起重机通用油漆施工工艺
起重机防腐油漆施工方案及流程
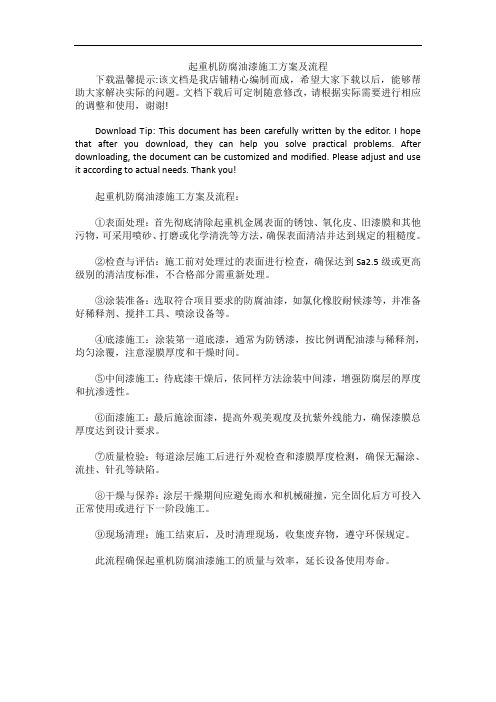
起重机防腐油漆施工方案及流程下载温馨提示:该文档是我店铺精心编制而成,希望大家下载以后,能够帮助大家解决实际的问题。
文档下载后可定制随意修改,请根据实际需要进行相应的调整和使用,谢谢!Download Tip: This document has been carefully written by the editor. I hope that after you download, they can help you solve practical problems. After downloading, the document can be customized and modified. Please adjust and use it according to actual needs. Thank you!起重机防腐油漆施工方案及流程:①表面处理:首先彻底清除起重机金属表面的锈蚀、氧化皮、旧漆膜和其他污物,可采用喷砂、打磨或化学清洗等方法,确保表面清洁并达到规定的粗糙度。
②检查与评估:施工前对处理过的表面进行检查,确保达到Sa2.5级或更高级别的清洁度标准,不合格部分需重新处理。
③涂装准备:选取符合项目要求的防腐油漆,如氯化橡胶耐候漆等,并准备好稀释剂、搅拌工具、喷涂设备等。
④底漆施工:涂装第一道底漆,通常为防锈漆,按比例调配油漆与稀释剂,均匀涂覆,注意湿膜厚度和干燥时间。
⑤中间漆施工:待底漆干燥后,依同样方法涂装中间漆,增强防腐层的厚度和抗渗透性。
⑥面漆施工:最后施涂面漆,提高外观美观度及抗紫外线能力,确保漆膜总厚度达到设计要求。
⑦质量检验:每道涂层施工后进行外观检查和漆膜厚度检测,确保无漏涂、流挂、针孔等缺陷。
⑧干燥与保养:涂层干燥期间应避免雨水和机械碰撞,完全固化后方可投入正常使用或进行下一阶段施工。
⑨现场清理:施工结束后,及时清理现场,收集废弃物,遵守环保规定。
此流程确保起重机防腐油漆施工的质量与效率,延长设备使用寿命。
吊车外墙涂料施工方案(精选9篇)
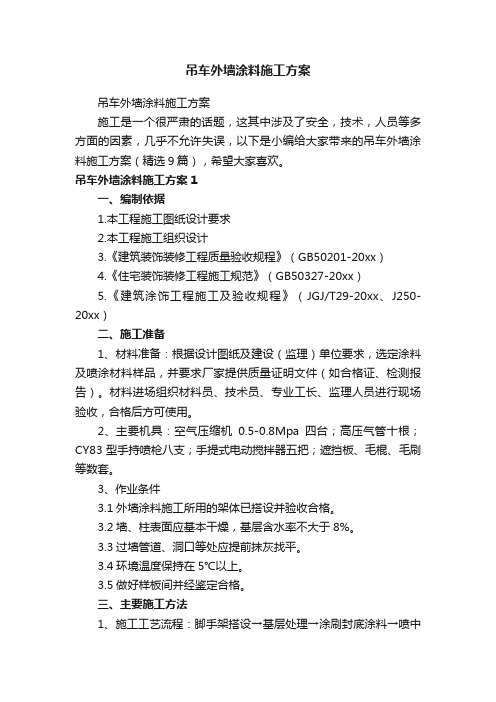
吊车外墙涂料施工方案吊车外墙涂料施工方案施工是一个很严肃的话题,这其中涉及了安全,技术,人员等多方面的因素,几乎不允许失误,以下是小编给大家带来的吊车外墙涂料施工方案(精选9篇),希望大家喜欢。
吊车外墙涂料施工方案1一、编制依据1.本工程施工图纸设计要求2.本工程施工组织设计3.《建筑装饰装修工程质量验收规程》(GB50201-20xx)4.《住宅装饰装修工程施工规范》(GB50327-20xx)5.《建筑涂饰工程施工及验收规程》(JGJ/T29-20xx、J250-20xx)二、施工准备1、材料准备:根据设计图纸及建设(监理)单位要求,选定涂料及喷涂材料样品,并要求厂家提供质量证明文件(如合格证、检测报告)。
材料进场组织材料员、技术员、专业工长、监理人员进行现场验收,合格后方可使用。
2、主要机具:空气压缩机0.5-0.8Mpa四台;高压气管十根;CY83型手持喷枪八支;手提式电动搅拌器五把;遮挡板、毛棍、毛刷等数套。
3、作业条件3.1外墙涂料施工所用的架体已搭设并验收合格。
3.2墙、柱表面应基本干燥,基层含水率不大于8%。
3.3过墙管道、洞口等处应提前抹灰找平。
3.4环境温度保持在5℃以上。
3.5做好样板间并经鉴定合格。
三、主要施工方法1、施工工艺流程:脚手架搭设→基层处理→涂刷封底涂料→喷中涂→喷面涂→验收合格→脚手架拆除2、脚手架搭设本工程涂料施工外架采用双排落地脚手架,其搭设要求如下:2.1地基处理与底座安装A、回填土地基应分层夯填密实,密实度达到要求;B、地基表面采用C20素砼浇筑平整,外架底座边设置排水明沟;C、脚手架立杆和排距要求进行放线和定位;D、立杆垫板采用木枋,垫板铺放应平整,且不得悬空。
2.2杆件搭设A、脚手架搭设顺序放置纵向扫地杆→立杆→横向扫地杆→第一步横向水平杆→第一步纵向水平杆→栏杆→连墙杆→第二步横向水平杆→第二步纵向水平杆→栏杆→······B、立杆搭设注意事项相临立杆的对接扣件不得设在同一步距内,错开距离应符合要求。
起重机防腐油漆施工方案及流程
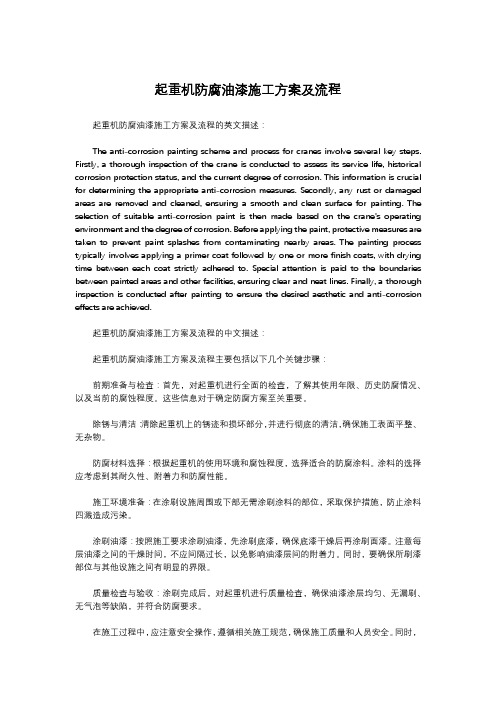
起重机防腐油漆施工方案及流程起重机防腐油漆施工方案及流程的英文描述:The anti-corrosion painting scheme and process for cranes involve several key steps. Firstly, a thorough inspection of the crane is conducted to assess its service life, historical corrosion protection status, and the current degree of corrosion. This information is crucial for determining the appropriate anti-corrosion measures. Secondly, any rust or damaged areas are removed and cleaned, ensuring a smooth and clean surface for painting. The selection of suitable anti-corrosion paint is then made based on the crane's operating environment and the degree of corrosion. Before applying the paint, protective measures are taken to prevent paint splashes from contaminating nearby areas. The painting process typically involves applying a primer coat followed by one or more finish coats, with drying time between each coat strictly adhered to. Special attention is paid to the boundaries between painted areas and other facilities, ensuring clear and neat lines. Finally, a thorough inspection is conducted after painting to ensure the desired aesthetic and anti-corrosion effects are achieved.起重机防腐油漆施工方案及流程的中文描述:起重机防腐油漆施工方案及流程主要包括以下几个关键步骤:前期准备与检查:首先,对起重机进行全面的检查,了解其使用年限、历史防腐情况、以及当前的腐蚀程度。
桥门式起重机通用涂漆工艺规程(18)
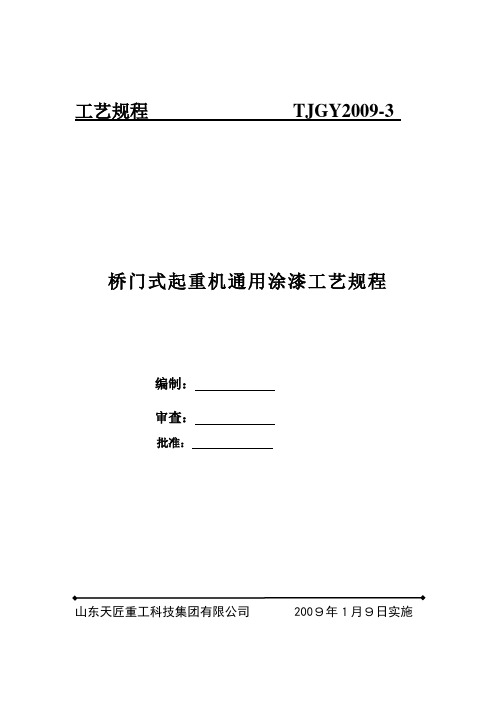
工艺规程TJGY2009-3桥门式起重机通用涂漆工艺规程编制:审查:批准:山东天匠重工科技集团有限公司2009年1月9日实施目录1、除锈 (1)2、涂漆 (1)3、涂漆质量检查 (2)4、表面质量 (4)1、除锈1.1除锈前钢板有水份、油污、灰尘时,应用压缩空气、洗涤剂吹干或脱脂。
1.2表面除锈:见表1 表12、涂漆2.1涂漆施工温度:见表2 表22.2涂漆种类选择见表3 表32.3不涂装部位:铭牌、机械加工配合面、制动轮圆柱表面、齿轮接手,涂漆前应涂上润滑脂或用塑料包扎。
2.4底漆应在金属结构件除锈检验合格后24小时之内涂上。
2.5涂漆应按如下顺序进行:先涂底漆,再涂中间漆。
每次涂漆应在前一涂层干燥后进行。
一般涂漆间隔时间见如下表:(即表4)表4 间隔时间单位:小时2.6涂漆道数、厚度、工作粘度(涂4#杯测,25℃)见表5表53、涂漆质量检查3.1涂漆外观质量检查见表6。
3.2漆厚度部位检查:3.2.1一般每涂完一道油漆后检查漆膜厚度,测量时,主梁、端梁各10处。
见表73.2.2测量仪器:用两点式微磁厚度仪及其基准试片。
表6表73.3漆膜附着力检查:用专用刀在漆膜上划六条互相垂直间距为2mm的直线,如图1所示,刀痕要划到钢板上。
操作时,切割刀应垂直于切割平面。
用力均匀,以25~50mm/秒速度切割,然后用软毛刷沿着方格图形的对角线轻轻地向后刷5次,向前刷5次。
如在切口交叉处涂层有少许薄片分离。
划格区受影响明显地不大于5%,即为合格,超过为不合格。
图14、表面质量4.1油漆漆膜厚度要求:底漆一道,厚度≥25μm;面漆涂2道,漆膜厚度≥50μm;漆膜总后度应≥75μm。
4.2漆膜附着力技术要求:按ISO 2409《色漆和清漆一划格试验》中一级质量要求并按ISO 2409划格试验方法,在主梁、端梁上各取10处进行测试其等级评定方法。
见图1操作方法:(1)用专用切刀和钢尺在漆膜上切割格子图形。
(2)切割条数在格子图形的一边上为6条。
起重机金属结构件除锈油漆工艺守则
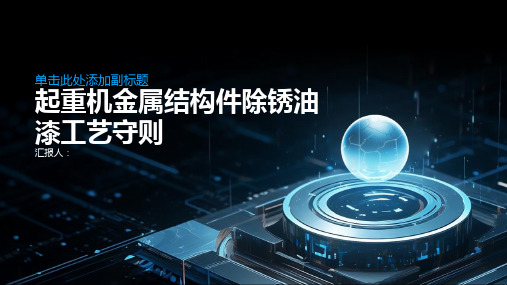
废水处理:对废水进行净化 处理,减少对环境的影响
噪声控制:采用低噪声设备 和技术,减少噪声对环境的
影响
资源回收利用:对废旧金属 结构件进行回收利用,减少
资源浪费
感谢观看
汇报人:
金属结构件涂漆质量检查
金属结构件验收程序
07
安全与环保要求
操作过程中的安全防护措施
佩戴个人防护装备:操作人员必须佩戴合适的个人防护装备,如防护眼镜、防护 手套、防护鞋等,以防止油漆溅入眼睛或接触皮肤。
保持通风良好:在操作过程中,应保持工作场所通风良好,以减少有害气体和粉 尘的浓度。
禁止吸烟和明火:在工作场所禁止吸烟和任何形式的明火,以防止火灾和爆炸事 故。
检查油漆涂装是否达到规 定厚度和标准
检查固化效果
表面硬度:检查金属结构件表 面是否达到规定硬度
附着力:检查油漆是否牢固附 着在金属表面
外观质量:检查金属结构件表 面是否平整、光滑、无气泡、 无裂纹等
尺寸精度:检查金属结构件尺 寸是否符合设计要求
验收标准与程序
金属结构件表面质量检查
金属结构件尺寸精度检查
定期检查和维护设备:定期检查和维护油漆设备,确保其正常运转,防止因设备 故障而导致的事故。
遵守安全操作规程:操作人员必须遵守安全操作规程,按照规定的步骤进行操作, 避免因操作不当而导致的事故。
废气、废水、废渣的处理要求
添加 标题
废气处理:应采取有效的措施,减少废气排放,如使用低挥发性有机化合物、加强通风等。
加热干燥
加热方式:采用红外线、电热、蒸汽等加热方式 加热温度:根据油漆类型和干燥时间确定 加热时间:根据油漆的干燥性能和厚度确定 注意事项:避免过度加热导致油漆起泡或变形
起重机现场涂装方案

起重机现场防腐油漆施工方案吊车外表生锈、腐蚀严重,油漆脱落,现根据现场情况及业主建议,提出施工方案:一、起重机大车走台平面及小车平面机械除锈(除锈等级中级),对局部地方进行补漆,刷红丹环氧防锈底漆两遍,高级氟碳面漆两遍。
二、起重机大车走台小车平台的侧面及底部机械除锈(除锈等级中级),对局部地方进行补漆,对刷红丹环氧防锈底漆两遍,高级氟碳面漆两遍。
三、轨道底部铁板,刷沥青漆一底一面,轨道机械除锈等级中级,刷沥青漆一底一面。
四、除锈方法:电动工具除锈,除锈等级为S t2级。
金属面标准:氧化皮部分破裂脱落,是堆粉状,除锈后肉眼可以见到腐蚀小凹点。
金属除锈质量标准:完全除去金属表面的油脂,疏松氧化皮,浮锈等杂物,紧附的氧化皮点蚀锈坑或旧漆等斑点残留物的面积在任何100㎜×100㎜的面积上不得超过1/3。
五、涂料要求:1、底漆采用环氧防锈底漆,面漆采用高级氟碳面漆。
(附氟碳漆的性能)氟碳漆是由氟碳树脂为主要成分的A、B双组分油漆,它具有以下特点:(1)超强耐候性、防腐蚀性、强自洁性。
(2)强附著性、高装饰性、防水、防老化、耐酸、耐碱。
(3)良好的柔韧性、抗划伤性、耐洗刷性。
(4)优异的耐褪色、不开裂、耐粉化、耐磨损性能等其它普通防腐油漆所不能达到的特性。
2、涂料的品种、性能、颜色、涂刷层数及表面标记等应符合设计规定,涂料应有生产厂家的合格证书。
3、涂料的耐温性能,抗腐性能应按输热介说度及环境条件进行选择。
按涂料工艺要求稀释至适当温度,搅拌均匀,色调一致,及时使用,涂料应密封保存,自然。
4、干燥的现场涂漆应防止漆膜油漆污物和损坏,漆膜为干燥固化剂不得由下道工序施工。
六、涂漆质量应符合以下要求:1、与基础面黏结牢固,厚度符合要求,面层色调一致,光亮清洁,无皱纹、无气泡。
2、漆膜均匀,完整无漏涂,无损坏。
七、设备维护保养:1、对设备的电缆表面进行擦洗除污,检查是否有破损。
2、对钢丝绳、减速机、卷扬机和电机进行清洁保养并进行上油处理。
起重机规程:06起重机涂装工艺规程
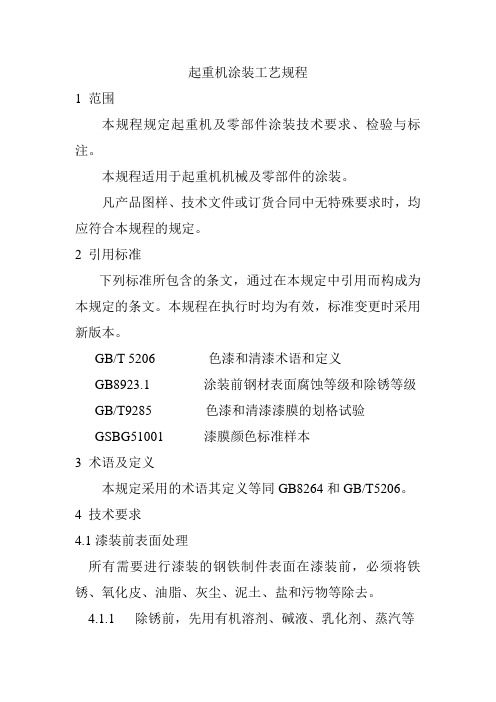
起重机涂装工艺规程1 范围本规程规定起重机及零部件涂装技术要求、检验与标注。
本规程适用于起重机机械及零部件的涂装。
凡产品图样、技术文件或订货合同中无特殊要求时,均应符合本规程的规定。
2 引用标准下列标准所包含的条文,通过在本规定中引用而构成为本规定的条文。
本规程在执行时均为有效,标准变更时采用新版本。
GB/T 5206 色漆和清漆术语和定义GB8923.1 涂装前钢材表面腐蚀等级和除锈等级GB/T9285 色漆和清漆漆膜的划格试验GSBG51001 漆膜颜色标准样本3 术语及定义本规定采用的术语其定义等同GB8264和GB/T5206。
4 技术要求4.1漆装前表面处理所有需要进行漆装的钢铁制件表面在漆装前,必须将铁锈、氧化皮、油脂、灰尘、泥土、盐和污物等除去。
4.1.1 除锈前,先用有机溶剂、碱液、乳化剂、蒸汽等除去钢铁制件表面的抽脂、污垢。
4.1.2 钢铁制件表面的除锈方法、等级及适用范围见JB/T5000.12---2007表1。
4.1.3 若焊接结构件成型后需要热处理,则除锈工序应放在热处理工序之后进行。
4.1.4 除锈的待涂表面与涂底漆的间隔时间不得多于6h。
酸洗除锈后立即经磷化处理的待涂表面与涂底漆的间隔时间不得少于48h(冬季寒冷不得少于72h)。
涂漆前表面均不得有返锈或污染。
4.1.5 用于制造结构件的钢铁板材及型材(壁厚大于5mm),应预先进行除锈。
除锈等级Sa21/2级,并立即涂保养底漆即进行制造前的表面预处理。
涂料技术要求见JB/T5000.12---2007附录A中表A6。
推荐厚度范围15~30um,推荐涂料品种:无机硅酸锌底漆、环氧富锌底漆、磷化底漆、铁红环氧脂底漆。
4.2 涂层设计要求4.2.1 各种涂装类别、产品使用环境、适用产品及部件范围、推荐涂层厚度及涂料品种JB/T5000.12---2007表2。
4.2.2 产品中一些特殊部位及部件的涂装技术要求。
4.2.2.1 铆接件相互接触的表面,在连接前必须涂厚度30~40um防锈漆,所用涂料见JB/5000.12---2007表2中A、B类底漆的规定。
工程吊车涂料施工方案模板

工程吊车涂料施工方案模板项目名称:XX工程吊车涂料施工项目地点:XX地区1. 项目概况1.1 项目背景和意义工程吊车作为一种重要的施工机械,在建筑、桥梁、码头等工程项目中起着重要的作用。
工程吊车的外观涂料不仅可以美化外观,还可以起到防腐、防锈、防腐蚀的作用。
因此,对工程吊车的涂料施工非常重要。
本次施工的项目为XX工程吊车的涂料施工,旨在提高工程吊车的外观质量,延长使用寿命,降低后期维护成本。
1.2 项目施工内容本次涂料施工将涉及以下内容:1) 工程吊车的外观清理和表面处理;2) 工程吊车的底漆施工;3) 工程吊车的面漆施工;2. 施工准备工作2.1 施工材料的准备施工所需材料包括外墙清洁剂、底漆、面漆等。
2.2 施工设备的准备施工所需设备包括清洗设备、喷涂设备、干燥设备等。
2.3 施工人员的准备施工所需人员包括清洁人员、涂料施工人员、质检人员等。
3. 施工流程3.1 工程吊车的外观清理和表面处理首先,对工程吊车的外墙进行清洁处理,使用外墙清洁剂配合高压水枪清洗吊车表面,去除污垢、油渍等杂质。
清洁完毕后,对表面进行打磨处理,以增加底漆的附着力。
3.2 工程吊车的底漆施工清洁和打磨完毕后,进行底漆施工。
根据底漆的特性,选择适当的喷涂设备,对工程吊车进行底漆施工。
施工完成后,进行干燥处理,保证底漆的固化。
3.3 工程吊车的面漆施工底漆固化后,进行面漆施工。
根据面漆的特性,选择适当的喷涂设备,对工程吊车进行面漆施工。
施工完成后,进行干燥处理,保证面漆的固化。
根据需要,可以进行第二次面漆施工,以确保涂层的均匀度和质量。
4. 质量验收标准4.1 外观质量涂料施工完成后,应保证工程吊车的外观光洁度,涂层应均匀、无明显瑕疵。
4.2 涂层厚度根据涂料的要求,应保证涂层的厚度在合理范围内。
4.3 耐磨性和耐候性施工完成后,应进行耐磨性和耐候性测试,确保涂料的质量符合要求。
5. 安全措施5.1 涂料施工中,施工人员应使用防护装备,避免涂料对人体的伤害。
CMP油漆施工说明

青岛武船重工有限公司600吨龙门吊CMP油漆涂装施工说明制造厂商:通州市新宇钢结构有限公司上海豪力起重机械有限公司油漆厂商:中涂化工(上海)有限公司2008年12月1概要1.1对青岛武船重工有限公司600吨龙门起重机防腐涂装,采用防腐性能优异、耐海洋性气候、性能可靠的世界一流涂料产品――CMP油漆,在按《涂装工艺规程》及本施工说明施工的前提下,本涂层系统的耐久性(防腐寿命)能满足业主提出的15年以上的要求。
1.2本说明适用600吨龙门起重机主梁、钢性腿、柔性腿等结构件及配套制造的上下小车、维修起重机及车行走机构等部位的涂装工作。
1.3在施工时应严格执行本说明及产品使用说明书的有关规定,接受产品服务工程师的现场指导。
2各道涂层工艺及技术参数2.1钢材预处理:未使用CMP油漆。
2.2主构件等外部表面(1034+6135H+6135H+5525)(1)EPICON ZINC RICH PRIMER B-2环氧富锌底漆1034一道a.干膜厚度:50μm 稀释剂:EPICON THINNER 参考稀释比例:10—25%(体积比)b.混合比:主剂:固化剂=70:30(体积比),主剂和固化剂应以指定比例进行混合并确保状态均匀。
由于混合不好会减弱它的干燥特性,所以混合应采用气动混合机或具有类似功能的机器进行。
c.在喷涂时,应加入稀释剂稀释,但不能超过指定的量。
d.在应用前涂料需经过足够长时间的熟化,熟化不充足会引起漆霜。
e.混合适用期:5℃以下参考5℃数据 5℃ 72小时 10℃ 60小时 20℃ 48小时 30℃ 24小时。
注意:超过混合使用期的油漆不得使用。
f.施工条件:温度一般不低于5℃;相对湿度最大85%,钢板温度大于露点温度3℃以上;无气喷涂;枪嘴Graco719;漆压84-112公斤/平方厘米;粘度9-13秒(福特杯4号)。
(2)UMEGUARD SX改性环氧漆6135H二道a.干膜厚度:80+80/75+75μm 稀释剂:EPICON THINNER 稀释比例:0—5%(体积比)b.混合比:主剂:固化剂=85:15(体积比)主剂和固化剂应以指定比例进行混合并确保状态均匀。
起重机的油漆选择及表面处理

起重机的油漆选择及表面处理起重机所采用的油漆和油漆方法,应适用使用地区气候环境条件,油漆及涂装工艺应符合所认可的标准和规范。
油漆前应对需涂漆的部位表面进行清洁、除锈处理。
油漆涂装应在气温10-32℃范围内进行,但也考虑油漆制造商的油漆使用规范。
涂装场地应通风良好,遇到潮湿、尘土飞扬或烈日爆晒等情况应采取措施,否则应停止涂装工作。
油漆全部采用无气压力喷涂设备,油膜厚度采用公制的干膜厚度计来测量。
油漆使用前进行搅拌,直到油漆全部成份完全混合。
如油漆成份有快速沉淀倾向时,经常搅动。
当同一种颜色连续涂装时,分层进行,每一层都有足够的对比度,以便鉴定是否全部覆盖。
摩擦型联结表面进行喷砂处理,以确保结合面有足够的摩擦系数。
承重型联结面或普通螺栓的联结面允许涂漆,其他联结的接合面可不涂漆,但要有防锈措施。
机加工表面在检验后,装运前或放到露天堆场前涂一层防锈油。
卖方应负责对在运输和安装中碰掉的漆膜进行现场补漆,补漆的层数不能减少,运往现场的油漆,溶剂和添加剂应采用同一制造厂产品,并带有铭牌的原包装。
起重机涂装的寿命要求不小于5年。
即在产品验收后不得出现锈斑、剥落、分化或其他缺陷。
涂色方案在技术审查时,由卖方制定,买方认可。
所有油漆品牌,由买方确定。
车轮轮辐涂红色、轮缘涂白色、轨道和压板涂黑色。
表面处理------钢材涂漆前采用喷丸处理,达到瑞典SIS标准的Sa2.5标准。
底漆-------涂环氧富锌底漆,其固体含量按重量计不少于80%;按体积计最少为50%。
中间漆-------中间漆采用环氧云铁底漆,其固体含量以体积计不少于50%。
面漆------采用聚氨脂固化丙烯聚氨脂面漆,固体含量以体积计不少于60%。
油漆、涂层数、干膜厚度按下表要求执行:部位涂层涂料名称道数涂层厚度(um)钢材预涂底漆环氧富锌底漆1 25外表面底漆环氧富锌底漆1 70中间漆环氧云铁底漆1 100面漆聚氨基甲酸酯可复涂面漆2 80(每层40)外部结构的最小干膜总厚度250内表面底漆环氧富锌底漆1 70中间漆环氧云铁底漆1 100面漆聚氨基甲酸酯可复涂面漆1 50内部结构的最小干膜总厚度220封闭的箱型结构内表面涂二层底漆。
起重机通用油漆施工工艺

1 目的为了达到油漆涂装的防腐效果及外表的美观,中途油漆建议在油漆施工中应严格按照以下要求进行操作。
2 范围本标准规定了喷丸件、涂漆件的质量要求与检验方法。
本标准适用于甲板机械、船用起重机、铸件毛坯的防护、装饰用途漆膜层的质量检验。
3总则油漆施工是一个非常重要的步骤,在油漆选定的情况下,油漆的质量是要靠施工工艺来实现的。
在本施工工艺中,将从一下几个方面给出控制原则:3.1表面处理要求3.2油漆的涂装方法及预涂装3.3施工质量控制3.4施工环境控制3.5油漆的储存使用(详见相关施工指导)3.6质量记录3.7不合格处置3.8安全方面详细工艺如下3.1 表面处理要求3.1.1 喷丸前检查3.1.1 喷丸前采用温水加清洁剂(3%~5%),使用高压清洗枪喷洗工件表面因转运、探伤等原因形成的油污、脏物;干燥后才能进行喷丸。
3.1.2 目测工件表面不允许有油脂、污垢、裂缝、焊瘤、蚀坑等缺陷,允许有铁锈、机械杂质。
3.1.3 冷焊件喷丸前钢板原始锈蚀等级不超过GB/T 8923规定的锈蚀等级B级要求。
3.1.4检查工件的孔、机加面、螺孔等应保护的部位是否根据要求进行保护。
3.1.5 表面预处理a)进行抛丸处理前,须进行底材表面预处理,即将表面的污染物如油污,油脂及其它处理干净。
b)抛丸处理前需要对一下部位用电动工具进行打磨处理:I. 底材表面的钻孔边缘、气割面及其边缘II.焊缝突起的部分、焊渣以及飞溅的焊点这些部位应处理到表面平整,或有一定坡度的起伏表面,以保证油漆能以较均匀的漆膜覆盖钢铁表面。
c)钢材的边角及边缘钢材的边角及边缘,由于这些部位较尖,在喷涂时不能达到设计的漆膜厚度,因此这些部位必须用电动工具打磨成圆角(r =2cm)。
d)要进行防腐涂装的表面,必须用喷砂或抛丸的处理的方法对底材进行处理至ISO8501-1:1988 Sa 2.5级。
其文字表达即为:达到非常彻底的喷砂除锈处理。
在不放大的情况下进行观察时,表面应无可见的油脂、污物、附着不牢的氧化皮、铁锈、旧油漆及其它杂质。
起重机金属结构件除锈油漆工艺守则
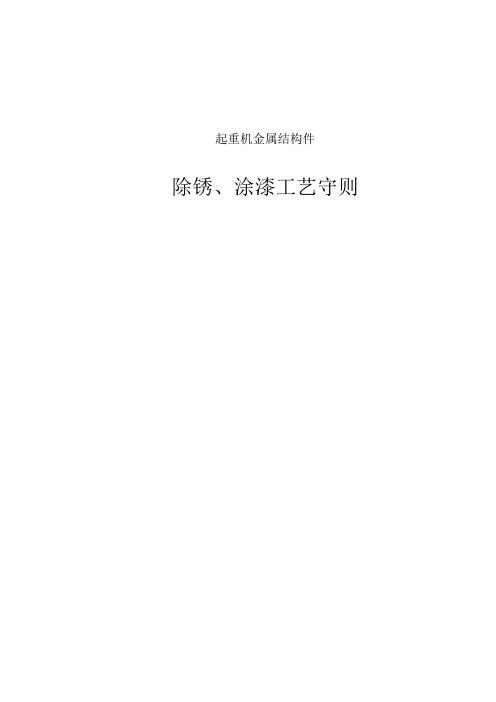
起重机金属结构件除锈、涂漆工艺守则目录一、总贝IJ (2)二、除锈,清理表面 (3)三、涂底漆 (3)四、涂刮腻子 (4)五、涂表面漆 (4)六、涂漆方法 (5)七、涂防化学过氯乙烯漆 (7)八、施工安全要求 (7)九、拆车和零件箱的包装 (7)十、本厂起重机常用的油漆种类 (8)十一、典型件涂底漆要求 (9)十二、起重机涂漆典型工艺过程 (10)一、总则(-)本工艺守则适用于各类起重机产品,对除锈涂漆无特殊要求的其他产品,也可按本守则进行。
(二)油漆颜色按部颁标准Jp2279—78标准执行。
涂漆技术,施工要求等按本厂Q/DQ110—74及Q/DQ111-74{援外}标准执行。
二、除锈、清理表面1、除锈前要做好一切准备工作,如工具,防护用具的准备工作,设备检查,并将加工表面,轴孔及接手,走轮,瓦盖等部件上的间隙,都用胶皮和挡板堵塞当好后,进行除锈。
2、除锈①清除铁锈,氧化皮,污泥,焊渣等(允许抛丸时难以除净地方有残存的少量氧化铁皮)并将残存的少量氧化皮手工除掉。
②机械除锈的喷丸咀,直径采用8mm,使用中不得超过12mm,超过时应换新的。
③除锈后的金属表面应仔细用压缩空气吹净。
3、去除旧漆①当旧漆膜全部变色,整个表面起皱纹,老化,下层漆膜脱落和肉眼可见的漆面裂纹,起泡及出现锈斑等缺陷时,根据具体情况将旧漆全部或局部清除。
允许存在漆层坚固,附着力较好的旧漆。
②使用手工镶去旧漆时,镯后须用钢丝刷刷净,在用砂布打去表面旧漆毛刺,也可以采用机械除锈方法去除旧漆。
③用压缩空气将表面清理干净。
三、涂底漆(刷涂、浸漆、喷涂)1、除锈工作完成后,清理干净金属表面,应及时涂上底漆。
2、涂底漆的金属表面必须干燥,不能有水分,露霜,潮气层存在。
3、涂底漆应在清洁、干燥的地方进行,环境温度最低不得低于5C,相对湿度应低于70-80%,在室外施工时,禁止在烈日、下雨和雾、风沙时喷(刷)漆。
4、根据产品技术要求涂一遍底漆,如需涂二遍底漆的产品必须待第一遍底漆干燥后方可进行,一般干燥时间在温度18°C~23°C时为24~48小时。
起重运输机械产品涂漆标准

起重运输机械产品涂漆标准
起重运输机械产品的涂漆标准主要包括以下几个方面:
1. 涂层材料选择:涂层材料应选择符合机械产品所在工作环境的要求,具有良好的防腐、抗氧化、耐磨等性能,并且符合相关国家或地区的环保要求。
2. 表面预处理:在涂装之前,需要对产品表面进行一系列的预处理工艺,如除锈、除油、除尘等,以保证涂层的附着力和持久性。
3. 涂装工艺:涂装工艺包括底漆和面漆的施工,底漆主要用于增强涂层的附着力和防锈效果,面漆主要用于增加产品的美观度和耐候性。
涂料的涂布应均匀、无麻点、无杂质等缺陷。
4. 涂层厚度:涂装时需要控制好涂层的厚度,以保证产品的防腐蚀性能和美观度。
涂层的厚度应符合相关的国家或地区标准。
5. 涂层质量检验:涂层施工完毕后需要进行质量检验,检查涂层的附着力、耐腐蚀性、耐磨性等性能是否符合相关的标准要求。
总之,起重运输机械产品的涂漆标准主要包括涂料材料的选择、表面预处理、涂装工艺、涂层厚度和质量检验等方面,以确保涂层能够满足产品在使用过程中的要求。
起重运输机械产品涂漆标准

起重运输机械产品涂漆标准
起重运输机械产品涂漆标准根据具体的国家或地区的法规和标准可能会有所不同,一般包括以下方面:
1. 表面处理:在涂漆之前,必须对机械产品的表面进行适当的处理,去除污垢、油脂和杂质,并确保表面平整和光滑。
2. 涂料选择:选择合适的涂料,根据机械产品的使用环境、耐磨性、防腐性和美观性等要求来确定。
3. 涂布方法:选取适当的涂布方法,可以是喷涂、滚涂或刷涂等,确保涂料均匀覆盖整个机械产品的表面。
4. 涂布层数:根据涂料的种类和要求,确定适当的涂布层数,以保证涂层的厚度和质量。
5. 干燥和固化:在涂漆完成后,要进行适当的干燥和固化过程,以确保涂层具有足够的硬度和耐久性。
6. 防腐保护:对于起重运输机械产品,防腐保护是非常重要的,涂漆标准要求涂层具有良好的防腐性能,能够有效地防止机械产品受到腐蚀。
7. 检测和验收:对于涂漆的机械产品,需要进行严格的检测和验收,确保涂层符合标准要求,没有质量问题。
以上是一般涂漆标准的一些要点,具体的起重运输机械产品涂漆标准还需要参考当地的法规和标准进行详细的规定和操作。
塔吊翻新喷漆方案及流程
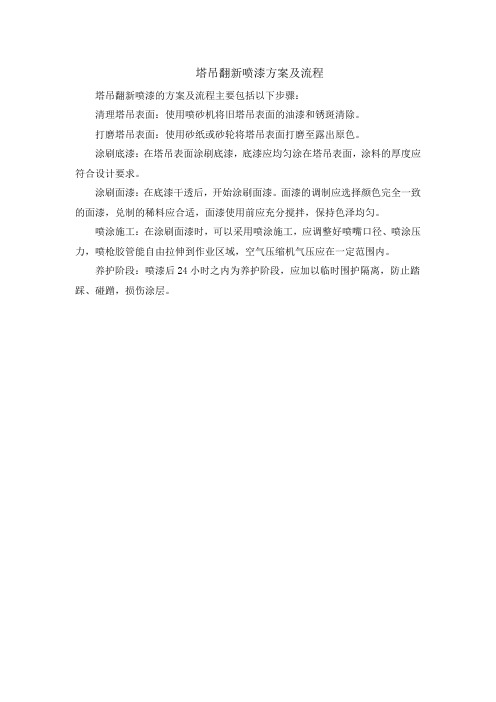
塔吊翻新喷漆方案及流程
塔吊翻新喷漆的方案及流程主要包括以下步骤:
清理塔吊表面:使用喷砂机将旧塔吊表面的油漆和锈斑清除。
打磨塔吊表面:使用砂纸或砂轮将塔吊表面打磨至露出原色。
涂刷底漆:在塔吊表面涂刷底漆,底漆应均匀涂在塔吊表面,涂料的厚度应符合设计要求。
涂刷面漆:在底漆干透后,开始涂刷面漆。
面漆的调制应选择颜色完全一致的面漆,兑制的稀料应合适,面漆使用前应充分搅拌,保持色泽均匀。
喷涂施工:在涂刷面漆时,可以采用喷涂施工,应调整好喷嘴口径、喷涂压力,喷枪胶管能自由拉伸到作业区域,空气压缩机气压应在一定范围内。
养护阶段:喷漆后24小时之内为养护阶段,应加以临时围护隔离,防止踏踩、碰蹭,损伤涂层。
起重机公司涂装工艺指导书2021

起重机公司涂装工艺指导书2021涂装作业指导书1.目的规范涂装工艺参数和作业要求,确保涂装产品质量符合要求。
2.适用范围适用于公司涂装产品的生产和检验作业。
3.使用设备喷漆枪及相关检测设备4.工艺要求4.1工艺参数4.1.1调漆单组份油漆:红面漆与稀释剂的重量比例为1:0.25,粘度为20~30S黄面漆与稀释剂的重量比例为1:0.2,粘度为20~30S铁锈红底漆与稀释剂的重量比例为1:0.25,粘度为20~30S双组份油漆:黄面漆、固化剂与稀释剂的重量比例为4:1:1,粘度为20~30S4.1.单组份油漆:一般零部件,底漆两遍,每遍时间间隔为1~1.5小时,头遍漆膜厚度为18±5μm,总漆膜厚度为30±5μm,面漆两遍,每遍时间间隔为2~2.5小时,总漆膜厚度为≥60μm(包括底漆)每批调好漆的油漆应当在当天用完,确实用不完的必须密闭保存。
双组份油漆:一般零部件,底漆两遍,每遍时间间隔为1~1.5小时,头遍漆膜厚度为18±5μm,总漆膜厚度为30±5μm,面漆两遍,每遍时间间隔为2~2.5小时,总漆膜厚度为≥60μm(包括底漆)根据零部件的多少调制相当数量的油漆,调制好的油漆当时必须用完。
4.1.3喷涂气压空气压力应为0.48~0.62Mpa4.2 作业流程4.2.1一般零部件先喷涂底漆两遍,再喷涂面漆两遍。
单组份油漆每批调好漆的油漆应当在当天用完,确实用不完的必须密闭保存,双组份油漆根据零部件的多少调制相当数量的油漆,调制好的油漆当时必须用完。
4.2.2作业环境应清洁、干燥、空气流通,光线充足。
第一遍底漆。
先试喷使雾化效果达到最佳,尖角、棱角边缘等难以保证漆膜厚度的部位应先喷涂一遍,然后再进行整体涂装,操作时应遵循从里到外、从上到下,从边角到大面的顺序,为使喷涂均匀,每枪应迭压前一枪的1/3-2/3,运枪速度应均匀一致,不可时快时慢,喷涂要均匀,无漏涂、无流挂、起泡粗粒等缺陷,喷涂时起枪收枪应在工件之外。
起重机现场涂装方案

起重机现场防腐油漆施工方案吊车外表生锈、腐蚀严重,油漆脱落,现根据现场情况及业主建议,提出施工方案:一、起重机大车走台平面及小车平面机械除锈(除锈等级中级),对局部地方进行补漆,刷红丹环氧防锈底漆两遍,高级氟碳面漆两遍。
二、起重机大车走台小车平台的侧面及底部机械除锈(除锈等级中级),对局部地方进行补漆,对刷红丹环氧防锈底漆两遍,高级氟碳面漆两遍。
三、轨道底部铁板,刷沥青漆一底一面,轨道机械除锈等级中级,刷沥青漆一底一面。
四、除锈方法:电动工具除锈,除锈等级为S t2级。
金属面标准:氧化皮部分破裂脱落,是堆粉状,除锈后肉眼可以见到腐蚀小凹点。
金属除锈质量标准:完全除去金属表面的油脂,疏松氧化皮,浮锈等杂物,紧附的氧化皮点蚀锈坑或旧漆等斑点残留物的面积在任何100㎜×100㎜的面积上不得超过1/3。
五、涂料要求:1、底漆采用环氧防锈底漆,面漆采用高级氟碳面漆。
(附氟碳漆的性能)氟碳漆是由氟碳树脂为主要成分的A、B双组分油漆,它具有以下特点:(1)超强耐候性、防腐蚀性、强自洁性。
(2)强附著性、高装饰性、防水、防老化、耐酸、耐碱。
(3)良好的柔韧性、抗划伤性、耐洗刷性。
(4)优异的耐褪色、不开裂、耐粉化、耐磨损性能等其它普通防腐油漆所不能达到的特性。
2、涂料的品种、性能、颜色、涂刷层数及表面标记等应符合设计规定,涂料应有生产厂家的合格证书。
3、涂料的耐温性能,抗腐性能应按输热介说度及环境条件进行选择。
按涂料工艺要求稀释至适当温度,搅拌均匀,色调一致,及时使用,涂料应密封保存,自然。
4、干燥的现场涂漆应防止漆膜油漆污物和损坏,漆膜为干燥固化剂不得由下道工序施工。
六、涂漆质量应符合以下要求:1、与基础面黏结牢固,厚度符合要求,面层色调一致,光亮清洁,无皱纹、无气泡。
2、漆膜均匀,完整无漏涂,无损坏。
七、设备维护保养:1、对设备的电缆表面进行擦洗除污,检查是否有破损。
2、对钢丝绳、减速机、卷扬机和电机进行清洁保养并进行上油处理。
吊臂吊架及抱索器喷漆工艺

吊臂吊架及抱索器喷漆工艺
1、用干净棉纱沾取少量汽油,将吊臂吊架及抱索器外表面的油污
擦拭干净。
2、先用粗砂纸打磨吊臂吊架及抱索器外表面的锈迹,再用细砂纸
整体打磨使外表面平整。
3、用干净棉纱沾取少量汽油,擦去表面的浮尘和铁锈。
4、将车门机构关闭,若两辆车厢同时喷漆,需将两车用绳子固定
在一起。
5、用彩条布将车厢覆盖,只露出吊臂吊架部分。
6、打开气泵,装上油水分离器,安装喷枪。
7、将面漆(钻石银)与稀释剂按3:1比例调和,并搅拌均匀。
8、调整喷枪的出漆量、出气量、雾化形状,尽量调整到出漆量较
少,雾化较均匀的状态。
9、对吊臂吊架及抱索器外表面按照从上到下的顺序喷涂面漆,注
意不要在同一地点喷漆时间过长,避免油漆过多后下流。
10、待第一遍面漆干透后再用同样的方法喷第二遍面漆。
11、用稀释剂清洗喷枪。
12、将清漆与固化剂按4:1的比例调和,并搅拌均匀。
13、调整喷枪的出漆量、出气量、雾化形状,尽量调整到出漆量较
少,雾化较均匀的状态。
14、对吊臂吊架及抱索器外表面按照从上到下的顺序喷涂清漆。
15、待第一遍清漆干透后再用同样的方法喷第二遍清漆。
16、用稀释剂清洗喷枪,并将喷枪浸泡在稀释剂中。
17、待清漆干透后,取下彩条布,清理现场。
- 1、下载文档前请自行甄别文档内容的完整性,平台不提供额外的编辑、内容补充、找答案等附加服务。
- 2、"仅部分预览"的文档,不可在线预览部分如存在完整性等问题,可反馈申请退款(可完整预览的文档不适用该条件!)。
- 3、如文档侵犯您的权益,请联系客服反馈,我们会尽快为您处理(人工客服工作时间:9:00-18:30)。
1 目的为了达到油漆涂装的防腐效果及外表的美观,中途油漆建议在油漆施工中应严格按照以下要求进行操作。
2 范围本标准规定了喷丸件、涂漆件的质量要求与检验方法。
本标准适用于甲板机械、船用起重机、铸件毛坯的防护、装饰用途漆膜层的质量检验。
3总则油漆施工是一个非常重要的步骤,在油漆选定的情况下,油漆的质量是要靠施工工艺来实现的。
在本施工工艺中,将从一下几个方面给出控制原则:3.1表面处理要求3.2油漆的涂装方法及预涂装3.3施工质量控制3.4施工环境控制3.5油漆的储存使用(详见相关施工指导)3.6质量记录3.7不合格处置3.8安全方面详细工艺如下3.1 表面处理要求3.1.1 喷丸前检查3.1.1 喷丸前采用温水加清洁剂(3%~5%),使用高压清洗枪喷洗工件表面因转运、探伤等原因形成的油污、脏物;干燥后才能进行喷丸。
3.1.2 目测工件表面不允许有油脂、污垢、裂缝、焊瘤、蚀坑等缺陷,允许有铁锈、机械杂质。
3.1.3 冷焊件喷丸前钢板原始锈蚀等级不超过GB/T 8923规定的锈蚀等级B级要求。
3.1.4检查工件的孔、机加面、螺孔等应保护的部位是否根据要求进行保护。
3.1.5 表面预处理a)进行抛丸处理前,须进行底材表面预处理,即将表面的污染物如油污,油脂及其它处理干净。
b)抛丸处理前需要对一下部位用电动工具进行打磨处理:I. 底材表面的钻孔边缘、气割面及其边缘II.焊缝突起的部分、焊渣以及飞溅的焊点这些部位应处理到表面平整,或有一定坡度的起伏表面,以保证油漆能以较均匀的漆膜覆盖钢铁表面。
c)钢材的边角及边缘钢材的边角及边缘,由于这些部位较尖,在喷涂时不能达到设计的漆膜厚度,因此这些部位必须用电动工具打磨成圆角(r =2cm)。
d)要进行防腐涂装的表面,必须用喷砂或抛丸的处理的方法对底材进行处理至ISO8501-1:1988 Sa 2.5级。
其文字表达即为:达到非常彻底的喷砂除锈处理。
在不放大的情况下进行观察时,表面应无可见的油脂、污物、附着不牢的氧化皮、铁锈、旧油漆及其它杂质。
残留的痕迹仅显示点状或条纹状的轻微色斑。
e)表面粗糙度应达到40-75µm ISO8501-1的标准。
(抛丸后钢表面的粗糙度指抛丸时钢砂打击在钢板上残留痕迹的深度,粗糙度过小,钢板表面平滑,涂层附着力差,粗糙度大,油漆不能覆盖住粗糙度的波峰,易形成点蚀,而且会增加油漆消耗量。
(为了正确评定表面处理的质量,许多国家都制订了表面处理质量评定标准。
其中最为著名的是瑞典工业标准SIS055900:1967,目前在世界上被广泛采用。
国际标准化组织色漆和清漆技术委员会涂装前钢材表面处理分会也制订了国际标准ISO8501-1.1988其它如日本、美国、英国、澳大利亚、中国(GB8932)与瑞典,ISO标准相同。
)3.1.2 构件表面处理验收合格后,务必用压缩空气吹净钢表面砂粒,灰尘等污物。
3.1.3工件验收合格后,必须在4小时内进行涂装。
3.1.4如喷砂构件表面发生氧化,则整个氧化部位应重新作喷砂处理,并达到喷砂标准。
3.1.5对需要焊接部位,用5-8cm宽的胶带纸封住。
3.1.6抛丸处理表面一旦完成后,应及时安排喷涂底漆。
因为抛丸处理过的表面,铁完全曝露在大气中,很容易与大气中的氧气和水汽发生锈蚀反应而产生黄锈。
在一般正常天气环境中,建议在四个小时内完成底漆的喷涂,如果在潮湿的天气环境下,更应该尽快完成底漆的涂装,以免底材表面产生锈蚀而影响涂装质量,或不得不再一次进行喷砂处理。
3.2油漆预涂装及涂装方法3.2.1 涂装前表面检验3.2.1 .1铸件表面的凸起、缩孔和浇胃口应在规定的范围内,型砂及炉渣清除干净。
铸件表面应力求平整,非机加面不平度在任意600mm长度上不大于4.5mm。
3.2.1.2 切削件、冲压件及冷作件的毛刺应去除干净。
3.2.1.3焊接凹凸处应打磨光滑,工件表面无焊渣和飞溅。
3.2.1.4 工件表面应清理干净,无油脂、铁锈、焊渣、灰尘、水、酸、碱等其它杂质。
3.2.1.5经喷丸处理合格后的工件,在表面露点湿度≥3℃,相对湿度≤85%的条件下与涂漆相隔时间不得超过6h。
3.2.2 涂装前准备检查3.2.2.1 对于不需要涂漆的部位应进行油封、包扎,一般包括铭牌、标牌、油嘴,需工作的机加面、玻璃、密封橡胶、外部软管、电缆、表盘、电控箱、各种阀件等。
3.2.2.2检查所用涂料的品种、牌号、颜色、出厂日期是否有效并符合工艺要求。
3.2.2.3熟悉双组分涂料产品使用说明书和涂装工艺文件,检查其配比正确性。
双组分涂料混合后必须经15min~30min熟化后才能施工。
3.2.2.4涂料如需稀释处理,除工艺有要求外,刷涂时稀释剂加入量不超过涂料总体积的3%,采用天气喷涂的不超过5%。
3.2.2.5 检查涂料施工设备是否符合涂料的施工要求,所用设备必须完好正常、清洁干净。
3.2.2.6 检查油漆工是否为特证漆工,并满足工艺文件规定要求。
3.2.3 涂装检查3.2.3.1 刷涂刷涂时刷涂方向应采取先左右后上下的方向进行涂装。
先横向扩展,然后纵向理顺,使涂料均匀分布,亦可先纵向扩展,在横向理顺,循序渐进,不得有遗漏。
遇有表面粗糙,边缘弯角和凸出等部位应先预涂一道。
3.2.3.2 辗涂辗筒涂装时,辗筒上涂料应均匀分布,涂装时滚动速度要保持一定,不可太快,切忌过分用力压展辗筒,对于焊缝,切痕等凸出部位,应先预涂一道。
3.2.4高压无气喷涂3.2.4.1检查喷涂设备及枪嘴孔径是否符合工艺规定要求。
3.2.4.2 检查喷涂用压缩空气压力应大于0.5Mpa,枪机喷出压力应符合工艺规定要求。
3.2.4.3 高压无气喷涂时,喷枪与被涂工件面保持垂直,喷枪移动时应与被涂工件面保持等距,防止喷枪作长距离或弧型移动,喷枪与被涂工件面距离为工程甲板机械产品300mm~500mm。
3.2.4.4喷枪移动速度,当膜厚低时则移动速度快些,膜厚高时则移动速度慢些。
3.2.4..5 拐角和表面形状比较复杂的部位,应先预涂一道,然后继续快速喷涂为宜。
3.2.5 涂装间隔检查检查涂装间隔是否符合工艺规定的要求,如果超过最大的涂装间隔则要求将漆面充分打磨粗糙再加涂,以保证漆膜间的结合力。
对于环氧类涂料则最好低于工艺中规定的最大涂装间隔,以保证漆膜之间的结合力。
3.2.6涂装施工后必须按涂装工艺中规定的干燥设备、干燥温度和时间进行干燥。
3.2.7整机最终表面涂装前,应用温水加清洗剂(3%~5%),使用高压清洗枪清洗工件表面因运转、调试形成的油污和脏物。
3.2.8漆膜未干透钱如果污损,应干燥后打磨或用砂纸清理,并重新涂装,要求与未污损部位一致,因装配、焊接等造成漆膜损坏处于清理干净脏物,并将损坏处修出一定的坡度,然后按工艺重新涂装,要求新旧漆膜一致。
3.2.8漆膜厚度检查如有漆膜厚度要求时,使用湿膜测试片、干膜测厚仪检测漆膜的湿厚和干厚。
膜厚公差下限为-10%,上限为50%。
3.2.9铸件表面的凹陷处,如涂装工艺允许刮腻子时,每层不超过0.5mm。
刮腻子应在完全干燥的底漆上进行,腻子应彻底干燥后再进行打磨清理干净。
3.2.10漆膜外观质量检查3.2.10.1 底漆:目测漆膜表面应均匀、完整并干透,不允许有针孔、气泡皱纹、裂纹、脱落、漏涂。
严重流挂等缺陷,允许有少量小面积流挂及修护痕迹。
3.2.10.2中层漆:目测漆膜表面应均匀,完整并干透,不允许有针孔、气泡、皱纹、裂纹、严重流挂、漏涂、层间剥离,允许有少量小面积的流挂及修护痕迹。
3.2.10.3面漆(零部件):目测漆膜表面基本平整、光滑、色泽无显著的差异,不允许有流挂、起皱、起泡、针孔、层间剥离等缺陷。
3.2.11整机出厂涂装外质量检查3.2.11.1产品内表面防护性涂层,要求漆膜完整、色泽无严重的差异,允许有不影响防护功能是轻微流痕、小堆集、色差和修补痕迹。
3.2.11.2产品表面装饰性涂层:漆膜完整、色泽基本一致、表面不允许有修整痕迹及影响性能的色裂、起泡、缩孔等现象、3.2.12 注意事项3.2.12.1为了确保涂装质量,必须严格涂料厂商产品说明书的规定进行施工。
3.2.12.2 构件大面积喷涂前,必须对手动焊缝、自由边、角落、R孔及难以喷涂的位置先进行预涂工作,保证喷涂的质量。
3.2.12.3每覆涂一道油漆建议表面用手工砂皮纸进行打磨清理颗粒、垃圾等物。
3.2.12.4如果温度低于5℃时,油漆混合后放置15分钟左右,然后开始喷涂。
3.2.12.5 根据不同的油漆,选用合适的喷漆泵和喷枪嘴,严格控制涂装的复涂间隔期。
3.2.12.6喷涂时,喷枪始终与被平面保持垂直,左右上下移动时,要注意与被涂面等距离移动,避免手腕转动而成为弧形移动,以保持膜厚的均匀。
3.2.12.7喷涂距离通常为300-400毫米,喷幅为50%左右,运行速度要根据膜厚的条件而定,过快达不到设计干膜厚度,过慢会引起漆膜过厚和流挂。
3.2.12.8钢板温度在5℃— 38℃时,必须要调整喷涂作业时间,防止油漆的缺陷。
3.2.12.9最后一道油漆施工结束后,表面应无针眼、气泡、发白、流挂、露点、缩孔及缩边、色差、橘皮、渗色、浮色、漆雾等漆病出现。
3.2.12.10晚上施工时必须有足够的照明,在箱体内喷涂油漆时必须有防爆风机和防爆灯,防止安全的意外发生及油漆漏涂。
3.3施工质量控制3.3.1油漆的准备和使用• 开罐—开罐前检查和确认涂料的品种、牌号和出厂日期,开罐后检查涂料是否有色差和变色(固化剂)沉淀和严重返粗、橘皮,发现涂料过期变质应禁止使用。
• 搅拌—混合前基料和固化剂要分别搅拌,混合后再搅拌;双组份涂料应用动力搅拌机搅拌;严重板结、胶化的不能强行稀释搅拌继续使用。
• 混合—双组份和三组份的涂料一定要按比例调配;有时固化剂比率小,因此一定要倒得干净。
• 熟化—有的双组份涂料必须要按说明书的要求进行熟化;熟化可以避免涂料“移滑”。
• 混合后的使用时限—涂料超过使用的时间后不能稀释后再使用;超过使用时限的涂料,使用后会影响涂层的性能。
• 稀释—涂料的黏度在出厂前已调好,通常不需要加稀释剂;如果需要添加稀释时,不要超过体积的5%;冬季、夏季温度低和高时可以适量加入稀释剂,减少涂料黏度和干喷。
• 过滤—部分产品涂料为了喷涂中顺利,必须进行过滤;有时喷涂一些特殊涂料时需要折涂喷漆泵上的滤网,保证喷漆的流畅。
•双组份油漆的主漆和固化剂一旦混合后有一定的使用时间(在2小时内使用结束)。
因此,要注意用多少就混合多少,以免造成浪费。
3.3.2 膜厚的控制a)施工时,须进行湿膜厚度的检查,以做到对所喷的干膜厚度有一个相对的预测。
施工各道油漆时,要注意漆膜均匀,并达到规定的漆膜厚度,以保证涂装质量及保证年限。
b)目测:在光线充足地方目力距漆膜表面为30cm-40cm察观。