固定床、流化床、移动床、浆态床比较
流化床,固定床

①对强放热反应固定床温度难控,浆态床易控,这造成固定床催化效率要比浆态床低,因反应温度不能太高,而且固定床内催化剂有一部分没用。
固定床存在床层阻力,压降比浆态床大,在反应器内部,浆态床几乎没压降,但在催化剂过滤器两端的压降会比较大②固定床工业放大比浆态床容易;浆态床内构件比固定床复杂;浆态床虽可实现催化剂在线更换,但细小催化剂分离比较困难;浆态床对催化剂强度的要求比固定床高;固定床停车更换催化剂要比浆态床麻烦的多。
③如果是气液固三相反应,浆态床的气体传质比固定床差,对气体分布的要求较高,如果加热盘管和气体分布设计不好,会在反应器内部出现死区或过热区。
现在大体积大直径的浆态床国内还没有加工技术,国际上也只有少数几家能加工,比如日本,固定床国内都能做。
浆态床催化剂过滤器国内的技术也不过关。
浆态床反应器合成甲醇的优点:1)床层的等温性由于有导热系数大,比热容大的惰性液相热载体和存在高度湍动的气液固三相,导致反应热迅速分散并传向冷却介质,使得床层接近等温操作。
因而,其温度分布和传热速率均优于固定床,不会出现床层温度不合理分布、局部过热及对催化剂和设备造成危害等情况。
2)反应的高效性由于浆态床中一般采用200目甚至更细颗粒催化剂,催化剂表面积大,内表面利用率高,催化剂有效系数接近1,催化剂的利用效率远高于气固相反应。
较佳的温度又兼顾了化学平衡与反应速率的推动力,从而加快了反应速度,且可获得较大的原料气转化率和转化量。
3)原料的适应性由于有优良的传热性能,使得浆态床合成甲醇的原料气适应性强,反应物主要成分CO可大范围内变化,而这对于固定床来说是不可能的。
4)操作的可塑性由于气液固三相有优良的传热性能,加之床层压降低,操作气速或质量空速可在较大范围内变化,反应器操作弹性大。
5)节能的现实性;由于原料气转化率高、循环气量减少、热效率高,因而合成工序可节能25%~30%左右。
6)联产的可行性原则上可用各种合成气制甲醇,特别是可使煤的燃烧、发电、供汽和化工产品联产,大大提高煤的有效利用率,改善经济效益,并可较容易地做到对现有生产装置的技术改造与产品更换。
反应器分类及特点

反应器分类及特点在化工、生物和医药等领域,反应器是实现化学反应的重要设备之一。
根据不同的分类标准,反应器可以分为多种类型。
以下是几种常见的反应器及其特点:1.固定床反应器固定床反应器是一种常见的反应器类型,其特点是在反应器中装填一定量的固体催化剂或固定床催化剂,使反应在催化剂表面进行。
这种反应器的优点是操作简单、催化剂活性高、选择性好,适用于小规模、高附加值的化工生产。
但是,固定床反应器的缺点是催化剂使用寿命有限,需要定期更换或再生。
2.活动床反应器活动床反应器是一种动态反应器,其特点是催化剂在反应器内处于运动状态。
这种反应器的优点是可以根据需要随时更换催化剂,并且可以通过控制催化剂的移动速度来优化反应过程。
但是,活动床反应器的缺点是需要复杂的机械传动系统和密封装置,维护成本较高。
3.流化床反应器流化床反应器是一种高效、大规模的反应器类型,其特点是在反应器中装填一定量的固体颗粒,使反应在颗粒表面进行。
这种反应器的优点是可以实现连续操作、生产能力大、催化剂使用寿命长等。
但是,流化床反应器的缺点是对于某些反应过程控制难度较大,可能会存在局部过热或反应不均匀等问题。
4.膜反应器膜反应器是一种新型的反应器类型,其特点是在反应器中装填一定量的膜材料,使反应在膜表面进行。
这种反应器的优点是可以实现分离和反应两个过程的集成,具有高效、环保等优点。
但是,膜反应器的缺点是膜材料的选择和控制难度较大,需要解决膜堵塞和污染等问题。
5.光敏反应器光敏反应器是一种利用光能激发化学反应的反应器类型,其特点是在反应器中引入光源和光敏剂等元素,通过光能激发化学反应。
这种反应器的优点是可以实现选择性高、条件温和的反应过程。
但是,光敏反应器的缺点是需要精密的光学系统和控制系统,维护成本较高。
6.电化学反应器电化学反应器是一种利用电能实现化学反应的反应器类型,其特点是在反应器中引入电极和电解质等元素,通过电能激发化学反应。
这种反应器的优点是可以实现条件温和、环境友好的化学过程。
固定床移动床的特点

固定床移动床的特点固定床:固定床反应器又称填充床反应器,装填有固体催化剂或固体反应物用以实现多相反应过程的一种反应器。
固体物通常呈颗粒状,粒径2~15mm左右,堆积成一定高度(或厚度)的床层。
床层静止不动,流体通过床层进行反应。
它与流化床反应器及移动床反应器的区别在于固体颗粒处于静止状态。
固定床反应器主要用于实现气固相催化反应,如氨合成塔、二氧化硫接触氧化器、烃类蒸汽转化炉等。
用于气固相或液固相非催化反应时,床层则填装固体反应物。
涓流床反应器也可归属于固定床反应器,气、液相并流向下通过床层,呈气液固相接触。
1、分类固定床反应器有三种基本形式:①轴向绝热式固定床反应器。
流体沿轴向自上而下流经床层,床层同外界无热交换。
②径向绝热式固定床反应器。
流体沿径向流过床层,可采用离心流动或向心流动,床层同外界无热交换。
径向反应器与轴向反应器相比,流体流动的距离较短,流道截面积较大,流体的压力降较小。
但径向反应器的结构较轴向反应器复杂。
以上两种形式都属绝热反应器,适用于反应热效应不大,或反应系统能承受绝热条件下由反应热效应引起的温度变化的场合。
③列管式固定床反应器。
由多根反应管并联构成。
管内或管间置催化剂,载热体流经管间或管内进行加热或冷却,管径通常在25~50mm之间,管数可多达上万根。
列管式固定床反应器适用于反应热效应较大的反应。
此外,尚有由上述基本形式串联组合而成的反应器,称为多级固定床反应器。
例如:当反应热效应大或需分段控制温度时,可将多个绝热反应器串联成多级绝热式固定床反应器,反应器之间设换热器或补充物料以调节温度,以便在接近于最佳温度条件下操作。
2、特点固定床反应器的优点是:①返混小,流体同催化剂可进行有效接触,当反应伴有串联副反应时可得较高选择性。
②催化剂机械损耗小。
③结构简单。
固定床反应器的缺点是:①传热差,反应放热量很大时,即使是列管式反应器也可能出现飞温(反应温度失去控制,急剧上升,超过允许范围)。
固定床移动床流化床

固定床:当气体以较小的速度流过固定床时,流动气体的上升阻力不致使颗粒的运动状态发生变化,床高维持不变;床层压降随流速对数增大而增大。
流化床:固体颗粒可以像水等液体一样在设备内有明显的界面,即使设备倾斜,界面仍会保持水平;床层压降不随流速变化(基本不变)。
输送床:固体颗粒在设备内无明显界面;床层压力随流速增大而减小。
流化床和沸腾床可能只是叫法上不同。
流化床,也就是沸腾床,接触面大,传热传质效率高,时空产率高,但返混严重。
需要注意的是不能堵塞气体分布器,堵了很麻烦的。
固定床和移动床比较适合气-气、气-液和液-液反应,床层本身作为[wiki]催化剂[/wiki],优点是返混小,固相带出少,分离简单。
流化床的床型是设计中很重要的,与反应体系的匹配要求比较高。
此外,操作中的气速、带出量、与配套的旋风等分离设备设计比较严格。
流化床的传热和破汽泡、沟流措施也是研究比较多的。
固定床反应器是一种被广泛采用的多相催化反应器,反应器内填充有固定不动的固体颗粒,可以是固体催化剂也可以是固体反应物.例如管式固定床反应器,管内装催化剂,管内装催化剂,反应物料自上而下通过床层,管间为载热体与管内反应物进行换热,以维持所需的温度条件.此外,固定床反应器也可用于气固及液固非催化反应.沸腾床是流化床的一种,固体在流化床反应器内流动,流体和固体颗粒所构成的床层犹如沸腾的液体. 沸腾床反应器下部设有分布板,板上放固体颗粒,流体自分布板下送入,当流体速度达到一定数值后,固体颗粒开始松动,再增大流速就进入流化状态.反应器内一般设有挡板,换热器,及流体与固体分离装置等内部部件.移动床与固定床相似,不同的是固体颗粒自顶部连续加入,由底部卸出.沸腾床因为固体处于运动状态,反应或传热效果好,但动力消耗大,而且在煤调湿中粉尘携带量大.固定床:固定床反应器又称填充床反应器,装填有固体催化剂或固体反应物用以实现多相反应过程的一种反应器。
固体物通常呈颗粒状,粒径2~15mm左右,堆积成一定高度(或厚度)的床层。
渣油加氢技术对比

渣油加氢技术对比文摘自亚洲石化科技大会发言报告,转载请注明来源。
前言在全社会对可持续发展和绿色环保的呼声日趋强烈的今天,炼油企业面临原油价格持续上涨、原油性质变重变差、轻质油品需求量上升和燃油及环保标准更加严格的竞争压力也越来越大。
原油深度加工和清洁燃料生产技术将进一步得到快速发展,并仍将是世界炼油技术发展的主要方向。
在原油深度加工方面,最大限度地把重油转化为轻质油和化工原料,是炼油企业最主要的目的。
渣油深加工的重要手段是大力发展加氢型装置,增加轻质油收率,提高原油利用率,降低SOX和碳的排放,这是我国炼油企业向资源节约型、环境友好型的新型企业发展需求,因此经济环保的渣油加氢技术受到企业的广泛关注。
分四大类,即固定床、沸腾床、移动床和浆态床渣油加氢,已工业化的有固定床、沸腾床和移动床三种。
其中,固定床加氢工艺技术最成熟,发展最快,装置最多,加工能力约占85.5%;沸腾床加氢技术和移动床技术日益成熟,不断得到推广应用;浆态床加氢技术取得突破性进展,处于工业示范阶段。
在重油渣油加氢技术中,固定床工艺无疑是最成熟、可靠和应用最广泛的工艺,在未来10~20年仍将是渣油加氢的主流工艺技术。
固定床渣油加氢技术发展趋势:一是开发更高性能的催化剂、优化的加工工艺以及低成本的催化剂制备技术,适应原料油的重质化和劣质化,为催化裂化装置提供更优质的原料并进一步延长装置运转周期;二是开发装置单系列大型化工程技术,降低能耗和投资;三是开发渣油加氢和催化裂化等组合技术,提高轻质油收率,使经济效益最大化。
渣油固定床加氢技术。
固定床渣油加氢装置单系列大型化无疑会带来节省能耗和降低投资的好处,以在建的某厂2000 kt/a 渣油加氢装置为例,采用单系列比采用两系列节省投资至少1.5亿元。
固定床渣油加氢单系列最大处理量取决于反应器筒径的制造能力,根据国内机械加工水平,中国石化致力于进行渣油加氢单系列处理量最大化的技术开发,在优化投资与能耗的前提下,目前的技术储备可实现单系列3000 kt/a 处理量的工程实践。
反应器分类

固定床反应器:时可得较高选择性。
②催化剂机械损耗小。
③结构简单。
固定床反应器的缺点是:①传热差,反应放热量很大时,即使是列管式反应器也可能出现飞温(反应温度失去控制,急剧上升,超过允许范围)。
②操作过程中催化剂不能更换,催化剂需要频繁再生的反应一般不宜使用,常代之以流化床反应器或移动床反应器。
流化床反应器:一种利用气体或液体通过颗粒状固体层而使固体颗粒处于悬浮运动状态,并进行气固相反应过程或液固相反应过程的反应器。
在用于气固系统时,又称沸腾床反应器。
流化床反应器的结构有两种形式:①有固体物料连续进料和出料装置,用于固相加工过程或催化剂迅速失活的流体相加工过程。
例如催化裂化过程,催化剂在几分钟内即显著失活,须用上述装置不断予以分离后进行再生。
②无固体物料连续进料和出料装置,用于固体颗粒性状在相当长时间(如半年或一年)内,不发生明显变化的反应过程。
与固定床反应器相比,流化床反应器的优点是:①可以实现固体物料的连续输入和输出;②流体和颗粒的运动使床层具有良好的传热性能,床层内部温度均匀,而且易于控制,特别适用于强放热反应。
但另一方面,由于返混严重,可对反应器的效率和反应的选择性带来一定影响。
再加上气固流化床中气泡的存在使得气固接触变差,导致气体反应得不完全。
因此,通常不宜用于要求单程转化率很高的反应。
此外,固体颗粒的磨损和气流中的粉尘夹带,也使流化床的应用受到一定限制。
为了限制返混,可采用多层流化床或在床内设置内部构件。
这样便可在床内建立起一定的浓度差或温度差。
此外,由于气体得到再分布,气固间的接触亦可有所改善。
(何为返混呢?在有降液管的塔板上,液体横流过塔板与气体呈错流状态,液体中易挥发组分的浓度将沿着流动的方向逐渐下降,但是当上升气体在塔板上使液体形成涡流时,浓度高的液体和浓度低的液体就混在一起,破坏了液体沿流动方向的浓度变化,这种现象叫返混现象。
)移动床反应器:一种用以实现气固相反应过程或液固相反应过程的反应器。
固定床移动床流化床

固定床:当气体以较小的速度流过固定床时,流动气体的上升阻力不致使颗粒的运动状态发生变化,床高维持不变;床层压降随流速对数增大而增大。
流化床:固体颗粒可以像水等液体一样在设备内有明显的界面,即使设备倾斜,界面仍会保持水平;床层压降不随流速变化(基本不变)。
输送床:固体颗粒在设备内无明显界面;床层压力随流速增大而减小。
流化床和沸腾床可能只是叫法上不同。
流化床,也就是沸腾床,接触面大,传热传质效率高,时空产率高,但返混严重。
需要注意的是不能堵塞气体分布器,堵了很麻烦的。
固定床和移动床比较适合气-气、气-液和液-液反应,床层本身作为[wiki]催化剂[/wiki],优点是返混小,固相带出少,分离简单。
流化床的床型是设计中很重要的,与反应体系的匹配要求比较高。
此外,操作中的气速、带出量、与配套的旋风等分离设备设计比较严格。
流化床的传热和破汽泡、沟流措施也是研究比较多的。
固定床反应器是一种被广泛采用的多相催化反应器,反应器内填充有固定不动的固体颗粒,可以是固体催化剂也可以是固体反应物.例如管式固定床反应器,管内装催化剂,管内装催化剂,反应物料自上而下通过床层,管间为载热体与管内反应物进行换热,以维持所需的温度条件.此外,固定床反应器也可用于气固及液固非催化反应.沸腾床是流化床的一种,固体在流化床反应器内流动,流体和固体颗粒所构成的床层犹如沸腾的液体. 沸腾床反应器下部设有分布板,板上放固体颗粒,流体自分布板下送入,当流体速度达到一定数值后,固体颗粒开始松动,再增大流速就进入流化状态.反应器内一般设有挡板,换热器,及流体与固体分离装置等内部部件.移动床与固定床相似,不同的是固体颗粒自顶部连续加入,由底部卸出.沸腾床因为固体处于运动状态,反应或传热效果好,但动力消耗大,而且在煤调湿中粉尘携带量大.固定床:固定床反应器又称填充床反应器,装填有固体催化剂或固体反应物用以实现多相反应过程的一种反应器。
固体物通常呈颗粒状,粒径2~15mm左右,堆积成一定高度(或厚度)的床层。
精细化学品化学试题(原题及答案)
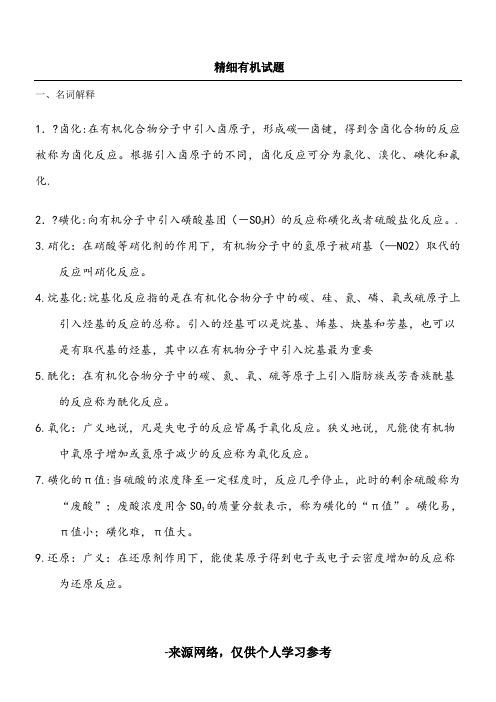
精细有机试题一、名词解释1.?卤化:在有机化合物分子中引入卤原子,形成碳—卤键,得到含卤化合物的反应被称为卤化反应。
根据引入卤原子的不同,卤化反应可分为氯化、溴化、碘化和氟化.2.?. 3.4.5.6.7.π值小;磺化难,π值大。
9.还原:广义:在还原剂作用下,能使某原子得到电子或电子云密度增加的反应称为还原反应。
狭义:能使有机物分子中增加氢原子或减少氧原子,或两者兼尔有之的反应称为还原反应。
10.氯化深度:氯与甲苯的物质的量比.12.相比:指硝酸与被硝化物的量比。
13.硝酸比:指硝酸与被硝化物的量比。
14.123.4.用5.6.7.。
891011121314.151617181920%,65%20在连续分离器中,可加入叔辛胺以加速硝化产物与废酸分离。
21硝酸比指硝酸与被硝化物的量比。
22相比指混酸与被硝化物的物质的量之比。
23氯化物碱性水解可引入羟基基团。
24还原反应是指有机分子中氢原子增加或氧原子减少的反应。
25羧酸酐比羧酸更容易发生酰化反应(填“容易”或“难”)。
26C-烷基化反应中应用最广泛的催化剂是AlCl3。
27乙酸与醇类按等物质的量反应制备酯,伯醇的反应活性最大,仲醇的反应活性较大,叔醇反应活性最小。
28正丙烯与苯反应主要得到异丙基苯。
29酯交换反应的类型有:酯醇交换、酯酸交换和酯酯交换。
30对于N-酰化反应,酰化剂反应活性的大小顺序:乙酰氯>乙酸酐>乙酸(填“>”或“<”)。
31通常甲苯氧化生产苯甲酸。
32氯化反应与磺化反应的反应机理均属于亲电取代。
33.常见酯交换方法有羧酸法酸酐法,酰氯法酯交换法。
34.催化加氢重要催化剂有骨架镍载体型、钯—碳催化剂、铜—硅胶载体型、有机金属络合物。
35.工业上付-克芳烃烷基化反应中,常用的烷基化剂是烯烃、卤烷。
36.烯烃作C-烷基化剂时,总是引入带支链的烷基.某些有机物在室温遇到空气会发生缓慢氧化,这种现象叫做自动氧化,其反应历程属于自由15.硝酸比指硝酸与被硝化物的量比。
固定床气流床流化床的具体区别

固定床、气流床、流化床的具体区别基本代表了三代煤气化技术。
固定床就是床层基本不动或者说缓慢向下移动,一般经历四个不同阶段,用蒸汽、空气(或富氧造气),采用块煤,气化温度较低,生产负荷小,煤气成分复杂,含焦油酚等,废水处理较难。
流化床相对固定床来说,气化剂流速更快,将床层吹起,不断上下浮动,象水沸腾一样。
属第二代煤气化技术,现在锅炉用的比较多,部分制气也有用的如温克勒。
气化床采用纯氧作气化剂,气流速度更快,煤粉或煤浆为原料,被喷头雾化,瞬间经历干馏、燃烧、还原等几个阶段,煤颗粒在被气化的过程中随气体一起流动,因此称气流床。
生产能力更大,气化效率高,目前新上项目大多采用气流床。
固定床气化是块煤从炉顶加入,自上而下经历干燥、干馏、还原、氧化和灰渣层,灰渣最终经灰箱排出炉外;气化剂自下而上经灰渣层预热后进入氧化层和还原层,生成的煤气显热用于煤的干馏和干燥。
流化床气化是气化剂由炉下部吹入,使细粒煤(﹤6mm)在炉内呈并逆流反应,气化剂通过煤粉层,使燃料处于悬浮状态,固体颗粒的运动如沸腾的液体一样,也称沸腾床气化炉。
气流床气化是原料煤(煤粉或水煤浆)由气化剂夹带入炉,进行并流式燃烧和气化反应。
受气化空间的限制,反应时间很短(1~10s),为了弥补反应时间短的缺陷,要求入炉煤粉粒度很细,以保证有足够的反应面积。
并流气化气固相相对速度低,气化反应是朝着反应物浓度低的方向进行,为增大反应推动力,提高反应速度,必须提高反应温度(火焰中心温度在2000℃以上)和反应压力,所以采用液态排渣是并流气化的必然结果。
1.移动床(固定床),鲁奇和BGL,2.气流床气化技术,当今世界上较为先进的有美国GE(Texaco)气化技术、荷兰壳牌谢尔(Shell)粉煤加压气化技术、德国未来能源公司GSP粉煤气化技术,以及国内自主研发的多喷嘴和多元料浆水煤浆气化技术等。
流化床气化炉采用粉煤作为原料,用氧化剂(氧气或者空气)来进行流化。
其温度一般控制在1000℃以下,以防止会融化后与炉床里的物质发生结聚。
生物接触氧化法固定床与流化床比较
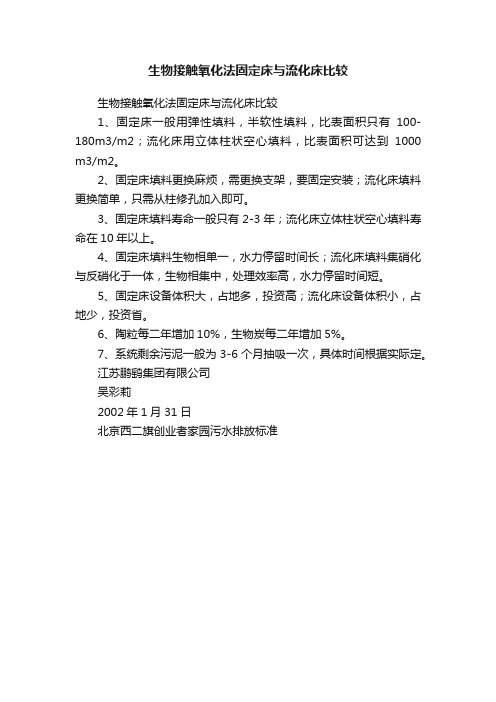
生物接触氧化法固定床与流化床比较
生物接触氧化法固定床与流化床比较
1、固定床一般用弹性填料,半软性填料,比表面积只有100-180m3/m2;流化床用立体柱状空心填料,比表面积可达到1000 m3/m2。
2、固定床填料更换麻烦,需更换支架,要固定安装;流化床填料更换简单,只需从柱修孔加入即可。
3、固定床填料寿命一般只有2-3年;流化床立体柱状空心填料寿命在10年以上。
4、固定床填料生物相单一,水力停留时间长;流化床填料集硝化与反硝化于一体,生物相集中,处理效率高,水力停留时间短。
5、固定床设备体积大,占地多,投资高;流化床设备体积小,占地少,投资省。
6、陶粒每二年增加10%,生物炭每二年增加5%。
7、系统剩余污泥一般为3-6个月抽吸一次,具体时间根据实际定。
江苏鹏鹞集团有限公司
吴彩莉
2002年1月31日
北京西二旗创业者家园污水排放标准
江苏鹏鹞集团有限公司吴彩莉
2002年1月31日。
煤化工复习资料 2

一、填空题1、煤炭气化是煤或煤焦与(气化剂)在高温下发生化学反应将煤或煤焦中有机物转变为(煤气)的过程。
2、煤炭气化如果按固体燃料的运动状态分类可以分为:(移动床气化)、(流化床气化)、(气流床气化)、熔融床气化。
3、煤气化的基本条件包括:气化原料和(气化剂);发生气化的反应容器,即煤气化炉或煤气发生炉;(气化炉内保持一定的温度);维持一定的炉内压。
4、具体的气化过程所采用的炉型不同,操作条件不同,所使用的气化剂及燃料组成不同,但基本都包括几个主要的过程,即煤的(煤的干燥)、(煤的干馏)、(主要化学反应过程)。
5、一般认为,在煤的气化阶段中发生了下述反应:(燃烧反应)、(气化反应)、(甲烷生成反应)及其他反应。
6、在煤的气化过程中,影响化学平衡的因素主要有两个,首先是温度的影响:升高温度有利于(吸)热反应的进行;降低反应温度有利于(放)热反应反应的进行;其次是压力的影响:加压使平衡向体积(减小)或分子数(减小)的方向移动,加压有利于生产能力的提高。
7、一般来说,煤中挥发分越(高),转变为焦油的有机物就越多,煤气的产率下降。
8、不同煤种,其变质程度不同,随着变质程度的(增加),气化时所消耗的水蒸气,氧气等气化剂的数量也相应增大。
9、各种不同结构的气化炉基本上由三大部分组,即(加煤机构)、(炉体)和(除灰装置)。
10、德士古气化炉是一种以(水煤浆)进料的加压气流床气化装置,该炉有两种不同的炉型,根据粗煤气采用的冷却方法不同可分为(淬冷型)、(全热回收型)。
11、温克勒气化工艺流程包括(煤的预处理)、(气化)、(粗煤气的显热回收)、(煤气的除尘冷却)。
12、鲁奇炉的排渣方式主要有(固态排渣)和(液态排渣)两种。
13、所谓气流床,就是气化剂将煤粉夹带进人气化炉,进行(并流)气化。
14、煤气产率是指每千克(燃料)在气化后转化为(煤气)的体积,它也是重要的技术经济指标之一.15、汽氧比是指气化剂中(水蒸气)和(氧气)的组成比例。
流化床

1固定床与流化床的比较。
固定床(绝热式、连续式换热式)的优点:不易磨损;接近平推流;可控制停留时间。
缺点:传热较差;催化剂的更换必须停产进行。
流化床优点:实现固体物料连续输出输入;良好的传热性能,温度均匀,适用于强放热反应;便于催化剂的再生、循环,适用于催化剂失活率较高的反应。
缺点:降低产物的收率;降低转化率;催化剂的流失难以脱离实验放大实验操作。
2固定床催化反应器的比较与选型固定床催化反应器有多钟形式,各有不同的特点与适应情况;不同类型的反应所适用的反应器类型是不相同的,有的反应如高压下氨合成反应,大型装置采用多段绝热式,而中小型装置常采用内冷自热式反应器。
如果反应是强吸热并且要求在高温下进行和热通量大但催化剂不易失活,如烃类蒸汽转化反应,则应采用连续换热管式反应器,如果反应是强吸热的气-固相催化反应并且所伴有的深度氧化副反应的活化能和反应热都比主反应高必须加大比传热面积和严格控制反应温度,应采用外冷管式反应器,如果强放热反应所采用的催化剂活性温度范围很窄,应采用流化床反应器以控制床层温度。
绝热反应器与管式反应器相比,结构更简单,易加工、投资少,可以防止出现偏流和沟流,如果反应的绝热温升比较大或催化剂允许的反应温度范围较小,应采用多段绝热而段间采用间接换热或冷激的方式。
3简述相反应及其动力学的研究内容?参加反应的各种物质均处于同一个相内进行的化学反应称为均相反应,均相反应动力是研究各种因素如温度,催化剂,反应物质组成和压力等对反应速率,反应物分布的邮箱,并确定表达这些影响因素与反应速率之间定量关系的速率方程。
3简述等温恒容平推流反应器空时、反应时间、停留时间三者关系?空时是反应器的有效容积与进料流体的容积流速之比。
反应时间是反应物料进入反应器后从实际发生反应的时刻到反应达某一程度所需的反应时间。
停留时间指反应时间物进入反应器时刻算起到离开反应器内共停留了多少时间。
由于平推流反应器内物料不发生反混,具有相同的停留时间且等于反应时间,恒容时的空时等于体积流速比,所以三者相等。
固定床、移动床、流化床反应器区别

固定床、移动床、流化床反应器区别固定床、移动床、流化床反应器,这三种反应器都是有固体颗粒床层的反应器一、首先,“床”指的是什么?大量固体颗粒堆积在一起,便形成了具有一定高度的颗粒床层,这就是名称里的"床"。
这些固体颗粒可以是反应物,也可以是催化剂。
如何区分固定床、移动床、流化床反应器如果这个颗粒床层是固定不动的,就叫固定床。
如果这个颗粒床层是整体移动的,固体颗粒自顶部连续加入,又从底部卸出,颗粒相互之间没有相对运动,而是以一个整体的状态移动,叫做移动床。
当流体(气体或液体)通过颗粒床层时,进行反应。
如果将流体通过床层的速度提高到一定数值,固体颗粒已经不能维持不变的状态,全部悬浮于流体之中,固体颗粒之间进行的是无规则运动,整个固体颗粒的床层,可以像流体一样流动,这即是流动床。
二、固定床反应器的详细介绍又称填充床反应器,内部装填有固体催化剂或固体反应物,以实现多相反应。
固体物通常呈颗粒状,堆积成一定高度(或厚度)的床层,床层静止不动,流体通过床层进行反应。
固定床反应器主要用于实现气固相催化反应,如氨合成塔、二氧化硫接触氧化器、烃类蒸汽转化炉等。
用于气固相或液固相非催化反应时,床层则填装固体反应物。
涓流床反应器也可归属于固定床反应器,气、液相并流向下通过床层,呈气液固相接触。
优点:(1)催化剂机械磨损小。
(2)床层内流体的流动接近于平推流,与返混式的反应器相比,可用较少量的催化剂和较小的反应器容积来获得较大的生产能力。
(3)由于停留时间可以严格控制,温度分布可以适当调节,因此特别有利于达到高的选择性和转化率。
(4)可在高温高压下操作。
缺点:(1)固定床中的传热较差。
(2)催化剂的再生、更换均不方便,催化剂的更换必须停产进行。
(3)不能使用细粒催化剂,但固定床反应器中的催化剂不限于颗粒状,网状催化剂早已应用于工业上。
目前,蜂窝状、纤维状催化剂也已被广泛使用。
固定床反应器的分类(一)按传热方式分类1、绝热式反应器绝热式固定床催化反应器在反应过程中,床层不与外界进行热量交换。
(完整word版)煤制甲醇工艺

煤制甲醇工艺Coal methanol synthesis process张凯兰州交通大学摘要:甲醇是重要的化工原料,市场需求量大;随着甲醇汽油,特别是大比例甲醇汽油的推广使用,甲醇将来的需求量必然会日益增加.此外,甲醇汽油的推广和及高硫、劣质煤生产甲醇的项目都属于环保项目,并已经在国内推广开来.本文简单介绍国内现行的以煤为原料的甲醇生产工艺流程.煤制甲醇即以煤为原料的甲醇生产工艺。
在工业上,生产甲醇的主要原料为:煤炭、天然气、焦炉气;其次的原料还有以重油、石脑油、焦炉煤气、乙炔尾气等.以煤炭为主生产甲醇,这种结构符合我国油气资源不足、煤炭资源相对丰富的国情。
关键词:煤化工;甲醇;工艺流程;Abstract: methanol is an important chemical raw materials, market demand is big; With methanol gasoline, especially large proportion to promote the use of methanol gasoline, methanol demand is bound to be increasing in the future. In addition, the promotion and and high sulfur, methanol gasoline inferior coal in the production of methanol project belong to environmental protection projects, and has been popularized in China. The paper simply introduces the current domestic methanol production process with coal as raw material, coal to methanol to coal as the raw material of methanol production process. In industry, the main raw material of producing methanol as: coal,natural gas, coke oven gas; Second raw material and with heavy fuel oil, naphtha, coke oven gas,acetylene gas, etc。
催化剂评价装置

催化剂评价装置
催化剂评价装置一般都是非标设计的试验撬装装置,根据不同的催化剂机理,其评价装置的特性、重点、精度都不近相同。
下面,我只是举例说明一些催化剂评价装置的特点,其实,还有一些石油、化工、煤化工、精细化工、生物医药、环保的非标设备也是类似的,并不一定每个设备都有崔催化剂。
1,石油方面,加氢催化剂、烷基化、催化裂化、重整、加氢异构等等,这里涉及的催化剂的试验条件比较宽泛,需要关注的参数有催化剂的空速、稀释比、吸放热反应、高径比、氢油比、氢耗等等,涉及的温度从几十度到500甚至更高温度,催化剂的反应方式有固定床、流化床、移动床、悬浮床、浆态床、沸腾床等等。
2,煤化工方面,最近的煤化工也比较热,从费托合成的反应,到甲醇系列的MT0,MTP,MTA,MTG,DMMN,MTBE,甲醇甲苯PX等等,其催化剂的形式也多种多样,催化剂评价装置在煤化工的应用上,需要有成熟的经验才能少走弯路。
3,环保方面,脱硫脱硝,大气VOCs处理,SCR,污水处理,污泥处理,脱氮,脱磷,脱臭,热解等等,最近随着环保力度的增大,环保的试验设备需求也是越来越多。
4,其它方面,例如聚乙烯、聚丙烯、聚丁烯、萘二甲酸、环十二酮、异丁烯、液体橡胶、戊醛、等等聚合、精细化工方向,蒸馏、精馏、萃取、吸附、分离的试验,也是需求很大。
5,试验装置需要做好,需要一个认真、耐心的团队,并且不怕挫折和困难,因为大部分催化剂的研发,是属于先进的化工领域,有些创新和设计,都是前人没有的,在执行过程中,遇到困难在所难免。
在我们进行悬浮床研发的过程中,确实勇于面对困难,不断创新和改造,终于实现了连续开车,使得我们的催化剂评价,得到很好的效果,所以,你还是需要根据你的催化剂性能,目标,方向,来选择,适合你的品牌。
反应器类型
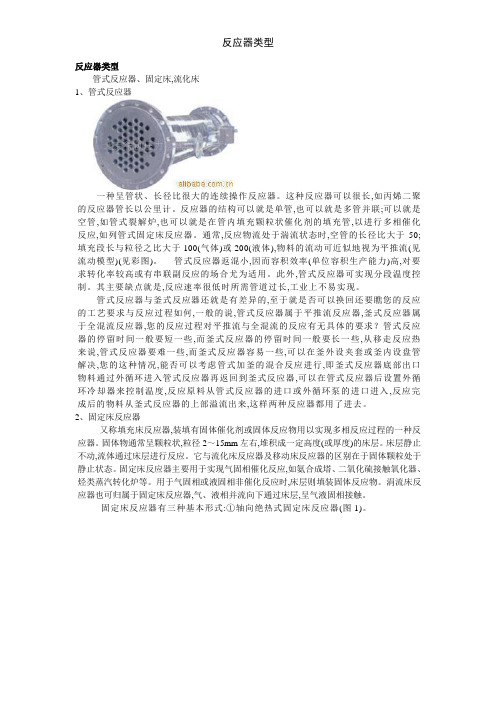
反应器类型管式反应器、固定床,流化床1、管式反应器一种呈管状、长径比很大的连续操作反应器。
这种反应器可以很长,如丙烯二聚的反应器管长以公里计。
反应器的结构可以就是单管,也可以就是多管并联;可以就是空管,如管式裂解炉,也可以就是在管内填充颗粒状催化剂的填充管,以进行多相催化反应,如列管式固定床反应器。
通常,反应物流处于湍流状态时,空管的长径比大于50;填充段长与粒径之比大于100(气体)或200(液体),物料的流动可近似地视为平推流(见流动模型)(见彩图)。
管式反应器返混小,因而容积效率(单位容积生产能力)高,对要求转化率较高或有串联副反应的场合尤为适用。
此外,管式反应器可实现分段温度控制。
其主要缺点就是,反应速率很低时所需管道过长,工业上不易实现。
管式反应器与釜式反应器还就是有差异的,至于就是否可以换回还要瞧您的反应的工艺要求与反应过程如何,一般的说,管式反应器属于平推流反应器,釜式反应器属于全混流反应器,您的反应过程对平推流与全混流的反应有无具体的要求?管式反应器的停留时间一般要短一些,而釜式反应器的停留时间一般要长一些,从移走反应热来说,管式反应器要难一些,而釜式反应器容易一些,可以在釜外设夹套或釜内设盘管解决,您的这种情况,能否可以考虑管式加釜的混合反应进行,即釜式反应器底部出口物料通过外循环进入管式反应器再返回到釜式反应器,可以在管式反应器后设置外循环冷却器来控制温度,反应原料从管式反应器的进口或外循环泵的进口进入,反应完成后的物料从釜式反应器的上部溢流出来,这样两种反应器都用了进去。
2、固定床反应器又称填充床反应器,装填有固体催化剂或固体反应物用以实现多相反应过程的一种反应器。
固体物通常呈颗粒状,粒径2~15mm左右,堆积成一定高度(或厚度)的床层。
床层静止不动,流体通过床层进行反应。
它与流化床反应器及移动床反应器的区别在于固体颗粒处于静止状态。
固定床反应器主要用于实现气固相催化反应,如氨合成塔、二氧化硫接触氧化器、烃类蒸汽转化炉等。
多相反应器的设计与分析
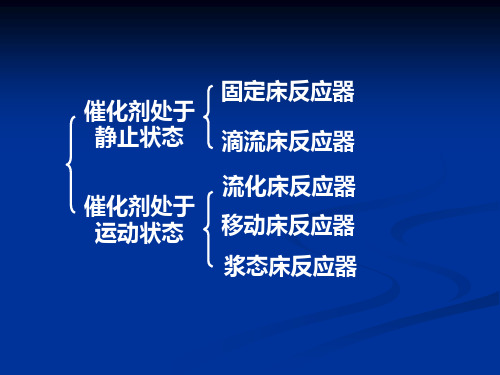
固定床内径向速度分 布不同于空管。 从床层中心开始,随 着径向位置的增大, 流速增加,在离器壁 的距离等于1~2倍颗粒 直径处,流速最大, 然后随径向位置增大
而降低至壁面处为0.
流体流过固定床时所产生的压力损失:
颗粒的粘滞曳力
孔隙变化 流体与颗粒的碰撞 流体的再分布
层流时 占主体
高流速及薄床 层中流动时占
Pe uLr Da
固定床反应器
对流传递速率 扩散传递速率
轴向质扩散的彼克列数 轴向热扩散的彼克列数
(Pea )m
ud p Da
( Pea
)h
ud pc p ea
气体 液体
Re d pu 10
(Pea )m 0.3 ~ 1
(Pea )m 2
(2)多釜串联模型
固定床内流体的轴向混合情况可用N个等体积的
3、可以使用粒度很小的固体物料或催化剂; 消除内扩散阻力,充分发挥催化剂效能,抑制串联 副反应。
4、压降不随气速变化。
缺点: 1、磨损和气体带走造成催化剂损失,需不断向反应 器中补充催化剂; 2、返混严重; 3、气体以气泡形式通过床层造成气固接触不良;
二、气固流态化特性 1、最小流化速度
Lmf 床层颗粒开始流化时的床层高度; mf 床层颗粒开始流化时的孔隙率;
合理简化
固定床的非均相数学模型:
活塞流模型(一维); 有轴向返混的一维模型; 有径向浓度分布和温度分布的二维模型。
衡算方程:
物料衡算:
GwA0
MA
dX A dZ
0b
RA
热量衡算:
GC pt
dT dZ
0b RA Hr
4U dt
T
TC
动量衡算: 边界条件:
化工中常见三种反应器

化工生产中常见的反应器药物工程系石化(03)班姚春飞二零一一年十二月七日固定床反应器定义:又称填充床反应器,装填有固体催化剂或固体反应物用以实现多相反应过程的一种反应器。
固体物通常呈颗粒状,粒径2~15mm 左右,堆积成一定高度(或厚度)的床层。
床层静止不动,流体通过床层进行反应。
它与流化床反应器及移动床反应器的区别在于固体颗粒处于静止状态。
固定床反应器主要用于实现气固相催化反应,如氨合成塔、二氧化硫接触氧化器、烃类蒸汽转化炉等。
用于气固相或液固相非催化反应时,床层则填装固体反应物。
多相反应过程的一种反应器。
固体物通常呈颗粒状,粒径2~15mm左右,堆积成一定高度(或厚度)的床层。
床层静止不动,流体通过床层进行反应。
它与流化床反应器及移动床反应器的区别在于固体颗粒处于静止状态。
固定床反应器主要用于实现气固相催化反应,如氨合成塔、二氧化硫接触氧化器、烃类蒸汽转化炉等特征:优点:①返混小,流体同催化剂可进行有效接触,当反应伴有串联副反应时可得较高选择性。
②催化剂机械损耗小。
③结构简单。
缺点:①传热差,反应放热量很大时,即使是列管式反应器也可能出现飞温。
②操作过程中催化剂不能更换。
应用:基本化学(烃类水蒸气转化、一氧化碳变换、氨合成甲醇合成)石油化工工业(催化重整加氢、脱烷基异构化)流化床反应器简介:流化床反应器是一种利用气体或液体通过颗粒状固体层而使固体颗粒处于悬浮运动状态,并进行气固相反应过程或液固相反应过程的反应器。
在用于气固系统时,又称沸腾床反应器结构:流化床反应器的结构有两种形式:①有固体物料连续进料和出料装置,用于固相加工过程或催化剂迅速失活的流体相加工过程。
例如催化裂化过程,催化剂在几分钟内即显著失活,须用上述装置不断予以分离后进行再生。
②无固体物料连续进料和出料装置,用于固体颗粒性状在相当长时间(如半年或一年)内,不发生明显变化的反应过程。
优缺点:优点:①可以实现固体物料的连续输入和输出;②流体和颗粒的运动使床层具有良好的传热性能,床层内部温度均匀,而且易于控制,特别适用于强放热反应;③便于进行催化剂的连续再生和循环操作,适于催化剂失活速率高的过程的进行,缺点:①由于固体颗粒和气泡在连续流动过程中的剧烈循环和搅动,无论气相或固相都存在着相当广的停留时间分布,导致不适当的产品分布,阵低了目的产物的收率;②反应物以气泡形式通过床层,减少了气-固相之间的接触机会,降低了反应转化率;③由于固体催化剂在流动过程中的剧烈撞击和摩擦,使催化剂加速粉化,加上床层顶部气泡的爆裂和高速运动、大量细粒催化剂的带出,造成明显的催化剂流失;④床层内的复杂流体力学、传递现象,使过程处于非定常条件下,难以揭示其统一的规律,也难以脱离经验放大。
煤的气化方法与煤气的种类 1

混合煤气
定义 以空气和水为气化剂,与加热中的原 料煤或焦炭反应的生成的煤气,称为混合 煤气。是人工煤气的一种,常见的人工煤 气还有空气煤气、水煤气、富氧煤气。广 气还有空气煤气、水煤气、富氧煤气。广 泛应用于冶金、建材行业及工业锅炉的一 种低热值气体燃料。
半水煤气 性质:将蒸汽和空气(或富氧空气) 按1:1的比例一起吹入煤气发生炉中与赤热的无烟 1:1的比例一起吹入煤气发生炉中与赤热的无烟 煤或焦炭作用而产生的煤气。是水煤气和发生炉 煤气的混合气体。也可将分别制成的水煤气和发 生炉煤气按一定比例配合而得。是混合煤气的特 例。这种煤气在除去氧、一氧化碳、二氧化碳、 硫化物等杂质后,其氢与氮的组成为3 硫化物等杂质后,其氢与氮的组成为3:1的半水 煤气,作为合成氨的原料气。也可用作燃料,但 与普通水煤气相比,热值较低。 防护措施: 严加密闭。空气中浓度超标时,必须佩戴防 毒面具。紧急事态抢救或撤离时,佩戴正压式呼 吸器,现场严禁吸烟。
固定床气化炉与流化床气化炉性能 比较
技术性能
从目前情况来看,固定床和流化床气化炉的设计运行 时间,一般都小于5000h。前者结构简单,坚固耐用;后 时间,一般都小于5000h。前者结构简单,坚固耐用;后 者结构较复杂,安装后不易移动,但占地较小,容量一般 较固定床的容量大。启动时,固定床加热比较缓慢,需较 长时间达到反应温度;流化床加热迅速,可频繁起停。 长时间达到反应温度;流化床加热迅速,可频繁起停。 运行过程中,固定床床内温度不均匀,固体在床内停 留时间过长,而气体停留时间较短,压力降较低;流化床 床温均匀,气固接触混合良好,气固停留时间都较短,床 内压力降较高。固定床的运行负荷可在设计负荷的20%~ 内压力降较高。固定床的运行负荷可在设计负荷的20%~ 110%之间变动,而流化床由于受气流速度必须满足流化 110%之间变动,而流化床由于受气流速度必须满足流化 条件所限,只能在设计负荷的50%~120%之间变化。 条件所限,只能在设计负荷的50%~120%之间变化。
- 1、下载文档前请自行甄别文档内容的完整性,平台不提供额外的编辑、内容补充、找答案等附加服务。
- 2、"仅部分预览"的文档,不可在线预览部分如存在完整性等问题,可反馈申请退款(可完整预览的文档不适用该条件!)。
- 3、如文档侵犯您的权益,请联系客服反馈,我们会尽快为您处理(人工客服工作时间:9:00-18:30)。
四种反应器形式比较一、固定床反应器(一)概念凡是流体通过不动的固体物料形成的床层面进行反应的设备都称为固定床反应器。
而其中尤以利用气态的反应物料,通过由固体催化剂所构成的床层进行反应的气固相催化反应器在化工生产中应用最为广泛。
例如石油炼制工业中的加氢裂化、歧化、异构化、加氢精制等;无机化学工业中的合成氨、硫酸、天然气转化等;有机化学工业中的乙烯氧化制环氧乙烷、乙烯水合制乙醇、乙苯脱氧制苯乙烯、苯加氢制环己烷等。
(二)特点结构简单、操作稳定、便于控制、易实现大型化和连续化生产等优点,是现代化工和反应中应用很广泛的反应器。
1、优点主要表现在以下几个方面:1)在生产操作中,除床层极薄和气体流速很低的特殊情况外,床层内气体的流动皆可看成是理想置换流动,因此在化学反应速度较快,在完成同样生产能力时,所需要的催化剂用量和反应器体积较小。
2)气体停留时间可以严格控制,温度分布可以调节,因而有利于提高化学反应的转化率和选择性。
3)催化剂不易磨损,可以较长时间连续使用。
4)适宜于高温高压条件下操作。
2、由于固体催化剂在床层中静止不动,相应地产生一些缺点:1)催化剂载体往往导热性不良,气体流速受压降限制又不能太大,导致床层中传热性能较差,也给温度控制带来困难。
对于放热反应,在换热式反应器的入口处,因为反应物浓度较高,反应速度较快,放出的热量往往来不及移走,而使物料温度升高,这又促使反应以更快的速度进行,放出更多的热量,物料温度继续升高,直到反应物浓度降低,反应速度减慢,传热速度超过了反应速度时,温度才逐渐下降。
所以在放热反应时,通常在换热式反应器的轴向存在一个最高的温度点,称为“热点”。
如设计或操作不当,则在强放热反应时,床内热点温度会超过工艺允许的最高温度,甚至失去控制而出现“飞温”。
此时,对反应的选择性、催化剂的活性和寿命、设备的强度等均极不利。
2)不能使用细粒催化剂,否则流体阻力增大,破坏了正常操作,所以催化剂的活性内表面得不到充分利用。
3)催化剂的再生、更换均不方便。
(三)形式轴向绝热式、径向绝热式、列管式。
绝热式固定床反应器结构简单,催化剂均匀堆置于床内,一般有下列特点:床层直径远大于催化剂颗粒直径;床层高度与催化剂颗粒直径之比一般超过100;与外界没有热量交换,床层温度沿物料的流向而变化。
换热式固定床反应器以列管式为多,通常管内装催化剂,管间走载热体,一般有下列特点:催化剂的粒径小于管径的8倍;利用载热体来移走或供给热量,床层温度维持稳定。
二、流化床反应器(一)概念流化床反应器(沸腾床反应器、膨胀床反应器)流体(气体或液体)以较高流速通过床层,带动床内固体颗粒运动,使大量固体颗粒悬浮于运动的流体从而使颗粒具有类似于流体的某些宏观表现特性,并在流动的主体流中进行反应。
流化床反应器是工业上应用较广泛的一类反应器,适用于催化或非催化的气—固、液—固和气—液—固反应系统。
流化床反应器的结构型式很多,传统流化床反应器一般都由壳体、气体分布装置、内部构件、换热装置、气因分离装置、催化剂的加入和卸出装置等组成。
化学工业广泛使用固体流态化技术进行固体的物理加工、颗粒输送、催化和非催化化学加工。
目前流态化技术作为一门基础技术已经渗透到国民经济的许多部门,在化工、炼油、冶金、能源、原子能、材料、轻工、生化、机械、环保等各项领域中都可以见到。
(二)特点1、流化床内的固体粒子像流体一样运动,由于流态化的特殊运动形式,使这种反应器具有如下优点:1)由于可采用细粉颗粒,并在悬浮状态下与流体接触,流固相界面积大(可高达3280~16400m2/m3),有利于非均相反应的进行,提高了催化剂的利用率。
2)由于颗粒在床内混合激烈,使颗粒在全床内的温度和浓度均匀一致,床层与内浸换热表面间的传热系数很高[200~400W/(m2*K)],全床热容量大,热稳定性高,这些都有利于强放热反应的等温操作。
这是许多工艺过程的反应装置选择流化床的重要原因。
3)流化床内的颗粒群有类似流体的性质,可以大量地从装置中移出、引入,并可以在两个流化床之间大量循环。
这使得一些反应—再生、吸热—放热、正反应—逆反应等反应耦合过程和反应—分离耦合过程得以实现。
使得易失活催化剂能在工程中使用。
4)流体与颗粒之间传热、传质速率也较其它接触方式为高。
5)由于流—固体系中孔隙率的变化可以引起颗粒曳力系数的大幅度变化,以致在很宽的范围内均能形成较浓密的床层。
所以流态化技术的操作弹性范围宽,单位设备生产能力大,设备结构简单、造价低,符合现代化大生产的需要。
2、流化床反应器的缺点1)气体流动状态与活塞流偏离较大,气流与床层颗粒发生返混,以致在床层轴向没有温度差及浓度差。
加之气体可能成大气泡状态通过床层,使气固接触不良,使反应的转化率降低。
因此流化床一般达不到固定床的转化率。
2)催化剂颗粒间相互剧烈碰撞,造成催化剂的破损,导致催化剂损失以及带来的除尘的困难,要有回收和集尘装置;内构件复杂;操作要求高等。
3)由于固体颗粒的磨蚀作用,管子和容器的磨损严重。
综上所述,流化床反应器比较适用于下述过程:热效应很大的放热或吸热过程;要求有均一的催化剂温度和需要精确控制温度的反应;催化剂寿命比较短,操作较短时间就需更换(或活化)的反应;有爆炸危险的反应,某些能够比较安全地在高浓度下操作的氧化反应。
流化床反应器一般不适用如下情况:要求高转化率的反应;要求催化剂层有温度分布的反应。
(三)形式散式流化床、鼓泡床、湍动床、快速床三、移动床反应器(一)概念固定床催化剂一般无法进行连续再生,而流化床催化剂可以很好地进行连续再生,但只适用于催化剂颗粒较小的工艺。
催化剂颗粒大,难以形成流态化,为了使再生连续进行,可以使用移动床。
在移动床中,当催化剂由于积炭而迅速失活时,可通过特制的闭锁装置,利用催化剂本身的重力,缓缓地将催化剂移出反应器。
这些待再生的催化剂,通过机械传送或气体输送,进入再生器自上而下地再生,再生过的催化剂则用同样的办法,输送回反应器,这样实现了反应与再生的连续操作。
这种系统,催化剂床层相当于在系统移动,称为移动床。
这类反应器最先应用于石油炼制的催化裂化工艺,后来又推广到连续催化重整工艺,丙烷脱氢。
(二)特点1、连续运转催化剂随着反应时间的增加,表面积炭相应增加,活性下降。
为了确保一定的反应速率,必须将积炭的催化剂移出反应器,不断地补充新鲜的或再生过的催化剂,以保持催化剂的平均活性,这种不间断的过程,确保了反应系统操作的连续性。
2、可以在较苛刻的反应条件下稳定运转固定床的缺点之一是反应初期与末期的催化剂活性变化大,因而反应深度不同,导致产品的分布及产品的质量都有差异,甚至影响到处理量的变化。
移动床反应器,由于催化剂活性可以调节,在一定范围内保持恒定,整个反应器也可以在较苛刻的条件下进行,有利于充分利用催化剂的潜力。
3、较低的反应压力从理论上讲,对于一定的空速及原料特性,反应压力越低,可以减少生焦、提高脱氢效率,增加目的产品收率,氢纯度也就越高。
同时压力低对降低对设备的要求、减少投资是非常有利的,重整的发展历史也表明了这点。
固定床反应器的重整反应压力为3.43MPa,第一代连续重整反应压力为0.69~0.98 MPa,第二代连续重整压力只有0.29~0.49 MPa。
4、操作比较复杂移动床反应器工艺不太适宜强烈放热的反应。
反应器、再生器中的催化剂始终都在流动状态,从上而下依靠重力流动,提升可用氢气或惰性气体。
为了保证整个系统的平稳循环,对控制系统的要求较高,操作相应比固定床反应器要复杂。
四、桨态床反应器(一)概念浆态床反应器(悬浮床反应器)气体以鼓泡形式通过悬浮有固体细粒的液体(浆液)层,以实现气液固相反应过程的反应器,因此一般又叫三相床反应器。
浆态反应器中液相可以是反应物,也可以是悬浮固体催化剂的载液。
浆态反应器中有两个流体相,所以操作方式比较多样,例如气液两相均为连续进出料,气液两相均为间歇进出料,以及液相为间歇进出料而气相为连续进出料等,可以适应反应系统的不同要求。
(二)特点1、优点:反应器结构简单,成本低,容易大型化;易于在线更换催化剂;液相介质热容大,在强放热条件下,易于反应器内部热量分布均匀,催化剂床层不易飞温,可提高产物选择性;使用细颗粒催化剂,使催化剂颗粒内表面利用较充分,无内扩散影响,有利于提高产物选择性;反应器相比固定床反应器小得多,尾气循环压缩机能耗大大减小;当液相连续进出料时,催化剂排出再生比较方便。
2、缺点:催化剂颗粒小,且容易磨损,会给操作带来麻烦,存在催化剂细粉的分离问题,所以液固分离装置要求高;连续操作时返混严重,当有串联副反应存在时会使选择性降低;液固比通常较高,在有液相副反应时可使选择性降低。
(三)形式浆态反应器有两种基本形式:其一是搅拌釜式,利用机械搅拌使浆液混合,适用于固体含量高、气体流量小或气液两相均为间歇进料的场合;其二是三相流化床式,借助气体上升时的作用使固体悬浮,并使浆液混合,避免了机械搅拌的轴封问题,尤适于高压反应。
1、按操作方式分类 :1)间歇操作反应器在反应之前将原料一次性加入反应器中,直到反应达到规定的转化率,即得反应物,通常带有搅拌器的釜式反应器。
特点:操作弹性大,主要用于小批量生产。
2)连续操作反应器反应物连续加入反应器产物连续引出反应器,属于稳态过程,可以采用釜式、管式和塔式反应器。
特点:适宜于大规模的工业生产,生产能力较强,产品质量稳定易于实现自动化操作。
3)半连续操作反应器预先将部分反应物在反应前一次加入反应器,其余的反应物在反应过程中连续或断连续加入,或者在反应过程中将某种产物连续地从反应器中取出,属于非稳态过程。
特点:反应不太快,温度易于控制,有利于提高可逆反应的转化率 。
2、按流体流动及混合型式分类造成三种反应器中流体流动型态不同是由于物料在不同反应器中的返混程度不一样。
返混:是指反应器内不同年龄的流体微元之间的混合,返混代表时间上的逆向混合。
1)平推流反应器物料在长径比很大的管式反应器中流动时,如果反应器中每一微元体积里的流体以相同的速度向前移动,此时在流体的流动方向不存在返混,这就是平推流。
特点:各物料微元通过反应器的停留时间相同 ,物料在反应器中沿流动方向逐段向前移动,无返混 ,物料组成和温度等参数沿管程递变,但是每一个截面上物料组成和温度等参数在时间进程中不变 ,连续稳态操作,结构为管式结构。
2)理想混合流反应器反应器的物料微元与器内原有的物料微元瞬间能充分混合(反应器中的强烈搅拌),反应器中各点浓度相等不随时间变化。
特点:各物料微元在反应器的停留时间不相同, 物料充分混合,返混最严重 ,反应器中各点物料组成和温度相同,不随时间变化 ,连续搅拌釜式反应器 。
3)非理想混合流反应器实际反应器主要是由于工业生产中在反应器中的死角、沟流、旁路、短路及不均匀的速度分布使物料流动型态偏离理想流动。