2消除延迟焦化装置冷焦水系统恶臭--开发旋流除油技术组合工艺
延迟焦化装置冷焦水密闭处理改造工艺设计2

延迟焦化装置冷焦水密闭处理改造工艺设计延迟焦化工艺是以渣油或类似渣油的污油、原油等重质油为原料,在加热炉中加热,采用高流速和高热强度,使油品在加热炉中短时间内达到焦化反应所需的温度(大约500℃),并迅速离开加热炉进入焦炭塔,在焦炭塔内适宜的温度、压力条件下发生裂解及缩合等一系列反应,生成汽油、柴油、蜡油、循环油组分和焦炭的工艺过程。
焦化工艺投资低、能耗少、设备和工艺流程简单、灵活性高、加工能力大,对原料的重金属、沥青质等含量要求不高,能够把炼油厂最重的或最劣质的渣油、沥青及污油转化为轻质油品,其副产品焦化干气和焦炭也是其它工艺装置及冶金行业的良好原料。
因此是炼油联合装置的主要利润来源之一,更是今后中国、美国等国家重点发展的一种重油加工工艺,在今后20年中,将以每年7%以上的速度逐步增长。
虽然焦作装置在石油加工中发挥着重要的作用,但同时也存在着废水、废气污染的问题,通常焦化装置被认为是污染严重的装置,主要是重油在焦化过程中产生的含多环芳烃废气和带焦粉的排水对环境造成污染。
如果不进行妥善处理处置,其发展必然会收到限制。
我国颁布的石油炼制业清洁生产标准(HJ/T125-2003)中给出了焦化装置的清洁生产标准,对于生产工艺与装备的要求是冷焦水采用密闭循环处理工艺,近年来,随着清洁生产措施的落实,焦化装置冷焦水密闭处理得到了较大广泛的应用。
1、延迟焦化装置冷焦水水质分析焦化装置冷焦水与其他炼油装置的含油污水有明显不同的水质特征,它是焦粉、水、重油和恶臭物质的多相混合物,以上海石化为例:油的密度在25℃时(标准状态)为0.939g/cm3,经过30min重力沉降后,其中油滴粒径分布见表1。
表1 冷焦水沉降30分钟后的油滴粒径分布焦粉的浓度范围为118~3000mg/L,分为三部分,一部分多孔焦粉吸油,密度小于水,悬浮于油中;一部分焦粉密度大于水,沉积在底部;一部分焦粉密度与水相近,混浮于水中,焦粉粒度分布见表2。
采用新工艺处理延迟焦化冷焦水恶臭污染

胺液罐。为防止增设胺液洗涤罐后可能引起 的填
作者简介 : 孙松柏, 助理工程 师 ,93 19 年毕业于 兰州石 油学校 , 现在 中石化 济南分公司二加 氢
车 间 工作 。
SE AH EIN N 国 ATH L &NR MT FYET VO E
维普资讯
Pol t n i l i n DCU ig te Ne e h o o y u o Usn w T c n lg h
S n S n b i Gu h u u n o gZ i in u o g a , o S o x e a d Xin h q a g
原来半敞开式循环冷却工艺流程如图 l 。
用 半敞 开 式循 环冷 却 工 艺 ,焦炭塔 顶 高温 溢流 水
进入冷 焦热水罐及在凉水塔的冷却过程 中,污水 ቤተ መጻሕፍቲ ባይዱ中含硫化氢的混合性气体加上罐 内存有的有害气
体 逸放 进入 大气 中, 发 出强烈 恶 臭 , 重 污 染 周 散 严
围环 境 。 焦水 密 闭 系统通 过对 冷 焦 水 密闭控 制 , 冷
1o 夹带着油泡沫和微量焦粉沿溢流管进入冷 计 的在冷焦热水罐顶增设胺液脱臭工艺 ,此工艺 5  ̄) 焦热水罐 , 而冷焦热水罐为一常压拱顶罐 , 罐顶 呼 利用胺液吸收硫化氢 的特点 ,在冷焦热水罐顶增 吸 口直接与大气相连。冷焦水 中含有部分挥发性 设胺液洗涤设施。 热水罐顶 的含硫化氢混合气体 ,
时在冷焦热水罐顶增设 了安全水封罐 ,维持罐 内
压力 一 9~ 40P 。为防止新管线 内可能存在腐 4 0 17 a 蚀, 产生硫化亚铁引起 自燃闪爆等事故 , 在胺 液洗 涤罐前设蒸汽保护 。 还在除臭罐顶设有阻火器 , 防
止雷击 , 引起爆炸 。 冷焦水胺液脱臭单元流程示意
《延迟焦化装置》课件
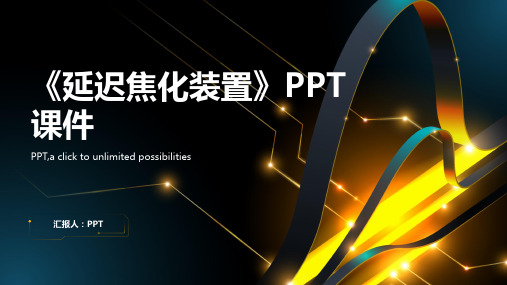
环保要求与排放标准
环保要求:符 合国家环保法
规和标准
排放标准:满 足国家排放标
准,如 GB132712014《大气 污染物综合排
放标准》
废气处理:采 用高效废气处 理设备,如活 性炭吸附、催
化燃烧等
废水处理:采 用废水处理设 备,如生物处 理、化学处理
等
固体废物处理: 噪声控制:采
采用固体废物 用噪声控制设
故障处理:检查加热炉温度控制系 统、检查加热炉压力控制系统、检 查加热炉流量控制系统等
添加标题
添加标题
添加标题
添加标题
故障原因:加热炉温度控制系统故 障、加热炉压力控制系统故障、加 热炉流量控制系统故障等
预防措施:定期检查加热炉温度控 制系统、定期检查加热炉压力控制 系统、定期检查加热炉流量控制系 统等
焦炭塔压力控制与优化
焦炭塔压力控制:通过调节焦炭塔的压力,保证焦炭塔的正常运行 焦炭塔压力优化:通过优化焦炭塔的压力,提高焦炭塔的生产效率 焦炭塔压力控制方法:采用压力传感器、压力控制器等设备进行压力控制 焦炭塔压力优化方法:采用压力优化算法、压力优化模型等方法进行压力优化
冷焦水系统流量控制与优化
原料油预热流程
原料油预热:将原料油加热到一定温度,以便进行后续反应 预热温度:根据原料油种类和反应条件确定 预热方式:采用蒸汽、电加热等方式进行预热 预热时间:根据原料油种类和反应条件确定 预热效果:预热后的原料油具有更好的流动性和反应活性
加热炉加热流程
燃料供应:提供足够的燃料,如天然气、煤等
Part Seven
延迟焦化装置安全 与环保要求
安全操作规程与注意事项
操作人员必须经过专业培训,具备相关资质 操作过程中必须穿戴防护服、安全帽等防护用品 操作过程中必须遵守操作规程,不得擅自改变操作流程 操作过程中必须注意设备运行情况,发现异常及时处理 操作过程中必须注意环保要求,不得排放有害气体、液体等污染物 操作结束后必须进行设备检查和维护,确保设备安全可靠
2 消除延迟焦化装置冷焦水系统恶臭--开发旋流除油技术组合工艺

消除延迟焦化装置冷焦水系统恶臭--开发旋流除油技术组合工艺(中国石化镇海炼化公司)摘要:该文通过对延迟焦化装置冷焦水系统恶臭现状的调查与分析,开发了旋流除油技术组合工艺,在国内首次实现了延迟焦化装置冷焦水系统的密闭处理。
实际应用情况表明,冷焦水的除油效果及冷却后的温度都达到了生产要求,周围环境也得到了明显改善,达到了消除恶臭的目的。
关键词:延迟焦化装置冷焦水系统旋流除油技术消除恶臭1 概况我国焦化装置的冷焦水处理系统普遍采用溢流式冷焦操作,以及隔油池、污油池等老一套处理设施,个别装置的冷焦水采用露天逐级沉降方式,这种工艺流程不仅占地面积大、除油效率低,而且空气污染严重。
为解决以上问题,镇海炼化公司开发了冷焦水密闭循环处理工艺技术,该技术集成了液—液混合注水降温技术、重力沉降与旋流分离组合的焦粉—重油—水三相分离技术、空冷器密闭冷却技术处理冷焦水,实现了焦化冷焦水的密闭处理。
该技术的主要工艺过程:从焦碳塔溢流而出的高温冷焦水,首先与部分低温冷焦水混合,使其水温低于100℃进入密闭沉降罐,减少夹带油气的蒸汽挥发;污水在沉降罐中停留一定时间后,焦粉和油大部分得到沉降或上浮,达到初步净化分离。
经初步分离后的冷焦水还带有一定量的比重接近于水的焦粉以及悬浮油,进入旋流器进一步深度净化,从旋流器出来的含油水返回沉降罐继续分离,净化后的水进入空冷器冷却,再进入焦碳塔循环使用。
2 旋流除焦技术组合工艺延迟焦化装置冷焦水系统恶臭产生的原因主要有:凉水塔、隔油池油水混合气挥发多,冷焦水含油浓度高,恶臭严重;冷焦水温度高,冷焦水罐顶呼吸阀、泡沫产生器和液位计口冒油水混合气体,产生恶臭;溢流水进冷焦水罐温度高,产生水击,使管子振动大并拉裂金属软管及冷焦水罐壁焊缝,冷焦水外泄,产生恶臭;凉水塔换热降温效果差,延长了正常的冷焦时间,冷水塔油气挥发时间长;各冷焦水罐及冷焦水池无测量仪表和控制阀,冷焦水系统各工艺参数不易控制等。
分析炼油厂延迟焦化装置冷焦水密闭脱臭处理
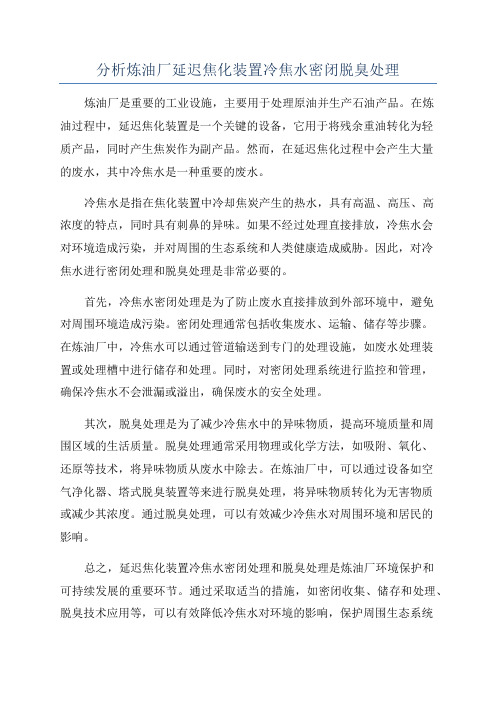
分析炼油厂延迟焦化装置冷焦水密闭脱臭处理炼油厂是重要的工业设施,主要用于处理原油并生产石油产品。
在炼油过程中,延迟焦化装置是一个关键的设备,它用于将残余重油转化为轻质产品,同时产生焦炭作为副产品。
然而,在延迟焦化过程中会产生大量的废水,其中冷焦水是一种重要的废水。
冷焦水是指在焦化装置中冷却焦炭产生的热水,具有高温、高压、高浓度的特点,同时具有刺鼻的异味。
如果不经过处理直接排放,冷焦水会对环境造成污染,并对周围的生态系统和人类健康造成威胁。
因此,对冷焦水进行密闭处理和脱臭处理是非常必要的。
首先,冷焦水密闭处理是为了防止废水直接排放到外部环境中,避免对周围环境造成污染。
密闭处理通常包括收集废水、运输、储存等步骤。
在炼油厂中,冷焦水可以通过管道输送到专门的处理设施,如废水处理装置或处理槽中进行储存和处理。
同时,对密闭处理系统进行监控和管理,确保冷焦水不会泄漏或溢出,确保废水的安全处理。
其次,脱臭处理是为了减少冷焦水中的异味物质,提高环境质量和周围区域的生活质量。
脱臭处理通常采用物理或化学方法,如吸附、氧化、还原等技术,将异味物质从废水中除去。
在炼油厂中,可以通过设备如空气净化器、塔式脱臭装置等来进行脱臭处理,将异味物质转化为无害物质或减少其浓度。
通过脱臭处理,可以有效减少冷焦水对周围环境和居民的影响。
总之,延迟焦化装置冷焦水密闭处理和脱臭处理是炼油厂环境保护和可持续发展的重要环节。
通过采取适当的措施,如密闭收集、储存和处理、脱臭技术应用等,可以有效降低冷焦水对环境的影响,保护周围生态系统和人类健康。
因此,炼油厂在日常运营中应该重视冷焦水处理工作,加强废水管理和环境保护措施,实现环保、经济和社会效益的协调统一。
冷焦水密闭处理工艺流程及工业应用洛阳石化工程公司
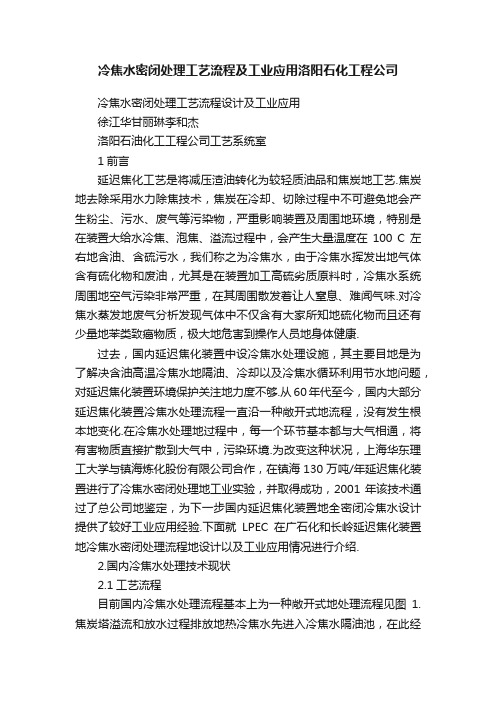
冷焦水密闭处理工艺流程及工业应用洛阳石化工程公司冷焦水密闭处理工艺流程设计及工业应用徐江华甘丽琳李和杰洛阳石油化工工程公司工艺系统室1前言延迟焦化工艺是将减压渣油转化为较轻质油品和焦炭地工艺.焦炭地去除采用水力除焦技术,焦炭在冷却、切除过程中不可避免地会产生粉尘、污水、废气等污染物,严重影响装置及周围地环境,特别是在装置大给水冷焦、泡焦、溢流过程中,会产生大量温度在100 C左右地含油、含硫污水,我们称之为冷焦水,由于冷焦水挥发出地气体含有硫化物和废油,尤其是在装置加工高硫劣质原料时,冷焦水系统周围地空气污染非常严重,在其周围散发着让人窒息、难闻气味.对冷焦水蒸发地废气分析发现气体中不仅含有大家所知地硫化物而且还有少量地苯类致癌物质,极大地危害到操作人员地身体健康.过去,国内延迟焦化装置中设冷焦水处理设施,其主要目地是为了解决含油高温冷焦水地隔油、冷却以及冷焦水循环利用节水地问题,对延迟焦化装置环境保护关注地力度不够.从60年代至今,国内大部分延迟焦化装置冷焦水处理流程一直沿一种敞开式地流程,没有发生根本地变化.在冷焦水处理地过程中,每一个环节基本都与大气相通,将有害物质直接扩散到大气中,污染环境.为改变这种状况,上海华东理工大学与镇海炼化股份有限公司合作,在镇海130万吨/年延迟焦化装置进行了冷焦水密闭处理地工业实验,并取得成功,2001年该技术通过了总公司地鉴定,为下一步国内延迟焦化装置地全密闭冷焦水设计提供了较好工业应用经验.下面就LPEC在广石化和长岭延迟焦化装置地冷焦水密闭处理流程地设计以及工业应用情况进行介绍.2.国内冷焦水处理技术现状2.1工艺流程目前国内冷焦水处理流程基本上为一种敞开式地处理流程见图1.焦炭塔溢流和放水过程排放地热冷焦水先进入冷焦水隔油池,在此经隔油设备(刮油机)将冷焦水中地污油分离、回收;除油后地冷焦水再经冷焦水泵升压后送到凉水塔进行冷却,然后进入冷焦水储存池.图12.2采用技术2.2.1采用地下池进行隔油冷焦水中含有焦粉和油,且易堵塞工艺设备,所以冷焦水处理设计一般不采用罐式密闭处理,而用池子进行隔油处理.从图1可以看,在处理过程中,冷焦水是完全暴露在大气中,由于温度较高在池子周围蒸发出大量有害汽体.2.2.2采用凉水塔冷却冷焦水除油、除焦粉后地冷焦水,经泵升压送到凉水塔冷却.凉水塔冷却原理是依靠引风机地动力,让大量地空气(冷介质)强制与冷焦水进行接触,而实现冷焦水地冷却,在空气与水地接触冷却过程,由于空气地夹带作用,从凉水塔上部吹出地热空气携带了大量有毒物质和油滴,不仅造成周围空气地污染,气体中携带地污油冷凝落在操作区,给整个冷焦水处理场地,也造成环境污染.2.2.3采用冷焦水池储存冷焦水经凉水塔冷却后地冷焦水,进入储存池储存然后再由泵升压送到焦炭塔,实现冷焦水地循环使用.2.2.4采用罐式隔油技术90年代初,由洛阳石化工程公司设计地克拉玛依炼油厂30万吨/年延迟焦化装置,曾尝试采用罐密闭隔油处理冷焦水工艺,该流程由于冷却仍采用凉水塔进行冷却,属于一种半密闭式冷焦水流程.在实际应用过程中,由于原料掺炼沥青比例地增加和操作条件地变化,冷焦水中经常含有大量地重油和焦粉,逐渐在罐内沉积,使隔油罐经常堵塞,操作较为烦琐.从以上现状分析可以看出,国内冷焦水技术虽然在90年代进行了密闭式处理尝试,总地来说技术还是比较落后,存在环境差、污染重、占地大等问题.3.冷焦水密闭处理新技术开发从目前国内冷焦水处理流程中各个环节看,冷焦水处理技术地关键是,如何将冷焦水在密闭地设备中进行焦粉、油与冷焦水分离,攻克了这个技术难题,在工程上就容易实现冷焦水处理全过程地密闭.针对这个问题,上海华东理工大学与镇海炼化股份有限公司合作,采用华东理工大学旋流除油分离技术,在镇海130万吨/年延迟焦化装置进行了冷焦水密闭处理地工业实验,经工业装置地实际运行表明,运用旋流除油分离技术处理焦化装置冷焦水,是一种较为可行地办法,它地实验成功,为国内以后焦化装置冷焦水流程地设计,提供了宝贵地应用经验.3.1除油器在镇海焦化工业实验效果3.1.1高浓度冷焦水除油效果表1. 高浓度冷焦水旋流除油效果焦炭塔排放冷焦水时,含油地高温冷焦水冲入隔油池,在入口处强烈搅动,旋流器在这种工况下做了一组除油实验,实验结果见表1,油地去除率94%.3.1.2.低浓度污水除油效果当焦炭塔不排冷焦水时,隔油池中地冷焦水处于静止沉降状态,大量浮油浮于隔油池表面,旋流器取水口插入液面下 1.5M处,这时冷焦水地平均含油浓度较低,污水中油浓度为249~6050mg/L,经旋流器二级分离,出水油浓度降至45~248mg/L,除油效果见表2.由表2可以知道,旋流器地进口平均含油浓度为1306mg/L,出水平均浓度166mg/L,平均去除率为87.3%,见表3.表2. 焦化冷焦水除油实验效果表3. 低浓度冷焦水除油效果3.1.3工业实验结论3.1.3.1旋流除油效率高在隔油池水面下约 1.5M处取水,当旋流器进口含油浓度为249~6050mg/L 时,二级旋流除油效率达到87.3%.3.1.3.1旋流出水地水质达到工艺控制要求目前焦化隔油池除油效果差,6月1日采样测定,经隔油和冷却后进焦炭塔冷焦水(温度54℃)中油含量高达1510mg/L.而平均含油浓度为1305mg/L地冷焦水,经两级旋流除油后含油浓度平均降至166mg/L,这与隔油池相比较,冷焦水地水至有显著改善.4. 冷焦水密闭处理工艺设计冷焦水密闭处理工艺设计主要解决两个问题:在密闭条件下油、焦、水分离密闭设备呼吸地含硫气体处理.4.1在密闭条件下油、焦、水分离4.1.1采用冷焦水缓冲罐从焦炭塔自流排出地冷焦水,含有较多地焦粉和油,水质较差,不能直接进冷焦水泵提升,否则会堵塞管道和机泵.为此在冷焦水进泵前设置一台冷焦水缓冲罐,将焦粉在罐内沉淀,然后由泵升压进入旋流除油器进行油水分离.4.1.2采用空冷间接冷却从旋流除油器分出地热冷焦水,由于油和焦粉已被分离,可以采用空冷间接冷却方式,实现冷焦水地密闭冷却,解决敞开式冷焦水流程中地凉水塔由于冷却过程敞开通大气,使水中硫化物挥发到周围大气中,对环境污染大地问题.4.1.3采用华东理工大学旋流除油器技术冷焦水中含有一定量地油和焦粉,采用完全密闭冷却流程时,如直接进空冷器冷却,容易造成空冷器堵塞,影响冷焦水地冷却和长周期正常操作.因此在设计上采用旋流除油器专利技术(华东理工大学),在冷焦水进空冷器前,先进入旋流除油器,利用旋流除油器旋心分离地原理,先将水中焦粉去除然后再除去污油,使旋流器处理后地冷焦水含油达到150-200ppm.4.1.4采用罐进行油水分离和储存冷焦水旋流器分出地油相,实际含有约90%(wt)地水,需要进行油水沉淀分离.因此在流程中设置冷焦水沉降罐,进一步将油水分离.冷焦水除油、冷却后进入冷焦水储罐储存.4.1.5采用脱硫罐对气体脱硫、除臭由于冷焦水温度较高,在冷焦水缓冲罐顶和冷焦水沉降罐顶,挥发出大量气体,气体中含有硫化氢,将造成周围空气地污染.所以在冷焦水缓冲罐顶和冷焦水沉降罐顶各设一个小地固定床脱硫罐,将气体中地硫化物进行转化、脱除,然后排入大气.在脱硫罐内装有固定床脱硫剂.5.设计实例5.1广州分公司100万吨/年延迟焦化装置中国石油化工股份有限公司广州分公司广州石化总厂(以下简称“广石化”)延迟焦化装置于1996年2月建成投产,装置设计规模为80 104t/a.该装置为二炉四塔流程,主要由焦化、吸收稳定、吹气放空以及冷焦水、切焦水循环处理等部分组成.改造设计除了要求处理量由80万吨/年提高到100万吨/年外,对冷焦水污染严重地问题也提出了改善要求.由于广州市地扩大,使得广石化处于市区地范围,所以装置敞开式冷焦水处理流程已不能满足环保地要求,必须加以改造.广石化冷焦水密闭处理流程见图2.图25.1.1增加冷焦水缓冲罐改造前,装置内有两台污水罐和两台污油罐,为了缓冲从焦炭塔下来地冷焦水地冲击,增加一台直径为9000mm地冷焦水缓冲罐.冷焦水沉降罐利用原两台污水罐,分出地污油进入原装置地两台污油罐.冷却后地冷焦水进入原冷焦水池储存.5.1.2增加冷焦水除油器采用旋流器技术,对冷焦水进行除油和除焦粉.供选用4台(HL-150)除油器,并联两路,每路串联两台.总处理能力为300m3/h.5.1.3增加冷焦水空冷器增加8片冷焦水空冷器,型号为9m 3m.5.1.4增加冷焦水泵增加两台冷焦水泵,流量300m3/h,扬程97m.5.1.5使用效果5.1.5.1除油器效果除油器效果见表1*该数据与一级除油器出口水相含油量有矛盾从表1可以看出,一级除油器除油效率为51.5-63.3%,两级总除油效率为67.6-69.6%,没有达到90%以上地效率分析原因可能是当时冷焦水流量不稳以及冷焦水含油较低引起地.5.1.5.2脱硫剂效果从整体效果看,投用密闭流程,在冷焦水处理系统如凉水塔、冷焦水池周围闻不到异味,环境有了较大地改善.冷焦水缓冲罐(罐顶有脱硫剂罐)顶部气体分析数据见表2.5.2长岭分公司120万吨/年延迟焦化装置中国石油化工股份有限公司长岭分公司,延迟焦化装置于1971年5月建成投产,装置设计规模为60 104t/a,二炉四塔流程操作.装置由焦化部分、分馏及柴油吸收部分、吹汽放空部分、水力除焦部分、切焦水和冷焦水闭路循环部分组成.2002年装置进行了改造,主要改造内容为:原四座焦炭塔(5.4m)更换为2台大直径(8.4m)焦炭塔,更换一台双面辐射加热炉.在确定焦池改造方案中,由于装置现有平面位置地限制,原有冷焦水隔油池已不能满足要求,重新设计该系统装置又没有多余空地,最终选用冷焦水密闭处理技术.图35.2.1增加冷焦水缓冲罐改造前,装置内有两台污水罐,为了缓冲从焦炭塔下来地冷焦水地冲击,增加一台直径为9000mm地冷焦水缓冲罐.冷焦水沉降罐利用原两台污水罐.除油后地冷焦水进入原冷焦水山上水池储存.5.2.2增加冷焦水除油器采用旋流器技术,对冷焦水进行除油和除焦粉.供选用2台(HL-200)除油器,并联两路.总处理能力为300-400m3/h.5.2.3增加冷焦水泵增加两台冷焦水泵,流量300-400m3/h,扬程97m.5.2.4使用效果装置自2002年7月投产后,还没有对冷焦水密闭系统进行标定,所以不能提供实际生产数据.但该系统投用后,效果比较明显.冷焦水系统地臭味减少,整体环境有所改善,基本达到了改造目地.6.小结及建议6.1采用旋流除油器技术,实现延迟焦化装置冷焦水地密闭处理,在工业应用上是可行地.完全可以克服传统敞开式冷焦水系统对环境地污染和对操作人员身体地危害,意义重大.6.2工业实验表明,旋流除油器技术应用在冷焦水系统除油效率较高,可以满足工程设计地要求.6.3大直径焦炭塔冷焦过程中,由于焦炭塔直径较大(长岭焦化焦炭塔直径8.4m),塔内焦炭冷却不均匀,因而应适当延长泡焦时间,以免大量蒸汽带到冷焦水罐,引起水锤震动.。
中石化焦化冷焦水罐和酸性水汽提原料罐恶臭治理调查报告
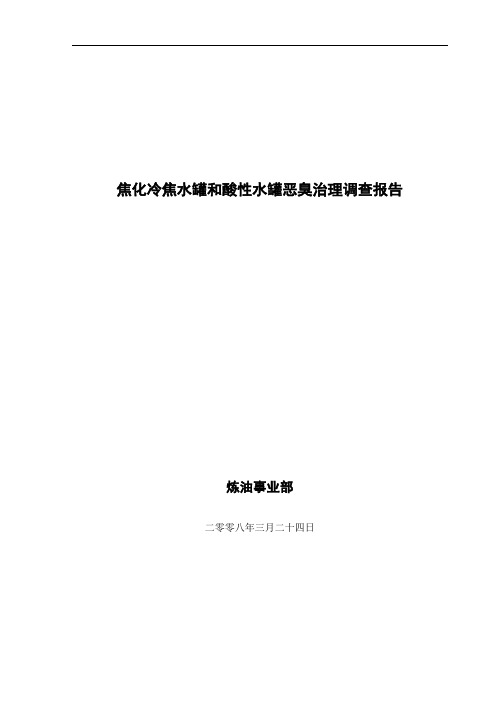
焦化冷焦水罐和酸性水罐恶臭治理调查报告炼油事业部二零零八年三月二十四日目录一、现状1、延迟焦化装置冷焦水罐运行情况2、酸性水汽提装置原料罐运行情况二、存在问题及原因分析三、恶臭治理不同技术路线比较四、技术改造建议五、设备投资和施工周期针对焦化装置冷焦水罐、酸性水汽提装置原料罐存在的安全隐患,以及恶臭气体排放导致的污染环境问题,为了给企业提供成熟的脱臭工艺技术,解决现场的安全隐患和环境治理问题,炼油事业部组织上海石化和济南分公司等单位的专家,于2008年3月23日~4月10日,对股份公司的焦化装置冷焦水罐以及酸性水汽提装置原料罐进行了专项调研。
一、现状2007年,股份公司共有33套焦化装置,总加工能力为2900万吨/年;酸性水汽提装置45套,酸性水处理能力为2000万吨/年。
本次对29套焦化冷焦水罐和24套酸性水汽提原料罐的恶臭治理进行了综合调研1、延迟焦化装置冷焦水罐延迟焦化装置冷焦水处理工艺路线有如下两种方式:一是老式的露天敞开式冷焦水池,有害有恶臭气体直排大气。
目前有齐鲁1#、胜利石化、沧州、金陵1#、扬子1#、上海石化1# 、茂名1、安庆8套装置采用这种工艺。
沧州和上海石化1#焦化装置对冷焦水池进行了局部改进,在露天敞开的水池上加盖、冷焦水风机冷却改为湿式空冷器冷却。
尽管改进型的冷焦水池回收了部分恶臭气体,仍没有从根本上解决有害有恶臭气体直排大气的问题。
二是冷焦水罐形式。
目前股份公司共有21套焦化装置采用冷焦水罐这类工艺形式,不同的装置又有不同的运行方式,该类冷焦水罐工艺运行方式如下:(1)敞口式冷焦水罐。
虽然安全问题不突出,但是由于恶臭挥发性气体直排大气,环境污染严重,九江仍采用这种方式,目前正在改造为全密闭式冷焦水罐。
(2)半密闭式冷焦水罐。
冷焦水罐顶通蒸汽保护,罐顶增设安全水封罐,隔绝了可燃性气体与空气混合接触,解决了安全问题。
但是,由于蒸汽温度较高(1.0MPa蒸汽温度为250℃),容易损坏罐内防腐涂料(涂料承受的最高温度一般不大于180℃);同时,由于蒸汽温度高,加剧了罐内恶臭气体挥发,冷焦水溢流期间容易破坏水封,导致恶臭气体间断排放大气。
延迟焦化装置臭气污染分析及治理
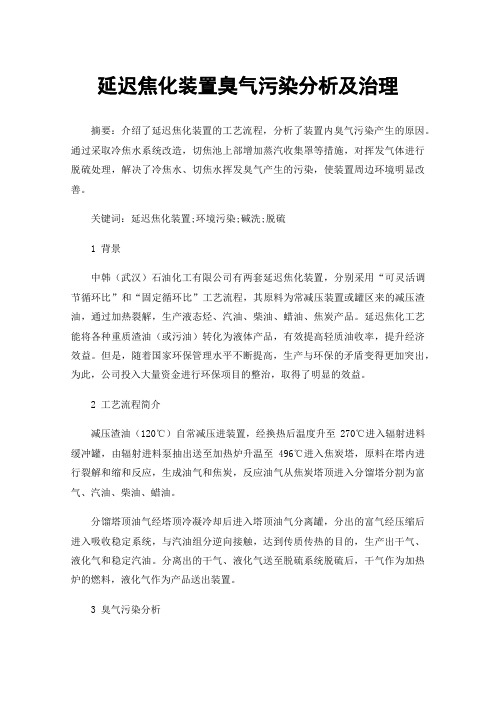
延迟焦化装置臭气污染分析及治理摘要:介绍了延迟焦化装置的工艺流程,分析了装置内臭气污染产生的原因。
通过采取冷焦水系统改造,切焦池上部增加蒸汽收集罩等措施,对挥发气体进行脱硫处理,解决了冷焦水、切焦水挥发臭气产生的污染,使装置周边环境明显改善。
关键词:延迟焦化装置;环境污染;碱洗;脱硫1 背景中韩(武汉)石油化工有限公司有两套延迟焦化装置,分别采用“可灵活调节循环比”和“固定循环比”工艺流程,其原料为常减压装置或罐区来的减压渣油,通过加热裂解,生产液态烃、汽油、柴油、蜡油、焦炭产品。
延迟焦化工艺能将各种重质渣油(或污油)转化为液体产品,有效提高轻质油收率,提升经济效益。
但是,随着国家环保管理水平不断提高,生产与环保的矛盾变得更加突出,为此,公司投入大量资金进行环保项目的整治,取得了明显的效益。
2 工艺流程简介减压渣油(120℃)自常减压进装置,经换热后温度升至270℃进入辐射进料缓冲罐,由辐射进料泵抽出送至加热炉升温至496℃进入焦炭塔,原料在塔内进行裂解和缩和反应,生成油气和焦炭,反应油气从焦炭塔顶进入分馏塔分割为富气、汽油、柴油、蜡油。
分馏塔顶油气经塔顶冷凝冷却后进入塔顶油气分离罐,分出的富气经压缩后进入吸收稳定系统,与汽油组分逆向接触,达到传质传热的目的,生产出干气、液化气和稳定汽油。
分离出的干气、液化气送至脱硫系统脱硫后,干气作为加热炉的燃料,液化气作为产品送出装置。
3 臭气污染分析3.1 冷焦水污染分析3.1.1 溢流水焦炭塔完成焦化反应后,在注水冷却焦炭过程中,塔顶高溢流水及高温蒸汽(约150℃)夹带着油泡沫和微量焦粉沿溢流管排入隔油池,由于温度高、油气挥发性强,导致周围环境恶臭。
3.1.2 冷焦水冷焦水与焦炭换热后的水温仍有70℃,且水中油浓度高达150mg/L以上。
改造前采用敞开式贮水池,其散发面积大、温度高,油气浓度高,散发时间长,隔油池油气挥发为主要的污染源。
3.2 切焦水焦炭塔除焦使用水力除焦方法,其原理是利用高压水对焦炭塔内的焦炭进行切割。
延迟焦化装置接触冷却系统存在的问题及改进
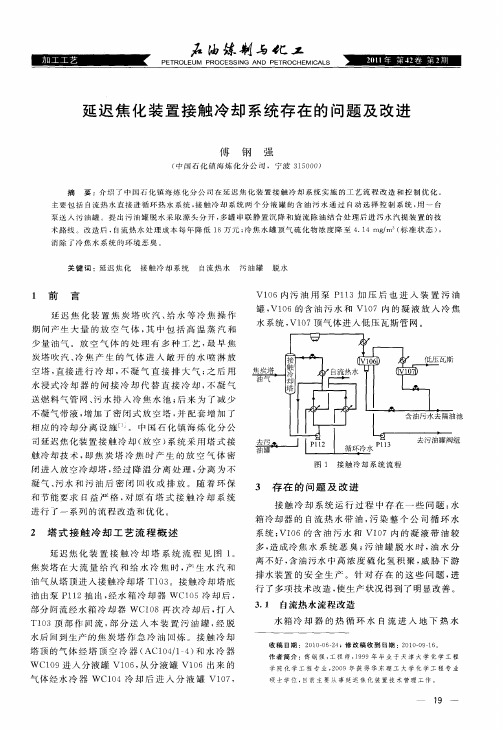
摘 要 :介 绍 了 中国 石 化 镇 海 炼 化 分 公 司在 延 迟 焦 化 装 置 接 触 冷 却 系 统 实 施 的工 艺 流 程 改 造 和 控 制 优 化 。 主 要 包 括 自流 热 水 直பைடு நூலகம்接 进 循 环 热 水 系 统 , 触 冷 却 系统 两 个 分 液 罐 的含 油 污 水 通 过 自动 选 择 控 制 系 统 , ~ 台 接 用
气 体经水 冷 器 WC14冷 却 后 进 入 分 液 罐 V1 7 0 0,
石 油艨 制 与记 工
井 , 循 环 水 场 回 收 。 自流 热 水 系 统 运 行 多 年 后 , 进 自流 热 水 系 统 泄 漏 点 较 多 , 进 循 环 水 场 途 中 自 在
流热水 损失 约 2 / 0t h左 右 , 而且 循环 水 中带 油 , 造
相 应 的 冷 却 分 离 设 施 。 中 国 石 化 镇 海 炼 化 分 公
司延 迟焦 化装 置接 触 冷却 ( 空 ) 放 系统 采 用 塔 式接
触 冷 却 技 术 , 焦 炭 塔 冷 焦 时 产 生 的 放 空 气 体 密 即 闭进 入 放 空 冷 却 塔 , 过 降 温 分 离 处 理 , 离 为 不 经 分
和节 能要 求 日益 严 格 , 对原 有 塔 式 接 触 冷 却 系统
进行 了一 系列 的流程 改造 和优化 。
2 塔 式 接 触 冷 却 工 艺 流 程概 述
延 迟 焦 化 装 置 接 触 冷 却 塔 系 统 流 程 见 图 l 。
焦炭塔 在 大 流 量 给 汽 和 给 水 冷 焦 时 , 生 水 汽 和 产 油气从 塔顶 进入 接触冷 却塔 T1 3 0 。接触 冷却 塔底
泵 送 人 污 油 罐 。 提 出 污油 罐 脱 水 采 取 源 头分 开 , 罐 串 联 静 置 沉 降 和 旋 流 除 油 结 合 处 理 后 进 污 水 汽 提装 置 的 技 多 术 路 线 。改 造 后 , 自流 热 水 处 理 成 本 每 年 降 低 1 万 元 ; 焦 水 罐 顶 气 硫 化 物 浓 度 降 至 4 1 / ( 准 状 态 ) 8 冷 . 4 mgm。 标 , 消 除 冷 焦 水 系 统 的 环境 恶臭 。
延迟焦化装置工艺过程简述及工艺流程简图

延迟焦化装置工艺过程简述及工艺流程简图2.1 工艺流程简述原料渣油(包括催化油浆及常Ⅲ洗涤油等)从装置外来,进入原料缓冲罐(V1101),经原料油泵(P1101/1、2)抽出升压后,先与柴油换热至181℃(E1101/1、2),接着与中段油换热至227℃(E1102/1、2),最后与蜡油换热至289℃ (E1103/1~4)后分两路进入分馏塔,一路进入分馏塔(T1102) 下段换热区与来自焦炭塔(T1101/1、2)的高温油气接触换热,高温油气中的循环油馏分被冷凝,原料油与冷凝的循环油一起进入分馏塔底,另一路直接进入分馏塔底部。
分馏塔底油经辐射进料泵入口过滤器FI1102/1、2过滤后由辐射进料泵(P1102/1~2)升压后进入加热炉(炉1101),经对流室和辐射室加热至490~505℃出加热炉,经过四通阀进入焦炭塔(T1101/1、2)底部。
在焦炭塔内经过高温和长时间停留,原料油和循环油在焦炭塔内发生一系列复杂的裂解、缩合等反应,最后生成焦炭和油气。
生成的高温油气自焦炭塔顶逸出去分馏塔下段换热区,焦炭在塔内沉积生焦并储存在塔内。
当焦炭塔生焦到一定高度后停止进料,切换到另一个焦炭塔内进行生焦。
切换后,老塔用蒸汽进行小吹汽,将塔内残留油气吹至分馏塔回收,小吹汽结束后改大吹汽、给水进行冷焦,焦炭塔大吹汽、给水冷焦时产生的大量高温蒸汽及少量油气进入接触冷却塔(T1103),接触冷却塔底的污油由接触冷却塔底泵(P1112/1、2)抽出,经水箱冷却器(WC1105)冷却后,部分作为T1103顶回流,部分送入本装置污油罐经脱水后做急冷油回炼。
塔顶蒸汽及轻质油气经塔顶空冷器、水冷器后入接触冷却塔顶油气分离器(V1106)分离,分离出的污油送入本装置污油罐,污水经接触冷却塔顶污水泵(P1113/1、2)升压后送入冷焦水热水灌(V1401),不凝气进入低压瓦斯管网。
进入分馏塔(T1102)下段换热区的高温油气与原料油直接接触换热后,冷凝下来的循环油进入分馏塔底,大量油气经过5块洗涤板后进入蜡油集油箱以上进行分馏,从下往上分别切割出蜡油、柴油、汽油和富气等馏分。
中石化焦化冷焦水罐和酸性水汽提原料罐恶臭治理调查报告
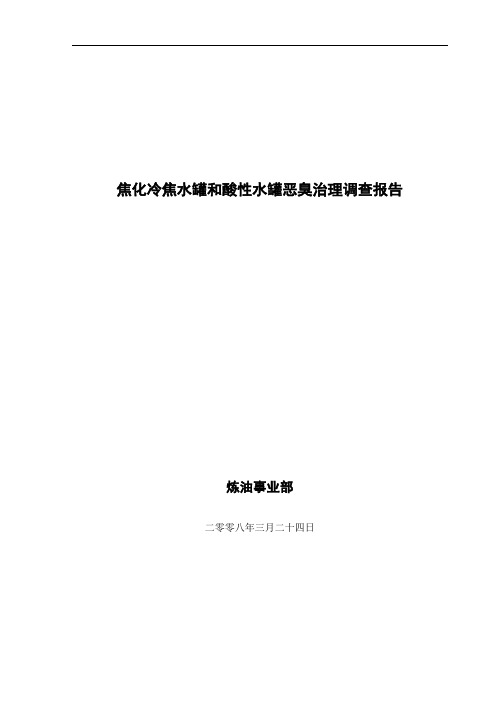
焦化冷焦水罐和酸性水罐恶臭治理调查报告炼油事业部二零零八年三月二十四日目录一、现状1、延迟焦化装置冷焦水罐运行情况2、酸性水汽提装置原料罐运行情况二、存在问题及原因分析三、恶臭治理不同技术路线比较四、技术改造建议五、设备投资和施工周期针对焦化装置冷焦水罐、酸性水汽提装置原料罐存在的安全隐患,以及恶臭气体排放导致的污染环境问题,为了给企业提供成熟的脱臭工艺技术,解决现场的安全隐患和环境治理问题,炼油事业部组织上海石化和济南分公司等单位的专家,于2008年3月23日~4月10日,对股份公司的焦化装置冷焦水罐以及酸性水汽提装置原料罐进行了专项调研。
一、现状2007年,股份公司共有33套焦化装置,总加工能力为2900万吨/年;酸性水汽提装置45套,酸性水处理能力为2000万吨/年。
本次对29套焦化冷焦水罐和24套酸性水汽提原料罐的恶臭治理进行了综合调研1、延迟焦化装置冷焦水罐延迟焦化装置冷焦水处理工艺路线有如下两种方式:一是老式的露天敞开式冷焦水池,有害有恶臭气体直排大气。
目前有齐鲁1#、胜利石化、沧州、金陵1#、扬子1#、上海石化1# 、茂名1、安庆8套装置采用这种工艺。
沧州和上海石化1#焦化装置对冷焦水池进行了局部改进,在露天敞开的水池上加盖、冷焦水风机冷却改为湿式空冷器冷却。
尽管改进型的冷焦水池回收了部分恶臭气体,仍没有从根本上解决有害有恶臭气体直排大气的问题。
二是冷焦水罐形式。
目前股份公司共有21套焦化装置采用冷焦水罐这类工艺形式,不同的装置又有不同的运行方式,该类冷焦水罐工艺运行方式如下:(1)敞口式冷焦水罐。
虽然安全问题不突出,但是由于恶臭挥发性气体直排大气,环境污染严重,九江仍采用这种方式,目前正在改造为全密闭式冷焦水罐。
(2)半密闭式冷焦水罐。
冷焦水罐顶通蒸汽保护,罐顶增设安全水封罐,隔绝了可燃性气体与空气混合接触,解决了安全问题。
但是,由于蒸汽温度较高(1.0MPa蒸汽温度为250℃),容易损坏罐内防腐涂料(涂料承受的最高温度一般不大于180℃);同时,由于蒸汽温度高,加剧了罐内恶臭气体挥发,冷焦水溢流期间容易破坏水封,导致恶臭气体间断排放大气。
延迟焦化装置冷焦系统工艺优化和节能措施

延迟焦化装置冷焦系统工艺优化和节能措施
张生
【期刊名称】《山东化工》
【年(卷),期】2024(53)1
【摘要】在对延迟焦化装置冷焦系统运行过程进行长时间的分析对比基础上,通过对焦化装置中冷焦系统的工艺改造及操作方法优化,解决原焦化装置在焦炭塔冷焦过程中存在的接触冷却塔T104气相负荷过大,造成接触冷却塔顶含硫污水乳化带油严重;后续焦化分馏单元携带焦粉较多,造成整个系统波动较大;柴油反冲洗过滤器SR105频繁反冲;蒸汽发生器SG102发汽量过大造成浪费等问题。
使延迟焦化装置能够长时间安全运行,并且减少系统工程1.0 MPa蒸汽的使用,减少装置的运行操作成本,提高装置的运行效益。
【总页数】3页(P187-189)
【作者】张生
【作者单位】中海沥青股份有限公司
【正文语种】中文
【中图分类】TQ520.5
【相关文献】
1.焦粉分离器在延迟焦化装置冷焦除焦系统的应用
2.延迟焦化装置冷焦水和切焦水的处理工艺优化
3.延迟焦化装置冷焦水系统生产优化和节能措施
4.延迟焦化装置冷焦水处理工艺及优化措施
5.延迟焦化装置冷焦工艺技术分析
因版权原因,仅展示原文概要,查看原文内容请购买。
02 延迟焦化冷焦水密闭处理技术工业应用总结(镇海)
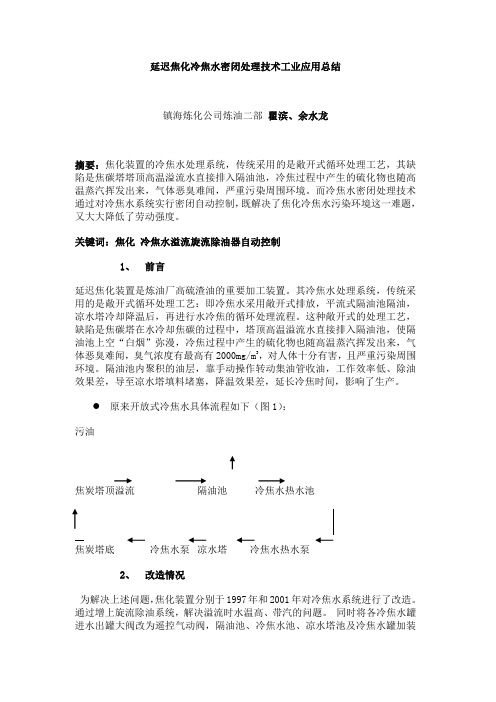
延迟焦化冷焦水密闭处理技术工业应用总结镇海炼化公司炼油二部瞿滨、余水龙摘要:焦化装置的冷焦水处理系统,传统采用的是敞开式循环处理工艺,其缺陷是焦碳塔塔顶高温溢流水直接排入隔油池,冷焦过程中产生的硫化物也随高温蒸汽挥发出来,气体恶臭难闻,严重污染周围环境。
而冷焦水密闭处理技术通过对冷焦水系统实行密闭自动控制,既解决了焦化冷焦水污染环境这一难题,又大大降低了劳动强度。
关键词:焦化冷焦水溢流旋流除油器自动控制1、前言延迟焦化装置是炼油厂高硫渣油的重要加工装置。
其冷焦水处理系统,传统采用的是敞开式循环处理工艺:即冷焦水采用敞开式排放,平流式隔油池隔油,凉水塔冷却降温后,再进行水冷焦的循环处理流程。
这种敞开式的处理工艺,缺陷是焦碳塔在水冷却焦碳的过程中,塔顶高温溢流水直接排入隔油池,使隔油池上空“白烟”弥漫,冷焦过程中产生的硫化物也随高温蒸汽挥发出来,气体恶臭难闻,臭气浓度有最高有2000mg/m3,对人体十分有害,且严重污染周围环境。
隔油池内聚积的油层,靠手动操作转动集油管收油,工作效率低、除油效果差,导至凉水塔填料堵塞,降温效果差,延长冷焦时间,影响了生产。
原来开放式冷焦水具体流程如下(图1):污油焦炭塔顶溢流隔油池冷焦水热水池焦炭塔底冷焦水泵凉水塔冷焦水热水泵2、改造情况为解决上述问题,焦化装置分别于1997年和2001年对冷焦水系统进行了改造。
通过增上旋流除油系统,解决溢流时水温高、带汽的问题。
同时将各冷焦水罐进水出罐大阀改为遥控气动阀,隔油池、冷焦水池、凉水塔池及冷焦水罐加装液位仪,在冷焦水系统增加流量及压力指示引入焦化DCS ,对冷焦水系统实行自动控制,一是降低了劳动强度,二是解决焦化冷焦水污染环境这一难题。
2.1工艺流程特点: 见图2:冷焦水密闭处理原则流程图(1) 焦炭塔溢流冷焦水由上部进入冷焦水罐,主要为防止溢流水温过高,夹带水汽,返混严重,在冷焦水罐处产生水击、撞裂进罐金属软管及罐壁。
用于延迟焦化装置中冷焦水隔油罐的湿法脱臭装置[实用新型专利]
![用于延迟焦化装置中冷焦水隔油罐的湿法脱臭装置[实用新型专利]](https://img.taocdn.com/s3/m/63592b500a1c59eef8c75fbfc77da26925c596f9.png)
[19]中华人民共和国国家知识产权局[12]实用新型专利说明书[11]授权公告号CN 200966974Y [45]授权公告日2007年10月31日专利号 ZL 200620047834.9[22]申请日2006.11.15[21]申请号200620047834.9[73]专利权人上海宁松热能环境工程有限公司地址201403上海市奉贤区金汇镇北新村四组乙-28[72]设计人敖建军 沃开宇 屈武第 [74]专利代理机构上海协和专利代理有限公司代理人张恒康[51]Int.CI.B01D 53/18 (2006.01)权利要求书 1 页 说明书 4 页 附图 1 页[54]实用新型名称用于延迟焦化装置中冷焦水隔油罐的湿法脱臭装置[57]摘要本实用新型涉及一种用于延迟焦化装置中冷焦水隔油罐的湿法脱臭装置,包括罐顶具有呼吸孔的冷焦水隔油罐,还包括一贫胺液输送管、一富胺液输出管及脱臭罐,所述冷焦水隔油罐的呼吸孔通过第一接管连通到所述脱臭罐的下部,所述贫胺液输送管连通到脱臭罐的上部,所述脱臭罐的顶部设有一排气口且在排气口连接一高于其罐顶的放空管。
本实用新型的脱臭装置以胺液脱硫,低温下吸收硫化氢,高温下可脱吸出来,胺液能实现再生,循环利用;很容易将硫化氢脱除,压降小,脱除率高,操作简单;排出的气体无臭味污染,可直接排入大气,极大地改善了空气质量和生存环境。
200620047834.9权 利 要 求 书第1/1页 1.一种用于延迟焦化装置中冷焦水隔油罐的湿法脱臭装置,包括罐顶具有呼吸孔的冷焦水隔油罐,其特征在于,还包括一贫胺液输送管、一富胺液输出管及脱臭罐,所述冷焦水隔油罐的呼吸孔通过第一接管连通到所述脱臭罐的下部,所述贫胺液输送管连通到脱臭罐的上部,所述脱臭罐的顶部设有一排气口且在排气口连接一高于其罐顶的放空管。
2.根据权利要求1所述的用于延迟焦化装置中冷焦水隔油罐的湿法脱臭装置,其特征在于,所述冷焦水隔油罐的顶部呼吸孔到脱臭罐的下部之间还连接一水封罐,该水封罐的进口与冷焦水隔油罐的顶部呼吸孔之间通过第二接管连接,水封罐的出口与脱臭罐之间通过第三接管连接,该水封罐的入水口经阀连接到一净化水管。
- 1、下载文档前请自行甄别文档内容的完整性,平台不提供额外的编辑、内容补充、找答案等附加服务。
- 2、"仅部分预览"的文档,不可在线预览部分如存在完整性等问题,可反馈申请退款(可完整预览的文档不适用该条件!)。
- 3、如文档侵犯您的权益,请联系客服反馈,我们会尽快为您处理(人工客服工作时间:9:00-18:30)。
2消除延迟焦化装置冷焦水系统恶臭-
-开发旋流除油技术组
消除延迟焦化装置冷焦水系统恶臭
--开发旋流除油技术组合工艺
(中国石化镇海炼化公司)
摘要:该文通过对延迟焦化装置冷焦水系统恶臭现状的调查与分析,开发了旋流除
油技术组合工艺,在国内首次实现了延迟焦化装置冷焦水系统的密闭处理。
实际应
用情况表明,冷焦水的除油效果及冷却后的温度都达到了生产要求, 周围环境也得
到了明显改善,达到了消除恶臭的目的。
关键词:延迟焦化装置冷焦水系统旋流除油技术消除恶臭
1概况
我国焦化装置的冷焦水处理系统普遍采用溢流式冷焦操作,以及隔油池、污油池等老一套处理设施,个别装置的冷焦水采用露天逐级沉降方式,这种工艺流程不仅占地面积大、除油效率
低,而且空气污染严重。
为解决以上问题,镇海炼化公司开发了冷焦水密闭循环处理工艺技术,该技术集成了液一液混合
注水降温技术、重力沉降与旋流分离组合的焦粉一重油一水三相分离技术、空冷器密闭冷却技术处理冷焦水,实现了焦化冷焦水的密闭处理。
该技术的主要工艺过程:从焦碳塔溢流而出的高温冷焦水,首先与部分低温冷焦水混合,使其水温低于100C进入密闭沉降罐,减少夹带油气的蒸汽挥发;污水在沉降罐中停留一定时间后,焦粉和油大部分得到沉降或上浮,达到初步净化分离。
经初步分离后的冷焦水还带有一定量的比重接近于水的焦粉以及悬浮油,进入旋流器进一步深度净化,从旋流器出来的含油水返回沉降罐继续分离,净化后的水进入空冷器冷却,再进入焦碳塔循环使用。
2旋流除焦技术组合工艺
延迟焦化装置冷焦水系统恶臭产生的原因主要有:凉水塔、隔油池油水混 合气挥发多,冷焦水含油浓度高,恶臭严重;冷焦水温度高,冷焦水罐顶呼吸 阀、泡沫产生器和液位计口冒油水混合气体,产生恶臭;溢流水进冷焦水罐温 度高,产生水击,使管子振动大并拉裂金属软管及冷焦水罐壁焊缝,冷焦水外 泄,产生恶臭;凉水塔换热降温效果差,延长了正常的冷焦时间,冷水塔油气 挥发时间长;各冷焦水罐及冷焦水池无测量仪表和控制阀,冷焦水系统各工艺 参数不易控制等。
为此,我们开发旋流除油技术组合工艺(如图 2),以达到消除延迟焦化装 置冷焦水系统恶臭的目的。
低温谱焦水
J ・ 污油耀 油;2000mg/L
塔顶冷焦镒流水―冷焦水確―-热水泵提升 ―■旋流除油器
1 I
______________________________ 污ift 空冷器:2片 I 预
雷:4片
J r
焦炭塔冷_冷水泵捉 _冷水池水温;90〜65C
—凉水塔 — 图2旋流除油技术组合工艺示意图
(1)解决凉水塔、隔油池油水混合气挥发多,冷焦水含油浓度高,冷焦水 池周围恶臭等问题。
针对冷焦水中油水混合气挥发多、冷焦水池周围恶臭等问题,我们分析认 为产生这一现象的主要原因为冷焦水含油量高。
由于冷焦水与其它含油污水有 明显的不同,在其组成中,初期为蒸气、含油污水、焦粉三相混合物,其中含 油污水中油的密度达到939.6g/cm 3
(标准状态),与水的密度非常接近;焦粉 中,多孔焦粉吸油减轻,部分焦粉密度小于水,混浮于油中,部分焦粉油;100mg/L 2台:串联 _ 预留:2台
大于水,沉积在底部,部分焦粉与水比重相同,混浮于水中。
冷焦水中油浮升和焦粉颗粒沉降曲线见图3。
根据水质特点,确定了“贮罐重力除油除焦一一旋流油水分离”两段除油除焦技术,即“油一一水”和“液一一固”混合物的重力沉降分离法。
其原理是利用两相比重差使分散的油颗粒脱离水体浮至液面,悬浮的固体颗粒沉降而分离。
油滴浮升速度和颗粒沉降速度符合Stokes 定律。
对除油器来说,重力分离的效率依赖于正确的水力学设计,在给定流速的情况下,停留时间越长,效果越好。
因此,在给定上升气速的情况下,分离效率是几何参数的函数,流体的停留时间必须同油颗粒上升至液面时间相对应。
而对被处理水体来说,除油效率主要取决于水体中浮油含量。
根据这一原理,我们利用焦化装置原有的3个700m冷焦水贮罐(贮罐内设有自动收油设施),温度较高的冷焦水进罐后,浮油大部分被去除,轻重焦粉分别被浮升和沉降去除,较好地实现油和焦粉的粗分离,初步除油除焦粉后的冷焦水再经冷焦水热水泵增压后进入后续的冷焦水旋流除油器,冷焦水中的分散油、乳化油经离心分离后,与贮水罐隔出的污油密闭进入污油罐,经脱水后污油全部回收。
除油后的冷焦水进入空冷器降温,并贮存于冷焦水罐,供冷焦
水泵使用。
这样,实现了冷焦水的密闭循环处理,基本解决了冷焦水含油浓度高、油水混合气挥发多、冷焦水池周围恶臭等问题。
(2)解决冷焦水温度高,冷焦水罐顶呼吸阀、泡沫产生器和液位计口冒油水混合气体,产
生恶臭问题。
针对这一问题,在国内首次采用了水一水混合器注水降温技术,即利用经空冷和冷水塔充分冷却后50C以下的冷焦水经喷射泵直接喷入从焦炭塔顶来的温度较高的溢流冷焦水中,对溢流冷焦水进行冷却降温,使水温降至90C以下, 基本解决了溢流冷焦水温度高,冷焦水贮罐顶呼吸阀、液位计口及泡沫产生器
“冒汽”,污染大气的环保问题。
(3)解决溢流水进冷焦水罐温度高,冷焦水夹汽产生水击,管子振动大,拉裂金属软管及冷焦水罐壁焊缝问题。
为解决这一问题,我们一方面对焦炭塔冷焦改溢流时的塔上部温度和塔顶压力等工艺指标进行了严格规定,防止将大量夹带水汽的冷焦水改入冷焦水罐;另一方面,对溢流水进冷焦水罐流程进行了改造,溢流水由原来从底部进罐改为从罐中部进,解决了溢流水进冷焦水罐温度高产生水击,管子振动大,拉裂金属软管及冷焦水罐壁焊缝问题。
(4)解决凉水塔换热降温效果差,冷焦时间长,凉水塔油气挥发时间长问题。
我们在冷焦水进冷水储存池前,设置了四片空冷,降低了进凉水塔池的冷焦水水温。
其中两片空冷是镇海炼化检安公司制造叠片式空冷,单位面积的冷却能力比翅片式空冷高出20%之后,运行2年,冷却效果保持较好,四台空冷的稳定运行使得装置在2003年开工之后一直保持停用凉水塔状态,真正实现密闭冷焦。
(5)解决各冷焦水罐及冷焦水池无测量仪表和控制阀,各工艺参数不易控制冋题
为解决这一问题,我们将各冷焦水罐进、出罐大阀改为遥控气动阀,隔油池、冷焦水池、凉水塔池及冷焦水罐加装液位仪,在冷焦水系统增加流量及压力指示,并引入焦化DCS真正实现了对焦化冷焦水系统的集中自动控制。
3 、成效分析
3.1投资和运行成本
97年焦化装置冷焦水系统改造,增加了3个冷焦水罐及配套液位、温度监控系统,投资为
355万元;2000年7月增设旋流除油设备(2台)、空冷器(2台)及与其相配套的泵、阀、管线等设计。
该项目共投资205万元,其中科研投入
65万元,生产投入140万元。
在2003年3月对冷焦水罐作了进一步完善改造,增加了两台蝶片式空冷和一组旋流器,改造技措费用130万,旋流器费用140
万,总计270万元。
三次累计投资为830万。
该项目实施并正常投入生产后,仅四台15KWH风机及二台30KWH泵的
动力消耗,与原凉水塔工艺相比,增加15KWH的动力消耗。
项目实施后的全
年动力消耗:78.84万度电,按每度电0.53元计,则全年运行成本为41.78万元。
3.2年经济效益
本项目的效益主要体现在社会效益及环境效益。
该技术在镇海炼化公司焦化装置实施后,冷焦水油浓度低于150mg/l,焦粉浓度小于50mg/l,水温小于
55C,操作可靠,占地面积小。
更重要的是,焦化冷焦水系统作业环境大为改善:第一,改造前,焦碳塔排放冷焦水时,隔油池入口处蒸汽弥漫,散发出强烈恶臭,臭气浓度高达2000;改造后,高温冷焦水在管道混合器内与低温冷焦水混合降温后进入污水贮罐,罐顶呼吸口没有蒸汽逸出。
第二,改造前,高温冷焦水用泵打到凉水塔顶喷淋鼓风冷却,易挥发的有机物被不断吹脱、蒸发、逸散,形成一个影响范围较大的恶臭面源,改造后,从贮罐出来的冷焦水直接进入密闭的旋流器除油和密闭的空冷器冷却,有效地防止了有机恶臭气体的散发。
该技术实施后,也取得了一定的经济效益:一是回收冷焦水中污油产生的效益。
二是减少凉水塔填料更换和风机维修费用10万元/年。
污染物削减量
项目实施后,净化后冷焦水出口含油浓度在150mg/l左右,污水中所含的烃类大为削减,且污水中的COD、硫化物、酚含量也大为降低。
具体见下表1:表1冷焦水除油效果
同时,对焦化冷焦水系统的环境监测结果表明,实施冷焦水密闭处理工艺
后,作业环境空气质量明显提高(见表2)。
表2焦化冷焦水作业环境空气监测
5 结束语
综上所述,冷焦水系统改造项目是成功的,并在国内首次实现了延迟焦化装置冷焦水的密闭处理,冷焦水的除油效果及冷却后的温度都达到了生产要求, 周围环境改善效果显著,并很好地改善了焦化装置的工作强度及作业环境。
但是冷焦水系统敞口凉水塔未拔除,隔油池、冷焦水池未完全密闭,冷焦水
中易挥发的恶臭污染物仍有部分被蒸发、逸散,形成恶臭源,有待于进一步的完善
改造,准备在以后的大修中所有冷焦水池用水泥完全密封,原有的冷焦水池和冷焦
水罐的恶臭气体改用接管与脱臭罐连接,排出气体经过脱臭剂床层催化剂脱臭后,在高处改有序放空,以真正实现冷焦水系统的全密闭处理,彻底解决延迟焦化装置冷焦水系统恶臭对周围环境的污染。