煅烧高硅、高铝料的操作、调整方法
高饱和高铝氧率配料方案的实践

1 原 燃 材 料 分 析
原燃材 料化 学分 析见 表 l表 2 、 。
表 1 无烟 煤 的工 业 分 析
大胆 地尝 试 和改 进 。本 文 就 高饱 和 高 铝氧 率 配料
方 案 的试生 产情 况作一 总结 。
山 西 阳 泉 表 2 原 材 料 化 学 分 析
M d % A d % V d% a/ a/ a/
日产 2 0 50的新 型干法 生产 线 ,对原 有 的生 产线 以 节能 降耗提 高熟 料质 量为重 点进 行技术 改造 。 () 1应用 新技 术节 电 。几 年来 , 先后 在风 机 、 水 泵 、 粉机 、 选 收尘 器上 安装 了 7 0台套变 频调 速器 , 在 l 8台 10 k 至 3 5k 电. 上 实行 电 容无 功 00 W 3 OW 机 自动 补偿 , 同时将 降压启 动改 为软启 动 , 少 电力 减
况 见表 3 表 4 、 。
表 3 新 、 方 案 的 熟 料化 学成 分 老
方 案 比表 面积 安 定 性
初 凝 /h rn 终 凝/h mn ( : i) a ( : i)
抗折/ a MP
3 d 2d 8
抗压/ a MP
3 d 2d 8
3 技 术 措 施
的均 化方式 , 确保 人窑 生料粉 的成 分 和配热 的均 来
3 1 适 当降低生 料细 度 . 由于饱 和 比 K H升 高 ,粘土用 量 降低 , 成球 塑 性 受 到一定 影 响 , 生料 细度控 制偏 指标下 限。
3 2 加 强人 窑生 料粉 的均 化 .
匀稳 定 , 严禁 出磨 即人 窑 , 立窑煅 烧创 造 良好 的 为
条件。
施综 合改 造 , 大窑 径 , 加保 温层 , 扩 增 配套 玻纤 大布 袋 除尘设施 。立 窑生 产工艺 改 造后 , 不单 台时产 量 从 l .t 高到 2t 15 提 8,熟料 抗压 强度 上升 5个 M a P, 吨熟 料标 准煤 耗从 15 g 降到 l7 g 4k 下 1k ,全年 节 煤 达 90 t 同时 , 司还 扩建 3 m 的晒场 , 0 0。 公 万 利用 自 - 然 光照 晒料 降 低高 炉水 渣等 不 产 生二 次扬 尘 物 料
高铝孰料煅烧总结 文档
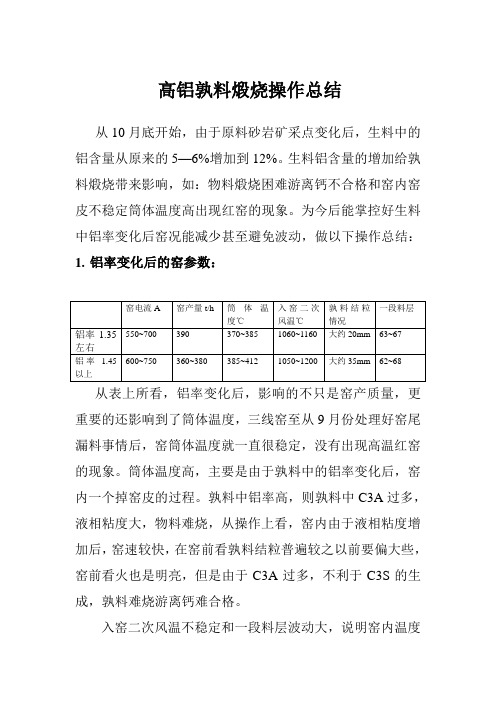
高铝孰料煅烧操作总结从10月底开始,由于原料砂岩矿采点变化后,生料中的铝含量从原来的5—6%增加到12%。
生料铝含量的增加给孰料煅烧带来影响,如:物料煅烧困难游离钙不合格和窑内窑皮不稳定筒体温度高出现红窑的现象。
为今后能掌控好生料中铝率变化后窑况能减少甚至避免波动,做以下操作总结:1.铝率变化后的窑参数:从表上所看,铝率变化后,影响的不只是窑产质量,更重要的还影响到了筒体温度,三线窑至从9月份处理好窑尾漏料事情后,窑筒体温度就一直很稳定,没有出现高温红窑的现象。
筒体温度高,主要是由于孰料中的铝率变化后,窑内一个掉窑皮的过程。
孰料中铝率高,则孰料中C3A过多,液相粘度大,物料难烧,从操作上看,窑内由于液相粘度增加后,窑速较快,在窑前看孰料结粒普遍较之以前要偏大些,窑前看火也是明亮,但是由于C3A过多,不利于C3S的生成,孰料难烧游离钙难合格。
入窑二次风温不稳定和一段料层波动大,说明窑内温度场不稳定,给操作上带来不稳定的因素。
2.铝率高后的操作方法:1.在生料铝率变化前,事先由原料磨出磨率值中得到,与质量调度人员联系,是否为原料或者原煤成分发生变化引起;2.得到铝率变化是由于原燃材料波动引起,第一时间与分厂相关领导联系告知生产情况,第一时间采取预防措施;3.在操作过程中,密切跟踪窑况变化,从各个参数中判断大窑运行情况,从窑头看火和出窑孰料判断窑内窑皮是否稳定、窑内热工制度是否正常,从而第一时间做出调整,如:增加窑头煤、增加窑内通风、减产等;4.通过观察筒体温度判断出窑内温度场的变化和窑皮的掉挂情况,第一时间得出铝率高后对窑内窑皮的影响。
如果筒体温度上升过快,则通过调整燃烧器或者增加外部冷却;5.稳定分解炉温度和入窑二次风温,两者都要兼顾,减少操作上人为的波动,给窑况带来不必要的影响;6.操作上有预见性和责任心,把实际生产情况及时汇报给分厂相关领导,并将自己的操作思想与相关人员进行交流。
3.小结:此次铝率高,事先没有做好应急预案,虽然时间短,但是也给生产带来较大的影响。
铝率及液相性质对高硅酸三钙含量硅酸盐水泥熟料烧成过程的影响
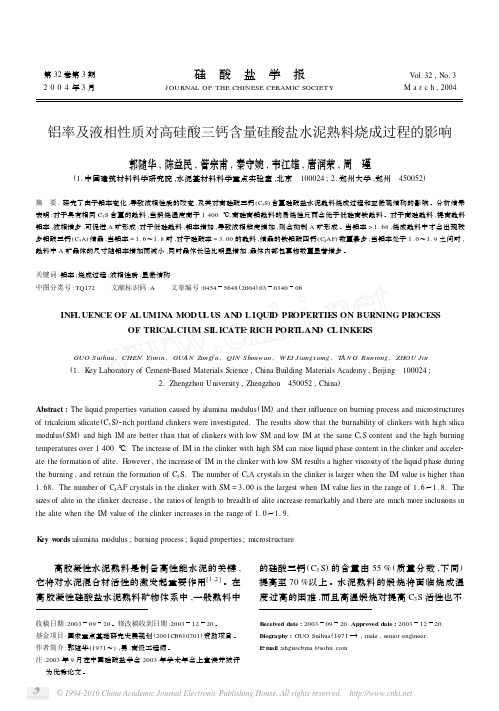
2. 28 8. 3 1. 98 ±0. 02 0. 92 8. 4
为优秀论文 。
Received date : 2003 09 20. Approved date : 2003 12 20. Biography : GUO Suihua (1971 —) , male , senior engineer. E2mail :shguocbma @sohu. com
© 1994-2010 China Academic Journal Electronic Publishing House. All rights reserved.
生料 片 于 120 ℃烘 干 。将 高 温 炉 温 度 升 至
800 ℃后 ,将生料片置于炉内 ,待炉温稳定约 5 min 后 ,开始升温至设定煅烧温度 ,保温 30 min 后出炉 。 采用风扇将出炉熟料试样冷却至室温 。
对所得熟料进行如下测试 : (1) 采用乙二醇酒精 溶液快速滴定法测试游离钙含量 ; (2) 测量其相对于 生料的线性收缩量 ,借以判断液相量的相对变化 ; (3) 采用 X 射线衍射 ( X2ray diff raction , XRD) 分析 确定矿物组成 ,分析熟料矿物形成的基本动力学过 程 ; (4) 分析烧成熟料试样的亚微观结构 ,判断熟料 亚微观结构的形成条件 。
1. 35 8. 8 2. 94 1. 46 1. 03 0. 72
1. 65 9. 69 4. 02 1. 39 1. 17 0. 86
1. 94 8. 2 3. 38 2. 05 1. 07 1. 47
2. 22 9. 9 2. 55 ±0. 02 0. 81 10. 92
4. 13 2. 19
5. 79 68. 18 14. 75 4. 58 2. 10 0. 83 2. 57 18. 40 3. 61 59. 00 6. 70 2. 77
生料成分对熟料煅烧的影响
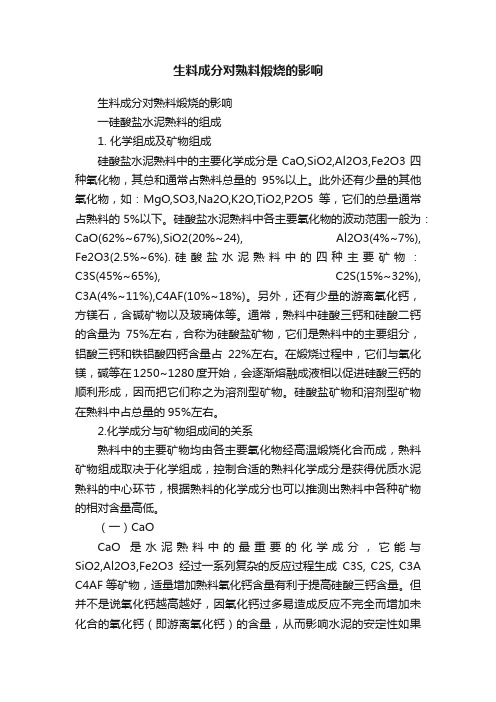
生料成分对熟料煅烧的影响生料成分对熟料煅烧的影响一硅酸盐水泥熟料的组成1. 化学组成及矿物组成硅酸盐水泥熟料中的主要化学成分是CaO,SiO2,Al2O3,Fe2O3四种氧化物,其总和通常占熟料总量的95%以上。
此外还有少量的其他氧化物,如:MgO,SO3,Na2O,K2O,TiO2,P2O5等,它们的总量通常占熟料的5%以下。
硅酸盐水泥熟料中各主要氧化物的波动范围一般为:CaO(62%~67%),SiO2(20%~24), Al2O3(4%~7%), Fe2O3(2.5%~6%).硅酸盐水泥熟料中的四种主要矿物:C3S(45%~65%), C2S(15%~32%), C3A(4%~11%),C4AF(10%~18%)。
另外,还有少量的游离氧化钙,方镁石,含碱矿物以及玻璃体等。
通常,熟料中硅酸三钙和硅酸二钙的含量为75%左右,合称为硅酸盐矿物,它们是熟料中的主要组分,铝酸三钙和铁铝酸四钙含量占22%左右。
在煅烧过程中,它们与氧化镁,碱等在1250~1280度开始,会逐渐熔融成液相以促进硅酸三钙的顺利形成,因而把它们称之为溶剂型矿物。
硅酸盐矿物和溶剂型矿物在熟料中占总量的95%左右。
2.化学成分与矿物组成间的关系熟料中的主要矿物均由各主要氧化物经高温煅烧化合而成,熟料矿物组成取决于化学组成,控制合适的熟料化学成分是获得优质水泥熟料的中心环节,根据熟料的化学成分也可以推测出熟料中各种矿物的相对含量高低。
(一)CaOCaO是水泥熟料中的最重要的化学成分,它能与SiO2,Al2O3,Fe2O3经过一系列复杂的反应过程生成C3S, C2S, C3A C4AF等矿物,适量增加熟料氧化钙含量有利于提高硅酸三钙含量。
但并不是说氧化钙越高越好,因氧化钙过多易造成反应不完全而增加未化合的氧化钙(即游离氧化钙)的含量,从而影响水泥的安定性如果熟料中氧化钙过低,则生成硅酸三钙太少,硅酸二钙却相应增加。
会降低水泥的胶凝性。
高温煅烧设备操作方法

高温煅烧设备操作方法高温煅烧设备操作方法一、概述高温煅烧设备是一种常用于矿石、陶瓷等物料的加热处理设备,通过提高温度来使物料发生化学反应或改变物理性质。
本文将详细介绍高温煅烧设备的操作方法。
二、准备工作在操作高温煅烧设备之前,首先需要进行一系列的准备工作:1. 熟悉设备:熟悉设备的结构、工作原理和操作流程。
2. 检查设备:仔细检查设备的各项参数,确保设备处于正常工作状态。
3. 工作区域准备:确保操作区域干燥、通风良好,无杂物阻碍操作。
4. 个人防护:佩戴合适的个人防护装备,如防火服、安全帽、面罩、手套等。
三、操作步骤1. 打开电源:按照设备说明书操作,确保电源可以正常供电。
2. 打开排气系统:排气系统用于排出设备内部的废气,打开排气系统以保持设备内的压力和温度稳定。
3. 加入物料:根据操作要求将待煅烧的物料加入设备内,注意加入量不要过多,以免超过设备的承载能力。
4. 设置温度:根据煅烧物料的要求,设定设备的温度。
注意调整温度时要逐渐升高,避免突然升温导致物料受损或设备损坏。
5. 控制时间:根据物料的煅烧时间要求,设定设备的煅烧时间。
6. 监控设备状态:在整个煅烧过程中,需要时刻监控设备的工作状态,包括温度、压力等参数,如果发现异常情况,要及时采取相应措施。
7. 结束煅烧:当煅烧时间到达设定时间后,关闭设备的加热装置,并等待设备冷却至安全温度后才能对设备进行其他操作。
8. 清洁设备:煅烧结束后,需要对设备进行清洁,包括清理设备内积聚的物料残留物等。
四、注意事项1. 安全第一:在操作过程中,要始终将安全放在首位,严禁制止各种违章作业,如开启设备盖子或不按要求穿戴个人防护装备等。
2. 预防温度过高:在操作设备的过程中,要确保设备温度不会过高,以免发生设备破裂或火灾等事故。
3. 合理控制时间:煅烧时间过长可能会导致物料过度煅烧,损坏或浪费物料;煅烧时间过短则无法达到预期的煅烧效果。
4. 注意排气系统:排气系统的畅通与否直接影响设备内部的稳定性和安全性,要经常检查排气系统是否有堵塞现象。
高硅石灰石煅烧中控操作要点

高硅石灰石煅烧中控操作要点发布时间:2021-05-03T08:49:10.829Z 来源:《中国科技人才》2021年第4期作者:王金辉[导读] 石灰是转炉炼钢最重要的造渣材料之一。
炼钢过程中石灰参与造渣反应的能力通常用石灰的"活性度"来表示,一般将用酸碱滴定法测定的活性度在300mL(4N-HCl)以上的石灰称为活性石灰。
金泥化工有限责任公司 737000摘要:近年来,经济发展迅速,矿山质量发生变化,石灰石SiO2含量高,导致生产困难。
通过在矿山开采、生料配料、熟料煅烧等环节加强管控与技术创新,不需外购石灰石,全用自有矿山高硅石灰石(SiO2含量12%)配料,能够稳定生产熟料硅酸率达到3.1左右的优质硅酸盐水泥熟料(3d抗压强度29.0MPa,28d抗压强度59.0MPa)。
关键词:高硅石灰石煅烧;中控操作;要点引言石灰是转炉炼钢最重要的造渣材料之一。
炼钢过程中石灰参与造渣反应的能力通常用石灰的"活性度"来表示,一般将用酸碱滴定法测定的活性度在300mL(4N-HCl)以上的石灰称为活性石灰。
1几种窑型的比较目前,国内较常使用的机械化立窑窑体形状有以下几种:圆截面形、椭圆截面形和准矩形截面形,当然还有根据这几种窑型改进的窑型。
椭圆截面形和准矩形截面形相对于圆截面形来说,对布料设备要求高,一台布料设备很难保证物料在窑体内的均匀性,所以在没有燃料、燃烧方式的特殊要求下,一般采用较少。
圆截面形在布料过程中,因为物料在所有方向的分布概率相等,对于石灰窑布料的均匀性而言,圆截面形布料的方式更加简单,对设备要求更低。
圆截面形窑体又分为:直筒形、截圆锥形、花瓶型。
直筒形窑体,窑的内径上下相同。
这种窑的主要优点是:结构简单、稳固和砌筑方便;具有较小的容积表面积,向周围介质的散热损失小。
缺点是:当混合料粒度发生变化时,物料下落和气流沿窑身整个截面分布的均匀性较差,窑壁效应明显。
铝用阳极煅烧车间生产工艺调整方案
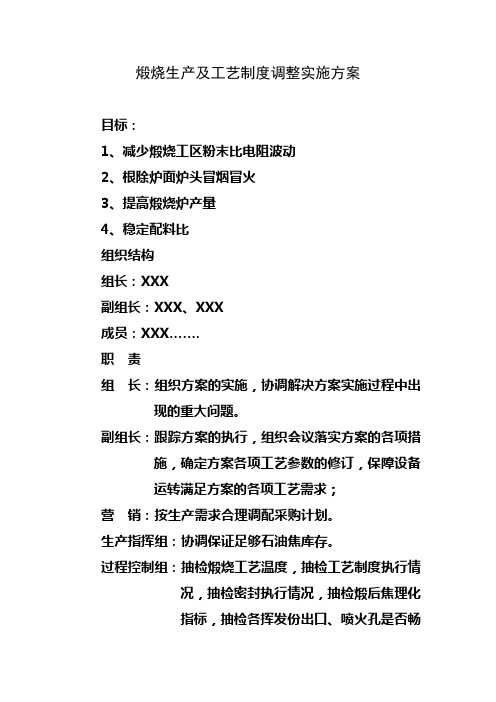
煅烧生产及工艺制度调整实施方案目标:1、减少煅烧工区粉末比电阻波动2、根除炉面炉头冒烟冒火3、提高煅烧炉产量4、稳定配料比组织结构组长:XXX副组长:XXX、XXX成员:XXX…….职责组长:组织方案的实施,协调解决方案实施过程中出现的重大问题。
副组长:跟踪方案的执行,组织会议落实方案的各项措施,确定方案各项工艺参数的修订,保障设备运转满足方案的各项工艺需求;营销:按生产需求合理调配采购计划。
生产指挥组:协调保证足够石油焦库存。
过程控制组:抽检煅烧工艺温度,抽检工艺制度执行情况,抽检密封执行情况,抽检煅后焦理化指标,抽检各挥发份出口、喷火孔是否畅通,排料系统是否正常。
煅烧区域:按方案组织生产,及时反馈方案执行中的问题,收集各点工艺数据,检查生产中工艺纪律执行,排查煅烧炉破损火道,根据火道破损程度确定排料方案。
企管部:保证分析数据准确、及时。
XX炭素专家组:处理解决方案执行中出现的工艺问题,制定解决方案。
二、工艺参数:火道首层负压 20-35Pa老系统四层火道温度 1200-1300℃新系统五层火道温度 1200-1300℃(特殊火道除外)炉头料颗粒度:不大于70mm,2mm以下不大于40%三、工艺调整:1、负压的调整:①、5#、6#煅烧炉中间火道首层负压20-35 Pa,边火道比中间火道提升5Pa,即1#火道和24#火道首层负压25-40 Pa。
②、新系统煅烧炉中间火道首层负压15-30 Pa,边火道比中间火道提升5Pa,即1#火道和24#火道首层负压20-35 Pa。
③、负压的控制通过8层的负压拉板完成,负压控制在中间值为最佳,各条火道负压平稳相近。
④、由于各火道负压存在互相的影响,调整应多次进行。
⑤、破损的火道,应根据实际情况分别对待。
⑥、制定相应制度,按时测量调整负压。
2、排料时间的调整根据少排勤排的原则,增加每小时的排料次数,每小时不少于7次3、配料比的调整①、保证同时库存不少于3家,每种原料不少于1000吨。
5-焙烧煅烧法
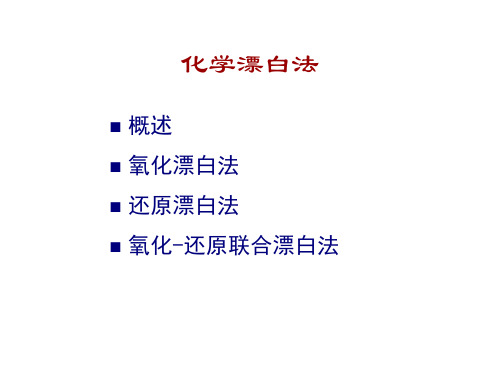
连二亚硫酸钠漂白法
Fe2O3+Na2S2O4+H2SO4=Na2SO4+2FeSO3+H2O
化学选矿
概述 浸出法 化学漂白法 煅烧法
煅烧法
概述 煅烧方法 煅烧工艺 煅烧工艺设备
概述
非金属矿煅烧的目的: 脱除杂质,提高产品的纯度和白度 脱除碳质、有机物 脱除硫化物 改变矿物现状,有利于下一道工序的进行 石英岩的煅烧和急冷——有利于超细磨矿的 进行
特点:具有优良的电性能 用途:电缆绝缘层的电性能
改良剂,或用于橡胶制品及 橡胶密封材料的填料 要求:这种煅烧高岭土除脱 羟基要求完全外,对白度 、 活性要求不太严格。
高岭土的煅烧
700-860 ℃煅烧的高岭土 特点:高岭石的层状晶体结
构遭到破坏,在层间形成多 孔结构,扩大了吸附能力及 比表面积,活性好 用途:制备合成沸石、农药 载体或催化剂载体等。 要求:除了对产品有较高白 度要求外,对产品活性、细 度及铝硅比亦有要求。
用于高岭土煅烧的回转窑多为间接加热回转窑。
回转窑
回转窑
燃烧气体以逆流方式由燃烧室进入煅烧炉。
高岭土由高端尾喂料机给入,借助于筒体的斜度 和旋转,窑内物料一面沿周向翻滚,一面沿轴向 移动。
工作原理:将煤加入 燃烧室的炉栅上,一 次空气由灰坑穿过炉 栅,经过煤层与煤燃 烧。
燃烧产物从挡火墙和 窑墙所围成的喷火口 喷到窑顶,再从窑顶 经过窑内的高岭土匣 钵倒流至窑底,最后 由吸火孔、支烟道及 主烟道向烟囱排出。
倒焰窑工作流程图 1---窑室;2---燃烧室; 3---灰坑;4---窑底吸火孔; 5---支烟道;6---主烟道; 7---挡火墙;8---窑墙; 9---窑顶;10---喷火孔
煅烧工段操作说明书

操作要求及说明一、烧工段的主要控制内容:1、通过对窑运行参数的控制来调控出料的白度。
2、产品的筛余物、黑点。
二、影响煅烧高岭土产品白度的主要因素:1、物料水分。
物料水分的高低影响物料在窑内的脱水时间,稳定的物料水分对煅烧白度的稳定有直接的影响。
2、窑转速。
窑转速的高低决定了煅烧时间和窑内物料的填充率,对产品白度和窑产量有直接影响。
3、进料量。
进料的稳定对窑产量和白度的稳定与提高有极大的帮助。
4、进风量。
窑头进风一方面为窑内煅烧提供氧气,另一方面还会降低窑内的实际煅烧温度。
窑的进风量还决定了窑头的温度高低。
5、窑头物料的容重的大小会影响窑的实际进料量和窑头进风量的需要量,因此对煅烧的影响很大。
合理控制窑头料仓的料位来减小容重的变化。
6、煅烧温度。
控制合理、稳定的煅烧温度对窑产量和产品白度有直接的关系。
温度的变化往往比控制煤气的开度变化滞后,所以操作者要有简单的控制知识。
三、煅烧工段主要控制参数:1、温度:燃烧室温度:1130~1150℃窑头温度:≥630℃2、风机开度:一次风机≥65%二次风机10%~15%引风机:180~280A3、回转窑参数:转速:≥40HZ电流:<50A进料:窑头大料仓≥15HZ,小料仓≥10HZ窑尾负压:自然进风。
旋风筒物料白度≥94.5%(短时间下限为93.7%)四、一般不合格品的处置:一般不合格品是指出窑物料白度在90%~93.5%之间的物料,可以在白度大于94.5时按≤5%的速率从打散机均匀加入,保证包装白度≥93.0%。
五、环境与定置要求:本工段的主要废弃物是地面垃圾、废机油、废润滑脂、废棉纱和窑头泄漏的粉料。
地面垃圾每班集中运到垃圾池处理,废机油、废润滑脂和废棉纱分别在车间内定置存放集中处理,泄漏的粉料每班下班前集中运到喷雾工段过筛后加入。
岗位的物料和工具的放置见本岗位“定置图”。
设备原理及操作一、主要设备及名称:1、1#窑主要设备配制及名称:日常使用的工具:内六角扳手、活扳手、梅花扳手、铁锹、扫帚二、煅烧及物料输送原理:1、低温除湿阶段又称焙干、烘干或预热阶段。
高硅石灰石煅烧中控操作要点

福建海峡水泥有限公司是由中材国际南京水泥工业设计研究院设计的日产 6000t 熟料新型干法水泥生产线。烧成窑中配置了一台Ф5.0x74m 回转窑、烧成窑 头配置第四代冷却机、熟料储存为一个Ф60 米的圆库,储量 10 万吨。
石中 SiO2 含量(质量分数)在 5%以下。受制于资源因素的制约,公司开采的石灰 石中 SiO2 含量均在 8%左右。对石灰石破碎、生料粉磨效率及熟料煅烧造成非常不 利的影响。
选用碾压方式时应综合考虑各种因素。若是沥青面层较厚,则应该选用振动 压路机进行作业,而在混合料较软时,则建议使用胶轮压路机进行施工作业。在 对待接茬缝方面,在能够保证平整度的情境下,通常应该选用图1○2的方法,若 是无法确保平整度,则应该选用图1○1的方法。当出现碾压推移现象时,要准确 的寻找其出现的原因,并积极地采取措施。
经过中控全体窑操同仁的共同努力,与各部门的协同配合下,在慢慢摸索的 过程中,通过采用以上调控操作措施,有效提高熟料的质量,使得熟料结粒良好,
解,提高炉中温度可加速 CaCO3 的分解,使出炉物料的分解率在 92%以上,提高 物料的分解率减轻了回转窑的煅烧力度,从而稳定生产线的热工制度。 2.3 火焰形状与煤粉质量的控制
4 水泥与混凝土生产 Cement and concrete production
高硅石灰石煅烧中控操作要点
李进鑫 (福建水泥股份有限公司德化海峡分公司, 福建 泉州 352516)
中图分类号:TB332 文献标识码:A 文章编号 1007-6344(2020)02-0001-01
摘要:通过对某新型干法水泥熟料线存在的石灰石硅含量过高对生产存在的影响,寻找中控操作的最佳方案。 关键词:高硅石灰石;中控操作要点
拟[J].中国电机工程学报,2019,39(23):6952-6963+7108.
高氧化镁石灰石煅烧熟料的配料工艺方法
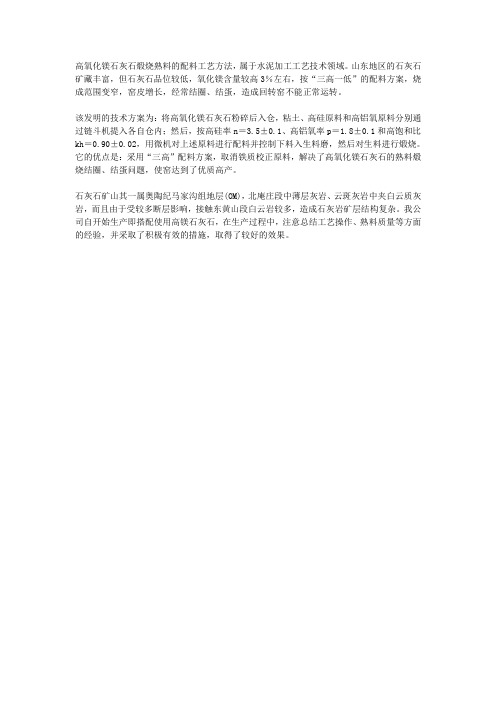
高氧化镁石灰石煅烧熟料的配料工艺方法,属于水泥加工工艺技术领域。
山东地区的石灰石矿藏丰富,但石灰石品位较低,氧化镁含量较高3%左右,按“三高一低”的配料方案,烧成范围变窄,窑皮增长,经常结圈、结蛋,造成回转窑不能正常运转。
该发明的技术方案为:将高氧化镁石灰石粉碎后入仓,粘土、高硅原料和高铝氧原料分别通过链斗机提入各自仓内;然后,按高硅率n=3.5±0.1、高铝氧率p=1.8±0.1和高饱和比kh=0.90±0.02,用微机对上述原料进行配料并控制下料入生料磨,然后对生料进行煅烧。
它的优点是:采用“三高”配料方案,取消铁质校正原料,解决了高氧化镁石灰石的熟料煅烧结圈、结蛋问题,使窑达到了优质高产。
石灰石矿山其一属奥陶纪马家沟组地层(OM),北庵庄段中薄层灰岩、云斑灰岩中夹白云质灰岩,而且由于受较多断层影响,接触东黄山段白云岩较多,造成石灰岩矿层结构复杂。
我公司自开始生产即搭配使用高镁石灰石,在生产过程中,注意总结工艺操作、熟料质量等方面的经验,并采取了积极有效的措施,取得了较好的效果。
工业硅、硅铁冶炼时如何加料和控制料面高度?(加料和控制料面高度方法与措施)

工业硅、硅铁冶炼时如何加料和控制料面高度?(加料和控制料面高度方法与措施)工业硅冶炼的基本反应,是利用碳质材料中的碳,将硅石中二氧化硅的硅还原出来的反应。
要使这一反应顺利进行,必须有良好的炉况。
正确的加料方法,是获得良好炉况、达到高产量低消耗的关键环节之一。
因此,加料时应注意以下几点:(1)每批料必须混合均匀后加入炉内,不准偏加料。
每批料的配比,是根据硅冶炼的化学反应原理和所用原料的成分,并结合实际情况计算出来的。
所以,加入炉内的每批料的组成,必须符合批料的配比。
均匀地混合炉料是保证炉内反应正常进行的重要操作条件。
如果炉料未经均匀混合或任意选择性的加入炉内,这就是同常所说的“偏加料”,其结果是在炉内局部区域造成硅石过剩或焦碳过剩,这两种情况都不利于炉内反映顺利进行,而使炉况恶化。
可见,炉料混合均匀是十分重要的。
(2)炉料要连续地一小批一小批地加入炉内。
这样不但易于控制料面的高度,而且可以使加入炉料的组成及其分布比较均匀。
(3)必须适当地控制料面的高度。
料面高度过高则电极上升,料面过低易塌料,两者都不能充分的利用热量,都会对炉况产生不利的影响。
料面高度控制适当,可使电极较深的插入炉料中,从而提高炉温和扩大坩埚,使炉料可得到充分的预热,促使炉内反应加快进行。
(4)加料时要随时观察炉况,如料面透气性及电极动态等,必要时应采取相应的措施进行处理。
(5)应使炉料与电极成垂直方向加入,但要防止炉料碰撞电极。
这种加料方法,可使料面成为低料面宽锥体的形状,不致引起电极波动。
小容量工业硅矿热炉,因其炉温度较低,熔炼速度较慢,应力求减小热量损失。
加料时应注意如下几点:①勤加、薄盖。
②随时注意刺火并在处理火后应及时加料。
③在保持适当的锥体和料面的前提下,进行焖烧,直到出硅后将炉料捣下去,再重新加料焖烧。
现在工业硅生产的加料方式,大多采用加料机加料。
加料时应注意以下几点:①少加勤快为宜。
不能一次加得过多,以便保持良好的料面透气性。
煅烧过程中氧化镁行量过高问题

表5调整后熟料物理性能
方案80μm筛余/%比表面积(m2/kg)标准稠度用水量/% SO3
/%凝结时间抗折强度
/MPa抗压强度/MPa
初凝终凝3d 28d 3d 28d
如果熟料MgO含量较高(3.2%~4.2%),液相表面张力大幅度下降,含4%MgO时的表面张力为0.51N/m,迫使其煅烧温度要比正常温度低,煅烧范围要比正常窄,不利于f-CaO的吸收和晶体发育。表现在熟料外观结粒细小,飞砂严重。同时,在煅烧方面表现为易烧性好,但烧结范围变窄,操作难度大。
如果熟料MgO含量过高(>4.2%),熟料出现结球严重,窑电流平均达450A以上,频繁出现结大球,冷却破碎之后的熟料大多数为黄块,窑头飞砂严重。我们采取常规的降铁措施,现象不但没有扭转,反而更加恶劣,反常规调整,却有效果。从资料[1]得知,MgO含量>4.2%时,熟料液相黏度增加,使阿利特结晶困难,从而使结粒变大,窑内极易结圈、结蛋。
3.3.2降低并稳定入窑分解率
控制入窑物料表观分解率在90%左右,最高不超过94%。在生产实践中,常出现因为入窑物料分解率过高达96%,熟料升重降低,质量下降。分析认为,由于分解率过高,也就是生料预烧较好,使液相提前出现,窑内碳酸盐分解带缩短,固相反应带相应拉长,使化学反应产物活性降低,从而导致熟料升重降低,熟料实物质量下降。
配方2 2.3 353 23.6 2.3 105 150 6.2 9.0 32.5 62.6
配方3 2.3 350 23.6 2.2 100 145 6.0 8.9 32.1 61.9
煅烧硅酸铝
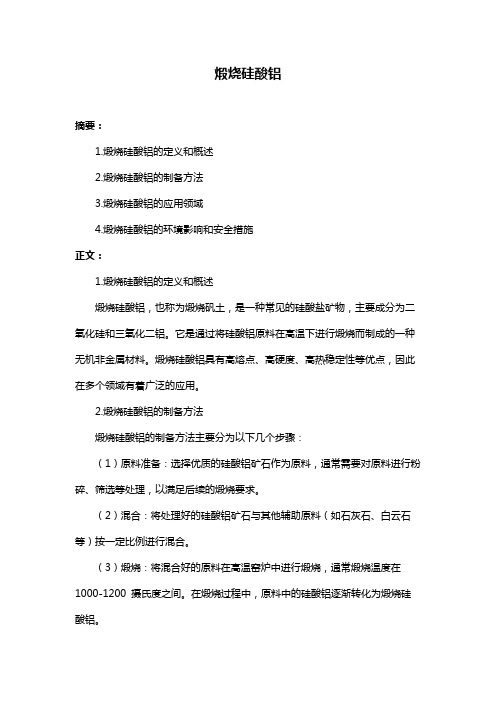
煅烧硅酸铝摘要:1.煅烧硅酸铝的定义和概述2.煅烧硅酸铝的制备方法3.煅烧硅酸铝的应用领域4.煅烧硅酸铝的环境影响和安全措施正文:1.煅烧硅酸铝的定义和概述煅烧硅酸铝,也称为煅烧矾土,是一种常见的硅酸盐矿物,主要成分为二氧化硅和三氧化二铝。
它是通过将硅酸铝原料在高温下进行煅烧而制成的一种无机非金属材料。
煅烧硅酸铝具有高熔点、高硬度、高热稳定性等优点,因此在多个领域有着广泛的应用。
2.煅烧硅酸铝的制备方法煅烧硅酸铝的制备方法主要分为以下几个步骤:(1)原料准备:选择优质的硅酸铝矿石作为原料,通常需要对原料进行粉碎、筛选等处理,以满足后续的煅烧要求。
(2)混合:将处理好的硅酸铝矿石与其他辅助原料(如石灰石、白云石等)按一定比例进行混合。
(3)煅烧:将混合好的原料在高温窑炉中进行煅烧,通常煅烧温度在1000-1200 摄氏度之间。
在煅烧过程中,原料中的硅酸铝逐渐转化为煅烧硅酸铝。
(4)冷却与粉碎:煅烧完成后,将产物进行冷却,然后进行粉碎,以满足不同应用场景的需求。
3.煅烧硅酸铝的应用领域煅烧硅酸铝广泛应用于以下几个领域:(1)陶瓷行业:煅烧硅酸铝作为陶瓷釉料的主要成分,可提高陶瓷制品的硬度、光泽度和热稳定性。
(2)耐火材料:煅烧硅酸铝的高熔点和高热稳定性使其成为优质的耐火材料,可用于制作炉膛、高温炉等设备。
(3)化工行业:煅烧硅酸铝可作为催化剂和催化剂载体,用于石油化工、化学肥料等生产过程。
(4)环保领域:煅烧硅酸铝具有很好的吸附性能,可用于废水处理、空气净化等环保领域。
4.煅烧硅酸铝的环境影响和安全措施煅烧硅酸铝生产过程中,可能会产生一定程度的环境污染,如粉尘、废气等。
为了降低环境影响,企业需采取相应的环保措施,如封闭式生产、废气处理等。
高温锻铝炉安全操作规程
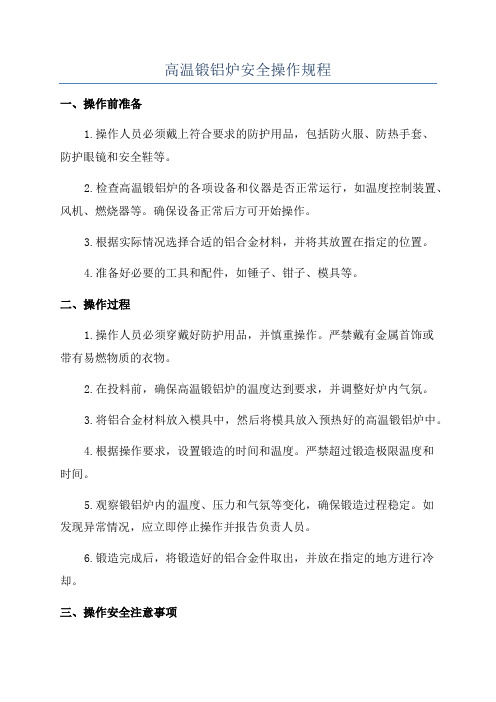
高温锻铝炉安全操作规程一、操作前准备1.操作人员必须戴上符合要求的防护用品,包括防火服、防热手套、防护眼镜和安全鞋等。
2.检查高温锻铝炉的各项设备和仪器是否正常运行,如温度控制装置、风机、燃烧器等。
确保设备正常后方可开始操作。
3.根据实际情况选择合适的铝合金材料,并将其放置在指定的位置。
4.准备好必要的工具和配件,如锤子、钳子、模具等。
二、操作过程1.操作人员必须穿戴好防护用品,并慎重操作。
严禁戴有金属首饰或带有易燃物质的衣物。
2.在投料前,确保高温锻铝炉的温度达到要求,并调整好炉内气氛。
3.将铝合金材料放入模具中,然后将模具放入预热好的高温锻铝炉中。
4.根据操作要求,设置锻造的时间和温度。
严禁超过锻造极限温度和时间。
5.观察锻铝炉内的温度、压力和气氛等变化,确保锻造过程稳定。
如发现异常情况,应立即停止操作并报告负责人员。
6.锻造完成后,将锻造好的铝合金件取出,并放在指定的地方进行冷却。
三、操作安全注意事项1.在进行铝合金锻造过程中,严禁使用手直接接触炉内铝合金材料。
2.高温锻铝炉周围必须保持干燥、整洁,严禁堆放易燃、易爆物品。
3.炉体温度过高时,操作人员不可太靠近炉体,应远离高温区域。
4.高温锻铝炉一旦出现故障或异常情况,应立即切断电源,并报告维修。
5.操作人员严禁擅自调整高温锻铝炉的温度和时间设置,必须经过负责人员的批准。
6.高温锻铝炉操作结束后,应及时清理设备周围的污物和杂物。
四、事故处理1.在高温锻铝炉操作过程中,如果发生事故,首先要确保自己的安全,然后迅速通知负责人员。
2.在发生火灾时,应迅速切断电源,并使用灭火器或灭火器材进行扑灭,如无法控制火势,应迅速撤离,确保自己的生命安全。
3.在发生人身伤害事故时,应立即停止操作,并帮助伤者进行急救,同时通知负责人员及时处理。
硅酸铝制备过程的

陶瓷与玻璃行业
硅酸铝在陶瓷和玻璃行业中作为主 要原料,用于生产高品质的产品。
其他领域如涂料、橡胶、化妆品,作为添 加剂使用。市场现状与趋势
市场需求稳定增长
随着建筑和工业领域的不断发展,硅酸铝市场需求稳步增长。
高品质产品供不应求
目前高品质的硅酸铝产品市场供应紧张,价格较高。
技术创新推动市场发展
总结词
生产效率问题主要受到反应速度、设备能力和原材料的 影响。
详细描述
通过改进反应条件,如提高反应温度和压力,可以加速 化学反应,提高生产效率。此外,优化设备配置和提升 设备能力也可以提高生产效率。
设备腐蚀问题
总结词
设备腐蚀问题主要源于化学反应产生的腐蚀性物质。
详细描述
为解决设备腐蚀问题,需要选择耐腐蚀的设备材料, 如不锈钢和钛合金等。同时,加强设备的维护和保养 ,及时更换受损部件,以延长设备的使用寿命。
随着生产技术的不断进步,硅酸铝产品的性能不断提高,推动市场 进一步发展。
未来发展方向与挑战
扩大应用领域
进一步开拓硅酸铝在其他领域的 应用,如新能源、电动汽车等。
提高产品质量
加大研发投入,提高硅酸铝产品 的性能和质量,满足高端领域的
需求。
环保与可持续发展
关注环保和可持续发展,采用绿 色生产工艺,降低能耗和排放。
03
参考文献3
该文献主要关注硅酸铝在高温下的性能表现,研究了硅酸铝在高温下的
热膨胀行为、热导率、抗热震性能等,为硅酸铝在高温领域的应用提供
了实验依据。
THANKS
感谢观看
其他方法
其他制备硅酸铝的方法还包括化学气相沉积法、电化学法、 微乳液法等。
这些方法各有优缺点,需要根据具体需求选择合适的方法。
煅烧硅酸铝
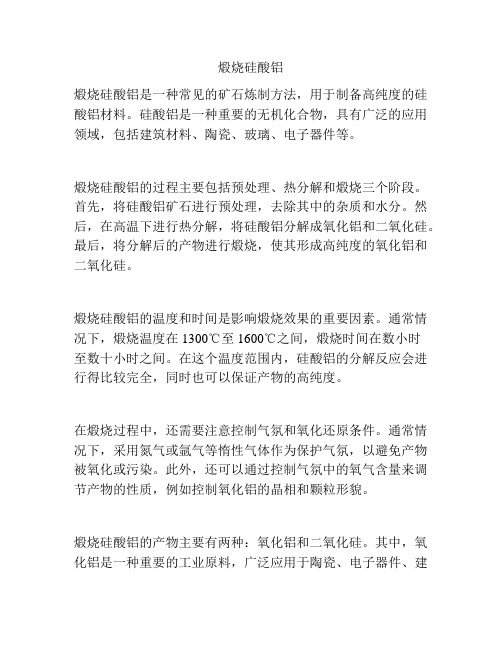
煅烧硅酸铝煅烧硅酸铝是一种常见的矿石炼制方法,用于制备高纯度的硅酸铝材料。
硅酸铝是一种重要的无机化合物,具有广泛的应用领域,包括建筑材料、陶瓷、玻璃、电子器件等。
煅烧硅酸铝的过程主要包括预处理、热分解和煅烧三个阶段。
首先,将硅酸铝矿石进行预处理,去除其中的杂质和水分。
然后,在高温下进行热分解,将硅酸铝分解成氧化铝和二氧化硅。
最后,将分解后的产物进行煅烧,使其形成高纯度的氧化铝和二氧化硅。
煅烧硅酸铝的温度和时间是影响煅烧效果的重要因素。
通常情况下,煅烧温度在1300℃至1600℃之间,煅烧时间在数小时至数十小时之间。
在这个温度范围内,硅酸铝的分解反应会进行得比较完全,同时也可以保证产物的高纯度。
在煅烧过程中,还需要注意控制气氛和氧化还原条件。
通常情况下,采用氮气或氩气等惰性气体作为保护气氛,以避免产物被氧化或污染。
此外,还可以通过控制气氛中的氧气含量来调节产物的性质,例如控制氧化铝的晶相和颗粒形貌。
煅烧硅酸铝的产物主要有两种:氧化铝和二氧化硅。
其中,氧化铝是一种重要的工业原料,广泛应用于陶瓷、电子器件、建筑材料等领域。
它具有高的绝缘性能、耐高温性能和化学稳定性,是制备高性能陶瓷和电子器件的重要材料。
而二氧化硅则主要应用于玻璃、光纤、半导体等领域,具有优良的光学性能和导电性能。
总之,煅烧硅酸铝是一种重要的工艺方法,用于制备高纯度的氧化铝和二氧化硅材料。
通过控制煅烧条件和气氛,可以得到具有不同性能和形貌的产物,满足不同领域的需求。
随着科技的不断发展,对于高性能材料的需求也越来越大,因此研究和改进煅烧硅酸铝的工艺方法具有重要意义。
- 1、下载文档前请自行甄别文档内容的完整性,平台不提供额外的编辑、内容补充、找答案等附加服务。
- 2、"仅部分预览"的文档,不可在线预览部分如存在完整性等问题,可反馈申请退款(可完整预览的文档不适用该条件!)。
- 3、如文档侵犯您的权益,请联系客服反馈,我们会尽快为您处理(人工客服工作时间:9:00-18:30)。
煅烧高硅、高铝料的操作、调整方法从硅酸盐物理化学角度讨论飞砂的成因。
飞砂产生与否主要取决于熟料液相量和液相性质(主要是表面张力)。
飞砂有两类:一类是熟料液相量太少而产生;另一类是粘散料,由于液相表面张力太小所致。
碱、硫和MgO等微组分含量高能使液相表面张力降低,特别是碱和硫酸盐含量高将使液相表面张力降低更明显。
所谓飞砂是回转窑烧成带产生大量细粒并飞扬的熟料。
这种飞砂料的大小一般在1mm以下,在窑内到处飞扬。
飞砂料的出现,既影响熟料质量,又影响窑的操作。
据报导,大同水泥厂曾因飞砂料的出现被迫降低煅烧温度,从而使熟料强度下降5MPa。
关于飞砂的成因,主要是SiO2含量太高、Al2O3和Fe2O3含量太低,因而液相出现太慢、液相量太少,熟料难以结粒,导致飞砂;另一原因是火焰太长,煅烧温度不够高,在料层中还存在大量不飞扬的料粒,未能结粒,待物料进入冷却带,细料粒才到处飞扬。
克服飞砂的方法,若是由于SiO2太高引起则应适当降低硅酸率;若是由于煅烧操作中火焰太长而引起,则应适当缩短火焰或缩短高温带。
笔者认为,还有一种飞砂是由于粘散料引起,而粘散料的产生则是由于高温液相的表面张力太小所致。
乔龄山在分析飞砂形成机理时认为,“国内水泥生产者忽视了液相表面张力和结粒的问题”他还指出:“硫酸盐饱和度过高降低了液相粘度和表面张力”。
他所提出的表面张力太小形成的飞砂实际上是一种粘散料,这种飞砂的产生与液相量少所引起的飞砂在机理上完全不同。
因此,解决这种飞砂的措施也应该完全有别于液相量少所产生的飞砂。
本文在前人研究工作的基础上从硅酸盐物理化学角度讨论飞砂的成因并提出预防和解决飞砂问题的措施或途径。
1 回转窑内物料结粒的机理从水泥工艺学原理看,水泥熟料是一种多矿物的集合体,是结晶细小的人造岩石。
这些结晶一般都在100μm以下,即小于0.1mm。
有人认为,水泥熟料中矿物晶体的平均尺寸为:阿利特65μm以下,贝利特55μm以下。
出冷却机的熟料块度一般都在5~25mm,甚至更大些,是什么力量使几十微米的小晶体“粘结”成几毫米至几十毫米的熟料?答案是熟料液相,是熟料液相将这些细小的晶体“粘结”起来。
因此,熟料液相的数量和性质对熟料的结粒大小起着关键作用。
液相的什么性质使它对小晶体有粘结力?主要是表面张力。
水泥熟料的烧结是在有液相的情况下进行的。
在固相反应之前,物料呈粉状。
在过渡带主要是固相反应,生料中的CaO与SiO2、Al2O3、Fe2O3起化学反应生成C2S、C3A和C4AF,此外尚有一部分未起化学反应的CaO(约12%~13%),物料呈细粒状或粉状。
到了烧成带,随着煅烧温度提高,开始出现液相,其液相量大约在20%~28%。
在水泥熟料烧结过程中,液相有2种作用:一是为C2S+CaO→C3S的反应提供条件,使C2S和CaO溶于液相起化学反应,生成C3S;另一作用是像“胶结剂”一样,润湿窑内物料,从而使出窑熟料块度远远大于入窑物料的粒度。
从硅酸盐物理化学角度看,物料烧结的主要动力是粒子的表面张力。
物料烧结一种是固相与固相之间的烧结;另一种是有液相或汽相情况下的烧结。
我们首先讨论有液相而不存在化学反应情况下的烧结。
粒子拉紧的毛细管力主要有2部分:一是沿液相弯曲表面的2个方向上的压力差引起的力ΔP=σ(1/ρ2-1/ρ1),式中σ和ρ2、ρ1分别为液相弯曲面上的表面张力和半径,液相内部的压力比外部的小,颗粒在力的作用下受到压紧作用,其作用力F1=ΔP•S,式中S 为液相与固体界面压力的垂直方向的投影面积,即粒子之间的凹桥强度与液相表面张力及粒子的直径成正比;另一作用力是沿液相与固体接触的周长,由液相表面张力引起的力F2。
F2=Cσsin(ψ+θ),C表示湿润周长;ψ表示取决于液相量的角;θ表示湿润边界角。
拉紧颗粒的总力为F=F1+F2。
从上面的公式可看出,这2种拉紧颗粒的力都与表面张力成正比。
另外,存在着将2个颗粒分开的外力,此力与颗粒的质量P即与颗粒直径的三次方成正比,因此由表面张力粘结而成的颗粒强度与液相表面张力成正比,而与粒径成反比。
即最终团粒的大小取决于表面张力和粒径大小。
当颗粒尺寸因粘结而大到一定程度时,颗粒不再增大。
在水泥熟料煅烧过程中,若液相包围的是化学成分相同的2个粒子,则这2个粒子只能靠冷却时液相的凝固而把它们连接起来。
不过,在熟料颗粒生长时,2个化学成分不同的粒子如C2S 和CaO,则表面张力的粘结可为结晶所代替。
因为C2S和CaO 通过溶解扩散进行化学反应而结晶出C3S,粒子由固相连接,使液相连接由固相连接所代替。
如果这2个粒子间没有或有很少液相,若煅烧温度足够高,则也可在粒子内的接触处形成C3S。
但由于没有液相,这些晶体只能靠堆积作用与其它C3S相结合,它们通过表面的相互接触而吸引在一起,因此易产生粉状物料。
在生产中,若SM太高,液相量太少,则缺乏足够的液相将C2S和CaO相连或润湿,或IM太高,液相大量出现太迟,就易产生粉状物料,即飞砂现象。
2 飞砂产生的原因2.1 液相量不足是飞砂的主要原因从上面的讨论可以看出,产生飞砂主要是液相量太少的缘故。
物料在烧成带停留的时间很短,预分解窑约10~15min,湿法窑最长也不过25~30min。
若没有液相,C2S和CaO粒子通过固相反应长大至1mm以上是十分困难的。
其结果是,这些细粒子随窑内气体悬浮并被气体带走,即所谓飞砂。
飞砂料的CaO含量高,其硅酸率达3.31,说明飞砂料中液相很少,即飞砂是由液相量不足引起。
液相量太大,熟料易结大块,这是众所周知的事实。
反过来说,液相量少则熟料结粒小,液相量太少则熟料结粒太小,则产生飞砂。
铝率太高,液相量随温度提高而增加的速度太慢,也易产生飞砂。
还原气氛使Fe2O3变成FeO,也使液相量减少,从而产生飞砂。
很多人认为过渡带长是飞砂的原因。
,过渡带长只是现象,其根本原因在于液相量少,或液相量增加的速度太慢,不能及时产生足够的液相将C2S和C3S等晶体连结在一起或通过化学反应生成C3S而连结在一起,因此产生飞砂。
2.2 表面张力太小是产生粘散料飞砂的原因粘散料的特点是烧成带物料过粘,成片状下塌滑动,很少滚动,难以结粒,产生大量飞砂。
液相表面张力太小是粘散料产生的主要原因。
根据V•V•提姆阿瑟夫[5]的计算,熟料平均粒径与表面张力有一个近乎线性的关系,表面张力每减少0.1N/m,熟料粒度减小10mm。
当硫酸盐化程度从67%增大至140%时(硫酸盐含量从1.4%增加到2.3%),熟料d50从6mm下降至1.5mm。
根据提姆阿瑟夫的测定,硫酸盐化程度从67%增加至140%时,液相表面张力减少0.05N/m,也就是说,表面张力减少0.05N/m,熟料粒径从6mm下降至1.5mm,粒度减少了4.5mm。
据此可以认为,液相表面张力太小,会使熟料粒度变细,从而产生飞砂。
熟料含有镁、碱和硫中任何一种时,都会降低液相表面张力。
当MgO含量增加1%时,表面张力降低0.019N/m,含4%MgO时的表面张力为0.51N/m。
Na2O、K2O和SO3在熔融物中含量小于2%时,表面张力降低最剧烈。
当分别加入2%的Na2O、K2O和SO3时,1450℃饱和熔融物表面张力从0.58N/m相应降低至0.46N/m、0.35N/m和0.36N/m。
当继续增加这些氧化物浓度达4%时,表面张力分别降低至0.40N/m、0.320N/m和0.333N/m。
而纯的Na2O和K2O的表面张力约为0.275N/m和0.150N/m。
因此,在熟料中含有较多的碱和硫时,液相表面张力大幅度下降,熟料结粒细小,飞砂严重。
淮海水泥厂发现,当入窑生料中R2O大于1.0%时,物料难以结粒,大量飞砂产生。
大同水泥厂的生料R2O>1.2%时,飞砂频繁出现;当窑灰入窑量增加时,易出现飞砂。
这2种情况均是由于碱含量大,使液相表面张力降低引起的。
因为窑灰中碱含量比生料的高,窑灰入窑量增加就意味着增加碱含量。
珠江水泥厂原来控制LSF=94、SM=2.4、IM=1.5,窑的操作较好,熟料质量高,后来希望再进一步提高熟料质量而将LSF提高到96(SM和IM不变),结果窑煅烧状况较差,飞砂很大,窑口积“雪人”,三次风管沉降室堵塞,而熟料质量未见升高反而下降。
SM和IM保持不变,意味着液相量并不减少,为什么仅提高LSF就产生飞砂,可能是LSF提高迫使提高煅烧温度。
煅烧温度提高,液相量应增加,表面张力的温度系数为负值,温度每提高1℃,表面张力下降2.3×10-4N/m。
若提高煅烧温度50℃,表面张力将下降0.0115N/m。
大同水泥厂曾采用降低煅烧温度的方法减少飞砂,收到成效。
降低煅烧温度其实质是增大液相表面张力,从而使结粒变大。
3 避免飞砂的措施3.1 配料方案必须与煅烧温度相适应液相量太少和液相量的大量出现太迟是飞砂的主要原因,因此保持适当的液相量是避免飞砂的主要措施。
由于液相量与熟料的化学成分和煅烧温度有关,合理的配料方案和合适的煅烧温度是十分必要的。
从配料方案来看,反映液相量的率值主要是硅酸率,而液相量随温度而增加的速度与铝率有关。
硅酸率太高则液相量太少,铝率太高则液相随温度提高增加速度慢,即液相大量出现的时间迟。
煅烧温度高,则液相量增大,反之降低煅烧温度则液相量减少。
因此配料方案必须与熟料煅烧温度相适应。
如果熟料煅烧温度高,则硅酸率可高些,铝率也可高些;反之则不能。
例如,国内大型预分解窑熟料硅酸率一般都在2.5以上,但对某些小型旋风预热器窑,2.5的硅酸率可能偏高。
某一600t/d的五级旋风预热器窑所用的燃煤与某大型预分解窑的相同,当硅酸率为2.5时,飞砂严重,后来将硅酸率降低至2.3左右,熟料煅烧正常,强度达64MPa,产量也达到设计指标。
在这里要指出2个问题,一是不同窑型煅烧温度可能不同。
一般说来,大型预分解窑内煅烧温度高,旋风预热器窑煅烧温度比预分解窑低,但比湿法窑或干法中空窑的高些。
因此,配料方案必须根据窑型和窑径大小而异。
其次,煅烧温度与火焰温度和火焰形状有关。
而影响火焰温度的主要因素有煤粉的质量(发热量、水分和细度)以及一、二次风温,特别是二次风温的高低以及一、二次风的比例。
一般说来,煤的发热量高,煤粉的细度细,水分少,二次风温高且用量大,则火焰温度高。
就相同质量的煤粉而言,使用三通道喷煤管由于一次风比例小,二次风比例大,火焰粗短,其火焰温度比单通道喷煤管的火焰温度高。
另外,由于结构的原因,三通道喷煤管使煤粉的燃烧状况比单通道喷煤管要好,火焰粗短。
此外用篦冷机冷却熟料时二次风温比单筒和多筒冷却机的高。
还有一点,就是考虑硅酸率时,必须考虑一些微组分如MgO、R2O 和SO3的影响,因为这些微组分都会在烧成过程中以液相出现,增加液相量并影响液相粘度以及液相表面张力。