热处理常见问题与解答
精品范文-热处理知识问答100问:常见热处理知识问答

精品范文-热处理知识问答100问:常见热处理知识问答常见热处理知识问答(1)、怎样区分热处理件和没有热处理的工件?问题补充:工人不小心把一个未经热处理的生件和一批调试好的经过热处理的工件混在一起,现在如何把他们区分开来,不要切割工件看金相啊,那样会破坏产品,要急着发货?热处理工艺30Cr 经正火、再淬火、然后回火,生件是铸件未经热处理。
两者都经过了抛丸处理颜变色分不出来了,还有硬度都是在35-45 之间了,靠硬度无法区分。
如果也不能通过硬度和热处理氧化色来判别。
我建议你通过敲击声音来辨别。
铸件和淬火+回火态工件金相组织不同,内耗有差异,通过轻轻敲击,可能能分辨。
(2)、H13模具钢如何热处理硬度才能达到58℃?进行1050~1100℃加热淬火,油淬,可以达到要求,但一般热作模具是不要求这么高的硬度的,这么高的硬度性能会很差,不好用,一般在HRC46~50性能好、耐用。
(3)、模具热处理过后表面用什么洗白?问题补充:我是开模具抛光店的,一般模具都用油石先打过再拿去渗氮,渗氮回来又要用油石把那一层黑的擦白,再抛光很麻烦,不擦白打不出镜面来,材料有H13 的,有进口的好多种,如果有药水能洗白的话,就可以直接抛光了。
(1)可以用不锈钢酸洗液,或者盐酸清洗。
喷砂处理也可以。
磨床磨的话费用高,而且加工量大,有可能使尺寸不达标的。
盐酸洗不掉的话,估计您用的是高铬的模具钢?是D2还是H13?高铬模具钢的氧化层比较难洗掉。
用不锈钢酸洗液应该可以,磨具商店或者不锈钢商店都有卖的。
(2)你们没有不锈钢酸洗膏吗?那种可以。
H13这类含铬比较高的模具钢,氧化层是难以用盐酸洗掉的。
还有一个办法,我自己也在用。
你们的模具既然已经油石磨过,表面就是比较光滑的。
实际上,可以先只用粗的油石打磨,或者用砂带打磨,之后就去热处理。
回来之后再用细油石打磨。
而我用的办法是,用纤维轮先打磨,就可以有效的把黑皮去除,再研磨抛光。
或者喷砂,用800 目的碳化硼做一遍喷砂试试,应该就能够去除黑皮,还不需要化太多功夫重磨。
热处理知识问答100问:常见热处理知识问答

热处理知识问答100问:常见热处理知识问答下面是分享的常见热处理知识问答。
供大家参考!常见热处理知识问答1、怎样区分热处理件和没有热处理的工件?问题补充:工人不小心把一个未经热处理的生件和一批调试好的经过热处理的工件混在一起,现在如何把他们区分开来,不要切割工件看金相啊,那样会破坏产品,要急着发货?热处理工艺30Cr 经正火、再淬火、然后回火,生件是铸件未经热处理。
两者都经过了抛丸处理颜变色分不出来了,还有硬度都是在35-45 之间了,靠硬度无法区分。
如果也不能通过硬度和热处理氧化色来判别。
我建议你通过敲击声音来辨别。
铸件和淬火+回火态工件金相组织不同,内耗有差异,通过轻轻敲击,可能能分辨。
2、H13模具钢如何热处理硬度才能达到58℃?进行1050~1100℃加热淬火,油淬,可以达到要求,但一般热作模具是不要求这么高的硬度的,这么高的硬度性能会很差,不好用,一般在HRC46~50性能好、耐用。
3、模具热处理过后表面用什么洗白?问题补充:我是开模具抛光店的,一般模具都用油石先打过再拿去渗氮,渗氮回来又要用油石把那一层黑的擦白,再抛光很麻烦,不擦白打不出镜面来,材料有H13 的,有进口的好多种,如果有药水能洗白的话,就可以直接抛光了。
(1)可以用不锈钢酸洗液,或者盐酸清洗。
喷砂处理也可以。
磨床磨的话费用高,而且加工量大,有可能使尺寸不达标的。
盐酸洗不掉的话,估计您用的是高铬的模具钢?是D2还是H13?高铬模具钢的氧化层比较难洗掉。
用不锈钢酸洗液应该可以,磨具商店或者不锈钢商店都有卖的。
(2)你们没有不锈钢酸洗膏吗?那种可以。
H13这类含铬比较高的模具钢,氧化层是难以用盐酸洗掉的。
还有一个办法,我自己也在用。
你们的模具既然已经油石磨过,表面就是比较光滑的。
实际上,可以先只用粗的油石打磨,或者用砂带打磨,之后就去热处理。
回来之后再用细油石打磨。
而我用的办法是,用纤维轮先打磨,就可以有效的把黑皮去除,再研磨抛光。
热处理题及答案
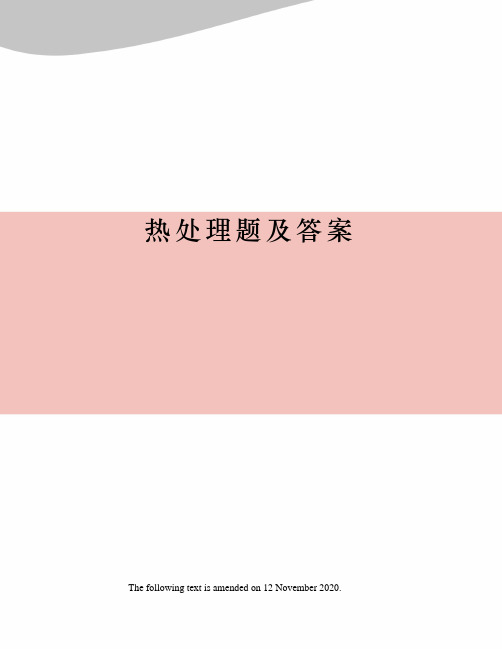
热处理题及答案 The following text is amended on 12 November 2020.1、判断下列说法是否正确:(1)钢在奥氏体化后,冷却时形成的组织主要取决于钢的加热温度。
错误,钢在奥氏体化后,冷却时形成的组织主要取决于钢的冷却速度。
(2)低碳钢与高碳钢工件为了便于切削加工,可预先进行球化退火。
错误,低碳钢工件为了便于切削加工,预先进行热处理应进行正火(提高硬度)或完全退火。
而高碳钢工件则应进行球化退火(若网状渗碳体严重则在球化退火前增加一次正火),其目的都是为了将硬度调整到HB200左右并细化晶粒、均匀组织、消除网状渗碳体。
(3)钢的实际晶粒度主要取决于钢在加热后的冷却速度。
错误,钢的实际晶粒度主要取决于钢的加热温度。
(4)过冷奥氏体冷却速度快,钢冷却后的硬度越高错误,钢的硬度主要取决于含碳量。
(5)钢中合金元素越多,钢淬火后的硬度越高错误,钢的硬度主要取决于含碳量。
(6)同一钢种在相同加热条件下,水淬比油淬的淬透性好,小件比大件的淬透性好。
正确。
同一钢种,其C曲线是一定的,因此,冷速快或工件小容易淬成马氏体。
(7)钢经过淬火后是处于硬脆状态。
基本正确,低碳马氏体韧性要好些,而高碳马氏体硬而脆。
(8)冷却速度越快,马氏体的转变点Ms和Mf越低。
正确。
(9)淬火钢回火后的性能主要取决于回火后的冷却速度。
错误,淬火钢回火后的性能主要取决于回火温度。
(10)钢中的含碳量就等于马氏体的含碳量错误,钢中的含碳量是否等于马氏体的含碳量,要看加热温度。
完全奥氏体化时,钢的含碳量等于奥氏体含碳量,淬火后即为马氏体含碳量。
如果是部分奥氏体化,钢的含碳量一部分溶入奥氏体,一部分是未溶碳化物,从而可以减轻马氏体因含碳量过高的脆性,也能细化晶粒,此时马氏体含碳量要低于钢的含糖碳量。
2、将含碳量为%的两个试件,分别加热到760℃和900℃,保温时间相同,达到平衡状态后以大于临界冷速的速度快速冷却至室温。
球墨铸铁的热处理分析及解决方法

球墨铸铁的热处理分析及解决方法球墨铸铁是一种重要的工程材料,具有优良的力学性能和耐磨性。
然而,在使用过程中,由于各种原因,球墨铸铁可能会出现一些问题,如变形、裂纹、硬度不均匀等。
这时,可以通过热处理来解决这些问题。
本文将分析球墨铸铁的热处理问题,并提出解决方法。
首先,球墨铸铁的热处理常见问题之一是变形。
球墨铸铁的热处理时,由于不均匀加热或急冷等原因,容易出现变形现象。
解决这一问题的主要方法是控制加热温度和冷却速度。
在加热过程中,应采用均匀加热的方法,避免局部过热;在冷却过程中,应选择适当的冷却介质和冷却速度,避免温度梯度过大。
其次,球墨铸铁的热处理中可能出现的问题是裂纹。
裂纹通常是由于内应力过大引起的。
解决裂纹问题的方法包括适当的预热和退火处理。
预热可以减轻内应力,提高热处理的成功率;而退火处理可以缓解内应力,提高零件的延展性,减少裂纹的产生。
此外,球墨铸铁的热处理中还可能出现硬度不均匀的问题。
球墨铸铁的硬度主要由铁素体和珠光体的比例决定。
如果硬度不均匀,一般是由于珠光体的形貌和分布不均匀引起的。
解决硬度不均匀的方法包括适当的退火处理和控制热处理过程中的冷却速度。
退火处理可以使珠光体更均匀地分布在铸件中,提高硬度的均匀性;而控制冷却速度可以使珠光体形成更细小的球状,进一步提高硬度的均匀性。
此外,还有一些其他常见的球墨铸铁热处理问题,如氧化、贝氏体转变等。
解决这些问题的具体方法需要根据具体情况来定。
例如,对于氧化问题,可以选择合适的炉气调节和瓦斯清洁方法,避免在加热过程中产生氧化;对于贝氏体转变问题,可以通过控制退火温度和保温时间来解决。
综上所述,球墨铸铁的热处理的主要问题包括变形、裂纹、硬度不均匀等。
解决这些问题的方法包括控制加热温度和冷却速度,适当的预热和退火处理,控制热处理过程中的冷却速度等。
同时,对于其他常见的问题如氧化、贝氏体转变等,也需要根据具体情况选择合适的解决方法。
通过科学的热处理方法,可以提高球墨铸铁的性能和质量,延长其使用寿命。
热处理常见问题与解答
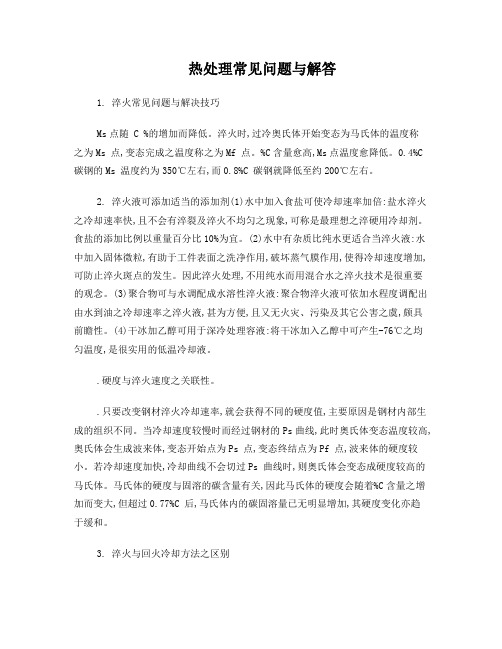
热处理常见问题与解答1. 淬火常见问题与解决技巧Ms点随 C %的增加而降低。
淬火时,过冷奥氏体开始变态为马氏体的温度称之为Ms 点,变态完成之温度称之为Mf 点。
%C含量愈高,Ms点温度愈降低。
0.4%C 碳钢的Ms 温度约为350℃左右,而0.8%C 碳钢就降低至约200℃左右。
2. 淬火液可添加适当的添加剂(1)水中加入食盐可使冷却速率加倍:盐水淬火之冷却速率快,且不会有淬裂及淬火不均匀之现象,可称是最理想之淬硬用冷却剂。
食盐的添加比例以重量百分比10%为宜。
(2)水中有杂质比纯水更适合当淬火液:水中加入固体微粒,有助于工件表面之洗净作用,破坏蒸气膜作用,使得冷却速度增加,可防止淬火斑点的发生。
因此淬火处理,不用纯水而用混合水之淬火技术是很重要的观念。
(3)聚合物可与水调配成水溶性淬火液:聚合物淬火液可依加水程度调配出由水到油之冷却速率之淬火液,甚为方便,且又无火灾、污染及其它公害之虞,颇具前瞻性。
(4)干冰加乙醇可用于深冷处理容液:将干冰加入乙醇中可产生-76℃之均匀温度,是很实用的低温冷却液。
.硬度与淬火速度之关联性。
.只要改变钢材淬火冷却速率,就会获得不同的硬度值,主要原因是钢材内部生成的组织不同。
当冷却速度较慢时而经过钢材的Ps曲线,此时奥氏体变态温度较高,奥氏体会生成波来体,变态开始点为Ps 点,变态终结点为Pf 点,波来体的硬度较小。
若冷却速度加快,冷却曲线不会切过Ps 曲线时,则奥氏体会变态成硬度较高的马氏体。
马氏体的硬度与固溶的碳含量有关,因此马氏体的硬度会随着%C含量之增加而变大,但超过0.77%C 后,马氏体内的碳固溶量已无明显增加,其硬度变化亦趋于缓和。
3. 淬火与回火冷却方法之区别淬火常见的冷却方式有三种,分别是:(1)连续冷却;(2)恒温冷却及(3)阶段冷却。
为求淬火过程降低淬裂的发生,临界区域温度以上,可使用高于临界冷却速率的急速冷却为宜;进入危险区域时,使用缓慢冷却是极为重要的关键技术。
热处理基础知识问答2
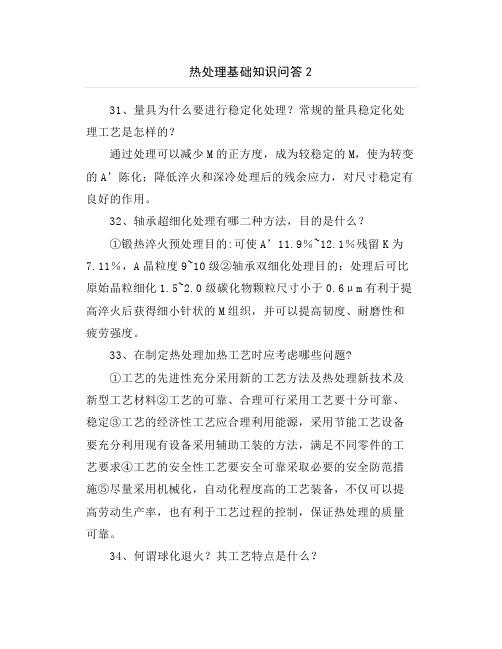
热处理基础知识问答231、量具为什么要进行稳定化处理?常规的量具稳定化处理工艺是怎样的?通过处理可以减少M的正方度,成为较稳定的M,使为转变的A’陈化;降低淬火和深冷处理后的残余应力,对尺寸稳定有良好的作用。
32、轴承超细化处理有哪二种方法,目的是什么?①锻热淬火预处理目的:可使A’11.9%~12.1%残留K为7.11%,A晶粒度9~10级②轴承双细化处理目的:处理后可比原始晶粒细化1.5~2.0级碳化物颗粒尺寸小于0.6μm有利于提高淬火后获得细小针状的M组织,并可以提高韧度、耐磨性和疲劳强度。
33、在制定热处理加热工艺时应考虑哪些问题?①工艺的先进性充分采用新的工艺方法及热处理新技术及新型工艺材料②工艺的可靠、合理可行采用工艺要十分可靠、稳定③工艺的经济性工艺应合理利用能源,采用节能工艺设备要充分利用现有设备采用辅助工装的方法,满足不同零件的工艺要求④工艺的安全性工艺要安全可靠采取必要的安全防范措施⑤尽量采用机械化,自动化程度高的工艺装备,不仅可以提高劳动生产率,也有利于工艺过程的控制,保证热处理的质量可靠。
34、何谓球化退火?其工艺特点是什么?答:所谓钢的球化退火是使钢中的碳化物球化而进行的退火工艺。
1普通球化退火钢中碳化物球状化加热温度AC1+20-30保温时间取决于工件透烧时间,但不宜长。
冷却速度一般在炉内以10-20度/H冷却,冷到550度以下出炉空冷。
2等温球化退火主要用于高碳工具钢合金工具钢。
该工艺球化充分易控制,周期较短,事宜大件。
加热温度为AC1+20-30度,保温时间取决于工件透烧时间。
保温温度为AC1+20—30度,等温时间取决于TTT曲线。
35、为什么亚共析钢经正火后可获得比退火高的强度和硬度?答:退火和正火所得到的都是珠光型组织。
但是正火和退火比较时,正火的珠光体是在较大的过冷度下得到的,因而对亚共析钢来说,析出的先共析铁素体较少,珠光体数量较多,珠光体片间距较小。
热处理安全隐患及应对措施

热处理安全隐患及应对措施热处理加工中的不安全因素主要包括以下几个方面:1.热处理设备的安全性:热处理设备的安全性是热处理加工中的重要问题。
设备的设计、制造、安装和使用过程中都可能存在安全隐患。
例如,加热炉、冷却设备、热处理生产线等可能出现故障,如电源中断、设备失灵等问题,导致设备不能正常运行。
此外,设备的维护和保养也是保证设备安全性的重要环节,设备的老化、磨损和腐蚀等问题也可能导致设备的安全性受到影响。
2.热处理加工过程的安全性:热处理加工过程的安全性也是热处理加工中的重要问题。
热处理过程中可能产生高温、高压、腐蚀等危险因素,如果操作不当或防护措施不到位,可能会导致安全事故的发生。
例如,加热炉内的气体成分、温度和压力等参数的控制不当,可能会导致炉内爆炸或燃烧等事故。
此外,热处理过程中的化学反应和物理变化也可能导致安全事故的发生。
3.人员安全:热处理加工中的人员安全也是需要注意的问题。
操作人员需要具备相应的技能和知识,并严格按照操作规程进行操作。
如果操作人员技能不足或操作不当,可能会引发安全事故。
此外,操作人员也需要了解并遵守相关的劳动安全规定,例如穿戴防护服、使用安全工具等。
4.环境污染:热处理加工过程中可能会产生废气、废水和固体废弃物等污染物,如果处理不当可能会对环境和人类健康造成危害。
例如,废气中的有害物质可能会对大气造成污染,废水中的有害物质可能会对水源造成污染,而固体废弃物则可能会对土壤和地下水造成污染。
因此,需要对废弃物进行合理的处理和处置,以减少对环境和人类健康的危害。
总之,热处理加工中的不安全因素主要包括设备安全性、过程安全性、人员安全性和环境污染等方面。
为了减少这些不安全因素的发生,需要采取相应的预防措施和管理措施,如加强设备维护和保养、严格控制工艺参数、提高操作人员的技能和知识、加强废弃物处理和环境管理等。
热处理基础知识问答3

热处理基础知识问答3展开全文56、珠光体有哪几类?他们的形态和性能特点是什么?珠光体的组织形态可以分为两类:片状珠光体和粒状珠光体。
A片状珠光体,是由相互交替排列的渗碳体和铁素体所组成(1)片状珠光体的形成首先在奥氏体的晶界上析出渗碳体的晶核,并呈片状向境内长大,在其两侧出现了贫碳的奥氏体,促使铁素体在奥氏体上于渗碳体的界面上形核长大,生成层片状铁素体,并使其附近的奥氏体富碳,又促使渗碳体沿奥氏体—铁素体界面形核长大。
如此反复交替,最终形成片状珠光体,当珠光体的上述方式向横向发展的同时,片状铁素体前沿的奥氏体中的碳向渗碳体的前沿扩散,促使转广体也沿着纵向长大,其结果形成珠光体领域。
在一个奥氏体晶粒内,可形成若干个珠光体领域。
(2)珠光体的片间距珠光体的片间距是指珠光体中相邻两片渗碳体间的平均距离,其大小主要取决于转变温度(过冷度)。
转变温度越低,片层间距就越小,珠光体组织越细,渗碳体的弥散度也就越大。
B粒状珠光体,粒状珠光体的形成也是一个渗碳体和铁素体交替析出的过程,其中,渗碳体的析出是以奥氏体晶粒内的未溶碳化物火富碳区的非自发晶核,由于各项成长近似一致,最终成为在铁素体基体上均匀分布着粒状(球状)渗碳体的粒状珠光体,一般认为奥氏体化温度较低有利于形成粒状珠光体。
C珠光体的力学性能,片状珠光体的强度和硬度,随片层间距的减小而提高;粒状珠光体其强度硬度较低,塑性,韧性较好。
57、为了使钢在加热过程中获得细小的奥氏体晶粒度可采取哪些措施?A:加热温度和保温时间:温度越高、保温时间越长,奥氏体晶粒长得越快、晶粒越粗大。
奥氏体晶粒长大速度是随着温度的升高而呈指数关系增加;而在高温下,保温时间对晶粒长大的影响教低温要大。
B:加热速度:加热速度越大、过热度越大,奥氏体实际形成温度就越高,由于形核率与长大速度的比值增大。
因而,可以获得小的初始晶粒。
这也说明,快速加热能获得细小的奥氏体晶粒。
C:钢的化学成分:随着钢种碳含量的增加,但又不足以形成未溶碳化物时,奥氏体晶粒容易长大而粗化。
热处理常见介质及问题处理

工件进行淬火冷却所使用的介质称为淬火冷却介质(或淬火介质)。
理想的淬火介质应具备的条件是使工件既能淬成马氏体,又不致引起太大的淬火应力。
这就要求在C曲线的“鼻子”以上温度缓冷,以减小急冷所产生的热应力;在“鼻子”处冷却速度要大于临界冷却速度,以保证过冷奥氏体不发生非马氏体转变;在“鼻子”下方,特别使Ms点一下温度时,冷却速度应尽量小,以减小组织转变的应力。
常用的淬火介质有水、水溶液、矿物油、熔盐、熔碱等。
● 水水是冷却能力较强的淬火介质。
来源广、价格低、成分稳定不易变质。
缺点是在C曲线的“鼻子”区(500~600℃左右),水处于蒸汽膜阶段,冷却不够快,会形成“软点”;而在马氏体转变温度区(300~100℃),水处于沸腾阶段,冷却太快,易使马氏体转变速度过快而产生很大的内应力,致使工件变形甚至开裂。
当水温升高,水中含有较多气体或水中混入不溶杂质(如油、肥皂、泥浆等),均会显著降低其冷却能力。
因此水适用于截面尺寸不大、形状简单的碳素钢工件的淬火冷却。
● 盐水和碱水在水中加入适量的食盐和碱,使高温工件浸入该冷却介质后,在蒸汽膜阶段析出盐和碱的晶体并立即爆裂,将蒸汽膜破坏,工件表面的氧化皮也被炸碎,这样可以提高介质在高温区的冷却能力。
其缺点是介质的腐蚀性大。
一般情况下,盐水的浓度为10%,苛性钠水溶液的浓度为10%~15%。
可用作碳钢及低合金结构钢工件的淬火介质,使用温度不应超过60℃,淬火后应及时清洗并进行防锈处理。
● 油冷却介质一般采用矿物质油(矿物油)。
如机油、变压器油和柴油等。
机油一般采用10号、20号、30号机油,油的号越大,黏度越大,闪点越高,冷却能力越低,使用温度相应提高。
目前使用的新型淬火油主要有高速淬火油、光亮淬火油和真空淬火油三种。
高速淬火油是在高温区冷却速度得到提高的淬火油。
获得高速淬火油的基本途径有两种,一种是选取不同类型和不同黏度的矿物油,以适当的配比相互混合,通过提高特性温度来提高高温区冷却能力;另一种是在普通淬火油中加入添加剂,在油中形成粉灰状浮游物。
热处理基础知识问答

热处理基础知识问答1、什么是热处理将固态金属或合金采取适当方式进行加热,保温一定的时间,以一定的冷却速度冷却以改变其组织,从而获得所需性能的一种工艺方法。
2、热处理的目的是什么通过适当的热处理工艺改变钢的内部组织结构,来控制相变过程中组织转变的程度和转变产物的形态,从而改善钢的性能。
3、热处理的条件是什么必须有固态相变转变的合金才可以进行热处理。
4、热处理的工艺过程是什么(1)加热:临界点+△T值(2)保温(3)冷却:临界点-△T值一定冷却速度5、主要参数有哪些(1)加热温度T(2)保温时间t(3)冷却速度V,冷却介质决定冷却速度,如:水、盐水、碱水、空气6、按处理阶段及目的可分为哪几种(1)预处理目的是消除偏析、内应力,为最终热处理或后续的加工获得平衡组织。
(2)最终处理作为工件处理的最后工序,获得最终组织。
7、按热处理工艺参数可分为哪几种(1)普通热处理这是生产中最常用的热处理工艺,如退火、正火、淬火、回火等。
这类的热处理一般不会额外的加入其他元素,主要是通过自身组织转变来得到所需要的性能。
(2)化学热处理这类在热处理在齿轮、轴等耐磨件上会经常用到。
工件进行化学热处理时,会在表面一层渗入其他的元素,而对心部的成分不会产生什么影响。
一般渗入什么元素,我们就称为渗×处理,如表面渗C、渗N,C、N共渗等。
(3)表面热处理综合了上述两类热处理的特点,即热处理时不加入其他元素,而且只是针对表面进行的热处理,不影响心部的组织,如表面淬火,但其要求工件的含碳量较高。
8、什么是退火退火是将金属和合金加热到适当温度,保持一定时间,然后缓慢冷却的热处理工艺。
退火后组织亚共析钢是铁素体加片状珠光体;共析钢或过共析钢则是粒状珠光体。
总之退火组织是接近平衡状态的组织。
9、退火的目的是什么(1)降低钢的硬度,提高塑性,以利于切削加工及冷变形加工。
(2)细化晶粒,消除因铸、锻、焊引起的组织缺陷,均匀钢的组织和成分,改善钢的性能或为以后的热处理作组织准备。
热处理部分析题及答案解析

热处理部分析题及答案一、名词解释1.热处理:热处理是将钢在固态下加热到预定的温度,并在该温度下保持一段时间,然后以一定的速度冷却下来的一种热加工工艺。
2.奥氏体化:钢加热获得奥氏体的转变过程3.起始晶粒度:奥氏体形成刚结束,其晶粒边界刚刚相互接触时的晶粒大小。
4.本质晶粒度:根据标准试验方法(YB27—64),经930℃±10℃,保温3~8 小时后测得奥氏体晶粒大小。
5.实际晶粒度:钢在某一具体加热条件下所获得的奥氏体晶粒大小。
6.过冷奥氏体:在临界转变温度以下存在但不稳定,将要发生转变的奥氏体。
7.退火:将钢加热到相变温度Ac1以上或以下,保温以后缓慢冷却(一般随炉冷却)以获得接近平衡状态是将钢件或钢材加热到Ac3以上20℃~30℃,经完全奥氏体化后进行随炉缓慢冷却,以获得近于平衡组织的热处理工艺。
组织的一种热处理工艺。
8.完全退火:将钢件或钢材加热到Ac3以上20℃~30℃,经完全奥氏体化后进行随炉缓慢冷却,以获得近于平衡组织的热处理工艺。
9.不完全退火:将钢件或钢材加热到Ac3以上20℃~30℃,经完全奥氏体化后进行随炉缓慢冷却,以获得近于平衡组织的热处理工艺。
10.扩散退火:将工件加热到略低于固相线的温度(亚共析钢通常为1050℃~1150℃),长时间(一般10~20小时)保温,然后随炉缓慢冷却到室温的热处理工艺。
11.正火:将钢材或钢件加热到临界温度以上,保温后空冷的热处理工艺。
12.淬火:将亚共析钢加热到Ac3以上,共析钢与过共析钢加热到Ac1以上(低于Accm)的温度,保温后以大于临界冷却速度Vk的速度快速冷却,使奥氏体转变为马氏体的热处理工艺。
13.钢的淬透性:指奥氏体化后的钢在淬火时获得马氏体的能力,其大小用钢在一定条件下淬火获得的淬透层深度来表示。
14.回火:淬火后再将工件加热到Ac1温度以下某一温度,保温后再冷却到室温的一种热处理工艺。
15.化学热处理:是将钢件置于一定温度的活性介质中保温,使一种或几种元素渗入它的表面,改变其化学成分和组织,达到改进表面性能,满足技术要求的热处理过程。
热处理知识问答100问

热处理知识问答100问热处理知识问答100问(钢铁)热处理知识问答目录第一章热处理原理 (4)1. 什么是热处理 (4)2. 热处理的目的是什么 (4)3. 热处理的条件是什么 (4)4. 热处理的工艺过程是什么 (4)5. 主要参数有哪些 (4)6. 按处理阶段及目的可分为哪几种 (4)7. 按热处理工艺参数可分为哪几种 (4)8. 什么是退火 (5)9. 退火的目的是什么 (5)10. 退火工艺的种类有哪些 (5)11. 什么是均匀化退火 (5)12. 什么是完全退火 (6)13. 什么是不完全退火 (6)14. 什么是等温退火 (6)15. 什么是球化退火 (6)16. 什么是再结晶退火 (7)17. 什么是去应力退火 (7)18. 什么是回火 (8)19. 回火的目的是什么 (8)20. 回火的种类有哪些 (8)21. 低温回火得到的组织及目的是什么 (8)22. 中温回火得到的组织及目的是什么 (8)23. 高温回火得到的组织及目的是什么 (9)24. 什么是正火 (9)25. 正火的目的是什么 (9)26. 什么是淬火 (9)27. 淬火的目的是什么 (10)28. 加热及保温时间如何确定 (10)29. 怎样控制冷却速度 (10)第二章缺陷及影响 (11)30. 淬火裂纹的影响因素有哪些 (11)31. 钢件的冶金质量对淬火裂纹有何影响 (11)32. 钢的含碳量和合金元素对钢的淬裂倾向有何影响 (11)33. 原始组织对淬裂性有何影响 (11)34. 为何会发生重复淬火开裂现象 (12)35. 零件尺寸和结构对淬裂性有何影响 (12)36. 工艺因素对淬火裂纹有何影响 (12)37. 加热不当可引起哪些裂纹 (13)38. 升温速度过快为何会引起裂纹 (13)39. 表面增碳或脱碳为何会引起裂纹 (13)40. 过热或过烧为何会引起裂纹 (13)41. 在含氢气氛中加热为何会引起裂纹 (13)42. 淬火加热温度和热处理应力有何关系 (14)43. 晶粒大小同淬火加热温度有何关系 (14)44. 冷却为何会引起裂纹 (14)45. 加热过程有哪些缺陷 (14)46. 什么是过热现象 (14)47. 什么是一般过热 (14)48. 产生断口遗传的原因是什么 (14)49. 什么是粗大组织的遗传现象 (15)50. 什么是过烧现象 (15)51. 什么是脱碳和氧化 (15)52. 防止氧化和减少脱碳的措施有哪些 (15)53. 热处理应力对材料性能有何影响 (15)54. 为何会产生热处理应力 (16)55. 热应力与组织应力综合作用会导致什么结果 (16) 第三章质量异常及处理 (17)56. 热处理线有哪三种基本工艺流程 (17)57. 表面质量缺陷产生的原因及如何控制 (17)58. 钢管弯曲产生的原因及如何避免 (17)59. 水淬设备常见故障有哪些 (18)60. 如何解决水淬上料装置热金属检测器故障 (18)61. 斯维顿杠杆故障产生的原因是什么 (18)62. 移动门故障产生的原因是什么 (18)63. 淬火旋转装置故障产生的原因是什么 (18)64. 压紧装置故障产生的原因是什么 (19)65. 钢管到位装置故障产生的原因是什么 (19)66. 出料翻板故障产生的原因是什么 (19)67. 外喷水挡块接行开关故障产生的原因是什么 (19)68. 步进梁装置故障产生的原因是什么 (19)69. 出口翻板故障产生的原因是什么 (19)70. 什么原因会导致液压站故障 (20)71. 什么原因会导致干油泵故障 (20)72. 变频器故障的后果是什么 (20)73. 什么原因会导致水处理故障 (20)74. 高压水除鳞有何故障 (20)75. 热处理炉常见的故障有哪些 (20)76. 如何解决烧嘴熄灭 (20)77. 如何解决烧嘴无法点燃 (20)78. 如何处理电流、煤气、空气流量不足现象 (20)79. 怎样解决烧嘴熄灭后无法复位现象 (21)80. 液压泵自动关闭后怎样解决 (21)81. 控温时的注意哪些事项 (21)82. 热风放散阀有什么作用 (22)83. 淬火炉空气预热器的作用是什么 (22)84. 生产过程中如何控制炉温 (22)85. 焖炉时怎样进行炉温控制 (23)86. 控温时要注意那些方面 (23)87. 升温速度为何不能过快 (24)88. 降温方法有哪几种 (24)89. 水淬斯惠顿停在半空不动的原因是什么及解决方法 (24)90. 水淬时管子卡在淬火轮与移动门之间后怎样解决 (25)91. 多根管子翻到淬火炉入炉辊道前的原因是什么 (25)92. 如何解决钢管进炉后歩进梁不动作 (25)93. 回火炉入炉前会发生哪些异常 (26)94. 混钢有哪些预防措施 (26)第四章热处理岗位质量职责 (27)95. 为何要设备巡检 (27)96. 水淬设备都检查哪些项目 (27)97. 热处理炉都检查哪些项目 (27)98. 怎样做到质量控制 (27)99. 料流控制的原则是什么 (28)100.热处理工有哪些具体职责 (28)第一章热处理原理 (4)1. 什么是热处理 (4)2. 热处理的目的是什么 (4)3. 热处理的条件是什么 (4)4. 热处理的工艺过程是什么 (4)5. 主要参数有哪些 (4)6. 按处理阶段及目的可分为哪几种 (4)7. 按热处理工艺参数可分为哪几种 (4)8. 什么是退火 (5)9. 退火的目的是什么 (5)10. 退火工艺的种类有哪些 (5)11. 什么是均匀化退火 (5)12. 什么是完全退火 (6)13. 什么是不完全退火 (6)14. 什么是等温退火 (6)15. 什么是球化退火 (6)16. 什么是再结晶退火 (7)17. 什么是去应力退火 (7)18. 什么是回火 (8)19. 回火的目的是什么 (8)20. 回火的种类有哪些 (8)21. 低温回火得到的组织及目的是什么 (8)22. 中温回火得到的组织及目的是什么 (8)23. 高温回火得到的组织及目的是什么 (9)24. 什么是正火 (9)25. 正火的目的是什么 (9)26. 什么是淬火 (9)27. 淬火的目的是什么 (10)28. 加热及保温时间如何确定 (10)29. 怎样控制冷却速度 (10)第二章缺陷及影响 (11)30. 淬火裂纹的影响因素有哪些 (11)31. 钢件的冶金质量对淬火裂纹有何影响 (11)32. 钢的含碳量和合金元素对钢的淬裂倾向有何影响 (11)33. 原始组织对淬裂性有何影响 (11)34. 为何会发生重复淬火开裂现象 (12)35. 零件尺寸和结构对淬裂性有何影响 (12)36. 工艺因素对淬火裂纹有何影响 (12)37. 加热不当可引起哪些裂纹 (13)38. 升温速度过快为何会引起裂纹 (13)39. 表面增碳或脱碳为何会引起裂纹 (13)40. 过热或过烧为何会引起裂纹 (13)41. 在含氢气氛中加热为何会引起裂纹 (13)42. 淬火加热温度和热处理应力有何关系 (14)43. 晶粒大小同淬火加热温度有何关系 (14)44. 冷却为何会引起裂纹 (14)45. 加热过程有哪些缺陷 (14)46. 什么是过热现象 (14)47. 什么是一般过热 (14)48. 产生断口遗传的原因是什么 (14)49. 什么是粗大组织的遗传现象 (15)50. 什么是过烧现象 (15)51. 什么是脱碳和氧化 (15)52. 防止氧化和减少脱碳的措施有哪些 (15)53. 热处理应力对材料性能有何影响 (15)54. 为何会产生热处理应力 (16)55. 热应力与组织应力综合作用会导致什么结果 (16) 第三章质量异常及处理 (17)56. 热处理线有哪三种基本工艺流程 (17)57. 表面质量缺陷产生的原因及如何控制 (17)58. 钢管弯曲产生的原因及如何避免 (17)59. 水淬设备常见故障有哪些 (18)60. 如何解决水淬上料装置热金属检测器故障 (18)61. 斯维顿杠杆故障产生的原因是什么 (18)62. 移动门故障产生的原因是什么 (18)63. 淬火旋转装置故障产生的原因是什么 (18)64. 压紧装置故障产生的原因是什么 (19)65. 钢管到位装置故障产生的原因是什么 (19)66. 出料翻板故障产生的原因是什么 (19)67. 外喷水挡块接行开关故障产生的原因是什么 (19)68. 步进梁装置故障产生的原因是什么 (19)69. 出口翻板故障产生的原因是什么 (19)70. 什么原因会导致液压站故障 (20)71. 什么原因会导致干油泵故障 (20)72. 变频器故障的后果是什么 (20)73. 什么原因会导致水处理故障 (20)74. 高压水除鳞有何故障 (20)75. 热处理炉常见的故障有哪些 (20)76. 如何解决烧嘴熄灭 (20)77. 如何解决烧嘴无法点燃 (20)78. 如何处理电流、煤气、空气流量不足现象 (20)79. 怎样解决烧嘴熄灭后无法复位现象 (21)80. 液压泵自动关闭后怎样解决 (21)81. 控温时的注意哪些事项 (21)82. 热风放散阀有什么作用 (22)83. 淬火炉空气预热器的作用是什么 (22)84. 生产过程中如何控制炉温 (22)85. 焖炉时怎样进行炉温控制 (23)86. 控温时要注意那些方面 (23)87. 升温速度为何不能过快 (24)88. 降温方法有哪几种 (24)89. 水淬斯惠顿停在半空不动的原因是什么及解决方法 (24)90. 水淬时管子卡在淬火轮与移动门之间后怎样解决 (25)91. 多根管子翻到淬火炉入炉辊道前的原因是什么 (25)92. 如何解决钢管进炉后歩进梁不动作 (25)93. 回火炉入炉前会发生哪些异常 (26)94. 混钢有哪些预防措施 (26)第四章热处理岗位质量职责 (27)95. 为何要设备巡检 (27)96. 水淬设备都检查哪些项目 (27)97. 热处理炉都检查哪些项目 (27)98. 怎样做到质量控制 (27)99. 料流控制的原则是什么 (28)100.热处理工有哪些具体职责 (28)第一章热处理原理1. 什么是热处理将固态金属或合金采取适当方式进行加热,保温一定的时间,以一定的冷却速度冷却以改变其组织,从而获得所需性能的一种工艺方法。
热处理知识问答

37、淬火的目的?
38、淬火温度的确定?
39、淬火保温时间的确定原则?
40、淬火介质有哪三类?
41、水剂淬火介质有哪些?
42、油剂淬火介质有哪些:
43、淬火冷却过程是三个阶段是什么?
44、淬火冷却方法有哪些?
45、什么是钢的淬硬性和淬透性?
46、什么是回火?
47、回火的目的是什么?
27、过冷奥氏体的组织转变类型有哪几种?
答:过冷奥氏体的组织转变类型有三种:(1)珠光体型转变;(2)贝氏体型转变;(3)马氏体型转变。
28、珠光体型转变有哪些特点?
答:C和Fe都扩散,转变能在等温时进行,转变彻底进行,奥氏体能全部转变。(珠光体、索氏体、托氏体)
29、贝氏体型转变有哪些特点?
答:C能扩散,Fe不能扩散,转变能在等温时进行,转变彻底进行,奥氏体能全部转变。(上贝氏体、下贝氏体)
答:中频感应加热的常用频率为1-8kHz,用于获得3-5mm厚的硬化层的工件。
58、感应加热方式有哪两种?
答:感应加热有同时加热法和连续加热法。
59、感应加热表面淬火的冷却方式主要有哪两种?
答:(1)喷射冷却:通过感应器或喷水圈内壁的小孔将淬火冷却介质喷射到工件的红热表面急冷;
(2)浸液冷却:将工件需淬硬的表面同时加热到淬火温度,然后立即整体浸入淬火槽或转入喷水圈中急冷。
30、马氏体型转变有哪些特点?
答:C和Fe都不能扩散,转变不能在等温时进行,转变不能彻底进行,奥氏体不能全部转变。转变后比容(体积)增大。
31、共析钢在不同冷却速度下的产物?
答:
炉冷为P,空冷为S,油冷为T+M+AR+C,V临为M+AR+C,水冷为
热处理常见工问题及解决方法

热处理知识培训一、表面热处理分类表面热处理的目的:提高零件表面的硬度,强化零件表层,而心部保持原有良好综合机械性能。
1. 表面淬火:感应加热、火焰淬火、电接触加热、电解液淬火、激光淬火、电子束加热等表面热处理方式;2. 化学热处理:渗碳、氮化、碳氮共渗、氮碳共渗、渗S、渗Cr、渗Al、渗硼等;3. 表面涂覆:①气相沉积涂覆TiC(硬度可达Hv3000)②离子涂③真空溅射TiN二、感应加热的基本原理1. 电磁感应、涡流发热热能来源由两部分组成:1)闭合回路在交变的磁场中会产生感应电流工件中有电阻存在,就会发热,称为涡流发热(Q=),这是感应加热主要热能来源。
2)钢铁(零件)大部分为铁磁性材料,有很大剩磁,在交变磁场中剩磁和退磁反复不断进行,导致磁滞发热,但当铁磁性钢铁材料加热到770℃以上,将失去磁性,μ=1,此时不再存在磁滞发热,感应加热速度变慢。
居里点——770℃当感应器一施感导体中流过交变电流时,在它周围就要产生同样频率的交变磁场,感应器内的工件,可以看作无数个不同直径的金属圆环所组成的闭合回路,闭合回路在交变磁场中会产生感应电流,所以工件内将产生与感应器中频率相同而方向相反的感应电流——称为涡流,涡流因工件的电阻而转换成热能(涡流发热)。
2. 交变电流的特性 表面效应——集肤效应 Δ——电流透入深度 I 0——工件表面最大电流密度 e=770℃以下的电流渗透深度为Δ冷 770℃以上的电流渗透深度为Δ热 3. Δ=5030ρμf(厘米) 感应电流在工件截面的分布 ρ=ρ0(1+αt )其中:ρ——工件材料电阻率(单位:欧姆·厘米) μ——材料导磁率(单位:高斯/奥斯特) f ——电流频率(单位:赫) ρ0——20℃时的电阻率 α——系数 t ——温度 对于钢铁材料Δ热>Δ冷 Δ冷=20f(mm ) Δ热=500~600f (mm )(f 越小,淬加层就越深) 以45钢为例 4. 感应加热分类和加热方法 1)根据频率大小分为四类:设备 频率 淬火深度(mm )适用 高频设备200~300KHz~小轴 小模数齿轮 超音频 30~60KHz ~轴类 3~6模数齿轮中频1~8KHz 6~18较大轴较大模数齿轮工频50Hz 80~100 大型轴、轧辊类2)加热方法分为:同时加热:用于较小的工件加热,工件自转但不在感应圈中移动。
热处理操作及常见问题排除方法

热处理操作及常见问题排除方法摘要:热处理是锅炉及主蒸汽压力合金钢管道必不可少的一项重要工序,如何做好热处理这项工作是每一热处理负责人应该考虑的首要工作,在热处理过程中往往会出现停电、加热片(绳)烧断、温度无法达到设定温度等等这样那样的问题,要想焊口热处理合格避免这些问题的出现应该首先从以下几个方面入手:关键词:热处理一:操作前的准备及操作方法介绍:1.热处理设备要使用足够达到最大电流的电缆线,并确保电缆线完好;使用独立漏保,并确保漏电保护器合格。
2.选择合格的加热设备,相关仪、设备表要在有效期内使用。
3.选择合适的热电偶并经过相关单位校验,补偿导线也要对应型号,且不可图省事用普通导线代替。
4.选择对应型号的加热片,温控仪表电压要符合加热片要求,这一点往往是加热片烧坏的主要因素,比如Φ133的加热片所需额定电压110V,刚处理完Φ273的焊口的电压是220V,操作人员往往看着热处理工艺卡只调时间参数,电压参数很多时候漏调,这样加热很快就会烧坏加热片。
5.加热片的选择必须要和管子匹配,加热片不可叠加使用,否则很容易会烧坏加热片;也不可选的加热片比管子小,会产生应力不均匀,达不到热处理消除应力的效果,现场可配备适量的加热绳解决此问题。
6.选择合格的保温材料,保温宽度要符合规范要求。
7.升温前首先检查管口是否封堵严密,其次把热电偶用两道14#铁丝与管道绑紧,热电偶触头要紧挨焊缝,捆绑加热片前要用少量保温棉把热电偶和加热片隔离防止热电偶和加热丝接触,加热片要用两道12#铁丝扎紧,加热片外用厚度不小于60mm的保温棉保温,并用3道12#铁丝扎紧,冬季施工要适当增加保温宽度和厚度。
焊口包扎完毕要确保保温棉紧贴加热片,不可留有空隙。
8.开机升温时要先打开设备本身带的总开关,再打开仪表电源开关,然后开始调节各项参数;热处理结束则先关闭仪表电源开关,再关闭设备总开关。
下面介绍最常用的主蒸汽管道材质:12Cr1MoVG/规格Φ325×25热处理操作;此种规格按《火力发电厂焊接热处理技术规程》DL/T819-2010规范要求需要恒温温度在720-750度恒温1小时,但在现实施工中有时很难达到实际测量温度和设定温度同步,我们可以适当延长恒温时间,一般10-15分钟为宜,最长不要超过30分钟,时间过长不但会影响焊缝质量还会浪费时间。
热处理基础知识问与答4
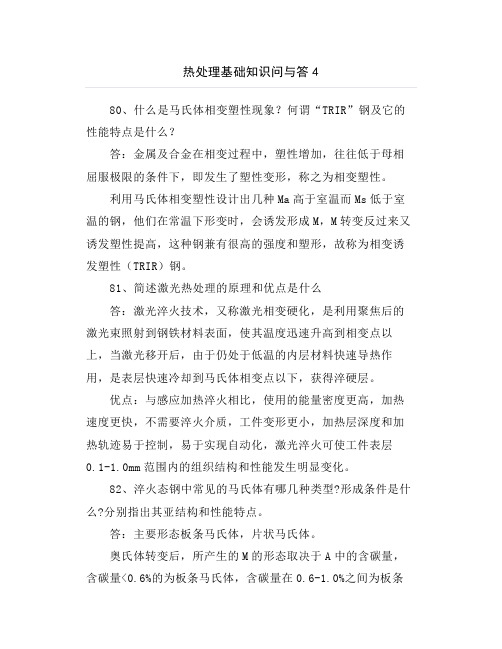
热处理基础知识问与答480、什么是马氏体相变塑性现象?何谓“TRIR”钢及它的性能特点是什么?答:金属及合金在相变过程中,塑性增加,往往低于母相屈服极限的条件下,即发生了塑性变形,称之为相变塑性。
利用马氏体相变塑性设计出几种Ma高于室温而Ms低于室温的钢,他们在常温下形变时,会诱发形成M,M转变反过来又诱发塑性提高,这种钢兼有很高的强度和塑形,故称为相变诱发塑性(TRIR)钢。
81、简述激光热处理的原理和优点是什么答:激光淬火技术,又称激光相变硬化,是利用聚焦后的激光束照射到钢铁材料表面,使其温度迅速升高到相变点以上,当激光移开后,由于仍处于低温的内层材料快速导热作用,是表层快速冷却到马氏体相变点以下,获得淬硬层。
优点:与感应加热淬火相比,使用的能量密度更高,加热速度更快,不需要淬火介质,工件变形更小,加热层深度和加热轨迹易于控制,易于实现自动化,激光淬火可使工件表层0.1-1.0mm范围内的组织结构和性能发生明显变化。
82、淬火态钢中常见的马氏体有哪几种类型?形成条件是什么?分别指出其亚结构和性能特点。
答:主要形态板条马氏体,片状马氏体。
奥氏体转变后,所产生的M的形态取决于A中的含碳量,含碳量<0.6%的为板条马氏体,含碳量在0.6-1.0%之间为板条和针状混合的M,>1%的为针状马氏体。
板条马氏体的亚结构主要由高密度的位错组成,并存在条间A。
板条马氏体具有较高的强度和硬度,而且塑性任性也好。
片状马氏体的亚结构主要由互相平行的细小孪晶组成,并集中在M片的中央部分,具有高硬度,脆性大。
83、淬火态钢中常见的马氏体形态有哪几种?分别说出它们的亚结构。
板条、片(针)状;位错、孪晶84、晶体中的位错有两种基本类型?位错在晶体中主要运动方式有哪两种?刃、螺;滑移、攀移85、零件失效的主要形式分为哪四大类?答:材料的变形,断裂,磨损和腐蚀。
86、对高碳钢实施球化退火工艺的目的是什么?试画出等温球化退火的工艺曲线。
a8常见热处理问题与解答

常見熱處理問題與解答(1)淬火常見問題與解決技巧※Ms點隨C%的增加而降低淬火時,過冷沃斯田體開始變態為麻田散體的溫度稱之為Ms點,變態完成之溫度稱之為Mf點。
%C含量愈高,Ms點溫度愈降低。
0.4%C碳鋼的Ms溫度約為350℃左右,而0.8%C碳鋼就降低至約200℃左右。
※淬火液可添加適當的添加劑(1)水中加入食鹽可使冷卻速率加倍:鹽水淬火之冷卻速率快,且不會有淬裂及淬火不均勻之現象,可稱是最理想之淬硬用冷卻劑。
食鹽的添加比例以重量百分比10%為宜。
(2)水中有雜質比純水更適合當淬火液:水中加入固體微粒,有助於工件表面之洗淨作用,破壞蒸氣膜作用,使得冷卻速度增加,可防止淬火斑點的發生。
因此淬火處理,不用純水而用混合水之淬火技術是很重要的觀念。
(3)聚合物可與水調配成水溶性淬火液:聚合物淬火液可依加水程度調配出由水到油之冷卻速率之淬火液,甚為方便,且又無火災、污染及其他公害之虞,頗具前瞻性。
(4)乾冰加乙醇可用於深冷處理容液:將乾冰加入乙醇中可產生-76℃之均勻溫度,是很實用的低溫冷卻液。
※硬度與淬火速度之關聯性只要改變鋼材淬火冷卻速率,就會獲得不同的硬度值,主要原因是鋼材內部生成的組織不同。
當冷卻速度較慢時而經過鋼材的Ps曲線,此時沃斯田體變態溫度較高,沃斯田體會生成波來體,變態開始點為Ps點,變態終結點為Pf點,波來體的硬度較小。
若冷卻速度加快,冷卻曲線不會切過Ps曲線時,則沃斯田體會變態成硬度較高的麻田散體。
麻田散體的硬度與固溶的碳含量有關,因此麻田散體的硬度會隨著%C含量之增加而變大,但超過0.77%C後,麻田散體內的碳固溶量已無明顯增加,其硬度變化亦趨於緩和。
※淬火與回火冷卻方法之區別淬火常見的冷卻方式有三種,分別是:(1)連續冷卻;(2)恆溫冷卻及(3)階段冷卻。
為求淬火過程降低淬裂的發生,臨界區域溫度以上,可使用高於臨界冷卻速率的急速冷卻為宜;進入危險區域時,使用緩慢冷卻是極為重要的關鍵技術。
新整理[常见热处理工艺产品]常见热处理知识问答
![新整理[常见热处理工艺产品]常见热处理知识问答](https://img.taocdn.com/s3/m/5394dc25960590c69fc37654.png)
[常见热处理工艺产品]常见热处理知识问答1、怎样区分热处理件和没有热处理的工件?问题补充:工人不小心把一个未经热处理的生件和一批调试好的经过热处理的工件混在一起,现在如何把他们区分开来,不要切割工件看金相啊,那样会破坏产品,要急着发货?热处理工艺 30Cr 经正火、再淬火、然后回火,生件是铸件未经热处理。
两者都经过了抛丸处理颜变色分不出来了,还有硬度都是在35-45 之间了,靠硬度无法区分。
如果也不能通过硬度和热处理氧化色来判别。
我建议你通过敲击声音来辨别。
铸件和淬火+回火态工件金相组织不同,内耗有差异,通过轻轻敲击,可能能分辨。
2、H13模具钢如何热处理硬度才能达到58℃?进行1050~1100℃加热淬火,油淬,可以达到要求,但一般热作模具是不要求这么高的硬度的,这么高的硬度性能会很差,不好用,一般在HRC46~50性能好、耐用。
3、模具热处理过后表面用什么洗白?问题补充:我是开模具抛光店的,一般模具都用油石先打过再拿去渗氮,渗氮回来又要用油石把那一层黑的擦白,再抛光很麻烦,不擦白打不出镜面来,材料有H13 的,有进口的好多种,如果有药水能洗白的话,就可以直接抛光了。
(1)可以用不锈钢酸洗液,或者盐酸清洗。
喷砂处理也可以。
磨床磨的话费用高,而且加工量大,有可能使尺寸不达标的。
盐酸洗不掉的话,估计您用的是高铬的模具钢?是D2还是 H13?高铬模具钢的氧化层比较难洗掉。
用不锈钢酸洗液应该可以,磨具商店或者不锈钢商店都有卖的。
(2)你们没有不锈钢酸洗膏吗?那种可以。
H13这类含铬比较高的模具钢,氧化层是难以用盐酸洗掉的。
还有一个办法,我自己也在用。
你们的模具既然已经油石磨过,表面就是比较光滑的。
实际上,可以先只用粗的油石打磨,或者用砂带打磨,之后就去热处理。
回来之后再用细油石打磨。
而我用的办法是,用纤维轮先打磨,就可以有效的把黑皮去除,再研磨抛光。
或者喷砂,用800 目的碳化硼做一遍喷砂试试,应该就能够去除黑皮,还不需要化太多功夫重磨。
- 1、下载文档前请自行甄别文档内容的完整性,平台不提供额外的编辑、内容补充、找答案等附加服务。
- 2、"仅部分预览"的文档,不可在线预览部分如存在完整性等问题,可反馈申请退款(可完整预览的文档不适用该条件!)。
- 3、如文档侵犯您的权益,请联系客服反馈,我们会尽快为您处理(人工客服工作时间:9:00-18:30)。
热处理常见问题与解答1. 淬火常见问题与解决技巧Ms点随 C %的增加而降低。
淬火时,过冷奥氏体开始变态为马氏体的温度称之为Ms 点,变态完成之温度称之为Mf 点。
%C含量愈高,Ms点温度愈降低。
0.4%C碳钢的Ms 温度约为350℃左右,而0.8%C 碳钢就降低至约200℃左右。
2. 淬火液可添加适当的添加剂(1)水中加入食盐可使冷却速率加倍:盐水淬火之冷却速率快,且不会有淬裂及淬火不均匀之现象,可称是最理想之淬硬用冷却剂。
食盐的添加比例以重量百分比10%为宜。
(2)水中有杂质比纯水更适合当淬火液:水中加入固体微粒,有助于工件表面之洗净作用,破坏蒸气膜作用,使得冷却速度增加,可防止淬火斑点的发生。
因此淬火处理,不用纯水而用混合水之淬火技术是很重要的观念。
(3)聚合物可与水调配成水溶性淬火液:聚合物淬火液可依加水程度调配出由水到油之冷却速率之淬火液,甚为方便,且又无火灾、污染及其它公害之虞,颇具前瞻性。
(4)干冰加乙醇可用于深冷处理容液:将干冰加入乙醇中可产生-76℃之均匀温度,是很实用的低温冷却液。
.硬度与淬火速度之关联性。
.只要改变钢材淬火冷却速率,就会获得不同的硬度值,主要原因是钢材内部生成的组织不同。
当冷却速度较慢时而经过钢材的Ps曲线,此时奥氏体变态温度较高,奥氏体会生成波来体,变态开始点为Ps 点,变态终结点为Pf 点,波来体的硬度较小。
若冷却速度加快,冷却曲线不会切过Ps 曲线时,则奥氏体会变态成硬度较高的马氏体。
马氏体的硬度与固溶的碳含量有关,因此马氏体的硬度会随着%C含量之增加而变大,但超过0.77%C 后,马氏体内的碳固溶量已无明显增加,其硬度变化亦趋于缓和。
3. 淬火与回火冷却方法之区别淬火常见的冷却方式有三种,分别是:(1)连续冷却;(2)恒温冷却及(3)阶段冷却。
为求淬火过程降低淬裂的发生,临界区域温度以上,可使用高于临界冷却速率的急速冷却为宜;进入危险区域时,使用缓慢冷却是极为重要的关键技术。
因此,此类冷却方式施行时,使用阶段冷却或恒温冷却(麻回火)是最适宜的。
回火处理常见的冷却方式包括急冷和徐冷两种冷却方法,其中合金钢一般使用急冷;工具钢则以徐冷方式为宜。
工具钢自回火温度急冷时,因残留奥氏体变态的缘故而易产生裂痕,称之为回火裂痕;相同的,合金钢若采用徐冷的冷却方式,易导致回火脆性。
淬火后,残留奥氏体的所扮演的角色.淬火后的工件内常存在马氏体与残留奥氏体,在常温放置一段长久时间易引起裂痕的发生,此乃因残留奥氏体产生变态、引起膨胀所导致,此现象尤其再冬天寒冷的气候下最容易产生。
此外,残留奥氏体另一个大缺点为硬度太低,使得工具的切削性劣化。
可使用深冷处理促使马氏体变态生成,让残留奥氏体即使进一步冷却也无法再产生变态;或以外力加工的方式,使不安定的残留奥氏体变态成马氏体,降低残留奥氏体对钢材特性之影响。
4 淬火处理后硬度不足的原因淬火的目的在使钢材表面获得满意的硬度,若硬度值不理想,则可能是下列因素所造成:(1)淬火温度或奥氏体化温度不够;(2)可能是冷却速率不足所致;(3)工件表面若热处理前就发生脱碳现象,则工件表面硬化的效果就会大打折扣;(4)工件表面有锈皮或黑皮时,该处的硬度就会明显不足,因此宜先使用珠击法将工件表面清除干净后,再施以淬火处理。
5 淬裂发生的原因会影响淬裂的主要原因包括:工件的大小与形状、碳含量高低、冷却方式及前处理方法等。
钢铁热处理会产生淬裂,导因于淬火过程会产生变态应力,而这个变态应力与马氏体变态的过程有关,通常钢材并非一开始产生马氏体变态即发生破裂,而是在马氏体变态进行约50%时(此时温度约150℃左右),亦即淬火即将结束前发生。
因此淬火过程,在高温时要急速冷却,而低温时要缓慢冷却,若能掌握『先快后缓』的关键,可将淬火裂痕的情况降至最低。
6 过热容易产生淬火裂痕.加热超过是当的淬火温度100℃以上,称之为过热。
过热时,奥氏体之结晶颗粒变得粗大化,导致淬火后生成粗大的马氏体而脆化,易使针状马氏体之主干出现横裂痕(此称为马氏体裂痕),此裂痕极易发展成淬火裂痕。
因此,当您的工件在奥氏体化温度时产生过热现象时,后续的淬火、冷却均无法阻止淬裂的产生,故有人把『过热』称为发生淬火裂痕的元凶。
7 淬火前的组织会影响淬火裂痕?.淬火前的组织当然会影响淬火的成败。
最正常的前组织应该是正常化组织或退火组织(波来体结构),若淬火前组织为过热组织、球状化组织均会有不同的结果。
过热组织易产生淬火裂痕,球状化组织则可以均匀淬硬而避免淬裂及淬弯,因此工具钢或高碳钢在淬火前,可施行球状化处理已是淬火重要技术之一。
此时可施以球状化退火或调质球状化处理以获得球状碳化物。
碳化物若以网状组织存在,则容易由该处发生淬火裂痕。
8 淬火零件因常温放置引起之瑕疵淬火后的零件,若长时间放置在室温,可能发生搁置裂痕及搁置变形两种缺陷。
搁置裂痕又称为时效裂痕,尤其在冬天寒冷的夜晚,随温度之下降导致残留奥氏体变态为马氏体,使裂痕因此而产生,又称之为夜泣裂痕。
搁置变形又称之为时效变形,乃淬火工件放置于室温引起尺寸形状变化之现象,大多导因于回火处理不完全所致。
为防止搁置变形,需让钢材组织安定化,因此首先要消除不安定之残留奥氏体(实施深冷处理)。
接着实施200℃~250℃的回火处理使马氏体安定化。
9 回火常见问题与解决技巧100℃热水回火之优点低温回火常使用180℃至200 ℃左右来回火,使用油煮回火。
其实若使用100℃的热水来进行回火,会有许多优点,包括:(1)100℃的回火可以减少磨裂的发生;(2)100℃回火可使工件硬度稍增,改善耐磨性;(3)100℃的热水回火可降低急速加热所产生裂痕的机会;(4)进行深冷处理时,降低工件发生深冷裂痕的机率,对残留奥氏体有缓冲作用,增加材料强韧性;(5)工件表面不会产生油焦,表面硬度稍低,适合磨床研磨加工,亦不会产生油煮过热干烧之现象。
10 二次硬化之高温回火处理对于工具钢而言,残留应力与残留奥氏体均对钢材有着不良的影响,浴消除之就要进行高温回火处理或低温回火。
高温回火处理会有二次硬化现象,以SKD11 而言,530℃回火所得钢材硬度较200℃低温回火稍低,但耐热性佳,不会产生时效变形,且能改善钢材耐热性,更可防止放电加工之加工变形,益处甚多。
.在300 ℃左右进行回火处理,为何会产生脆化现象?.部分钢材在约270℃至300℃左右进行回火处理时,会因残留奥氏体的分解,而在结晶粒边界上析出碳化物,导致回火脆性。
二次硬化工具钢当加热至500℃~600℃之间时才会引起分解,在300℃并不会引起残留奥氏体的分解,故无300℃脆化的现象产生。
11 回火产生之回火裂痕以淬火之钢铁材料经回火处理时,因急冷、急热或组织变化之故而产生之裂痕,称之为回火裂痕。
常见之高速钢、SKD11 模具钢等回火硬化钢在高温回火后急冷也会产生。
此类钢材在第一次淬火时产生第一次马氏体变态,回火时因淬火产生第二次马氏体变态(残留奥氏体变态成马氏体),而产生裂痕。
因此要防止回火裂痕,最好是自回火温度作徐徐冷却,同时淬火再回火的作业中,亦应避免提早提出回火再急冷的热处理方式。
12 回火产生之回火脆性可分为300℃脆性及回火徐冷脆性两种。
所谓300℃脆性系指部分钢材在约270℃至300 ℃左右进行回火处理时,会因残留奥氏体的分解,而在结晶粒边界上析出碳化物,导致回火脆性。
所谓回火徐冷脆性系指自回火温度(500℃~600℃)徐冷时出现之脆性,Ni-Cr 钢颇为显著。
回火徐冷脆性,可自回火温度急冷加以防止,根据多种实验结果显示,机械构造用合金钢材,自回火温度施行空冷,以10℃/min 以上的冷却速率,就不会产生回火徐冷脆性。
13 高周波淬火常见之问题高周波淬火处理常见的缺陷有淬火裂痕、软点及剥离三项。
高周波淬火最忌讳加热不均匀而产生局部区域的过热现象,诸如工件锐角部位、键槽部位、孔之周围等均十分容易引起过热,而导致淬火裂痕的发生,上述情形可藉由填充铜片加以降低淬火裂痕发生的可能性。
另外高周波淬火工件在淬火过程不均匀,会引起工件表面硬度低的缺点,称之为软点,此现象系由于高周波淬火温度不均匀、喷水孔阻塞或孔的大小与数目不当所致。
第三种会产生的缺失是表面剥离现象,主要原因为截面的硬度变化量大或硬化层太浅,因此常用预热的方式来加深硬化层,可有效防止剥离现象。
14 不锈钢为何不能在500℃至650℃间进行回火处理?大部分的不锈钢在固溶化处理后,若在475℃至500℃之间长时间持温时,会产生硬度加大、脆性亦大增的现象,此称之为475℃脆化,主要原因有多种说法,包括相分解、晶界上有含铬碳化物的析出及Fe-Cr 化合物形成等,使得常温韧性大减,且耐蚀性亦甚差,一般不锈钢的热处理应避免常时间持温在这个温度范围。
另外在600℃至700℃之间长时间持温,会产生s相的析出,此s相是Fe-Cr金属间化合物,不但质地硬且脆,还会将钢材内部的铬元素大量耗尽,使不锈钢的耐蚀性与韧性均降低。
15为何会产生回火变形?会产生回火变形的主要原因为回火淬火之际产生的残留硬力或组织变化导致,亦即因回火使张应力消除而收缩、压应力的消除而膨胀,包括回火初期析出e碳化物会有若干收缩、雪明碳铁凝聚过程会大量收缩、残留沃斯田铁变态成麻田散铁会膨胀、残留沃斯田铁变态成变韧铁会膨胀等,导致回火后工件的变形。
防止的方法包括:(1)实施加压回火处理;(2)利用热浴或空气淬火等减少残留应力;(3)用机械加工方式矫正及(4)预留变形量等方式。
16 回火淬性的种类(1)270℃~350℃脆化:又称为低温回火淬性,大多发生在碳钢及低合金钢。
(2)400℃~550℃脆化:通常构造用合金钢再此温度范围易产生脆化现象。
(3)475℃脆化:特别指Cr 含量超过13%的肥粒铁系不锈钢,在400℃至550℃间施以回火处理时,产生硬度增加而脆化的现象,在475℃左右特别显著。
(4)500℃~570℃脆化:常见于加工工具钢、高速钢等材料,在此温度会析出碳化物,造成二次硬化,但也会导致脆性的提高。
17 退火常见问题与解决技巧工件如何获得性能优异之微细波来体结构?退火处理会使钢材变软,淬火处理会使钢材变硬,相比较之下,如施以『正常化』处理,则可获得层状波来铁组织,可有效改善钢材的切削性及耐磨性,同时又兼具不会产生裂痕、变形量少与操作方便等优点。
然而正常化处理是比较难的一种热处理技术,因为它采用空冷的方式冷却,会受到许多因素而影响空冷效果,例如夏天和冬天之冷却效果不同、工件大小对空冷速率有别、甚至风吹也会影响冷却速率。
因此正常化处理要使用各种方法来维持均一性,可利用遮阳、围幕、坑洞、风扇等。
18 正常化处理与退火处理之差异正常化处理维加热至A3 点或Acm 点以上40~ 60℃保持一段时间,使钢材组织变成均匀的奥氏体结构后,在静止的空气中冷却至室温的热处理程序。