转炉炼钢主要过程及特点
转炉工艺流程

转炉工艺流程转炉工艺流程是一种重要的冶炼方法,主要用于炼钢过程中。
它可以通过高温和氧化剂将生铁中的杂质去除,得到高纯度的钢材。
下面将介绍转炉工艺流程的主要步骤和流程。
首先,将生铁和废钢等原料加入转炉中。
生铁是从高炉中得到的,含有较多的杂质。
废钢则是来自于废弃的钢铁制品,通过再生利用可以减少资源浪费。
接下来,将炉膛中的空气预热并压缩成雾状,形成高压氧枪。
高压氧枪将高速喷射的氧气和炉膛中的原料充分混合,并在高温下进行氧化反应。
这个步骤被称为“吹炼”,它的作用是将生铁中的杂质氧化并去除。
在吹炼过程中,氧化反应会产生大量的热量,使炉温急剧上升。
为了控制温度,需要加入适量的废钢和石灰石等冷却剂。
这些冷却剂可以吸收部分热量,同时还可以用于与杂质反应生成渣。
当炉温升至一定程度后,会进行凿渣操作。
凿渣是将转炉中的渣从炉膛底部排出的过程。
渣中含有大量的杂质,需要及时清理,以保证后续冶炼的顺利进行。
在凿渣之后,转炉中的钢水与冷却剂继续进行反应。
这时的炉温已经下降,反应速率较慢。
冷却剂会吸热,将剩余的热量带走。
同时,继续吹入氧气,使冷却剂氧化并与杂质很好地结合,形成不溶于钢水的浮渣。
这个过程被称为“吹碱”,它能进一步净化钢水,并使其达到所需的成分要求。
最后,将净化后的钢水倾注出炉。
倾钢是将钢水从转炉中倾出的过程。
为了保证钢水的流动性,可以在转炉背部设置倾钢孔,通过倾钢孔将钢水导入倾钢罐中。
倾钢过程需要控制倾出速度和流量,以保证钢水的质量和稳定性。
总结起来,转炉工艺流程包括原料加入、吹炼、凿渣、吹碱和倾钢等主要步骤。
通过这些步骤,可以将生铁中的杂质氧化并去除,从而得到高纯度的钢材。
转炉工艺流程在炼钢过程中起到了重要的作用,提高了钢材的质量和效率。
炼钢转炉工艺流程
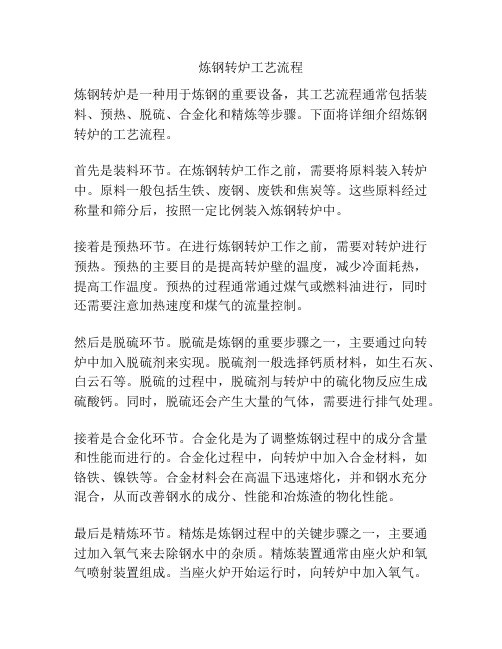
炼钢转炉工艺流程炼钢转炉是一种用于炼钢的重要设备,其工艺流程通常包括装料、预热、脱硫、合金化和精炼等步骤。
下面将详细介绍炼钢转炉的工艺流程。
首先是装料环节。
在炼钢转炉工作之前,需要将原料装入转炉中。
原料一般包括生铁、废钢、废铁和焦炭等。
这些原料经过称量和筛分后,按照一定比例装入炼钢转炉中。
接着是预热环节。
在进行炼钢转炉工作之前,需要对转炉进行预热。
预热的主要目的是提高转炉壁的温度,减少冷面耗热,提高工作温度。
预热的过程通常通过煤气或燃料油进行,同时还需要注意加热速度和煤气的流量控制。
然后是脱硫环节。
脱硫是炼钢的重要步骤之一,主要通过向转炉中加入脱硫剂来实现。
脱硫剂一般选择钙质材料,如生石灰、白云石等。
脱硫的过程中,脱硫剂与转炉中的硫化物反应生成硫酸钙。
同时,脱硫还会产生大量的气体,需要进行排气处理。
接着是合金化环节。
合金化是为了调整炼钢过程中的成分含量和性能而进行的。
合金化过程中,向转炉中加入合金材料,如铬铁、镍铁等。
合金材料会在高温下迅速熔化,并和钢水充分混合,从而改善钢水的成分、性能和冶炼渣的物化性能。
最后是精炼环节。
精炼是炼钢过程中的关键步骤之一,主要通过加入氧气来去除钢水中的杂质。
精炼装置通常由座火炉和氧气喷射装置组成。
当座火炉开始运行时,向转炉中加入氧气。
氧气与钢水中的碳、硅等杂质反应生成气体,从而达到去除杂质的目的。
以上就是炼钢转炉的工艺流程简介。
当然,实际的工艺流程还需要根据具体的钢种、需求和设备状况进行调整。
随着科技的发展,炼钢转炉的工艺流程也在不断创新和改进,以提高钢水的质量和生产效率,降低能源消耗和环境污染。
转炉炼钢工艺流程

转炉炼钢工艺流程转炉炼钢是一种常用的钢铁冶炼工艺,通过高温炼炉将生铁和废钢进行冶炼,以生产高品质的钢材。
下面将详细介绍转炉炼钢的工艺流程。
1. 原料准备转炉炼钢的原料主要包括生铁和废钢。
生铁是从高炉中得到的铁水,含有较高的碳含量,而废钢则是来自废旧钢材的回收利用。
在进行炼钢之前,需要对原料进行严格的筛选和分类,确保原料的质量符合生产要求。
2. 转炉炉前准备在进行转炉炼钢之前,需要对转炉进行一系列的准备工作。
首先是清理转炉内部的残渣和杂质,确保转炉内部的清洁。
然后对转炉进行加热,使其达到适宜的工作温度。
同时,还需要准备氧气、燃料和炉渣等辅助材料,以保障炼钢过程中的顺利进行。
3. 转炉炼钢过程转炉炼钢的主要过程包括炉前处理、吹炼、脱硫、脱磷、合金加入和出钢等环节。
首先是炉前处理,将预先准备好的生铁和废钢装入转炉中。
然后启动吹炼工艺,通过吹入高压氧气和燃料,使炉内的温度迅速升高,生铁和废钢开始熔化并发生氧化还原反应。
在这个过程中,炉内的温度可以达到数千摄氏度,将原料中的杂质和不纯物质燃尽,确保钢水的纯净度。
接下来是脱硫和脱磷的过程,通过向炉内加入适量的脱硫剂和脱磷剂,将钢水中的硫和磷等有害元素去除,提高钢材的质量和纯度。
在炼钢的过程中,根据需要还可以向炉内加入一定比例的合金元素,如铬、锰、钼等,以调整钢材的化学成分和性能。
最后是出钢过程,当炼钢结束后,通过倾炉口将炼好的钢水倒入钢包中,再经过连铸、轧制等工艺,最终得到成品钢材。
4. 转炉炼钢的优点转炉炼钢相比其他炼钢工艺具有以下优点:一是能够利用废钢资源,实现资源的循环利用;二是生产成本较低,能够生产出高品质的钢材;三是炼钢过程中能够控制钢材的化学成分和性能,满足不同用途的需要。
总之,转炉炼钢是一种成熟、高效的钢铁冶炼工艺,通过严格的工艺流程和操作规范,能够生产出优质的钢材产品,满足市场和用户的需求。
转炉炼钢工艺过程..
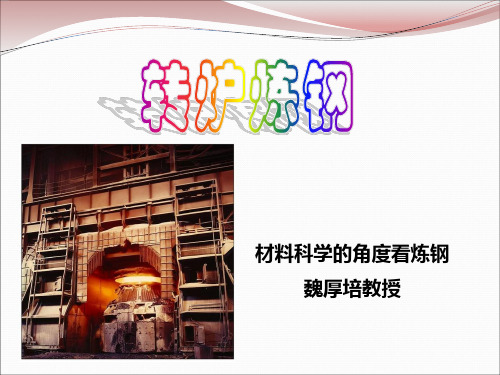
产生的氧化壳层,铁量约占70%-75%。氧化铁皮还 有助于化渣和冷却作用,使用时应加热烘烤,保持 干燥。
铁矿石中铁的氧化物存在形式是Fe2O3、Fe3O4和FeO
其氧含量分别是30.06%,27.64%和22.28%。
三、转炉冶炼五大制度
1. 装料制度
2. 供氧制度
3. 造渣制度 4. 温度制度
LD转炉
• 1970年后,由于发明了用
碳氢化合物保护的双层套 管式底吹氧枪 而出现了底 吹法,各种类型的底吹法 转炉(如OBM,Q-BOP,LSW等) 在实际生产中显示出许多 优于顶吹转炉之处,使一 直居于首位的顶吹法受到 挑战和冲击。
OBM装置
•继奥地利人Dr.Edaurd等 于1973年研究转炉顶底复 吹炼钢之后,世界各国普 遍开展了转炉复吹的研究 工作,出现了各种类型的 复吹转炉,到20世纪80年 代初开始正式用于生产。
(1)成分;
(2)带渣量; (3)温度。
1)硅(Si)
硅是重要的发热元素,铁水中含Si量高,炉内的化学热增加,铁水中Si量增
加0.10%,废钢的加入量可提高1.3%-1.5%。
铁水含Si量高,渣量增加,有利于脱磷、脱硫。
硅含量过高会使渣料和消耗增加,易引起喷溅,金属收得率降低,同时渣中 过量的SiO2,也会加剧对炉衬的侵蚀,影响石灰渣化速度,延长吹炼时间。 通常铁水中的硅含量为0.30%-0.60%为宜。
近几年中国年产钢量
2009
2007 2002 钢产量达到4.89亿t 粗钢产量达到 5.678亿t
2005 年产钢量为1.82亿t 2003 钢产量达到3.5亿t
预计2010年 将突破6亿t
钢产量首次突破2 亿t,达到2.234亿t
转炉炼钢工艺简介
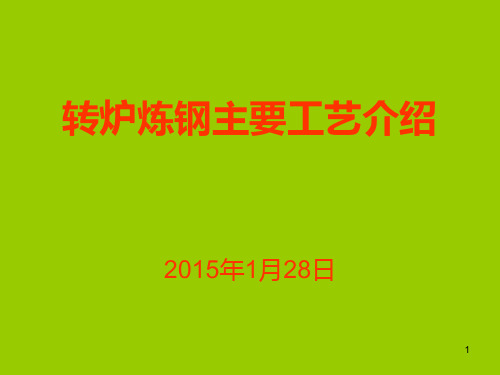
18
萤石作用及要求
• 作用
造渣加入萤石可以加速石 灰的溶解,萤石的助熔作 用是在很短的时间内能够 改善炉渣的流动性,但过 多的萤石用量,会加剧炉 衬的损坏,并污染环境。
• 质量要求 • CaF2≥75%, SiO2≤23%,S≤0.20%, P≤0.08%,H2O≤3.0% • 粒度:5-60mm
渣量=(石灰+镁球或熟白)×(2-3)
8
铁水成分及温度影响
• Mn的影响 • 锰是弱发热元素,铁水中Mn氧化后形成的(MnO)可促 进石灰溶解,加快成渣;减少氧枪粘钢,终点钢中余 锰高,能够减少合金用量,利于提高金属收得率;锰 在降低钢水硫含量和硫的危害方面起到有利作用。 Mn/Si的比值为0.8~1.00时对转炉的冶炼操作控制最 为有利。当前使用较多的为低锰铁水,一般铁水中 [Mn]=0.20%~0.40%。
6.设备少,投资节省。
4
炉顶料仓 振动给料器 电子称 带式运输机 密封料仓 传动机构 实 心 轴
汽包 氧 枪 风 机 不 回 收 时 放 空 回收煤气 进入煤气柜
烟 道
文氏管 脱水器
溜 槽
洗 涤 塔
沉淀池
电动机 渣 罐 转 炉 吸 滤 池
水封逆止阀 送往高炉利用
支架Hale Waihona Puke 氧气顶吹转炉工艺流程示意图
5
二 、转炉炼钢用主要原材料
28
2.1装料制度:废钢量的确定
• 热量来源于:
• 转炉炼钢不需要外来热源;
铁水物理热及元素氧化化学热。 铁水及废钢的合理配比须根据炉子的热平衡计算确定。 • 硅的作用 优点:因发热量大,增大废钢加入量,一般铁水中Si增 加0.1%,废钢比增大1%。 缺点:增大渣量,侵蚀炉衬一般控制在0.3-0.5%。
转炉炼钢的主要化学反应
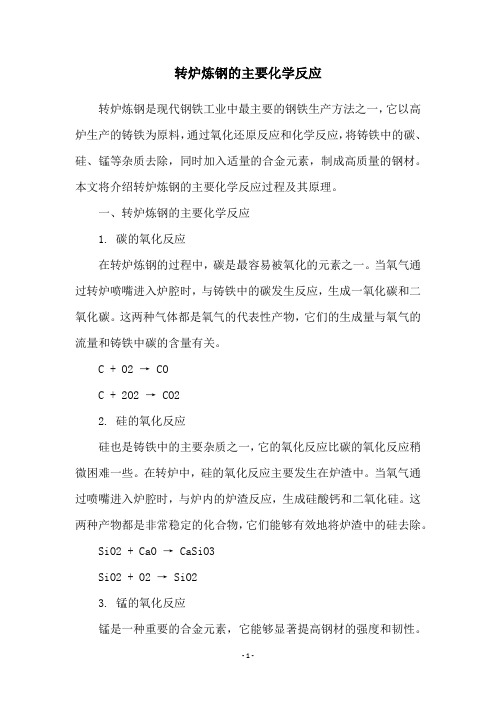
转炉炼钢的主要化学反应转炉炼钢是现代钢铁工业中最主要的钢铁生产方法之一,它以高炉生产的铸铁为原料,通过氧化还原反应和化学反应,将铸铁中的碳、硅、锰等杂质去除,同时加入适量的合金元素,制成高质量的钢材。
本文将介绍转炉炼钢的主要化学反应过程及其原理。
一、转炉炼钢的主要化学反应1. 碳的氧化反应在转炉炼钢的过程中,碳是最容易被氧化的元素之一。
当氧气通过转炉喷嘴进入炉腔时,与铸铁中的碳发生反应,生成一氧化碳和二氧化碳。
这两种气体都是氧气的代表性产物,它们的生成量与氧气的流量和铸铁中碳的含量有关。
C + O2 → COC + 2O2 → CO22. 硅的氧化反应硅也是铸铁中的主要杂质之一,它的氧化反应比碳的氧化反应稍微困难一些。
在转炉中,硅的氧化反应主要发生在炉渣中。
当氧气通过喷嘴进入炉腔时,与炉内的炉渣反应,生成硅酸钙和二氧化硅。
这两种产物都是非常稳定的化合物,它们能够有效地将炉渣中的硅去除。
SiO2 + CaO → CaSiO3SiO2 + O2 → SiO23. 锰的氧化反应锰是一种重要的合金元素,它能够显著提高钢材的强度和韧性。
在转炉炼钢的过程中,锰的氧化反应主要发生在炉渣中。
当氧气通过喷嘴进入炉腔时,与炉渣中的锰反应,生成锰酸钙和二氧化锰。
这两种产物都能有效地将炉渣中的锰去除。
MnO + CaO → CaMnO32MnO2 → 2MnO + O24. 磷的还原反应磷是一种非常有害的杂质元素,它能够降低钢材的强度和韧性。
在转炉炼钢的过程中,磷的还原反应主要发生在钢水中。
当还原剂进入钢水中时,与钢水中的磷反应,生成磷化氢和磷化钙。
这两种产物都是非常稳定的化合物,它们能够有效地将钢水中的磷去除。
2P + 3H2 → 2PH3CaO + P2O5 → Ca3(PO4)2二、转炉炼钢的原理转炉炼钢的原理是以氧化还原反应和化学反应为基础,通过控制氧气的流量和喷入位置,使铸铁中的碳、硅、锰等杂质被氧化,同时加入适量的合金元素,制成高质量的钢材。
转炉炼钢的原理

转炉炼钢的原理转炉炼钢是一种重要的钢铁生产方法,采用该方法可以将铁矿石中的杂质和金属硫化物等有害物质去除,以及控制钢中的碳含量和其他合金元素的含量,从而获得高质量的钢材产品。
本文旨在介绍转炉炼钢的原理及其过程。
转炉炼钢工艺的基本原理是利用氧气吹炼方法进行炉内冶炼,使铁矿石中的有害杂质在氧气作用下被氧化,然后与炉内产生的石灰石、石英等炉渣反应,形成不溶于炉渣的化合物,以提高钢液的纯度。
同时,通过调整吹氧量和控制炉内温度,可以控制钢液中碳含量的变化。
转炉炼钢过程主要分为三个阶段:加料阶段、吹氧阶段和出钢阶段。
在加料阶段,将预先加热的螺旋矿和选矿的矿粉等物料投入转炉中。
同时,加入适量的废钢、废铁等回收材料,以及石灰石、石英、矿石探配剂等辅助材料。
将物料均匀分层投放,以保持炉内的物料分布均匀。
然后,关闭转炉顶部的炉门,拉低炉盖。
进入吹氧阶段后,先进行预吹,即用高压压缩空气吹除炉中的不稳定气体,使炉内形成正压。
然后,将氧气管道引入炉内并开始吹氧。
氧气吹入炉内后,会与铁水中的杂质发生反应,如硅、锰、磷等元素被氧化为相应的氧化物。
同时,氧气作用下的高温也有利于炉渣反应,形成包裹在钢水外层的炉渣。
炉渣起到各种有益作用,如控制钢液温度、保护合金、去除杂质、调整钢中含碳量等。
吹氧阶段需要控制吹氧的时间和吹氧量,以及炉内温度。
一般来说,在吹氧早期,吹氧速度较快,氧气用量较大,温度逐渐上升。
当氧气吹过一定时间后,可适当减小吹氧速度,控制氧气用量,以调整钢液的碳含量。
在这个过程中,还会根据转炉炉内的温度来调整加入的料种和炉渣配比,以保持合金的正常运行。
最后,进入出钢阶段,打开转炉顶部的出钢口,将钢水流入连铸机或浇铸坑中。
在出钢过程中,还会加入脱氧剂、合金等物料,以进一步调整钢液的成分。
同时,通过控制出钢速度和流量等参数,可以控制钢液的形成和凝固过程,获得所需的钢材。
转炉炼钢的原理主要是通过氧气吹炼方法,将铁矿石中的有害物质去除,并控制钢液中的成分和温度。
转炉炼钢主要过程及特点

合金化
向钢水中加入合金元素使其 达到成品钢成分要求
转炉设备
供料系统
转炉系统 供气系统 净化系统 辅助设备
转炉冶炼的基本原理 ----物料平衡及热平衡
纯氧顶吹转炉炼钢优点
(1)生产速度快 因为用纯氧吹炼,会高速降碳, 快速提温,大大缩短冶炼时间。。 (2)品种多、质量好 纯氧顶吹转炉既能炼普通 钢,也能炼普通低碳钢。如首钢采用这种方法成功 地试炼了一百多种钢材。用纯氧吹炼,钢中氮、氢 等有害气体含量较低。 (3)基建投资和生产费用低 纯氧顶吹转炉的基 建投资相当于同样生产量的平炉车间的60~70%, 生产费用也低于平炉。
(4)3~5min后加入第二批渣料继续吹炼(随吹炼进行钢中碳逐渐降低, 约12min后火焰微弱,停吹);
(5)倒炉,测温、取样,并确定补吹时间或出钢;
(6)出钢,同时(将计算好的合金加入钢包中)进行脱氧合金化。
炼钢原料
转炉炼钢的原材料分为金属料、非金属料和气 体。金属料包括铁水、废钢、铁合金,非金属料包 括造渣料、熔剂、冷却剂,气体包括氧气、氮气、 氩气、二氧化碳等。非金属料是在转炉炼钢过程 中 为了去除磷、硫等杂质,控制好过程温度而加入的 材料。主要有造渣料(石灰、白云石),熔剂(萤 石、氧化铁皮),冷却剂(铁矿石、石灰石、废 钢),增碳剂和燃料(焦炭、石墨籽、煤块、重 油)。
转炉炼钢生产工艺
装料制度
造渣制度 供气制度 温度制度 出
钢 脱氧及合金化
装料制度
装入量是指每炉装 入的铁水和废钢的总量,一 般废钢占15~30%,装入量分 为三种形式: 1.定量装入:整个炉役期保 持每炉的金属装入量不变; 2.定深装入:随容积的扩大 而增加装入量,保持熔池的 深度不变; 3.分阶段定量装入:将整个 炉役分为若干阶段,每阶段 定量装入.
转炉炼钢流程

转炉炼钢流程
转炉炼钢是一种常用的钢铁冶炼方法,通过将生铁和废钢放入转炉中,加入适
量的废钢和铁合金,然后进行氧气吹炼,最终得到所需的钢铁产品。
下面将详细介绍转炉炼钢的流程。
首先,将生铁和废钢装入转炉。
生铁是从高炉中得到的铁水,含有较高的碳含量,而废钢是回收利用的废旧钢铁制品。
将这些原料装入转炉后,需要按照一定的比例加入适量的废钢和铁合金,以调整炉料的成分和温度。
接下来是转炉的氧气吹炼过程。
在炉料准备好后,通过转炉底部的氧气鼓风装
置向炉内吹入高压氧气。
氧气与炉内的炉料发生化学反应,使得炉内温度迅速升高,同时氧气氧化了炉料中的杂质和碳,使其逐渐融化。
这个过程需要严格控制氧气的流量和时间,以确保炉内的温度和化学反应达到理想状态。
随着氧气吹炼的进行,炉内的炉料逐渐熔化,形成熔体。
在这个过程中,需要
不断搅拌炉料,以保证炉内温度和成分的均匀性。
同时,根据所需的钢铁品种,可以在这个阶段适量加入合金元素,以调整钢铁的成分和性能。
最后,是炉渣处理和出钢过程。
在炉料完全熔化后,炉内会生成一层炉渣,这
是氧气吹炼过程中产生的氧化物和其他杂质的混合物。
通过合理的炉渣处理方法,可以将炉渣与熔体分离,最终得到所需的钢铁产品。
同时,需要注意控制出钢的速度和温度,以保证钢水的质量和成分符合要求。
总的来说,转炉炼钢流程是一个复杂而精密的过程,需要严格控制各个环节,
以确保最终产品的质量和性能。
通过合理的操作和管理,可以实现高效、低成本的钢铁生产,满足不同领域的需求。
炼钢转炉工艺流程

炼钢转炉工艺流程
《炼钢转炉工艺流程》
炼钢转炉是一种常见的钢铁冶炼设备,采用氧气作为原料,通过不断升温、熔化、脱碳和合金化,将生铁或废钢冶炼成高品质的钢材。
其工艺流程主要包括加料、通氧、出渣、出钢四个主要过程。
首先是加料过程,将生铁、废钢、合金等原料按照一定的配比投入转炉中,并在炉内预热至适宜的温度。
加料过程中需要保证稳定的投料速度和均匀的加热,以确保后续工艺的顺利进行。
接着是通氧过程,氧气通过一定的喷嘴直接通入炉内,与炉料进行充分的混合和燃烧,产生高温的炉内环境。
在此过程中需要控制氧气的进气量和温度,使炉内气氛能够达到最佳的燃烧条件,促进炉料的融化和氧化还原反应的进行。
随后是出渣过程,炉脚下部设置有出渣孔,脱碳反应产生的气体和氧化物等杂质会通过这一孔口不断排出。
出渣的效率和质量直接关系到后续的钢液质量和工艺稳定性。
出渣过程需要通过适当的控制和处理,使得炉内的杂质尽可能排出并避免对钢液产生影响。
最后是出钢过程,当炉内的炉料达到设计要求后,将铁水通过转炉底部的出钢孔排出,经过连铸机进行浇铸成型。
出钢过程需要严格控制排钢速度和温度,以确保钢液的质量和成型的规格。
总的来说,炼钢转炉工艺流程需要进行一系列严格的操作和控制,确保原料得到充分融化和反应,以得到满足生产要求的高品质钢材。
转炉炼钢原理及工艺

转炉炼钢原理及工艺
转炉炼钢是通过加热合金材料,然后将其在氧气中抽出到转炉,形成一个旋转坩埚里,再使材料在转炉内不断熔化、混合、渣滓沉淀,达到钢的熔化和净化,最后冷却固化,即可获得均匀的高质量的钢的过程。
转炉炼钢的工艺路径主要包括:原料进炉、熔炼、净化、合金添加、出炉等步骤。
1、原料进炉:将碳钢和合金料装入转炉,加热至溶化温度,开始熔融。
2、熔炼:转炉内熔融的温度受多种因素的影响,如加料量、加料温度、炉气系统的平衡性、熔炼时间等。
3、净化:即清洁熔化渣滓,消除杂质,把金属液中的杂质置于渣滓中,让金属液纯度升高。
4、合金添加:将净化后的钢液入合金添加系统,加入合金钢料,使钢液按照要求的成分,营造钢种具有相应的技术性能。
5、出炉:金属液改变形态,冷却成指定的形状和尺寸,经过纯化后形成高质量钢。
转炉炼钢工艺流程

转炉炼钢工艺流程
炼钢是现代钢铁行业中至关重要的环节之一,而转炉炼钢工艺是其中一种主要
的炼钢方法。
转炉炼钢是利用转炉进行钢水冶炼的工艺过程,其主要特点是生产能力大、生产成本低、生产效率高等优点,因而在钢铁行业中占有重要地位。
在转炉炼钢工艺流程中,首先需要准备炼钢原料。
炼钢原料一般包括废钢、生铁、废钢等,各种原料按一定比例经过预处理后,被送入转炉进行炼钢。
转炉通常由熔炼室和吹氧室组成,熔炼室用于炉内的熔炼过程,吹氧室则用于吹送氧气进入转炉,与炉内的金属物质进行反应。
在转炉炼钢的过程中,主要分为三个阶段:氧吹阶段、脱碳阶段和保温混炼阶段。
首先是氧吹阶段,主要是将转炉内的废钢等原料加热至熔化状态,同时通过吹送氧气,将废钢中的杂质氧化,从而提高钢水的纯度。
接着是脱碳阶段,通过加入适量的脱碳剂,将炼钢中的碳含量控制在一定范围内,以满足钢材的力学性能要求。
最后是保温混炼阶段,主要是控制转炉内的温度和成分均匀性,确保生产出合格的钢水。
转炉炼钢工艺流程的优点在于生产效率高、产品质量稳定、生产能力大等,被
广泛应用于钢铁行业的生产中。
然而,转炉炼钢过程中也存在一定的问题与挑战,例如转炉炼钢比较耗能,废气排放量较大等环境问题,因此随着环保意识的提高,炼钢行业也在不断探索新的炼钢技术与工艺。
总的来说,转炉炼钢工艺是钢铁生产中一种重要的炼钢方法,其工艺流程复杂,涉及多方面的技术知识与操作技巧。
随着科技的进步和环保意识的提高,转炉炼钢工艺也在不断创新与改进,以满足不断提高的生产需求和环保要求。
转炉炼钢工艺流程介绍

转炉炼钢工艺流程介绍
转炉炼钢是一种常见的钢铁生产工艺,下面是其工艺流程的介绍:
1. 铁水预处理:首先,将铁水经过除渣工序,去除其中的杂质和非金属物质,提高炉内的纯净度和质量。
2. 转炉兑炉:之后,将预处理后的铁水加入转炉中,同时加入适量的废钢、废铁等回收材料。
这些回收材料能够提供多种元素和合金,有助于调整并优化转炉内的化学成分。
3. 吹氧气:然后,通过吹氧装置向转炉中喷吹氧气。
氧气与铁水中的杂质反应生成氧化物,如氧化碳、氧化硅等,这些氧化物随废气排出转炉。
4. 炼钢反应:转炉内的铁水经过吹氧反应后,温度升高,同时炉内的化学反应也进行着。
在高温和高氧气作用下,铁水中的碳、硅等元素会逐渐氧化和燃烧,生成气体和渣。
5. 加入合金:根据需要,再加入一定量的合金,如镍、铬、锰等。
合金的加入可以调整钢的成分和性能,改善钢的质量。
6. 钢包炉脱氧:在转炉炼钢过程中,钢中可能还含有一定量的氧气。
为了降低钢中的氧含量,通常还需将钢浇入预先加入了脱氧剂的钢包炉中,并进行搅拌。
脱氧剂能与钢中的氧气反应生成气体,进一步减少钢中的氧含量。
7. 出钢和连铸:最后,将炼制好的钢浇入连铸机中,进行连续铸造,制成钢坯。
这些钢坯经过后续的轧制和加工,可制成各种形状和规格的钢材。
值得注意的是,转炉炼钢是一个复杂的过程,涉及到许多工艺参数和控制指标,操作人员需要根据实际情况进行调整和控制,以达到所需的钢材质量。
转炉炼钢原理及工艺介绍
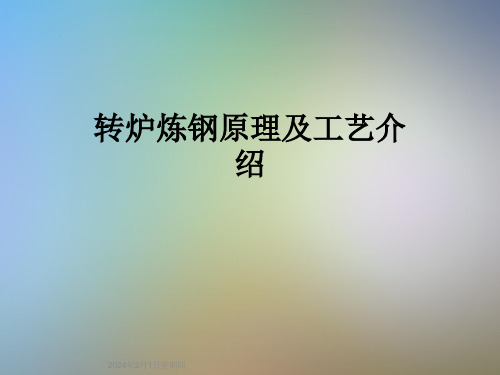
锰的氧化反应有三种情况:
(1)锰与气相中的氧直接作用
[Mn]+ 1/2{O2}=(MnO)
(2)锰与溶于金属中的氧作用
[Mn]+ [O2] =(MnO)
(3)锰的氧化与还原
3)锰与炉渣中氧化亚铁作用
[Mn]+(FeO)=(MnO)+ [Fe]
第三个反应在炉渣——金属界面上迸行,是锰氧化的主要反应。
锰的氧化还原与硅的氧化还原相比有以下基本特点:
1)在冶炼初期锰和硅一样被迅速大量氧化,但锰的氧化程度要低些
,这是由于硅与氧的结合能力大于锰与氧的结合能力;
2)MnO为弱碱性氧化物,在碱性渣中( MnO)大部分呈自由状态存
在。因此,在一定条件下可以被还原。由于锰的氧化反应是放热反应,故
温度升高有利于锰的还原。所以在生产实践中冶炼后期熔池中会出现回锰
1)在某一温度下,几种元素同时和氧相遇时,位置低的元素先氧化。如1500℃ 时,氧化顺序为Al、Si、C、V、Mn。
2)位置低的元素可将位置高的氧化物还原。炼钢过程中脱氧就是利用Al、Si等 元素将FeO还原。
3)CO的分解压曲线的斜率与其它氧化物的不同,它与Si、Mn、V等的氧化物分 解与压CO曲分线解有压一曲交线点相,交此点点对所应对的应温的度温为度15称30为℃氧,化当转t>化15温30度℃。时例,如Si,先S于iOC2被分氧解化压;曲当线 t<1530℃时,则C先于Si被氧化。1530℃即为Si、C的氧化转化温度。
• 所谓炼钢,就是通过冶炼降低生铁中的 碳和去除有害杂质,在根据对钢性能的要求 加入适量的合金元素,使其成为具有高的强 度、韧性或其他特殊性能的钢。
•二、炼钢基本原理
• 因此,炼钢的基本任务可归纳为:
转炉炼钢原理及工艺介绍
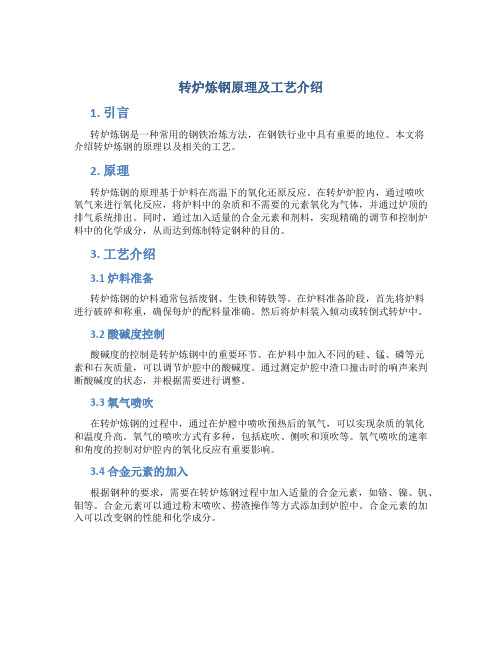
转炉炼钢原理及工艺介绍1. 引言转炉炼钢是一种常用的钢铁冶炼方法,在钢铁行业中具有重要的地位。
本文将介绍转炉炼钢的原理以及相关的工艺。
2. 原理转炉炼钢的原理基于炉料在高温下的氧化还原反应。
在转炉炉腔内,通过喷吹氧气来进行氧化反应,将炉料中的杂质和不需要的元素氧化为气体,并通过炉顶的排气系统排出。
同时,通过加入适量的合金元素和剂料,实现精确的调节和控制炉料中的化学成分,从而达到炼制特定钢种的目的。
3. 工艺介绍3.1 炉料准备转炉炼钢的炉料通常包括废钢、生铁和铸铁等。
在炉料准备阶段,首先将炉料进行破碎和称重,确保每炉的配料量准确。
然后将炉料装入倾动或转倒式转炉中。
3.2 酸碱度控制酸碱度的控制是转炉炼钢中的重要环节。
在炉料中加入不同的硅、锰、磷等元素和石灰质量,可以调节炉腔中的酸碱度。
通过测定炉腔中渣口撞击时的响声来判断酸碱度的状态,并根据需要进行调整。
3.3 氧气喷吹在转炉炼钢的过程中,通过在炉膛中喷吹预热后的氧气,可以实现杂质的氧化和温度升高。
氧气的喷吹方式有多种,包括底吹、侧吹和顶吹等。
氧气喷吹的速率和角度的控制对炉腔内的氧化反应有重要影响。
3.4 合金元素的加入根据钢种的要求,需要在转炉炼钢过程中加入适量的合金元素,如铬、镍、钒、钼等。
合金元素可以通过粉末喷吹、捞渣操作等方式添加到炉腔中。
合金元素的加入可以改变钢的性能和化学成分。
3.5 钢渣处理在转炉炼钢过程中,钢渣是产生的副产物。
钢渣中含有大量的氧化物和杂质,需要进行适当的处理。
一般采用钢渣保温、捞渣、保护渣、中性渣等措施来处理钢渣,以确保钢渣中的氧化元素被充分还原并排出炉外。
3.6 出钢经过一系列的氧化还原反应和调度控制,转炉中的炼钢过程逐渐接近尾声。
当出钢温度达到要求后,打开炉底的出钢口,将液态钢水流入连铸机进行继续加工。
4. 总结转炉炼钢是一种重要的钢铁冶炼方法,其原理是基于氧化和还原反应。
通过适当的酸碱度控制、氧气喷吹和合金元素的加入,可以实现炼制特定钢种的目的。
转炉炼钢工艺

转炉炼钢工艺引言转炉炼钢工艺是一种常用的钢铁生产工艺,其原理是使用巨大的转炉进行冶炼,通过高温燃烧将生铁中的杂质熔化分离,得到高品质的钢铁产品。
本文将详细介绍转炉炼钢工艺的过程、设备和优势。
工艺过程转炉炼钢工艺主要由以下几个步骤组成:1.加炉:在转炉中加入一定数量的生铁和废钢,根据不同的钢种和质量要求控制添加比例。
2.预热:通过燃料燃烧加热炉体,将炉体温度升至一定的范围,为后续冶炼做准备。
3.唤氧:将预先加入的氧气注入转炉中,氧气与炉内的碳、硫等元素发生反应,使其氧化生成气体冒出炉口。
4.碱性脱硫:在钢水中加入一定量的含碱性物质的脱硫剂,使浸渍在钢水中的硫元素氧化为气体并脱出。
5.酸性脱磷:在钢水中加入一定量的含酸性物质的脱磷剂,使浸渍在钢水中的磷元素氧化为气体并脱出。
6.合金化:根据需要,在钢水中加入一定量的合金元素,如铬、锰等,以调节钢的性能。
7.保温装钢:将炉中冶炼好的钢水倒入铸钢坑、铸型等装置中进行冷却和凝固。
设备转炉炼钢工艺需要使用专用的转炉设备,该设备主要由以下几个组成部分:1.转炉本体:转炉本体是整个工艺最关键的部分,它承载着冶炼过程的全部任务。
转炉一般采用大型圆筒形设计,底部有一定数量的喷孔以供氧气进入。
2.转炉支承:转炉支承是将转炉本体固定在地基上的部分,以保证炉体的稳定运行。
3.强制鼓风系统:由鼓风机、风箱等组成,用于向转炉中供给氧气,促进燃烧和炉内反应的进行。
4.喷吹系统:包括氧枪、煤粉喷吹器等,用于将氧气、燃料喷入转炉中,以调节炉内的温度和氧气含量。
5.出渣系统:用于将炉内产生的渣料排出转炉,保持炉内清洁。
工艺优势转炉炼钢工艺相比于其他炼钢工艺具有以下优势:1.生产能力强大:转炉炼钢工艺灵活可调,产能大。
转炉设备可以进行批量生产,快速完成大批量的钢水冶炼,满足市场需求。
2.冶炼效率高:转炉炼钢工艺采用高温燃烧和强制鼓风系统,能够快速将生铁中的杂质熔化脱除,同时还可以进行合金化调节,提高钢的质量和性能。
转炉炼钢的生产流程

转炉炼钢的生产流程转炉炼钢是一种重要的冶金工艺,被广泛应用于钢铁行业。
它通过加热和加氧化剂引入熔融金属中来减少金属的碳含量,从而得到高品质的钢材。
本文将介绍转炉炼钢的生产流程,包括前处理、炉区处理、后处理等环节,总共约2000字。
一、前处理1. 取样转炉炼钢首先需要取样,用于对生铁进行分析。
根据分析结果,生产人员可以得出目标钢品的成分和质量等要求,进而调整转炉冶炼过程。
2. 预热生铁虽然已经经过高温处理,但与转炉的温度相差较大,如果直接加入炉中容易导致转炉窑身破裂。
因此需要对生铁进行预热,以逐渐提高温度,减缓温度差,从而防止炉身爆裂。
3. 拉钢拉钢是指将电炉或其他熔炼炉中的钢水,利用转炉进行进一步脱碳脱硫,调整成分等处理的一种前处理技术。
在拉钢时,还会掺入一些铁合金、废钢和矿渣等材料,以改变金属的成分和质量。
二、炉区处理1. 装料装料是指将经过预处理的生铁/钢水和其他掺杂物料等投入到转炉中进行炉区处理的一种操作。
转炉一般采用叶片式料斗,使得物料能够均匀地分布在炉身中。
2. 加料加料在转炉炼钢中也是一种常规操作,用于控制钢水的碳含量和改变金属的成分。
一般的加料包括生铁、废钢、蒸馏铁等,它们都会影响炉内的氧化还原反应和金属的物理性能。
3. 加热加热是指将转炉炉内的物料进行预热和加热,以达到合适的操作温度。
炉胆内的加热方式主要有三种:氧燃烧加热、燃气加热和电炉加热。
氧燃烧加热的方式最为常见,可以在短时间内提高炉内的温度。
4. 氧吹氧吹是指向转炉炉内喷氧并形成氧气流,以使炉内物料氧化、燃烧和熔化的过程。
氧吹的目的是通过加入氧气来移除金属中的不想要的杂质(如碳、硅、锰等)。
氧吹还可以逐渐提高炉内物料的温度和浓度,并促进金属内部组织的再分布。
5. 碱度/酸度控制炉区处理过程中,炉内物料的碱度或酸度也需要得到控制。
通过氧化反应,转炉炉内会产生一定量的氧化钙、氧化铁等碱性物质。
这些碱性物质需要与掺入的酸性物料(如蒸馏铁、锰矿等)进行反应,以控制炉内物料的酸碱程度。
转炉炼钢原理及工艺介绍

转炉炼钢原理及工艺介绍引言转炉炼钢是一种常用的钢铁生产工艺,具有高效、灵活、环保等特点。
本文将介绍转炉炼钢的原理及工艺流程。
一、转炉炼钢原理转炉炼钢是通过在高温下将生铁与废钢等原料进行反应,去除杂质,调整合金成分来生产钢铁。
其原理基于以下几个重要的化学反应步骤:1.氧化反应:在高温下,将生铁中的杂质氧化为气体或溶于渣中。
主要的氧化反应有:Fe+C+O2=FeO+CO、Mn+C+O2=MnO+CO等。
2.还原反应:在氧化反应的基础上,通过还原剂(如脱氧剂)来还原产生的氧化物。
主要还原反应有:FeO+CO=Fe+CO2、MnO+CO=Mn+CO2等。
3.合金化反应:在还原反应的基础上,通过加入适量合金元素来调整合金成分。
合金化反应可以通过添加合金块、废钢等方式实现。
通过以上化学反应的组合,转炉炼钢可以控制合金成分、去除杂质、调整温度等,从而得到符合要求的钢铁产品。
二、转炉炼钢工艺介绍转炉炼钢的工艺可以分为以下几个主要步骤:1.预处理:生铁、废钢等原料经过破碎、除尘等处理后,进入转炉炉前料斗。
2.加料:原料从炉前料斗通过螺旋输送机被输送至转炉炉缸中。
3.预热:将炉缸中的原料进行预热,以提高反应效果。
4.吹炼:将炉底引入的高纯氧吹入炉缸中,通过氧化反应和还原反应去除杂质、调整合金成分。
5.加料:在吹炼过程中,适量添加合金块、废钢等调整合金成分。
6.测温:通过测温仪器监测和调节炉内温度。
7.出渣:通过倾炉装置将产生的渣浆从转炉中排出。
8.抽炉:将炉内得到的钢液通过倾炉装置倾出,并进行钢液处理(如脱氧、出气、精炼等)9.浇铸:将经过处理的钢液进行浇铸,得到需要的钢铁产品。
三、转炉炼钢的优势转炉炼钢工艺具有以下几个优势:1.高效:转炉炼钢的操作灵活,能够快速调整合金成分和生产规格,生产效率高。
2.资源利用:转炉炼钢可以利用废钢等再生资源,减少资源浪费。
3.环保:转炉炼钢排放的烟尘、废气等污染物可以通过环保设施进行处理,达到环保要求。
- 1、下载文档前请自行甄别文档内容的完整性,平台不提供额外的编辑、内容补充、找答案等附加服务。
- 2、"仅部分预览"的文档,不可在线预览部分如存在完整性等问题,可反馈申请退款(可完整预览的文档不适用该条件!)。
- 3、如文档侵犯您的权益,请联系客服反馈,我们会尽快为您处理(人工客服工作时间:9:00-18:30)。
脱氧及合金化
脱氧
吹炼终点钢水 [O]=0.02~0.08%, 向 钢 中 加 入一种(或几种)与氧亲和力 比 Fe 大 的 元 素 , 常 用 脱 氧 剂 Fe-Si 、 Fe-Mn 、 Al 、 Si-AlCa、Si-Al-Ba等;
合金化
向钢水中加入合金元素使其 达到成品钢成分要求
❖ 供料系统 ❖ 转炉系统 ❖ 供气系统 ❖ 净化系统 ❖ 辅助设备
炼钢原料
转炉炼钢的原材料分为金属料、非金属料和气 体。金属料包括铁水、废钢、铁合金,非金属料包 括造渣料、熔剂、冷却剂,气体包括氧气、氮气、 氩气、二氧化碳等。非金属料是在转炉炼钢过程 中 为了去除磷、硫等杂质,控制好过程温度而加入的 材料。主要有造渣料(石灰、白云石),熔剂(萤 石、氧化铁皮),冷却剂(铁矿石、石灰石、废 钢),增碳剂和燃料(焦炭、石墨籽、煤块、重 油)。
(3)基建投资和生产费用低 纯氧顶吹转炉的基 建投资相当于同样生产量的平炉车间的60~70%, 生产费用也低于平炉。
温度制度
随铁水中元素氧 化,金属液相线温度升 高,浇注也要求过热度, 升温是炼钢重要任务 之一.
出钢温度T的确定:
T= 浇 注 钢 种 液 相 线 温 度 + 浇 注过热度+钢水镇静及炉 外精炼温度降+出钢温度 降
出钢
出钢过程
先测定[C]、[P]、 [S]及T,判断是否满足 出钢要求,否则补吹;采 用挡渣技术与红包出 钢.
转炉设备
转炉冶炼的基本原理 ----物料平衡及热平衡
纯氧顶吹转炉炼钢优点
(1)生产速度快 因为用纯氧吹炼,会高速降碳, 快速提温,大大缩短冶炼时间。。
(2)品种多、质量好 纯氧顶吹转炉既能炼普通 钢,也能炼普通低碳钢。如首钢采用这种方法成功 地试炼了一百多种钢材。用纯氧吹炼,钢中氮、氢 等有害气体含量较低。
转炉一炉钢的基本冶炼过程
(1)上炉出钢、倒渣,检查炉衬和倾动设备等并进行必要的修补和修理; (2)倾炉,加废钢、兑铁水,摇正炉体(至垂直位置); (3)降枪开吹,同时加入第一批渣料(起初炉内噪声较大,从炉口冒出赤
色烟雾,随后喷出暗红的火焰;3~5min后硅锰氧接近结束,碳氧反应 逐渐激烈,炉口的火焰变大,亮度随之提高;同时渣料熔化,噪声减 弱); (4)3~5min后加入第二批渣料继续吹炼(随吹炼进行钢中碳逐渐降低, 约12min后火焰微弱,停吹); (5)倒炉,测温、取样,并确定补吹时间或出钢; (6)出钢,同时(将计算好的合金加入钢包中)进行脱氧合金化。
入氧气体积; 供氧强度:单位时间向熔池吨
钢提供氧气的体积; 氧气工作压力:设定压力测定
点的氧气压力(0.8~1.2MPa); 枪位:喷头至静止金属熔池液
面的距离(化渣枪位、基本 吹炼枪位、拉碳枪位)
供气制度(底部供气)
底பைடு நூலகம்类型
非氧化性气体:Ar、N2
氧化性气体:O2、CO2、空气
底吹过程
吹炼前期N2搅拌,后期N2、Ar 切换;底部供气强度 ≯0.3Nm3/t.min
转炉炼钢主要过程及特点
刘莉莉 115611002
转炉炼钢
转炉炼钢(converter steelmaking)是以铁水、 废钢、铁合金为主要原料,不借助外加能源,靠铁 液本身的物理热和铁液组分间化学反应产生热量而 在转炉中完成炼钢过程。转炉按耐火材料分为酸性 和碱性,按气体吹入炉内的部位有顶吹、底吹和侧 吹;按气体种类为分空气转炉和氧气转炉。碱性氧 气顶吹和顶底复吹转炉由于其生产速度快、产量大, 单炉产量高、成本低、投资少,为目前使用最普遍 的炼钢设备。转炉主要用于生产碳钢、合金钢及铜 和镍的冶炼 。
转炉炼钢生产工艺
❖ 装料制度 ❖ 造渣制度 ❖ 供气制度 ❖ 温度制度 ❖出 钢 ❖ 脱氧及合金化
装料制度
❖
装入量是指每炉装
入的铁水和废钢的总量,一
般废钢占15~30%,装入量分
为三种形式:
❖ 1.定量装入:整个炉役期保 持每炉的金属装入量不变;
❖ 2.定深装入:随容积的扩大 而增加装入量,保持熔池的 深度不变;
❖ 3.渣中(MgO):为防止炉渣侵蚀炉衬, 造渣时加入含镁材料,一般终渣(MgO) 为6~8%,采用溅渣护炉则8~10%.
❖ 4.造渣方法:单渣法、双渣法、双渣 留渣法.渣料分批加入,开吹时加入 1/2~1/3,其余分批加入.
❖ 顶部供气
供气制度
❖ 底部供气
供气制度(顶部供气)
供氧操作控制以下参数: 氧气流量:单位时间向熔池吹
❖ 3.分阶段定量装入:将整个 炉役分为若干阶段,每阶段 定量装入.
造渣制度
❖
造渣制度包括以下内容:
❖ 1.炉渣碱度和石灰加入量:碱度指渣 中碱性氧化物/酸性氧化物,一般为 2.5~4.0,高[S]、[P]铁水控制在 3.5~4.0,吨钢石灰消耗70~80kg
❖ 2:炉渣氧化性:用∑(%FeO)表示,高利 于成渣,脱P,但降低金属回收率.一般 初期高,终点15%左右,[C]、[P]要求 高时,控制在20~25%。