高炉炼铁工艺.ppt
合集下载
高炉炼铁安全ppt课件

四、炼铁常见事故分析及预防
2、物体打击 大锤、榔头使用不当;高处物件坠落;清理渣铁壕、板结 物料时发生崩块击中人员,尤其是眼睛;使用卡机卸风口、中 套时突然断裂,游锤飞出击打伤人。 此类事故的预防目前主要以软措施为主,如做好工器具的检查 确认、制定科学的安全防范措施和作业标准、尽量减少作业时 间与频次等。有条件的,可以自动化的机械设备(如使用挖掘 机进行渣铁壕解体,使用专用装置更换风口等)代替人工操作 或将人员的操作控制设置在远端进行计算机控制,从空间上实 现人机分离,但需要先进的技术与生产力做后盾。
并 罐 式 无 钟 炉 顶
串 罐 式 无 钟 炉 顶
一、炼铁厂除高炉本体外的几个系统
• 3.送风系统 主要包括高炉鼓风机和热风炉(含助燃风机、 冷风管道、热风管道、煤气管道、助燃空气管 道、烟气管道和烟囱等)。
• 4.煤气除尘系统 一般包括煤气上升管、煤气下降管、重力除 尘器(或旋风除尘器)、洗涤塔、文氏管、脱 水器等。高压操作的高炉还有高压阀组。
二、炼铁生产的主要危险因素
• 炼铁生产工艺设备复杂、作业种类多、 作业环境差,劳动强度大。 • 炼铁生产过程中存在的主要危险因素有: • 高温辐射、铁水和熔渣喷溅与爆炸、高 炉煤气中毒、高炉煤气燃烧爆炸、煤粉 爆炸、烟尘、噪声、机具及车辆伤害、 高处作业危险等。
三、炼铁生产的主要事故类别和 原因
熔剂、燃料等 球磨机高炉来自炼工艺流程图焦碳
混合机
石灰石 选 球 盘 除 尘 器
洗 涤 塔
天然矿
竖
文 氏 管
脱 水 器
炉
带 冷
除 尘 器
料
仓
烟
助 燃 风
高 炉
囱 热 风
热 风 炉
球磨机 鼓 风 机 集 煤 罐 贮 煤 罐 喷 吹 罐
高炉炼铁工艺流程(简介) PPT

C CC R GP
BB B PG R
CCC RGP
BB B PG R
C
A
B
H
C
A
B
H
C
A
B
H
C
A
B
H
燃
B
B
B
F
B
B
B
B
B
B
B
B
B
烧
a
室
n
蓄
1
热
混
F
室
风
a n
室
热
2
B
M
B
M
B
M
B
M
风
总
热管
风
S t
4H S
H
3H S
H
2H S
H
1H S
H
阀
a c
BF 空 CO G 气 G 冷风阀
k
W
.
SW
S
SW
S
SW
S
混合器
N2
加压、流化气
高炉概况和工艺流程
项目
DC 1VS 2VS
处理煤气量 (m3/h) 700000 700000 700000
进口粉尘浓度 (g/m3) 13.5
5
0.1
出口粉尘浓度 (mg/m3) 5000
100
<10
TRT是 炉煤气余压透平发电
高炉节能回收重要措施,工
是通过高炉的高压并带有预
THANK YOU
柱,能储存一定量的渣、铁。 ⑵适应炉料下降和煤气上升的规律,减少炉料下降和煤气上升的阻
力,为顺行创造条件,有效的利用煤气的热能化学能,降低燃耗。 ⑶易于生成保护性的渣皮,有利于延长炉衬的寿命。
高炉炼铁概述PPT课件

过程
①还原过程 实现矿石中金属元素(主要是Fe)和氧 元素的化学分离; ② 造渣过程 实现已还原的金属与脉石的熔融态机械 分离; ③ 传热及渣铁反应过程 实现成分及温度均合格的液态铁水。
23
1. 1高炉原料
高炉原料
—高炉炼铁—
铁矿石
熔剂
其它含铁代用品
天然块矿 人造富矿
烧结矿 球团矿
碱性熔剂―石灰, 石灰石,白云石 酸性熔剂― 硅石 特殊熔剂― 萤石
4
1.1钢铁工业概况
—高炉炼铁—
1.1.1国民经济中钢铁工业的地位
评价一个国家的工业发达程度
工业化水平
工业生产所占比重
工业机械化、 自动化程度
工业化水平的标志
劳动生产率↑ 需要大量机械设备
国民生活水准
交
市
民
生
通
政
用
活
工
设
住
用
具
施
宅
品
需要大量基础材料
钢铁产品
5
➢价格低廉有较高的强度和韧性 ➢易于加工制造 ➢所需原料资源丰富 ➢ 冶炼工艺成熟、效率高
13 、修风率
定义:高炉修风时间占规定作业时间的百分数。
14、炉龄
定义:从高炉点火开炉到停炉大修,或高炉相邻两次
的大修之间的冶炼时间。
34
第一章 思考题
—高炉炼铁—
1、试述3种钢铁生产工艺的特点。 2、简述高炉冶炼过程的特点及三大主要过程。 3、画出高炉本体图,并在其图上标明四大系统。 4、归纳高炉炼铁对铁矿石的质量要求。 5、试述焦炭在高炉炼铁中的三大作用及其质量要求。 6、试述高炉喷吹用煤粉的质量要求。 7、熟练掌握高炉冶炼主要技术经济指标的表达方式。
①还原过程 实现矿石中金属元素(主要是Fe)和氧 元素的化学分离; ② 造渣过程 实现已还原的金属与脉石的熔融态机械 分离; ③ 传热及渣铁反应过程 实现成分及温度均合格的液态铁水。
23
1. 1高炉原料
高炉原料
—高炉炼铁—
铁矿石
熔剂
其它含铁代用品
天然块矿 人造富矿
烧结矿 球团矿
碱性熔剂―石灰, 石灰石,白云石 酸性熔剂― 硅石 特殊熔剂― 萤石
4
1.1钢铁工业概况
—高炉炼铁—
1.1.1国民经济中钢铁工业的地位
评价一个国家的工业发达程度
工业化水平
工业生产所占比重
工业机械化、 自动化程度
工业化水平的标志
劳动生产率↑ 需要大量机械设备
国民生活水准
交
市
民
生
通
政
用
活
工
设
住
用
具
施
宅
品
需要大量基础材料
钢铁产品
5
➢价格低廉有较高的强度和韧性 ➢易于加工制造 ➢所需原料资源丰富 ➢ 冶炼工艺成熟、效率高
13 、修风率
定义:高炉修风时间占规定作业时间的百分数。
14、炉龄
定义:从高炉点火开炉到停炉大修,或高炉相邻两次
的大修之间的冶炼时间。
34
第一章 思考题
—高炉炼铁—
1、试述3种钢铁生产工艺的特点。 2、简述高炉冶炼过程的特点及三大主要过程。 3、画出高炉本体图,并在其图上标明四大系统。 4、归纳高炉炼铁对铁矿石的质量要求。 5、试述焦炭在高炉炼铁中的三大作用及其质量要求。 6、试述高炉喷吹用煤粉的质量要求。 7、熟练掌握高炉冶炼主要技术经济指标的表达方式。
高炉炼铁工艺介绍.ppt

炉喉板等。 • ⑷ 造渣制度的调整: • 炉渣性能:流动性,熔化性(长渣和短渣),稳定性,脱硫能力等。 • 炉渣性能的调整:碱度(二元,三元,四元),加MgO(适应高AI2O3量),
低碱度排碱金属,提高脱硫能力等。
七、与高炉密切相关的几个系统
• 1、上料系统:包括料场、矿槽、振动筛、 称量漏斗、上料皮带机。本系统的任务是 将原、燃料运到炉顶按料单装入受料漏斗。
从出铁口放出,铁矿石中的脉石、焦炭 及喷吹物中的灰分与加入炉内的石灰石 等熔剂结合生成炉渣,从出铁口和出渣 口排出。
4、煤气从炉顶导出,经除尘后,作 为工业用煤气
二、高炉内型结构
1、炉喉
• 炉喉是炉料进高炉的装入口,也是煤气的 导出口,对炉料和煤气分布起控制和调节 作用
2、炉身
• 炉料在炉身预热和预还原,炉身直径自上 而下逐渐扩大以适应炉料受热膨胀和减少 炉料与炉强之间的摩擦力,
• (2)矿石的粒度。相同质量的矿石,粒度越小与煤气的接触面积则 越大,煤气的用程度越好。
• (3)煤气温度。随着温度升高不论是界面化学反应还是扩散速度均 是加快的,同时在高温下活化分子数目增加,促进还原反应进行。
• (4)煤气压力。提高煤气压力使气体密度加大,增加了单位时间内 与矿石表面碰撞的还原剂的分子数,从而加快还原反应。
2、上部装入的铁矿石、燃料和熔剂在重力作用下
向下运动,从高炉下部的风口吹进热风(1000~ 1300℃),喷入油、煤或天然气等燃料,燃料燃烧 产生大量高温还原性气体向上运动,炉料经过加热、
还原、熔化、造渣、渗碳、脱硫等一系列物理化学 过程,最后生成液态炉渣和生铁
3、还原反应生成的铁汇聚到炉缸定期
1、块状带
• 炉内料柱的上部,矿石与焦炭始终保持明 显的固态的层次缓慢下降,但层状逐渐趋 于水平,而且厚度也逐渐变薄
低碱度排碱金属,提高脱硫能力等。
七、与高炉密切相关的几个系统
• 1、上料系统:包括料场、矿槽、振动筛、 称量漏斗、上料皮带机。本系统的任务是 将原、燃料运到炉顶按料单装入受料漏斗。
从出铁口放出,铁矿石中的脉石、焦炭 及喷吹物中的灰分与加入炉内的石灰石 等熔剂结合生成炉渣,从出铁口和出渣 口排出。
4、煤气从炉顶导出,经除尘后,作 为工业用煤气
二、高炉内型结构
1、炉喉
• 炉喉是炉料进高炉的装入口,也是煤气的 导出口,对炉料和煤气分布起控制和调节 作用
2、炉身
• 炉料在炉身预热和预还原,炉身直径自上 而下逐渐扩大以适应炉料受热膨胀和减少 炉料与炉强之间的摩擦力,
• (2)矿石的粒度。相同质量的矿石,粒度越小与煤气的接触面积则 越大,煤气的用程度越好。
• (3)煤气温度。随着温度升高不论是界面化学反应还是扩散速度均 是加快的,同时在高温下活化分子数目增加,促进还原反应进行。
• (4)煤气压力。提高煤气压力使气体密度加大,增加了单位时间内 与矿石表面碰撞的还原剂的分子数,从而加快还原反应。
2、上部装入的铁矿石、燃料和熔剂在重力作用下
向下运动,从高炉下部的风口吹进热风(1000~ 1300℃),喷入油、煤或天然气等燃料,燃料燃烧 产生大量高温还原性气体向上运动,炉料经过加热、
还原、熔化、造渣、渗碳、脱硫等一系列物理化学 过程,最后生成液态炉渣和生铁
3、还原反应生成的铁汇聚到炉缸定期
1、块状带
• 炉内料柱的上部,矿石与焦炭始终保持明 显的固态的层次缓慢下降,但层状逐渐趋 于水平,而且厚度也逐渐变薄
高炉炼铁简述PPT课件.ppt

火灾袭来时要迅速疏散逃生,不可蜂 拥而出 或留恋 财物, 要当机 立断, 披上浸 湿的衣 服或裹 上湿毛 毯、湿 被褥勇 敢地冲 出去
构建高效率、低消耗、低成本、低排放生产体系
LOREM
高效IPS低U耗M
DOLOR
LOREM
节IP能S减UM排
DOLOR
L循O环RE经M IPS济UM
DOLOR
低碳冶炼
2.高炉本体及主要构成
密闭的高炉本体是冶炼生铁的主 体设备。它是由耐火材料砌筑成 竖式圆筒形,外有钢板炉壳加固 密封,内嵌冷却设备保护。
高炉内部工作空间的形状称为高 炉内型从自上而下分为炉喉、炉 身、炉腰、炉腹、炉缸五个部分 。该容积总和为它的有效容积, 反应高炉多具备的生产能力。
5
hf
火灾袭来时要迅速疏散逃生,不可蜂 拥而出 或留恋 财物, 要当机 立断, 披上浸 湿的衣 服或裹 上湿毛 毯、湿 被褥勇 敢地冲 出去
火灾袭来时要迅速疏散逃生,不可蜂 拥而出 或留恋 财物, 要当机 立断, 披上浸 湿的衣 服或裹 上湿毛 毯、湿 被褥勇 敢地冲 出去
9/27/2024
火灾袭来时要迅速疏散逃生,不可蜂 拥而出 或留恋 财物, 要当机 立断, 披上浸 湿的衣 服或裹 上湿毛 毯、湿 被褥勇 敢地冲 出去
4号高炉炉容4350 m3 在4号高炉的设计过程 中,采用了41项新技 术。主要有:紧凑的 总图布局、旋转布料 器加固定料罐的串罐 中心卸料式无料钟、 炉缸高挂渣性能的热 压小炭砖耐材、冷却 壁与冷却壁板结合的 全炉身冷却型式、国 内集成的喷煤技术、 新英巴法转鼓水渣处 理工艺、环缝洗涤煤 气统、平坦化出铁场
火灾袭来时要迅速疏散逃生,不可蜂 拥而出 或留恋 财物, 要当机 立断, 披上浸 湿的衣 服或裹 上湿毛 毯、湿 被褥勇 敢地冲 出去
现代高炉炼铁工艺-PPT

1. 现代高炉炼铁工艺
1.1 高炉炼铁生产流程 1.2 高炉本体及主要构成 1.3 高炉冶炼产品 1.4 高炉技术经济指标
1
1.1 高炉炼铁工艺流程
1.1.1高炉冶炼工艺流程
1、工艺原理
高炉是一个密闭的连续的逆流反
应器。炉料充满整个高炉空间,形成
料柱.原燃料从炉顶装入,高温热空
气从下部鼓入;产生的高温还原性气
16
(3)冷却设备
炉衬的温度状态是决定其侵蚀速度的重要因素 之一,冷却设备保护耐火砖衬的工作表面温度低于 其允许的温度,使其不因受热变形而被坏。强大的 冷却还可在高炉下部形成渣皮,代替炉衬工作;
根据高炉各部位热负荷及结构的不同,高炉冷却 可采取多种形式和方法.
17
18
19
高炉安装的铜冷却壁
20
利用特殊矿或采用特殊的冶炼工艺,利用高炉
可以生产出含钛、钒的铁水,以及锰铁、硅铁等
铁合金。
78
2、高炉渣
炉渣主要成分有:CaO、SiO2、Al2O3、MgO。 其中炉渣碱度:CaO/SiO2 =1.05-1.25。
3、高炉煤气
每冶炼一吨铁产生1800m3左右的煤气,煤气 中含有CO20%~25%,是钢铁企业重要的二次能 源。
与湿式除尘技术相比,干式除尘具有以下优 点:
(1)提高煤气净化程度;
(2)降低新水消耗和动力消耗;
(3)由于煤气温度高不含水,可提高煤气余 压发电量(增加30% )和二次能源(煤气温度 高100℃)利用效率。
57
缺点: (1)对温度比较敏感,煤气温度过高,
过低都不行; (2)设备多,运行后维护量大,由十几
4、炉尘(又称瓦斯灰)
被煤气携带出炉外的粉状炉料,称为炉尘(约 20kg/t铁),可回收作为烧结原料。
1.1 高炉炼铁生产流程 1.2 高炉本体及主要构成 1.3 高炉冶炼产品 1.4 高炉技术经济指标
1
1.1 高炉炼铁工艺流程
1.1.1高炉冶炼工艺流程
1、工艺原理
高炉是一个密闭的连续的逆流反
应器。炉料充满整个高炉空间,形成
料柱.原燃料从炉顶装入,高温热空
气从下部鼓入;产生的高温还原性气
16
(3)冷却设备
炉衬的温度状态是决定其侵蚀速度的重要因素 之一,冷却设备保护耐火砖衬的工作表面温度低于 其允许的温度,使其不因受热变形而被坏。强大的 冷却还可在高炉下部形成渣皮,代替炉衬工作;
根据高炉各部位热负荷及结构的不同,高炉冷却 可采取多种形式和方法.
17
18
19
高炉安装的铜冷却壁
20
利用特殊矿或采用特殊的冶炼工艺,利用高炉
可以生产出含钛、钒的铁水,以及锰铁、硅铁等
铁合金。
78
2、高炉渣
炉渣主要成分有:CaO、SiO2、Al2O3、MgO。 其中炉渣碱度:CaO/SiO2 =1.05-1.25。
3、高炉煤气
每冶炼一吨铁产生1800m3左右的煤气,煤气 中含有CO20%~25%,是钢铁企业重要的二次能 源。
与湿式除尘技术相比,干式除尘具有以下优 点:
(1)提高煤气净化程度;
(2)降低新水消耗和动力消耗;
(3)由于煤气温度高不含水,可提高煤气余 压发电量(增加30% )和二次能源(煤气温度 高100℃)利用效率。
57
缺点: (1)对温度比较敏感,煤气温度过高,
过低都不行; (2)设备多,运行后维护量大,由十几
4、炉尘(又称瓦斯灰)
被煤气携带出炉外的粉状炉料,称为炉尘(约 20kg/t铁),可回收作为烧结原料。
高炉炼铁工艺资料课件

送风
向高炉内鼓入热风,提供 反应所需氧气。
高炉炼铁的工艺流程
01
02
燃烧
焦炭与氧气发生燃烧反应,产 生高温和还原性气体。
渣铁分离
高温下矿石熔化,渣铁分离, 生铁从炉缸排出。
03
排渣
将炉渣排出高炉。
04
回收利用
回收高温气体和余热,降低能 耗。
02
高炉设备与操作
高炉的结构与设计
要点一
和产 品质量有着重要影响。
高炉的操作与管理
总结词
高炉操作涉及众多工艺参数的调控,包括原料供应、送风、渣铁处理等,需要经验丰富 的操作人员。
详细描述
高炉操作的核心是控制好原料供应的配比和品质,以及送风的温度和压力。根据高炉的 工艺要求和产品需求,操作人员需不断调整各项参数,如焦炭加入量、矿石配比、送风 温度等,以保证高炉的稳定运行和高效生产。同时,渣铁处理也是高炉操作的重要环节
要点二
详细描述
高炉的结构通常包括炉缸、炉身、炉腹、炉腰和炉喉等部 分,各部分的设计需满足不同的工艺要求。炉缸是铁水的 产出地,要求有良好的保温性和耐火材料;炉身用于容纳 和加热铁矿石和焦炭,设计时应考虑传热效率和气体流动 ;炉腹、炉腰和炉喉则是根据不同冶炼阶段的需要,调整 矿石和焦炭的分布和加热方式。
高炉炼铁工艺资料课件
目录 Contents
• 高炉炼铁工艺简介 • 高炉设备与操作 • 原料与燃料 • 炼铁过程中的化学反应 • 环境保护与可持续发展
01
高炉炼铁工艺简介
高炉炼铁的定义与重要性
定义
高炉炼铁是一种将铁矿石还原成 液态生铁的工艺过程。
重要性
高炉炼铁是现代钢铁工业的基础 ,为各行业提供大量优质钢材。
高炉炼铁生产工艺 PPT
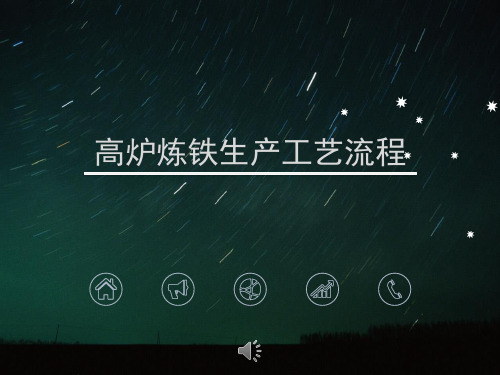
熔结层中砖与砖已烧结成一个整体,能抵抗铁水 的渗入,并且坑底面的铁水温度也较低,砖缝已 不再是铁水渗入的薄弱环节,这时炉衬损坏的主 要原因转化为铁水中的碳将砖中二氧化硅还原成 硅,并被铁水所吸收的化学侵蚀。 生产实践表明:采用炉底冷却的大高炉炉底侵蚀 深度约1~2m,而没有炉底冷却的高炉侵蚀深度 可达4~5m。 从炉底破损机理看出,影响炉底寿命的因素:首 先是它承受的高压,其次是高温,再次是铁水和 渣水在出铁时的流动对炉底的冲刷,炉底的砖衬 在加热过程中产生温度应力引起砖层开裂,此外 在高温下渣铁也对砖衬有化学侵蚀作用,特别是 渣液的侵蚀更为严重。
②软熔带: 炉料由开始软化到软化终了的区域。此区域是由 许多固态焦炭层和粘结在一起的半熔融的矿石层 组成,焦炭与矿石相间层次分明。由于矿石呈软 熔状透气性极差,上升的煤气流主要从像窗口一 样的焦炭层通过,因此又称其为“焦窗”。软熔 带的上缘是软化线,即矿石开始软化的温度;下 缘是熔化线,即矿石熔化的温度,它和矿石的软 熔温度区间相一致;其最高部位称为软熔带顶部, 其最低部位与炉墙相连接,称为软熔带的根部。 ③滴落带: 矿石熔化后呈液滴状滴落的区域,它位于软熔带 之下,矿石熔化后形成的渣铁像雨滴一样穿过固 态焦炭层而滴落进入炉缸。
五段式高炉内型如下图。
(2)高炉冶炼的基本过程 高炉生产过程就是将铁矿石在高温下冶炼成生铁 的过程。全过程是在炉料自上而下、煤气自下而 上的运动、相互接触过程中完成的。 高炉生产所用的原料是含铁的矿石包括烧结矿、 球团矿和天然富矿石;燃料主要是焦炭;辅助原 料为熔剂和洗炉剂等。通过上料系统和炉顶装料 系统按一定料批、装入顺序从炉顶装入炉内,从 风口鼓入经热风炉加热到1000~1300℃的热风, 炉料中的焦炭在风口前与鼓入热风中的氧发生燃 烧反应,产生高温和还原性气体,这些还原性气 体在上升过程中加热缓慢下行的炉料,并将铁矿 石中的铁氧化物还原成为金属铁
高炉炼铁工艺流程及主要设备简介 ppt课件

13
三、高炉冶炼主要设备简介
受料斗主 要包括: 受料斗篦 子、受料 斗衬板; 受料斗的 最大容积:
16m³
14
三、高炉冶炼主要设备简介
挡料阀
上密阀
料罐
挡料阀(瓜皮 阀):φ650; 料罐及上密封 阀:φ700, 料罐最大容积
16m³
15
三、高炉冶炼主要设备简介
节流阀(料流 阀:φ600 1、外径: Ф1200 mm 2、孔距: Ф1120mm 内径: Ф400mm
下密接近开关
16
三、高炉冶炼主要设备简介
气密箱(布料器) 喉管通径:
500mm; 倾 动速度:
0~8°/s; 溜槽旋转速度:
9.8r/min; 公称压力:
0.2MPa 正常控制温度:
≤70℃ 冷却水压力:
0.2MPa
17
三、高炉冶炼主要设备简介
溜槽:L=1600
18
三、高炉冶炼主要设备简介
19
4
一、高炉炼铁工艺流程详解
5
炼铁工艺流程图
烧结料 球团料 焦炭 杂品
上料皮带机 振筛
槽下振筛
中
料仓
皮带机
间 仓
铁包 铁路 炼钢
铁 水 沟
渣铁 分离器
铁水大沟
料车
高炉
渣 沟
冲渣水管道
渣沟
供回 水水 管管 道道
净环水泵房
冷却塔
鼓风机
热风炉
助燃风机
煤气外网管道
重力 除尘
布袋 除尘
调压阀组 TRT发电
渣池 水渣场
35
三、高炉冶炼主要设备简介
上图为槽下翻板 筛分合格的原料经皮带运输到翻板,经翻板中间仓下料口放料至 料车中。
三、高炉冶炼主要设备简介
受料斗主 要包括: 受料斗篦 子、受料 斗衬板; 受料斗的 最大容积:
16m³
14
三、高炉冶炼主要设备简介
挡料阀
上密阀
料罐
挡料阀(瓜皮 阀):φ650; 料罐及上密封 阀:φ700, 料罐最大容积
16m³
15
三、高炉冶炼主要设备简介
节流阀(料流 阀:φ600 1、外径: Ф1200 mm 2、孔距: Ф1120mm 内径: Ф400mm
下密接近开关
16
三、高炉冶炼主要设备简介
气密箱(布料器) 喉管通径:
500mm; 倾 动速度:
0~8°/s; 溜槽旋转速度:
9.8r/min; 公称压力:
0.2MPa 正常控制温度:
≤70℃ 冷却水压力:
0.2MPa
17
三、高炉冶炼主要设备简介
溜槽:L=1600
18
三、高炉冶炼主要设备简介
19
4
一、高炉炼铁工艺流程详解
5
炼铁工艺流程图
烧结料 球团料 焦炭 杂品
上料皮带机 振筛
槽下振筛
中
料仓
皮带机
间 仓
铁包 铁路 炼钢
铁 水 沟
渣铁 分离器
铁水大沟
料车
高炉
渣 沟
冲渣水管道
渣沟
供回 水水 管管 道道
净环水泵房
冷却塔
鼓风机
热风炉
助燃风机
煤气外网管道
重力 除尘
布袋 除尘
调压阀组 TRT发电
渣池 水渣场
35
三、高炉冶炼主要设备简介
上图为槽下翻板 筛分合格的原料经皮带运输到翻板,经翻板中间仓下料口放料至 料车中。
高炉炼铁工艺流程与主要设备演示教学71页PPT
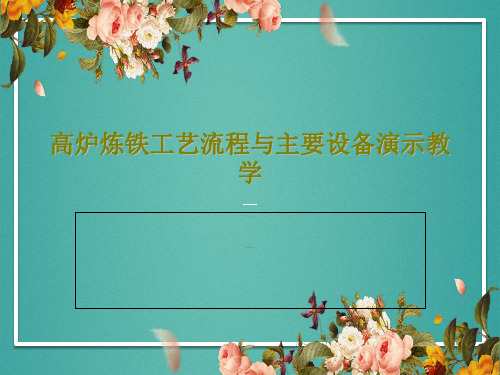
高炉炼铁工艺流程与主要设备演示教 学
1、 舟 遥 遥 以 轻飏, 风飘飘 而吹衣 。 2、 秋 菊 有 佳 色,裛 露掇其 英。 3、 日 月 掷 人 去,有 志不获 骋。 4、 未 言 心 相 醉,不 再接杯 酒。 5、 黄 发 垂 髫 ,并怡 然自乐 。
谢谢你的阅读
❖ 知识就是财富 ❖ 丰富你的人生
71、既然我已经踏上这条道路,那么,任何东西都不应妨碍我沿着这条路走下去。——康德 72、家庭成为快乐的种子在外也不致成为障碍物但在旅行之际却是夜间的伴侣。——西塞罗 73、坚持意志伟大的事业需要始终不渝的精神。——伏尔泰 74、路漫漫其修道远,吾将上下而求索。——屈原 75、内外相应,言行相称。——韩非
ቤተ መጻሕፍቲ ባይዱ
1、 舟 遥 遥 以 轻飏, 风飘飘 而吹衣 。 2、 秋 菊 有 佳 色,裛 露掇其 英。 3、 日 月 掷 人 去,有 志不获 骋。 4、 未 言 心 相 醉,不 再接杯 酒。 5、 黄 发 垂 髫 ,并怡 然自乐 。
谢谢你的阅读
❖ 知识就是财富 ❖ 丰富你的人生
71、既然我已经踏上这条道路,那么,任何东西都不应妨碍我沿着这条路走下去。——康德 72、家庭成为快乐的种子在外也不致成为障碍物但在旅行之际却是夜间的伴侣。——西塞罗 73、坚持意志伟大的事业需要始终不渝的精神。——伏尔泰 74、路漫漫其修道远,吾将上下而求索。——屈原 75、内外相应,言行相称。——韩非
ቤተ መጻሕፍቲ ባይዱ
高炉炼铁工艺培训课程(PPT 96页)

2020/7/3/12:52:59
44
2.1.1.1 几个基本概念
1 矿物(Minerals):地壳中具有均一内部结构、化学 组成及一定物理、化学性质的天然化合物或自然 元素称为矿物。其中能够为人类利用的称为有用 矿物。
2 矿石(Ore):在现代的技术经济条件下,能以工业 规模从中提取金属、金属化合物或其它产品的矿 物称为矿石。
2020/7/3/12:52:59
99
铁矿石处理工艺流程
矿石(ore)→破碎(crush)→筛分 (screen)→富矿(high-grade ore)→混匀(mix)→高炉;
矿石→破碎→筛分→贫矿 (lean ore)→磨矿 (grinding)→筛分→选矿 →造块→人造富矿→高炉
2020/7/3/12:52:59
分解反应: 结晶水的分解:褐铁矿(mFe2O3·nH2O) 高岭土(Al2O3·2SiO2·2H2O) 熔剂分解:CaCO3=CaO+CO2(750℃以上) MgCO3=MgO+CO2(720℃)
2020/7/3/12:52:59
20 20
烧结过程的主要反应
还原与再氧化反应:Fe、Mn等
靠近燃料颗粒处:3Fe2O3+CO=2Fe3O4+CO2; Fe3O4+CO=3FeO+CO2;
高炉冶炼是连续生产过程,必须尽可能为其提 供数量充足、品味高、强度好、粒度均匀粉末 少、有害杂质少及性能稳定的原料。
2020/7/3/12:52:59
88
铁矿石
磁铁矿(Fe3O4)-magnettie 赤铁矿(Fe2O3)-hematite
褐铁矿(mFe2O3·nH2O)-limonite 菱铁矿(FeCO3)-siderite
宝钢高炉炼铁工艺介绍ppt课件
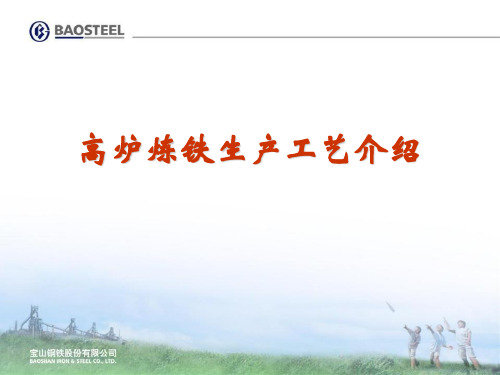
1 2 0 m /m i n
CC OO O
炉顶装料
BF
喷煤系统
重力 除尘器
热风
1VS 2VS
TRT
调压阀组
消音器
水封装置
冷风
HS HS
HS
HS
最高风温
1310℃
最高拱顶温度 1450℃
最高废气温度
350℃
混铁车
高炉脱硅装 置
2、高炉工艺流程介绍
高炉冶炼物流流程
原燃料 鼓风机
矿石 焦炭 辅料 煤粉
高温鼓风
1、行车、悬臂吊车等起重设备; 2、泥炮; 3、开口机; 4、移盖机; 5、摆动流嘴; 6、残铁开口机; 7、主沟、渣铁沟; 8、液压系统。
2.6高炉炉前工艺流程
2、高炉工艺流程介绍
2.7高炉炉渣处理流程
2、高炉工艺流程介绍
渣处理方式
水渣:熔渣经过冷却水急冷,产生细碎颗粒状水渣,用于制作水泥。 干渣:熔渣放入坑中,洒水冷却,冷却后挖掘清运出厂,用于铺路。
水渣处理工艺
LASA法:粗粒分离槽与脱水槽脱水;电消耗大,管道易磨损,占地大 。 INBA法:转鼓与成品槽脱水,水电消耗少,管道阀门寿命长,占地少。 新INBA法:较INBA法增加了蒸汽冷却装置,环保,耗电增多。
2.7高炉炉渣处理流程
压缩空气
烟囱
2、高炉工艺流程介绍
风扇
冷却 塔
炉渣
渣水槽
渣水沟
冲渣水
P 事故水
渣皮带
输送皮带
渣槽
转鼓
P
集水槽 温水槽
P
水渣
P
P
2.7高炉炉渣处理流程
2、高炉工艺流程介绍
2.8高炉除尘系统
高炉炼铁工艺课件

直接还原成大量碱蒸气,随煤气上升到低温区又被氧化成 碳酸盐沉积在炉料和炉墙上,部分随炉料下降,从而反复 循环积累。其危害主要为:与炉衬作用生成钾霞石
(K2O﹒Al2O3﹒2SiO2),体积膨胀40%而破坏炉衬;与 炉衬作用生成低熔点化合物,粘接在炉墙上,易导致结瘤; 与焦炭作用生成嵌入式化合物(CKCN),体积膨胀很大, 破坏焦炭高温强度,从而影响高炉下部料柱的透气性。 (6)铜。铜是贵重的有色金属,在钢中的含量不超过0.3% 时,能增强金属的抗腐蚀性能,但当含铜量超过0.3%时, 钢的焊接性能降低,并产生热脆。 2. 有益元素。许多铁矿石中常伴有锰、铬、钒、钛、镍等元 素,形成多种共生矿。这些金属能改善钢材的性能,是重 要的合金元素,故称之为有益元素。
菱
FeCO3
48.230~40 Nhomakorabea25
P,S↓熔 烧后易 还原
各类铁矿石图
磁铁矿 褐铁矿
赤铁矿
菱铁矿
2.1.2 高炉冶炼对铁矿石的要求
铁矿石是高炉冶炼的主要原料,决定铁矿石质量优劣 的主要因素是化学成分、物理性质及其冶金性能。高炉冶 炼对铁矿石的要求是:含铁量高,脉石少,有害杂质少, 化学成分稳定,粒度均匀,具有良好的还原性及一定的机 械强度等性能。 2.1.2.1 铁矿石品位 铁矿石的品位即指铁矿石的含铁量,以TFe%表示。品 位是评价铁矿石质量的主要指标。经验表明:铁矿石含铁 量每增加1%,焦比将降低2%,产量提高3%,因为随着矿 石品位的提高,脉石含量越少,溶剂用量和渣量减少,既 节省热量消耗,又有利于炉况顺行。一般实际含铁量大于 理论含铁量70%~90%时方可直接入炉,成为富矿 。贫矿必须经过选矿和造块才能入炉冶炼。
3、送风系统。包括鼓风机、热风炉、热风总管,送风支管。 本系统的任务是把从鼓风机房送出的冷风加热并送入高炉。 4、喷吹系统。包括磨煤机、集煤罐、储煤罐、喷煤罐、混 合器和喷枪。本系统的任务是磨制、收存和计量后把煤粉 从风口喷入高炉。 5、渣铁处理系统。包括出铁厂、泥炮、开口机、铁水罐、 水渣池等。本系统的任务是定期将炉内的渣铁出净,保证 高炉连续生产。 6、煤气处理系统。包括煤气上升管、下降管、重力除尘器、 布袋除尘器、静电除尘器。本系统的任务是将炉顶引出的 含尘很高的荒煤气净化成合乎要求的净煤气。
高炉炼铁生产工艺流程及主要设备(共7张PPT)
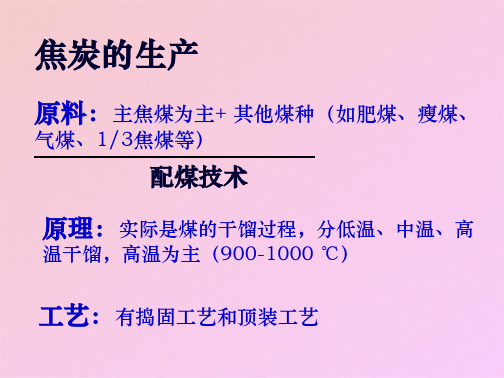
增长率(%)
炼焦企业分独立炼焦和钢厂联1合9焦7化5企-业2(产0能160/4)年。 中国焦炭产量及增长率
2010年亿吨,占世界68%。
炼焦企业分独立炼焦和钢厂联合焦化企业(产能6/4)。
截至到目前,统计在册炼焦企业997家,分布在29个省市,华北、华东和东北地区为主,占比超过70%
现货市场概况——三个“5第0一0”00
我原国料焦 :炭主逐焦年煤产为量主增+ 其长他情1煤况00种0(0如肥煤、瘦煤、气煤、1/3焦煤等)
0
世界第一生产大国:2009年亿吨,占世界60%左右。
0
-20
产量
增长率
炼焦企业分布区域化
截至到目前,统计在册炼焦企业997家, 分布在29个省市,华北、华东和东北地 区为主,占比超过70%
炼焦企业分独立炼焦和钢厂联合焦化企业 (产能6/4)。
美国, 3.30%
其他, 16%
1200万吨以上,约占世界贸易
量的%。
印度, 3.74%
国内贸易量,2009年独立焦
乌克兰,
化厂产量亿吨,商品化率62%。 4.50% 俄罗斯,
6.80%
日本, 9%
中国, 57%
我国焦炭逐年产量增长情况
产量(万吨) 1975 1977 1979 1981 1983 1985 1987 1989 1991 1993 1995 1997 1999 2001 2003 2005 2007 2009
2008年我国焦炭产量地区分布
排 名 地区 产量/万吨 占比 1 山西 8235.94 25.5% 2 河北 3923.5 12.1%
3 山东 2885.57 8.9%
100%
4 河南 2041.67 6.3%
炼焦企业分独立炼焦和钢厂联1合9焦7化5企-业2(产0能160/4)年。 中国焦炭产量及增长率
2010年亿吨,占世界68%。
炼焦企业分独立炼焦和钢厂联合焦化企业(产能6/4)。
截至到目前,统计在册炼焦企业997家,分布在29个省市,华北、华东和东北地区为主,占比超过70%
现货市场概况——三个“5第0一0”00
我原国料焦 :炭主逐焦年煤产为量主增+ 其长他情1煤况00种0(0如肥煤、瘦煤、气煤、1/3焦煤等)
0
世界第一生产大国:2009年亿吨,占世界60%左右。
0
-20
产量
增长率
炼焦企业分布区域化
截至到目前,统计在册炼焦企业997家, 分布在29个省市,华北、华东和东北地 区为主,占比超过70%
炼焦企业分独立炼焦和钢厂联合焦化企业 (产能6/4)。
美国, 3.30%
其他, 16%
1200万吨以上,约占世界贸易
量的%。
印度, 3.74%
国内贸易量,2009年独立焦
乌克兰,
化厂产量亿吨,商品化率62%。 4.50% 俄罗斯,
6.80%
日本, 9%
中国, 57%
我国焦炭逐年产量增长情况
产量(万吨) 1975 1977 1979 1981 1983 1985 1987 1989 1991 1993 1995 1997 1999 2001 2003 2005 2007 2009
2008年我国焦炭产量地区分布
排 名 地区 产量/万吨 占比 1 山西 8235.94 25.5% 2 河北 3923.5 12.1%
3 山东 2885.57 8.9%
100%
4 河南 2041.67 6.3%
高炉炼铁工艺课件
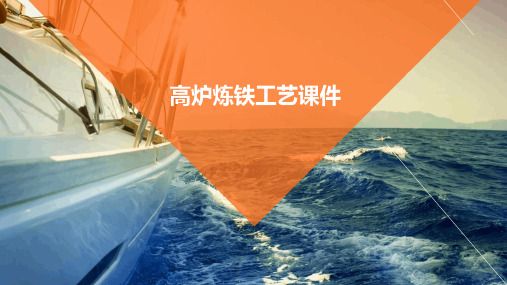
熔融还原技术
将部分碳素燃烧过程移至高炉外,降低高炉内的碳含量,提高生铁 质量。
高压操作技术
通过提高高炉内的压力,增加煤气在炉内的停留时间,提高生铁产 量和降低能耗。
谢谢聆听
布料规律
根据高炉的生产需求和原料特性,制定不同的布料方案,以实现煤气和铁水的均匀分布,提高高炉的 产量和效率。
风口、渣口和铁口的操作
风口
位于炉膛的底部,用于向炉内提供氧 气,助燃焦炭,并产生高温煤气。操 作人员需定期检查风口状态,保证其 通畅。
渣口
铁口
位于炉膛的另一侧,用于排放铁水。 铁口操作需注意控制铁水的流量和温 度,以保证高炉的正常运行和钢铁产 品的质量。
位于炉膛的一侧,用于排放高炉产ቤተ መጻሕፍቲ ባይዱ 的渣。渣口操作需注意控制渣的排出 量和成分,以降低对环境的污染。
04 高炉炼铁的环保与节能
高炉炼铁的排放与治理
排放物种类
高炉炼铁过程中会产生大量的废 气、废水和固体废弃物,如粉尘
、炉渣和瓦斯等。
排放物危害
这些排放物若未经处理直接排放, 会对环境造成严重污染,影响人类 健康和生态平衡。
铁氧化物的还原机理
Fe2O3→Fe3O4→FeO→Fe 铁氧化物还原过程中,低价氧化物更容易还原成金属铁。
碳的气化反应与燃烧反应
碳气化反应
C+CO2→2CO
碳燃烧反应
2C+O2→2CO
炉渣的形成与作用
炉渣的形成
高炉炼铁过程中,矿石中的脉石、焦 炭中的灰分等与熔融的炉渣相混而成 。
炉渣的作用
去除有害杂质、维持生铁质量、保持 高炉热平衡等。
治理措施
采取有效的治理措施,如安装除尘 器、建设污水处理设施和固体废弃 物处理设施等,以减少污染物排放 。
将部分碳素燃烧过程移至高炉外,降低高炉内的碳含量,提高生铁 质量。
高压操作技术
通过提高高炉内的压力,增加煤气在炉内的停留时间,提高生铁产 量和降低能耗。
谢谢聆听
布料规律
根据高炉的生产需求和原料特性,制定不同的布料方案,以实现煤气和铁水的均匀分布,提高高炉的 产量和效率。
风口、渣口和铁口的操作
风口
位于炉膛的底部,用于向炉内提供氧 气,助燃焦炭,并产生高温煤气。操 作人员需定期检查风口状态,保证其 通畅。
渣口
铁口
位于炉膛的另一侧,用于排放铁水。 铁口操作需注意控制铁水的流量和温 度,以保证高炉的正常运行和钢铁产 品的质量。
位于炉膛的一侧,用于排放高炉产ቤተ መጻሕፍቲ ባይዱ 的渣。渣口操作需注意控制渣的排出 量和成分,以降低对环境的污染。
04 高炉炼铁的环保与节能
高炉炼铁的排放与治理
排放物种类
高炉炼铁过程中会产生大量的废 气、废水和固体废弃物,如粉尘
、炉渣和瓦斯等。
排放物危害
这些排放物若未经处理直接排放, 会对环境造成严重污染,影响人类 健康和生态平衡。
铁氧化物的还原机理
Fe2O3→Fe3O4→FeO→Fe 铁氧化物还原过程中,低价氧化物更容易还原成金属铁。
碳的气化反应与燃烧反应
碳气化反应
C+CO2→2CO
碳燃烧反应
2C+O2→2CO
炉渣的形成与作用
炉渣的形成
高炉炼铁过程中,矿石中的脉石、焦 炭中的灰分等与熔融的炉渣相混而成 。
炉渣的作用
去除有害杂质、维持生铁质量、保持 高炉热平衡等。
治理措施
采取有效的治理措施,如安装除尘 器、建设污水处理设施和固体废弃 物处理设施等,以减少污染物排放 。
- 1、下载文档前请自行甄别文档内容的完整性,平台不提供额外的编辑、内容补充、找答案等附加服务。
- 2、"仅部分预览"的文档,不可在线预览部分如存在完整性等问题,可反馈申请退款(可完整预览的文档不适用该条件!)。
- 3、如文档侵犯您的权益,请联系客服反馈,我们会尽快为您处理(人工客服工作时间:9:00-18:30)。
通常析碳反应量较少,对冶炼进程影响不大
锰的还原
Mn氧化物得还原顺序 MnO2 → Mn2O3 → Mn3O4 → MnO
MnO2,Mn2O3极不稳定,还原产物中H2O和CO2→100 %,Mn3O4很容易还原,平衡气相成份中CO<10% 这三类锰的氧化物在高炉上部就可全部转化为 MnO
还原皆为放热反应,热效应较大。其结果高温区 扩大,导致碳的气化反应过分发展,焦比升高
反应开始温度 Tb=1923K=1650℃ SiO2 (s)+C=SiO(g)+CO △G0 =159200-78.7T
反应开始温度 Tb=2022K=1749℃
高炉冶炼温度条件下,硅的还原很困难
推测:高炉风口带的高温区时,Si才能开始还原 事实:高炉解剖研究的结果说明,在软熔带下沿形成的液态铁 水中含[Si]、[S]量即已开始增高,下降到风口水平面时[Si]、 [S]含量达到最大值。尔后,在炉缸下部铁滴穿过渣层时,[Si] 、[S]又转移入渣,最后降低至出炉成份
增大硫的挥发量;很有限 加大渣量;意味着多消耗熔剂,降低生产率,而且
随焦比升高,入炉S增加。不希望,必要时可采用 增大硫的分配系数LS。提高渣底脱S能力,生产中达
到LS值一方面取决于该条件下炉渣去S反应热力学平 衡,另一方面动力学
炼铁与炼钢脱S条件比较
条件பைடு நூலகம்温度
R r’[s]
FeO Ls
(3)提高生铁[Si]量:可促使渣铁接触时,[Si] 氧化为(SiO2)发生相应的耦合反应,(MnO)下降
硅的还原
Si的还原历程
Si的氧化物有二种:SiO2,SiO(气) ,逐级转化 >1500℃ SiO2—4SiO(气)—4Si <1500℃ SiO2—Si SiO2(s)+2C=Si(s)+2CO △G0 =174300-90.6T
析碳反应
热力学条件:煤气中CO在上升过程中,当温度降到400— 600℃时:
2CO=CO2十C
动力学条件:在高炉中存在催化剂新相金属铁,Fe3C、FeO 以及H2等,高炉内仍有一定数量的析碳反应发生。
危害:消耗高炉上部气体还原剂中的CO,析出的碳素渗入炉 墙可破坏炉衬,渗入炉料则可使炉料破碎、产生粉末阻碍煤 气流,其自身形成的粉末阻塞炉料间空隙,是透气性下降。
5)在保证高炉顺行及产品质量合格的前提下,炉渣还原 矿炉衬起保护作用:钛渣护炉(2-3%TiO2)
TiO2→[Ti] [Ti]+[C](或N) →Ti(C,N)>2000℃
Ti(C,N)在铁水中溶解度随温度升高而升高,随温度 降低而降低。一旦高炉炉底有侵蚀,传热加快,局部降温 Ti(C,N)在低温区富集→自动衬炉
铁及渣中含硫在炉腹以下沿炉高的变化
对高炉操作的影响:炉渣容纳了全部入炉硫量的约85%,随煤 气逸出炉外的<10%,而生铁中的含硫小于总入炉硫量的5%。 S 的富集对高炉操作不产生K,Na,Zn类似的影响
降低[%S]应采取的措施:
降低硫负荷;硫负荷主要来源于焦炭,使用低S焦炭 如用高S焦炭,则应降低焦比
(1)初渣的生成
1)过程
①固相反应
主要变化:在温度较低 (500-700℃)的固体颗粒 状态下,即开始形成部分低 熔点化合物,是初渣的孕育 阶段。
位置:软熔带之上。
②矿石软化
主要变化:矿石在下降过程中 温度逐渐升高,当接近和达到其熔 化温度等温线水平时,开始出现微 小的局部熔化(矿石软化开始),
2.3.4炉渣去硫
研究炉渣去硫的意义
硫是钢铁产品中的有害杂质,操作中稍有失误即可能使生 铁含硫量超过规定标准。对高炉冶炼这一环节来说,研究硫 在高炉中的行为以及脱除硫的反应机理,以保证即使冶炼条 件发生一定范围的波动时仍可使含硫低于规定标准
硫的来源及分布
来源:矿石:块矿,烧结矿,球团矿-少
熔剂:石灰石,白云石 -少
概念:在铁渣界面中发生氧化还原反应引起元素的迁移 要点:a.氧化还原反应(不同物相)
b.元素迁移(不同物相)
2.3.1炉渣在高炉冶炼过程中的作用
炉渣来源
矿石脉石 焦炭灰分 炉衬破坏 操作加入
(2)造渣的目的及要求
1)造渣的目的 ①实现金属与氧化物脉石的机械或物理分离。 ②在化学上进一步实现Fe-O的分离(还原过程)及保 证生铁质量,
2)造渣的要求
①有良好的流动性,不给冶炼操作带来任何困难; ②有参与所希望的化学反应的充分能力,如[Si]、[Mn]或 其他有益元素的还原;吸收S及碱金属等; ③能满足允许煤气顺利通过及渣铁,渣气良好分离的力学条 件; ④稳定性好,不致因冶炼条件的改变,炉渣性能急剧恶化。
(3) 炉渣的作用
1)渣铁分离。 2)渣铁间进行合金元素的还原和脱S反应,起着控制 生铁成分的作用。 3)炉渣的形成造成高炉内的软熔带及滴下带,对炉 内煤气分布及炉料下降都有很大影响。 4)某些元素的富集,实现共生矿元素的分离。如高 炉富锰渣,稀土渣。
增大硫的挥发量;很有限 加大渣量;意味着多消耗熔剂,降低生产率,而且
随焦比升高,入炉S增加。不希望,必要时可采用 增大硫的分配系数LS。提高渣底脱S能力,生产中达
到LS值一方面取决于该条件下炉渣去S反应热力学平 衡,另一方面动力学
降低[%S]应采取的措施:
降低硫负荷;硫负荷主要来源于焦炭,使用低S焦炭 如用高S焦炭,则应降低焦比
燃料:焦,煤
-多(80%以上)
硫负荷:冶炼每吨生铁炉料带入硫的千克数称为“硫负 荷”。一般条件下,硫负荷<10千克。
S在高炉中的行为 主要是在风口前发生 燃烧反应时,以气态化 合物的形式(如SiS、H 2升S、。C在S或煤C气OS与)随下煤降气的上炉 料和滴落的渣铁相遇时, 分别被吸收。在炉内高 温与低温区间存在一个 循环过程。被炉料和渣 铁吸收的硫少部份进入 燃烧带后再次气化,参 加循环运动,而大部份 在渣铁反应时转入炉渣 排出炉外
在风口区的SiO2的还原:
SiO2(焦炭)+C=SiO(g)+CO SiC+CO=SiO(g)+2C 2SiO2+SiC=3SiO(g)+CO
lg PSiO PCO 35896 17.957
aSiO 2
T
lg PSiO 4296 0.197
PCO
T
lg PS2iO PCO 76088 36.11
炼铁 1400-1500℃
1.0-1.2 高[S][Si][P]↑
<1.0% 理论渣100-200, 实际20-50
炼钢 1600- 1650℃
2.5-3.5 低
([C][P][Si]↓) <2.0%
理论 10, 实际接近10
生产中期望铁水【S】很低:炼钢成本低,能生产优质钢, 扩大钢种
MnO比FeO更难还原,只能用C还原
MnO的还原
MnO的还原只能用C进行,成渣后渣中(MnO)与赤热 焦炭反应,或与饱和[C]的液态铁液接触时渣铁之间 的反应:
(MnO)+C=[Mn]+CO △Go =69050-50.20T
Mn在渣铁中的分配比的计算
KMn=α[Mn] PCO/α(MnO) αC α[Mn] = γMn′[%Mn] α(MnO)= γ(MnO) (%Mn) αC=1
位置:在高炉内从开始软化到 熔化滴落之前。
决定因素:a开始软化温度。
b软化温度区间。
对高炉冶炼的影响:矿石软化是造渣过程对高炉顺行最有影响 的一个环节。其产物是粘稠状物质。对煤气阻力很大,也降低 了炉料下降的(阻力增大)速度,严重时会造成炉子不顺(出 现悬料)
③初渣形成
主要变化:随温度升高,软 化了的物质开始熔化,并处于 向下流动状态。这时形成的渣 即为初渣。矿、焦呈分层状态, 只是固态矿石变成了软熔层。
6)冲洗渣:加入CaF2,MnO,FeO形成流动性很好的渣。 冲洗结瘤是事故处理底短期行为。
7)专用渣:在不影响炼铁的前提下,希望炉渣是一种 产品,如水泥掺和料。
2.3.2造渣过程简述
高炉渣按其成渣过程有初渣,中间渣,终渣之分。 初渣:指在高炉的适当温度区域(软熔带)刚开始 出现的液相炉渣。 中间渣:指处于滴落过程中成分、温度在不断变化 的液相炉渣。 终渣:指已经下达炉缸,并周期性地从炉内排出地 液相炉渣。
位置:出现初渣的区域是在 炉身下部,较晚的则是在炉腹 上部,高炉出现初渣的区域称 为成渣带(软熔带)。
2)初渣成分的特点
已大部分还原到FeO或金属铁,初渣中FeO含量较高,熔剂CaO很少参加 造渣,碱度与矿石本身的碱度相似,各处成分不均匀。
(2)中间渣
主要变化:初渣与煤气、焦 炭接触(在滴落过程中),在不 断的反应过程中,逐渐失去 (FeO)、(MnO)等。同时吸收焦 炭灰份及煤气中携带的物质如SiO、 SiS、碱金属(K,Na)的蒸汽等。 碱性熔剂(CaO,MgO)等也会在初 渣滴落过程中逐被吸收。这时炉 渣中能降低熔点的(FeO),(MnO) 因还原而逐渐减少。能提高熔点 的CaO,MgO增加。
高炉
上部
软熔带
风口
熔池
新日铁
0.2
广田
0.2
俄罗斯
0.2
首钢
0.18
2.38
0.62
2
0.85
2.91
1.25
4.22
1.42
尚有其他类型的Si的还原过程存在
SiO2的还原机理
气相反应机理
内容:Si的还原是通过气相的SiO及SiS等中间化 合物进行的。在风口带的高温区内,焦炭及其灰 份中所含S以及SiO2,活度值大,与C的接触条件 极好,在高温下反应生成气相产物SiO及SiS,随 高温煤气而上升。当遇到由软熔带向下滴落的渣 及铁液时则被吸收。到风口带(气相物的发源地) 时吸收量达到了最大值
锰的还原
Mn氧化物得还原顺序 MnO2 → Mn2O3 → Mn3O4 → MnO
MnO2,Mn2O3极不稳定,还原产物中H2O和CO2→100 %,Mn3O4很容易还原,平衡气相成份中CO<10% 这三类锰的氧化物在高炉上部就可全部转化为 MnO
还原皆为放热反应,热效应较大。其结果高温区 扩大,导致碳的气化反应过分发展,焦比升高
反应开始温度 Tb=1923K=1650℃ SiO2 (s)+C=SiO(g)+CO △G0 =159200-78.7T
反应开始温度 Tb=2022K=1749℃
高炉冶炼温度条件下,硅的还原很困难
推测:高炉风口带的高温区时,Si才能开始还原 事实:高炉解剖研究的结果说明,在软熔带下沿形成的液态铁 水中含[Si]、[S]量即已开始增高,下降到风口水平面时[Si]、 [S]含量达到最大值。尔后,在炉缸下部铁滴穿过渣层时,[Si] 、[S]又转移入渣,最后降低至出炉成份
增大硫的挥发量;很有限 加大渣量;意味着多消耗熔剂,降低生产率,而且
随焦比升高,入炉S增加。不希望,必要时可采用 增大硫的分配系数LS。提高渣底脱S能力,生产中达
到LS值一方面取决于该条件下炉渣去S反应热力学平 衡,另一方面动力学
炼铁与炼钢脱S条件比较
条件பைடு நூலகம்温度
R r’[s]
FeO Ls
(3)提高生铁[Si]量:可促使渣铁接触时,[Si] 氧化为(SiO2)发生相应的耦合反应,(MnO)下降
硅的还原
Si的还原历程
Si的氧化物有二种:SiO2,SiO(气) ,逐级转化 >1500℃ SiO2—4SiO(气)—4Si <1500℃ SiO2—Si SiO2(s)+2C=Si(s)+2CO △G0 =174300-90.6T
析碳反应
热力学条件:煤气中CO在上升过程中,当温度降到400— 600℃时:
2CO=CO2十C
动力学条件:在高炉中存在催化剂新相金属铁,Fe3C、FeO 以及H2等,高炉内仍有一定数量的析碳反应发生。
危害:消耗高炉上部气体还原剂中的CO,析出的碳素渗入炉 墙可破坏炉衬,渗入炉料则可使炉料破碎、产生粉末阻碍煤 气流,其自身形成的粉末阻塞炉料间空隙,是透气性下降。
5)在保证高炉顺行及产品质量合格的前提下,炉渣还原 矿炉衬起保护作用:钛渣护炉(2-3%TiO2)
TiO2→[Ti] [Ti]+[C](或N) →Ti(C,N)>2000℃
Ti(C,N)在铁水中溶解度随温度升高而升高,随温度 降低而降低。一旦高炉炉底有侵蚀,传热加快,局部降温 Ti(C,N)在低温区富集→自动衬炉
铁及渣中含硫在炉腹以下沿炉高的变化
对高炉操作的影响:炉渣容纳了全部入炉硫量的约85%,随煤 气逸出炉外的<10%,而生铁中的含硫小于总入炉硫量的5%。 S 的富集对高炉操作不产生K,Na,Zn类似的影响
降低[%S]应采取的措施:
降低硫负荷;硫负荷主要来源于焦炭,使用低S焦炭 如用高S焦炭,则应降低焦比
(1)初渣的生成
1)过程
①固相反应
主要变化:在温度较低 (500-700℃)的固体颗粒 状态下,即开始形成部分低 熔点化合物,是初渣的孕育 阶段。
位置:软熔带之上。
②矿石软化
主要变化:矿石在下降过程中 温度逐渐升高,当接近和达到其熔 化温度等温线水平时,开始出现微 小的局部熔化(矿石软化开始),
2.3.4炉渣去硫
研究炉渣去硫的意义
硫是钢铁产品中的有害杂质,操作中稍有失误即可能使生 铁含硫量超过规定标准。对高炉冶炼这一环节来说,研究硫 在高炉中的行为以及脱除硫的反应机理,以保证即使冶炼条 件发生一定范围的波动时仍可使含硫低于规定标准
硫的来源及分布
来源:矿石:块矿,烧结矿,球团矿-少
熔剂:石灰石,白云石 -少
概念:在铁渣界面中发生氧化还原反应引起元素的迁移 要点:a.氧化还原反应(不同物相)
b.元素迁移(不同物相)
2.3.1炉渣在高炉冶炼过程中的作用
炉渣来源
矿石脉石 焦炭灰分 炉衬破坏 操作加入
(2)造渣的目的及要求
1)造渣的目的 ①实现金属与氧化物脉石的机械或物理分离。 ②在化学上进一步实现Fe-O的分离(还原过程)及保 证生铁质量,
2)造渣的要求
①有良好的流动性,不给冶炼操作带来任何困难; ②有参与所希望的化学反应的充分能力,如[Si]、[Mn]或 其他有益元素的还原;吸收S及碱金属等; ③能满足允许煤气顺利通过及渣铁,渣气良好分离的力学条 件; ④稳定性好,不致因冶炼条件的改变,炉渣性能急剧恶化。
(3) 炉渣的作用
1)渣铁分离。 2)渣铁间进行合金元素的还原和脱S反应,起着控制 生铁成分的作用。 3)炉渣的形成造成高炉内的软熔带及滴下带,对炉 内煤气分布及炉料下降都有很大影响。 4)某些元素的富集,实现共生矿元素的分离。如高 炉富锰渣,稀土渣。
增大硫的挥发量;很有限 加大渣量;意味着多消耗熔剂,降低生产率,而且
随焦比升高,入炉S增加。不希望,必要时可采用 增大硫的分配系数LS。提高渣底脱S能力,生产中达
到LS值一方面取决于该条件下炉渣去S反应热力学平 衡,另一方面动力学
降低[%S]应采取的措施:
降低硫负荷;硫负荷主要来源于焦炭,使用低S焦炭 如用高S焦炭,则应降低焦比
燃料:焦,煤
-多(80%以上)
硫负荷:冶炼每吨生铁炉料带入硫的千克数称为“硫负 荷”。一般条件下,硫负荷<10千克。
S在高炉中的行为 主要是在风口前发生 燃烧反应时,以气态化 合物的形式(如SiS、H 2升S、。C在S或煤C气OS与)随下煤降气的上炉 料和滴落的渣铁相遇时, 分别被吸收。在炉内高 温与低温区间存在一个 循环过程。被炉料和渣 铁吸收的硫少部份进入 燃烧带后再次气化,参 加循环运动,而大部份 在渣铁反应时转入炉渣 排出炉外
在风口区的SiO2的还原:
SiO2(焦炭)+C=SiO(g)+CO SiC+CO=SiO(g)+2C 2SiO2+SiC=3SiO(g)+CO
lg PSiO PCO 35896 17.957
aSiO 2
T
lg PSiO 4296 0.197
PCO
T
lg PS2iO PCO 76088 36.11
炼铁 1400-1500℃
1.0-1.2 高[S][Si][P]↑
<1.0% 理论渣100-200, 实际20-50
炼钢 1600- 1650℃
2.5-3.5 低
([C][P][Si]↓) <2.0%
理论 10, 实际接近10
生产中期望铁水【S】很低:炼钢成本低,能生产优质钢, 扩大钢种
MnO比FeO更难还原,只能用C还原
MnO的还原
MnO的还原只能用C进行,成渣后渣中(MnO)与赤热 焦炭反应,或与饱和[C]的液态铁液接触时渣铁之间 的反应:
(MnO)+C=[Mn]+CO △Go =69050-50.20T
Mn在渣铁中的分配比的计算
KMn=α[Mn] PCO/α(MnO) αC α[Mn] = γMn′[%Mn] α(MnO)= γ(MnO) (%Mn) αC=1
位置:在高炉内从开始软化到 熔化滴落之前。
决定因素:a开始软化温度。
b软化温度区间。
对高炉冶炼的影响:矿石软化是造渣过程对高炉顺行最有影响 的一个环节。其产物是粘稠状物质。对煤气阻力很大,也降低 了炉料下降的(阻力增大)速度,严重时会造成炉子不顺(出 现悬料)
③初渣形成
主要变化:随温度升高,软 化了的物质开始熔化,并处于 向下流动状态。这时形成的渣 即为初渣。矿、焦呈分层状态, 只是固态矿石变成了软熔层。
6)冲洗渣:加入CaF2,MnO,FeO形成流动性很好的渣。 冲洗结瘤是事故处理底短期行为。
7)专用渣:在不影响炼铁的前提下,希望炉渣是一种 产品,如水泥掺和料。
2.3.2造渣过程简述
高炉渣按其成渣过程有初渣,中间渣,终渣之分。 初渣:指在高炉的适当温度区域(软熔带)刚开始 出现的液相炉渣。 中间渣:指处于滴落过程中成分、温度在不断变化 的液相炉渣。 终渣:指已经下达炉缸,并周期性地从炉内排出地 液相炉渣。
位置:出现初渣的区域是在 炉身下部,较晚的则是在炉腹 上部,高炉出现初渣的区域称 为成渣带(软熔带)。
2)初渣成分的特点
已大部分还原到FeO或金属铁,初渣中FeO含量较高,熔剂CaO很少参加 造渣,碱度与矿石本身的碱度相似,各处成分不均匀。
(2)中间渣
主要变化:初渣与煤气、焦 炭接触(在滴落过程中),在不 断的反应过程中,逐渐失去 (FeO)、(MnO)等。同时吸收焦 炭灰份及煤气中携带的物质如SiO、 SiS、碱金属(K,Na)的蒸汽等。 碱性熔剂(CaO,MgO)等也会在初 渣滴落过程中逐被吸收。这时炉 渣中能降低熔点的(FeO),(MnO) 因还原而逐渐减少。能提高熔点 的CaO,MgO增加。
高炉
上部
软熔带
风口
熔池
新日铁
0.2
广田
0.2
俄罗斯
0.2
首钢
0.18
2.38
0.62
2
0.85
2.91
1.25
4.22
1.42
尚有其他类型的Si的还原过程存在
SiO2的还原机理
气相反应机理
内容:Si的还原是通过气相的SiO及SiS等中间化 合物进行的。在风口带的高温区内,焦炭及其灰 份中所含S以及SiO2,活度值大,与C的接触条件 极好,在高温下反应生成气相产物SiO及SiS,随 高温煤气而上升。当遇到由软熔带向下滴落的渣 及铁液时则被吸收。到风口带(气相物的发源地) 时吸收量达到了最大值