机械制造基础铸造过程仿真技术
铸造凝固过程数值模拟
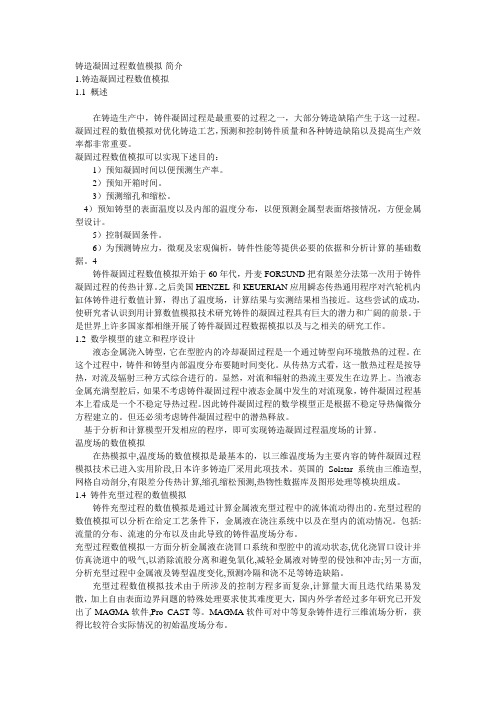
铸造凝固过程数值模拟-简介1.铸造凝固过程数值模拟1.1 概述在铸造生产中,铸件凝固过程是最重要的过程之一,大部分铸造缺陷产生于这一过程。
凝固过程的数值模拟对优化铸造工艺,预测和控制铸件质量和各种铸造缺陷以及提高生产效率都非常重要。
凝固过程数值模拟可以实现下述目的:1)预知凝固时间以便预测生产率。
2)预知开箱时间。
3)预测缩孔和缩松。
4)预知铸型的表面温度以及内部的温度分布,以便预测金属型表面熔接情况,方便金属型设计。
5)控制凝固条件。
6)为预测铸应力,微观及宏观偏析,铸件性能等提供必要的依据和分析计算的基础数据。
4铸件凝固过程数值模拟开始于60年代,丹麦FORSUND把有限差分法第一次用于铸件凝固过程的传热计算。
之后美国HENZEL和KEUERIAN应用瞬态传热通用程序对汽轮机内缸体铸件进行数值计算,得出了温度场,计算结果与实测结果相当接近。
这些尝试的成功,使研究者认识到用计算数值模拟技术研究铸件的凝固过程具有巨大的潜力和广阔的前景。
于是世界上许多国家都相继开展了铸件凝固过程数据模拟以及与之相关的研究工作。
1.2 数学模型的建立和程序设计液态金属浇入铸型,它在型腔内的冷却凝固过程是一个通过铸型向环境散热的过程。
在这个过程中,铸件和铸型内部温度分布要随时间变化。
从传热方式看,这一散热过程是按导热,对流及辐射三种方式综合进行的。
显然,对流和辐射的热流主要发生在边界上。
当液态金属充满型腔后,如果不考虑铸件凝固过程中液态金属中发生的对流现象,铸件凝固过程基本上看成是一个不稳定导热过程。
因此铸件凝固过程的数学模型正是根据不稳定导热偏微分方程建立的。
但还必须考虑铸件凝固过程中的潜热释放。
基于分析和计算模型开发相应的程序,即可实现铸造凝固过程温度场的计算。
温度场的数值模拟在热模拟中,温度场的数值模拟是最基本的,以三维温度场为主要内容的铸件凝固过程模拟技术已进入实用阶段,日本许多铸造厂采用此项技术。
英国的Solstar系统由三维造型,网格自动剖分,有限差分传热计算,缩孔缩松预测,热物性数据库及图形处理等模块组成。
铸造过程的模拟仿真技术及在发动机零部件设计上的应用

热应力数值模拟
铸锻材料与工艺研究所
铸件凝固过程中的热应力数值模拟涉及凝固 过程复杂的传热分析、随温度和组织变化的力学 模型、铸件和铸型之间的相互作用和热裂的发生 等。
铸件热应力模拟可以预测铸件凝固过程中应 力和变形的动态变化,在此基础上进行热裂的预 测,并对铸件残余应力和残余变形进行分析,为 铸件尺寸精度控制提供依据。
化技术可以有效地发现铸件可能产生缺陷的位置
和种类,从而指导工艺人员采取恰当的工艺措施 加以避免。
ห้องสมุดไป่ตู้
发动机工程研究院
铸造过程的模拟仿真技术
铸锻材料与工艺研究所
通过数值模拟的应用,可以分析铸件中存在
的各种缺陷的产生原因,进而采取相应工艺措施 来消除缺陷,实现工艺优化,同时可以节省大量 的人力、物力和财力,缩短产品从设计到应用的 周期,增强产品的市场竞争能力。
发动机工程研究院
铸锻材料与工艺研究所
数值模拟: 在计算机上实现的一个特定的计算,通
过数值计算和图像显示,履行一个虚拟的物 理实验—数值试验。
发动机工程研究院
有限元法
铸锻材料与工艺研究所
发动机工程研究院
有限元法
铸锻材料与工艺研究所
有限元法(FEM-finite element method)
横浇道
压铸压射速度----压室内冲头推动金属 液时的移动速度。
慢压射速度----通常包括冲头越过浇料 口这段行程。一般为0.1~0.5m/s。
快压射速度----确定内浇道截面积、内 浇口速度,然后根据压室直径得到。
直浇道
内浇道
发动机工程研究院
铸锻材料与工艺研究所
铸件充型过程(流场)数值模拟
排溢系统----熔融金属在填充型腔过程中,排除型 腔内的气体、涂料余烬以及流动金属前沿的冷金 属的通道和处所。
基于虚拟现实的铸造工艺流程仿真

基于虚拟现实的铸造工艺流程仿真大部分机械工程专业的学生并没有真正意义上的进行铸造工艺实验,多数是从书上获得理论知识,或者是在金工实习时,听或观察老师的操作,使得很多学生并不熟悉真正的铸造是如何进行的。
针对这种情况,本文利用虚拟现实的技术仿真铸造工艺的流程,使得学生可以在没有现实设备的基础下,也能依靠自学或者书本的知识,自己进行虚拟的铸造实验。
铸造工艺有很多类型,本文选择了压力铸造工艺流程的仿真。
压力铸造是一种精密的铸造技术,是一种不可或缺的铸造技术,也是机械工程专业的学生必须掌握的铸造技术。
虚拟现实技术综合利用计算机仿真技术、计算机图形学等等多种技术,通过产生视觉、听觉等,使得用户产生一种身临其境的感觉。
其中很多软件能实现这种技术,本文采用了容易掌握和理解的EON Studio来实现压铸工艺的仿真。
本文首先对压力铸造作了简介,对其四种类型:热室压力铸造、冷室卧式压力铸造、冷室立式压力铸造和冷室全立式压力铸造的工艺流程进行了详细的分析,并且选择了热室压力铸造和冷室卧式压力铸造进行工艺仿真。
而后简单介绍了EON Studio的重要功能,采用多种节点的配合作用,实现了对压力铸造工艺流程的仿真。
I第一章绪论1.1 选题的背景及意义机械工程是社会发展和国民经济建设的基础学科之一。
机械类专业人才的培养在整个教育中是非常重要的一部分。
但我国机械专业的教学长期以来沿用原苏联的教学模式。
而这种教学模式存在着严重的弊端,例如专业口径较窄、专业划分过细、内容相对过深、体系过于陈旧。
随着我国的新技术的迅速发展,使机械工程、机械制造比以前的时代发生了根本性变化。
这种传统的机械类教学模式必须彻底改革,不然就不会有创新。
实验教学是一种将课本知识结合到实际的教学方式,实验教学不仅巩固了学生课本上的基础知识,而且还能够培养学生的实际操作能力和动脑能力。
由于机械专业属于工科类教学,对学生的实践动手操作能力要求极高,所以实验教学是提高机械工程专业学生实践动手操作能力的一个重要教学环节。
机械制造基础-铸造过程仿真技术

五砂芯设计
• 根据铸件结构知,需要模样一套,芯盒18个,具 体如工艺图上所示,其中下芯顺序为17、18-1612-7、8-9、11-10、12-15-2、3-4、5-14-6、13 • 1#芯与16#芯不留芯头间隙,其余砂芯上箱芯头 间隙1mm,下箱芯头间隙0.5mm;砂芯分段部位做 成直面,芯盒做稍板。 • 下面的下芯芯座周边做出R3mm集砂槽;16#减轻 如图,7#(8#)芯做减轻,吃砂量大于50mm。
六浇注系统设计
由于该铸件的材料为B级钢,采用转 包式浇注系统,大铸件,从铸件外导框端头引 入钢液,采用过桥浇注,一箱一件。 1、确定包内直径:采用10t漏包,Ø45mm包孔浇 注铸件 2、浇注时间:t=Q/q=447/42=10.6s,浇注过程中, 应遵循缓流→全速→缓收流的浇注原则,且由 于改侧架壁厚偏厚,因此点浇冒口3次。
应
砂型重力铸造(实例2)
用
实
例
材料:ZG1Cr18Ni12Mo2Ti,船用炮座铸造工艺装配图
实际生产运用
应
砂型重力铸造(实例2)
用
实
例
材料:ZG1Cr18Ni12Mo2Ti,船用炮座浇注过程模拟
实际生产运用
应
砂型重力铸造(实例2)
用
实
例
材料:ZG1Cr18Ni12Mo2Ti,船用炮座浇注过程模拟状态图
数据库
一铸件的材质和结构
• 铸件的三维图
一铸件的材质和结构
• 该铸件为火车轴的侧架,铸件的材质为 B级钢, (即C25钢)该铸件属于箱式结构,复杂薄壁 铸件,轮廓尺寸为2235mm×565mm×420mm,质 量为314KG,体积为4.0×107mm3 。内腔连接 筋较多,平均壁厚25mm,最大厚度为31mm。中 央导框框磨耗板面不加工,外导框间距、滑槽 中心多个圆孔等配合面尺寸要求高 。
浅谈铸造过程模拟仿真技术

浅谈铸造过程模拟仿真技术赵建华陈红兵【摘要】摘要:经过几十年的发展,铸造过程数值模拟技术取得了巨大进步,对实际生产产生了重要作用。
本文介绍了铸造过程数值模拟的研究方向及其基本理论,例如,充型过程数值模拟、凝固过程数值模拟、应力场数值模拟、微观组织的数值模拟和模拟技术发展趋势。
【期刊名称】大型铸锻件【年(卷),期】2007(000)004【总页数】4【关键词】铸造过程;数值模拟;发展趋势铸造过程的数值模拟技术是铸造行业的重要发展方向,包括凝固过程(温度场)数值模拟,铸件充型过程(流场)数值模拟,铸造热应力数值模拟,铸造合金的微观组织模拟,以及铸造缺陷(缩孔、缩松及热裂)的预测[1]。
研究任何一种物理现象,都可归结为确定表示这种现象特点的各物理量之间的关系。
对于复杂的物理过程,应该用数学物理方法来确定各量的关系。
数值模拟就是通过软件对铸件充型凝固过程的数值计算。
通过计算结果来分析铸造工艺参数对铸件成型的影响,从而可以优化铸造工艺参数以及改变结构设计,以便获取优质铸件。
铸造是生产机械产品毛坯的重要方法,在国民经济、国防建设中占有重要的地位。
随着激烈的市场竞争,用传统的铸造试错法进行铸件设计、生产已不能适应市场需求,唯一出路就是利用现代技术来改造传统工艺、方法。
铸造过程的数值模拟及优化技术CAE(computer aided engineering)是铸造技术发展的必然趋势。
铸造CAE技术是获取优质铸件的必要手段,可以提高产品的竞争力,缩短产品的开发周期,降低成本,可以为企业和社会带来巨大的经济效益。
铸造过程的数值模拟技术包括以下几个方面,现分别进行介绍。
1 铸件充型过程数值模拟铸件充型过程中会产生氧化、传热、热损失、冲击破坏等一系列化学和物理变化,因此,充型过程与铸件质量密切相关[1,4]。
采用数值计算方法,不仅可以模拟出液态金属在铸型中的流动状态,而且可以根据模拟得到的液态金属流动速度、压力变化规律来优化浇注系统的设计,防止浇道中吸气,消除流股分离以避免氧化,减轻对铸型的冲蚀等。
CAE技术实现铸造工艺精益化生产及质量追溯

CAE技术实现铸造工艺精益化生产及质量追溯CAE技术实现铸造工艺精益化生产及质量追溯近年来,随着制造业的发展,铸造工艺精益化生产和质量追溯成为了企业追求效益和质量的关键。
在这一背景下,CAE(计算机辅助工程)技术越来越被广泛应用于铸造行业,为铸造工艺的优化、控制和质量追溯提供了强大的支持和保障。
I. CAE技术在铸造工艺优化中的应用CAE技术是一种通过计算机模拟和仿真技术,对铸造过程进行优化和预测的方法。
在铸造工艺优化中,CAE技术能够通过以下几个方面的应用实现铸造工艺的精益化生产。
1. 输入参数优化通过CAE技术,可以对铸造工艺的输入参数进行优化。
通过建立数值模拟模型,可以预测不同输入参数对产品质量的影响,并通过优化算法得到最佳的输入参数组合。
这样可以在保证质量的同时,最大限度地提高生产效率。
2. 工艺参数优化CAE技术可以模拟铸造过程中的温度、流场、应力等参数,通过调整工艺参数,如浇注温度、浇注速度等,实现铸件内部缺陷的最小化。
同时,通过模拟模型的优化,可以减少试验和成本,提高工艺的稳定性和一致性。
3. 设备布局优化在铸造生产过程中,设备的布局对生产效率和质量有着重要的影响。
通过CAE技术,可以模拟生产车间的布局,分析车间内的流程和物流,优化设备的布局,提高生产效率和质量水平。
II. CAE技术在铸造质量追溯中的应用1. 产品质量预测通过CAE技术,可以预测铸件的缺陷和性能。
通过数值模拟模型,可以分析铸件的应力、变形等参数,预测可能出现的缺陷情况,并及时采取措施进行调整和优化。
同时,CAE技术也可以模拟进行性能测试,如疲劳强度、磨损等,为产品的性能评估提供参考。
2. 缺陷原因分析当铸件出现缺陷时,CAE技术可以通过模拟分析,找出其产生的原因。
通过模拟模型,可以观察到铸造过程中的温度、应力等参数分布情况,从而找到缺陷产生的根本原因。
这有助于进一步改进和优化铸造工艺,减少缺陷发生的概率。
3. 质量溯源随着质量追溯的要求越来越高,通过CAE技术可以实现对产品质量的溯源。
铸造虚拟仿真技术的应用及工艺缺陷分析

铸造虚拟仿真技术的应用及工艺缺陷分析摘要:铸造工艺模拟展示了专家用户的质量现状。
铸造虚拟仿真技术是现代企业先进设计的必备方法之一。
随着铸造虚拟仿真技术的发展,企业对掌握和了解铸造CAE技术人才有着迫切的需求。
结合国家人才培养的重大战略需求,落实清华大学的育人理念,通过对工程实践和创新教育发展趋势的研究,凝练中心发展理念,清华大学基础工业训练中心与MAGMA合作,并将会用MAG-MA教育版软件为清华大学以及周边大学的学生提供模拟课程及体验。
本文就铸造虚拟仿真技术的应用及工艺缺陷展开探讨。
关键词:虚拟仿真;MAGMA软件;缺陷分析引言由于影响铸件质量的因素众多,物理、冶金和铸件几何的复杂的相互作用,所以铸造经验是“优化制造工程”的主要依据。
1模拟仿真技术在铸造生产中的应用传统铸造生产模式中,浇冒口系统设计、铸型的设计与材料的选择、铸造缺陷的预测与控制等铸造工艺设计工作,往往需要依靠大量的铸造实际生产经验。
这种工艺设计模式对于形状结构较为简单的零件,或是具有相似结构铸件的设计与生产时,是有一定优势的。
但是在生产大型复杂铸件以及新产品的设计与开发,且没有相关实际生产经验时,只能通过反复的工艺试验来确定最合理的工艺参数,且浇冒口系统、冷铁等的放置位置也不能得到精确控制,铸件的质量难以得到保证。
尤其对于多样性、少批量、高技术要求,甚至是个性化定制的产品,这种工艺探索模式不仅需要更长的设计和反复工艺试验的周期,同时大量的工艺试验也耗费大量的生产成本,显然这种工艺设计模式已经无法满足现代铸造生产模式的要求,而铸造模拟技术则解决了这一问题。
利用铸造模拟技术对金属液的流动充型过程、凝固温度场分布以及缩孔、缩松等可能出现的铸造缺陷类型、位置及数量等进行模拟与分析。
然后根据铸造模拟结果优化工艺设计,优化后再次进行相应的铸造模拟,经过反复的模拟分析与工艺优化,直至消除铸造缺陷为止,从而获得最佳的铸造生产工艺。
这种利用模拟仿真进行工艺设计与优化的方式,可有效缩短工艺设计与生产周期,提升铸件品质。
金属材料锻造过程建模与仿真分析

金属材料锻造过程建模与仿真分析金属材料锻造是一种常见的金属加工方法,通过将金属材料加热至一定温度,然后施加压力将其塑性变形,最终得到所需形状的零件或产品。
在现代工业生产中,锻造被广泛应用于航空航天、汽车制造、机械制造等领域。
为了实现高效、精确和可靠的锻造过程,建模与仿真技术成为不可或缺的工具。
锻造过程的建模是将现实世界中的物理过程转化为数学模型的过程。
通过建立准确的模型,可以帮助我们提前预测和评估锻造过程中的各种参数,如温度分布、应力分布、变形量等,从而指导生产过程和优化工艺方案。
常用的建模方法包括有限元法、计算流体力学等。
有限元法是一种常用的建模与仿真技术,广泛应用于金属材料锻造过程中。
该方法将整个锻造过程分割成许多小的有限元,然后通过求解数学方程来模拟材料的变形、温度变化以及其他物理过程。
通过有限元法,我们可以得到锻件的应力分布、应变分布、温度分布等信息,为优化工艺参数和设计模具提供参考。
在建模过程中,要考虑的因素有很多。
首先是金属材料的本构关系。
不同的金属材料具有不同的力学特性,包括弹性模量、屈服强度、流动应力等。
这些参数的准确描述对于建模分析十分重要。
其次是摩擦因数。
在锻造过程中,摩擦是一个不可忽视的因素,它会影响材料的变形行为以及所需要的锻造压力。
除了金属材料的参数,锻造过程的温度变化也需要考虑。
在锻造开始的时候,金属材料是需要被加热的。
温度的变化会直接影响到材料的流动行为和变形行为。
因此,在建模过程中需要准确地考虑温度的变化规律。
此外,还需要考虑锻造过程中的机械加载情况以及模具形状对锻件变形的影响等问题。
在完成建模之后,仿真分析是必不可少的一步。
通过对建模结果的仿真分析,可以预测锻造过程中可能出现的问题,如应力集中、材料破裂等,并采取相应的措施来解决这些问题。
同时,仿真分析还可以对不同的工艺参数进行比较和评估,从而找到最佳的工艺参数。
正如上述所提到的,金属材料锻造过程的建模与仿真分析在现代工业生产中具有重要的地位。
河北工业大学科技成果——铸件凝固过程模拟与工艺优化

河北工业大学科技成果——铸件凝固过程模拟与工艺优化项目简介铸件的成形过程是在铸型中完成的,因此它的可控性很差。
随着计算机技术的发展,铸件凝固过程计算机模拟仿真技术随之诞生。
本项目利用计算机对铸件的整个生产工艺流程(工艺设计、配料、熔炼、造型、浇铸、炉前分析等)全过程进行计算机辅助设计和工艺分析,对整个生产系统进行时时监控,对工艺参数进行闭环调整,及时发现生产过程中可能出现的漏洞并采取相应措施予以改进,以生产出高品质的铸件。
本项目是铸造行业的前沿技术,研究利用计算机模拟仿真技术控制铸造工艺过程,铸造出精密铸件。
市场前景在我国大多数企业的铸件产品出品率、成品率及质量都不高,铸件缺陷较多,严重的降低了企业的有效生产效率,从而阻碍了企业发展的脚步。
我们通过对现有铸件的工艺方案的分析,应用先进软件进行三维造型,设计合理的浇注工艺,对凝固过程模拟与优化,从而消除缩孔、缩松与冷隔等缺陷。
该技术适用于所有的铸造企业,能够显著提高逐渐的成品率,为企业创造更多利润,提高企业的竞争力。
规模与投资服务器与高配置计算机,资金需求不超过20万元。
生产设备利用企业现有的铸造设备,以及高配置的计算机以和相关的模拟软件。
效益分析年产10000吨,废品率降低按10%计算,可节约成本200万元。
合作方式合作开发。
铸造工艺仿真设计前处理及过程处理应用技术

铸造工艺仿真设计前处理及过程处理应用技术房文亮;王仲珏;高洪;杨光耀【摘要】This paper,analyzes and summarizes the main contents and methods of preprocessing and pro-cessing technology of simulation design of casting process in every part.It proposes the technological roadmap of the process and the platform and the steps of every application by applying ProCAST and MAGMAsoft in order to provide theoretical and technical support for efficiently applying the simulation design of casting process.%以应用ProCAST和MAGMAsoft 2款软件为例,针对铸造工艺仿真设计前处理和过程处理每个环节的主要内容与使用方法进行了较为详细地归纳、分析和总结。
提出了处理过程的技术路线,并系统地介绍了每项应用内容的操作平台与使用步骤,从而为高效地应用铸造工艺仿真设计提供理论和技术支持。
【期刊名称】《安徽工程大学学报》【年(卷),期】2015(000)002【总页数】5页(P57-61)【关键词】铸造工艺仿真设计;前处理;过程处理;应用技术【作者】房文亮;王仲珏;高洪;杨光耀【作者单位】安徽工程大学机械与汽车工程学院,安徽芜湖 241000;安徽工程大学机械与汽车工程学院,安徽芜湖 241000;安徽工程大学机械与汽车工程学院,安徽芜湖 241000;安徽工程大学机械与汽车工程学院,安徽芜湖 241000【正文语种】中文【中图分类】TG249当前世界主流的铸造仿真软件包括国外(ProCAST、MAGMAsoft、Anycasting、Flow-3D、Solid-CAST、Ansys、Novacast)及国内(华铸CAE、华星)9款软件[1-2].虽然它们都是进行铸造仿真计算的工具,但其设计思路和方法并不相同.课题组对这9款软件进行了较为系统地学习和研究,分析了各自特点,并对其共性的内容进行了归纳和总结.为更好地应用铸造工艺仿真设计,主要以ProCAST和MAGMAsoft 2款软件为例,在介绍了铸造工艺仿真设计的前处理及过程处理基本内容的基础上,提出了其每个环节的主要内容和使用方法,以及处理过程中每项应用内容的操作平台与使用步骤,可为铸造工艺仿真设计的学习者提供一些参考. 铸造工艺仿真设计的前处理是进行铸造仿真模拟的前提和重要保障,它不仅决定了后续模拟的精确性,而且还影响模拟速度的快慢.其中,前处理主要包括几何建模和网格划分.1.1 几何建模几何建模有2种方法:①利用铸造仿真软件自带的建模功能建模;②通过其他的三维制图软件(如UG、Pro/E、Solidwork等)建模后导出为铸造仿真软件可接受的实体格式(如STL、PARASOLIDS、IGS、STEP等)再导入到仿真软件中.除Ansys具有较强的建模功能外,其他大多数铸造仿真软件的建模功能都较弱或者没有此功能,主要采用后一种方法.UG在三维实体造型方面表现突出,能够对各种结构复杂的三维实体进行细致、准确地绘制,推荐使用.在导出时有些铸造仿真软件需要将铸件和浇冒口系统求和后一起导出(如ProCAST、Ansys、Novacast 等),另一些则需分开导出(如MAGMAsoft、Anycasting、Flow-3D、SolidCAST、华铸CAE、清华铸造之星等).1.2 网格划分网格划分的好坏直接影响后续模拟分析的速度和精度[3].在网格划分中要综合考虑各种因素,主要包括网格形状和大小的选择.网格形状主要分为2种:三角形和四边形.三角形单元划分灵活,可适应复杂的几何形状,精度高,如发动机缸体、汽车轮毂等;四边形单元则要求铸件结构比较规则.网格的大小决定了网格的数量和密度,对于同一铸件的网格划分,网格越小,网格数量和密度越大,精度越高,但模拟速度慢.确定网格大小的基本原则是零件的最薄壁厚要大于网格的单元长度.活塞尾的网格划分实例如图1所示.该产品长2.834 65 in,高1.306 97 in,结构复杂程度适中,拐角处较多,故选择三角形网格.产品最薄壁厚为0.078 74 in,网格的单元长度设为0.05 in.以ProCAST软件为例,对铸件活塞尾进行网格划分,网格数量为136 737,节点数为26 266.可以看出,网格质量良好,没有坏面.网格划分原理主要为有限元法和有限差分法.有限元法能够针对复杂铸件的曲面和结构单元较多、拐角处结构复杂等特点对其进行细致的网格划分,精度高,但计算量大,硬件配置要求高,网格形状一般采用三角形.ProCAST是基于有限元法的铸造仿真软件,其主要提供了3种接口方式实现与其他前处理软件的连接[4]:①其他前处理软件建模后把模型导入MeshCAST,用MeshCAST划分网格;②其他前处理软件建模并划分面网格后再导入MeshCAST中;③其他前处理软件建模并划分体网格后导入ProCAST中,并进行后续工作.针对这3种接口方式可以导入的文件类型分别为:①STL、IGES、PARASOLIDS、STEP、Binary STL、Re-start;②PATRAN Surface Mesh、I-DEAS Surface Mesh;③PATRAN Volume Mesh、I-DEAS Volume Mesh.用于ProCAST的前处理软件有Hypemesh、Pro/E和Geomesh等[5-7],经试验比较发现:①Hyper Mesh的网格划分功能强大,可对导入的模型进行细致的网格划分,导出的面网格文件与MeshCAST的兼容性好,错误少,推荐使用;②Pro/E可建模并划分面网格后导入到MeshCAST中划分体网格,但网格划分模块受到软件本身的限制,功能较弱,比较适用于习惯于使用Pro/E的工作者;③Geomesh可对导入的模型进行面网格的划分,但要求模型的错误较少,适合结构不复杂的模型.其他大多数铸造仿真软件则基于有限差分法.该方法数据结构简单、算法简洁,因此,网格划分简单、速度快,硬件配置要求低,得到广泛应用.但精度较低,适合结构简单的铸件.网格形状一般采用四边形.经前处理后,针对具体铸件的铸造方法、铸件结构和铸件材质,需制定出合理的工艺方案技术路线,具体为:铸件缺陷分析与预测→确定仿真内容→选择仿真软件→仿真计算和结果分析→工艺方案改进和优化→合格(优化)工艺→制定技术和生产管理文件→指导生产实践.依据技术路线进行铸造工艺仿真设计的过程处理,该处理过程是模拟运算的核心,直接决定了仿真的真实性和可靠性.其中,过程处理主要包括材料数据的获取、存储、调用以及参数设置等.2.1 获取材料数据的方法材料数据的获取方法主要有计算法、试验法、反求法和摄取法,较常用的为计算法和试验法.(1)计算法.计算法是指通过软件自带的材料性能计算功能来进行材料各种性能参数的计算和添加的方法.ProCAST针对不同的材料特性,提供了3种计算模型:Scheil model、Lever rule、Back Diffusion.了解不同材料的特性后,可进行材料数据的录入和计算.具体方法为:打开ProCAST软件的材料性能计算模块,找到“Material”菜单下的“Assign”并打开,可看到材料数据的列表,选择“Add”,将已知材料的化学成分输入到“Composition”子菜单中,选择计算模型“Apply”后,点击“Store”,ProCAST通过内部的计算模块计算出该种材料的热、流动等物性参数.以HT150为例,HT150的化学成分如表1所示.计算后的导热率和比热参数曲线图如图2、图3所示.(2)试验法.试验法是指通过数学计算和实测来获取材料相关参数的方法.对于新开发的材料、非标准钢号以及已知材料的部分性能参数,常需要设计试验方案进行计算和实测,获取材料的相关参数,以便存储到铸造仿真软件中.该方法简单、原始,不再举例说明.获取相关参数的方法与步骤:①化学成分:金属材料常采用光谱分析;②力学性能参数:新开发材料的力学性能参数,如弹性模量和泊松比,可以采用电测法和引伸计法测定等;③热物性参数:直接测量法.非稳态线性法测定热导率,激光脉冲法测定热扩散系数、比热容和导热系数等;间接测量法.射线衍射法测试高温液态金属密度,比较法测定热容,根据计算公式λ=ρCpa测定导热系数[8]等;④铸造工艺参数:金属的冶炼温度、出炉温度、浇注温度、浇注时间和模具预热温度等参数可根据相关铸造原理计算并通过生产实际进行实测.(3)反求法.反求法是相对于正向求解来说的,即通过等号右边的已知量来反推等号左边的未知量.反求法可以利用实际的测试温度数据来确定边界条件和材料的热物理性能,最大限度地提高模拟结果的可靠性,如界面换热系数.通过阅读相关文献和技术资料[9],简述反求法的操作步骤:①选取铸件的若干个节点进行凝固过程的温度数据采集,并全部记录原始数据;②按照正常的模拟步骤设置PreCAST里的参数,选择“Inverse”菜单下的“Boundary Condtions”,勾选“Activate”,选择计算对象;③在“Inverse Setting”里输入所测得温度点的节点编号,设置相关计算参数;④按照prefix.tt文件的格式编辑实测温度场获得温度-时间数据,并保存为prefixim.dat文件;⑤返回主界面,点击ProCAST菜单下的“Inverse”,启动逆运算.(4)摄取法.摄取法是指通过其他数据库软件与铸造仿真软件之间建立数据接口,将数据库软件内的材料数据信息导入到铸造仿真软件中,补充和完善数据库.一些研究人员已开发了多款可服务于Pro-CAST的材料数据库软件,如JMat Pro软件和吴翠姑等人开发的“铸造材料数据库”软件[10].以JMat Pro为例:①点击“export”,选择“all to Procast format”,导出ProCAST格式热物理参数,如图4所示.修改材料名称为“AA2024”并保存;②打开JMatPro软件安装目录里的ProCAST文件夹,找到导出的数据文件MATL.DB,并用记事本打开,复制全部数据粘贴到Program Files\ESIGroup\ProCAST\2008.0\dat\db里的MATL.DB文件里,保存并退出,打开ProCAST的材料数据模块可看到导入的AA2024材料,如图5所示.2.2 存储和调用材料数据(1)存储材料数据.存储材料数据是指将获得的材料相关参数数据存储到铸造仿真软件内的方法和过程.针对铸造仿真软件的材料数据存储难的问题,MAGMAsoft 提供了一个二次开发平台,利用其数据库系统可对MAGMAsoft数据库中没有的材料数据进行添加和存储,包括Global、User和Project 3个模块,现有文献已阐述地很详细,不再举例说明.以User为例简述其操作步骤:①选择数据库(Database)菜单中的“User”模块;②在弹出新材料命名窗口中写入材料名称,点击“OK”确认,选择“Edit”;③选择“Edit”菜单下的“General Parameters”选项,在设定基本参数的选项中写入相关参数并按回车确认.接着在Edit菜单中选择“Composition”选项,写入材料各成分的质量分数;④打开“Data”菜单,点击“save”进行保存.(2)调用材料数据.调用材料数据是指将其他标准的数据转换为适合某款铸造仿真软件的标准数据并为其所用的方法和过程.大多数铸造仿真软件由于是不同国家研发的,因此数据标准也不相同,如MAGMAsoft采用的是德国标准.如何将其他途径获得的不同标准数据在仿真软件中调用是一个难点,本文将阐述MAGMAsoft不同标准数据的调用方法和步骤,简单易懂,读者可依此方法操作,不再举例说明:①将国内或国际标准和德国标准对照,若在德国标准钢号表中能够找到该材料,则在MAGMAsoft数据库中找到该材料并使用;②针对MAGMAsoft中没有的标准材料,可查询其他铸造CAE软件材料库、专门的材料数据库软件或相关标准手册中的材料数据,在MAGMAsoft数据库中新建该材料,将其相关参数输入到材料数据库并保存.2.3 参数设置参数设置是指针对具体铸造工艺方案对铸造仿真软件中的相关参数进行设置的方法和过程.参数设置是铸造工艺仿真设计的一个重要内容,由于不同的铸造仿真软件开发的原理、角度和工程模型并不相同,因此参数设置内容会有所不同.相比于其他铸造仿真软件来说,MAGMAsoft的参数设置内容最为全面和细致,设置方法便捷,每设置完一个参数才能进入到下一个环节,避免了设置过程中产生遗漏和重复. MAGMAsoft的参数设置内容及步骤为:模型、过程计算选择→材料设置→传热系数设置→边界条件设置→具体铸造工艺参数设置→充型设置→凝固设置→应变设置→计算设置.其难点在于材料设置,下面简述其具体设置方法:①打开MAGMAsoft的“Simulition”界面,进入材料设置界面,如图6所示;②选择需设置的模型,点击“select data”,选择数据库和材料类型,如图7所示,点击“ok”,然后点击“parameters”,根据需要设置涂层参数.模型前面带“+”符号的表示一个材料组,可点击“expand”对材料组内的单个模型即模型前面带“-”号的进行材料设置,操作方法同上.在铸造工艺仿真设计的前处理过程中需重视网格划分的重要性,在确保网格质量良好前提下,尽量减少网格数量,节约模拟运算的时间.对于大多数铸造仿真软件来说,材料数据的获取、存储以及参数设置内容和方法基本类似,只是具体操作方法不同,这为铸造工作者能够高效地利用铸造仿真软件创造了条件.通过对铸造工艺仿真设计的前处理及过程处理的主要内容和常用方法较为详细的阐述,为铸造工艺仿真设计的初学者能够快速掌握这门技术提供了一定的参与.【相关文献】[1]马玉乐.计算机仿真技术在消失模鋳造工艺设计中的应用[D].芜湖:安徽工程大学,2012. [2] S M Xiong,W B Lee.An efficient thermal analysis system for the die casting process [J].Journal of Materials Processing Technology,2002,128:18-30.[3]方志平.侧架CAD/CAE/CAM技术研究[D].哈尔滨:哈尔滨理工大学,2005.[4]苏大为,赵玉涛,王雷刚,等.前处理软件与ProCAST的接口连接方式[J].特种铸造及有色合金,2007,27(5),348-350.[5]王旭东.Pro/E与ProCAST的接口连接方式[J].机车车辆工艺,2005(2):45-46.[6]边弘晔,李鹤,闻邦椿.Hyper Mesh有限元前处理关键技术研究[J].机床与液压,2008,36(4):161-164.[7]柳朝华,郭志英.网格划分技术在塑料法兰CAE中的应用[J].模具技术,2006,8(4):8-10.[8]付金良.国内标准材料数据库的开发及在铸造CAE中的应用[D].兰州:兰州理工大学,2007.[9]郝炜,康健,马敏团,等.铸型界面换热系数的测定方法研究[J].热加工工艺,2007,36(27):11-15.[10]吴翠姑.铸造CAE软件数据库管理系统的研究与开发[D].天津:河北工业大学,2008.。
铸造仿真分析报告

铸造仿真分析报告1. 引言本文档为铸造仿真分析的报告,根据实际铸造工艺和仿真数据,对铸件的铸造过程进行了分析和评估。
通过仿真分析,可以提供准确的铸造工艺参数和辅助决策,从而优化铸造工艺,提高产品质量,降低生产成本。
本报告将详细介绍铸造仿真所涉及的模型、材料和分析结果,供相关人员参考。
2. 铸造模型在铸造仿真分析中,我们选择了某个具体的铸造模型进行仿真。
该模型是由CAD软件建模生成的三维几何模型,包括铸件和模具。
模具的形状和尺寸与真实情况一致,并考虑了芯子的位置和形状。
同时,还考虑了其他辅助结构和装备,如浇口、浇道和支撑结构等。
3. 材料参数在仿真分析中,材料参数是非常重要的输入。
通过实验和研究,我们得到了铸造材料的各种物理和力学参数。
这些参数包括材料的热尺寸、导热系数、比热容和机械性能等。
在铸造过程中,这些参数将直接影响到铸件的温度分布和变形情况。
4. 工艺参数铸造工艺参数是指在铸造过程中控制和调节的参数,如浇注温度、浇注速度、浇注方向和冷却时间等。
这些参数对于铸造过程的控制非常重要,能够直接影响铸件的质量和性能。
5. 仿真结果根据铸造模型和输入的材料参数和工艺参数,进行了铸造仿真。
通过仿真软件的模拟计算,得到了一系列的仿真结果。
这些结果包括铸件的温度分布、凝固曲线、应力分布和变形情况等。
这些结果能够直观地展示铸造过程的物理特性和工艺效果。
6. 结果分析根据仿真结果,我们对铸件的铸造过程进行了详细的分析。
根据温度分布,可以判断出铸件的凝固过程和热传导情况。
通过应力分布和变形情况,可以评估铸件的内部质量和外观形态。
同时,还可以根据仿真结果对铸造工艺参数进行优化和调整,以改善铸件的质量和性能。
7. 结论通过铸造仿真分析,我们得到了铸件的详细铸造过程和相关的物理特性。
通过分析模型和仿真结果,我们可以对铸造工艺参数进行优化和调整,以提高铸件的质量和效率。
此外,仿真分析还可以帮助我们预测和解决一些潜在的问题,如热裂纹和变形等。
金属铸造成形过程的数值模拟

金属铸造成形过程的数值模拟金属铸造是一种复杂的成形工艺,在这个过程中,金属经历了从液态到固态的转变。
为了了解金属铸造过程中的物理和化学变化,生产厂家通常会使用数值模拟技术来模拟这个过程。
数值模拟技术是一种预测性技术,它可以模拟金属铸造的温度场、压力等参数,甚至可以预测颗粒的行为。
在这篇文章中,我们将深入探究金属铸造成形过程的数值模拟技术。
首先,让我们简要介绍金属铸造成形的过程。
通常,金属铸造分为砂型铸造、金属型铸造和压铸等几种类型。
每种类型的铸造工艺都有其独特的特点,但它们的基本处理程序是相似的。
在标准的金属铸造过程中,首先熔化金属,随后将熔化的金属倒入模具或模型中,然后等待金属冷却成形。
数值模拟是一种可以预测金属铸造成形的过程,可帮助制造商优化成形过程并减少生产成本。
铸造数值模拟的过程包括数学描述、数值方法、计算机仿真等几个步骤。
数学描述是指将铸造过程中涉及到的物理各参数用数学公式表示出来,包括温度、流体力学、热力学和相变等。
数值方法是指使用计算机模拟数学公式,对金属铸造过程进行数值计算。
这个过程中,需要选取合适的数值方法、计算模型和模拟系统。
最后,计算机仿真帮助生产厂商检查结果并进行模拟验证。
在金属铸造成形的数值模拟过程中,最重要的功能之一是热仿真模块。
这个模块使用计算机模拟成形过程中金属的温度场变化。
不同铸造过程中的有不同的需求——砂型铸造需要精确地控制铸型的壁厚和冷却速度,而金属熔模铸造需要保证金属的温度始终保持在一定范围内。
在这个过程中,需要研究的一些关键问题是:铸造过程中温度场的分布情况,铸件表面和内部的固相发展、应力态、收缩和裂缝分布、铸件质量等。
通过数值模拟技术,生产厂商可以对这些问题进行系统的研究并改进生产工艺,以提高金属铸造的质量和效率。
除了热仿真模块以外,金属铸造成形过程中的还需要进行液态流体力学模块的建模。
这个模块可以模拟固液相态变化以及流体动力学等过程。
在这个模块中,铸造中的流体力学问题涉及到:流动场、流体力学性质、子集模型的分析等等。
机械制造基础-铸造过程仿真技术PPT课件
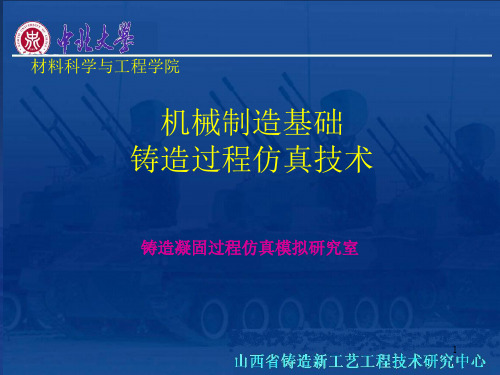
铸造模拟软件简介
铸造模拟软件可以对铸件形成过程中流场、温度场进 行模拟,并且能够对铸造过程中产生的缺陷(如浇不足, 冷隔,缩孔缩松缺陷)进行预测,从而对铸造过程所涉及 的工艺参数工艺方案等做出评价和优化,达到降低铸造废 品率,节省材料和劳动力,最大可能在降低成本,以及大 幅度在缩短铸造工艺定型周期。
材料科学与工程学院
机械制造基础 铸造过程仿真技术
铸造凝固过程仿真模拟研究室
1
内容介绍
(1)铸造工艺设计; (2)铸造模拟软件简介; (3)铸造CAD/CAE集成; (4)铸造模拟技术发展趋势; (5)实例应用; (6)凝固微观组织模拟研究
2
铸造模拟技术发展趋势
(1)由宏观模拟向微观模拟发展 可以预测组织、结构、性能,从而调整生产工艺,生产出理
6
软件组成及功能
3.软件产品系列
· 砂型重力铸造CAE · 砂型低压铸造CAE · 金属型重力铸造CAE · 金属型低压铸造CAE · 熔模精密铸造CAE · 压力铸造CAE .差压铸造CAE .消失模铸造CAE
7
软件组成及功能
铸造模拟软件
前处理
模拟计算
后处理
模型 建立
网格剖分 充型模拟 凝固模拟 应力模拟
想的凝固组织,达到优良的综合力学性能。 (2)单一分散向耦合集成方向发展
流场、温度场、应力/应变场、组织场等之间的耦合,以真实 模拟复杂的实际热加工过程。 (3)共性、通用向专用、特性方向发展
**解决特种热加工工艺模拟及工艺优化问题: 压铸、低压铸造、金属型铸造、实型铸造、连续铸造等特种铸造。
**解决铸件的缺陷消除问题
10
二铸造工艺方法的选择
• 综合分析该铸件,选择用砂型铸造,由于该铸 件为大型铸件,结构复杂。外型采用Z2520II 型造型机,一箱一件,水玻璃砂;手工制芯, 一箱一件 过桥浇注。
铸造成形工艺过程的数值模拟仿真及其应用

铸造成形工艺过程的数值模拟仿真及其应用王华侨;张颖;费久灿;王德跃【摘要】本文对国内外常用的几款铸造成形工艺模拟仿真软件的功能进行了简要介绍,希望对从事铸造行业的产品设计师、模具设计师、铸造工艺师提供一定的参考借鉴作用,从而为提高企业的铸造工艺水平搭建一个更好的优化设计,以及成形工艺的数字化工艺优化设计、制造、仿真集成的先进平台.【期刊名称】《金属加工:热加工》【年(卷),期】2011(000)005【总页数】6页(P59-64)【作者】王华侨;张颖;费久灿;王德跃【作者单位】中国三江航天集团国营红阳机械厂,湖北孝感,432100;中国三江航天集团国营红阳机械厂,湖北孝感,432100;中国三江航天集团国营红阳机械厂,湖北孝感,432100;中国三江航天集团国营红阳机械厂,湖北孝感,432100【正文语种】中文铸造仿真模拟优化软件是为评价和优化铸造产品与铸造工艺而开发的,借助于铸造仿真模拟优化软件系统平台,铸造工程师在完成铸造工艺编制之前,就能够对铸件在形成过程中的流场、温度场和应力场进行仿真分析并预测铸件的质量、优化铸造设备参数和工艺方案。
通过模拟金属铸造过程中的流动过程,精确显示充填不足、冷隔、裹气和热节的位置,以及残余应力与变形,准确地预测缩孔、缩松和铸造过程中微观组织的变化。
图1所示为铸造仿真模拟分析的典型过程。
本文对国内外常用的几款铸造成形工艺模拟仿真软件华铸CAE/InteCAST、AnyCasting、ProCAST等软件的功能与实例应用进行了简要介绍,希望对铸造行业的产品设计师、模具设计师、铸造工艺师提供一定的参考借鉴作用,从而为提高企业的铸造工艺水平搭建一个更好的优化设计,以及成形工艺的数字化工艺优化设计、制造、仿真集成的先进平台。
HZCAE/InteCAST是中国铸造领域著名的模拟分析系统,是分析和优化铸件铸造工艺的重要工具。
它以铸件充型过程、凝固过程数值模拟技术为核心对铸件进行铸造工艺分析。
某型机械加工过程的模拟与仿真

某型机械加工过程的模拟与仿真机械加工是现代工业制造中不可或缺的环节之一,通过模拟与仿真可以有效提高机械加工的效率和精确度。
本文将以某型机械加工过程的模拟与仿真为主题,探讨其在实际应用中的意义和技术。
一、机械加工过程的模拟与仿真是什么?机械加工过程的模拟与仿真是利用计算机技术对机械加工过程进行虚拟重建和仿真模拟。
通过对加工物体、切削工具、切削参数等进行建模,并运用计算机算法模拟切削力、切削振动、表面质量等加工过程中的关键参数,从而实现对加工过程的准确预测和优化。
二、机械加工过程的模拟与仿真的意义1. 提高加工效率:传统的机械加工方式往往需要经历多次试验和调整才能达到理想的加工结果。
而通过模拟与仿真,可以在计算机上快速预测不同加工参数下的加工结果,避免了大量试验和调整的时间和成本,大大提高了加工效率。
2. 优化加工工艺:模拟与仿真技术可以对加工工艺进行全面的分析和优化。
通过对切削力、切削温度、振动等关键参数进行仿真分析,可以找出加工过程中的瓶颈和薄弱环节,针对性地进行改进和优化,提高加工质量和加工速度。
3. 节约资源:传统的加工方式往往需要大量的物料和能源。
而通过模拟与仿真,可以在计算机上进行无风险的试验,避免了实际加工过程中的资源浪费。
同时,模拟与仿真还可以通过优化工艺参数,降低切削力和切削振动,从而减少能源消耗和刀具磨损,进一步节约资源。
三、机械加工过程的模拟与仿真技术1. 加工物体建模:在机械加工过程的模拟与仿真中,首先需要对加工物体进行三维建模。
可以使用计算机辅助设计软件,如SolidWorks或AutoCAD等,将加工物体准确地绘制出来。
这些模型还可以进一步导入到仿真软件中进行后续模拟。
2. 切削工具建模:在模拟与仿真中,还需要对切削工具进行建模。
根据实际工艺要求和切削工具的几何参数,可以使用计算机辅助设计软件,如CATIA或Pro/ENGINEER等,对切削工具进行三维建模,并导入到仿真软件中进行仿真分析。
铸造成形工艺模拟和工艺CAD

铸造成形工艺模拟和工艺CAD概述铸造成形过程是一个涉及熔融金属流体力学、弹塑性力学、物理化学、结晶学、传热学及凝固学等多门理论的复杂过程。
大部分铸造缺陷产生于充型及凝固过程或与之密切相关。
铸造工艺过程模拟技术将具备理论描述而难以用手工计算的工艺过程,采用现代高速发展的计算机应用技术,通过计算机屏幕展现在我们面前。
铸造工艺过程发生在高温下,过程开放性差,具有不可视性和工艺过程测试上的困难,因而对在工艺过程中金属液的流动及凝固过程缺乏直观了解,对出现的缺陷缺少科学解释和定量描述。
随着计算机软硬件技术的飞速发展,给铸造工艺过程模拟技术带来了新的生机,为其发展提供了技术保障,尤其是彩色图形终端功能的提高,为模拟结果带来了视觉上的新感受。
该项技术的主要内容有:铸件凝固补缩过程数值模拟;铸件热应力及残余应力的数值模拟;铸件充型过程的数值模拟;铸件微观组织生长过程中的数值模拟等。
这些研究内容既有区别,但相互之间也有一定的联系,这些内容中,铸件凝固过程温度场数值模拟是基础。
铸件微观组织预测铸件微观组织决定铸件的力学性能。
凝固理论的发展与完善,使人们从理论上掌握了铸件凝固过程中微观组织形成的机理,但真正开展微观组织形成过程计算机数值模拟研究工作,还是在计算机应用技术得到普及与发展以后,80年代末期,在铸件凝固过程宏观温度场的数值模拟技术的基础上,铸件微观组织形成过程数值模拟研究进人高潮,引起了许多国家研究人员的关注[72~75]。
微观组织模拟的目的是通过模拟来预测组织,进而优化工艺,控制微观组织的形成,获得品质优良的铸件。
目前,铸件微观组织计算机模拟预测已成为铸造工艺过程计算机模拟技术研究领域中最前沿的研究内容。
由于其研究技术起点高,内容新,理论深,难度大,能够代表这一研究领域的最高水平,而引起各国从事铸造过程模拟研究的专家和学者的极大关注和兴趣,采用多种方法进行研究,以下简述几种有代表性的方法。
1.固相份数法固相份数法从宏观温度场人手,以凝固过程固相份数为媒介,与微观形核生长过程联系起来,半定量地估算出铸件不同部位的凝固组织,如晶粒数、晶粒分布、晶粒尺寸、及二次臂距等。
- 1、下载文档前请自行甄别文档内容的完整性,平台不提供额外的编辑、内容补充、找答案等附加服务。
- 2、"仅部分预览"的文档,不可在线预览部分如存在完整性等问题,可反馈申请退款(可完整预览的文档不适用该条件!)。
- 3、如文档侵犯您的权益,请联系客服反馈,我们会尽快为您处理(人工客服工作时间:9:00-18:30)。
3、铸件的尺寸公差:规定该侧架铸件一般公差 按HB6103-1986 CT7。
4、机械加工余量 :据《铸造工艺设计》表1-13 知砂型铸造机械造型铸钢件等级为E~H,这 里取H为+7mm。
五砂芯设计
• 根据铸件结构知,需要模样一套,芯盒18个,具 体如工艺图上所示,其中下芯顺序为17、18-1612-7、8-9、11-10、12-15-2、3-4、5-14-6、 13
• 1#芯与16#芯不留芯头间隙,其余砂芯上箱芯头 间隙1mm,下箱芯头间隙0.5mm;砂芯分段部 位做成直面,芯盒做稍板。
• 下面的下芯芯座周边做出R3mm集砂槽;16#减 轻如图,7#(8#)芯做减轻,吃砂量大于 50mm。
六浇注系统ቤተ መጻሕፍቲ ባይዱ计
由于该铸件的材料为B级钢,采用转包式 浇注系统,大铸件,从铸件外导框端头引入钢 液,采用过桥浇注,一箱一件。
二铸造工艺方法的选择
• 综合分析该铸件,选择用砂型铸造,由于该铸 件为大型铸件,结构复杂。外型采用Z2520II 型造型机,一箱一件,水玻璃砂;手工制芯, 一箱一件 过桥浇注。
三分型面选择
分型面在侧架纵向中心平面;为保证侧架滑槽的 尺寸精度,将其设置在下型,铸号面位于上型。
四工艺参数的确定
1、铸件最小铸出壁厚:砂型铸造最小铸出壁厚 为6~8mm,所以该铸件可以采用砂型铸造。
数据库
缺陷预测
一铸件的材质和结构
• 铸件的三维图
一铸件的材质和结构
• 该铸件为火车轴的侧架,铸件的材质为 B级钢, (即C25钢)该铸件属于箱式结构,复杂薄壁 铸件,轮廓尺寸为 2235mm×565mm×420mm,质量为 314KG,体积为4.0×107mm3 。内腔连接筋 较多,平均壁厚25mm,最大厚度为31mm。 中央导框框磨耗板面不加工,外导框间距、滑 槽中心多个圆孔等配合面尺寸要求高 。
材料科学与工程学院
机械制造基础 铸造过程仿真技术
铸造凝固过程仿真模拟研究室
内容介绍
(1)铸造工艺设计; (2)铸造模拟软件简介; (3)铸造CAD/CAE集成; (4)铸造模拟技术发展趋势; (5)实例应用; (6)凝固微观组织模拟研究
铸造模拟技术发展趋势
(1)由宏观模拟向微观模拟发展 可以预测组织、结构、性能,从而调整生产工艺,生产出理想的
软件组成及功能
3.软件产品系列
· 砂型重力铸造CAE · 砂型低压铸造CAE · 金属型重力铸造CAE · 金属型低压铸造CAE · 熔模精密铸造CAE · 压力铸造CAE .差压铸造CAE .消失模铸造CAE
软件组成及功能
铸造模拟软件
前处理
模拟计算
后处理
模型 建立
网格剖分 充型模拟 凝固模拟 应力模拟
软件组成及功能
1.系统功能特点: (1)软件适合于多材质(铸钢、铸铁、铸造有色合金等),
多种铸造方法(普通砂铸、金属型铸造、精密铸造、 低压铸造、压力铸造、消失模铸造等)。 (2)系统具有开放的数据库体系,包括200多种铸造材料 参数并且用户根据需要可以自行添加材料数据库。 (3)系统软件中文界面友好、操作方便。 2.系统运行环境 硬件(推荐配置):PIV 2.8CPU;内存≥512M,硬盘 ≥40G。 软件:Win2000、WinNT、Window XP等操作系统
数为14 mm。M41 # > M保,因此可以选用。
3、铸件工艺出品率的校核
八冷铁的设计
分析铸件整体结构,通过view cast模拟结果 :铸 件需要在侧壁安放方形冷铁,冷铁长、宽、高各尺 寸分别为30、30、30(单位mm), 在中央圆凸台上 其尺寸大小为直径为Ø40,高度为30mm 圆冷铁
铸造模拟软件简介
铸造模拟软件可以对铸件形成过程中流场、温度场进行模 拟,并且能够对铸造过程中产生的缺陷(如浇不足,冷隔, 缩孔缩松缺陷)进行预测,从而对铸造过程所涉及的工艺 参数工艺方案等做出评价和优化,达到降低铸造废品率, 节省材料和劳动力,最大可能在降低成本,以及大幅度在 缩短铸造工艺定型周期。
1、确定包内直径:采用10t漏包,Ø45mm包孔 浇注铸件
2、浇注时间:t=Q/q=447/42=10.6s,浇注过 程中,应遵循缓流→全速→缓收流的浇注原则, 且由于改侧架壁厚偏厚,因此点浇冒口3次。
3、按包孔断面确定浇注系统各断面
采用过桥水口两个内浇道由分型面引入,根据ΣF 孔∶ΣF直∶ΣF横∶ΣF内=1:(1.8~2):(1.8~2):2 确定直浇道、横浇道、内浇道的断面尺寸为:直浇 道为圆形断面2个Ø45×2mm:横浇道为梯形断面2 个(50.60)×50mm:内浇道为梯形断面2个(50.60) ×50mm。
凝固组织,达到优良的综合力学性能。 (2)单一分散向耦合集成方向发展
流场、温度场、应力/应变场、组织场等之间的耦合,以真实模 拟复杂的实际热加工过程。 (3)共性、通用向专用、特性方向发展
**解决特种热加工工艺模拟及工艺优化问题: 压铸、低压铸造、金属型铸造、实型铸造、连续铸造等特种铸造。
**解决铸件的缺陷消除问题
铸造模拟技术发展趋势
(4)重视提高数值模拟精度和速度的基础性研究 重视在热加工基础理论、新的数理模型、新的算法、
前后处理、精确的基础数据获得与积累等基础性研究 (5)重视物理模拟及精确测试技术 (6)在并行环境下,工艺模拟与生产系统其它技术环节
实现集成,成为先进制造系统的重要组成部分 **产品、模具CAD/CAE/CAM/RPM系统集成 **与PDM(Product Data Management)系统集成
直浇道截面示意图
内浇道截面图
• 外浇道与内浇道尺寸一致 • 3.6.4确定各道长度:直浇道高度为420mm,横
浇道长度为170mm,内浇道长度为20mm。
七冒口设计
1.上侧冒口设计: 运用模数法 1)铸件模数: 外侧导框结构如图所示, 热节圆直径Ø=34 mm ,则其模数M件=Ø/2 = 17 mm。 2)冒口模数:保温冒口的模数 M保= 0. 8 M件= 0. 8×17 = 13. 6 mm。 3) 选择冒口:2 # 保温冒口套的尺寸如图 所示,其模