热处理质量控制程序
热处理控制程序
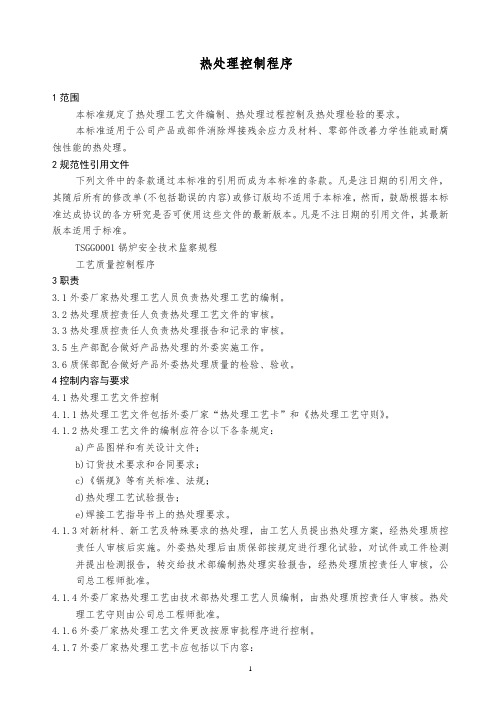
热处理控制程序1范围本标准规定了热处理工艺文件编制、热处理过程控制及热处理检验的要求。
本标准适用于公司产品或部件消除焊接残余应力及材料、零部件改善力学性能或耐腐蚀性能的热处理。
2规范性引用文件下列文件中的条款通过本标准的引用而成为本标准的条款。
凡是注日期的引用文件,其随后所有的修改单(不包括勘误的内容)或修订版均不适用于本标准,然而,鼓励根据本标准达成协议的各方研究是否可使用这些文件的最新版本。
凡是不注日期的引用文件,其最新版本适用于标准。
TSGG0001锅炉安全技术监察规程工艺质量控制程序3职责3.1外委厂家热处理工艺人员负责热处理工艺的编制。
3.2热处理质控责任人负责热处理工艺文件的审核。
3.3热处理质控责任人负责热处理报告和记录的审核。
3.5生产部配合做好产品热处理的外委实施工作。
3.6质保部配合做好产品外委热处理质量的检验、验收。
4控制内容与要求4.1热处理工艺文件控制4.1.1热处理工艺文件包括外委厂家“热处理工艺卡”和《热处理工艺守则》。
4.1.2热处理工艺文件的编制应符合以下各条规定:a)产品图样和有关设计文件;b)订货技术要求和合同要求;c)《锅规》等有关标准、法规;d)热处理工艺试验报告;e)焊接工艺指导书上的热处理要求。
4.1.3对新材料、新工艺及特殊要求的热处理,由工艺人员提出热处理方案,经热处理质控责任人审核后实施。
外委热处理后由质保部按规定进行理化试验,对试件或工件检测并提出检测报告,转交给技术部编制热处理实验报告,经热处理质控责任人审核,公司总工程师批准。
4.1.4外委厂家热处理工艺由技术部热处理工艺人员编制,由热处理质控责任人审核。
热处理工艺守则由公司总工程师批准。
4.1.6外委厂家热处理工艺文件更改按原审批程序进行控制。
4.1.7外委厂家热处理工艺卡应包括以下内容:a)热处理件的主要尺寸、重量及编号:b)热处理类型(消应力、改善力学性能、耐腐蚀、恢复原热处理状态等);c)热处理施工方法(炉内整体、炉内分析、局部)和热处理加热设备;d)热处理加热过程时间—温度控制曲线图(入炉温度上、下限;出炉温度上下限;冷却介质和方式);以及在升温和保温期间,炉内受热处理的产品加热区域的温差要求。
热处理质量控制

热处理质量控制规定结合许可项目特性和本单位实际情况,依据安全技术规范、标准的要求,制定热处理控制的范围、程序、内容如下:1.热处理工艺基本要求:热处理是将材料放在一定的介质内加热、保温、冷却,通过改变材料表面或内部组织结构,来控制其性能的一种综合工艺过程。
在实际生产过程中,要使热处理这道加工工序顺利有效的执行,通常需要以下几个方面的要求:a. 具有一定专业理论水平,熟悉本职业务,并有一定实践经验的热处理生产、技术和检验人员。
b. 热处理工艺文件。
本厂所处理的产品材料45钢、40Cr,所用热处理工艺文件为自编表格:45钢、40Cr热处理工艺规程表。
c. 热处理加热设备: RT3-180-9全纤维中温台车炉(淬火加热炉)一台、RJ2-120-6井式回火炉一台。
d. 热处理淬火槽和淬火介质:发黑、法兰槽7个,热处理淬火槽3个(其中一个为备用槽,另外两个为生产中使用的淬火槽),淬火介质为浓度10%盐水。
e. 检验设备及器具:盐水密度计,温度计(测淬火介质温度),台式洛氏硬度计一台,便携式里氏硬度计一台。
2.热处理过程中的质量控制热处理过程中的质量控制是热处理质量管理的重要组成部分。
热处理质量控制,就是对整个热处理过程中的一切影响零件热处理质量的因素实施全面控制,全过程全员参与热处理质量工作,把质量保证的重点从最终检验的被动把关,转移到生产过程当中的质量控制上来,把零件热处理缺陷消灭在质量的形成过程中。
从而确保零件热处理质量,确保产品使用的安全可靠和寿命。
热处理过程质量控制主要包括以下几方面:2.1 待热处理工件的核查或验收为了确保热处理质量,工件进入热处理车间后首先应对热处理前的原始资料、工件外观、形状及尺寸进行核查或验收。
通常这些项目都标注在相应的工艺技术文件或质量管理文件中,经验收合格后,才能进行热处理生产。
2.1.1 原始资料原始资料包括待热处理工件的试验数据、供货状态、热处理前的加工方式和加工质量及预先热处理类型。
热处理质量控制规程
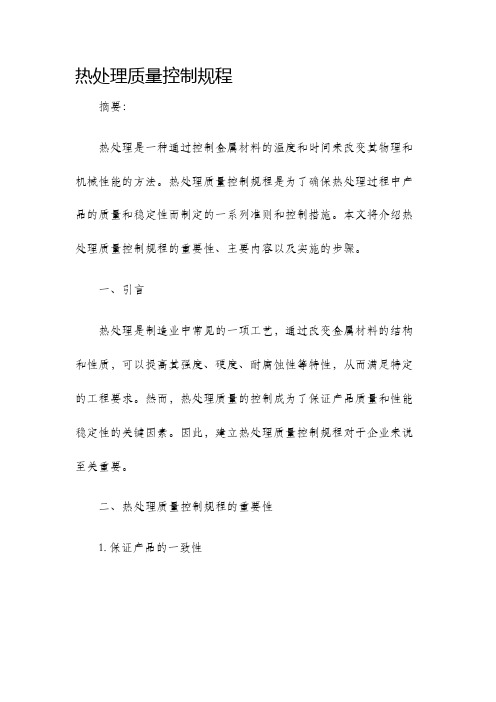
热处理质量控制规程摘要:热处理是一种通过控制金属材料的温度和时间来改变其物理和机械性能的方法。
热处理质量控制规程是为了确保热处理过程中产品的质量和稳定性而制定的一系列准则和控制措施。
本文将介绍热处理质量控制规程的重要性、主要内容以及实施的步骤。
一、引言热处理是制造业中常见的一项工艺,通过改变金属材料的结构和性质,可以提高其强度、硬度、耐腐蚀性等特性,从而满足特定的工程要求。
然而,热处理质量的控制成为了保证产品质量和性能稳定性的关键因素。
因此,建立热处理质量控制规程对于企业来说至关重要。
二、热处理质量控制规程的重要性1. 保证产品的一致性热处理质量控制规程规定了具体的热处理参数、工艺流程和检测标准,确保了不同批次的产品在热处理过程中得到相同的处理条件,从而使产品的性能和质量具有一致性。
2. 确保产品的可靠性热处理过程中,温度、时间等参数的控制直接影响产品的材料结构和性能。
通过严格按照热处理质量控制规程的要求进行操作,可以降低产品在使用过程中的失效率,提高产品的可靠性。
3. 提高生产效率热处理质量控制规程规定了合理的热处理工艺和参数,通过合理的控制可以减少热处理过程中的浪费和缺陷产生,提高生产效率和降低生产成本。
三、热处理质量控制规程的主要内容1. 热处理工艺参数的设定热处理质量控制规程应包括热处理工艺参数的设定,如热处理温度、保温时间、冷却方式等。
这些参数是热处理过程中影响产品性能的重要因素,必须根据产品的要求和材料的特性进行合理的设定。
2. 热处理设备的选用和维护热处理质量控制规程应规定合适的热处理设备的选用和使用要求,并要求定期进行维护和检修,确保设备的运行正常和稳定。
3. 检测和评估方法的制定热处理质量控制规程要求制定合理的检测和评估方法,包括非破坏性检测方法和材料性能评估方法等。
这些方法可以用于验证热处理工艺的有效性并评估产品的质量。
4. 记录和文件管理要求热处理质量控制规程要求进行完整的记录和文件管理,包括热处理参数、设备运行情况、检测结果等信息的记录和保存,以便于追溯和分析。
热处理质量控制程序
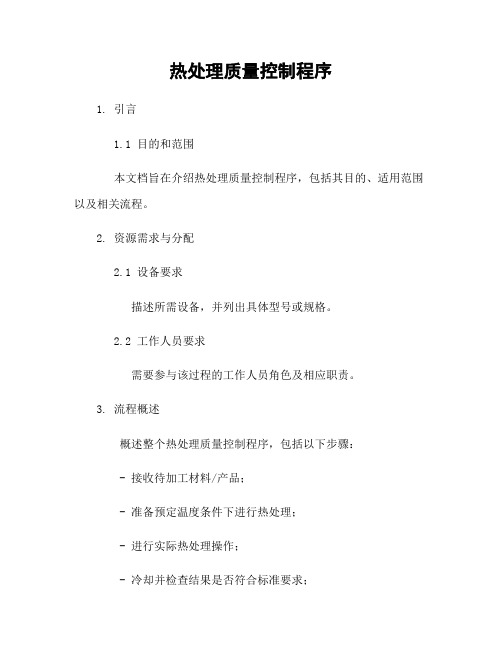
热处理质量控制程序1. 引言1.1 目的和范围本文档旨在介绍热处理质量控制程序,包括其目的、适用范围以及相关流程。
2. 资源需求与分配2.1 设备要求描述所需设备,并列出具体型号或规格。
2.2 工作人员要求需要参与该过程的工作人员角色及相应职责。
3. 流程概述概述整个热处理质量控制程序,包括以下步骤: - 接收待加工材料/产品;- 准备预定温度条件下进行热处理;- 进行实际热处理操作;- 冷却并检查结果是否符合标准要求;4 . 环境监测在每次执行前,请确保环境满足特定参数。
此部分描述了必须遵循的环境监测指南。
5 . 加载和安装样品此章节详细说明如何正确加载和安装待加工材料/产品到对应设备中。
6 . 温度调节对于不同类型的物资(例如金属),根据其性能选择恰当的温度。
此章节描述了如何调整和控制热处理过程中的温度。
7 . 时间设定根据材料/产品类型,设置适当的时间以确保达到所需效果。
本部分提供关于不同材料或产品所需时间范围的指导。
8. 冷却描述冷却步骤及其重要性,并列出常用冷却方法。
9. 检查与测试详细说明在完成热处理后进行哪些检查和测试操作,包括使用什么工具、测量参数等内容。
10. 记录与报告此章节介绍记录必须保存多长时间以及需要怎样格式化报告来跟踪质量数据。
11. 风险管理可能发生问题并提供相应解决方案,在执行程序时注意安全风险防护措施。
12 . 监督与改进确立监督机制,并持续评估该流程是否满足预期目标。
根据实验结果对程序进行优化和改善。
13 . 术语表在文档结尾处添加一个法律名词注释列表,为读者理解相关条款做参考依据14.附件提示有任何相关文件或附件需要参考。
本文档涉及附件:无本文所涉及的法律名词及注释:1. 热处理 - 一种改变材料物理性质的过程,通常通过加热和冷却来实现。
2. 质量控制程序 - 为确保产品符合特定标准而采取的计划、方法和活动集合。
3. 温度调节 - 控制温度以达到预期效果,并确保在安全范围内进行操作。
热处理过程中的质量控制
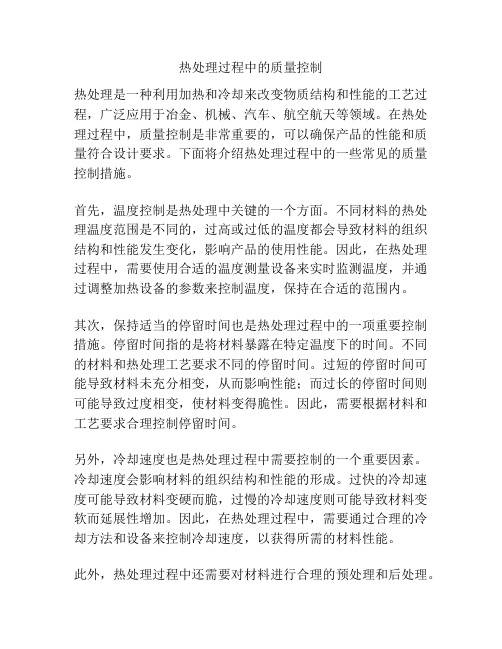
热处理过程中的质量控制热处理是一种利用加热和冷却来改变物质结构和性能的工艺过程,广泛应用于冶金、机械、汽车、航空航天等领域。
在热处理过程中,质量控制是非常重要的,可以确保产品的性能和质量符合设计要求。
下面将介绍热处理过程中的一些常见的质量控制措施。
首先,温度控制是热处理中关键的一个方面。
不同材料的热处理温度范围是不同的,过高或过低的温度都会导致材料的组织结构和性能发生变化,影响产品的使用性能。
因此,在热处理过程中,需要使用合适的温度测量设备来实时监测温度,并通过调整加热设备的参数来控制温度,保持在合适的范围内。
其次,保持适当的停留时间也是热处理过程中的一项重要控制措施。
停留时间指的是将材料暴露在特定温度下的时间。
不同的材料和热处理工艺要求不同的停留时间。
过短的停留时间可能导致材料未充分相变,从而影响性能;而过长的停留时间则可能导致过度相变,使材料变得脆性。
因此,需要根据材料和工艺要求合理控制停留时间。
另外,冷却速度也是热处理过程中需要控制的一个重要因素。
冷却速度会影响材料的组织结构和性能的形成。
过快的冷却速度可能导致材料变硬而脆,过慢的冷却速度则可能导致材料变软而延展性增加。
因此,在热处理过程中,需要通过合理的冷却方法和设备来控制冷却速度,以获得所需的材料性能。
此外,热处理过程中还需要对材料进行合理的预处理和后处理。
预处理包括材料表面的清洁和去除氧化物等处理,以提高热处理的效果。
后处理主要是对热处理后的材料进行调质、淬火、固溶等处理,以进一步改善材料的性能。
对于这些预处理和后处理工艺,需要严格控制各个工艺环节的参数,确保处理效果的稳定性和一致性。
综上所述,热处理过程中的质量控制是确保产品性能和质量的关键。
通过合理控制加热温度、停留时间、冷却速度,以及进行适当的预处理和后处理,可以获得符合设计要求的材料性能和质量。
同时,需要建立完善的质量控制体系,对热处理过程中的各个环节进行监控和记录,以便进行质量追溯和问题分析,不断提升热处理过程的稳定性和一致性。
热处理质量控制程序(二)2024

热处理质量控制程序(二)引言:热处理是一种常见的材料加工工艺,通过控制材料的温度和处理时间,可以改变材料的结构和性能。
为确保热处理的质量,需要建立一套有效的质量控制程序。
本文将阐述热处理质量控制程序的具体内容。
正文:1.温度测量与控制- 确定热处理过程中的目标温度- 选择合适的温度传感器- 定期校准温度传感器- 对温度进行实时监测与记录- 使用合适的加热设备进行温度控制2.时间控制与监测- 确定热处理的持续时间- 使用计时设备进行时间控制- 监测热处理时间的准确性- 进行时间记录与分析- 针对不同材料和处理要求,制定相应的时间控制方法3.冷却控制与评估- 确定合适的冷却速率- 选择合适的冷却介质- 监测冷却速率的准确性- 进行冷却效果的评估与记录- 针对不同材料和处理要求,制定相应的冷却控制方法4.处理环境控制- 确保热处理过程的干净和无尘- 控制热处理过程的湿度- 避免杂质和粉尘对材料的污染- 定期清洁和维护热处理设备- 加强对处理环境的检查和监测5.质量检验与分析- 定期进行热处理质量的检验- 使用合适的检测设备和方法- 对处理后的材料进行物理和化学性能测试- 分析并记录测试结果- 根据测试结果进行热处理程序的调整和优化总结:热处理质量控制程序是保证热处理质量稳定性和产品性能的重要环节。
通过温度测量与控制、时间控制与监测、冷却控制与评估、处理环境控制以及质量检验与分析等措施的综合运用,可以确保热处理的稳定性和一致性,提高产品的质量和性能,满足用户需求。
热处理质量控制
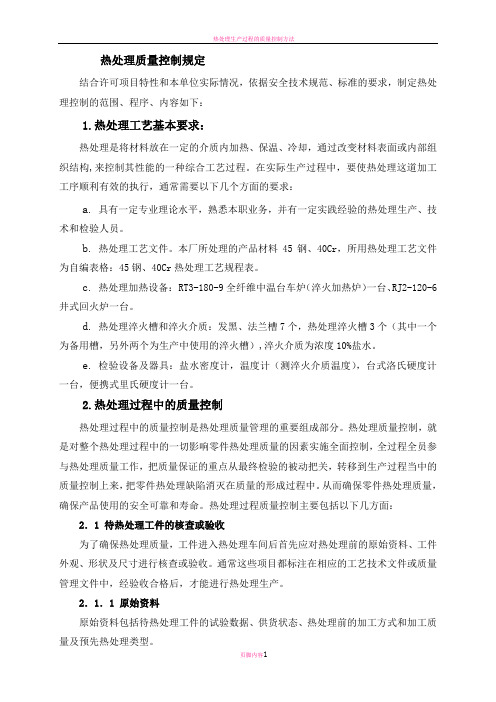
热处理质量控制规定结合许可项目特性和本单位实际情况,依据安全技术规范、标准的要求,制定热处理控制的范围、程序、内容如下:1.热处理工艺基本要求:热处理是将材料放在一定的介质内加热、保温、冷却,通过改变材料表面或内部组织结构,来控制其性能的一种综合工艺过程。
在实际生产过程中,要使热处理这道加工工序顺利有效的执行,通常需要以下几个方面的要求:a. 具有一定专业理论水平,熟悉本职业务,并有一定实践经验的热处理生产、技术和检验人员。
b. 热处理工艺文件。
本厂所处理的产品材料45钢、40Cr,所用热处理工艺文件为自编表格:45钢、40Cr热处理工艺规程表。
c. 热处理加热设备: RT3-180-9全纤维中温台车炉(淬火加热炉)一台、RJ2-120-6井式回火炉一台。
d. 热处理淬火槽和淬火介质:发黑、法兰槽7个,热处理淬火槽3个(其中一个为备用槽,另外两个为生产中使用的淬火槽),淬火介质为浓度10%盐水。
e. 检验设备及器具:盐水密度计,温度计(测淬火介质温度),台式洛氏硬度计一台,便携式里氏硬度计一台。
2.热处理过程中的质量控制热处理过程中的质量控制是热处理质量管理的重要组成部分。
热处理质量控制,就是对整个热处理过程中的一切影响零件热处理质量的因素实施全面控制,全过程全员参与热处理质量工作,把质量保证的重点从最终检验的被动把关,转移到生产过程当中的质量控制上来,把零件热处理缺陷消灭在质量的形成过程中。
从而确保零件热处理质量,确保产品使用的安全可靠和寿命。
热处理过程质量控制主要包括以下几方面:2.1 待热处理工件的核查或验收为了确保热处理质量,工件进入热处理车间后首先应对热处理前的原始资料、工件外观、形状及尺寸进行核查或验收。
通常这些项目都标注在相应的工艺技术文件或质量管理文件中,经验收合格后,才能进行热处理生产。
2.1.1 原始资料原始资料包括待热处理工件的试验数据、供货状态、热处理前的加工方式和加工质量及预先热处理类型。
热处理质量控制程序

热处理质量控制程序一、目的本程序规定了热处理过程的质量控制要求和方法,以确保热处理后的产品符合设计要求和相关标准。
二、适用范围本程序适用于公司内所有经过热处理工序的产品,包括金属材料、非金属材料和其他材料。
三、职责1、热处理部门:负责热处理过程的实施,包括制定热处理工艺、操作设备、监控热处理参数等。
2、质量部门:负责对热处理过程进行监控和检验,确保热处理质量符合要求。
3、设计部门:负责提供热处理产品的设计要求和相关标准。
四、程序步骤1、设计部门应明确热处理产品的设计要求和相关标准,并在产品设计文件中予以规定。
2、热处理部门应根据设计要求和相关标准,制定热处理工艺,包括加热温度、保温时间、冷却速度等参数。
3、质量部门应对热处理工艺进行审核,确保其合理性和可行性。
4、热处理部门应按照制定的热处理工艺进行操作,并监控热处理过程中的参数,如温度、时间等。
5、质量部门应对热处理后的产品进行检验,包括外观检查、尺寸检测、力学性能测试等,确保其符合设计要求和相关标准。
6、如果发现热处理后的产品存在质量问题,应立即停止生产,并对问题进行分析和整改。
7、质量部门应对热处理过程进行定期评估,以确保热处理质量持续改进。
五、记录和报告1、热处理部门应记录热处理过程中的参数,如温度、时间等,并保存记录。
2、质量部门应对热处理后的产品进行检测,并将检测结果记录在质量报告中。
3、如果发现质量问题,应立即向质量部门报告,并采取相应措施进行整改。
4、质量部门应对热处理过程进行定期评估,并将评估结果报告给相关部门。
六、持续改进5、根据质量报告的反馈结果,针对存在的问题进行改进;6、定期对热处理设备和工艺进行检查和维护,确保其正常运行;7、不断更新热处理技术和设备,提高热处理质量和效率;8、对热处理过程进行统计和分析,找出潜在的问题和改进点;9、通过与同行业的交流和合作,引进先进的热处理技术和设备,提高公司的热处理水平。
七、培训与沟通1.对新员工进行热处理知识和技能的培训;2.对现有员工进行定期的热处理知识和技能的培训和考核;3.加强与客户的沟通和协作,了解客户的需求和反馈;4.与其他部门进行有效的沟通和协作,确保整个生产过程的顺利进行。
热处理质量控制规程

热处理质量控制规程摘要:本文档详细介绍了热处理质量控制规程的重要性和应遵循的基本要求。
通过严格执行这些规程,可以最大限度地确保热处理过程的质量稳定性和可靠性。
1. 引言热处理是制造业中常见的一项工艺技术,通过对金属或合金进行加热和冷却,以改变其物理和化学性质。
热处理质量控制是确保最终产品的质量符合客户要求的关键环节。
2. 质量控制原则2.1 完善的质量管理体系:建立并持续改进质量管理体系,包括制定适用于热处理工艺的质量管理程序和要求。
2.2 严格的工艺和设备控制:确保热处理工艺参数和设备的准确性和稳定性,如加热时间、加热温度和冷却速度的控制。
2.3 合理的操作流程:制定详细的操作规程,确保操作人员按照规程进行操作,并建立记录以供追溯。
2.4 严格的材料控制:对热处理材料进行严格的检验和控制,包括材料质量、化学成分和机械性能等。
2.5 完整的记录和档案:对热处理过程的关键参数、操作记录和检验结果进行完整的记录和归档,以供质量追溯和问题排查。
3. 质量控制程序3.1 热处理工艺设计:根据产品的要求和技术规范,制定热处理工艺设计方案,包括加热温度、保温时间和冷却速度等参数的确定。
3.2 材料检验:对待热处理的材料进行严格的检验,确保其质量和性能符合要求。
3.3 设备校验和维护:定期对热处理设备进行校验和维护,确保设备的准确性和稳定性。
3.4 热处理过程控制:按照工艺要求进行热处理过程的控制,包括加热、保温和冷却等环节的控制。
3.5 检验和测试:对热处理后的产品进行检验和测试,包括检查材料硬度、显微组织和化学成分等。
3.6 记录和归档:对热处理过程的关键参数和检验结果进行详细记录和归档,以备质量追溯和问题排查使用。
4. 质量控制指标4.1 加热温度和保温时间:确保加热温度和保温时间符合工艺要求,并保持在允许范围内。
4.2 冷却速度:确保在冷却过程中控制合适的速度,以避免产生过火或冷却不足等缺陷。
4.3 显微组织:通过金相显微组织检验,评估热处理的效果和结构形态是否符合要求。
热处理质量控制程序(含表格)

热处理质量控制程序(ISO9001-2015)1. 范围本规程规定了我厂热处理工件的生产过程,适用于我厂所有需热处理的工件。
由铆焊一车间编制,热处理班具体执行。
2. 引用文件a)钢件的淬火与回火b)热处理炉有效加热区测定方法c)抽样标准d)热处理生产过程安全卫生要求e)火力发电厂焊接热处理技术规程3. 职责3.1技术人员的职责a.熟悉相关规程,熟练掌握、严格执行本规程,组织热处理人员业务学习。
b.负责编制热处理施工方案、作业指导书等技术文件。
c.指导并监督热处理工的工作。
d.收集、汇总、整理热处理资料3.2热处理工的职责a.执行本规程,按规程规定、作业书、工艺卡进行施工。
b.记录热处理操作过程。
c.在热处理后进行自检。
4. 基本要求4.1热处理人员要求热处理人员必须经过专门的培训,具有丰富的热处理技能,熟悉热处理设备的操作。
4.2 设备要求4.2.1炉子、仪表要求所用炉子、仪表均需符合国家相关标准。
1、2、3号炉应符合控温精度±5℃,保温精度±15℃的要求,4、5号炉应符合控温精度±5℃,保温精度±20℃的要求。
自动记录仪所打曲线读数误差不得大于0.5%。
并且应按照相关标准定期检测仪表与炉体。
4.2.2 工装要求热处理工装必须符合实际、能保证工件质量、操作方便、自重轻、耐用。
在使用前必须检查是否有破损,裂纹,能不能承受工件重量。
4.2.3 工件要求凡需进行热处理的零件不应有裂纹、夹渣、折叠等缺陷,不得有大面积的黑皮。
凡需表面淬火处理的工件表面应有较高的光洁度,不得有飞边、毛刺、刀痕等缺陷。
大型锻件在热处理前应进行100%超声波探伤。
4.2.4 检测仪器要求热处理的检查仪器必须符合国家相关标准,并按照要求定期送检。
4.2.5 辅助设备要求热处理辅助设备包括行车、冷却水管、绳索、夹具等,都要有专人负责并定期检查。
4.3.6 安全要求a. 热处理作业时应穿戴必要的劳动防护用品,防止烫伤、触电,在吊装4、5号炉内工件时必须系好安全带。
热处理质量控制规程(一)2024

热处理质量控制规程(一)引言概述:热处理是金属材料加工过程中的重要环节,通过改变材料的结构与性质,以达到所需的力学性能和耐用性。
为了保证热处理的质量,制定了热处理质量控制规程。
本文将从五个大点来阐述热处理质量控制规程的要点。
正文:一、设备与设施的要求1. 选择合适的设备和设施,如热处理炉、淬火油等。
2. 设备应具备稳定的温度控制和压力控制。
3. 设备应定期进行检查和维修,确保正常运行。
二、质量控制标准的制定1. 根据热处理的具体要求制定相应的质量控制标准。
2. 标准应包括热处理过程中的温度、时间、介质等要素。
3. 标准应与相关国际标准或行业标准相对接,以确保质量一致性。
三、原材料控制1. 熔炼原材料应满足特定的成分要求。
2. 原材料在热处理前应进行化学分析和物理性能测试。
3. 确保原材料的质量符合热处理的要求。
四、热处理过程控制1. 确定热处理工艺参数,包括温度、时间、加热速率等。
2. 采用合适的热处理工艺,如淬火、回火等。
3. 监控热处理过程中的温度和时间,确保符合标准要求。
4. 严格控制热处理介质的浓度和温度。
五、质量检验与记录1. 进行热处理后的金属材料的物理性能测试,如硬度、韧性等。
2. 对热处理后的材料进行化学成分分析,确保符合标准要求。
3. 保留完整的热处理过程和结果记录,以备查证。
4. 定期对热处理质量进行内部审核或外部认证。
总结:热处理质量控制是确保金属材料达到所需性能的关键步骤。
通过设备与设施的要求、质量控制标准的制定、原材料控制、热处理过程控制以及质量检验与记录等方面的规程,可以有效控制热处理质量,提高金属材料的性能和可靠性。
热处理质量控制

热处理质量控制热处理质量控制1·引言1·1 背景1·2 目的1·3 范围1·4 参考文献2·热处理过程2·1 热处理定义2·2 热处理工艺流程2·2·1 加热2·2·2 保温2·2·3 冷却2·3 传热模式2·3·1 对流传热2·3·2 辐射传热2·3·3 导热2·4 热处理设备2·4·1 炉子2·4·2 温控装置2·5 热处理常见问题及解决方法3·热处理质量控制3·1 热处理工艺参数3·1·1 温度3·1·2 时间3·1·3 冷却速率3·2 熟料分析3·2·1 金相分析3·2·2 硬度测试3·2·3 耐蚀性测试3·3 热处理后金属材料性能测试 3·3·1 拉伸强度测试3·3·2 抗冲击性测试3·3·3 延展性测试3·4 热处理质量控制流程3·4·1 取样3·4·2 实施热处理3·4·3 进行熟料分析和性能测试3·4·4 分析结果评估3·5 热处理质量控制记录和报告4·附件附件1、热处理质量控制记录表本文档涉及附件:附件1:热处理质量控制记录表本文中涉及的法律名词及注释:1·热处理:将金属材料加热至一定温度,并在一定时间内保温后,通过冷却控制材料的结构和性能。
2·传热模式:●对流传热:通过流体对物体表面的传热方式。
《热处理控制程序[大全5篇]》
![《热处理控制程序[大全5篇]》](https://img.taocdn.com/s3/m/590c8ad0de80d4d8d05a4f2b.png)
《热处理控制程序[大全5篇]》第一篇:热处理控制程序热处理控制程序1、目的为外包的热处理的质量控制做出规定,以保证达到预期的热处理效果。
2、使用范围适用于公司压力管道安装工程零部件消除应力热处理和改善力学性能的热处理。
3、职责焊接热处理责任工程师对外包的热处理的质量负全责,并负责对外包的热处理单位进行定期评价。
4、工作程序4、1热处理工艺试验对于新材料、新工艺及特殊要求的热处理工序,应按规定的程序进行热处理工艺试验。
经焊接热处理责任工程师审核的热处理工艺试验报告,应作为编制热处理工艺的依据。
4、2热处理工艺编制(1)热处理工艺的编制依据a热处理工艺试验报告b焊接工艺指导书的热处理规定(2)热处理工艺由技术部负责编制,焊接热处理质控系统责任工程师审核批准。
(3)热处理工艺的修改,由技术部按规定的程序进行。
4.3热处理外包控制(1)对外包单位的评价a、热处理的外包单位必须取得有关部门颁发的热处理资格证书或取得同级及以上锅炉压力管道安装许可的单位。
外包单位的热处理操作工应进行配需,合格后上岗,能够熟练掌握热处理设备的性能和操作规程。
b、热处理的外包单位的热处理设备和热点仪表、测量仪器等应完好,其能力必须适应本公司的热处理产品的要求。
所有使用的测量记录仪表的精度、灵敏度、量程都应满足有关规定要求,且经检定合格并在有效期内。
(2)外包单位必须按照本单位所提供的热处理工艺指示书和热处理规程进行热处理。
(3)对外包单位所提供的热处理报告和热处理曲线图,必须经焊接热处理质控系统责任工程师签字确认。
(4)热处理记录及实验报告由质检部归入产品技术档案。
5、相关文件与记录《焊缝热处理工艺指示书》《焊缝热处理检验报告书》《焊缝热处理记录表》第二篇:热处理1.退火:指金属材料加热到适当的温度,保持一定的时间,然后缓慢冷却的热处理工艺。
常见的退火工艺有:再结晶退火、去应力退火、球化退火、完全退火等。
退火的目的:主要是降低金属材料的硬度,提高塑性,以利切削加工或压力加工,减少残余应力,提高组织和成分的均匀化,或为后道热处理作好组织准备等。
热处理质量控制程序
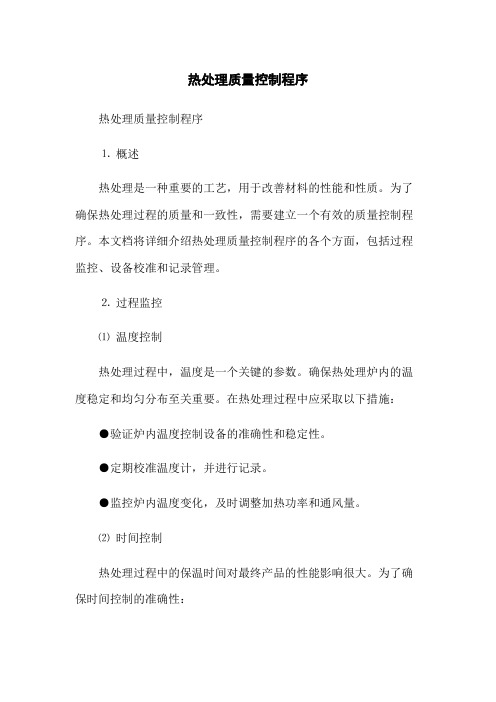
热处理质量控制程序热处理质量控制程序⒈概述热处理是一种重要的工艺,用于改善材料的性能和性质。
为了确保热处理过程的质量和一致性,需要建立一个有效的质量控制程序。
本文档将详细介绍热处理质量控制程序的各个方面,包括过程监控、设备校准和记录管理。
⒉过程监控⑴温度控制热处理过程中,温度是一个关键的参数。
确保热处理炉内的温度稳定和均匀分布至关重要。
在热处理过程中应采取以下措施:●验证炉内温度控制设备的准确性和稳定性。
●定期校准温度计,并进行记录。
●监控炉内温度变化,及时调整加热功率和通风量。
⑵时间控制热处理过程中的保温时间对最终产品的性能影响很大。
为了确保时间控制的准确性:●使用可靠的计时器,并定期校准。
●根据热处理工艺规范和产品要求,确保保温时间的准确控制。
●监控保温时间,记录每个批次的保温时间。
⑶气氛控制某些热处理过程需要控制炉内气氛的成分和压力。
为此,应:●定期检查气氛控制设备的可靠性,并进行记录。
●检测炉内气氛成分和压力,确保符合要求。
●采取适当的控制措施,如调整气氛流量和加气时间。
⒊设备校准⑴热处理炉热处理炉是热处理过程中最关键的设备,需要定期进行校准和维护:●检查炉内加热元件的完好性和连接状态。
●校准炉内温度控制设备。
●检查炉内气氛控制设备的完好性和控制准确性。
⑵温度计温度计是热处理过程中必不可少的工具,需要定期校准:●与信任的实验室合作,进行温度计的定期校准。
●校准前后记录温度计的误差,并进行修正。
⒋记录管理⑴过程记录每次热处理过程都应有详细的记录,包括温度、时间、气氛控制参数等:●记录炉内温度变化曲线,以评估温度控制的准确性。
●记录保温时间和保温温度,以评估保温过程的控制质量。
●记录气氛控制参数和炉内气氛成分,以评估气氛控制的准确性。
⑵产品检测记录每次热处理后应对产品进行检测,并记录结果:●记录产品硬度、宏观形貌和化学成分等检测结果。
●将检测结果与热处理工艺规范进行比较,以评估热处理质量。
⑶设备校准记录对热处理设备和温度计的校准都需要有相应的记录:●记录设备校准的日期、方法和结果。
热处理质量控制程序

为确保压力容器产品或者零部件为消除残存应力,防止变形,稳定尺寸,改善力学性能及耐蚀性要求的热处理质量,本程序规定了热处理质量责任及质量控制要求。
本程序合用于公司压力容器产品或者零部件的热处理质量控制工作。
门归口管理。
生产部门负责热处理外协委托,质检部门负责热处理试件进场验收和热处理报告、记录等文件的确认。
普通要求本公司的产品热处理应委托有资格的合格单位进行分包。
热处理的分包方应经公司供应部门组织按 Q/XHJ— B703—2022 《供方评价和选择程序》规定对热处理分包方的人员素质,设备条件,测量手段,管理水平等方面进行评审合格,且在公司“合格供方名单”之中。
需进行热处理的产品或者零部件,在委托之前必须检验合格, 须返修的焊缝应在热处理前返修合格 .热处理后不得再进行焊接修补或者在受压件上焊接装配件。
经热处理后返回公司的产品或者零部件,应经检验员检验合格,方可流转使用。
热处理前准备(包括热处理设备和测量仪表,热处理前对热处理工艺、检验资料审核、测温点的布置,热处理试板在炉内位置等),热处理操作过程、热处理设备和测量装置、热处理检验和试验等方面质量控制由热处理分包方负责.热处理工艺热处理工艺编制审批和修改由热处理分包方负责,条件允许时,第Ⅰ、Ⅱ类压力容器和第Ⅲ类简单的热处理(如局部焊后热处理、焊后消除应力热处理等)可由本公司编制热处理工艺表卡(表样 D06。
39 )热处理工艺表卡由公司焊接技术人员编制,经热处理责任人审核认可.热处理工艺如分包方编制时,其热处理工艺应符合热处理有关安全技术规范、标准要求且经本公司热处理责任人的审核认可. 3。
2。
3 热处理工艺普通应包括:a。
热处理的主要尺寸和分量;b.热处理类型(焊后消除应力热处理或者改善力学性能、耐晶间腐蚀性能热处理等);c.热处理施工方法(炉内、炉外、局部,分段)和热处理设备;d。
热处理时间 -温度控制(如装炉温度、升温速度、保温温度、保温的时间、降温速度、出炉温度、冷却介质和方式等);e.测温热电偶配置数量及其所在部位的标注;f。
热处理过程中的质量控制范文

热处理过程中的质量控制范文热处理是一种改变金属材料组织结构和性质的方法。
在实际的生产过程中,热处理起到了至关重要的作用。
对于热处理过程,除了掌握热处理的基本原理和技术方法,还需要对热处理过程中的质量控制有深刻的认识,并采用科学的方法进行操作。
本文将介绍热处理过程中的质量控制范文。
热处理中的质量控制1.原材料的入库检验:在进行热处理过程之前,需要对原材料进行入库检验。
入库检验的主要目的是对原材料的质量状况进行了解、评估和记录,确保原材料的质量符合相关的要求,从而为后续的生产过程提供可靠的保障。
2.加热温度的控制:在进行热处理过程时,需要控制金属的加热温度。
加热温度的高低直接影响金属组织的性质和质量,因此加热温度的控制至关重要。
为了保证加热温度的准确性,通常采用温度控制器进行控制。
对于一些高要求的产品,还需要进行多点测温,确保加热过程中的温度均匀性。
3.保温时间的控制:在进行热处理过程时,需要设定保温时间。
保温时间的长短对产品的性质和质量也有很大的影响。
通常采用定时器进行控制。
为了确保产品的稳定性和均匀性,需要进行多点测温,并根据测量结果进行适当的调整。
4.冷却速率的控制:在进行热处理过程之后,需要对金属材料进行冷却。
冷却速率的快慢直接影响金属的组织结构和性质,并会对产品的质量产生直接的影响。
对于不同的金属材料,需要采用不同的冷却方式和速率。
常见的冷却方式有自然冷却、水冷却、油冷却等。
在进行冷却过程时,需要控制冷却速率,确保冷却过程的稳定性和均匀性。
5.存储和运输控制:在进行热处理过程之后,需要对产品进行存储和运输。
存储和运输控制是产品实际应用中的最后一道质量控制环节,也是非常重要的一环。
在进行存储和运输控制时,需要对产品的尺寸、重量、形状等进行严格的检验,并采用合适的包装材料,确保产品不会在运输过程中发生意外情况。
总结热处理是一种重要的加工和处理方法,质量控制是热处理过程中不可或缺的一部分。
通过对原材料的入库检验、加热温度的控制、保温时间的控制、冷却速率的控制和存储和运输控制等方面的质量控制,可以最大程度地保证产品的质量,从而为用户提供更好的产品体验。
热处理控制程序

由本公司提出委托,分包方专职技术人员编制热处理工艺后,会签分包方热处理责任人,也可由本公司的工艺人员编制,热处理责任人审核。
热处理工艺应至少包括:入炉温度、升温速度、保温温度、保温时间、冷却速度及冷却方式等。
5. 热处理工艺的实施
由外单位分包热处理时,热处理工序控制由分包方负责。根据产品数量及重要程度,本公司检验人员有权决定是否到现场监视热处理工序,工序完成后由分包方提供热处理检验记录及温度——时间记录,由本公司检验人员审核后存入产品质量档案。
热处理控制程序
无锡市志成生化工程装备有限公司
程序控制文件
标准号
版本号
Rev.1
热处理控制程序
页码
PAGE1OF 4
1. 范围
适用于有焊后热处理要求的压力容器产品,热处理分包时的质量控制。
2. 热处理的实施
本公司委托有能力进行压力容器产品热处理的外单位进行焊后热处理。
3. 热处理分包方的评定
当委托外单位进行热处理时,事前应由热处理责任人会同相关人员对承接热处理的分包方进行综合评定,评定内容包括:质量保证能力及制度执行情况;热处理炉规格、能力、测温点数量及布置、温度——时间记录仪校正状态、专职的热处理操作人员及检验员、质量记录控制等。
9. 相关的质量记录
序号
记录名称
表格格式
责任Байду номын сангаас门
归档部门
保存期限
1
热处理委托单
JL.09-01
技术质量部
技术质量部
长期
6. 产品焊接试板
无锡市志成生化工程装备有限公司
程序控制文件
标准号
版本号
Rev.1
热处理控制程序
外协热处理质量控制程序

外协热处理质量控制程序外协热处理是一种非常重要的工业生产过程,可以通过改变金属材料的结构,性能和工艺获得新的材料,特别适用于汽车、航空航天、武器制造、机械制造等各个领域。
然而,热处理的质量控制非常重要,如果质量不佳,会对金属材料的性能和使用寿命产生不可逆的影响,在实际生产中对产品质量的稳定性和可靠性产生重大影响。
因此,建立一套完整且可行的外协热处理质量控制程序十分必要。
一、热处理的工艺流程及关键控制点热处理工艺包括加热、保温和冷却三个阶段。
加热阶段是将金属材料升温至一定温度,然后持续一定时间以确保金属内部温度均匀,达到热处理效果。
保温阶段是将已加热的金属材料保持一定时间,使材料内部结构得到重新组织,以改善其物理性能。
冷却阶段是在保证材料冷却速度的同时,控制冷却速度,以达到预期的效果。
在加热阶段,关键控制点包括加热时长,加热温度,加热速率等因素,以确保金属内部温度均匀。
在保温阶段,关键控制点包括保温时间,保温温度,以及保温环境等因素,以确保材料内部结构得到重新组织。
在冷却阶段,关键控制点包括冷却速率,冷却方式等因素,以确保金属材料的硬度和韧性等物理性能得到均衡发展。
二、建立外协热处理质量控制程序的原则1.全面实施热处理流程的质量控制全面实施热处理流程的质量控制,可以从加工前最开始阶段进行调查、询问材料使用目的和所需的物理、化学特性等,进行可行性分析和技术方案制定,保障整个生产流程的稳定性和材料特性的稳定性,谨防生产过程各阶段出现不良品,不留任何后遗症,真正切实提高产品的质量。
2.制定热处理工艺参数每一种材料都有适合自己的热处理工艺参数,根据材料结构、形状、尺寸等因素制定出针对性的热处理工艺参数,保障整个热处理过程的温度、时间、环境的合理性和稳定性,统一流程管理,防止因个别操作不当而导致全批次产品不合格。
3.加强工艺质量控制工作热处理工艺的过程中添加的冷却液、保温坩埚、加热装置等都要经过检验,确保其合法、合格,杜绝因材料问题而带来的品质问题。
- 1、下载文档前请自行甄别文档内容的完整性,平台不提供额外的编辑、内容补充、找答案等附加服务。
- 2、"仅部分预览"的文档,不可在线预览部分如存在完整性等问题,可反馈申请退款(可完整预览的文档不适用该条件!)。
- 3、如文档侵犯您的权益,请联系客服反馈,我们会尽快为您处理(人工客服工作时间:9:00-18:30)。
热处理质量控制程序1 总则1.1为确保压力容器产品或零部件为消除残余应力,防止变形,稳定尺寸,改善力学性能及耐蚀性要求的热处理质量,本程序规定了热处理质量责任及质量控制要求。
1.2本程序适用于公司压力容器产品或零部件的热处理质量控制工作。
2 职责a.压力容器生产中产品或零部件的热处理质量控制工作由技术部门归口管理。
b.生产部门负责热处理外协委托,质检部门负责热处理试件进场验收和热处理报告、记录等文件的确认。
c.供应部门负责热处理分包方的评价和选择。
3 控制要求3.1一般要求3.1.1本公司的产品热处理应委托有资格的合格单位进行分包。
3.1.2热处理的分包方应经公司供应部门组织按Q/XHJ-B703-2010《供方评价和选择程序》规定对热处理分包方的人员素质,设备条件,测量手段,管理水平等方面进行评审合格,且在公司“合格供方名单”之中。
3.1.3需进行热处理的产品或零部件,在委托之前必须检验合格,须返修的焊缝应在热处理前返修合格。
热处理后不得再进行焊接修补或在受压件上焊接装配件。
3.1.4经热处理后返回公司的产品或零部件,应经检验员检验合格,方可流转使用。
3.1.5热处理前准备(包括热处理设备和测量仪表,热处理前对热处理工艺、检验资料审核、测温点的布置,热处理试板在炉内位置等),热处理操作过程、热处理设备和测量装置、热处理检验和试验等方面质量控制由热处理分包方负责。
3.2热处理工艺3.2.1热处理工艺编制审批和修改由热处理分包方负责,条件允许时,第Ⅰ、Ⅱ类压力容器和第Ⅲ类简单的热处理(如局部焊后热处理、焊后消除应力热处理等)可由本公司编制热处理工艺表卡(表样D06.39)热处理工艺表卡由公司焊接技术人员编制,经热处理责任人审核认可。
3.2.2热处理工艺如分包方编制时,其热处理工艺应符合热处理有关安全技术规范、标准要求且经本公司热处理责任人的审核认可。
3.2.3热处理工艺一般应包括:a.热处理的主要尺寸和重量;b.热处理类型(焊后消除应力热处理或改善力学性能、耐晶间腐蚀性能热处理等);c.热处理施工方法(炉内、炉外、局部,分段)和热处理设备;d.热处理时间—温度控制(如装炉温度、升温速度、保温温度、保温的时间、降温速度、出炉温度、冷却介质和方式等);e.测温热电偶配置数量及其所在部位的标注;f.热处理试板在炉内的位置及支撑加强防止变形的措施;g.对随炉热处理试件要求;h.当容器进行局部环带或分段焊后热处理时,对加热器件的设置和保温措施的要求等。
3.2.4 对新材料、新工艺进行热处理试验和评定,评定由热处理分包方进行,评定报告经公司热处理责任人审核认可。
3.3 热处理设备和测量装置a.热处理设备的温度测量,记录装置应有足够的测量范围和准确度,所有计量器具都应在检定的有效期内。
b.测温电偶的测温端应布置在热处理件加热部位的表面,测量点布置分布应均匀,应采用自动测温记录仪记录时间—温度,以控制热处理全过程。
c.热处理设备应定期检修,每次检修应测定有效区温差是否满足热处理工艺要求。
3.4 热处理操作3.4.1 热处理操作者应熟悉热处理标准、规范、工艺、设备和测量装置。
试验前应对热处理工艺、检验资料的完整性进行审核。
3.4.2 热处理操作者应经培训、考核合格、取得操作资格证持证上岗。
3.4.3 热处理操作者应严格执行工艺,完成热处理操作。
3.4.4 热处理的仪表自动时间—温度记录纸应由仪表人员更换,并经热处理检验员确认。
3.4.5 热处理操作者应按操作记录填写“热处理操作记录”和“热处理装炉记录”等,并签名和注明日期。
3.4.6 车间热处理工艺人员负责监督热处理操作,检查热处理记录,并核实与热处理工艺是否一致。
3.5 检验和试验3.5.1 热处理检验员对热处理操作是否符合热处理工艺要求进行检查,并在热处理自动记录表上签名确认,并注明日期。
3.5.2 随炉热处理试件按图样标准规定要求进行力学性能、金像分析、耐腐蚀等试验后,由试验人员签发试验报告,热处理温度—时间自动控制热处理记录,应经热处理责任人认可,经检验责任人归档。
3.5.3 上述记录、报告不符合热处理工艺要求时,应按《手册》“不合格品控制”规定进行处理。
3.6 记录报告审查3.6.1 热处理分包方提供的热处理检验报告应有检验员、审核人签字,并注明日期。
热处理温度—时间自动热处理记录应注明热处理炉号、工件号/产品编号、热处理日期、热处理操作工和热处理责任人签字等。
3.6.2 热处理责任人应对全部热处理记录、报告进行审查,确认签字是否满足热处理工艺要求。
3.6.3 热处理记录报告应归入产品质量档案,以供监督检验单位的检查。
4 样表a.D02.37 热处理工艺卡理化实验管理程序1 总则1.1 为了确保产品的理化、金相试验,符合法规标准和规范要求,使各项报告正确可靠,本程序规定了理化、金相试验质量控制的责任和控制要求。
1.2 本程序适用于第Ⅰ、Ⅱ、Ⅲ类压力容器理化、金相试验的管理工作。
2 职责理化、金相试验的管理和控制,由质检部负责归口管理,生产、技术、车间等部门予以配合。
3 控制要求3.1 人员资格3.1.1 理化责任人负责压力容器制造过程的材料,焊接工艺评定,焊工考试,产品焊接试板,热处理试板等理化、金相检验工作。
3.1.2 理化责任人由总经理任命,并对理化、金相检验报告正确性、可靠性负责。
3.1.3 理化、金相试验人员须经资格培训,考核合格后持证上岗。
外委的理化、金相试验及化学分析人员资格由理化实验分包方负责。
3.1.4 理化实验的分包方,公司按Q/XHJ-B703-2010《供方评价和选择程序》评审合格,且在公司合格供方名单之中。
3.2 试验设备和仪器3.2.1 理化、金相试验设备和仪器及理化试验室的条件,必须满足公司压力容器的许可项目要求。
3.2.2 理化、金相试验室的设备和仪器,必须符合国家级压力容器行业现行标准,并随标准的更新而更新。
3.2.3理化、金相试验设备和仪器,应编制周期检定计划,经有资格的法定计量单位检定合格,并粘贴明显计量标志,在有效期内使用。
超过检定周期进行的试验结果一律无效。
3.2.4 理化责任人负责编制理化、金相试验设备和仪器的操作规程,并指定专人操作管理、维护和保养,设备完好率100%。
发现问题,应立即停止试验,并向理化责任人报告处理。
3.2.5 质检部理化试验室负责理化、金相试验设备和仪器的管理(包括立卷建档)和检定。
3.3 试验的委托3.3.1 理化、金相试验委托单位应填写“理化试验委托单”(样表D02.05)连同标记清晰、并经检验合格的试件,交质控系统相关负责人审核委托内容,应符合《手册》有关规定。
对试验委托内容和试件进行审核验收。
然后交理化试验室进行试验。
3.3.2 公司理化试验室对不常做的特殊实验,(如晶间腐蚀、化学成分分析等)由理化责任人委托公司评审合格的分包方进行。
3.3.3 原材料试件、产品焊接试件、焊工考试试件、焊接工艺评定试件等,经外观和无损检测合格后和“工序传递卡”一同转到生产车间进行试件试样制备。
3.4 试样制备3.4.1 相关负责人负责试样制备的取样部位、数量,并下发试样加工图纸和试样加工工艺规程。
3.4.2 车间按工艺规程要求进行取样,加工制备。
、3.4.3 试样必须有清晰的识别和可追溯检查标记。
3.4.4 试样加工成形后,检验员需按工艺规程检验合格,再经理化责任人验收后方可交付试验。
3.5 试验、记录、报告3.5.1 各专业试验人员,按理化责任人审核签发的“理化试验委托单”的检验项目、试样制备、试验方法等标准的要求,复核试样,做好试验记录台帐(包括:拉伸、弯曲、冲击、管材工艺性试验,不锈钢耐酸钢晶间腐蚀倾向试验等),并开具出试验结果报告(包括:化学分析、晶间腐蚀试验、机械性能试验、金相检验等)。
3.5.2 试验结果报告,由试验人员填写,另一试验人员审核,理化责任人确认,并加盖理化检验责任人章后签发,并由检验人员归入质量档案。
对产品焊接试板的机械性能试验报告,检验员应填写“产品焊接试板力学和弯曲性能检验报告”(样表D02.19)并收存于产品质量证明书中,提供给顾客建档备查。
3.5.3 试验环境条件(温度、湿度)必须符合标准要求。
3.5.4 试验试样和剩余试样由理化试验室保存,保存期为产品出公司后3~个月。
3.6 理化检验分包控制3.6.1 理化检验的分包应分包给有资格的单位进行试验,并按Q/XHJ-B703-2010《供方评价和选择程序》对分包人员素质、理化设备条件、理化检验手段、管理水平和资质等方面进行评价、选择重新评价,并作出分包方评价报告,评价报告应包括理化质控系统的建立和运行,试验设备能力、试验人员素质等。
3.6.2 经评定合格的分包方,公司尚需分包技术协议,明确“试验项目全过程接受公司理化检验质控系统的质量控制”条款和双方的责任。
分包方所具备的理化检验能力,必须满足公司压力容器的许可项目要求。
3.6.3 分包方开具的理化检验报告应经理化责任人审查判断并签字确认,然后转交检验员归档保存。
3.7 监督检验安全监察、监督检验、顾客等单位对理化、金相检验报告有怀疑时,有权提出重新试验、验证等要求。
4 记录表格a. D02.05 理化实验委托单b. D02.19 产品焊接试板力学和弯曲性能检验报告。