钛合金轧制影响因素
轧制工艺对Ti—62A钛合金厚板组织及性能的影响
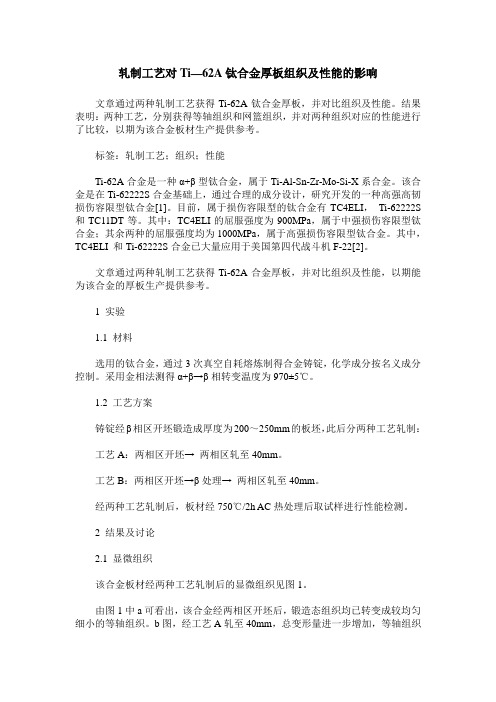
轧制工艺对Ti—62A钛合金厚板组织及性能的影响文章通过两种轧制工艺获得Ti-62A钛合金厚板,并对比组织及性能。
结果表明:两种工艺,分别获得等轴组织和网篮组织,并对两种组织对应的性能进行了比较,以期为该合金板材生产提供参考。
标签:轧制工艺;组织;性能Ti-62A合金是一种α+β型钛合金,属于Ti-Al-Sn-Zr-Mo-Si-X系合金。
该合金是在Ti-62222S合金基础上,通过合理的成分设计,研究开发的一种高强高韧损伤容限型钛合金[1]。
目前,属于损伤容限型的钛合金有TC4ELI,Ti-62222S 和TC11DT等。
其中:TC4ELI的屈服强度为900MPa,属于中强损伤容限型钛合金;其余两种的屈服强度均为1000MPa,属于高强损伤容限型钛合金。
其中,TC4ELI 和Ti-62222S合金已大量应用于美国第四代战斗机F-22[2]。
文章通过两种轧制工艺获得Ti-62A合金厚板,并对比组织及性能,以期能为该合金的厚板生产提供参考。
1 实验1.1 材料选用的钛合金,通过3次真空自耗熔炼制得合金铸锭,化学成分按名义成分控制。
采用金相法测得α+β→β相转变温度为970±5℃。
1.2 工艺方案铸锭经β相区开坯锻造成厚度为200~250mm的板坯,此后分两种工艺轧制:工艺A:两相区开坯→ 两相区轧至40mm。
工艺B:两相区开坯→β处理→ 两相区轧至40mm。
经两种工艺轧制后,板材经750℃/2h AC热处理后取试样进行性能检测。
2 结果及讨论2.1 显微组织该合金板材经两种工艺轧制后的显微组织见图1。
由图1中a可看出,该合金经两相区开坯后,锻造态组织均已转变成较均匀细小的等轴组织。
b图,经工艺A轧至40mm,总变形量进一步增加,等轴组织更加均匀细小,为典型的等轴组织。
d图,经工艺B轧至40mm,β晶粒(c图,β处理后)在变形过程中被破碎,原始β晶粒内的α片变短,各α片层交错排列,形成网篮组织。
TC2钛合金轧制管材表面裂纹产生原因分析
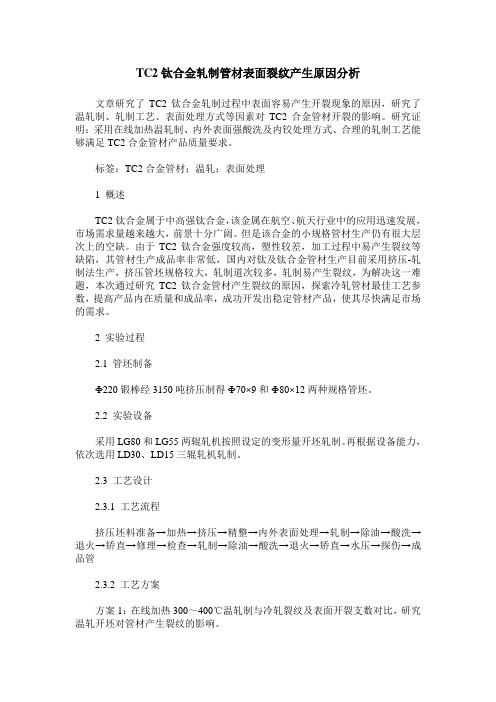
TC2钛合金轧制管材表面裂纹产生原因分析文章研究了TC2钛合金轧制过程中表面容易产生开裂现象的原因,研究了温轧制、轧制工艺、表面处理方式等因素对TC2合金管材开裂的影响。
研究证明:采用在线加热温轧制、内外表面强酸洗及内铰处理方式、合理的轧制工艺能够满足TC2合金管材产品质量要求。
标签:TC2合金管材;温轧;表面处理1 概述TC2钛合金属于中高强钛合金,该金属在航空、航天行业中的应用迅速发展,市场需求量越来越大,前景十分广阔。
但是该合金的小规格管材生产仍有很大层次上的空缺。
由于TC2钛合金强度较高,塑性较差,加工过程中易产生裂纹等缺陷,其管材生产成品率非常低,国内对钛及钛合金管材生产目前采用挤压-轧制法生产,挤压管坯规格较大,轧制道次较多,轧制易产生裂纹,为解决这一难题,本次通过研究TC2钛合金管材产生裂纹的原因,探索冷轧管材最佳工艺参数,提高产品内在质量和成品率,成功开发出稳定管材产品,使其尽快满足市场的需求。
2 实验过程2.1 管坯制备Ф220锻棒经3150吨挤压制得Ф70×9和Ф80×12两种规格管坯。
2.2 实验设备采用LG80和LG55两辊轧机按照设定的变形量开坯轧制。
再根据设备能力,依次选用LD30、LD15三辊轧机轧制。
2.3 工艺设计2.3.1 工艺流程挤压坯料准备→加热→挤压→精整→内外表面处理→轧制→除油→酸洗→退火→矫直→修理→检查→轧制→除油→酸洗→退火→矫直→水压→探伤→成品管2.3.2 工艺方案方案1:在线加热300~400℃温轧制与冷轧裂纹及表面开裂支数对比,研究温轧开坯对管材产生裂纹的影响。
方案2:制管坯进行一道次或两道次内铰处理,外表面多次扒皮及强酸洗等多种处理方式,尽可能消除裂纹的产生源头,研究其对管材产生裂纹的影响。
方案3:合理设计管材轧制各道次加工率,减径率与减壁率的匹配(Q值),工模具的合理设计,使变形过程中的应力分布更有利于塑性的发挥,减少裂纹的产生。
《TA2工业纯钛板带材轧制粘辊机理及影响因素研究》范文

《TA2工业纯钛板带材轧制粘辊机理及影响因素研究》篇一一、引言随着工业技术的不断发展,TA2工业纯钛板带材因其优良的耐腐蚀性、高强度和良好的加工性能,在航空、化工、医疗等领域得到了广泛应用。
在TA2工业纯钛板带材的生产过程中,轧制技术是一项关键技术。
然而,轧制过程中常会出现粘辊现象,这严重影响了产品的质量和生产效率。
因此,研究TA2工业纯钛板带材轧制粘辊的机理及其影响因素,对于提高产品质量、优化生产过程具有重要意义。
二、TA2工业纯钛板带材轧制粘辊机理TA2工业纯钛板带材轧制粘辊的机理主要涉及到材料本身的特性、轧制工艺参数以及设备状态等因素。
在轧制过程中,由于钛板带材表面与轧辊之间的摩擦作用,以及钛板带材的粘性特性,容易导致粘辊现象的发生。
具体来说,当TA2工业纯钛板带材进入轧机时,其表面与轧辊接触并产生摩擦。
由于钛的粘性较大,当摩擦力超过一定限度时,钛板带材与轧辊之间的界面会产生粘附现象,导致粘辊。
此外,轧制过程中的温度、压力、速度等工艺参数也会影响粘辊的程度。
三、影响因素研究(一)材料因素1. 钛板带材的成分与组织:TA2工业纯钛的成分和组织结构对其粘辊性能具有重要影响。
不同成分和组织结构的钛板带材,其粘性特性和表面能也会有所不同,从而影响粘辊的程度。
2. 表面处理:钛板带材的表面处理方式,如清洁度、粗糙度等,也会影响其与轧辊之间的摩擦性能,从而影响粘辊现象的发生。
(二)工艺因素1. 轧制温度:轧制温度是影响粘辊的重要因素。
当温度过高时,钛板带材的粘性增大,容易发生粘辊;而温度过低则会导致轧制困难,也可能引发其他问题。
2. 轧制压力和速度:轧制压力和速度是影响轧制过程的重要因素。
过大的压力和速度可能导致钛板带材与轧辊之间的摩擦力增大,从而增加粘辊的风险。
(三)设备因素1. 轧辊材质与表面处理:轧辊的材质和表面处理方式对减少粘辊现象具有重要作用。
不同材质和表面处理的轧辊,其抗粘性能和耐磨性能会有所不同。
《TA2工业纯钛板带材轧制粘辊机理及影响因素研究》
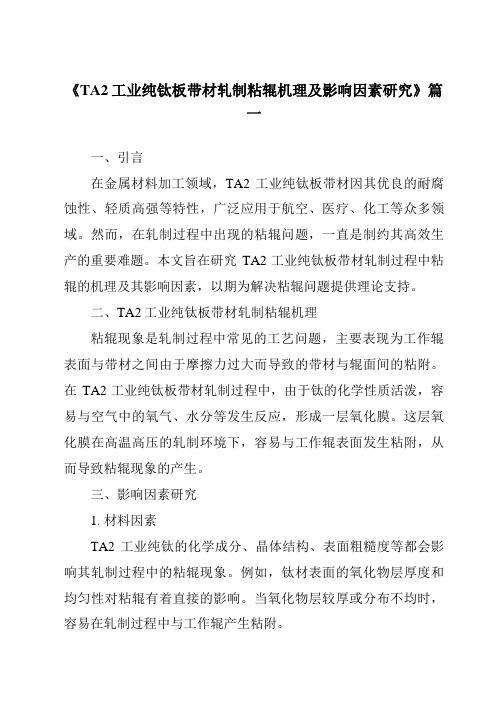
《TA2工业纯钛板带材轧制粘辊机理及影响因素研究》篇一一、引言在金属材料加工领域,TA2工业纯钛板带材因其优良的耐腐蚀性、轻质高强等特性,广泛应用于航空、医疗、化工等众多领域。
然而,在轧制过程中出现的粘辊问题,一直是制约其高效生产的重要难题。
本文旨在研究TA2工业纯钛板带材轧制过程中粘辊的机理及其影响因素,以期为解决粘辊问题提供理论支持。
二、TA2工业纯钛板带材轧制粘辊机理粘辊现象是轧制过程中常见的工艺问题,主要表现为工作辊表面与带材之间由于摩擦力过大而导致的带材与辊面间的粘附。
在TA2工业纯钛板带材轧制过程中,由于钛的化学性质活泼,容易与空气中的氧气、水分等发生反应,形成一层氧化膜。
这层氧化膜在高温高压的轧制环境下,容易与工作辊表面发生粘附,从而导致粘辊现象的产生。
三、影响因素研究1. 材料因素TA2工业纯钛的化学成分、晶体结构、表面粗糙度等都会影响其轧制过程中的粘辊现象。
例如,钛材表面的氧化物层厚度和均匀性对粘辊有着直接的影响。
当氧化物层较厚或分布不均时,容易在轧制过程中与工作辊产生粘附。
2. 工艺因素轧制温度、轧制速度、轧制压力等工艺参数对粘辊现象有着显著影响。
高温环境下,钛材的表面氧化反应加剧,增加了粘辊的风险。
而轧制速度过快或压力过大,都会导致工作辊与带材之间的摩擦力增大,从而增加粘辊的可能性。
3. 设备因素工作辊的材质、表面粗糙度以及硬度等也会影响粘辊现象。
如工作辊表面粗糙度过大或硬度不足,容易在轧制过程中产生微小的凹槽或划痕,这些缺陷会成为粘附点,导致粘辊。
4. 环境因素环境湿度、空气中的杂质等也会对TA2工业纯钛板带材的轧制过程产生影响。
高湿度环境下,钛材表面更容易形成氧化膜,增加粘辊的风险。
而空气中的杂质则可能附着在工作辊表面,形成杂质粘附,进一步加剧了粘辊现象。
四、结论与展望通过对TA2工业纯钛板带材轧制粘辊机理及影响因素的研究,我们了解到粘辊现象的产生是由多种因素共同作用的结果。
钛合金热轧缺陷

钛合金热轧缺陷钛合金是一种重要的结构材料,具有优异的力学性能和耐腐蚀性。
然而,在钛合金的热轧过程中,可能会出现一些缺陷,这些缺陷可能会对材料的性能和可靠性产生负面影响。
本文将探讨钛合金热轧过程中可能出现的一些常见缺陷,并提供相应的解决方法。
1. 表面缺陷在钛合金的热轧过程中,表面缺陷是最常见的问题之一。
这些缺陷可能包括划痕、氧化皮、气泡等。
划痕可能是由于轧辊表面的磨损或杂质引起的,而氧化皮则是由于钛合金与空气中的氧气反应形成的。
气泡则可能是由于热轧过程中未能完全排除气体引起的。
为了解决这些表面缺陷,可以采取一些措施。
首先,应确保轧辊表面的光洁度和平整度,以减少划痕的产生。
其次,在热轧过程中,应采取适当的气氛保护措施,以防止钛合金与氧气反应形成氧化皮。
此外,还可以通过增加热轧过程中的压力和温度,以促使气泡从材料中排出。
2. 内部缺陷除了表面缺陷外,钛合金的热轧过程中还可能出现一些内部缺陷,如夹杂物、晶界偏差等。
夹杂物是指在钛合金中存在的杂质或非金属颗粒,可能会降低材料的强度和韧性。
晶界偏差则是指晶界的错位或错配,可能会导致材料的脆性增加。
为了解决这些内部缺陷,可以采取一些措施。
首先,应在钛合金的制备过程中加强杂质的控制,以减少夹杂物的生成。
其次,在热轧过程中,应控制好轧制温度和速度,以减少晶界偏差的产生。
此外,还可以通过热处理等方法,对钛合金进行后续处理,以消除或减少内部缺陷。
3. 尺寸偏差在钛合金的热轧过程中,尺寸偏差也是一个需要关注的问题。
尺寸偏差可能会导致制品的尺寸不符合要求,从而影响其后续加工和使用。
尺寸偏差可能是由于轧辊的磨损或变形引起的,也可能是由于热轧过程中的温度和压力控制不当引起的。
为了解决尺寸偏差问题,可以采取一些措施。
首先,应定期检查和维护轧辊,确保其表面的光洁度和平整度。
其次,在热轧过程中,应严格控制温度和压力,以确保制品的尺寸符合要求。
此外,还可以通过采用在线尺寸检测系统等先进技术手段,实时监测和调整热轧过程中的尺寸偏差。
《TA2工业纯钛板带材轧制粘辊机理及影响因素研究》
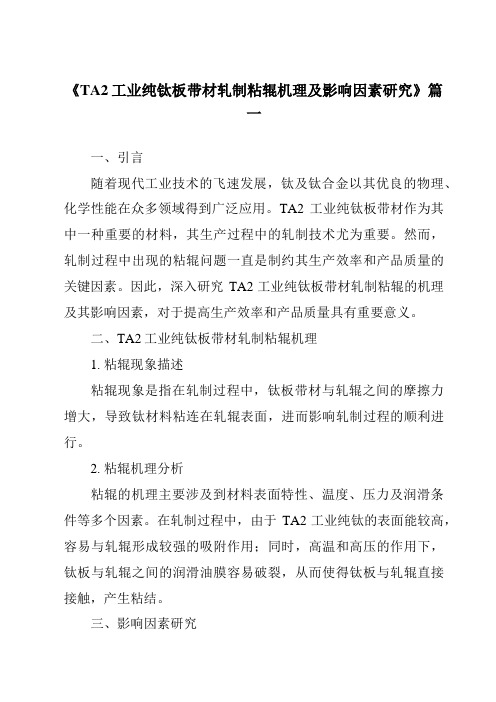
《TA2工业纯钛板带材轧制粘辊机理及影响因素研究》篇一一、引言随着现代工业技术的飞速发展,钛及钛合金以其优良的物理、化学性能在众多领域得到广泛应用。
TA2工业纯钛板带材作为其中一种重要的材料,其生产过程中的轧制技术尤为重要。
然而,轧制过程中出现的粘辊问题一直是制约其生产效率和产品质量的关键因素。
因此,深入研究TA2工业纯钛板带材轧制粘辊的机理及其影响因素,对于提高生产效率和产品质量具有重要意义。
二、TA2工业纯钛板带材轧制粘辊机理1. 粘辊现象描述粘辊现象是指在轧制过程中,钛板带材与轧辊之间的摩擦力增大,导致钛材料粘连在轧辊表面,进而影响轧制过程的顺利进行。
2. 粘辊机理分析粘辊的机理主要涉及到材料表面特性、温度、压力及润滑条件等多个因素。
在轧制过程中,由于TA2工业纯钛的表面能较高,容易与轧辊形成较强的吸附作用;同时,高温和高压的作用下,钛板与轧辊之间的润滑油膜容易破裂,从而使得钛板与轧辊直接接触,产生粘结。
三、影响因素研究1. 材料表面特性TA2工业纯钛的表面粗糙度、化学成分及氧化程度等都会影响其与轧辊的吸附作用。
表面粗糙度越大,吸附作用越强;化学成分中的活性元素容易与轧辊发生化学反应,导致粘辊。
2. 温度因素轧制温度是影响粘辊的重要因素。
温度过高会导致润滑油膜破裂,降低润滑效果;同时,高温下钛的表面易发生氧化,增加与轧辊的吸附力。
3. 压力因素轧制压力直接影响钛板与轧辊的接触状态。
压力过大容易导致润滑条件恶化,增加粘辊的风险。
4. 润滑条件润滑油的种类、性能及使用方式对防止粘辊至关重要。
良好的润滑条件能够有效地降低钛板与轧辊之间的摩擦力,减少粘辊现象的发生。
四、应对措施及展望针对TA2工业纯钛板带材轧制粘辊问题,可以采取以下措施:一是优化材料表面处理工艺,降低表面能;二是控制轧制温度和压力在合理范围内;三是选择合适的润滑油及其使用方式;四是研发新型的防粘辊技术。
展望未来,随着材料科学和工艺技术的不断发展,相信能够有效解决TA2工业纯钛板带材轧制粘辊问题,进一步提高生产效率和产品质量。
《2024年TA2工业纯钛板带材轧制粘辊机理及影响因素研究》范文
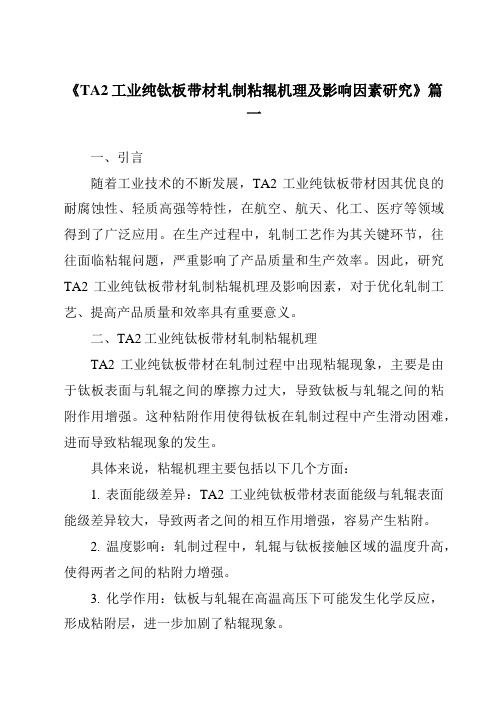
《TA2工业纯钛板带材轧制粘辊机理及影响因素研究》篇一一、引言随着工业技术的不断发展,TA2工业纯钛板带材因其优良的耐腐蚀性、轻质高强等特性,在航空、航天、化工、医疗等领域得到了广泛应用。
在生产过程中,轧制工艺作为其关键环节,往往面临粘辊问题,严重影响了产品质量和生产效率。
因此,研究TA2工业纯钛板带材轧制粘辊机理及影响因素,对于优化轧制工艺、提高产品质量和效率具有重要意义。
二、TA2工业纯钛板带材轧制粘辊机理TA2工业纯钛板带材在轧制过程中出现粘辊现象,主要是由于钛板表面与轧辊之间的摩擦力过大,导致钛板与轧辊之间的粘附作用增强。
这种粘附作用使得钛板在轧制过程中产生滑动困难,进而导致粘辊现象的发生。
具体来说,粘辊机理主要包括以下几个方面:1. 表面能级差异:TA2工业纯钛板带材表面能级与轧辊表面能级差异较大,导致两者之间的相互作用增强,容易产生粘附。
2. 温度影响:轧制过程中,轧辊与钛板接触区域的温度升高,使得两者之间的粘附力增强。
3. 化学作用:钛板与轧辊在高温高压下可能发生化学反应,形成粘附层,进一步加剧了粘辊现象。
三、影响因素分析TA2工业纯钛板带材轧制粘辊现象受多种因素影响,主要包括以下几个方面:1. 材料因素:钛板的化学成分、组织结构、表面状态等都会影响其与轧辊之间的相互作用,从而影响粘辊现象的发生。
2. 工艺因素:轧制温度、轧制速度、轧制压力等工艺参数对粘辊现象具有重要影响。
例如,温度过高会增大钛板与轧辊之间的粘附力;轧制速度过快可能导致钛板表面损伤,增加粘辊风险。
3. 设备因素:轧辊的材质、表面粗糙度、硬度等也会影响粘辊现象。
例如,轧辊表面粗糙度过大,容易在钛板表面形成凹槽,导致局部温度升高,从而加剧粘辊现象。
四、研究方法及实验结果为了深入研究TA2工业纯钛板带材轧制粘辊机理及影响因素,可以采用以下研究方法:1. 理论分析:通过分析钛板与轧辊之间的相互作用力、表面能级差异、化学作用等,揭示粘辊机理。
TA18钛合金管冷轧开裂原因分析

TA18钛合金管冷轧开裂原因分析钛合金管是一种高强度、耐腐蚀性好的材料,广泛应用于航空、航天、化工、医疗等领域。
然而,在冷轧过程中,钛合金管可能会出现开裂问题,严重影响产品质量和使用安全。
下面将针对钛合金管冷轧开裂的原因进行详细分析。
首先,可能的原因之一是材料的内部缺陷。
钛合金管在冷轧过程中受到很大的压力和变形,如果材料本身存在缺陷,如气孔、夹杂物等,就会成为应力的集中点,从而导致开裂。
这种情况下,解决的关键是加强材料的检测和质量控制,尽量避免带有缺陷的材料进入冷轧生产环节。
其次,冷轧过程中的工艺参数设置也会对钛合金管的开裂产生影响。
冷轧涉及到的工艺参数有很多,如轧制温度、轧制速度、轧制压力等。
过高或过低的温度、速度或压力都可能导致应力过大,从而引发开裂。
因此,在冷轧过程中,需要合理设置这些参数,确保在一定范围内进行,避免应力过大。
此外,材料的化学成分也会对钛合金管的开裂产生一定的影响。
有些元素的含量过高或过低,会导致材料的结构和性能发生变化,从而增加了开裂的风险。
因此,在合金设计和材料选择阶段,需要合理控制化学成分的含量,确保材料的稳定性和可靠性。
另外,冷轧过程中材料的变形程度也会对开裂产生影响。
如果材料的变形过大,应力会集中在一些部分,容易引发开裂。
因此,在冷轧过程中,需要合理设计轧制工艺,控制变形程度,避免应力过大。
此外,还需要关注冷轧过程中的润滑与冷却措施。
适当的润滑可以减少摩擦力,降低材料的应力,从而降低开裂的风险。
冷却措施可以控制材料的温度,避免温度过高导致应力过大。
因此,在冷轧生产中,需要合理选择润滑剂和冷却方式,确保材料的冷轧过程稳定可靠。
最后,应加强生产过程中的质量控制和检测手段。
通过先进的检测设备和技术,及时发现材料的缺陷和问题,进行调整和改进,以确保产品质量。
总之,钛合金管冷轧开裂问题的原因可能涉及材料本身的缺陷、冷轧工艺参数设置、材料的化学成分、材料的变形程度、润滑与冷却措施以及生产质量控制等多个方面。
《TA2工业纯钛板带材轧制粘辊机理及影响因素研究》
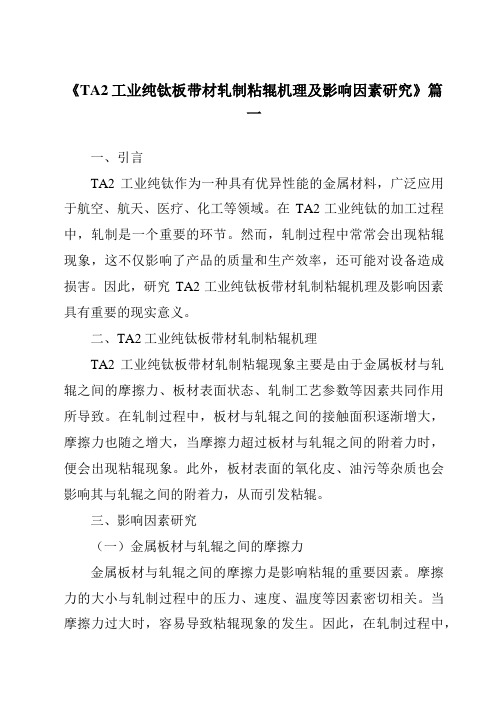
《TA2工业纯钛板带材轧制粘辊机理及影响因素研究》篇一一、引言TA2工业纯钛作为一种具有优异性能的金属材料,广泛应用于航空、航天、医疗、化工等领域。
在TA2工业纯钛的加工过程中,轧制是一个重要的环节。
然而,轧制过程中常常会出现粘辊现象,这不仅影响了产品的质量和生产效率,还可能对设备造成损害。
因此,研究TA2工业纯钛板带材轧制粘辊机理及影响因素具有重要的现实意义。
二、TA2工业纯钛板带材轧制粘辊机理TA2工业纯钛板带材轧制粘辊现象主要是由于金属板材与轧辊之间的摩擦力、板材表面状态、轧制工艺参数等因素共同作用所导致。
在轧制过程中,板材与轧辊之间的接触面积逐渐增大,摩擦力也随之增大,当摩擦力超过板材与轧辊之间的附着力时,便会出现粘辊现象。
此外,板材表面的氧化皮、油污等杂质也会影响其与轧辊之间的附着力,从而引发粘辊。
三、影响因素研究(一)金属板材与轧辊之间的摩擦力金属板材与轧辊之间的摩擦力是影响粘辊的重要因素。
摩擦力的大小与轧制过程中的压力、速度、温度等因素密切相关。
当摩擦力过大时,容易导致粘辊现象的发生。
因此,在轧制过程中,需要合理控制轧制压力、速度和温度等参数,以减小摩擦力,降低粘辊风险。
(二)板材表面状态板材表面的清洁度、粗糙度等状态对粘辊现象有着重要影响。
表面油污、氧化皮等杂质会降低板材与轧辊之间的附着力,从而引发粘辊。
因此,在轧制前需要对板材表面进行清洗和处理,以降低表面杂质对轧制过程的影响。
(三)轧制工艺参数轧制工艺参数是影响粘辊现象的关键因素。
包括轧制速度、轧制压力、轧辊表面硬度等。
在合理的工艺参数范围内,可以有效地降低粘辊风险。
例如,适当降低轧制速度和压力,可以提高板材与轧辊之间的附着力,从而减少粘辊现象的发生。
此外,选择合适的轧辊材料和表面处理技术也能有效降低粘辊风险。
四、结论通过对TA2工业纯钛板带材轧制粘辊机理及影响因素的研究,我们可以得出以下结论:1. 粘辊现象主要由金属板材与轧辊之间的摩擦力、板材表面状态及轧制工艺参数共同作用所导致。
最新-影响钛合金加工性能的原由 精品
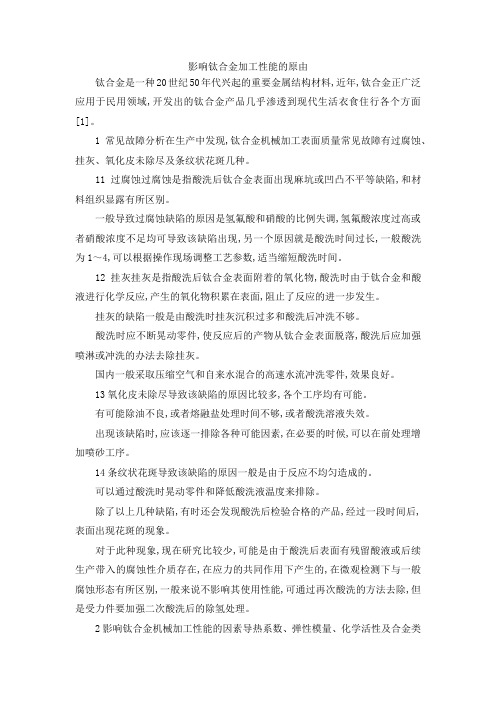
影响钛合金加工性能的原由钛合金是一种20世纪50年代兴起的重要金属结构材料,近年,钛合金正广泛应用于民用领域,开发出的钛合金产品几乎渗透到现代生活衣食住行各个方面[1]。
1常见故障分析在生产中发现,钛合金机械加工表面质量常见故障有过腐蚀、挂灰、氧化皮未除尽及条纹状花斑几种。
11过腐蚀过腐蚀是指酸洗后钛合金表面出现麻坑或凹凸不平等缺陷,和材料组织显露有所区别。
一般导致过腐蚀缺陷的原因是氢氟酸和硝酸的比例失调,氢氟酸浓度过高或者硝酸浓度不足均可导致该缺陷出现,另一个原因就是酸洗时间过长,一般酸洗为1~4,可以根据操作现场调整工艺参数,适当缩短酸洗时间。
12挂灰挂灰是指酸洗后钛合金表面附着的氧化物,酸洗时由于钛合金和酸液进行化学反应,产生的氧化物积累在表面,阻止了反应的进一步发生。
挂灰的缺陷一般是由酸洗时挂灰沉积过多和酸洗后冲洗不够。
酸洗时应不断晃动零件,使反应后的产物从钛合金表面脱落,酸洗后应加强喷淋或冲洗的办法去除挂灰。
国内一般采取压缩空气和自来水混合的高速水流冲洗零件,效果良好。
13氧化皮未除尽导致该缺陷的原因比较多,各个工序均有可能。
有可能除油不良,或者熔融盐处理时间不够,或者酸洗溶液失效。
出现该缺陷时,应该逐一排除各种可能因素,在必要的时候,可以在前处理增加喷砂工序。
14条纹状花斑导致该缺陷的原因一般是由于反应不均匀造成的。
可以通过酸洗时晃动零件和降低酸洗液温度来排除。
除了以上几种缺陷,有时还会发现酸洗后检验合格的产品,经过一段时间后,表面出现花斑的现象。
对于此种现象,现在研究比较少,可能是由于酸洗后表面有残留酸液或后续生产带入的腐蚀性介质存在,在应力的共同作用下产生的,在微观检测下与一般腐蚀形态有所区别,一般来说不影响其使用性能,可通过再次酸洗的方法去除,但是受力件要加强二次酸洗后的除氢处理。
2影响钛合金机械加工性能的因素导热系数、弹性模量、化学活性及合金类型和显微组织是影响钛合金机械加工性能的主要因素。
冷轧工艺改进对钛合金板材力学性能的影响研究
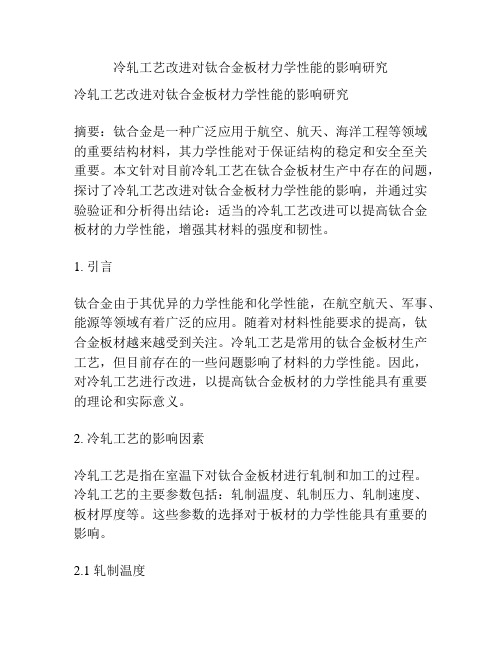
冷轧工艺改进对钛合金板材力学性能的影响研究冷轧工艺改进对钛合金板材力学性能的影响研究摘要:钛合金是一种广泛应用于航空、航天、海洋工程等领域的重要结构材料,其力学性能对于保证结构的稳定和安全至关重要。
本文针对目前冷轧工艺在钛合金板材生产中存在的问题,探讨了冷轧工艺改进对钛合金板材力学性能的影响,并通过实验验证和分析得出结论:适当的冷轧工艺改进可以提高钛合金板材的力学性能,增强其材料的强度和韧性。
1. 引言钛合金由于其优异的力学性能和化学性能,在航空航天、军事、能源等领域有着广泛的应用。
随着对材料性能要求的提高,钛合金板材越来越受到关注。
冷轧工艺是常用的钛合金板材生产工艺,但目前存在的一些问题影响了材料的力学性能。
因此,对冷轧工艺进行改进,以提高钛合金板材的力学性能具有重要的理论和实际意义。
2. 冷轧工艺的影响因素冷轧工艺是指在室温下对钛合金板材进行轧制和加工的过程。
冷轧工艺的主要参数包括:轧制温度、轧制压力、轧制速度、板材厚度等。
这些参数的选择对于板材的力学性能具有重要的影响。
2.1 轧制温度轧制温度是指冷轧过程中板材的实际温度。
常用的冷轧温度范围为室温到液氮温度。
低温轧制可以降低板材的塑性变形能力,从而提高板材的强度和硬度。
2.2 轧制压力轧制压力是指冷轧过程中实际施加在板材上的压力。
轧制压力的大小直接影响着板材的厚度变化和晶粒细化程度。
适当增加轧制压力可以提高板材的强度和硬度,但过大的压力会使晶粒细化过程受到限制。
2.3 轧制速度轧制速度是指冷轧过程中板材的运动速度。
适当增加轧制速度可以使板材的塑性变形变得均匀,从而提高板材的力学性能。
2.4 板材厚度板材厚度是指冷轧后所得到的板材的实际厚度。
板材的厚度对于其力学性能有较大影响,一般来说,较薄的板材具有较高的强度和韧性。
3. 实验方法和结果分析3.1 实验方法选择一种常见的钛合金材料进行实验,使用不同的冷轧工艺参数进行轧制,包括轧制温度、轧制压力、轧制速度和板材厚度。
轧制工艺对BTi—6431S钛合金薄板组织和性能的影响
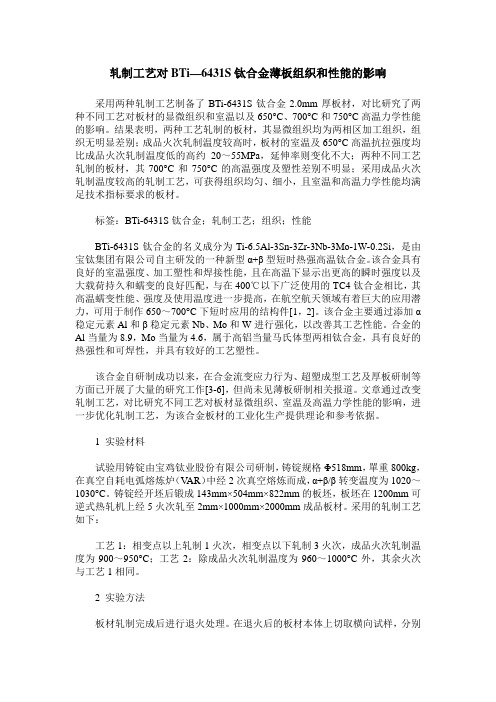
轧制工艺对BTi—6431S钛合金薄板组织和性能的影响采用两种轧制工艺制备了BTi-6431S钛合金2.0mm厚板材,对比研究了两种不同工艺对板材的显微组织和室温以及650°C、700°C和750°C高温力学性能的影响。
结果表明,两种工艺轧制的板材,其显微组织均为两相区加工组织,组织无明显差别;成品火次轧制温度较高时,板材的室温及650°C高温抗拉强度均比成品火次轧制温度低的高约20~55MPa,延伸率则变化不大;两种不同工艺轧制的板材,其700°C和750°C的高温强度及塑性差别不明显;采用成品火次轧制温度较高的轧制工艺,可获得组织均匀、细小,且室温和高温力学性能均满足技术指标要求的板材。
标签:BTi-6431S钛合金;轧制工艺;组织;性能BTi-6431S钛合金的名义成分为Ti-6.5Al-3Sn-3Zr-3Nb-3Mo-1W-0.2Si,是由宝钛集团有限公司自主研发的一种新型α+β型短时热强高温钛合金。
该合金具有良好的室温强度、加工塑性和焊接性能,且在高温下显示出更高的瞬时强度以及大载荷持久和蠕变的良好匹配,与在400℃以下广泛使用的TC4钛合金相比,其高温蠕变性能、强度及使用温度进一步提高,在航空航天领域有着巨大的应用潜力,可用于制作650~700°C下短时应用的结构件[1,2]。
该合金主要通过添加α稳定元素Al和β稳定元素Nb、Mo和W进行强化,以改善其工艺性能。
合金的Al当量为8.9,Mo当量为4.6,属于高铝当量马氏体型两相钛合金,具有良好的热强性和可焊性,并具有较好的工艺塑性。
该合金自研制成功以来,在合金流变应力行为、超塑成型工艺及厚板研制等方面已开展了大量的研究工作[3-6],但尚未见薄板研制相关报道。
文章通过改变轧制工艺,对比研究不同工艺对板材显微组织、室温及高温力学性能的影响,进一步优化轧制工艺,为该合金板材的工业化生产提供理论和参考依据。
钛合金轧制新工艺
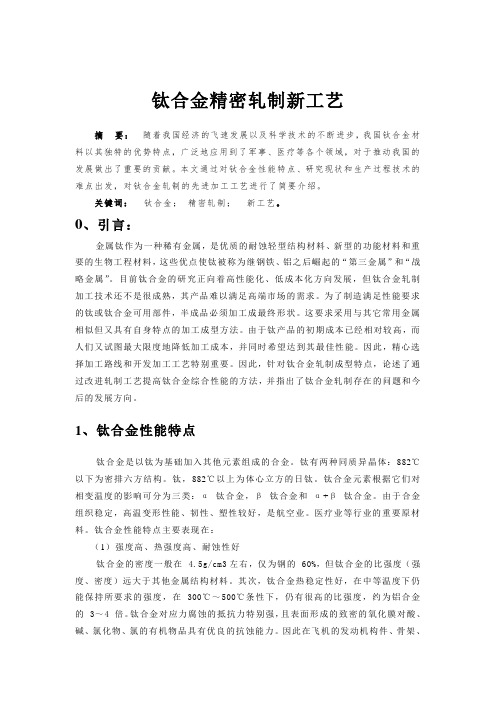
钛合金精密轧制新工艺摘要:随着我国经济的飞速发展以及科学技术的不断进步,我国钛合金材料以其独特的优势特点,广泛地应用到了军事、医疗等各个领域,对于推动我国的发展做出了重要的贡献。
本文通过对钛合金性能特点、研究现状和生产过程技术的难点出发,对钛合金轧制的先进加工工艺进行了简要介绍。
关键词:钛合金;精密轧制;新工艺。
0、引言:金属钛作为一种稀有金属,是优质的耐蚀轻型结构材料、新型的功能材料和重要的生物工程材料,这些优点使钛被称为继钢铁、铝之后崛起的“第三金属”和“战略金属”。
目前钛合金的研究正向着高性能化、低成本化方向发展,但钛合金轧制加工技术还不是很成熟,其产品难以满足高端市场的需求。
为了制造满足性能要求的钛或钛合金可用部件,半成品必须加工成最终形状。
这要求采用与其它常用金属相似但又具有自身特点的加工成型方法。
由于钛产品的初期成本已经相对较高,而人们又试图最大限度地降低加工成本,并同时希望达到其最佳性能。
因此,精心选择加工路线和开发加工工艺特别重要。
因此,针对钛合金轧制成型特点,论述了通过改进轧制工艺提高钛合金综合性能的方法,并指出了钛合金轧制存在的问题和今后的发展方向。
1、钛合金性能特点钛合金是以钛为基础加入其他元素组成的合金。
钛有两种同质异晶体:882℃以下为密排六方结构。
钛,882℃以上为体心立方的日钛。
钛合金元素根据它们对相变温度的影响可分为三类:α钛合金,β钛合金和α+β钛合金。
由于合金组织稳定,高温变形性能、韧性、塑性较好,是航空业。
医疗业等行业的重要原材料。
钛合金性能特点主要表现在:(1)强度高、热强度高、耐蚀性好钛合金的密度一般在 4.5g/cm3左右,仅为钢的 60%,但钛合金的比强度(强度、密度)远大于其他金属结构材料。
其次,钛合金热稳定性好,在中等温度下仍能保持所要求的强度,在 300℃~500℃条性下,仍有很高的比强度,约为铝合金的 3~4 倍。
钛合金对应力腐蚀的抵抗力特别强,且表面形成的致密的氧化膜对酸、碱、氯化物、氯的有机物品具有优良的抗蚀能力。
轧制工艺对Ti55钛合金超塑性板材力学性能的影响
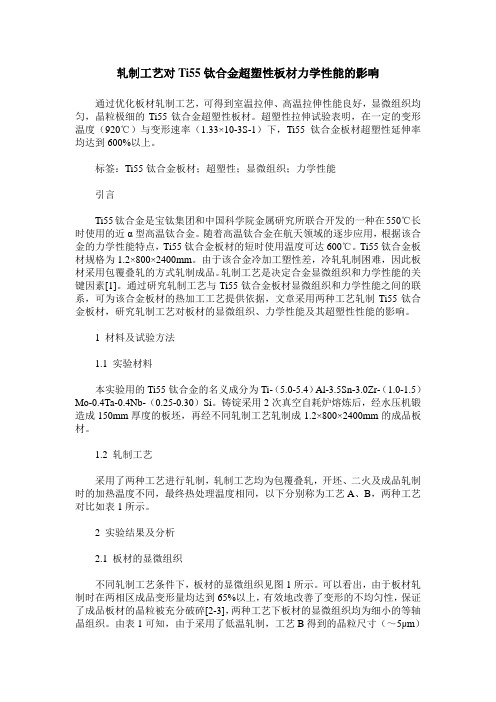
轧制工艺对Ti55钛合金超塑性板材力学性能的影响通过优化板材轧制工艺,可得到室温拉伸、高温拉伸性能良好,显微组织均匀,晶粒极细的Ti55钛合金超塑性板材。
超塑性拉伸试验表明,在一定的变形温度(920℃)与变形速率(1.33×10-3S-1)下,Ti55钛合金板材超塑性延伸率均达到600%以上。
标签:Ti55钛合金板材;超塑性;显微组织;力学性能引言Ti55钛合金是宝钛集团和中国科学院金属研究所联合开发的一种在550℃长时使用的近α型高温钛合金。
随着高温钛合金在航天领域的逐步应用,根据该合金的力学性能特点,Ti55钛合金板材的短时使用温度可达600℃。
Ti55钛合金板材规格为1.2×800×2400mm。
由于该合金冷加工塑性差,冷轧轧制困难,因此板材采用包覆叠轧的方式轧制成品。
轧制工艺是决定合金显微组织和力学性能的关键因素[1]。
通过研究轧制工艺与Ti55钛合金板材显微组织和力学性能之间的联系,可为该合金板材的热加工工艺提供依据,文章采用两种工艺轧制Ti55钛合金板材,研究轧制工艺对板材的显微组织、力学性能及其超塑性性能的影响。
1 材料及试验方法1.1 实验材料本实验用的Ti55钛合金的名义成分为Ti-(5.0-5.4)Al-3.5Sn-3.0Zr-(1.0-1.5)Mo-0.4Ta-0.4Nb-(0.25-0.30)Si。
铸锭采用2次真空自耗炉熔炼后,经水压机锻造成150mm厚度的板坯,再经不同轧制工艺轧制成1.2×800×2400mm的成品板材。
1.2 轧制工艺采用了两种工艺进行轧制,轧制工艺均为包覆叠轧,开坯、二火及成品轧制时的加热温度不同,最终热处理温度相同,以下分别称为工艺A、B,两种工艺对比如表1所示。
2 实验结果及分析2.1 板材的显微组织不同轧制工艺条件下,板材的显微组织见图1所示。
可以看出,由于板材轧制时在两相区成品变形量均达到65%以上,有效地改善了变形的不均匀性,保证了成品板材的晶粒被充分破碎[2-3],两种工艺下板材的显微组织均为细小的等轴晶组织。
《TA2工业纯钛板带材轧制粘辊机理及影响因素研究》范文
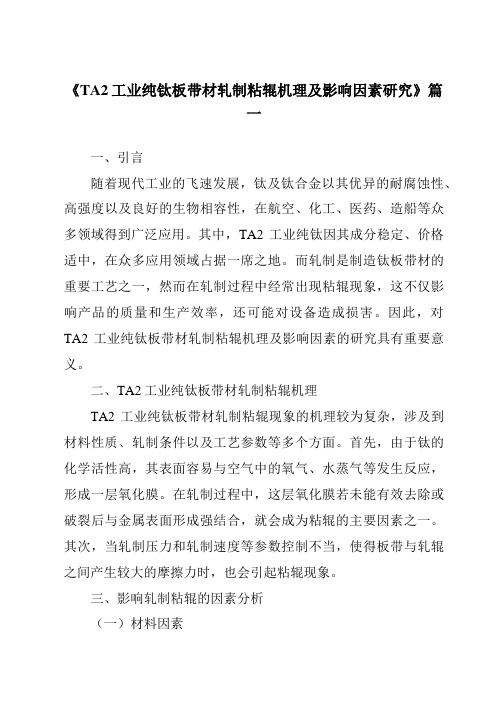
《TA2工业纯钛板带材轧制粘辊机理及影响因素研究》篇一一、引言随着现代工业的飞速发展,钛及钛合金以其优异的耐腐蚀性、高强度以及良好的生物相容性,在航空、化工、医药、造船等众多领域得到广泛应用。
其中,TA2工业纯钛因其成分稳定、价格适中,在众多应用领域占据一席之地。
而轧制是制造钛板带材的重要工艺之一,然而在轧制过程中经常出现粘辊现象,这不仅影响产品的质量和生产效率,还可能对设备造成损害。
因此,对TA2工业纯钛板带材轧制粘辊机理及影响因素的研究具有重要意义。
二、TA2工业纯钛板带材轧制粘辊机理TA2工业纯钛板带材轧制粘辊现象的机理较为复杂,涉及到材料性质、轧制条件以及工艺参数等多个方面。
首先,由于钛的化学活性高,其表面容易与空气中的氧气、水蒸气等发生反应,形成一层氧化膜。
在轧制过程中,这层氧化膜若未能有效去除或破裂后与金属表面形成强结合,就会成为粘辊的主要因素之一。
其次,当轧制压力和轧制速度等参数控制不当,使得板带与轧辊之间产生较大的摩擦力时,也会引起粘辊现象。
三、影响轧制粘辊的因素分析(一)材料因素1. 钛板的表面处理:TA2工业纯钛板的表面状态对轧制过程有显著影响。
表面粗糙度、氧化膜的厚度和性质等都会影响其与轧辊的摩擦性能。
2. 钛板的化学成分:钛板中的杂质元素和合金元素含量也会影响其与轧辊的摩擦系数和粘附性。
(二)工艺因素1. 轧制温度:轧制温度对粘辊现象有着直接影响。
当温度过高时,金属的塑性增加,摩擦力增大,导致粘辊现象更容易发生。
2. 轧制速度:过高的轧制速度会使单位时间内摩擦热量的产生增多,也可能加剧粘辊现象。
3. 轧制压力:轧制压力过大或过小都可能造成板带与轧辊之间的摩擦状态不均或摩擦力过大,从而引发粘辊。
(三)设备因素1. 轧辊的材质和表面处理:轧辊的材质、硬度以及表面粗糙度等都会影响其与钛板的摩擦性能。
某些特殊涂层或表面处理可以减少粘辊现象的发生。
2. 设备维护与清洁:设备定期的维护和清洁对防止粘辊同样重要,例如保持轧辊清洁以去除可能导致的结合强度不均等异物。
《TA2工业纯钛板带材轧制粘辊机理及影响因素研究》范文

《TA2工业纯钛板带材轧制粘辊机理及影响因素研究》篇一一、引言在金属材料加工领域,TA2工业纯钛板带材因其优异的性能被广泛应用于航空、航天、医疗、化工等众多领域。
轧制工艺作为其生产过程中的关键环节,对于产品的质量及性能具有决定性影响。
然而,轧制过程中常出现的粘辊问题,不仅影响了生产的效率和产品质量,还可能造成设备的损坏和操作人员的工作强度增加。
因此,研究TA2工业纯钛板带材轧制粘辊的机理及其影响因素,对于提高产品质量、降低生产成本和保障生产安全具有重要意义。
二、TA2工业纯钛板带材轧制粘辊机理TA2工业纯钛板带材轧制粘辊的机理主要涉及到材料本身的物理化学性质、轧制工艺参数以及设备条件等多个方面。
首先,TA2纯钛的表面能较高,容易与轧辊表面产生吸附作用,导致粘辊现象的发生。
此外,纯钛的导热性较差,轧制过程中产生的热量不易迅速散失,使得轧辊与钛板之间的摩擦热效应加剧,进一步加剧了粘辊的可能性。
其次,轧制工艺参数如轧制速度、轧制力、轧制温度等也会对粘辊现象产生影响。
例如,当轧制速度过快或轧制力过大时,会使轧辊与钛板之间的摩擦力增大,从而增加了粘辊的风险。
而当轧制温度过高时,钛板的塑性变形能力增强,但同时也使得其表面容易与轧辊发生粘附。
最后,设备条件如轧辊的材质、表面粗糙度以及润滑条件等也会影响粘辊现象的发生。
如果轧辊的材质选择不当或表面粗糙度过大,会降低其抗粘附性能;而润滑条件不良则会使摩擦系数增大,从而加剧粘辊现象的发生。
三、影响因素分析影响TA2工业纯钛板带材轧制粘辊的因素主要包括材料因素、工艺因素和设备因素三个方面。
(一)材料因素TA2纯钛的化学成分、组织结构和表面状态等材料因素对粘辊现象具有重要影响。
例如,钛板中杂质元素的含量、晶粒大小以及表面粗糙度等都会影响其与轧辊之间的相互作用力,从而影响粘辊的发生。
(二)工艺因素轧制工艺参数如轧制速度、轧制力、轧制温度等是影响粘辊的重要因素。
这些参数的选择与控制直接影响着钛板的塑性变形能力和与轧辊之间的摩擦状态,从而影响粘辊现象的发生。
钛合金轧制影响因素
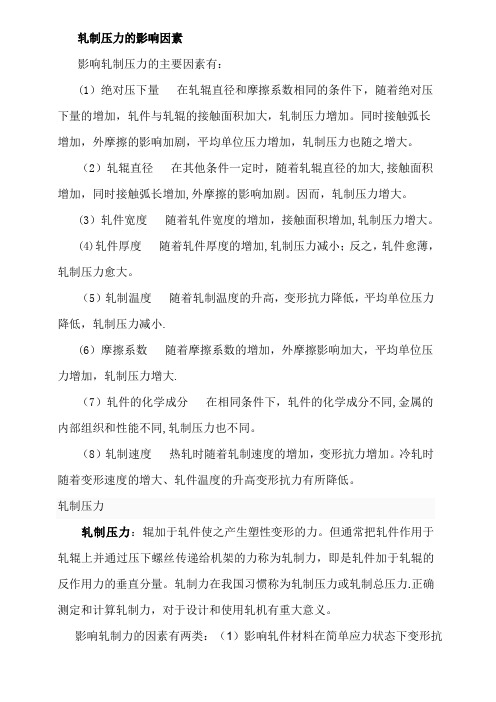
轧制压力的影响因素影响轧制压力的主要因素有:(1)绝对压下量在轧辊直径和摩擦系数相同的条件下,随着绝对压下量的增加,轧件与轧辊的接触面积加大,轧制压力增加。
同时接触弧长增加,外摩擦的影响加剧,平均单位压力增加,轧制压力也随之增大。
(2)轧辊直径在其他条件一定时,随着轧辊直径的加大,接触面积增加,同时接触弧长增加,外摩擦的影响加剧。
因而,轧制压力增大。
(3)轧件宽度随着轧件宽度的增加,接触面积增加,轧制压力增大。
(4)轧件厚度随着轧件厚度的增加,轧制压力减小;反之,轧件愈薄,轧制压力愈大。
(5)轧制温度随着轧制温度的升高,变形抗力降低,平均单位压力降低,轧制压力减小.(6)摩擦系数随着摩擦系数的增加,外摩擦影响加大,平均单位压力增加,轧制压力增大.(7)轧件的化学成分在相同条件下,轧件的化学成分不同,金属的内部组织和性能不同,轧制压力也不同。
(8)轧制速度热轧时随着轧制速度的增加,变形抗力增加。
冷轧时随着变形速度的增大、轧件温度的升高变形抗力有所降低。
轧制压力轧制压力:辊加于轧件使之产生塑性变形的力。
但通常把轧件作用于轧辊上并通过压下螺丝传递给机架的力称为轧制力,即是轧件加于轧辊的反作用力的垂直分量。
轧制力在我国习惯称为轧制压力或轧制总压力.正确测定和计算轧制力,对于设计和使用轧机有重大意义。
影响轧制力的因素有两类:(1)影响轧件材料在简单应力状态下变形抗力σ0的因素,如化学成分、组织、轧制温度和速度、加工硬化等。
(2)影响变形应力状态的因素,如轧辊直径、轧件尺寸、表面摩擦、外力(张力或推力)等。
确定轧制力的方法有理论计算、经验公式计算和实测法三种.在熔炼TiNiCr低温超弹性合金(形状记忆合金)时,对Ti、Ni、Cr、C、H、O、N成份的控制,是获得理想合金的关键。
首先O含量的增加不仅使相变温度下降,而且使记忆性能和力学性能恶化。
O在高温下与Ti发生反应,熔炼时尤为剧烈,同时O和Ti生成的化合物一般是不可逆的,所以要严格控制熔炼时材料中的氧平衡量.还有Ti和耐火材料几乎都会发生反应。
钛及钛合金管材轧制工艺研究现状
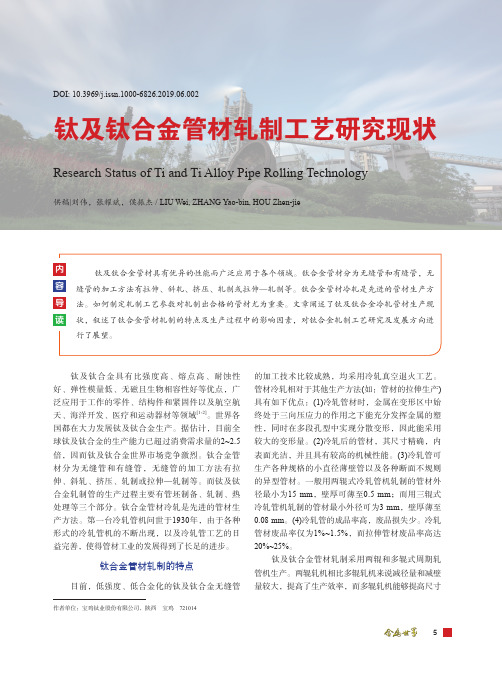
5作者单位:宝鸡钛业股份有限公司,陕西 宝鸡 721014钛及钛合金管材轧制工艺研究现状Research Status of Ti and Ti Alloy Pipe Rolling Technology供稿|刘伟,张耀斌,侯振杰 / LIU Wei, ZHANG Yao-bin, HOU Zhen-jieDOI: 10.3969/j.issn.1000-6826.2019.06.002钛及钛合金具有比强度高、熔点高、耐蚀性好、弹性模量低、无磁且生物相容性好等优点,广泛应用于工作的零件、结构件和紧固件以及航空航天、海洋开发、医疗和运动器材等领域[1-2]。
世界各国都在大力发展钛及钛合金生产。
据估计,目前全球钛及钛合金的生产能力已超过消费需求量的2~2.5倍,因而钛及钛合金世界市场竞争激烈。
钛合金管材分为无缝管和有缝管,无缝管的加工方法有拉伸、斜轧、挤压、轧制或拉伸—轧制等。
而钛及钛合金轧制管的生产过程主要有管坯制备、轧制、热处理等三个部分。
钛合金管材冷轧是先进的管材生产方法。
第一台冷轧管机问世于1930年,由于各种形式的冷轧管机的不断出现,以及冷轧管工艺的日益完善,使得管材工业的发展得到了长足的进步。
钛合金管材轧制的特点目前,低强度、低合金化的钛及钛合金无缝管的加工技术比较成熟,均采用冷轧真空退火工艺。
管材冷轧相对于其他生产方法(如:管材的拉伸生产)具有如下优点:(1)冷轧管材时,金属在变形区中始终处于三向压应力的作用之下能充分发挥金属的塑性,同时在多段孔型中实现分散变形,因此能采用较大的变形量。
(2)冷轧后的管材,其尺寸精确,内表面光洁,并且具有较高的机械性能。
(3)冷轧管可生产各种规格的小直径薄壁管以及各种断面不规则的异型管材。
一般用两辊式冷轧管机轧制的管材外径最小为15 mm ,壁厚可薄至0.5 mm ;而用三辊式冷轧管机轧制的管材最小外径可为3 mm ,壁厚薄至0.08 mm 。
(4)冷轧管的成品率高,废品损失少。
热轧钛板成材率的影响因素与提高措施
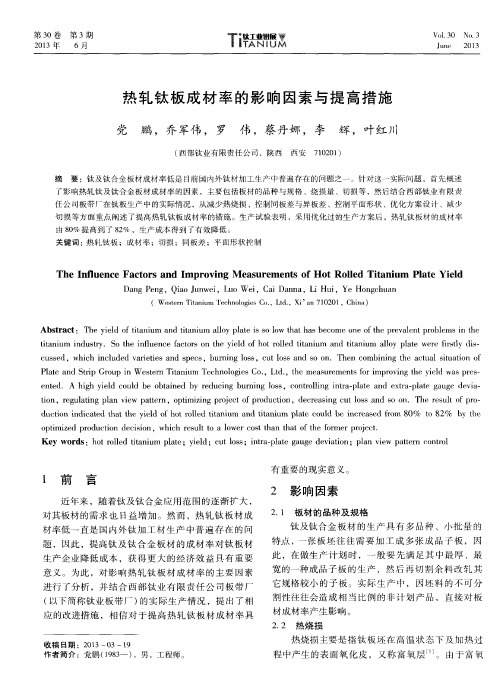
任公 司板带厂在钛板生产 中的实际情况 ,从减少热烧损 、控制 同板差 与异板 差 、控制平面形状 、优化方案设计 、减少 切损等方 面重点阐述 了提高热 轧钛 板成 材率 的措施 。生产试验表明 ,采用优化过的生产方案后 ,热 轧钛 板材的成材率 由8 0 %提高到了 8 2 % ,生产成本得 到了有效 降低 。
措施 。
值 ,分 为纵 向 同板 差 和 横 向 同板 差两 种 。 其 中 ,影
响钛 板纵 向 同板差 的主要 因素有 :① 轧 制 力 的变化 , 当采 取 低 速 咬入 、抛 出 ,高 速 轧 制 时 ,轧 制 速 度 的 变化 会造成 轧 制 力 变 化 ,从 而 导 致 轧 件 头尾 与 中部
辊 底式 电 阻炉 配备 了完 善 的热 工 自动 化 控 制 系 统 , 采 用 多 区域 分 区控温 ,控 温 精 度可 达 ±1℃ 。此 外 , 可根据 需要 使 钛 板坯 在 炉 内连 续 或 间 歇 摆 动 ,从 而 获得 较 高 的加 热 质 量 。另 外 ,由 于该 辊 底 式 电阻 炉
纹 ,且 随着 轧 制 的进 行 ,微 裂 纹 将 进 一 步 扩 展 ,严
重 时会 贯 穿 整 个 板 坯 。 因此 ,在 每 火 次 轧 制 前 ,需
将钛 坯表 面 的 富 氧 层 打磨 干 净 ,且 富 氧 层 越 厚 ,打
磨量 越大 ,从 而 导致成 材率 下降 。
2 . 3 切损
收 稿 日期 :2 0 1 3— 0 3—1 9 作 者简 介 :党鹏 ( 1 9 8 3 一) ,男 ,工 程 师 。
热烧损 主要 是 指 钛 板 坯 在 高温 状 态下 及加 热 过
程 中产生 的 表 面氧 化 皮 ,又称 富氧 层 。 由于 富 氧
《TA2工业纯钛板带材轧制粘辊机理及影响因素研究》
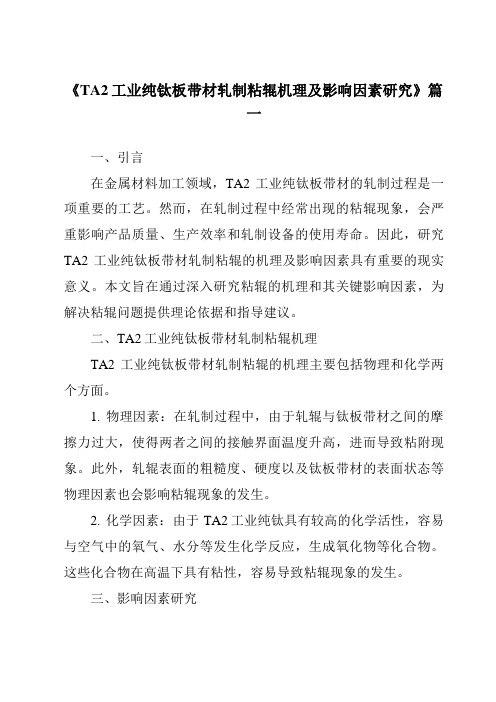
《TA2工业纯钛板带材轧制粘辊机理及影响因素研究》篇一一、引言在金属材料加工领域,TA2工业纯钛板带材的轧制过程是一项重要的工艺。
然而,在轧制过程中经常出现的粘辊现象,会严重影响产品质量、生产效率和轧制设备的使用寿命。
因此,研究TA2工业纯钛板带材轧制粘辊的机理及影响因素具有重要的现实意义。
本文旨在通过深入研究粘辊的机理和其关键影响因素,为解决粘辊问题提供理论依据和指导建议。
二、TA2工业纯钛板带材轧制粘辊机理TA2工业纯钛板带材轧制粘辊的机理主要包括物理和化学两个方面。
1. 物理因素:在轧制过程中,由于轧辊与钛板带材之间的摩擦力过大,使得两者之间的接触界面温度升高,进而导致粘附现象。
此外,轧辊表面的粗糙度、硬度以及钛板带材的表面状态等物理因素也会影响粘辊现象的发生。
2. 化学因素:由于TA2工业纯钛具有较高的化学活性,容易与空气中的氧气、水分等发生化学反应,生成氧化物等化合物。
这些化合物在高温下具有粘性,容易导致粘辊现象的发生。
三、影响因素研究1. 轧制温度:轧制温度是影响粘辊现象的关键因素之一。
当轧制温度过高时,钛板带材与轧辊之间的摩擦系数增大,导致粘附现象加剧。
因此,合理控制轧制温度对于减少粘辊现象具有重要意义。
2. 轧辊表面状态:轧辊表面的粗糙度、硬度以及是否存在缺陷等都会影响粘辊现象的发生。
优化轧辊表面状态,如采用表面涂层、抛光等手段,可以降低粘辊现象的发生。
3. 钛板带材的表面状态:钛板带材的表面粗糙度、清洁度以及是否存在氧化皮等也会影响粘辊现象。
因此,在轧制前对钛板带材进行表面处理,如酸洗、抛光等,可以改善其表面状态,从而减少粘辊现象。
4. 轧制压力:轧制压力是影响轧制过程的重要因素。
适当的轧制压力可以保证钛板带材与轧辊之间的良好接触,但过大的轧制压力可能导致摩擦力增大,从而加剧粘辊现象。
因此,合理控制轧制压力对于减少粘辊现象具有重要意义。
5. 原料成分与组织:TA2工业纯钛的化学成分、晶粒大小以及组织结构等也会影响其轧制过程中的粘辊现象。
- 1、下载文档前请自行甄别文档内容的完整性,平台不提供额外的编辑、内容补充、找答案等附加服务。
- 2、"仅部分预览"的文档,不可在线预览部分如存在完整性等问题,可反馈申请退款(可完整预览的文档不适用该条件!)。
- 3、如文档侵犯您的权益,请联系客服反馈,我们会尽快为您处理(人工客服工作时间:9:00-18:30)。
轧制压力的影响因素影响轧制压力的主要因素有:(1)绝对压下量在轧辊直径和摩擦系数相同的条件下,随着绝对压下量的增加,轧件与轧辊的接触面积加大,轧制压力增加。
同时接触弧长增加,外摩擦的影响加剧,平均单位压力增加,轧制压力也随之增大。
(2)轧辊直径在其他条件一定时,随着轧辊直径的加大,接触面积增加,同时接触弧长增加,外摩擦的影响加剧。
因而,轧制压力增大。
(3)轧件宽度随着轧件宽度的增加,接触面积增加,轧制压力增大。
(4)轧件厚度随着轧件厚度的增加,轧制压力减小;反之,轧件愈薄,轧制压力愈大。
(5)轧制温度随着轧制温度的升高,变形抗力降低,平均单位压力降低,轧制压力减小。
(6)摩擦系数随着摩擦系数的增加,外摩擦影响加大,平均单位压力增加,轧制压力增大。
(7)轧件的化学成分在相同条件下,轧件的化学成分不同,金属的内部组织和性能不同,轧制压力也不同。
(8)轧制速度热轧时随着轧制速度的增加,变形抗力增加。
冷轧时随着变形速度的增大、轧件温度的升高变形抗力有所降低。
轧制压力轧制压力:辊加于轧件使之产生塑性变形的力。
但通常把轧件作用于轧辊上并通过压下螺丝传递给机架的力称为轧制力,即是轧件加于轧辊的反作用力的垂直分量。
轧制力在我国习惯称为轧制压力或轧制总压力。
正确测定和计算轧制力,对于设计和使用轧机有重大意义。
影响轧制力的因素有两类:(1)影响轧件材料在简单应力状态下变形抗力σ0的因素,如化学成分、组织、轧制温度和速度、加工硬化等。
(2)影响变形应力状态的因素,如轧辊直径、轧件尺寸、表面摩擦、外力(张力或推力)等。
确定轧制力的方法有理论计算、经验公式计算和实测法三种。
在熔炼TiNiCr低温超弹性合金(形状记忆合金)时,对Ti、Ni、Cr、C、H、O、N成份的控制,是获得理想合金的关键。
首先O含量的增加不仅使相变温度下降,而且使记忆性能和力学性能恶化。
O在高温下与Ti发生反应,熔炼时尤为剧烈,同时O和Ti生成的化合物一般是不可逆的,所以要严格控制熔炼时材料中的氧平衡量。
还有Ti和耐火材料几乎都会发生反应。
其次C含量对TiNiCr低温超弹性合金的力学性能影响不明显,但对热弹性马氏体的相变有影响,C在Ni中有大的溶解度,形成的TiC会阻碍孪晶界的运动及马氏体的再取向,使相变滞后扩大,回复率下降,对形状记忆效应和超弹性都不利。
而且,C和单质Ti和Ni均反应,使TiNi合金中的C含量增加,然而C和TiNi合金的反应并不剧烈,可使C质量分数控制在0.05%左右。
碳质量分数控制在0.05%左右。
所以通常使用三高石墨坩埚真空感应熔炼制备合金锭,这样可降低熔炼时碳的污染,保证碳和氧的含量小于500p。
g/L。
固溶热处理:将合金加热至高温单相区恒温保持,使过剩相充分溶速冷却,以得到过饱和固溶体的热处理工艺。
时效处理可分为自然时效和人工时效两种,自然时效是将铸件置于露天场地半年以上,便其缓缓地发生变形,从而使残余应力消除或减少,人工时效是将铸件加热到550~650℃进行去应力退火,它比自然时效节省时间,残余应力去除较为彻底。
金属的强度和塑性和晶粒大小都有关系。
首先是强度,存在一个霍尔佩奇公式,材料强度随晶粒大小变小而变强,温度升高强度会大幅减小,可是这个公式在纳米晶粒时候不适用,纳米晶的强度增强的更大;但单晶体强度不遵循上述规律,单晶体的强度很强,并且在高温时候仍能保持很强强度。
塑形,是晶粒越细塑形越好。
细化晶粒的方法,1.凝固控制,包括晶粒细化剂(一般是中间合金),晶粒细化元素;缩短凝固时间,这个不能太过,太多会产生非晶;凝固过程施加电磁搅拌之类的外力物理细晶。
2.已经成锭的可以锻造细化晶粒(这种方法在一定条件下可以制备纳米晶,参考卢柯院士的相应文章);冷加工轧制可以在轧制方向细化晶粒,然后再结晶也可以细化晶粒。
金属冷变形程度的大小对再结晶形核机制和再结晶晶粒尺寸的影响晶体再结晶需要一个最小变形量,称为临界变形量。
但变形量小于临界变形量时,不发生再结晶。
当高于临界变形量时,能再结晶但晶粒粗大。
以后随变形量增加,晶粒尺寸变小。
形核机制有两种:1、已存在晶界的引出形核:晶粒变形小的时候较易发生这种;2、亚晶合并形核或直接长大:变形率大的。
再结晶形核是现存于局部高能量区域内的,以多边化形成的亚晶为基础形核。
亚晶粒本身是在剧烈应变的基体通过多边化形成的,几乎无位错的低能量地区,它通过消耗周围的高能量区长大成为再结晶的有效核心,因此,随着形变度的增大,会产生更多的亚晶而有利于再结晶形核。
当变形量很小时,储存能不足以驱动再结晶,晶粒尺寸为原始晶粒尺寸。
当变形量增大到一定程度时,此时的畸变能已足以引起再结晶,但由于变形程度不大,形核率与长大速率比值很小,因此得到特别粗大晶粒。
随着变形量增大,驱动形核与长大的储存能不断增大,而形核率增大较快,使形核率与长大速率比值增大,得到再结晶晶粒越来越细化。
一次再结晶完成时标示着储存能消耗殆尽,若再结晶充分,也说明再结晶晶粒靠在一起了,再结晶晶粒停止长大。
对于后面的问题,可以如下理解:形变程度小,意味着再结晶形核的场所少,形核率低,在储存能足够的基础上,这些再结晶新晶粒有充分的空间满足其长大(只要给足温度条件)(能量多,形核少,再结晶新晶粒就可以长得比较粗大);当形变程度大,再结晶的形核率高,再结晶新晶粒形核长大很快遇到相邻再结晶晶粒,两者都是“干净”的晶粒,提早终止了长大(能量多,形核也多,再结晶新晶粒基本均匀长大,总体长大的相对较小)。
所以,才会考虑利用大应变提高形核率细化组织。
入口锥的主要参数是入口锥角β和长度L。
入口锥角β的大小要适当,角度过大润滑剂不易储存,易造成拉拔润滑不良;角度过小,则拉拔时产生的金属屑、粉末等不易随润滑剂流掉,堆积于模孔中影响制品的质量,甚至还会造成夹灰、划沟、拉断等缺陷。
生产中硬质合金模的入口锥角β大小一般为40°,入口锥的长度L一般取定径带直径的0.6倍。
棒材拉拔中润滑锥常用R=4~8mm的圆弧代替。
在回复阶段硬度的变化很小,约占总变化的1/5;在再结晶阶段变化很大,占4/5。
硬度一般是和强度成正比例的一个性能指标,所以由此推论,回复过程中强度的变化也应该和硬度的变化相似。
形变引起的硬度和强度的增加量主要取决于位错密度,由此可推出,在回复过程中,位错密度的减小有限,只有达到再结晶阶段时,位错密度才会显著下降。
位错密度的数量级我不清楚了,但是其强度和位错密度的关系差不多是个U型字母,既开始随着位错密度增大,金属强度是降低的,在退火状态下是金属强度最低的时候,之后随着位错密度增加,强度增加,这里就比如说加工硬化,位错增加,硬度提高了热电偶测温原理两种不同金属焊接成的闭合电路叫做热电偶。
由于不同金属自由电子的气密度不一样,在焊接处两种金属中的自由电子相互扩散出现差异,致使两金属接触处出现一个电势差,此为接触电动势。
接触电动势除了与两种金属性质有关外还与温度有关,在温度相同的情况下,两接头处电动势数值相等,方向相反,总电动势为零。
如果两接头处温度不同,两电动势数值不同,总电动势就不为零,闭合电路就会出现电流,这种由温差引起的电流叫做温差电流。
用温差电偶测量温度的方法是:令一个接头的温度已知,另一接头插入待测温度的物体中,测出电偶内出现的温差电流,便可推知被测温度。
加工硬化:金属材料在再结晶温度以下塑性变形时,由于晶粒发生滑移,出现位错的缠结,使晶粒拉长、破碎和纤维化,使金属的强度和硬度升高,塑性和韧性降低的现象,称加工硬化或冷作硬化。
随着冷变形程度的增加,金属材料强度和硬度指标都有所提高,但塑性、韧性有所下降。
加工硬化简介:金属材料在再结晶温度以下塑性变形时强度和硬度升高,而塑性和韧性降低的现象。
又称冷作硬化。
产生原因是,金属在塑性变形时,晶粒发生滑移,出现位错的缠结,使晶粒拉长、破碎和纤维化,金属内部产生了残余应力等。
加工硬化的程度通常用加工后与加工前表面层显微硬度的比值和硬化层深度来表示。
在纳米材料中也会出现加工硬化现象,此时的硬化行为多认为和位错运动密切相关。
加工硬化给金属件的进一步加工带来困难。
如在冷轧钢板的过程中会愈轧愈硬以致轧不动,因而需在加工过程中安排中间退火,通过加热消除其加工硬化。
又如在切削加工中使工件表层脆而硬,从而加速刀具磨损、增大切削力等。
但有利的一面是,它可提高金属的强度、硬度和耐磨性,特别是对于那些不能以热处理方法提高强度的纯金属和某些合金尤为重要。
如冷拉高强度钢丝和冷卷弹簧等,就是利用冷加工变形来提高其强度和弹性极限。
又如坦克和拖拉机的履带、破碎机的颚板以及铁路的道岔等也是利用加工硬化来提高其硬度和耐磨性的。
固溶强化:合金元素固溶于基体金属中造成一定程度的晶格畸变从而使合金强度提高的现象。
原理:融入固溶体中的溶质原子造成晶格畸变,晶格畸变增大了位错运动的阻力,使滑移难以进行,从而使合金固溶体的强度与硬度增加。
这种通过融入某种溶质元素来形成固溶体而使金属强化的现象称为固溶强化。
在溶质原子浓度适当时,可提高材料的强度和硬度,而其韧性和塑性却有所下降。
影响因素(1)溶质原子的原子分数越高,强化作用也越大,特别是当原子分数很低时,强化作用更为显著。
(2)溶质原子与基体金属的原子尺寸相差越大,强化作用也越大。
(3)间隙型溶质原子比置换原子具有较大的固溶强化效果,且由于间隙原子在体心立方晶体中的点阵畸变属非对称性的,故其强化作用大于面心立方晶体的;但间隙原子的固溶度很有限,故实际强化效果也有限。
(4)溶质原子与基体金属的价电子数目相差越大,固溶强化效果越明显,即固溶体的屈服强度随着价电子浓度的增加而提高。
程度:固溶强化的程度主要取决于两个因素:1.原始原子和添加原子之间的尺寸差别。
尺寸差别越大,原始晶体结构受到的干扰就越大,位错滑移就越困难。
2.合金元素的量。
加入的合金元素越多,强化效果越大。
如果加入过多太大或太小的原子,就会超过溶解度。
这就涉及到另一种强化机制,分散相强化。
3.间隙型溶质原子比置换型原子具有更大的固溶强化效果。
4.溶质原子与基体金属的价电子数相差越大,固溶强化作用越显著。
效果:1.屈服强度、拉伸强度和硬度都要强于纯金属2.绝大部分情况下,延展性低于纯金属3.导电性比纯金属低很多4.抗蠕变,或者在高温下的强度损失,通过固溶强化可以得到改善解理断裂是在正应力作用产生的一种穿晶断裂,即断裂面沿一定的晶面(即解理面)分离。
解理断裂常见于体心立方和密排六方金属及合金,低温、冲击载荷和应力集中常促使解理断裂的发生。
面心立方金属很少发生解理断裂。
解理断裂通常是宏观脆性断裂,它的裂纹发展十分迅速,常常造成零件或构件灾难性的总崩溃。
解理断裂断口的轮廓垂直于最大拉应力方向。
新鲜的断口都是晶粒状的,有许多强烈反光的小平面(称为解理刻面)。