炼钢工艺的发展历程
炼钢的发展历史

04 炼钢技术发展展望
高纯净度钢的研发
高纯净度钢
随着科技的发展,高纯净度钢的需求量 越来越大,其研发成为炼钢技术的重要 发展方向。高纯净度钢具有更高的强度 、韧性和耐腐蚀性,广泛应用于汽车、 建筑、石油化工等领域。
VS
研发进展
目前,国内外钢铁企业正在加大高纯净度 钢的研发力度,通过优化炼钢工艺、选用 高品质原料、加强质量检测等方式,不断 提高高纯净度钢的性能和品质。
高效、低能耗炼钢技术
高效炼钢
为了提高炼钢效率,降低生产成本, 钢铁企业不断探索高效炼钢技术。通 过改进炼钢设备、优化炼钢流程、提 高自动化水平等方式,实现炼钢周期 的缩短和产量的提高。
生铁技术
生铁技术出现在公元前3世纪左 右,是中国古代炼钢技术的重 大突破。
生铁技术采用高炉炼铁,将铁 矿石和焦炭放入高炉中,通过 高温还原反应将铁矿石还原成 生铁。
生铁具有较高的碳含量和杂质 含量,需要通过反复锻打和渗 碳来提高质量。
熟铁技术
熟铁技术出现在公元10世纪左右,是 生铁技术的进一步发展。
电弧炉炼钢
总结词
灵活性、环保、高品质
详细描述
电弧炉炼钢是一种灵活性的炼钢方法,通过使用电弧炉将废钢铁熔化并除去杂质,得到高品质的钢水 。这种方法具有环保、高品质等优点,但成本相对较高,主要用于特殊钢材的冶炼。
03 现代炼钢技术
氧气顶吹转炉炼钢
氧气顶吹转炉炼钢技术是一种现代化的炼钢工艺,通过向熔 融钢液中吹入氧气,使钢液中的杂质和有害元素氧化,从而 得到纯净的钢水。这种技术具有高效、低耗、环保等优点, 已成为现代钢铁工业的主要炼钢方法之一。
炼钢工艺简介(1)
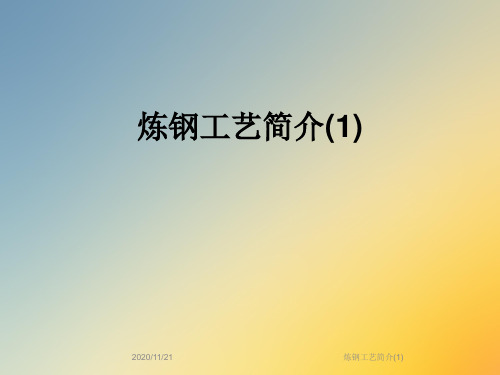
氧气顶吹转炉炼钢法的特点
• 利于自动化生产和开展综合利用 • 氧气顶吹转炉炼钢冶炼时间短,生产率高
,其机械化程度较高,有利于实现生产过程 的自动化,也有利于开展综合利用,如回收 煤气、炉尘(做烧结矿原料)等。
炼钢工艺简介(1)
四、炼钢基本原理
炼钢基本原理
一、什么叫钢
一般把碳小于2.11%的铁碳合金称为钢。 二、什么叫炼钢
炼钢工艺简介(1)
氧气顶吹转炉炼钢法的特点
• 原料消耗少,热效率高、成本低 • 氧气顶吹转炉炼钢的金属消耗一般为1100~1140
公斤/吨钢,稍高于平炉(但在良好燥作情况下 ,金属消耗与平炉接近)。但由于顶吹转炉的热 源是利用铁水本身的物理热和化学热,热效率高 ,不需外加热源,因此在燃料和动力消耗方面均 较平炉、电炉低。由于氧气顶吹转炉炼钢法具有 高的生产率和低的消耗,所以钢的成本也较低。
四、一炼钢技术经济指标
一炼钢在今年前几个月与国内部分同类生产厂指标相比, 在钢铁料消耗、日历作业率上差别较大.而与全国平均水平相 比各项指标均好于同时期的全国平均水平。 ➢ 钢铁料消耗比莱钢高21kg/t,比全国平均低了7.4 kg/t ➢ 日历作业率上比南京低15.56%,比全国平均高2.64% ➢ 氧气消耗比莱钢高3.78m3/t,比全国平均低3.85m3/t。 ➢ 转炉冶炼周期比安阳多1.56min,比全国平均低6.9min。 ➢ 炉衬寿命比莱钢略低。 ➢ 具体对比数据见附表。
➢音频化渣技术:2000年转炉与上海工业大学合作开发的音 频化渣技术,该项技术能根据炉内反应的声音,分析炉渣 的性质,及时指导氧枪枪位控制,促进化渣
炼钢工艺简介(1)
➢ 转炉数据静态模拟控制:2001年,转炉与上海阿塞克自动 化公司合作,开发出转炉数据静态模拟控制系统,使小转炉 炼钢局部实现自动化,降低了劳动强度,改善了生产环境, 提高了转炉作业率及生产效率。
炼钢技术的发展史
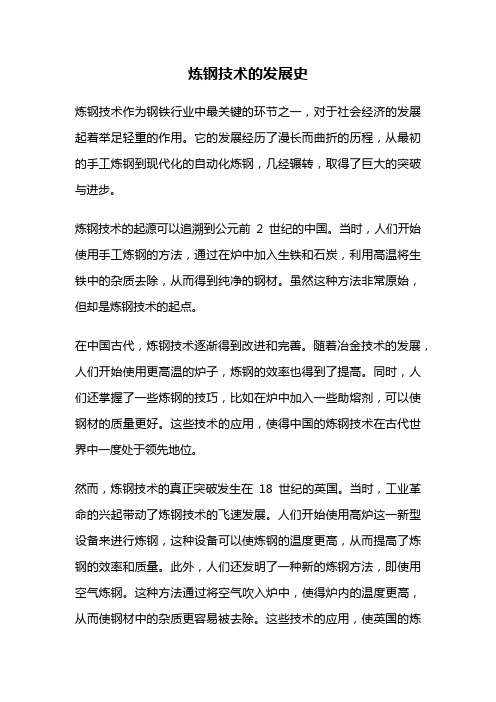
炼钢技术的发展史炼钢技术作为钢铁行业中最关键的环节之一,对于社会经济的发展起着举足轻重的作用。
它的发展经历了漫长而曲折的历程,从最初的手工炼钢到现代化的自动化炼钢,几经辗转,取得了巨大的突破与进步。
炼钢技术的起源可以追溯到公元前2世纪的中国。
当时,人们开始使用手工炼钢的方法,通过在炉中加入生铁和石炭,利用高温将生铁中的杂质去除,从而得到纯净的钢材。
虽然这种方法非常原始,但却是炼钢技术的起点。
在中国古代,炼钢技术逐渐得到改进和完善。
随着冶金技术的发展,人们开始使用更高温的炉子,炼钢的效率也得到了提高。
同时,人们还掌握了一些炼钢的技巧,比如在炉中加入一些助熔剂,可以使钢材的质量更好。
这些技术的应用,使得中国的炼钢技术在古代世界中一度处于领先地位。
然而,炼钢技术的真正突破发生在18世纪的英国。
当时,工业革命的兴起带动了炼钢技术的飞速发展。
人们开始使用高炉这一新型设备来进行炼钢,这种设备可以使炼钢的温度更高,从而提高了炼钢的效率和质量。
此外,人们还发明了一种新的炼钢方法,即使用空气炼钢。
这种方法通过将空气吹入炉中,使得炉内的温度更高,从而使钢材中的杂质更容易被去除。
这些技术的应用,使英国的炼钢技术在世界范围内取得了领先地位,为工业革命的进一步发展提供了强大的动力。
随着科学技术的不断进步,炼钢技术在20世纪得到了进一步的发展。
人们提出了一种新的炼钢方法,即使用电炉炼钢。
这种方法利用电能产生高温,使炼钢的过程更加精确和可控,从而提高了炼钢的效率和质量。
与此同时,人们还发明了一种新的炼钢设备,即连铸机。
这种设备可以将炼钢后的钢水直接浇铸成坯料,大大提高了生产效率。
这些技术的引入,使得炼钢技术进入了一个新的时代,为钢铁行业的发展带来了革命性的变革。
近年来,随着信息技术的不断发展,炼钢技术也在不断创新。
人们开始使用先进的自动化设备和控制系统,实现炼钢过程的自动化和智能化。
同时,人们还利用大数据和人工智能等技术,对炼钢过程进行优化和精确控制,提高了炼钢的效率和质量。
炼铁的发展历史
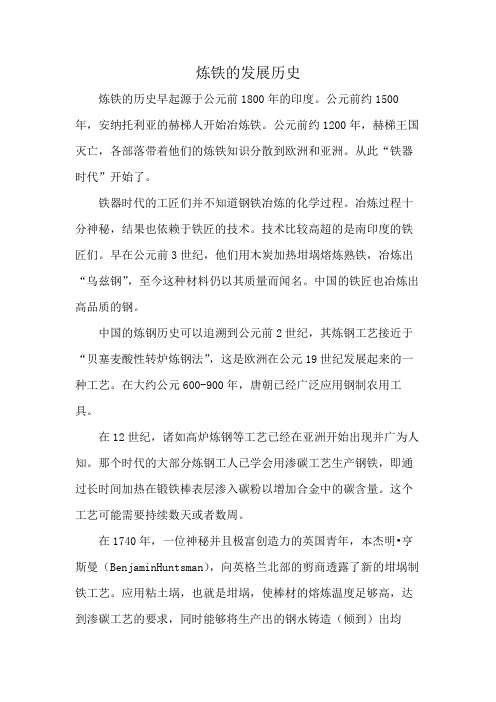
炼铁的发展历史炼铁的历史早起源于公元前1800年的印度。
公元前约1500年,安纳托利亚的赫梯人开始冶炼铁。
公元前约1200年,赫梯王国灭亡,各部落带着他们的炼铁知识分散到欧洲和亚洲。
从此“铁器时代”开始了。
铁器时代的工匠们并不知道钢铁冶炼的化学过程。
冶炼过程十分神秘,结果也依赖于铁匠的技术。
技术比较高超的是南印度的铁匠们。
早在公元前3世纪,他们用木炭加热坩埚熔炼熟铁,冶炼出“乌兹钢”,至今这种材料仍以其质量而闻名。
中国的铁匠也冶炼出高品质的钢。
中国的炼钢历史可以追溯到公元前2世纪,其炼钢工艺接近于“贝塞麦酸性转炉炼钢法”,这是欧洲在公元19世纪发展起来的一种工艺。
在大约公元600-900年,唐朝已经广泛应用钢制农用工具。
在12世纪,诸如高炉炼钢等工艺已经在亚洲开始出现并广为人知。
那个时代的大部分炼钢工人已学会用渗碳工艺生产钢铁,即通过长时间加热在锻铁棒表层渗入碳粉以增加合金中的碳含量。
这个工艺可能需要持续数天或者数周。
在1740年,一位神秘并且极富创造力的英国青年,本杰明•亨斯曼(BenjaminHuntsman),向英格兰北部的剪商透露了新的坩埚制铁工艺。
应用粘土埚,也就是坩埚,使棒材的熔炼温度足够高,达到渗碳工艺的要求,同时能够将生产出的钢水铸造(倾到)出均匀、高质量的铸锭,相对过去,该工艺提高了产量。
尽管亨斯曼的发明还未实现低成本、高产量地生产高品质钢的目标,仍需要后人继续努力。
但正是他的技术推动英国谢菲尔德成为19到20世纪大的炼钢中心之一。
工业革命是一个技术革新和创造层出不穷的时代,亨斯曼的坩埚技术只是这个时期众多发明中的一项。
工业革命起源于英国,其对世界范围内的制造、贸易和社会各领域产生了巨大影响。
工业革命始于18世纪,那时铁在工业领域独领风骚。
而到20世纪末,钢成为新的霸主,成为现代世界位于核心地位的金属材料。
蒸汽泵驱动水车发电,即使在枯水期也能为高炉提供动力。
焦炭和生铁供应充足,铁逐渐替代了木材成为建筑材料的新秀。
制钢工艺从初步冶炼到钢铁完整的演变历程
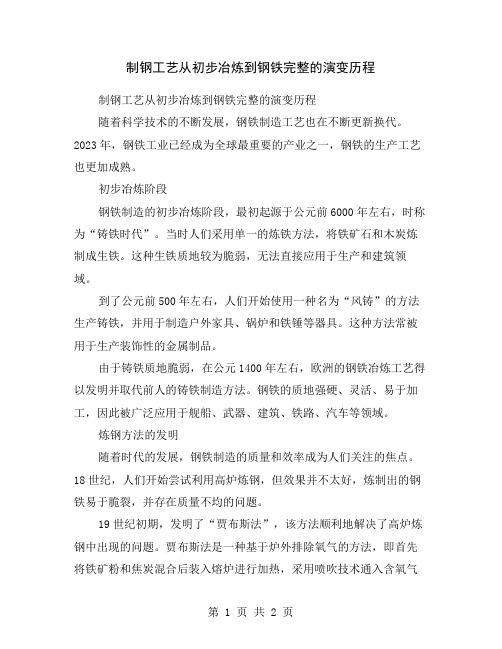
制钢工艺从初步冶炼到钢铁完整的演变历程制钢工艺从初步冶炼到钢铁完整的演变历程随着科学技术的不断发展,钢铁制造工艺也在不断更新换代。
2023年,钢铁工业已经成为全球最重要的产业之一,钢铁的生产工艺也更加成熟。
初步冶炼阶段钢铁制造的初步冶炼阶段,最初起源于公元前6000年左右,时称为“铸铁时代”。
当时人们采用单一的炼铁方法,将铁矿石和木炭炼制成生铁。
这种生铁质地较为脆弱,无法直接应用于生产和建筑领域。
到了公元前500年左右,人们开始使用一种名为“风铸”的方法生产铸铁,并用于制造户外家具、锅炉和铁锤等器具。
这种方法常被用于生产装饰性的金属制品。
由于铸铁质地脆弱,在公元1400年左右,欧洲的钢铁冶炼工艺得以发明并取代前人的铸铁制造方法。
钢铁的质地强硬、灵活、易于加工,因此被广泛应用于舰船、武器、建筑、铁路、汽车等领域。
炼钢方法的发明随着时代的发展,钢铁制造的质量和效率成为人们关注的焦点。
18世纪,人们开始尝试利用高炉炼钢,但效果并不太好,炼制出的钢铁易于脆裂,并存在质量不均的问题。
19世纪初期,发明了“贾布斯法”,该方法顺利地解决了高炉炼钢中出现的问题。
贾布斯法是一种基于炉外排除氧气的方法,即首先将铁矿粉和焦炭混合后装入熔炉进行加热,采用喷吹技术通入含氧气的空气,原材料中的碳和铁被氧气氧化并排出炉外,同时会产生大量的热量,熔炉内的温度大大提高,钢铁得以熔化。
这种方法使钢铁的质量得到显著提高。
自动化生产的挑战21世纪的现在,钢铁制造技术已经高度自动化,从事钢铁生产的人员减少,自动化的生产设备更加高效。
智能制造技术对于工艺流程的监测、控制和优化等方面有着优异的表现。
在此过程中,智能设备不仅能够实现材料的自动调配,而且还能够自动监测过程中的参数以确保质量和工艺的稳健性,保证了生产线的持续性和效率。
这使得钢铁生产商能够实现产量的扩张,并高效地向客户提供产品,从而获得更大的收益。
未来的展望钢铁生产技术发生了重大变化,随着数字化和智能化技术的不断进步,钢铁生产的工艺进一步升级,并且将变得更加智能化和自动化。
金属冶炼的发展历程与前景展望

未来金属冶炼行业将朝着绿色化、智能化、高效化的方向发展,市场规模有望进一 步扩大。
工业发展:随着工业化进程的加速,对金属材料的需求不断增长 基础设施建设:建设交通、能源、通讯等基础设施需要大量金属材料 汽车制造业:汽车制造业的发展对金属材料的需求不断攀升 电子产品制造:随着电子产品更新换代加速,对金属材料的需求持续增长
属
电化学冶炼: 利用电解原理 将金属从矿石
中提取出来
真空蒸馏法: 在真空条件下 通过蒸馏的方
法提取金属
钢铁冶炼:以铁矿石和焦炭为主要原料,通过高炉熔炼而成。 铝冶炼:采用电解铝的方法,以氧化铝和碳素材料为原料,通过电解过程获得铝。 铜冶炼:以铜矿石为原料,通过火法或湿法冶金过程提取纯铜。 钛冶炼:以钛矿石为原料,通过氯化、镁还原等过程制备纯钛。
金属冶炼的发展历程 与前景展望
汇报人:
目录
添加目录标题
金属冶炼的历史
金属冶炼的种类与 工艺
金属冶炼的市场与 需求
金属冶炼的挑战与 前景
添加章节标题
金属冶炼的历史
铜器时代:使用天然铜和陨铁制作工具和武器
铁器时代:公元前1000年左右,炼铁技术出现,铁器逐渐普及
炼钢技术:18世纪中叶,贝塞麦转炉炼钢法和托马斯平炉炼钢法发明,提高钢铁 质量和产量
资源循环利用:加强金属冶炼过程中的资源循环利用,减少对自然资源的依赖,实现 可持续发展。
政策支持:政府应加大对金属冶炼行业的政策支持,鼓励企业进行环保技术创新,推 动行业的可持续发展。
感谢您的观看
汇报人:
技术创新不断涌现:金属冶炼行业持续进行技术创新,如采用新型熔炼技术、降低能耗和排放、提高金属回收率 等,为行业的可持续发展提供了有力支撑。
炼钢工艺的发展历程
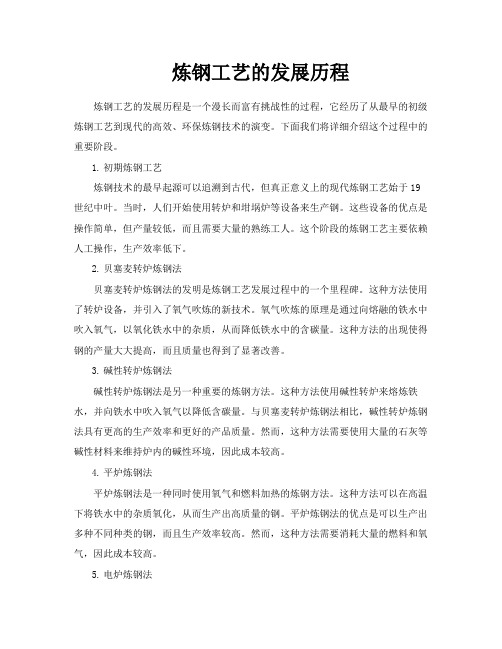
炼钢工艺的发展历程炼钢工艺的发展历程是一个漫长而富有挑战性的过程,它经历了从最早的初级炼钢工艺到现代的高效、环保炼钢技术的演变。
下面我们将详细介绍这个过程中的重要阶段。
1.初期炼钢工艺炼钢技术的最早起源可以追溯到古代,但真正意义上的现代炼钢工艺始于19世纪中叶。
当时,人们开始使用转炉和坩埚炉等设备来生产钢。
这些设备的优点是操作简单,但产量较低,而且需要大量的熟练工人。
这个阶段的炼钢工艺主要依赖人工操作,生产效率低下。
2.贝塞麦转炉炼钢法贝塞麦转炉炼钢法的发明是炼钢工艺发展过程中的一个里程碑。
这种方法使用了转炉设备,并引入了氧气吹炼的新技术。
氧气吹炼的原理是通过向熔融的铁水中吹入氧气,以氧化铁水中的杂质,从而降低铁水中的含碳量。
这种方法的出现使得钢的产量大大提高,而且质量也得到了显著改善。
3.碱性转炉炼钢法碱性转炉炼钢法是另一种重要的炼钢方法。
这种方法使用碱性转炉来熔炼铁水,并向铁水中吹入氧气以降低含碳量。
与贝塞麦转炉炼钢法相比,碱性转炉炼钢法具有更高的生产效率和更好的产品质量。
然而,这种方法需要使用大量的石灰等碱性材料来维持炉内的碱性环境,因此成本较高。
4.平炉炼钢法平炉炼钢法是一种同时使用氧气和燃料加热的炼钢方法。
这种方法可以在高温下将铁水中的杂质氧化,从而生产出高质量的钢。
平炉炼钢法的优点是可以生产出多种不同种类的钢,而且生产效率较高。
然而,这种方法需要消耗大量的燃料和氧气,因此成本较高。
5.电炉炼钢法随着电力技术的发展,电炉炼钢法逐渐成为了主流的炼钢方法。
这种方法使用电能来熔化铁水,并向铁水中吹入氧气以降低含碳量。
电炉炼钢法的优点是可以实现自动化操作,提高生产效率,而且产品质量也得到了显著改善。
此外,由于电能的价格相对较为稳定,因此电炉炼钢法的成本也较为可控。
6.现代炼钢工艺近年来,随着环保意识的提高和能源价格的上涨,现代炼钢工艺开始朝着高效、环保的方向发展。
其中,最具有代表性的技术包括:连铸技术、连轧技术、循环利用技术等。
古代炼钢技术

古代炼钢技术引言:炼钢是一项古老而重要的冶金技术,古代人们通过不断探索和实践,逐渐发展出了独特的炼钢工艺。
本文将从古代炼钢的起源、工艺流程以及对社会经济的影响等方面进行探讨。
一、古代炼钢的起源古代炼钢技术的起源可以追溯到公元前6世纪的中国。
据史书记载,当时的中国冶金学家在铁制品的生产过程中,意外发现了一种可以提高铁质品质的方法。
这一方法后来被称为“炼钢”。
二、古代炼钢的工艺流程古代炼钢的工艺流程相对简单,主要包括矿石选矿、炼铁、炼钢等环节。
1. 矿石选矿古代炼钢首先需要选取合适的矿石。
常用的矿石有铁矿石、锰矿石等。
选矿的原则是优先选择含铁量高、杂质较少的矿石。
2. 炼铁炼钢的第一步是炼铁。
古代人们使用的主要炼铁方法是青铜法。
这种方法是将铁矿石与富含铜的青铜矿石一起熔炼,使铁与铜发生反应生成铁铜合金,再通过特殊的冶炼工艺将铁铜合金中的铜去除,得到纯净的铁。
3. 炼钢在获得纯净的铁后,古代人们进行炼钢。
炼钢的方法有多种,其中最为常见的是碳化法和火焰法。
碳化法是将铁与含碳物质如木炭等混合加热,使铁中的碳含量增加,从而提高铁的质量。
火焰法则是将铁放入高温炉中,通过燃烧炉内的燃料产生的高温使铁融化,然后通过控制冷却速度,使铁内部的晶体结构得到重新排列,从而改善铁的性能。
三、古代炼钢对社会经济的影响古代炼钢技术的发展对社会经济产生了深远的影响。
古代炼钢技术的出现提高了铁器的质量和产量,使得铁器逐渐替代青铜器成为主流。
铁器的出现极大地改善了人们的生活,推动了农业、手工业和交通运输等领域的发展。
炼钢技术的发展使得古代冶金工艺逐渐完善,为后来冶金学的发展奠定了基础。
古代炼钢技术的经验和知识被传承并发展,为后来的冶金学家提供了宝贵的借鉴和启示。
古代炼钢技术的发展也推动了冶铁业的繁荣。
冶铁业的兴盛带动了相关产业的发展,如采矿业、运输业等,为社会经济的发展做出了重要贡献。
结语:古代炼钢技术是人类智慧的结晶,为社会经济的发展做出了重要贡献。
中国古代的钢铁冶炼技术简史
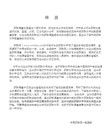
中国古代钢铁发展的特点与其他各国不同。世界上长期采用固态还原的块炼铁和固体渗碳钢,而中国铸铁和生铁炼钢一直是主要方法。由于铸铁和生铁炼钢法的发明与发展,中国的冶金技术在明代中叶以前一直居世界先进水平。
我国古代炼钢技术至迟发明于春秋晚期。由先秦到西汉中晚期,主要制钢工艺是块铁渗碳法;由汉代到明清,主要又是炒钢法和灌钢法,其次还有百炼钢法和炒铁渗碳法,汉魏南北朝时还有“铸铁脱碳钢”,汉代还有坩埚炼钢法。炒钢工艺主要生产一般的可锻铁(包括钢和熟铁),灌钢工艺主要生产含碳较高的刃钢,百炼钢是对普通炒钢的再加工。
到了晋朝又发明了 “灌钢法”,这是中国古代炼钢技术的又一重大成就,采用这种炼铁法为原料制造出来的刀,就是著名的优质兵器――“宿铁刀”。
把加热的铁急剧冷却,提高硬度的淬火技术,早在中国的古代就为人们所掌握,并普遍采用这种处理方法来提高兵刃的硬度。中国人发明了用不同的液体来淬火,从而提高兵刃质量的方式。其中包括用不同河流,不同月份的水。而且还把野兽的尿液和脂肪作为冷却剂,用于淬火处理上,起到了惊人的效果。
此外,在中国很早的古代就掌握了把加热的铁漫漫冷却处理的回火技术,并广泛用于不同用途的兵器的制造中。
据〈中华百科要览〉记载:中国是最早用煤炼铁的国家,汉代时已经试用,宋、元时期已普及。到明代(公元1368~1644年)已能用焦炭冶炼生铁。
中国的生铁炼钢 生铁和韧性铸铁的大规模生产导致了生铁制钢的发明。在汉代先后发明了以下几种生铁制钢的方法。
灌钢 中国生铁制钢技术自战国初期到汉代经过几百年的历程,从块炼铁、渗碳炼钢发展到生铁固体脱碳炼钢、炒钢、炼制熟铁,以及重新渗碳硬化或淬火硬化。在这个基础上,发明了利用液态生铁对熟铁进行扩散渗碳炼钢的方法。这一方法的最早记载见于《北齐书·綦母怀文传》,称为“宿铁”,后世称为灌钢,又称团钢。这是中国古代炼钢技术的又一重大成就。
炼钢的过程
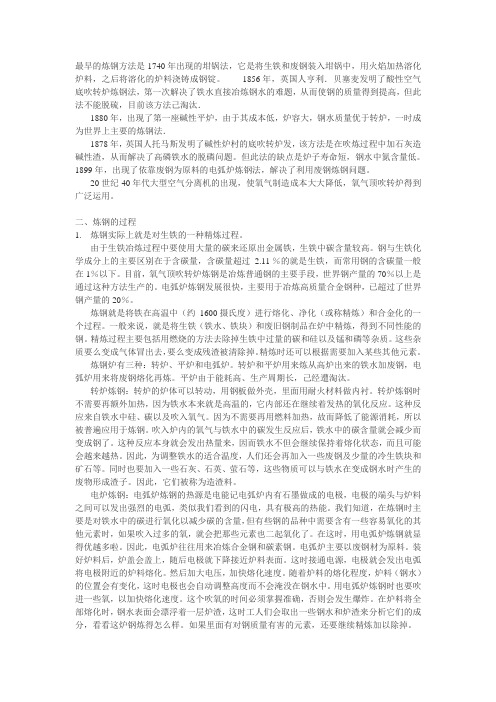
最早的炼钢方法是1740 年出现的坩锅法,它是将生铁和废钢装入坩锅中,用火焰加热溶化炉料,之后将溶化的炉料浇铸成钢锭。
1856 年,英国人亨利.贝塞麦发明了酸性空气底吹转炉炼钢法,第一次解决了铁水直接冶炼钢水的难题,从而使钢的质量得到提高,但此法不能脱硫,目前该方法己淘汰.1880 年,出现了第一座碱性平炉,由于其成本低,炉容大,钢水质量优于转炉,一时成为世界上主要的炼钢法.1878 年,英国人托马斯发明了碱性炉村的底吹转炉发,该方法是在吹炼过程中加石灰造碱性渣,从而解决了高磷铁水的脱磷问题。
但此法的缺点是炉子寿命短,钢水中氮含量低。
1899 年,出现了依靠废钢为原料的电弧炉炼钢法,解决了利用废钢炼钢问题。
20 世纪40 年代大型空气分离机的出现,使氧气制造成本大大降低,氧气顶吹转炉得到广泛运用。
二、炼钢的过程1.炼钢实际上就是对生铁的一种精炼过程。
由于生铁冶炼过程中要使用大量的碳来还原出金属铁,生铁中碳含量较高。
钢与生铁化学成分上的主要区别在于含碳量,含碳量超过 2.11 %的就是生铁,而常用钢的含碳量一般在1%以下。
目前,氧气顶吹转炉炼钢是冶炼普通钢的主要手段,世界钢产量的70%以上是通过这种方法生产的。
电弧炉炼钢发展很快,主要用于冶炼高质量合金钢种,已超过了世界钢产量的20%。
炼钢就是将铁在高温中(约1600 摄氏度)进行熔化、净化(或称精炼)和合金化的一个过程。
一般来说,就是将生铁(铁水、铁块)和废旧钢制品在炉中精炼,得到不同性能的钢。
精炼过程主要包括用燃烧的方法去除掉生铁中过量的碳和硅以及锰和磷等杂质。
这些杂质要么变成气体冒出去,要么变成残渣被清除掉。
精炼时还可以根据需要加入某些其他元素。
炼钢炉有三种:转炉、平炉和电弧炉。
转炉和平炉用来炼从高炉出来的铁水加废钢,电弧炉用来将废钢熔化再炼。
平炉由于能耗高、生产周期长,己经遭淘汰。
转炉炼钢:转炉的炉体可以转动,用钢板做外壳,里面用耐火材料做内衬。
炼钢工艺——精选推荐

炼钢⼯艺1 炼钢⼯艺发展概述亨利·贝塞麦于1855年发明了酸性空⽓底吹转炉炼钢法,⾸次解决了⽤铁⽔冶炼液态钢的问题,使得炼钢⽣产的质量、产量实现了跨越性质的提⾼。
相隔10年之后,法国⼈马丁利⽤蓄热池原理发明了平炉炼钢法。
由于平炉炼钢法适应于各种原材料条件(铁⽔和废钢可⽤任何⽐例),平炉炼钢法长期占居炼钢⼯艺主导地位,平炉钢占全世界总产钢量的80%以上。
湘钢在1999年以前⼀直处于这种局⾯:平炉—→模铸—→初轧开坯—→模列式轧机—→普通线材,采⽤多⽕成材⼯艺,成本消耗偏⾼,多项技术经济指标在全国冶⾦⾏业内排名⼀直靠后。
1940年代,⼤型空⽓分离机问世后,能够提供⾼纯度、⼤量廉价的氧⽓,随后诞⽣了氧⽓顶吹转炉。
1952年在奥地利林茨城和1953年在多纳维茨城先后建成了30吨的转炉车间并投⼊⼯业⽣产。
由于转炉⽣产率⾼,成本低,质量较⾼,投资低于平炉,便于实现⾃动化,因此在世界上发展迅速,并逐步取代了平炉。
回顾⼆炼钢⼚⾃1996年8⽉1#转炉投产以来的发展进程及其对于湘钢的⽣存环境所带来的影响,也印证了这⼀规律。
⾃从20世纪开始发展电炉炼钢,该⼯艺长期以来⼀直作为熔炼特殊钢和⾼合⾦钢的⽅法。
由于质量要求很⾼和市场需求巨⼤,伴随电⼒⼯业技术进步和供电能⼒提⾼,采⽤超⾼功率电弧炉和炉外精炼技术已经成为国内外应⽤⽇益⼴泛的冶⾦⽣产⽅式。
我国电⼒建设的⼤发展,电弧炉炼钢⼯艺也将逐步改变其⽬前状况。
氧⽓转炉炼钢⼯艺已成为⽬前世界上最为主要的炼钢⽅法,即使到21世纪的前期,转炉钢的⽣产⽐例仍将保持在60~70%。
回顾50年氧⽓转炉炼钢发展史,可以划分为三个发展时期:转炉⼤型化时期(1950~1970年)这⼀历史时期,以转炉⼤型化为技术核⼼,逐步完善转炉炼钢⼯艺与设备。
先后开发出⼤型转炉设计制造技术、OG除尘与煤⽓回收技术、计算机⾃动与副枪动态控制技术、镁碳砖综合砌炉与喷补挂渣等护炉技术,转炉炉龄达到2000炉。
铁的冶炼发展历程
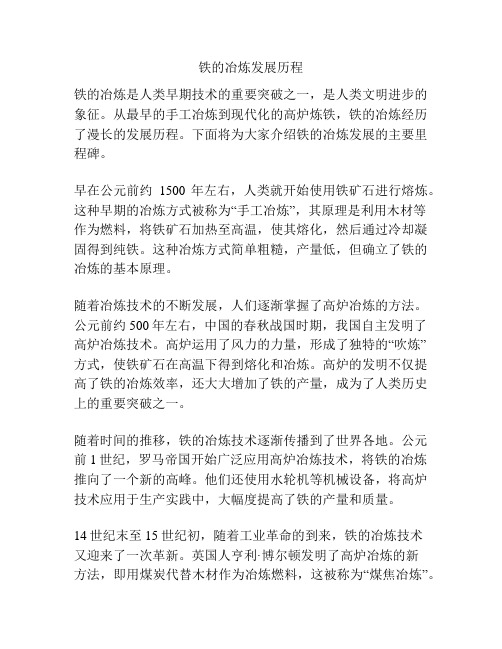
铁的冶炼发展历程铁的冶炼是人类早期技术的重要突破之一,是人类文明进步的象征。
从最早的手工冶炼到现代化的高炉炼铁,铁的冶炼经历了漫长的发展历程。
下面将为大家介绍铁的冶炼发展的主要里程碑。
早在公元前约1500年左右,人类就开始使用铁矿石进行熔炼。
这种早期的冶炼方式被称为“手工冶炼”,其原理是利用木材等作为燃料,将铁矿石加热至高温,使其熔化,然后通过冷却凝固得到纯铁。
这种冶炼方式简单粗糙,产量低,但确立了铁的冶炼的基本原理。
随着冶炼技术的不断发展,人们逐渐掌握了高炉冶炼的方法。
公元前约500年左右,中国的春秋战国时期,我国自主发明了高炉冶炼技术。
高炉运用了风力的力量,形成了独特的“吹炼”方式,使铁矿石在高温下得到熔化和冶炼。
高炉的发明不仅提高了铁的冶炼效率,还大大增加了铁的产量,成为了人类历史上的重要突破之一。
随着时间的推移,铁的冶炼技术逐渐传播到了世界各地。
公元前1世纪,罗马帝国开始广泛应用高炉冶炼技术,将铁的冶炼推向了一个新的高峰。
他们还使用水轮机等机械设备,将高炉技术应用于生产实践中,大幅度提高了铁的产量和质量。
14世纪末至15世纪初,随着工业革命的到来,铁的冶炼技术又迎来了一次革新。
英国人亨利·博尔顿发明了高炉冶炼的新方法,即用煤炭代替木材作为冶炼燃料,这被称为“煤焦冶炼”。
这一新技术极大地丰富了原料来源,推动了铁的冶炼效率的大幅提升,加速了工业革命的进程。
到了18世纪末,人们又取得了对炼钢技术的突破。
英国的亨利·贝塞莫尔发明了气体熔融炼钢法,将工业生产中的铁炼制至钢的水平。
这种炼钢技术使铁产业得以进一步发展,为钢铁产业的崛起奠定了基础。
到了19世纪中叶,铁和钢的冶炼技术逐渐向现代化迈进。
人们利用焦炉、转炉、电炉等新型设备,进一步改良和提高了冶炼工艺。
此外,各国对铁和钢的冶炼技术进行了积极的研究与交流,推动了全球钢铁产业的不断发展。
在现代化工业技术的推动下,铁的冶炼也进一步实现了自动化和集约化。
钢铁冶金的发展历史

钢铁冶金的发展历史
钢铁冶金是人类历史上的重要发明之一,其发展历史可追溯到公元前3千年左右的铜器时代。
以下是钢铁冶金的发展历史:
1. 古代冶炼技术
最早的钢铁是由古代的中东地区采用冶铁技术制得的,这种钢铁叫做“大陆钢”,因为其产地集中在大陆地区。
大陆钢制造起来较为简单,通常采用炭火烧炼铁矿石,然后利用锻打工艺锤打铁块,最终得到钢铁。
2. 驱动力机械的革命性发展
17世纪末至18世纪初,欧洲的工业革命使得钢铁冶炼技术得到极大的改进,新的动力机械得到广泛应用,例如蒸汽机和水力机械。
随着机械的发展,一种新的化学结构被发现,即硼化钢,这种钢铁具有较好的硬度和韧性。
3. 高温炼铁技术的引入
20世纪初,高温炼铁技术被引入,这种技术可以高效地提取铁矿石中的铁,并且可以控制来自炉墙的热量。
这使得钢铁冶炼变得更加高效和经济。
此外,喷射式金属喷雾也被广泛应用,其可以将钢铁微粒化,使得其表面更平滑,更具韧性。
4. 钢铁制造的现代化
20世纪的钢铁制造变得越来越现代化,特别是在发达国家。
在德国和日本等国,高温炉的控制技术已经高度发展,大大提高了铁水质量,并缩短了炼钢时间,使得生产更加高效和经济。
此外,一种新的金属材料被发现,并被广泛应用于汽车和飞机制造等领域。
这种新材料就是钛合金,它比传统的钢铁具有更高的强度和更轻的重量。
综上所述,钢铁冶金的发展历史可以追溯到古代,经历了几千年的发展和变迁。
随着技术和工艺的不断改进,钢铁冶金得到进一步的提高和现代化,目前已经成为现代工业生产必不可少的重要材料。
炼钢历史的发展过程

炼钢历史的发展过程
近代主要的炼钢方法首推 1885 年在英国获得专利的贝 塞麦法,即酸性空气气底吹转炉炼钢 法 1865年开始生产的平炉炼钢法 1952年在奥地利首先投产的顶吹氧气转炉炼钢开 创了发展炼钢生产的新阶段。
三种主要方法
氧气底吹转炉:1968年以来,西欧在传统的托马斯转炉上发 展了底吹氧气转炉炼钢法处理铁水, 美国又进而在底吹氧气转炉上采 用喷石灰分吹炼低磷铁水。 底吹氧与LD相比, 具有对熔池搅拌强烈, 脱磷能力强,能冶炼超低碳钢,铁和猛地氧化损失较少,炉内反应平 稳,减少钢渣喷溅,脱氧、脱磷效果好,能用高磷生铁吹炼,更接近 平衡态等优越性 ,曾受到很多国家重视。 顶底复合吹炼: 在LD及底吹氧气的基础上, 出现了顶底复合吹 炼转炉炼钢法, 既有LD的特点又有底吹转炉的特点, 又克服了各自 的不足,因此,得到迅速发展。 电炉炼钢法:1904年出现了电弧炉, 它以废钢和铁水作为主 要原料,通过电弧加热获得高温,可控制炉内气氛,特别是适合冶炼 合金钢,尤其是高级合金钢和特殊钢,被各国普遍采用,产量稳定增 长。近年来,电弧炉炼钢除普遍氧强化外,有些国家还用大型超高功 率电弧炉(容量最大已达400T)生产普通碳素钢,与氧气转炉炼 钢相竞争。
钢铁冶炼技术发展历程
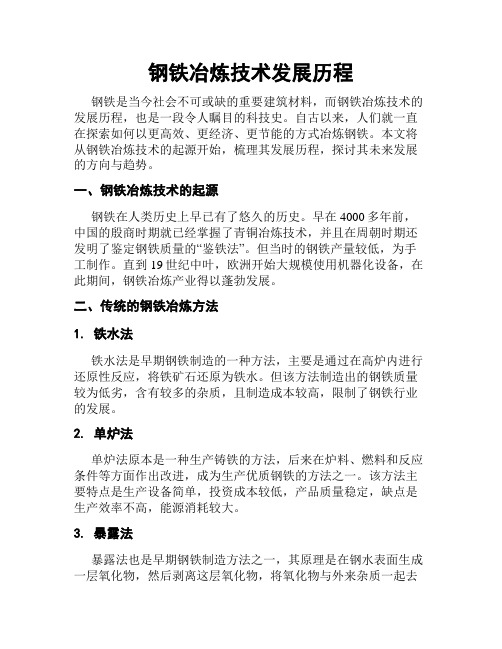
钢铁冶炼技术发展历程钢铁是当今社会不可或缺的重要建筑材料,而钢铁冶炼技术的发展历程,也是一段令人瞩目的科技史。
自古以来,人们就一直在探索如何以更高效、更经济、更节能的方式冶炼钢铁。
本文将从钢铁冶炼技术的起源开始,梳理其发展历程,探讨其未来发展的方向与趋势。
一、钢铁冶炼技术的起源钢铁在人类历史上早已有了悠久的历史。
早在4000多年前,中国的殷商时期就已经掌握了青铜冶炼技术,并且在周朝时期还发明了鉴定钢铁质量的“鉴铁法”。
但当时的钢铁产量较低,为手工制作。
直到19世纪中叶,欧洲开始大规模使用机器化设备,在此期间,钢铁冶炼产业得以蓬勃发展。
二、传统的钢铁冶炼方法1. 铁水法铁水法是早期钢铁制造的一种方法,主要是通过在高炉内进行还原性反应,将铁矿石还原为铁水。
但该方法制造出的钢铁质量较为低劣,含有较多的杂质,且制造成本较高,限制了钢铁行业的发展。
2. 单炉法单炉法原本是一种生产铸铁的方法,后来在炉料、燃料和反应条件等方面作出改进,成为生产优质钢铁的方法之一。
该方法主要特点是生产设备简单,投资成本较低,产品质量稳定,缺点是生产效率不高,能源消耗较大。
3. 暴露法暴露法也是早期钢铁制造方法之一,其原理是在钢水表面生成一层氧化物,然后剥离这层氧化物,将氧化物与外来杂质一起去除,达到提高钢铁质量的目的。
但该方法需要人工进行操作,不仅生产效率低,而且操作繁琐。
三、现代钢铁冶炼技术的发展1. 转炉法转炉法是一种在工业应用中非常成功的钢铁冶炼技术,被称为第二次工业革命的代表工艺之一。
该方法的主要优点是能大量生产高质量的钢铁,同时还能实现钢铁冶炼的自动化,大大提高生产效率。
2. 电弧炉法电弧炉法是20世纪初开发的一种钢铁制造技术,其主要原理是利用高强度电弧穿过钢铁熔体,以产生高热能并使杂质被氧化并消除。
这种方法具有生产效率高,产品质量稳定的特点,并且获得了过去无法预见的高品质优质钢铁。
3. 化学还原法化学还原法是指利用化学反应将铁矿石还原为铁水,主要原理是在还原气氛中将铁矿石还原为铁水。
钢铁冶炼工艺及其发展
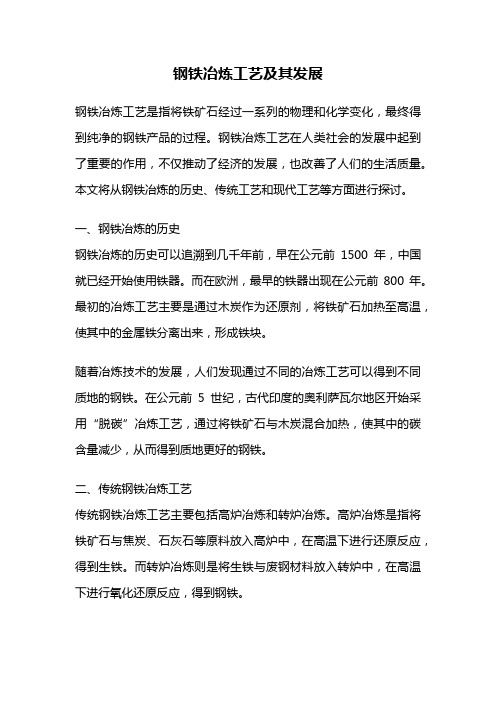
钢铁冶炼工艺及其发展钢铁冶炼工艺是指将铁矿石经过一系列的物理和化学变化,最终得到纯净的钢铁产品的过程。
钢铁冶炼工艺在人类社会的发展中起到了重要的作用,不仅推动了经济的发展,也改善了人们的生活质量。
本文将从钢铁冶炼的历史、传统工艺和现代工艺等方面进行探讨。
一、钢铁冶炼的历史钢铁冶炼的历史可以追溯到几千年前,早在公元前1500年,中国就已经开始使用铁器。
而在欧洲,最早的铁器出现在公元前800年。
最初的冶炼工艺主要是通过木炭作为还原剂,将铁矿石加热至高温,使其中的金属铁分离出来,形成铁块。
随着冶炼技术的发展,人们发现通过不同的冶炼工艺可以得到不同质地的钢铁。
在公元前5世纪,古代印度的奥利萨瓦尔地区开始采用“脱碳”冶炼工艺,通过将铁矿石与木炭混合加热,使其中的碳含量减少,从而得到质地更好的钢铁。
二、传统钢铁冶炼工艺传统钢铁冶炼工艺主要包括高炉冶炼和转炉冶炼。
高炉冶炼是指将铁矿石与焦炭、石灰石等原料放入高炉中,在高温下进行还原反应,得到生铁。
而转炉冶炼则是将生铁与废钢材料放入转炉中,在高温下进行氧化还原反应,得到钢铁。
传统冶炼工艺存在一些问题,如资源消耗大、能源浪费等。
因此,人们开始研究和开发新的冶炼工艺,以提高效率和降低能耗。
三、现代钢铁冶炼工艺现代钢铁冶炼工艺主要包括基本氧炉冶炼、电弧炉冶炼和气体还原法冶炼等。
基本氧炉冶炼是指将生铁和废钢放入基本氧炉中,在高温下进行氧化还原反应,得到高质量的钢铁产品。
这种冶炼工艺具有生产效率高、能源消耗低和环境污染少的特点,因此在现代钢铁工业中得到了广泛应用。
电弧炉冶炼是指通过电弧加热的方式将废钢材料熔化,并加入适量的合金元素,得到高品质的合金钢产品。
电弧炉冶炼工艺具有灵活性强、适应性广的特点,可以根据不同的需求生产出各种类型的钢材。
气体还原法冶炼是指利用氢气或甲烷等气体作为还原剂,将铁矿石加热至高温,使其还原生成金属铁。
这种冶炼工艺具有能源消耗低、环境友好等优点,逐渐得到了工业界的关注和应用。
中国转炉炼钢工艺的发展史
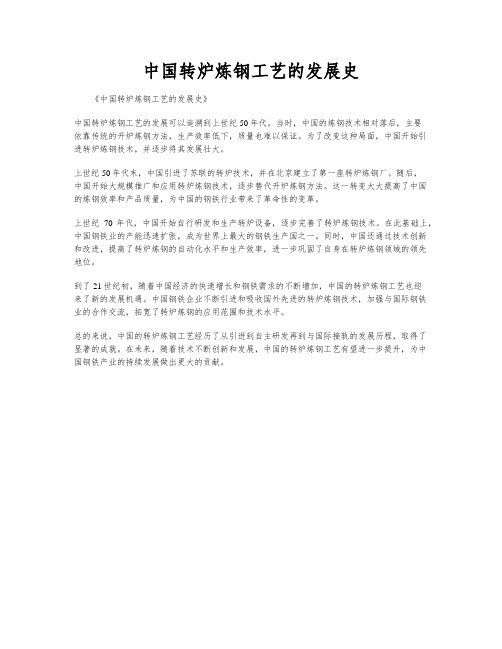
中国转炉炼钢工艺的发展史
《中国转炉炼钢工艺的发展史》
中国转炉炼钢工艺的发展可以追溯到上世纪50年代。
当时,中国的炼钢技术相对落后,主要
依靠传统的开炉炼钢方法,生产效率低下,质量也难以保证。
为了改变这种局面,中国开始引进转炉炼钢技术,并逐步将其发展壮大。
上世纪50年代末,中国引进了苏联的转炉技术,并在北京建立了第一座转炉炼钢厂。
随后,
中国开始大规模推广和应用转炉炼钢技术,逐步替代开炉炼钢方法。
这一转变大大提高了中国的炼钢效率和产品质量,为中国的钢铁行业带来了革命性的变革。
上世纪70年代,中国开始自行研发和生产转炉设备,逐步完善了转炉炼钢技术。
在此基础上,中国钢铁业的产能迅速扩张,成为世界上最大的钢铁生产国之一。
同时,中国还通过技术创新和改进,提高了转炉炼钢的自动化水平和生产效率,进一步巩固了自身在转炉炼钢领域的领先地位。
到了21世纪初,随着中国经济的快速增长和钢铁需求的不断增加,中国的转炉炼钢工艺也迎
来了新的发展机遇。
中国钢铁企业不断引进和吸收国外先进的转炉炼钢技术,加强与国际钢铁业的合作交流,拓宽了转炉炼钢的应用范围和技术水平。
总的来说,中国的转炉炼钢工艺经历了从引进到自主研发再到与国际接轨的发展历程,取得了显著的成就。
在未来,随着技术不断创新和发展,中国的转炉炼钢工艺有望进一步提升,为中国钢铁产业的持续发展做出更大的贡献。
中国历史上炼钢技术的演变

中国历史上炼钢技术的演变汉代工农业生产和军事活动的需要,使各种制钢技术得到蓬勃发展。
西汉前期刘胜墓所出钢剑,经检验是由块炼铁渗碳反复锻打而成的,由于锻打次数增多,钢的质量比战国燕下都钢剑有明显提高。
到了东汉时期,又出现了以炒钢为原料的经“三十炼”的金马书刀和钢刀。
《汉金文录》著录的永元错金书刀,铭文为“永元十六年(公元104年)广汉郡工官……卅炼史成长荆守丞主”。
1974年山东苍山县出土的东汉钢刀,铭文有“永初六年(公元112年)五月丙午造卅炼大刀吉祥”,为接近共析成份(碳含量千分之八)的高碳钢锻成。
稍后一些时期,在东汉中平年间(公元184—189年)又出现具有“百炼清刚”铭文的百炼钢刀。
另一卓越的制钢工艺——铸铁脱碳成钢,则是从高度成熟的铸铁柔化术衍变而来。
通过长期反复的实践,汉代冶铁工匠对于生铁的机械性能随着碳份的高低而变化这一点已有深入的认识。
在实践上,他们能够把碳含量达4%左右或更高的铸铁,经过脱碳使内层也消除白口铁的组织,通体都成为高碳钢。
这样,就创造了一种在固态下通过高温脱碳处理,把生铁变成钢的先进工艺。
郑州东史马出土的东汉铁剪和南阳东汉铁戟等,就是这样制成的。
由于生铁在浇注过程中,非金属和金属夹杂物可上浮撇去,金属组织较为纯净。
因此,铸铁脱碳后所得到的钢,和现代碳素滚珠轴承钢的质量相近。
这种制钢工艺从目前资料看,是我国所独有,很有独创精神。
西汉时期钢铁技术最重大的成就是炒钢(或炒铁)的发明。
它是在地面上挖出缶状炉缸,内层涂以耐火泥,上置顶盖,做成炒钢炉。
冶炼时,将生铁料烧成熔融或半熔融状态,鼓风吹炼并加搅拌,使成为熟铁,或在有控制地脱碳的条件下成为低中碳钢以至高碳钢。
流传至今的传统炼钢工艺仍沿用了这种方法。
因为它以生铁为原料,价廉易得,生产率高,因此和其它制钢方法相比,有极大的优越性。
它的出现和逐步推广改变了整个冶铁生产的面貌,是钢铁发展史上有划时代意义的大事情。
炒钢技术及热锻制钢,大大促进了百炼钢的发展,使之进入成熟阶段。
炼钢工艺的发展历程

炼钢工艺的发展历程2008年12月8日摘自冶金自动化网炼钢方法(1)最早出现的炼钢方法是1740年出现的坩埚法,它是将生铁和废铁装入由石墨和粘土制成的坩埚内,用火焰加热熔化炉料,之后将熔化的炉料浇成钢锭。
此法几乎无杂质元素的氧化反应。
炼钢方法(2)1856年英国人亨利·贝塞麦发明了酸性空气底吹转炉炼钢法,也称为贝塞麦法,第一次解决了用铁水直接冶炼钢水的难题,从而使炼钢的质量得到提高,但此法要求铁水的硅含量大于0.8%,而且不能脱硫。
目前已淘汰。
炼钢方法(3)1865年德国人马丁利用蓄热室原理发明了以铁水、废钢为原料的酸性平炉炼钢法,即马丁炉法。
1880年出现了第一座碱性平炉。
由于其成本低、炉容大,钢水质量优于转炉,同时原料的适应性强,平炉炼钢法一时成为主要的炼钢法。
炼钢方法(4)1878年英国人托马斯发明了碱性炉衬的底吹转炉炼钢法,即托马斯法。
他是在吹炼过程中加石灰造碱性渣,从而解决了高磷铁水的脱磷问题。
当时,对西欧的一些国家特别适用,因为西欧的矿石普遍磷含量高。
但托马斯法的缺点是炉子寿命底,钢水中氮的含量高。
炼钢方法(5)1899年出现了完全依靠废钢为原料的电弧炉炼钢法(EAF),解决了充分利用废钢炼钢的问题,此炼钢法自问世以来,一直在不断发展,是当前主要的炼钢法之一,由电炉冶炼的钢目前占世界总的钢的产量的30-40%。
炼钢方法(6)瑞典人罗伯特·杜勒首先进行了氧气顶吹转炉炼钢的试验,并获得了成功。
1952年奥地利的林茨城(Linz)和多纳维兹城(Donawitz)先后建成了30吨的氧气顶吹转炉车间并投入生产,所以此法也称为LD法。
美国称为BOF法(Basic Oxygen Furnace)或BOP法,如图1所示。
图1 BOF法炼钢方法(7)1965年加拿大液化气公司研制成双层管氧气喷嘴,1967年西德马克西米利安钢铁公司引进此技术并成功开发了底吹氧转炉炼钢法,即OBM法(Oxygen Bottom Maxhuette) 。
炼钢的发展历史

氧气顶吹转炉炼钢法的发展
19世纪中叶,从空气中大量分离氧气技术的成功,能为工业生 产提供大量的廉价的氧气,使得贝塞麦使用纯氧炼钢的设想成为可 能,从此产生了各种氧气炼钢法。氧气顶吹转炉炼钢法产生于19世 纪40年代末期,由瑞土人罗伯特·杜勒试验成功,采用从转炉炉口伸 入炉内的水冷氧气喷枪,在熔池上方供氧进行吹炼,经过不断改进 形成了氧气顶吹转炉的雏形。因为当时奥地利缺乏废钢和燃料,不 适合发展平炉和电炉炼钢法,而铁矿含磷量低,发热量少,不适合 发展底吹转炉炼钢法,因此氧气顶吹转炉炼钢法在奥地利最先得到 发展。奥地利钢铁公司根据罗伯持·杜勒的设计在2t、10t、15t转炉 上进行氧气顶吹试验,取得了丰富的经验。于1952年在林茨城, 1953年在多纳维茨城先后建成了30t氧气顶吹转炉炼钢车间并投入 生产,所以氧气顶吹转炉炼钢法又称为LD法(取这两个城市名称的 第一个字母L、D做为代称)。
6)利于自动化生产和开展综合利用 氧气顶吹转炉炼钢时问短,生产率高,其机械化程度较高,有 利于实现生产过程的白动化,也有利于开展综合利用,如回收煤气 、炉尘等。 以上是氧气顶吹转炉炼钢的主要优点,但也存在一些不足之处 ,例如,它能冶炼钢的品种不及电炉;炼钢过程中金属烧损较大; 脱磷、脱硫的能力不强;另外,由于氧气从炉口吹入,不是直接穿 过熔池,与金属的接触面不够大,因而氧气的利用率和热效率不够 高。
4)基建投资少、建设速度快 由于氧气顶吹转炉车间设备简单,所占厂房面积和所需要的重 型设备的数量比平炉车间少,因此投资可比相同产量的平炉车间低 30%一40%。而且生产规模越大,基建投资就越省,同时车间建设 速度比平炉车间快得多。 5)原料消耗少,热效率高、成本低 氧气顶吹转炉炼钢的金属消耗极为1100一1140Kg/t钢,稍高于 平炉(但在良好操作情况下,金属消耗与平炉接近)。但由于顶吹转 炉的热源是利用铁水本身的物理热和化学热,热效率高,不需外加 热源,因此在燃料和动力消耗方面均较平炉、电炉低。由于氧气顶 吹转炉炼钢法具有高的生产率和低的消耗,所以钢的成本也较低。
- 1、下载文档前请自行甄别文档内容的完整性,平台不提供额外的编辑、内容补充、找答案等附加服务。
- 2、"仅部分预览"的文档,不可在线预览部分如存在完整性等问题,可反馈申请退款(可完整预览的文档不适用该条件!)。
- 3、如文档侵犯您的权益,请联系客服反馈,我们会尽快为您处理(人工客服工作时间:9:00-18:30)。
炼钢工艺的发展历程
2008年12月8日摘自冶金自动化网
炼钢方法(1)
最早出现的炼钢方法是1740年出现的坩埚法,它是将生铁和废铁装入由石墨和粘土制成的坩埚内,用火焰加热熔化炉料,之后将熔化的炉料浇成钢锭。
此法几乎无杂质元素的氧化反应。
炼钢方法(2)
1856年英国人亨利·贝塞麦发明了酸性空气底吹转炉炼钢法,也称为贝塞麦法,第一次解决了用铁水直接冶炼钢水的难题,从而使炼钢的质量得到提高,但此法要求铁水的硅含量大于0.8%,而且不能脱硫。
目前已淘汰。
炼钢方法(3)
1865年德国人马丁利用蓄热室原理发明了以铁水、废钢为原料的酸性平炉炼钢法,即马丁炉法。
1880年出现了第一座碱性平炉。
由于其成本低、炉容大,钢水质量优于转炉,同时原料的适应性强,平炉炼钢法一时成为主要的炼钢法。
炼钢方法(4)
1878年英国人托马斯发明了碱性炉衬的底吹转炉炼钢法,即托马斯法。
他是在吹炼过程中加石灰造碱性渣,从而解决了高磷铁水的脱磷问题。
当时,对西欧的一些国家特别适用,因为西欧的矿石普遍磷含量高。
但托马斯法的缺点是炉子寿命底,钢水中氮的含量高。
炼钢方法(5)
1899年出现了完全依靠废钢为原料的电弧炉炼钢法(EAF),解决了充分利用废钢炼钢的问题,此炼钢法自问世以来,一直在不断发展,是当前主要的炼钢法之一,由电炉冶炼的钢目前占世界总的钢的产量的30-40%。
炼钢方法(6)
瑞典人罗伯特·杜勒首先进行了氧气顶吹转炉炼钢的试验,并获得了成功。
1952年奥地利的林茨城(Linz)和多纳维兹城(Donawitz)先后建成了30吨的氧气顶吹转炉车间并投入生产,所以此法也称为LD法。
美国称为BOF法(Basic Oxygen Furnace)或BOP法,
如图1所示。
图1 BOF法
炼钢方法(7)
1965年加拿大液化气公司研制成双层管氧气喷嘴,1967年西德马克西米利安钢铁公司引进此技术并成功开发了底吹氧转炉炼钢法,即OBM法(Oxygen Bottom Maxhuette) 。
1971年美国钢铁公司引进OBM法,1972年建设了3座200吨底吹转炉,命名为Q-BOP (Quiet BOP) ,如图2所示。
图2 Q-BOP法
炼钢方法(8)
在顶吹氧气转炉炼钢发展的同时,1978-1979年成功开发了转炉顶底复合吹炼工艺,即从转炉上方供给氧气(顶吹氧),从转炉底部供给惰性气体或氧气,它不仅提高钢的质量,而且降低了炼钢消耗和吨钢成本,更适合供给连铸优质钢水,如图3所示。
图3 转炉顶底复合吹炼法
炼钢方法(9)
我国首先在1972-1973年在沈阳第一炼钢厂成功开发了全氧侧吹转炉炼钢工艺。
并在唐钢等企业推广应用,如图4所示。
图4 全氧侧吹转炉炼钢法
总之,炼钢技术经过200多年的发展,技术水平、自动化程度得到了很大的提高,21世纪炼钢技术会面临更大的挑战,相信会有不断的新技术涌现。
AOD精炼技术的发展
2010-3-4 15:13:07
(1)脱碳工艺的改进
新日铁光制铁所当w([C])≥0.7%时,在60 t AOD采用纯氧吹炼,温度>1 580℃时,w(Cr)20%,首先氧化碳,当w([C])≤0.7%,采用O2;Ar(N2)连续变化方式脱碳,当w([C])≤0.10%用纯氩吹炼,用钢中余氧及渣中的Cr2O3进一步脱碳。
光制铁所采用这种方法,前期氧利用率与传统方法一致,但脱碳速度得到提高,氧枪没有出现熔损加大问题,后期氧利用率CRE提高6%,结果FeSi消耗降低了0.7 kg/t。
(2)深脱硫工艺按照传统的AOD操作,脱碳终了加入FeSi进行Cr2O3的还原操作,然后扒去85%以上的渣子再加入CaO、CaF2及粉状FeSi或CaSi进行脱硫的精炼操作,这样对成本、精炼时间、操作条件都十分不利。
新日铁光制所采用Al代替FeSi进行脱硫,取得满意的效果,w(S)<10×10-6,还原精炼时间缩短5~17 min,如下图。
渣子碱度要求CaO+MgOΠSiO2+Al2O3=2.8~3.5
(3)以N2代Ar及供氧强度的提高Ar作为AOD精炼的主要气体,因其价格较高,在不锈钢精炼时用N2代Ar,其代Ar率达到20%~40%,对于w([N])为400×10-6~800×10-6的钢可以在脱碳一期、二期代Ar,产品w([N])要求1 500×10-6~2 500×10-6,脱碳期全部用N2代Ar,产品w([N])要求3 000×10-6,可以全程用N2代Ar。
日本太平洋金属八户厂在生产304钢时代Ar率达到80%,产品w([N])<580×10-6,小于该钢允许w([N])650×10-6的要求。
AOD供氧强度提高:供氧强度Nm3/min•t是提高脱碳速度,缩短精炼时间,废钢加入量多少及降低成本的关键工艺参数。
经过不断研究,供氧强度已由过去0.8 Nm3/min•t提高到1~1.5Nm3/min•t, 有顶枪时应大于2Nm3Πmin•t。
供氧强度提高后,熔池温度的控制,国际上普遍采有加入5%~10%的清洁废钢或铁合金的办法,这样初炼炉(电炉)的冶炼时间及电耗也得到了改善。
(4)AOD+顶枪(AOD-CB法)(KCB-S法)
日本大同特殊钢公司星崎工场,依据不同元素与氧反应产生的热量及相对成本进行比较,发现只有碳生成CO后再氧化为CO2时,其反应热最高,相对成本最低。
这是钢水中Si、Mn、Cr、Al、Fe氧化结果所不如。
于是发明了AOD-CB工艺,与传统工艺相比,升温速度由7℃Πmin提高到17.5℃/min。
CRE提高5%,脱碳速度由0.055%Πmin提高到0.087%Πmin,电耗降低78 kW•hΠt,FeSi减少25%,时间减少11 min,炉龄达到235炉。
顶吹工艺有软吹硬吹两种方式,硬吹即进入熔池的氧全部与钢水进行反应,软吹即60%进行反应,40%与CO进行二次燃烧生产CO2。
硬吹工艺比传统的AOD工艺其脱碳时间缩短44%。
软吹可缩短31%,但是软吹可以提高废钢加入量,降低FeSi消耗及电耗。
日本往友金属和歌山工厂90 t AOD在1982年即进行复吹技术,精炼时间缩短
20 min,FeSi降到7.5 kgΠt,氩耗降到11.3 Nm3/t。
由于顶吹氧突出的优点,新建或改造AOD都把顶吹作为必备的工艺手段。
(5)AOD-VCR法(V-AOD法)
AOD精炼工艺在生产w([C])≥300×10-6的不锈钢时,优越性十分突出,但是生产w([C+N])≤300×10-6时就非常困难,其结果是精炼时间长,氩气消耗高,炉衬寿命低,FeSi消耗高。
经济性差。
日本新日铁光制铁厂,日本大同特殊钢公司经过研究开发了AOD+真空的精炼方法,大同制钢于1990年在涩川厂投产20 t AOD-VCR,1992年在知多厂投产70 t AOD-VCR,光制铁厂于1996年投产60 t V-AOD。
其工艺技术为,当钢中w([C])>0.1%时按传统工艺由底侧处风枪吹入O2/Ar(N2),当w([C])<0.1%时停止吹氧改由Ar(N2),同时将真空罩套在AOD炉帽上,真空度为2.0~2.67 kpa,底吹Ar/(N2)流量为20~30 Nm3/min,在强大的搅拌下,钢水中的余氧及渣中的氧化物,进行脱碳, 经过10~20 min,熔池温降50~70℃,钢中w([C+N])达到100×10-6以下。
不同钢种应用AOD-VCR 的碳、氮浓度见表3。
AOD-VCR其底吹搅拌能力是SS-VOD的13~20倍,是VODC的32~44倍,因此创造了脱碳、脱氮动力学及热力学条件,若达到同样[C]、[N]质量分数,SS-VOD需40 min以上。
若要求w([C])≤150×10-6,w([N])≤300×10-6,采用AOD—VCR比AOD可以缩短精炼时间21%。
(6)使用不同原料的AOD精炼工艺
HM-AOD法:用经过脱磷,脱硅的铁水直接入AOD的精炼方法,要求铁水w(P)≤0.015%,w(Si)≤0.20%,铁水温度> 300℃。
第一阶段CRE达到90%与LD-AOD比,生产成本降低4%。
用液态FeCr、FeNi直接生产不锈钢方法:日太平洋公司八户工场为了节约原料,降低能耗研制这种方法。
通过调查不同炉型的热效率发,电弧炉为47%,LD为68%,相反AOD则为0%,所以把初炼炉定为AOD。
通过把液态FeCr、FeNi兑入AOD-CB中进行炼取得了明显效果,铬回收率达到99%,脱碳速提高
0.018%Πmin,升温提高20%~70%,FeSi耗减少10%~15%,以N2代Ar率达到84%。
AOD吹炼过程中加铬矿石法:日本往友金属和歌山厂采用脱磷,脱硅铁水兑入AOD中,同时加入铬矿,最大加入量为50 kgΠt,铁水中的碳可以还原40%~80%的氧化铬,其余加入FeSi还原,不足的铬用FeCr调整,实践证明生产成本明显降低。
(7)不同能源介质的AOD—TH法
日本大同特殊钢采用顶枪油+氧烧咀产生2 600℃高温,升温速度提高140%,Cr损失明显减少。
(8)AOD精炼方法在不锈钢脱磷研究方面也取得进步。
目前正在开展的工作还有溅渣护炉,风口喷粉(石灰、Fe2O3)技术,风口蘑菇头的控制技术,风口不规则形状的研究,侧吹流体力学的研究,使炉体几何尺寸、风口位置、供气等达到优化。