模具表面强化处理技术
模具表面强化技术及其应用
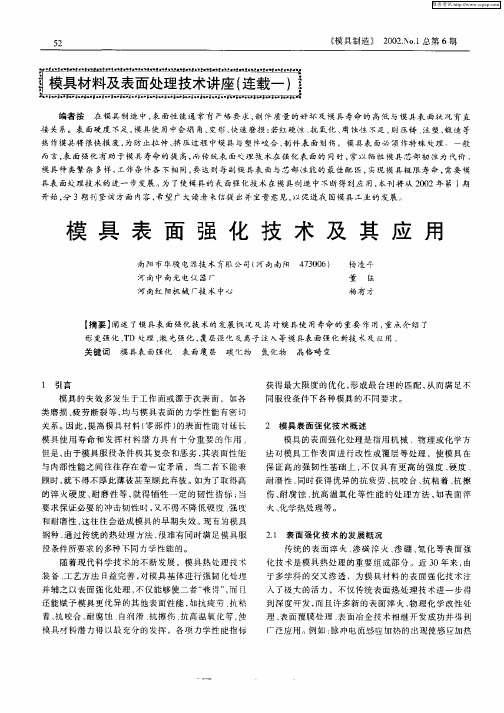
l 引 言
获得 晟 大限 度的优 化 , 形成最 合理 的匹 配 , 而满 足不 从
同服役 条件 下各 种模具 的不 同要 求 。
2 模 具 表 面 强 化 技 术 概 述
模具 的失 效 多发 生于 工作 面或 源 于次 表面 ,如各 类磨 损 、 劳断 裂等 , 与模 具表 面 的力学 性能 有密 切 疲 均
并 辅 之 以表面 强化 处理 , 不仅 能够使 二者 “ 得 ”而 且 兼 , 还能 赋予 模具 更咬台 、 腐蚀 、 抗 耐 自润滑 、 擦伤 、 高 温氧化 等 , 抗 抗 使
模具 材料 潜力 得 以最充 分 的发 挥 ,各项 力 学性 能指标
热作模 县将很 快报 废 , 为防 止拉 仲 、 挤压 过程 中摸具 与 塑件 喧夸 、 制件 表 面划 伤 ,模 具 表 面必 须作 特殊 处理 一一般
而言 . 面强化 有助 于模 具 寿命 的提 高 , 表 而传 统表 面处理技 术在 强化 表 面的 同时 , 以牺 牲 模具 芯部 韧性 为 代 价。 常 模具种 类繁 杂 多样 , I作条件 各 不相 同, 达 到每 副模 具表 面与芯部 一 要 洼能的 最佳 配 匹 , 实现 模 具极 限寿命 , 需要 模
模具 的表 面强 化处 理是 指 用机 械 、物 理 或化 学方
法对 模 具工 作表 面进行 改性 或 覆层 等处 理 ,使模 具在
保 证 高的强 韧 性 基础 上 , 仅具 有 更 高 的 强 度 、 度 、 不 硬
耐磨 性 . 时获得 优异 的抗 疲 劳 、 同 抗咬 合 、 抗粘 着 、 抗擦
关 系。因此 , 高模 具 材料 ( 提 零部 件 ) 的表面性 能对 延长 模 具使 用 寿命 和 发 挥 材 料潜 力 具 有 十分 重 要 的作 用 。 但 是 , 于模 具 服役条 件 极其 复杂 和恶 劣 , 由 其表 面性 能
压铸模具冲蚀表面强化处理

Working Load:150 T
Tool steel Hardness Surface treatment performance
Failure due to
Original 8407
50 HRC -
热疲劳龟裂
B,解决方案 1,选用具有在高温环境中高强度和高硬度 高韧性的模具材料(如DIEVAR,8407). 2,设计好的冷却水孔,降低模具表面温度. 3,增加模具表面压应力,细化压缩表面晶 粒,增加表面硬度(如ABP表面强化处理).
黏着的机理
• 黏着是指压铸产品与模具之间粘合,造成产 品和模具的表面损伤.
裂纹弥合,在制品上不再有明显裂纹复制的 痕迹
ABP是提高模具耐热疲劳性,抵抗早期龟 裂即经济又实惠的方法!!
三、 ASO: 提高模具抗侵蚀性能的表面处理
ASO表面强化处理
什么是 ASO 表面处理?
ASO采用特别开发专用的设备,进
行蒸汽加热,在模具表面生成致密 的,稳定的具有保护性的Fe3O4氧化
22.3
失重率
17.3
12.3 7.3 2.3
无表面处理 ABP ASN ASN+ASO
-2.7 十分钟 十五分钟 三十分钟 动态熔损时间
DIEVAR表面处理熔损试验比较
22.3
失重率
17.3
12.3 7.3 2.3
无表面处理 ABP ASN ASN+ASO
-2.7 十分钟 十五分钟 三十分钟 动态熔损时间
采用较低的冲头速度以降低卷气-这样设置冲头会较慢的运动到注 料口
目录
一、模具的失效方式及解决方案 二、ABP:
提高模具抗热疲劳龟裂的表面处理 三、 ASO:
模具的表面处理技术

模具的表面处理技术模具在工作中除了要求基体拥有充足高的强度跟韧性的合理搭配外,其表面性能对模具的工作性能跟运用寿命至关紧要。
这些表面性能指:耐磨损性能、耐腐蚀性能、摩擦系数、疲乏性能等。
这些性能的改善,单纯倚靠基体材料的改进跟提升是非常有限的,也是不经济的,而通过表面处理技术,往往能够收到事半功倍的效果,这也正是表面处理技术得到快速进展的原因。
模具的表面处理技术,是通过表面涂覆、表面改性或复合处理技术,更改模具表面的形态、化学成分、组织结构跟应力状态,以取得所需表面性能的系统工程。
从表面处理的方式上,又可分为:化学方法、物理方法、物理化学方法跟机械方法。
虽然旨在提升模具表面性能新的处理技术连续涌现,但在模具制造中应用较多的重要是渗氮、渗碳跟硬化膜沉积。
渗氮工艺有气体渗氮、离子渗氮、液体渗氮等方式,每一种渗氮方式中,都有若干种渗氮技术,能够适应不一样钢种不一样工件的要求。
由于渗氮技术可形成优良性能的表面,而且渗氮工艺跟模具钢的淬火工艺有良好的协调性,同时渗氮温度低,渗氮后不需白热化冷却,模具的变形微小,因此模具的表面强化是采纳渗氮技术较早,也是应用zui广泛的。
模具渗碳的目标,重要是为了提升模具的整体强韧性,即模具的工作表面拥有高的强度跟耐磨性,由此引入的技术思路是,用较低级的材料,即通过渗碳淬火来取代较另外材料,从而降低制造成本。
硬化膜沉积技术目前较成熟的是CVD、PVD。
为了加添膜层工件表面的结合强度,现今进展了多种加强型CVD、PVD技术。
硬化膜沉积技术zui早在工具(刀具、刃具、量具等)上应用,效果,多种刀具已将涂覆硬化膜作为标准工艺。
模具自上个世纪80时代开始采纳涂覆硬化膜技术。
目前的技术条件下,硬化膜沉积技术(重要是设备)的成本较高,依旧只在一些精密、长寿命模具上应用,假如采纳建设热处理中心的方式,则涂覆硬化膜的成本会大大降低,越来越多的模具假如采纳这一技术,能够整体提升我国的模具制造水平。
模具表面强化技术及其应用

硬“ 涂层 ” 实为渗 层 ) 由于这些 碳化 物具 有很 高 的硬 ( 。
度 . 以经 T 所 D法 处理 的模 具可获 得特别 优异 的力 学性 能 。一 般来说 , 采用 T D处理 与采用 C D( 学气相 沉 V 化 积 )P V 等 离子 化 学 气 相 沉 积 ) 方法 进 行 的表 面 、 C D( 等 硬 化 处理效 果 相近 似 , 由 于 T 但 D法 设备 简 单 、 操作 简 便 、 本低廉 、 以是一 种 很有 发展前 途 的表 面强化 处 成 所 理 技术 。T D处 理 在国外 应 用 已相 当普 遍 , 在 国 内报 但
《 模具 制造 》 2 0 .o2总第 7期 0 2N
不同。
5 1 处理 的性能 比较 。
由 于碳 化 物 中 的 C来 自工 件 ( 材 ) 身 , 此 要 基 本 因
求 基材 的台碳 量在 04 - %以上 , 般 以含碳 量 较高 的工 一
具钢最适 宜作 T 处理 的基材 。 D
44 T . D处理 的工 艺 参数 影响 T D涂层厚 度 的主要 因素是 盐浴 温度 、 理 时 处 间和 基材 的化 学 成分 , 关 系为 = t ̄ , 中 D 为 其 Ae 式 “ 覆 ” 厚 度 (I )t 浸 渍 时间 () T为工 艺 温 度 涂 层 [I ; 为 i1 1 s; ( ; 为 碳 化 物 层 的 扩 散 激 活 能 ( 为 174 ~ K)9 约 6. 7
道 并不 多见 。
43 碳 化 物 的 形 成 机 理 _
第5章 模具钢料的热处理-模具表面处理技术

第二节模具表面处理工艺概述模具是现代工业之母。
随着社会经济的发展,特别是汽车、家电工业、航空航天、食品医疗等产业的迅猛发展,对模具工业提出了更高的要求。
如何提高模具的质量、使用寿命和降低生产成本,成为各模具厂及注塑厂当前迫切需要解决的问题。
模具在工作中除了要求基体具有足够高的强度和韧性的合理配合外,其表面性能对模具的工作性能和使用寿命至关重要。
这些表面性能指:耐磨损性能、耐腐蚀性能、摩擦系数、疲劳性能等。
这些性能的改善,单纯依赖基体材料的改进和提高是非常有限的,也是不经济的,而通过表面处理技术,往往可以收到事半功倍的效果;模具的表面处理技术,是通过表面涂覆、表面改性或复合处理技术,改变模具表面的形态、化学成分、组织结构和应力状态,以获得所需表面性能的系统工程。
从表面处理的方式上,又可分为:化学方法、物理方法、物理化学方法和机械方法。
在模具制造中应用较多的主要是渗氮、渗碳和硬化膜沉积。
◆提高模具的表面的硬度、耐磨性、摩擦性、脱模性、隔热性、耐腐蚀性;◆提高表面的高温抗氧化性;◆提高型腔表面抗擦伤能力、脱模能力、抗咬合等特殊性能;减少冷却液的使用;◆提高模具质量,数倍、几十倍地提高模具使用寿命。
减少停机时间;◆大幅度降低生产成本与采购成本,提高生产效率和充分发挥模具材料的潜能。
◆减少润滑剂的使用;◆涂层磨损后,还退掉涂层后,再抛光模具表面,可重新涂层。
在模具上使用的表面技术方法多达几十种,从表面处理的方式上,主要可以归纳为物理表面处理法、化学表面处理法和表面覆层处理法。
模具表面强化处理工艺主要有气体氮化法、离子氮化法、点火花表面强化法、渗硼、TD法、CVD化学气相淀积、PVD物理气相沉积、PACVD离子加强化学气相沉积、CVA铝化化学气相沉积、激光表面强化法、离子注入法、等离子喷涂法等等。
下面综述模具表面处理中常用的表面处理技术:一、物理表面处理法:表面淬火是表面热处理中最常用方法,是强化材料表面的重要手段,分高频加热表面淬火、火焰加热表面淬火、激光表面淬火。
模具材料及表面强化处理1

模具材料及表面强化处理1引言模具是工业生产中必不可少的工具,它们在制造产品的过程中起着至关重要的作用。
模具材料的选择和表面强化处理对于模具的性能和寿命有着重要的影响。
本文将介绍常见的模具材料以及常用的表面强化处理方法。
一、模具材料1.1 铸造模具材料1.1.1 灰铁灰铁常用于生产小型模具,其具有良好的耐磨性和可加工性。
然而,由于其脆性较高,不适用于生产大型模具。
1.1.2 钢钢是最常用的模具材料之一,具有良好的强度和耐磨性。
根据工作条件的不同,可以选择碳素钢、合金钢或工具钢作为模具材料。
1.1.3 铝合金铝合金模具具有较低的密度和良好的导热性能,适用于高速冲压和热压成型。
1.2 塑料模具材料1.2.1 铝合金铝合金模具用于生产小型塑料制品,如手机壳等。
它具有良好的导热性和低重量,适用于高速注塑。
1.2.2 硅橡胶硅橡胶模具适用于制造高精度的塑料制品,如光学镜片。
它具有较低的粘附性和高弹性,便于脱模。
二、表面强化处理方法2.1 热处理热处理是常用的表面强化处理方法之一,通过控制材料的加热和冷却过程,使材料的组织结构得到改善,提高其硬度和耐磨性。
2.2 表面喷涂表面喷涂是一种常见的表面强化处理方法,通过在模具表面喷涂一层具有高硬度和耐磨性的材料,如陶瓷涂层或金属涂层,增加模具的寿命和耐磨性。
2.3 氮化处理氮化处理是一种提高模具硬度和耐磨性的表面强化处理方法。
在高温下,将模具表面与氨气反应,形成氮化层,提高模具的硬度和耐磨性。
2.4 氧化处理氧化处理是一种常用的提高模具抗氧化性能的表面强化处理方法。
通过在模具表面形成氧化层,阻止金属与氧气的直接接触,降低模具的氧化速度。
三、结论模具的材料选择和表面强化处理对于模具的性能和寿命有着重要的影响。
灰铁、钢和铝合金是常用的铸造模具材料,而铝合金和硅橡胶是常用的塑料模具材料。
常见的表面强化处理方法包括热处理、表面喷涂、氮化处理和氧化处理,通过这些方法可以提高模具的硬度、耐磨性和抗氧化性能。
第十章-模具表面强化技术

*
表面化学热处理技术
二、渗氮(氮化)
(一)气体渗氮
表2 部分模具钢的气体渗氮工艺规范
牌号
处理 方法
渗氮工艺规范
渗氮层 深度/mm
表面硬度
阶段
渗氮温度/℃
时间/h
氨分解率/%
30CrMnSiA
一段
—
500±5
25~30
20~30
0.2~0.3
(一)气体渗氮
(1) 经过渗氮后钢表面形成一层极硬的合金氮化物,渗氮层的硬度一般可达到68~72HRC,不需要再经过淬火便具有很高的表面硬度和耐磨层,而且还可以保持到600~650℃而不明显下降。
(2) 渗氮后钢的疲劳极限可提高15%~35%。这是由于渗氮层的体积增大,使工件表面产生了残余压应力。
(3) 渗氮后的钢具有很高的抗腐蚀能力。
>58HRC
Cr12MoV
760~800HV
*
表面化学热处理技术
二、渗氮(氮化)
(二)离子渗氮
离子渗氮有如下特点:
(1) 渗氮速度快,生产周期短。
(2) 渗氮层质量高。
(3) 工件的变形小。
(4) 对材料的适应性强。
氮碳共渗
提高硬度、耐磨性、抗粘附性、抗蚀性、耐热疲劳性
冷挤模、拉深模、挤压模穿孔针
渗硼
具有极好的表面硬度、耐磨性、抗粘附性、抗氧化性、热硬性、良好的抗蚀性
挤压模、拉深模
碳氮硼三元共渗
提高硬度、强度、耐磨性、耐疲劳性、抗蚀性
挤压模、冲头针尖
盐浴覆层 (TD处理)
提高硬度、耐磨性、耐热疲劳性、抗蚀性、抗粘附性、抗氧化性
模具表面处理工艺
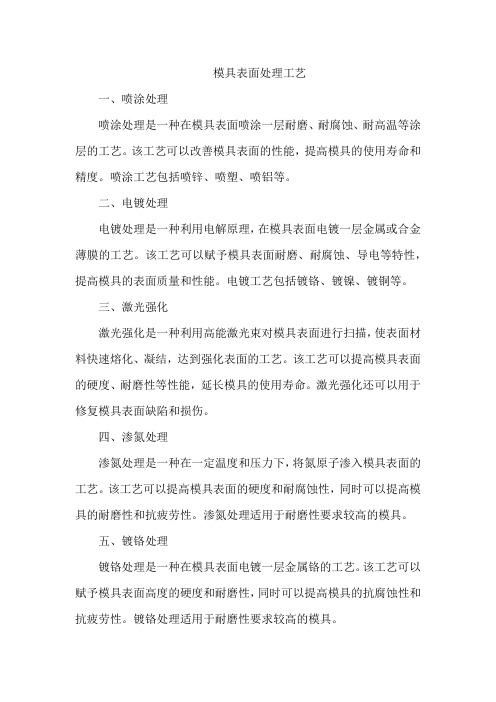
模具表面处理工艺一、喷涂处理喷涂处理是一种在模具表面喷涂一层耐磨、耐腐蚀、耐高温等涂层的工艺。
该工艺可以改善模具表面的性能,提高模具的使用寿命和精度。
喷涂工艺包括喷锌、喷塑、喷铝等。
二、电镀处理电镀处理是一种利用电解原理,在模具表面电镀一层金属或合金薄膜的工艺。
该工艺可以赋予模具表面耐磨、耐腐蚀、导电等特性,提高模具的表面质量和性能。
电镀工艺包括镀铬、镀镍、镀铜等。
三、激光强化激光强化是一种利用高能激光束对模具表面进行扫描,使表面材料快速熔化、凝结,达到强化表面的工艺。
该工艺可以提高模具表面的硬度、耐磨性等性能,延长模具的使用寿命。
激光强化还可以用于修复模具表面缺陷和损伤。
四、渗氮处理渗氮处理是一种在一定温度和压力下,将氮原子渗入模具表面的工艺。
该工艺可以提高模具表面的硬度和耐腐蚀性,同时可以提高模具的耐磨性和抗疲劳性。
渗氮处理适用于耐磨性要求较高的模具。
五、镀铬处理镀铬处理是一种在模具表面电镀一层金属铬的工艺。
该工艺可以赋予模具表面高度的硬度和耐磨性,同时可以提高模具的抗腐蚀性和抗疲劳性。
镀铬处理适用于耐磨性要求较高的模具。
六、喷丸处理喷丸处理是一种利用高速气流将弹丸喷射到模具表面,使表面材料发生塑性变形的工艺。
该工艺可以改善模具表面的粗糙度和形状精度,同时可以提高模具的抗疲劳性和耐磨性。
喷丸处理适用于各种类型的模具。
七、氧化处理氧化处理是一种将金属表面氧化成氧化膜的工艺。
该工艺可以提高模具表面的硬度和耐磨性,同时可以增强模具的抗腐蚀性和抗氧化性。
氧化处理适用于钢铁、铝合金等金属材质的模具。
八、抛光处理抛光处理是一种利用抛光机械对模具表面进行抛光加工的工艺。
该工艺可以改善模具表面的粗糙度和形状精度,同时可以提高模具的抗腐蚀性和抗疲劳性。
抛光处理适用于各种类型的模具。
九、渗碳处理渗碳处理是一种在高温下将碳原子渗入模具表面的工艺。
该工艺可以提高模具表面的硬度和耐磨性,同时可以增强模具的抗疲劳性和韧性。
金属模具表面超硬化处理—TD技术简介

金属模具表面超硬化处理—TD技术简介TD能做什么?1、能让磨损失效的冷作模具在同等工况下使用寿命平均提高10倍。
2、能让模具(工装)的使用成本降低50%甚至以上。
一、原理TD模具表面超硬化处理技术,采用金属碳化物扩散覆层TD (Thermal Diffusion Coating Process)原理,是在一定的处理温度下将工件置于硼砂熔盐及其特种介质中,通过特种熔盐中的金属原子和工件中的碳、氮原子产生化学反应,扩散在工件表面而形成一层几微米至二十余微米的钒、铌、铬、钛等金属碳化层。
经本公司不断地持续改进,目前在解决冷作模具磨损失效的应用其技术、品质、成本和响应速度等综合优势居行业领先地位。
二、技术特点---只适合于磨损失效且在常温下工作的工件(模具、标准件、机械部件)。
λ模具表面硬度大大提高,全面解决磨损、拉毛等现象。
同等工况下,使用寿命平均提高十倍以上;λ与基体冶金结合,表现出最优异的抗剥离性;可反复处理;λλ不论工件形状如何,都能形成均匀的被覆层,处理过程中模具变形较小;λ被覆后的表面粗糙度与处理前大致相同,若母材表面加工光滑,处理后可直接使用。
三、选择TD的理由成本理由:λ直接成本模具使用寿命大大提高,降低了模具的制作和维修费用。
间接成本产品废次品率大幅降低;不用经常拆装、维修模具,劳动效率大幅提高。
λ技术及工艺理由:彻底解决模具磨损、拉毛等现象,产品外观好(无划伤),工差小(理论工差≤15um)。
λ环保理由:部分冲压加工工艺中可完全省去原用的磷化、皂化工序,生产过程更环保、更安全,生产现场更易于管理。
λ营销及企业核心竞争力理由:综合成本低(价廉)、产品质量高(外观好、工差小)、供货及时(不用经常拆修模具,产量能得到基本保证)是提高核心竞争力的最原始也是最根本的、最高级的利器。
四、TD最直接的应用λ所有以磨损失效的冷作模具、标件:冲压、挤压、冷镦工艺中的成形、整形、翻边、翻孔、引伸类模具(工件)。
模具表面强化技术应用现状及发展
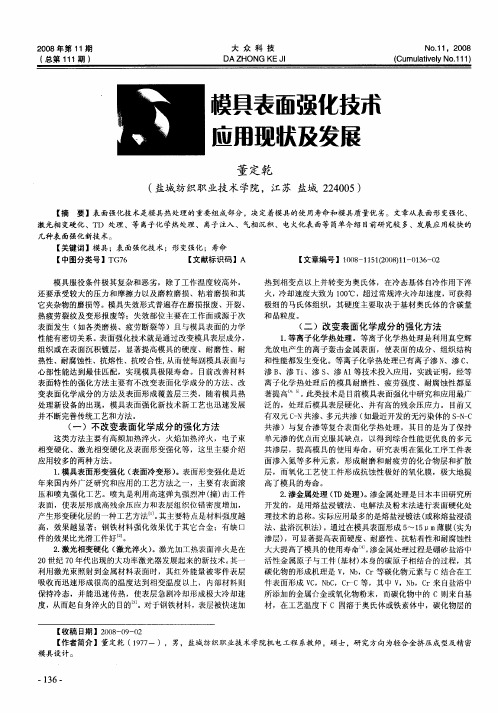
( )改 变表面 化学成 分的强 化方法 二
1等 离子 化学热处理。等离子化学热处理是利用真空辉 . 光放 电产生的离子轰击金属表面 ,使表面的成分、组织结构
和性 能都发生变化 。等离子化学热处理 已有离子渗 N 、渗 C 、 渗B 、渗 T 、渗 S i 、渗 A 等技术投入应用,实践证 明,经等 1 离子化学热处理后的模具耐磨性 、疲劳强度、耐腐蚀性都显 著提 高 ’ 此类技术是 目前模具表面强化 中研究和应用最广 。 泛的 ,处理后模具表层硬化、并有高的残余压应力 。目前又 有双元 C N共渗、多元共渗 ( - 如最近 开发 的无污染体的 S N C - — 共渗 )与复合渗等复合表面化学热处理 ,其 目的是为 了保持 单元渗的优点而克服其缺点 ,以得到综合性能更优 良的多元 共渗层 ,提高模具的使用寿命 。研究表 明在氮化工序工件表 面渗入氮等多种元素,形成耐磨和耐疲劳 的化合物层和扩散 层,而氧化工艺使工件形成抗蚀性极好的氧化膜 ,极大地提 高了模具的寿命 。 2渗金属处理 (D处理 ) 渗金属处理是 日本丰 田研究所 . T 。 开 发 的 ,是 用 熔 盐 浸 镀 法 、 电解 法 及 粉 末 法 进 行 表 面 硬 化 处 理技术的总称 。实际应用最多的是熔盐浸镀法 ( 或称熔盐浸渍 法、盐浴沉积法) 。通过在模 具表面形成 5 5. ~1 1m薄膜 ( 1 实为 渗层) ,可显著提高表面硬度、耐磨性、抗粘着性和 耐腐蚀性 大大提高了模具的使用寿命 。 渗金属处理过程是硼砂盐浴中 活性金属原子与工件 ( 基材 ) 本身 的碳原子相结合 的过程 ,其 碳化物的形成机理是 V b r等碳化物 元素与 C结合在工 ,N ,C 件表面形成 V ,N C rC等 ,其中 V b r来 自盐浴中 C b ,C — ,N ,c 所 添 加 的 金属 含 金 或 氧 化 物 粉 末 ,而 碳 化 物 中的 C 则来 自基
模具表面喷丸强化

模具表面喷丸强化随着现代工业技术的发展,对于模具使用性能提出了更高的要求。
努力缩短模具的生产周期提高模具的质量,延长模具寿命,直接或间接带来的社会效益和经济效益是难以估量的。
材料和热处理是影响模具质量、性能和使用寿命最重要的内在因素。
60%模具的早期失效,是由材料和热处理的因素造成的。
为了提高模的强度及模具的耐磨性,充分挖掘模具材料的性能潜力,延长模具服役寿命,采取了许多有效的措施,从省能源、省资源、充分发挥材料的性能潜力,获得特殊性能和最大技术经济效益出发,发展和应用表面强化工艺技术是提高模具使用性能和寿命的极重要的发展方向,喷丸强化就是其中的一项经济、简便而有效的模具表面处理工艺方法,值得大力推广。
喷丸强化是借助于硬丸粒,高速、连续锤击金属表面,使其产生强烈的冷作硬化。
通过喷丸可以明显改变金属表面的应力状态、显微硬度、表层的微观形貌和相成分,从而提高模具的疲劳强度、抗冲击磨损及抗应力腐蚀性能。
喷丸还可改变模具的表面粗糙度,并有效地去除电火花加工而产生的表面变质层。
喷丸强化方法简单易行,节约能源,适用于落料模、冷作模、冷镦模和热锻模等以疲劳失效形式为主的模具,如锻模服役时,要经受弯曲和热膨胀,常发生因局部屈服而导致显微裂纹,喷丸处理产生压应力能推迟显微裂纹的形成,从而延迟模具龟裂发生,模具经喷丸强化后使用寿命情况如表1所示。
喷丸强化原理喷丸过程就是大量弹丸喷射到零件表面上的过程,而弹丸喷射到零件表面上有如无数小锤对表面锤击,因此,金属零件表面产生极为强烈的塑性形变,使零件表面产生一定厚度的冷作硬化层,称为表面强化层,此强化层会显著地提高零件在高温和高湿工作下的疲劳强度。
零件表面形成的强化层之所以会改善其疲劳性能,其原因是在此层内有着完全不同于基体(即零件心部)的应力状态及组织结构,一般地说零件疲劳强度的提高与表面强化层内以下三个因素有关:(1)表面层的宏观残余应力;(2)表面层的微观应力;(3)表面层的微细嵌镶组织。
TD处理概述

TD处理TD模具表面超硬化处理技术,采用金属碳化物扩散覆层TD(Thermal Diffusion Carbide Coating Process)原理,是在一定的处理温度下将工件至于硼砂熔盐及其特种介质中,通过特种熔盐中的金属原子和工件中的碳、氮原子产生化学反应,扩散在工件表面而形成一层几微米至二十余微米的钒、铌、铬、钛的等金属碳化层。
概述原理TD模具表面超硬化处理技术经研究不断的持续改进,在解决冷作模具磨损失效的应用其技术、品质、成本和响应速度等方面有很大的优势。
技术特点热扩散法碳化物覆层处理(Thermal Diffusion Carbide Coating Process),简称TD覆层处理,是一种通过高温扩散作用于工件表面形成一层数微米至数十微米的金属碳化物覆层,其结构如上图所示。
该覆层具有极高的硬度,HV可达3200左右,且与母体材料冶金结合。
实践证明,这种覆层具有极高的耐磨,抗咬合,耐蚀等性能,可提高工件寿命数倍至数十倍,具有极高的使用价值。
主要效益1.大幅度提高工模具或工件的使用寿命,节省生产成本或运行成本。
2.大幅度改善产品外观,提高产品尺寸的均一性,提升产品质量。
3.大幅度节省维修时间和劳动强度,并减少因维修停机所带来的损失。
4.摩擦系数降低,抗咬合性能大幅度提高,无须润滑或减少润滑或无须采用高级润滑产品。
技术比较通过在工件表面形成一层高硬度的耐磨材料是提高工件耐磨,抗咬合,耐蚀等性能,从而提高其使用寿命的有效而又经济的方法,TD覆层处理技术以碳化钒覆层为例,其表面硬度可达HV3200左右,较传统的表面处理方法如渗碳HV~900;渗氮HV~1200;镀硬铬HV~1000;甚至渗硼HV 1200~1800等表面处理的硬度高得多,因此具有远优于这些表面处理方法的耐磨性能。
物理气相沉积(PVD),物理化学气相沉积(PCVD),化学气相沉积(CVD),TD覆层处理是现代的几种表面超硬化处理方法,其中PVD,PCVD 工艺温度低,变形较小,所形成的氮化钛覆层HV可达2000左右,但由于这两种方法形成的氮化钛涂层与母体材料的结合力较差,实际应用中,容易出现涂层的剥落,在使用条件较为苛刻的场合,如引伸类模具;根本就无法达到满意的使用效果,甚至根本无效果.因此PVD,PCVD往往难以发挥超硬化合物覆层的性能优势.高温CVD法形成的碳化钛覆层与TD覆层处理获得的表面覆层硬度接近,并且高温CVD法和TD覆层处理的覆层与基体都是冶金结合,具有PVD和PCVD无法比拟的膜基结合力,因此是目前最有效的表面超硬化方法.相比而言,CVD覆层的运行成本较高,后续处理也比较麻烦,其应用主要集中在硬质合金工件上.而TD覆层处理由于后续处理比较方便,因此既可以用于钢铁材料,也可以用于硬质合金.此外,TD覆层处理技术在无须褪去原先覆层的情况下,可以进行多次重复处理.应用范围TD覆层处理可广泛应用于由于各类磨损所引起的模具与工件或工件与工件之间的拉伤或磨损超差的问题.其中因咬合或粘结而引起的拉伤或拉毛问题,TD覆层处理是目前世界上最好的解决方法之一.因磨损而引起的工件尺寸超差等问题,通过TD覆层处理后,提高使用寿命上十倍是很正常的.所处理工件的材料,含碳量大于0.3%的各类钢铁材料,硬质合金等.一般推荐各类中高合金工模具钢.TD处理的特点随着社会(汽车行业)的发展,人们对各个方面都有更高的要求。
模具表面强化技术及其应用

高密度 能量 ( 能束 ) 面强 化是近 年来 发展 起 来 高 表
,
属表 面施 以极 高能 量使 之发 生物理 、化 学 变
化, 达到金 属表 面 强化 的一种 新 技术 , 利用高 密度 能 量 进 行热 处理 , 具有 节 约能 源 , 防止 环 境 污染 、 提高 生 产 率及产 品质量 等优 点 , 光 热处 理是最 重要 的一 种 , 激 其
有 :红 宝石 激 光器 、钕玻 璃 激光器 和 钇铝石 榴激 光 器 ( A 目f Y G) 水激光 器效 率一 般 不超 过 3 , 用 于穿 孔 、 % 可
1. 纵 台 l 控装 置 1_ 记 录 装 置 1. 统 打字 机 4操 5数 6磁带 7系
C 光器 是在 谐 振腔 内通过 放 电 ,激 发 激 光器 O激
一
见图 l。 2
般是 连续 波 , 也 可 以脉 冲式工 作 . 但 由于 C 光器 O激
一
能够长 时间稳定 连续 振荡 , 故具 有 以下 优点 :
() 1电一光 转 换效 率 高 , 一般 约为 1%~ 0 , 0 2% 而其
他类 型 如红 宝石 激光 器仅 为 2 %
中 的 C N 、 e ( 积 比约为 11 j利 用电 激发 O 、 H 气 体 :56 ,
现象获得 激光 。C 光器按 气 流循 环方 向 、 电方 向 O激 放
维普资讯
《 具制 造》 2 0 .o 模 0 2N . 3总第 8 期
制 、 作 安全 、 格 便宜 。 操 价
6 . 檄光射束
1 0气体 喷嘴
7弯曲反射镜 .
1.- 工作 台 1 Y x
8聚光系统
1. 处 理 工 件 2 被
模具的热处理及表面强化技术

第9章模具的热处理及表面强化技术模具热处理及表面强化是模具制造中的关键工艺之一,直接关系到模具的制造精度、力学性能(如强度等)、使用寿命以及制造成本,是保证模具质量和使用寿命的重要环节。
模具在实际生产使用中表明,在模具的全部失效中,由于热处理不当所引起的失效居于首位。
在模具设计制造过程中,若能正确选用钢材,选择合理的热处理及表面强化技术工艺,对充分发挥材料的潜在性能、减少能耗、降低成本、提高模具的质量和使用寿命都将起到重大的作用。
当前模具热处理技术发展较快的领域是真空热处理技术和模具的表面强化技术。
9.1模具的热处理9.1.l模具钢的热处理模具钢的热处理工艺是指模具钢在加热、冷却过程中,根据组织转变规律制定的具体热处理加热、保温和冷却的工艺参数。
根据加热、冷却方式及获得组织和性能的不同,热处理工艺可分为常规热处理、表面热处理(表面淬火和化学热处理等)等。
根据热处理在零件生产工艺流程中的位置和作用,热处理又可分为预备热处理和最终热处理。
模具钢的常规热处理主要包括退火、正火、淬火和回火。
由于真空热处理技术具有防止加热氧化、不脱碳、真空除气、变形小及硬度均匀等特点,近年来得到广泛的推广应用。
1.退火工艺退火一般是指将模具钢加热到临界温度以上,保温一定时间,然后使其缓冷至室温,获得接近于平衡状态组织的热处理工艺。
其组织为铁素体基体上分布着碳化物。
目的是消除钢中的应力,降低模具材料的硬度,使材料成分均匀,改善组织,为后续工序(机加工、冷加工成形、最终热处理等)做准备。
退火工艺根据加热温度不同可分为:1)完全退火将模具钢加热到临界温度A c3以上20~30℃,保温足够的时间,使其组织完全奥氏体化,然后缓慢冷却,以获得接近平衡状态组织的热处理工艺。
其目的是为了降低硬度、均匀组织、消除内应力和热加工缺陷、改善切削加工性能和冷塑性变形性能,为后续热处理或冷加工做准备。
2)不完全退火将钢加热到A c1~A c3(亚共析钢)或A c1~A ccm(过共析钢)之间,保温一定时间后缓慢冷却,以获得接近于平衡组织的热处理工艺。
模具钢的热处理与表面处理技术

模具钢的热处理与表面处理技术一、预热处理预热处理是模具钢热处理的第一步,其主要目的是消除模具钢在锻造、铸造过程中产生的内应力,防止在后续的热处理过程中产生变形和裂纹。
预热处理通常采用高温回火或等温退火的方法进行。
二、锻造锻造是模具钢热处理的另一个重要步骤,其主要目的是通过改变模具钢的显微组织结构,提高其力学性能和抗冲击能力。
锻造过程中,模具钢的加热温度、变形程度和冷却速度都会对其最终的组织结构和性能产生重要影响。
三、退火退火是模具钢热处理中常用的一种方法,其主要目的是通过将模具钢加热到一定温度,保温一定时间,然后缓慢冷却,以获得理想的显微组织和机械性能。
退火过程中的加热温度和冷却速度对模具钢的性能有着重要影响。
四、淬火淬火是模具钢热处理中非常关键的一步,其主要目的是通过快速冷却,使模具钢的表面和心部同时达到临界点以下,获得马氏体组织,从而提高模具钢的硬度、强度和耐磨性。
淬火过程中的冷却速度对模具钢的显微组织和性能有着重要影响。
五、回火回火是模具钢热处理的另一个重要步骤,其主要目的是通过将模具钢加热到一定温度,保温一定时间,然后缓慢冷却,以调整模具钢的显微组织结构,提高其韧性和抗冲击能力。
回火过程中的加热温度和保温时间对模具钢的性能有着重要影响。
六、深冷处理深冷处理是模具钢热处理的一种方法,其主要目的是通过将模具钢冷却到零下70℃以下,提高模具钢的硬度、强度和耐磨性。
深冷处理过程中的冷却速度和冷却时间对模具钢的性能有着重要影响。
七、表面强化处理表面强化处理是模具钢热处理的一种方法,其主要目的是通过物理或化学手段,提高模具钢表面的硬度和抗磨性。
表面强化处理的方法有很多种,包括渗碳、渗氮、高频淬火等。
八、渗氮渗氮是模具钢表面强化处理的一种方法,其主要目的是通过将模具钢表面渗入氮元素,提高其表面的硬度和抗磨性。
渗氮处理后的模具钢具有较高的耐腐蚀性和耐磨性。
九、渗碳渗碳是模具钢表面强化处理的一种方法,其主要目的是通过将模具钢表面渗入碳元素,提高其表面的硬度和抗磨性。
塑料模具的表面强化技术研究

塑料模具表面强化技术的方法 , 手段和效 果以及其优缺 点。
二、 塑 料 模 具 的简 介 及 其 分 类
料杂质 少、 组织微细均一 、 无纤维方 向性 、 抛光时不应 出现麻 点 或桔皮状缺 陷。 ( 4 ) 良好的热 稳定性 。 塑料注射模的零件形状往
淬 火后难 以加工 , 因 此 应 尽 量 选 用 具 有 良好 的 热 1 . 塑料 模 具 的简 介 。塑 料模 具 , 是 塑料 加 工 工业 中和 塑料 往 比较 复 杂 , 当模 具 成 型 加 工 经 热 处 理 后 因 线 膨 胀 系 数 小 , 热 处 成型机配套 , 赋予塑料制 品以完整 构型和精确 尺寸的工具 。由 稳 定 性 的 ,
2 ) 优 良的切削加工性 。大多数塑料成型模 塑料模 具的表面强化技术是提高塑料模具使用寿命 , 提 升模具 于提高其耐磨性 。(
除E MD 加工 外 还 需 进 行 一 定 的切 削 加 工 和 钳 工 修 配 。 为延 的 使 用 性 能 的 一 项 重 要 的技 术 和 途 径 , 是 国 内外 模 具 工 业 和 技 具 ,
要求 型腔表面 的粗糙度值小 。例如, 注塑模型腔表面 粗糙 具的使用性能和 使用寿命 。这种表 面强化技术在发达 国家 的模 制 品,
具 制 造 中 已经 得 到 了广 泛 的应 用 , 取 得 了非 常 显 著 的成 果 。本 度 值 要 求 小 于 R a 0 . 1 ~O . 2 5的水 平 , 光学面 则要求 R a < 0 . 0 1 i r m, 减 小 表 面 粗 糙度 值 。 为 此 选 用 的 钢 材 要 求 材 文 从 塑 料 模 具 的工 作 条 件 和 失 效 方式 等 进 行 分 析 , 介 绍 了 一 些 型腔 须进 行抛 光 ,
模具表面处理种类和作用

模具是作为制造业的重要工艺装备,它的使用性能,特别是使用寿命反映了一个国家的工业水平,并直接影响到产品的更新换代和在国际市场上的竞争能力。
因此,各国都非常重视模具工业的发展和模具寿命的提高工作。
目前,我国模具的寿命还不高,模具消耗量很大,因此,提高我国的模具寿命是一个十分迫切的任务。
模具热处理对使用寿命影响很大。
我们经常接触到的模具损坏多半是热处理不当而引起。
据统计,模具由于热处理不当,而造成模具失效的占总失效率的50%以上,所以国外模具的热处理,愈来愈多地使用真空炉、半真空炉和无氧化保护气氛炉。
模具热处理工艺包括基体强韧化和表面强化处理。
基体强韧化在于提高基体的强度和韧性,减少断裂和变形,故它的常规热处理必须严格按工艺进行。
表面强化的主要目的是提高模具表面的耐磨性、耐蚀性和润滑性能。
表面强化处理方法很多,主要有渗碳、渗氮、渗硫、渗硼、氮碳共渗、渗金属等。
采用不同的表面强化处理工艺,可使模具使用寿命提高几倍甚至于几十倍,近几年又出现了一些新的表面强化工艺,本文着重四个方面介绍,供同行参考。
一、低温化学热处理1.离子渗氮为了提高模具的抗蚀性、耐磨性、抗热疲劳和防粘附性能,可采用离子渗氮。
离子渗氮的突出优点是显著地缩短了渗氮时间,可通过不同气体组份调节控制渗层组织,降低了渗氮层的表面脆性,变形小,渗层硬度分布曲线较平稳,不易产生剥落和热疲劳。
可渗的基体材料比气体渗氮广,无毒,不会爆炸,生产安全,但对形状复杂模具,难以获得均匀的加热和均匀的渗层,且渗层较浅,过渡层较陡,温度测定及温度均匀性仍有待于解决。
离子渗氮温度以450~520℃为宜,经处理6~9h后,渗氮层深约0.2~0.3m m。
温度过低,渗层太薄;温度过高,则表层易出现疏松层,降低抗粘模能力。
离子渗氮其渗层厚度以0.2~0.3m m为宜。
磨损后的离子渗氮模具,经修复和再次离子渗氮后,可重新投入使用,从而可大大地提高模具的总使用寿命。
2.氮碳共渗氮碳共渗工艺温度较低(560~570℃),变形量小,经处理的模具钢表面硬度高达900~1000H V,耐磨性好,耐蚀性强,有较高的高温硬度,可用于压铸模、冷镦模、冷挤模、热挤模、高速锻模及塑料模,分别可提高使用寿命1~9倍。
模具表面强化技术

本 工艺处 理模 具 :下料 一全 部 加工到 位 ( 无须 力 ,使模具容易磨损 ;另一方面 ,不锈 钢板料 易与模 热处理 )一本工艺处理 ( 基体硬 化与表面处理 一次完
具表面形 成粘结 ( 咬合 ) ,使焊 管及 模具 表面 形成拉 成 ) 。一磨 内孔 一成 品 伤 。因此 ,好的不锈钢成型模具必须具备极 高的耐磨 由 工艺流 程可 看 出 ,采 用本 工艺 可缩 短模具 的
1 技术简介 ,
扩散法金 属碳化物覆 层技术是将 工件置于特 挥 超硬膜 层 的性能优 势 ,此外 ,该技 术不存 在绕
种介 质 中 ,经 扩散作 用于 工件表面形 成一层 数微 镀 性 问题 ,后 续基体 硬化 处理 方便 ,并可 多次重 米至 数十微米 的金 属碳化物层 。该碳 化物 层具有 复处理 ,使 该技术 的适 用性 更为广 泛 。 极高的硬 度 ,H V可达 10 ~3 0 ( 0 0 0 由碳化物种类 6
4适 用范 围 .
.
1 8.第0 数控机床市场 1 6期
维普资讯
超 硬化 处 理技 术 已成 功应 用
于不锈钢焊管成 型模具上。 经 该技 术 处理 的模 具 在其 表 面形成硬 度高达 H 3 0 左右 V 00
的金 属 碳 化物 层 ,该 碳化 物
维普资讯
技术 前 沿
模 具表面强化 技木
● 文 / 层技术 化物覆层 ,与基体形成冶金结合 .具有 P D、P V V CD
无法 比拟 的膜基 结合 力 ,因此该 技术 真正能 够发
由扩 散法金 属碳化 物覆层 技术形 成的金 属碳
层致密 ,与基体结合紧密 ,不 影 响工件 的表 面光 洁 度 ,具 有极高 的耐 磨 ,抗咬合 性能 , 可从 根本 上 解决 焊 管 的拉毛
- 1、下载文档前请自行甄别文档内容的完整性,平台不提供额外的编辑、内容补充、找答案等附加服务。
- 2、"仅部分预览"的文档,不可在线预览部分如存在完整性等问题,可反馈申请退款(可完整预览的文档不适用该条件!)。
- 3、如文档侵犯您的权益,请联系客服反馈,我们会尽快为您处理(人工客服工作时间:9:00-18:30)。
机电设备维修课程技术论文论文题目:工件表面强化技术系别机电工程系专业年级学生姓名学号日期2015年6月目录摘要....................................................................................................低温化学热处理1.离子渗氮2.氮碳共渗3.碳氮硼三元共渗二、气相沉积1.物理气相沉积2.化学气相沉积3.物理化学气相沉积三、激光热处理1.激光淬火2.激光熔凝硬化3.激光合金化四、稀土元素表面强化1.稀土碳共渗2.稀土碳氮共渗3.稀土硼共渗4.稀土硼铝共渗摘要:模具热处理不当是造成模具失效的重要原因之一,本文研究了目前模具表面强化处理的一些新工艺,分析了低温化学热处理、气相沉积、激光热处理以及稀土元素表面强化等新工艺的模具表面强化特点,为使用表面强化技术提高模具使用寿命提供参考。
关键词:模具;表面强化处理;工艺;寿命模具是各工业部门的重要工艺装备,它的使用性能,特别是使用寿命反映了一个国家的工业水平,并直接影响到产品的更新换代和在国际市场上的竞争能力。
因此,各国都非常重视模具工业的发展和模具寿命的提高工作。
目前,我国模具的寿命还不高,模具消耗量很大,因此,提高我国的模具寿命是一个十分迫切的任务。
模具热处理对使用寿命影响很大。
我们经常接触到的模具损坏多半是热处理不当而引起。
据统计,模具由于热处理不当,而造成模具失效的占总失效率的50%以上,所以国外模具的热处理,愈来愈多地使用真空炉、半真空炉和无氧化保护气氛炉。
模具热处理工艺包括基体强韧化和表面强化处理。
基体强韧化在于提高基体的强度和韧性,减少断裂和变形,故它的常规热处理必须严格按工艺进行。
表面强化的主要目的是提高模具表面的耐磨性、耐蚀性和润滑性能。
表面强化处理方法很多,主要有渗碳、渗氮、渗硫、渗硼、氮碳共渗、渗金属等。
采用不同的表面强化处理工艺,可使模具使用寿命提高几倍甚至于几十倍,近几年又出现了一些新的表面强化工艺,本文着重四个方面叙述如下,一、低温化学热处理1.离子渗氮为了提高模具的抗蚀性、耐磨性、抗热疲劳和防粘附性能,可采用离子渗氮。
离子渗氮的突出优点是显著地缩短了渗氮时间,可通过不同气体组份调节控制渗层组织,降低了渗氮层的表面脆性,变形小,渗层硬度分布曲线较平稳,不易产生剥落和热疲劳。
可渗的基体材料比气体渗氮广,无毒,不会爆炸,生产安全,但对形状复杂模具,难以获得均匀的加热和均匀的渗层,且渗层较浅,过渡层较陡,温度测定及温度均匀性仍有待于解决。
离子渗氮温度以450~520℃为宜,经处理6~9h后,渗氮层深约0.2~0.3mm。
温度过低,渗层太薄;温度过高,则表层易出现疏松层,降低抗粘模能力。
离子渗氮其渗层厚度以0.2~0.3mm为宜。
磨损后的离子渗氮模具,经修复和再次离子渗氮后,可重新投入使用,从而可大大地提高模具的总使用寿命。
2.氮碳共渗氮碳共渗工艺温度较低(560~570℃),变形量小,经处理的模具钢表面硬度高达900~1000HV,耐磨性好,耐蚀性强,有较高的高温硬度,可用于压铸模、冷镦模、冷挤模、热挤模、高速锻模及塑料模,分别可提高使用寿命1~9倍。
但气体氮碳共渗后常发生变形,膨胀量占化合物厚度的25%左右,不宜用于精密模具。
处理前必经去应力退火和消除残余应力。
例如:Cr12MoV钢制钢板弹簧孔冲孔凹模,经气体氮碳共渗和盐浴渗钒处理后,可使模具寿命提高3倍。
又如:60Si2钢制冷镦螺钉冲头,采用预先渗氮、短时碳氮共渗、直接淬油、低温淬火及较高温度回火处理工艺,可改善心部韧性,提高冷镦冲头寿命2倍以上。
碳氮共渗工艺如图1所示。
3.碳氮硼三元共渗三元共渗可在渗氮炉中进行,渗剂为含硼有机渗剂和氨,其比例为1∶7,共渗温度为600℃,共渗时间4h,共渗层化合物层厚3~4μm,扩散层深度为0.23mm,表面硬度为HV011050。
经共渗处理后模具的寿命显著提高。
例如:3Cr2W8V钢热挤压成形模,按图2所示工艺处理后,再经离子碳、氮、硼三元共渗处理,可使模具的使用寿命提高4倍以上。
图2模具热处理工艺曲线二、气相沉积气相沉积技术是一种获得薄膜(膜厚0.1~5μm)的技术。
即在真空中产生待沉积的材料蒸汽,该蒸汽冷凝于基体上形成所需的膜。
该项技术包括物理气相沉积(PVD)、化学气相沉积(CVD)、物理化学气相沉积(PCVD)。
它是在钢、镍、钴基等合金及硬质合金表面建立碳化物等覆盖层的现代方法,覆盖层有碳化物、氮化物、硼化物和复合型化合物等。
1.物理气相沉积物理气相沉积技术,由于处理温度低,热畸变小,无公害,容易获得超硬层,涂层均匀等特点,应用于精密模具表面强化处理,显示出良好的应用效果。
采用PVD处理获得的TiN层可保证将塑料模的使用寿命提高3~9倍,金属压力加工工具寿命提高3~59倍。
螺钉头部凸模采用TiN层寿命不长,易发生脱落现象。
2.化学气相沉积化学气相沉积技术,沉积物由引入高温沉积区的气体离解所产生。
CVD处理的模具形状不受任何限制。
CVD可以在含碳量大于0.8%的工具钢、渗碳钢、高速钢、轴承钢、铸铁以及硬质合金等表面上进行。
气相沉积TiC、TiN能应用于挤压模、落料模和弯曲模,也适用于粉末成型模和塑料模等。
在金属模具上涂覆TiC、TiN覆层的工艺,其覆层硬度高达3000HV,且耐磨性好、抗摩擦性能提高、冲模的使用寿命可提高1~4倍。
3.物理化学气相沉积由于CVD处理温度较高,气氛中含氯化氢多,如处理不当,易污染大气。
为克服上述缺点,用氩气作载体,发展中温CVD法,处理温度750~850℃即可。
此法在耐磨性、耐蚀性方面不亚于高温CVD法。
PCVD兼具CVD与PVD技术的特点,但要求精确监控,保证工艺参数稳定。
三、激光热处理近几年来,激光热处理技术在汽车工业、工模具工业中得到了广泛的应用。
它改善金属材料的耐蚀性,特别是在工模具工业中,经激光热处理的工模具的组织性能比常规热处理有很大的改善。
1.激光淬火由于激光处理时的冷速极快,因而可使奥氏体晶粒内部形成的亚结构在冷却时来不及回复及再结晶,从而可获得超细的隐针马氏体结构,可显著提高强韧性,延长模具使用寿命。
现用于激光淬火的模具材料有CrWMn、Cr12MoV、9CrSi、T10A、W6Mo5Cr4V2、W18Cr4V、GCr15等。
这些钢种经激光淬火后,其组织性能均得到很大的改善。
例如,GCr15冲孔模,把其硬度由HRC58~62降至HRC45~50,并用激光进行强化处理,白亮层硬度为HV849,基体硬度为HV490,硬化层深度为0.37mm,模具使用寿命提高2倍以上。
又如,CrWMn钢加热时易在奥氏体晶界上形成网状的二次碳化物,显著增加脆性,降低冲击韧性,耐磨性也不能满足要求。
采用激光淬火可获细马氏体和弥散分布的碳化物颗粒,消除了网状。
在淬火回火态下激光淬火可获得最大硬化层深度及最高硬度HV1017.2。
2.激光熔凝硬化用高能激光照射工件表面,被照射区将以极高的速率熔化,一旦光源消除,熔区依靠金属基体自身冷却,冷却速度极快。
5CrNiMo渗硼层在激光熔凝处理后,与原始渗硼层相比,强化层深度增加,强化层硬度趋于平缓,渗硼层的脆性得到改善。
3.激光合金化激光表面合金化的合金元素为W、Ti、Ni、Cr等,以Ni、Cr为合金元素时,合金化层组织为以奥氏体为基体的胞状树枝晶,以Ti作为激光表面合金化元素时,具有组织变质作用,能使合金化层的网状碳化物变为继续网状或离散分布的碳化物。
例如,T10A以Cr为激光表面合金化元素时,合金化层硬度可达HV900~1000。
又如,CrWMn复合粉末激光合金化,可获得综合技术指标优良的合金层,经测定,体积磨损量为淬火CrWMn的1/10,其使用寿命提高14倍。
四、稀土元素表面强化在模具表面强化中,稀土元素的加入对改善钢的表层组织结构、物理、化学及机械性能都有极大影响。
稀土元素具有提高渗速(渗速可提高25%~30%,处理时间可缩短1/3以上),强化表面(稀土元素具有微合金化作用,能改善表层组织结构,强化模具表面),净化表面(稀土元素与钢中P、S、As、Sn、Sb、Bi、Pb等低熔点有害杂质发生作用,形成高熔点化合物,同时抑制这些杂质元素在晶界上的偏聚,降低渗层的脆性)等多种功能。
1.稀土碳共渗RE-C共渗可使渗碳温度由920~930℃降低至860~880℃,减少模具变形及防止奥氏体晶粒长大;渗速可提高25~30%(渗碳时间缩短1~2h);改善渗层脆性,使冲击断口裂纹形成能量和裂纹扩展能量提高约30%。
2.稀土碳氮共渗RE-C-N共渗可提高渗速25%~32%,提高渗层显微硬度及有效硬化层深度;使模具的耐磨性及疲劳极限分别提高1倍及12%以上;模具耐蚀性提高15%以上。
RE-C-N共渗处理用于5CrMnMo钢制热锻模,其寿命提高1倍以上。
3.稀土硼共渗RE-B共渗的耐磨性较单一渗硼提高1.5~2倍,与常规淬火态相比提高3~4倍,而韧性则较单一渗硼提高6~7倍;可使渗硼温度降低100℃~150℃,处理时间缩短一半左右。
采用RE-B共渗可使Cr12钢制拉深模寿命提高5~10倍,冲模寿命提高几倍至数十倍。
4.稀土硼铝共渗RE-B-AI共渗所得共渗层,具有渗层较薄、硬度很高的特点,铝铁硼化合物具有较高的热硬性和抗高温氧化能力。
H13钢稀土硼铝共渗渗层致密,硬度高(HV011900~2000),相组成为d值发生变化(偏离标准值)的FeB和Fe2B相。
经稀土硼铝共渗后,铝挤压模使用寿命提高2~3倍,铝材表面质量提高1~2级。
模具表面强化处理的方法还有很多,我们要结合各种模具的工作条件及其使用的经济性等因素综合考虑。
因为通过扩散、浸渗、涂覆、溅射、硬化等方法,改变表面层的成份和组织,就可使零件具有内部韧、表面硬、耐磨、耐热、耐蚀、抗疲劳、抗粘结的优异性能,可几倍乃至几十倍地提高模具使用寿命。