压铸产品质量控制计划
压铸铝合金控制计划

容量频率ADC12化学成分★1材料的牌号ADC12化学元素含量:Si:9.6~12,Fe≤1.0,Cu:1.5~3.5,Mn≤0.5,Zn≤1.0,Mg≤0.3,Ni≤0.5,Sn≤0.2光谱分析仪1个样块每批次隔离退货力学性能抗拉强度Mpa≥185,屈服强度Mpa≥105,布氏硬度HB≥72,延伸率%≥1万能试验机布氏硬度计2个样件每批次隔离退货成分按A380材料成分标准目测100%每批次隔离退货ROHS ★2铅(Pb)≤0.4%(4000ppm)、汞(Hg)≤0.1%(1000ppm)、六价铬(Cr6+)≤0.1%(1000ppm)、多溴联苯(PBB)≤0.1%(1000ppm)、多溴二苯醚(PBDE)≤0.1%(1000ppm)、镉(cd)为0.01%(100ppm)供应商实验室一次每年ROHS报告隔离退货ROHS ★2铅(Pb)≤0.1%(1000ppm)、汞(Hg)≤0.1%(1000ppm)、六价铬(Cr6+)≤0.1%(1000ppm)、多溴联苯(PBB)≤0.1%(1000ppm)、多溴二苯醚(PBDE)≤0.1%(1000ppm)、镉(cd)为0.01%(100ppm)供应商实验室一次每年ROHS报告隔离退货耐盐雾性耐中性盐雾144H 盐雾试验机1个样板每批塑粉《进料检验指导书》隔离/上报/退货色差ΔE≤1.0色差仪2个样板每批塑粉《进料检验指导书》隔离/上报/退货膜厚60um-160um 膜厚仪2个样板每批塑粉《进料检验指导书》隔离/上报/退货外观不能有残缺,不能有毛边目视隔离/上报/退货尺寸按配件图纸检验+适配数显卡尺隔离/上报/退货外观无毛刺目视隔离/上报/退货尺寸按配件图纸检验数显卡尺隔离/上报/退货储存先进先出存放、原材料牌号与指定区域相符仓库管理办法目测100%每批次隔离调整铝水温度铝液温度控制在670±30℃测温棒温度控制,目视检查显示器●1次■1次●2H ■2H 自检《作业指导书》巡检《检验指导书》压铸巡检检验记录表调整新旧料配比新料与旧料配比7:3称重方式将铝锭和回料按7:3放入熔化炉●100%●每班自检《作业指导书》新旧料配比日报表调整除渣每炉铝液添加0.5±0.05KG除渣剂进行除渣2满勺,按时除渣。
压铸车间5s现场规划【经验】

现场管理是一个压铸厂的企业形象、管理水平、产品质量控制和精神面貌的综合反映,是衡量企业综合素质及管理水平高低的重要标志。
搞好压铸生产现场管理,有利于增强压铸企业竞争力, 消除“跑、冒、漏、滴”和“脏、乱、差”状况,提高产品质量和员工素质,保证安全生产,对提高压铸企业经济效益,增强压铸企业实力具有十分重要的意义。
压铸生产现场管理方法(经典)我是目录一、优秀现场管理的标准和要求二、现场管理的基本方法三、生产现场的质量控制四、现场的组织结构设计原则及职能五、生产现场员工的管理六、生产计划的制定要求七、生产成本的控制八、现场管理制度一、优秀现场管理的标准和要求1、什么是现场管理:现场管理就是指用科学的管理制度、标准和方法对生产现场各生产要素,包括人(工人和管理人员)、机(设备、工具、工位器具)、料(原材料)、法(加工、检测方法)、环(环境)、信(信息)等进行合理有效的计划、组织、协调、控制和检测,使其处于良好的结合状态,达到优质、高效、低耗、均衡、安全、文明生产的目的。
2、优秀生产现场管理的标准1)定员合理,技能匹配;2)材料工具,放置有序;3)场地规划,标注清析;4)工作流程,有条不紊;5)规章制度,落实严格;6)现场环境,卫生清洁;7)设备完好,运转正常;8)安全有序,物流顺畅;9)定量保质,调控均衡;10)登记统计,应记无漏。
3、现场管理六要素(5M1E分析法)现场管理的六个要素即:人、机、料、法、环、测。
----也称为5M1E分析法。
1) 人(Man):操作者对质量的认识、技术、身体状况等;2) 机器(Machine):设备、测量仪器的精度和维护保养状况等;3) 材料(Material):材料能否达到要求的性能等;4) 方法(Method):生产工艺、设备选择、操作规程等;5) 测量(Measurement):测量时采取的方法是否标准、正确;6) 环境(Environment):工作现场的技术要求和清洁条件等;由于这五个因素的英文名称的第一个字母是M和E,简称为5M1E。
压铸品质控制计划
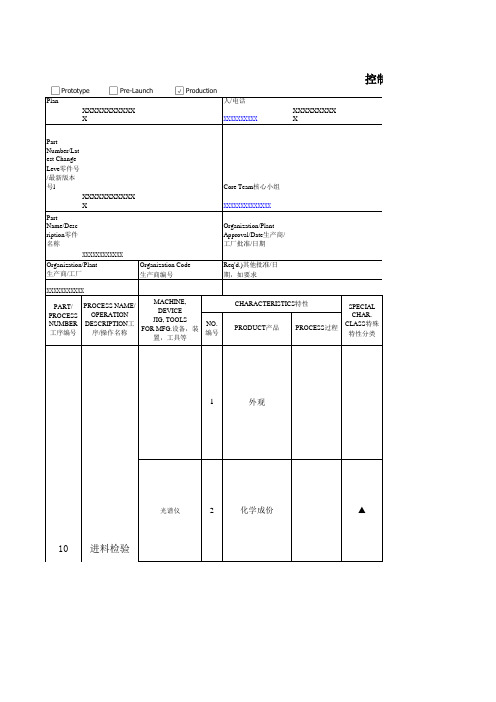
XXXXXXXXXXX
PART/ PROCESS NUMBER 工序编号
PROCESS NAME/ OPERATION
DESCRIPTION工 序/操作名称
MACHINE, DEVICE
JIG, TOOLS FOR MFG.设备,装
置,工具等
NO. 编号
CHARACTERISTICS特性 PRODUCT产品 PROCESS过程
1次
批 光谱记录
通知采购
取样:任取1块合金锭,锯
10-30mm的锯缝,合金组织 应致密、无氧化皮、无明显
目测visual
偏析,熔渣等及夹杂物。
1次
批 检验记录
通知采购
违禁物质特性,符合Q/CAM266
第三方
1次 每年 第三方报告
通知采购
按仓储操作指导书:产品包装无破
损及材料标识应清晰,定置摆放、
无混料、所喷颜色与
Part Name/Desc ription零件 名称
XXXXXXXXXXXX
Organization/Plant 生产商/工厂
Organization Code 生产商编号
Core Team核心小组
XXXXXXXXXXXXXX
Organization/Plant Approval/Date生产商/ 工厂批准/日期 Other Approval/Date (If Req'd.)其他批准/日 期,如要求
ContrPorlototype
Pre-Launch
Plan
XXXXXXXXXXX
X
Production
Key Contact/Phone联络
人/电话
XXXXXXXXXX
压铸控制计划范例

压铸控制计划范例【背景】压铸是一种常用于生产大型、复杂零件的加工工艺。
该工艺使用高压将熔化金属注入压铸模具中,然后通过冷却和凝固来形成所需的零件。
为了确保产品质量,减少缺陷和增加生产效率,需要制定一份压铸控制计划。
【目标】该压铸控制计划的目标是确保生产的压铸零件符合规格要求,并提高产品质量和生产效率。
【内容】1.质量控制-制定合格品标准:明确压铸零件的尺寸、表面光洁度、材料硬度等质量要求。
-制定首件检验标准:确保生产出的第一件产品满足质量标准。
-制定过程控制标准:对压铸工艺中的各个步骤、参数进行监控和控制,确保产品质量稳定。
-制定末件检验标准:对生产出的每个压铸零件进行全面检验,确保产品质量符合要求。
2.设备维护-制定设备维护计划:定期对压铸设备进行保养和维护,确保设备正常运行,减少故障发生率。
-制定备用设备准备计划:在设备故障时,及时准备备用设备,避免生产中断。
-建立设备维修记录:记录设备维护和维修情况,为以后的维护提供参考。
3.员工培训-制定员工培训计划:定期培训压铸操作人员,提高其操作技能和质量意识。
-建设员工技能档案:记录员工培训情况和技能水平,为岗位调整和晋升提供依据。
-开展质量安全培训:加强员工的质量和安全意识,确保操作规范和安全生产。
4.数据分析-收集生产数据:定期收集压铸生产的相关数据,如生产数量、不良品数量等。
-进行数据分析:通过对数据的统计和分析,找出生产中的问题和改进措施。
-制定改进措施:根据数据分析结果,制定相应的改进措施,优化生产流程和工艺。
5.过程改进-建立问题反馈机制:鼓励员工提出问题和改进意见,并建立相应的反馈机制。
-进行改进措施评估:对提出的改进措施进行评估和实施,确保改进效果。
-持续改进:不断进行过程改进,提高压铸生产质量和效率。
【执行】该压铸控制计划由相关部门和人员执行,包括质量部、生产部、设备维护人员和培训人员。
各部门和人员要按照计划的要求进行工作,并定期进行评估和改进。
压铸生产年度工作计划
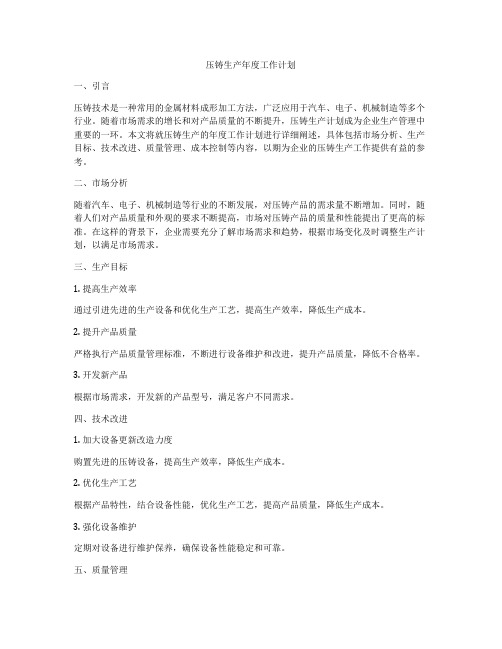
压铸生产年度工作计划一、引言压铸技术是一种常用的金属材料成形加工方法,广泛应用于汽车、电子、机械制造等多个行业。
随着市场需求的增长和对产品质量的不断提升,压铸生产计划成为企业生产管理中重要的一环。
本文将就压铸生产的年度工作计划进行详细阐述,具体包括市场分析、生产目标、技术改进、质量管理、成本控制等内容,以期为企业的压铸生产工作提供有益的参考。
二、市场分析随着汽车、电子、机械制造等行业的不断发展,对压铸产品的需求量不断增加。
同时,随着人们对产品质量和外观的要求不断提高,市场对压铸产品的质量和性能提出了更高的标准。
在这样的背景下,企业需要充分了解市场需求和趋势,根据市场变化及时调整生产计划,以满足市场需求。
三、生产目标1. 提高生产效率通过引进先进的生产设备和优化生产工艺,提高生产效率,降低生产成本。
2. 提升产品质量严格执行产品质量管理标准,不断进行设备维护和改进,提升产品质量,降低不合格率。
3. 开发新产品根据市场需求,开发新的产品型号,满足客户不同需求。
四、技术改进1. 加大设备更新改造力度购置先进的压铸设备,提高生产效率,降低生产成本。
2. 优化生产工艺根据产品特性,结合设备性能,优化生产工艺,提高产品质量,降低生产成本。
3. 强化设备维护定期对设备进行维护保养,确保设备性能稳定和可靠。
五、质量管理1. 强化员工培训加强对员工的技术培训,提高员工对产品质量的认识,提升员工技能。
2. 完善质量管理体系建立健全的质量管理体系,确保产品生产的每一个环节都符合质量管理要求。
3. 加强产品检测加大产品检测力度,确保产品质量符合标准要求。
六、成本控制1. 降低原材料成本与供应商合作,争取更优惠的原材料价格,降低生产成本。
2. 降低人工成本优化生产流程,提高生产效率,降低人工成本。
3. 降低能源成本采用节能技术,降低生产能源成本,提高生产效益。
七、总结通过对压铸生产的年度工作计划的详细阐述,相信可以为企业的生产工作提供有益的参考。
产品质量保证计划

产品保证计划1 严格控制制造过程中的影响因素:1.1熔化:1.1. 1温度过高会造成铝合金的晶粒粗大,因此,必须控制铝合金的熔化温度(780℃~~800℃),同时做好记录。
1.1.2坩埚刷涂料要均匀,否则会对坩埚有腐蚀,使铝液增铁,影响铸件性能。
1.1. 3回炉料加放过多会造多铁超标,因此,必须控制回炉料,严格按配比操作,保证铸件的化学成份合格,同时做好记录。
1.1. 4精炼温度(710℃~~730℃)要达到要求,并且撇碴要干净,否则会使铝液精炼不完全,有杂质,影响铸件的性能。
1.1.5熔化好的铝液的的成份指标符合顾客提供的图纸要求。
1. 2压铸:1. 2.1铝液的保温温度要在范围之内(650℃~~690℃),温度过高会在压铸时跑水,从而影响铸件的内部质量,易产生气孔;温度过低则会使铸件的表面出现冷隔、欠铸等铸造缺陷。
1. 2.2加工表面不允许存有欠铸、裂纹、及孔眼类等铸造缺陷,机械加工后的表面不允许存有影响使用的铸造缺陷,因此,必须控制压铸工艺,减少铸造缺陷,满足铸件技术要求,同时做好相关记录。
1、2.3机械性能:在熔化过程控制好熔化温度和材料的化学成份,从而保证铸件的机械性能,并符合顾客提供的图纸要求。
1. 3时效:铸件必须经自然时效7天以上。
1. 4机加1.4.1机加产品的位置度、粗糙度、垂直度影响装配的尺寸要求全部满足图纸要求。
1.4.2机加产品要求加工面不允许有碰伤、磕伤、擦伤等现象存在。
1.4.3机加产品加工后清洗要求清洗干净,无毛刺。
1.4.4机加后产品的包装要求牢靠,纸箱不会破损。
2、XXXX可靠性目标为:2.1 压铸生产铸件的产能是180--200件/8小时,机加生产成品的产能是50件/8小时。
2.2 尺寸精度合格率达到99%,主要尺寸精度合格率达到100%。
2.3铸件质量原因造成顾客退货率和市场退货率控制在20000PPm以内。
2. 4由于铸件质量原因造成顾客退货或市场退货的,我公司负责三包。
压铸车间生产管理制度

压铸车间生产管理制度1. 目的和范围- 本制度的目的是为了确保压铸车间的生产过程安全、高效、顺利,保证产品质量,提高生产效率。
- 本制度适用于压铸车间的生产管理。
2. 生产计划管理- 由生产部门制定每日、每周、每月的生产计划,包括产品数量、工艺要求、生产时间等。
- 生产计划应提前与其他相关部门沟通,确保原材料供应、设备维护等配套工作完成。
3. 设备管理- 压铸车间应对设备进行定期巡检、保养,确保设备状态良好。
- 发现设备故障应立即报修,维修人员应及时处理。
4. 原材料管理- 原材料应严格按照生产计划和工艺要求进行采购和入库。
- 入库原材料应进行清点、检验,合格后方可使用。
- 原材料使用应按照先进先出原则,确保存储时间合理。
5. 生产过程管理- 操作员应按照工艺要求进行操作,确保操作过程的安全、准确。
- 生产过程中应严禁私自更改工艺参数,如有需要应及时向主管汇报并获得批准。
- 生产过程中发现异常情况应及时上报,采取相应的措施进行处理。
6. 产品质量管理- 生产过程中应进行过程控制和出厂检验,确保产品符合质量要求。
- 出现不良品应进行分类、统计原因,并采取措施避免类似问题的再次发生。
- 当产品质量不符合要求时,应及时对生产过程进行调整和改进。
7. 安全管理- 生产过程中应严格遵守安全操作规程,禁止酗酒、吸烟等不良行为。
- 工作人员应佩戴个人防护装备,确保人员安全。
8. 环境保护管理- 压铸车间应遵守环境保护相关法律法规,做好废物的分类收集、处理。
- 减少能源消耗,提高能源利用效率,推行清洁生产。
9. 员工培训与考核- 新员工应进行入职培训,了解生产管理制度和操作规程。
- 定期对员工进行培训,提高员工的技能水平和工作效率。
- 对员工进行考核和评价,及时发现问题并采取相应措施。
10. 不符合项处理- 对于生产过程中发现的不符合项,应立即采取措施进行整改并进行记录。
- 整改措施的执行情况要进行跟踪和检查,确保问题得到彻底解决。
压铸车间质量管理方案

压铸车间质量管理方案压铸车间是生产压铸件的重要场所,质量管理在压铸车间中尤为重要。
良好的质量管理方案能够确保产品质量稳定,提高生产效率,降低生产成本,增强企业竞争力。
本文将从流程控制、设备维护、员工培训和质量监控四个方面,探讨如何建立一套有效的压铸车间质量管理方案。
一、流程控制压铸车间的生产流程是影响产品质量的关键因素之一。
为确保产品质量稳定,应建立科学、规范的生产工艺流程,并制定详细的作业指导书。
作业指导书应包括每个工序的具体操作步骤、操作要点、质量要求和质量检验方法等内容,以确保每个工序的操作符合质量要求。
同时,应加强对生产工艺流程和作业指导书的培训,提高员工对流程的理解和执行能力。
二、设备维护设备是保证产品质量的基础。
为确保设备正常运行,应建立完善的设备维护制度。
制定设备维护计划,按照计划进行定期保养、维修和更换备件,确保设备的可靠性和稳定性。
同时,建立设备维护记录,记录设备维护情况和故障处理过程,以便分析设备故障原因,采取相应措施预防故障的发生。
三、员工培训员工是质量管理的重要一环。
为提高员工的职业素质和技术水平,应加强员工培训。
培训内容包括质量意识培养、工艺知识培训、操作技能培训和质量管理知识培训等。
培训形式可以采取内部培训、外部培训和岗位轮换等方式,使员工全面掌握所需的知识和技能,提高工作效率和质量水平。
四、质量监控质量监控是质量管理的核心环节。
建立有效的质量监控体系,可以及时发现和纠正质量问题,确保产品质量符合要求。
质量监控包括原材料检验、过程控制和成品检验等环节。
原材料检验应严格按照标准进行,确保原材料质量稳定可靠;过程控制要加强对关键工序和关键参数的监控,及时调整工艺参数,防止质量问题的发生;成品检验要建立完善的检验方法和标准,对产品进行全面检测,确保产品质量符合要求。
以上是建立一套有效的压铸车间质量管理方案的主要内容。
通过科学的流程控制、设备维护、员工培训和质量监控,能够有效提高产品质量,确保压铸车间的生产效率和竞争力。
压铸控制计划范例
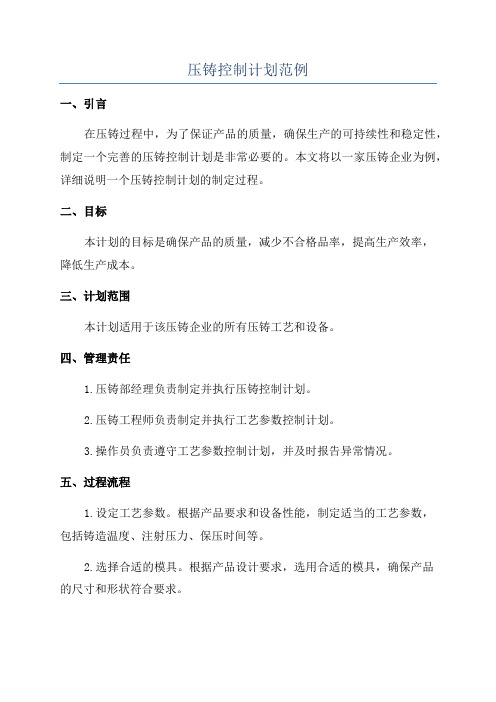
压铸控制计划范例一、引言在压铸过程中,为了保证产品的质量,确保生产的可持续性和稳定性,制定一个完善的压铸控制计划是非常必要的。
本文将以一家压铸企业为例,详细说明一个压铸控制计划的制定过程。
二、目标本计划的目标是确保产品的质量,减少不合格品率,提高生产效率,降低生产成本。
三、计划范围本计划适用于该压铸企业的所有压铸工艺和设备。
四、管理责任1.压铸部经理负责制定并执行压铸控制计划。
2.压铸工程师负责制定并执行工艺参数控制计划。
3.操作员负责遵守工艺参数控制计划,并及时报告异常情况。
五、过程流程1.设定工艺参数。
根据产品要求和设备性能,制定适当的工艺参数,包括铸造温度、注射压力、保压时间等。
2.选择合适的模具。
根据产品设计要求,选用合适的模具,确保产品的尺寸和形状符合要求。
3.准备材料。
选用合适的铸造材料,并按照配方准确称量,防止材料的异相反应和杂质的混入。
4.进行模具预热。
通过对模具进行适当的预热,确保铸造过程中温度的均匀分布。
5.铸造操作。
将准备好的铸造材料倒入模具中,控制注射温度、注射压力和注塑时间。
6.保压操作。
在注射结束后,进行保压操作,以保证铸件的密实性和尺寸精度。
7.铸件取出。
待冷却后,将铸件从模具中取出,并进行修边、打磨等工艺处理。
8.检测和检验。
对铸件进行尺寸、外观、材料成分等多个方面的检测和检验,确保产品符合设计和客户要求。
9.记录和分析。
对每一次生产过程进行记录和分析,及时发现问题并采取纠正措施。
六、控制方法1.控制工艺参数。
通过严格控制工艺参数,如温度、压力、时间等,确保产品的质量和尺寸稳定。
2.定期保养设备。
对压铸设备进行定期保养和维护,确保设备的可靠性和稳定性。
3.培训操作员。
对操作员进行培训,提高其操作技能和质量意识,降低人为错误。
4.定期检测和校准检测设备。
对检测设备进行定期检测和校准,确保测试数据的准确性和可靠性。
5.定期召开质量会议。
通过召开质量会议,总结经验,分享问题,促进团队间的沟通和合作。
铝制品车间质量控制计划
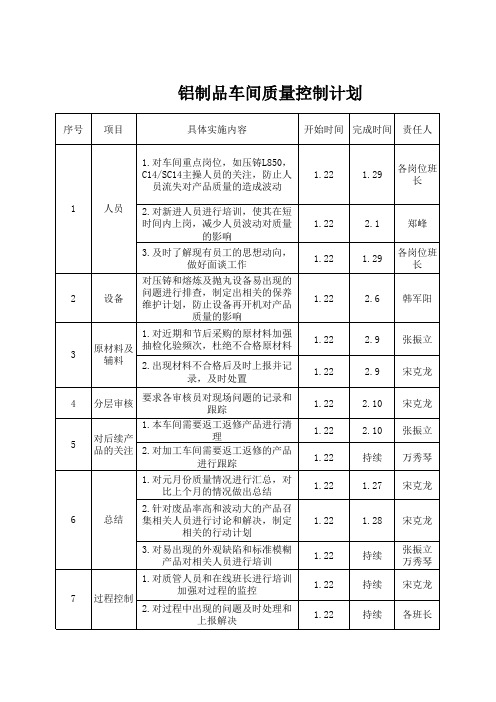
7
过程控制
品车间质量控制计划
备注
2.9 2.9 2.10 2.10 持续 1.27 1.28 持续 持续 持续
张振立 宋克龙 宋克龙 张振立 万秀琴 宋克龙 宋克龙 张振立 万秀琴 宋克龙 各班长
4
分层审核
5
1.本车间需要返工返修产品进行清 理 对后续产 品的关注 2.对加工车间需要返工返修的产品 进行跟踪 1.对元月份质量情况进行汇总,对 比上个月的情况做出总结
铝制品车间质量控制计划
序号 项目 具体实施内容 1.对车间重点岗位,如压铸L850, C14/SC14主操人员的关注,防止人 员流失对产品质量的造成波动 1 人员 2.对新进人员进行培训,使其在短 时间内上岗,减少人员波动对质量 的影响 3.及时了解现有员工的思想动向, 做好面谈工作 2 设备 对压铸和熔炼及抛丸设备易出现的 问题进行排查,制定出相关的保养 维护计划,防止设备再开机对产品 质量的影响 开始时间 完成时间 责任人
1.22
1.29
各岗位班 长
1.22 1.22
2.1 1.29
郑峰 各岗位班 长 韩军阳
1.22
2.6
3
1.对近期和节后采购的原材料加强 原材料及 抽检化验频次,杜绝不合格原材料 辅料 2.出现材料不合格后及时上报并记 录,及时处置 要求各审核员对现场问题的记录和 跟踪
1.22 1.22 1.22 1.22 1.22 1.22 1.22 1.22 1.22 1.22
铝合金压铸件控制计划

铝合金压铸件控制计划1.引言2.原材料采购选择优质的铝合金原料对于保证产品质量至关重要。
首先,要选择有良好信誉的供应商,并与之建立长期合作关系。
其次,要对进货的铝合金原料进行全面的物理与化学性能检测,确保其符合产品要求。
最后,在采购过程中,要严格控制原材料的质量、规格和数量,防止出现偷工减料等问题。
3.生产工艺控制3.1铝液的准备铝液是压铸件的原材料,其温度、成分和纯度直接影响产品的质量。
在铝液的准备过程中,应确保炉温达到设定温度,并在加工过程中定期检测铝液的成分和纯度,以及温度的稳定性。
3.2模具的设计与制作模具是铸造过程中的关键因素之一,其设计和制作需要经验丰富且具有高精度的技术人员。
在模具设计和制作过程中,要根据产品的要求和工艺要求,选择合适的材料和加工工艺。
同时,在模具加工过程中,要进行严格的检测和测量,确保模具的精度和质量。
3.3压铸过程控制压铸是铝合金压铸件的成型过程,在压铸过程中,要严格控制铝液的温度、压力和铸造时间。
同时,还要监控压铸机的工作状态,确保其正常运行。
3.4后处理在铝合金压铸件的后处理过程中,包括去除余脱模剂、清洗、修整和热处理等环节。
这些环节需要严格按照工艺要求进行操作,并进行必要的质量检测和测量,以确保产品的精度和质量。
4.设备检测设备的检测是压铸件质量控制的重要环节。
首先,要定期对压铸机进行维护和保养,确保其正常运行。
其次,在每一批产品生产之前,要对压铸机进行调试和校验,确保其精度和稳定性。
同时,还要对成品进行抽样检测和测量,对不合格品进行追踪和整改。
5.质量管理体系为了提高铝合金压铸件的质量,应建立完善的质量管理体系。
首先,要制定详细的工作操作规范和质量检测标准,确保每个环节的工作都按照规定进行。
其次,要建立质量跟踪和评价机制,对每一批产品进行质量检测和评估,及时发现问题并采取措施进行改进。
6.结论。
压铸车间月工作计划暨总结

一、工作计划1. 优化生产流程(1)对现有生产流程进行梳理,找出瓶颈环节,制定改进措施。
(2)优化生产设备布局,提高生产效率。
(3)加强生产计划管理,确保生产任务按时完成。
2. 提高产品质量(1)加强原材料采购管理,确保原材料质量稳定。
(2)加强生产过程控制,严格执行生产工艺要求。
(3)开展质量培训,提高员工质量意识。
3. 降本增效(1)加强能源管理,降低生产成本。
(2)优化生产计划,提高设备利用率。
(3)加强设备维护保养,降低设备故障率。
4. 安全生产(1)加强安全生产教育,提高员工安全意识。
(2)严格执行安全生产规章制度,确保生产安全。
(3)定期进行安全隐患排查,及时整改。
5. 团队建设(1)加强团队凝聚力,提高团队协作能力。
(2)开展员工培训,提升员工技能水平。
(3)关心员工生活,营造良好的工作氛围。
二、工作总结1. 生产进度本月生产任务按时完成,产品合格率达到95%以上。
针对生产过程中的瓶颈环节,采取了优化生产流程、提高设备利用率等措施,生产效率得到有效提升。
2. 产品质量通过加强原材料采购、生产过程控制和质量培训,本月产品质量得到明显提高。
产品合格率达到95%以上,客户满意度较高。
3. 降本增效本月通过加强能源管理、优化生产计划和设备维护保养,生产成本得到有效控制。
设备利用率提高5%,生产成本降低3%。
4. 安全生产本月安全生产形势稳定,未发生安全事故。
通过加强安全生产教育、严格执行规章制度和定期排查隐患,员工安全意识得到提高。
5. 团队建设本月团队凝聚力得到加强,员工协作能力得到提升。
通过开展员工培训和关心员工生活,员工满意度较高。
三、下一步工作计划1. 持续优化生产流程,进一步提高生产效率。
2. 加强产品研发,提升产品竞争力。
3. 深入推进降本增效工作,降低生产成本。
4. 加强安全生产管理,确保生产安全。
5. 持续加强团队建设,提升团队整体实力。
总之,本月压铸车间各项工作取得了一定的成绩,但仍存在一些不足。
压铸件控制计划标准模板
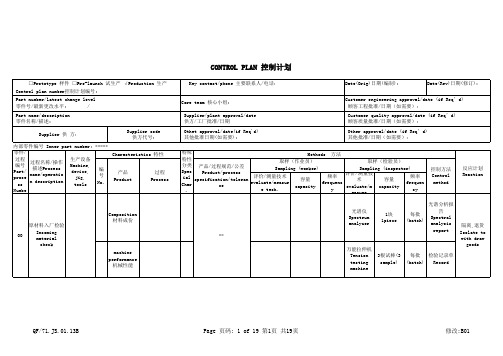
目测 visual 对比样件 contrast sample
100%
连续 (continu
e)
目测 visual
1模(1 cavities)
隔离
Each 4hours 每4小时
Check Location inspection 现场检验
通知领班、巡 检
segregate,in form forman
零件/
过程 编号 Part/ proce ss
过程名称/操作 描述Process name/operatio n description
生产设备 Machine, device,
jig, tools
编 号 No.
Numbe
Characteristics 特性
产品 Product
过程 Process
去料柄
100% 100% 100% 100%
连续 (continu
e)
隔离
Check 通知领班、巡
Location
检
inspection segregate,in
现场检验 form forman
and patrol
连续 Continuo
us
连续 Continuo
us
目测 visual inspection
us inspection
5件 5 pcs
每4小时 检验记录单 Each 4 inspection hours record
Concentrate
05
smelting raw materials原材
料集中熔炼
熔化炉 melt furnace
2
3
回料比例 温度
特殊
Methods 方法
压铸铝合金控制计划
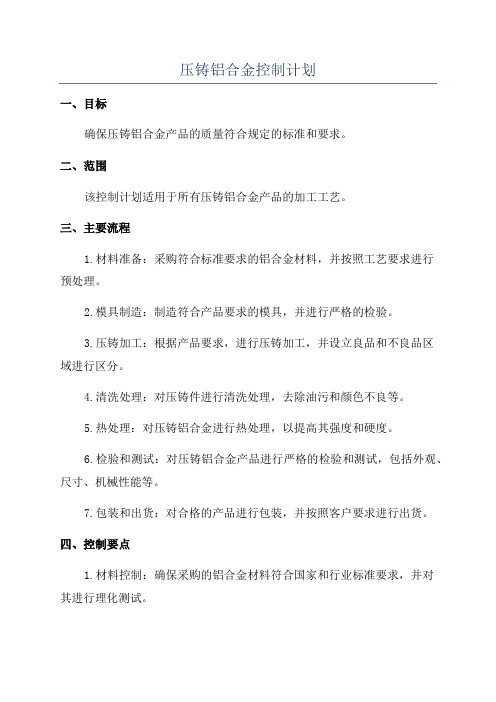
压铸铝合金控制计划一、目标确保压铸铝合金产品的质量符合规定的标准和要求。
二、范围该控制计划适用于所有压铸铝合金产品的加工工艺。
三、主要流程1.材料准备:采购符合标准要求的铝合金材料,并按照工艺要求进行预处理。
2.模具制造:制造符合产品要求的模具,并进行严格的检验。
3.压铸加工:根据产品要求,进行压铸加工,并设立良品和不良品区域进行区分。
4.清洗处理:对压铸件进行清洗处理,去除油污和颜色不良等。
5.热处理:对压铸铝合金进行热处理,以提高其强度和硬度。
6.检验和测试:对压铸铝合金产品进行严格的检验和测试,包括外观、尺寸、机械性能等。
7.包装和出货:对合格的产品进行包装,并按照客户要求进行出货。
四、控制要点1.材料控制:确保采购的铝合金材料符合国家和行业标准要求,并对其进行理化测试。
2.模具控制:制造模具时,确保其尺寸和质量符合产品要求,并进行定期维护和检修。
3.工艺控制:对压铸加工过程中的参数进行控制,包括压力、温度、时间等,以确保产品质量的稳定性。
4.清洗控制:确保清洗过程中使用的清洗剂符合要求,并对清洗效果进行定期检验。
5.热处理控制:根据产品要求,对压铸铝合金进行热处理,确保其物理性能满足要求。
6.检验控制:严格按照检验标准对产品进行检验,确保不合格产品不流入市场。
7.包装控制:对合格产品进行包装,确保其在运输过程中不受到损坏。
五、质量控制方法1.抽样检验:根据国家和行业标准,制定抽样检验方案,并定期进行抽样检验。
2.巡检:对压铸加工过程中的关键环节进行巡检,及时发现问题并进行纠正。
3.符合性评估:对每个工序的合格率进行统计,并及时分析不合格品的原因,采取措施进行改进。
4.培训:对操作人员进行培训,确保他们对工艺要求、产品质量标准等有清晰的认识。
六、责任及权限1.生产部门负责生产过程的具体实施,包括材料准备、加工、清洗、热处理等。
2.质量部门负责制定和执行控制计划,对产品质量进行监督和管理。
3.技术部门负责对工艺进行优化和改进,并对相关参数进行监控和调整。
铸造工程质量管理制度内容
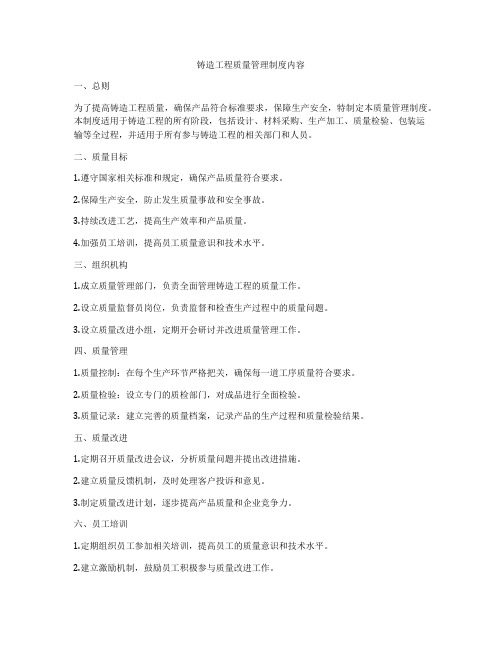
铸造工程质量管理制度内容一、总则为了提高铸造工程质量,确保产品符合标准要求,保障生产安全,特制定本质量管理制度。
本制度适用于铸造工程的所有阶段,包括设计、材料采购、生产加工、质量检验、包装运输等全过程,并适用于所有参与铸造工程的相关部门和人员。
二、质量目标1.遵守国家相关标准和规定,确保产品质量符合要求。
2.保障生产安全,防止发生质量事故和安全事故。
3.持续改进工艺,提高生产效率和产品质量。
4.加强员工培训,提高员工质量意识和技术水平。
三、组织机构1.成立质量管理部门,负责全面管理铸造工程的质量工作。
2.设立质量监督员岗位,负责监督和检查生产过程中的质量问题。
3.设立质量改进小组,定期开会研讨并改进质量管理工作。
四、质量管理1.质量控制:在每个生产环节严格把关,确保每一道工序质量符合要求。
2.质量检验:设立专门的质检部门,对成品进行全面检验。
3.质量记录:建立完善的质量档案,记录产品的生产过程和质量检验结果。
五、质量改进1.定期召开质量改进会议,分析质量问题并提出改进措施。
2.建立质量反馈机制,及时处理客户投诉和意见。
3.制定质量改进计划,逐步提高产品质量和企业竞争力。
六、员工培训1.定期组织员工参加相关培训,提高员工的质量意识和技术水平。
2.建立激励机制,鼓励员工积极参与质量改进工作。
3.培养专业技术人员,提高企业的技术水平和竞争力。
七、责任追究对生产中发生的质量事故和安全事故进行彻底调查,并追究相关责任人的责任。
八、附则本制度经公司质量管理部门审定并正式实施,如有变动需经相关部门审批后生效。
本制度解释权归公司所有。
铝合金压铸件控制计划

版本:A/0编制日期:修订日期:客户工程部门批准客户质量部门批准其他批准容量频率原材料输入ZL104化学成份对照表ZL104化学成份对照表-进料标准对照供方材质报告1次每批供方原材料分析报告10领料1ZL104领料单1预热后平稳投入,去除表面浮渣液面无浮渣,隔膜目识目识2精炼温度800℃~850℃温度表3浇注温度630℃~650℃温度表1模具温度150℃以上温度表2主压力10~13MPa 压力表3增压20~25MPa压力表4外观技术要求目测3件2小时5气孔小于0.3mm目测3件2小时6尺寸¢85(-0.3;+0.3)卡尺3件2小时首未检巡检记录表40清理毛剌锉刀1外观要求表面光洁平整,不允许有秘孔,缩孔,裂纹,花纹,缺料等铸造缺陷;目识3件2小时首未检巡检记录表抛光110包装1混装,少装,标识不清包装标准目识100%检验每批检验记录表***有限公司控制计划控制计划编号主要联系人电话/传真:零件名称小组成员:零件图号供应商/生产部批准/日期:供应商/生产部名称公司代码其他批准:过程编号过程名称/操作描述制造设备名称制造模具/工装/工具特性特殊特性分类方法控制方法编号产品过程产品/过程规范/公差评价/测量技术取样首未检巡检记录表20熔炼熔炉每炉每4小时检测一次备注:★表示重要工艺卡压铸工艺参数监控记录表30压铸300T 压铸机每班4小时抽检一次工艺卡Pre-Launch/试生产Prototype/试样Pre-Launch/量产第页共页反应计划不良退供应商浇出浮渣调整参数停机检查原因/调机/不合品报废隔离,查明起因,改进工艺隔离,查明起因隔离,查明起因,返工隔离,返工。
基于FMEA的X公司压铸质量管理改进

基于FMEA的X公司压铸质量管理改进基于FMEA的X公司压铸质量管理改进摘要:随着市场竞争的加剧,企业面临着越来越高的质量要求。
本文以X公司为研究对象,采用FMEA(失效模式与影响分析)方法,对其压铸质量管理进行改进,提出了一套系统化的质量管理方案,旨在提高压铸产品的质量水平,降低不良率,提高客户满意度,增加企业竞争力。
1. 引言随着现代工业的发展,压铸技术在制造业中得到了广泛应用,特别是在汽车、电子、航空航天等领域。
然而,由于压铸工艺的复杂性和多变性,往往会导致不可预知的质量问题。
因此,压铸质量管理成为企业追求优质产品的关键。
2. FMEA简介FMEA是一种系统性的方法,通过对可能的失效模式和其影响进行评估和分析,找出失效的根本原因,并据此制定相应的改进措施。
FMEA方法可以帮助企业在产品设计、工艺设计、制造过程等各个环节识别潜在的质量问题,从而减少质量风险。
3. X公司现状分析在对X公司进行调研和分析后,我们发现其存在以下问题:一是产品不良率较高,质量稳定性差;二是生产过程中存在一些关键工艺参数的控制不力;三是员工对质量管理的认识不够深入。
4. 基于FMEA的压铸质量管理改进方案(1)建立FMEA团队:组建专门的质量改进团队,包括设计、工艺、生产等各个环节的负责人,制定改进计划和目标。
(2)制定FMEA分析计划:明确分析的对象、范围和方法,确定评估指标和评分标准。
(3)识别潜在失效模式:通过分析历史数据、经验交流和现场实地调研等方法,识别可能的失效模式和其影响。
(4)评估失效影响程度:利用量化方法对失效影响的严重程度进行评估,确定影响程度高的失效模式。
(5)分析失效原因:利用一流图、鱼骨图等工具,深入研究影响程度高的失效模式的根本原因,找出存在的问题。
(6)制定改进措施:根据分析结果,制定相应的改进措施,包括设计优化、工艺调整、加强培训等方面。
(7)实施改进措施:按照计划逐步实施改进措施,并进行效果跟踪和评估。
压铸件CP控制计划范例
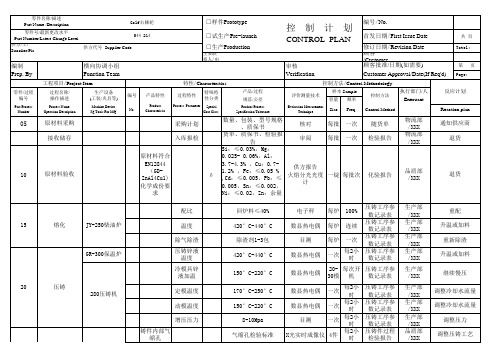
主要联 系人/电
控制计划
CONTROL PLAN
审核
编号/No.
首发日期/First Issue Date 修订日期/Revision Date 顾客 /Customer 顾客批准/日期(如需要)
共页 Totel:
第页
Prep. By
零件/过程 编号
Part/Process Number
20- 每次开 压铸工序参 30模 机 数记录表
数显热电偶
一次
每2小 时
数显热电偶
一次
每2小 时
目测
一次
每2小 时
X光实时成像仪 4件
每2小 时
压铸工序参 数记录表
压铸工序参 数记录表
压铸工序参 数记录表
压铸件过程 检验报告
生产部 /XXX
生产部 /XXX
生产部 /XXX
生产部 /XXX
生产部 /XXX
Reaction plan
采购计划
入库报检
原材料符合 EN12844 (GD-
ZnAl4Cu1) 化学成份要
求
数量、包装、型号规格 、质保书
核对
每批 一次 随货单
货单、质保书、检验报 告
审阅
每批 一次 检验报告
Si:≤0.03%,Mg:
0.025- 0.06%,Al:
ê
3.7-4.3% ,Cu:0.71.2% ,Fe:≤0.05 % ,Cd:≤0.005,Pb:≤ 0.005,Sn:≤0.002,
检验
去料柄 毛坯检验
手工 手工
Verification
Customer Approval/Date(If Req'd) Page:
铝合金压铸控制计划模板
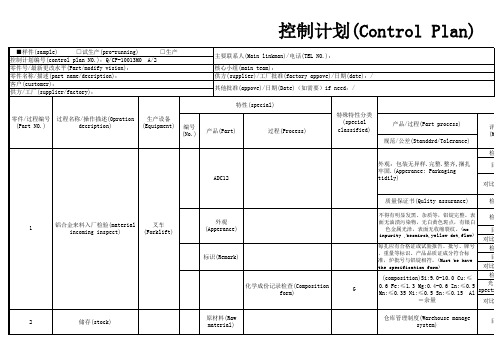
符合检验基准书(comply Parameter)
目视(
烘烤温度200℃(Baking temprature),时间30分钟(time)
目视(
符合作业标准书(comply Parameter)
目视(
游标卡尺
设备运转完好无异常(Equipment regular)
目视( 耳闻(Ea
四轴机床,治
7
CNC
目视(
检查设备状态(Check equipment status)
熔化温度(Metal temprature)
熔炉(Oven)
温度保温(Oven temprature)
压铸机
(420T)
3
压铸(die-casting)
模具,容器 (Die casting
machine/
mould/Oven
铝锭与回 recycle )
外观
检查设备状态(Check equipment
(Apperance)
status)
外观
6
去毛刺(de-burrying)
锉刀(File Grater)
(Apperance) 尺寸
(Dimention)
检查设备状态(Check equipment
status)
四轴机床,治
7
CNC
具,容器
设备运转完好无异常(Equipment regular)
1次(time)
班(shift)
设备点检记录 (sequenced dection
remark)
重新调整或维修 (adjustorfix)
目视(visual)
1次(time)
1H(hour)
熔炉温度记录表(oven 调整到正确温度(re-
压铸车间年度工作计划
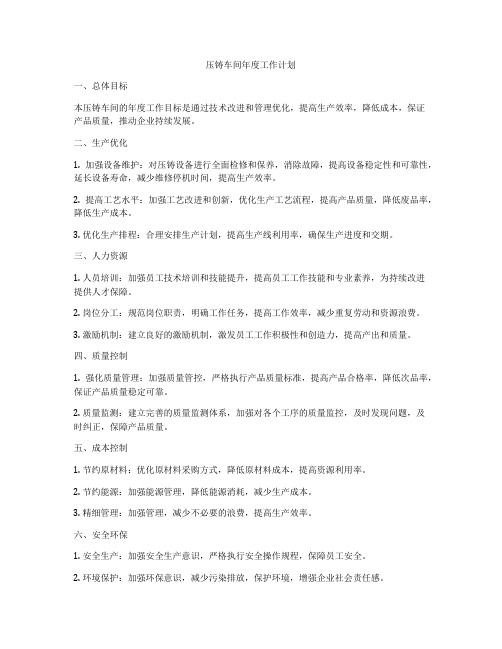
压铸车间年度工作计划一、总体目标本压铸车间的年度工作目标是通过技术改进和管理优化,提高生产效率,降低成本,保证产品质量,推动企业持续发展。
二、生产优化1. 加强设备维护:对压铸设备进行全面检修和保养,消除故障,提高设备稳定性和可靠性,延长设备寿命,减少维修停机时间,提高生产效率。
2. 提高工艺水平:加强工艺改进和创新,优化生产工艺流程,提高产品质量,降低废品率,降低生产成本。
3. 优化生产排程:合理安排生产计划,提高生产线利用率,确保生产进度和交期。
三、人力资源1. 人员培训:加强员工技术培训和技能提升,提高员工工作技能和专业素养,为持续改进提供人才保障。
2. 岗位分工:规范岗位职责,明确工作任务,提高工作效率,减少重复劳动和资源浪费。
3. 激励机制:建立良好的激励机制,激发员工工作积极性和创造力,提高产出和质量。
四、质量控制1. 强化质量管理:加强质量管控,严格执行产品质量标准,提高产品合格率,降低次品率,保证产品质量稳定可靠。
2. 质量监测:建立完善的质量监测体系,加强对各个工序的质量监控,及时发现问题,及时纠正,保障产品质量。
五、成本控制1. 节约原材料:优化原材料采购方式,降低原材料成本,提高资源利用率。
2. 节约能源:加强能源管理,降低能源消耗,减少生产成本。
3. 精细管理:加强管理,减少不必要的浪费,提高生产效率。
六、安全环保1. 安全生产:加强安全生产意识,严格执行安全操作规程,保障员工安全。
2. 环境保护:加强环保意识,减少污染排放,保护环境,增强企业社会责任感。
七、技术改进1. 引进先进技术:加强技术研发和创新,引进先进的压铸技术和设备,提高生产水平。
2. 自主创新:鼓励员工自主创新,提高技术水平,增强企业竞争力。
八、与其他部门合作1. 与销售部门合作:加强与销售部门的沟通,制定合理的生产计划,确保产品交期。
2. 与采购部门合作:加强与采购部门的协调,优化原材料采购方式,降低采购成本。
- 1、下载文档前请自行甄别文档内容的完整性,平台不提供额外的编辑、内容补充、找答案等附加服务。
- 2、"仅部分预览"的文档,不可在线预览部分如存在完整性等问题,可反馈申请退款(可完整预览的文档不适用该条件!)。
- 3、如文档侵犯您的权益,请联系客服反馈,我们会尽快为您处理(人工客服工作时间:9:00-18:30)。
2H/次 首件时 1H/次 1H/次 1H/次 1H/次 1H/次
记录在巡检报 表中注明
记录在巡检报 表中注明 记录在巡检报 表中注明
记录在巡检报 表中注明
记录在巡检报 表中注明
记录在巡检报 表中注明
记录在巡检报 表中注明
不良品处置方式 通知领班和组长 通知领班和组长 通知领班和组长 通知领班和组长 通知领班和组长 通知领班和组长 通知领班和组长 通知领班和组长 通知领班和组长 通知领班和组长 通知领班和组长 通知领班和组长
产品名称 序号 流程
1
压铸
2
除水口
3
挫披锋
4
钻孔
压铸产品质量控制计划
压铸产品
产品适用范围
通用
管控特性
管控方法
频率
记录
生产前模具预热 脱模剂喷雾状况 砂孔,裂纹验证 排渣粉加入状况 尺寸符合性验证
料温稳定性 水口处砂孔
变形 变形,未除净
孔径 孔距 孔位
机台开机和更换新模具时,必须对其进行加温
首件时
记录在巡检报 表中注明
喷雾均匀
1H/次
记录在巡检报 表中注明
车制,磨光,剖开产品,在放大镜下面观察
4H/次
记录在巡检报 表中注明
每天至少加入一次
每天一次
记录在巡检报 表中注明
用卡尺,高度尺和试装结合的方式
首件时
记录在巡检报 表中注明
用红外线测温仪进行测量 试验水口处砂孔是否能消除 将产品放在大理石平台上,验证其是否有变形现象 目视观察有无将批锋处理干净 用塞规检查孔直径是否符合要求 检查孔间距是否正确,用相关联的产品进行试装 检查加工的孔是否在图纸要求的位置
1H/次 1H/次 1H/次 1H/次 1H/次 1H/次
记录在巡检报 表中注明
记录在巡检报 表中注明
记录在巡检报 表中注明
记录在巡检报 表中注明
记录在巡检报 表中注明
记录在巡检报 表中注明
通知领班和组长 通知领班和组长 通知领班和组长 通知领班和组长 通知领班和组长 通知领班和组长
备注
5
攻牙
6 槽位加工
牙径 扭力 滑牙,烂牙 槽深度 槽宽度 装配无松动
用螺纹规验证牙径是否符合要求 使用对应规格的螺丝安装在牙孔上面,再用扭力计测 定其扭力值
用放大镜观察牙孔内有无烂牙现象
用卡尺和高度表测量其深度是否符合图纸要求
用卡尺表测量其深度是否符合图纸要求
用有效的,正确的关联部件进行组装,不能松动