, since cold working improves the strength of aluminum. Most large rivets are hot-driven, however.ShaftVirtually all machines contain shafts. The most common shape for shafts is circular and the cross section can be either solid or hollow (hollow shafts can result in weight savings).Shafts are mounted in bearings and transmit power through such devices as gears, pulleys, cams and clutches. These devices introduce forces which attempt to bend the shaft; hence, the shaft must be rigid enough to prevent overloading of the supporting bearings. In general, the bending deflection of a shaft should not exceed 0.01 in. per ft. of length between bearing supports.For diameters less than 3 in., the usual shaft material is cold-rolled steel containing about 0.4 percent carbon. Shafts are either cold-rolled or forged in sizes from 3 in. to 5 in. .For sizes above 5 in. , shafts are forged and machined to size. Plastic shafts are widely used for light load applications. One advantage of using plastic is safety in electrical applications, since plastic is a poor conductor of electricity.Another important aspect of shaft design is the method of directly connecting one shaft to another. This is accomplished by devices such as rigid and flexible couplings.BearingA bearing can be defined as a member specifically designed to support moving machine components. The most common bearing application is the support of a rotating shaft that is transmitting power from one location to another. Since there is always relative motion between a bearing and its mating surface, friction is involved. In many instances, such as the design of pulleys, brakes, and clutches, friction is desirable. However, in the case of bearings, the reduction of friction is one of the prime considerations:Friction results in loss of power, the generation of heat, and increased wear of mating surfaces.The concern of a machine designer with ball bearings and roller bearings is fivefold as follows:(1) Life in relation to load; (2) stiffness, i.e. deflections under load;(3) friction; (4) wear; (5) noise. For moderate loads and speeds the correct selection ofa standard bearing on the basis of load rating will usually secure satisfactoryperformance. The deflection of the bearing elements will become important where loads are high, although this is usually of less magnitude than that of the shafts or other components associated with the bearing. Where speeds are high special cooling arrangements become necessary which may increase frictional drag. Wear is primarily associated with the introduction of contaminants, and sealing arrangements must be chosen with regard to the hostility of the environment.Notwithstanding the fact that responsibility for the basic design of ball bearings and roller bearings rests with the bearing manufacturer, the machine designer must form a correct appreciation of the duty to be performed by the bearing and be concerned not only with bearing selection but with the conditions for correct installation.The fit of the bearing races onto the shaft or onto the housings is of critical importance because of their combined effect on the internal clearance of the bearing as well as preserving the desired degree of interference fit. Inadequate interference can induce serious trouble from fretting corrosion. The inner race is frequently located axially by abutting against a shoulder. A radius at this point is essential for the avoidance of stress concentration and ball races are provided with a radius or chamfer to allow space for this.A journal bearing, in its simplest form, is a cylindrical bushing made of a suitable material and containing properly machined inside and outside diameters. The journal is usually the part of a shaft or pin that rotates inside the bearing.Journal bearings operate with sliding contact, to reduce the problems associated with sliding friction in journal bearings, a lubricant is used in conjunction with compatible mating materials. When selecting the lubricant and mating materials, one must take into account bearing pressures, temperatures and also rubbing velocities. The principle function of the lubricant in sliding contact bearings is to prevent physical contact between the rubbing surfaces. Thus the maintenance of an oil film under varying loads, speeds and temperature is the prime consideration in sliding contact bearings.Introduction to Machinery DesignMachinery design is either to formulate an engineering plan for the satisfaction of a specified need or to solve an engineering problem. It involves a range of disciplines in materials, mechanics, heat, flow, control, electronics and production.Machinery design may be simple or enormously complex, easy or difficult, mathematical or nonmathematical, it may involve a trivial problem or one of great importance. Good design is the orderly and interesting arrangement of an idea to provide certain results or effects. A well-designed product is functional, efficient, and dependable. Such a product is less expensive than a similar poorly designed product that does not function properly and must constantly be repaired.People who perform the various functions of machinery design are typically called industrial designers. He or she must first carefully define the problem, using an engineering approach, to ensure that any proposed solution will solve the right problem. It is important that the designer begins by identifying exactly how he or she will recognize a satisfactory alternative, and how to distinguish between two satisfactory alternatives in order to identify the better. So industrial designers must have creative imagination, knowledge of engineering, production techniques, tools, machines, and materials to design a new product for manufacture, or to improve an existing product.In the modern industrialized world, the wealth and living standards of a nation are closely linked with their capabilities to design and manufacture engineering products. It can be claimed that the advancement of machinery design and manufacturing can remarkably promote the overall level of a country’s industrization. Our country is playing a more and more vital role in the global manufacturing industry. To accelerate such an industrializing process, highly skilled design engineers having extensive knowledge and expertises are needed.Machinery ComponentsThe major part of a machine is the mechanical system. And the mechanical system is decomposed into mechanisms, which can be further decomposed into mechanical components. In this sense, the mechanical components are the fundamental elements of machinery. On the whole, mechanical components can be classified as universal and special components. Bolts, gear, and chains are the typical examples of the universal components, which can be used extensively in different machines across various industrial sectors. Turbine blades, crankshaft and aircraftpropeller are the examples of the special components, which are designed for some specific purposes.Mechanical Design ProcessProduct design requires much research and development. Many concepts of an idea must be studied, tried, refined, and then either used or discarded. Although the content of each engineering problem is unique, the designers follow the similar process to solve the problems.Recognition of NeedSometimes, design begins when a designer recognizes a need and decides to do something about it. The need is often not evident at, all; recognition is usually triggered by a particular adverse circumstance or a set of random circumstances, which arise almost simultaneously. Identification of need usually consists of an undefined and vague problem statement.Definition of ProblemDefinition of problem is necessary to fully define and understand the problem, after which it is possible to restate the goal in a more reasonable and realistic way than the original problem statement. Definition of the problem must include all the specifications for the thing that is to be designed. Obvious items in the specifications are the speeds, feeds, temperature limitations, maximum range, expected variation in the variables, and dimensional and weight limitations.SynthesisThe synthesis is one in which as many alternative possible design approaches are sought, usually without regard for their value or quality. This is also sometimes called the ideation and invention step in which the largest possible number of creative solutions is generated. The synthesis activity includes the specification of material, addition of geometric features, and inclusion of greater dimensional detail to the aggregate design.AnalysisAnalysis is a method of determining or describing the nature of something by separating it into its parts. In the process the elements, or nature of the design, are analyzed to determine the fit between the proposed design and the original design goals.EvaluationEvaluation is the final proof of a successful design and usually involves thetesting of a prototype in the laboratory. Here we wish to discover if the design really satisfies the needs.The above description may give an erroneous impression that this process can be accomplished in a linear fashion as listed. On the contrary, iteration is required within the entire process, moving from any step back to any previous step, in all possible combinations, and doing this repeatedly.PresentationCommunicating the design to others is the finial, vital presentation step in the design process. Basically, there are only three means of communication. These are the written, the oral, and the graphical forms. A successful engineer will be technically competent and versatile in all three forms of communication. The competent engineer should not be afraid of the possibility of not succeeding in a presentation. In fact, the greatest gains are obtained by those willing to risk defeat.Contents of Machinery DesignMachinery design is an important technological basic course in mechanical engineering education. Its objective is to provide the concepts, procedures, data, and decision analysis techniques necessary to design machine elements commonly found in mechanical devices and systems; to develop engineering students’ competence of machine design that is the primary concern of machinery manufacturing and the key to manufacture good products.Machinery design covers the following contents:Provides an introduction to the design process, problem formulation, safety factors.Reviews the material properties and static and dynamic loading analysis, including beam, vibration and impact loading.Reviews the fundamentals of stress and defection analysis.Introduces static failure theories and fracture-mechanics analysis for static loads.Introduces fatigue-failure theory with the emphasis on stress-life approaches to high-cycle fatigue design, which is commonly used in the design of rotation machinery.Discusses thoroughly the phenomena of wear mechanisms, surface contact stresses, and surface fatigue.Investigates shaft design using the fatigue-analysis techniques.Discusses fluid-film and rolling-element bearing theory and application.Gives a thorough introduction to the kinematics, design and stress analysis of spur gears, and a simple introduction to helical, bevel, and worm gearing.Discusses spring design including helical compression, extension and torsion springs.Deals with screws and fasteners including power screw and preload fasteners.Introduces the design and specification of disk and drum clutches and brakes.机械零件(I)齿轮齿轮是直接接触,成对工作的实体,在称为齿的凸出物的连续啮合作用下,齿轮能将运动和力从一个旋转轴传递到另一个旋转轴,或从一个轴传递到一个滑块(齿条)。
机械工程及自动化专业外文翻译--齿轮的特点和作用

外文原文:Gear features and functionsAbstractGears in the mechanical equipment to achieve an integral, it is a lot of superior performance. The appropriate gear and reasonable use of transmission gears can improve equipment performance but also could prolong gear life.KeywordsGear, characteristics, fault, applicationWheel gear's spreading to move is a the most wide kind of the application spreads to move a form in the modern machine.Its main advantage BE1 spreads to move to settle, work than in a moment steady, spread to move accurate credibility, can deliver space arbitrarily sport and the motive of the of two stalks;Power and speed scope2 applies are wide;3 spreads to move an efficiency high, η =0.92-0.98;4 work is dependable, service life long;5 Outline size outside the is small, structure tightly packed.The wheel gear constituted to°;;;from wheel gear, stalk, bearings and box body decelerates a machine, useding for prime mover and work machine or performance organization of, have already matched to turn soon and deliver a function of turning , the application is extremely extensive in the modern machine.6 Local deceleration machine much with the wheel gear spread to move, the pole spread to move for lord, but widespread exist power and weightratio small, or spread to move ratio big but the machine efficiency leada low problem.There are also many weaknesses on material quality and craftlevel moreover, the especially large deceleration machine's problem ismore outstanding, the service life isn't long.The deceleration machineof abroad, with Germany, Denmark and Japan be placed in to lead a position,occupying advantage in the material and the manufacturing craft specially,decelerating the machine work credibility like, service life long.But itspreads to move a form to still take settling stalk wheel gear to spreadto move as lord, physical volume and weight problem, don't also resolvelike The direction which decelerates a machine to is the facing big powerand spread to move ratio, small physical volume, high machine efficiencyand service life to grow greatly nowadays develops.Decelerating theconnecting of machine and electric motor body structure is also the formwhich expands strongly, and have already produced various structure formsand various products of power model numbers.Be close to ten several inthe last yearses, control a technical development because of the moderncalculator technique and the number, make the machine process accuracy,process an efficiency to raise consumedly, pushed a machine to spread thediversification of movable property article thus, the mold piece of thewhole machine kit turns, standardizing, and shape design the art turn,making product more fine, the beauty turns. Become a set a machine material In 21 centuries medium, the wheel gear is still a machine to spreada dynamic basic C tool machine and the craft technical development,pushed a machine to spread to move structure to fly to develop soon.Bespreading to move the electronics control, liquid in the system designto press to spread to move, wheel gear, take the mixture of chain to spreadto move, will become become soon a box to design in excellent turn to spreadto move a combination of direction.The academics that is in spread movethe design crosses, will become new spread a movable property article theimportant trend of the development. Is the use of gear teeth of two gears meshing each other transmission of mechanical power and motion transmission. According to the relative position of the gear axis parallel to axis of cylindrical sub-gear drive, bevel gear axis intersect and cross-axis helical drive gear. Compact structure, high efficiency, long life and so on. Gear refers to the main, driven wheel gear direct, movement and power transmission devices. Of all the mechanical transmission, the most widely used gear can be used to transfer between any two axes of motion and power.The characteristics of gear is: a smooth gear transmission, the transmission ratio accurate, reliable, high efficiency, long life, the use of power, speed and size range. For example, transmission of power from small to almost 100,000 kilowatts; speeds of up to 300m / s; gear diameter from a few millimeters to more than 20 meters. However, the need for specialized gear manufacturing equipment, the meshing noise transmission. Gear failure for the five forms, should be the appropriate design criteria established. However, tooth wear, plastic deformation and so on, as they have not been widely established and well-established engineering practice to use the calculation method and design data, so the gear drive design, it is usually only on the guarantee that the tooth root bending fatigue strength and tooth surface to ensure contact fatigue strength calculation of the two criteria. For high-power high-speed gear transmission (such as aero-engine main drive, drive turbine-generator unit, etc.), but also ensure the tooth surface by the anti-bonding capacity calculation guidelines. As for the ability to resist other failure, although generally not at present be calculated, but the measures to be taken to strengthen the tooth's ability to resist these failures.1 closed gear transmission Informed by practice, in the closed gear transmission, usually to ensure that the main tooth contact fatiguestrength. Tooth surface hardness for high strength and low core-tooth gear (such as 20,20 Cr steel by quenching after carburizing gears) or a more brittle material of the gear, usually at the tooth root bending fatigue strength to ensure that the main. If the two gears are hardened and the tooth surface hardness as high as, then as the case may be. Larger transmission power, such as the input power of 75kW closed more than gear, heat, easy to lead to bad lubrication and gear damage, such as glue, in order to control the temperature rise, but also for calculation of cooling capacity.2 open-gear transmission Open (semi-open) gear drive, according to tooth surface is supposed to be based to ensure that anti-wear and anti-fracture ability Dedendum two criteria are calculated, but as mentioned earlier, on the tooth surface abrasion resistance of the method of calculating capacity is not perfect yet, so off-type (semi-open) gear drive, the current only to ensure that the tooth root bending fatigue strength as a design criteria. In order to extend the open (semi-open) the life of gear, the specific needs of visualization to be obtained by increasing the appropriate modulus. Reducer is the prime mover with an independent closed between the work gear to reduce speed and to increase torque. In addition, in some occasions, there are devices used for growth, and known as the accelerator. When the motor output shaft speed input from the initiative, the drive pinion rotation, and the drive pinion gear movement, and a large number of teeth than the gear pinion, and the speed ratio gear pinion slow, then the shaft gear ( output shaft) output, which has played the role of output slowdown. Reducer of the type, variety, many types have been formulated for the trip (the country) the subject of more than 40 kinds of reducer. Reducer is based on the type of gear used, tooth profile curve divided; reducer species is based on the use of the different needs of the reducer structure; the type of reducer in the basic structure ofthe tooth surface, based on hardness, transmission level, the shaft type, assembly type, installation type, connection type and other factors designed reducer different characteristics. Reducer connected with the work load of the state of more complex machines, a great impact on the speed reducer is a reducer selection and calculation of an important factor in the load reducer that is the work of the state machine (from the motives) of the load, and is usually divided into three categories: 1 uniform load;2 Medium impact load; 3 strong impact load. Mechanical aspects of the slowdown in the devices typically are:1 for the speed is relatively small, less torque on the gear drive system - ranging from a pair of gear teeth (speed) or a range of gear teeth ( variable speed). Large number of teeth for which the driving wheel, a large number of teeth used for the driven wheel.2 for speed is relatively small, a larger torque on the gear drive system - a screw and a gear. Screw driving force with which to make decisions. If the gear teeth for N, while rotating around each gear, screw on the ring must be rotating N.3 for the speed ratio, and torque transmission on a large turbine vice - a rod and a vortex turbine. Used to decide under which vortex dynamics. If the turbine for the number of teeth N, while rotating around each turbine, vortex must be rotating N pole lap. Air power plant is typically used for turbine Vice reducer.Its role is to:1 deceleration at the same time increase the output torque, torque output by motor output by the ratio of reduction ratio, but bearing in mind that do not exceed the rated torque reducer.2 The speed at the same time reducing the load inertia, the reduction of inertia than the square of speed. We can look at General Electric has a value of inertia. There is a general helical gear reducer reducer(including parallel shaft helical gear reducer, worm gear reducer, bevel gear reducer, etc.), planetary gear reducer, cycloid reducer, worm gear reducer, planetary-type friction mechanical CVT machine and so on. And we have a common type of speed reducer:1 worm gear reducer is a main feature of the reverse self-locking function, can have a larger reduction ratio, input shaft and output shaft axis is not the same, nor in the same plane . But in general larger, the transmission efficiency is not high, the accuracy is not high.2 harmonic of the harmonic drive speed reducer is to use flexible components of the elastic deformation controlled to convey movement and momentum, and volume not very high accuracy, but the drawback is the limited life Flexspline, the impact of intolerance, rigidity and metal pieces compared to poor.3 planetary reducer compare the advantage of compact structure, the return gap small, high precision, long life, rated output torque can do a lot. Enter the speed can not be too high. However, the price a little expensive. Mechanical transmission is the use of mechanical power transmission and motion transmission. Mechanical transmission in mechanical engineering in a wide range of applications, there are a variety of forms, can be divided into two categories1 by mechanical friction between the transmission of power and movement of the friction drive, including belt drive, rope drive and friction wheel drive and so on. Easy to achieve continuously variable friction transmission, and most of them can adapt to the larger axis of the transmission distance of occasions, been able to play a buffer containing the spin and the role of the protection gear, but generally can not be used for high-power transmission of the occasion, there is no guarantee that an accurate the transmission ratio.2 items by active engagement with the follower, or through transmissionof power or middleware meshing engagement campaign drive, including the gear drive, chain drive, screw drive and harmonic drive and so on. Meshing can be used for high-power transmission of the occasions, the exact transmission ratio, but the general requirements for the manufacture of high precision and accuracy of the installation. The form of mechanical transmission is divided into: friction drive, chain drive, gear drive, belt drive, under vortex turbine drive, ratchet drive, the crankshaft connecting rod drive, pneumatic drive, hydraulic transmission (hydraulic plane), universal joint transmission,steel transmission (the most widely elevator) drive coupling, spline drive.中文译文:齿轮的特点和作用摘要齿轮实现在机械设备中不可缺少的组成,它很多优越的性能。
轴和齿轮的设计及应用外文翻译、中英文翻译、外文文献翻译

英文原文:SHAFT AND GEAR DESIGNAbstract: The important position of the wheel gear and shaft can' t falter in traditional machine and modern machines. The wheel gear and shafts mainly install the direction that delivers the dint at the principal axis box. The passing to process to make them can is divided into many model numbers, useding for many situations respectively. So we must be the multilayers to the understanding of the wheel gear and shaft in many waysKey words : Wheel gear ; ShaftIn the force analysis of spur gears, the forces are assumed to act in a single plane .We shall study gears in which the forces have three dimensions.The reason for this, in the case of helical gears, is that the teeth are not parallel to the axis of rotation. And in the case of bevel gears, the rotational axes are not parallel to each other. There are also other reasons, as we shall learn.Helical gears are used to transmit motion between parallel shafts. The helix angle is the same on each gear, but one gear must have a right-hand helix and the other a left-hand helix. The shape of the tooth is an involute helicoid. If a piece of paper cut in the shape of a parallelogram is wrapped around a cylinder, the angular edge of the paper becomes a helix. If we unwind this paper, each point on the angular edge generates an involute curve. The surface obtained when every point on the edge generates an involute is called an involute helicoid. The initial contact of spur-gear teeth is a line extending all the way across the face of the tooth. The initial contact of helical gear teeth is a point, which changes into a line as the teeth come into more engagement. In spur gears the line of contact is parallel to the axis of the rotation; in helical gears, the line is diagonal across the face of the tooth. It is this gradual of the teeth and the smooth transfer of load from one tooth to another, which give helical gears the ability to transmit heavy loads at high speeds. Helical gears subject the shaft bearings to both radial and thrust loads. When the thrust loads become high or are objectionable for other reasons, it may be desirable to use double helical gears. A double helical gear (herringbone) is equivalent to two helical gears of opposite hand, mounted side byside on the same shaft. They develop opposite thrust reactions and thus cancel out the thrust load. When two or more single helical gears are mounted on the same shaft,the hand of the gears should be selected so as to produce the minimum thrust load Crossed-helical, or spiral, gears are those in which the shaft centerlines are neither parallel nor intersecting. The teeth of crossed-helical fears have point contact with each other, which changes to line contact as the gears wear in. For this reason they will carry out very small loads and are mainly for instrumental applications, and are definitely not recommended for use in the transmission of power There is on difference between a crossed heli cal gear and a helical gear until they are mounted in mesh with each other. They are manufactured in the same way. A pair of meshed crossed helical gears usually have the same hand; that is , a right-hand driver goes with a right-hand driven. In the design of crossed-helical gears, the minimum sliding velocity is obtained when the helix angle are equal. However, when the helix angle are not equal, the gear with the larger helix angle should be used as the driver if both gears have the same handWorm gears are similar to crossed helical gears. The pinion or worm has a small number of teeth, usually one to four, and since they completely wrap around the pitch cylinder they are called threads. Its mating gear is called a worm gear, which is not a true helical gear. A worm and wormgear are used to provide a high angular-velocity reduction between nonintersecting shafts which are usually at right angle. The worm gear is not a helical gear because its face is made concave to fit the curvature of the worm in order to provide line contact instead of point contact. However, a disadvantage of worm gearing is the high sliding velocities across the teeth, the same as with crossed helical gearsWorm gearing are either single or double enveloping. A single-enveloping gearing is one in which the gear wraps around or partially encloses the worm. . A gearing in which each element partially encloses the other is, of course, a double-enveloping worm gearing. The important difference between the two is that area contact exists between the teeth of doubleenveloping gears while only line contact between those of single-enveloping gears. The worm and worm gear of a set have the same hand ofhelix as for crossed helical gears, but the helix angles are usually quite different The helix angle on the worm is generally quite large, and that on the gear very small Because of this, it is usual to specify the lead angle on the worm, which is the complement of the worm helix angle, and the helix angle on the gear; the two angles are equal for a 90-deg. Shaft angleWhen gears are to be used to transmit motion between intersecting shaft, some of bevel gear is required. Although bevel gear are usually made for a shaft angle of 90 deg. They may be produced for almost any shaft angle. The teeth may be cast, milled, or generated. Only the generated teeth may be classed as accurate. In a typical bevel gear mounting, one of the gear is often mounted outboard of the bearing. This means that shaft deflection can be more pronounced and have a greater effect on the contact of teeth. Another difficulty, which occurs in predicting the stress in bevel-gear teeth, is the fact the teeth are tapered.Straight bevel gears are easy to design and simple to manufacture and give very good results in service if they are mounted accurately and positively. As in the case of squr gears, however, they become noisy at higher values of the pitch-line velocity In these cases it is often go od design practice to go to the spiral bevel gear, which is the bevel counterpart of the helical gear. As in the case of helical gears, spiral bevel gears give a much smoother tooth action than straight bevel gears, and hence are useful where high speed are encountered. It is frequently desirable, as in the case of automotive differential applications, to have gearing similar to bevel gears but with the shaft offset. Such gears are called hypoid gears because their pitch surfaces are hyperboloids of revolution The tooth action between such gears is a combination of rolling and sliding alonga straight line and has much in common with that of worm gears A shaft is a rotating or stationary member, usually of circular cross section, having mounted upon it such elementsas gears, pulleys, flywheels, cranks, sprockets, and other power-transmission elements. Shaft may be subjected to bending, tension, compression, or torsional loads, acting singly or in combination with one another. When they are combined, one may expect to find both static and fatigue strength tobe important design considerations, since a single shaft may be subjected to static stresses, completely reversed, and repeated stresses, all acting at the same time The word "shaft" covers numerous variations, such as axles and spindles. Anaxle is a shaft, wither stationary or rotating, nor subjected to torsion load. A shirt rotating shaft is often called a spindle. When either the lateral or the torsional deflection of a shaft must be held to close limits, the shaft must be sized on the basis of deflection before analyzing the stresses. The reason for this is that, if the shaft is made stiff enough so that the deflection is not too large, it is probable that the resulting stresses will be safe. But by no means should the designer assume that they are safe; it is almost always necessary to calculatethem so that he knows they are within acceptable limits Whenever possible, the power-transruission elements, such as gears or pullets, should be located close to the supporting bearings, This reduces the bending moment, and hence the deflection and bending stress.Although the von Mises-Hencky-Goodman method is difficult to use in design of shaft, it probably comes closest to predicting actual failure. Thus it is a good way of checking a shaft that has already been designed or of discovering why a particular shaft has failed in service. Furthermore, there are a considerable number of shaft-design problems in which the dimension are pretty well limited by other considerations, such as rigidity, and it is only necessary for the designer to discover something about the fillet sizes, heat-treatment, and surface finish and whether or not shot peening is necessary in order to achieve the required life and reliability Because of the similarity of their functions, clutches and brakes are treated together. In a simplified dynamic representation of a friction clutch, or brake two in ertias 11 and 12 traveling at the respective angular velocities Wl and W2, one of which may be zero in the case of brake, are to be brought to the same speed by engaging the clutch or brake. Slippage occurs because the two elements are running at different speeds and energy is dissipated during actuation, resulting in a temperature rise. In analyzing the performance of these devices we shall beinterested in the actuating force, the torque transmitted, the energy loss and the temperature rise. The torque transmitted is related to the actuating force, the coefficient of friction, and the geometry of the clutch or brake. This is problem in static, which will have to be studied separately for eath geometric configuration. However, temperature rise is related to energy loss and can be studied without regard to the type of brake or clutch because the geometry of interest is the heat-dissipating surfaces. The various types of clutches and brakes may be classified as fllows1. Rim type with internally expanding shoes2. Rim type with externally contracting shoes3。
机械制造专业外文翻译-轴、联轴器和滚动轴承
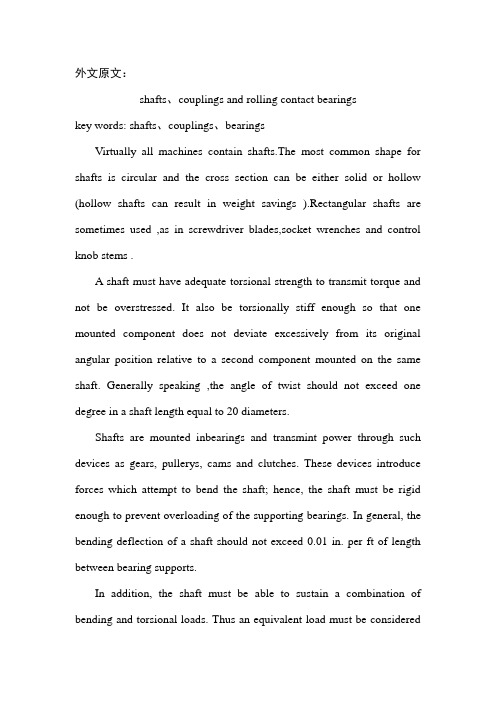
外文原文:shafts、couplings and rolling contact bearingskey words: shafts、couplings、bearingsVirtually all machines contain shafts.The most common shape for shafts is circular and the cross section can be either solid or hollow (hollow shafts can result in weight savings ).Rectangular shafts are sometimes used ,as in screwdriver blades,socket wrenches and control knob stems .A shaft must have adequate torsional strength to transmit torque and not be overstressed. It also be torsionally stiff enough so that one mounted component does not deviate excessively from its original angular position relative to a second component mounted on the same shaft. Generally speaking ,the angle of twist should not exceed one degree in a shaft length equal to 20 diameters.Shafts are mounted inbearings and transmint power through such devices as gears, pullerys, cams and clutches. These devices introduce forces which attempt to bend the shaft; hence, the shaft must be rigid enough to prevent overloading of the supporting bearings. In general, the bending deflection of a shaft should not exceed 0.01 in. per ft of length between bearing supports.In addition, the shaft must be able to sustain a combination of bending and torsional loads. Thus an equivalent load must be consideredwhich takes into account both torsion and bending. Also, the allowable stress must contain a factor of safety which includes fatigue, since torsional and bending stress reversals occur.For diameters less than 3 in. , the usual shaft material is cold-rolled ateel containing about 0.4 percent carbon. Shafts are either cold-rolled or forged in sizes from 3 in. to 5 in. ,shafts are forged and machined to size .Pleastic shafts are widely used for light load applications. One advantage of using plastic is safety in electrical applications ,since plastic is a poor conductor of electricity.Components such as gears and pulleys are mounted on shafts by means of key .The design of the key and the corresponding keyway in the shaft must be prperly evaluated. For example ,stress concentrations occur in shafts due to keyways ,and the material removed to form the keyway further weakens the shaft.If shafts are run at cirtical speeds ,severe vibrations can occur which can seriously damage a machine. It is important to know the magnitude of these critical speeds so that they can be avoided. As a general rule of thumb,the difference between the operating speed and the critical speed should be at least 20 percent .Another important aspect of shaft design is the method of directly connecting one shaft to another. This is accomplished by devices such as rigid and flexible couplings.A coupling is a device for connecting the eds of adjacent shafts. In machine construction, ouplings are used to effect a semipermanent connection between adjacent rotating shafts. The connection is permanent in the sense that it is not meant to be broken during the useful life of the machine, but it can be broken and restored in an emergency or when worn parts are replaced.There are several types of shaft couplings, their characteristics depend on the purpose for which they are used. If an exceptionally long shaft is required in a manufacturing plant or a propeller shaft on a ship, it is made in sections that are coupled together with rigid couplings. A common type of rigid coupling consists of two mating radial flanges(disks) that are cttached by key-driven hubs to the eds of adjacent shaft sections and bolted together through the flanges to form a rigid connection. Alignment of the connected shafts is usually effeted by means of a rabbet joint on the face of the flanges.In connecting shafts belonging to separate devices (such as an electric motor and a gearbox ),precise aligning of the shafts is difficult and a flexible coupling is used. This coupling connects theshafts in such a way as to minimize the harmful effects of shaft misalignment. Flexible couplings also permit the shafts to deflect under their separate systems of with one another. Flexible couplings can also serve to reduce the intensity of shock loads and vibrations transmitted from one shaft to another.Virtually all shafts contain rolling contact bearings.The concern of a machine designer with ball and roller bearings is fivefold as follows:(a) life in relation to load; (b) stiffness ,i.e. deflections under load; (c) friction;(d) wear; (e) noise. For moderate loads and speeds the correct selection of a standard bearing on the basis of load rating will usually secure satisfactory performance. The deflection of the bearing elements will become important where loads are high, although this is usuallyof less magnitude than that of the shafts or other components associated with the bearing. Where speeds are high special cooling arrangements become necessary which may increase frictional drag. Wear is primarily associated with the introduction of contaminants, and sealing arrangements must be chosen with regard the hostility of the environment.Because the high quality and low price of ball and roller bearings depends on quantity production, the task of the machine designer becomes one of selection rather than design. Rolling-contact bearings are generally made with ateel which is through-hardened toabout 900HV,although in many mechanisms special races are not provided and the interacting surfaces are hardened to about 600 HV. It is not surprising that, owing to the high stresses involved, a predominant form of failure should be metal fatigue, and a good deal of work is currently in progress intended to improve the reliability of this type of bearing. Design can bebased on accepted values of life and it is generral practice in the bearing industry to define the load capacity of the bearing as that value below which 90 lpercent of a batch will exceed a lift of ane million revolutions.Notwithstanding the fact that responsibility for the basic design of ball and roller bearings rests with the bearing manufacturer, the machine designer must form a correct appreciation of the duty to be performed by the bearing and be concerned not only with bearing selection but with the conditions for correct installation.The fit of the bearing races onto the shaft or onto the housings is of critical importance because of their combined effect on the internal clearance of the bearing as well as preserving the desired degree of interference fit. Inadequate interference can induce serious trouble from fretting corrosion. The inner race is frequently located axially by abutting against a shoulder. A radius at this point is essential for the avoidance of stress concentration and ball races are provides with a radius or chamfer to allow space for this .Where life is not the determining factor in design, it is usual to determine maximum loading by the amount towhich a bearing will deflect under load. Thus the concept of “static load-carrying capacity” is understood to mean the load that can be alpplied to a bearing, which is either stationary or subject to slight swiveling motions, without impairing its running qualities for subsequent rotational motion. This has beendetermined by practical experience as the load which when applied to a bearing results in a total deformation of the rolling element and raceway at any point of contact not exceeding 0.01 percent of the rolling-element diameter. This would correspond to a permanent deformation of 0.00025 mm for a ball 25mm in diameter.The successful functioning of many bearing depends upon providing them with adequate protection against their environment, and in some circumstances the enviroration of the bering surfaces. Achievement of the correct functioning of seals is an essential part of bearing design. Moreover, seals which are applied to moving parts for any purpose are of interest to tribologists because they are components of bearing systems and can only be designed satisfactorily on the basis of the approlpriate bearing theory. Notwithstanding their importance, the amount of research effort that has been devoted to the understanding of the understanding of the behavior of seals has been small when compared with that devoted to other aspects of bearing technology.References:1 Erickson.Belt and Application for Engineers.Marcel Dekker.Inc,19972 South,Mancuso.Mechanical Power Transmission Components.1994中文译文:轴、联轴器和滚动轴承关键词:轴、联轴器、轴承实际上,几乎所有的机器中都装有轴。
齿轮和轴的介绍外文文献翻译、中英文翻译

XX设计(XX)外文资料翻译院系专业学生姓名班级学号外文出处Manufacturing Engineering andTechnology-Machining附件:1.外文资料翻译译文(约3000汉字);2.外文资料原文(与课题相关的1万印刷符号左右)。
附件1:外文资料翻译译文齿轮和轴的介绍摘要在传统机械和现代机械中齿轮和轴的重要地位是不可动摇的。
齿轮和轴主要安装在主轴箱来传递力的方向。
通过加工制造它们可以分为许多的型号,分别用于许多的场合。
所以我们对齿轮和轴的了解和认识必须是多层次多方位的。
关键词:齿轮;轴在直齿圆柱齿轮的受力分析中,是假定各力作用在单一平面的。
我们将研究作用力具有三维坐标的齿轮。
因此,在斜齿轮的情况下,其齿向是不平行于回转轴线的。
而在锥齿轮的情况中各回转轴线互相不平行。
像我们要讨论的那样,尚有其他道理需要学习,掌握。
斜齿轮用于传递平行轴之间的运动。
倾斜角度每个齿轮都一样,但一个必须右旋斜齿,而另一个必须是左旋斜齿。
齿的形状是一渐开线螺旋面。
如果一张被剪成平行四边形(矩形)的纸张包围在齿轮圆柱体上,纸上印出齿的角刃边就变成斜线。
如果我展开这张纸,在血角刃边上的每一个点就发生一渐开线曲线。
直齿圆柱齿轮轮齿的初始接触处是跨过整个齿面而伸展开来的线。
斜齿轮轮齿的初始接触是一点,当齿进入更多的啮合时,它就变成线。
在直齿圆柱齿轮中,接触是平行于回转轴线的。
在斜齿轮中,该先是跨过齿面的对角线。
它是齿轮逐渐进行啮合并平稳的从一个齿到另一个齿传递运动,那样就使斜齿轮具有高速重载下平稳传递运动的能力。
斜齿轮使轴的轴承承受径向和轴向力。
当轴向推力变的大了或由于别的原因而产生某些影响时,那就可以使用人字齿轮。
双斜齿轮(人字齿轮)是与反向的并排地装在同一轴上的两个斜齿轮等效。
他们产生相反的轴向推力作用,这样就消除了轴向推力。
当两个或更多个单向齿斜齿轮被在同一轴上时,齿轮的齿向应作选择,以便产生最小的轴向推力。
外文翻译---齿轮的设计、制造和应用

毕业设计(论文)外文资料翻译学院:专业:机械设计制造及其自动化姓名:学号:外文出处: Mechanism and Machine Theory34 (1999) 857-876(用外文写)附件: 1.外文资料翻译译文;2.外文原文。
附件1:外文资料翻译译文动力传动圆锥渐开线齿轮的设计、制造和应用Dr. J. Börner,K. Humm,Dr. F. Joachim,Dr. H. akaria,ZF Friedrichshafen AG , 88038Friedrichshafen, Germany;[摘要]圆锥渐开线齿轮(斜面体齿轮)被用于交叉或倾斜轴变速器和平行轴自由侧隙变速器中。
圆锥齿轮是在齿宽横断面上具有不同齿顶高修正(齿厚)的直齿或斜齿圆柱齿轮。
这类齿轮的几何形状是已知的,但应用在动力传动上则多少是个例外。
ZF公司已将该斜面体齿轮装置应用于各种场合:4W D轿车传动装置、船用变速器(主要用于快艇)机器人齿轮箱和工业传动等领域。
斜面体齿轮的模数在0. 7 mm-8 mm之间,交叉传动角在0°- 25°。
之间。
这些边界条件需要对斜面体齿轮的设计、制造和质量有一个深入的理解。
在锥齿轮传动中为获得高承载能力和低噪声所必须进行的齿侧修形可采用范成法磨削工艺制造。
为降低制造成本,机床设定和由于磨削加工造成的齿侧偏差可在设计阶段利用仿真制造进行计算。
本文从总体上介绍了动力传动变速器斜面体齿轮的研发,包括:基本几何形状、宏观及微观几何形状的设计、仿真、制造、齿轮测量和试验。
1前言在变速器中如果各轴轴线不平行的话,转矩传递可采用多种设计,例如:伞齿轮或冠齿轮、万向节轴或圆锥渐开线齿轮(斜面体齿轮)。
圆锥渐开线齿轮特别适用于小轴线角度(小于15°),该齿轮的优点是在制造、结构特点和输入多样性等方而的简易。
圆锥渐开线齿轮被用于直角或交叉轴传动的变速器或被用于平行轴自由侧隙工况的变速器。
中英文文献翻译-轴和齿轮的设计及应用

英文原文:SHAFT AND GEAR DESIGNAbstract: The important position of the wheel gear and shaft can' t falter in traditional machine and modern machines. The wheel gear and shafts mainly install the direction that delivers the dint at the principal axis box. The passing to process to make them can is divided into many model numbers, useding for many situations respectively. So we must be the multilayers to the understanding of the wheel gear and shaft in many waysKey words : Wheel gear ; ShaftIn the force analysis of spur gears, the forces are assumed to act in a single plane .We shall study gears in which the forces have three dimensions.The reason for this, in the case of helical gears, is that the teeth are not parallel to the axis of rotation. And in the case of bevel gears, the rotational axes are not parallel to each other. There are also other reasons, as we shall learn.Helical gears are used to transmit motion between parallel shafts. The helix angle is the same on each gear, but one gear must have a right-hand helix and the other a left-hand helix. The shape of the tooth is an involute helicoid. If a piece of paper cut in the shape of a parallelogram is wrapped around a cylinder, the angular edge of the paper becomes a helix. If we unwind this paper, each point on the angular edge generates an involute curve. The surface obtained when every point on the edge generates an involute is called an involute helicoid. The initial contact of spur-gear teeth is a line extending all the way across the face of the tooth. The initial contact of helical gear teeth is a point, which changes into a line as the teeth come into more engagement. In spur gears the line of contact is parallel to the axis of the rotation; in helical gears, the line is diagonal across the face of the tooth. It is this gradual of the teeth and the smooth transfer of load from one tooth to another, which give helical gears the ability to transmit heavy loads at high speeds. Helical gears subject the shaft bearings to both radial and thrust loads. When the thrust loads become high or are objectionable for other reasons, it may be desirable to use double helical gears. A double helical gear (herringbone) is equivalent to two helical gears of opposite hand, mounted side byside on the same shaft. They develop opposite thrust reactions and thus cancel out the thrust load. When two or more single helical gears are mounted on the same shaft,the hand of the gears should be selected so as to produce the minimum thrust load Crossed-helical, or spiral, gears are those in which the shaft centerlines are neither parallel nor intersecting. The teeth of crossed-helical fears have point contact with each other, which changes to line contact as the gears wear in. For this reason they will carry out very small loads and are mainly for instrumental applications, and are definitely not recommended for use in the transmission of power There is on difference between a crossed heli cal gear and a helical gear until they are mounted in mesh with each other. They are manufactured in the same way. A pair of meshed crossed helical gears usually have the same hand; that is , a right-hand driver goes with a right-hand driven. In the design of crossed-helical gears, the minimum sliding velocity is obtained when the helix angle are equal. However, when the helix angle are not equal, the gear with the larger helix angle should be used as the driver if both gears have the same handWorm gears are similar to crossed helical gears. The pinion or worm has a small number of teeth, usually one to four, and since they completely wrap around the pitch cylinder they are called threads. Its mating gear is called a worm gear, which is not a true helical gear. A worm and wormgear are used to provide a high angular-velocity reduction between nonintersecting shafts which are usually at right angle. The worm gear is not a helical gear because its face is made concave to fit the curvature of the worm in order to provide line contact instead of point contact. However, a disadvantage of worm gearing is the high sliding velocities across the teeth, the same as with crossed helical gearsWorm gearing are either single or double enveloping. A single-enveloping gearing is one in which the gear wraps around or partially encloses the worm. . A gearing in which each element partially encloses the other is, of course, a double-enveloping worm gearing. The important difference between the two is that area contact exists between the teeth of doubleenveloping gears while only line contact between those of single-enveloping gears. The worm and worm gear of a set have the same hand ofhelix as for crossed helical gears, but the helix angles are usually quite different The helix angle on the worm is generally quite large, and that on the gear very small Because of this, it is usual to specify the lead angle on the worm, which is the complement of the worm helix angle, and the helix angle on the gear; the two angles are equal for a 90-deg. Shaft angleWhen gears are to be used to transmit motion between intersecting shaft, some of bevel gear is required. Although bevel gear are usually made for a shaft angle of 90 deg. They may be produced for almost any shaft angle. The teeth may be cast, milled, or generated. Only the generated teeth may be classed as accurate. In a typical bevel gear mounting, one of the gear is often mounted outboard of the bearing. This means that shaft deflection can be more pronounced and have a greater effect on the contact of teeth. Another difficulty, which occurs in predicting the stress in bevel-gear teeth, is the fact the teeth are tapered.Straight bevel gears are easy to design and simple to manufacture and give very good results in service if they are mounted accurately and positively. As in the case of squr gears, however, they become noisy at higher values of the pitch-line velocity In these cases it is often go od design practice to go to the spiral bevel gear, which is the bevel counterpart of the helical gear. As in the case of helical gears, spiral bevel gears give a much smoother tooth action than straight bevel gears, and hence are useful where high speed are encountered. It is frequently desirable, as in the case of automotive differential applications, to have gearing similar to bevel gears but with the shaft offset. Such gears are called hypoid gears because their pitch surfaces are hyperboloids of revolution The tooth action between such gears is a combination of rolling and sliding alonga straight line and has much in common with that of worm gears A shaft is a rotating or stationary member, usually of circular cross section, having mounted upon it such elementsas gears, pulleys, flywheels, cranks, sprockets, and other power-transmission elements. Shaft may be subjected to bending, tension, compression, or torsional loads, acting singly or in combination with one another. When they are combined, one may expect to find both static and fatigue strength tobe important design considerations, since a single shaft may be subjected to static stresses, completely reversed, and repeated stresses, all acting at the same time The word "shaft" covers numerous variations, such as axles and spindles. Anaxle is a shaft, wither stationary or rotating, nor subjected to torsion load. A shirt rotating shaft is often called a spindle. When either the lateral or the torsional deflection of a shaft must be held to close limits, the shaft must be sized on the basis of deflection before analyzing the stresses. The reason for this is that, if the shaft is made stiff enough so that the deflection is not too large, it is probable that the resulting stresses will be safe. But by no means should the designer assume that they are safe; it is almost always necessary to calculatethem so that he knows they are within acceptable limits Whenever possible, the power-transruission elements, such as gears or pullets, should be located close to the supporting bearings, This reduces the bending moment, and hence the deflection and bending stress.Although the von Mises-Hencky-Goodman method is difficult to use in design of shaft, it probably comes closest to predicting actual failure. Thus it is a good way of checking a shaft that has already been designed or of discovering why a particular shaft has failed in service. Furthermore, there are a considerable number of shaft-design problems in which the dimension are pretty well limited by other considerations, such as rigidity, and it is only necessary for the designer to discover something about the fillet sizes, heat-treatment, and surface finish and whether or not shot peening is necessary in order to achieve the required life and reliability Because of the similarity of their functions, clutches and brakes are treated together. In a simplified dynamic representation of a friction clutch, or brake two in ertias 11 and 12 traveling at the respective angular velocities Wl and W2, one of which may be zero in the case of brake, are to be brought to the same speed by engaging the clutch or brake. Slippage occurs because the two elements are running at different speeds and energy is dissipated during actuation, resulting in a temperature rise. In analyzing the performance of these devices we shall beinterested in the actuating force, the torque transmitted, the energy loss and the temperature rise. The torque transmitted is related to the actuating force, the coefficient of friction, and the geometry of the clutch or brake. This is problem in static, which will have to be studied separately for eath geometric configuration. However, temperature rise is related to energy loss and can be studied without regard to the type of brake or clutch because the geometry of interest is the heat-dissipating surfaces. The various types of clutches and brakes may be classified as fllows1. Rim type with internally expanding shoes2. Rim type with externally contracting shoes3。
机械制造 毕业设计 外文英文文献 翻译 齿轮和齿轮传动
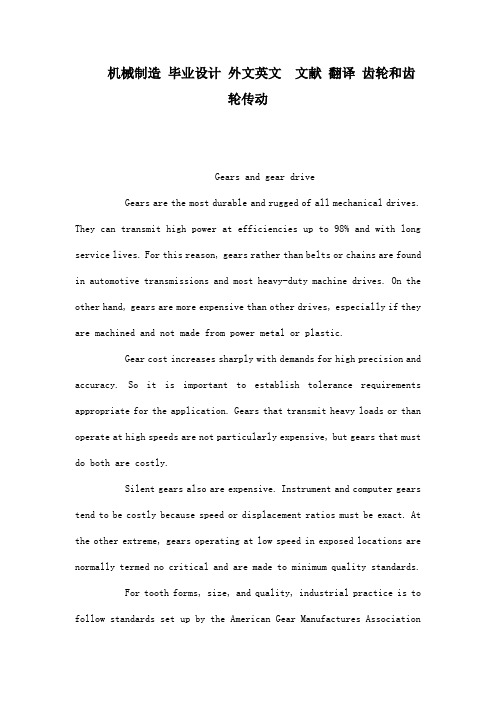
机械制造毕业设计外文英文文献翻译齿轮和齿轮传动Gears and gear driveGears are the most durable and rugged of all mechanical drives. They can transmit high power at efficiencies up to 98% and with long service lives. For this reason, gears rather than belts or chains are found in automotive transmissions and most heavy-duty machine drives. On the other hand, gears are more expensive than other drives, especially if they are machined and not made from power metal or plastic.Gear cost increases sharply with demands for high precision and accuracy. So it is important to establish tolerance requirements appropriate for the application. Gears that transmit heavy loads or than operate at high speeds are not particularly expensive, but gears that must do both are costly.Silent gears also are expensive. Instrument and computer gears tend to be costly because speed or displacement ratios must be exact. At the other extreme, gears operating at low speed in exposed locations are normally termed no critical and are made to minimum quality standards.For tooth forms, size, and quality, industrial practice is to follow standards set up by the American Gear Manufactures AssociationAGMA.Tooth formStandards published by AGMA establish gear proportions and tooth profiles. Tooth geometry is determined primarily by pitch, depth, and pressure angle.Pitch:Standards pitches are usually whole numbers when measured as diametral pitch P. Coarse-pitch gearing has teeth larger than 20 diametral pitch ?usually 0.5 to 19.99. Fine-pitch gearing usually has teeth of diametral pitch 20 to 200.Depth: Standardized in terms of pitch. Standard full-depth have working depth of 2/p. If the teeth have equal addendaas in standard interchangeable gears the addendum is 1/p. Stub teeth have a working depth usually 20% less than full-depth teeth. Full-depth teeth have a larger contract ratio than stub teeth. Gears with small numbers of teeth may have undercut so than they do not interfere with one another during engagement. Undercutting reduce active profile and weakens the tooth.Mating gears with long and short addendum have larger load-carrying capacity than standard gears. The addendum of the smaller gear pinion is increased while that of larger gear is decreased, leaving the whole depth the same. This form is know as recess-action gearing.Pressure Angle: Standard angles are and . Earlier standards include a 14-pressure angle that is still used. Pressure angle affectsthe force that tends to separate mating gears. High pressure angle decreases the contact ratio ratio of the number of teeth in contact but provides a tooth of higher capacity and allows gears to have fewer teeth without undercutting.Backlash: Shortest distances between the non-contacting surfaces of adjacent teeth .Gears are commonly specified according to AGMA Class Number, which is a code denoting important quality characteristics. Quality number denote tooth-element tolerances. The higher the number, the closer the tolerance. Number 8 to 16 apply to fine-pitch gearing.Gears are heat-treated by case-hardening, through-hardening, nitriding, or precipitation hardening. In general, harder gears are stronger and last longer than soft ones. Thus, hardening is a device that cuts the weight and size of gears. Some processes, such as flame-hardening, improve service life but do not necessarily improve strength.Design checklistThe larger in a pair is called the gear, the smaller is called the pinion.Gear Ratio: The number of teeth in the gear divide by the number of teeth in the pinion. Also, ratio of the speed of the pinion to the speed of the gear. In reduction gears, the ratio of input to output speeds.Gear Efficiency: Ratio of output power to input power. includesconsideration of power losses in the gears, in bearings, and from windage and churning of lubricant.Speed: In a given gear normally limited to some specific pitchline velocity. Speed capabilities can be increased by improving accuracy of the gear teeth and by improving balance of the rotating parts.Power: Load and speed capacity is determined by gear dimensions and by type of gear. Helical and helical-type gears have the greatest capacity to approximately 30,000 hp. Spiral bevel gear are normally limited to 5,000 hp, and worm gears are usually limited to about 750 hp.Special requirementsMatched-Set Gearing: In applications requiring extremely high accuracy, it may be necessary to match pinion and gear profiles and leads so that mismatch does not exceed the tolerance on profile or lead for the intended application.Tooth Spacing: Some gears require high accuracy in the circular of teeth. Thus, specification of pitch may be required in addition to an accuracy class specification.Backlash: The AMGA standards recommend backlash ranges to provide proper running clearances for mating gears. An overly tight mesh may produce overload. However, zero backlash is required in some applications.Quiet Gears: To make gears as quit as possible, specify thefinest pitch allowable for load conditions. In some instances, however, pitch is coarsened to change mesh frequency to produce a more pleasant, lower-pitch sound. Use a low pressure angle. Use a modified profile to include root and tip relief. Allow enough backlash. Use high quality numbers. Specify a surface finish of 20 in. or better. Balance the gear set. Use a nonintegral ratio so that the same teeth do not repeatedly engage if both gear and pinion are hardened steel. If the gear is made of a soft material, an integral ratio allows the gear to cold-work and conform to the pinion, thereby promoting quiet operation. Make sure critical are at least 20% apart from operating speeding or speed multiples and from frequency of tooth mesh.Multiple mesh gearMultiple mesh refers to move than one pair of gear operating in a train. Can be on parallel or nonparallel axes and on intersection or nonintersecting shafts. They permit higer speed ratios than are feasible with a single pair of gears .Series trains:Overall ratio is input shaft speed divided by output speed ,also the product of individual ratios at each mesh ,except in planetary gears .Ratio is most easily found by dividing the product of numbers of teeth of driven gears by the product of numbers of teeth of driving gears.Speed increasers with step-up rather than step-down ratios mayrequire special care in manufacturing and design. They often involve high speeds and may creste problems in gear dynamics. Also, frictional and drag forces are magnified which, in extreme cases , may lead to operational problems.Epicyclic Gearing:Normally, a gear axis remains fixed and only the gears rotates. But in an epicyclic gear train, various gears axes rotate about one anther to provide specialized output motions. With suitable clutchse and brakes, an epicyclic train serves as the planetary gear commonly found in automatic transmissions.Epicyclic trains may use spur or helical gears, external or internal, or bevel gears. In transmissions, the epicyclic or planetary gears usually have multiple planets to increase load capacity.In most cases, improved kinematic accuracy in a gearset decreases gear mesh excitation and results in lower drive noise. Gearset accuracy can be increased by modifying the tooth involute profile, by substituting higher quality gearing with tighter manufacturing tolerances, and by improving tooth surface finish. However, if gear mesh excitation generaters resonance somewhere in the drive system, nothing short of a “perfect” gearset will substantially reduce vibration and noise.Tooth profiles are modified to avoid interferences which can result from deflections in the gears, shafts, and housing as teeth engageand disendgage. If these tooth interferences are not compensated for by profile modifications, gears load capacity can be seriously reduced. In addition, the drive will be noisier because tooth interferences generate high dynamic loads. Interferences typically are eliminated by reliving the tooth tip, the tooth flank, or both. Such profile modifications are especially important for high-load , high-speed drives. The graph of sound pressure levelvs tip relief illustrates how tooth profile modifications can affect overall drive noise. If the tip relief is less than this optimum value, drive noise increases because of greater tooth interference; a greater amount of tip relief also increase noise because the contact ratio is decreased.Tighter manufacturing tolerances also produce quietier gears. Tolerances for such parameters as profile error, pitch AGMA quality level. For instance, the graph depicting SPL vs both speed and gear quality shows how noise decreases example, noise is reduced significantly by an increase in accuracy from an AGMA Qn 11 quality to an AGNA Qn 15 quality. However, for most commercial drive applications, it is doubtful that the resulting substantial cost increase for such an accuracy improvement can be justified simply on the basis of reduced drive noise.Previously, it was mentioned that gears must have adequate clearance when loaded to prevent tooth interference during the course of meshing. Tip and flank relief are common profile modifications thatcontrol such interference. Gears also require adequate backlash and root clearance. Noise considerations make backlash an important parameter to evaluate during drive design. Sufficient backlash must be provided under all load and temperature conditions to avoid a tight mesh, which creates excessively high noise level. A tight mesh due to insufficient backlash occurs when the drive and coast side of a tooth are in contact simultaneously. On the other hand, gears with excessive backlash also are noisy because of impacting teeth during periods of no load or reversing load. Adequate backlash should be provided by tooth thinning rather than by increase in center distance. Tooth thinning dose not decrease the contact ratio, whereas an increase in center distance does. However, tooth thinning does reduce the bending fatigue, a reduction which is small for most gearing systems.齿轮和齿轮传动在所有的机械传动形式中,齿轮传动是一种最结实耐用的传动方式。
机械类毕业设计外文翻译范文

机械类毕业设计外文翻译、毕业设计(论文)外译文题目:轴承的摩擦与润滑10 月 15 日外文文献原文:Friction , Lubrication of BearingIn many of the problem thus far , the student has been asked to disregard or neglect friction . Actually , friction is present to some degree whenever two parts are in contact and move on each other. The term friction refers to the resistance of two or more parts to movement.Friction is harmful or valuable depending upon where it occurs. friction is necessary for fastening devices such as screws and rivets which depend upon friction to hold the fastener andthe parts together. Belt drivers, brakes, and tires are additional applications where friction is necessary.The friction of moving parts in a machine is harmful because it reduces the mechanical advantage of the device. The heat produced by friction is lost energy because no work takes place. Also , greater power is required to overcome the increased friction. Heat is destructive in that it causes expansion. Expansion may cause a bearing or sliding surface to fit tighter. If a great enough pressure builds up because made from low temperature materials may melt.There are three types of friction which must be overcome in moving parts: (1)starting, (2)sliding, and(3)rolling. Starting friction is the friction between two solids that tend to resist movement. When two parts are at a state of rest, the surface irregularities of both parts tend to interlock and form a wedging action. T o produce motion in these parts, the wedge-shaped peaks and valleys of the stationary surfaces must be made to slide out and over each other. The rougher the two surfaces, the greater is starting friction resulting from their movement .Since there is usually no fixed pattern between the peaks and valleys of two mating parts, the irregularities do not interlock once the parts are in motion but slide over each other. The friction of the two surfaces is known as sliding friction. As shown in figure ,starting friction is always greater than sliding friction .Rolling friction occurs when roller devces are subjected to tremendous stress which cause the parts to change shape or deform. Under these conditions, the material in front of a roller tends to pile up and forces the object to roll slightly uphill. This changing of shape , known as deformation, causes a movement of molecules. As a result ,heat is produced from the addedenergy required to keep the parts turning and overcome friction.The friction caused by the wedging action of surface irregularities can be overcome partly by the precision machining of the surfaces. However, even these smooth surfaces may require the use of a substance between them to reduce the friction still more. This substance is usually a lubricant which provides a fine, thin oil film. The film keeps the surfaces apart and prevents the cohesive forces of the surfaces from coming in close contact and producing heat .Another way to reduce friction is to use different materials for the bearing surfaces and rotating parts. This explains why bronze bearings, soft alloys, and copper and tin iolite bearings are used with both soft and hardened steel shaft. The iolite bearing is porous. Thus, when the bearing is dipped in oil, capillary action carries the oil through the spaces of the bearing. This type of bearing carries its own lubricant to the points where the pressures are the greatest.Moving parts are lubricated to reduce friction, wear, and heat. The most commonly used lubricants are oils, greases, and graphite compounds. Each lubricant serves a different purpose. The conditions under which two moving surfaces are to work determine the type of lubricant to be used and the system selected for distributing the lubricant.On slow moving parts with a minimum of pressure, an oil groove is usually sufficient to distribute the required quantity of lubricant to the surfaces moving on each other .A second common method of lubrication is the splash system in which parts moving in a reservoir of lubricant pick up sufficient oil which is then distributed to all moving parts during each cycle. This system is used in the crankcase of lawn-mower engines to lubricate the crankshaft, connecting rod ,and parts of the piston.A lubrication system commonly used in industrial plants is the pressure system. In this system, a pump on a machine carries the lubricant to all of the bearing surfaces at a constant rate and quantity.There are numerous other systems of lubrication and a considerable number of lubricants available for any given set of operating conditions. Modern industry pays greater attention to the use of the proper lubricants than at previous time because of the increased speeds, pressures, and operating demands placed on equipment and devices.Although one of the main purposes of lubrication is reduce friction, any substance-liquid , solid , or gaseous-capable of controlling friction and wear between sliding surfaces can be classed as a lubricant.V arieties of lubricationUnlubricated sliding. Metals that have been carefully treated to remove all foreign materials seize and weld to one another when slid together. In the absence of such a high degree of cleanliness, adsorbed gases, water vapor ,oxides, and contaminants reduce frictio9n and the tendency to seize but usually result in severe wear; this is called “unlubricated ”or dry sliding.Fluid-film lubrication. Interposing a fluid film that completely separates the sliding surfaces results in fluid-film lubrication. The fluid may be introduced intentionally as the oil in the main bearing of an automobile, or unintentionally, as in the case of water between a smooth tuber tire and a wet pavement. Although the fluid is usually a liquid such as oil, water, and a wide。
机械类英语论文翻译.doc

机械类英语论文翻译.doc轴承内径 bearing bore diameter轴承寿命 bearing life轴承套圈 bearing ring轴承外径 bearing outside diameter轴颈 journal轴瓦、轴承衬 bearing bush轴端挡圈 shaft end ring轴环 shaft collar轴肩 shaft shoulder轴角 shaft angle轴向 axial direction轴向齿廓 axial tooth profile轴向当量动载荷 dynamic equivalent axial load轴向当量静载荷 static equivalent axial load轴向基本额定动载荷 basic dynamic axial load rating轴向基本额定静载荷 basic static axial load rating 轴向接触轴承 axial contact bearing轴向平面 axial plane轴向游隙 axial internal clearance轴向载荷 axial load轴向载荷系数 axial load factor轴向分力 axial thrust load主动件 driving link主动齿轮 driving gear主动带轮 driving pulley转动导杆机构 whitworth mechanism转动副 revolute (turning) pair转速 swiveling speed rotating speed转动关节 revolute joint转轴 revolving shaft转子 rotor转子平衡 balance of rotor装配条件 assembly condition锥齿轮 bevel gear锥顶 common apex of cone锥距 cone distance锥轮 bevel pulley; bevel wheel锥齿轮的当量直齿轮 equivalent spur gear of the bevel gear 锥面包络圆柱蜗杆 milled helicoids worm准双曲面齿轮 hypoid gear子程序 subroutine子机构 sub-mechanism自动化 automation自锁 self-locking自锁条件 condition of self-locking自由度 degree of freedom, mobility。
轴类毕业设计英文翻译、外文文献翻译
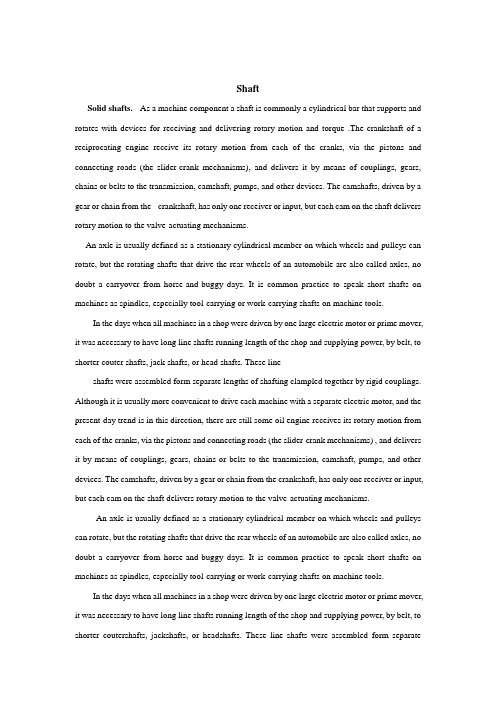
ShaftSolid shafts. As a machine component a shaft is commonly a cylindrical bar that supports and rotates with devices for receiving and delivering rotary motion and torque .The crankshaft of a reciprocating engine receive its rotary motion from each of the cranks, via the pistons and connecting roads (the slider-crank mechanisms), and delivers it by means of couplings, gears, chains or belts to the transmission, camshaft, pumps, and other devices. The camshafts, driven by a gear or chain from the crankshaft, has only one receiver or input, but each cam on the shaft delivers rotary motion to the valve-actuating mechanisms.An axle is usually defined as a stationary cylindrical member on which wheels and pulleys can rotate, but the rotating shafts that drive the rear wheels of an automobile are also called axles, no doubt a carryover from horse-and-buggy days. It is common practice to speak short shafts on machines as spindles, especially tool-carrying or work-carrying shafts on machine tools.In the days when all machines in a shop were driven by one large electric motor or prime mover, it was necessary to have long line shafts running length of the shop and supplying power, by belt, to shorter couter shafts, jack shafts, or head shafts. These lineshafts were assembled form separate lengths of shafting clampled together by rigid couplings. Although it is usually more convenient to drive each machine with a separate electric motor, and the present-day trend is in this direction, there are still some oil engine receives its rotary motion from each of the cranks, via the pistons and connecting roads (the slider-crank mechanisms) , and delivers it by means of couplings, gears, chains or belts to the transmission, camshaft, pumps, and other devices. The camshafts, driven by a gear or chain from the crankshaft, has only one receiver or input, but each cam on the shaft delivers rotary motion to the valve-actuating mechanisms.An axle is usually defined as a stationary cylindrical member on which wheels and pulleys can rotate, but the rotating shafts that drive the rear wheels of an automobile are also called axles, no doubt a carryover from horse-and-buggy days. It is common practice to speak short shafts on machines as spindles, especially tool-carrying or work-carrying shafts on machine tools.In the days when all machines in a shop were driven by one large electric motor or prime mover, it was necessary to have long line shafts running length of the shop and supplying power, by belt, to shorter coutershafts, jackshafts, or headshafts. These line shafts were assembled form separatelengths of shafting clampled together by rigid couplings. Although it is usually more convenient to drive each machine with a separate electric motor, and the present-day trend is in this direction, there are still some situation in which a group drive is more economical.A single-throw crankshaft that could be used in a single-cylinder reciprocating engine or pump is shown in Figure 21. The journals A andB rotate in the main bearings,C is the crankpin that fits in a bearing on the end of the connecting rod and moves on a circle of radius R about the main bearings, whileD andE are the cheeks or webs.The throw R is one half the stroks of the piston, which is connected, by the wrist pin, to the other end of the connecting rod and guided so as to move on a straight path passing throw the axis XX. On a multiple-cylinder engine the crankshaft has multiple throws---eight for a straight eight and for a V-8---arranged in a suitable angular relationship.Stress and strains. In operation, shafts are subjected to a shearing stress, whose magnitude depends on the torque and the dimensions of the cross section. This stress is a measure of resistance that the shaft material offers to the applied torque. All shafts that transmit a torque are subjected to torsional shearing stresses.In addition to the shearing stresses, twisted shafts are also subjected to shearing distortions. The distorted state is usually defined by the angle of twist per unit length; i.e., the retation of one cross section of a shaft relative to another cross section at a unit distance from it.Shafts that carry gears and pulleys are bent as well as twisted, and the magniude of the bending stresses, which are tensile on the convex side of the bend and compressive on the concave side, will depend on the load, the distance between the bearings of the shaft cross section.The combination of bending and twisting produces a state of stress in the shaft that is more complex than the state of pure shears produced by torsion alone or the state of tension-compression produced by bending alone.To the designer of shaft it is important to know if the shaft is likely to fail because of an excessive normal stress. If a piece of chalk is twisted, it will invariably rupture on a plane at about 45 degrees to the axis. This is because the maximum tensile stresses act on this plane, and chalk is weak in tension. Steel shafting is usually designed so that the maximum shearing stress produced by bending and torsion is less than a specified maximum.Shafts with circular cross sections are easier to produce in the steel mill, easier to machine, andeasier to support in bearings than shafts with other cross section; there is seldom any need for using noncircular shapes. In addition, the strength and stiffness, both in bending and torsion, are more easily calculated for circular shafts. Lastly, for a given amount of materials the circular shafts has the smallest maximum shearing stress for a given torque, and the highest torsional rigidity.The shearing in a circular shaft is highest at the surface and drops off to zero at the axis. This means that most of the torque is carried by the material on and near the surface.Critical speeds. In the same way that a violin string vibrates when stroked with a bow, a cylindrical shaft suspended between two bearings has a natural frequency of lateral vibration. If the speed of revolution of the shaft coincides with the natural frequency, the shaft experience a whirling critical speed and become noisy. These speeds are more likely to occur with long, flexible shafts than with short, stiff ones. The natural frequency of a shaft can be raised by increasing its stiffness.If a slender rod is fixed to the ceiling ta one end and supports a heavy disk at the other end, the disk will oscillate back and forth around the rod axis like a torsion pendulum if given an initial twist and let go. The frequency of the oscillations will depend on the torsional stiffness of the rod and the weight of the disk; the stiffer the rod and the lighter the disk the higher the frequency. Similar torsional oscillations can occur in the crankshafts of reciprocating engines, particularly those with many crank throws and a heavy flywheel. Each crank throw and part of the associated connecting rod acts like a small flywheel, and for the crankshaft as a whole, there are a number of ways or modes in which there small flywheels can oscillate back and forth around the shaft axis in opposition to one another and to the main flywheel. For each of these modes there corresponds a natural frequency of oscillation.When the engine is operating the torques delivered to the crankshaft by the connecting rods fluctuate, and if the crankshaft speed is such that these fluctuating impulses are delivered at a speed corresponding to one of the natural torsional frequencies of the shaft, torsional oscillations will be superimposed on the rotary motion of the shafts. Such speed are known as torsional critical speeds, and they can cause shaft failures. A number of devices to control the oscillations of crankshafts have been invented.Flexible shafts. A flexible shaft consists of a number of superimposed tightly wound right-and left-hand layers of helically wound wires wrapped about a single center wire or mandrel. The shaft is connected to source of power and the driven member by special fittings attached to the end of theshaft. Flexible easings of metallic or nonmetallic materials, which guide and protect the shaft and retain the lubricant, are also available. Compared with solid shafts, flexible shafts can be bent to much smaller radii without being overstressed.For transmitting power around corners and for considerable distances flexible shafts are usually cheaper and more convenient than belts, chains, or gears. Most speedometers on automobiles are driven by flexible shafts running from the transmission to the dashboard. When a valve, a switch, or other control devices is in a hard-to-reach location, it can be operated by a flexible shaft from a more convenient position. For portable tools such as sanders, grinders, and drilling machines, flexible shafts are practically indispensable.KEY, SPLINES AND PINSKeys, splines, and pins. When power is being transmitted from a machine member such as a coupling, a gear, a flywheel, or a pulley to the shaft on which it is mounted, means must be provided for preventing relative motion between the shaft and the member. On helical and bevel gears, relative movement along the shaft caused by the thrust(axial) loads is prevented by a step in the shaft or by having the gear contact the bearing directly or through a tubular spacer. When axial loads are incidental and of small magnitude, the members are kept from sliding along the shaft by means of a set screw. The primary purpose of keys, splines, and pins is to prevent relative rotary movement.A commonly used type of key has a square cross section and is sunk half in the shaft and half in the hub of the other member. If the key is made of steel(which is commonly the case)of the same strength as the shaft and has a width and depth equal to one fourth of the shaft diameter(this proportion is closely approximated in practice) then it will have the same torque capacity as the solid shaft if its length is 1.57 times that of the shaft diameter. Another common type of key has a rectangular cross section with a depth to width ratio of 0.75. Both of these keys may either be straight or tapered in depth. The straight keys fit snugly on the sides of the key ways only, the tapered keys on all sides. Gib-head keys are tapered keys with a projection on one end to facilitate removal.Woodruff keys are widely used on machine tools and motor vehicles. The key is a segment of adisk and fits in a keyway in the shaft that is with a special milling cutter. Though the extra depth of these keys weakens the shaft considerably, it prevents any tendency of the key to rotate or move axially. Woodruff keys are particularly suitable for tapering shaft ends.Because they weaken the shafts less, keys with straight or tapered circular cross sections are sometimes used in place of square and rectangular keys, but the keyways, half in the shaft and half in the shaft and half in the hub, must be cut with a drill after assembly,and interchangeability of parts is practically impossible. When a large gear blank is made by shrinking a high-strength rim on a cheaper cast center, circular keys, snugly fitted, are frequently used to ensure a permanent connection.Splines are permanent keys integral with the shaft, fitting in keyways cut in the hub. The dimensions of splined fittings are standardized for both permanent (press) fits and sliding fits. The teeth have either straight or involute profiles;the latter are stronger, more easily measured, and have a self-centring action when twisted.Tapered circular pins can be used to restrain shaft-mounted members from both axial and rotary movement. The pin fits snugly in a reamed tapered hole that is perpendicular to the shaft surface. A number of straight pins that grip by deforming elastically or plastically when driven into straight holes are commercially available.All the keys and pins that have been described are standard driving devices. In some cases they inadequate, and unorthodox means must be employed. For driving small gear in which there is no room between the bore and the roots of the teeth for a longitudinal keyway, a transverse radial slot on the end of the gear can be made to fit a radial protuberance on the shaft. For transmitting moderate loads, a cheaper and effective connection can be made by forming a series of longitudinal serrations on the shaft with a knurling tool and pressing the shaft into the hole in the driven member, it will cut grooves in the hole and provide, in effect, a press-fitted splined connection. Press and shrink fits are also used, and they can provide surprisingly firm connections, but the dimensions of the connected member must be closely controlled.轴实心轴轴作为机械零件通常是一根圆柱形杆,用来支撑部件并随部件一起转动以接受和传递转动和扭矩。
机械零件齿轮中英文对照外文翻译文献

(文档含英文原文和中文翻译)中英文资料对照外文翻译Machine Parts (I)GearsGears are direct contact bodies, operating in pairs, that transmit motion and force from one rotating shaft to another or from a shaft to a slide (rack), by means of successively engaging projections called teeth.Tooth profiles. The contacting surfaces of gear teeth must be aligned in such a way that the drive is positive; i.e., the load transmitted must not depend on frictional contact. As shown in the treatment of direct contact bodies, this requires that thecommon normal to the surfaces not to pass through the pivotal axis of either the driver or the follower.As it is known as direct contact bodies, cycloidal and involute profiles profiles provide both a positive drive and a uniform velocity ratio;i.e., conjugate action.Basic relations. The smaller of a gear pair is called the pinion and the larger is the gear. When the pinion is on the driving shaft the pair is called the pinion and the larger is the gear. When the pinion is on the driving shaft the pair acts as a speed reducer; When the gear drives, the pair is a speed incrreaser. Gears are more frequently used to reduce speed than to increase it.If a gear having N teeth rotates at n revolutions per minute, the product N*n has the dimension “teeth per minute”. This product must be the same for both members of a mating pair if each tooth acquires a partner from the mating gear as it passes through the region of tooth engagement.For conjugate gears of all types, the gear ratio and the speed ratio are both given by the ratio of the number of teeth on the gear to the number of teeth on the pinion. If a gear has 100 teeth and a mating pinion has 20, the ratio is 100/20=5. Thus the pinion rotates five times as fast as the gear, regardless of the gear. Their point of tangency is called the pitch point, and since it lies on the line of centers, it is the only point at which the profiles have pure roling contact. Gears on nonparallel, non-intersecting shafts also have pitch circles, but the rolling-pitch –circle concept is not valid.Gear types are determined largely by the disposition of the shafts; in addition, certain types are better suited than others for large speed changes. This means that if a specific disposition of the shafts is required, the type of gear will more or less be fixed. On the other hand, if a required speed change demands a certain type, the shaft positions will also be fixed.Spur gears and helical gears. A gear having tooth elements that are straight and parallel to its axis is known as a spur gear. A spur pair can be used to connect parallel shafts only.If an involute spur pinion were made of rubber and twisted uniformly so that the ends rotated about the axis relative to one another, the elements of the teeth, initially straight and parallel to the axis, would become helices. The pinion then in effect would become a helical gear.Worm and bevel gears. In order to achieve line contact and improve the load carrying capacity of the crossed axis helical gears, the gear can be made to curvepartially around the pinion, in somewhat the same way that a nut envelops a screw. The result would be a cylindrical worm and gear. Worms are also made in the shape of an hourglass, instead of cylindrical, so that they partially envelop the gear. This results in a further increase in load-carrying capacity.Worm gears provide the simplest means of obtaining large ratios in a single pair. They are usually less efficient than parallel-shaft gears, however, because of an additional sliding movement along the teeth.V-beltThe rayon and rubber V-belt are widely used for power transmission. Such belts are made in two series: the standard V-belt and the high capacity V-belt. The belts can be used with short center distances and are made endless so that difficulty with splicing devices is avoided.First, cost is low, and power output may be increased by operating several belts side by side. All belts in the drive should stretch at the same rate in order to keep the load equally divided among them. When one of the belts breaks, the group must usually be replaced. The drive may be inclined at any angle with tight side either top or bottom. Since belts can operate on relatively small pulleys, large reductions of speed in a single drive are possible.Second,the included angle for the belt groove is usually from 34°to 38°.The wedging action of the belt in the groove gives a large increase in the tractive force developed by the belt.Third,pulley may be made of cast iron, sheet steel, or die-cast metal. Sufficient clearance must be provided at the bottom of the groove to prevent the belt from bottoming as it becomes narrower from wear. Sometimes the larger pulley is not grooved when it is possible to develop the required tractive force by running on the inner surface of the belt. The cost of cutting the grooves is thereby eliminated. Pulleys are on the market that permit an adjustment in the width of the groove. The effective pitch diameter of the pulley is thus varied, and moderate changes in the speed ratio can be secured.Chain DrivesThe first chain-driven or “safety” bicycle appeared in 1874, and chains were used for driving the rear wheels on early automobiles. Today, as the result of modern design and production methods, chain drives that are much superior to their prototypes are available, and these have contributed greatly to thedevelopment of efficient agricultural machinery, well-drilling equipment, and mining and construction machinery. Since about 1930 chain drives have become increasingly popular, especially for power saws, motorcycle, and escalators etc.There are at least six types of power-transmission chains; three of these will be covered in this article, namely the roller chain, the inverted tooth, or silent chain, and the bead chain. The essential elements in a roller-chain drive are a chain with side plates, pins, bushings (sleeves), and rollers, and two or more sprocket wheels with teeth that look like gear teeth. Roller chains are assembled from pin links and roller links. A pin link consists of two side plates connected by two pins inserted into holes in the side plates. The pins fit tightly into the holes, forming what is known as a press fit. A roller link consists of two side plates connected by two press-fitted bushings, on which two hardened steel rollers are free to rotate. When assembled, the pins are a free fit in the bushings and rotate slightly, relative to the bushings when the chain goes on and leaves a sprocket.Standard roller chains are available in single strands or in multiple strands, In the latter type, two or more chains are joined by common pins that keep the rollers in the separate strands in proper alignment. The speed ratio for a single drive should be limited to about 10∶1; the preferred shaft center distance is from 30 to 35 times the distance between the rollers and chain speeds greater than about 2500 feet (800 meters) per minute are not recommended. Where several parallel shafts are to be driven without slip from a single shaft, roller chains are particularly well suited.An inverted tooth, or silent chain is essentially an assemblage of gear racks, each with two teeth, pivotally connected to form a closed chain with the teeth on the inside, and meshing with conjugate teeth on the sprocket wheels. The links are pin-connected flat steel plates usually having straight-sided teeth with an included angle of 60 degrees. As many links are necessary to transmit the power and are connected side by side. Compared with roller-chain drives, silent-chain drives are quieter, operate successfully at higher speeds, and can transmit more load for the same width. Some automobiles have silent-chain camshaft drives.Bead chains provide an inexpensive and versatile means for connecting parallel or nonparallel shafts when the speed and power transmitted are low. The sprocket wheels contain hemispherical or conical recesses into which the beads fit. The chains look like key chains and are available in plain carbon and stainless steel and also in the form of solid plastic beads molded on a cord. Bead chains are used oncomputers, air conditioners, television tuners, and Venetian blinds. The sprockets may be steel, die-cast zinc or aluminum, or molded nylon.Machine Parts (II)FastenerFasteners are devices which permit one part to be joined to a second part and, hence, they are involved in almost all designs.There are three main classifications of fasteners, which are described as follows:(1) Removable. This type permits the parts to be readily disconnected without damaging the fastener. An example is the ordinary nut-and-bolt fastener.(2) Semi permanent. For this type, the parts can be disconnected, but some damage usually occurs to the fastener. One such example is a cotter pin.(3) Permanent. When this type of fastener is used, it is intended that the parts will never be disassembled. Examples are riveted joints and welded joints.The importance of fasteners can be realized when referring to any complex product. In the case of the automobile, there are literally thousands of parts which are fastened together to produce the total product. The failure or loosening of a single fastener could result in a simple nuisance such as a door rattle or in a serious situation such as a wheel coming off. Such possibilities must be taken into account in the selection of the type of fastener for the specific application.Nuts, bolts, and screws are undoubtedly the most common means of joining materials. Since they are so widely used, it is essential that these fasteners attain maximum effectiveness at the lowest possible cost. Bolts are, in reality, carefully engineered products with a practically infinite use over a wide range of services.An ordinary nut loosens when the forces of vibration overcome those of friction. In a nut and lock washer combination, the lock washer supplies an independent locking feature preventing the nut from loosening. The lock washer is useful only when the bolt might loosen because of a relative change between the length of the bolt and the parts assembled by it. This change in the length of the bolt can be caused by a number of factors-creep in the bolt, loss of resilience, difference in thermal expansion between the bolt and the bolted members, or wear. In the above static cases, the expanding lock washer holds the nut under axial load and keeps the assembly tight. When relative changes are caused by vibration forces, the lock washer is not nearly as effective.Rivets are permanent fasteners. They depend on deformation of their structure for their holding action. Rivets are usually stronger than the thread-type fastener and are more economical on a first-cost basis. Rivets are driven either hot or cold,depending upon the mechanical properties of the rivet material. Aluminum rivets, for instance, are cold-driven, since cold working improves the strength of aluminum. Most large rivets are hot-driven, however.ShaftVirtually all machines contain shafts. The most common shape for shafts is circular and the cross section can be either solid or hollow (hollow shafts can result in weight savings).Shafts are mounted in bearings and transmit power through such devices as gears, pulleys, cams and clutches. These devices introduce forces which attempt to bend the shaft; hence, the shaft must be rigid enough to prevent overloading of the supporting bearings. In general, the bending deflection of a shaft should not exceed 0.01 in. per ft. of length between bearing supports.For diameters less than 3 in., the usual shaft material is cold-rolled steel containing about 0.4 percent carbon. Shafts are either cold-rolled or forged in sizes from 3 in. to 5 in. .For sizes above 5 in. , shafts are forged and machined to size. Plastic shafts are widely used for light load applications. One advantage of using plastic is safety in electrical applications, since plastic is a poor conductor of electricity.Another important aspect of shaft design is the method of directly connecting one shaft to another. This is accomplished by devices such as rigid and flexible couplings.BearingA bearing can be defined as a member specifically designed to support moving machine components. The most common bearing application is the support of a rotating shaft that is transmitting power from one location to another. Since there is always relative motion between a bearing and its mating surface, friction is involved. In many instances, such as the design of pulleys, brakes, and clutches, friction is desirable. However, in the case of bearings, the reduction of friction is one of the prime considerations:Friction results in loss of power, the generation of heat, and increased wear of mating surfaces.The concern of a machine designer with ball bearings and roller bearings is fivefold as follows:(1) Life in relation to load; (2) stiffness, i.e. deflections under load;(3) friction; (4) wear; (5) noise. For moderate loads and speeds the correct selection ofa standard bearing on the basis of load rating will usually secure satisfactoryperformance. The deflection of the bearing elements will become important where loads are high, although this is usually of less magnitude than that of the shafts or other components associated with the bearing. Where speeds are high special cooling arrangements become necessary which may increase frictional drag. Wear is primarily associated with the introduction of contaminants, and sealing arrangements must be chosen with regard to the hostility of the environment.Notwithstanding the fact that responsibility for the basic design of ball bearings and roller bearings rests with the bearing manufacturer, the machine designer must form a correct appreciation of the duty to be performed by the bearing and be concerned not only with bearing selection but with the conditions for correct installation.The fit of the bearing races onto the shaft or onto the housings is of critical importance because of their combined effect on the internal clearance of the bearing as well as preserving the desired degree of interference fit. Inadequate interference can induce serious trouble from fretting corrosion. The inner race is frequently located axially by abutting against a shoulder. A radius at this point is essential for the avoidance of stress concentration and ball races are provided with a radius or chamfer to allow space for this.A journal bearing, in its simplest form, is a cylindrical bushing made of a suitable material and containing properly machined inside and outside diameters. The journal is usually the part of a shaft or pin that rotates inside the bearing.Journal bearings operate with sliding contact, to reduce the problems associated with sliding friction in journal bearings, a lubricant is used in conjunction with compatible mating materials. When selecting the lubricant and mating materials, one must take into account bearing pressures, temperatures and also rubbing velocities. The principle function of the lubricant in sliding contact bearings is to prevent physical contact between the rubbing surfaces. Thus the maintenance of an oil film under varying loads, speeds and temperature is the prime consideration in sliding contact bearings.Introduction to Machinery DesignMachinery design is either to formulate an engineering plan for the satisfaction of a specified need or to solve an engineering problem. It involves a range of disciplines in materials, mechanics, heat, flow, control, electronics and production.Machinery design may be simple or enormously complex, easy or difficult, mathematical or nonmathematical, it may involve a trivial problem or one of great importance. Good design is the orderly and interesting arrangement of an idea to provide certain results or effects. A well-designed product is functional, efficient, and dependable. Such a product is less expensive than a similar poorly designed product that does not function properly and must constantly be repaired.People who perform the various functions of machinery design are typically called industrial designers. He or she must first carefully define the problem, using an engineering approach, to ensure that any proposed solution will solve the right problem. It is important that the designer begins by identifying exactly how he or she will recognize a satisfactory alternative, and how to distinguish between two satisfactory alternatives in order to identify the better. So industrial designers must have creative imagination, knowledge of engineering, production techniques, tools, machines, and materials to design a new product for manufacture, or to improve an existing product.In the modern industrialized world, the wealth and living standards of a nation are closely linked with their capabilities to design and manufacture engineering products. It can be claimed that the advancement of machinery design and manufacturing can remarkably promote the overall level of a country’s industrization. Our country is playing a more and more vital role in the global manufacturing industry. To accelerate such an industrializing process, highly skilled design engineers having extensive knowledge and expertises are needed.Machinery ComponentsThe major part of a machine is the mechanical system. And the mechanical system is decomposed into mechanisms, which can be further decomposed into mechanical components. In this sense, the mechanical components are the fundamental elements of machinery. On the whole, mechanical components can be classified as universal and special components. Bolts, gear, and chains are the typical examples of the universal components, which can be used extensively in different machines across various industrial sectors. Turbine blades, crankshaft and aircraftpropeller are the examples of the special components, which are designed for some specific purposes.Mechanical Design ProcessProduct design requires much research and development. Many concepts of an idea must be studied, tried, refined, and then either used or discarded. Although the content of each engineering problem is unique, the designers follow the similar process to solve the problems.Recognition of NeedSometimes, design begins when a designer recognizes a need and decides to do something about it. The need is often not evident at, all; recognition is usually triggered by a particular adverse circumstance or a set of random circumstances, which arise almost simultaneously. Identification of need usually consists of an undefined and vague problem statement.Definition of ProblemDefinition of problem is necessary to fully define and understand the problem, after which it is possible to restate the goal in a more reasonable and realistic way than the original problem statement. Definition of the problem must include all the specifications for the thing that is to be designed. Obvious items in the specifications are the speeds, feeds, temperature limitations, maximum range, expected variation in the variables, and dimensional and weight limitations.SynthesisThe synthesis is one in which as many alternative possible design approaches are sought, usually without regard for their value or quality. This is also sometimes called the ideation and invention step in which the largest possible number of creative solutions is generated. The synthesis activity includes the specification of material, addition of geometric features, and inclusion of greater dimensional detail to the aggregate design.AnalysisAnalysis is a method of determining or describing the nature of something by separating it into its parts. In the process the elements, or nature of the design, are analyzed to determine the fit between the proposed design and the original design goals.EvaluationEvaluation is the final proof of a successful design and usually involves thetesting of a prototype in the laboratory. Here we wish to discover if the design really satisfies the needs.The above description may give an erroneous impression that this process can be accomplished in a linear fashion as listed. On the contrary, iteration is required within the entire process, moving from any step back to any previous step, in all possible combinations, and doing this repeatedly.PresentationCommunicating the design to others is the finial, vital presentation step in the design process. Basically, there are only three means of communication. These are the written, the oral, and the graphical forms. A successful engineer will be technically competent and versatile in all three forms of communication. The competent engineer should not be afraid of the possibility of not succeeding in a presentation. In fact, the greatest gains are obtained by those willing to risk defeat.Contents of Machinery DesignMachinery design is an important technological basic course in mechanical engineering education. Its objective is to provide the concepts, procedures, data, and decision analysis techniques necessary to design machine elements commonly found in mechanical devices and systems; to develop engineering students’ competence of machine design that is the primary concern of machinery manufacturing and the key to manufacture good products.Machinery design covers the following contents:Provides an introduction to the design process, problem formulation, safety factors.Reviews the material properties and static and dynamic loading analysis, including beam, vibration and impact loading.Reviews the fundamentals of stress and defection analysis.Introduces static failure theories and fracture-mechanics analysis for static loads.Introduces fatigue-failure theory with the emphasis on stress-life approaches to high-cycle fatigue design, which is commonly used in the design of rotation machinery.Discusses thoroughly the phenomena of wear mechanisms, surface contact stresses, and surface fatigue.Investigates shaft design using the fatigue-analysis techniques.Discusses fluid-film and rolling-element bearing theory and application.Gives a thorough introduction to the kinematics, design and stress analysis of spur gears, and a simple introduction to helical, bevel, and worm gearing.Discusses spring design including helical compression, extension and torsion springs.Deals with screws and fasteners including power screw and preload fasteners.Introduces the design and specification of disk and drum clutches and brakes.机械零件(I)齿轮齿轮是直接接触,成对工作的实体,在称为齿的凸出物的连续啮合作用下,齿轮能将运动和力从一个旋转轴传递到另一个旋转轴,或从一个轴传递到一个滑块(齿条)。
齿轮机械机构类外文翻译、中英文翻译
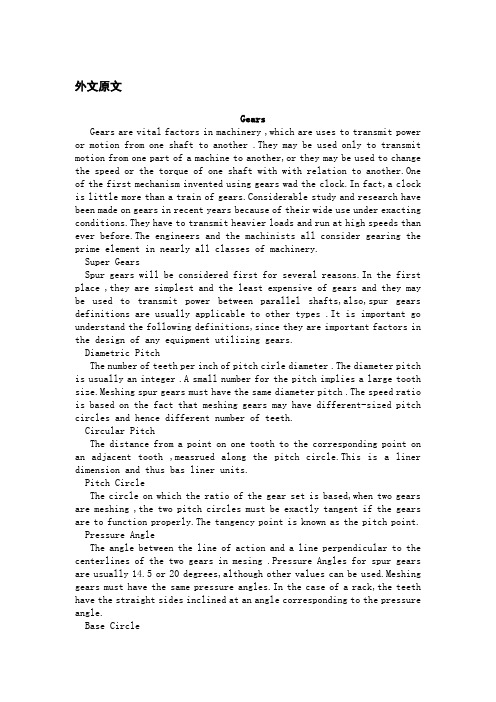
外文原文GearsGears are vital factors in machinery ,which are uses to transmit power or motion from one shaft to another .They may be used only to transmit motion from one part of a machine to another,or they may be used to change the speed or the torque of one shaft with with relation to another.One of the first mechanism invented using gears wad the clock.In fact,a clock is little more than a train of gears.Considerable study and research have been made on gears in recent years because of their wide use under exacting conditions.They have to transmit heavier loads and run at high speeds than ever before.The engineers and the machinists all consider gearing the prime element in nearly all classes of machinery.Super GearsSpur gears will be considered first for several reasons.In the first place ,they are simplest and the least expensive of gears and they may be used to transmit power between parallel shafts,also,spur gears definitions are usually applicable to other types .It is important go understand the following definitions,since they are important factors in the design of any equipment utilizing gears.Diametric PitchThe number of teeth per inch of pitch cirle diameter .The diameter pitch is usually an integer .A small number for the pitch implies a large tooth size.Meshing spur gears must have the same diameter pitch .The speed ratio is based on the fact that meshing gears may have different-sized pitch circles and hence different number of teeth.Circular PitchThe distance from a point on one tooth to the corresponding point on an adjacent tooth ,measrued along the pitch circle.This is a liner dimension and thus bas liner units.Pitch CircleThe circle on which the ratio of the gear set is based,when two gears are meshing ,the two pitch circles must be exactly tangent if the gears are to function properly.The tangency point is known as the pitch point. Pressure AngleThe angle between the line of action and a line perpendicular to the centerlines of the two gears in mesing .Pressure Angles for spur gears are usually 14.5 or 20 degrees,although other values can be used.Meshing gears must have the same pressure angles.In the case of a rack,the teeth have the straight sides inclined at an angle corresponding to the pressure angle.Base CircleA circle tangent to the line of action (or pressure line ) .The base circle is the imaginary circle about which an involutes cure is developed .Most spur gears follow an involutes cure from the base circle to the top of the tootch,this cure can be visualized by observing a point on a taut cord an it is unwound from a cylinder .In a gear ,the cylinder is the best circle.AddendumThe radial distance form the pitch circle to the top of the tooth . DedendumThe radial distance from file pitch circle to the root of the tooth. ClearanceThe difference between the addendum and the addendum.Face WidthThe width of the tooth measured axially.FaceThe surface between the pitch circle and the top of the tooth. FlankThe surface between the pitch circle and the bottom of the tooth. Helical GearsThese gears have their tooth element at an angle or helix to the axis of the gear.They are more difficult and expensive to make than spur gears,but are quieter and stronger. They may be used to transmit power between parallel shafts at an angle to each in the same or different planes.Herringbone GearsA herringbone gear is equivalent to a right-hand and a left-hand helical gear placed side by side.Because of the angle of the tooth,helical gears create considerable side thrust on the shaft. A herringbone gear corrects this thrust by neutralizing it ,allowing the use of a small thrust bearing instead of a large one and perhaps eliminating one altogether.Often a central groove is made round the gear for ease in machining.Bevel GearsBevel gears are used to connect shafts, which are not parallel to each ually the shafts are 90 deg.To each other, but they may be more or less than 90 deg.The two meshing gears may have the same number of teeth for the purpose of changing direction of motion only,or they may have a different number of teeth for the purpose of changing both speed and direction .The faces of the teeth lie on the surface of the frustum of a cone,therefore the teeth elements are not parallel to each other it can be seen that this lack of parallelism creates a machining problem so that two passes with a tool must be made.The tooth elements may be straight or spiral ,so that we have plain anti spiral evel gears.Worm and Worm GearsA worm-and-worm-gear combination is used chiefly where it is desired to obtain a high gear reduction in a limited space,normally the worm drivers the worm gear and is not reversible ,that is to say,the worm gear can not drive the worm.Most worms can be rotated in either direction,clockwise or counterclockwise.RacksA rack is a gear with an infinite radius,or a gear with its perimeter stretched out into a straight line.It is used to change reciprocating motion to rotary motion or vice versa.A lathe rack and pinion is a good example of this mechanism.Various materials are used in manufacturing gears .Usually,the materials selected depends on the method used for making the gear and the application to which it will be put.Gears can be cast,cut,or extruded.Typical materials include cast iron,cast steel,plain carbon steel,alloy steel aluminum,phosphor bronze,laminated phonetics,and nylon.中文翻译齿轮齿轮是机器中的动力元件,用来传递轴与轴之间的运动及动力。
最新齿轮和轴的介绍毕业设计外文翻译
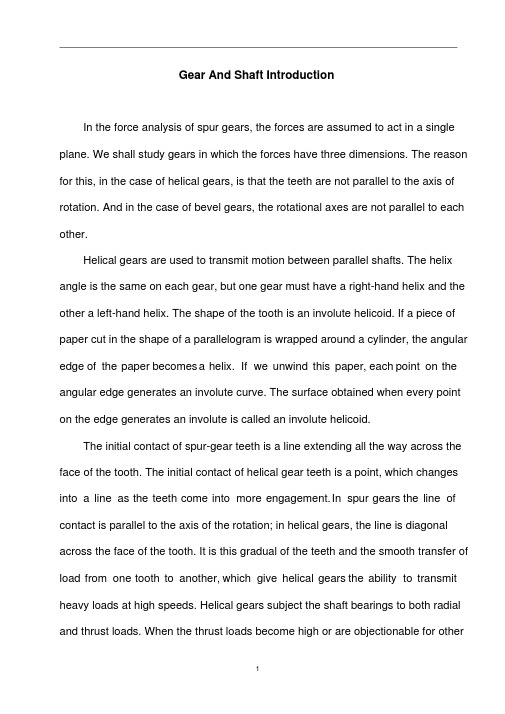
Gear And Shaft IntroductionIn the force analysis of spur gears, the forces are assumed to act in a single plane. We shall study gears in which the forces have three dimensions. The reason for this, in the case of helical gears, is that the teeth are not parallel to the axis of rotation. And in the case of bevel gears, the rotational axes are not parallel to each other.Helical gears are used to transmit motion between parallel shafts. The helix angle is the same on each gear, but one gear must have a right-hand helix and the other a left-hand helix. The shape of the tooth is an involute helicoid. If a piece of paper cut in the shape of a parallelogram is wrapped around a cylinder, the angular edge of the paper becomes a helix. If we unwind this paper, each point on the angular edge generates an involute curve. The surface obtained when every point on the edge generates an involute is called an involute helicoid.The initial contact of spur-gear teeth is a line extending all the way across the face of the tooth. The initial contact of helical gear teeth is a point, which changes into a line as the teeth come into more engagement. In spur gears the line of contact is parallel to the axis of the rotation; in helical gears, the line is diagonal across the face of the tooth. It is this gradual of the teeth and the smooth transfer of load from one tooth to another, which give helical gears the ability to transmit heavy loads at high speeds. Helical gears subject the shaft bearings to both radial and thrust loads. When the thrust loads become high or are objectionable for otherreasons, it may be desirable to use double helical gears. A double helical gear (herringbone) is equivalent to two helical gears of opposite hand, mounted side by side on the same shaft. They develop opposite thrust reactions and thus cancel out the thrust load. When two or more single helical gears are mounted on the same shaft, the hand of the gears should be selected so as to produce the minimum thrust load.Crossed-helical, or spiral, gears are those in which the shaft centerlines are neither parallel nor intersecting. The teeth of crossed-helical fears have point contact with each other, which changes to line contact as the gears wear in. For this reason they will carry out very small loads and are mainly for instrumental applications, and are definitely not recommended f or use in the transmission of power. There is on difference between a crossed helical gear and a helical gear until they are mounted in mesh with each other. They are manufactured in the same way. A pair of meshed crossed helical gears usually have the same hand; that is ,a right-hand driver goes with a right-hand driven. In the design of crossed-helical gears, the minimum sliding velocity is obtained when the helix angle are equal. However, when the helix angle are not equal, the gear with the larger helix angle should be used as the driver if both gears have the same hand.Worm gears are similar to crossed helical gears. The pinion or worm has a small number of teeth, usually one to four, and since they completely wrap around the pitch cylinder they are called threads. Its mating gear is called a worm gear, which is not a true helical gear. A worm and worm gear are used to provide a highangular-velocity reduction between nonintersecting shafts which are usually at right angle. The worm gear is not a helical gear because its face is made concave to fit the curvature of the worm in order to provide line contact instead of point contact. However, a disadvantage o f worm gearing is the high sliding velocities across the teeth, the same as with crossed helical gears.Worm gearing are either single or double enveloping. A single-enveloping gearing is one in which the gear wraps around or partially encloses the worm.. A gearing in which each element partially encloses the other is, of course, a double-enveloping worm gearing. The important difference between the two is that area contact exists between the teeth of double-enveloping gears while only line contact between those of single-enveloping gears. The worm and worm gear of a set have the same hand of helix as for crossed helical gears, but the helix angles are usually quite different. The helix angle on the worm is generally quite large, andthat on the gear very small. Because of this, it is usual to specify the lead angle on the worm, which is the complement of the worm helix angle, and the helix angleon the gear; the two angles are equal for a 90-deg. Shaft angle.When gears are to be used to transmit motion between intersecting shaft, some of bevel gear is required. Although bevel gear are usually made for a shaft angle of 90 deg. They may be produced for almost any shaft angle. The teeth may be cast, milled, or generated. Only the generated teeth may be classed as accurate. In a typical bevel gear mounting, one of the gear is often mounted outboard of theWhen either the lateral or the torsional deflection of a shaft must be held to close limits, the shaft must be sized on the basis of deflection before analyzing the stresses. T he reason for this is that, if the shaft is made stiff enough so that the deflection is not too large, it is probable that the resulting stresses will be safe. But by no means should the designer assume t hat they are safe; it is almost always necessary t o calculate them so that he knows they are within acceptable limits. Whenever possible, the power-transmission elements, such as gears or pullets, should be located close to the supporting bebearing. This means that shaft deflection can be more pronounced and have a greater effect on the contact of teeth.A shaft is a rotating or stationary member, usually of circular cross section, having mounted upon it such elementsas gears, pulleys, flywheels, cranks, sprockets, and other power-transmission elements. Shaft may be subjected to bending, tension, compression, or torsional loads, acting singly or in combination with one another. When they are combined, one may expect to find both static and fatigue strength to be important design considerations, since a single shaft may be subjected to static stresses, completely reversed, and repeated stresses, all acting at the same time.covers numerous variations, such as axles and spindles.The word “shaft” Anaxle is a shaft, wither stationary or rotating, nor subjected to torsion load. A shirt rotating shaft is often called a spindle.arings, This reduces the bending moment, and hence the deflection and bending stress.Because of the similarity of their functions, clutches and brakes are treated together. In a simplified dynamic representation of a friction clutch, or brake, two inertias I1 and I2 traveling at the respective angular velocities W1 and W2, one of which may be zero in the case of brake, are to be brought to the same speed by engaging the clutch or brake. Slippage occurs because the two elements are running at different speeds and energy is dissipated during actuation, resulting in a temperature rise. In analyzing the performance of these devices we shall be interested in the actuating force, the torque transmitted, the energy loss and the temperature rise. The torque transmitted is related to the actuating force, the coefficient of friction, and the geometry of the clutch or brake. This is problem in static, which will have to be studied separately for eath geometric configuration. However, temperature rise is related to energy loss and can be studied without regard to the type of brake or clutch because the geometry of interest is the heat-dissipating surfaces. The various types of clutches and brakes may be classified as fllows:1. Rim type with internally expanding shoes2. Rim type with externally contracting shoes3. Band type4. Disk or axial type5. Cone type6. Miscellaneous typeThe analysis of all type of friction clutches and brakes use the same general procedure. The following step are necessary:1. Assume or determine the distribution of pressure on the frictional surfaces.2. Find a relation between the maximum pressure and the pressure at any point3. Apply the condition of statical equilibrium to find (a) the actuating force, (b) the torque, and (c) the support reactions.Miscellaneous clutches include several types, such as the positive-contact clutches, overload-release clutches, overrunning clutches, magnetic fluid clutches, and others.Introduciton of MachiningHave a shape as a processing method, all machining process for the production of the most commonly used and most important method. Machining process is a process generated shape, in this process, Drivers device on the workpiece material to be in the form of chip removal. Although in some occasions, the workpiece under no circumstances, the use of mobile equipment to the processing, However, the majority of the machining is not only supporting the workpiece also supporting tools and equipment to complete.Machining know the process has two aspects. Small group of low-cost production. For casting, forging and machining pressure, every production of a specific shape of the workpiece, even a spare parts, almost have to spend the high cost of processing. Welding to rely on the shape of the structure, to a large extent,depend on effective in the form of raw materials. In general, through the use of expensive equipment and without special processing conditions, can be almost any type of raw materials, mechanical processing to convert the raw materials processed into the arbitrary shape of the structure, as long as the external dimensions large enough, it is possible. Because of a production of spare parts, even when the parts and structure of the production batch sizes are suitable for the original casting, Forging or pressure processing to produce, but usually prefer machining.Strict precision and good surface finish, Machining the second purpose is the establishment of the high precision and surface finish possible on the basis of. Many parts, if any other means of production belonging to the large-scale production, Well Machining is a low-tolerance and can meet the requirements of small batch production. Besides, many parts on the production and processing of coarse process to improve its general shape of the surface. It is only necessary precision and choose only the surface machining. For instance, thread, in addition to mechanical processing, almost no other processing method for processing. Another example is the blacksmith pieces keyhole processing, as well as training to be conducted immediately after the mechanical completion of the processing. Primary Cutting ParametersCutting the work piece and tool based on the basic relationship between the following four elements to fully describe : the tool geometry, cutting speed, feed rate, depth and penetration of a cutting tool.Cutting Tools must be of a suitable material to manufacture, it must be strong, tough, hard and wear-resistant. Tool geometry -- to the tip plane and cutter angle characteristics -- for each cutting process must be correct.Cutting speed is the cutting edge of work piece surface rate, it is inches per minute to show. In order to effectively processing, and cutting speed must adapt to the level of specific parts -- with knives. Generally, the more hard work piece material, the lower the rate.Progressive Tool to speed iscut into the work piece speed. If the work piece or tool for rotating movement, feed rate per round over the number of inches to the measurement. When the work piece or tool for reciprocating movement and feed rate on each trip through the measurement of inches. Generally, in other conditions, feed rate and cutting speed is inversely proportional to。
机械毕业设计英文外文翻译75齿轮
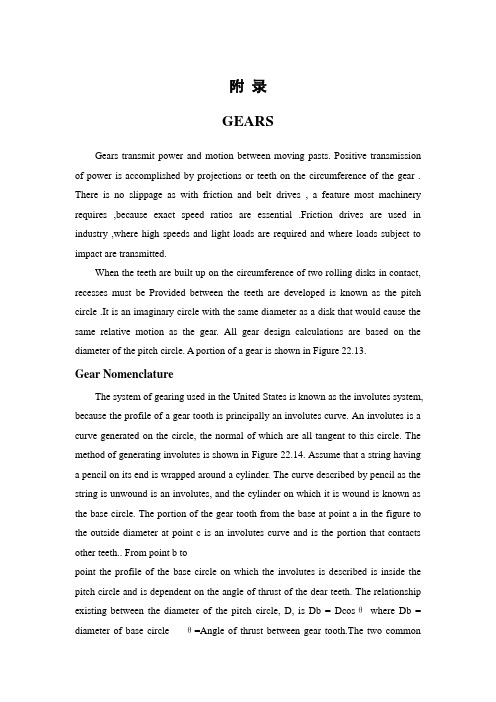
附录GEARSGears transmit power and motion between moving pasts. Positive transmission of power is accomplished by projections or teeth on the circumference of the gear . There is no slippage as with friction and belt drives , a feature most machinery requires ,because exact speed ratios are essential .Friction drives are used in industry ,where high speeds and light loads are required and where loads subject to impact are transmitted.When the teeth are built up on the circumference of two rolling disks in contact, recesses must be Provided between the teeth are developed is known as the pitch circle .It is an imaginary circle with the same diameter as a disk that would cause the same relative motion as the gear. All gear design calculations are based on the diameter of the pitch circle. A portion of a gear is shown in Figure 22.13.Gear NomenclatureThe system of gearing used in the United States is known as the involutes system, because the profile of a gear tooth is principally an involutes curve. An involutes is a curve generated on the circle, the normal of which are all tangent to this circle. The method of generating involutes is shown in Figure 22.14. Assume that a string having a pencil on its end is wrapped around a cylinder. The curve described by pencil as the string is unwound is an involutes, and the cylinder on which it is wound is known as the base circle. The portion of the gear tooth from the base at point a in the figure to the outside diameter at point c is an involutes curve and is the portion that contacts other teeth.. From point b topoint the profile of the base circle on which the involutes is described is inside the pitch circle and is dependent on the angle of thrust of the dear teeth. The relationship existing between the diameter of the pitch circle, D, is Db = Dcosθwhere Db = diameter of base circle θ=Angle of thrust between gear tooth.The two commonsystems have their thrust angles or lines of action at 141/2︒and 20︒.Figure 22.13 Nomencla ture for Involute spur gearOther angles are possible, but with larger angles the radial force component tending to force the gears apart becomes greater. If a common tangent is drawn to the pitch circles of two meshing gears. The base circle on which the involutes are drawn are tangent to the line of action.Most gears transmitting power use the 200, full-deep, involutes tooth form. These gears have the same tooth proportion as the 141/20 full–depth involutes but are stronger at their base because of greater thickness. The 200, fine –pitch involutes gears are-similar to the regular 200 involutes and are made in sizes ranging from 20 to 200 diametral pitch. These gears are used primarily for transmitting motion rather the power. The 200 stub tooth gear has smaller tooth depth than the 200. Full –depth gear and is consequently stronger. Involutes gears fulfill all laws of gearing and have the advantage over some other curves in that the contact action is affected by slight variation of gear center distance.Figure 22.14 Mothod of genera an Involute tooth surfaceThe nomenclature of a gear tooth is illustrated in Figure 22.13. the principal definitions and tooth parts for standard 141/20 and 200 involutes gears are discussed here.The addendum of a tooth is the radial distance from the pitch circle to the outside diameter of addendum circle. Numerically, it is equal to 1 divided by the diametral pitch P.The addendum is the radial distance from the pitch circle to the root or addendum circle. It is equal to the addendum plus the tooth clearance.Tooth thickness is the thickness of the tooth measure on the pitch circle. For cut gears the tooth thickness and tooth space are equal. Cast gears are provided with some backlash, the difference between the tooth thickness and tooth space measured on the pitch circle.The face of a gear tooth is that surface lying between the pitch circle and the addendum circle.The flank of a gear tooth is that surface lying between the pitch circle and the root circle.Clearance is a small distance provided so that the top of a meshing tooth will not touch the bottom land of the other gear as it passes the line of centers.Table 22.2gives the proportions of standard 141/200 involutes gears expressed in term of diametral pitch P and number of teeth N.Table 22.2 American Gear Manufactures Association Standard for Involute GearingPitch of GearsThe circuit pitch p is the distance from a point on one tooth to the corresponding point on an adjacent tooth, and is measured on the pitch circle. Expressed as an equation.Metrical gearing is based on the module(mod) instead of the diametral pitch p, as in the English system. The basic metric module formula is mod =D/N=amount of pitch diameter per tooth =millimeters per tooth measured on the pitch diameter. Also, mod=1/p is expressed in millimeters. Also, mod p=25.4.P = πD/N where D = diameter of the pitch circleN = number of teethThe diametral pitch p, often referred to as the pitch of a gear is the ratio of the number of teeth to the pitch diameter. It may be expressed by the following equation: P = N/DUpon multiplying these two equations the following relationship between circular and diametral pitch results.Hence,knowing the value of either pitch we may obtail the other by dividing into π.Gears and gear cutters are standardized according to diametral pitch. This pitch can be expressed in even figures or fractions. Circular pitch, being an actual distance,it is expressed in inches and fractions of an inch. A 6-inth gear (6diametral pitch) is one that has 6teeth per inch of pitch diameter . If the pitch diameter is 3 inch, the number of teeth is 3 x 6 or 18.The outside diameter of the gear is equal to the pitch diameter plus twice the addendum distance or 3 in.+2 x 1/6,which is 3.333in.Any involutes gear of a given diametral pitch will mesh properly with a gear of any other size of the same diametral pitch. However, in cutting gears of various diameters a slight difference in the cutter is necessary to allow for the change in curvature of the involutes as the diameter increases. The extreme case would be a rack tooth ,which would have a straight line as the theoretical tooth profile. For practical reasons the number of teeth in an involutes gear should not be less than 12.Gear speedThe speeds in rooms ,s and S, of two meshing gears vary inversely with both the pitch diameter and the number of teeth .This may be expressed as follows:Figure 22.15 Nomenclature for meshing gear and pinons/S = D/d =T/twhere Dand d represent pitch diameter as included as indicated in Figure 22.15.T and t represent number of teeth on the gear and pinion.Center distance : L = (D+d)/2The speed ratio for a worm gear set depends on the number of teeth on the gear and the lead of the worm. For a single=threaded worm the ratio isRpm worm/rpm gear = T/tKinds of gearsThe gears most commonly used are those that transmission power between two parallel shafts. Such gears having their tooth elements parallel to the ratating shaftsare known as spur gears, the smaller of the two being known as a pinion (Figure 22.15).If the elements of the teeth are twisted or helical,as known in figure 22.16B,they are known as helical gears. These gears amay be for connecting shafts that are at an angle in the same or different planes. Helical gears are smooth acting because there is always more than one tooth in contact. Some power is lost because of end thrust, and provision must be made to compensate for this thrust in the bearings. The herringbone gear is equivalent to two helical gears, one having right-hand and the other a left-hand helix.Figre 22.17 All elements of straight bevel converge at the one opex of the gears Usually, when two shafts are in the same plane but at an angle with one another, a bevel gear is used. Such a gear is similar in appearance to the frustum of a cone having all the elements of the teeth intersecting at a point, as shown in Figure 22.17. Bevel gears are made with either straight or spiral teeth. When the shafts are at right angles and the two bevel gears are the same size, they are known as miter gears (figure 22.16A). Hypoid gears, an interesting modification of bevel gears shown as Figure 22.16F, have their shaft at right angles by they do not intersect as do the shaft for bevel gears. Correct teeth for these gears are difficult to construct, although a generating process has been developed that produces satisfactory teeth. Zero gears (Figure 22.16D)have curved teeth but have a zero helical angle. They are produced on machines that cut spiral bevels and hypoids. Worm gearing is used where a large speed reduction is desired. The small driving gear is called a worm and the driving gear is called a worm and the driven gear a wheel. The worm resembles a large screw and is set in close to the wheel circumference, the teeth of the wheel being curving toconform to the diameter of the worm. The shafts for such gears are at right angles but not in the same plane. These gears are similar to helical gears in their application, but differ considerably in appearance and method of manufacture. A worm gear set is shown in Figure 22.16C.Rack gears, which are straight and have no curvature, represent a gear of infinite radius and are used in feeding mechanisms and for reciprocating. They may have either straight or helical teeth. If the rack is bent in the form of a circle, it becomes a bevel gear having a cone apex angle of 180ºknown as crown gear. the teeth all converge at the center of the disk and mesh properly with a bevel gear of the same pitch. A gear with internal teeth, known as an annular gear, can be cut to mesh with either a spur or bevel gear, depending on whether the shafts are parallel or intersecting.Methods of Making GearsMost gears are produced by some machining process. Accurate machine work is essential for high-speed, long-wearing, quite-operating gears. Die and investment casting of gears has proved satisfactory, but the materials are limited to low-temperature-melting metals and alloys. Consequently, these gears do not have the wearing qualities of heat-treated steel gears. Stamping though reasonably accurate, can be used only in making thin gears from sheet metal.Commercial methods employed in producing gears are summarized as follows: A: Casting 1.sand casting 2.Die casting 3.Precision and investment castingB: StampingC: Machining 1.Formed-tooth process a. From cutter in milling machine b. From cutter in broaching machine c. From cutter in shaper 2.Template process 3.Cutter generating process a. cutter gear b. Hobbing c. Rotary cutter d. Reciprocating cutters simulating a rackD: Power metallurgyE: ExtrudingF: RollingG: GrindingH: Plastic moldingForm Tooth ProcessA formed milling cutter, as shown in Figure22.18,is commonly used for cutting a spur gear. Such a cutter used on a milling machine is formed according to the shape of the tooth space to de removed. Theoretically, there should be a different-shape cutter for each size gear of a given pitch as there is a slight change in the curvature of the involutes. However, one cutter can be used for several gears having different numbers of teeth without much sacrifice in their operation. Each pitch cutter is made in eight slightly varying shapes to compensate for this change.They vary from no.1, which is used to cut gears from 135 teeth to a rack, to no.8, which cuts gears having 12 or 13 teeth. The eight standard involutes cutters are listed in Table 22.3.Setup of a milling machine to cut spur gears are illustrated in Figure 22.18. A discussion of this process is given the chapter on milling is an accurate process for cutting spur, helical, and worm gears. Although sometimes used for bevel gears, the process is not accurate because of the gradual change in tooth thickness. When used for bevel gears at least two cuts are necessary for each tooth space. The usual practice is to take one center cut of proper depth and about equal to the space at the small end of the tooth. Two shaving cuts are then on each side of the tooth space to give the tooth its proper shape.Figure 22.18 Setup for cutting a spir gear on a milling machineTable 22.3 Standard Involute cuttersNo.1135 teeth to a rackNo.255 to 134 teethNo.335 to 54 teethNo.426 to 34 teethNo.521 to 25 teethNo.617 to 20 teethNo.714 to 16 teethNo.812 to 13 teethThe formed-tooth principle may also be utilized in a broaching machine by making the broaching tool conform to the teeth space. Small internal gears can be completely cut in one pass by having a round broaching tool made with the same number of cutters as the gear has teeth. Broaching tool is limited to large-scale production because of the cost of cutters.齿轮运动部件之间的能量和运动由齿轮来传递。
机械类外文文献翻译(中英文翻译)
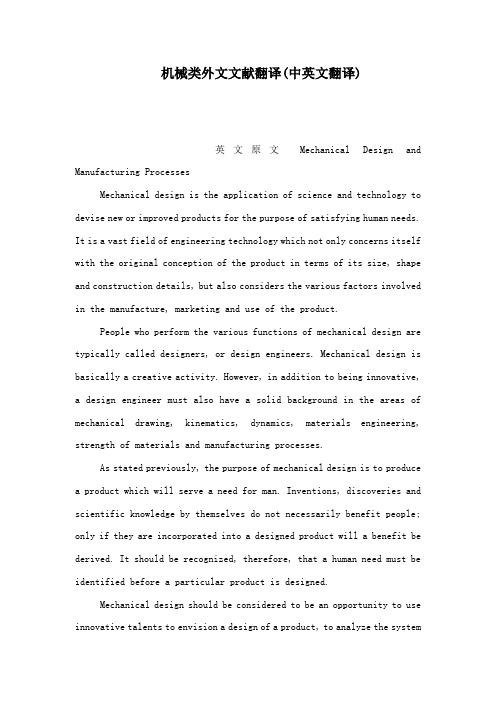
机械类外文文献翻译(中英文翻译)英文原文Mechanical Design and Manufacturing ProcessesMechanical design is the application of science and technology to devise new or improved products for the purpose of satisfying human needs. It is a vast field of engineering technology which not only concerns itself with the original conception of the product in terms of its size, shape and construction details, but also considers the various factors involved in the manufacture, marketing and use of the product.People who perform the various functions of mechanical design are typically called designers, or design engineers. Mechanical design is basically a creative activity. However, in addition to being innovative, a design engineer must also have a solid background in the areas of mechanical drawing, kinematics, dynamics, materials engineering, strength of materials and manufacturing processes.As stated previously, the purpose of mechanical design is to produce a product which will serve a need for man. Inventions, discoveries and scientific knowledge by themselves do not necessarily benefit people; only if they are incorporated into a designed product will a benefit be derived. It should be recognized, therefore, that a human need must be identified before a particular product is designed.Mechanical design should be considered to be an opportunity to use innovative talents to envision a design of a product, to analyze the systemand then make sound judgments on how the product is to be manufactured. It is important to understand the fundamentals of engineering rather than memorize mere facts and equations. There are no facts or equations which alone can be used to provide all the correct decisions required to produce a good design.On the other hand, any calculations made must be done with the utmost care and precision. For example, if a decimal point is misplaced, an otherwise acceptable design may not function.Good designs require trying new ideas and being willing to take a certain amount of risk, knowing that if the new idea does not work the existing method can be reinstated. Thus a designer must have patience, since there is no assurance of success for the time and effort expended. Creating a completely new design generally requires that many old and well-established methods be thrust aside. This is not easy since many people cling to familiar ideas, techniques and attitudes. A design engineer should constantly search for ways to improve an existing product and must decide what old, proven concepts should be used and what new, untried ideas should be incorporated.New designs generally have "bugs" or unforeseen problems which must be worked out before the superior characteristics of the new designs can be enjoyed. Thus there is a chance for a superior product, but only at higher risk. It should be emphasized that, if a design does not warrant radical new methods, such methods should not be applied merely for the sake of change.During the beginning stages of design, creativity should be allowedto flourish without a great number of constraints. Even though many impractical ideas may arise, it is usually easy to eliminate them in the early stages of design before firm details are required by manufacturing. In this way, innovative ideas are not inhibited. Quite often, more than one design is developed, up to the point where they can be compared against each other. It is entirely possible that the design which is ultimately accepted will use ideas existing in one of the rejected designs that did not show as much overall promise.Psychologists frequently talk about trying to fit people to the machines they operate. It is essentially the responsibility of the design engineer to strive to fit machines to people. This is not an easy task, since there is really no average person for which certain operating dimensions and procedures are optimum.Another important point which should be recognized is that a design engineer must be able to communicate ideas to other people if they are to be incorporated. Communicating the design to others is the final, vital step in the design process. Undoubtedly many great designs, inventions, and creative works have been lost to mankind simply because the originators were unable or unwilling to explain their accomplishments to others. Presentation is a selling job. The engineer, when presenting a new solution to administrative, management, or supervisory persons, is attempting to sell or to prove to them that this solution is a better one. Unless this can be done successfully, the time and effort spent on obtaining the solution have been largely wasted.Basically, there are only three means of communication available tous. These are the written, the oral, and the graphical forms. Therefore the successful engineer will be technically competent and versatile in all three forms of communication. A technically competent person who lacks ability in any one of these forms is severely handicapped. If ability in all three forms is lacking, no one will ever know how competent that person is!The competent engineer should not be afraid of the possibility of not succeeding in a presentation. In fact, occasional failure should be expected because failure or criticism seems to accompany every really creative idea. There is a great deal to be learned from a failure, and the greatest gains are obtained by those willing to risk defeat. In the final analysis, the real failure would lie in deciding not to make the presentation at all. To communicate effectively, the following questions must be answered:(1) Does the design really serve a human need?(2) Will it be competitive with existing products of rival companies?(3) Is it economical to produce?(4) Can it be readily maintained?(5) Will it sell and make a profit?Only time will provide the true answers to the preceding questions, but the product should be designed, manufactured and marketed only with initial affirmative answers. The design engineer also must communicate the finalized design to manufacturing through the use of detail and assembly drawings.Quite often, a problem will occur during the manufacturing cycle [3].It may be that a change is required in the dimensioning or tolerancing of a part so that it can be more readily produced. This fails in the category of engineering changes which must be approved by the design engineer so that the product function will not be adversely affected. In other cases, a deficiency in the design may appear during assembly or testing just prior to shipping. These realities simply bear out the fact that design is a living process. There is always a better way to do it and the designer should constantly strive towards finding that better way.Designing starts with a need, real or imagined. Existing apparatus may need improvements in durability, efficiently, weight, speed, or cost. New apparatus may be needed to perform a function previously done by men, such as computation, assembly, or servicing. With the objective wholly or partly defined, the next step in design is the conception of mechanisms and their arrangements that will perform the needed functions.For this, freehand sketching is of great value, not only as a record of one's thoughts and as an aid in discussion with others, but particularly for communication with one's own mind, as a stimulant for creative ideas.When the general shape and a few dimensions of the several components become apparent, analysis can begin in earnest. The analysis will have as its objective satisfactory or superior performance, plus safety and durability with minimum weight, and a competitive east. Optimum proportions and dimensions will be sought for each critically loaded section, together with a balance between the strength of the several components. Materials and their treatment will be chosen. These important objectives can be attained only by analysis based upon the principles ofmechanics, such as those of statics for reaction forces and for the optimumutilization of friction; of dynamics for inertia, acceleration, and energy; of elasticity and strength of materials for stress。
机械专业毕业设计外文翻译行星齿轮机构

毕业设计中英文翻译 学生姓名:学生姓名:学号:学号: 学 院:院:专 业:业:指导教师:指导教师:年月机械设计制造及其自动化Planetary GearsIntroductionThe Tamiya planetary gearbox is driven by a small DC motor that runs at about 10,500 rpm on 3.0V DC and draws about 1.0A. The maximum speed ratio is 1:400, giving an output speed of about 26 rpm. Four planetary stages are supplied with the gearbox, two 1:4 and two 1:5, and any combination can be selected. Not only is this a good drive for small mechanical applications, it provides an excellent review of epicycle gear trains. The gearbox is a very well-designed plastic kit that can be assembled in about an hourwith very few tools. The source for the kit is given in the References.Let's begin by reviewing the fundamentals of gearing, and the trick of analyzing epicyclic gear trains.Epicyclic Gear TrainsA pair of spur gears is represented in the diagram by their pitch circles, which are tangent at the pitch point P. The meshing gear teeth extend beyond the pitch circle by the addendum, and the spaces between them have a depth beneath the pitch circle by the dedendum. If the radii of the pitch circles are a and b, the distance between the gear shafts is a + b. In the action of the gears, the pitch circles roll on one another without slipping. To ensure this, the gear teeth must have a proper shape so that when the driving gear moves uniformly, so does the driven gear. This means that the line of pressure, normal to the tooth profiles in contact, passes through the pitch point. Then, the transmission of power will be free of vibration and high speeds are possible. We won't talk further about gear teeth here, having stated this fundamental principle of gearing.If a gear of pitch radius a has N teeth, then the distance between corresponding points on successive teeth will be 2πa/N, a quantity called the circular pitch. If two gears are to mate, the circular pitches must be the same. The pitch is usually stated as the ration 2a/N, called the diametral pitch. If you count the number of teeth on a gear, then the pitch diameter is the number of teeth times the diametral pitch. If you know the pitch diameters of two gears, then you can specify the distance between the shafts.The velocity ratio r of a pair of gears is the ratio of the angular velocity of the driven gear to the angular velocity of the driving gear. By the condition of rolling of pitch circles, r = -a/b = -N1/N2, since pitch radii are proportional to the number of teeth. The angular velocity n of the gears may be given in radians/sec, revolutions per minute (rpm), or any similar units. If we take one direction of rotation as positive, then the other direction is negative. This is the reason for the (-) sign in the above expression. If one of the gears is internal (having teeth on its inner rim), then the velocity ratio is positive, since the gears will rotate in the same direction.The usual involute gears have a tooth shape that is tolerant of variations in the distance between the axes, so the gears will run smoothly if this distance is not quite correct. The velocity ratio of the gears does not depend on the exact spacing of the axes, but is fixed by the number of teeth, or what is the same thing, by the pitch diameters. Slightly increasing the distance above its theoretical value makes the gears run easier, since the clearances are larger. On the other hand, backlash is also increased, which may not be desired in some applications.An epicyclic gear train has gear shafts mounted on a moving arm or carrier that can rotate about the axis, as well as the gears themselves. The arm can be an input element, or an output element, and can be held fixed or allowed to rotate. The outer gear is the ring gear or annulus. A simple but very commonepicyclic train is the sun-and-planet epicyclic train, shown in the figure at the left. Three planetary gears are used for mechanical reasons; they may be considered as one in describing the action of the gearing. The sun gear, the arm, or the ring gear may be input or output links.If the arm is fixed, so that it cannot rotate, we have a simple train of three gears. Then, n2/n1 = -N1/N2, n3/n2 = +N2/N3, and n3/n1 = -N1/N3. This is very simple, and should not be confusing. If the arm is allowed to move, figuring out the velocity ratios taxes the human intellect. Attempting this will show the truth of the statement; if you can manage it, you deserve praise and fame. It is by no means impossible, just invoved. However, there is a very easy way to get the desired result. First, just consider the gear train locked, so it moves as a rigid body, arm and all. All three gears and the arm then have a unity velocity ratio. The trick is that any motion of the gear train can carried out by first holding the arm fixed and rotating the gears relative to one another, and then locking the train and rotating it about the fixed axis. The net motionis the sum or difference of multiples of the two separate motions that satisfies the conditions of the problem (usually that one element is held fixed). To carry out this program, construct a table in which the angular velocities of the gears and arm are listed for each, for each of the two cases. The locked train gives 1, 1, 1, 1 for arm, gear 1, gear 2 and gear 3. Arm fixed gives 0, 1, -N1/N2, -N1/N3. Suppose we want the velocity ration between the arm and gear 1, when gear 3 is fixed. Multiply the first row by a constant so that when it is added to the second row, the velocity of gear 3 will be zero. This constant is N1/N3. Now, doing one displacement and then the other corresponds to adding the two rows. We find N1/N3, 1 + N1/N3, N1/N3 -N1/N2.The first number is the arm velocity, the second the velocity of gear 1, so the velocity ratio between them is N1/(N1 + N3), after multiplying through by N3. This is the velocity ratio we need for the Tamiya gearbox, where the ring gear does not rotate, the sun gear is the input, and the arm is the output. The procedure is general, however, and will work for any epicyclic train.One of the Tamiya planetary gear assemblies has N1 = N2 = 16, N3 = 48, while the other has N1 = 12, N2 = 18, N3 = 48. Because the planetary gears must fit between the sun and ring gears, the condition N3 = N1 + 2N2 must be satisfied. It is indeed satisfied for the numbers of teeth given. The velocity ratio of the first set will be 16/(48 + 16) = 1/4. The velocity ratio of the second set will be 12/(48 + 12) = 1/5. Both ratios are as advertised. Note that the sun gear and arm will rotate in the same direction.The best general method for solving epicyclic gear trains is the tabular method, since it does not contain hidden assumptions like formulas, nor require the work of the vector method. The first step is to isolate the epicyclic train, separating the gear trains for inputs and outputs from it. Find the input speeds or turns, using the input gear trains. There are, in general, two inputs, one of which may be zero in simple problems. Now prepare two rows of the table of turns or angular velocities. The first row corresponds to rotating around the epicyclic axis once, and consists of all 1's. Write down the second row assuming that the arm velocity is zero, using the known gear ratios. The row that you want is a linear combination of these two rows, with unknown multipliers x and y. Summing the entries for the input gears gives two simultaneous linear equations for x and y in terms of the known input velocities. Now the sum of the two rows multiplied by their respective multipliers gives the speeds of all the gears of interest. Finally, find the output speed with the aid of the output gear train. Be careful to get the directions of rotation correct, with respect to a direction taken as positive.The Tamiya Gearbox KitThe parts are best cut from the sprues with a flush-cutter of the type used in electronics. The very small bits of plastic remaining can then be removed with a sharp X-acto knife. Carefully remove all excess plastic, as the instructions say.Read the instructions carefully and make sure that things are the right way up and in the correct relative positons. The gearbox units go together easily with light pressure. Note that the brown ones must go together in the correct relative orientation. The 4mm washers are the ones of which two are supplied, and there is also a full-size drawing of one in the instructions. The smaller washers will not fit over the shaft, anyway. The output shaft is metal. Use larger long-nose pliers to press the E-ring into position in its groove in front of the washer. There is a picture showing how to do this. There was an extra E-ring in my kit. The three prongs fit into the carriers for the planetary gears, and are driven by them.Now stack up the gearbox units as desired. I used all four, being sure to put a 1:5 unit on the end next to the motor. Therefore, I needed the long screws. Press the orange sun gear for the last 1:5 unit firmly on the motor shaft as far as it will go. If it is not well-seated, the motor clip will not close. It might be a goodidea to put some lubricant on this gear from the tube included with the kit. If you use a different lubricant, test it first on a piece of plastic from the kit to make sure that it is compatible. A dry graphite lubricant would also work quite well. This should spread lubricant on all parts of the last unit, which is the one subject to the highest speeds. Put the motor in place, gently but firmly, wiggling it so that the sun gear meshes. If the sun gear is not meshed, the motor clip will not close. Now put the motor terminals in a vertical column, and press on the motor clamp.The reverse of the instructions show how to attach the drive arm and gives some hints on use of the gearbox. I got an extra spring pin, and two extra 3 mm washers. If you have some small washers, they can be used on the machine screws holding the gearbox together. Enough torque is produced at the output to damage things (up to 6 kg-cm), so make sure the output arm can rotate freely. I used a standard laboratory DC supply with variable voltage and current limiting, but dry cells could be used as well. The current drain of 1 A is high even for D cells, so a power supply is indicated for serious use. The instructions say not to exceed 4.5V, which is good advice. With 400:1 reduction, the motor should run freely whatever the output load.My gearbox ran well the first time it was tested. I timed the output revolutions with a stopwatch, and found 47s for 20 revolutions, or 25.5 rpm. This corresponds to 10,200 rpm at the motor, which is close to specifications. It would be easy to connect another gearbox in series with this one (parts are included to make this possible), and get about 4 revolutions per hour. Still another gearbox would produce about one revolution in four days. This is an excellent kit, and I recommend it highly.Other Epicyclic TrainsA very famous epicyclic chain is the Watt sun-and-planet gear, patented in 1781 as an alternative to the crank for converting the reciprocating motion of a steam engine into rotary motion. It was invented by William Murdoch. The crank, at that time, had been patented and Watt did not want to pay royalties. An incidental advantage was a 1:2 increase in the rotative speed of the output. However, it was more expensive than a crank, and was seldom used after the crank patent expired. Watch the animation on Wikipedia.The input is the arm, which carries the planet gear wheel mating with the sun gear wheel of equal size. The planet wheel is prevented from rotating by being fastened to the connecting rod. It oscillates a little, but always returns to the same place on every revolution. Using the tabular method explained above, the first line is 1, 1, 1 where the first number refers to the arm, the second to the planet gear, and the third to the sun gear. The second line is 0, -1, 1, where we have rotated the planet one turn anticlockwise. Adding, we get 1, 0, 2, which means that one revolution of the arm (one double stroke of the engine) gives two revolutions of the sun gear.We can use the sun-and-planet gear to illustrate another method for analyzing epicyclical trains in which we use velocities. This method may be more satisfying than the tabular method and show moreclearly how the train works. In the diagram at the right, A and O are the centres of the planet and sun gears, respectively. A rotates about O with angular velocity ω1, which we assume clockwise. At the position shown, this gives Aa velocity 2ω1 upward, as shown. Now the planet gear does not rotate, so all points in it move with the same velocity as A. This includes the pitch point P, which is also a point in the sun gear, which rotates about the fixed axis O with angular velocity ω2. Therefore, ω2 = 2ω1, the same result as with the tabular method.The diagram at the left shows how the velocity method is applied to the planetary gear set treated above. The sun and planet gears are assumed to be the same diameter (2 units). The ring gear is then of diameter 6. Let us assume the sun gear is fixed, so that the pitch point P is also fixed. The velocity of point A is twice the angular velocity of the arm. Since P is fixed, P' must move at twice the velocity of A, or fourtimes the velocity of the arm. However, the velocity of P' is three times the angular velocity of the ring gear as well, so that 3ωr = 4ωa. If the arm is the input, the velocity ratio is then 3:4, while if the ring is the input, the velocity ratio is 4:3.A three-speed bicycle hub may contain two of these epicyclical trains, with the ring gears connected (actually, common to the two trains). The input from the rear sprocket is to the arm of one train, while the output to the hub is from the arm of the second train. It is possible to lock one or both of the sun gears to the axle, or else to lock the sun gear to the arm and free of the axle, so that the train gives a 1:1 ratio. The three gears are: high, 3:4, output train locked; middle, 1:1, both trains locked, and low, 4:3 input train locked. Of course, this is just one possibility, and many different variable hubs have been manufactured. The planetary variable hub was introduced by Sturmey-Archer in 1903. The popular AW hub had the ratios mentioned here.Chain hoists may use epicyclical trains. The ring gear is stationary, part of the main housing. The input is to the sun gear, the output from the planet carrier. The sun and planet gears have very different diameters, to obtain a large reduction ratio.The Model T Ford (1908-1927) used a reverted epicyclic transmission in which brake bands applied to the shafts carrying sun gears selected the gear ratio. The low gear ratio was 11:4 forward, while the reverse gear ratio was -4:1. The high gear was 1:1. Reverted means that the gears on the planet carrier shaft drove other gears on shafts concentric with the main shaft, where the brake bands were applied. The floor controls were three pedals: low-neutral-high, reverse, transmission brake. The hand brake applied stopped theleft-hand pedal at neutral. The spark advance and throttle were on the steering column.The automotive differential, illustrated at the right, is a bevel-gear epicyclic train. The pinion drives the ring gear (crown wheel) which rotates freely, carrying the idler gears. Only one idler is necessary, but more than one gives better symmetry. The ring gear corresponds to the planet carrier, and the idler gears to the planet gears, of the usual epicyclic chain. The idler gears drive the side gears on the half-axles, which correspond to the sun and ring gears, and are the output gears. When the two half-axles revolve at the same speed, the idlers do not revolve. When the half-axles move at different speeds, the idlers revolve. The differential applies equal torque to the side gears (they are driven at equal distances by the idlers) while allowing them to rotate at different speeds. If one wheel slips, it rotates at double speed while the other wheel does not rotate. The same (small) torque is, nevertheless, applied to both wheels.The tabular method is easily used to analyze the angular velocities. Rotating the chain as a whole gives 1, 0, 1, 1 for ring, idler, left and right side gears. Holding the ring fixed gives 0, 1, 1, -1. If the right side gear is held fixed and the ring makes one rotation, we simply add to get 1, 1, 2, 0, which says that the left side gear makes two revolutions. The velocity method can also be used, of course. Considering the (equal) forces exerted on the side gears by the idler gears shows that the torques will be equal.ReferencesTamiya Planetary Gearbox Set, Item 72001-1400. Edmund Scientific, Catalog No. C029D, itemD30524-08 ($19.95).C. Carmichael, ed., Kent's Mechanical Engineer's Handbook, 12th ed. (New York: John Wiley and Sons, 1950). Design and Production V olume, p.14-49 to 14-43.V. L. Doughtie, Elements of Mechanism, 6th ed. (New York: John Wiley and Sons, 1947). pp. 299-311. Epicyclic gear. Wikipedia article on epicyclic trains.Sun and planet gear. Includes an animation.行星齿轮机构简介简介Tamiya 行星轮变速箱由一个约行星轮变速箱由一个约 10500 10500 r/min,3.0V r/min,3.0V,,1.0A 的直流电机运行。
- 1、下载文档前请自行甄别文档内容的完整性,平台不提供额外的编辑、内容补充、找答案等附加服务。
- 2、"仅部分预览"的文档,不可在线预览部分如存在完整性等问题,可反馈申请退款(可完整预览的文档不适用该条件!)。
- 3、如文档侵犯您的权益,请联系客服反馈,我们会尽快为您处理(人工客服工作时间:9:00-18:30)。
机械类外文翻译—轴和齿轮的设计及应用摘要在传统机械和现代机械中齿轮和轴的重要地位是不可动摇的。
齿轮和轴主要安装在主轴箱来传递力的方向。
通过加工制造它们可以分为许多的型号,分别用于许多的场合。
所以我们对齿轮和轴的了解和认识必须是多层次多方位的。
关键词:齿轮;轴在直齿圆柱齿轮的受力分析中,是假定各力作用在单一平面的。
我们将研究作用力具有三维坐标的齿轮。
因此,在斜齿轮的情况下,其齿向是不平行于回转轴线的。
而在锥齿轮的情况中各回转轴线互相不平行。
像我们要讨论的那样,尚有其他道理需要学习,掌握。
斜齿轮用于传递平行轴之间的运动。
倾斜角度每个齿轮都一样,但一个必须右旋斜齿,而另一个必须是左旋斜齿。
齿的形状是一溅开线螺旋面。
如果一张被剪成平行四边形(矩形)的纸张包围在齿轮圆柱体上,纸上印出齿的角刃边就变成斜线。
如果我展开这张纸,在血角刃边上的每一个点就发生一渐开线曲线。
直齿圆柱齿轮轮齿的初始接触处是跨过整个齿面而伸展开来的线。
斜齿轮轮齿的初始接触是一点,当齿进入更多的啮合时,它就变成线。
在直齿圆柱齿轮中,接触是平行于回转轴线的。
在斜齿轮中,该先是跨过齿面的对角线。
它是齿轮逐渐进行啮合并平稳的从一个齿到另一个齿传递运动,那样就使斜齿轮具有高速重载下平稳传递运动的能力。
斜齿轮使轴的轴承承受径向和轴向力。
当轴向推力变的大了或由于别的原因而产生某些影响时,那就可以使用人字齿轮。
双斜齿轮(人字齿轮)是与反向的并排地装在同一轴上的两个斜齿轮等效。
他们产生相反的轴向推力作用,这样就消除了轴向推力。
当两个或更多个单向齿斜齿轮被在同一轴上时,齿轮的齿向应作选择,以便产生最小的轴向推力。
交错轴斜齿轮或螺旋齿轮,他们是轴中心线既不相交也不平行。
交错轴斜齿轮的齿彼此之间发生点接触,它随着齿轮的磨合而变成线接触。
因此他们只能传递小的载荷和主要用于仪器设备中,而且肯定不能推荐在动力传动中使用。
交错轴斜齿轮与斜齿轮之间在被安装后互相捏合之前是没有任何区别的。
它们是以同样的方法进行制造。
一对相啮合的交错轴斜齿轮通常具有同样的齿向,即左旋主动齿轮跟右旋从动齿轮相啮合。
在交错轴斜齿设计中,当该齿的斜角相等时所产生滑移速度最小。
然而当该齿的斜角不相等时,如果两个齿轮具有相同齿向的话,大斜角齿轮应用作主动齿轮。
蜗轮与交错轴斜齿轮相似。
小齿轮即蜗杆具有较小的齿数,通常是一到四齿,由于它们完全缠绕在节圆柱上,因此它们被称为螺纹齿。
与其相配的齿轮叫做蜗轮,蜗轮不是真正的斜齿轮。
蜗杆和蜗轮通常是用于向垂直相交轴之间的传动提供大的角速度减速比。
蜗轮不是斜齿轮,因为其齿顶面做成中凹形状以适配蜗杆曲率,目的是要形成线接触而不是点接触。
然而蜗杆蜗轮传动机构中存在齿间有较大滑移速度的缺点,正像交错轴斜齿轮那样。
蜗杆蜗轮机构有单包围和双包围机构。
单包围机构就是蜗轮包裹着蜗杆的一种机构。
当然,如果每个构件各自局部地包围着对方的蜗轮机构就是双包围蜗轮蜗杆机构。
着两者之间的重要区别是,在双包围蜗轮组的轮齿间有面接触,而在单包围的蜗轮组的轮齿间有线接触。
一个装置中的蜗杆和蜗轮正像交错轴斜齿轮那样具有相同的齿向,但是其斜齿齿角的角度是极不相同的。
蜗杆上的齿斜角度通常很大,而蜗轮上的则极小,因此习惯常规定蜗杆的导角,那就是蜗杆齿斜角的余角;也规定了蜗轮上的齿斜角,该两角之和就等于90度的轴线交角。
当齿轮要用来传递相交轴之间的运动时,就需要某种形式的锥齿轮。
虽然锥齿轮通常制造成能构成90度轴交角,但它们也可产生任何角度的轴交角。
轮齿可以铸出,铣制或滚切加工。
仅就滚齿而言就可达一级精度。
在典型的锥齿轮安装中,其中一个锥齿轮常常装于支承的外侧。
这意味着轴的挠曲情况更加明显而使在轮齿接触上具有更大的影响。
另外一个难题,发生在难于预示锥齿轮轮齿上的应力,实际上是由于齿轮被加工成锥状造成的。
直齿锥齿轮易于设计且制造简单,如果他们安装的精密而确定,在运转中会产生良好效果。
然而在直齿圆柱齿轮情况下,在节线速度较高时,他们将发出噪音。
在这些情况下,螺旋锥齿轮比直齿轮能产生平稳的多的啮合作用,因此碰到高速运转的场合那是很有用的。
当在汽车的各种不同用途中,有一个带偏心轴的类似锥齿轮的机构,那是常常所希望的。
这样的齿轮机构叫做准双曲面齿轮机构,因为它们的节面是双曲回转面。
这种齿轮之间的轮齿作用是沿着一根直线上产生滚动与滑动相结合的运动并和蜗轮蜗杆的轮齿作用有着更多的共同之处。
轴是一种转动或静止的杆件。
通常有圆形横截面。
在轴上安装像齿轮,皮带轮,飞轮,曲柄,链轮和其他动力传递零件。
轴能够承受弯曲,拉伸,压缩或扭转载荷,这些力相结合时,人们期望找到静强度和疲劳强度作为设计的重要依据。
因为单根轴可以承受静压力,变应力和交变应力,所有的应力作用都是同时发生的。
“轴”这个词包含着多种含义,例如心轴和主轴。
心轴也是轴,既可以旋转也可以静止的轴,但不承受扭转载荷。
短的转动轴常常被称为主轴。
当轴的弯曲或扭转变形必需被限制于很小的范围内时,其尺寸应根据变形来确定,然后进行应力分析。
因此,如若轴要做得有足够的刚度以致挠曲不太大,那么合应力符合安全要求那是完全可能的。
但决不意味着设计者要保证;它们是安全的,轴几乎总是要进行计算的,知道它们是处在可以接受的允许的极限以内。
因之,设计者无论何时,动力传递零件,如齿轮或皮带轮都应该设置在靠近支持轴承附近。
这就减低了弯矩,因而减小变形和弯曲应力。
虽然来自M.H.G方法在设计轴中难于应用,但它可能用来准确预示实际失效。
这样,它是一个检验已经设计好了的轴的或者发现具体轴在运转中发生损坏原因的好方法。
进而有着大量的关于设计的问题,其中由于别的考虑例如刚度考虑,尺寸已得到较好的限制。
设计者去查找关于圆角尺寸、热处理、表面光洁度和是否要进行喷丸处理等资料,那真正的唯一的需要是实现所要求的寿命和可靠性。
由于他们的功能相似,将离合器和制动器一起处理。
简化摩擦离合器或制动器的动力学表达式中,各自以角速度w1和w2运动的两个转动惯量I1和I2,在制动器情况下其中之一可能是零,由于接上离合器或制动器而最终要导致同样的速度。
因为两个构件开始以不同速度运转而使打滑发生了,并且在作用过程中能量散失,结果导致温升。
在分析这些装置的性能时,我们应注意到作用力,传递的扭矩,散失的能量和温升。
所传递的扭矩关系到作用力,摩擦系数和离合器或制动器的几何状况。
这是一个静力学问题。
这个问题将必须对每个几何机构形状分别进行研究。
然而温升与能量损失有关,研究温升可能与制动器或离合器的类型无关。
因为几何形状的重要性是散热表面。
各种各样的离合器和制动器可作如下分类:1.轮缘式内膨胀制冻块;2.轮缘式外接触制动块;3.条带式;4.盘型或轴向式;5.圆锥型;6.混合式。
分析摩擦离合器和制动器的各种形式都应用一般的同样的程序,下面的步骤是必需的:1.假定或确定摩擦表面上压力分布;2.找出最大压力和任一点处压力之间的关系;3.应用静平衡条件去找寻(a)作用力;(b)扭矩;(c)支反力。
混合式离合器包括几个类型,例如强制接触离合器、超载释放保护离合器、超越离合器、磁液离合器等等。
强制接触离合器由一个变位杆和两个夹爪组成。
各种强制接触离合器之间最大的区别与夹爪的设计有关。
为了在结合过程中给变换作用予较长时间周期,夹爪可以是棘轮式的,螺旋型或齿型的。
有时使用许多齿或夹爪。
他们可能在圆周面上加工齿,以便他们以圆柱周向配合来结合或者在配合元件的端面上加工齿来结合。
虽然强制离合器不像摩擦接触离合器用的那么广泛,但它们确实有很重要的运用。
离合器需要同步操作。
有些装置例如线性驱动装置或电机操作螺杆驱动器必须运行到一定的限度然后停顿下来。
为着这些用途就需要超载释放保护离合器。
这些离合器通常用弹簧加载,以使得在达到预定的力矩时释放。
当到达超载点时听到的“喀嚓”声就被认定为是所希望的信号声。
超越离合器或连轴器允许机器的被动构件“空转”或“超越”,因为主动驱动件停顿了或者因为另一个动力源使被动构件增加了速度。
这种离合器通常使用装在外套筒和内轴件之间的滚子或滚珠。
该内轴件,在它的周边加工了数个平面。
驱动作用是靠在套筒和平面之间契入的滚子来获得。
因此该离合器与具有一定数量齿的棘轮棘爪机构等效。
磁液离合器或制动器相对来说是一个新的发展,它们具有两平行的磁极板。
这些磁极板之间有磁粉混合物润滑。
电磁线圈被装入磁路中的某处。
借助激励该线圈,磁液混合物的剪切强度可被精确的控制。
这样从充分滑移到完全锁住的任何状态都可以获得。
加工基础作为产生形状的一种加工方法,机械加工是所有制造过程中最普遍使用的而且是最重要的方法。
机械加工过程是一个产生形状的过程,在这过程中,驱动装置使工件上的一些材料以切屑的形式被去除。
尽管在某些场合,工件无承受情况下,使用移动式装备来实现加工,但大多数的机械加工是通过既支承工件又支承刀具的装备来完成。
机械加工在知道过程中具备两方面。
小批生产低费用。
对于铸造、锻造和压力加工,每一个要生产的具体工件形状,即使是一个零件,几乎都要花费高额的加工费用。
靠焊接来产生的结构形状,在很大程度上取决于有效的原材料的形式。
一般来说,通过利用贵重设备而又无需特种加工条件下,几乎可以以任何种类原材料开始,借助机械加工把原材料加工成任意所需要的结构形状,只要外部尺寸足够大,那都是可能的。
因此对于生产一个零件,甚至当零件结构及要生产的批量大小上按原来都适于用铸造、锻造或者压力加工来生产的,但通常宁可选择机械加工。
严密的精度和良好的表面光洁度,机械加工的第二方面用途是建立在高精度和可能的表面光洁度基础上。
许多零件,如果用别的其他方法来生产属于大批量生产的话,那么在机械加工中则是属于低公差且又能满足要求的小批量生产了。
另方面,许多零件靠较粗的生产加工工艺提高其一般表面形状,而仅仅是在需要高精度的且选择过的表面才进行机械加工。
例如内螺纹,除了机械加工之外,几乎没有别的加工方法能进行加工。
又如已锻工件上的小孔加工,也是被锻后紧接着进行机械加工才完成的。
基本的机械加工参数刀具的基本关系是以以下四个要素来充分描述的:刀具的几何形状,切削速度,进给速度,和吃刀深度。
切削刀具必须用一种合适的材料来制造,它必须是强固、韧性好、坚硬而且耐磨的。
刀具的几何形状——以刀尖平面和刀具角为特征——对于每一种切削工艺都必须是正确的。
切削速度是切削刃通过工件表面的速率,它是以每分钟英寸来表示。
为了有效地加工,切削速度高低必须适应特定的工件——刀具配合。
一般来说,工件材料越硬,速度越低。
进给速度是刀具切进工件的速度。
若工件或刀具作旋转运动,进给量是以每转转过的英寸数目来度量的。
当刀具或工件作往复运动时,进给量是以每一行程走过的英寸数度量的。
一般来说,在其他条件相同时,进给量与切削速度成反比。