模具常见异常及处理方法
关于模具的异常报告

关于模具的异常报告450-04-76模具用料POM该模具的76号产品粘模严重,并且脱模不顺;同时该产品的批锋较多,给正常生产带来一定的困难,其原因是该产品的后模省模不到位,;同时产品的筋位多,致使产品在脱模时有一定的困难,而该产品的批锋多是模具的滑块碰模不好而产生的批锋.建议解决方法:(1):把76号产品的后模重新省模并且在产品的边缘开多一个冷料孔其目的是让产品在脱模时后模无阻力,而冷料孔是铺助产品脱模.(2)关于产品的批锋多主要是模具制作时滑块与模具飞模不好,现在只能从新烧焊,再重新飞模以达到没有批锋的效果.(该模具省模.烧焊及重新飞模.加开冷料井所有费用累计¥2000元)450-04-19模具用料POM+GF10﹪该模具的前模漏水,致使前模无法装水生产,导致产品的生产周期严重延长;而后模冷却又不是很到位,同时19号产品的前端又无法通水,这样就导致了19号产品内部容易热收缩,出现在假缺胶现象;而打油生产是为了冷却模芯使产品不容易热收缩,给正常生产造成了极大的不便;同时也也给品质带来了隐患.建议解决方法:(1)查找前模漏水的原因,看是否有补救的方法,如果有补救的方法则从新钻运水道加强模具的冷却系统;如果品没有补救的方法则重新开前模;而后模也只能是加强产品的冷却系统,也得多开运水道,才能真正的使模具得到及时有效的冷却.(该模具前后模加开运水所需费用¥2500元,其中包括前模漏水的地方烧焊.飞模) 450-04-18-21模具用料PPS该模前后模都无运水,产品无法及时有效的冷却;使模具的温度降不下来,由于该料的性能和PA相近,产品需要及时有效的冷却,而该模具根本就没有冷却系统,使产品无法冷却,导致18号产品容易出现如拉高.变形.收缩等一系列的质量问题,同时又加长了产品的生产周期,质量也无法得到保证,模具在这次生产时模温一度达到了近200℃,完全造出了PPS料所需的模温;而18号产品的前端有缩水现象是前模排气不好,也和模具上没有冷却系统有很大的关连;而21号产品表面有明显的不平整现象是模具的滑块也不是很平整,使做出来的产品外观不光滑,并且也有热收缩现象,再者模具没有冷却水,如果大批量的生产很容易让模具的司同.顶针.滑块.顶板.导柱出现烧死.建议解决方法:(1)给模具加上冷却系统,让模具得到有效冷却(加开运水道),给18号产品的前模加开排气槽,让模具里面的气有地方排出去;关于21号产品表面不平整现象,可以将模具的两个滑块进行省模抛平整.模具加开运水以后能有效的让模具的司同.顶针.滑块.顶板.导柱得到有效的冷却,不容易出现烧死的情况.(该模具前后模全部加开运水以及21号产品的滑块.抛光.省模所的费用累计¥4500元)450-04-32模用用料POM由于该模具的制作工艺有一定的问题,模具无法试模,并且产品严重粘前模.建议解决方法:(1)将该模具的前模两个相件重新做.(由于该模具前模相件需重新设计制作,所用工艺非常复杂,其目的是保证产品能顺利的脱离前模,所需费用¥5500元)925-04-51模具用料PP51号产品批锋太多,并且产品批锋调机无改善,即使让员工加工也无法达到正常的品质标准,给生产带来极大的不便.建议解决方法:(1)将该产品的模芯烧焊,然后进行飞模,以达到没有批锋的效果.(模具烧焊.飞模¥1500元)925-04-81-80-84-85模具用料ABS该模具已出现严重拉伤,影响到产品质量以及模具的使用寿命,同时产品的分型线已出现拉伤并且产品已出批锋,无法人为有效的去加工,并且在产品电镀以后容易出现严重的外观问题,使产品质量无法保证同时生产周期也延长.建议解决方法:将模具凡是拉伤的地方全部烧焊,再进行飞模,以确保产品质量和模具使用寿命都有保障.(由于该模具是特大维修前后模,需要前后拉伤的地方全部烧焊,同时也涉及到打火花.省模.抛光.重新抄数,累计所需费用¥6500元)450-04-36-25模具用料ABS该模具的弹簧力度不够,无法让顶板得到有力的回位;如果顶板不及时回位容易出现模具顶针的拉伤以及扁顶容易断裂,影响模具的使用寿命.建议解决方法:(1)把该模具的弹簧更换或加多弹簧,以达到顶板能及时回位的效果,同时模具在这次试模的时候扁顶以经断裂,需要更换。
模具异常应急处理方案

模具异常应急处理方案概述模具在使用过程中可能会出现异常情况,例如损坏、卡料、卡模等问题,这些问题可能会导致生产线停产,对企业生产造成严重影响。
因此,建立一套完善的模具异常应急处理方案对企业具有重要意义。
本文将介绍一套完整的模具异常应急处理方案,以帮助企业在出现问题时快速处理。
方案第一步:分析问题当模具出现异常时,首先需要进行问题分析,确定问题来源和具体情况。
常见的模具异常有:•损坏•卡料•卡模•漏油•加热不足/过热不同的异常情况有不同的应对措施,因此需要对问题进行准确定位,以便后续快速处理。
第二步:应急措施在确定了问题来源后,需要立即进行应急处理,以防止问题继续扩大影响。
常见的应急措施有:损坏•立即停止模具使用•进行检查,确定损坏情况•将损坏模具报修或更换•对生产计划进行调整卡料•停止模具使用•逆向调试•手动/半自动排出料块•检查料斗、送料器、熔融机等设备•对生产计划进行调整卡模•停止模具使用•确定卡模原因,对照图纸进行排除•检查空气、水、油路•如果无法排除,将模具拆卸维修•对生产计划进行调整漏油•停止模具使用•检查润滑管路,确定漏油地点•停止润滑系统,防止继续漏油•更换润滑管路或零部件•对生产计划进行调整加热不足/过热•停止模具使用•检查加热系统设备•确定故障原因•更换加热元件或维修加热系统•对生产计划进行调整第三步:修复问题在进行了应急措施后,需要对问题进行彻底修复,以保证模具的正常使用。
常见的修复措施有:•更换零部件/配件•打磨、切削、加工等方式进行修复•相关设备故障维修•对模具进行清洗、维护、保养第四步:预防措施为了避免模具异常情况的再次发生,需要对问题进行分析并采取有效预防措施。
常见的预防措施有:•做好模具的日常维护、保养工作•定期检查模具设备的各项指标•对生产设备进行合理调整,防止对模具造成损伤•增加备品备件库存数量,避免停工时间过长结论模具异常情况在生产中是不可避免的,但建立完善的应急处理方案和预防措施,可以有效减少对企业生产造成的影响。
模具异常应急处理方案

模具异常应急处理方案1. 前言模具在许多制造工艺中扮演着重要的角色,因此,模具出现异常问题时需要针对性地解决。
本文将介绍模具异常的标志,异常的原因以及在发现异常时如何快速应急处理。
2. 模具异常标志模具异常可能会表现出以下标志:2.1 产量下降模具异常可能会导致产品的次品率增加,从而降低产量。
当发现产量下降时,需要立即停机,检查模具的情况。
2.2 产品尺寸变化模具异常可能会导致产品尺寸变化,从而导致模具与产品之间的配合关系发生变化。
因此,在发现产品尺寸变化时,需要立即停机,检查模具的情况。
2.3 模具表面损坏模具表面损坏可能会导致产品表面质量下降。
因此,在发现模具表面损坏时,需要立即停机,检查模具的情况。
3. 模具异常原因模具异常的原因可能包括以下几个方面:3.1 模具设计问题模具设计问题可能会导致产品尺寸不一致,模具表面损坏等问题。
3.2 运行问题模具的运行问题可能会导致模具表面损坏,产品尺寸变化等问题。
例如,模具的运行速度过快、润滑不足或电路故障等问题。
3.3 保养问题模具保养不当可能会导致模具表面损坏、零件老化、粘附物等问题。
4. 模具异常应急处理方案当发现模具异常时,需要立即停机,检查模具的情况。
根据异常情况,下面是一些常用的应急处理方案:4.1 清洗模具清洗模具可以解决由于粘附物、导热油等原因所导致的模具异常问题。
4.2 更换损坏件当发现零件损坏时,需要及时更换零件。
必要时,需要联系供应商进行更换。
4.3 更换润滑剂当发现摩擦力过大时,需要及时更换润滑剂。
必要时,需要联系润滑剂供应商进行更换。
4.4 更改制造工艺当发现制造工艺存在缺陷时,需要及时更改制造工艺,以避免模具异常问题。
5. 总结模具异常对于制造工艺来说是一个非常致命的问题,因此,我们需要在生产过程中时刻关注模具的情况。
当遇到模具异常问题时,要注意及时进行应急处理,以避免对工厂产生过大的影响。
模具异常应急处理方案

模具异常应急处理方案背景模具是生产制造过程中必不可少的工具,它们可以帮助生产出高质量的产品。
然而,由于模具在使用过程中承受了巨大的力量和压力,它们也可能会出现异常状况。
这些异常可能会导致工作进度延迟、产生废品和工作效率降低。
为了在发生异常时能够快速解决问题,需要建立一套有效的异常应急处理方案。
异常类型在生产制造中,模具异常主要有以下几种类型:1.模具损坏:由于使用次数过多或者设计不合理,模具可能会出现损坏的情况。
例如,模具的部件磨损严重、弯曲、裂开或者掉落等。
2.模具卡死:当模具受到异常力量或者由于磨损不良,可能会导致模具卡死,无法正常运作。
3.模具误差:模具使用过程中可能出现误差。
例如,模具的尺寸出现偏差、偏移或者旋转等,影响到产品的质量和精度。
4.模具温度:模具温度的控制对于产品的成形和质量至关重要。
当温度过高或者过低,会导致理化特性的变化,影响生产质量。
异常应急处理方案为了应对模具生产中出现的异常情况,需要建立一套完整的异常应急处理方案,该方案应包含以下几个方面:1. 预防措施预防措施是避免模具异常发生的最有效手段。
建议在生产过程中采取以下措施:•定期检查模具的磨损情况,按时更换或者修理模具部件•在使用模具之前,必须认真检查、清洁完整,确保无异常•按照使用说明书正确操作和维护模具。
•对于重要的生产工艺过程,需要建立完善的温度、压力等参数的检测和监控系统。
2. 快速判断模具异常在模具使用过程中,发现异常情况后,需要快速判断该异常情况的严重程度和范围。
如果该异常情况对于生产产品没有重大影响,可以延迟其处理并暂停生产。
如果其对产品生产影响很大,需要立即查找原因并修复。
3. 快速响应发现模具异常情况后,需要快速响应并采取措施,以减少生产影响。
建议做到以下几点:•建立一套完善的报警机制,及时通知相关人员;•在最短时间内召开紧急会议,确定应急处理的流程和责任方;•分配应急处理人员,在最短时间内找出并处理异常。
模具异常处理流程

模具异常处理流程
嗨,小伙伴们!今天咱们来唠唠模具异常处理的流程。
这模具要是出了异常啊,可别慌,按下面这些法子来,一般都能解决问题的。
首先呢,当发现模具异常了,你得赶紧停下来手中的活儿。
这就好比你开车的时候发现车有点不对劲,你肯定不会还一个劲儿往前开吧?这时候要做的就是确认异常的状况。
这个很重要哦!你得仔细看看,是模具的某个部件损坏了呢,还是运作起来不太顺畅?我觉得这一步得特别细心,千万不能走马观花似的瞅一眼就完事儿了。
接下来呀,就是要判断这个异常的严重程度。
要是小毛病,像有个小零件稍微有点松动之类的,那可能咱们自己就能动手解决。
不过呢,如果是那种看起来比较严重的,比如说模具都变形了,那可就别轻易乱动了。
根据我的经验,这时候要是乱动,可能会让问题变得更糟呢!
要是确定自己能处理的小异常,那就可以开始着手解决啦。
找合适的工具,这工具可得找对喽!别拿着个扳手就想把所有问题都搞定,不同的问题得用不同的工具嘛。
在处理的时候呢,要小心谨慎。
我就见过有人处理的时候毛毛躁躁的,结果本来一个小问题,最后弄成了大麻烦。
要是自己搞不定的大异常,那怎么办呢?当然是找专业的人来帮忙啦。
不过在找专业人士之前,最好把你之前观察到的异常情况详细地告诉他们。
这样他们就能更快地找出问题所在,你说是不是这个理儿?
等专业人士来处理的时候,你也别闲着呀。
可以在旁边看着,学习学习。
说不定下次再遇到类似的问题,你自己就能解决了呢。
刚开始可能会觉得在旁边看有点无聊,但习惯了就好了,这可是个学习的好机会呀!。
模具常见问题分析及其解决方法

模具常见问题分析及其解决方法概述模具是工业生产中常用的一种工具,它在各个行业中被广泛应用。
然而,随着使用时间的增加,模具也会出现各种问题。
本文将详细分析模具常见问题,并提供相应的解决方法,以帮助读者更好地应对模具问题。
问题一:模具磨损严重模具磨损是使用寿命过程中常见的问题之一。
其主要表现为模具表面磨损或凹陷。
磨损的原因可能是: - 使用材料硬度较高 - 使用时间较长 - 模具润滑不足 - 模具设计不合理解决方法: - 使用耐磨性能更好的模具材料,如优质钢材 - 定期进行模具保养和维护,及时更换磨损严重的部件 - 在使用过程中保持适当的模具润滑,减少磨损 - 对模具进行优化设计,减少出现磨损的可能性问题二:模具尺寸偏差大模具尺寸偏差大是另一个常见问题。
这可能导致生产出的产品尺寸不准确,影响产品质量。
尺寸偏差大的原因包括: - 模具制造过程中的测量误差 - 模具材料膨胀或收缩不均匀 - 模具结构设计不合理解决方法: - 提高模具制造过程中的测量精度,并进行多次验证 - 选择合适的模具材料,控制材料膨胀或收缩的影响 - 对模具结构进行优化设计,避免尺寸偏差的产生问题三:模具易生锈模具易生锈是模具在使用过程中常见的问题之一。
模具生锈不仅影响外观,还可能导致模具损坏。
模具易生锈的原因可能是: - 环境湿度较高 - 模具存放不当 - 模具润滑不足解决方法: - 控制使用环境湿度,尽量保持干燥 - 对模具进行正确的存放,避免受潮或受酸碱腐蚀 - 在使用过程中,保持模具的适度润滑,防止生锈问题四:模具易断裂模具易断裂是一种严重的问题,可能导致模具报废,造成生产线停机。
模具易断裂的原因包括: - 模具结构设计不合理 - 模具材料不合格或强度低 - 模具使用过程中发生过载解决方法: - 对模具结构进行优化设计,提高其受力性能 - 选择合适的模具材料,确保其强度和韧性满足要求 - 在使用过程中,避免过载操作,及时发现并处理异常情况问题五:模具易堵塞模具易堵塞是模具在使用过程中常见的问题,特别是对于塑料注塑模具。
模具常见异常及处理方法
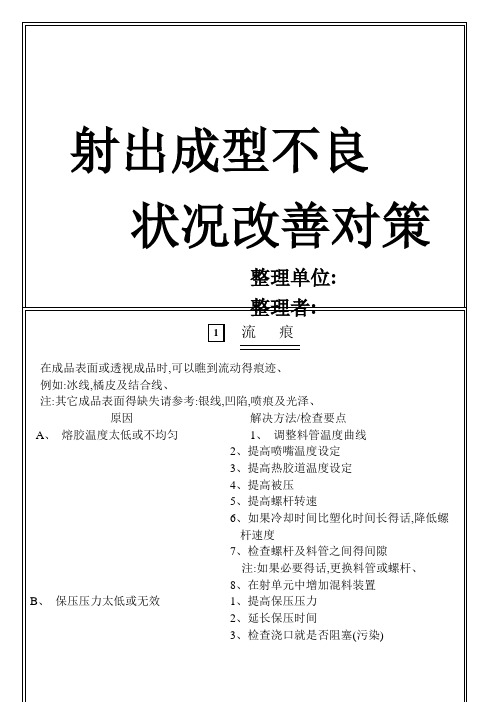
注:如果必要得话,加大浇口C、射出速度/压力不正确1、调整射出速度2、调整射出速度曲线3、调整射出压力4、调整射出曲线5、检查浇口就是否阻塞(污染)注:如果必要得话,加大浇口D、塑料流动不足1、检查浇口位置注:如果必要得话,增加或安排浇口位置(平衡) E、模具太冷或模具冷却不均匀而造成1、提高模具高度塑流动不良或不规则2、检查模具冷却就是否均匀/或阻塞F、模具污染如:过度润滑1、检查模具得合模面就是否污染注:如果必要得,清洁并拋光2、减少使用或不使用润滑剂,不管就是内部(在C、成品与模面粘合太紧而无法顶出1、检查模具表面就是否受损注:尤其就是垂直于模具运动方向得模具表面,必要得话,加以整修并拋光2、使用润滑剂,不管就是参合塑料里面或者喷离型剂3、检查模具:1)调整拔模角度2)调整倒角3)调整圆弧4、避免产生真空5、使用空气顶出针使顶出更容易D、顶针太小,不正确得顶针位置1、调整顶针控制安排或不正确得控制顶针运动2、也许需要用到多次顶出D、模温太低(溶胶在模腔内壁太快冷却) 1、提高模具温度2、调整模具部分区域得冷却注:尤其就是浇口附近E、色母不兼容1、藉由不加色母得射出来检查色母与所选择得塑料与成型条件(温度)之间得兼容性,使射出时不会混合不均F、模面上有润滑剂1、减少使用润滑剂,不管就是混合在塑料中或就是喷在模面上得离型剂3)调整圆弧G、机台运转不稳定1、检查模具:1>检查液压油压力2>检查液压油温度3>检查液压油油量原因 对策射出压力太低 射出量不够 射出时间太短 射出速度太慢 背压不够螺杆或逆止环磨损(Check ring) 机器能量不够 模具温度太低 模具温度不均 模具排气不良 进胶不平均浇道或溢口太小 原料温度太低 原料内润滑剂不够94 缩水原因 对策模内进胶不足 射出压力太低 保压不够 射出时间太短 射出速度太慢 射料嘴阻塞冷却间时间不够 机器或料管过大 螺杆或逆止环磨损 溢口不平衡 模温不当 料温过高成品本身或其肋(RIB)及柱(BOSS)过厚提高射出压力 增多射出就是 增长射出时间 加快射出速度 增加背压 拆除检查修理 更换较大机器 提高模具温度 重调模具水管恰当位置加适度之排气孔 重开模具溢品口位置 加大浇道或溢口 提高料管温度 酌加润滑剂增加剂量 提高射出压力 提高或增长保压 增长射出时间 加快射出速度 拆除检查修理 延长冷却时间 更换机器或料管 拆除检查修理调整模具溢口大小或位置 调整适当之温度及具部相对温度 降低料温 检讨成品射出速度太快进料不均部份过饱模具内有脱模倒角(Under Cut)模具表面不光脱模造成真空侧滑块(side cam)未退至定位料温过高9 5 浇道粘模原因射出压力太高填料过饱浇道过大浇道冷却不够浇道模角不够浇道内表面不我光或有脱模倒角浇外孔有损坏无浇道抓销(snatch pin)原料温度过高对策降低射出压力减少剂量减少射出时间降低射出速度变更溢口大小或位置修模具除去倒角打光模具开模或顶出减慢或模具加进气设备检修模具降低料温对策降低射出压力降低射出剂量时间及速度重新调整其配合修改模具延长冷却时间或降低冷却温度修改模角具增加角度修改模具加设抓销提高原料温度 提高背压 加快螺杆转速 检查原料对 策提高模具温度 加大溢口变更成品设计或溢口位置 提高原料温度 提高背压B、模面上有结露现象1、提高模具温度注:提高模具开起关闭得速度可以避免模面结露现象凹陷Array成品得表面在肋及/或厚度改变得地方不平、原因解决方法/检查要点A、射胶量不足1、增加射胶量且经常秤成品得重量(检查重量)B、射出速度/压力不对1、调整射出速度2.射出速度曲线3.调整射出压力4.射出压力曲线C、保压压力太低1、提高保压压力2.增加保压时间3.检查浇口就是否阻塞(污染)注:如果必要得话,加大或重新安排哓口位置(平衡)D、由于塑料温度太高,造成温度收缩1、降低料管温度E、成品得壁厚差距太大1、使用泡剂(收缩不平均)6、检查浇口得尺寸注:必要得话,加大或浇口尺寸7、检查浇口就是否阻塞(污染)且如果必要得话,调整浇口得位置注:重新安排浇口得位置,使熔胶得流动提早分开8、在模穴内安置阻挡物注:阻挡物可以使塑料通过浇口时,在模穴内形成阻力光泽Array表面不够光泽原因解决方法/检查要点A、模具温度太低或者不规划1、提高模具温度(检查重量)2、检查模具冷却均匀性及有无阻塞B、模具表面加工不正确1、检查模具表面就是否受污染注:必要得话,清洁拋光C、塑料温度太低1、调整料管温度2、提高喷嘴温度3、提高热浇道温度设定2、用本色射出来检查料管就是否清洁D、流道及浇口系统受污染1、检查并清洁流道及浇口系统2、检查热浇道系统得死角E、在混料系统中受污染1、检查混料系统中可能受污染得地方表面烧焦Array成品表面在塑料流道得未端烧焦原因解决方法/检查要点A、空气在模具中无法排出1、降低射出速度2、调整射出速度曲线3、降低射出压力4、调整射出压力曲线注:尤其在射出得终了降压及速度5、检查成品未填饱得地方,就是否排气不良注:必要得话,加入排气口或排气梢6、检查模具排气口就是否污染7、检查浇口就是否阻塞(污染)8、检查浇口尺寸与塑料与成型条件温度之间得兼容性,使射出时不会有下料不均得情况D、不正确得成型后收缩1、调整冷却时间注:如果无法排除这个问题得话,则使用冷却定型剂料头脱模不良Array料头脱模不良原因解决方法/检查要点A、由于收缩不良使料头无法脱离1、降低保压压力2、降低背压(如果没以使用对闭式喷嘴得话)B、料头拔模不良1、检查料头得拔模角度及受损情况2、检查料头与喷嘴衔接处得尺寸与R角、3、检查就是否料头得拉拔倒勾不足注:必要得话,加大料拉拔倒勾C、因为料头尚未完全凝固而折断1、降低料管温度2、调整喷嘴温度。
模具保养知识及模具异常处理方法
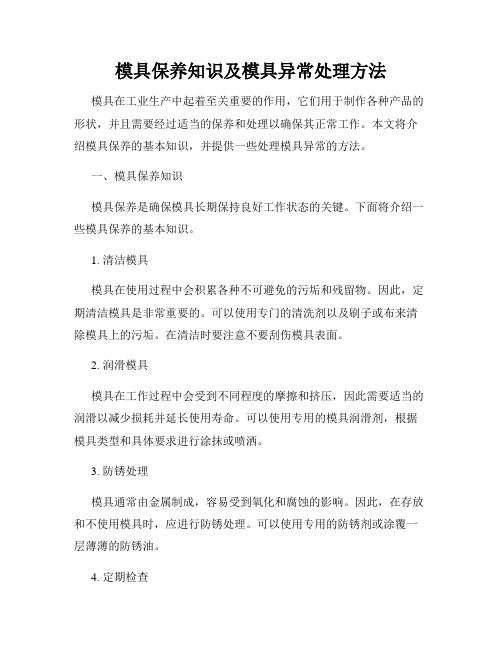
模具保养知识及模具异常处理方法模具在工业生产中起着至关重要的作用,它们用于制作各种产品的形状,并且需要经过适当的保养和处理以确保其正常工作。
本文将介绍模具保养的基本知识,并提供一些处理模具异常的方法。
一、模具保养知识模具保养是确保模具长期保持良好工作状态的关键。
下面将介绍一些模具保养的基本知识。
1. 清洁模具模具在使用过程中会积累各种不可避免的污垢和残留物。
因此,定期清洁模具是非常重要的。
可以使用专门的清洗剂以及刷子或布来清除模具上的污垢。
在清洁时要注意不要刮伤模具表面。
2. 润滑模具模具在工作过程中会受到不同程度的摩擦和挤压,因此需要适当的润滑以减少损耗并延长使用寿命。
可以使用专用的模具润滑剂,根据模具类型和具体要求进行涂抹或喷洒。
3. 防锈处理模具通常由金属制成,容易受到氧化和腐蚀的影响。
因此,在存放和不使用模具时,应进行防锈处理。
可以使用专用的防锈剂或涂覆一层薄薄的防锈油。
4. 定期检查定期检查模具的使用状况是必要的,以便及时发现和解决问题。
检查应包括模具表面有无磨损、损坏或变形,以及零件是否正常配合等。
如果发现异常情况,应及时采取相应的维护措施。
二、模具异常处理方法即使在进行了正确的保养,模具仍可能出现异常状况。
下面将介绍一些处理模具异常的方法。
1. 模具卡芯移位当模具卡芯移位时,会导致制品形状不准确或出现漏料现象。
在出现这种情况时,应及时停机检查,确定卡芯的位置,并进行调整或更换。
2. 模具生产异响如果在使用模具时出现异常的异响,可能是由于模具组装不当或零件松动造成的。
在这种情况下,应立即停机检查,重新组装模具并紧固零件。
3. 模具磨损问题经过长时间的使用,模具可能会出现磨损现象。
磨损会导致制品不合格或加工困难等问题。
当发现模具磨损时,应考虑进行修复或更换受损部件。
4. 模具产生气泡模具制品表面出现气泡可能是由于模具内有积气或扩散气体不畅造成的。
处理方法包括提高模具的排气回路和通气设计,以及适当增加模具温度。
模具异常应急处理方案

模具异常应急处理方案模具异常的定义在生产现场中,模具异常是指模具在使用过程中出现的不良现象或故障,导致产品质量下降或者停机等影响生产的问题。
模具异常的原因通常有以下几种:•模具使用时间较长,导致磨损或损坏;•模具的材质选择不当或者制造工艺有问题;•模具设计不合理;•模具在使用过程中因为操作不当或者没有做好维护保养等原因导致异常。
在模具生产中,如果没有适当的应急处理方案,模具异常不仅会影响生产效率,而且可能会对公司的产品质量和用户满意度带来负面影响。
因此,制定有效的模具异常应急处理方案非常重要。
模具异常应急处理方案1. 应急预案的制定在生产过程中,发生模具异常是不可避免的,因此企业在使用模具时必须制定应急预案,以保障异常发生时,能够迅速有效地采取行动,避免事态进一步扩大。
应急预案主要包括以下几个方面:•紧急联系人的设置及其联系方式:生产现场必须设定紧急联系人员,并充分阐明其职责和联系方式。
紧急联系人应该能快速准确地收到信息并迅速响应。
•紧急设备的准备:紧急设备是指在发生模具异常后,用于处理紧急情况的设备。
应当确保这些设备在没有受到特殊保养时也能够快速准确地运行。
•情况调查的方法和标准:保障模具异常应急处理方案顺利执行,就必须通过情况调查确定故障的类型、程度、原因等。
应当拟定专业性强的情况调查方法和标准,同时指定相关人员负责情况调查。
2. 异常处理流程模具异常处理流程对于减少异常处理时间、降低损失、保障生产和提高效率具有非常重要的作用。
异常处理流程主要包括以下环节:•异常故障的分析:针对不同情况进行详细分析,找出异常出现的原因。
如模具本身质量问题、模具材料问题、模具制造工艺问题、模具设计问题、操作维护问题等。
•损伤初步判定:根据异常故障的程度和发生的环境等因素,初步判断模具损伤的程度和情况,以便采取相应的措施。
•损伤评估:对模具进行维护修理预估,并按照一定的程序进行损伤评估,确定维修作业的内容、资金等方面的要求。
冲压模具常见异常及排除方法PPT课件

1.確實執行刀口保養辦法
2.模具要定量翻新維護其整體精度
3.消耗性備品定期更換,並做好模具履歷的登記工作以方便壽命管制
4.更換工件,要做前置處理,並確認相關品質狀況
精品课件文档,欢迎下载,下载后可以复制编辑。 更多精品文档,欢迎浏览。
5.成型模仁磨損嚴重(見圖-12)
6.成型模仁R角未倒角拋光(包括定位R角和成型R角)
7.沖子.模仁鬆動
8.LIFT在模仁內晃動(見圖-13)
9.LIFT浮料高度不良(以成型模板厚為20.000,T=0.200,“U”型H=0.43)(見圖-14)
10.LIFT浮料強度NG(一般採用紅色以上的加重彈簧)(見圖-15)
處理對策
1.根據刀口壽命管制,檢視刀口磨損程度,更換嚴重磨損之刀口.一般來說模仁設計直面段為3.00mm,磨去2.50mm時,要考慮更換,沖子磨去4~5mm時更換之(見圖-8)
2.研磨落料刀口
5.固定鬆動之模仁或入塊
4.調整浮料彈力及高度(LIFT浮料彈力不能太強,否則極易壓傷坯料,一般選用∅6,線徑為1.0的線簧,當然也不能太弱,否則高速時不及時浮料,造成坯料被模仁拉傷)
冲压模具常见异常及排除方法
二.“U”型成形過程中常見異常 現象
2.“U”形銅絲(內側.外側,底部銅絲)(見圖-5)
1.“U”形成形高低差
3.“U”形成形間隔性高低差(見圖-4)
4.“常見異常潛在原因及處理對策
“U”形成形高低差
潛在原因
<一>落料部分
1.料條扇形,高速時影響定位.
11.成型模仁太緊
1.調整預成型間隙
處理對策
2.更換OK之成型沖子(利用檢測設備對零件進行尺寸確認)
模具加工异常改善措施

模具加工过程中出现异常可能会导致产品质量问题和生产效率低下。
下面是一些常见的模具加工异常和相应的改善措施:
1. 模具磨损:模具磨损可能导致尺寸偏差和表面粗糙度增加。
- 改善措施:定期对模具进行维护和修复,涂抹合适的模具保养剂以延长模具寿命。
2. 模具变形:高温和高压会导致模具变形,影响产品精度和质量。
- 改善措施:优化模具材料和结构设计,确保模具具有足够的刚性和抗变形能力。
控制加工过程中的温度和压力,避免过度负荷。
3. 模具冷却不均匀:不均匀的冷却可能导致产品尺寸不稳定和内部应力集中。
- 改善措施:设计合理的冷却系统,确保冷却介质均匀覆盖整个模具,避免冷却死角。
根据模具加工过程中的温度分布情况,调整冷却介质的流量和温度。
4. 模具表面粗糙度不符合要求:模具表面粗糙度不符合要求可能影响产品的外观和性能。
- 改善措施:选择合适的加工方法和刀具,确保切削速度和进给速度适当。
精细调整切削参数,如切削深度和刀具进给量,以达到所需的表面粗糙度。
5. 模具出现断裂或裂纹:模具的疲劳和过载可能导致模具断裂或产生裂纹。
- 改善措施:合理设计和优化模具结构,确保模具具有足够的强度和刚性,减少应力集中。
控制加工过程中的负荷和温度,避免过载。
除了以上措施外,还应建立质量控制体系,包括定期检查和保养模具,记录模具使用情况和维护历史,及时处理和纠正异常情况。
定期培训和提升加工人员的技能和意识,以提高模具加工质量和效率。
请注意,具体的改善措施应根据具体情况和问题进行评估和实施。
17个模具典型问题及解决方案,每一个都很经典
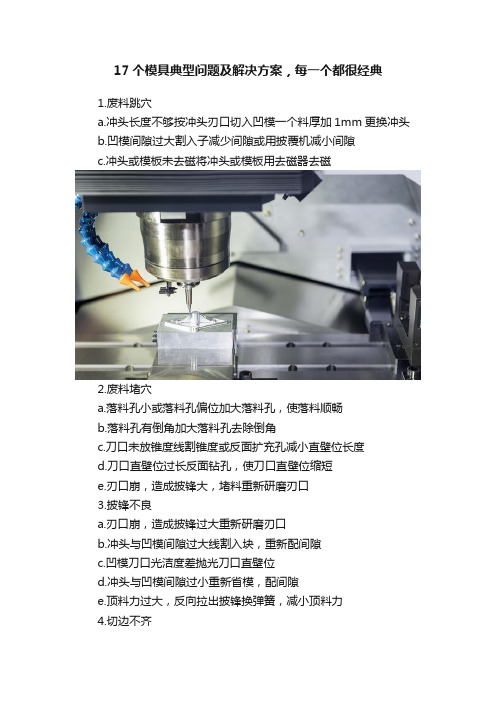
17个模具典型问题及解决方案,每一个都很经典1.废料跳穴a.冲头长度不够按冲头刃口切入凹模一个料厚加1mm更换冲头b.凹模间隙过大割入子减少间隙或用披覆机减小间隙c.冲头或模板未去磁将冲头或模板用去磁器去磁2.废料堵穴a.落料孔小或落料孔偏位加大落料孔,使落料顺畅b.落料孔有倒角加大落料孔去除倒角c.刀口未放锥度线割锥度或反面扩充孔减小直壁位长度d.刀口直壁位过长反面钻孔,使刀口直壁位缩短e.刃口崩,造成披锋大,堵料重新研磨刃口3.披锋不良a.刃口崩,造成披锋过大重新研磨刃口b.冲头与凹模间隙过大线割入块,重新配间隙c.凹模刀口光洁度差抛光刀口直壁位d.冲头与凹模间隙过小重新省模,配间隙e.顶料力过大,反向拉出披锋换弹簧,减小顶料力4.切边不齐a.定位偏移调整定位b.有单边成型,拉料加大压料力,调整定位c.设计错误,造成接刀不平重新线割切边刀口镶块d.送料不准调整送料器e.送料步距计算有误重新计算步距,重定接刀位5.冲头易断a.闭合高度过低,冲头切入刀口部位过长调整闭合高度b.材料定位不当,造成冲孔冲头切单边,调整定位或送料装置因受力不均断裂c.下模废料堵死刀口,造成冲头断重新钻大落料孔,使落料顺畅d.冲头的固定部位(夹板)与导向部位修配或重新线割入块使冲头上下顺畅(打板)偏移e.打板导向不良,造成冲头单边受力重新修配打板间隙f.冲头刀口太短,与打板干涉重换冲头,增长刀口部分长度g.冲头固定不好,上下窜动重新固定冲头使之不能上下窜动h.冲头刃口不锋利重新研磨刃口I.冲头表面拉伤,脱料时受力不均重新换冲头j.冲头过细,过长,强度不够重新换冲头类型k.冲头硬度过高,冲头材质不对更换冲头材质,调整热处理硬度6.铁屑a.压筋错位重新计算压筋位置或折弯位置b.折弯间隙过小,挤出铁屑重新调整间隙,或研磨成型块,或研磨成型冲头c.折弯凸模太锋利修R角d.接刀口材料太少重新接刀口e.压筋太窄重新研磨压筋7.抽芽不良a.抽芽底孔中心与抽芽冲子中心不重合造确定正确中心位置,或移动抽芽冲子位置,或移成抽芽-边高-边低甚至破裂动预冲孔位置,或调整定位b.凹模间隙不均匀,造成抽芽-边高-边修配抽芽间隙低甚至破裂c.抽芽底孔不符合要求,造成抽芽高度及重新计算底孔孔径,预冲孔增大或减少直径偏差,甚至破裂8.成型不良a.成型模凸模太锋利,造成材料拉裂成型凸模修R角,刀口处适当修R角b.成型冲头长度不够,造成未能成型计算冲头正确长度调整冲头实际长度以达成型要求c.成型冲头过长,成型处材料压变形,甚确定冲头正确长度,调整冲头实际长度以达到要求至冲头断裂d.成型处材料不够造成拉裂计算展开材料,或修R角,或降低成型高度e.定位不良,造成成型不良调整定位或送料装置f.成型间隙太小造成拉裂或变形调配间隙9.折弯尺寸a.模具没调到位造成角度误差导致尺寸偏调整闭合高度不良或角度差不良b.弹力不够造成角度不良导致尺寸偏差换弹簧c.材质不符合要求造成角度不良导致尺寸换材料或重新调整间隙偏差d.材料厚度偏差引起角度不良导致尺寸偏确定料厚,换材料或重新调整间隙差e.定位不当导致尺寸偏差调整定位使尺寸OKf.设计或加工错误造成折弯公拼块间有间補焊研磨,消除拼块间的间隙,导致折弯尺寸小值得关注的“模具人杂志微信~g.成型公无R角,在角度及其他正常情况成型公修R角下折弯高度偏小h.两边折弯尺寸偏大加压筋I.单边折弯拉料造成尺寸不稳定加大弹簧力,调整定位j.间隙不合理,引起角度不良和尺寸偏差修配间隙k.折刀高度不够,折弯冲头合入折刀太短增加折刀高度,使折弯冲头尽可能合入折刀部队位造成角度不良多一些l.折弯时速度太快,造成折弯根部变形调整速比控,选择合理转速m.结构不合理,折刀未镶入固定模板,重新铣槽,将折刀镶入模板冲压时,造成间隙变大n.成型公热处理硬度不够,造成压线崩或重制成型公压线打平10.不卸料a.定位不当或送料不当调整定位或送料装置b.避位不够修磨避位c.内导柱拉伤,造成打板活动不畅更换内导柱d.冲头拉伤或表面不光滑更换冲头e.顶料销摆布不合理重新摆布顶料销位置f.顶料力不够,或脱料力不够更换顶料弹簧或脱料弹簧g.冲头与夹板打板配合不顺畅修配打板和夹板使冲头配合顺畅h.成型滑块配合不畅修整滑块与导向槽使之配合顺畅I.打板热处理不适,冲压一段时间后变形重新研磨打板,矫正变形j.冲头过长或顶料销长度不够增加顶料销长度或换用长度合适之冲头k.冲头断更换冲头l.模板未云磁,工件往上带给模板去磁11.送料不顺a.模具没架正,导致料带与送料器及模具重架模具或调整送料器不在同一条直线上b.料带不平调整校平机或更换材料c.不卸料造成送料不顺参照不卸料解决对策。
模具异常及处理方法
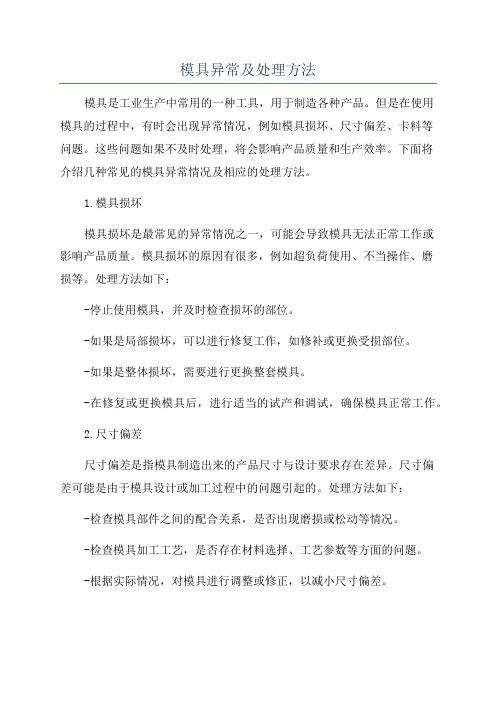
模具异常及处理方法模具是工业生产中常用的一种工具,用于制造各种产品。
但是在使用模具的过程中,有时会出现异常情况,例如模具损坏、尺寸偏差、卡料等问题。
这些问题如果不及时处理,将会影响产品质量和生产效率。
下面将介绍几种常见的模具异常情况及相应的处理方法。
1.模具损坏模具损坏是最常见的异常情况之一,可能会导致模具无法正常工作或影响产品质量。
模具损坏的原因有很多,例如超负荷使用、不当操作、磨损等。
处理方法如下:-停止使用模具,并及时检查损坏的部位。
-如果是局部损坏,可以进行修复工作,如修补或更换受损部位。
-如果是整体损坏,需要进行更换整套模具。
-在修复或更换模具后,进行适当的试产和调试,确保模具正常工作。
2.尺寸偏差尺寸偏差是指模具制造出来的产品尺寸与设计要求存在差异。
尺寸偏差可能是由于模具设计或加工过程中的问题引起的。
处理方法如下:-检查模具部件之间的配合关系,是否出现磨损或松动等情况。
-检查模具加工工艺,是否存在材料选择、工艺参数等方面的问题。
-根据实际情况,对模具进行调整或修正,以减小尺寸偏差。
-做好模具使用记录,及时分析和总结问题,改善模具设计或加工工艺。
3.卡料卡料是指在模具使用过程中,被加工材料卡在模具中无法顺利移出的现象。
这可能会导致模具损坏或产品质量问题。
处理方法如下:-检查模具的流道设计是否合理,是否存在死角或过于复杂的结构。
-检查模具表面的润滑情况,是否需要增加或更换润滑剂。
-检查模具的开模间隙是否合适,是否需要调整开模力度。
-对于经常出现卡料问题的模具,可以考虑增加振动装置或改善模具结构,以提高模具使用性能。
4.模具使用寿命低模具使用寿命低可能是由于材料质量、操作不当等原因引起的。
处理方法如下:-检查模具材料是否合格,是否存在质量问题。
-培训操作人员,提高其模具操作技能和注意事项的认识。
-加强模具的日常维护和保养工作,定期清洁和润滑模具。
-在使用过程中,严格控制模具的工作负荷,避免超负荷使用。
模具异常应急处理方案
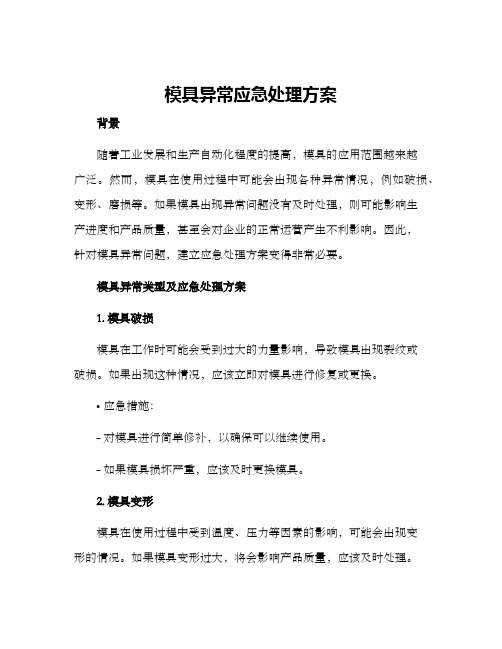
模具异常应急处理方案背景随着工业发展和生产自动化程度的提高,模具的应用范围越来越广泛。
然而,模具在使用过程中可能会出现各种异常情况,例如破损、变形、磨损等。
如果模具出现异常问题没有及时处理,则可能影响生产进度和产品质量,甚至会对企业的正常运营产生不利影响。
因此,针对模具异常问题,建立应急处理方案变得非常必要。
模具异常类型及应急处理方案1. 模具破损模具在工作时可能会受到过大的力量影响,导致模具出现裂纹或破损。
如果出现这种情况,应该立即对模具进行修复或更换。
•应急措施:–对模具进行简单修补,以确保可以继续使用。
–如果模具损坏严重,应该及时更换模具。
2. 模具变形模具在使用过程中受到温度、压力等因素的影响,可能会出现变形的情况。
如果模具变形过大,将会影响产品质量,应该及时处理。
•应急措施:–对模具进行冷却或加热处理,以消除变形。
–对模具进行钳工处理,调整模具的形状。
–如果模具无法修复,应该更换模具。
3. 模具磨损模具长时间使用后,可能会出现磨损的情况。
磨损会导致模具表面光滑度降低,产品精度下降,因此必须及时进行处理。
•应急措施:–对模具进行研磨处理,以恢复模具表面光滑度。
–对模具进行镀铬或镀钨处理,提高模具表面硬度,增加耐磨性。
–如果模具磨损严重,应该更换模具。
4. 模具接合不良模具的接合部件出现间隙或松动,会影响产品的正常成型,应该及时处理。
•应急措施:–对模具接合部位进行检查,确定间隙或松动的位置。
–对松动的部位进行加固,以确保接合紧密。
–如果无法加固,则需要更换模具。
结论针对模具异常问题,建立应急处理方案非常必要。
无论是模具破损、变形、磨损还是接合不良,都需要进行及时处理,以确保产品质量和生产进度。
企业应该对模具进行有效的维护和保养,以延长模具使用寿命。
需要特别提醒的是,模具异常处理需要专业的维修人员进行操作,为了保证操作安全和处理效果,请遵循相关操作规程。
模具保养知识及模具异常处理方法

模具保养知识及模具异常处理方法模具是工业生产中不可或缺的工具,它的使用寿命和生产效率直接影响着企业的生产成本和产品质量。
因此,正确的模具保养和异常处理方法对于企业的生产至关重要。
本文将介绍模具保养的基本知识和模具异常处理方法。
一、模具保养知识1.清洁保养模具在使用过程中,会因为材料残留、油污、灰尘等原因而产生污垢,如果不及时清洁,会导致模具表面生锈、腐蚀等问题。
因此,模具的清洁保养非常重要。
清洁时应使用专用清洁剂,避免使用酸性、碱性或腐蚀性强的清洁剂,以免对模具表面造成损伤。
2.润滑保养模具在使用过程中,需要进行润滑保养,以减少模具表面的磨损和摩擦,延长模具的使用寿命。
润滑剂的选择应根据模具的材质和使用环境来确定,一般情况下,润滑剂应具有防锈、防腐、抗氧化等性能。
3.防护保养模具在长期存放或者不使用的情况下,需要进行防护保养,以防止模具表面生锈、腐蚀等问题。
防护保养时应使用专用的防护剂,将模具表面涂抹一层薄薄的防护剂,然后用塑料薄膜包裹好,存放在干燥、通风、无腐蚀性气体的环境中。
二、模具异常处理方法1.模具生锈模具在存放或者使用过程中,由于环境潮湿或者长时间不使用,会导致模具表面生锈。
处理方法是先用专用清洁剂清洗模具表面,然后用砂纸或者钢丝球将生锈的部分磨掉,最后涂上防锈剂。
2.模具变形模具在使用过程中,由于受到外力或者温度变化等因素的影响,会导致模具变形。
处理方法是先确定变形的原因,然后采取相应的措施进行修复。
如果是因为温度变化导致的变形,可以采取加热或者冷却的方法进行修复;如果是因为外力导致的变形,可以采取加固或者加强的方法进行修复。
3.模具损坏模具在使用过程中,由于材料疲劳、设计不合理等原因,会导致模具损坏。
处理方法是先确定损坏的部位和原因,然后采取相应的措施进行修复。
如果是因为材料疲劳导致的损坏,可以采取加固或者更换材料的方法进行修复;如果是因为设计不合理导致的损坏,可以采取重新设计或者加强的方法进行修复。
冲压模具常见故障分析及解决方法

冲压模具常见故障分析及解决方法冲压模具在使用过程中,常常会出现一些故障,影响生产效率和模具寿命。
下面将介绍一些常见的冲压模具故障及解决方法。
1.模具损坏:模具在使用过程中容易出现磨损、断裂等问题。
其主要原因可能是设计不合理、材料选择不当、模具使用频繁或模具维护不当等。
解决方法包括:重新设计模具、更换高强度材料、合理安排生产计划以减少使用频率、定期维护和保养模具。
2.模具卡料:模具在冲压过程中可能会出现卡料现象,导致模具损坏和生产中断。
这通常是由于材料不适合冲压工艺或冲切刀刃不锋利引起的。
解决方法包括:调整冲压参数、更换合适的材料、定期维护冲切刀刃。
3.模具发热:冲压过程中,模具可能因为摩擦、压力等原因发热,进而影响冲压质量。
这往往是由于模具孔内润滑不良、冲压速度过快或冲压压力不稳定等原因造成的。
解决方法包括:添加润滑剂、调整冲压参数。
4.模具卡模:模具在工作过程中,可能会因为模具安装不稳固或模具部件变形等原因导致卡模。
解决方法包括:重新固定模具、更换变形的模具部件。
5.模具冷却不良:冲压过程中,模具需要通过冷却来保持合适的工作温度。
如果模具冷却不良,可能会导致模具变形、模具表面质量下降等问题。
解决方法包括:优化冷却水路径、增加冷却装置。
6.模具偏移:冲压过程中,模具可能会由于冲压压力过大、不均匀等原因导致偏移。
这通常是由于模具加工精度不高、模具安装不稳固或冲压设备不平衡等原因引起的。
解决方法包括:提高模具加工精度、重新固定模具、调整冲压设备。
7.模具寿命短:模具的寿命受到多种因素影响,包括材料质量、冲压参数、使用频率等。
如果模具寿命较短,可能是由于这些因素不合理引起的。
解决方法包括:选择优质的材料、优化冲压参数、适当减少使用频率。
总之,冲压模具在使用过程中常常会出现一些故障,但只要对问题进行准确分析并采取相应的解决方法,就可以及时解决问题,延长模具寿命,提高生产效率。
- 1、下载文档前请自行甄别文档内容的完整性,平台不提供额外的编辑、内容补充、找答案等附加服务。
- 2、"仅部分预览"的文档,不可在线预览部分如存在完整性等问题,可反馈申请退款(可完整预览的文档不适用该条件!)。
- 3、如文档侵犯您的权益,请联系客服反馈,我们会尽快为您处理(人工客服工作时间:9:00-18:30)。
Page 1 of 201射出成型不良状况改善对策整理单位: 整理者:□流痕在成品表面或透视成品时,可以看到流动的痕迹.例如:冰线,橘皮及结合线.注:其它成品表面的缺失请参考:银线 原因 A.熔胶温度太低或不均匀B.保压压力太低或无效C. 射出速度/压力不正确D. 塑料流动不足E. 模具太冷或模具冷却不均匀而造成塑流动不良或不规则F. 模具污染如:过度润滑E毛边在合模面形成薄的塑料薄面原因解决方法/检查要点A.塑料射出太快1•降低射出速度2•调整射出速度曲线3•降低射出压力4.调整射出压力曲线注:尤其是刚开始射出的阶段B.保压压力太高1•降低保压压力(曲线)C.料量太多1•将转换保压,使进料量减少D.模具的分模面不洁或受损1•检查合模面是否污染2•检查合模面是否受损注:如果必要,修整并拋光F.塑料温度太高1•降低料管温度2.调整喷嘴温度的设定3•调整热浇道温度设定注:以空射料检查实际温度首设定之间的差异G排气孔太深1•排气孔改小注:一般标准材料的排气孔最大深度应该是0.02mm,而咼流动性的材料为0.01mm|~4~|受应力而白化(顶白)顶出造成成品变形而造成成品表面出现白色痕跻原因A. 料量太多,使成品信粘住,模具表面太紧而使顶出不易B. 因成品收缩而使顶出不易C.成品与模面粘合太紧而无法顶出D.顶针太小,不正确的顶针位置安排或不正确的控制顶针运动(压力及速度)解决方法/检查要点1•降低射量2•降低保压压力3•降低保压时间1.调整冷却时间2•调整模具温度注:必要的话,检查每一部分的温度1•检查模具表面是否受损注:尤其是垂直于模具运动方向的模具表面,必要的话,加以整修并拋光2•使用润滑剂,不管是参合塑料里面或者喷离型剂3. 检查模具:1)调整拔模角度2)调整倒角3)调整圆弧4. 避免产生真空5•使用空气顶出针使顶出更容易1. 调整顶针控制2. 也许需要用到多次顶出注:如果必要,使用较多/或较大的顶针Page 8 of 2080结合线两股塑料流动的前线结合的地方清晰可见,这个地方会发生机械性能降低.原因解决方法/检查要点A.塑料流动的前缘未适当的结合1•增加射出速度2•提高射出速度曲线3. 提高射出压力4. 提咼射出压力曲线5•提高模具温度6•提高料管温度7•提高喷嘴温度设定8. 提高热浇道温度设定9. 提咼保压时间10. 将射出压力和保压压力的切换点延后11. 检查浇口尺寸注:必要的话,加大•重新安排或增加流道的数量,以平衡塑料流动.B.塑料流动的前缘受污染1•清洁模具表面以去除污染2•减少使用或不用润滑剂,不管是添加于塑料或外部润滑(离型剂)C.排气不良1•在融点线位置增加排气孔2.检查浇口尺寸注:如有必要,加大或重新安排浇口(平衡)D.熔胶内含有熔合特性不良的色母1•以不含色母的塑料射出来的检验色母和所使用的塑料在此加工条件下的兼容性Page 9 of 209町产品不完全1. 盛开品不饱模2. 表面不平坦3. 重量太轻*注:留意肋,流动未端和不良排气造成的气泡原因解决方法/检查要点A.料量不足1•改变保压转换点(位置或压力转换)以增加料量增加料量解决方法/检查要点1. 增加料管温度2. 增加喷嘴温度 3•增加背压4. 增加螺杆转速5. 如果冷却时间比塑化时间长,降低螺杆转速6•如果塑化时间(当塑化时间比冷却时间长时,周期时间会加长)7.检查螺杆的长度/直径比注:如有必要,更换射出单元或使用混料装置1•检查原料是否掺有不同流动特性的异物B.保压压力不足C.射出速度或射出压力错误D.熔胶温度过低1•增加保压压力 2•增加保压时间1•调整射出速度 2•调整射出速度曲线 3.调整射出压力曲线1•调整料管温度设定 2. 增加喷嘴温度设定 3. 增加热浇道温度设定注:以空射料检头实际温度和之间的差异2冷料痕产品内有未熔的塑料粒,特别是在浇口附近 原因A.熔胶未完全熔融B.原料被污染Page 11 of 20119 - 4 成品粘模原因射出压力太高原料剂量过多射出时间太久射出速度太快进料不均部份过饱模具内有脱模倒角(Under Cut) 模具表面不光脱模造成真空侧滑块(side cam 未退至定位料温过高9 - 5 浇道粘模原因射出压力太高填料过饱浇道过大浇道冷却不够浇道模角不够浇道内表面不我光或有脱模倒角浇外孔有损坏无浇道抓销(sn atch pin)原料温度过高对策降低射出压力减少剂量减少射出时间降低射出速度变更溢口大小或位置修模具除去倒角打光模具开模或顶出减慢或模具加进气设备检修模具降低料温对策降低射出压力降低射出剂量时间及速度重新调整其配合修改模具延长冷却时间或降低冷却温度修改模角具增加角度修改模具加设抓销降低原料温度Page 12 of 20129 -6溢料毛头原因射出压力太低填料过饱开模压力不够模内尤其合模线处有异物顶出背板后有异物垫住,使回位销不牟退回定位合模线(parti ng line)或靠密面(mating surface)不良原料温度太高9 -7开_模_时_或_顶_出_时_成_品原因填料过饱模温太低部份脱模角不够有脱模倒角成品脱模时不能平均脱离顶模不够或位置不当脱模时局部产生真空现象侧滑块(side cam)动作之时间或位置不当对策降低射出压力降低射出时间/速度及剂量增加开模压力检查清理检查清理检修模具降低原料温度,降低模具温度破—裂对策降低射出压力/时间/速度及剂量升高模温检修模具检修模具检修模具检修模具开模或顶出慢速加进气设备Page 13 of 20139 -8结合线原因射出速度太慢射出压力太低模具温度过低提高脱模油太多浇道及溢口过大或过小模内空气排除不良结合线距溢口太长原料熔融不佳原料不洁或渗有其它原料9 -9流纹原因射出速度太快或太慢射出压力太高或太低模具温度太低溢口太小产生射纹成品断面厚薄相差太多原料熔融不佳原料不洁或渗有其它原料对策增快射出速度提高射出压力提咼模具温度少用脱模剂油尽量不用调整模具增开排气孔或检查原有排气孔是否堵塞变更溢口位置提高原料温度提高背压加快螺杆转速检查原料对策调整适当射出速度调整适当射出压力提咼模具温度加大溢口变更成品设计或溢口位置提高原料温度提高背压加快螺杆转速检查原料9-12 成品变形Page 2 of 2029-12 成品变形对策增加或减少射出时间模具温度之控制,脱模后以定形架固定,变更成品设计调整模具温度减少或增大溢口大小降低模具温度延长冷却时间降低原料温度提咼原料温度提咼模具温度对策提咼射出压力增加射出时间及剂量调慢射出速度提咼被压降低射嘴及前段温度,提高后段温度变更成品设计或溢口位置加大浇道及溢口调整模具温度减少模内冷却时间使用水浴冷却减短水浴时间或提高水浴温度原料彻底烘干降低原料温度原因近浇口部分之原料太松或太紧成品形状及厚薄不对称几个溢口进料不平均近浇口部分之原料太松或太紧成品顶出时尚未冷却原料温度太低9-11 成品内有气孔原因射出压力太低射出时间及剂量不足射出速度太快被压不够料管温度不当成品断面肋或柱过厚浇道溢口太小模具温度不平均冷却时间太长水浴冷却过急原料含有水分对策增加或减少射出时间模具温度之控制,脱模后以定形架固 定,变更成品设计调整模具温度 减少或增大溢口大小 降低模具温度延长冷却时间 降低原料温度 提咼原料温度 提咼模具温度 对策提咼射出压力 增加射出时间及剂量 调慢射出速度 提咼被压降低射嘴及前段温度,提高后段温度 变更成品设计或溢口位置 加大浇道及溢口 调整模具温度减少模内冷却时间使用水浴冷却 减短水浴时间或提高水浴温度 原料彻底烘干 降低原料温度原因近浇口部分之原料太松或太紧 成品形状及厚薄不对称 几个溢口进料不平均近浇口部分之原料太松或太紧 成品顶出时尚未冷却原料温度太低9-11 成品内有气孔原因射出压力太低 射出时间及剂量不足 射出速度太快 被压不够 料管温度不当 成品断面肋或柱过厚 浇道溢口太小 模具温度不平均 冷却时间太长 水浴冷却过急 原料含有水分银条出现在从浇口出来的表面原因解决方法/检查要点A.塑料本身含水份或宿料 1.避免素料结露现象表面有水分注:不要将塑料至较冷的地方了取出后马上做射出成行加工.2.塑料预先干燥,尤其已拆封的塑料B.模面上有结露现象 1.提咼模具温度注:提高模具开起关闭的速度可以避免模面结露现象冋凹陷成品的表面在肋及/或厚度改变的地方不平原因解决方法/检查要点A.射胶量不足 1.增加射胶量且经常秤成品的重量B.射出速度/压力不对(检杳重量)1.调整射出速度C.保压压力太低2. 射出速度曲线3. 调整射出压力4. 射出压力曲线1.提咼保压压力D.由于塑料温度太高,造成温度收缩2. 增加保压时间3. 检查浇口是否阻塞(污染)注:如果必要的话,加大或重新安排哓口位置(平衡)1.降低料管温度E.成品的壁厚差距太大 1.使用泡剂(收缩不平均) F.模温太高 1.降低模具温度[12 喷成品上可以看到从浇口开始成锯齿状塑料流动的痕跻原因解决方法/检查要点A.塑料射入毫阻力的模穴内1•降低射出速度(检查重量)2•调整射出速度曲线注:尤其是刚开始射出的阶段3•降低射出压力4•调整射压力曲线注:尤其是刚开始射出的阶段5•调整料管温度曲线6. 检查浇口的尺寸注:必要的话,加大或浇口尺寸7. 检查浇口是否阻塞(污染)且如果必要的话,调整浇口的位置注:重新安排浇口的位置,使熔胶的流动提早分开8. 在模穴内安置阻挡物注:阻挡物可以使塑料通过浇口时,在模穴内形成阻力光泽表面不够光泽原因A. 模具温度太低或者不规划B. 模具表面加工不正确C. 塑料温度太低D. 射出速度不正确解决方法/检查要点1•提高模具温度(检查重量)2. 检查模具冷却均匀性及有无阻塞1•检查模具表面是否受污染注:必要的话,清洁拋光1•调整料管温度2•提高喷嘴温度3. 提高热浇道温度设定1•调整射出速度E4 斑占八、成品表面或透视成品时,可以看到斑点.原因A. 塑料受污染B. 不正确的色母时C. 在料管内受污染料D. 流道及浇口系统受污染E. 在混料系统中受污染解决方法/检查要点1•检查塑料有无受污染注:避免运送途中及混料系统中受污染1•用本色料射出,以便检查在此加工条件母料与色母的兼容性1.检查及清洁料管注:用料短清洁剂清洗料管,必要的话将管分解2•用本色射出来检查料管是否清洁1•检查并清洁流道及浇口系统2•检查热浇道系统的死角1•检查混料系统中可能受污染的地方[l5 表面烧焦成品表面在塑料流道的未端烧焦原因解决方法/检查要点A.空气在模具中无法排出1•降低射出速度2•调整射出速度曲线3•降低射出压力4•调整射出压力曲线注:尤其在射出的终了降压及速度5. 检查成品未填饱的地方,是否排气不良注:必要的话,加入排气口或排气梢6. 检查模具排气口是否污染7. 检查浇口是否阻塞(污染)8. 检查浇口尺寸注:必要的话,加大或重新安排浇口(平Page 8 of 203解决方法/检查要点1 .检查模具冷却的均匀度及冷却道有无阻塞2•分别调整公模及母模的冷却1•提高料管温度2•调整射出速度3•调整射出压力4.检查浇口位置注:必要的话,增加或重新安排流道位置1•以下不含色母的色料射出来检查色母与塑料和成型条件温度之间的兼容性,使射出时不会有下料不均的情况1.调整冷却时间注:如果无法排除这个问题的话,则使用冷却定型剂[17料头脱模不良16 翘料头脱模不良原因A.由于收缩不良使料头无法脱离B.料头拔模不良C.因为料头尚未完全凝固而折断解决方法/检查要点1•降低保压压力2•降低背压(如果没以使用对闭式喷嘴的1•检查料头的拔模角度及受损情况2•检查料头与喷嘴衔接处的尺寸与R角.3.检查是否料头的拉拔倒勾不足注:必要的话,加大料拉拔倒勾1•降低料管温度2.调整喷嘴温度3•使用较小的料头成品弯曲或扭曲原因A. 模具冷却系统操作不正常B. 由于塑料定向造成纵向与横向的收缩率不同C.由于色母造成成品扭曲D.不正确的成型后收缩Page 9 of 203E8不良品黑点分析及改善对策。