芳烃联合装置
芳烃联合装置

硫含量,wt%,≯
0.02
蒸发残余物,mg/100ml,≯
二甲苯精馏单元采用精密分馏工艺,将混合芳烃中的C8A、C9A分离出来,分别作为原料提供给吸附分离和歧化单元,从而将联合装置各单元有机的联合起来。二甲苯塔采用加压操作,操作压力为1.0Mpa(a),利用塔顶和塔底高温物流分别作为其它单元集中供热热源,多余的塔顶汽相通过蒸汽发生器发生1.0Mpa蒸汽,全塔的热量均被利用,节能效果显著。
二甲苯异构化单元采用UOP的ISOMAR工艺,选用乙苯异构型I-9K催化剂,在反应过程中建立限定性平衡,通过环烷烃中间体将乙苯最大限度地转化为二甲苯,采用这种催化剂可以从混合二甲苯中获取最高产率的对二甲苯。该催化剂稳定性好,反应压力和氢油比低,不需注氯,减少了系统腐蚀,改善了操作环境。
吸附分离单元采用UOP的PAREX工艺,通过多通道旋转阀实现连续逆流接触,利用分子筛选择吸附PX,再用解吸剂对二乙基苯将PX置换解吸,从而达到分离PX的目的。选用最新分子筛吸附剂ADS-27,改进吸附系统设备和优化工艺参数,增大了吸附塔的处理能力,对二甲苯单程收率可提高到97%,纯度达到99.80%。
5
⑤6#溶剂油及橡胶工业用溶剂油
项目产品
6#溶剂油
橡胶工业用溶剂油
馏
程
初馏点,℃,≮
60
80
98%点,℃,≯
85
110℃馏出量,%,≮
93
120℃馏出量,%,≮
98
残留量,%
1.5
芳烃含量,%,≯
1.5
3.2
溴指数,≯
1000
溴价,≯
0.14
密度(20℃),kg/m3
655-681
色度号,≮
+25
芳烃联合装置的设计优化

芳烃联合装置的设计优化曹坚(中国石化工程建设公司,北京,100101)摘要:以某石化公司拟新建的450 kt/a对二甲苯芳烃联合装置为个案,从技术和经济评价两方面对几个不同处理量的工艺装置的组合方案进行了设计计算,探讨了利用富含芳烃的乙烯裂解汽油作为芳烃原料的可行性和优越性。
关键词:芳烃联合装置优化石油化工厂中的乙烯和芳烃联合装置是最基本的两个基础原料装置,其原料大多来源于石脑油。
因此如何优化乙烯和芳烃原料,减少对原料石脑油的依赖程度,优化芳烃联合装置设计方案,是当前发展石油化工的重要课题。
对二甲苯(PX)主要用于生产精对苯二甲酸(PTA)和对苯二甲酸二甲酯(DMT),而PTA和DMT再和乙二醇、1,4-丁二醇等生成聚对苯二甲酸乙二醇酯(PET)和聚对苯二甲酸丁二醇酯(PBT)等聚酯。
PET、PBT是进一步生产涤纶、聚酯切片、聚酯中空容器和轮胎工业用聚酯帘子布的原材料。
此外,PX还是生产涂料、染料、农药和医药的原料。
在世界合成纤维的产量中涤纶占63%,可以说PX是化纤工业最主要的原料之一。
并且聚酯还是重要的包装材料,在美国,此种用途现已超过纤维。
随着世界聚酯消费量的不断增长,PX的消耗也随之稳步增长。
由于PX装置流程复杂,主要原料通常是石脑油,与上游炼油装置关系紧密,公用工程及储运系统要求高,因此在我国PX装置都建设在炼油厂下游,单独的或民营的PX生产厂目前还没有。
但是以PX作为原料的PTA装置以及再下游的聚酯装置的合资化、民营化投资趋势目前在江浙地区发展很快,正是这一地区的PTA及聚酯装置的飞速发展直接导致了我国在未来几年内PX的严重短缺。
因此,为满足我国PX不断增长的市场需求,未来几年内,除已有PX装置挖潜扩能外,建设新的PX装置势在必行。
1 芳烃原料的优化方案1.1原料选择在石油化工厂中,芳烃联合装置通常以对二甲苯(联产邻二甲苯)为目的产品,作为下游PTA装置的原料。
要生产最大量的对二甲苯,除了催化重整和乙烯裂解汽油中的二甲苯外,主要是采用歧化烷基转移的工艺方法把甲苯和C9芳烃在分子筛催化剂作用下进行歧化和烷基转移反应生成混合二甲苯和苯,混合二甲苯再通过二甲苯临氢异构化工艺转化为对二甲苯。
芳烃联合装置低温热回收技术研究
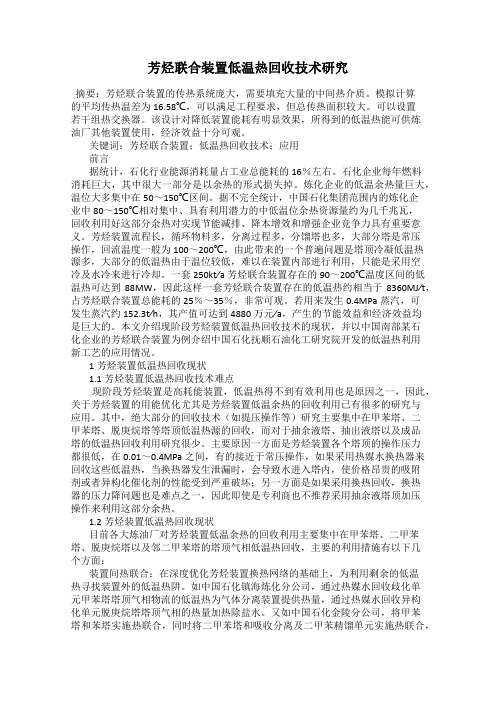
芳烃联合装置低温热回收技术研究摘要:芳烃联合装置的传热系统庞大,需要填充大量的中间热介质。
模拟计算的平均传热温差为16.58℃,可以满足工程要求,但总传热面积较大。
可以设置若干组热交换器。
该设计对降低装置能耗有明显效果,所得到的低温热能可供炼油厂其他装置使用,经济效益十分可观。
关键词:芳烃联合装置;低温热回收技术;应用前言据统计,石化行业能源消耗量占工业总能耗的16%左右。
石化企业每年燃料消耗巨大,其中很大一部分是以余热的形式损失掉。
炼化企业的低温余热量巨大,温位大多集中在50~150℃区间。
据不完全统计,中国石化集团范围内的炼化企业中80~150℃相对集中、具有利用潜力的中低温位余热资源量约为几千兆瓦,回收利用好这部分余热对实现节能减排、降本增效和增强企业竞争力具有重要意义。
芳烃装置流程长,循环物料多,分离过程多,分馏塔也多,大部分塔是常压操作,回流温度一般为100~200℃,由此带来的一个普遍问题是塔顶冷凝低温热源多,大部分的低温热由于温位较低,难以在装置内部进行利用,只能是采用空冷及水冷来进行冷却。
一套250kt∕a芳烃联合装置存在的90~200℃温度区间的低温热可达到88MW,因此这样一套芳烃联合装置存在的低温热约相当于8360MJ∕t,占芳烃联合装置总能耗的25%~35%,非常可观。
若用来发生0.4MPa蒸汽,可发生蒸汽约152.3t∕h,其产值可达到4880万元∕a,产生的节能效益和经济效益均是巨大的。
本文介绍现阶段芳烃装置低温热回收技术的现状,并以中国南部某石化企业的芳烃联合装置为例介绍中国石化抚顺石油化工研究院开发的低温热利用新工艺的应用情况。
1芳烃装置低温热回收现状1.1芳烃装置低温热回收技术难点现阶段芳烃装置是高耗能装置,低温热得不到有效利用也是原因之一,因此,关于芳烃装置的用能优化尤其是芳烃装置低温余热的回收利用已有很多的研究与应用。
其中,绝大部分的回收技术(如提压操作等)研究主要集中在甲苯塔、二甲苯塔、脱庚烷塔等塔顶低温热源的回收,而对于抽余液塔、抽出液塔以及成品塔的低温热回收利用研究很少。
芳烃装置(1)

抽提蒸馏部分工艺流程图(一)
抽提蒸馏部分工艺流程图(二)
二甲苯分馏装置
把混合二甲苯、C9芳烃分离的装置。当有生产邻二甲苯方案时,
拥有抽提、歧化、异构化及吸附分离等芳烃分离专利技术
的公司有数家,各有其特点,且从七十年代开始至今各家 工艺技术和催化剂均不断发展。
预加氢装置
预加氢装置是重整原料的精制装置,目的是脱除石脑
油原料中的硫、氮、砷、铅、铜、烯烃和水等杂质, 保证重整进料中的硫<0.5ppm,氮<0.5ppm,水<4ppm 。 预加氢有循环氢流程或一次通过流程,汽提塔底通常 采用重沸炉加热,采用国产催化剂及工艺技术。
苯
苯是最重要的单环芳烃,也是较为廉价的有机溶剂。
主要用于生产苯乙烯、异丙苯、苯酚、氯苯、烷基苯、 硝基苯、尼龙66盐、苯胺、环己酮、顺酐等衍生物。 也用于农药、医药、染料和部分中间体的生产。 苯的物理性质: 具有特殊芳香味的的液体,熔点5.54℃,沸点 80.1℃,爆炸极限1.5-8.0%,不溶于水、可溶于醇、醚, d420=0.8786,剧毒,有致癌作用。
芳烃联合装置通常包括催化重整、芳烃抽提、歧化及烷基转移、
二甲苯异构化、吸附分离等五项专利技术; 目前拥有全套工艺生产技术的专利商有美国UOP和法国IFP两家, 他们分别开发了分离PX的吸附分离核心技术。 国内外其它公司分别拥有一些单项工艺技术。 UOP拥有生产芳烃的全套专利技术,各项工艺技术先进,尤其 是分离PX的旋转阀模拟移动床吸附分离技术,对二甲苯回收率 高(>97.0%),纯度高(>99.9%),工艺操作简便,安全可靠,安 装方便。 目前UOP已设计和建设了81套装置,其中投产了71套,总PX产 量超过1500万吨/年,装置规模从2.1万吨/年到120万吨/年不等。 目前采用1台V#旋转阀,两台吸附塔最大装置负荷为45-50万吨 对二甲苯/年,采用两台吸附塔和两台V#旋转阀的流程,PX产 品规模可达到100万吨/年。
芳烃部工艺---芳烃部装置简介--81页ppt
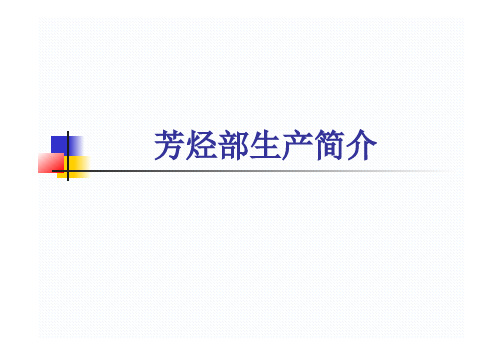
装置概况1#MTBE/1-丁烯装置装置由中国石化总公司齐鲁石化设计院设计,外围工程包括界外管道, 丁烯-1储罐等设计由原上海石化金山设计院负责。
装置设计年处理抽余碳四10万吨/年,甲醇2.68万吨/年,MTBE 产量4万吨/年,2001年改造后提高到7.4万吨/年,丁烯-1产量2.5万吨/年。
装置概况4#汽油加氢装置装置原设计年处理裂解汽油20万吨,装置于1998年4月30日开车一次成功,产出合格加氢汽油。
2002年进行了增量改造,改造后装置处理量增加至30万吨/年裂解汽油(以8000小时计),年产加氢汽油20.52万吨、副产C5馏份5.3万吨、C9馏份4.17万吨。
2008年7月,装置对一、二段催化剂进行了更换,使用了由上海石化研究院设计研究的SHP-01,SHP-02/02F催化剂。
装置概况1#芳烃抽提装置装置是由上海金山设计院根据德国克虏伯公司提供的吗呋啉(NFM)抽提蒸馏专利技术进行设计的国产化芳烃抽提装置,于1998年5月27日开车投料一次成功。
原设计处理能力为30万吨/年加氢汽油,后来因40万吨/年乙烯改扩建工程扩展配套需要,装置于2002年1月进行了扩能改造,改造后处理能力增加至42万吨/年(以8000小时计),装置年产纯苯19.04万吨、甲苯9.8万吨、C8+馏分7.28万吨、抽余油5.88万吨。
装置概况预加氢装置170万吨/年石脑油预加氢处理装置的基础设计是由中国石化集团上海工程有限公司(SSEC)负责设计 。
装置主要产品为精制石脑油,年产量约为161.88万吨,可送往3套连续重整装置作原料。
本装置副产品为含硫轻石脑油,年产量约为8.27万吨,通过管道送往罐区,作乙烯裂解装置原料。
装置概况2#MTBE装置10万吨/年M TBE(甲基叔丁基醚)的基础设计由中国石化集团上海工程有限公司(SSEC)负责设计,山东齐鲁石化工程有限公司提供工艺包,施工建设则有中国石化第五建设工程公司和石建公司承接。
芳烃联合装置关键单元过程优化研究
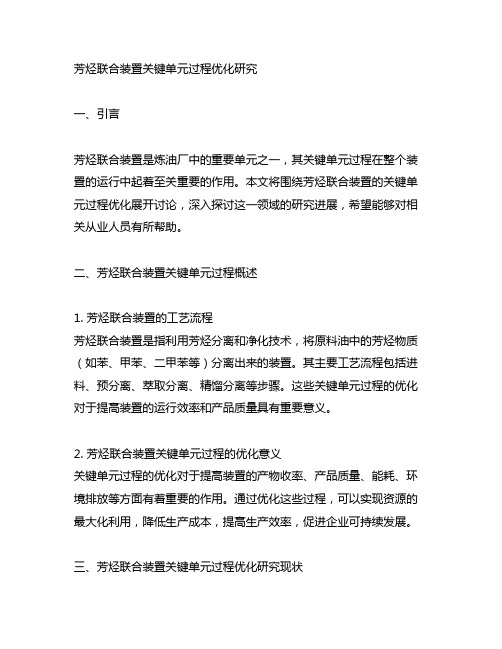
芳烃联合装置关键单元过程优化研究一、引言芳烃联合装置是炼油厂中的重要单元之一,其关键单元过程在整个装置的运行中起着至关重要的作用。
本文将围绕芳烃联合装置的关键单元过程优化展开讨论,深入探讨这一领域的研究进展,希望能够对相关从业人员有所帮助。
二、芳烃联合装置关键单元过程概述1. 芳烃联合装置的工艺流程芳烃联合装置是指利用芳烃分离和净化技术,将原料油中的芳烃物质(如苯、甲苯、二甲苯等)分离出来的装置。
其主要工艺流程包括进料、预分离、萃取分离、精馏分离等步骤。
这些关键单元过程的优化对于提高装置的运行效率和产品质量具有重要意义。
2. 芳烃联合装置关键单元过程的优化意义关键单元过程的优化对于提高装置的产物收率、产品质量、能耗、环境排放等方面有着重要的作用。
通过优化这些过程,可以实现资源的最大化利用,降低生产成本,提高生产效率,促进企业可持续发展。
三、芳烃联合装置关键单元过程优化研究现状1. 传统的关键单元过程优化方法过去,对于芳烃联合装置关键单元过程的优化,主要采用经验分析和现场试验相结合的方法。
这种方法在一定程度上能够改善装置的运行情况,但存在效率低、周期长、成本高等问题。
2. 现代优化技术在芳烃联合装置中的应用随着信息技术和工艺技术的不断发展,现代优化技术在芳烃联合装置中得到了广泛的应用。
基于数学建模、优化算法和人工智能等技术,可以对关键单元过程进行深度优化,实现更精准、更高效的运行。
四、芳烃联合装置关键单元过程优化研究的挑战与未来发展1. 挑战当前在芳烃联合装置关键单元过程优化研究中尚存在一些挑战,如数据获取与建模、优化算法的选择与应用、优化结果的验证与实施等方面需要加强研究。
2. 未来发展方向针对上述挑战,未来的研究可以从以下几个方面展开:一是加强芳烃联合装置过程数据的采集与分析,构建更准确的数学模型;二是结合人工智能和大数据技术,研发更高效的优化算法;三是加强优化结果的实时监控和调整,实现优化算法的实际应用。
芳烃联合装置节能措施及效益分析
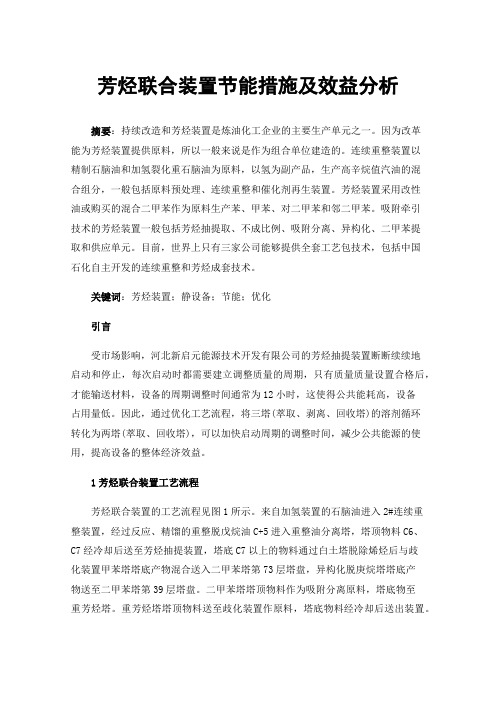
芳烃联合装置节能措施及效益分析摘要:持续改造和芳烃装置是炼油化工企业的主要生产单元之一。
因为改革能为芳烃装置提供原料,所以一般来说是作为组合单位建造的。
连续重整装置以精制石脑油和加氢裂化重石脑油为原料,以氢为副产品,生产高辛烷值汽油的混合组分,一般包括原料预处理、连续重整和催化剂再生装置。
芳烃装置采用改性油或购买的混合二甲苯作为原料生产苯、甲苯、对二甲苯和邻二甲苯。
吸附牵引技术的芳烃装置一般包括芳烃抽提取、不成比例、吸附分离、异构化、二甲苯提取和供应单元。
目前,世界上只有三家公司能够提供全套工艺包技术,包括中国石化自主开发的连续重整和芳烃成套技术。
关键词:芳烃装置;静设备;节能;优化引言受市场影响,河北新启元能源技术开发有限公司的芳烃抽提装置断断续续地启动和停止,每次启动时都需要建立调整质量的周期,只有质量质量设置合格后,才能输送材料,设备的周期调整时间通常为12小时,这使得公共能耗高,设备占用量低。
因此,通过优化工艺流程,将三塔(萃取、剥离、回收塔)的溶剂循环转化为两塔(萃取、回收塔),可以加快启动周期的调整时间,减少公共能源的使用,提高设备的整体经济效益。
1芳烃联合装置工艺流程芳烃联合装置的工艺流程见图1所示。
来自加氢装置的石脑油进入2#连续重整装置,经过反应、精馏的重整脱戊烷油C+5进入重整油分离塔,塔顶物料C6、C7经冷却后送至芳烃抽提装置,塔底C7以上的物料通过白土塔脱除烯烃后与歧化装置甲苯塔塔底产物混合送入二甲苯塔第73层塔盘,异构化脱庚烷塔塔底产物送至二甲苯塔第39层塔盘。
二甲苯塔塔顶物料作为吸附分离原料,塔底物至重芳烃塔。
重芳烃塔塔顶物料送至歧化装置作原料,塔底物料经冷却后送出装置。
在吸附分离单元经吸附、解吸后得到产品对二甲苯送出装置,抽余液(贫二甲苯)送至异构化进行反应,再送至二甲苯塔。
图1芳烃联合装置工艺流程示意2芳烃抽提装置蒸汽用能现状及分析在芳香抽提装置中,3.7 MPa(g)过热蒸汽和锅炉水从装置管网通过过热器和过热器,产生3.7 MPa(g)satt蒸汽和2.2 MPa(g)satt蒸汽,分别发送到每个蒸汽消耗装置。
芳烃联合装置工程大型化探讨

芳烃联合装置工程大型化探讨摘要:芳烃最初来源于煤焦化工艺,但焦化芳烃在数量、质量上不能满足有机工业需求。
为弥补不足,品质优良的石油芳烃得到迅速发展,目前已成为芳烃主要来源,占全部芳烃来源的80%以上。
芳烃联合装置是石油化工芳烃原料的核心生产装置,它以直馏、乙烯裂解汽油或加氢裂化重石脑油等为原料,生产苯、甲苯、邻二甲苯、间二甲苯、对二甲苯(PX)和重芳烃等芳烃类产品。
典型的芳烃联合装置通常包括二甲苯分离、吸附分离和二甲苯异构化、歧化及烷基转移、苯甲苯分馏、芳烃抽提等装置,在炼油工业催化重整通常也归属于芳烃联合装置。
文中主要是指以制取高纯度PX为目标的芳烃联合装置。
关键词:PX;芳烃装置;工程大型化;反应器;塔引言随着国民经济的快速发展,化工原料的需求日益旺盛,芳烃作为重要的化工原料,是承接上游炼化及下游化纤、化工行业的重要桥梁。
大型芳烃联合装置以连续重整装置的重整脱戊烷油、化工装置的加氢裂解汽油等为原料,主要产品为对二甲苯,同时副产苯、粗甲苯、抽余油、重芳烃、富氢气、富乙烷轻质气等。
联合装置主要由二甲苯分馏、吸附分离、芳烃抽提、苯/甲苯分馏、歧化汽提、异构化六套装置组成。
其中,二甲苯分馏、吸附分离、芳烃抽提、苯/甲苯分馏、歧化汽提均以精馏分离过程为主,涉及塔釜再沸、塔顶冷凝、进出料换热、各装置间的热集成等多个传热过程,需要大量传热设备的参与,近年来各种强化传热技术也逐渐应用到芳烃联合装置中,其中强化沸腾传热技术的应用为芳烃装置的节能降耗,以及芳烃装置的大型化发展提供了有力保障1芳烃联合装置工程大型化发展历程工程大型化通常有2层含义:装置规模大型化及设施极限值大型化。
20世纪50年代,美国德克萨斯州有了世界第1套芳烃装置。
70年代,美国UOP公司开始转让Parex吸附分离工艺。
日本东丽株式会社在1970年研究成功类似吸附工艺,称为Aromax工艺。
20世纪90年代,法国Axens(IFP)公司和英国BP公司先后进行了分离PX技术的研究,“Eluxyl法分离”、“深冷结晶分离”和“络合分离”等工艺相继问世并用于工业生产。
四川石化芳烃联合装置流程
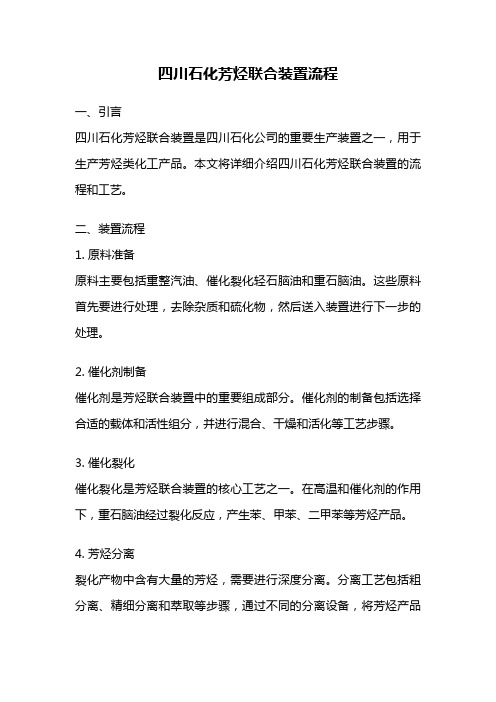
四川石化芳烃联合装置流程一、引言四川石化芳烃联合装置是四川石化公司的重要生产装置之一,用于生产芳烃类化工产品。
本文将详细介绍四川石化芳烃联合装置的流程和工艺。
二、装置流程1. 原料准备原料主要包括重整汽油、催化裂化轻石脑油和重石脑油。
这些原料首先要进行处理,去除杂质和硫化物,然后送入装置进行下一步的处理。
2. 催化剂制备催化剂是芳烃联合装置中的重要组成部分。
催化剂的制备包括选择合适的载体和活性组分,并进行混合、干燥和活化等工艺步骤。
3. 催化裂化催化裂化是芳烃联合装置的核心工艺之一。
在高温和催化剂的作用下,重石脑油经过裂化反应,产生苯、甲苯、二甲苯等芳烃产品。
4. 芳烃分离裂化产物中含有大量的芳烃,需要进行深度分离。
分离工艺包括粗分离、精细分离和萃取等步骤,通过不同的分离设备,将芳烃产品纯度提高到要求的水平。
5. 芳烃加氢芳烃加氢是为了改善产品质量和满足特定需求。
在加氢装置中,通过与氢气的反应,将芳烃中的不饱和化合物和杂质去除,提高产品的稳定性和纯度。
6. 产品处理经过前面几步骤的处理,得到的产品需要进行进一步的处理。
这包括脱硫、脱氮、脱氧等工艺步骤,以确保产品质量符合标准。
7. 产品储存和出厂经过处理的产品储存在储罐中,待需要时进行出厂。
在出厂前,要进行产品质量检验,确保产品符合要求,并进行包装和运输。
三、装置特点1. 高效节能:四川石化芳烃联合装置采用先进的催化裂化技术和催化剂,能够高效地将原料转化为芳烃产品,降低能源消耗和环境排放。
2. 产品多样化:芳烃联合装置可以生产苯、甲苯、二甲苯等多种芳烃产品,以满足不同行业的需求。
3. 质量稳定:装置采用严格的质量控制措施,确保产品质量稳定可靠,符合国家和行业标准。
4. 自动化控制:装置采用先进的自动化控制系统,可以实现对整个生产过程的监控和控制,提高生产效率和安全性。
四、结论四川石化芳烃联合装置是一套高效节能、产品多样化的装置。
通过原料准备、催化裂化、芳烃分离、芳烃加氢、产品处理等工艺步骤,可以将原料转化为高纯度的芳烃产品。
芳烃联合装置脱扬子石化烯烃反应器运行优化方案设计
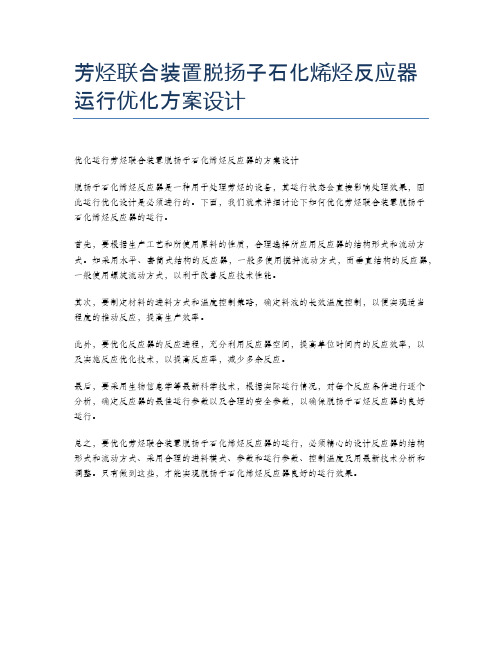
芳烃联合装置脱扬子石化烯烃反应器运行优化方案设计
优化运行芳烃联合装置脱扬子石化烯烃反应器的方案设计
脱扬子石化烯烃反应器是一种用于处理芳烃的设备,其运行状态会直接影响处理效果,因此运行优化设计是必须进行的。
下面,我们就来详细讨论下如何优化芳烃联合装置脱扬子石化烯烃反应器的运行。
首先,要根据生产工艺和所使用原料的性质,合理选择所应用反应器的结构形式和流动方式。
如采用水平、套筒式结构的反应器,一般多使用搅拌流动方式,而垂直结构的反应器,一般使用螺旋流动方式,以利于改善反应技术性能。
其次,要制定材料的进料方式和温度控制策略,确定料液的长效温度控制,以便实现适当程度的推动反应,提高生产效率。
此外,要优化反应器的反应进程,充分利用反应器空间,提高单位时间内的反应效率,以及实施反应优化技术,以提高反应率,减少多余反应。
最后,要采用生物信息学等最新科学技术,根据实际运行情况,对每个反应条件进行逐个分析,确定反应器的最佳运行参数以及合理的安全参数,以确保脱扬子石烃反应器的良好运行。
总之,要优化芳烃联合装置脱扬子石化烯烃反应器的运行,必须精心的设计反应器的结构形式和流动方式、采用合理的进料模式、参数和运行参数、控制温度及用最新技术分析和调整。
只有做到这些,才能实现脱扬子石化烯烃反应器良好的运行效果。
芳烃联合装置
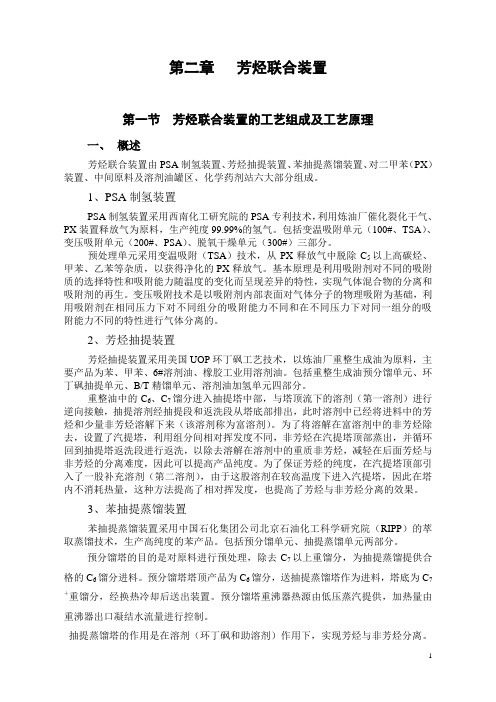
0.29
3
水
0.85
119
2.86
0.09
合计
100
14005
336.13
11.21
出料
1
氢气
2.83
396.2
9.51
0.32
2
解吸气
96.76
13551
325.22
10.84
3
反应水
0.41
57.8
1.4
0.05
合计
100.00
14005
336.13
11.21
2、芳烃联合装置
序号
物料
收率,%
120
硫含量,wt%,≯
0.02
蒸发残余物,mg/100ml,≯
3
油渍试验
合格
机械杂质及水分
无
无
铜片腐蚀(50℃,3h),级,≯
1
水溶性酸或碱
无
无
博士试验
通过
⑥邻二甲苯
项目
指标
颜色(Pt-Co色号),≯
20
酸洗比色
酸层颜色不深于重铬酸钾含量为0.15g/l的标准比色液的颜色
总硫含量,wtppm,≯
1
数据
Kg/h
T/d
×104t/a
进料
1
重整生成油
97.07
68750
4650
55.00
2
重整氢气
2.93
5075
49.8
1.66
合计
100
70825
1699.8
56.66
出料
1
PX
37.94
26875
645
石油炼化--芳烃联合装置静设备特点及节能技术的应用

连续重整和芳烃装置是炼化企业的重要生产装置之一,由于重整可为芳烃装置提供原料,一般作为联合装置建设。
连续重整装置以精制石脑油、加氢裂化重石脑油为原料,生产高辛烷值汽油调和组分,副产氢气,一般包括原料预处理、连续重整、催化剂再生单元。
芳烃装置以重整生成油或外购混合二甲苯为原料,生产苯、甲苯、对二甲苯和邻二甲苯等产品。
吸附分离工艺技术的芳烃装置一般包括芳烃抽提、歧化、吸附分离、异构化、二甲苯分馏及公用工程单元。
芳烃联合装置静设备具有台位数多、规格大、材料和结构特殊、内构件复杂等特点。
下表为某100万t/a芳烃项目静设备统计,主要静设备数量433台,各工艺包方设备种类和结构虽有区别,但大致数量和功能类似。
随着装置大型化和炼化工程技术的不断发展和创新,为节省投资、节能降耗和安稳长满优运行,越来越多的静设备新材料、新结构和新技术得到了应用。
一、主要静设备特点1 反应器类1.1.1 原料预处理单元反应器根据原料组成,设置预加氢、脱氯或脱烯烃反应器等,其原理是在催化剂和氢气作用下,脱去原料油中含硫、氮、氯、砷、烯烃等杂质,以避免重整催化剂发生不同程度的中毒而影响其性能和寿命。
反应器一般为高温、高压、临氢操作的轴向热壁反应器,壳体材质一般为奥氏体不锈钢+铬钼钢的复合钢板,内装入口分配器、去垢篮和出口收集器等不锈钢内构件,结构相对简单。
1.1.2 重整反应器和再生器不同工艺包方虽在催化剂、结构和布置型式上有所差别,但操作基本都是低压和高温操作,重整反应器还是临氢环境,结构上都是热壁径向反应器,内部设置中心管、扇形筒或外筛网等内件,介质经扇形筒径向穿过催化剂床层,再经中心管集合到出口。
中心管一般由多孔内筒和焊接条形筛网外筒组成;扇形筒有布满长圆孔的扇形筒、焊接条形筛网扇形筒、焊接条形筛网制矩形筒或上下段截面积不同的矩形筒几种型式;外筛网的功能与扇形筒一样,但安装、检修不如扇形筒方便,也由焊接条形筛网制成。
重整反应器壳体一般选用抗氢腐蚀和耐热的Cr-Mo钢材料,内件为S32168材料;再生器壳体和内件一般选用耐高温的S31608材料。
PX生产技术芳烃联合装置
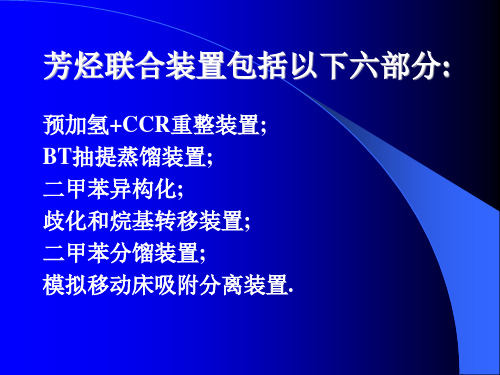
4,歧化和烷基转移
甲苯歧化反应
2 CH3
CH3 CH3 +
烷基转移反应
CH3
CH3 + (CH3)2
CH3 2 CH3
增加了一个烷基转移反应的功能 碳十芳 烃轻质化
甲苯 + 四甲苯 二甲苯 + 三甲苯
CH3 CH3 + (CH3)3
CH3
CH3
CH3 + (CH3)2
20世纪80年代 1982 1971
20世纪80年代
RIPP的SKI工业和催化剂业绩
1,国内10套芳烃联合装置11条二甲苯异构 化生产线中8套采用SKI催化剂,UOP催 化剂2套;
2,近期的镇海(IFP工艺专利,RIPP催化 剂)、福建、福佳等联合装置采用了 RIPP的工艺和催化剂;
3,SKI异构化催化剂的总处理量已经达到 500Mt/年;
Lurgi
二甲亚砜(DMSO)
IFP
IFP
N-甲酰基吗啉(NFM) Morphylane KRUPP
N-甲基吡咯烷酮(NMP) Distapex
Lurgi
环丁砜或NFM+助溶剂
SED
RIPP
1952 1968 1961 1962 1967 1969
2001
工业 套数*
49 50 116 12 5 12 6
2, BT抽提蒸馏装置
几种芳烃抽提工艺
溶剂
方法名称
开 发商
工业化 时间
二(三)甘醇(DEG,TEG)
Udex
UOP / DOW
四甘醇(TTEG)
Tetra Union Carbide
环丁砜(Sulfolane) Sulfolane Shell / UOP
芳烃联合装置C8芳烃资源在炼化一体化加工优化设计

芳烃联合装置是炼化一体化原油加工中的重要组成部分,其主要作用是通过催化剂的作用将原油中的不饱和烃、饱和烃以及杂质分子进行分解、重组和裂解,从而生产出高附加值的芳烃化合物,如苯、甲苯、二甲苯、乙苯(BTX)[1]。
芳烃联合装置也可以裂解重负荷的原油分子,将其分解成较小的碳链分子,从而提高产品的选择性和降低产品中杂质的含量[2]。
芳烃联合装置还能生产一些可替代燃料的产品,如甲醇和二甲醚,这些产品在燃料领域具有广泛的应用,特别是作为清洁燃料的替代品[3]。
芳烃联合装置在炼化一体化原油加工中扮演着关键的角色,通过催化作用、分解和重组反应,提高了芳烃产品的产量和质量,同时去除了原油中的杂质,为石化工业提供了重要的化工原料和清洁燃料。
1 C8芳烃资源优化利用1.1 C8芳烃的来源及特点C8芳烃,又称为甲基萘或甲基萘基芳烃,是一类含有8个碳原子的环烃化合物。
其通常是从石化工业中的裂解过程中获得的,主要来源包括裂解轻烃、液化石油气和催化裂解等。
C8芳烃具有一系列特点,如稳定的分子结构、高化学反应活性、具有一定的毒性和易挥发性等。
1.2 C8芳烃转化为对二甲苯技术分析将C8芳烃转化为对二甲苯是一项重要的技术,因为对二甲苯是一种重要的化工中间体,用于制造塑料、涂料、树脂、溶剂和纤维等[4]。
该技术的步骤通常包括3个方面。
(1)裂解:C8芳烃首先经过催化或非催化裂解,将其分解成较小的芳香烃分子,通常在高温和压力下进行。
(2)同分异构体分离:在裂解产物中,不仅包含对二甲苯,还包括甲苯、乙苯和其他同分异构体。
通过分馏和分离技术,将对二甲苯从其他成分中分离出来。
(3)同分异构体转化:将分离得到的甲苯、乙苯等同分异构体转化为对二甲苯,通常通过芳烃异构化或选择性氧化等催化反应进行。
1.3 优化利用为了优化C8芳烃的资源利用,以下措施可以考虑。
(1)催化技术优化:采用高效的催化剂和反应条件,提高对二甲苯的选择性,降低其他副产物的生成。
芳烃联合装置节能降耗方法探讨

芳烃联合装置节能降耗方法探讨摘要:随着能源资源的日益紧张和环境问题的加剧,节能降耗已成为各行各业关注的焦点。
芳烃联合装置作为石化行业中的重要工艺,其能源消耗也成为亟待解决的问题之一。
本文旨在探讨芳烃联合装置的节能降耗方法,以提高生产效率、减少能源消耗,达到可持续发展的目标。
基于此,本篇文章对芳烃联合装置节能降耗方法探讨进行研究,以供参考。
关键词:芳烃;联合装置;节能降耗;研究引言芳烃联合装置是石化行业中常见的生产工艺之一,它在生产芳烃类化工产品方面具有重要地位。
然而,由于能源消耗和环境污染等问题,如何实现节能降耗已成为当前该领域中亟待解决的难题。
本文旨在探讨芳烃联合装置的节能降耗方法,以期为相关行业提供一些参考和借鉴。
1芳烃联合装置能耗较高的实际表现1.1炼制过程芳烃联合装置的生产流程通常需要进行煤制气、裂解、重整等一系列复杂的化学反应。
这些反应需要消耗大量的能源,如煤炭、天然气或石油等。
1.2能源转化效率由于芳烃联合装置中涉及多个工艺环节,能源转化效率可能不高。
部分能源可能被浪费或损失,导致能耗增加。
1.3设备能效设备在运行过程中存在能量损失的情况,例如传热效率低、循环泵功率消耗大、泄漏等问题,都会引起额外的能耗。
1.4运行管理对于芳烃联合装置来说,合理的运行管理非常重要。
操作不当、设备维护不到位等因素可能导致能源的浪费,增加能耗。
2传统芳烃联合装置的节能方法2.1工艺优化通过对芳烃联合装置的生产工艺进行优化,减少能源的消耗。
可以采用新的催化剂或催化剂组合,提高反应的选择性和转化率,降低废料产生量。
同时,通过提高产品纯度和回收利用废热等方式,实现能源的有效利用。
2.2设备改进优化和改进关键设备,提高设备的能效。
例如,改善换热器的结构和管路设计,提高传热效率,减少热能损失;采用高效的分离设备,提高产品分离和回收利用的效率;改造泵站,减少泵功率消耗等。
2.3节约利用废热利用余热回收装置对废气、废水以及高温烟气中的热能进行回收和再利用。
芳烃联合装置能耗指标表
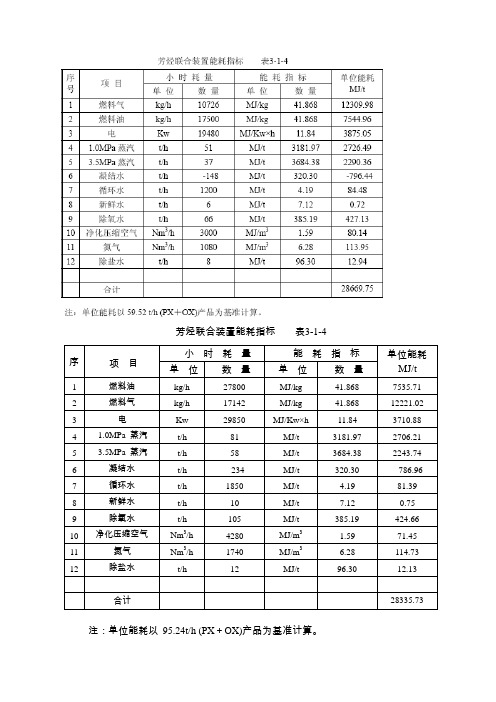
46
193
0
2135
氮气(Nm3/h)
0
146
0
0
0
0
0
0
0
146
苛性钠(20b)kg/h
0
33
0
0
0
0
0
0
0
33
氯剂(C2CL4)kg/d
0
53
0
0
0
0
0
0
0
53
去离子水t/h
1
6
0
0
0
0
0
0
0
7
干燥气(Nm3/h)
0
1448
0
0
0
0
0
0
0
1448
燃料(Gcal/h)
37.8
134.0
0.0
0.0
157.1
0.0
41.7
19.3
44.6
434.5
燃料气Gcal/h
-124.0
净燃料消耗Gcal/h
310.5
高压蒸汽(t/h)
消耗
0.0
21.3
3.6
60.0
0.0
0.0
4.7
4.0
0.0
93.6
产出
0.0
-52.5
0.0
0.0
0.0
0.0
0.0
1
6
0
0
0
0
0
0
0
7
干燥气(Nm3/h)
0
1346
0
0
0
0
0
0
0
1346
2、XyMax方案B(乙苯脱烷基)
PX芳烃联合装置余热优化利用与节能改造
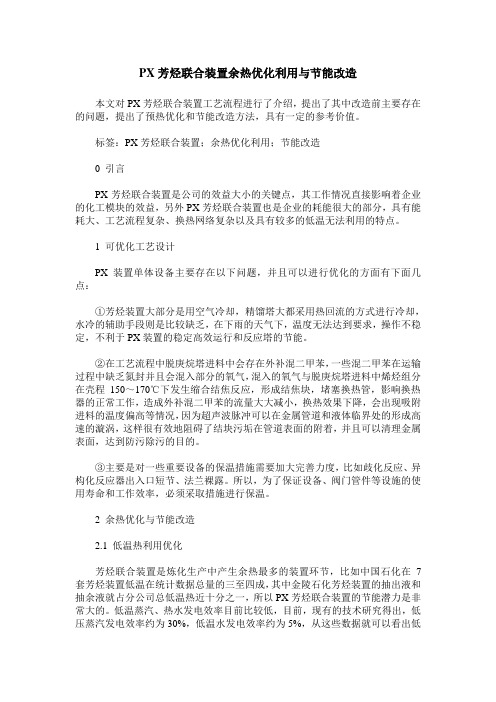
PX芳烃联合装置余热优化利用与节能改造本文对PX芳烃联合装置工艺流程进行了介绍,提出了其中改造前主要存在的问题,提出了预热优化和节能改造方法,具有一定的参考价值。
标签:PX芳烃联合装置;余热优化利用;节能改造0 引言PX芳烃联合装置是公司的效益大小的关键点,其工作情况直接影响着企业的化工模块的效益,另外PX芳烃联合装置也是企业的耗能很大的部分,具有能耗大、工艺流程复杂、换热网络复杂以及具有较多的低温无法利用的特点。
1 可优化工艺设计PX 装置单体设备主要存在以下问题,并且可以进行优化的方面有下面几点:①芳烃装置大部分是用空气冷却,精馏塔大都采用热回流的方式进行冷却,水冷的辅助手段则是比较缺乏,在下雨的天气下,温度无法达到要求,操作不稳定,不利于PX装置的稳定高效运行和反应塔的节能。
②在工艺流程中脱庚烷塔进料中会存在外补混二甲苯,一些混二甲苯在运输过程中缺乏氮封并且会混入部分的氧气,混入的氧气与脱庚烷塔进料中烯烃组分在壳程150~170℃下发生缩合结焦反应,形成结焦块,堵塞换热管,影响换热器的正常工作,造成外补混二甲苯的流量大大减小,换热效果下降,会出现吸附进料的温度偏高等情况,因为超声波脉冲可以在金属管道和液体临界处的形成高速的漩涡,这样很有效地阻碍了结块污垢在管道表面的附着,并且可以清理金属表面,达到防污除污的目的。
③主要是对一些重要设备的保温措施需要加大完善力度,比如歧化反应、异构化反应器出入口短节、法兰裸露。
所以,为了保证设备、阀门管件等设施的使用寿命和工作效率,必须采取措施进行保温。
2 余热优化与节能改造2.1 低温热利用优化芳烃联合装置是炼化生产中产生余热最多的装置环节,比如中国石化在7套芳烃装置低温在统计数据总量的三至四成,其中金陵石化芳烃装置的抽出液和抽余液就占分公司总低温热近十分之一,所以PX芳烃联合装置的节能潜力是非常大的。
低温蒸汽、热水发电效率目前比较低,目前,现有的技术研究得出,低压蒸汽发电效率约为30%,低温水发电效率约为5%,从这些数据就可以看出低温热的利用还是有很大的改进潜力的。
- 1、下载文档前请自行甄别文档内容的完整性,平台不提供额外的编辑、内容补充、找答案等附加服务。
- 2、"仅部分预览"的文档,不可在线预览部分如存在完整性等问题,可反馈申请退款(可完整预览的文档不适用该条件!)。
- 3、如文档侵犯您的权益,请联系客服反馈,我们会尽快为您处理(人工客服工作时间:9:00-18:30)。
第二章芳烃联合装置第一节芳烃联合装置的工艺组成及工艺原理一、概述芳烃联合装置由PSA制氢装置、芳烃抽提装置、苯抽提蒸馏装置、对二甲苯(PX)装置、中间原料及溶剂油罐区、化学药剂站六大部分组成。
1、PSA 制氢装置PSA制氢装置采用西南化工研究院的PSA专利技术,利用炼油厂催化裂化干气、PX 装置释放气为原料,生产纯度99.99%的氢气。
包括变温吸附单元(100#、TSA)、变压吸附单元(200#、PSA)、脱氧干燥单元(300#)三部分。
预处理单元采用变温吸附(TSA)技术,从PX释放气中脱除C5以上高碳烃、甲苯、乙苯等杂质,以获得净化的PX 释放气。
基本原理是利用吸附剂对不同的吸附质的选择特性和吸附能力随温度的变化而呈现差异的特性,实现气体混合物的分离和吸附剂的再生。
变压吸附技术是以吸附剂内部表面对气体分子的物理吸附为基础,利用吸附剂在相同压力下对不同组分的吸附能力不同和在不同压力下对同一组分的吸附能力不同的特性进行气体分离的。
2、芳烃抽提装置芳烃抽提装置采用美国UOP环丁砜工艺技术,以炼油厂重整生成油为原料,主要产品为苯、甲苯、6#溶剂油、橡胶工业用溶剂油。
包括重整生成油预分馏单元、环丁砜抽提单元、B/T 精馏单元、溶剂油加氢单元四部分。
重整油中的C6、C7馏分进入抽提塔中部,与塔顶流下的溶剂(第一溶剂)进行逆向接触,抽提溶剂经抽提段和返洗段从塔底部排出,此时溶剂中已经将进料中的芳烃和少量非芳烃溶解下来(该溶剂称为富溶剂)。
为了将溶解在富溶剂中的非芳烃除去,设置了汽提塔,利用组分间相对挥发度不同,非芳烃在汽提塔顶部蒸出,并循环回到抽提塔返洗段进行返洗,以除去溶解在溶剂中的重质非芳烃,减轻在后面芳烃与非芳烃的分离难度,因此可以提高产品纯度。
为了保证芳烃的纯度,在汽提塔顶部引入了一股补充溶剂(第二溶剂),由于这股溶剂在较高温度下进入汽提塔,因此在塔内不消耗热量,这种方法提高了相对挥发度,也提高了芳烃与非芳烃分离的效果。
3、苯抽提蒸馏装置苯抽提蒸馏装置采用中国石化集团公司北京石油化工科学研究院(RIPP)的萃取蒸馏技术,生产高纯度的苯产品。
包括预分馏单元、抽提蒸馏单元两部分。
预分馏塔的目的是对原料进行预处理,除去C7以上重馏分,为抽提蒸馏提供合格的C6馏分进料。
预分馏塔塔顶产品为C6馏分,送抽提蒸馏塔作为进料,塔底为C7 +重馏分,经换热冷却后送出装置。
预分馏塔重沸器热源由低压蒸汽提供,加热量由重沸器出口凝结水流量进行控制。
抽提蒸馏塔的作用是在溶剂(环丁砜和助溶剂)作用下,实现芳烃与非芳烃分离。
抽提蒸馏塔塔顶产品为非芳烃,作为非芳烃副产品送出装置,塔底产物为富含苯的溶剂,送溶剂回收塔作为进料。
抽提蒸馏塔重沸器热源由中压蒸汽提供,通过控制加热蒸汽量来调节热负荷,加热蒸汽分成两股进行控制,主流股(约80%)由定流量控制,次流股流量(约20%)由灵敏板温度与流量串级控制。
溶剂回收塔的作用是实现苯产品与溶剂的分离。
溶剂回收塔在减压下操作,塔顶残压由压力控制器控制回收塔蒸汽喷射泵的尾气返回量或氮气吸入量进行调节。
溶剂回收塔塔顶产物为苯产品,经白土处理后送往苯检验罐,塔底贫溶剂大部分直接循环使用,少部分去溶剂再生罐进行减压蒸发再生后循环使用。
溶剂回收塔重沸器热源由中压蒸汽提供,加热量由重沸器出口凝结水流量进行控制。
溶剂再生罐实际上是一个减压蒸发器,操作压力由压力控制器控制再生罐蒸汽喷射泵的尾气返回量或氮气吸入量进行调节。
溶剂再生罐热量由内插式溶剂再生罐加热器提供,加热热源为中压蒸汽,加热量由蒸汽凝结水流量进行调节。
再生后溶剂送至贫溶剂泵入口循环使用。
溶剂再生罐罐底残渣采用不定期方式排出。
4、对二甲苯装置对二甲苯装置采用美国UOP 的专利工艺技术,主要生产纯度99.8%的对二甲苯(PX)产品,并富产苯、邻二甲苯(0X)、重芳烃等。
包括甲苯歧化-烷基转移单元、二甲苯异构化单元、二甲苯精馏单元、吸附分离单元四部分。
甲苯歧化-烷基转移单元采用U0P 的TAT0RAY 工艺,选用活性、选择性及稳定性较高的新一代TA-4 催化剂,在高温作用下,甲苯和C9A 发生歧化和烷基转移反应,生成目的产品苯和二甲苯。
可以通过调整甲苯和C9A 的比例来实现苯和二甲苯产品的分布。
2003 年月份催化剂进行了国产化,使用上海石油化工科学研究院自主开发的HAT-97催化剂,该催化剂最大的特点是可以加工3-5%的C io A,并且具有更高的选择性和转化率。
二甲苯异构化单元采用U0P 的IS0MAR 工艺,选用乙苯异构型I-9K 催化剂,在反应过程中建立限定性平衡,通过环烷烃中间体将乙苯最大限度地转化为二甲苯,采用这种催化剂可以从混合二甲苯中获取最高产率的对二甲苯。
该催化剂稳定性好,反应压力和氢油比低,不需注氯,减少了系统腐蚀,改善了操作环境。
吸附分离单元采用U0P 的PAREX 工艺,通过多通道旋转阀实现连续逆流接触,利用分子筛选择吸附PX,再用解吸剂对二乙基苯将PX置换解吸,从而达到分离PX 的目的。
选用最新分子筛吸附剂ADS-27,改进吸附系统设备和优化工艺参数,增大了吸附塔的处理能力,对二甲苯单程收率可提高到97%,纯度达到99.80%。
二甲苯精馏单元采用精密分馏工艺,将混合芳烃中的C8A、C9A 分离出来,分别作为原料提供给吸附分离和歧化单元,从而将联合装置各单元有机的联合起来。
二甲苯塔采用加压操作,操作压力为1.0Mpa(a),利用塔顶和塔底高温物流分别作为其它单元集中供热热源,多余的塔顶汽相通过蒸汽发生器发生1.0Mpa 蒸汽,全塔的热量均被利用,节能效果显著。
5、中间原料及溶剂油罐区负责芳烃联合装置的原料、甲苯、溶剂油的收储工作。
包括中间原料油罐区、溶剂油罐区、芳烃原料罐区三部分。
6化学药剂站负责化纤生产所需的醋酸、乙二醇、碱的收储工作。
包括化学药剂卸车台、化学药剂罐区两部分。
二、原料、产品质量指标1、原料①重整生成油②重整氢气③催化裂化干气2、产品①戊烷油②苯(苯抽提蒸馏)③苯(芳烃抽提)④苯(歧化)⑤6#溶剂油及橡胶工业用溶剂油⑥邻二甲苯⑦对二甲苯三、物料平衡1、PSA制氢装置2、芳烃联合装置第二节PSA制氢装置工艺过程及控制 一、原则流程图 从歧化单元高压氢气分离罐排出的低纯度氢气,作为PSA 勺原料气的一部分,先 进入TSA 预处理系统,在预处理系统中除掉原料气中的高烃组分。
TSA 预处理系统主 要由预处理吸附塔A101-1、A101-2再生气加热器E101、再生气冷却器E102和13只 程控阀KV101-KV109组成。
TSA 预 处理系统吸附塔的工作过程按下述过程完成 (以 A101-1塔为例):1、吸附(A):原料气从管道PG101进入,经过程控阀KV101A 进入吸 附塔A101-1。
在原料压力下,高烃组分被吸附剂吸附,净化气经程控阀 KV102A 管 道PG103进入变压吸附系统。
吸附过程结束后 KV101A KV102A 关闭。
2、逆放(D): 打开程控阀KV104A 吸附塔A101-1的气体经管道FG105限流阀V113再生气冷 却 器E102、管道FG106送出界区。
当吸附塔压力w 0.2MPa 打开程控阀KV106加速逆放。
逆放结束时吸附塔 A101-1的压力w 0.03MP&逆放时打开程控阀 KV107,再生气经 KV107管道FG107送出界区。
逆放结束时关闭程控阀 KV107。
3、加热再生,打开程 控阀KV103A KV104A KV106、KV108再生气加热器101的加热源是蒸 汽管网送来 的1.0MPa 的蒸汽。
在高温低压下,吸附剂吸附的杂质气体解吸出来被再生气体带出 吸附塔送出界区。
当吸附塔出口气体温度达到70T 左右,吸附剂得到彻底再生,力卩热 再生结束。
4、冷吹(C):关闭程控 阀KV108及蒸汽开关,开启程控阀KV109再生气 经程控阀KV109管道FG104 FG105进入吸附塔对吸附塔降温,当吸附剂达到常温时 冷吹结。
关闭程控阀KV109 KV103A KV104A 5、充压(R):为了给进行下一次吸附 做准备,必须对吸附塔进行充压至吸附压力。
打开程控阀 KV105利用另外一只吸附 塔出口的净化气经程控阀 KV105手动限流阀进入吸附塔 A101-1地其进行充压。
充压 至吸附压力,关闭程控阀KV105充压结束。
至此,吸附塔A101-1的一次循环完成, 下一步又开始吸附步骤。
吸附塔A101-2的循环步骤与吸附塔A101-1完全一样仅仅时 间错开,从而保证原料气连续进来,净化气连续输出。
从界区外送来的催化裂化干气进入原料气水分离罐 S201,分离掉液体后经调节阀控制 后与变温吸附来的净化气一起进入变压吸附系统。
吸附塔在一个循环过程中需 经过吸附 均压降 逆放 抽空及抽空冲洗 均压升 最终升压等步骤。
现以 8-3-3VP 流程的其中一个塔( A201- 1)为例对吸附塔的一个循环的工作过程进行详说明: 1、 吸附(A :原料气通过程控阀KV201— 1自下而上进入A201— 1塔,在0.6MPa 工作压 力下吸附原料中的杂质组分,末被吸附的氢气组分,通过程控阀 KV202-1 流出,其 中大部分作为产品输出,少部分通过调节阀HV201程控阀KV20A 2、KV20A 3、KV205 —4分别向吸附塔A201 — 2、A201 — 3、A201 — 4进行最终升压。
吸附步骤完毕,关 闭程控阀迓慨丰坯目■-二隱i£現】essaso 打LMZUi^h. 配鶴加%目畀刨展「X3H低圧踐妊目炜捉玉■ , 一二号吟超1屣卅h氢气至刊:••旳人43SSIU3/I LKV201—1 ,A201—1 停止进原料气。
2、一次均压降(E1D):A201—1 塔停止吸附后,打开程控阀KV20A 1、KV205- 5与刚结束二均升步骤的A201- 5塔出口端相连,实行第一级压力平衡,均压的A201—1、A201—5两塔压力基本相等,压力约为0.43MP&此步骤回收了一部分A201 —1塔中的有用气体,一次均压降结束关闭程控阀KV205- 1、KV205- 5。
3、二次均压降(E2D :打开程控阀KV204- 1、KV204- 6 使A201 —1塔剩余的气体通过程控阀KV204- 1、KV204- 6与A201- 6塔出口端相连,实行第二级压力平衡,至两塔压力基本相等,压力约为0.26MPa关闭程控阀KV204—6。
此步骤回收了一部分A201—1塔中的有用气体。
4、三次均压降(E3D :打开程控阀KV204-7,吸附塔A201—1塔剩余的气体仍顺着出品方向通过程控阀KV204—1、KV204—7 与刚完成程控步骤的A201—7 塔进行第三级压力平衡。