钢中夹杂物浅析
浅析硬线钢中非金属夹杂物
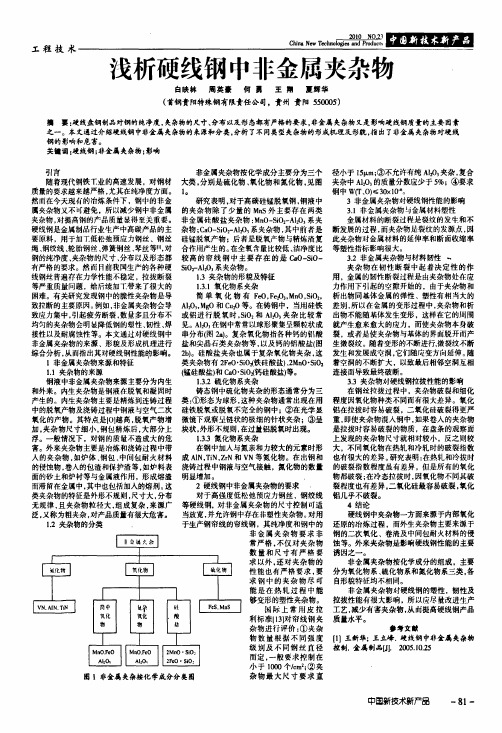
工程技术C hina N e w Technol—ogie型s and㈧嗣囡团圜圈阅Pr oducl^■嵋■0■饵篮工匠‘山■■;一浅析硬线钢巾非金属夹杂物白映林周英豪何勇王翔夏辉华(首钢贵阳特殊钢有限责任公司。
贵州贵阳550005‘)擅要:硬线盘钢制品时钢的纯净度,夹杂物的尺寸、分布以及形态都有严格的要求,非金属夹杂物又是影响硬线钢质量的主要因素./L--。
本文通过介绍硬线钢中非金属夹杂物的来源和分类。
分析了不同类型夹杂物的形成机理及形貌。
指出了非金属夹杂物对硬线钢的影响和危害。
关键词:硬线钢;非金属夹杂物;影响引育随着现代钢铁下业的高速发展,对钢材质量的要求越来越严格,尤其在纯净度方面。
然而在今天现有的冶炼条件下,钢中的非金属夹杂物又不bT避免。
所以减少钢中非金属夹杂物,对提高钢的产品质量显得至关重要。
硬线钢是金属制品行业生产中高碳产品的主要原料,用于加1二低松弛预应力钢丝、钢丝绳、钢纹线、轮胎钢丝、弹簧钢丝、琴丝等f11.对钢的纯净度、夹杂物的尺寸、分布以及形态都有严格的要求。
然而日前我国生产的各种硬线钢丝普遍存在力学性能不稳定,拉拔断裂等严重质量问题,给后续加T带来了很大的困难。
有关研究发现钢中的脆性夹杂物是导致拉断的主要原因。
例如,非金属夹杂物会导致应力集中,引起疲劳断裂,数量多且分布不均匀的夹杂物会明显降低钢的埋性、韧性、焊接性以及耐腐蚀性等。
本文通过对硬线钢中非金属夹杂物的来源、形貌及形成机理进行综合分析.从而指出其对硬线钢性能的影响。
l非金属夹杂物来源和特征1.1夹杂物的来源钢液中非金属夹杂物来源主要分为内生和外来。
内生夹杂物是钢液在脱氧和凝同时产生的。
内生夹杂物主要是精炼到连铸过程中的脱氧产物及浇铸过程中钢液与空气二次氧化的产物。
其特点是10】越高.脱氧产物增加,夹杂物尺寸细小,钢包精炼后,大部分上浮。
一般情况下,对钢的质量不造成大的危害。
外来夹杂物主要是冶炼和浇铸过程中带人的夹杂物,如炉体、钢包、中间包耐火材料的侵蚀物,卷入的包渣和保护渣等,如炉料表面的砂土和炉衬等与金属液作用.形成熔渣而滞留在金属中.其中也包括加入的熔荆。
钢中夹杂物知识.
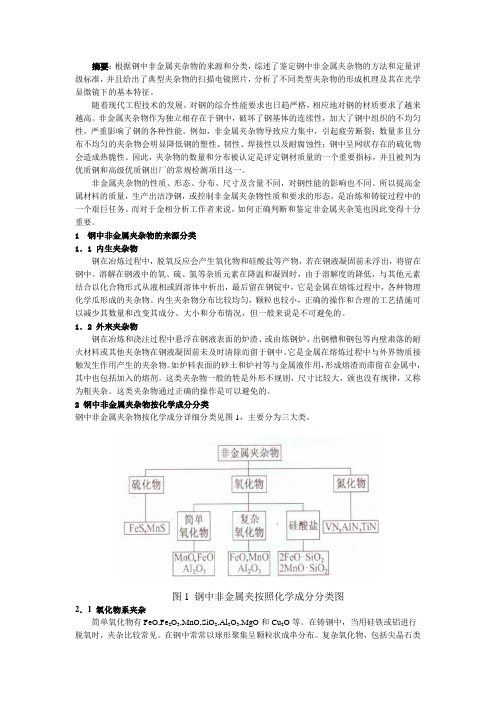
摘要:根据钢中非金属夹杂物的来源和分类,综述了鉴定钢中非金属夹杂物的方法和定量评级标准,并且给出了典型夹杂物的扫描电镜照片,分析了不同类型夹杂物的形成机理及其在光学显微镜下的基本特征。
随着现代工程技术的发展,对钢的综合性能要求也日趋严格,相应地对钢的材质要求了越来越高。
非金属夹杂物作为独立相存在于钢中,破坏了钢基体的连续性,加大了钢中组织的不均匀性,严重影响了钢的各种性能。
例如,非金属夹杂物导致应力集中,引起疲劳断裂;数量多且分布不均匀的夹杂物会明显降低钢的塑性、韧性、焊接性以及耐腐蚀性;钢中呈网状存在的硫化物会造成热脆性。
因此,夹杂物的数量和分布被认定是评定钢材质量的一个重要指标,并且被列为优质钢和高级优质钢出厂的常规检测项目这一。
非金属夹杂物的性质、形态、分布、尺寸及含量不同,对钢性能的影响也不同。
所以提高金属材料的质量,生产出洁净钢,或控制非金属夹杂物性质和要求的形态,是冶炼和铸锭过程中的一个艰巨任务。
而对于金相分析工作者来说,如何正确判断和鉴定非金属夹杂笺也因此变得十分重要。
1 钢中非金属夹杂物的来源分类1.1 内生夹杂物钢在冶炼过程中,脱氧反应会产生氧化物和硅酸盐等产物,若在钢液凝固前未浮出,将留在钢中。
溶解在钢液中的氧、硫、氮等杂质元素在降温和凝固时,由于溶解度的降低,与其他元素结合以化合物形式从液相或固溶体中析出,最后留在钢锭中,它是金属在熔炼过程中,各种物理化学瓜形成的夹杂物。
内生夹杂物分布比较均匀,颗粒也较小,正确的操作和合理的工艺措施可以减少其数量和改变其成分、大小和分布情况,但一般来说是不可避免的。
1.2 外来夹杂物钢在冶炼和浇注过程中悬浮在钢液表面的炉渣、或由炼钢炉、出钢槽和钢包等内壁肃落的耐火材料或其他夹杂物在钢液凝固前未及时清除而留于钢中。
它是金属在熔炼过程中与外界物质接触发生作用产生的夹杂物。
如炉料表面的砂土和炉衬等与金属液作用,形成熔渣而滞留在金属中,其中也包括加入的熔剂。
304不锈钢中夹杂物的控制

304不锈钢中夹杂物的控制304不锈钢是一种广泛应用的奥氏体不锈钢,具有优良的耐腐蚀性和高温强度。
然而,夹杂物的存在可能会对其组织和性能产生不利影响。
因此,控制304不锈钢中的夹杂物对于保证其质量和性能具有重要意义。
本文将介绍夹杂物控制的重要性、夹杂物的来源和分类,以及夹杂物控制的措施和效果。
夹杂物是指存在于金属内部或表面的非金属杂质。
在304不锈钢中,夹杂物可能会破坏材料的连续性,导致应力集中,降低材料的耐腐蚀性和力学性能。
夹杂物对304不锈钢组织和性能的影响主要表现在以下几个方面:降低材料的耐腐蚀性:夹杂物能够破坏不锈钢表面的氧化膜,加速局部腐蚀,降低材料的耐腐蚀性。
降低材料的力学性能:夹杂物会破坏材料的连续性,导致应力集中,降低材料的强度和韧性。
影响材料的加工性能:夹杂物可能引起材料加工过程中的缺陷,如裂纹、折叠等,影响加工质量和精度。
夹杂物主要分为有意夹杂物和无意夹杂物。
有意夹杂物是人为添加的,如为了改善材料的某些性能而特意加入的合金元素。
无意夹杂物是在冶炼、加工过程中引入的,如炉渣、耐火材料、以及与炉气、熔剂、燃料等反应生成的产物。
为了控制304不锈钢中的夹杂物,可以采取以下措施:增加夹杂物球化处理:通过适当的热处理,使夹杂物呈球形颗粒分布,降低其对材料性能的不利影响。
控制原材料及熔炼过程:选用低杂质含量的原材料,严格控制熔炼工艺,避免过度氧化和污染。
精炼和净化处理:采用精炼技术,如电渣重熔、真空熔炼等,去除熔体中的夹杂物;同时,进行净化处理,如加入稀土元素细化晶粒,提高材料的纯净度。
合理安排工艺流程:在加工过程中合理安排工艺流程,避免过度变形和加热,以减少夹杂物的引入。
采取上述控制措施后,可以显著降低304不锈钢中的夹杂物数量和尺寸,改善材料的组织和性能。
具体效果如下:夹杂物形态:通过控制措施,可以使夹杂物呈球形或不规则形态分布,降低其对材料性能的不利影响。
夹杂物分布:采取控制措施后,夹杂物分布更加均匀,避免了局部浓度过高现象,降低材料脆性。
夹杂物及其对钢性能的影响

夹杂物及其对钢性能的影响(1)夹杂物的分类钢在加工变形中,各类夹杂物变形性不同,按其变形能力分为三类:1.脆性夹杂物一般指那些不具有塑性变形能力的简单氧化物(Al2O3、Cr2O3、ZrO2等)、双氧化物(如FeO·Al2O3、MgO·Al2O3、CaO·6 Al2O3)、碳化物(TiC)、氮化物(TiN、Ti(CN)AlN、VN等)和不变形的球状或点状夹杂物(如球状铝酸钙和含SiO2较高的硅酸盐等)。
钢中铝硅钙夹杂物具有较高的熔点和硬度,当压力加工变形量增大时,铝硅钙被压碎并沿着加工方向而呈串链状分布,严重破坏了钢基体均匀的连续性。
2.塑性夹杂物这类夹杂物在钢经受加工变形时具有良好的塑性,沿着钢的流变方向延伸成条带状,属于这类的夹杂物含SiO2量较低的铁锰硅酸盐、硫化锰(MnS)、(Fe, Mn)S等。
夹杂物与钢基体之间的交界面处结合很好,产生裂纹的倾向性较小。
3.半塑性变形的夹杂物一般指各种复合的铝硅酸盐夹杂物,复合夹杂物中的基体,在热加工变形过程中产生塑性变形,但分布在基体中的夹杂物(如CaO·Al2O3、尖晶石型的双氧化物等)不变形,基体夹杂物随着钢基体的变形而延伸,而脆性夹杂物不变形,仍保持原来的几何形状,因此将阻碍邻近的塑性夹杂物自由延伸,而远离脆性夹杂物的部分沿着钢基体的变形方向自由延伸。
(2)夹杂物对钢性能的影响大量试验事实说明夹杂物对钢的强度影响较小,对钢的韧性危害较大,其危害程度又随钢的强度的增高而增加。
4.夹杂物变形性对钢性能的影响钢中非金属夹杂物的变形行为与钢基休之间的关系,可用夹杂物与钢基体之间的相对变形量来表示,即夹杂物的变形率v,夹杂物的变形率可在v=0~1这个范围受化,若变形率低,钢经加工变形后.由于钢产生塑性变形,而夹杂物基本不变形,便在夹杂物和钢基体的交界处产生应力集中,导致在钢与夹杂物的交界处产生微裂纹,这些微裂纹便成为零件在使用过程中引起疲劳破坏的隐患。
钢中夹杂物浅析

钢中夹杂物浅析1. 钢中夹杂物的分类1.1 根据钢中非金属夹杂物的来源分类(1)内生夹杂物钢在冶炼过程中,脱氧反应会产生氧化物和硅酸盐等产物,若在钢液凝固前未浮出,将留在钢中。
溶解在钢液中的氧、硫、氮等杂质元素在降温和凝固时,由于溶解度的降低,与其他元素结合以化合物形式从液相或固溶体中析出,最后留在钢锭中,它是金属在熔炼过程中,各种物理化学变化而形成的夹杂物。
内生夹杂物分布比较均匀,颗粒也较小,正确的操作和合理的工艺措施可以减少其数量和改变其成分、大小和分布情况,但一般来说是不可避免的。
(2)外来夹杂物钢在冶炼和浇注过程中悬浮在钢液表面的炉渣、或由炼钢炉、出钢槽和钢包等内壁剥落的耐火材料或其他夹杂物在钢液凝固前未及时清除而留于钢中。
它是金属在熔炼过程中与外界物质接触发生作用产生的夹杂物。
如炉料表面的砂土和炉衬等与金属液作用,形成熔渣而滞留在金属中,其中也包括加入的熔剂。
这类夹杂物一般的特征是外形不规则,尺寸比较大,分布也没有规律,又称为粗夹杂。
这类夹杂物通过正确的操作是可以避免的。
1.2 根据夹杂物的形态和分布,标准图谱分为A、B、C、D和DS五大类。
这五大类夹杂物代表最常观察到的夹杂物的类型和形态:(1)A类(硫化物类):具有高的延展性,有较宽范围形态比(长度/宽度)的单个灰色夹杂物,一般端部呈圆角;(2)B类(氧化铝类):大多数没有变形,带角的,形态比小(一般<3),黑色或带蓝色的颗粒,沿轧制方向排成一行(至少有3个颗粒);(3)C类(硅酸盐类):具有高的延展性,有较宽范围形态比(一般>3)的单个呈黑色或深灰色夹杂物,一般端部呈锐角;(4)D类(球状氧化物类):不变形,带角或圆形的,形态比小(一般<3),黑色或带蓝色的,无规则分布的颗粒;(5)DS 类(单颗粒球状类):圆形或近似圆形,直径>13μm的单颗粒夹杂物。
2. 钢中夹杂物主要类型及特征2.1 硫化物硫化物是钢液中所含的硫在凝固时以沉淀物析出形成的产物。
浅析XGLX82A帘线钢夹杂物的控制

采 取有 效措 施 , 制 夹 杂物 的质 量 等 级 和 大颗 粒 非 控
金 属 夹杂物 的产 生 。 2 钢 中 非 金 属 夹 杂 物 的 来 源 及 其 影 响 因 素
2 1 钢 中夹 杂 物 的 来 源 .
GB T 1 5 1—2 0 / S 4 6 1 9 E) 钢 中 / 0 6 0 5 I O 9 7: 9 8( 《
夹杂 物 的主要来 源 。 ( ) 火材 料 的侵 蚀 。炼 钢用 的耐 火材 料 中有 3耐 Mg S、 a A 的氧 化物 , 冶 炼 、 炼 、 、 iC 、 1 从 精 出钢浇 铸 整 个生 产过 程 中钢 液都 要 和耐 火 材料 接触 , 钢 过 程 炼 的 高温 钢 液 、 渣 的化 学 作用 , 钢 、 的机械 冲 刷 炉 及 渣 等或 多或 少侵 蚀耐火 材料 , 入钢液 , 为夹杂 物 。 进 成 () 4 出钢 过 程 渣 钢 混 出是 经 常发 生 的 , 易 将 容
业 纷 纷 介 人 研 究 开 发 。 目前 , 内 绝 大 多 数 帘 线 钢 国
铁 合 金 中的杂 质 、 矿 石 中 的脉 石 以 及 固体 材 料 表 铁 面 的泥沙 等都有 可能 带入 钢液 , 为夹 杂物 。 成 ( ) 炼 、 炼 和 浇 铸 过 程 的反 应 。钢 液 在 炉 2冶 精
( ai nrlDe at n ,Xiga Io n te o a y,Xiga ,He e ,0 4 2 ) Qu l yCo t p rme t t o n ti rn a d Se lC mp n n ti bi 5 0 7
Absr c : e s r e o ncuson i GLX8 ta t Th ou c fi l i n S 2A c e n — wie se li n l e s re r te sa ayz d,s m e mea u e o c n r lpr — o s r st o to o
夹杂物对钢材性能与生产顺行的影响

夹杂物对钢材性能与生产顺行的影响夹杂物是指在钢材中存在的一些异物,如氧化皮、氧化物、硫化物、夹杂气泡等。
这些夹杂物的存在会对钢材的性能和生产顺行产生一定的影响。
首先,夹杂物会对钢材的力学性能产生直接影响。
夹杂物的存在会降低钢材的强度和韧性,使其易于断裂。
夹杂物会导致钢材中的应力集中,从而加剧断裂的可能性。
此外,夹杂物还会影响钢材的延展性和可塑性,降低其变形能力和工艺性能。
这些力学性能的下降将直接影响钢材在使用过程中的可靠性和安全性。
其次,夹杂物会对钢材的腐蚀性能产生影响。
夹杂物的存在会破坏钢材表面的连续性,使钢材易于发生腐蚀。
特别是一些有害的夹杂物,如硫化物和氧化物,会加速钢材的腐蚀速度,缩短其使用寿命。
由于腐蚀会使钢材的断裂和损坏,因此夹杂物的存在对钢材的使用性能和耐久性有着重要的影响。
此外,夹杂物还对钢材的加工性能产生影响。
夹杂物会影响钢材的切削性能和焊接性能。
在切削过程中,夹杂物会导致切削刀具磨损加剧和加工表面粗糙度增加。
在焊接过程中,夹杂物容易成为焊接缺陷的起始点,导致焊接接头的质量下降。
因此,夹杂物的存在会影响钢材的加工效率和产品质量。
此外,夹杂物还会对钢材的热处理和热加工过程产生影响。
夹杂物的存在会干扰钢材的晶粒长大和相变行为,从而降低热处理的效果。
在热加工过程中,夹杂物会导致钢材易于开裂,影响产品的成形性和综合性能。
为了降低夹杂物对钢材性能和生产顺行的影响,可以采取以下措施:1.优化原料选择和质量控制,尽量避免夹杂物的产生。
2.加强钢材的清洁工艺,清除钢材表面的夹杂物。
3.通过合理的热处理工艺,尽可能使夹杂物迁移到钢材的边缘,减少对钢材性能的影响。
4.加强钢材的保护措施,减少钢材在储存和运输过程中的受污染风险。
5.加强钢材的检测技术,及时发现和排除含有夹杂物的钢材。
总之,夹杂物对钢材的性能和生产顺行有着重要的影响。
了解和控制夹杂物的存在对于提高钢材的性能和质量,确保钢材的安全可靠使用具有重要的意义。
钢中的非金属夹杂物

什么是非金属夹杂?钢中非金属夹杂物,如氧化物、硫化物、硅酸盐、氮化物等一般都呈独立相存在,主要是由炼钢中的脱氧产物和钢凝固时由于一系列物化反应所形成的各种夹杂物组成。
非金属夹杂的影响非金属夹杂物的存在,破坏了钢基体的连续性,使钢组织的不均匀性增大。
一般来说钢中非金属夹杂物,对钢的性能产生不良影响,如降低钢的塑性、韧性和疲劳性能,使钢的冷热加工性能乃至某些物理性能变坏等。
因此评定钢中夹杂物类别、级别对保证钢材质量十分重要。
分类按夹杂物的化学成分:氧化物、硫化物及氮化物。
根据夹杂物的可塑性:塑性夹杂物、脆性夹杂物、不变形夹杂物及半塑性夹杂物。
● 塑性夹杂物钢中塑性夹杂物在钢经受加工变形时具有良好塑性,沿着钢的流变方向延伸成条带状。
● 脆性夹杂物指那些不具有塑性的简单氧化物和复杂氧化物以及氮化物。
●不变形夹杂物这类夹杂物在铸态的钢中呈球状,而在钢凝固并经形变加工后,夹杂物保持球形不变。
● 半塑性夹杂物指各种多相的铝硅酸盐夹杂物。
其中作为基底的夹杂物(铝硅酸盐玻璃)一般当钢在热加工时具有塑性,但是在这基底上分布的析出相晶体(如Al2O3、尖晶石类氧化物)的塑性很差。
钢经热变形后,塑性夹杂物相(基底)随钢变形而延伸,但脆性的夹杂物相不变形,仍保持原来形状,只是彼此之间的距离被拉长。
按夹杂物的来源:内生夹杂物、外来夹杂物。
● 内生夹杂物在钢的熔炼、凝固过程中,脱氧、脱硫产物,以及随温度下降,S、O、N等杂质元素的溶解度下降,于是这些不溶解的杂质元素就形成非金属化合物在钢中沉淀析出,最后留在钢锭中。
内生夹杂物分布相对均匀,颗粒一般比较细小。
可以通过合理的熔炼工艺来控制其数量、分布和大小等,但一般来讲内生夹杂物总是存在的。
● 外来夹杂物炉衬耐火材料或炉渣等在钢的冶炼、出钢、浇铸过程中进入钢中来不及上浮而滞留在钢中称为外来夹杂物。
其特征是:外形不规则、尺寸比较大,偶尔在这里或在那里出现,正确的操作可以避免或减少钢中外来夹杂物的入侵。
关于钢中非金属夹杂物及有害(2)
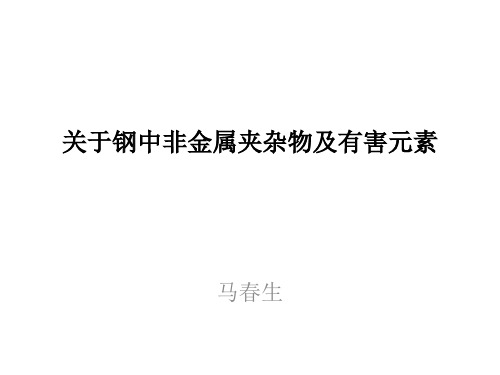
各种夹杂物的线膨胀系数(0~800℃)
夹杂物类型 钢基体 硫化物 成分 MnS CaS CaO(Al2O3)6 CaO(Al2O3)2 CaO(Al2O3) 12CaO 7(Al2O3) CaO3(Al2O3) MgO· Al2O3 MnO·Al2O3 FeO·Al2O3 Al2O3 Cr2O3 (Al2O3)2· (SiO2)2 (MnO)2· (Al2O3)2· (SiO2)2 TiN MnO MgO CaO FeO Fe2O3 热膨胀系数 泊松比 12.5 0.29 18.1 0.3 14.7 8.8 5 0.23 6.6 7.6 10.1 8.4 0.26 8 0.25 7 5 0.24 2 9.4 0.192 14.1 0.306 13.5 0.178 13.5 0.21 14.2 12.3 -
硫含量对钢断面收缩率的影响
磷对钢性能的影响
• 钢中磷可以增加钢的强度和硬度、提高抗大气腐蚀能力、改善 切削加工性能、增加钢的脆性、改善钢的流动性等作用,故在 生产低碳镀锡薄板钢、耐蚀钢、易切削钢、炮弹钢及离心铸造 用钢的时候适当增加钢中的磷含量。但是对于绝大多数钢种, 特别是特殊钢来说,磷是有害的元素。 • 磷对钢的危害主要表现为使钢产生“冷脆”现象。实验发现, 随着钢中磷含量的增加,钢的塑性和韧性降低,使钢的脆性增 加,由于低温时脆性增加更为严重,所以称为“冷脆”。 • 造成“冷脆”现象的原因是,磷能显著扩大固液相之间的两相 区,使磷在钢液凝固结晶时偏析很大,先结晶的等轴晶中磷含 量较低,而大量的磷在最后凝固的晶界处以Fe2P析出,形成高 磷脆性夹层,使钢的塑性和冲击韧性大大降低。 • 磷是“易偏析元素”,磷的存在影响钢成分的均匀性,从而影 响钢性能的均匀性。
钢种夹杂全解析

钢种夹杂全解析[引用2009-06-12 20:45:45]字号:大中小1、钢中夹杂物的长大、上浮与分离钢中尺寸较小的夹杂物颗粒不足以上浮去除,必须通过碰撞聚合成大颗粒,较大的夹杂物陆续上浮到渣层,离开钢液。
在强湍流下,夹杂物碰撞聚合非常迅速,例如在0.1m2/s3的强湍流条件下,夹杂物半径长大到100μm只要2min。
直径为100μm的Al2O3夹杂物从钢液表面下2.5m上浮到钢液表面需要4.8min,直径为20μm的夹杂物,上浮时间增加到119min。
从钢液中分离夹杂物的主要途径包括两种:(1)被表面的渣层吸附;(2)被壁面耐火材料吸附。
2、钢中夹杂物去除技术2.1气体搅拌2.1.1钢包吹氩吹氩搅拌是钢包炉重要的精炼手段之一,钢中夹杂物被气泡俘获去除的效率决定于吹入钢液中气泡数量和气泡尺寸。
钢包底吹氩用透气砖平均孔径一般为2~4mm,在常用的吹氩流量范围产生的气泡直径为10~20mm。
而有效去除夹杂物的最佳气泡直径为2~15mm,并且气泡在上浮过程会迅速膨胀。
因此,底吹氩产生的气泡捕获小颗粒夹杂物概率很小,对细小夹杂物去除效果不理想。
在钢包底吹氩过程中,过强的搅拌功会导致钢水的二次氧化及卷渣。
为了去除钢中的细小夹杂物颗粒,必须钢液中制造直径更小的气泡。
将氩气引入到足够湍流强度的钢液中,依靠湍流波动速度梯度产生的剪切力将气泡击碎,可将大气泡击碎成小气泡。
钢包与中间包之间的长水口具有高的湍流强度,在此区域钢水流速达到1~3m/s。
在长水口吹氩水模型研究表明,可获得0.5~1mm的细小气泡。
细小的气泡捕获夹杂物的概率很高。
这种方法可显著提高氩气泡去除夹杂物的效率。
2.1.2中间包气幕挡墙通过埋设于中间包底部的透气管或透气梁向钢液中吹入的气泡,与流经此处的钢液中的夹杂物颗粒相互碰撞聚合吸附,同时也增加了夹杂物的垂直向上运动,从而达到净化钢液的目的。
德国NMSG公司的应用结果表明,与不吹气相比,50~200μm大尺寸夹杂物全部去除,小尺寸夹杂物的去除效率增加50%。
连铸钢中的夹杂物及其引起的缺陷分析

连铸 钢 中的 非金属及 杂物 的来源主要 内生夹杂 物和 外来夹 杂物 , 钢 包 中间包到结晶器的过程 中采用保护 浇注方法进行 防治二次氧化 。 其 其 中内生夹杂 物 主要是 由于 钢水冷 却凝 固过 程的析 出物或 者是钢 脱氧 中应 做好 以下工作 : ①将 出钢 口的残渣 残钢 清理干 净, 以保证 不出现散 后产 生的 物质 , 而 外来 夹杂 物 主要是 钢水 和外 界之 间的机 械 或者 化学 流的现 象 。 ②在钢包 到中间包的过 程 中应采用 长水 E l 进行 保护, 而 中间
连 铸 钢中硅 酸盐 的夹 杂主要 是钢 水凝 固的过 程 中, 由于冷 却速 度 较 快导 致 钢水 中的液 态硅 酸盐 来 不及结 晶而 以玻璃 态的 留存 于钢 中。
2 。 2 使用高质量耐火材 料 如 果钢 液 中含有 >1 % 的锰 , 则 钢浇铸 的过 程中将 会严重侵蚀 浇铸
由于钢 中的夹杂 物形态 分布对钢 的性能 和钢的 质量 具有显著 的明 显, 因此 , 采用有效 的控制 方法控制 夹杂物 的形态分布也是 切实可行的 措施 。 在进 行控制 钢 中夹 杂物 的形 态分布时 可以 采用压 缩 气体 作为载 体将石灰 、 硅钙粉 等精炼 粉剂喷洒 到钢包 中, 然后 可以利用 气体 的搅拌 作用扩 大液体 钢和 粉剂的 接触面 积 , 其 中等精 炼粉剂 不仅能 够达 到脱 氧、 脱硫 、 改善化 学反应 的 目 的, 提 高钢的纯净度 的目的, 同时还 能够改
圈1连铸钢 口形态 变钢中夹杂 物的形态 及其 组成 。 1 . 2 连 铸钢中氧化铝杂 物及其缺陷 3 . 总 结 在镇静 钢加工生 产中, 氧化铝是 最为常见的夹 杂物 , 其也是 一种 对 综 上所 述 , 连铸钢 中的夹杂 物对 钢的质量 和钢 的性能 具有 很大 的 钢 性能 影 响最大 的一种 夹杂 物 , 氧化铝 夹杂 物是 一种脆 性不 变形夹 杂 影 响 , 因此 , 只有采 取 有效 的 方法 减 少钢 中的 夹杂 物 , 控 制夹 杂 物 形
钢的非金属夹杂物

钢的非金属夹杂物
钢的非金属夹杂物主要有氧化物、硅、磷、硫等。
1. 氧化物:钢材在高温下容易与氧气发生反应生成氧化物,主要有铝氧化物、铁氧化物、锰氧化物等。
氧化物夹杂物会降低钢材的强度和塑性,并且容易形成脆性氧化皮。
2. 硅:硅是钢材中常见的非金属夹杂物,主要来自原料和炼钢过程中的硅铁等添加剂。
硅夹杂物对钢的机械性能有较大影响,高硅含量会降低钢材的强度和韧性。
3. 磷:磷是钢材中的有害非金属夹杂物,容易导致钢的冷脆性增加,特别是在低温下会引起钢材的脆性断裂。
因此,钢材中磷含量的控制非常重要。
4. 硫:硫是钢材中常见的非金属夹杂物,主要来自原料和炼钢过程中的硫铁等添加剂。
高硫含量会降低钢的冷加工性能和焊接性能,还容易引起钢的脆性断裂。
为了降低非金属夹杂物对钢材性能的影响,炼钢过程中会采取适当的工艺措施和添加剂,如进行脱氧、脱硫等处理,以提高钢材的质量和性能。
轧制钢板夹杂物金相法分析步骤浅析

机|械|工|程轧制钢板夹杂物金相法分析步骤浅析肖摘 要静李侠马计平北京 100088)(中冶建筑研究总院有限公司本文从依据 GB/T10561 《钢中非金属夹杂物含量的测定标准评级图显微检验法》 标准进行夹杂物分析的角度 出发, 研究了实验室对轧制钢板夹杂物进行金相分析的方法和步骤, 提供了一种实验室金相法鉴定夹杂物的分析思 路, 对相关实验人员的工作具有一定的指导意义。
关键词 夹杂物评级 金相法 轧制钢板 TF769.2 中图分类号: 0 前言 近年来, 随着建筑钢结构行业的飞速发展, 对建筑用结构 钢的性能要求也越来越高,钢铁中非金属夹杂物的出现是不 可避免的, 因为非金属夹杂物破坏了金属基体的连续性、 均匀 性, 易引起应力集中, 造成机械性能下降, 导致材料的早期破 坏, 其影响程度主要取决于夹杂物的形状、 大小、 分布和聚集 状态。
受某工厂委托, 对其生产的 Q345 轧制厚板材进行非金 属夹杂物评级。
采用金相鉴定法对夹杂物进行观察鉴定,金 相法除了对夹杂物的化学成分、 晶体结构不能鉴别外, 可以直 接观察和鉴别夹杂物的形态、 大小、 数量、 分布、 类型等, 这种 方法操作简便、 容易实施、 直观且易与钢材质量联系起来。
目 前, 金相法是最广泛、 最有效的方法, 本文旨在提供一种实验 室采用的金相法鉴定夹杂物的分析思路。
1 实验方法 1.1 取样 根据国家标准 GB/T10561《钢中非金属夹杂物含量的测 定标准评级图显微检验法》 以及委托方要求, 夹杂物样品取样 规则如下: (1) 根据委托方要求, 在轧制钢板板宽 1/4 处取样; (2) 根据委托方和 GB/T10561 要求, 在板厚方向上, 距离 板材轧制上表面 1/4 处和 1/2 处分别取样; (3) 观察面为与轧向和板厚方向平行的 1/4 处和 1/2 处纵 截面。
取样位置如图 1 所示, 样品尺寸为 20mmΧ18mmΧ10mm, 阴影处为观察面。
钢中夹杂物

组织特征:黑色圆球状为氧化物 夹杂物,白色为基体(未经化学 腐蚀),组织特点为半球状夹杂 物在光学显微镜明场照明下可看 到半球面的表面呈现出黑白交替 的等色环。 材料:低碳钢焊缝区 腐蚀方法:未腐蚀
组织说明
放大倍数:500倍
02 球状透明夹杂物
组织特征:圆球状透明氧化物在 正交偏振光照射下,可看到在圆 形的夹杂物中有一个黑十字,这 种现象称为“黑十字”效应,这种 效应与夹杂物必须是透明的、球 形的有关。
组织说明
08 氮化钛( TiN )夹杂物
组织特征:夹杂物呈金黄色规则 外形分布,边缘有棱角,常呈多 边形。尤其在含CrMnTi材料中居 多。 材料:各类钢铁 腐蚀方法:未腐蚀
放大倍数:500倍
组织说明
09 氮化钛( TiN )夹杂物
组织特征:夹杂物呈金黄色规则 外形分布,边缘有棱角,常呈多 边形。尤其在含CrMnTi材料中居 多。 材料:各类钢铁 腐蚀方法:未腐蚀
放大倍数:500倍
组织说明
10 混合夹杂物
组织特征:夹杂物呈不同颜色及 不同形状,当混合夹杂物量多时, 材料的力学性能会受到很大的影 响,因每一颗夹杂物就象一个裂 纹分布在钢中。
材料:各类钢铁 腐蚀方法:未腐蚀
放大倍数:500倍组织源自明116珠光体116
组织说明
材料:低碳钢焊缝区
腐蚀方法:未腐蚀 放大倍数:500倍
组织说明
03 球状透明夹杂物
组织特征:圆球状透明氧化物在 正交偏振光照射下,可看到在圆 形的夹杂物中有一个黑十字,这 种现象称为“黑十字”效应,这种 效应与夹杂物必须是透明的、球 形的有关。 材料:低碳钢焊缝区 腐蚀方法:未腐蚀
放大倍数:500倍
组织说明
炼钢过程中夹杂物的生成与控制

炼钢过程中夹杂物的生成与控制炼钢是一种重要的工业生产过程,其主要目的是通过将炉料(如铁矿石和废钢铁)放入高温高压的熔炉中,使其与还原剂反应产生炉渣和钢水。
在炼钢过程中,夹杂物是不可避免的产物,但若不控制好夹杂物的生成和处理,将会对钢材的性能造成影响。
一、夹杂物的生成1. 炼钢原料中的夹杂物在炼钢过程中,钢铁厂使用的原料炉料中也含有很多夹杂物。
铁矿石中可能含有磁铁矿(Fe3O4)、方铅矿(PbS)、非磁性氧化铁等难以还原的杂质,在还原反应中难以完全还原,会留下大量夹杂物。
还有一些废钢铁,其表面可能覆盖着石灰、尘土、油脂等污物,这些污物也会在钢水中成为夹杂物。
2. 熔炼反应中的夹杂物熔炼反应中,通常需要加入气体(如氧气、氮气、煤气等)和其他物质来促进反应的进行。
在炉内加氧气时,由于气流不稳定、温度较高等因素的影响,很容易将炉外的氧气和空气带进熔池内,形成气泡。
这些气泡在熔池中翻滚,不断向上升腾,并带走了一些夹杂物。
同时,由于熔池中的温度较高,很容易与炉壁和炉料发生接触,将其熔化并带进熔池中,也会形成夹杂物。
3. 结晶过程中的夹杂物在冷却结晶的过程中,由于钢水在温度、浓度和结构等方面的变化,也会产生一些夹杂物。
比如说,当钢水流经炉铁水口时,由于温度急剧下降,容易出现结晶,从而使炉渣、氧化膜、炉渣酸性物质等固体杂质一起形成夹杂物。
二、夹杂物的控制方法1. 提高原料炉料的质量钢铁厂应该选择优质炉料作为原料炉料,减少夹杂物的含量。
同时,还要在熔炼过程中掌握好炉料的添加量和时间,避免在钢水中形成夹杂物。
2. 控制还原反应通过控制熔炼反应的强度和时间,可以减少因反应不充分而产生的夹杂物。
此外,还可以在熔池中加入一定量的草酸钡等物质,使其转化为气态物质,从而带走气体,减少夹杂物的含量。
3. 控制冷却速度在炉外输送钢水时,要注意控制输送速度和冷却速度,避免钢水与空气接触时间过长,从而减少氧化膜和炉渣等物质的形成。
在钢水过程中应当尽量避免在冷却过程中结晶,可以采用一定的技术手段,如增加钢水的流动性、提高冷却速度等方法,避免夹杂物的形成。
夹杂物对钢性能的影响

夹杂物对钢性能的影响钢中的非金属夹杂物主要是指钢中的氧化物、硫化物、硅酸盐和氮化物等。
其中,氧及硫的化合物最主要,对钢性能的影响最大。
这些化合物一般不具有金属的性质,并机械地混杂在钢的组织中,虽然对钢的强度影响很小,但对疲劳性能、冲击韧性和塑性影响很大。
由于夹杂物与基体金属的物性及机械性能,如弹性、塑性及热膨胀系数均有较大差别,在受力过程中,夹杂物不能随金属相应变形。
变形大的铁就会在变形小的夹杂物的周围产生塑性流动,它们的连接处应力的分布不均匀,出现了应力集中[8],并急剧地升高,导致微裂纹的发生,为材料的破坏提供了受力的薄弱区,加速了塑性破裂的过程。
因而导致钢的塑性、韧性及疲劳强度降低,方向性加强,加工性能变坏等。
不锈钢中的夹杂物对钢的机械性能,特别是钢的韧塑性、疲劳性能、冷加工性能以及切削加工性能等有强烈的影响。
在轧制过程中,夹杂物的存在不但影响不锈钢的内部质量和板材的表面光洁度,而且将降低产品的防锈蚀能力,目前国内不锈钢厂由于夹杂导致的产品报废率高达20%,甚至更高,大大降低了钢厂的生产效率和经济效益。
因此严格控制夹杂物的类型、大小、数量、形态和分布,提高钢的纯净度,向“零夹杂钢”努力已经是许多研究者的共识[9-11]。
因此,炼钢工作者应首先力求降低夹杂物的含量,利用复合脱氧剂,使脱氧过程中生成的夹杂物尽可能地浮出,并设法降低凝固过程中出现的二次脱氧产物的形成量。
对不可能排除而残留在钢中的夹杂可采用变形处理,改变其存在状态,以减小其对钢性能的危害性。
[8].陈聪.减少钢中夹杂物的途径及其变形处理[J].科技情报开发与经济,2005,15(13).275.[9].上海交通大学《金相分析》编写组. 金相分析[M].北京: 国防工业出版社. 1982,117~133.[10].李正邦. 超洁净钢的新进展[J]. 材料与冶金学报,2002,1(3): 161-465.[11].Fukumoto S,Mutcgell A.The manufacture of alloy swithzero oxidein clusion content[C],Proceedings of the 1991 Vacuum Metallurgy Conference on the Melting and Processing of Specialty Materials I&SS,Inc.Pitts-burgh, USA, 1991:3~7.典型夹杂物对不锈钢性能的影响MgO-Al2O3尖晶石是Al作奥氏体不锈钢的终脱氧剂时的主要氧化物夹杂。
钢中夹杂物的产生与去除途径
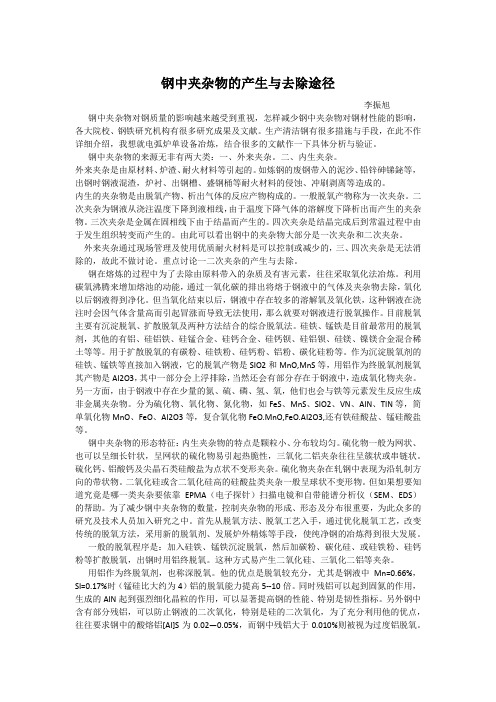
钢中夹杂物的产生与去除途径李振旭钢中夹杂物对钢质量的影响越来越受到重视,怎样减少钢中夹杂物对钢材性能的影响,各大院校、钢铁研究机构有很多研究成果及文献。
生产清洁钢有很多措施与手段,在此不作详细介绍,我想就电弧炉单设备冶炼,结合很多的文献作一下具体分析与验证。
钢中夹杂物的来源无非有两大类:一、外来夹杂。
二、内生夹杂。
外来夹杂是由原材料、炉渣、耐火材料等引起的。
如炼钢的废钢带入的泥沙、铅锌砷锑鉍等,出钢时钢液混渣,炉衬、出钢槽、盛钢桶等耐火材料的侵蚀、冲刷剥离等造成的。
内生的夹杂物是由脱氧产物、析出气体的反应产物构成的。
一般脱氧产物称为一次夹杂。
二次夹杂为钢液从浇注温度下降到液相线,由于温度下降气体的溶解度下降析出而产生的夹杂物。
三次夹杂是金属在固相线下由于结晶而产生的。
四次夹杂是结晶完成后到常温过程中由于发生组织转变而产生的。
由此可以看出钢中的夹杂物大部分是一次夹杂和二次夹杂。
外来夹杂通过现场管理及使用优质耐火材料是可以控制或减少的,三、四次夹杂是无法消除的,故此不做讨论。
重点讨论一二次夹杂的产生与去除。
钢在熔炼的过程中为了去除由原料带入的杂质及有害元素,往往采取氧化法冶炼。
利用碳氧沸腾来增加熔池的动能,通过一氧化碳的排出将熔于钢液中的气体及夹杂物去除,氧化以后钢液得到净化。
但当氧化结束以后,钢液中存在较多的溶解氧及氧化铁,这种钢液在浇注时会因气体含量高而引起冒涨而导致无法使用,那么就要对钢液进行脱氧操作。
目前脱氧主要有沉淀脱氧、扩散脱氧及两种方法结合的综合脱氧法。
硅铁、锰铁是目前最常用的脱氧剂,其他的有铝、硅铝铁、硅锰合金、硅钙合金、硅钙钡、硅铝钡、硅镁、镍镁合金混合稀土等等。
用于扩散脱氧的有碳粉、硅铁粉、硅钙粉、铝粉、碳化硅粉等。
作为沉淀脱氧剂的硅铁、锰铁等直接加入钢液,它的脱氧产物是SIO2和MnO,MnS等,用铝作为终脱氧剂脱氧其产物是AI2O3,其中一部分会上浮排除,当然还会有部分存在于钢液中,造成氧化物夹杂。
钢中夹杂物知识

摘要:根据钢中非金属夹杂物的来源和分类,综述了鉴定钢中非金属夹杂物的方法和定量评级标准,并且给出了典型夹杂物的扫描电镜照片,分析了不同类型夹杂物的形成机理及其在光学显微镜下的基本特征。
随着现代工程技术的发展,对钢的综合性能要求也日趋严格,相应地对钢的材质要求了越来越高。
非金属夹杂物作为独立相存在于钢中,破坏了钢基体的连续性,加大了钢中组织的不均匀性,严重影响了钢的各种性能。
例如,非金属夹杂物导致应力集中,引起疲劳断裂;数量多且分布不均匀的夹杂物会明显降低钢的塑性、韧性、焊接性以及耐腐蚀性;钢中呈网状存在的硫化物会造成热脆性。
因此,夹杂物的数量和分布被认定是评定钢材质量的一个重要指标,并且被列为优质钢和高级优质钢出厂的常规检测项目这一。
非金属夹杂物的性质、形态、分布、尺寸及含量不同,对钢性能的影响也不同。
所以提高金属材料的质量,生产出洁净钢,或控制非金属夹杂物性质和要求的形态,是冶炼和铸锭过程中的一个艰巨任务。
而对于金相分析工作者来说,如何正确判断和鉴定非金属夹杂笺也因此变得十分重要。
1 钢中非金属夹杂物的来源分类1.1 内生夹杂物钢在冶炼过程中,脱氧反应会产生氧化物和硅酸盐等产物,若在钢液凝固前未浮出,将留在钢中。
溶解在钢液中的氧、硫、氮等杂质元素在降温和凝固时,由于溶解度的降低,与其他元素结合以化合物形式从液相或固溶体中析出,最后留在钢锭中,它是金属在熔炼过程中,各种物理化学瓜形成的夹杂物。
内生夹杂物分布比较均匀,颗粒也较小,正确的操作和合理的工艺措施可以减少其数量和改变其成分、大小和分布情况,但一般来说是不可避免的。
1.2 外来夹杂物钢在冶炼和浇注过程中悬浮在钢液表面的炉渣、或由炼钢炉、出钢槽和钢包等内壁肃落的耐火材料或其他夹杂物在钢液凝固前未及时清除而留于钢中。
它是金属在熔炼过程中与外界物质接触发生作用产生的夹杂物。
如炉料表面的砂土和炉衬等与金属液作用,形成熔渣而滞留在金属中,其中也包括加入的熔剂。
钢中硫化铁夹杂物析出原理_概述说明以及解释

钢中硫化铁夹杂物析出原理概述说明以及解释1. 引言1.1 概述在现代钢铁冶炼过程中,硫化铁夹杂物的析出对于钢材的质量和性能具有重要影响。
硫化铁夹杂物是由于钢中含有过多的硫元素而形成的一种微观结构,在钢材中分布不均匀,并且会导致钢材在使用过程中出现脆化、断裂等问题。
因此,深入研究硫化铁夹杂物析出原理及其相应的控制技术具有重要的理论和实际意义。
1.2 文章结构本文将围绕硫化铁夹杂物析出原理展开全面系统的阐述。
首先,我们将介绍硫化铁夹杂物的含义和特点,探讨其在钢铁材料中的重要作用。
然后,我们将概述硫化铁夹杂物析出原理,并解释其形成与演变机制。
进一步地,我们将介绍并分析影响硫化铁夹杂物析出过程的关键因素,从实验方法与表征手段上进行详细说明。
最后,我们将总结当前已取得的研究成果,并提出未来研究的方向与展望。
1.3 目的本文旨在深入探讨钢中硫化铁夹杂物析出原理,全面了解其形成机理和影响因素。
通过研究不同的控制技术和措施,实现对硫化铁夹杂物的有效控制,以提高钢材的质量和性能。
为此,我们将介绍当前已有的相关研究工作,并总结实践中所取得的成果。
同时,本文还将对未来的研究方向进行展望,为进一步深入研究该领域提供参考。
以上是“1. 引言”部分内容,请根据此内容撰写文章。
2. 钢中硫化铁夹杂物析出原理2.1 硫化铁夹杂物的含义和特点在钢中,硫化铁是一种常见的夹杂物。
硫化铁夹杂物指的是由铁与硫元素结合形成的硫化铁晶体,通常呈现出片状、条状或球状的形态。
这些夹杂物在钢中存在的主要原因是来自于原材料中的硫元素和工艺过程中的硫污染。
2.2 析出原理的概述硫化铁夹杂物析出是指在钢水冷却过程中,由于温度下降和相应成分变化,导致溶解在钢中的硫与其他元素结合生成硫化物并析出。
当钢水冷却至一定温度时,其中所含的溶解性硫会与流动态产生相互作用,并进而促使以二聚、多聚体形态析出出来。
这些形成的固相颗粒就是我们所说的硫化铁夹杂物。
2.3 解释硫化铁夹杂物析出影响因素造成钢中硫化铁夹杂物析出量和分布情况的因素有很多。
- 1、下载文档前请自行甄别文档内容的完整性,平台不提供额外的编辑、内容补充、找答案等附加服务。
- 2、"仅部分预览"的文档,不可在线预览部分如存在完整性等问题,可反馈申请退款(可完整预览的文档不适用该条件!)。
- 3、如文档侵犯您的权益,请联系客服反馈,我们会尽快为您处理(人工客服工作时间:9:00-18:30)。
钢中夹杂物浅析
1. 钢中夹杂物的分类
1.1 根据钢中非金属夹杂物的来源分类
(1)内生夹杂物钢在冶炼过程中,脱氧反应会产生氧化物和硅酸盐等产物,若在钢液凝固前未浮出,将留在钢中。
溶解在钢液中的氧、硫、氮等杂质元素在降温和凝固时,由于溶解度的降低,与其他元素结合以化合物形式从液相或固溶体中析出,最后留在钢锭中,它是金属在熔炼过程中,各种物理化学变化而形成的夹杂物。
内生夹杂物分布比较均匀,颗粒也较小,正确的操作和合理的工艺措施可以减少其数量和改变其成分、大小和分布情况,但一般来说是不可避免的。
(2)外来夹杂物钢在冶炼和浇注过程中悬浮在钢液表面的炉渣、或由炼钢炉、出钢槽和钢包等内壁剥落的耐火材料或其他夹杂物在钢液凝固前未及时清除而留于钢中。
它是金属在熔炼过程中与外界物质接触发生作用产生的夹杂物。
如炉料表面的砂土和炉衬等与金属液作用,形成熔渣而滞留在金属中,其中也包括加入的熔剂。
这类夹杂物一般的特征是外形不规则,尺寸比较大,分布也没有规律,又称为粗夹杂。
这类夹杂物通过正确的操作是可以避免的。
1.2 根据夹杂物的形态和分布,标准图谱分为A、B、C、D和DS五大类。
这五大类夹杂物代表最常观察到的夹杂物的类型和形态:
(1)A类(硫化物类):具有高的延展性,有较宽范围形态比(长度/宽度)的单个灰色夹杂物,一般端部呈圆角;
(2)B类(氧化铝类):大多数没有变形,带角的,形态比小(一般<3),黑色或带蓝色的颗粒,沿轧制方向排成一行(至少有3个颗粒);
(3)C类(硅酸盐类):具有高的延展性,有较宽范围形态比(一般>3)的单个呈黑色或深灰色夹杂物,一般端部呈锐角;
(4)D类(球状氧化物类):不变形,带角或圆形的,形态比小(一般<3),黑色或带蓝色的,无规则分布的颗粒;
(5)DS 类(单颗粒球状类):圆形或近似圆形,直径>13μm的单颗粒夹杂物。
2. 钢中夹杂物主要类型及特征
2.1 硫化物
硫化物是钢液中所含的硫在凝固时以沉淀物析出形成的产物。
它在加工变形中本身不破碎、不变形,属于塑性夹杂物。
硫化物主要有硫化铁(FeS)、硫化锰(MnS)和铁锰硫化物(FeS·MnS)。
硫化铁往往独立存在,大部分处于铁素体中,具有不同的形状,色彩为亮黄色或略呈浅蓝色。
硫化锰则很少独立存在,一般都与硫化铁共存而形成硫化铁硫化锰(FeS·MnS)固溶体。
铁锰硫化合物在明视场下呈灰色或灰蓝色,随着硫化锰的含量减少,将由灰色变为亮黄色。
2.2 氧化物
氧化物为脆性夹杂物,它随着压力加工而破碎,沿金属变形的方向呈链状分
布。
在钢中常见的氧化物有FeO、MnO、SiO、Al
2O
3
、Cr
2
O
3
,等。
这些夹杂物在明
视场下大部分呈灰色至暗灰色,有时略呈紫色。
氧化亚铁(FeO)能溶解大量的氧化亚锰(MnO),从而形成FeO·MnO固溶体,呈纺锤形、小球状。
氧化铝(Al
2O
3
)属于脆性夹杂物,在加工中破碎为不规则的粒状,呈链状分布
于钢中。
不含杂质的三氧化二铝在明视场下呈黄白色,当含有杂质或合金元素时,色彩改变为灰蓝色或灰紫色。
2.3 硅酸盐
硅酸盐夹杂物成分非常复杂,它能够溶解氧化物和硫化物,从而形成各种类型的化合物、共晶体及机械混合物。
在钢中常见的硅酸盐夹杂物有铁硅酸盐
(2FeO·SiO
2)、锰硅酸盐(2MnO·SiO
2
)、铝硅酸盐(3Al
2
O
3
·2SiO
2
),钙硅酸盐
(CaO·SiO
2 )、(2CaO·SiO
2
)、(3CaO·SiO
2
)和铁锰硅酸盐(mFeO·nMnO·SiO
2
)。
在硅酸盐夹杂物中,除锰硅酸盐和铁硅酸盐为塑性易变形外,其它的硅酸盐类为脆性,在加工变形过程中都易破碎,在明视场下观察均呈灰色或暗灰色。
2.4 氮化物
氮化物属于脆性化合物,它在钢中一般不沉淀,常常与亲和力强的钛、钒、锆等合金元素形成稳定的氮化物或其他复杂氮化物型夹杂物。
氮化物的形态相当规则,一般都呈小晶体,多半具有立方体的形状,为正方形、棱形、三角形、长方形等,常在含钛、锆和钒钢中出现。
3. 钢中夹杂物对钢材质量的影响
夹杂物的危害性取决于其数量、形状、大小、分布以及其熔点和物理、化学的性能。
夹杂物呈串状或网络状态存在时,便分割了金属基体的连续性,从而降
低了塑性和强度,使钢在轧制、锻造或其他压力加工过程中,在夹杂物所处区域易形成裂纹。
当夹杂物具有低熔点(FeO与FeS共晶体熔点为985℃)的性质时,在热加工变形过程中,由于其熔融或软化,使钢产生热脆性而导致开裂。
另外,硫化物对金属抗腐蚀性和抗磨性也有不良的影响。
当钢中存在铝夹杂物(Al
2O
3
)或其他氮化物(A1N、TiN、ZrN)时,使钢的表面
硬度不均匀,造成冷加工切削和研磨困难,其表面粗糙度达不到技术要求。
当夹杂物分布于产品零件的表层时,会造成应力集中,早期因疲劳源会引起表层剥落或疲劳开裂。
当钢中夹杂物已超标时,给热处理和焊接工艺带来很大困难,例如造成化学热处理(渗碳、渗氮、碳氮共渗)渗层不均匀;在盐浴炉加热、电阻炉加热、感应加热淬火时,因夹杂物易造成应力集中而形成淬火开裂;在焊接时,将会导致焊接件的强度大大降低或开裂。
4. 钢中夹杂物的检测方法
鉴别钢中的非金属夹杂物的方法分为宏观法和微观法两大类。
宏观法即经常采用的断口鉴别法、硫印、酸蚀(冷蚀、热蚀)法、超声波鉴定法等,这些方法主要是来了解和研究大截面中夹杂物的分布状况。
微观鉴别方法有化学法、岩相法、X射线法、衍射分析法、电子探针(电子扫描)法、金相鉴定法。
前5种方法虽有其优点但都存在一定的局限性,必需与其他的方法配合方能实施。
而金相鉴定法除了对夹杂物的化学成分、晶体结构不能鉴别外,在光学金相显微镜下可以直接观察和鉴别夹杂物的形态、大小、数量、分布、类型、光学性能、塑性及抛光性能等,同时金相法还具有操作简便、容易实施的特点。
就目前而言,应用金相扫描电镜相结合的方法来鉴别非金属夹杂物是最广泛、最有效的方法。
欢迎您的下载,
资料仅供参考!
致力为企业和个人提供合同协议,策划案计划书,学习资料等等
打造全网一站式需求。