数控车床切削用量推荐表
车削切削用量选取参考表

0.40
0.1
外圆纵车
(Kr=0°)
YG6
(用切削液)
f≥αp
208
0.4
0.2
0.28
f>αp
208
0.2
0.4
0.28
切断及切槽
YG6(不用液)
?
?
高速钢(不用液)
?
18
?
可锻铸铁
外圆纵车
YG8
(不用切削液)
f≤
206
0.15
0.20
0.2
f>
140
0.15
0.45
0.2
高速钢
(用切削液)
速度计算的修正系数
切深αp(mm)
进给量f(mm/r)
kMv
ksv
kiv
kkr
k,krv
krεv
kBv
kkv
150
60
1
1
1
1
1
1
1
KV
Tm
αpxv
fyv
切削速度? v(m/min)
主轴转速(r/min)
128
270
注:1、有批注的所有表格均需录入数据。????????????????????????????????????????????????????????????
公式中的系数和指数
CV
XV
yV
m
碳素结构钢σb=
外圆纵车
(Kr>0°)
YT15
(不用切削液)
f≤
291
f≤
242
0.15
0.35
0.20
f>
235
0.15
0.45
0.20
数控车床刀具及切削用量的选择
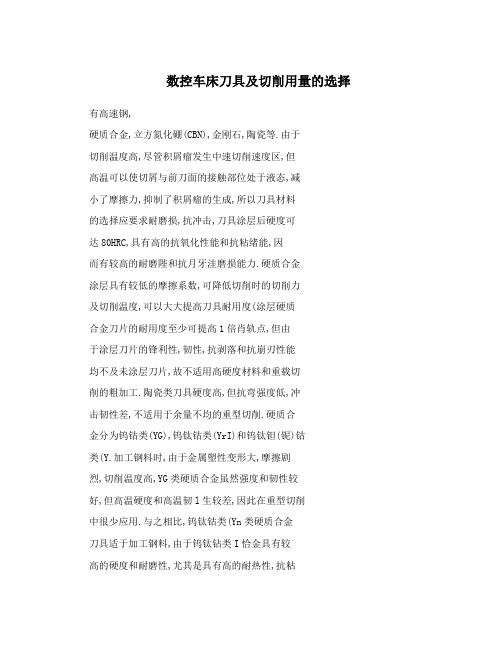
数控车床刀具及切削用量的选择有高速钢,硬质合金,立方氮化硼(CBN),金刚石,陶瓷等.由于切削温度高,尽管积屑瘤发生中速切削速度区,但高温可以使切屑与前刀面的接触部位处于液态,减小了摩擦力,抑制了积屑瘤的生成,所以刀具材料的选择应要求耐磨损,抗冲击,刀具涂层后硬度可达80HRC,具有高的抗氧化性能和抗粘绪能,因而有较高的耐磨陛和抗月牙洼磨损能力.硬质合金涂层具有较低的摩擦系数,可降低切削时的切削力及切削温度,可以大大提高刀具耐用度(涂层硬质合金刀片的耐用度至少可提高1倍肖轨点,但由于涂层刀片的锋利性,韧性,抗剥落和抗崩刃性能均不及未涂层刀片,故不适用高硬度材料和重载切削的粗加工.陶瓷类刀具硬度高,但抗弯强度低,冲击韧性差,不适用于余量不均的重型切削.硬质合金分为钨钴类(YG),钨钛钴类(YrI)和钨钛钽(铌)钴类(Y.加工钢料时,由于金属塑性变形大,摩擦剧烈,切削温度高,YG类硬质合金虽然强度和韧性较好,但高温硬度和高温韧l生较差,因此在重型切削中很少应用.与之相比,钨钛钴类(Yn类硬质合金刀具适于加工钢料,由于钨钛钻类I恰金具有较高的硬度和耐磨性,尤其是具有高的耐热性,抗粘结扩散能力和抗氧化能力也很好,在加工钢料时刀因此钨钛钴类01田具磨损较小,刀具耐用度较高, 类硬质合金是重型加工时较常用的刀具材料.然而在低速切削钢料时,由于切削过程不太平稳,钨钛钴类(YT)类合金的韧性较差,容易产生崩刃,而且在加工—些高强度合金材料时,它的耐用度下降很快,无法满足使用要求.如电站用机械产品工作于高温,高压,高转速的环境中,对材料(如26Cr2Ni4MoV,Mnl8CrlS)机械性能的要求非常高;而—些高硬度轧辊,表面硬度在淬火后可达HRS90,(Y类刀具在加工此类产品时就无法胜任,在这种隋况下应选用Yw类刀具或细晶粒,超细晶粒合金刀具等.细晶粒合金的搪陛好,更适用于加工冷硬铸铁类产品,效率较Yw类刀具可提高—倍以上.而且在加工—些高强度合金材料时,它的耐用度下降很快,无法满足使用要求.数控刀具与普通机床E所用的刀具相比,有许多不同的要求,主要有以下特点:1.】刚性好(尤其是粗加工刀具),精度高,抗振及热变形小;12互换陛好,便于快速换刀;13寿命高,切削性能稳定,可靠;1.4刀具的尺寸便于调整,以减少换刀调整时间;15刀具应能可靠地断屑或卷屑,以利于切屑的排除;1五系列化,标准化,以利于编程和刀具管理.在实际加工中发现涂层刀具比较适合切削的精加工,刀具的涂层减小了切屑与刀面问的摩擦, 减少了积屑瘤的发生,降低了刀具的磨损,延长了刀具的寿命.精加工阶段同样要求刀具耐磨损,但是精加工阶段的磨损形式是以粘蚀磨损为主,这时的切削速度虽然有了很大提高,但由于工件材质等原因, 仍然会产生积屑瘤,当积屑瘤增长到—定高度时会从刀具上剥离,将接触部位的刀具材料带走一部分,形成刀具的磨损,同时,剥离的积屑瘤会扎进工件表面,形成硬点,降低加工表面质量.因此,如果精加工时仍然采用普通硬质合金刀具,则刀具磨损非常快,换刀次数增多,不仅影响加工效率,也易在工件表面形成接刀痕迹,影响外观质量.解决这个问题的办法就是改变刀具材料.在实际加工中发现涂层刀具比饺适合高速切削的精加工,刀具的涂层减小了切屑与刀面问的摩擦,减少了积屑瘤的发生,降低了刀具的磨损,延长了刀具的寿命.2刀具角度的选择外圆的粗,半精车刚度高的工件时,由于粗加工或半精加工主要是切除多余金属层,为了减少走刀次数,减少切削时间,提高生产效率,切削力较大,故应选择稳固的刀片夹紧方式,为了增加刀尖强度,承受较大的切削力,刀尖角尽可能选择大一些.由于减小主偏角会导致径向分力Fy增大,当工艺系统的刚度较强时,可适当减小刀具主偏角.在一般加工条件下,用硬质合金车刀车碳钢和合金钢,在进给量和切削深度相同的条件下,减小主偏角能使切削厚度减小,切削宽度增大,使参与切削的切削刃长度变长,减少单位长度切削刃的负荷, 刀具强度高,散热条件好,从而提高刀具的使用寿命.3刀具结构的选择根据粗加工加工余量大,切削余量大的特点,用于粗加工的工时间,刀具寿命和加工质量.经济有效的加工方式!是合理的选择了切削条件.切削用量的三要素:切削速度,进给量和背吃刀量直接引起刀具的损伤.切削速度;V1rDJ1000;背吃刀量;affD一2;数控车削加工中的切削用量包括背吃刀量,切削速度和进给量f0选择切削用量时,应该在切削系统强度,刚性允许的条件下充分利用机床功率,最大地发挥刀具的切削性能.所选取的数值要在机床给定的切削参数允许范围内,同时要使主轴转速,背吃刀量和进给量三者都能相互适应,形成最佳的切削效果.具体的原则是:粗车时,在考虑加工经济l生的前提下以提高生产率为主,半精车和精车时,在保证工件加工精度和表面粗糙度的前提下兼顾提高加工效率.’4.1背吃刀量的确定.根据机床,夹具,刀具和工件组成的工艺系统刚度来确定背吃刀量‰在工艺系统刚度允许的隋况下,应以最少的进给次数切除加工余量,以提高加工效率.当零件的加工精度要求较高时,需要保留02,05ram的单边精车余量.42主轴转速的确定.依据机床的性能,被加工零件的材料和刀具允许的切削速度,查阅相关的数控加工切削用量资料,选取切削速度.在确定了切削速度vIl/mird之后,根据工件直径D用下面的公式便可计算出主轴转速n(r/mim).n=100Ovd~rD:式中,D是工件直径,单位为mm.一43进给量给速度)的确定.在确定进给量般来讲,整体刀具的刚性较好,但重型刀具的结构笨重,装卸比较困难,所以发展方向应该是机夹刀具.机夹刀具的刀片夹持结构及加工精度对于刀具的选择很重要,实际加工中发现,常用的机夹刀的夹紧形式可分为上压式,杠杆式和偏心销,楔块式等.对机夹刀具的制造精度要求也很高,因为即使微小的误差,也会使定位机构变成承力机构,由于切削的加工过程中切削力巨大,就会造成刀具的损坏.可采取的施包括:减小切削速度以降低切削刃温度;减小进给率以,刀片承受的应力;选用涂层刀具牌号以加强对前刀面的保护;改进刀具几何形状以减小直j妾作用于前刀面上的切削力. 粗车时,要选强度高,耐用度好的刀具,以便满足粗车时大背吃刀量,大进给量的要求.精车时, 要选精度高,耐用度好的刀具,以保证加工精度的要求.为减少换刀时间和方便对刀,应尽量采用机夹刀和机夹刀片.4切削用量的选择对于高效率的金属切削加工来说,被加工材料,切削工具,切削用量是三大要素.这些决定着加时,要考虑被加工零件的加工精度和表面粗糙度要求,刀具及工件的材料等因素,在保证加工表面质量要求的前提下,可选择较大的进给量以提高加工效率.粗加工时,—般切削用量选择较大,车削时首,以沙走刀的次数;其次,选择较大的进给量,最后才是选择较高的切削速度,伴随着切削速度的提高,刀尖温度会上升,会产生机械的,化学的,热的磨损,刀具磨损不仅影响加工质量,也会增加车床的负荷.切削速度提高20%,刀具寿命会减少1/2.精加工时,如果机床及刀具l生能允许,应尽可能提高切削速度,相应的可以采用较小的进给量,以利于表面质量的提高搬可取0.1,02romeo.如果刀片有修光刃,则可根据修光刃的宽度,适当加大进给量.当采用精车外圆表面时,进给量可以达到每转n1毫米,精加工时,加工余量较小,从而切削深度也较小,对于形状精度较高的表面,应分多次去除余量,这佯可以有效消除残留的形状误差,这_.十于易变形的工件尤其(下转207页)—42—市J政l与I路I桥浅谈高填土路基的质量监控高文民(黑龙江省大庆市肇州县交通局油田专用公路管理站,黑龙江大庆166400) 摘要:高速公路对我国的经济发展和社会生活起到了具大的推动作用,如何控制好高填土路基的施工质量,就显得尤为重要.关键词:高速公路;高填土路基;质量控制高速公路作为社会现代文明的产物,对我国的经济发展和社会生活起到了具大的推动作用,因其全封闭,全立交的特点,为满足快速,安全,经济,舒适等社会发展需要,而得到迅速发展,如何控制好高填土路基的施工质量,就显得尤为重要. 1高填土路基的主要病害路基是路面的基础,路基施工质量的好坏,直接影响到路面的质量,影响路面的使用寿命,行车舒适性和行车安全等,因此控制路基的施工质量,尤其是控制高填方路基的施工质量,对减少路基病害的发生,提高公路的使用寿命显得极为重要.高填方路基的主要病害有:整体或局部沉降,纵横向开裂,滑坍等,其产生的原因主要是工程地质和施工质量.这里主要谈如何控制高填方的施工质量,以减少病害的发生.2高填土路基的施工准备阶段高填方施工前对填料做下列试验项目:21液限,塑限,塑性指数,液陛指数;2.2颗;2’3密度;2.4相对密度;25重型击实;2.6CBR;2.7有机质含量及易溶盐含量.试验完成后要对液限,塑限,塑性指数,液性指数,重型击实试验,CBR试验等进行复核,以确保标准性试验的准确性.在开工前要在试验路段进行压实试验,确定路基施工的机械组合,压实遍数,松铺厚度,压实厚度,松铺系数等施工数据.3高填方路基的施工阶段实践证明,如压实度大于95%畴,填高每增加l米,工后沉降约为l厘米,而车辆荷载作用影响仅为80,150cm深度,路基沉降主要是自重作用,因此,路基的层问压实显然成为控制的重点. 路基压实度是保证路基强度及路面使用质量的关键,直接关系到路面的使用性能及寿命.如果路基压实度不足,在运营过程中,路面就可能产生辙槽,裂缝,沉陷等病害,使路面产生剪切破坏.控制层间压实度成为控制施工质量的重中之重,应从以-F几个方面着手:3.1为保证路基的填筑质量,在填筑前,必须对植被根系进行彻底挖除.挖除后的根穴要进行分层夯实,达到规定的压实度.清表与植根挖除后,按规定进行填前碾压.32填料控制路基填料不得使用淤泥,沼泽土,有~Lt-.,含草皮土,生活垃圾,树根和含有腐朽物质的土,施工中的不合格填料i弃掉.液限大于5O,塑性指数又大于26的土,以及含水量超过规定的土,不得直接作为填料.不同性质的土应分别填筑,不得混填.每种填料累计总厚不”ff/h于0.5m.当填料发生变化时,或同一种填料填筑超过2000m3时,都要取样进行重型击实试验,确定最大干密度及最佳含水量,以便指导路基的压实施工.33严格控制含水量含水量是影响压实效果的决定陛因素,含水量较小时,水膜润滑作用不明显,外部功能也不能克服粒间引力,土粒相对移动不容易,因此压实效果较差,压不密实;含水量过大时,土孔隙中会出现自由水,压实功能不能使气体排出,且压实功能的一部分被自由水抵消,减小了有效压力,压实效果也较差,会出现”弹簧”现象,且会粘轮.只有在最佳含水量时,最容易获得最佳的压实效果.理论上,在最佳含水量条件下压实到最大干密度的土体,强度相对最高,水稳定陛最好.因此必须严格检测用作填料土的含水量,只有在最佳含水量?的范围内才允许进行碾压.在施工现场主要用酒精燃烧法来测定填料土的含水量,如出现含水量?<?0--2%时,需加水均匀拌和;当(I’>?0+2%时,需要晾晒.如果施工现场条件允许的话,可采用分段填筑,分段晾晒,分段碾压的处理方法,并且尽量避开雨季施工. 34分层填筑,分层碾压路堤填筑直采用水平分层填筑法施工.采用机械压实时,分层的最大松铺厚度,不应超过30cm(机械摊铺不超过25em),填筑至路床顶面最后一层的最小压实厚度,不应小于8era.压实土层的密实度随深度递减,表面5em的密实度最高.施工中松铺厚度的控制采用插杆挂线,随机挖孔及水准量测综合控制.填料的摊铺采用平地机整平并辅以人工找平.路堤边缘往往压实不到位,土体松散,造成雨后滑坍,故施工中边缘部位要求宽填50era,以保证全宽路基的压实.因此段填方正处于山坡填筑,要求碾压时,定要由外侧向内侧开始碾压,如果由内侧向PI’~I碾压,将会对填料向9I-~,1挤推,造成边缘下沉.路基在压实过程中,并不是碾压遍数越多,压实效果越好,只有按试验路段中确定的碾压遍数进行碾压,才能保证每层的整个深度内的压实度处处均匀,达到设计规定的压实度.如碾压遍数过多,土的密实程度并不会有显着的提高,相反,会造成土体破坏,效果适得其反,且不经济.碾压过程中一定要控制好压路机的碾压速度,由试验路段确定.相邻两次的轮迹重叠应达到15,20era,保证压实均匀,不出现漏压现象.施工机械要求自重16T以上的振动压路机,推土机,平地机等,以保证碾压质量.35加强测试检验及压实控制某高填土路段要求填料最小强度,最大粒径,压实度.为保证压实效果,必须加强测试检验,检测方法采用灌砂法,检测频率为施工单位按每2000m检测4处,只有每一压实层,检验评定合格后,才允许填筑F一层,否则,需继续碾压处理,直至合格.当填料土质发生变化时,及同一填料填筑?科诺蠢2000m,后,必须重新做重型击实试验,确定最大干容重及最佳含水量,灌砂法所用的标准砂也必须经常标定,以保证压实度检测的准确可靠性,在灌砂法的操作工艺上,取土样的底面位置必须为每一压实层底部,以保证检测数据的真实有效.只有层层控制填土的压实度,才能保证全深度范围内的压实质量.3_6控制施工工艺,保证高填方路基的整体稳老l生当路堤在斜坡上填筑,其垂直路中线测得的原坡陡于1:5时,原地面要挖成台阶状,横坡陡峻地段的半填半挖路基,必须在山坡上从填方坡角向上挖成向内倾斜的台阶,坡度为,台阶宽度不应小于1m,并进行夯实.笔者所监理的高填方路段,所开台阶高1m,宽2m,向内倾斜,坡度不小于2%,利用小型机具进行夯实,施工中杜绝施工单位制造假台阶蒙混过关.为了进一步加强高填方路基的整体稳定陛.在地质条件较差路段,建议在台阶部位增设铺筑土工格栅的施工工艺.4地下水与地表水的排出水是引起路基各种病害的主要因素,我国南方省份年降水量大,山体地下水极其丰富,如处理不当,将会造成恶劣后果.为了将地下水畅通的排出路基以外.在肓沟修建过程中应注意:a检查盲沟基槽深度,底部高程,断面尺寸,平面位置;h检查盲沟基础(底部不透水层)强度,纵坡;c检查盲沟侧墙垂直度,钭坡度,纵向顺直度;d检查填筑的透水材料级配,含泥量,密实度,不同透水材料的填筑层次和土工合成材料.在以上项目的检查中,如发现不符合没计标准的,要及时纠正.随着路基填筑高度的增加,更应及时排除路基顶表积水,根据纵断面高程的变化,每隔25—30m设置一处临时排水水簸箕,这佯既防止了雨水冲刷边坡造成冲沟,又能将路基顶面积水排出,避免路基顶面积水引发的各种病害,为路基雨后及时施工创造了条件.(上接42页)重费.5结论综上所述,数控车削同普通车削相比,数控车削加工与普通车床切削加工大致相同.目前,数控车削的很多工艺及刀具资料都是以普通机械加工为依据,并不完全适用于数控机械加工,因此需要进一步专门深入研究.参考文献【lL械设计手册IMl北京:化学工业出版社,2004,矗惆济,周艳红.数控加工技术f.北京:国防工业出版社,2003,p1翟瑞波,白一几数控编程与操作实例[M1.北京:中国劳动和社会保障版社,2005.作者简介:李淑霞,大专学历,-=-:g~L实习指导教师一2O7一。
数控机床加工的切削用量

数控机床加工的切削用量包括切削速度V c (或主轴转速n)、切削深度a p 和进给量f ,其选用原则与普通机床基本相似,合理选择切削用量的原则是:粗加工时,以提高劳动生产率为主,选用较大的切削量;半精加工和精加工时,选用较小的切削量,保证工件的加工质量。
1. 数控车床切削用量 1)切削深度a p在工艺系统刚性和机床功率允许的条件下,尽可能选取较大的切削深度,以减少进给次数。
当工件的精度要求较高时,则应考虑留有精加工余量,一般为0.1~0.5mm 。
切削深度ap 计算公式:a p =式中: d w —待加工表面外圆直径,单位mm d m —已加工表面外圆直径,单位mm. 2)切削速度Vc① 车削光轴切削速度V c 光车切削速度由工件材料、刀具的材料及加工性质等因素所确定,表1为硬质合金外圆车刀切削速度参考表。
切削速度Vc 计算公式: Vc=式中: d —工件或刀尖的回转直径,单位mm n —工件或刀具的转速,单位r/min表1 硬质合金外圆车刀切削速度参考表2mw d d注:表中刀具材料切削钢及灰铸铁时耐用度约为60min。
②车削螺纹主轴转速n切削螺纹时,车床的主轴转速受加工工件的螺距(或导程)大小、驱动电动机升降特性及螺纹插补运算速度等多种因素影响,因此对于不同的数控系统,选择车削螺纹主轴转速n存在一定的差异。
下列为一般数控车床车螺纹时主轴转速计算公式:n≤–k式中:p—工件螺纹的螺距或导程,单位mm。
k—保险系数,一般为80。
3)进给速度进给速度是指单位时间内,刀具沿进给方向移动的距离,单位为mm/min,也可表示为主轴旋转一周刀具的进给量,单位为mm/r。
⑴确定进给速度的原则①当工件的加工质量能得到保证时,为提高生产率可选择较高的进给速度。
②切断、车削深孔或精车时,选择较低的进给速度。
③刀具空行程尽量选用高的进给速度。
④进给速度应与主轴转速和切削深度相适应。
⑵进给速度V f的计算V f = n f式中:n—车床主轴的转速,单位r/min。
(数控加工)数控加工的切削用量精编
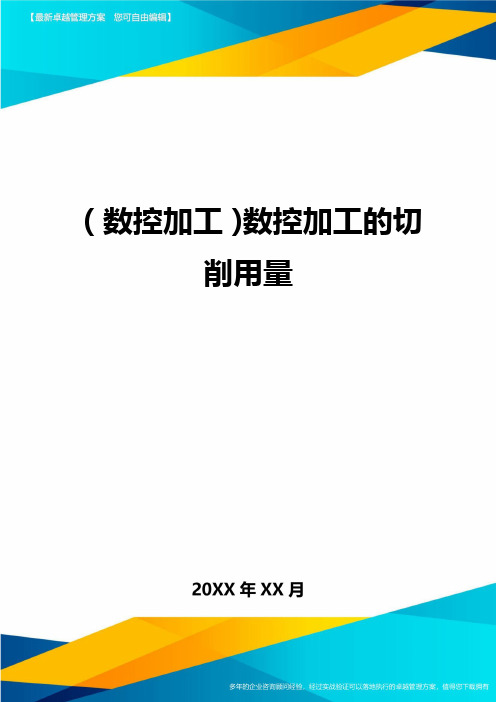
(数控加工)数控加工的切削用量数控加工的切削用量2009-6-119:42:00来源:作者:余英良,于辉阅读:1418次我要收藏1切削用量选择1.1数控加工花键轴的切削用量为了保证零件的加工精度,零件分为粗车加工和精车加工。
在粗、精车零件装夹方式和刀具选择的基础上,选定零件数控加工的切削参数如下:在数控精车车削加工中,零件轮廓轨迹的加工余量为0.8÷2=0.4mm。
主轴转速、背吃刀量等的选择参见表1。
表1数控加工花键轴工序卡及切削用量1.2数控加工轴承座的切削用量为了保证零件的加工精度,零件分为粗车加工和精车加工。
在粗、精车零件装夹方式和刀具选择的基础上,选定零件数控加工的切削参数如下:在数控精车车削加工中,零件轮廓轨迹的加工余量为0.8÷2=0.4mm。
主轴转速、背吃刀量等的选择参见表2。
表2数控加工轴承座工序卡及切削用量2相关内容概述金属切削加工的目的,就是用各种类型的金属切削刀具把J:件毛坯上的多余部分从毛坯上剥离开来,得到图样所要求的零件形状和尺寸。
图1车削加工中切削用量nextpage2.1切削用量切削用量是指机床在切削加工时的状态参数。
切削用量包括切削速度、进给速度和背吃刀量。
参见图1。
2.1.1切削速度切削刃上的切削点相对于工件运动的瞬时速度称为切削速度。
切削速度的单位为m/min。
切削速度和机床主轴转速之问进行转换的关系为:(1)2.1.2进给速度是刀具在单位时间内沿进给方向上相对于工件的位移量,单位为mm/min。
2.1.3背吃刀量己加工表面和待加工表面之问的垂直距离。
背吃刀量的计算公式为:(2)式(1)、式(2)中n为主轴(工件)转速,d为工件直径,dω、dm见图1。
在切削加工中,切削速度、进给速度和背吃刀量3个参数是相互关联的。
粗加工中,为提高效率,壹般采用较大的背吃刀量。
此时切削速度和进给速度相对较小;在半精加工和精加工阶段,壹般采用较大的切削速度、较小的进给量和背吃刀量,以获得较好的加工质量。
数控车削加工中的切削用量包括背吃刀量ap
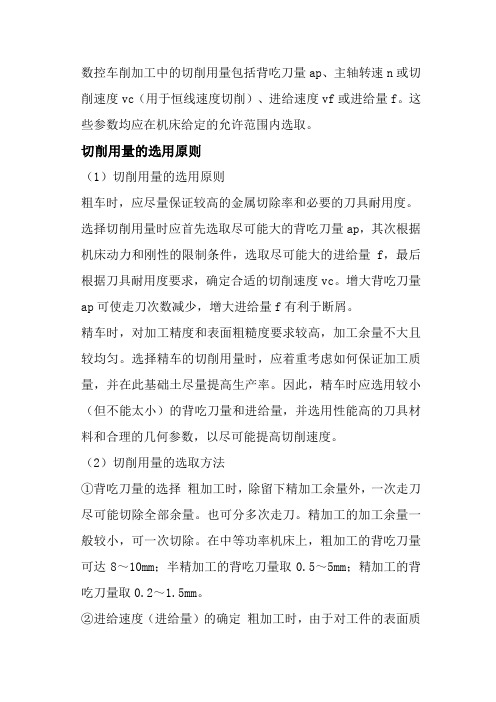
数控车削加工中的切削用量包括背吃刀量ap、主轴转速n或切削速度vc(用于恒线速度切削)、进给速度vf或进给量f。
这些参数均应在机床给定的允许范围内选取。
切削用量的选用原则(1)切削用量的选用原则粗车时,应尽量保证较高的金属切除率和必要的刀具耐用度。
选择切削用量时应首先选取尽可能大的背吃刀量ap,其次根据机床动力和刚性的限制条件,选取尽可能大的进给量f,最后根据刀具耐用度要求,确定合适的切削速度vc。
增大背吃刀量ap可使走刀次数减少,增大进给量f有利于断屑。
精车时,对加工精度和表面粗糙度要求较高,加工余量不大且较均匀。
选择精车的切削用量时,应着重考虑如何保证加工质量,并在此基础土尽量提高生产率。
因此,精车时应选用较小(但不能太小)的背吃刀量和进给量,并选用性能高的刀具材料和合理的几何参数,以尽可能提高切削速度。
(2)切削用量的选取方法①背吃刀量的选择粗加工时,除留下精加工余量外,一次走刀尽可能切除全部余量。
也可分多次走刀。
精加工的加工余量一般较小,可一次切除。
在中等功率机床上,粗加工的背吃刀量可达8~10mm;半精加工的背吃刀量取0.5~5mm;精加工的背吃刀量取0.2~1.5mm。
②进给速度(进给量)的确定粗加工时,由于对工件的表面质量没有太高的要求,这时主要根据机床进给机构的强度和刚性、刀杆的强度和刚性、刀具材料、刀杆和工件尺寸以及已选定的背吃刀量等因素来选取进给速度。
精加工时,则按表面粗糙度要求、刀具及工件材料等因素来选取进给速度。
进给速度νf 可以按公式ν f =f×n计算,式中f表示每转进给量,粗车时一般取0.3~0.8mm/r;精车时常取0.1~0.3mm/r;切断时常取0.05~0.2mm/r。
③切削速度的确定切削速度vc可根据己经选定的背吃刀量、进给量及刀具耐用度进行选取。
实际加工过程中,也可根据生产实践经验和查表的方法来选取。
粗加工或工件材料的加工性能较差时,宜选用较低的切削速度。
数控加工的切削用量

数控加工的切削用量2009-6-11 9:42:00 来源:作者:余英良,于辉阅读:1418次我要收藏1 切削用量选择1.1 数控加工花键轴的切削用量为了保证零件的加工精度,零件分为粗车加工和精车加工。
在粗、精车零件装夹方式与刀具选择的基础上,选定零件数控加工的切削参数如下:在数控精车车削加工中,零件轮廓轨迹的加工余量为0.8÷2=0.4 mm。
主轴转速、背吃刀量等的选择参见表1。
表1 数控加工花键轴工序卡及切削用量1.2 数控加工轴承座的切削用量为了保证零件的加工精度,零件分为粗车加工和精车加工。
在粗、精车零件装夹方式与刀具选择的基础上,选定零件数控加工的切削参数如下:在数控精车车削加工中,零件轮廓轨迹的加工余量为0.8÷2=0.4 mm。
主轴转速、背吃刀量等的选择参见表2。
表2 数控加工轴承座工序卡及切削用量2 相关内容概述金属切削加工的目的,就是用各种类型的金属切削刀具把J:件毛坯上的多余部分从毛坯上剥离开来,得到图样所要求的零件形状和尺寸。
图1 车削加工中切削用量nextpage 2.1 切削用量切削用量是指机床在切削加工时的状态参数。
切削用量包括切削速度、进给速度和背吃刀量。
参见图1。
2.1.1 切削速度切削刃上的切削点相对于工件运动的瞬时速度称为切削速度。
切削速度的单位为m/min。
切削速度与机床主轴转速之问进行转换的关系为:(1)2.1.2 进给速度是刀具在单位时间内沿进给方向上相对于工件的位移量,单位为mm/min。
2.1.3 背吃刀量己加工表面和待加工表面之问的垂直距离。
背吃刀量的计算公式为:(2)式(1)、式(2)中n为主轴(工件)转速,d为工件直径,dω、dm见图1。
在切削加工中,切削速度、进给速度和背吃刀量3个参数是相互关联的。
粗加工中,为提高效率,一般采用较大的背吃刀量。
此时切削速度和进给速度相对较小;在半精加工和精加工阶段,一般采用较大的切削速度、较小的进给量和背吃刀量,以获得较好的加工质量。
车削切削用量选取参考表

三、按表面粗糙度选择进给量的参考值
工件材料
粗糙度等级(Ra)
切削速度(m/min)
刀尖圆弧半径
0.5
1
2
进给量f mm/r
碳钢及合金碳钢
10~5
≤50
0.3~0.5
0.45~0.6
1
0.3
1.1
0.3
—
—
—
—
>18~30
1
0.3
1
0.3
1.1
0.3
1.3
0.4
1.4
0.4
—
—
>30~50
1.1
0.3
1
0.3
1.1
0.4
1.3
0.5
1.5
0.6
1.7
0.6
>50~80
1.1
0.3
1.1
0.4
1.2
0.4
1.4
0.5
1.6
0.6
1.8
0.7
>80~120
1.1
0.4
1.2
0.4
1.2
铸铁及铜合金
16×25
40
0.4~0.5
—
—
—
—
60
0.6~0.8
0.5~0.8
0.4~0.6
—
—
100
0.8~1.2
0.7~1
0.6~0.8
0.5~0.7
—
400
1~1.4
1~1.2
0.8~1
0.6~0.8
车削加工与刀具
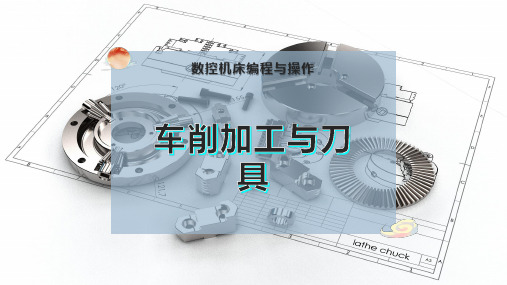
(4)主切削刃S
前刀面与后刀面相交处形成的切削
棱,用于切出工件上的过渡表面,是刀具主要的加工刃。
(5)副切削刃S’
前刀面与副后刀面相交处形成的切
削棱,主要作用是配合主切削刃,完成金属材料的切除。
(6)刀尖
主切削刃与副切削刃交接处形成的
切削点。刀尖有倒棱刀尖和倒圆刀尖两种。
数控机床加工的切削用量
车 刀 示 意 图
机床类型 数控车床 数控铣床 数控磨床 数控镗床
主运动 主轴(工件) 主轴(刀具) 主轴(砂轮刀具) 主轴(刀具)
进给运动 刀架 工作台
工作台(或砂轮轴) 工作台
数控机床加工的切削用量
(1)主运动 主运动是指机床提供的主要运动。主运动使刀具和工件
之间产生相对运动,从而使刀具的前刀面接近工件并对工件 进行切削。在车床上,主运动是机床上主轴的回转运动。这 一点对于普通车床和数控车床是一样的。
金属切除率是指每分钟切下工件材料的体积。它是衡量 切削效率高低的另一个指标。 (6)合成切削运动和合成切削速度
当主运动与进给运动同时进行时,刀具切削刃上某一点 相对于工件的运动称为合成切削运动,其大小与方向用合成 速度v表示,合成速度等于主运动与进给速度之和。
数控机床加工的切削用量
Vc V
Vf f
2)切削宽度aw
平行于加工表面度量的切削层尺寸, mm。 3)切削面积 Ac 切削层在基面投影中的面积。
数控机床加工的切削用量
切削层参数
数控机床编程与操作
数控机床加工的切削用量
2.切削用量
切削用量是指机床在切削加工时的状态参数(如图)。 不同类型的机床对切削用量参数的表述也略有不同,但其基 本的含义都是一致的。
数控机床加工的切削用量

数控机床加工的切削用量包括切削速度V c (或主轴转速n)、切削深度a p 和进给量f ,其选用原则与普通机床基本相似,合理选择切削用量的原则是:粗加工时,以提高劳动生产率为主,选用较大的切削量;半精加工和精加工时,选用较小的切削量,保证工件的加工质量。
1. 数控车床切削用量 1)切削深度a p在工艺系统刚性和机床功率允许的条件下,尽可能选取较大的切削深度,以减少进给次数。
当工件的精度要求较高时,则应考虑留有精加工余量,一般为0.1~0.5mm 。
切削深度ap计算公式:a p =式中: d w —待加工表面外圆直径,单位mm d m —已加工表面外圆直径,单位mm. 2)切削速度Vc① 车削光轴切削速度V c 光车切削速度由工件材料、刀具的材料及加工性质等因素所确定,表1为硬质合金外圆车刀切削速度参考表。
切削速度Vc 计算公式: Vc=式中: d —工件或刀尖的回转直径,单位mm n —工件或刀具的转速,单位r/min表1 硬质合金外圆车刀切削速度参考表2mw d d注:表中刀具材料切削钢及灰铸铁时耐用度约为60min。
②车削螺纹主轴转速n切削螺纹时,车床的主轴转速受加工工件的螺距(或导程)大小、驱动电动机升降特性及螺纹插补运算速度等多种因素影响,因此对于不同的数控系统,选择车削螺纹主轴转速n存在一定的差异。
下列为一般数控车床车螺纹时主轴转速计算公式:n≤–k式中:p—工件螺纹的螺距或导程,单位mm。
k—保险系数,一般为80。
3)进给速度进给速度是指单位时间内,刀具沿进给方向移动的距离,单位为mm/min,也可表示为主轴旋转一周刀具的进给量,单位为mm/r。
⑴确定进给速度的原则①当工件的加工质量能得到保证时,为提高生产率可选择较高的进给速度。
②切断、车削深孔或精车时,选择较低的进给速度。
③刀具空行程尽量选用高的进给速度。
④进给速度应与主轴转速和切削深度相适应。
⑵进给速度V f的计算 V f = n f式中:n—车床主轴的转速,单位r/min。
车削切削用量选取参考表

车削切削用量选取参考表
一、外圆车削背吃刀量选择表(端面切深减半)
K5()12.5S
2、粗车背吃刀量的景大值是受车床功率的大小决定的。
中尊功率机床可以达到8〜lOmm。
二、高速钢及硬质合金车刀车削外圆及端面的粗车进给量
1.断续切削、有冲击载荷时,乘以修正系数:k=0_75~0.85。
2、加工耐热钢尺其台金时,进给長应不大于ImmAo
3、无外皮时,表内进给昼应乘以系数:k=l.k
4.加工淬硬钢时,进给fi应减小。
硬度为HRC45-56时、乘以修正系教:0・8,硬度为HRC57・62,乘以修正系^:k=0.5o
三、按表面粗糙度选择进给量的参考值
四、车削切削速度参考数值表
五、外圆车削时切削速度公式中的系数和指数选择表
注:1、内表面加工(饉孔、孔内切槽、内表面成形车削)时,用外圆加工的车削
速度乘以系数0.9 O
2、用高速钢车刀加工结构钢、不锈钢尺铸钢,不用切削液时,车削速度乘以系数0.8。
3、用yr车刀对钢件切断尺切槽使用切削液时,车削速度乘以系数L4。
4、成形车削深轮廓尺复杂轮廓工件时,切削速度乘以系数0.85。
5、用高速钢车刀加工热处理钢件时,车削速度应减少:正火,乘以系数0.95; 退火,乘以系数0.9;调质,乘以系数0.8。
6、加工钢和铸鉄的机械性能改变时,车削速度的修正系kMv可按表《钢和铸铁的强度和硬度改变时车削速度的修正系敌kM»计算。
7、其他加工条件改变时,车削速度的修正系数见表《车削条件改变时的修正系数》。
六、车床切削速度计算表
2.
3、上述计算中:。
各类机床切削用量表
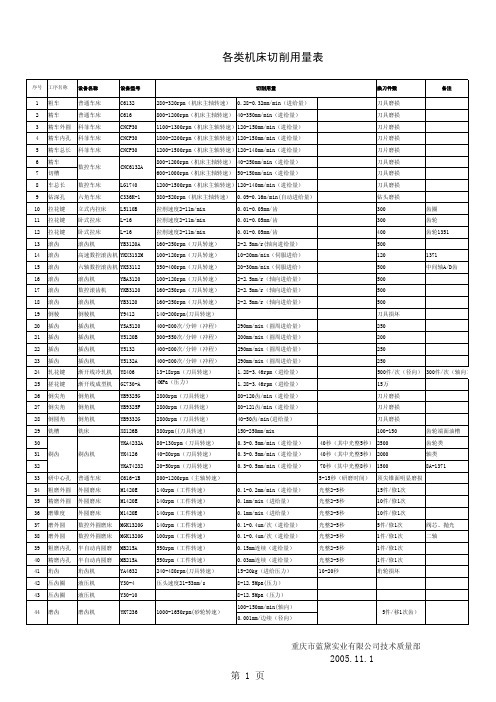
序号 工序名称 设备名称
设备型号
1 粗车
普通车床
C6132
2 精车
普通车床
C616
3 精车外圆 科菲车床
CNCP30
4 精车内孔 科菲车床
CNCP30
5 精车总长 科菲车床
CNCP30
6 精车 7 切槽
数控车床
CNC6132A
8 车总长 数控车床
LG1740
9 钻深孔 六角车床
C336K-1
8-12.5Mpa(压力)
1000-1650rpm(砂轮转速)
100-150mm/min(轴向) 0.001mm/边续(径向)
5件/移1次齿)
第1页
重庆市蓝黛实业有限公司技术质量部
2005.11.1
)
第2页
19 倒棱
倒棱机
Y9412
20 插齿
插齿机
YSA5120
21 插齿
插齿机
Y5120B
22 插齿
插齿机
Y5132
23 插齿
插齿机
Y5132A
24 轧花键 渐开线冷轧机 Y8406
25 搓花键 渐开线成型机 GZ730-A
26 倒尖角 倒角机
YB9325G
27 倒尖角 倒角机
YB9325F
28 倒圆角 倒角机
40秒(其中光整5秒) 2000
轴类
20-50rpm(刀具转速)
0.3-0.5mm/min(进给量)
70秒(其中光整8秒) 1500
8A-1371
800-1200rpm(主轴转速)
5-15秒(研磨时间) 顶尖锥面明显磨损
140rpm(工件转速)
0.1-0.2mm/min(进给量)
切削用量及加工余量的合理选择

削用量及加工余量的合理选择切削用量的选择,主要根据刀具耐用度和加工表面粗糟度,加工精度的要求。
切削用量愈大,刀具耐用度愈低。
切削速度Vc,进给量f和切削深度Ap刀具耐用度的影响不同,切削速度影响最大,进给量次之,切削深度影响最小。
(1)切削深度的选择切削深度应根据加工余量确定。
1)粗加工时,在留有精加工及半精加工的余量后,应尽可能一次走刀切除全部粗加工余量。
若粗切余量过大,不能一次切除,这时,应将第一次走刀的切削深度取大些,可占全部余量的2/3~3/4,以使精加工工序获得较小的表面粗糙度值及较高的加工精度。
2)切削零件表层有硬皮的铸、锻件或不锈钢等冷硬较严重的材料时,应使切削深度超过硬皮或冷硬层,以避免使切削刃在硬皮或冷硬层上切削。
(硬皮深度可达0.07~0.5mm)3)当冲击载荷较大(如断续切削)或工艺系统刚性较差时,应适当减小切削深度。
4)一般精切( 1.6!~ 0.8)时,可取=0.05~0.8mm;半精切( 6.3~ 3.2)时,可取=1.0~3.0mm.(2)进给量F的选择1)粗加工时,进给量主要受刀杆、刀具、机床、工件等的强度、刚度所能承受的切削力的限制,一般是根据刚度来选取。
2)精加工时,进给量主要受表面粗糙度要求的限制。
要求表面粗糙度小,应选取较小的F。
但F过小,切削厚度过薄,表面粗糙度反而大,而且刀具磨损加剧。
3)当刀具的副角较大,刀尖圆弧半径较大时,F可选较大值。
(3)切削速度的选择在保证刀具的经济耐用度及切削负荷不超过机床的额定功率的情况下选定切削速度。
1)粗车时,背后吃刀量和进给量均较大,故选较低的切削速度,精车时,则选较高的切削速度。
2)加工材料的加工性差时,切削速度选得低些。
如加工灰铸铁的切削速度比加工中碳钢低;而加工铝合金和铜合金的切削速度比加工中碳钢要高得多。
3)刀具材料的切削性能越好时,切削速度也可以越高。
如涂层硬质合金、陶瓷、金刚石和立方氮化硼刀具的切削速度。
切削用量的选择原则、方法
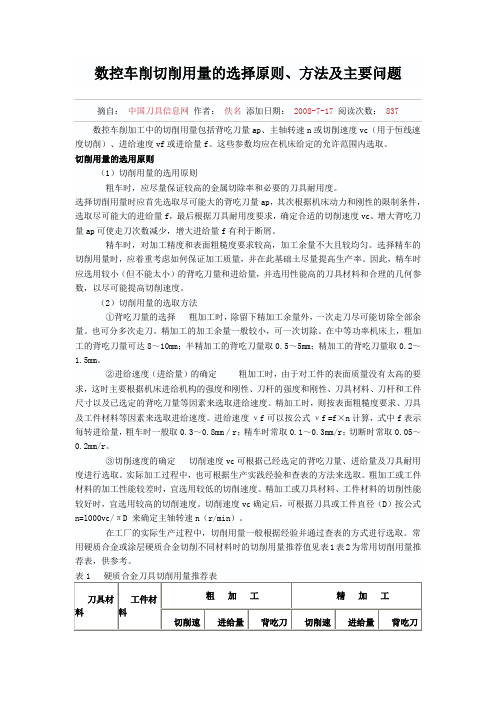
●螺纹加工程序段中指令的螺距值,相当于以进给量f(mm/r)表示的进给速度vf。如果将机床的主轴转速选择过高,其换算后的进给速度vf (mm/min)则必定大大超过正常值。
●刀具在其位移过程的始终,都将受到伺服驱动系统升降频率和数控装置插补运算速度的约束,由于升降频率特性满足不了加工需要等原因,则可能因主进给运动产生出的“超前”和“滞后”而导致部分螺牙的螺距不符合要求。
进给量(mm/r)
背吃刀量mm
硬质合金或涂层硬质合金
碳钢
220
0.2
3
260
0.l
0.4
低合金刚
1800.23来自2200.l0.4
高合金钢
120
0.2
3
160
0.l
0.4
铸铁
80
0.2
3
120
0.l
0.4
不锈钢
80
0.2
2
60
0.l
0.4
钛合金
40
0.2
1.5
150
0.l
0.4
灰铸铁
120
0.2
2
120
粗车时,应尽量保证较高的金属切除率和必要的刀具耐用度。
选择切削用量时应首先选取尽可能大的背吃刀量ap,其次根据机床动力和刚性的限制条件,选取尽可能大的进给量f,最后根据刀具耐用度要求,确定合适的切削速度vc。增大背吃刀量ap可使走刀次数减少,增大进给量f有利于断屑。
精车时,对加工精度和表面粗糙度要求较高,加工余量不大且较均匀。选择精车的切削用量时,应着重考虑如何保证加工质量,并在此基础土尽量提高生产率。因此,精车时应选用较小(但不能太小)的背吃刀量和进给量,并选用性能高的刀具材料和合理的几何参数,以尽可能提高切削速度。
车削切削用量选取参考表

0.75
YT5
170-220
0.5
335-490
0.4
中碳
175~225
1
52
0.2
165
200
0.18
YT15
305
0.18
520
0.13
4
40
0.4
125
150
0.5
YT14
200
0.4
395
0.25
8
30
0.5
100
120
0.75
YT5
160
0.5
305
0.4
碳 钢
低碳
100~200
4、加工淬硬钢时,进给量应减小。硬度为HRC45-56时,乘以修正系数:0.8, 硬度为HRC57-62,乘以修正系数:k=0.5。
三、按表面粗糙度选择进给量的参考值
工件材料
粗糙度等级(Ra)
切削速度(m/min)
刀尖圆弧半径
0.5
1
2
进给量fmm/r
碳钢及合金碳钢
10~5
≤50
0.3~0.5
0.45~0.6
1
0.3
1.1
0.3
—
—
—
—
>18~30
1
0.3
1
0.3
1.1
0.3
1.3
0.4
1.4
0.4
—
—
>30~50
1.1
0.3
1
0.3
1.1
0.4
1.3
0.5
1.5
0.6
1.7
0.6
>50~80
1.1
切削用量表

附2:切削用量表:
1.铣削速度V :指铣刀旋转时的圆周线速度,单位为m /min 。
计算公式:v=1000
n
d π
式中:d------铣刀直径,mm
n------主轴(铣刀);转速,r /
mm
从上式可得到:主轴(铣刀);转速 n=
d
v
1000 π 铣削速度v 推荐值
2.进给量F: 在铣削过程中,工件相对铣刀的移动速度称为进给量。
有三种表示方法:
1) 每齿进给量a f :mm/z 2) 每转进给量f :mm/r 3)
每分钟进给量v f :mm/min
三种进给量的关系为:v f=f·n=a f·z·n
1)铣削宽度a e:铣刀在一次进给中所切掉工件表层的宽度,单位为mm。
一般取铣刀直径的50%~60%
2) 背吃刀量a p:铣刀在一次进给中切掉工件表层的厚度,单位为mm。
一般粗加工立铣不得超过7mm,端铣2~5mm,精铣约0.1mm~0.5mm。
数控 车削切削用量选择概诉
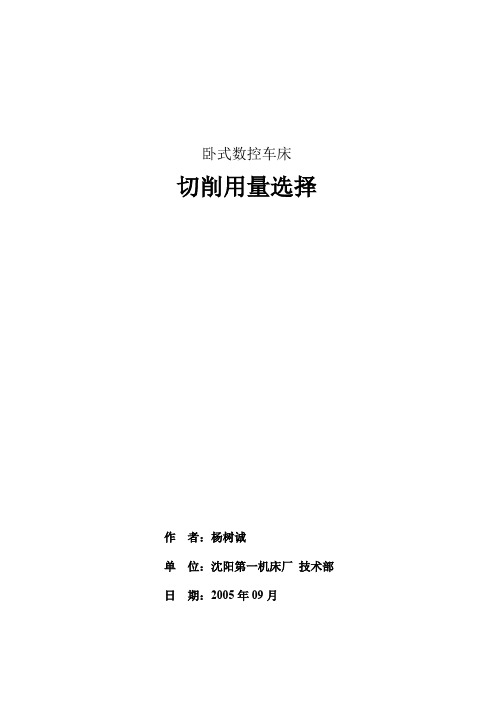
卧式数控车床切削用量选择作者:杨树诚单位:沈阳第一机床厂技术部日期:2005年09月本文着重提醒读者1.不要轻易按刀具样本的推荐值确定切削速度,那样刀具寿命很低。
一般情况下,硬质合金刀片可按刀具样本推荐值的0.64~0.71倍选择切削速度。
2.确定精加工和半精加工的进给量着眼于工件的表面粗糙度。
它还和刀尖半径有关。
文中列表表明三者对应关系,供选择进给量参考。
3.条件允许时希望粗加工吃刀深尽量大。
一方面有效提高生产率;一方面也为了消除表面硬皮.切除砂眼等缺陷,从而保护刀尖不与毛坯接触。
精加工时也不希望吃刀深太小,以免产生刮擦对粗糙度不利。
4.表5~表12列举了外圆.端面.内孔加工,切槽,车螺纹的切削用量推荐值。
供一般情况下采用。
目录一.原始资料 (1)二.选择切削用量的原则 (1)三.吃刀深αp (2)四.进给量f (2)五.切削速度V (4)六.切削用量推荐值 (5)切削用量选择关键词: 刀具耐用度 切削速度 表面粗糙度 进给量 吃刀深在售前服务编制加工工序卡以及调装设计中,都需要确定切削用量及计算节拍时间。
本文就卧式数控车床如何合理选择切削用量进行探讨。
一. 原始资料:无论编制加工工序卡-即制定工艺方案还是调装设计都需要掌握以下资 料,做为刀具选择.卡具设计以及选择切削用量的依据。
.1 工件图:包括形状.尺寸.公差.形位公差.粗糙度和其他技术要求。
特别强调的是本序 加工的部位必须明确,用于及可能影响装卡部位的形状要表示清楚。
2.毛坯图:毛坯形状.尺寸,加工余量,材料.硬度等。
3.生产纲领:即年产量或单件时间,这对招标项目尤为重要。
4.验收要求:机床验收时对工件考核什麽项目,有无Cp 值和其它要求。
5.用户对工件定位基准.卡紧面.辅助支承 等要求,或指定参考的卡具样式。
6. 对刀具选择要求:用国产刀具或国外指定厂家 的刀具,特殊刀具是否自备等。
7. 用户单位,件名.件号等也应标明,以便管理。
二 选择切削用量的原则:1. 总的要求:保证安全,不致发生人身事故或设备事故;保证加工质量。
车削用量参考表
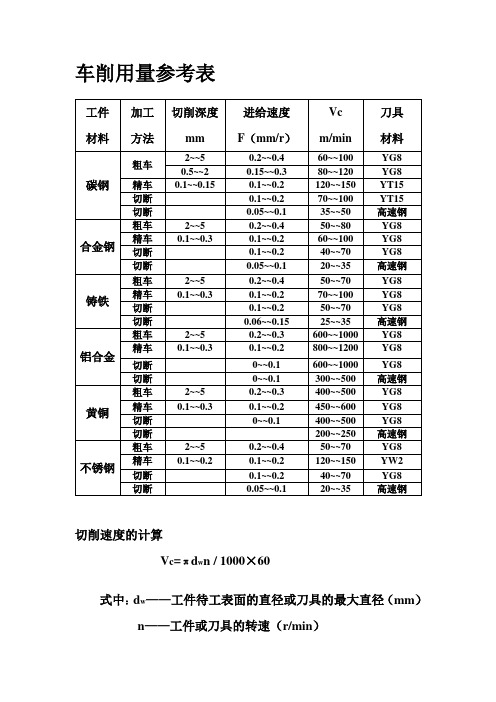
0.03~~0.18
中、高碳钢
220~~300
0.12~~0.25
0.07~~0.1
0.1~~0.2
0.03~~0.15
灰铸铁
180~~220
0.2~~0.4
0.1~~0.16
0.15~~0.3
0.05~~0.15
可锻铸铁
240~~280
0.1~~0.3
0.06~~0.09
0.1~~0.2
冷硬铸铁
10~~15
12~~18
30~~60
可锻铸铁
10~~15
20~~0
25~~40
35~~45
75~~110
低碳钢
10~~14
18~~28
20~~30
45~~70
中碳钢
10~~15
15~~25
18~~28
40~~60
高碳钢
10~~15
12~~20
30~~45
合金钢
35~~80
合金钢(硬)
30~~60
0.02~~0.08
合金钢
220~~280
0.1~~0.3
0.05~~0.08
0.12~~0.2
0.03~~0.08
工具钢
HRC36
0.12~~0.25
0.04~~0.08
0.07~~0.12
0.03~~0.08
铣刀的铣削速度Vc(m/min)
工件
材料
铣刀材料
碳素钢
高速钢
超高速刚
合金钢
碳化钛
碳化钨
铝合金
车削用量参考表
工件
材料
加工
方法
切削深度
数控车床常用数控刀具和切削用量的选择共70页文档
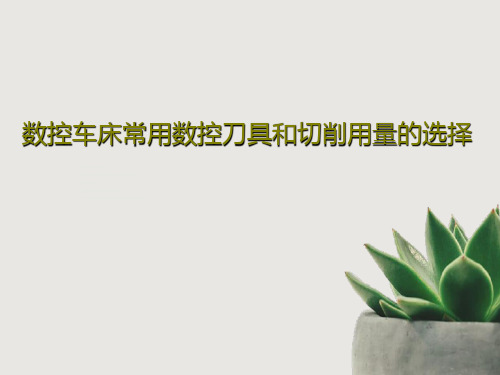
11、获得的成功越大,就越令人高兴 。野心 是使人 勤奋的 原因, 节制使 人枯萎 。 12、不问收获,只问耕耘。如同种树 ,先有 根茎, 再有枝 叶,尔 后花实 ,好好 劳动, 不要想 太多, 那样只 会使人 胆孝懒 惰,因 为不实 践,甚 至不接 触社会 ,难道 你是野 人。(名 言网) 13、不怕,不悔(虽然只有四个字,但 常看常 新。 14、我在心里默默地为每一个人祝福 。我爱 自己, 我用清 洁与节 制来珍 惜我的 身体, 我用智 慧和知 识充实 我的头 脑。 15、这世上的一切都借希望而完成。 农夫不 会播下 一粒玉 米,如 果他不 曾希望 它长成 种籽; 单身汉 不会娶 妻,如 果他不 曾希望 有小孩 ;商人 或手艺 人不会 工作, 如果他 不曾希 望因此 而有收 益。-- 马钉路 德。
▪
28、知之者不如好之者,好之者不如乐之者。——孔子
▪
29、勇猛、大胆和坚定的决心能够抵得上武器的精良。——达·芬奇
▪
30、意志是一个强壮的盲人,倚靠在明眼的跛子肩上。——叔本都过得舒适、愉快,这是不可能的,因为人类必须具备一种能应付逆境的态度。——卢梭
▪
27、只有把抱怨环境的心情,化为上进的力量,才是成功的保证。——罗曼·罗兰