(完整版)铝合金铸造工艺控制对铝锭质量的影响
铸造工艺对铝合金铸件质量的影响

产条件下。 满足 日益提高的质量要求和批量的生
圈1
罐体毛坯铸件
.
2 8.
电大理工
总第 2 8 4 期
2 3浇注 系统 的确 定 .
罐体毛坯铸件采用水平造型方法 , 浇注系统 采用对包、四个冒口缝隙浇注系统,见图 2 。此
铝合金 罐 体 树脂砂
浇注系统
1 铝合金低压铸造概况
铝 是人们 最 熟悉 的金属 之一 , 在众 多的轻 量
产任务 已成为我们的当务之急。 针对此类 问题, 本研究小组集思广益, 应用
化材料中铝合金是最重要的材料之一, 也是应用 最广 的轻量化材料。 由于铝的熔点低 , 流动性好 , 具有很好 的铸造性能, 因此容易制造 出形状复杂 的零件。由于铝合金密度小而 比强度高, 以在 所 机械工业、 汽车工业、 航空航天工业等领域得到 了广泛 的应用 。
低压铸造法是介于重力铸造和压力铸造之
间的一种铸造方法, 它利用气体压力将金属液压 入铸型, 并使铸件在一定压力下结晶凝固的特种 铸造方法。 低压铸造具有铸件尺寸精度较高、 充
高精度铸件的先河 。
22 . 铝合金铸件结构特 点 罐体毛坯铸件见图 1 ,结构较简单,但尺寸 较大,壁厚较薄, 且罐体两侧法兰均有 S 6气体 F 密封要求 , 传统砂型: 艺生产较为困难。 [ 经研究 小组调研论证决定在借鉴 A B类铸件工艺经验 B 基础上,对该件采用树脂砂造型工艺生产 。
的设计上借鉴了 A B B 类铸件的生产经验, 采用上 下箱分别造型 , 横浇道下过滤网的方式防止夹杂 物进入型腔。
浇建 蕞缝
热顶结构及铸造工艺对7075铝合金铸锭表面质量的影响
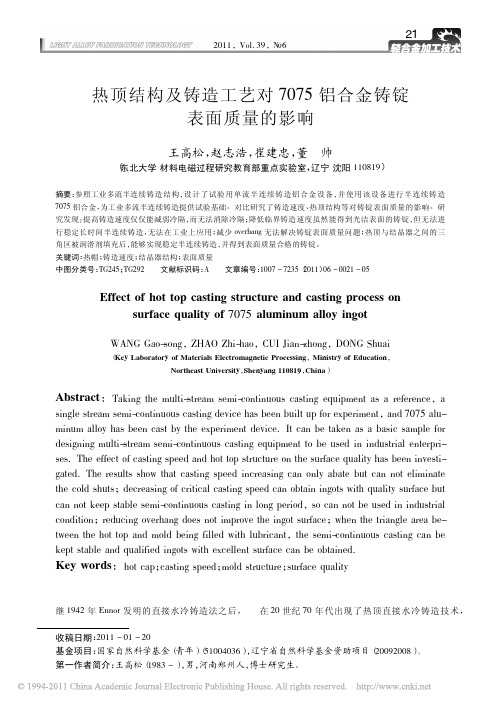
3 试验结果分析
从文献[2]可知,要想消除冷隔等缺陷,必须使 铸造速度大于临界铸造速度。对于 7075 铝合金通 过尝试在 不 改 变 其 他 铸 造 条 件 下 提 高 铸 造 速 度 试 验,虽然使铸 锭 表 面 冷 隔 减 弱,但 是 仍 未 消 除 冷 隔。 由此可见,由于该合金的特性,仅仅靠提高铸造速度 并不能实现铸造速度大于临界铸造速度。
Key words: hot cap; casting speed; mold structure; surface quality
继 1942 年 Ennor 发明
收稿日期:2011 - 01 - 20 基金项目:国家自然科学基金( 青年) ( 51004036) ,辽宁省自然科学基金资助项目( 20092008) 。 第一作者简介:王高松( 1983 - ) ,男,河南郑州人,博士研究生。
( Key Laboratory of Materials Electromagnetic Processing,Ministry of Education, Northeast University,Shenyang 110819,China)
Abstract: Taking the multi-stream semi-continuous casting equipment as a reference,a
在石墨环上端贴一层 6 mm 高的硅酸铝纸,图 3 所示为相应铸锭表面。从图 3 可以看出,石墨环不 做任何处理时,铸锭表面有冷隔缺陷,而石墨环上端 贴硅酸铝纸时,虽然减弱了冷隔缺陷,但铸锭表面却 增加了划痕缺陷。 2. 2. 2 改变石墨环状况
主要措施如下: ( 1) 使石墨环从上端开始向下有 高 10 mm 的区域未与结晶器接触,即使石墨环上端 有 10 mm 的高度未受到冷却; ( 2) 使石墨环从下端 开始向上有高 10 mm 的区域未与结晶器接触,该区 域未受到冷却; ( 3) 在( 1) 的基础上,在石墨环内表
铝合金熔炼工艺的质量控制
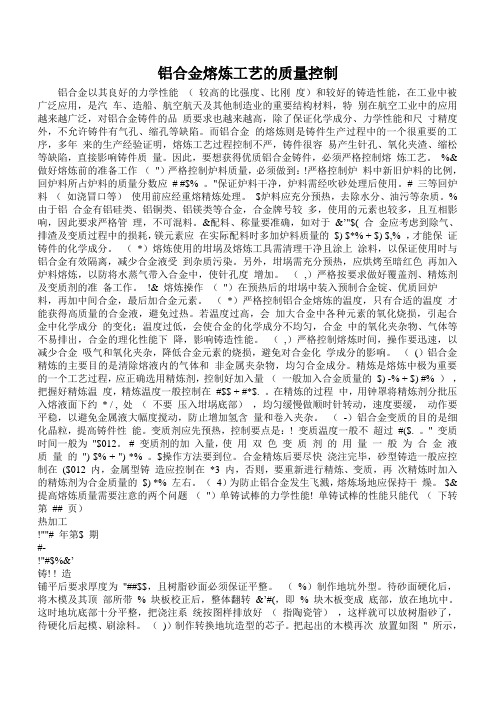
铝合金熔炼工艺的质量控制铝合金以其良好的力学性能(较高的比强度、比刚度)和较好的铸造性能,在工业中被广泛应用,是汽车、造船、航空航天及其他制造业的重要结构材料,特别在航空工业中的应用越来越广泛,对铝合金铸件的品质要求也越来越高,除了保证化学成分、力学性能和尺寸精度外,不允许铸件有气孔、缩孔等缺陷。
而铝合金的熔炼则是铸件生产过程中的一个很重要的工序,多年来的生产经验证明,熔炼工艺过程控制不严,铸件很容易产生针孔、氧化夹渣、缩松等缺陷,直接影响铸件质量。
因此,要想获得优质铝合金铸件,必须严格控制熔炼工艺。
%& 做好熔炼前的准备工作(")严格控制炉料质量,必须做到:!严格控制炉料中新旧炉料的比例,回炉料所占炉料的质量分数应# #$% 。
"保证炉料干净,炉料需经吹砂处理后使用。
# 三等回炉料(如浇冒口等)使用前应经重熔精炼处理。
$炉料应充分预热,去除水分、油污等杂质。
% 由于铝合金有铝硅类、铝铜类、铝镁类等合金,合金牌号较多,使用的元素也较多,且互相影响,因此要求严格管理,不可混料。
&配料、称量要准确,如对于&’"$( 合金应考虑到除气、排渣及变质过程中的损耗,镁元素应在实际配料时多加炉料质量的$) $*% + $) $,% ,才能保证铸件的化学成分。
(*)熔炼使用的坩埚及熔炼工具需清理干净且涂上涂料,以保证使用时与铝合金有效隔离,减少合金液受到杂质污染。
另外,坩埚需充分预热,应烘烤至暗红色再加入炉料熔炼,以防将水蒸气带入合金中,使针孔度增加。
(,)严格按要求做好覆盖剂、精炼剂及变质剂的准备工作。
!& 熔炼操作(")在预热后的坩埚中装入预制合金锭、优质回炉料,再加中间合金,最后加合金元素。
(*)严格控制铝合金熔炼的温度,只有合适的温度才能获得高质量的合金液,避免过热。
若温度过高,会加大合金中各种元素的氧化烧损,引起合金中化学成分的变化;温度过低,会使合金的化学成分不均匀,合金中的氧化夹杂物、气体等不易排出,合金的理化性能下降,影响铸造性能。
铝合金铸造工艺与铸锭质量的关系研究
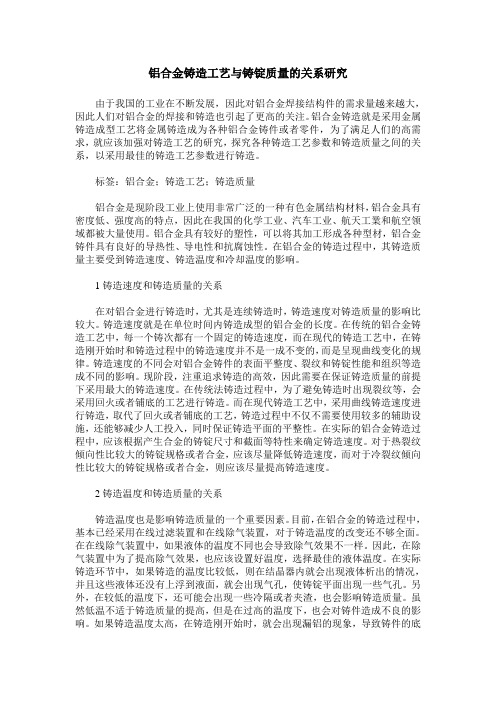
铝合金铸造工艺与铸锭质量的关系研究由于我国的工业在不断发展,因此对铝合金焊接结构件的需求量越来越大,因此人们对铝合金的焊接和铸造也引起了更高的关注。
铝合金铸造就是采用金属铸造成型工艺将金属铸造成为各种铝合金铸件或者零件,为了满足人们的高需求,就应该加强对铸造工艺的研究,探究各种铸造工艺参数和铸造质量之间的关系,以采用最佳的铸造工艺参数进行铸造。
标签:铝合金;铸造工艺;铸造质量铝合金是现阶段工业上使用非常广泛的一种有色金属结构材料,铝合金具有密度低、强度高的特点,因此在我国的化学工业、汽车工业、航天工業和航空领域都被大量使用。
铝合金具有较好的塑性,可以将其加工形成各种型材,铝合金铸件具有良好的导热性、导电性和抗腐蚀性。
在铝合金的铸造过程中,其铸造质量主要受到铸造速度、铸造温度和冷却温度的影响。
1铸造速度和铸造质量的关系在对铝合金进行铸造时,尤其是连续铸造时,铸造速度对铸造质量的影响比较大。
铸造速度就是在单位时间内铸造成型的铝合金的长度。
在传统的铝合金铸造工艺中,每一个铸次都有一个固定的铸造速度,而在现代的铸造工艺中,在铸造刚开始时和铸造过程中的铸造速度并不是一成不变的,而是呈现曲线变化的规律。
铸造速度的不同会对铝合金铸件的表面平整度、裂纹和铸锭性能和组织等造成不同的影响。
现阶段,注重追求铸造的高效,因此需要在保证铸造质量的前提下采用最大的铸造速度。
在传统法铸造过程中,为了避免铸造时出现裂纹等,会采用回火或者铺底的工艺进行铸造。
而在现代铸造工艺中,采用曲线铸造速度进行铸造,取代了回火或者铺底的工艺,铸造过程中不仅不需要使用较多的辅助设施,还能够减少人工投入,同时保证铸造平面的平整性。
在实际的铝合金铸造过程中,应该根据产生合金的铸锭尺寸和截面等特性来确定铸造速度。
对于热裂纹倾向性比较大的铸锭规格或者合金,应该尽量降低铸造速度,而对于冷裂纹倾向性比较大的铸锭规格或者合金,则应该尽量提高铸造速度。
2铸造温度和铸造质量的关系铸造温度也是影响铸造质量的一个重要因素。
再生铝合金铸造工艺中的质量控制与检测技术

再生铝合金铸造工艺中的质量控制与检测技术随着环境保护意识的增强和资源回收利用的重要性日益凸显,再生铝合金铸造工艺作为一种节约资源、降低碳排放的环保技术逐渐受到人们的关注和应用。
然而,再生铝合金铸造工艺中的质量控制与检测技术是保证产品质量且实现工艺优化的关键。
本文将对再生铝合金铸造工艺中的质量控制与检测技术进行探讨,并介绍其在提高铸件质量、减少废品率和优化工艺参数方面的应用。
一、质量控制技术1. 原料筛选与预处理在再生铝合金铸造工艺中,合适的原料选择和预处理对于保证铸件质量至关重要。
首先,对废铝进行严格的筛选,去除杂质和掺杂物,以减少不良杂质对于铸件性能的影响。
其次,对筛选后的废铝进行预处理,如除氧、脱气、脱渣等,以提高铝合金的纯度,降低夹杂物含量,从而减少井号和气孔等缺陷的产生。
2. 熔炼与浇注控制再生铝合金铸造的熔炼与浇注过程中,需要控制熔炼温度、保持合金液的均匀和正常浇注等因素,以保证铸件的致密性、干燥性和灵敏性等关键性能指标。
其中,采用先进的熔炼设备和技术可以提高熔炼效果,降低合金液中的夹杂物含量;而且采用恰当的浇注工艺参数,如浇注温度、浇注速度和浇注角度等,可以有效地防止缺陷的产生,提高铸件的完整性和表面质量。
二、检测技术1. 成分分析与合金验证再生铝合金铸造的质量控制离不开对合金成分的分析与验证。
常用的分析方法包括光谱分析、电感耦合等离子体发射光谱分析(ICP-AES)、X射线荧光光谱仪(XRF)等,用于检测成分偏差、非金属元素和杂质含量等。
同时,合金验证技术可以对铸件进行成分及性能检测,确保合金达到设计材料要求。
2. 缺陷检测与评估合金铸造中常见的缺陷包括夹杂物、井号、气孔等,这些缺陷对铸件的力学性能和可靠性产生重要影响。
因此,采用适当的缺陷检测与评估技术是质量控制的重要环节。
常用的方法包括X射线检测、超声波检测、电子显微镜等,能够对铸件进行非破坏性检测,提高缺陷的发现率和评估准确性。
(完整版)铝合金铸造工艺控制对铝锭质量的影响
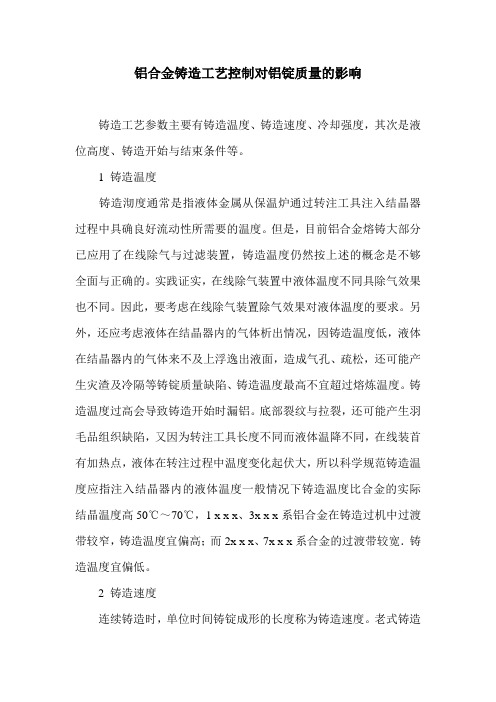
铝合金铸造工艺控制对铝锭质量的影响铸造工艺参数主要有铸造温度、铸造速度、冷却强度,其次是液位高度、铸造开始与结束条件等。
1 铸造温度铸造沏度通常是指液体金属从保温炉通过转注工具注入结晶器过程中具确良好流动性所需要的温度。
但是,目前铝合金熔铸大部分已应用了在线除气与过滤装置,铸造温度仍然按上述的概念是不够全面与正确的。
实践证实,在线除气装置中液体温度不同具除气效果也不同。
因此,要考虑在线除气装置除气效果对液体温度的要求。
另外,还应考虑液体在结晶器内的气体析出情况,因铸造温度低,液体在结晶器内的气体来不及上浮逸出液面,造成气孔、疏松,还可能产生灾渣及冷隔等铸锭质量缺陷、铸造温度最高不宜超过熔炼温度。
铸造温度过高会导致铸造开始时漏铝。
底部裂纹与拉裂,还可能产生羽毛品组织缺陷,又因为转注工具长度不同而液体温降不同,在线装首有加热点,液体在转注过程中温度变化起伏大,所以科学规范铸造温度应指注入结晶器内的液体温度一般情况下铸造温度比合金的实际结晶温度高50℃~70℃,1 x x x、3x x x系铝合金在铸造过机中过渡带较窄,铸造温度宜偏高;而2x x x、7x x x系合金的过渡带较宽.铸造温度宜偏低。
2 铸造速度连续铸造时,单位时间铸锭成形的长度称为铸造速度。
老式铸造通常是一个铸次为—个固定铸造速度;而现代铸造是曲线铸造速度,即铸造开始与铸造过程不是同一个铸造速度:铸造速度的快与慢对铸锭裂纹、铸锭表面质量、铸锭组织和性能有很大影响,在保证铸锭质量的前提下,应采用最高的铸造速度。
老式铸造法为解决某些合金及规格铸锭的裂纹问题,铸造时采用铺底或回火的工艺方法;而现代铸造法则采用曲线铸锭速度,取代了老式铸造的铺底或回火工艺,它既减少了一些辅助设施,又节省了人力与减轻劳动强度,还可以避免——些铸锭表面质量缺陷铸造速度的选择是依据所生产合金的特性与铸锭截面尺寸而定。
一般规律足冷裂纹倾向性较大的合金及铸锭规格,应提高铸造速度;而热裂纹倾向较大的合金及铸锭规格,则应降低铸造速度3 冷却强度冷却强度也称为冷却速度。
铸造铝合金锭的技术要求
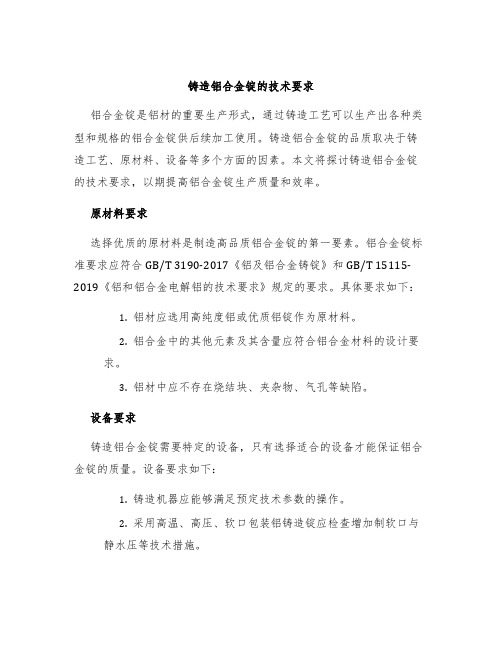
铸造铝合金锭的技术要求铝合金锭是铝材的重要生产形式,通过铸造工艺可以生产出各种类型和规格的铝合金锭供后续加工使用。
铸造铝合金锭的品质取决于铸造工艺、原材料、设备等多个方面的因素。
本文将探讨铸造铝合金锭的技术要求,以期提高铝合金锭生产质量和效率。
原材料要求选择优质的原材料是制造高品质铝合金锭的第一要素。
铝合金锭标准要求应符合GB/T 3190-2017《铝及铝合金铸锭》和GB/T 15115-2019《铝和铝合金电解铝的技术要求》规定的要求。
具体要求如下:1.铝材应选用高纯度铝或优质铝锭作为原材料。
2.铝合金中的其他元素及其含量应符合铝合金材料的设计要求。
3.铝材中应不存在烧结块、夹杂物、气孔等缺陷。
设备要求铸造铝合金锭需要特定的设备,只有选择适合的设备才能保证铝合金锭的质量。
设备要求如下:1.铸造机器应能够满足预定技术参数的操作。
2.采用高温、高压、软口包装铝铸造锭应检查增加制软口与静水压等技术措施。
3.挤压铝合金锭时,设备的运行稳定、铝推出均匀、速度适中。
4.出铝口应位于铸造温度调整和铝合金锭冷却之间,以减少成型缺陷。
工艺要求铸造铝合金锭的工艺包括模具铸造和挤压铸造。
不同的工艺具有不同的特点,因此需要采取不同的技术要求。
一下是针对铸造工艺和挤压工艺的技术要求:模具铸造1.模具要求为无缺陷清洁的铸造模具,并且有足够的强度和刚度,以确保模具铸造铝合金锭的形状和表面质量。
2.铝液铸造温度适宜,应控制在合理的范围内,以避免过热或过冷造成铸造缺陷。
3.铝液应保持一定的进口速度和进口深度,以达到所需的铸造形状和表面质量。
挤压铸造1.提高铝液的温度和流动性,使它能够顺利地进入挤压机,并能够顺畅地从针口挤出。
2.应注意控制挤出机的挤压速度、转子齿轮轮廓的形状和光洁度,从而达到所需的挤压截面形状和表面质量。
3.合理控制挤压速度、铝液温度和挤压热处理参数,从而保证挤出后的铝合金锭的组织均匀性。
质量控制要求铸造铝合金锭的质量控制要求包括外观质量、化学成分、硬度和收缩等方面。
铸造工艺对铝合金力学性能的影响研究

铸造工艺对铝合金力学性能的影响研究近年来,随着高科技的不断发展,铝合金的应用范围也越来越广泛,其良好的机械性能和轻质化特点被广泛关注。
而其中铸造工艺在铝合金力学性能中的影响也逐渐受到了研究者们的关注。
铝合金的铸造工艺包括了熔炼、充模、凝固和透过等过程,而在这一系列的铸造工艺中,一些细节问题可能会对铝合金的力学性能产生不同的影响。
首先来看铝合金的熔炼过程。
在熔炼的过程中,铝合金材料会与铸造炉中的炉底和炉壁接触,形成了不同的反应和影响。
例如,在受力环境中,铸炉石墨层会随时间的推移而不断磨损,形成一种纳米级的磨损表面,它会影响铝合金材料的热传导和流动性。
其次,铝合金的充模过程也会对力学性能产生影响。
在充模的过程中,铸造砂的密度、成型工艺和密封性都会影响铝合金的晶体生长。
而铝合金的晶体结构又对其力学性能产生较大的影响。
再来看铝合金的凝固过程。
凝固过程中,液体不均质性、成分偏差、温度变化和晶粒取向等因素都会对铝合金的力学性能产生影响。
特别是在大型铝合金铸件的凝固过程中,由于高尺度尺寸的挽救导致了流动不稳定和凝固缺陷,其对铝合金的力学性能影响会更大。
最后,铝合金的透过过程也会对其力学性能产生影响。
尤其是在高压下的气孔化合物,往往会对铝合金的可靠性存在影响。
因此,在铸造过程中,逐步完善铸造材料的透湿性高压条件,也势必会进一步提高铸造材料的力学性能。
综上所述,铝合金的铸造工艺对其力学性能产生的影响非常复杂而巨大。
因此,我们应该进一步研究铝合金的铸造工艺,从熔炼到透过全面考虑,提高铝合金的力学性能,进一步推进铝合金在高科技领域的应用。
铸造工艺对ZL101铝合金铸件质量影响的研究

铸造工艺对ZL101铝合金铸件质量影响的研究作者:黎静妮冯丽江韦凤萍潘荣禄钟佳梅来源:《理论与创新》2021年第01期【摘要】利用传统的重力铸造方法制备ZL101铝合金,采用硬度测试、拉伸性能测试等实验方法研究铸造工艺对ZL101铝合金铸件质量影响。
研究结果表明:熔炼温度为720℃,合理的保温时间能有效细化合金组织,当保温时间为20min时,粗大α-Al初生树枝晶向细小胞状晶与球状晶转变,共晶硅的形态也得到较好的改善,合金表现出较好的力学性能,其中抗拉强度为260 MPa,断后伸长率为6%,布氏硬度值为70 HBS。
【关键词】ZL101铝合金;铸造工艺;力学性能引言铸造是一种古老的制造方法,在我国可以追溯到6000年前。
随着工业技术的發展,大型铸件的质量直接影响着产品的质量,因此,铸造在机械制造业中占有重要的地位。
铸造技术的发展也很迅速,特别是19世纪末和20世纪上半叶,出现了很多的新的铸造方法,如低压铸造、陶瓷铸造、连续铸造等,在20世纪下半叶得到完善和实用化。
铸造是将通过熔炼的金属液体浇注入铸型内,经冷却凝固获得所需形状和性能的零件的制作过程。
铸造是常用的制造方法,制造成本低,工艺灵活性大,可以获得复杂形状和大型的铸件,在机械制造中占有很大的比重,如机床占60~80%,汽车占25%,拖拉机占50~60%。
由于现今对铸造质量、铸造精度、铸造成本和铸造自动化等要求的提高,铸造技术向着精密化、大型化、高质量、自动化和清洁化的方向发展,例如我国这几年在精密铸造技术、连续铸造技术、特种铸造技术、铸造自动化和铸造成型模拟技术等方面发展迅速。
ZL101铝合金是一种通过铸造方式制备得到的研究和应用最为广泛的铝硅镁合金,该合金中Si元素的占比约为6.5~7.5%,其中还含有少量的Mg(0.25~0.45%),为亚共晶合金。
该合金具有强度高、韧性以及良好的耐蚀性等多项优异力学性能和物理性能,并且还可以通过适当的热处理使其加工性能、材料塑性以及合金表面性能都获得显著提升,能够有效满足汽车部件的轻量化要求。
铝合金铸造工艺与铸锭质量的关系
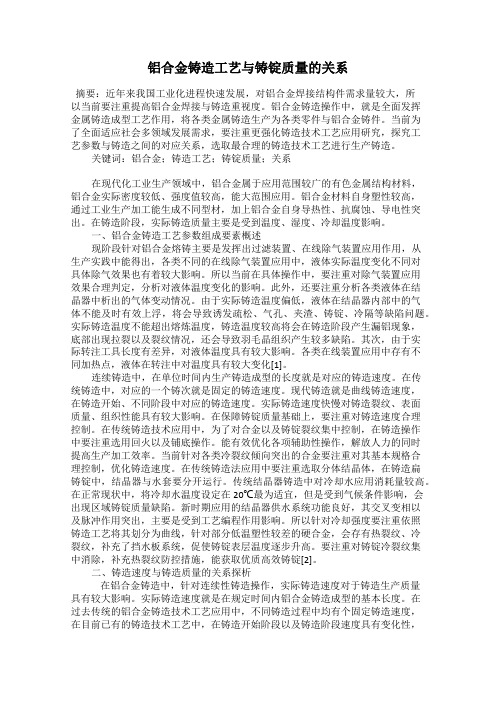
铝合金铸造工艺与铸锭质量的关系摘要:近年来我国工业化进程快速发展,对铝合金焊接结构件需求量较大,所以当前要注重提高铝合金焊接与铸造重视度。
铝合金铸造操作中,就是全面发挥金属铸造成型工艺作用,将各类金属铸造生产为各类零件与铝合金铸件。
当前为了全面适应社会多领域发展需求,要注重更强化铸造技术工艺应用研究,探究工艺参数与铸造之间的对应关系,选取最合理的铸造技术工艺进行生产铸造。
关键词:铝合金;铸造工艺;铸锭质量;关系在现代化工业生产领域中,铝合金属于应用范围较广的有色金属结构材料,铝合金实际密度较低、强度值较高,能大范围应用。
铝合金材料自身塑性较高,通过工业生产加工能生成不同型材,加上铝合金自身导热性、抗腐蚀、导电性突出。
在铸造阶段,实际铸造质量主要是受到温度、湿度、冷却温度影响。
一、铝合金铸造工艺参数组成要素概述现阶段针对铝合金熔铸主要是发挥出过滤装置、在线除气装置应用作用,从生产实践中能得出,各类不同的在线除气装置应用中,液体实际温度变化不同对具体除气效果也有着较大影响。
所以当前在具体操作中,要注重对除气装置应用效果合理判定,分析对液体温度变化的影响。
此外,还要注重分析各类液体在结晶器中析出的气体变动情况。
由于实际铸造温度偏低,液体在结晶器内部中的气体不能及时有效上浮,将会导致诱发疏松、气孔、夹渣、铸锭、冷隔等缺陷问题。
实际铸造温度不能超出熔炼温度,铸造温度较高将会在铸造阶段产生漏铝现象,底部出现拉裂以及裂纹情况,还会导致羽毛晶组织产生较多缺陷。
其次,由于实际转注工具长度有差异,对液体温度具有较大影响。
各类在线装置应用中存有不同加热点,液体在转注中对温度具有较大变化[1]。
连续铸造中,在单位时间内生产铸造成型的长度就是对应的铸造速度。
在传统铸造中,对应的一个铸次就是固定的铸造速度。
现代铸造就是曲线铸造速度,在铸造开始、不同阶段中对应的铸造速度。
实际铸造速度快慢对铸造裂纹、表面质量、组织性能具有较大影响。
再生铝合金铸造工艺技术的质量控制与改进

再生铝合金铸造工艺技术的质量控制与改进在现代工业中,再生铝合金铸造工艺技术的应用越来越广泛,它既能够有效利用废旧铝合金资源,又能制造出具有较高性能的产品。
然而,由于再生铝合金铸造工艺技术本身的复杂性,导致质量控制与改进成为该领域的挑战。
本文将讨论再生铝合金铸造工艺技术的质量控制与改进方法,以期提高再生铝合金铸造产品的质量和性能。
1. 原材料的选择与预处理再生铝合金铸造的质量控制首先涉及到原材料的选择与预处理。
由于废旧铝合金资源中可能含有杂质和不良成分,因此在使用前应通过适当的预处理方法进行净化。
例如,可以通过熔炼、氧化和过滤等步骤来去除杂质和不良成分,以确保再生铝合金的纯度和均匀性。
2. 温度控制与熔炼工艺改进再生铝合金的熔炼工艺对于铸造产品的质量具有重要影响。
在温度控制方面,应根据具体合金的熔点和热力学性质来确定适宜的熔炼温度,以保证铸造过程中合金的液相稳定性和流动性。
此外,熔炼工艺中的搅拌和除气措施也可以帮助减少气体夹杂和夹渣,提高再生铝合金铸造产品的密度和强度。
3. 模具设计与制造优化再生铝合金铸造过程中,模具设计与制造的合理性对于产品质量的控制具有重要作用。
在模具设计方面,应根据铸造产品的形状和尺寸要求,结合再生铝合金的流动性和固化特性,合理设计浇注系统和冷却系统。
在模具制造方面,应选择高质量的模具材料和精密加工工艺,以确保模具的准确性和耐用性。
4. 工艺参数的监控与调整在再生铝合金铸造工艺中,各项工艺参数的监控与调整对于产品质量的稳定性和一致性至关重要。
应通过实时监测和控制熔体温度、注入速度、浇注压力等工艺参数,以确保再生铝合金在铸造过程中的均匀性和一致性。
同时,根据产品质量的反馈信息,及时调整工艺参数,以实现最佳的铸造效果。
5. 检测与评估方法的应用为了确保再生铝合金铸造产品的质量,应采用适当的检测与评估方法进行质量控制。
例如,可以使用金相显微镜、扫描电子显微镜等分析工具,对铸造产品的显微组织和缺陷进行观察和评估。
铸造工艺参数对铸锭质量的影响

铸造工艺参数对铸锭质量的影响铸造工艺参数对铸锭质量的影响1、冷却速度对铸锭质量的影响冷却速度指铸锭的降温速度,又称冷却强度,用单位时间内下降的温度来表示,常用单位是℃/s。
但在实际生产中,这个单位不便于控制,由于在既定条件下,各种工具和工艺条件都是预先确定的,因此生产现场多采用冷却水压或冷却水流量作为冷却速度的度量。
在连续铸造过程中,铸锭内各点在同一时刻的冷却速度以及同一点在不同时刻的冷却速度都是变化的。
(1)冷却速度对铸锭组织的影响在直接水冷半连续铸造时,随着冷却强度的增加,铸锭结晶速度提高,熔体中溶质元素来不及扩散,过冷度增加,晶核增多,因而所得晶粒细小;同时,过渡带尺寸缩小,铸锭致密度提高,减小了疏松倾向。
此外提高冷却速度,还可细化一次晶化合物尺寸,减小区域偏析的程度。
铸模的导热条件是显著影响铸锭组织的重要因素,尤其是边缘部位的组织。
图1示出了扁铸锭中枝晶网尺寸分布情况:A是铸模中金属水平高的情况;B是铸模中金属水平低的情况;C是电磁铸造的,金属不和铸模接触,完全依靠喷射到铸锭上的水流把热量带走。
图1在不同水平铸造或电磁铸造的扁锭中的IPP分布情况(2)冷却速度对铸锭力学性能的影响。
冷却速度是决定铸锭力学性能的基本因素。
通常,随冷却速度增大,铸锭的平均力学性能得到提高。
冷却速度的这种作用主要是由下面两个原因引起的:一是随冷却速度增大,铸锭结晶速度提高,晶内结构细化;二是随冷却速度增大,铸锭过渡带尺寸缩小,铸锭致密度提高。
此外,提高冷却速度,还可细化一次晶化合物的尺寸,减小区域偏析的程度。
但是,合金成分不同,冷却速度对铸锭力学性能影响的程度是不一样的,对变形铝合金而言,大致可分为四个基本的类型:第一类是在所有温度下(从室温到熔点)均呈单相的合金,如各种牌号的高纯铝、工业纯铝、5A66、7A01等。
这些合金的铸态力学性能同冷却速度的关系不太强烈,冷却速度仅在能消除破坏金属连续性的缺陷(疏松、气孔)的极限速度之前有影响(见图2a)。
5083铝合金铸锭均匀化处理对铸锭和板材组织与性能的影响_吴欣凤

收稿日期:2007-04-29 第一作者简介:吴欣凤(1962-),女,黑龙江哈尔滨人,高级工程师。
5083铝合金铸锭均匀化处理对铸锭和板材组织与性能的影响吴欣凤(东北轻合金有限责任公司,黑龙江哈尔滨150060)摘要:系统研究了5083合金铸锭均匀化处理和不均匀化热处理对铸锭、成品板材组织和性能的影响。
通过高温瞬时试验、剥落腐蚀试验、扫描电镜及力学性能试验,对经均匀化和不经均匀化的5083铝合金铸锭的轧制制品进行对比分析。
关键词:5083铝合金;铸锭;均匀化处理;板材中图分类号:TG146.21;TG156 文献标识码:A 文章编号:1007-7235(2007)08-0048-06Effects of 5083aluminium alloy ingot homogenizing on properties and structures of ingot and platesWU Xin -feng(Northeast Light Alloy Co .,Ltd .,Harbin 150060,C hina )A bstract :The effects of 5083alu minium alloy ingot homogenizing and non -homogenizing on properties and structures of ingot and plates are researched .The rolling products by homogenizing ingot and non -homogenizing ingot are analysed and compared through high temperature property tests ,corrosion tests ,SE M analysis and machine property tests .Key words :5083aluminium alloy ;in got ;homogenizing ;plate 5083是Al -Mg 系铝合金,具有中等强度、良好的耐腐蚀性能和加工成形性能,被广泛用于交通运输、化工等领域。
高压铸造工艺参数对铝合金铸件质量的影响
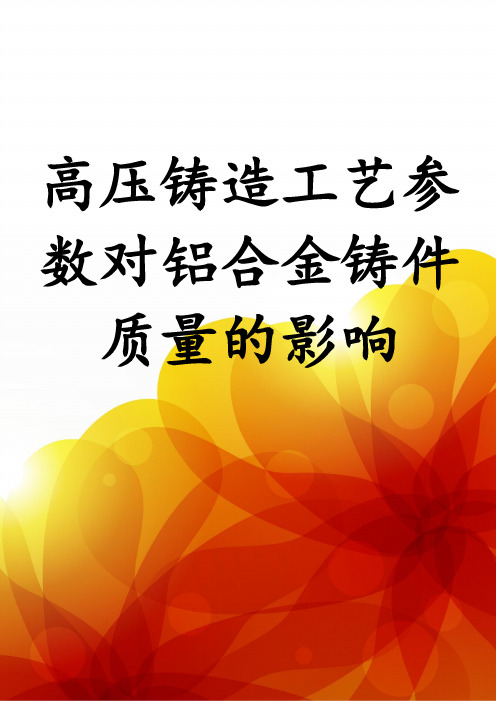
高压铸造工艺参数对铝合金铸件质量的影响高压铸造工艺参数对铝合金铸件质量的影响高压铸造是一种常用的铝合金铸造工艺,它可以通过施加高压来提高铸件的密实度和性能。
以下是高压铸造工艺参数对铝合金铸件质量的影响的步骤思考。
第一步:注射温度注射温度是指铝合金在注射过程中的温度。
注射温度的选择会影响到铸件的凝固过程和热处理的效果。
一般来说,较高的注射温度可以提高铝合金的流动性,但过高的温度可能导致铸件出现热裂纹等缺陷。
因此,选择适当的注射温度对于获得高质量的铝合金铸件至关重要。
第二步:模具温度模具温度是指铸造模具的温度。
模具温度的选择会影响到铸件的凝固速度和凝固过程中的温度梯度。
较高的模具温度可以加快铸件的凝固过程,减少凝固缩孔等缺陷的产生。
然而,过高的模具温度可能会导致铸件的表面粗糙度增加。
因此,需要在保证铸件表面质量的前提下选择适当的模具温度。
第三步:注射速度注射速度是指铝合金在注射过程中的流动速度。
注射速度的选择会影响到铸件的充型性能和缩孔的形成。
较高的注射速度可以提高铸件的充型性能,减少气体吸收和减少缩孔的产生。
然而,过高的注射速度可能会导致铸件表面出现气孔等缺陷。
因此,需要根据具体情况选择适当的注射速度。
第四步:压力持续时间压力持续时间是指在铸造过程中施加高压的时间。
压力持续时间的选择会影响到铸件的密实度和力学性能。
较长的压力持续时间可以提高铸件的密实度,但过长的时间可能会导致铸件出现过度压实等缺陷。
因此,需要平衡铸件的密实度和力学性能,选择适当的压力持续时间。
第五步:冷却时间冷却时间是指铸件冷却至室温所需的时间。
冷却时间的选择会影响到铸件的凝固过程和组织形成。
较长的冷却时间可以提高铸件的凝固性能和力学性能,减少组织缺陷的产生。
然而,过长的冷却时间可能会导致生产效率低下。
因此,需要在保证铸件质量的前提下选择适当的冷却时间。
总结:高压铸造工艺参数对铝合金铸件质量有着重要的影响。
通过合理选择注射温度、模具温度、注射速度、压力持续时间和冷却时间,可以提高铸件的密实度、凝固性能和力学性能,减少铸件缺陷的产生。
再生铝合金铸造工艺中的质量控制与质量管理方法

再生铝合金铸造工艺中的质量控制与质量管理方法铝合金是目前应用广泛的材料之一,其广泛应用于航空、汽车、建筑等领域。
再生铝合金铸造工艺是利用再生铝材料进行铸造的一种环保型工艺,具有成本低、资源节约和能源消耗少等优势。
为确保再生铝合金铸造工艺的高质量生产,需要积极采取质量控制与质量管理方法。
本文将重点讨论再生铝合金铸造工艺中的质量控制与质量管理方法。
一、原材料质量控制再生铝合金铸造工艺的原材料主要是再生铝材料。
为确保再生铝材料质量,需要进行有效的质量控制措施。
首先,进行原材料的筛选和分选工作,确保再生铝材料的杂质含量低。
其次,进行充分的再生铝材料检验,例如通过氧化铝含量、金属含量、硅含量等指标进行检测,以确保再生铝材料的化学成分符合标准要求。
在原材料质量控制方面,可采用相关仪器设备进行检测,如化学分析仪、金属检测仪等。
二、铸造工艺参数控制再生铝合金铸造工艺中,铸造的各个工艺参数对于产品质量具有重要影响。
因此,对于铸造工艺参数的控制是质量管理的关键。
首先,需要确定合适的铸造温度范围,以保证再生铝材料的流动性。
其次,根据铸件的形状和大小,确定合适的冷却时间和冷却速度。
此外,还需要确保铸造过程中的浇注速度、浇注压力以及模具的温度等参数控制在适当范围内。
通过合理控制这些铸造工艺参数,可以有效地提高再生铝合金铸件的质量。
三、质量管理体系建立质量管理是再生铝合金铸造工艺中的重要环节,建立科学有效的质量管理体系对于提高产品质量至关重要。
在质量管理体系中,应严格执行各个环节的工艺规程,确保所有工艺规范符合要求。
此外,建立健全的质量检测体系,通过对再生铝合金铸件进行严格的检测,如材料成分检测、尺寸检测、表面缺陷检测等,发现问题及时进行调整与整改措施,以确保产品符合客户要求。
四、员工培训与技能提升再生铝合金铸造工艺的质量控制与质量管理不仅仅依靠设备和工艺,员工的专业技能与经验同样重要。
因此,对于铸造工艺人员进行培训与技能提升尤为关键。
铸造工艺对对铸锭金相的影响

铸造工艺对金属铸锭组织的影响主讲教师:一、实验目的◆1.观察金属的结晶过程。
◆2.了解铸造工艺和金属的过热对铸锭宏观组织的影响。
二、实验原理金属及合金的晶粒大小、形状和分布与凝固条件、合金成分及其加工过程有关,实际生产中,铸锭不可能在整个截面上均匀冷却,并同时开始凝固。
因此,铸锭凝固后的组织一般是不均匀的,这种不均匀性将引起金属材料性能的差异。
1. 铸锭的典型组织金属铸锭横断面的宏观组织一般是由三个晶区组成。
由外向内依次分布为细晶区(外壳层)、柱状晶区和中心等轴晶区,如图1所示。
图1 金属铸锭横断面的宏观组织第一晶区是铸锭的外壳层,由细小等轴晶粒组成。
把液体金属浇入铸型,结晶刚开始时,由于铸型温度较低,形成较大的过冷度,同时模壁与金属产生摩擦及液体金属的激烈“骚动”,于是靠近型壁大量地形核,还由于型壁不是光滑的镜面,晶粒长大时,各枝晶主轴很快彼此相互接触,使晶粒不能继续长大,所以晶粒的尺寸不大,即形成细晶区。
图2表示在液体金属和铸型边界上结晶开始的情形。
等轴晶粒的第一晶区较薄,因此对铸锭的性能没有显著的影响。
第二晶区是柱状晶区。
液态金属与铸型接触处的型壁剧烈地过冷是在液体金属和铸型的分界面上生成很多小晶粒的原因,其中过冷与经过铸型激烈地传热有关,随着外壳层的形成,铸型变热,对液态金属的冷却作用减缓,这时只有处于结晶前沿的一层液态金属才是过冷的。
这个区域可以进行结晶,但一般不会产生新的晶核,而是以外壳层内壁上原有晶粒为基础进行长大。
同时,由于散热是沿着垂直于模壁的方向进行,而结晶时每个晶粒的成长又受到四周正在成长的晶体的限制,因而结晶只能沿着垂直于模壁的方向由外向里生长,结果形成彼此平行的柱状晶区如图3所示。
第三晶区是铸锭的中心部分,随着柱状晶的发展,模壁温度进一步升高,散热愈来愈慢,而成长着的柱状晶前沿的温度又由于结晶潜热的放出而有所升高。
这样整个截面的温度逐渐变为均匀。
当剩余液态金属都过冷到熔点以下时,就会在整个残留的液态金属中同时出现晶核而进行结晶。
再生铝合金铸造工艺技术的质量控制与生产管理
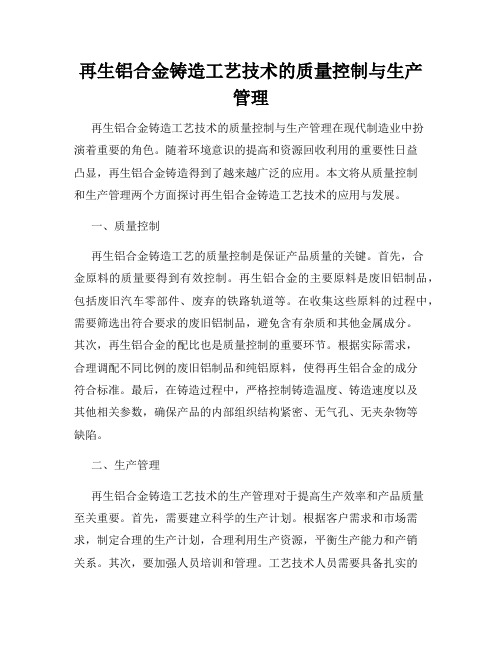
再生铝合金铸造工艺技术的质量控制与生产管理再生铝合金铸造工艺技术的质量控制与生产管理在现代制造业中扮演着重要的角色。
随着环境意识的提高和资源回收利用的重要性日益凸显,再生铝合金铸造得到了越来越广泛的应用。
本文将从质量控制和生产管理两个方面探讨再生铝合金铸造工艺技术的应用与发展。
一、质量控制再生铝合金铸造工艺的质量控制是保证产品质量的关键。
首先,合金原料的质量要得到有效控制。
再生铝合金的主要原料是废旧铝制品,包括废旧汽车零部件、废弃的铁路轨道等。
在收集这些原料的过程中,需要筛选出符合要求的废旧铝制品,避免含有杂质和其他金属成分。
其次,再生铝合金的配比也是质量控制的重要环节。
根据实际需求,合理调配不同比例的废旧铝制品和纯铝原料,使得再生铝合金的成分符合标准。
最后,在铸造过程中,严格控制铸造温度、铸造速度以及其他相关参数,确保产品的内部组织结构紧密、无气孔、无夹杂物等缺陷。
二、生产管理再生铝合金铸造工艺技术的生产管理对于提高生产效率和产品质量至关重要。
首先,需要建立科学的生产计划。
根据客户需求和市场需求,制定合理的生产计划,合理利用生产资源,平衡生产能力和产销关系。
其次,要加强人员培训和管理。
工艺技术人员需要具备扎实的专业知识和丰富的操作经验,能够熟练掌握再生铝合金铸造工艺技术,快速解决生产中的问题。
另外,还要加强设备维护和保养,避免因为设备故障导致生产中断或质量问题。
最后,要加强与供应商和客户的沟通与合作。
与供应商建立长期稳定的合作关系,确保原材料的质量和供应的及时性;与客户密切合作,了解他们的需求和反馈,不断改进产品质量和生产流程。
再生铝合金铸造工艺技术在质量控制和生产管理方面的应用与发展,不仅提高了产品质量,降低了成本,还减轻了环境污染和资源浪费。
随着科学技术的不断进步和市场需求的变化,相信再生铝合金铸造工艺技术将会在质量控制和生产管理方面取得更大的突破和进步。
总结起来,再生铝合金铸造工艺技术的质量控制与生产管理是一个综合性的工作,需要从合金原料的选择和配比、铸造过程的控制、生产计划的制定、人员培训与管理以及与供应商和客户的合作等多个方面进行全面考虑和综合应对。
铝合金熔铸过程质量的控制
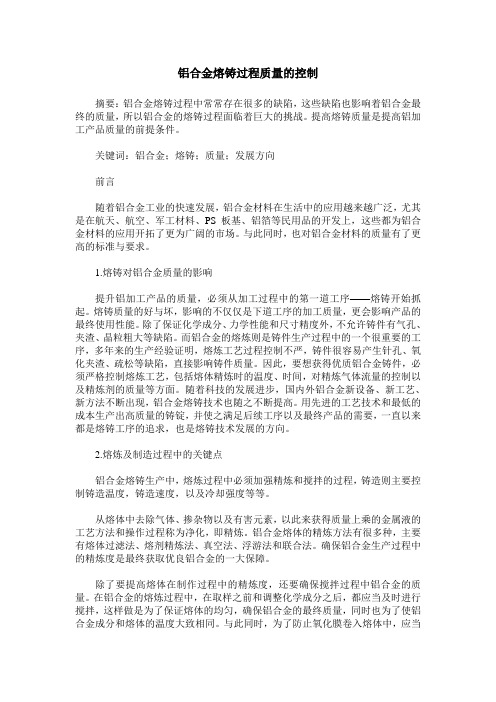
铝合金熔铸过程质量的控制摘要:铝合金熔铸过程中常常存在很多的缺陷,这些缺陷也影响着铝合金最终的质量,所以铝合金的熔铸过程面临着巨大的挑战。
提高熔铸质量是提高铝加工产品质量的前提条件。
关键词:铝合金;熔铸;质量;发展方向前言随着铝合金工业的快速发展,铝合金材料在生活中的应用越来越广泛,尤其是在航天、航空、军工材料、PS板基、铝箔等民用品的开发上,这些都为铝合金材料的应用开拓了更为广阔的市场。
与此同时,也对铝合金材料的质量有了更高的标准与要求。
1.熔铸对铝合金质量的影响提升铝加工产品的质量,必须从加工过程中的第一道工序——熔铸开始抓起。
熔铸质量的好与坏,影响的不仅仅是下道工序的加工质量,更会影响产品的最终使用性能。
除了保证化学成分、力学性能和尺寸精度外,不允许铸件有气孔、夹渣、晶粒粗大等缺陷。
而铝合金的熔炼则是铸件生产过程中的一个很重要的工序,多年来的生产经验证明,熔炼工艺过程控制不严,铸件很容易产生针孔、氧化夹渣、疏松等缺陷,直接影响铸件质量。
因此,要想获得优质铝合金铸件,必须严格控制熔炼工艺,包括熔体精炼时的温度、时间,对精炼气体流量的控制以及精炼剂的质量等方面。
随着科技的发展进步,国内外铝合金新设备、新工艺、新方法不断出现,铝合金熔铸技术也随之不断提高。
用先进的工艺技术和最低的成本生产出高质量的铸锭,并使之满足后续工序以及最终产品的需要,一直以来都是熔铸工序的追求,也是熔铸技术发展的方向。
2.熔炼及制造过程中的关键点铝合金熔铸生产中,熔炼过程中必须加强精炼和搅拌的过程,铸造则主要控制铸造温度,铸造速度,以及冷却强度等等。
从熔体中去除气体、掺杂物以及有害元素,以此来获得质量上乘的金属液的工艺方法和操作过程称为净化,即精炼。
铝合金熔体的精炼方法有很多种,主要有熔体过滤法、熔剂精炼法、真空法、浮游法和联合法。
确保铝合金生产过程中的精炼度是最终获取优良铝合金的一大保障。
除了要提高熔体在制作过程中的精炼度,还要确保搅拌过程中铝合金的质量。
铝合金熔炼与浇铸工艺参数对成分与性能的影响分析
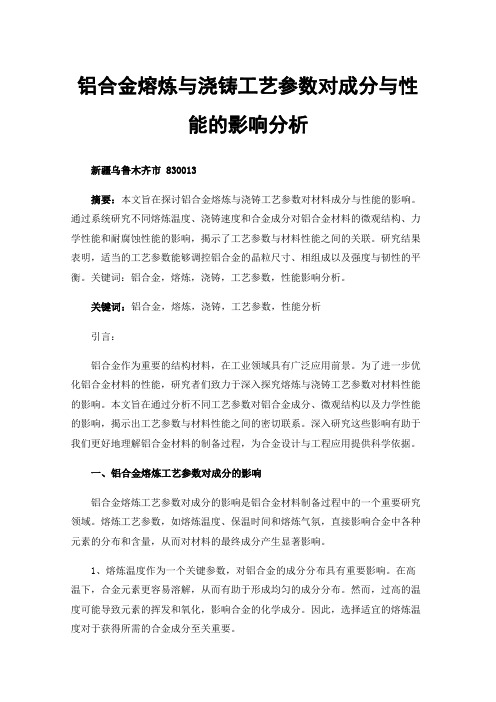
铝合金熔炼与浇铸工艺参数对成分与性能的影响分析新疆乌鲁木齐市830013摘要:本文旨在探讨铝合金熔炼与浇铸工艺参数对材料成分与性能的影响。
通过系统研究不同熔炼温度、浇铸速度和合金成分对铝合金材料的微观结构、力学性能和耐腐蚀性能的影响,揭示了工艺参数与材料性能之间的关联。
研究结果表明,适当的工艺参数能够调控铝合金的晶粒尺寸、相组成以及强度与韧性的平衡。
关键词:铝合金,熔炼,浇铸,工艺参数,性能影响分析。
关键词:铝合金,熔炼,浇铸,工艺参数,性能分析引言:铝合金作为重要的结构材料,在工业领域具有广泛应用前景。
为了进一步优化铝合金材料的性能,研究者们致力于深入探究熔炼与浇铸工艺参数对材料性能的影响。
本文旨在通过分析不同工艺参数对铝合金成分、微观结构以及力学性能的影响,揭示出工艺参数与材料性能之间的密切联系。
深入研究这些影响有助于我们更好地理解铝合金材料的制备过程,为合金设计与工程应用提供科学依据。
一、铝合金熔炼工艺参数对成分的影响铝合金熔炼工艺参数对成分的影响是铝合金材料制备过程中的一个重要研究领域。
熔炼工艺参数,如熔炼温度、保温时间和熔炼气氛,直接影响合金中各种元素的分布和含量,从而对材料的最终成分产生显著影响。
1、熔炼温度作为一个关键参数,对铝合金的成分分布具有重要影响。
在高温下,合金元素更容易溶解,从而有助于形成均匀的成分分布。
然而,过高的温度可能导致元素的挥发和氧化,影响合金的化学成分。
因此,选择适宜的熔炼温度对于获得所需的合金成分至关重要。
2、保温时间也对合金成分的均匀性产生影响。
较长的保温时间可以促使合金元素更充分地扩散,从而减小成分不均匀性。
然而,过长的保温时间可能引起合金元素的过度扩散,导致成分偏移。
因此,需要在保温时间上进行合理控制,以平衡成分均匀性和制备效率。
3、熔炼气氛是另一个重要的工艺参数,它可以影响氧化和还原反应,从而影响合金中氧、氮等杂质的含量。
通过调整熔炼气氛,可以有效控制合金中非金属元素的含量,进而影响材料的力学性能和耐腐蚀性能。
- 1、下载文档前请自行甄别文档内容的完整性,平台不提供额外的编辑、内容补充、找答案等附加服务。
- 2、"仅部分预览"的文档,不可在线预览部分如存在完整性等问题,可反馈申请退款(可完整预览的文档不适用该条件!)。
- 3、如文档侵犯您的权益,请联系客服反馈,我们会尽快为您处理(人工客服工作时间:9:00-18:30)。
铝合金铸造工艺控制对铝锭质量的影响
铸造工艺参数主要有铸造温度、铸造速度、冷却强度,其次是液位高度、铸造开始与结束条件等。
1 铸造温度
铸造沏度通常是指液体金属从保温炉通过转注工具注入结晶器过程中具确良好流动性所需要的温度。
但是,目前铝合金熔铸大部分已应用了在线除气与过滤装置,铸造温度仍然按上述的概念是不够全面与正确的。
实践证实,在线除气装置中液体温度不同具除气效果也不同。
因此,要考虑在线除气装置除气效果对液体温度的要求。
另外,还应考虑液体在结晶器内的气体析出情况,因铸造温度低,液体在结晶器内的气体来不及上浮逸出液面,造成气孔、疏松,还可能产生灾渣及冷隔等铸锭质量缺陷、铸造温度最高不宜超过熔炼温度。
铸造温度过高会导致铸造开始时漏铝。
底部裂纹与拉裂,还可能产生羽毛品组织缺陷,又因为转注工具长度不同而液体温降不同,在线装首有加热点,液体在转注过程中温度变化起伏大,所以科学规范铸造温度应指注入结晶器内的液体温度一般情况下铸造温度比合金的实际结晶温度高50℃~70℃,1 x x x、3x x x系铝合金在铸造过机中过渡带较窄,铸造温度宜偏高;而2x x x、7x x x系合金的过渡带较宽.铸造温度宜偏低。
2 铸造速度
连续铸造时,单位时间铸锭成形的长度称为铸造速度。
老式铸造
通常是一个铸次为—个固定铸造速度;而现代铸造是曲线铸造速度,即铸造开始与铸造过程不是同一个铸造速度:铸造速度的快与慢对铸锭裂纹、铸锭表面质量、铸锭组织和性能有很大影响,在保证铸锭质量的前提下,应采用最高的铸造速度。
老式铸造法为解决某些合金及规格铸锭的裂纹问题,铸造时采用铺底或回火的工艺方法;而现代铸造法则采用曲线铸锭速度,取代了老式铸造的铺底或回火工艺,它既减少了一些辅助设施,又节省了人力与减轻劳动强度,还可以避免——些铸锭表面质量缺陷铸造速度的选择是依据所生产合金的特性与铸锭截面尺寸而定。
一般规律足冷裂纹倾向性较大的合金及铸锭规格,应提高铸造速度;而热裂纹倾向较大的合金及铸锭规格,则应降低铸造速度
3 冷却强度
冷却强度也称为冷却速度。
冷却强度不但对铸锭的裂纹有影响,而且对铸锭的组织影响更大、随着冷却强度的增大,铸锭结晶速度提高,晶内结构更加细化;随着冷却强度增人,铸锭液穴变浅。
过渡带尺寸缩小.使金属补缩条件得到改善,减少或消除了铸锭中的疏松、气孔等缺陷.铸锭致密度提高:另外还可以细化一次品化合物的尺寸,减小区域偏析的程度。
老式铸造法多采用分体结晶器,尤其是铸造扁铸锭时.水套与结晶器是分开的。
随着铸造工艺技术的发展,现代铸造法的结晶器是一体的。
用老式结晶器铸造时冷却水消耗量大,因为老式结晶器供水不是封闭的,一部分冷却水敞火而起不到冷却作用,而且一次冷却与
二次冷却的冷却强度差别人,不可避免的产生一些铸锭质量缺陷;而用现代结晶器铸造时.冷却水消耗量小.实践证实它仅是老式结晶器用水量的70%左右。
目前国外多采用低液位结晶器铸造,其目的就是提高冷却强度,减少或消除一次冷却后气隙区的加热现象,因此几乎不存在二次冷却的淬火情况、扁铸锭普通铸造已经将结晶器高度降至100人,当然这需要操作者有很高的操作水平或增设液位白动控制系统。
冷冲却强度对冷却水温度的要求是不可忽视的,通常情况下,冷却水温设定在20、,但是由于地区气候条件。
供水设施条件及厂房温度等不同导致变化较大,因而出现地区性或季节性铸锭质量缺陷。
现代结晶器供水系统带有脉冲或交叉变相功能,均由工艺编程决定,因此冷却强度可依据铸造工艺需要设定为曲线,非凡是针对某些低温塑性不好的硬合金,铸造时冷裂纹和热裂纹几乎同时存在,附加挡水板系统,使铸锭表面温度升高到拉伸变形塑性温度,消除铸锭冷裂纹,工艺上再采取防止热裂纹措施,即可以获得优质铸锭
4 结束语
稳定的铸锭质量是铸造工艺参数最佳组合的结果,而最佳铸造工艺参数是根据铸造理论与实践结合而得出的。
目前铝合命材料在性能方面要求更高,老式铸造工艺装备已经不适应新技术发展的要求,加速其改造才能与时俱进。