第8章 铸造讲解
合集下载
铸造精品PPT课件
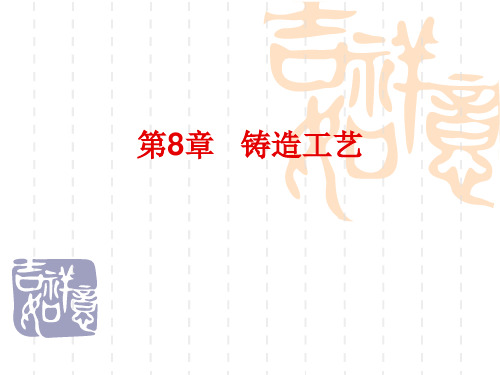
影响流动性因素:
合金种类:灰口铸铁,硅黄铜,
流动性最好,l 1000 mm 。铸钢 的流动性最差, l 200 mm;
成分:共晶合金的流动性最好; 结晶特征:结晶温度范围越大,
枝晶越发达,流动性越差;结晶 间隔越小,则流动性越好;
粘度:粘度越大,流动性越差; 结晶潜热:结晶潜热越小,流动
性越差。
▪凝固收缩
共晶成分或纯金属是在恒温下凝固,凝固收缩只由状态改变 引起,所以收缩较小,亦表现为液面下降。 ▪ 液态收缩和凝固收缩主要表现为合金体积上的缩减 ,用体收缩率(单位体积的百分收缩量)表示。它们 是铸件产生缩孔和缩松的根本原因。 ▪固态收缩
通常直接表现为铸件外形尺寸的减小,可用线收缩 率(单位长度的百分收缩量表示)。固态收缩是铸件 产生应力、变形和裂纹的根本原因。
§8-1 铸造概述
金属铸造
1. 定义:将熔炼好的液态金属浇注到与零件形状 尺寸相适应的铸型型腔内,待其冷却凝固后,获得毛坯 或零件的方法。
2.铸造方法:砂型铸造 特种铸造
优点与缺点
▪ 与其它金属加工方法相比,铸造具有如下优点: (1)原材料来源广。 (2)生产成本低。 (3)铸件形状与零件接近,形状、尺寸不受限制。 尤其适于制造内腔复杂的大型箱体件。
影响铸件收缩的主要因素:
➢化学成分:铸钢和白口铸铁收缩率大,灰铸铁、球墨铸 铁铁小(结晶时石墨产生的膨胀抵消了部分收缩); ➢浇注温度:T↑ →收缩率大; ➢铸件结构:壁厚不均匀↑ →收缩受阻↑ →收缩率小; ➢铸型条件:铸型、型芯阻碍收缩力↑ →收缩率小
2. 收缩导致的铸件缺陷
(1)缩孔和缩松
铸造的基本工艺过程
零件 模样 型砂 芯盒 砂箱 型芯
配制的型砂
铸造(全)讲解

铸造工艺基础
(4)涂料 为防止液态金属与砂型表面相互作用产生粘
砂等缺陷,在型腔表面涂覆一薄层涂料。常 用的涂料是石墨粉。石墨粉熔点大于3000℃ 在高温下与少量氧气化合而燃烧产生气体, 使液态金属与砂型不直接接触。
铸造工艺基础
2、模样和芯盒
(1)模样和芯盒 模样—用于形成铸型的型腔,它和铸 件的外形相适应。 芯盒—用于制造芯子,其内腔与芯子 的形状和尺寸相适应。
(1)型砂和芯砂应具备的性能:
①可塑性。 塌箱、冲砂、砂眼
②强度。
气孔
③耐火度。 ④透气性。
粘砂→切削 加工困难
⑤容让性。
内应力、裂纹
1
铸造工艺基础
1—砂粒
2—空隙
3—附加物
(2)型砂的组成
4—粘土膜
型砂
原砂
粘结剂
附加材料
旧砂
山 海河粘 膨 煤 锯
处
润
木
理
地 滨滨土 土 粉 屑
过
SiO2
强度、可塑性
铸造工艺基础
2、现状:
我国铸件产量从2000年起超越美国已连续6年位居世界第一。 十大铸件生产国可分为两类: 一类是发展中国家,虽然产量大,但铸件附加值低,小企业多,从业人 员队伍庞大,黑金属比重大。
一类是发达国家,如美国、日本及欧洲一些国家等,他们采用高新技术 主要生产高附加值铸件。 如表
在机械装备中,铸件占整机重量的比例很高 :
(2)制造ቤተ መጻሕፍቲ ባይዱ样和芯盒的注意要点
①分型面—铸型组元间的接合面。
②收缩余量—为了补偿铸件收缩,模 样比铸件图样尺寸增大的数值。
③机械加工余量—为保证铸件加工面 尺寸和零件精度,在铸造工艺设计时预 先增加而在机械加工时切去的金属层厚 度。
铸造ppt
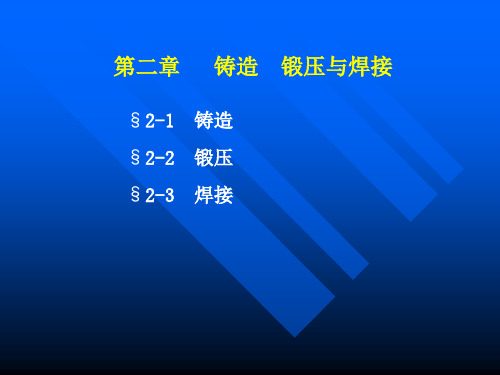
5、适于生产大批量有色金属铸件。
熔模铸造:
定义:在易熔模样(简称熔模)的表面包覆多层耐火
材料,然后将模样熔去,制成无分型面的型壳,经焙烧、 烧注而获得铸件的方法称为熔模铸造。
工艺过程:a) 压型
结壳脱模
e) 浇铸
b) 压制蜡模 c) 焊蜡模组 f) 带有浇铸系统的铸件
d)
a)
b)
c) d) 熔模铸造工艺过程
机器造型采用模板两箱造型。模板上安装模样、浇
注系统、并以分型面为界,分上、下两块,分别在两台 配对的造型机上造型。 紧砂方法 机械造型大都以压缩空气为动力来紧实型砂。
压实、振实、振压和抛砂。
3、造型、造芯及合箱 放置模样、填充、紧实型砂、起模、造出浇冒口和 通气口、合箱。最关键部分是起模。 起模方法: 顶箱起模:结构简单,
生产率低,劳动强度大,铸件尺寸精度和表面质量差,
特大型铸件只能采用手工造型。 1)整模造型 采用整体模样造型的方法。
整模造型过程 适用于最大截面在一端且为平面的铸件
1)分模造型 模样在最大截面处分为两半,分别处于上、下砂型内的造 型 方法称为分模造型。
分模造型过程 适用于最大截面在中间的铸件
2 、机器造型 机器造型在于使紧砂和起模两个步骤采用全部或者部 分实现机械化。可大大提高生产率和铸件质量,改善工 人劳动条件,适用于中、小型铸件的批量生产。
强度高,内部耐磨性好,还可节约贵重金属。
4)离心铸件内表面粗糙,尺寸不易控制,需增大加工 余量来保证铸件质量,且不适宜易产生偏析的合金。
连续铸造:
定义:是指将熔融金属连续不断地浇注到被成为结晶
器的特殊容器中,凝固的铸件不断从结晶器的另一端被引 出,从而获得任意长度的等横截面铸件的铸造方法。
熔模铸造:
定义:在易熔模样(简称熔模)的表面包覆多层耐火
材料,然后将模样熔去,制成无分型面的型壳,经焙烧、 烧注而获得铸件的方法称为熔模铸造。
工艺过程:a) 压型
结壳脱模
e) 浇铸
b) 压制蜡模 c) 焊蜡模组 f) 带有浇铸系统的铸件
d)
a)
b)
c) d) 熔模铸造工艺过程
机器造型采用模板两箱造型。模板上安装模样、浇
注系统、并以分型面为界,分上、下两块,分别在两台 配对的造型机上造型。 紧砂方法 机械造型大都以压缩空气为动力来紧实型砂。
压实、振实、振压和抛砂。
3、造型、造芯及合箱 放置模样、填充、紧实型砂、起模、造出浇冒口和 通气口、合箱。最关键部分是起模。 起模方法: 顶箱起模:结构简单,
生产率低,劳动强度大,铸件尺寸精度和表面质量差,
特大型铸件只能采用手工造型。 1)整模造型 采用整体模样造型的方法。
整模造型过程 适用于最大截面在一端且为平面的铸件
1)分模造型 模样在最大截面处分为两半,分别处于上、下砂型内的造 型 方法称为分模造型。
分模造型过程 适用于最大截面在中间的铸件
2 、机器造型 机器造型在于使紧砂和起模两个步骤采用全部或者部 分实现机械化。可大大提高生产率和铸件质量,改善工 人劳动条件,适用于中、小型铸件的批量生产。
强度高,内部耐磨性好,还可节约贵重金属。
4)离心铸件内表面粗糙,尺寸不易控制,需增大加工 余量来保证铸件质量,且不适宜易产生偏析的合金。
连续铸造:
定义:是指将熔融金属连续不断地浇注到被成为结晶
器的特殊容器中,凝固的铸件不断从结晶器的另一端被引 出,从而获得任意长度的等横截面铸件的铸造方法。
铸造工艺基础大全课件
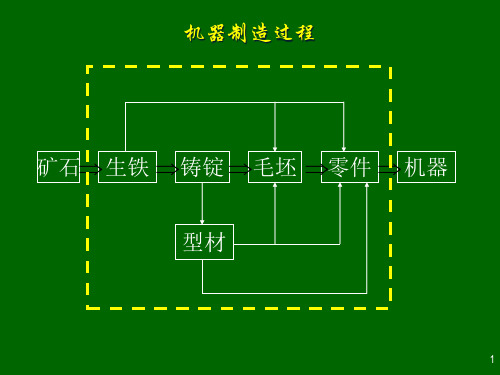
有残余应力旳铸件,经机械加工,一段时间 后,将产生变形,影响零件精度。
30
二 .铸件旳变形与预防 由铸造应力旳形成过程可知,铸件旳变形发生 在铸造应力超出材料旳屈服极限时。所以预 防铸件产生变形旳根本措施是消除铸造应力。 另外还能够从工艺上采用措施 1)反变形-----制造模型时采用反变形。 2)变化铸件构造----如改用弯轮辐替代直轮辐 3)设置拉筋----在铸造应力集中旳部位设置拉 筋,热处理后清除 4)控制打箱时间。
应力。 内应力发生在铸件凝固后来旳继续冷却过程中, 一般以为由下列三种情形产生: 1)二次结晶时,新相与旧相体积不同,膨胀与收缩将 产生----相变应力。 2)温度分布不同,各处收缩量不同步,内部相互制约, 产生---热应力。 3)收缩时受到铸型、型芯旳阻碍,产生----收缩应力。
26
应力状态------拉应力和压应力、剪应力。 应力性质-----分为临时应力和残余应力。 1 .热应力----因为铸件旳壁厚不均匀、各部分旳 冷却速度不同,使得在同一时期内铸件各部 分收缩不一致而引起旳应力。
机器制造过程
矿石生铁 铸锭 毛坯 零件 机器 型材
1
第二节 铸造
第一 铸造工艺基础 铸造----将液态合金浇注到与零件形 状、尺寸相适应旳铸型空腔中,待 其冷却凝固,以取得毛坯或零件旳 生产措施称为铸造。 影响铸件质量旳原因诸多,其中合 金旳铸造工艺性就是主要原因之一。
2
3
铸造生产过程
§1 液态合金旳充型 充型----液态合金填充铸型旳过程。 充型能力-----液态合金充斥铸型型腔,取得 形状完整、轮廓清楚铸件旳能力。 影响充型能力旳主要原因有: 一 .合金旳流动性 流动性----液态合金本身旳流动能力。
27
再结晶温度以上时,金 属处于塑性状态,不产
30
二 .铸件旳变形与预防 由铸造应力旳形成过程可知,铸件旳变形发生 在铸造应力超出材料旳屈服极限时。所以预 防铸件产生变形旳根本措施是消除铸造应力。 另外还能够从工艺上采用措施 1)反变形-----制造模型时采用反变形。 2)变化铸件构造----如改用弯轮辐替代直轮辐 3)设置拉筋----在铸造应力集中旳部位设置拉 筋,热处理后清除 4)控制打箱时间。
应力。 内应力发生在铸件凝固后来旳继续冷却过程中, 一般以为由下列三种情形产生: 1)二次结晶时,新相与旧相体积不同,膨胀与收缩将 产生----相变应力。 2)温度分布不同,各处收缩量不同步,内部相互制约, 产生---热应力。 3)收缩时受到铸型、型芯旳阻碍,产生----收缩应力。
26
应力状态------拉应力和压应力、剪应力。 应力性质-----分为临时应力和残余应力。 1 .热应力----因为铸件旳壁厚不均匀、各部分旳 冷却速度不同,使得在同一时期内铸件各部 分收缩不一致而引起旳应力。
机器制造过程
矿石生铁 铸锭 毛坯 零件 机器 型材
1
第二节 铸造
第一 铸造工艺基础 铸造----将液态合金浇注到与零件形 状、尺寸相适应旳铸型空腔中,待 其冷却凝固,以取得毛坯或零件旳 生产措施称为铸造。 影响铸件质量旳原因诸多,其中合 金旳铸造工艺性就是主要原因之一。
2
3
铸造生产过程
§1 液态合金旳充型 充型----液态合金填充铸型旳过程。 充型能力-----液态合金充斥铸型型腔,取得 形状完整、轮廓清楚铸件旳能力。 影响充型能力旳主要原因有: 一 .合金旳流动性 流动性----液态合金本身旳流动能力。
27
再结晶温度以上时,金 属处于塑性状态,不产
铸造基本知识及理论ppt课件

正确设置浇注位置和分型面是完成外型、取模、设置 浇冒系统和安装砂芯的需求。 ➢ 确定主要工艺参数:
正确选择收缩量、 机械加工余量和拔模 斜度等。
拔模斜度
➢ 浇注系统的设计:
浇注系统是铸型中液态金属流入型腔的通道;通常由 交口杯、直浇道、横浇道和内浇道等组成。 设计原那么:确保液态金属可以平 稳 而合理地充溢型腔。 ➢ 补缩系统的设计:
➢ 缩孔:
定义:缩孔是指金属液在铸模中冷却和凝固时, 在铸件的厚大部位及最后凝固部位构成一些容积 较产大生的缘孔由洞:。先
凝固区域堵住 液体流动的通 道,后凝固区 域收缩所缩减 的容积得不到
➢ 疏松:
定义:疏松是指金属液在铸模中冷却和凝固时, 在铸件的厚大部位及最后凝固部位构成一些分散 产性生的缘小由孔:洞。当合金的结晶温度范围很宽或铸件 断面温度梯度较小时,凝固过程中有较宽的糊状 凝固两相并存
温的过
分程类中:,分其为体三积类或,尺液寸态缩收减缩的、景凝象固。收缩和固态
收缩。
浇注温度
铸 液态收缩
件 温
开场凝固温度
体
度 降
凝固收缩
积 收
低
缩
凝固终止温度
固态收缩
室温
线收缩
收缩率: 体积收缩是指单位体积的收缩量〔体积收缩 率〕。 线体收积缩收是缩率指:单位长V度上V0V 的1V 收1缩1量0〔% 0线收缩率〕。
顺序凝固:是指经过在铸件上能够出现疏松的厚大部位 安装冒口或放置冷铁等工 艺措施,使铸件上远离冒 口的部位先凝固〔图中 Ⅰ〕,尔后在接近冒口的 部位凝固〔图中Ⅱ、Ⅲ〕, 最后是冒口本身凝固。
顺序凝固表示图
内置冷铁法 外置冷铁法
设置冒口法 冒口、冷铁共用法
➢ 裂纹与变形:
正确选择收缩量、 机械加工余量和拔模 斜度等。
拔模斜度
➢ 浇注系统的设计:
浇注系统是铸型中液态金属流入型腔的通道;通常由 交口杯、直浇道、横浇道和内浇道等组成。 设计原那么:确保液态金属可以平 稳 而合理地充溢型腔。 ➢ 补缩系统的设计:
➢ 缩孔:
定义:缩孔是指金属液在铸模中冷却和凝固时, 在铸件的厚大部位及最后凝固部位构成一些容积 较产大生的缘孔由洞:。先
凝固区域堵住 液体流动的通 道,后凝固区 域收缩所缩减 的容积得不到
➢ 疏松:
定义:疏松是指金属液在铸模中冷却和凝固时, 在铸件的厚大部位及最后凝固部位构成一些分散 产性生的缘小由孔:洞。当合金的结晶温度范围很宽或铸件 断面温度梯度较小时,凝固过程中有较宽的糊状 凝固两相并存
温的过
分程类中:,分其为体三积类或,尺液寸态缩收减缩的、景凝象固。收缩和固态
收缩。
浇注温度
铸 液态收缩
件 温
开场凝固温度
体
度 降
凝固收缩
积 收
低
缩
凝固终止温度
固态收缩
室温
线收缩
收缩率: 体积收缩是指单位体积的收缩量〔体积收缩 率〕。 线体收积缩收是缩率指:单位长V度上V0V 的1V 收1缩1量0〔% 0线收缩率〕。
顺序凝固:是指经过在铸件上能够出现疏松的厚大部位 安装冒口或放置冷铁等工 艺措施,使铸件上远离冒 口的部位先凝固〔图中 Ⅰ〕,尔后在接近冒口的 部位凝固〔图中Ⅱ、Ⅲ〕, 最后是冒口本身凝固。
顺序凝固表示图
内置冷铁法 外置冷铁法
设置冒口法 冒口、冷铁共用法
➢ 裂纹与变形:
铸造实训讲义
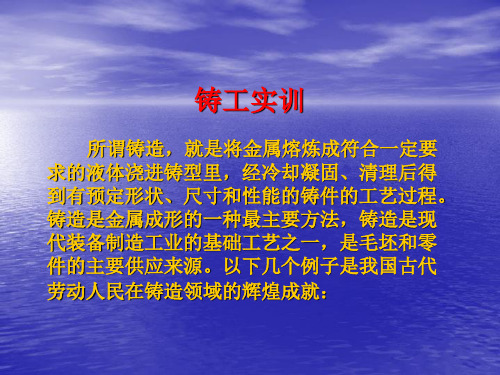
浇注系统示意图
底铸式示意图
铸型 铸型是用型砂、金属材料或其他耐火材 料制成的,主要由上型(上箱)、下型( 下箱)、浇注系统、型腔、型芯、冒口和 通气孔组成。用型砂制成的铸型称为砂型 。 冒口 是供补缩铸件用的铸型空腔,内存液态 金属。分明冒口和暗冒口。还具有观察、 排气和集渣的作用。
铸型装配示意图
造型工艺
1 、分型面;上砂型与下砂型的接触面,在铸造工艺
图上用箭头表示,并写上“上”,“下”字样 分型面选取原则: ① 尽量选取在铸件的最大截面处,便于起模和造型 ② 应简单平直,数量尽可能少,便于简化造型,减少 错箱 ③ 铸件全部或大部位于同一砂箱,减少型芯、活块数 量,利于型芯的定位排气
2、浇注系统: 外浇口:承接金属液并起缓冲和集渣作用。 有漏斗形或者盆式,使金属液平稳流入直 浇道。 直浇道:利用高度使液体产生静压力和流速, 保证液态金属充满型腔。直横相交处做成 大的球窝,返回后流入。 横浇道:分配金属液,起到挡渣、缓冲作用。 梯形截面 内浇道:控制金属液流入型腔的方向和流速, 调节铸件各部的冷却速度。截面多为扁梯 形或矩形。
手工造型基本步骤:
1. 将模型擦拭干净 2. 放在砂箱内造下型 3. 翻转下型180°将模型最大 截面处分型面修好 4. 放上箱撒分型砂,放浇口 棒,造上型 5. 扎通气孔拔浇口棒,修好 浇口处浇口,画定位线
6. 垂直向上搬开上型清理分 型面 7. 开横内浇道,修好铸型,清理好型内
砂粒 8. 在模样周边与砂型接触的地方刷适量 的水,把起模针放在模型的重心处, 用榔头四周敲击起模针使下部松动模 型,先慢后快垂直取走模型。
谢谢 !
马炳洲2017年3月于华清
整模造型示意图
分模造型
挖砂造型
铸造课件论述可编辑全文
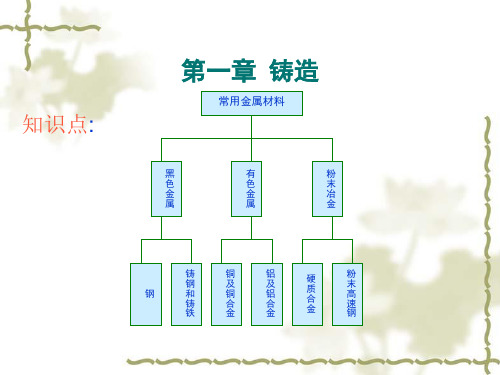
浇不足
冷隔
夹砂
气孔
夹渣
充型能力的决定因数
合金的流动性 铸型性质 浇注条件 铸件结构等
合金的充型能力
测试合金充型 能力的方法:
如右图,将合 金液浇入铸型中, 冷凝后测出充满型 腔的式样长度。浇 出的试样越长,合 金的流动性越好, 合金充型能力越好.
几种不同合金流动性的比较
比较下面几种合金流动性能 *铸钢的流动性
裂纹
当热应力大到一定程度会导致出现裂纹。
热应力的形成过程演示
热应力的消除方法
铸件的结构:铸件各部分能自由收缩
铸件的结构尽可能对称 铸件的壁厚尽可能均匀
工艺方面:采用同时凝固原则 时效处理:人工时效;自然时效
铸件的变形原因
结论: 厚部、心部受拉应力, 出现内凹变形。 薄部、表面受压应力, 出现外凸变形。
铸件的结构
凡能增加金属流动阻力和冷却速度,降低流速的因素,均能降低金属的流动性。 如型腔过窄,浇注系统结构复杂,直浇道过低,内浇道截面太小,型砂水分 过多或透气性不好,铸型材料热导性过大等,都会降低金属的流动性。
铸件结构对充型能力的影响
折算厚度:
复杂程度:
折算厚度也叫当量厚度 或模数,是铸件体积与铸件 表面积之比。折算厚度越大, 热量散失越慢,充型能力就 越好。
孕育铸铁应用:一般用于动载荷较小、静载荷较大, 对强度、硬度、和耐磨性要求较高的重要铸件,尤 其是厚大铸件,如床身、凸轮轴、汽缸体等
灰铸铁的铸造性能:流动性好、 收缩小,铸造性能好, 具有自身补缩的能力。
铸造工艺特点:冲天炉熔炼(金属炉料、燃料、熔剂) 砂型铸造 常采用同时凝固原则,高强度采用顺序凝固
成本低,原材料来源广泛, 价格低廉,一般不需要昂 贵的设备
第八章铸件形成技术基础幻灯片精品PPT课件

7
③ 在“多孔管”中流动
砂型具有透气性,其浇注系统和型腔可看作“多孔”的管道和容 器缺。陷:a)铸件表面粘砂:压力过大,金属液被压入型壁砂粒间的间隙内;
b)卷入性气孔:液流与浇道壁不贴附,外界气体被带入型腔
④ 紊流流动
紊流:指流体从一种稳定状态向另一种稳定状态变化过程中的一种无序状态。 流动时惯性力占主要地位。
金属型 (300℃)
砂型
砂型 砂型
浇注温度/℃ 1300
1600 1640 680-720
700 1040 1100
螺旋线长度/mm 1800 1300 1000 600
100 200 700-800
400-600 420 1000
6
二、液态金属的充型特点和对铸件质量的影响
① 粘性液体流动
水:无粘性,匀质的单相体 液体金属:粘性,非匀质的多相体(S、L、G)
1
§8-1 液态金属的充型
一、液态金属的充型能力
--铸件形成的第一阶段
基本概念:液态金属充满铸型型腔,获得形状完整、轮廓清晰
的铸件的能力,即液态金属充填铸型的能力,简称 液态金属的充型能力
实验证明,同一种金属用不同的铸造方法,所能铸造的铸件最小壁厚不同。 同样的铸造方法,由于金属不同,所能得到的最小壁厚也不同,如表所示。
22
⑤ 金属的比热容、密度和导热系数
比热容和密度较大的合金,因其本身含有较多的热量,在相同 的过热度下,保持液态的时间长,流动性好。 导热系数小的合金,热量散失慢,保持流动的时间长;导热系 数小,在凝固期间液固并存的两相区小,流动阻力小,故流动 性好。
⑥ 合金的熔炼过程
控制气体和夹杂物的含量,降低其含量,使粘度降低。
16
③ 在“多孔管”中流动
砂型具有透气性,其浇注系统和型腔可看作“多孔”的管道和容 器缺。陷:a)铸件表面粘砂:压力过大,金属液被压入型壁砂粒间的间隙内;
b)卷入性气孔:液流与浇道壁不贴附,外界气体被带入型腔
④ 紊流流动
紊流:指流体从一种稳定状态向另一种稳定状态变化过程中的一种无序状态。 流动时惯性力占主要地位。
金属型 (300℃)
砂型
砂型 砂型
浇注温度/℃ 1300
1600 1640 680-720
700 1040 1100
螺旋线长度/mm 1800 1300 1000 600
100 200 700-800
400-600 420 1000
6
二、液态金属的充型特点和对铸件质量的影响
① 粘性液体流动
水:无粘性,匀质的单相体 液体金属:粘性,非匀质的多相体(S、L、G)
1
§8-1 液态金属的充型
一、液态金属的充型能力
--铸件形成的第一阶段
基本概念:液态金属充满铸型型腔,获得形状完整、轮廓清晰
的铸件的能力,即液态金属充填铸型的能力,简称 液态金属的充型能力
实验证明,同一种金属用不同的铸造方法,所能铸造的铸件最小壁厚不同。 同样的铸造方法,由于金属不同,所能得到的最小壁厚也不同,如表所示。
22
⑤ 金属的比热容、密度和导热系数
比热容和密度较大的合金,因其本身含有较多的热量,在相同 的过热度下,保持液态的时间长,流动性好。 导热系数小的合金,热量散失慢,保持流动的时间长;导热系 数小,在凝固期间液固并存的两相区小,流动阻力小,故流动 性好。
⑥ 合金的熔炼过程
控制气体和夹杂物的含量,降低其含量,使粘度降低。
16
- 1、下载文档前请自行甄别文档内容的完整性,平台不提供额外的编辑、内容补充、找答案等附加服务。
- 2、"仅部分预览"的文档,不可在线预览部分如存在完整性等问题,可反馈申请退款(可完整预览的文档不适用该条件!)。
- 3、如文档侵犯您的权益,请联系客服反馈,我们会尽快为您处理(人工客服工作时间:9:00-18:30)。
1、合金成分的影响 纯金属和共晶成分合金的流动性最好。 合金的结晶间隔愈宽,其流动性愈差。铸铁中的
硅和磷能提高流动性,而硫和锰多以MnS的形式悬 浮在铁水中,阻碍着铁水的流动,使它的流动性变 差。 2、浇注条件的影响
温度,压力,充型速度。 3、铸型条件对流动性的影响
阻力,导热性,透气和排气。 4、铸件的凝固方式对合金的流动性影响较大
—
铸 件 发 动 机 机 体
铸 造 生 产
装 置
8.1.1 铸造的特点
铸造生产的优点: 1、适用范围广。铸件的外形尺寸和重量几乎不受
限制(大到几百吨,小到几克重)。 2、铸造材料广泛。 3、铸件尺寸精度高。 4、生产成本低。 铸造生产的缺点: 1、工序多、工艺过程控制较难、劳动强度大。 2、工艺过程控制较难,铸件质量不稳定。
• 概念:铸造性能是指合金铸造成形获得优质 铸件的能力。
• 合金的铸造性能指标:流动性、收缩性、氧 化性、偏析和吸气性等
8.2.1 合金的流动性和充型能力
• 合金的流动性是指熔融合金的流动能力, 浇注时液态金属填充铸型的能力。它与合 金种类、结晶特点、粘度等有关。流动性 好,充型能力强,可以得到形状复杂、轮 廓清晰铸件,缺陷少、补缩好;流动性差, 易于产生浇不足、冷隔。良好的流动性是 获得优质铸件的基本条件。
8.2.2 合金的收缩
金属由液态向固态的冷却过程中, 其体 积和尺寸减小的现象称为收缩。 三个收缩 阶段: 液态收缩,凝固收缩,固态收缩。在常 用的合金中,铸钢的收缩最大,灰铸铁的 最小。影响收缩的因素 :化学成分、浇注 温度、铸件结构和铸型条件等。
合金的收缩对铸件质量有着不利影响。 导致铸件产生缩孔和缩松,铸造内应力、 变形和裂纹等缺陷。
温度)之间的收缩。
• (3)固态收缩
• 是指合金从凝固终止温度冷却到室温之间的收缩, 这是处于固态下的收缩。
2、铸件缩孔、缩松
(1)缩孔: 液体金属浇注到铸型中后,经过液态收缩和凝
固收缩,体积会缩减。若其收缩得不到液体金属的及时补充, 则在铸件最后凝固部位形成孔洞,这种孔洞称为缩孔。形成
过程见图8-4:a.金属液充满型腔、b.形成硬壳、c.液 面下降、d.继续下降、e.形成缩孔。
第8章
铸造
本章任务: 1、掌握铸造工艺过程; 2、掌握铸造缺陷和预防措施; 3、熟悉铸造特点和铸造方法; 4、了解铸造原理和先进铸造方法。
8.1 概述
铸造是金属材料液态成形的一 种重要工艺方法,即将熔融金属浇 注、压射或吸入铸型型腔,冷却、 凝固后使之成为具有一定形状和性 能的铸件产品。
浇铸车间
8.1.2 铸件的凝固
• 铸造过程实际上是金属材料从固态→液态 →固态的转变过程。铸件的质量和机械性
能主要取决于柱状晶和等轴晶的比例。铸 件中柱状晶和等轴晶的比例一主面取决于 合金的成分,另一方面取决于铸件的凝固 方式。铸件的凝固一般存在固相区、凝固 区和液相区3个区域,根据凝固区宽度不同, 铸件的凝固方式可分为逐层凝固、糊状凝 固和中间凝固三种形式。
• 1、合金的收缩
• 合金的收缩分三个阶段(Ⅰ)液态收、(Ⅱ)凝固收缩、 (Ⅲ)固态收缩。
图8-3铸造合金的收缩
• 任何一种液态金属注入铸型以后,从浇注温度冷 却到常温都要经历三个互相联系的收缩阶段。
• (1)液态收缩
• 是指液态金属由浇注温度冷却到凝固开始温度 (液相线温度)间的收缩。
• (2)凝固收缩 • 是指从凝固开始温度到凝固结束温度(固相线
浇口
a)
b)
c)
d)
e)
图 8-4 缩孔形成示意图
(2)缩松
缩松是分散在铸件最后凝固部位的细小缩孔。形成原因:
由于结晶温度范围宽的合金呈糊状凝固,先析出的枝晶把液体 分隔开,使其收缩难以得到补充所致。形成过程如下图。
缩
松
凝
固
同ห้องสมุดไป่ตู้
前
时
沿
凝
固
区
a)
b)
c)
图 8-5 缩松形成示意图
(3)缩孔、缩松的防止
1、逐层凝固
纯金属或共晶成分合金凝固过程中不存在液、 固并存现象,液固界限清楚分开,称为逐层 凝固。
2、糊状凝固
合金的结晶温度范围很宽,温度分布较平坦 (内外温度较小),整个断面内均为液固并存, 先呈糊状而后固化,称为糊状凝固。
3、中间凝固
界于逐层凝固和湖状凝固之间
图8—1 铸件的凝固方式
8.2 合金的铸造性能
• (2)机械应力:机械应力是当铸件收缩时, 受到铸型、型芯或浇冒口等机械阻碍而产 生的应力。机械应力一般为拉应力,落砂 后阻碍消除,应力自行消失。
8-7 同时凝固示意图
3 、铸造应力、变形与裂纹
• 铸件凝固之后继续冷却时产生的应力,其 中部分一直保留到室温,成为残余内应力, 称为铸造内应力。
• 铸造应力主要包括热应力和机械应力。这 两种应力如果得不到及时消除,铸件在应 力作用下容易产生变形,甚至产生开裂。
• (1)热应力: 由于形状复杂,厚薄不均, 各部分的冷却速度不同,以至在同一时刻, 铸件各部位收缩不一致而引起的内应力称 为热应力。
浇注温度和浇注速度、浇注系统对铸件的收缩有影 响。快浇有利于“顺序凝固”。慢浇有利于“同时凝固”。 应该指出,两种方式在凝固上虽然是对立的,但在某个具 体铸件上以可以将两者结合应用。
•生产中常用的冷铁材料有铸铁、铝合金、石墨 和铜合金等 。 •可以制作冷铁的材料很多,凡是比砂型材料的 热导率、蓄热系数大的金属和非金属材料均可选 用。
①顺序凝固 防止缩孔的具体措施是采取顺序凝
固原则。所谓顺序凝固,就是采取一定的工艺措施 (如加放冒口、冷铁),保证铸件结构上各部分按照 远离冒口的部分最先凝固,然后是靠近冒口的部分, 最后才是冒口本身凝固的次序进行。
浇注系统
冒口
图—冒口补缩示意图
冷铁
a)
b)
c)
顺序凝固可使铸件各部位的收缩均得到金属液补缩, 而缩孔则移至冒口,最后将冒口切除,见图8-6所示。
图8-6 顺序凝固示意图
②同时凝固
同时凝固就是使铸件的各部位几乎同时冷却凝固, 以防止缩口产生。例如:在铸件比较厚的部位或紧靠厚的 部位处的铸型上安放冷铁,如图8-7所示。同时凝固可减 轻铸件热应力,防止铸件变形和开裂,但是容易在铸件心 部出现缩松。同时凝固仅适用于收缩小的合金铸件,如碳、 硅含量较高的灰口铸铁件。