轴承热处理后常见六大质量缺陷
热处理专科毕业设计GCr15轴承钢球的热处理工艺及缺陷分析

GCr15轴承钢球的热处理工艺及缺陷分析摘要:本论文重点对GCr15轴承钢球热处理工艺的设计进行了讨论,同时对热处理后其可能存在的热处理工艺缺陷进行了分析。
钢球在不同热处理工艺下虽然都能达到其使用要求,但所需的成本却大不相同,因此在满足其使用要求的同时也应该注意生产成本。
热处理常常因操作、原材料等产生缺陷,但只要有正确的热处理工艺并严格按工艺进行加工热处理缺陷也是可以避免的,即使产生了缺陷也可以采取相应的措施及时修复缺陷。
关键词:GCr15 轴承钢球热处理设计热处理工艺热处理缺陷引言滚动轴承是机械工业十分重要的基础标准件之一;滚动轴承依靠元件间的滚动接触来承受载荷,与滑动轴承相比:滚动轴承具有摩擦阻力小、效率高、起动容易、安装与维护简便等优点。
缺点是耐冲击性能较差、高速重载时寿命低、噪声和振动较大。
图 1 轴承及钢球实物图滚动轴承的基本结构(图 1):内圈、外圈、滚动体和保持架等四部分组成。
常用的滚动体有球、圆柱滚子、滚针、圆锥滚子。
轴承的内、外圈和滚动体,一般是用轴承钢(如GCr15、GCr15SiMn)制造,热处理后硬度应达到61~65HRC。
当滚动体是圆柱或滚针时,有时为了减小轴承的径向尺寸,可省去内圈、外圈或保持架,这时的轴颈或轴承座要起到内圈或外圈的作用。
为满足使用中的某些需要,有些轴承附加有特殊结构或元件,如外圈带止动环、附加防尘盖等。
滚动轴承钢球的工作条件极为复杂,承受着各类高的交变应力。
在每一瞬间,只有位于轴承水平面直径以下的那几个钢球在承受载荷,而且作用在这些钢球的载荷分布也不均匀。
力的变化由零增加到最大,再由最大减小到零,周而往复得增大和减小。
在运转过程中,钢球除受到外加载荷外,还受到由于离心力所引起的载荷,这个载荷随轴承转速的提高而增加。
滚动体与套圈及保持架之间还有相对滑动,产生相对摩擦。
滚动体和套圈的工作面还受到含有水分或杂质的润滑油的化学侵蚀。
在某些情况下,轴承零件还承受着高温低温和高腐蚀介质的影响。
几种常见热处理缺陷介绍
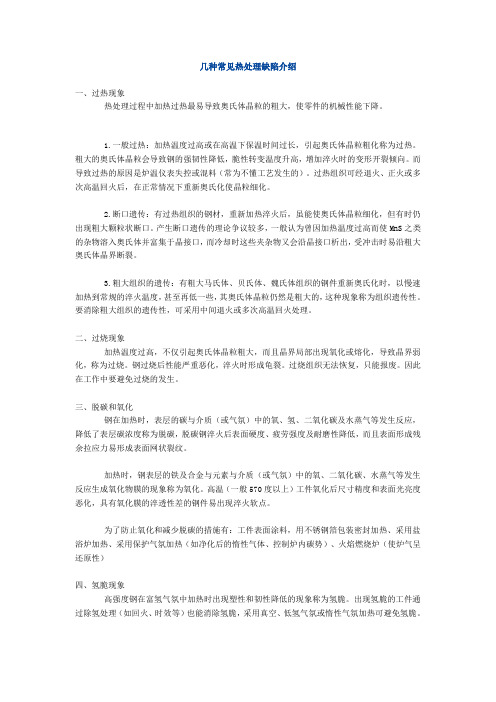
几种常见热处理缺陷介绍一、过热现象热处理过程中加热过热最易导致奥氏体晶粒的粗大,使零件的机械性能下降。
1.一般过热:加热温度过高或在高温下保温时间过长,引起奥氏体晶粒粗化称为过热。
粗大的奥氏体晶粒会导致钢的强韧性降低,脆性转变温度升高,增加淬火时的变形开裂倾向。
而导致过热的原因是炉温仪表失控或混料(常为不懂工艺发生的)。
过热组织可经退火、正火或多次高温回火后,在正常情况下重新奥氏化使晶粒细化。
2.断口遗传:有过热组织的钢材,重新加热淬火后,虽能使奥氏体晶粒细化,但有时仍出现粗大颗粒状断口。
产生断口遗传的理论争议较多,一般认为曾因加热温度过高而使MnS之类的杂物溶入奥氏体并富集于晶接口,而冷却时这些夹杂物又会沿晶接口析出,受冲击时易沿粗大奥氏体晶界断裂。
3.粗大组织的遗传:有粗大马氏体、贝氏体、魏氏体组织的钢件重新奥氏化时,以慢速加热到常规的淬火温度,甚至再低一些,其奥氏体晶粒仍然是粗大的,这种现象称为组织遗传性。
要消除粗大组织的遗传性,可采用中间退火或多次高温回火处理。
二、过烧现象加热温度过高,不仅引起奥氏体晶粒粗大,而且晶界局部出现氧化或熔化,导致晶界弱化,称为过烧。
钢过烧后性能严重恶化,淬火时形成龟裂。
过烧组织无法恢复,只能报废。
因此在工作中要避免过烧的发生。
三、脱碳和氧化钢在加热时,表层的碳与介质(或气氛)中的氧、氢、二氧化碳及水蒸气等发生反应,降低了表层碳浓度称为脱碳,脱碳钢淬火后表面硬度、疲劳强度及耐磨性降低,而且表面形成残余拉应力易形成表面网状裂纹。
加热时,钢表层的铁及合金与元素与介质(或气氛)中的氧、二氧化碳、水蒸气等发生反应生成氧化物膜的现象称为氧化。
高温(一般570度以上)工件氧化后尺寸精度和表面光亮度恶化,具有氧化膜的淬透性差的钢件易出现淬火软点。
为了防止氧化和减少脱碳的措施有:工件表面涂料,用不锈钢箔包装密封加热、采用盐浴炉加热、采用保护气氛加热(如净化后的惰性气体、控制炉内碳势)、火焰燃烧炉(使炉气呈还原性)四、氢脆现象高强度钢在富氢气氛中加热时出现塑性和韧性降低的现象称为氢脆。
热处理常见缺陷分析与对策-学习总结
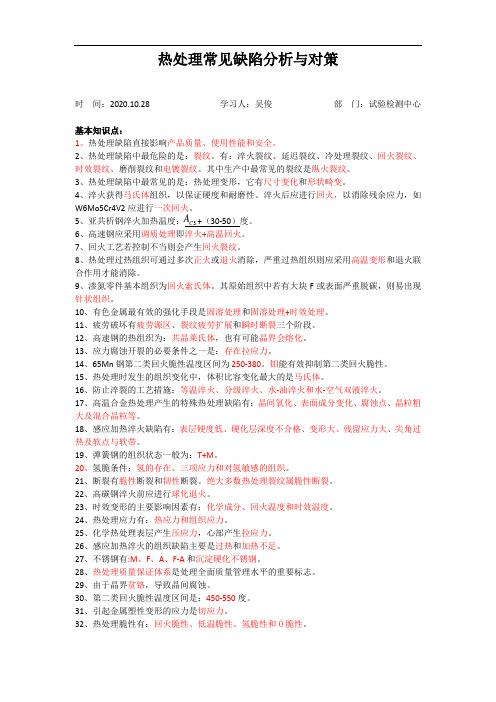
热处理常见缺陷分析与对策时 间:2020.10.28 学习人:吴俊 部 门:试验检测中心基本知识点:1、热处理缺陷直接影响产品质量、使用性能和安全。
2、热处理缺陷中最危险的是:裂纹。
有:淬火裂纹、延迟裂纹、冷处理裂纹、回火裂纹、时效裂纹、磨削裂纹和电镀裂纹。
其中生产中最常见的裂纹是纵火裂纹。
3、热处理缺陷中最常见的是:热处理变形,它有尺寸变化和形状畸变。
4、淬火获得马氏体组织,以保证硬度和耐磨性。
淬火后应进行回火,以消除残余应力,如W6Mo5Cr4V2应进行一次回火。
5、亚共析钢淬火加热温度: +(30-50)度。
6、高速钢应采用调质处理即淬火+高温回火。
7、回火工艺若控制不当则会产生回火裂纹。
8、热处理过热组织可通过多次正火或退火消除,严重过热组织则应采用高温变形和退火联合作用才能消除。
9、渗氮零件基本组织为回火索氏体。
其原始组织中若有大块F 或表面严重脱碳,则易出现针状组织。
10、有色金属最有效的强化手段是固溶处理和固溶处理+时效处理。
11、疲劳破坏有疲劳源区、裂纹疲劳扩展和瞬时断裂三个阶段。
12、高速钢的热组织为:共晶莱氏体,也有可能晶界会熔化。
13、应力腐蚀开裂的必要条件之一是:存在拉应力。
14、65Mn 钢第二类回火脆性温度区间为250-380。
钼能有效抑制第二类回火脆性。
15、热处理时发生的组织变化中,体积比容变化最大的是马氏体。
16、防止淬裂的工艺措施:等温淬火、分级淬火、水-油淬火和水-空气双液淬火。
17、高温合金热处理产生的特殊热处理缺陷有:晶间氧化、表面成分变化、腐蚀点、晶粒粗大及混合晶粒等。
18、感应加热淬火缺陷有:表层硬度低、硬化层深度不合格、变形大、残留应力大、尖角过热及软点与软带。
19、弹簧钢的组织状态一般为:T+M 。
20、氢脆条件:氢的存在、三项应力和对氢敏感的组织。
21、断裂有脆性断裂和韧性断裂。
绝大多数热处理裂纹属脆性断裂。
22、高碳钢淬火前应进行球化退火。
23、时效变形的主要影响因素有:化学成分、回火温度和时效温度。
轴承零件经热处理后会出现哪些问题

轴承零件经热处理后会出现哪些问题轴承零件经热处理后常见的质量缺陷有:淬火显微组织过热、欠热、淬火裂纹、硬度不够、热处理变形、表面脱碳、软点等。
1.过热从轴承零件粗糙口上可观察到淬火后的显微组织过热。
但要确切判断其过热的程度必须观察显微组织。
若在GCr15钢的淬火组织中出现粗针状马氏体,则为淬火过热组织。
形成原因可能是淬火加热温度过高或加热保温时间太长造成的全面过热;也可能是因原始组织带状碳化物严重,在两带之间的低碳区形成局部马氏体针状粗大,造成的局部过热。
过热组织中残留奥氏体增多,尺寸稳定性下降。
由于淬火组织过热,钢的晶体粗大,会导致零件的韧性下降,抗冲击性能降低,轴承的寿命也降低。
过热严重甚至会造成淬火裂纹。
2.欠热淬火温度偏低或冷却不良则会在显微组织中产生超过标准规定的托氏体组织,称为欠热组织,它使硬度下降,耐磨性急剧降低,影响轴承寿命。
3.淬火裂纹轴承零件在淬火冷却过程中因内应力所形成的裂纹称淬火裂纹。
造成这种裂纹的原因有:由于淬火加热温度过高或冷却太急,热应力和金属质量体积变化时的组织应力大于钢材的抗断裂强度;工作表面的原有缺陷(如表面微细裂纹或划痕)或是钢材内部缺陷(如夹渣、严重的非金属夹杂物、白点、缩孔残余等)在淬火时形成应力集中;严重的表面脱碳和碳化物偏析;零件淬火后回火不足或未及时回火;前面工序造成的冷冲应力过大、锻造折叠、深的车削刀痕、油沟尖锐棱角等。
总之,造成淬火裂纹的原因可能是上述因素的一种或多种,内应力的存在是形成淬火裂纹的主要原因。
淬火裂纹深而细长,断口平直,破断面无氧化色。
它在轴承套圈上往往是纵向的平直裂纹或环形开裂;在轴承钢球上的形状有S形、T形或环型。
淬火裂纹的组织特征是裂纹两侧无脱碳现象,明显区别与锻造裂纹和材料裂纹。
4.热处理变形轴承零件在热处理时,存在有热应力和组织应力,这种内应力能相互叠加或部分抵消,是复杂多变的,因为它能随着加热温度、加热速度、冷却方式、冷却速度、零件形状和大小的变化而变化,所以热处理变形是难免的。
滚动轴承常见的失效形式和原因分析范文

滚动轴承常见的失效形式及原因分析+浪逐风尖2008-11-05 10:55滚动轴承在使用过程中,由于很多原因造成其性能指标达不到使用要求时就产生了失效或损坏.常见的失效形式有疲劳剥落、磨损、塑性变形、腐蚀、烧伤、电腐蚀、保持架损坏等。
一,疲劳剥落疲劳有许多类型,对于滚动轴承来说主要是指接触疲劳。
滚动轴承套圈各滚动体表面在接触应力的反复作用下,其滚动表面金属从金属基体呈点状或片状剥落下来的现象称为疲劳剥落。
点蚀也是由于材料疲劳引起一种疲劳现象,但形状尺寸很小,点蚀扩展后将形成疲劳剥落。
疲劳剥落的形态特征一般具有一定的深度和面积,使滚动表面呈凹凸不平的鳞状,有尖锐的沟角.通常呈显疲劳扩展特征的海滩装纹路.产生部位主要出现在套圈和滚动体的滚动表面.轴承疲劳失效的机理很复杂,也出现了多种分析理论,如最大静态剪应力理论、最大动态剪应力理论、切向力理论、表面微小裂纹理论、油膜剥落理论、沟道表面弯曲理论、热应力理论等。
这些理论中没有一个理论能够全面解释疲劳的各种现象,只能对其中的部分现象作出解释。
目前对疲劳失效机理比较统一的观点有:1、次表面起源型次表面起源型认为轴承在滚动接触部位形成油膜的条件下运转时,滚动表面是以内部(次表面)为起源产生的疲劳剥落。
2、表面起源型表面起源型认为轴承在滚动接触部位未形成油膜或在边界润滑状态下运转时,滚动表面是以表面为起源产生的疲劳剥落。
3、工程模型工程模型认为在一般工作条件下,轴承的疲劳是次表面起源型和表面起源型共同作用的结果。
疲劳产生的原因错综复杂,影响因素也很多,有与轴承制造有关的因素,如产品设计、材料选用、制造工艺和制造质量等;也有与轴承使用有关的因素,如轴承选型、安装、配合、润滑、密封、维护等。
具体因素如下:A、制造因素1、产品结构设计的影响产品的结构设计是根据使用性能目标值来确定的,这些目标值如载荷容量、寿命、精度、可靠性、振动、磨损、摩擦力矩等。
在设计时,由于各种原因,会造成产品设计与使用的不适用或脱节,甚至偏离了目标值,这种情况很容易造成产品的早期失效。
轴承失效的九个阶段
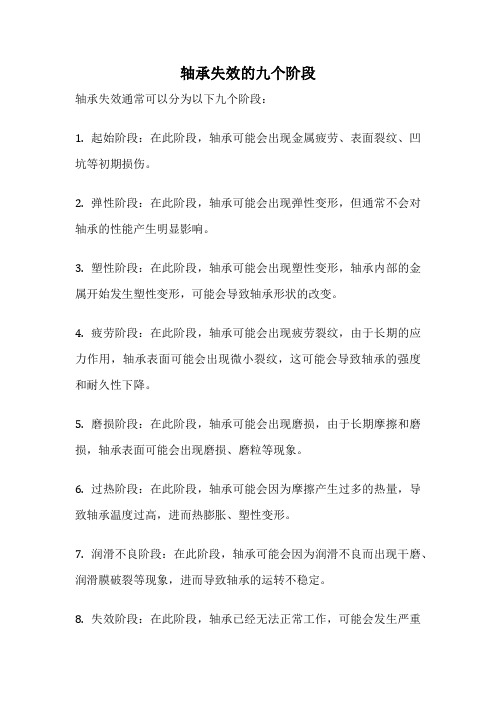
轴承失效的九个阶段
轴承失效通常可以分为以下九个阶段:
1. 起始阶段:在此阶段,轴承可能会出现金属疲劳、表面裂纹、凹坑等初期损伤。
2. 弹性阶段:在此阶段,轴承可能会出现弹性变形,但通常不会对轴承的性能产生明显影响。
3. 塑性阶段:在此阶段,轴承可能会出现塑性变形,轴承内部的金属开始发生塑性变形,可能会导致轴承形状的改变。
4. 疲劳阶段:在此阶段,轴承可能会出现疲劳裂纹,由于长期的应力作用,轴承表面可能会出现微小裂纹,这可能会导致轴承的强度和耐久性下降。
5. 磨损阶段:在此阶段,轴承可能会出现磨损,由于长期摩擦和磨损,轴承表面可能会出现磨损、磨粒等现象。
6. 过热阶段:在此阶段,轴承可能会因为摩擦产生过多的热量,导致轴承温度过高,进而热膨胀、塑性变形。
7. 润滑不良阶段:在此阶段,轴承可能会因为润滑不良而出现干磨、润滑膜破裂等现象,进而导致轴承的运转不稳定。
8. 失效阶段:在此阶段,轴承已经无法正常工作,可能会发生严重
的磨损、断裂、脱层等故障,导致轴承失效。
9. 结束阶段:在此阶段,轴承已经完全失效,无法继续使用,需要进行更换和修复。
轴承表面磨削出现缺陷的原因和分析

轴承表面磨削出现缺陷的原因和分析轴承在磨加工过程中,其工作表面是通过高速旋转的砂轮进行磨削的,因此在磨削时如果不按作业指导书进行操作和调整设备,就会在轴承工作表面出现种种缺陷,以致影响轴承的整体质量。
轴承在精密磨削时,由于粗糙要求很高,工作表面出现的磨削痕迹往往能用肉眼观察到其表面磨削痕迹主要有以下几种。
表现出现交叉螺旋线痕迹出现这种痕迹的原因主要是由于砂轮的母线平直性差,存在凹凸现象,在磨削时,砂轮与工件仅是部分接触,当工件或砂轮数次往返运动后,在工件表现就会再现交叉螺旋线且肉眼可以观察到。
这些螺旋线的螺距与工件台速度、工件转速大小有关,同时也与砂轮轴心线和工作台导轨不平行有关。
(一)螺旋线形成的主要原因1.砂轮修整不良,边角未倒角,未使用冷却液进行修整;2.工作台导轨导润滑油过多,致使工作台漂浮;3.机床精度不好;4.磨削压力过大等。
(二)螺旋线形成的具有原因1.V形导轨刚性不好,当磨削时砂轮产生偏移,只是砂轮边缘与工作表面接触;2.修整吵轮时工作台换向速度不稳定,精度不高,使砂轮某一边缘修整略少;3.工件本身刚性差;4.砂轮上有破碎太剥落的砂粒和工件磨削下的铁屑积附在砂轮表面上,为此应将修整好的砂轮用冷却水冲洗或刷洗干净;5.砂轮修整不好,有局部凸起等。
表面出现鱼鳞状表面再现鱼鳞状痕迹的主要原因是由于砂轮的切削刃不够锋利,在磨削时发生“啃住”现象,此时振动较大。
造成工件表面出现鱼鳞状痕迹的具体原因是:1.砂轮表面有垃圾和油污物;2.砂轮未修整圆;3.砂轮变钝。
修整不够锋利;4.金刚石紧固架不牢固,金刚石摇动或金刚石质量不好不尖锐;5.砂轮硬度不均匀等。
工作面拉毛表面再现拉毛痕迹的主要原因是由于粗粒度磨粒脱落后,磨粒夹在工件与砂轮之间而造成。
工件表面在磨削时被拉毛的具体原因是:1.粗磨时遗留下来的痕迹,精磨时未磨掉;2.冷却液中粗磨粒与微小磨粒过滤不干净;3.粗粒度砂轮刚修整好时磨粒容易脱落;4.材料韧性有效期或砂轮太软;5.磨粒韧性与工件材料韧性配合不当等。
谈轴承热处理的质量和新技术的研发

2 1 第 6 总 第 1 7期 0 0年 期 9
技术 工程
谈轴承热处理 的质量和新技术的研发
朱 俊
( 汉 风 神 汽 车修 理 厂 。湖 北 武汉 4 0 5 ) 武 3 0 5
摘 要 :根 据 轴 承 的结 构 特 点 和 对 轴 承用 钢 热 处 理 的 基本 要 求 ,本 文 介绍 r 承 零 部 件 的热 处理 技 术 、轴 承 热 处 理 的质 量 缺 轴
轴 承 钢 主要 用 于制 造 滚 动轴 承 的 滚 动体 和套 圈 。由于 轴承 应具 备 长寿命 、高 精度 、低 发热 量 、
炼 、电渣重 熔 、电子束 重 熔 等轴 承 钢 的 冶炼 技术 。 而 大 批 量 轴 承 钢 的冶 炼 由电弧 炉 熔 炼 ,发 展 成 各 种类 型初炼 炉 加炉外 精炼 。 在 热处 理 丁 艺 方 面 ,由 车底 式 炉 、罩 式 炉 发 展 成 连 续 可控 气 氛 退 火 炉 热 处 理 。 目前 ,连续 热 处理 炉 型最 长 为 1 0 5 m,加 _ 生 产 轴 承 钢 的球 化 组 T 织 稳定 和均 匀 ,脱 碳层 小 ,消耗 能量低 。 轴 承零 件 在 热 处 理 时 ,存 在 有 热 应 力 和 组 织 应 力 ,这 种 内应 力 能 相 互 叠 加 或 部分 抵 消 ,是 复 杂 多变 的 , 为 它 能 随 着 加 热 温 度 、加 热 速 度 、 冷 却 方 式 、冷却 速 度 、零 件 形 状 和 大 小 的 变 化 而 变 化 ,所 以热 处理 变形 是难 免 的 。认 识 和 掌 握 它 的变 化 规 律 可 以使 轴 承 零 件 的 变 形 ( 套 圈 的 椭 如
高 的要 求 。轴 承 寿 命 的影 响 因 素 很 多 ,其 中材 料
轴承零件锻造常见的加热缺陷及解决方法

内燃机与配件0引言中大型轴承零件制造工艺一般要经过钢材下料→锻造→去应力退火→金属切削加工→热处理→磨削加工→零件检验→成品装配→成品检测试验等工序。
而锻造是轴承零件加工的首道工序,也是所有后工序基础。
锻造质量的好坏,直接影响后工序加工和成品轴承的综合机械性能和轴承使用寿命。
轴承钢(常用GCr15、GCr15SiMn )锻造始锻温度为1050~1100℃之间、终锻温度为800~850℃之间。
在这一区域温度范围内,轴承钢塑性、锻造工艺性、获得的内部组织等关键性技术指标都较好。
由于是在高温状态下加工,轴承套圈热锻件在加热过程中不可避免地会产生氧化皮、脱碳、过热、过烧、加热裂开(内部裂纹)、折叠等缺陷,从而导致金属材料损耗过多,甚至废品。
也为后工序加工留下的质量隐患,且某些隐患在后工序加工过程中是不可完全修复的或者是不可逆的。
因此,理解上述加热缺陷产生的机理,掌握正确的加热工艺方法,尽最大可能减少或防止这些缺陷的产生,是提高锻件质量和锻造水平重要的有效途径之一,也是衡量锻造水平高低的重要技术指标之一。
本文从生产实践中总结出几种常见的轴承钢加热缺陷及防止办法如下:1氧化皮轴承钢锻件在加热过程中很容易产生氧化皮,产生的氧化皮极有可能会随着辗扩过程卷入到零件表面的辗扩流线方向,有的粗大,有的细如发丝,深浅不一,深度较深时,后工序不易及时发现,只有到成品零件才能看见。
氧化皮的产生同时造成锻件原材料的损耗,锻件每加热一次,便有1.5~3%的金属被氧化烧损。
另外氧化皮的产生降低了锻件表面的质量,被压入锻件内部时表面形成了凹陷并影响锻件的精度,如果氧化皮不处理,直接进行锻打还会导致锻件组织和性能的不均匀;如果氧化皮过硬就变相地降低了模具的使用寿命。
严重影响锻件的表面质量、锻模的精度和寿命,特别是对轴承寿命危害极大。
产生氧化皮的主要原因是因为金属表面的元素与炉气中O 2、CO 2、H 2O 及SO 2发生化学反应所致。
轴承套圈的常见缺陷及预防措施
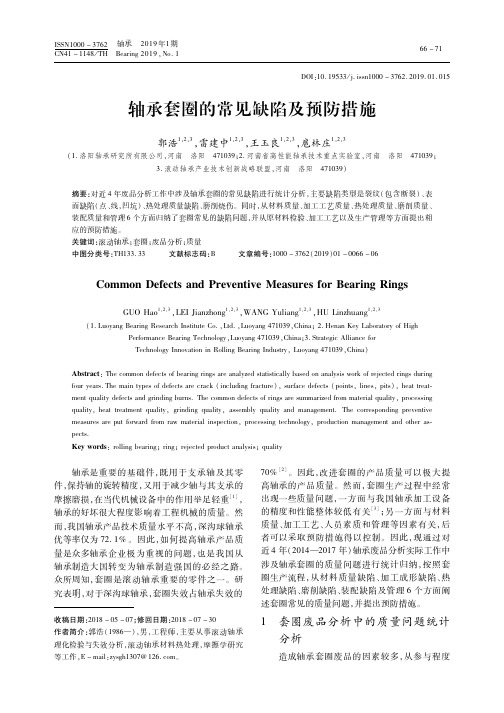
轴承套圈的常见缺陷及预防措施
郭浩1,2,3,雷建中1,2,3,王玉良1,2,3,扈林庄1,2,3
CommonDefectsandPreventiveMeasuresforBearingRings
GUOHao1,2,3,LEIJianzhong1,2,3,WANGYuliang1,2,3,HULinzhuang1,2,3
(1.LuoyangBearingResearchInstituteCo.,Ltd.,Luoyang471039,China;2.HenanKeyLaboratoryofHigh PerformanceBearingTechnology,Luoyang471039,China;3.StrategicAlliancefor TechnologyInnovationinRollingBearingIndustry,Luoyang471039,China)
(1.洛阳轴承研究所有限公司,河南 洛阳 471039;2.河南省高性能轴承技术重点实验室,河南 洛阳 471039; 3.滚动轴承产业技术创新战略联盟,河南 洛阳 471039)
摘要:对近 4年废品分析工作中涉及轴承套圈的常见缺陷进行统计分析,主要缺陷类型是裂纹(包含断裂)、表 面缺陷(点、线,凹坑)、热处理质量缺陷、磨削烧伤。同时,从材料质量、加工工艺质量、热处理质量、磨削质量、 装配质量和管理 6个方面归纳了套圈常见的缺陷问题,并从原材料检验、加工工艺以及生产管理等方面提出相 应的预防措施。 关键词:滚动轴承;套圈;废品分析;质量 中图分类号:TH133.33 文献标志码:B 文章编号:1000-3762(2019)01-0066-06
轴承产品缺陷分析报告

轴承产品缺陷分析报告滚动轴承和滑动轴承是应用在转动设备中应用最为广泛的机械零件,是轴及其它旋转构件的重要支承。
在日常的使用与维修中发现,轴承同时也是最容易产生故障的零件,对轴承零件的缺陷预测与分析具有很高的经济价值,所以轴承工作状态实时监控和诊断的研究受到广泛重视。
由于滚动轴承与滑动轴承在缺陷方面有许多共同点,缺陷分析方法可以通用,所以本文以讨论滚动轴承作为重点。
1.滚动轴承常见缺陷故障由于滚动轴承在实际生产中应用广泛,其产生的故障现象也多种多样,常见的有疲劳剥落、过量的永久变形和磨损。
1.疲劳剥落轴承在正常的条件下使用,内圈、外圈和滚动体上的接触应力是变化的,工作一段时间后,接触表面就可能发生疲劳点蚀,以致造成疲劳剥落。
所以疲劳剥落是轴承的正常失效形式,它决定了轴承的工作寿命。
2.过量的永久变形轴承在转速很低或者间歇往复摆动的工作状态时,在过大的静载荷或冲击载荷作用下,会使套圈滚道和滚动体接触处的局部应力超过材料的屈服强度,以致在表面发生过大的塑性变形,使轴承不能正常工作3.磨损在润滑不良和密封不严的情况下,轴承工作接触面容易发生磨损,转速越高,磨损越严重。
磨损会使轴承的游隙增加,振动和噪声增大,各项技术性能急剧下降,导致轴承失效。
此外,轴承还有胶合、烧伤、轴圈断裂、滚动体压碎、保持架磨损和断裂、锈蚀等失效形式。
在正常的使用条件下,这些失效是可以避免的,因此称为非正常失效。
2.轴承缺陷诊断方法轴承缺陷常用诊断分析方法可概括为以下几种:(1)检测润滑油温度、轴承温度及主油道润滑油压力波等物理参数(2)油样分析包括理化分析、污染度测试、发射光谱分析、红外线分析和铁谱分析(3)振动分析(4)声发射(AE)分析以上各种方法各有其特点,能够在一定程度上反应轴承缺陷。
第一种方法安装传感器简单、成本低但不实用,主要原因是测量温度有其滞后性,不能实时预测轴承缺陷。
油样分析只能测量油润滑轴承,但不能测量脂润滑轴承。
滚动轴承钢的热处理工艺
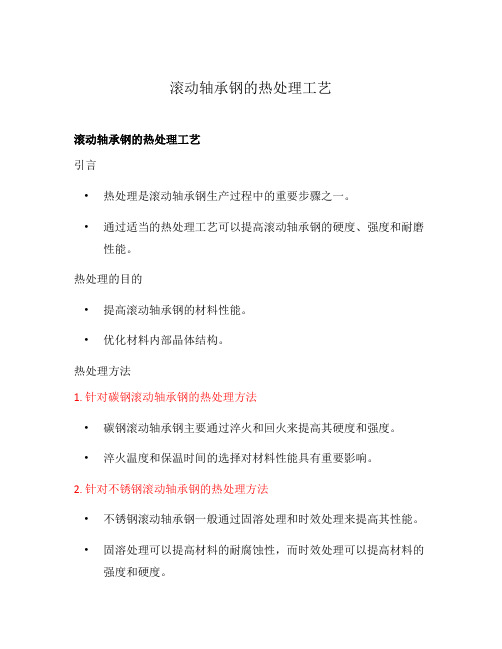
滚动轴承钢的热处理工艺滚动轴承钢的热处理工艺引言•热处理是滚动轴承钢生产过程中的重要步骤之一。
•通过适当的热处理工艺可以提高滚动轴承钢的硬度、强度和耐磨性能。
热处理的目的•提高滚动轴承钢的材料性能。
•优化材料内部晶体结构。
热处理方法1. 针对碳钢滚动轴承钢的热处理方法•碳钢滚动轴承钢主要通过淬火和回火来提高其硬度和强度。
•淬火温度和保温时间的选择对材料性能具有重要影响。
2. 针对不锈钢滚动轴承钢的热处理方法•不锈钢滚动轴承钢一般通过固溶处理和时效处理来提高其性能。
•固溶处理可以提高材料的耐腐蚀性,而时效处理可以提高材料的强度和硬度。
热处理工艺参数的选择•温度:热处理温度的选择要根据滚动轴承钢的材料成分和应用需求来确定。
•时间:保温时间对材料的相变和组织形成有重要影响,需要根据具体材料进行优化选择。
热处理设备与工艺控制•热处理设备应具备稳定的温度控制和加热均匀性。
•工艺控制要对温度、时间和冷却速率进行准确控制。
结论•滚动轴承钢的热处理工艺对其性能有重要影响。
•不同类型的滚动轴承钢需要采用不同的热处理方法。
•热处理工艺参数的选择和工艺控制对材料性能的优化具有重要作用。
以上是关于滚动轴承钢的热处理工艺的简要介绍,希望对读者有所帮助。
热处理工艺的影响因素•材料成分:滚动轴承钢种类和合金元素含量对热处理工艺有影响。
•热处理温度:温度的选择会影响材料的淬火效果和晶体结构。
•热处理时间:保温时间的长短会影响材料的相变和晶粒的成长。
淬火工艺的实施步骤1.加热:将滚动轴承钢加热至适当温度,使其达到相应的晶体状态。
2.隔离保温:将加热后的材料保持在该温度下一段时间,以确保晶粒得以重新组合。
3.快速冷却:迅速将材料从高温状态冷却至室温,通过冷却介质的选择和速度的控制来控制晶粒的结构。
回火工艺的实施步骤1.加热:将经过淬火处理的材料加热至适当的温度,通常要低于淬火温度。
2.保温:在合适温度下保持一段时间,使材料中的应力消除并实现组织调整。
轴承钢的质量要求及其缺陷
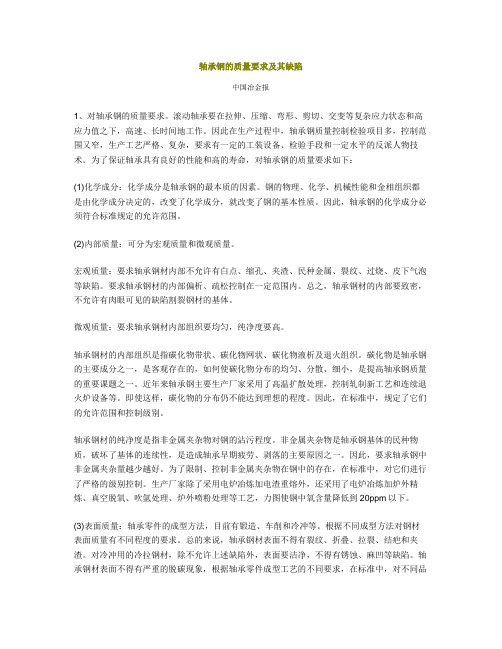
轴承钢的质量要求及其缺陷中国冶金报1、对轴承钢的质量要求。
滚动轴承要在拉伸、压缩、弯形、剪切、交变等复杂应力状态和高应力值之下,高速、长时间地工作。
因此在生产过程中,轴承钢质量控制检验项目多,控制范围又窄,生产工艺严格、复杂,要求有一定的工装设备、检验手段和一定水平的反派人物技术。
为了保证轴承具有良好的性能和高的寿命,对轴承钢的质量要求如下:(1)化学成分:化学成分是轴承钢的最本质的因素。
钢的物理、化学、机械性能和金相组织都是由化学成分决定的,改变了化学成分,就改变了钢的基本性质。
因此,轴承钢的化学成分必须符合标准规定的允许范围。
(2)内部质量:可分为宏观质量和微观质量。
宏观质量:要求轴承钢材内部不允许有白点、缩孔、夹渣、民种金属、裂纹、过烧、皮下气泡等缺陷。
要求轴承钢材的内部偏析、疏松控制在一定范围内。
总之,轴承钢材的内部要致密,不允许有肉眼可见的缺陷割裂钢材的基体。
微观质量:要求轴承钢材内部组织要均匀,纯净度要高。
轴承钢材的内部组织是指碳化物带状、碳化物网状、碳化物液析及退火组织。
碳化物是轴承钢的主要成分之一,是客观存在的,如何使碳化物分布的均匀、分散、细小,是提高轴承钢质量的重要课题之一。
近年来轴承钢主要生产厂家采用了高温扩散处理,控制轧制新工艺和连续退火炉设备等。
即使这样,碳化物的分布仍不能达到理想的程度。
因此,在标准中,规定了它们的允许范围和控制级别。
轴承钢材的纯净度是指非金属夹杂物对钢的沾污程度。
非金属夹杂物是轴承钢基体的民种物质,破坏了基体的连续性,是造成轴承早期疲劳、剥落的主要原因之一。
因此,要求轴承钢中非金属夹杂量越少越好。
为了限制、控制非金属夹杂物在钢中的存在,在标准中,对它们进行了严格的级别控制。
生产厂家除了采用电炉冶炼加电渣重熔外,还采用了电炉冶炼加炉外精炼、真空脱氧、吹氩处理、炉外喷粉处理等工艺,力图使钢中氧含量降低到20ppm以下。
(3)表面质量:轴承零件的成型方法,目前有锻造、车削和冷冲等。
深沟球轴承外圈表面凹坑缺陷研究
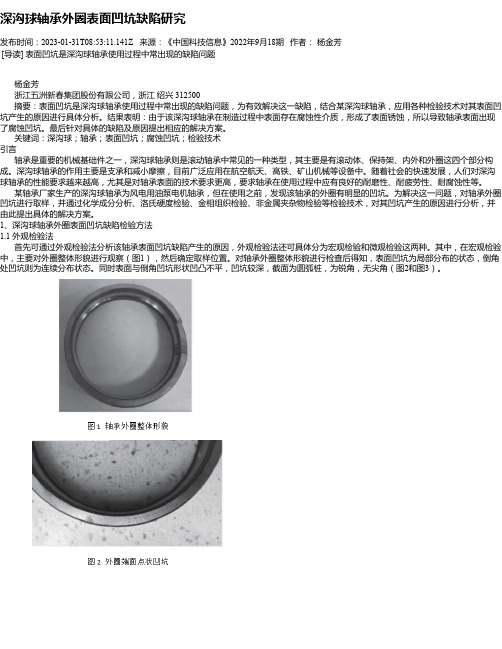
深沟球轴承外圈表面凹坑缺陷研究发布时间:2023-01-31T08:53:11.141Z 来源:《中国科技信息》2022年9月18期作者:杨金芳[导读] 表面凹坑是深沟球轴承使用过程中常出现的缺陷问题杨金芳浙江五洲新春集团股份有限公司,浙江绍兴 312500摘要:表面凹坑是深沟球轴承使用过程中常出现的缺陷问题,为有效解决这一缺陷,结合某深沟球轴承,应用各种检验技术对其表面凹坑产生的原因进行具体分析。
结果表明:由于该深沟球轴承在制造过程中表面存在腐蚀性介质,形成了表面锈蚀,所以导致轴承表面出现了腐蚀凹坑。
最后针对具体的缺陷及原因提出相应的解决方案。
关键词:深沟球;轴承;表面凹坑;腐蚀凹坑;检验技术引言轴承是重要的机械基础件之一,深沟球轴承则是滚动轴承中常见的一种类型,其主要是有滚动体、保持架、内外和外圈这四个部分构成。
深沟球轴承的作用主要是支承和减小摩擦,目前广泛应用在航空航天、高铁、矿山机械等设备中。
随着社会的快速发展,人们对深沟球轴承的性能要求越来越高,尤其是对轴承表面的技术要求更高,要求轴承在使用过程中应有良好的耐磨性、耐疲劳性、耐腐蚀性等。
某轴承厂家生产的深沟球轴承为风电用油泵电机轴承,但在使用之前,发现该轴承的外圈有明显的凹坑。
为解决这一问题,对轴承外圈凹坑进行取样,并通过化学成分分析、洛氏硬度检验、金相组织检验、非金属夹杂物检验等检验技术,对其凹坑产生的原因进行分析,并由此提出具体的解决方案。
1、深沟球轴承外圈表面凹坑缺陷检验方法1.1 外观检验法首先可通过外观检验法分析该轴承表面凹坑缺陷产生的原因,外观检验法还可具体分为宏观检验和微观检验这两种。
其中,在宏观检验中,主要对外圈整体形貌进行观察(图1),然后确定取样位置。
对轴承外圈整体形貌进行检查后得知,表面凹坑为局部分布的状态,倒角处凹坑则为连续分布状态。
同时表面与倒角凹坑形状凹凸不平,凹坑较深,截面为圆弧桩,为锐角,无尖角(图2和图3)。
轴承零件磨削缺陷形成原因及对策
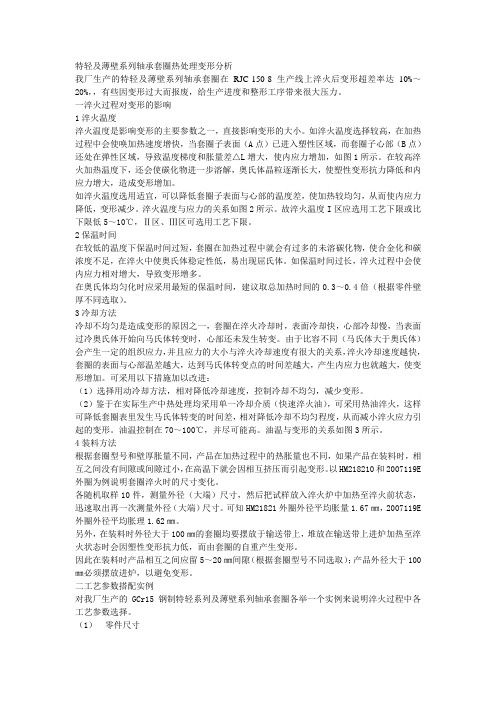
特轻及薄壁系列轴承套圈热处理变形分析我厂生产的特轻及薄壁系列轴承套圈在RJC-150-8生产线上淬火后变形超差率达10%~20%,,有些因变形过大而报废,给生产进度和整形工序带来很大压力。
一淬火过程对变形的影响1淬火温度淬火温度是影响变形的主要参数之一,直接影响变形的大小。
如淬火温度选择较高,在加热过程中会使唤加热速度增快,当套圈子表面(A点)已进入塑性区域,而套圈子心部(B点)还处在弹性区域,导致温度梯度和胀量差△L增大,使内应力增加,如图1所示。
在较高淬火加热温度下,还会使碳化物进一步溶解,奥氏体晶粒逐渐长大,使塑性变形抗力降低和内应力增大,造成变形增加。
如淬火温度选用适宜,可以降低套圈子表面与心部的温度差,使加热较均匀,从而使内应力降低,变形减少。
淬火温度与应力的关系如图2所示。
故淬火温度I区应选用工艺下限或比下限低5~10℃,Ⅱ区、Ⅲ区可选用工艺下限。
2保温时间在较低的温度下保温时间过短,套圈在加热过程中就会有过多的未溶碳化物,使合金化和碳浓度不足,在淬火中使奥氏体稳定性低,易出现屈氏体。
如保温时间过长,淬火过程中会使内应力相对增大,导致变形增多。
在奥氏体均匀化时应采用最短的保温时间,建议取总加热时间的0.3~0.4倍(根据零件壁厚不同选取)。
3冷却方法冷却不均匀是造成变形的原因之一,套圈在淬火冷却时,表面冷却快,心部冷却慢,当表面过冷奥氏体开始向马氏体转变时,心部还未发生转变。
由于比容不同(马氏体大于奥氏体)会产生一定的组织应力,并且应力的大小与淬火冷却速度有很大的关系,淬火冷却速度越快,套圈的表面与心部温差越大,达到马氏体转变点的时间差越大,产生内应力也就越大,使变形增加。
可采用以下措施加以改进:(1)选择用动冷却方法,相对降低冷却速度,控制冷却不均匀,减少变形。
(2)鉴于在实际生产中热处理均采用单一冷却介质(快速淬火油),可采用热油淬火,这样可降低套圈表里发生马氏体转变的时间差,相对降低冷却不均匀程度,从而减小淬火应力引起的变形。
轴承钢热处理应注意的几个问题

轴承钢热处理应注意的几个问题,很专业硬度1.退火硬度:热处理前要检验退火状态零件的硬度及组织。
GCr15:179-207HB(88-94HRB),其他为179-217HB(88-97HRB)。
若硬度不合格(过高、过低或不均匀),都要认真分析原因,可能对淬火产生影响(如,硬度不够,脱碳,过热,椭圆大等)。
2.淬回火硬度:壁厚不大于12mm时,淬火后≥63HRC,回火后60-65HRC;可能会遇到客户提出特殊的硬度要求,如61-64HRC等,但回火后硬度公差范围要大小于3HRC;正常淬火时,硬度值主要取决于回火温度。
3.硬度均匀性:标准规定,同一零件硬度均匀性一般为1HRC;外径大于200mm,不大于400mm时为2HRC;大于400mm时为3HRC.硬度不合格的表现:(1)硬度高:淬火温度高或加热时间长,冷速过快,碳势高(有增碳)。
(2)硬度低:淬火温度低或加热时间短,冷速慢,碳势低(有脱碳),材料脱碳。
(3)硬度不均匀:淬火温度低或加热时间短,冷速慢,材料脱碳,棍棒阴影。
金相组织1.马氏体正常情况下,GCr15的淬火温度为840 ℃左右,一般不超过850℃。
GCr15SiMn的淬火温度为820℃左右,一般不超过835℃。
过高或过低的温度会造成马氏体的过热或欠热。
标准规定马氏体1—5级合格(微型零件1—3级)。
加严为1—4级。
对于壁厚小(一般6-7mm以下)的产品可以1—3级。
马氏体粗细主要与加热温度和加热时间有关。
2.贝氏体贝氏体等温淬火一般使用的材料为GCr15 和GCr18Mo,GCr15钢加工的零件有效厚度多是控制在30mm内,GCr18Mo可以扩展到65mm。
加热温度:不论是GCr15还是GCr18Mo,温度多865~890℃;等温温度:不论是GCr15还是GCr18Mo,其Ms点一般为225℃,等温温度常用235-245℃。
保温时间:一般不应小于4小时。
按JB/T1255标准评定1-3级合格,贝氏体主要与加热温度和加热时间,等温温度及时间有关。
轴承材料质量标准

轴承材料质量标准一、钢材质量标准轴承钢材应采用优质合金钢,其质量应符合国家或行业标准。
钢材的化学成分、机械性能、金相组织、表面质量等应符合相关标准要求。
二、热处理质量标准轴承钢材的热处理包括淬火、回火和表面硬化处理等,其质量应符合以下要求:1.淬火后应获得均匀、细密的马氏体组织,无过热、过烧现象,淬火裂纹等缺陷。
2.回火后应获得均匀、细密的回火马氏体组织,无回火脆性、回火裂纹等缺陷。
3.表面硬化处理后,表面硬度应符合设计要求,无硬化不足、过度硬化等缺陷。
三、表面处理质量标准轴承的表面处理应符合以下要求:1.表面应无氧化皮、锈蚀、划痕等缺陷。
2.表面粗糙度应符合设计要求,一般应不大于Ra0.8。
3.表面硬度应符合设计要求,一般应不低于HRC58。
4.表面镀层质量应符合设计要求,无镀层脱落、起泡等现象。
四、尺寸公差标准轴承的尺寸公差应符合相关标准要求,一般应采用ISO标准或JIS标准。
尺寸公差应在规定范围内,以确保轴承的装配和使用性能。
五、粗糙度标准轴承的粗糙度应符合设计要求,一般应不大于Ra0.8。
粗糙度对轴承的摩擦性能、密封性能等有重要影响,应予以重视。
六、残余应力标准轴承钢材经过热处理后,内部会存在一定的残余应力。
残余应力对轴承的性能会产生负面影响,如引起变形、裂纹等。
因此,应采用适当的方法消除或降低残余应力,使其符合相关标准要求。
七、弹性模量标准轴承的弹性模量对轴承的性能具有重要影响,其值应符合设计要求。
弹性模量是衡量材料变形能力的指标,过大的弹性模量会导致轴承刚度不足,过小的弹性模量则可能导致过大的变形。
八、硬度标准轴承的硬度是衡量材料耐磨性、耐腐蚀性的重要指标。
硬度值应在设计要求的范围内,以保证轴承的使用寿命和性能。
常用的硬度测试方法包括布氏硬度(HB)、洛氏硬度(HR)等。
九、抗疲劳性能标准轴承在反复承受载荷的过程中,会产生疲劳裂纹,最终导致断裂。
因此,轴承的材料应具有较好的抗疲劳性能,以延长其使用寿命。
货车轴承缺陷类别

货车轴承缺陷类别
货车轴承缺陷类别
一、结构缺陷
1、外观缺陷:货车轴承的外观上有缺陷,如表面有明显损伤、氧化斑、表面裂痕等;
2、尺寸缺陷:货车轴承的尺寸有明显偏差,如轴承直径、轴孔直径、轴承间距等;
3、结构缺陷:货车轴承的结构有明显缺陷,如轴承内部结构不符合设计要求,封边缝不合格等;
4、材料缺陷:货车轴承材料有缺陷,如轴承内的滚动元件材料不合格,表面层涂层质量不合格等;
二、使用缺陷
1、装配缺陷:货车轴承装配有缺陷,如凸轮错位、唇环烙痕等;
2、操作缺陷:货车轴承的操作有缺陷,如轴承运转不顺畅、噪音过大等;
3、润滑缺陷:货车轴承润滑有缺陷,如润滑油与黄油混合使用,油膜不足等;
4、磨损缺陷:货车轴承的磨损有缺陷,如轴承表面磨损严重,内部磨损过多等。
货车轴承缺陷类别

货车轴承缺陷类别货车轴承是货车的重要组成部分,它承受着车辆的重量和运动力,保证了车辆的正常运行。
然而,由于使用时间的增加和使用环境的不同,轴承也会出现各种各样的缺陷。
本文将从轴承缺陷的类别入手,为大家介绍货车轴承的缺陷及其原因。
1. 疲劳裂纹疲劳裂纹是轴承最常见的缺陷之一。
它是由于轴承长期受到重复载荷作用而导致的。
在使用过程中,轴承会不断地承受着重量和运动力,这些力量会导致轴承表面的微小裂纹逐渐扩大,最终形成疲劳裂纹。
疲劳裂纹的出现会导致轴承的强度和刚度下降,甚至会导致轴承的断裂。
2. 磨损磨损是轴承的另一种常见缺陷。
它是由于轴承在长期使用过程中,表面与其他部件的摩擦而导致的。
磨损会导致轴承表面的光滑度下降,从而影响轴承的运转效率和寿命。
轴承的磨损程度与使用环境、润滑方式、负载大小等因素有关。
3. 腐蚀腐蚀是轴承的另一种常见缺陷。
它是由于轴承长期暴露在潮湿、腐蚀性气体或液体中而导致的。
腐蚀会导致轴承表面的金属材料被腐蚀,从而影响轴承的强度和刚度。
轴承的腐蚀程度与使用环境、润滑方式、负载大小等因素有关。
4. 偏心偏心是轴承的另一种常见缺陷。
它是由于轴承在使用过程中,轴承内外圈的中心线不重合而导致的。
偏心会导致轴承的运转不平稳,从而影响车辆的行驶稳定性和安全性。
轴承的偏心程度与轴承的安装方式、使用环境等因素有关。
5. 热损伤热损伤是轴承的另一种常见缺陷。
它是由于轴承在使用过程中,由于摩擦和负载而产生的热量过大,导致轴承表面的材料发生变化而产生的。
热损伤会导致轴承表面的硬度和强度下降,从而影响轴承的寿命和运转效率。
轴承的热损伤程度与使用环境、润滑方式、负载大小等因素有关。
货车轴承的缺陷类别有疲劳裂纹、磨损、腐蚀、偏心和热损伤等。
这些缺陷的出现会影响轴承的强度、刚度、运转效率和寿命,从而影响车辆的行驶稳定性和安全性。
因此,在使用货车时,我们应该定期检查轴承的状态,及时发现和处理轴承的缺陷,保证车辆的正常运行。
- 1、下载文档前请自行甄别文档内容的完整性,平台不提供额外的编辑、内容补充、找答案等附加服务。
- 2、"仅部分预览"的文档,不可在线预览部分如存在完整性等问题,可反馈申请退款(可完整预览的文档不适用该条件!)。
- 3、如文档侵犯您的权益,请联系客服反馈,我们会尽快为您处理(人工客服工作时间:9:00-18:30)。
轴承热处理后常见六大质量缺陷
轴承作为机械设备精密零部件,使用质量性能会直接影响到机械设备使用性能,因此我们在使用轴承时,一定要按照一定的性能要求,因此很多厂商为了提高轴承使用性能,进而采用热处理工艺进行提升,但是在热处理工艺后轴承常会出现六大质量缺陷,中华标准件网分享如下。
1、过热
从轴承零件粗糙口上可观察到淬火后的显微组织过热。
但要确切判断其过热的程度必须观察显微组织。
若在GCr15钢的淬火组织中出现粗针状马氏体,则为淬火过热组织。
形成原因可能是淬火加热温度过高或加热保温时间太长造成的全面过热;也可能是因原始组织带状碳化物严重,在两带之间的低碳区形成局部马氏体针状粗大,造成的局部过热。
过热组织中残留奥氏体增多,尺寸稳定性下降。
由于淬火组织过热,钢的晶体粗大,会导致零件的韧性下降,抗冲击性能降低,轴承的寿命也降低。
过热严重甚至会造成淬火裂纹。
2、欠热
淬火温度偏低或冷却不良则会在显微组织中产生超过标准规定的托氏体组织,称为欠热组织,它使硬度下降,耐磨性急剧降低,影响轴承寿命。
3、淬火裂纹
轴承零件在淬火冷却过程中因内应力所形成的裂纹称淬火裂纹。
造成这种裂纹的原因有:由于淬火加热温度过高或冷却太急,热应力和金属质量体积变化时的组织应力大于钢材的抗断裂强度;工作表面的原有缺陷(如表面微细裂纹或划痕)或是钢材内部缺陷(如夹渣、严重的非金属夹杂物、白点、缩孔残余等)在淬火时形成应力集中;严重的表面脱碳和碳化物偏析;零件淬火后回火不足或未及时回火;前面工序造成的冷冲应力过大、锻造折叠、深的车削刀痕、油沟尖锐棱角等。
总之,造成淬火裂纹的原因可能是上述因素的一种或多种,内应力的存在是形成淬火裂纹的主要原因。
淬火裂纹深而细长,断口平直,破断面无氧化色。
它在轴承套圈上往往是纵向的平直裂纹或环形开裂;在轴承钢球上的形状有S形、T形或环型。
淬火裂纹的组织特征是裂纹两侧无脱碳现象,明显区别与锻造裂纹和材料裂纹。
4、热处理变形
轴承零件在热处理时,存在有热应力和组织应力,这种内应力能相互叠加或部分抵消,是复杂多变的,因为它能随着加热温度、加热速度、冷却方式、冷却速度、零件形状和大小的变化而变化,所以热处理变形是难免的。
认识和掌握它的变化规律可以使轴承零件的变形(如套圈的椭圆、尺寸涨大等)置于可控的范围,有利于生产的进行。
当然在热处理过程中的机械碰撞也会使零件产生变形,但这种变形是可以用改进操作加以减少和避免的。
5、表面脱碳
轴承零件在热处理过程中,如果是在氧化性介质中加热,表面会发生氧化作用使零件表面碳的质量分数减少,造成表面脱碳。
表面脱碳层的深度超过最后加工的留量就会使零件报废。
表面脱碳层深度的测定在金相检验中可用金相法和显微硬度法。
以表面层显微硬度分布曲线测量法为准,可做仲裁判据。
6、软点
由于加热不足,冷却不良,淬火操作不当等原因造成的轴承零件表面局部硬度不够的现象称为淬火软点。
它象表面脱碳一样可以造成表面耐磨性和疲劳强度的严重下降。
(来源:热处理)。