第2章-裂解气分离.
化学工艺学课后习题及答案
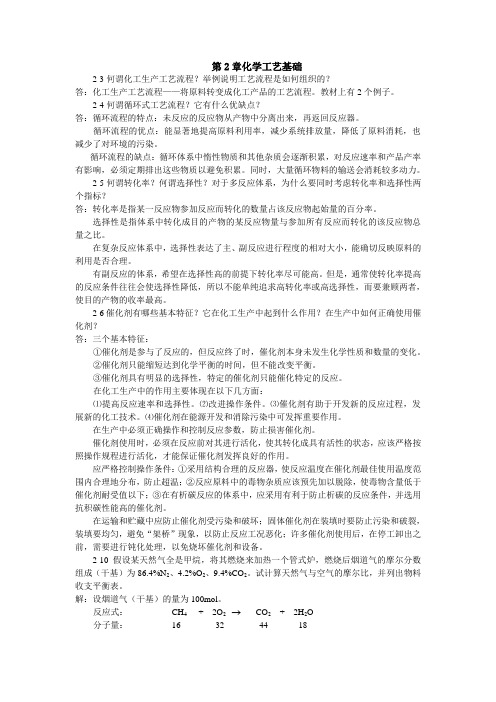
第2章化学工艺基础2-3何谓化工生产工艺流程?举例说明工艺流程是如何组织的?答:化工生产工艺流程——将原料转变成化工产品的工艺流程。
教材上有2个例子。
2-4何谓循环式工艺流程?它有什么优缺点?答:循环流程的特点:未反应的反应物从产物中分离出来,再返回反应器。
循环流程的优点:能显著地提高原料利用率,减少系统排放量,降低了原料消耗,也减少了对环境的污染。
循环流程的缺点:循环体系中惰性物质和其他杂质会逐渐积累,对反应速率和产品产率有影响,必须定期排出这些物质以避免积累。
同时,大量循环物料的输送会消耗较多动力。
2-5何谓转化率?何谓选择性?对于多反应体系,为什么要同时考虑转化率和选择性两个指标?答:转化率是指某一反应物参加反应而转化的数量占该反应物起始量的百分率。
选择性是指体系中转化成目的产物的某反应物量与参加所有反应而转化的该反应物总量之比。
在复杂反应体系中,选择性表达了主、副反应进行程度的相对大小,能确切反映原料的利用是否合理。
有副反应的体系,希望在选择性高的前提下转化率尽可能高。
但是,通常使转化率提高的反应条件往往会使选择性降低,所以不能单纯追求高转化率或高选择性,而要兼顾两者,使目的产物的收率最高。
2-6催化剂有哪些基本特征?它在化工生产中起到什么作用?在生产中如何正确使用催化剂?答:三个基本特征:①催化剂是参与了反应的,但反应终了时,催化剂本身未发生化学性质和数量的变化。
②催化剂只能缩短达到化学平衡的时间,但不能改变平衡。
③催化剂具有明显的选择性,特定的催化剂只能催化特定的反应。
在化工生产中的作用主要体现在以下几方面:⑴提高反应速率和选择性。
⑵改进操作条件。
⑶催化剂有助于开发新的反应过程,发展新的化工技术。
⑷催化剂在能源开发和消除污染中可发挥重要作用。
在生产中必须正确操作和控制反应参数,防止损害催化剂。
催化剂使用时,必须在反应前对其进行活化,使其转化成具有活性的状态,应该严格按照操作规程进行活化,才能保证催化剂发挥良好的作用。
有机化工生产技术-10-裂解气分离工艺流程

裂解气分离工艺流程授课内容:●裂解气分离工艺流程●裂解气分离过程操作知识目标:●掌握裂解气分离原则流程●掌握裂解气分离过程操作步骤和方法能力目标:●混合物精馏分离方案设计●混合物精馏分离过程操作条件制定思考与练习:●裂解气分离工艺流程主要由哪些过程构成?●裂解气分离过程操作主要异常现象及处理方法第四节裂解气深冷分离一、深冷分离流程1.深冷分离的任务裂解气经压缩和制冷、净化过程为深冷分离创造了条件—高压、低温、净化。
深冷分离的任务就是根据裂解气中各低碳烃相对挥发度的不同,用精馏的方法逐一进行分离,最后获得纯度符合要求的乙烯和丙烯产品。
2.三种深冷分离流程深冷分离工艺流程比较复杂,设备较多,能量消耗大,并耗用大量钢材,故在组织流程时需全面考虑,因为这直接关系到建设投资、能量消耗、操作费用、运转周期、产品的产量和质量、生产安全等多方面的问题。
裂解气深冷分离工艺流程,包括裂解气深冷分离中的每一个操作单元。
每个单元所处的位置不同,可以构成不同的流程。
目前具有代表性三种分离流程是:顺序分离流程,前脱乙烷分离流程和前脱丙烷分离流程。
(1)顺序分离流程顺序分离流程是按裂解气中各组分碳原子数由小到大的顺序进行分离,即先分离出甲烷、氢,其次是脱乙烷及乙烯的精馏,接着是脱丙烷和丙烯的精馏,最后是脱丁烷,塔底得碳五馏分。
图2-4 顺序分离工艺流程简图1—压缩Ⅰ、Ⅱ、Ⅲ段;2—碱洗塔;3—压缩Ⅳ、Ⅴ段;4—干燥器;5—冷箱;6—脱甲烷塔;7—第一脱乙烷塔;8—第二脱甲烷塔;9—乙烯塔;10—加氢反应器;11—脱丙烷塔;12—第二脱乙烷塔;13—丙烯塔;14—脱丁烷塔;15-甲烷化;16-氢气干燥器顺序深冷分离流程如图2-4所示。
裂解气经过压缩机Ⅰ、Ⅱ、Ⅲ段压缩(1),压力达到1.0MPa,送入碱洗塔(2),脱除酸性气体。
碱洗后的裂解气再经压缩机的Ⅳ、Ⅴ段压缩(3),压力达到3.7MPa,送入干燥器(4)用分子筛脱水。
干燥后的裂解气进入冷箱(5)逐级冷凝,分出的凝液分为四股按其温度高低分别进入脱甲烷塔(6)的不同塔板,分出的富氢经过甲烷化(15)脱除CO及干燥器(16)脱水后,作为碳二馏分和碳三馏分加氢脱炔用氢气。
第2章生产单体的原料路线

裂解反应比脱氢反应容易进行,碳链长的比碳链短易产 生断链反应。 石油有热裂化和催化裂化两种
热裂解
目的: 提高汽油的产量。通过加 热使分子能量升高,满足链断裂 所需能量,从而分解成其他物质。
缺点:温度过高,发生结焦现象
催化裂解
目的: 提高汽油的质量和产量。 降低反应温度,增加低碳烯烃 产率和轻质芳烃产率,提高裂 解产品分布的灵活性。
干燥的裂解气的分离: 裂解气除含低级烯烃、烷烃外,还有H2。它们在常 温下是气体,分离提纯困难。 制取高纯度的乙烯和丙烯必须用深度冷冻分离法(深 冷分离法)处理裂解气。 深冷分离法是将干燥的裂解气冷冻到-100℃左右, 使除H2和CH4以外的低级烃全部冷凝液化,然后将 它们在适当的温度和压力下逐一分离。而H2和CH4 的分离是将其冷冻到-165℃,使 CH4 液化,最后得 到富氢气体。 裂解气的冷冻是通过乙烯和丙烯冷冻系统来完成的。 低级烯烃经精馏分离得到的主要产品: 乙烯收率为25%~26%,丙烯收率为16%~18% , C4馏分收率为11%~12% 。副产品是H2和CH4。
压缩机:一系列用于气体物料压缩和冷冻系统提供动 力。
蒸馏塔: 一系列用来分离各种产品和副产品。
(4)裂解气分离精制:
高温裂解产物是多组分的低级烯烃与烷烃的混合物, 少量的酸性气体和炔烃等杂质,还有一些水蒸气。 生产高纯度的单一烯烃必须进行精制分离。
裂解气精制分离: 用3%~5%NaOH溶液洗涤裂解气,脱除酸性气体 (CO2、H2S等)。 炔烃(乙炔和甲基乙炔)杂质一般用钯催化剂,进行 选择性加氢转化为烯烃; 大部分水蒸汽在气体压缩过程中冷凝已除去,少量的 水则用分子筛进行干燥。
4. 聚氨酯类 所需单体:多异氰酸酯、多羟基化合物。 5. 有机硅聚合物 所需单体:甲基硅氧烷。 6. 酚醛树脂 所需单体:甲醛、苯酚。 7. 脲醛树脂 所需单体:甲醛、尿素。 8. 环氧树脂 所需单体:双酚A、环氧氯丙烷。
有机化工习题
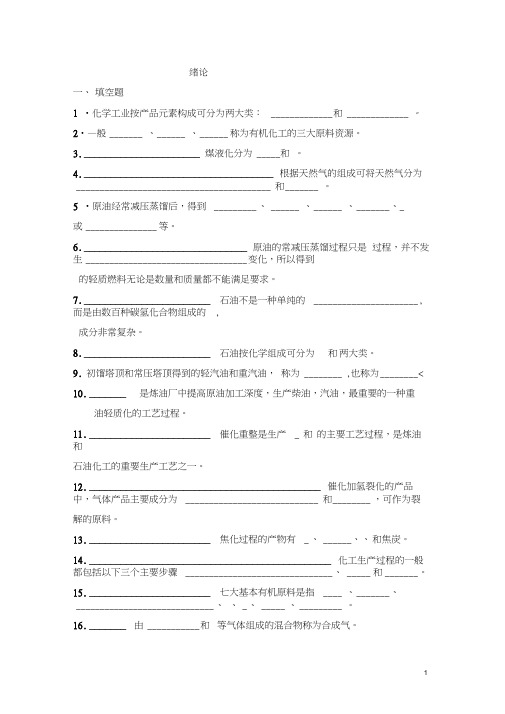
绪论一、填空题1 •化学工业按产品元素构成可分为两大类:_____________ 和 _____________ 。
2•—般_______ 、______ 、______ 称为有机化工的三大原料资源。
3. ______________________ 煤液化分为 _____ 和。
4. ____________________________________ 根据天然气的组成可将天然气分为_________________________________________ 和_______ 。
5•原油经常减压蒸馏后,得到_________ 、______ 、______ 、_______ 、_或_______________ 等。
6. _______________________________ 原油的常减压蒸馏过程只是过程,并不发生__________________________________ 变化,所以得到的轻质燃料无论是数量和质量都不能满足要求。
7. ________________________ 石油不是一种单纯的______________________ ,而是由数百种碳氢化合物组成的 ,成分非常复杂。
8. ________________________ 石油按化学组成可分为和两大类。
9.初馏塔顶和常压塔顶得到的轻汽油和重汽油,称为 ________ ,也称为________ <10. _______ 是炼油厂中提高原油加工深度,生产柴油,汽油,最重要的一种重油轻质化的工艺过程。
11. _______________________ 催化重整是生产_ 和的主要工艺过程,是炼油和石油化工的重要生产工艺之一。
12. ____________________________________________ 催化加氢裂化的产品中,气体产品主要成分为____________________________ 和________ ,可作为裂解的原料。
裂解气分离设计范文

裂解气分离设计范文裂解气分离设计是一种常见的化工过程,用于将原料气体进行分离和提纯。
该过程主要用于石油化工工业中,在裂解炉中对重质石油化工原料进行热裂解,生成炼油气等多种气体组分,然后通过分离和提纯过程,将所需的各种气体分离出来。
裂解气分离设计的关键步骤包括原料气体的预处理、主分离过程和后处理过程。
其中,原料气体的预处理是为了去除杂质和调整气体组分的组成,以满足下一步的分离要求。
该步骤通常包括氢气、烯烃、硫化氢和一氧化碳等气体的除去,并根据具体工艺要求,调整气体组分的比例。
主分离过程是指将原料气体中的不同组分进行有效分离的过程。
常用的主分离技术包括吸收、膜分离、吸附和蒸馏等。
吸收是指通过溶剂将原料气体中的特定组分吸收到液相中,从而达到分离的目的。
常用的溶剂包括乙二醇、N-甲基吡咯烷酮和脱氟溶剂等。
膜分离是通过选择适当的膜材料,根据不同气体分子的大小和极性差异,使其通过膜的速率不同,从而实现分离。
吸附是指利用吸附剂的亲和性差异,将原料气体中的特定组分吸附到固体表面上,然后通过调整吸附条件,使吸附剂释放出被吸附的组分。
蒸馏是利用原料气体中各组分的沸点差异,通过加热和冷凝的方式,将各组分逐一分离出来。
后处理过程是指对分离出来的气体进行进一步净化和提纯的过程。
常见的后处理技术包括冷却凝结、压缩和吸附等。
冷却凝结是将气体通过冷却和压缩,使其凝结成液体,然后通过重力分离或离心分离的方式,将液体与气体分离。
压缩是将气体通过增加压力,使其体积减小,从而使其中的杂质浓度增加,然后通过吸附或冷却凝结的方式将杂质去除。
吸附是通过在固体表面上吸附分子的方式,将气体中的杂质吸附到固体表面上,从而净化气体。
裂解气分离设计的关键是选择合适的分离技术和优化操作条件。
在选择分离技术时,需要考虑气体组分的差异和目标分离效果,并综合考虑经济性、操作简便性和安全性等因素。
优化操作条件可以通过调整温度、压力、流量和各组分的比例等参数,以达到最佳的分离效果和经济效益。
第2章生产单体的原料路线2

加拿大 1752 11.91 348 221
伊朗 1370 9.31 425 185
伊拉克 1150 7.82 264 69.4
•石油用途很广,其需要经过加工制成各种产品 才能满足各种需求。
第2章生产单体的原料路线2
• (2)石油炼制工业
•指原油经石油炼制加工得到单体及其他石油产品的工业。
•石油炼厂主要生产装置:
第2章生产单体的原料路线2
•第二节 从石油和天然气获得的石油化工原料路线
•1. 石油的组成及炼制 •(1)石油(原油)的组成
• 石油主要存在于地球表面以下的一种有气味的从黄色到黑
色的粘稠液体, 比水轻(密度大约在0.75~1.0),不溶于水。 • 主要为:碳、氢两种元素所组成的各种烃类混合物(C: 83%~87%。H:11%~14%),并含有少量的含氮、含硫、 含氧化合物。 •石油中的化合物分:烃类、非烃类以及胶质和沥青三大类。
• 5. 有机硅聚合物 • 所需单体:甲基硅氧烷。
• 6. 酚醛树脂 • 所需单体:甲醛、苯酚。
• 7. 脲醛树脂 • 所需单体:甲醛、尿素。
• 8. 环氧树脂 • 所需单体:双酚A、环氧氯丙烷。
• 三. 溶剂 • 1. 烃类溶剂 • 如:加氢汽油、己烷、抽余油。
第2章生产单体的原料路线2
• 2. 芳香族溶剂 • 如:甲苯、二甲苯。
•一些石油裂解装置的主要作用:
•裂解炉:裂解反应在管式裂解炉中进行。为减少副反 应,提高烯烃收率,液态烃在高温裂解区的停留时间 仅0.2~0.5秒。
•急冷锅炉:将800℃的裂解气用水冷却,同时水被加 热成高温高压的水蒸气,作为驱动汽轮和压缩机透平 (涡轮:透平是英文turbine的音译)的动力使用(即 回收能量),同时停止裂解反应。
《化工工艺学》第二章烃类热裂解
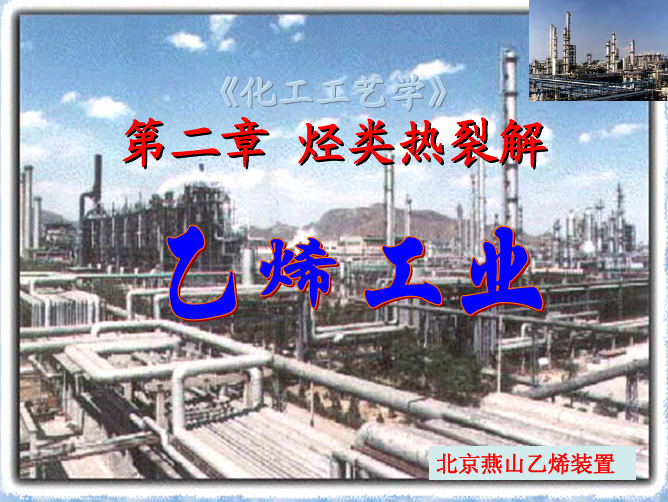
第二章 烃类热烈解(乙烯的生产)
3
第一节:热裂解原理
¾ 乙烯性质、用途、生产方法 * ¾ 乙烯产品标准*
生成。
第二章 烃类热烈解(乙烯的生产)
24
(三)停留时间的影响
定义:物料从反应开始到达某一转化率时,在 反应器中经历的时间。 裂解管式反应器特点:
① 非等温 ② 非等容
1、停留时间的计算 2、τ的影响 3、T— τ的关系
第二章 烃类热烈解(乙烯的生产)
25
1、停留时间的计算
①表观停留时间:t R
EC-C> EC-H
乙烷裂解的三个阶段
*链引发: C2 H 6 ⎯⎯k1→CH3 + CH3 CH3 + C2 H 6 ⎯⎯k2 →CH 4 + C2 H5
*链传递:C H3 + C2H6 ⎯⎯→CH4 + C 2H5 C2H5 ⎯⎯k3→C2H4 + H
C2H6 H
*链终止:H
第二章 烃类热烈解(乙烯的生产)
16
(一)族 组 成
¾ 简称PONA值,即P烷烃、 O烯烃、 N环 烷烃、A芳烃。
¾从表中比较:同条件下,原料愈轻,乙 烯收率增加;分子量愈大,(N+A)量愈 大,乙烯收率愈小,液态产物量愈大。
第二章 烃类热烈解(乙烯的生产)
17
(二)原料含氢量
¾ 原料中同C原子数时含H量:烷烃>环烷烃>芳烃。
=
新鲜原料量
× 100 %
第2章-裂解气分离

解决办法
多段压缩和 冷却相结合
二烯烃高温度下聚合和结焦
裂解气经压缩,压力升高 温度升高
裂解气压缩后限制的原因
高压法和低压法的比较
高压法 分离温度高 多耗压缩功 低压法 分离温度低 少耗压缩功 多耗冷量
少耗冷量
塔釜温度高,易 聚合,相对挥发度 低,分离困难
塔釜温度低,不易聚合, 相对挥发度大,分离容 易
第二节 压缩和制冷系统
目的和任务 压力与温度的关系
多级压缩的优点
制冷剂的选择
需要大量冷量和耐低温设备
解决办法
常压,冷凝、精馏分离温度低
裂解气常压沸点很低
加压 提高组分的沸点 提高操作温度
压缩的原因
一、裂解气的压缩
1.压力与温度的关系
根据物质的冷凝温度随压力增加而升高的规律,对 裂解气加压,从而使各组分的冷凝点升高,这既有利于 分离,又可节约冷冻量和低温材料。
裂解气分离方法
用吸收剂吸收除甲烷和氢气以外的其它 组分,然后根据溶解度不同进行精馏, 把各组分从吸收剂中逐一分离。
流程简单,动力设备少,投资少,但技 术经济指标和产品纯度差,已被淘汰。
油吸收
精馏分离
在-100℃左右的低温下,将裂解气中除 氢和甲烷以外的其它烃类全部冷凝下来。 然后利用裂解气中各种烃类的相对挥发 度不同,在合适的温度和压力下,以精 馏的方法将各组分分离开来,达到分离 的目的 。
90· 6
1· 019 1· 99
92· 2
2· 108 2· 11
2· 0
此外,对裂解气压缩冷却,还能除掉相当量的水份和 重质烃,以减少后继干燥及低温分离的负担。
多级压缩优势
节约压缩功耗
聚合物合成工艺学第2章生产单体的原料路线

CH2
CH2
+CH2
CH
CH2
+Cl2+O2
CH2Cl
CH2Cl
CH2
CHCl
+CH3COOH+O2
CH2
CH
OOCCH3
聚乙烯 乙丙橡胶
聚氯乙烯 聚乙酸乙烯酯
聚乙烯醇
+C6H6 AlCl3
C2H5
C6H5 -H2
CH2
维纶树脂
CH
C6H5
聚苯乙烯 ABS树脂 丁苯橡胶
O2
CH2
CH2
O
CH2
OH
CH2
➢ 矿产资源是不可再生的。
2-2 石油化工路线
石油化工路线
原油
石油炼制得
炼厂气和 汽油、石脑油、
煤油、柴油 高温裂解 等馏分
裂解气
分离
乙烯、 丙烯、丁烯、
丁二烯等
液体
加氢后
芳烃
催化重 整
萃取 分离
苯、 甲苯、二甲苯等
芳烃化合物
原油
石油
从油田开采出来未经 加工的石油称为原油
性质: 褐红色 至黑色 的粘稠 液体。 比水轻 不溶于水
不饱和聚酯树脂 聚芳酰胺
于DMF中进入第一汽提塔与溶剂DMF分离。
粗丁二烯气体经压缩液化送入第二萃取蒸
馏塔(塔3),一部分则回第一萃取蒸馏塔。 在塔 (3)中丁二烯被馏出进入塔 (5)进行第一
次精馏。脱除了甲基乙炔的丁二烯,再进
入塔 (6)进行第二次精馏,塔顶得精丁二烯, 塔底高沸点物为顺丁烯-2,丁二烯-1,2, 乙 剂基DM乙F炔中、含C有5馏一分部等分。丁塔二(烯3)和底乙部烯流基出乙的炔溶, 送入塔 (4)以回收丁二烯。含有乙烯基乙炔 的DMF经精制后回收DMF。
第二章烃类热裂解反应
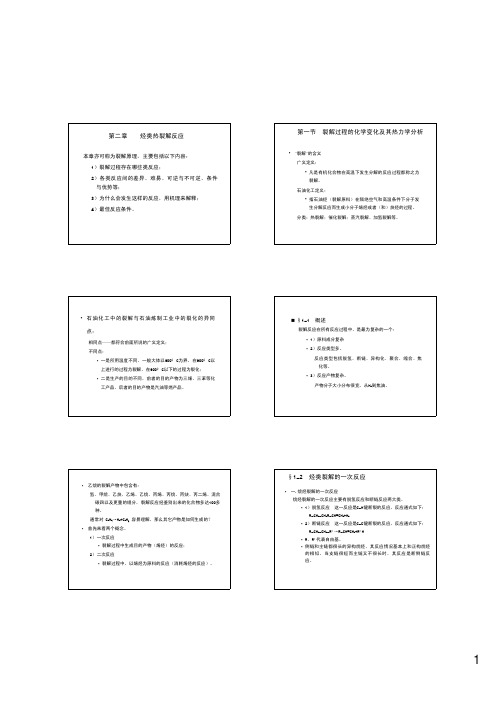
:,Dβ=289.8k J/m o l,而烷的容易程度按下列顺序递增:烷烃的C-C键<双键β位置的C-和反应过程的标准吉布斯函准吉布斯函数变,简称标衡常数。
——化合物i 在化学反应中的化学计量系数;化合物i 的标准生成吉布斯函数,k J /m o l ;度的函数:=A +B T +C T 2+D T 3、C 、D 为计算系数。
几种烃的计算系数见教材52页表2-1。
得,示反应达到平衡时成物愈占率越高,反应可能向向进行而若是正值,并负值的情若时就可以第二节裂解反应机理和动力学规律•§2-1自由基链反应机理一.乙烷的自由基链反应机理•首先从裂解过程最简单的乙烷脱氢生成乙烯的反应谈起。
C2H6→C2H4+H2•该反应式只是说明了从什么反应物分子,按什么计量关系,最后生成什么产物分子。
但这个反应式仅给出了总的反应结果,并不说明反应进行的途径。
说道这里我们不禁要问:是不是乙烷分子中两个C-H键断裂而脱下就生成乙烯分子哪?还是通过生成其他的中间物质,经过几步才生成乙烯哪?乙烷的裂解反应的三个阶段:如表中数据所示,乙烷中C-C键的解离能是88.0k c a l/l,而C-H键的解离能是98.0k c a l/m o l,所以乙烷的引发是C-C键的断裂引起的。
第二阶段是链增长反应,又称链传递反应或链转移反应就是自由基与分子反应,生成目的产物及新的自由基的程。
第三阶段是链终止反应。
如果链增长阶段不受阻碍的继链反应长度L c h在乙烷裂解中:随着温度的上升链长度是减小的,但乙烯的生成对于乙烷的分解的相对速度仍是一个很大的数值。
而且从各个基元反应的速度常数看乙烷引发反应的k11远小于其主基元反应的k33、k44、k55。
乙烷的引发反应是整个反应的控制步骤,而随着温度的上升,k比k33、k44、k55增大的倍数要大的多,所以提高温度对提高整个反应速度是有利的,此时链长度仍是很大的数值。
1.烃类在裂解时的几条规律1.烃烃分子中不同位置氢原子与自由基的反应速度不同,其反应途径也不同。
第2章-裂解气分离

第二节 压缩和制冷系统
目的和任务 压力与温度的关系
多级压缩的优点
制冷剂的选择
需要大量冷量和耐低温设备
解决办法
常压,冷凝、精馏分离温度低
裂解气常压沸点很低
加压 提高组分的沸点 提高操作温度
压缩的原因
一、裂解气的压缩
1.压力与温度的关系
根据物质的冷凝温度随压力增加而升高的规律,对 裂解气加压,从而使各组分的冷凝点升高,这既有利于 分离,又可节约冷冻量和低温材料。
高压下的氨蒸气的冷凝点是比较高的。例如把 若液氨在 1.55MPa 压力下汽化,由于沸点为 氨蒸气加压到 1.55MPa 时,其冷凝点是 40℃, 40℃,不能得到低温,为此,必须把高压下的 此时,氨蒸气在冷凝器中变为液氨,可由普通 液氨,通过膨胀阀降压到0.12MPa,若在此压 冷水将所放出的热量带走。 力下汽化,温度可降到-30℃。由于此过程进 行的很快,汽化热量来不及从周围环境吸取, 全部取自液氨本身。节流后形成低压,低温的 汽液混合物进入蒸发器。在此液氨又重新开始 下一次低温蒸发吸热。反复进行,形成一个闭 合循环操作过程。
降低出口温度
段间净化、分离
便于在压缩段间进行净化和分离水、 酸性气体、脱重组分。
制冷系统
分离要求
制冷
制冷剂
低于环境温 度的深冷温 度条件下进 行(制冷原 因)
创造环境空 气、水等 所不能实现 的低温条件
制冷循环中 完成热量转 移的工作介 质
二、制冷
1、冷冻循环制冷 2、节流膨胀制冷
3、热泵
1、冷冻循环制冷
制冷原理
冷冻剂自液态汽化时,要从物料中吸收热量, 使物料温度降低。所吸收的热量,在热值上等于 它的汽化潜热。 液体的汽化温度(即沸点)是随压力的变化而改 变的,压力越低,相应的汽化温度也越低。
裂解气的分离裂解气的组成及分离方法.pdf

第二章裂解气的分离第一节裂解气的组成及分离方法一、裂解气的组成及分离要求石油烃裂解的气态产品—裂解气是一个多组分的气体混合物,包括以下:一、低级烃类,主要是甲烷、乙烯、乙烷、丙烯、丙烷与碳四、碳五、碳六等烃类,二、氢气三、少量杂质,如硫化氢和二氧化碳、水份、炔烃、一氧化碳等,基本有机原料乙烯、丙烯等,根据工业上的需要,使之达到一定的纯度。
裂解、分离、合成是有机化工生产中的三大加工过程。
(各种有机产品的合成,对于原料纯度的要求是不同的。
例如用乙烯与苯烷基化生产乙苯时,对乙烯纯度要求不太高。
生产聚乙烯、聚丙烯要求乙烯、丙烯纯度在99.9%或99.5%以上。
)二、裂解气分离方法简介裂解气的分离和提纯工艺,是以精馏分离的方法完成的。
精馏方法要求将组分冷凝为液态。
甲烷和氢气不容易液化,碳二以上的馏分相对地比较容易液化。
分离过程的主要矛盾:将裂解气中的甲烷和氢气先行分离。
工业生产上采用的裂解气分离方法,主要有深冷分离和油吸收精馏分离两种。
油吸收法:利用裂解气中各组分在某种吸收剂中的溶解度不同,用吸收剂吸收除甲烷和氢气以外的其它组分,然后用精馏的方法,把各组分从吸收剂中逐一分离。
特点:此方法流程简单,动力设备少,投资少,但技术经济指标和产品纯度差,现已被淘汰。
冷冻温度高于-50℃称为浅度冷冻(简称浅冷);而在-50~-l00℃之间称为中度冷冻;把等于或低于-100℃称为深度冷冻(简称深冷)。
表2-1 不同裂解原料得到的几种裂解气组成%(体积)深冷分离:在-100℃左右的低温下,将裂解气中除了氢和甲烷以外的其它烃类全部冷凝下来。
然后利用裂解气中各种烃类的相对挥发度不同,在合适的温度和压力下,以精馏的方法将各组分分离开来,达到分离的目的。
因为这种分离方法采用了-100℃以下的冷冻系统,故称为深度冷冻分离,简称深冷分离。
特点:它的经济技术指标先进,产品纯度高,分离效果好,但投资较大,流程复杂,动力设备较多,需要大量的耐低温合金钢。
第1章 裂解气分离

C2馏分后加氢工艺
脱乙烷塔顶 回流罐C2气
预热、注氢 一段加氢
反应气
冷却 二段加氢
反应气
冷却 C2吸收绿油
C2馏分 干燥
乙烯精馏
乙烯
后加氢工艺流程
加氢脱炔催化剂
钯系: ①温度较低 ②乙烯损失低(0· 2%~ 0· ) 5% 后 加 氢 前 加 氢
③残余乙炔低(5×10-6)
非钯系:①进料杂质含量限制不严; ②温度较高;
生产实际
一般设置两台干燥器,轮流进行干燥和再生
尝试画出流程: 提示:
两个干燥剂罐并联串联? 控制阀如何设置? 再生时如何实现温升 如何实现再生后的重新使用?
典型的两个吸附器 轮流操作的流程图
炔烃脱除
来源 裂解过程中生成 乙炔集于C2馏分 甲基乙炔和丙二 烯富集于C3馏分
危害
对产品再加工不利, 影响催化剂寿命, 恶化产品质量,形 成不安全因素,产 生副产品
前加氢与后加氢比较
前加氢
流程简化,节省投资
后加氢
工艺流程或控制复杂。 需设第二脱甲烷塔或侧 线采出塔 氢气定量供给,加氢选 择性好,温度较易控制, 不易发生飞温问题 加氢原料气中杂质少, 催化剂使用周期长,产 品纯度也高。
操作稳定性差。
氢气自给,过量,副
反应剧烈,选择性差, 造成乙烯和丙烯损失, 严重时还会导致反应温 度失控,床层飞温,威 胁生产安全。
甲烷化法:催化剂存 在的条件下,使裂解 气中的一氧化碳催化 加氢生成甲烷和水, 达到脱除CO的目的
CO脱除的方法
CO H 2 CH 4 H 2O
裂解气的深冷分离系统
脱甲烷塔 丙烯精馏
分离流程
裂解气分离

裂解气分离工业生产上采用的裂解气分离方法,主要有深冷分离法和油吸收精馏分离法两种。
本章重点介绍深冷分离方法。
裂解气分离分离原理:在基本有机化学工业中,把冷冻温度高于-50℃的称为浅度冷冻,简称“浅冷”;温度在-50~-100℃的称为中度冷冻;冷冻温度等于或低于-100℃的称为深度冷冻,简称“深冷”。
因为裂解气分离方法采用了-100℃以下的冷冻系统,所以工业上称为深冷分离法。
这种方法的分离原理就是利用裂解气中各种烃的相对挥发度不同,在低温下除了氢气和甲烷以外,把其余的烃类都冷凝下来,然后在精馏塔内进行多组分精馏分离,利用不同的精馏塔,把各种烃逐个分离下来。
其实质是冷凝精馏过程。
深冷分离流程:图1-24是深冷分离流程示意图:主要设备:1碱洗塔、2干燥塔、3脱甲烷塔、4脱乙烷塔、5乙烯塔、6脱丙烷塔、7脱丁烷塔、8丙烷塔、9冷箱、10加氢脱炔反应器、11绿油塔。
就分离过程来说,可以概括成三大部份:(1)压缩和冷冻系统:使裂解气加压降温,同时脱除重组分,为分离创造条件。
(2)气体净化系统:包括脱除酸性气体、脱水、脱除乙炔和脱除一氧化碳(即甲烷化,用于净化氢气)。
(3)精馏分离系统:包括一系列的精馏塔,以便分离出甲烷、乙烯、丙烯、C4馏分以及C5馏分。
顺序分离流程分离步骤是:①裂解气经过离心式压缩机压缩后,送入碱洗塔,脱去酸性气体。
减洗后的裂解气经过压缩机去干燥器脱水,干燥后的裂解气在前冷箱中分离出富氢气体,再进入脱甲烷塔,塔顶脱去甲烷馏分,塔底的液体是C2以上馏分,进入脱乙烷塔,进入脱乙烷塔的塔顶分出C2馏分,塔底的液体为C3以上馏分。
②从脱乙烷塔塔顶出来的C2馏分经过换热升温,进行气相加氢脱乙炔气,脱乙炔以后的气体进入绿油塔,在绿油塔内用乙烯塔来的侧线馏分洗去绿油,干燥,然后送去乙烯塔。
脱乙烯塔塔底的液体进入脱丙烯塔,在塔顶分出C3馏分,塔底的液体为C4馏分,液体里面含有二烯烃,易聚合结焦,所以脱丙烯塔塔底温度不适宜超过一百度,并且必须加入阻聚剂。
第二章 裂解反应系统

第二章裂解反应系统第二章:裂解反应系统一、裂解反应原理和工艺流程(一)裂解反应原理1、裂解的一次反应和二次反应烃类热裂解的过程非常复杂,它分为一次反应和二次反应。
一次反应是指由原料烃类经裂解生成乙烯和丙烯的反应。
二次反应主要是指一次反应生成的乙烯、丙烯等低级烯烃进一步发生反应生成多种产物,甚至最后结焦或生碳的反应。
烃类热裂解的一次反应主要是发生脱氢和断链反应。
脱氢反应是C-H键断裂的反应,生成烯烃和氢气。
如:R-CH2-CH3 R-CH=CH2+H2(烷烃裂解通式)断链反应是C-C键断裂的反应,反应产物是碳原子数少的烷烃和烯烃。
R-CH2-CH2-R’ R-CH=CH2+R’H(烷烃裂解通式)或(Cm+nH2(m+n)+2)CmH2m+CnH2n+2脱氢和断链都是吸热反应,所以裂解时必须供给大量的热。
在相同的裂解温度下,脱氢比断链所需的热量大,要加快脱氢反应必须采取更高温度。
环烷烃、芳香烃、烯烃等也均可发生一次反应(断链和脱氢),但均有各自不同的特点。
烃类热裂解过程的二次反应比一次反应复杂,原料烃一次反应后生成了氢,甲烷和一些低分子量的烯烃如乙烯、丙烯、丁烯、异丁烯、戌烯等。
在裂解温度下,氢及甲烷很稳定,而烯烃可继续反应,主要的二次反应有:①反应生成的较大分子烯烃可以继续裂解生成乙烯,丙烯等小分子烯烃或二烯径;②烯烃能够发生聚合,环化,缩合,最后直至转化成焦;③烯烃加氢和脱氢;④烃类分解生碳。
总之,在二次反应中除了较大分子的烯烃裂解能够增产乙烯外,其余的反应都要消耗乙烯,降低乙烯收率。
尤其是结焦和生碳反应,只要有结焦和生碳的条件,就能在设备表面形成固体结焦层,给正常操作带来不利影响。
因此,在裂解炉的设计过程中,均采用高温、短停留时间、低烃分压和快速急冷为设计条件,以保证目的产品。
2、自由基反应机理烃类热裂解过程甚为复杂。
据研究认为烃类热裂解是自由基型连锁反应。
在高温下,C-C键发生断链,形成非常活泼的反应基团―自由基,它很容易与其他自由基成分子发生反应,现以轻柴油中的链烷烃为例说明如下:自由基连锁反应是分三个阶段进行的: a)链引发R1H R2+R3b)链传递R2+R1H R2H+R1 R3+R1H R3H+R1 CnH2n+R4c)链终止R1+R4 生成物首先,原料烃R1H的C-C链在高温下断链生成两个游离自由基R2和R3,然后R2和R3与原料烃反应脱氢生成游离基R1,由于R1对热不稳定,所以R1分解成烯烃CnH2n和游离基R4,最后R4和R1反应生成稳定的生成物。
- 1、下载文档前请自行甄别文档内容的完整性,平台不提供额外的编辑、内容补充、找答案等附加服务。
- 2、"仅部分预览"的文档,不可在线预览部分如存在完整性等问题,可反馈申请退款(可完整预览的文档不适用该条件!)。
- 3、如文档侵犯您的权益,请联系客服反馈,我们会尽快为您处理(人工客服工作时间:9:00-18:30)。
深冷分离
深冷操作的系统组成
1、压缩冷 冻系统
该系统的任务是加压、降温,以保证分离过程 顺利进行。
2、气体净 化系统
为了排除对后继操作的干扰,提高产品的纯度, 通常设置有脱酸性气体、脱水、脱炔和脱一氧化 碳等操作过程。
3、低温精馏 分离系统
这是深冷分离的核心,其任务是将各组分进行分 离并将乙烯、丙烯产品精制提纯。它由一系列塔器 构成,如脱甲烷塔,乙烯精馏塔和丙烯精馏塔等。
单位 MPa
绝热指数=cp/cv
单位 kp 2 ( k源自1) / k T2 T1 ( ) p1
绝热过程,压力升高,温度也上升
不同压力下某些组分的沸点℃
压力 组分 H2 CH4 C2H4 C2H6 C3H6 1.103 10.13 15.19 20.26 25.23 30.39 ×105Pa ×105Pa ×105Pa ×105Pa ×105Pa ×105Pa -263 -162 -104 -86 -47.7 -244 -129 -55 -33 9 -239 -114 -39 -18 29 -238 -107 -29 -7 37 -237 -101 -20 3 44 -235 -95 -13 11 47
裂解气分离方法简介
裂解气的分离、提纯工作,是以 精馏 方法完成
的,精馏方法要求将组分冷凝为液态。
氢气常压沸点为-263 ℃、甲烷-161.5℃,很难 液化,碳二以上的馏分相对地比较容易液化 ( 乙 烯沸点-103.68 ℃ )。 因此,分离过程的 主要矛盾 是如何将裂解气中 的甲烷和氢气先行分离。
但不能任意加压,若压力增高:
对设备材料强度要求增高;
动力消耗增大;
使低温分离系统精馏塔釜温升高,易引起一些 不饱和烃(二烯烃)的聚合 使烃类相对挥发度降低,增加了分离的困难。
因此,在深冷分离中要采用经济上合理而技术上 可行的压力,一般为3.54~3.95MPa。
裂解气是复杂的混合物
裂解气分离定义:
要得到高纯度的单一的烃,如重要的基本有机原料乙烯、 丙烯等,就需要将它们与其它烃类和杂质等分离开来, 并根据工业上的需要,使之达到一定的纯度,这一操作 过程,称为裂解气的分离。
第二章 裂解气分离
主要内容
第一节:裂解气的组成与分离方法 第二节:压缩与制冷 第三节:气体净化 第四节: 裂解气深冷分离 第五节:裂解气分离操作中的异常 现象
0.76
0.18 0.09 4.36
裂解气的组成:
①、富氢(13.18%) ②、C1~C4各类烃混合物(通过相应分离流程分离) a、H2S b、CO2 脱酸性 气体
c、CO
③、含有少量杂质
脱一氧化碳, 甲烷化法:CO+3H2O
CH4+H2O
d、H2O 脱水 e、二烯烃:丙二烯(主要) f、炔烃:主要乙炔、丙炔 ④、C>4 各类烃(通过相应分离流程分离)
第二节 压缩和制冷系统
目的和任务 压力与温度的关系
多级压缩的优点
制冷剂的选择
需要大量冷量和耐低温设备
解决办法
常压,冷凝、精馏分离温度低
裂解气常压沸点很低
加压 提高组分的沸点 提高操作温度
压缩的原因
一、裂解气的压缩
1.压力与温度的关系
根据物质的冷凝温度随压力增加而升高的规律,对 裂解气加压,从而使各组分的冷凝点升高,这既有利于 分离,又可节约冷冻量和低温材料。
气态产物
裂解气(目的乙烯、丙烯)
石 油 烃
液态产物
裂解汽油 裂解轻柴油 燃料油
固态产物
焦、碳
轻柴油裂解气组成
成分 H2 CO CH4 C2H2 C2H4 C2H6 丙二烯+丙炔 C3H6 %,mol 13.1828 0.1751 21.2489 0.3688 29.0363 7.7953 0.5419 11.4757 成分 C3H8 1,3-丁二烯 异丁烯 正丁烯 C5 C6~C8非芳烃 苯 甲苯 %,mol 0.3558 2.4194 2.7085 0.0754 0.5147 0.6941 2.1398 0.9296 成分 二甲苯+乙苯 苯乙烯 C9~200℃馏分 CO2 硫化物 H2O %,mol 0.3578 0.2192 0.2397 0.0578 0.272 5.04
裂解气分离方法
用吸收剂吸收除甲烷和氢气以外的其它 组分,然后根据溶解度不同进行精馏, 把各组分从吸收剂中逐一分离。
流程简单,动力设备少,投资少,但技 术经济指标和产品纯度差,已被淘汰。
油吸收
精馏分离
在-100℃左右的低温下,将裂解气中除 氢和甲烷以外的其它烃类全部冷凝下来。 然后利用裂解气中各种烃类的相对挥发 度不同,在合适的温度和压力下,以精 馏的方法将各组分分离开来,达到分离 的目的 。
第一节 裂解气的组成与分离方法
低级烃类 裂 解 气 的 组 成 及 分 离 方 法 1.组成 一、裂解气的组 成及分离要求 氢气
少量杂质
2.分离要求
深冷分离
二、裂解气分离方法简介 深冷操作的系统组成 油吸收精馏分离
几种裂解气组成%(体积) 组分
H2 CO+CO2+H2S CH4 C2H2 C2H4 C2H6 C3H4 C3H6 C3H8 C4 C5 ≥C6 H2 O
乙烷裂解
34.0 0.19 4.39 0.19 31.51 24.35
原料来源 石脑油裂解 轻柴油裂解
14.09 0.32 26.78 0.41 26.10 5.78 0.48 10.30 0.34 4.85 1.04 4.53 4.98 13.18 0.27 21.24 0.37 29.34 7.58 0.54 11.42 0.36 5.21 0.51 4.58 5.40
分离要求
各种有机产品的合成,对于原料纯度的要求是不同的。 所以分离的程度可根据后续产品合成的要求来确定。
有的产品对原料纯度要求不高,例如用 乙烯与苯烷基化生产乙苯时,对乙烯纯 对于聚合用的乙烯和丙烯的质量要求则很 严,生产聚乙烯、聚丙烯要求乙烯、丙烯 度要求不太高,则可以分离纯度低一些, 纯度在 99.9%或99.5%以上,其中有机杂质 用丙烯与苯烷基化生产异丙苯时,甚至 不允许超过 5 10PPm。这就要求对裂解气 可以用丙烯 -~ 丙烷混合馏分。 进行精细的分离和提纯。