热处理质量控制程序说课讲解
热处理质量控制规程

热处理质量控制规程热处理质量控制规程一、引言1.1 目的本规程旨在确保热处理质量控制的科学性、合理性和可操作性,以提高热处理工艺的稳定性和产品质量的一致性。
1.2 范围本规程适用于公司热处理车间的各类热处理工艺,并包括相关的质量控制措施。
1.3 参考1.3.1 国家标准:GB/T 16825-2010 金属材料的热处理术语。
1.3.2 公司标准:YY/T 1626-2016 金属热处理工艺规范。
二、术语和定义2.1 热处理热处理是指通过加热、保温和冷却等一系列工艺,改变金属材料的组织结构,从而获得所需的力学性能和物理性能的过程。
2.2 热处理工艺热处理工艺是指热处理过程中所采用的加热、保温、冷却等一系列控制参数和工艺操作。
2.3 热处理质量控制热处理质量控制是指通过严格控制热处理工艺参数,确保产品达到设计要求的质量控制方法和措施。
三、热处理质量控制流程3.1 热处理工艺参数的制定3.1.1 根据产品要求、材料特性和工艺性能,制定合理的热处理工艺参数。
3.1.2 进行试验验证,确定最佳的热处理工艺参数。
3.2 设备和环境条件的控制3.2.1 确保热处理设备处于良好工作状态,定期进行维护和检修。
3.2.2 控制热处理工作区的环境条件,包括温度、湿度和洁净度等。
3.3 材料的准备与检查3.3.1 对待热处理的材料进行准确的标识和记录,确保正确性和完整性。
3.3.2 对材料进行外观检查,排除表面缺陷、氧化层和油污等。
3.4 加热和保温3.4.1 选择适当的加热设备和加热方式,确保加热均匀和稳定。
3.4.2 控制加热速率,避免材料过快或过慢的加热导致质量问题。
3.4.3 确定适当的保温时间和温度,保证零件达到所需的热处理效果。
3.5 冷却和回火3.5.1 选择合适的冷却介质和冷却速度,确保材料达到所需的组织和性能。
3.5.2 对需要回火的材料进行回火处理,消除残余应力和提高材料的韧性。
3.6 检测和评价3.6.1 根据产品要求和标准,进行热处理质量的检测和评价。
热处理质量控制程序
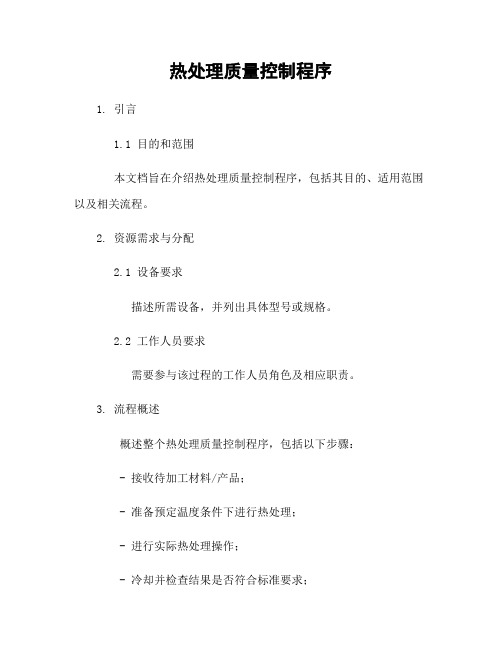
热处理质量控制程序1. 引言1.1 目的和范围本文档旨在介绍热处理质量控制程序,包括其目的、适用范围以及相关流程。
2. 资源需求与分配2.1 设备要求描述所需设备,并列出具体型号或规格。
2.2 工作人员要求需要参与该过程的工作人员角色及相应职责。
3. 流程概述概述整个热处理质量控制程序,包括以下步骤: - 接收待加工材料/产品;- 准备预定温度条件下进行热处理;- 进行实际热处理操作;- 冷却并检查结果是否符合标准要求;4 . 环境监测在每次执行前,请确保环境满足特定参数。
此部分描述了必须遵循的环境监测指南。
5 . 加载和安装样品此章节详细说明如何正确加载和安装待加工材料/产品到对应设备中。
6 . 温度调节对于不同类型的物资(例如金属),根据其性能选择恰当的温度。
此章节描述了如何调整和控制热处理过程中的温度。
7 . 时间设定根据材料/产品类型,设置适当的时间以确保达到所需效果。
本部分提供关于不同材料或产品所需时间范围的指导。
8. 冷却描述冷却步骤及其重要性,并列出常用冷却方法。
9. 检查与测试详细说明在完成热处理后进行哪些检查和测试操作,包括使用什么工具、测量参数等内容。
10. 记录与报告此章节介绍记录必须保存多长时间以及需要怎样格式化报告来跟踪质量数据。
11. 风险管理可能发生问题并提供相应解决方案,在执行程序时注意安全风险防护措施。
12 . 监督与改进确立监督机制,并持续评估该流程是否满足预期目标。
根据实验结果对程序进行优化和改善。
13 . 术语表在文档结尾处添加一个法律名词注释列表,为读者理解相关条款做参考依据14.附件提示有任何相关文件或附件需要参考。
本文档涉及附件:无本文所涉及的法律名词及注释:1. 热处理 - 一种改变材料物理性质的过程,通常通过加热和冷却来实现。
2. 质量控制程序 - 为确保产品符合特定标准而采取的计划、方法和活动集合。
3. 温度调节 - 控制温度以达到预期效果,并确保在安全范围内进行操作。
锅炉安装修理改造热处理的质量控制程序

锅炉安装修理改造热处理的质量控制程序热处理是锅炉安装、修理、改造中部件消除焊接残余应力,改善力学性能或耐腐蚀性能的重要手段,也是保证锅炉安装、修理、改造产品质量和使用性能的基础。
为了对热处理工作的质量进行控制与管理,特制定了JNZK-CX-07-2010《热处理工艺控制程序》。
该程序对以下方面做出了规定:1.1热处理工作的管理
1.1.1规定了热处理工作进行分包。
1.1.2规定了由热处理责任人组织对分包方进行评价。
1.1.3规定了由热处理分包方负责编制热处理工艺和热处理作业指导书。
1.2热处理质量管理
1.2.1规定了由热处理责任人对热处理工艺和热处理作业指导书进行确认签字后分发、使用的要求。
1.2.2规定了热处理文件的管理。
1.2.3规定了热处理分包的控制。
1.3相关文件
JNZK-CX-07-2010《热处理控制程序》。
热处理质量管控CQI9教材课件

金属学基础知识—铁碳合金
铁素体—碳熔于α-Fe晶格间歇形成的间 歇固熔体,称为铁素体.用F表示。用于铁 素体的含碳量低,所以铁素体的组织与 纯铁相似。具有良好的塑性和韧性,而 强度和硬度较低。
(另有δ铁素体,是碳熔于δ-Fe晶格间歇 中形成的间歇固熔体。)
金属学基础知识—铁碳合金
奥氏体—碳熔于γ-Fe晶格间隙中形成的 间隙固溶体,称为奥氏体。用A表示。由 于奥氏体的溶碳比铁素体多,因此奥氏 体的强度和硬度较铁素体高,并且是单 一的固溶体,所以其塑性较好,变形抗 力较低。绝大多数钢在进行压力加工和 热处理时,都加热到奥氏体区域。
ISO/TS 16949:2002条款8.2.2.2 要求组织 应审核每个制造过程以确定它的有效性。热处 理过程有适用性和有效性应利用CQI-9第二版 特殊过程:热处理系统的评审(Heat Treat
顾客特殊要求
System Assessment,HTSA)来确定,这文件由 AIAG出版。有效性的评估应包括组织的自我评 审、已采取措施,并维护所有的记录。
2007 年9月 4.1.12 热处理过程
ISO/TS 16949:2002条款要求,组织应审 核每一个制造过程以确定其有效性。热处理过 程的适用性和有效性应利用AIAG所发行的CQI9第二版特殊过程:热处理系统评审(CQI-9 Special Process: Heat Treat
顾客特殊要求
SystemAssessment, HTSA)来加以确定,并维 护其记录。其有效性的评估应包括组织的自我 评审、已采取的措施和已被维护的记录。
金属学基础知识—晶格类型
体心立方晶格:他的晶胞是一个立方体,在立 方体的八个角和立方体的中心,各排列一下原 子.属于这类晶格类型的金属有钨/铬/矾及a铁;
热处理质量控制程序(二)2024

热处理质量控制程序(二)引言:热处理是一种常见的材料加工工艺,通过控制材料的温度和处理时间,可以改变材料的结构和性能。
为确保热处理的质量,需要建立一套有效的质量控制程序。
本文将阐述热处理质量控制程序的具体内容。
正文:1.温度测量与控制- 确定热处理过程中的目标温度- 选择合适的温度传感器- 定期校准温度传感器- 对温度进行实时监测与记录- 使用合适的加热设备进行温度控制2.时间控制与监测- 确定热处理的持续时间- 使用计时设备进行时间控制- 监测热处理时间的准确性- 进行时间记录与分析- 针对不同材料和处理要求,制定相应的时间控制方法3.冷却控制与评估- 确定合适的冷却速率- 选择合适的冷却介质- 监测冷却速率的准确性- 进行冷却效果的评估与记录- 针对不同材料和处理要求,制定相应的冷却控制方法4.处理环境控制- 确保热处理过程的干净和无尘- 控制热处理过程的湿度- 避免杂质和粉尘对材料的污染- 定期清洁和维护热处理设备- 加强对处理环境的检查和监测5.质量检验与分析- 定期进行热处理质量的检验- 使用合适的检测设备和方法- 对处理后的材料进行物理和化学性能测试- 分析并记录测试结果- 根据测试结果进行热处理程序的调整和优化总结:热处理质量控制程序是保证热处理质量稳定性和产品性能的重要环节。
通过温度测量与控制、时间控制与监测、冷却控制与评估、处理环境控制以及质量检验与分析等措施的综合运用,可以确保热处理的稳定性和一致性,提高产品的质量和性能,满足用户需求。
热处理质量控制和检测培训课件

质量控制标准
01
02
03
04
制定质量控制计划: 明确质量控制目标、
方法和步骤
建立质量控制体系: 建立质量管理体系, 确保质量控制流程
的实施
实施质量控制措施: 采取有效措施,确 保产品质量符合要
求
质量检测:对生产 过程中的产品进行 质量检测,确保产
品质量符合要求
质量控制流程
01
制定质量控制计划:明确质 量控制目标、方法和标准
3
检测技术
检测方法
目视检测:通过 肉眼观察工件表 面缺陷
磁粉检测:利用 磁粉吸附在工件 表面缺陷处,形 成可见的磁痕
超声波检测:利 用超声波在工件 内部传播,检测 工件内部缺陷
射线检测:利用X 射线或γ射线穿 透工件,检测工 件内部缺陷
涡流检测:利用 涡流在工件表面 流动,检测工件 表面缺陷
渗透检测:利用 渗透液渗透到工 件表面缺陷处, 形成可见的渗透 痕迹
质量控制工具
01
统计过程控制(SPC):通过 监控过程参数来确保产品质 量的稳定性
02
质量功能展开(QFD):将客 户需求转化为产品特性和生产 过程的设计要求
03
失效模式和效应分析(FMEA): 评估产品设计和生产过程中的 潜在失效模式及其影响
04
六西格玛管理(Six Sigma): 通过减少缺陷和变异来提高产 品质量和生产效率
量控制
定期进行设 备检查和维 护,确保设 备正常运行
加强员工培 训,提高操 作技能和意
识ห้องสมุดไป่ตู้
建立完善的 质量管理体 系,确保质 量控制和检 测的有效性
谢谢
回火设备:用于回火处理的
03
热处理质量控制程序

热处理质量控制程序一、目的本程序规定了热处理过程的质量控制要求和方法,以确保热处理后的产品符合设计要求和相关标准。
二、适用范围本程序适用于公司内所有经过热处理工序的产品,包括金属材料、非金属材料和其他材料。
三、职责1、热处理部门:负责热处理过程的实施,包括制定热处理工艺、操作设备、监控热处理参数等。
2、质量部门:负责对热处理过程进行监控和检验,确保热处理质量符合要求。
3、设计部门:负责提供热处理产品的设计要求和相关标准。
四、程序步骤1、设计部门应明确热处理产品的设计要求和相关标准,并在产品设计文件中予以规定。
2、热处理部门应根据设计要求和相关标准,制定热处理工艺,包括加热温度、保温时间、冷却速度等参数。
3、质量部门应对热处理工艺进行审核,确保其合理性和可行性。
4、热处理部门应按照制定的热处理工艺进行操作,并监控热处理过程中的参数,如温度、时间等。
5、质量部门应对热处理后的产品进行检验,包括外观检查、尺寸检测、力学性能测试等,确保其符合设计要求和相关标准。
6、如果发现热处理后的产品存在质量问题,应立即停止生产,并对问题进行分析和整改。
7、质量部门应对热处理过程进行定期评估,以确保热处理质量持续改进。
五、记录和报告1、热处理部门应记录热处理过程中的参数,如温度、时间等,并保存记录。
2、质量部门应对热处理后的产品进行检测,并将检测结果记录在质量报告中。
3、如果发现质量问题,应立即向质量部门报告,并采取相应措施进行整改。
4、质量部门应对热处理过程进行定期评估,并将评估结果报告给相关部门。
六、持续改进5、根据质量报告的反馈结果,针对存在的问题进行改进;6、定期对热处理设备和工艺进行检查和维护,确保其正常运行;7、不断更新热处理技术和设备,提高热处理质量和效率;8、对热处理过程进行统计和分析,找出潜在的问题和改进点;9、通过与同行业的交流和合作,引进先进的热处理技术和设备,提高公司的热处理水平。
七、培训与沟通1.对新员工进行热处理知识和技能的培训;2.对现有员工进行定期的热处理知识和技能的培训和考核;3.加强与客户的沟通和协作,了解客户的需求和反馈;4.与其他部门进行有效的沟通和协作,确保整个生产过程的顺利进行。
热处理讲稿-第九讲热处理质量检验
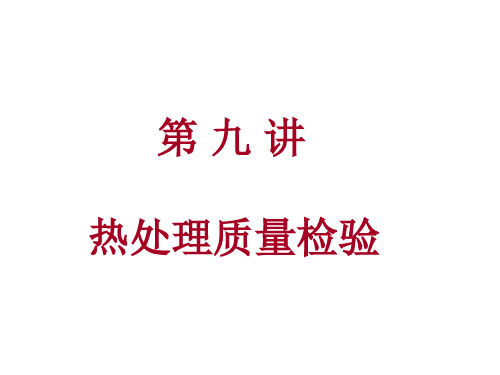
3. 操作与技能 a. 操 作
左手拿零件,右手拿锉刀,把工件贴置在工作台棱 边上,用一定的压力在工件上来回锉动,锉刀要放平 稳,用力要均匀。根据锉痕深浅和手感确定硬度高低。
b. 定 值 当工件的硬度范围未知时,先用一把60HRC标准锉
刀试锉,工件若能被锉动,再换一把55HRC的标准锉 刀接着试锉;若工件未能被锉动,锉刀在工件上打滑, 这时可用一把58HRC的标准锉刀试锉。锉刀稍微锉动 划出道痕,这表明工件硬度就是58HRC。
c. 脱碳 50钢零件
加热时,传 热介质中的 氧气等氧化 性气体与的 碳元素发生 化学反应, 使表层含碳 量降低的现
象。
氧化为零件加热时介质中的氧、二氧化碳和
水蒸气等与铁反应,生成氧化物的过程
在30CrNi3A零件上 电火花线切割制备 人造裂口:经520℃ 回火后,线切割表层 形成了0.01mm厚的 氧化层,无脱C现象
2. 金相试样的截取
钢铁零件微观金相检测的取样和制备方法,根据 GB/T13298--1991《金属显微组织检验方法》规定执行。 根据实践经验,金相试样合适的规格是:长和宽尺寸为 12~15mm,高15 ~ 20mm。
取样部位要考虑钢的各向异性的特性。即材料在不
同的方向上组织结构不尽相同。与变形方向平行的面, 称为纵向;与变形方向垂直的面,称为横向。所以不同 的截面取样获得的检测结果有所不同。根据标准规定, 脱碳、渗碳、氮化和有效硬化层深度等显微长度测量项 目,以及球化退火、正火、淬火、调质和晶粒度等试验 项目应按横向取样;带状偏析组织、非金属夹杂物等项 目应按纵向取样。
3. 金相检验方法
a. 金相试样制备—包括取样、制作(磨光、抛光、 腐蚀),在仪器上观察。 b.金相仪器设备—广义的金相试验包括低倍酸蚀试 验(铝合金为碱蚀),其低倍形态和缺陷采用肉眼、 放大镜和体视镜观察和评级;金相试验通常指显微 观察,指在放大倍率≥100×的显微镜下评判,必要 时还得借助电子显微镜观察分析的结果。 C.金相检验标准—主要包括试验方法标准和特定零 件检验等标准。如非金属夹杂物评级标准、金属平 均晶粒度测定方法和钢件渗碳淬火回火金相检验等 标准。
热处理中的热处理质量控制技术

热处理中的热处理质量控制技术热处理是一种重要的工业过程,它可以对金属材料进行加工和改变其性能。
在进行热处理时,确保热处理质量的一致性和稳定性是至关重要的。
这就需要运用热处理质量控制技术来确保产品质量。
热处理的质量控制技术可以从多个方面来考虑。
其中最重要的是,要把控热处理温度、时间和处理环境。
这些因素直接影响热处理后材料的性质和质量。
首先,热处理温度是影响热处理效果的最重要因素。
温度不合适会导致材料内部结构与性能发生剧烈变化,从而造成热处理质量不稳定。
温度的过高或过低都会对热处理质量产生影响。
技术人员需要根据不同的材料特性和所需热处理效果,确定合适的温度范围,来确保热处理的稳定性和一致性。
其次,热处理时间也是影响热处理质量的关键因素之一。
热处理时间短,则材料的性能可能无法完全改变;热处理时间长则会导致材料过度脆化或淬火不完全等情况。
因此,需要技术人员进行热处理时间的调整和控制,以确保热处理量的一致性和稳定性。
最后,处理环境也是影响热处理质量的重要因素之一。
在热处理过程中,处理环境会直接影响材料硬度、韧性等性能。
例如在淬火工艺中,冷却介质的选择直接决定了淬火后的结构和性能。
因此,技术人员需要掌握不同材料对处理环境的要求,并进行相应的调整和控制,以确保热处理产品质量的稳定性。
总之,热处理中的热处理质量控制技术是确保产品质量和稳定性的关键。
需要技术人员具备精湛的技术和丰富的经验,通过合理的温度、时间、处理环境等热处理参数的控制,来确保热处理的一致性和稳定性。
同时,还要注重设备的维护和保养,不断提高热处理质量控制技术的水平和精度。
只有如此才能保证热处理产品的质量和竞争力。
热处理全面质量控制分解课件

多元化服务
热处理企业将提供更多元化的服务,如个性 化定制、一站式解决方案等。
THANKS
感谢观看
详细描述
真空热处理技术的成本相对较低,同时具有高效率的 特点,可以在短时间内完成大量的热处理工作。
真空热处理技术
总结词
环保、节能
详细描述
真空热处理技术是一种环保和节能的技术, 不会产生有害气体和废渣,同时可以减少能
源的消耗。
离子渗氮技 术
总结词
高耐磨性、高抗疲劳性
详细描述
离子渗氮技术是一种表面强化技术,通过离子注入和氮 化处理相结合,能够提高材料的耐磨性和抗疲劳性。
质量管理体系持续改进
持续改进的概念
持续改进的方法
持续改进是质量管理体系的核心,它 强调在不断识别问题并采取措施来解 决问题的过程中不断提高产品质量和 服务水平。
常见的持续改进方法包括:PDCA循 环(计划-执行-检查-行动)、5W1H 分析法(何事-何人-何时-何地-何因如何)和鱼骨图等。这些方法可以帮 助组织识别问题并找到根本原因,从 而采取有效的措施来解决这些问题理体系概念与构成
质量管理体系的概念
质量管理体系是一种通过建立组织内部流程、标准和系统来确保产品或服务质量的全面框架。它涵盖 了从原材料采购到最终产品交付的整个过程,并强调在所有环节中持续改进以满足客户需求。
质量管理体系的构成
一个有效的质量管理体系通常包括组织结构、职责和权限、流程、标准和系统。这些要素协同工作, 以确保从原材料到最终产品的整个过程的顺畅运行。
激光热处理技术
总结词
高精度、高效率
详细描述
激光热处理技术是一种高精度和高效率的热处理技术,能够实现局部加热和快 速冷却。
热处理质量控制程序(一)2024
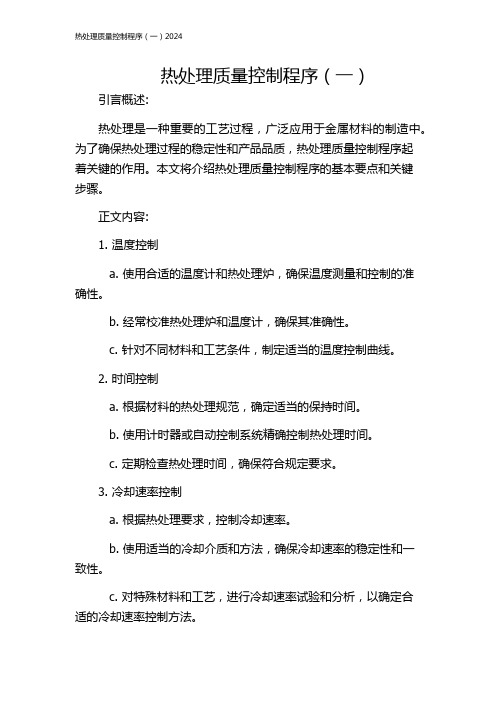
热处理质量控制程序(一)引言概述:热处理是一种重要的工艺过程,广泛应用于金属材料的制造中。
为了确保热处理过程的稳定性和产品品质,热处理质量控制程序起着关键的作用。
本文将介绍热处理质量控制程序的基本要点和关键步骤。
正文内容:1. 温度控制a. 使用合适的温度计和热处理炉,确保温度测量和控制的准确性。
b. 经常校准热处理炉和温度计,确保其准确性。
c. 针对不同材料和工艺条件,制定适当的温度控制曲线。
2. 时间控制a. 根据材料的热处理规范,确定适当的保持时间。
b. 使用计时器或自动控制系统精确控制热处理时间。
c. 定期检查热处理时间,确保符合规定要求。
3. 冷却速率控制a. 根据热处理要求,控制冷却速率。
b. 使用适当的冷却介质和方法,确保冷却速率的稳定性和一致性。
c. 对特殊材料和工艺,进行冷却速率试验和分析,以确定合适的冷却速率控制方法。
4. 气氛控制a. 根据热处理要求,选择合适的气氛。
b. 使用气氛控制系统,确保热处理过程中的气氛环境稳定。
c. 定期监测和分析热处理过程中的气氛成分,确保符合要求。
5. 产品检测a. 采用合适的检测方法,对热处理后的产品进行质量检测。
b. 定期检查热处理设备和工艺参数,确保热处理效果良好。
c. 分析和记录热处理过程中的异常情况,并采取相应的纠正措施。
总结:热处理质量控制程序是确保热处理过程稳定性和产品品质的关键。
通过温度、时间、冷却速率和气氛的控制,以及对产品的检测和分析,可以有效地保证热处理的质量。
为了确保程序的有效性,应定期检查和校准热处理设备,并记录和分析热处理过程中的异常情况,及时采取纠正措施。
热处理质量控制规程(一)

热处理质量控制规程(一)引言概述:热处理是金属材料加工过程中的重要环节,通过改变材料的结构与性质,以达到所需的力学性能和耐用性。
为了保证热处理的质量,制定了热处理质量控制规程。
本文将从五个大点来阐述热处理质量控制规程的要点。
正文:一、设备与设施的要求1. 选择合适的设备和设施,如热处理炉、淬火油等。
2. 设备应具备稳定的温度控制和压力控制。
3. 设备应定期进行检查和维修,确保正常运行。
二、质量控制标准的制定1. 根据热处理的具体要求制定相应的质量控制标准。
2. 标准应包括热处理过程中的温度、时间、介质等要素。
3. 标准应与相关国际标准或行业标准相对接,以确保质量一致性。
三、原材料控制1. 熔炼原材料应满足特定的成分要求。
2. 原材料在热处理前应进行化学分析和物理性能测试。
3. 确保原材料的质量符合热处理的要求。
四、热处理过程控制1. 确定热处理工艺参数,包括温度、时间、加热速率等。
2. 采用合适的热处理工艺,如淬火、回火等。
3. 监控热处理过程中的温度和时间,确保符合标准要求。
4. 严格控制热处理介质的浓度和温度。
五、质量检验与记录1. 进行热处理后的金属材料的物理性能测试,如硬度、韧性等。
2. 对热处理后的材料进行化学成分分析,确保符合标准要求。
3. 保留完整的热处理过程和结果记录,以备查证。
4. 定期对热处理质量进行内部审核或外部认证。
总结:热处理质量控制是确保金属材料达到所需性能的关键步骤。
通过设备与设施的要求、质量控制标准的制定、原材料控制、热处理过程控制以及质量检验与记录等方面的规程,可以有效控制热处理质量,提高金属材料的性能和可靠性。
热处理质量控制程序
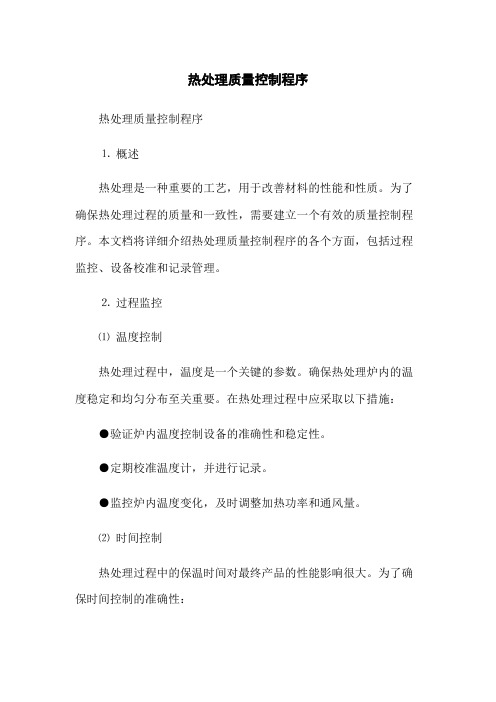
热处理质量控制程序热处理质量控制程序⒈概述热处理是一种重要的工艺,用于改善材料的性能和性质。
为了确保热处理过程的质量和一致性,需要建立一个有效的质量控制程序。
本文档将详细介绍热处理质量控制程序的各个方面,包括过程监控、设备校准和记录管理。
⒉过程监控⑴温度控制热处理过程中,温度是一个关键的参数。
确保热处理炉内的温度稳定和均匀分布至关重要。
在热处理过程中应采取以下措施:●验证炉内温度控制设备的准确性和稳定性。
●定期校准温度计,并进行记录。
●监控炉内温度变化,及时调整加热功率和通风量。
⑵时间控制热处理过程中的保温时间对最终产品的性能影响很大。
为了确保时间控制的准确性:●使用可靠的计时器,并定期校准。
●根据热处理工艺规范和产品要求,确保保温时间的准确控制。
●监控保温时间,记录每个批次的保温时间。
⑶气氛控制某些热处理过程需要控制炉内气氛的成分和压力。
为此,应:●定期检查气氛控制设备的可靠性,并进行记录。
●检测炉内气氛成分和压力,确保符合要求。
●采取适当的控制措施,如调整气氛流量和加气时间。
⒊设备校准⑴热处理炉热处理炉是热处理过程中最关键的设备,需要定期进行校准和维护:●检查炉内加热元件的完好性和连接状态。
●校准炉内温度控制设备。
●检查炉内气氛控制设备的完好性和控制准确性。
⑵温度计温度计是热处理过程中必不可少的工具,需要定期校准:●与信任的实验室合作,进行温度计的定期校准。
●校准前后记录温度计的误差,并进行修正。
⒋记录管理⑴过程记录每次热处理过程都应有详细的记录,包括温度、时间、气氛控制参数等:●记录炉内温度变化曲线,以评估温度控制的准确性。
●记录保温时间和保温温度,以评估保温过程的控制质量。
●记录气氛控制参数和炉内气氛成分,以评估气氛控制的准确性。
⑵产品检测记录每次热处理后应对产品进行检测,并记录结果:●记录产品硬度、宏观形貌和化学成分等检测结果。
●将检测结果与热处理工艺规范进行比较,以评估热处理质量。
⑶设备校准记录对热处理设备和温度计的校准都需要有相应的记录:●记录设备校准的日期、方法和结果。
热处理全面质量控制 ppt课件

1
第二个特点是热处理质量影响大,热处理 生产成炉批量投入,连续生产,一旦出现热处 理质量问题,对生产和产品的影响面很大;另 一方面热处理对象大部分是经过加工的半成品 件或成品件,如果出现热处理质量问题,其损 失都很大;更主要的是热处理缺陷漏检很容易 发生严重的机械事故,造成损失更大。因此, 从质量控制观点来看,热处理属于特种工艺, 要采取特殊措施,实施全面质量控制,制定专 门的工艺规程和检验规程。在ISO 9000系列标 准认证中,对热处理都特别给予关注,都列为 必检内容。
d> 0.45
0.05 0.07
0 .1 0
26
(4)其他要求 对于热处理加热包铝铝合金零件的设备,要
求具有足够的加热能力,以保证固溶处理加热 时尽快回复到温,防止包铝层与基体之间发生 不应有的扩散现象。
感应热处理加热电源输出功率及频率必须满 足热处理要求,输出功率控制在±5%,或输出 电压在±2.5%范围内。感应热处理机床和限时 装置应满足工艺要求。
表,进行炉子温度的自动控制,此外这两支热电偶
中应有一支并联报警装置,一旦出现超温时能自动
报警并切断电源,这种配置称之为“双联温度系
统”,另外还可采用控温、记录、报警三者分别独
立的系统,称之为“三联温度系统”。
14
热处理炉的温度测量装置应能准确地 反映出真实温度,具有足够的精度、可 靠性和稳定性。温度测量装置包括热电 偶、补偿导线及仪表,都应符合要求, 并定期检定合格。
7
三、人员素质控制
因为热处理生产过程每一步骤都是由 人操作完成的,所以人员素质是确保质量 的根本要素。热处理各类人员应具有相应 专业知识和技能,熟悉有关技术文件和规 章制度,还应了解质量控制和管理基本知 识。坚持培训、考核、发证和持证上岗等 一系措施和办法。有些关键零件的热处理, 还明确规定由一定等级以上工人操作。
热处理过程中的质量控制
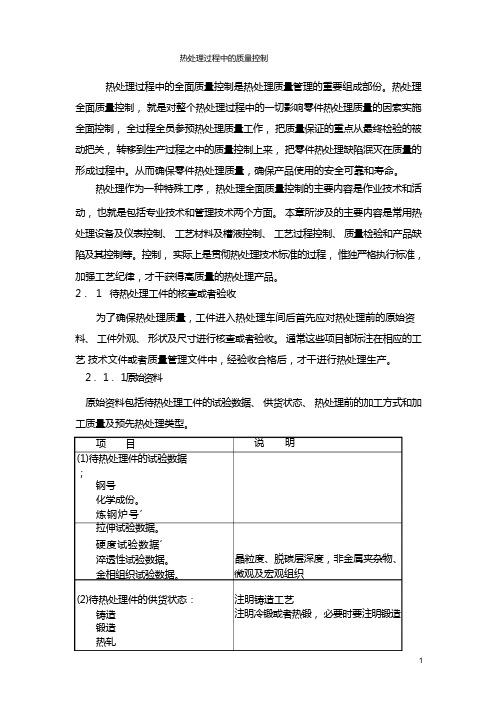
热处理过程中的质量控制热处理过程中的全面质量控制是热处理质量管理的重要组成部份。
热处理全面质量控制, 就是对整个热处理过程中的一切影响零件热处理质量的因索实施 全面控制, 全过程全员参预热处理质量工作, 把质量保证的重点从最终检验的被 动把关, 转移到生产过程之中的质量控制上来, 把零件热处理缺陷泯灭在质量的 形成过程中。
从而确保零件热处理质量,确保产品使用的安全可靠和寿命。
热处理作为一种特殊工序, 热处理全面质量控制的主要内容是作业技术和活 动, 也就是包括专业技术和管理技术两个方面。
本章所涉及的主要内容是常用热 处理设备及仪表控制、 工艺材料及槽液控制、 工艺过程控制、 质量检验和产品缺 陷及其控制等。
控制, 实际上是贯彻热处理技术标准的过程, 惟独严格执行标准, 加强工艺纪律,才干获得高质量的热处理产品。
2. 1 待热处理工件的核查或者验收为了确保热处理质量,工件进入热处理车间后首先应对热处理前的原始资 料、 工件外观、 形状及尺寸进行核查或者验收。
通常这些项目都标注在相应的工艺 技术文件或者质量管理文件中,经验收合格后,才干进行热处理生产。
2. 1. 1原始资料原始资料包括待热处理工件的试验数据、 供货状态、 热处理前的加工方式和加 工质量及预先热处理类型。
说 明晶粒度、脱碳层深度,非金属夹杂物、 微观及宏观组织注明铸造工艺注明冷锻或者热锻, 必要时要注明锻造比项 目 (1)待热处理件的试验数据;钢号化学成份。
炼钢炉号’ 拉伸试验数据。
硬度试验数据’ 淬透性试验数据。
金相组织试验数据。
(2)待热处理件的供货状态:铸造 锻造 热轧冷拔项 目 说 明(3)待热处理件热处理前的加土方式:切削方法及切削量。
冲压或者拉制 冷轧或者冷挤压 焊接热校正或者冷校正。
(4)待热处理件的预先热处理类型: 正火(或者正火回火)彻底退火 球化退火去应力退火 . 调质注:对普通工件,有*号的项目可以省略。
冶金质量控制教学课件-热处理过程中的质量控制

热处理过程中控制什么?
➢ 一 、 工艺控制
➢
1 . 加热温度与速度控制
➢
2 . 保温温度与时间控制
➢
3 . 冷却速度与(转移) 时间控制
➢ 二 、 组织控制
➢
1 . 再结晶晶粒尺寸控制
➢
2 . 沉淀相形貌 、尺寸 、分布控制
➢
3 . 凝固第二相形貌 、尺寸 、分布控制(变质后通过热处理改善形貌
不同淬火速率时A356铝合金样品基体淬火态和人工时效态的显微硬度
)
不同淬火速率时 A356合金样品T5时效后的显微组织
(a) 25 ℃water quench ; (b) 80 ℃ water quench ; (c) Air cooling 1; (d) Air cooli
流动空气
非流动空气
二 、组织控制
➢ 1. 再结晶晶粒尺寸控制 ➢ 2. 沉淀相形貌 、尺寸 、分布控制 ➢ 3. 凝固第二相形貌 、尺寸 、分布控制
(变质后通过热处理改善形貌)
沉淀相形貌 、尺寸 、分布
)
凝固第二相形貌 、尺寸 、分布
三 、缺陷控制
➢ 1. 过烧控制 ➢ 2. 变形控制 ➢ 3. 气孔控制
)
共晶硅开始过烧
➢ 三 、 缺陷控制
➢
1 . 过烧控制
➢
2 . 变形控制
)
➢
3 . 气孔控制
➢ 四 、 性能控制
➢
1 . 物理(包含力学) 性能控制
➢
2 加热温度与速度控制 ➢ 2. 保温温度与时间控制 ➢ 3. 冷却速度与(转移) 时间控制
__________________
)
共晶硅过烧
外协热处理质量控制程序

外协热处理质量控制程序外协热处理是一种非常重要的工业生产过程,可以通过改变金属材料的结构,性能和工艺获得新的材料,特别适用于汽车、航空航天、武器制造、机械制造等各个领域。
然而,热处理的质量控制非常重要,如果质量不佳,会对金属材料的性能和使用寿命产生不可逆的影响,在实际生产中对产品质量的稳定性和可靠性产生重大影响。
因此,建立一套完整且可行的外协热处理质量控制程序十分必要。
一、热处理的工艺流程及关键控制点热处理工艺包括加热、保温和冷却三个阶段。
加热阶段是将金属材料升温至一定温度,然后持续一定时间以确保金属内部温度均匀,达到热处理效果。
保温阶段是将已加热的金属材料保持一定时间,使材料内部结构得到重新组织,以改善其物理性能。
冷却阶段是在保证材料冷却速度的同时,控制冷却速度,以达到预期的效果。
在加热阶段,关键控制点包括加热时长,加热温度,加热速率等因素,以确保金属内部温度均匀。
在保温阶段,关键控制点包括保温时间,保温温度,以及保温环境等因素,以确保材料内部结构得到重新组织。
在冷却阶段,关键控制点包括冷却速率,冷却方式等因素,以确保金属材料的硬度和韧性等物理性能得到均衡发展。
二、建立外协热处理质量控制程序的原则1.全面实施热处理流程的质量控制全面实施热处理流程的质量控制,可以从加工前最开始阶段进行调查、询问材料使用目的和所需的物理、化学特性等,进行可行性分析和技术方案制定,保障整个生产流程的稳定性和材料特性的稳定性,谨防生产过程各阶段出现不良品,不留任何后遗症,真正切实提高产品的质量。
2.制定热处理工艺参数每一种材料都有适合自己的热处理工艺参数,根据材料结构、形状、尺寸等因素制定出针对性的热处理工艺参数,保障整个热处理过程的温度、时间、环境的合理性和稳定性,统一流程管理,防止因个别操作不当而导致全批次产品不合格。
3.加强工艺质量控制工作热处理工艺的过程中添加的冷却液、保温坩埚、加热装置等都要经过检验,确保其合法、合格,杜绝因材料问题而带来的品质问题。
热处理质量控制规程(二)2024
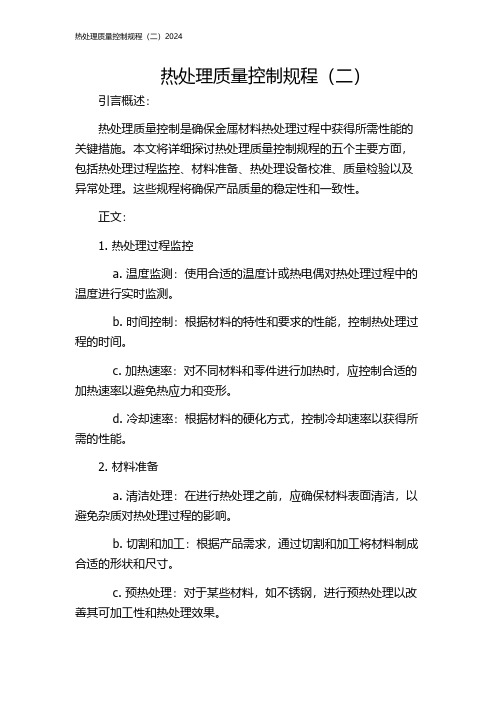
热处理质量控制规程(二)引言概述:热处理质量控制是确保金属材料热处理过程中获得所需性能的关键措施。
本文将详细探讨热处理质量控制规程的五个主要方面,包括热处理过程监控、材料准备、热处理设备校准、质量检验以及异常处理。
这些规程将确保产品质量的稳定性和一致性。
正文:1. 热处理过程监控a. 温度监测:使用合适的温度计或热电偶对热处理过程中的温度进行实时监测。
b. 时间控制:根据材料的特性和要求的性能,控制热处理过程的时间。
c. 加热速率:对不同材料和零件进行加热时,应控制合适的加热速率以避免热应力和变形。
d. 冷却速率:根据材料的硬化方式,控制冷却速率以获得所需的性能。
2. 材料准备a. 清洁处理:在进行热处理之前,应确保材料表面清洁,以避免杂质对热处理过程的影响。
b. 切割和加工:根据产品需求,通过切割和加工将材料制成合适的形状和尺寸。
c. 预热处理:对于某些材料,如不锈钢,进行预热处理以改善其可加工性和热处理效果。
3. 热处理设备校准a. 温度校准:定期对热处理设备中的温度计进行校准,确保其准确度和稳定性。
b. 加热速率校准:通过校准加热功率和时间,确保热处理设备的加热速率符合要求。
c. 冷却速率校准:通过调整冷却介质的流量和温度,控制热处理设备的冷却速率。
4. 质量检验a. 硬度测试:使用硬度计对热处理后的材料进行硬度测试,以评估其力学性能。
b. 显微组织观察:通过金相显微镜对热处理后的材料进行显微组织观察,以评估其晶粒尺寸和相组成。
c. 化学成分分析:使用化学分析仪对热处理后的材料进行化学成分分析,以确保其符合要求。
5. 异常处理a. 异常情况记录和报告:对于热处理中的异常情况,及时记录并报告相关人员,以便进行必要的调查和处理。
b. 异常样品保留:对于出现异常的热处理样品,应保留一定数量的样品以供进一步分析和评估。
c. 异常情况分析与改进:对于经常出现的异常情况,需进行深入分析并制定改进措施,以减少类似问题的发生。
热处理工序质量控制

热处理工序质量控制6.1.1 全过程掌握应建立自来料验收、热处理前清理、预热、加热、保温、冷却、回火、清理、校正、检验、防锈入库等全过程的质量掌握系统。
6.1.2 掌握点通过热处理常见缺陷(变形、裂纹、白点、过热、过烧、脱碳、硬度不足、硬度不均、机械性能差等)的统计调查,找出存在的主要质量缺陷,进行工序质量因素分析。
在工艺试验验证的基础上,确定主要原因及其掌握措施,设立掌握点。
同时,对重要的关键件也应加强工序检查,细化工艺文件,进行重点掌握。
6.1.3 前工序质量的影响应重视热处理前工序质量对最终热处理质量的影响,合理支配工艺路线和前道工序的质量掌握。
例如,机械加工应尽量削减加工应力,留意过渡圆角,防止应力集中,对长径比较大的轴类零件在粗加工或半精加工后,应支配消退内应力的退火,以削减淬火变形及开裂。
锻件应防止过热、过烧、终锻温度过低等造成的热处理缺陷。
6.1.4 工艺参数的监督加强对工艺参数的检测和记录。
一般热处理时要掌握加热温度、升温速度、保温时间、冷却方式、冷却速度、冷却介质及温度、出炉温度等工艺参数。
化学热处理时对渗碳过程还应严格掌握碳势,离子氮化时还应掌握氮化温度、保温时间、升温速度等参数。
应严格按工艺文件的规定执行,对关键件应填写热处理技术记录卡片,记录主要工艺参数及有关的条件,操作工人现场记录数据,检验人员现场核对并签字。
6.1.5 工序检验加强工序过程中的质量抽检,实行工序流转的签卡制度,凡抽检不合格的产品不得转序。
研究代用质量特性值与质量特性的相关关系,用检测代用质量特性值来快速、精确评定工艺质量,以便准时调整工艺参数。
例如,高速钢的淬火可通过对试件(或试样)晶粒度的测定,掌握晶粒度的波动范围来防止制件过热或硬度不足,削减热处理变形。
又如锻后热处理时,可通过掌握含氢量来防止锻件出现白点。
6.1.6 工装与设备6.1.6.1 关键或主要设备应备有温度指示仪表及报警装置,并实行自动记录。
- 1、下载文档前请自行甄别文档内容的完整性,平台不提供额外的编辑、内容补充、找答案等附加服务。
- 2、"仅部分预览"的文档,不可在线预览部分如存在完整性等问题,可反馈申请退款(可完整预览的文档不适用该条件!)。
- 3、如文档侵犯您的权益,请联系客服反馈,我们会尽快为您处理(人工客服工作时间:9:00-18:30)。
热处理质量控制程序热处理质量控制程序1 总则1.1为确保压力容器产品或零部件为消除残余应力,防止变形,稳定尺寸,改善力学性能及耐蚀性要求的热处理质量,本程序规定了热处理质量责任及质量控制要求。
1.2本程序适用于公司压力容器产品或零部件的热处理质量控制工作。
2 职责a.压力容器生产中产品或零部件的热处理质量控制工作由技术部门归口管理。
b.生产部门负责热处理外协委托,质检部门负责热处理试件进场验收和热处理报告、记录等文件的确认。
c.供应部门负责热处理分包方的评价和选择。
3 控制要求3.1一般要求3.1.1本公司的产品热处理应委托有资格的合格单位进行分包。
3.1.2热处理的分包方应经公司供应部门组织按Q/XHJ-B703-2010《供方评价和选择程序》规定对热处理分包方的人员素质,设备条件,测量手段,管理水平等方面进行评审合格,且在公司“合格供方名单”之中。
3.1.3需进行热处理的产品或零部件,在委托之前必须检验合格,须返修的焊缝应在热处理前返修合格。
热处理后不得再进行焊接修补或在受压件上焊接装配件。
3.1.4经热处理后返回公司的产品或零部件,应经检验员检验合格,方可流转使用。
3.1.5热处理前准备(包括热处理设备和测量仪表,热处理前对热处理工艺、检验资料审核、测温点的布置,热处理试板在炉内位置等),热处理操作过程、热处理设备和测量装置、热处理检验和试验等方面质量控制由热处理分包方负责。
3.2热处理工艺3.2.1热处理工艺编制审批和修改由热处理分包方负责,条件允许时,第Ⅰ、Ⅱ类压力容器和第Ⅲ类简单的热处理(如局部焊后热处理、焊后消除应力热处理等)可由本公司编制热处理工艺表卡(表样D06.39)热处理工艺表卡由公司焊接技术人员编制,经热处理责任人审核认可。
3.2.2热处理工艺如分包方编制时,其热处理工艺应符合热处理有关安全技术规范、标准要求且经本公司热处理责任人的审核认可。
3.2.3热处理工艺一般应包括:a.热处理的主要尺寸和重量;b.热处理类型(焊后消除应力热处理或改善力学性能、耐晶间腐蚀性能热处理等);c.热处理施工方法(炉内、炉外、局部,分段)和热处理设备;d.热处理时间—温度控制(如装炉温度、升温速度、保温温度、保温的时间、降温速度、出炉温度、冷却介质和方式等);e.测温热电偶配置数量及其所在部位的标注;f.热处理试板在炉内的位置及支撑加强防止变形的措施;g.对随炉热处理试件要求;h.当容器进行局部环带或分段焊后热处理时,对加热器件的设置和保温措施的要求等。
3.2.4 对新材料、新工艺进行热处理试验和评定,评定由热处理分包方进行,评定报告经公司热处理责任人审核认可。
3.3 热处理设备和测量装置a.热处理设备的温度测量,记录装置应有足够的测量范围和准确度,所有计量器具都应在检定的有效期内。
b.测温电偶的测温端应布置在热处理件加热部位的表面,测量点布置分布应均匀,应采用自动测温记录仪记录时间—温度,以控制热处理全过程。
c.热处理设备应定期检修,每次检修应测定有效区温差是否满足热处理工艺要求。
3.4 热处理操作3.4.1 热处理操作者应熟悉热处理标准、规范、工艺、设备和测量装置。
试验前应对热处理工艺、检验资料的完整性进行审核。
3.4.2 热处理操作者应经培训、考核合格、取得操作资格证持证上岗。
3.4.3 热处理操作者应严格执行工艺,完成热处理操作。
3.4.4 热处理的仪表自动时间—温度记录纸应由仪表人员更换,并经热处理检验员确认。
3.4.5 热处理操作者应按操作记录填写“热处理操作记录”和“热处理装炉记录”等,并签名和注明日期。
3.4.6 车间热处理工艺人员负责监督热处理操作,检查热处理记录,并核实与热处理工艺是否一致。
3.5 检验和试验3.5.1 热处理检验员对热处理操作是否符合热处理工艺要求进行检查,并在热处理自动记录表上签名确认,并注明日期。
3.5.2 随炉热处理试件按图样标准规定要求进行力学性能、金像分析、耐腐蚀等试验后,由试验人员签发试验报告,热处理温度—时间自动控制热处理记录,应经热处理责任人认可,经检验责任人归档。
3.5.3 上述记录、报告不符合热处理工艺要求时,应按《手册》“不合格品控制”规定进行处理。
3.6 记录报告审查3.6.1 热处理分包方提供的热处理检验报告应有检验员、审核人签字,并注明日期。
热处理温度—时间自动热处理记录应注明热处理炉号、工件号/产品编号、热处理日期、热处理操作工和热处理责任人签字等。
3.6.2 热处理责任人应对全部热处理记录、报告进行审查,确认签字是否满足热处理工艺要求。
3.6.3 热处理记录报告应归入产品质量档案,以供监督检验单位的检查。
4 样表a.D02.37 热处理工艺卡理化实验管理程序1 总则1.1 为了确保产品的理化、金相试验,符合法规标准和规范要求,使各项报告正确可靠,本程序规定了理化、金相试验质量控制的责任和控制要求。
1.2 本程序适用于第Ⅰ、Ⅱ、Ⅲ类压力容器理化、金相试验的管理工作。
2 职责理化、金相试验的管理和控制,由质检部负责归口管理,生产、技术、车间等部门予以配合。
3 控制要求3.1 人员资格3.1.1 理化责任人负责压力容器制造过程的材料,焊接工艺评定,焊工考试,产品焊接试板,热处理试板等理化、金相检验工作。
3.1.2 理化责任人由总经理任命,并对理化、金相检验报告正确性、可靠性负责。
3.1.3 理化、金相试验人员须经资格培训,考核合格后持证上岗。
外委的理化、金相试验及化学分析人员资格由理化实验分包方负责。
3.1.4 理化实验的分包方,公司按Q/XHJ-B703-2010《供方评价和选择程序》评审合格,且在公司合格供方名单之中。
3.2 试验设备和仪器3.2.1 理化、金相试验设备和仪器及理化试验室的条件,必须满足公司压力容器的许可项目要求。
3.2.2 理化、金相试验室的设备和仪器,必须符合国家级压力容器行业现行标准,并随标准的更新而更新。
3.2.3理化、金相试验设备和仪器,应编制周期检定计划,经有资格的法定计量单位检定合格,并粘贴明显计量标志,在有效期内使用。
超过检定周期进行的试验结果一律无效。
3.2.4 理化责任人负责编制理化、金相试验设备和仪器的操作规程,并指定专人操作管理、维护和保养,设备完好率100%。
发现问题,应立即停止试验,并向理化责任人报告处理。
3.2.5 质检部理化试验室负责理化、金相试验设备和仪器的管理(包括立卷建档)和检定。
3.3 试验的委托3.3.1 理化、金相试验委托单位应填写“理化试验委托单”(样表D02.05)连同标记清晰、并经检验合格的试件,交质控系统相关负责人审核委托内容,应符合《手册》有关规定。
对试验委托内容和试件进行审核验收。
然后交理化试验室进行试验。
3.3.2 公司理化试验室对不常做的特殊实验,(如晶间腐蚀、化学成分分析等)由理化责任人委托公司评审合格的分包方进行。
3.3.3 原材料试件、产品焊接试件、焊工考试试件、焊接工艺评定试件等,经外观和无损检测合格后和“工序传递卡”一同转到生产车间进行试件试样制备。
3.4 试样制备3.4.1 相关负责人负责试样制备的取样部位、数量,并下发试样加工图纸和试样加工工艺规程。
3.4.2 车间按工艺规程要求进行取样,加工制备。
、3.4.3 试样必须有清晰的识别和可追溯检查标记。
3.4.4 试样加工成形后,检验员需按工艺规程检验合格,再经理化责任人验收后方可交付试验。
3.5 试验、记录、报告3.5.1 各专业试验人员,按理化责任人审核签发的“理化试验委托单”的检验项目、试样制备、试验方法等标准的要求,复核试样,做好试验记录台帐(包括:拉伸、弯曲、冲击、管材工艺性试验,不锈钢耐酸钢晶间腐蚀倾向试验等),并开具出试验结果报告(包括:化学分析、晶间腐蚀试验、机械性能试验、金相检验等)。
3.5.2 试验结果报告,由试验人员填写,另一试验人员审核,理化责任人确认,并加盖理化检验责任人章后签发,并由检验人员归入质量档案。
对产品焊接试板的机械性能试验报告,检验员应填写“产品焊接试板力学和弯曲性能检验报告”(样表D02.19)并收存于产品质量证明书中,提供给顾客建档备查。
3.5.3 试验环境条件(温度、湿度)必须符合标准要求。
3.5.4 试验试样和剩余试样由理化试验室保存,保存期为产品出公司后3~个月。
3.6 理化检验分包控制3.6.1 理化检验的分包应分包给有资格的单位进行试验,并按Q/XHJ-B703-2010《供方评价和选择程序》对分包人员素质、理化设备条件、理化检验手段、管理水平和资质等方面进行评价、选择重新评价,并作出分包方评价报告,评价报告应包括理化质控系统的建立和运行,试验设备能力、试验人员素质等。
3.6.2 经评定合格的分包方,公司尚需分包技术协议,明确“试验项目全过程接受公司理化检验质控系统的质量控制”条款和双方的责任。
分包方所具备的理化检验能力,必须满足公司压力容器的许可项目要求。
3.6.3 分包方开具的理化检验报告应经理化责任人审查判断并签字确认,然后转交检验员归档保存。
3.7 监督检验安全监察、监督检验、顾客等单位对理化、金相检验报告有怀疑时,有权提出重新试验、验证等要求。
4 记录表格a. D02.05 理化实验委托单b. D02.19 产品焊接试板力学和弯曲性能检验报告。