催化裂化装置反应再生单元停工操作法
催化裂化装置产品精制碱渣处理烟气中和单元停工操作法

催化裂化装置产品精制碱渣处理烟气中和单元停工操作法一、轻燃油精制部分1.系统退碱液V26101、 V26102、R26101AB、T26101碱液汇总后去V26106,V26106碱渣通过P26102去槽车出装。
2.系统水顶油精制系统水顶油:轻燃油精制系统水顶油和吸收稳定系统水顶油同时进行,走正常流程出装置T22304底→MI26101→精制系统→出装,V26102反复抽空三次以上。
3.在轻燃油线水顶时,碱液系统接受水洗,碱液系统中水集于V26106统一排放。
4.水洗顶油结束,打开各塔、罐排污阀放水,放完后关排污阀。
注意:在水顶油过程中,T22302、T22304、V26102要反复抽空3~4次,系统中残留轻燃油才能较彻底清除。
吸收稳定和轻燃油精制系统水顶结束后,关进出该系统的界区阀,8字盲板倒向。
5.系统内各塔罐底部通入蒸汽进行蒸煮,开各塔罐顶部放空。
二、液化气干气脱硫单元1.干气由T22303来→管线P26201→管线P26207→燃料气管网→火炬跨过V26202、T26202。
2.液化气由正常流程从精制系统送至罐区。
3.干气、液化气与胺液系统分离,胺液系统循环再生。
4.停进料后,尽量保证T26201、T26202压力,配和溶剂继续循环再生8小时,直至分析合格为止。
5.溶剂停止再生后,联系溶剂再生岗位以30℃/h 逐渐降低温度,用溶剂三塔循环量控制降温速度。
6.当溶剂再生系统具备退溶剂条件时,将T26201、T26202中胺液退至再生系统,退溶剂时,胺液在现场玻璃板液面计留50%可视液位,严防干气、液化气入溶剂再生系统。
7.由稳定单元给水,液化气脱硫醇系统开始水顶液化气。
8.液化气 干气脱硫单元水运P26201给水T26201溶剂再生系统T26202LV22514FV22508LV22512FV22506水运结束后就地排放。
三、液化气脱硫醇单元1. 液化气脱硫醇系统退碱液V26301、V26303、T26301、T26303碱液汇总后去V26106,V26106碱渣通过P26102去槽车出装。
催化裂化装置气分单元停工操作法

催化裂化装置气分单元停工操作法一、气分装置停车操作1.停车前各塔罐液位逐渐降低至20%左右。
2.接到停车指令后,切断进料,关闭V24001进料调节阀和手阀。
3.注意观察V24001罐液面,当P24001抽空V24001罐无物料时,停P24001。
4.T24001切断进料后,逐渐减少T24001回流量,减小E24002加热蒸汽量,当V24002罐无物料时,切出E24003。
停T24001回流泵P24002和T24002进料泵P24003,T24001底物料自压去中间罐区,压空后关闭塔底抽出阀,逐步减少塔底重沸器加热蒸汽量,缓慢降温,最后全关蒸气调节阀FV24153。
5.T24002停止进料后,逐渐减少T24002回流量,减小E24004加热蒸汽量,当回流罐V24003无物料后,停回流泵P24004,切出E24005,维持T24002塔压力,待T24002底物料压空后,停止向T24003A进料,关塔底抽出阀,逐步减少塔底重沸器加热蒸汽量,缓慢降温,最后全关FV24157。
6.停T24003A进料时,逐渐减少T24003A塔底取热量,维持T24003B塔底返回量,丙烯产品走不合格线出装置,逐渐减少T24003B顶回流量,加大出装量,同时注意T24003B 底液面,减少内回流量。
7.T24003A/B塔物料全部由丙烷不合格线出装。
8.当V24004无物料时,停回流泵P24006和丙烯产品泵P24007;T24003B底液位空时,停精丙烯塔中间泵P24005,T24003A塔底物料自压出装。
二、系统退料、泄压1.操作要点(1)改好残余物料出装流程。
(2)全装置共分3个系统:T24001塔系统、T24002塔系统、精丙烯塔系统。
各个系统必须隔开,严禁窜压。
(3)按压力由高到低的顺序,先后打开T24002、V24003、T24001、V24002、T24003A、T24003B、V24004底部停工抽出阀,启动P24009抽残料出装。
催化裂化装置吸收稳定单元停工操作法

催化裂化装置吸收稳定单元停工操作法一、吸收稳定单元退油当反应切断进料后,分馏岗位将V22203A、B中轻燃油抽空后,停T22304至T22301的补充吸收油,退油原则尽量将油赶至T22304,各抽出泵抽空后停泵,退油结束。
分馏一中扫线开始前T22304油退完。
轻油由T22301V22302T22302T22304精制单元出装置贫吸收油走付线不经T22303,直接返T22201A,T22303中油压回T22201A,现场注意T22303液位不要压空,严禁干气窜入T22201A。
稳定塔在再沸器出口温度变化不大的情况下,加大稳定轻燃油出装量,在保证塔顶温度不变的情况下尽量加大液化气外送量,V22303无液面时,停P22306AB。
二、吸收稳定单元水顶油1. 分馏未吹扫干净E22310管程,T22304严禁进水,防止突沸。
2. 不合格轻燃油出装置线:新鲜水P22202FV22218管线P22218/2管线P22222不合格轻罐油3. 新鲜水走正常流程进T22301:P22202给水FV22218T22301P22203给水FV222184. T22301一中、二中回流线:一中:二中:P22303LV22302E22303T22301 P22304LV22303E22304T223015. 凝缩油线:T22301P22302FV22302V22302P22301FV22306E22305T22302FV22305V22301注水P22309LV229016. 脱乙烷轻燃油线:T22302P22305FV22307E22307T223047. 稳定塔回流线:P22306给水FV22308T223048. T22301补充吸收剂线:P22307FV22301T22301T223049. 吸收稳定单元撇油。
吸收稳定单元改为三塔循环流程,2小时后,将T22301、V22302抽空,水全部集中在T22302、T22304中,两塔内水位要高,以撇油线在P22307入口见水为准。
催化裂化装置反应再生单元停工操作法

催化裂化装置反应再生单元停工操作法一、反应切断进料,停富气压缩机1. 首先将重油提升管酸性水、粗轻燃油、船燃油、以及轻燃油提升管急冷油、凝缩油、回炼液化气进料停止;同时将两个提升管预提升干气改为预提升蒸汽。
2. 重油提升管以10t/h的速度降低进料负荷,轻燃油提升管保持相同速率降低轻燃油进料,同时联系油品罐区降低原料油进装量,使V22201液位降至20%。
3. 缓慢关闭烟机入口蝶阀,待烟机入口碟阀全关后,全关烟机入口闸阀,再生压力由烟机旁路双动滑阀控制。
4. 反应进料降量要平稳,随着生焦量的减少,相应的减少主风量,控制烟气氧含量维持在3~5%,同时保证再生器出口温度≮650℃,温度低可喷燃烧油,控制反应温度在510℃左右。
5. 随着反应负荷降低,外取热器、油浆、塔底油及二中取热量会逐渐减少,因此要逐步提高开工锅炉的发汽量,保证系统蒸汽压力平稳。
6. 随着反应负荷降低,调整富气压缩机转速,逐步降低反应压力至80KPa;再生压力相应降至100KPa。
7. 当重油进料量降至60t/h时,首先关闭轻燃油提升管进料,再投重油提升管进料联锁,切断进料,原料油改走关原料油进料喷嘴切断回炼油回炼,。
V22202事故旁通线去手阀。
8. 反应切断进料,两器循环烧焦2小时后,再生器喷燃烧油维持系统温降速度小于30℃/h。
9. 反应切断进料后,富气压缩机反飞动阀全开,此时反应压力改由富气机入口大、小放火炬阀控制,此时应控制好两器压力平衡,避免压力波动过大。
10. 视低压蒸汽用量,关闭富气压缩机透平蒸汽,停富气压缩机。
关闭富气压缩机进出口气动闸阀,润滑油油运30分钟后停润滑油循环。
二、转、卸催化剂1. 反应切断进料,可启用再生器大型卸料线开始卸剂,控制卸料温度≯430℃,卸料过程应密切注意管线及催化剂罐受热情况。
2. 当提升管出口温度低于480℃,此时可进行转剂,应维持负压差(再生器压力100KPa,反应器压力120KPa),先关死两个再生滑阀(应现场手动摇死),将反应器内催化剂转入再生器。
140万吨重油催化裂化装置操作规程

目录第一章装置概况 (1)第一节装置简介 (1)第二节物料平衡及催化剂 (4)第三节主要工艺流程说明 (6)第四节主要设计条件及工艺计算汇总 (21)第五节消耗指标及能耗 (34)第六节装置设备规格表 (42)第七节机械规格表 (50)第八节安全阀规格表 (62)第九节装置仪表规格表 (63)第十节反再部分设备仪表管嘴明细表 (81)第十一节限流孔板表 (86)第十二节装置开工以来大的动改项目汇总 (88)第二章岗位操作法 (89)第一节反应――再生单元操作法 (89)第二节 CO焚烧炉-余热锅炉单元操作法 (131)第三节机组单元操作法 (169)第一部分三机组单元操作法 (169)第二部分备用风机操作法 (193)第三部分增压风机操作法 (202)第四部分气压机单元操作法 (209)第四节分馏单元操作法 (233)第五节吸收-稳定单元操作法 (253)第六节汽油脱臭单元操作法 (273)第七节脱硫单元操作法 (278)第八节特殊设备操作法 (291)第九节装置开停工步骤 (300)第十节装置生产运行大事记 (301)第三章装置安全常识 (307)第一节基本概念 (307)第二节基本常识 (310)第三节基本技能 (315)第四节有关规定、规章制度、标准 (317)第一章装置概况第一节装置简介一. 装置设计依据及规模中国石油化工股份有限公司济南分公司为原油一次加工能力500万吨/年的大型燃料-润滑-化工型石油加工企业。
鉴于分公司原油加工量逐年递增的实际情况,原有二次加工能力已不能满足生产发展的需要,增上本套140万吨/年重油催化裂化装置,对提高济南分公司原油加工深度及为下游化工装置提供原料将发挥重要作用。
本装置催化裂化部分由中国石化北京设计院设计,设计规模为140万吨/年,产品精制部分由济炼设计室设计,设计规模为干气10万吨/年、液化气20万吨/年、汽油70万吨/年,由中石化第二、第十建安公司建设安装。
催化裂化装置反应再生系统工艺流程
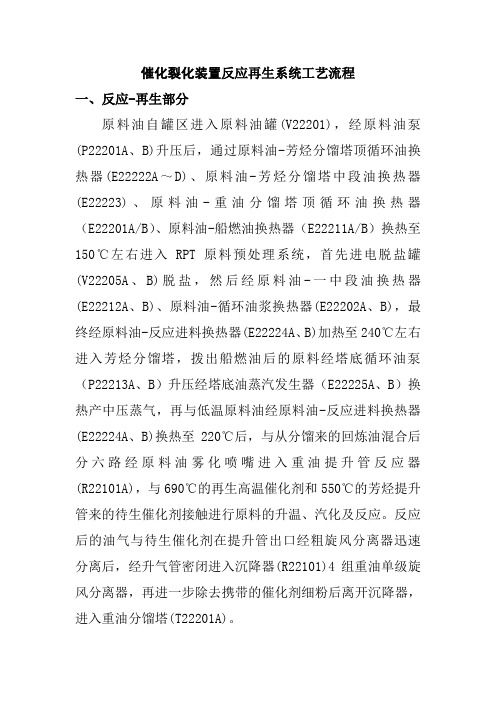
催化裂化装置反应再生系统工艺流程一、反应-再生部分原料油自罐区进入原料油罐(V22201),经原料油泵(P22201A、B)升压后,通过原料油-芳烃分馏塔顶循环油换热器(E22222A~D)、原料油-芳烃分馏塔中段油换热器(E22223)、原料油-重油分馏塔顶循环油换热器(E22201A/B)、原料油-船燃油换热器(E22211A/B)换热至150℃左右进入RPT原料预处理系统,首先进电脱盐罐(V22205A、B)脱盐,然后经原料油-一中段油换热器(E22212A、B)、原料油-循环油浆换热器(E22202A、B),最终经原料油-反应进料换热器(E22224A、B)加热至240℃左右进入芳烃分馏塔,拨出船燃油后的原料经塔底循环油泵(P22213A、B)升压经塔底油蒸汽发生器(E22225A、B)换热产中压蒸气,再与低温原料油经原料油-反应进料换热器(E22224A、B)换热至220℃后,与从分馏来的回炼油混合后分六路经原料油雾化喷嘴进入重油提升管反应器(R22101A),与690℃的再生高温催化剂和550℃的芳烃提升管来的待生催化剂接触进行原料的升温、汽化及反应。
反应后的油气与待生催化剂在提升管出口经粗旋风分离器迅速分离后,经升气管密闭进入沉降器(R22101)4组重油单级旋风分离器,再进一步除去携带的催化剂细粉后离开沉降器,进入重油分馏塔(T22201A)。
重油分馏塔分馏后的塔顶油气经冷凝冷却后进入油气分离器(V22203A),分离出的粗轻燃油分四路经雾化喷嘴进入芳烃提升管反应器(R22101B),与690℃催化剂接触进行原料的升温、汽化及反应。
反应后的油气与待生催化剂在提升管出口经粗旋风分离器迅速分离后,经升气管密闭进入沉降器内轻燃油单级旋风分离器,再进一步除去携带的催化剂细粉后离开沉降器,进入芳烃分馏塔(T22201B)。
油气分离出来的待生催化剂与重油部分的待生催化剂一起进入反应沉降器的汽提段。
重油催化裂化反应再生单元操作法

重油催化裂化反应再生单元操作法一、正常操作1.提升管出口温度(8TIC101)的控制反应温度对反应速度、产品分布和质量、再生烧焦率和设备结焦都有很大影响,它是日常生产中调节反应转化率和改变生产方案的最主要的调节参数之一。
提升管出口温度的设计值为510~538℃。
该温度的确定:1)用于改变生产方案:液化气方案(510~515℃)汽油方案(503~510℃)柴油方案(497~503℃)2)控制设备结焦:a.反应终了温度偏高,热裂化反应严重,热裂化缩合结焦--“硬焦”。
b.反应终了温度偏低,油气中重沸物冷凝、聚合结焦--“软焦”。
3) 降低再生烧焦率:减少非反应焦--可汽提炭,温度在汽提影响因素中起很大作用。
4) 对产品质量的影响:提高温度可以提高汽油辛烷值,但随着温度的升高汽油烯烃含量增加。
主要影响因素:1)催化剂循环量增加,反应温度上升。
2)原料油预热温度(8TIC201)上升,反应温度上升。
3)进料量及回炼比的变化。
4)进料性质改变影响反应转化率,反应温度变化。
5)原料带水,反应温度下降。
6)二再温度(8TI154)升高,反应温度上升。
7)反应沉降器压力(8PI108)升高,反应温度下降。
8)提升管注汽量的变化。
9)预提升介质及介质量的变化。
10)终止剂注入量增大,反应温度下降。
11)再生斜管流化不好,反应温度变化。
12)新鲜催化剂补充量的变化。
13)再生剂定炭高低的变化。
14)钝化剂是否加注及注入量多少的影响。
15)反应助剂是否加入及加入量多少的影响。
16)仪表或滑阀失灵。
调节方法:1)正常情况下,通过8TIC101调节再生滑阀开度改变催化剂循环量来自动控制提升管出口温度。
2)注入终止剂后,可视转化率和产品分布情况适当调整反应温度。
3)适当调整外取热器取热量,保证相对平稳的再生温度。
4)再生斜管流化不好时应尽快查明原因进行处理,以建立良好的催化剂循环量。
5)滑阀失灵引起自锁时(除跟踪失调外),应相对平稳各操作参数,尽量减少波动。
第三章催化裂化装置岗位操作法

第三章岗位操作法1. 反应岗位操作法1.1 任务、操作原则:根据原料油性质、催化剂性质、生产方案,选择合适的操作参数,控制好物料、热量、压力三大平衡,保持两器流化畅通,精心调节,发现问题及时联系处理,避免各类事故的发生。
使用分子筛催化剂,将重质原料油在提升管反应器内转化为干气、液化气、汽油、柴油、油浆和焦炭等,优化再生条件,提高烧焦强度,保持催化剂活性,控制合适的反应深度,精心调节,提高目的产品收率,降低能耗。
将反应后的油气送至分馏塔,再生烟气送至烟机余热锅炉。
在装置中,由于热平衡的制约,各操作变量相互关联,难以将某一操作变量孤立出来研究。
相反,在实验室试验装置中,靠电加热,催化裂解的操作变量能够独立于热平衡,使改变某一操作变量,维持其它变量恒定成为可能,并研究其对催化裂解的影响,其结果对工业装置有很大的指导性。
对催化裂解的关键操作变量分别讨论力图突出某一变量的影响,但因催化裂解各操作变量的相互关联性,难以将某一变量的影响和其它变量的影响严格区分开来,只有深刻理解其间的关联,才能深刻理解操作变量对催化裂解的影响。
(一)反应温度反应温度对反应速度和产品质量都有重大影响,催化裂解反应温度一般比蜡油催化裂化要高15--30℃。
1.据文献介绍,反应温度每提高10℃,反应速度提高10~20%。
2.•高反应温度可以提高液化气中烯烃产率(C3、C4)。
汽油辛烷值提高了,但产率下降。
3.•低反应温度又适逢大回炼比和低活性催化剂,可以显著提高轻油收率。
同时,柴油的十六烷值和汽油的诱导期升高,因油气中的烯烃随着裂解条件的缓和而减少。
4. 在大比例掺炼渣油时,如热量过剩,采用低反应温度有利于催化裂解装置维持热平衡,如热量不过剩,则可以提高掺炼比。
(二)反应压力反应压力是独立操作变量,但一般是不能任意改变的,须从装置的压力、设备及各部分情况来综合考虑。
反应压力的提高增加了反应物的浓度和反应时间,有利于提高反应速度和转化率。
催化裂化装置停工方案

加氢裂化装置正常停工一般程序和方法

加氢裂化装置正常停工一般程序和方法1.1停工前的准备1.1.1停工前先通知调度、原料、化验、仪表、电修、钳工等有关单位。
1.1.2停工时由于管线易凝,应彻底检查伴热是否开大畅通,确保装置内外管线不被蜡油凝堵。
1.1.3列出所有的盲板,并准备好盲板。
1.1.4氮气分析,必须保证氮气纯度>99.9%。
严防氮气置换时氧气进入系统,产生爆炸性气体。
1.1.5联系调度、原料,准备好停工常二线柴油约1000吨,经DAO线进装置。
1.1.6准备好碱Na2CO31000kg。
1.1.7停工过程中,要有意识的测试个紧急停车系统的正常。
1.2停工步骤(一)反应1.停DAO,反应降温降量,分馏产品改线1.1停DAO,处理管线逐步降低DAO的掺炼比例直至停DAO,调整好操作保证产品质量合格。
DAO管线先用冲洗油(本装置柴油)置换,再用蒸汽吹扫。
1.2反应降温降量1.2.1以15℃/h的降温速度,把R1002的入口温度降低20℃,增加R1002床层间的冷氢量,当R1002的所有床层温度比正常低20℃或更多时,降量至40t/h,每次降量5t,稳定1小时后再下一次降量。
降量过程中尽可能保证转化率不变。
若部分循环,降量同时逐渐降低循环油量直至停循环,若减压塔底油外放不及,则尾油部分改走减压侧线流程。
1.2.2当新鲜进料量降为正常值的一半后,在30分钟内降低R1001入口15℃。
用冷氢控制R1001催化剂床层出口温度相等。
R1002的出口温度比正常低15℃更多以后,在1小时内降低R1002所有催化剂床层入口温度25℃。
1.2.3 R1002中所有催化剂床层温度低于正常值45℃或更多时,逐渐中断新鲜进料和循环油,并继续氢气循环。
在中断进料后,尽快用循环氢把油自高压泵出口把进料线,炉管,换热器组的油冲洗入R1001。
注意:启用吹扫氢时,要缓慢进行。
1.2.4降温时,用TIC1114、TIC1147及使用床层急冷氢,降反应器入口温度的同时,相应地降低后几个床层温度,使各床层降温同步进行。
催化裂化操作规程
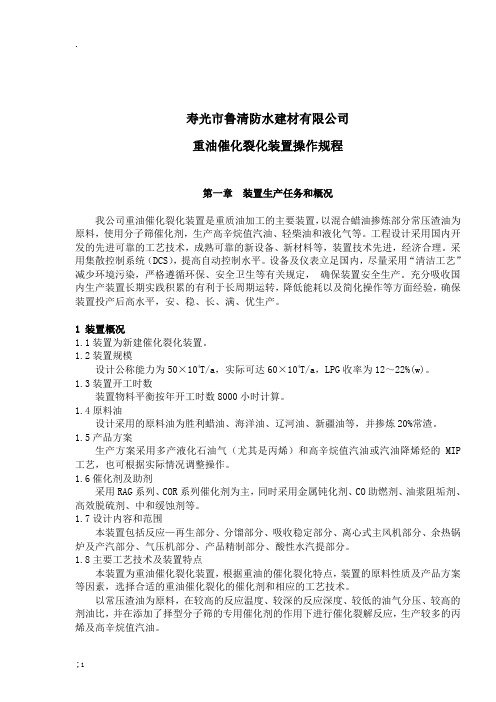
寿光市鲁清防水建材有限公司重油催化裂化装置操作规程第一章装置生产任务和概况我公司重油催化裂化装置是重质油加工的主要装置,以混合蜡油掺炼部分常压渣油为原料,使用分子筛催化剂,生产高辛烷值汽油、轻柴油和液化气等。
工程设计采用国内开发的先进可靠的工艺技术,成熟可靠的新设备、新材料等,装置技术先进,经济合理。
采用集散控制系统(DCS),提高自动控制水平。
设备及仪表立足国内,尽量采用“清洁工艺”减少环境污染,严格遵循环保、安全卫生等有关规定,确保装置安全生产。
充分吸收国内生产装置长期实践积累的有利于长周期运转,降低能耗以及简化操作等方面经验,确保装置投产后高水平,安、稳、长、满、优生产。
1 装置概况1.1装置为新建催化裂化装置。
1.2装置规模设计公称能力为50×104T/a,实际可达60×104T/a,LPG收率为12~22%(w)。
1.3装置开工时数装置物料平衡按年开工时数8000小时计算。
1.4原料油设计采用的原料油为胜利蜡油、海洋油、辽河油、新疆油等,并掺炼20%常渣。
1.5产品方案生产方案采用多产液化石油气(尤其是丙烯)和高辛烷值汽油或汽油降烯烃的MIP 工艺,也可根据实际情况调整操作。
1.6催化剂及助剂采用RAG系列、COR系列催化剂为主,同时采用金属钝化剂、CO助燃剂、油浆阻垢剂、高效脱硫剂、中和缓蚀剂等。
1.7设计内容和范围本装置包括反应—再生部分、分馏部分、吸收稳定部分、离心式主风机部分、余热锅炉及产汽部分、气压机部分、产品精制部分、酸性水汽提部分。
1.8主要工艺技术及装置特点本装置为重油催化裂化装置,根据重油的催化裂化特点,装置的原料性质及产品方案等因素,选择合适的重油催化裂化的催化剂和相应的工艺技术。
以常压渣油为原料,在较高的反应温度、较深的反应深度、较低的油气分压、较高的剂油比,并在添加了择型分子筛的专用催化剂的作用下进行催化裂解反应,生产较多的丙烯及高辛烷值汽油。
催化裂化装置紧急停工应急预案

催化裂化装置紧急停工应急预案1.目的为确保在催化装置故障时,总调度室应急指挥协调工作的有序开展,特制订该应急预案。
2.适用范围适用于公司在1000万吨/年生产线全流程生产时,催化发生故障时,总调度室的应急指挥和协调工作。
3.预案启动条件催化装置遇到停电或关键设备故障,生产无法继续进行下去。
4.应急要求炼油部、油品处、动力厂根据渣油加氢可能出现的紧急停工,制定相应应急预案,并贯彻落实到操作层。
5.应急要点及程序5.1:原料改出装置5.1.1:原料供应来源描述:渣油加氢加氢重油走561线进装置;常减压减二线热蜡油走装置互供线进催化;北罐区开泵付罐区渣油走577线进装置;焦化、重整液态烃进装置作为提升管提升气;重整拔头油走三垅口274线阀组进催化V203;聚丙烯装置尾气、芳烃010线轻烃、S-Zorb轻烃、240万汽提塔回流管汽油进V203。
5.1生产装置原料改动原则5.2.1 常减压装置装置加工量按最低负荷控制(60%负荷,加工量14000t/d 左右),停止掺炼排水污油,渣油加氢装置立即降量生产,停止带炼罐区蜡油或和渣油。
5.2.2 催化切断减二线蜡油进料后,富余的常减压减二线轻蜡油 立即投用冷却器E133、E138降温外放,原则上安排进六垅,流程为:1#常减压500线阀→六垅蜡油罐。
常减压蜡油流程示意图:罐区500线六垅平台蜡油流程示意图北罐区500六垅500常减压189六垅189常减压燃料油190六垅190焦蜡225六垅2251#192六垅六垅!#催化常减压直供轻蜡油、重蜡油停进催化装置,渣油加氢装置加氢重油停进催化,1#催化在保证生产安全的前提下适当提加工量以平衡加氢重油,富余部分在五垅平台经561线改进热油罐接收。
五垅山脚加氢重油阀组示意图561线去五垅去焦化去1#催化五垅来5.2.3 如焦化蜡油在催化,则安排改至1#催化或渣油加氢装置,如焦化在带炼冷渣,则立即安排装置停止带炼。
5.2.4 因原料中断,通知S-Zorb 装置改循环;如果催化汽油在S-Zorb 装置边界分流去了1#催化预碱洗,则通知S-Zorb 人员关闭去1#催化的阀门,并告知1#催化。
催化裂化装置反应再生系统操作

任务二 反应再生岗操作 -------反应再生系统操作
要点回顾与检查
同学们上节课已经学习了反应再生系统流程和操作变量。 检查同学们掌握的情况: 1、简述反应再生系统工艺流程? 2、反应再生系统操作变量有哪些?
任务布置
简述右图反应再生系统工 艺流程。
1.控制物料、热量、压 力三大平衡,保持两器 流化通畅。 2.根据反应再生系统操 作规程调整控制参数。
(一)温度控制: 反应再生系统主要控制的温度点有:原料预热温度、
反应器出口温度、再生器床层温度等。
(二)压力控制 反应再生系统主要控制的压力点有:再生器压力、反应 沉降器压力等。 (三)汽提蒸汽 (四)再生烟气氧含量的控制 若再生烟气氧含量过高,再生器稀相易发生二次燃烧; 过低时,再生器定碳量不易控制到低于0.1%,且易发生碳 堆。该参数是判断再生器工况的一个重要参数。
(五)反应深度的控制 反应深度是裂化反应过程转化率高低的标志。可通过观 察富气和粗汽油产率及回炼油罐和分馏塔底液位高低来判 断。反应深度过高,裂化反应过程中会将汽油、轻柴油及 中间产物进一步裂化,进而转化为气体和焦炭。反应深度 的变化反映在分馏塔底液面变化是非常明显的。当分馏操 作平稳,回炼油罐液面恒定,分馏塔底液面上升,说明反 应深度减少。
二、非正常操作 1.反应温度大幅度波动 2、反应压力大幅波动 3、沉降器汽提段藏量突然波动 4.催化剂“架桥” 5、再生器压力大幅波动
能力提升
能力提升
Description of the contents
1.仿真训练参数调整 2.观看平台反应再生系统操作视频
任务布置
简述右图反应再生系统工 艺流程。
1.控制物料、热量、压 力三大平衡,保持两器 流化通畅。 2.根据反应再生系统操 作规程调整控制参数。
催化裂化装置两机开停机单元操作

催化裂化装置两机开机、停机操作步骤第一节主风机组操作一.试运准备工作(二).试运前的准备工作1.组成一个由施工、生产、设计及制造四方参加的试车领导小组,负责试车的组织和指挥工作;2.试车前必须编制详细试车方案,并经试车领导小组讨论批准;3.由熟悉本机组的熟练操作工人担任试车工作的操作人员,由熟悉本机组的熟练安装人员参加试车中的维护工作;4.向参加试车人员详细交代试车方案和有关注意事项,包括安全注意事项,操作人员必须熟悉操作规程,并需经考试合格后才能上岗;5.准备各种消防器材,放置在现场,特别放在油站及烟机附近;6.必须有专职工程师签署的安装记录并经试车领导小组审查和批准;7.安装必要的检测仪表,供试车记录和分析用。
例如:八线示波器(记录主电机启动全过程的有关参数);振动频谱分析仪(检测和记录各单机运转时振动情况并及时分析其频谱等);烟气含尘粒子分析仪等。
二.各系统组成试运(一).润滑油系统试运转[P]—启动润滑油箱电加热器,将油加热到25℃,油箱进行脱水[P]—启动润滑油系统的主油泵,建立油系统的循环[P]—调整润滑油压力,在进油集合管处为0.15MPa[P]—润滑油系统进行自保项目试验[P]—逐步降低上油集合管处油压至0.11MPa时,应发出低油压报警信号且辅助油泵自启动[P]—使上油集合管处油压继续下降至0.08MPa时应报警,并发出停机信号(P)—过滤器差压大于或等于0.15MPa应报警(P)—当上油集合管处油压低于0.14MPa时,主电机不能启动(P)—当上述检验合格后,进行润滑油系统的运转,运转时间最低为72小时,以分析油质合格为准(P)—若经72小时运转后油质分析合格,且各自保联锁准确无误,可视为油系统试运合格(P)—油系统试运合格后,由机修人员清洗过滤器,各轴瓦,拆除进油管道上的临时滤网(二).盘车装置的试运转[P]—将润滑油系统投用(P)—确认润滑油系统正常[P]—投入盘车装置,点动盘车(P)—确认点动盘车无异常[P]—投入连续盘车(P)—仔细确认检查各单机有无摩擦及其他异常声音(P)—确认盘车正常[P]—停电动盘车器(P)—在大小齿轮惰走时观察盘车装置脱离情况(三).电机无负荷试运转1.试运转前的准备工作(P)—确认电修按有关电气规程检查电机绝缘电阻和高压部分接线(P)—确认电修已经将高低压配电设备以及电动/发电机等电气设备的整定、试验、调校均已完成(P)—全面检查各螺栓紧固情况应符合要求(P)—确认机修将电机与齿轮箱之间的联轴器断开并固定好电机侧的半个联轴器(P)—盘车检查转子,无异常声音,转动灵活[P]—投入监测、控制仪表[P]—按操作规程启动润滑油主油泵,建立正常的润滑油系统工作循环[P]—冷却水系统送水2.检查转向(P)—准备工作全部检查合格[P]—用手动开关进行瞬时启动电动机(即转子转速未达额定转速时立即停车)(P)—检查转向及转子转动情况(P)—转向合格后,准备正式启动电动机3.启动电动机[P]—记录启动电流、电压、启动时间等,运行中每半小时记录一次电流、电压、轴承温度、定子温度和轴振动等,如有异常情况须立即停机进行处理(P)—连续运行两小时,无异常情况各项指标符合技术文件规定,视为电动机空负荷试运转合格[P]—停机,并记录惰走时间。
加氢裂化装置正常停工程序

加氢裂化装置正常停工程序正常停工是由于装置运行至末期,设备需要检修维护、催化剂需卸出再生或催化剂需要部分或全部更换而进行的有计划停工。
一、停工前准备工作1、装置停工前,工程技术人员编制好停工网络统筹图,使停工各个步骤按时间表准点进行。
2、根据每次停工要求,详细制订停工措施(如停工方案,吹扫方案,中和清洗方案等),若进行催化剂更换或器外再生应制订相应的卸剂和装剂方案。
3、按停工检修项目要求制定出盲板图,并按要求准备妥所有的盲板。
编制出需加、拆的盲板表。
4、通知与装置有关的单位作好相应的停工准备,工程技术人员在停工前要把制订好的停工方案发放到班组。
操作工必须根据停工方案熟练掌握本岗位的停工步骤,充分做好停工准备。
5、根据停工检修项目要求,提出需要检修、维护、清扫的设备或其它工作,通知有关维修部门,以便做好相应的准备工作。
6、停工后所需的用品、材料均应准备妥当。
7、联系调度准备低氮油约1200吨,落实产品及不合格产品的走向。
8、通知分析站作好相关项目分析的准备工作。
9、联系调度准备好停工用的蒸汽和足够的高、低压氮气。
二、停工程序1)反应降温降量,分馏产品改线(1)反应降温降量①以15℃/h的降温速度,均匀降低1401-R-101催化剂床层温度比正常反应温度低20℃,同时均匀降低1401-R-102催化剂床层温度比正常反应温度低20℃,然后继续以15℃/h 的降温速度,均匀降低催化剂床层温度(CAT)至310℃,最后用冷氢使所有床层温度低于325℃。
同时降量至110t/h,降量速度6t/h。
反应温度至340℃,可逐步把尾油改长循环。
②降温时,用高压换热器旁路1401-TIC-0801、反应进料加热炉出口温控及使用急冷气,降反应器入口温度的同时,相应地降低后几个床层的温度,使各床层降温同步进行。
③降低进料时,反应器进料和反应产物在短期内物料会不平衡,因此,每次降量的幅度要小,且注意调整1401-TIC-0801。
催化裂化装置正常停车步骤

催化裂化装置正常停车步骤第一节反应-再生单元停工操作法一、反应切断进料,停富气压缩机1. 首先将重油提升管酸性水、粗轻燃油、船燃油、以及轻燃油提升管急冷油、凝缩油、回炼液化气进料停止;同时将两个提升管预提升干气改为预提升蒸汽。
2. 重油提升管以10t/h的速度降低进料负荷,轻燃油提升管保持相同速率降低轻燃油进料,同时联系油品罐区降低原料油进装量,使V22201液位降至20%。
3. 缓慢关闭烟机入口蝶阀,待烟机入口碟阀全关后,全关烟机入口闸阀,再生压力由烟机旁路双动滑阀控制。
4. 反应进料降量要平稳,随着生焦量的减少,相应的减少主风量,控制烟气氧含量维持在3~5%,同时保证再生器出口温度≮650℃,温度低可喷燃烧油,控制反应温度在510℃左右。
5. 随着反应负荷降低,外取热器、油浆、塔底油及二中取热量会逐渐减少,因此要逐步提高开工锅炉的发汽量,保证系统蒸汽压力平稳。
6. 随着反应负荷降低,调整富气压缩机转速,逐步降低反应压力至80KPa;再生压力相应降至100KPa。
7. 当重油进料量降至60t/h时,首先关闭轻燃油提升管进料,再投重油提升管进料联锁,切断进料,原料油改走事故旁通线去V22202。
切断回炼油回炼,关原料油进料喷嘴手阀。
8. 反应切断进料,两器循环烧焦2小时后,再生器喷燃烧油维持系统温降速度小于30℃/h。
9. 反应切断进料后,富气压缩机反飞动阀全开,此时反应压力改由富气机入口大、小放火炬阀控制,此时应控制好两器压力平衡,避免压力波动过大。
10. 视低压蒸汽用量,关闭富气压缩机透平蒸汽,停富气压缩机。
关闭富气压缩机进出口气动闸阀,润滑油油运30分钟后停润滑油循环。
二、转、卸催化剂1. 反应切断进料,可启用再生器大型卸料线开始卸剂,控制卸料温度≯430℃,卸料过程应密切注意管线及催化剂罐受热情况。
2. 当提升管出口温度低于480℃,此时可进行转剂,应维持负压差(再生器压力100KPa,反应器压力120KPa),先关死两个再生滑阀(应现场手动摇死),将反应器内催化剂转入再生器。
催化裂化装置反应再生系统单独停工检修

f r o m o t h e r s y s t e ms , a b n o m a r l l f u i d i z e d r e a s o n s o f c a t a l y s t i n r e g e n e r a t i o n s y s t e m we r e f o u n d a n d s o l v e d s u c c e s s f u l l y,
利 用 常减 压 电脱盐装 置 消缺 改造 时机 ,对催 化 裂化装 置 反应 再生 系统 单独 停工检 修 ,此 次消 缺 目 的很 明确 : 即查 找催 化裂 化装 置待 生线 路流 化异 常 、
能力为 1 . 0 Mt / a , 设 计 中采用 了洛 阳工程 公 司开发 的 RO C C — VA型专利技 术 ,包括 同轴式 两器 ( 反应 器一
l _ l 卟
措施 的u ,其它多是对一些关键设备检修进行一些
阐述 。反应 再生 系 统多是 关 于反应 器衬 里及 关键 内 构 件检 修 ‘ ,像 关 于催 化裂 化装 置反应 再生 系 统单 独 停 工检修 的文章 很少 。 通过 制定 完善 的停 工吹 扫 、
馏 、吸收 稳定 等系 统 隔离 ,在反应 再 生系 统单 独停 工 检修 期 间做 好相 应 的安全措 施 。 以前 石化 系统 关 于催化 检 修 的文献 报道 ,有 阐述装 置 整体检 修 安全 改造 , 设. 4 Mt / a 。催 化 装 置流 程简 图见 图 1 。
J I ANG He n g, SUN Ku n, YUFu- Do n g
( S i n o p e c Qi n g d a o P e t r o c h e mi c a l C o . , L t d . , S h a n d o n g Q i n g d a o 2 6 6 0 4 3 ,C h i n a )
催化裂化装置停开工培训讲义

外取热流化不死 床即可
4
讨论:是先切 进料后停机还 是先停气压机 后切进料?
四、切断进料
反应
5
分馏
吸稳
在分馏热源不足 时,重沸器走旁 路,三塔循环降 温,保持系统压 力。
机组
气压机停机后, 按气压机停机要 求开关各阀门。
热工
余热锅炉保证液 位,关闭并汽大 阀和饱和汽进汽 阀,开放空。 油浆发汽停上水
机组 热工
扫机组有 关管线 所有汽包放 净水
待打开人孔
扫线完毕, 与外联系线 加盲板;水冲 洗、煮塔
12
扫线完毕, 与外联系线 加盲板;开 塔顶放空蒸 塔24小时; 后开始钝化
关闭与外界 联系阀门
七、蒸塔 钝化
分馏
粗汽油转污油
吸稳
机组
热工
注意蒸汽压力, 外引蒸汽保证低 压蒸汽压力
及时将V-1303内 气压机维持运 液化气送净,防 转,适当增加反 止气压机切除后, 飞动阀开度,全 液化气泵抽空。 开时可降转数。 做好停气压机的 准备,与反应联 系好按规程停气 压机。 保持系统压力和 三塔循环; 停气压机
适量外甩,降低 塔底液位
备机试运 部分盲板拆除 试通放火炬线 人员安排
提前清楚盲板位置 分顶蝶阀、放火炬大小阀
曾出现的问题:2007年停工分顶 蝶阀失灵全关,0.3MPa,安全阀 没跳,设备问题
停工准备
扫线大表 扫线注意事项
扫线难点:1、E1312如何做到不互 串?2、焦蜡罐放净油?、3、粗汽 油罐、4、分馏一中线、
常减压提前停工时催化装置准备工作
地下线切水、 开两台冷蜡 泵等
提前将过热蒸汽改进减温减压器
2007年停工投过热蒸 汽进减压器时,造成 汽轮机飞车,原因是 饱和蒸汽阀未关严
- 1、下载文档前请自行甄别文档内容的完整性,平台不提供额外的编辑、内容补充、找答案等附加服务。
- 2、"仅部分预览"的文档,不可在线预览部分如存在完整性等问题,可反馈申请退款(可完整预览的文档不适用该条件!)。
- 3、如文档侵犯您的权益,请联系客服反馈,我们会尽快为您处理(人工客服工作时间:9:00-18:30)。
催化裂化装置反应再生单元停工操作法
一、反应切断进料,停富气压缩机
1. 首先将重油提升管酸性水、粗轻燃油、船燃油、以及轻燃油提升管急冷油、凝缩油、回炼液化气进料停止;同时将两个提升管预提升干气改为预提升蒸汽。
2. 重油提升管以10t/h的速度降低进料负荷,轻燃油提升管保持相同速率降低轻燃油进料,同时联系油品罐区降低原料油进装量,使V22201液位降至20%。
3. 缓慢关闭烟机入口蝶阀,待烟机入口碟阀全关后,全关烟机入口闸阀,再生压力由烟机旁路双动滑阀控制。
4. 反应进料降量要平稳,随着生焦量的减少,相应的减少主风量,控制烟气氧含量维持在3~5%,同时保证再生器出口温度≮650℃,温度低可喷燃烧油,控制反应温度在510℃左右。
5. 随着反应负荷降低,外取热器、油浆、塔底油及二中取热量会逐渐减少,因此要逐步提高开工锅炉的发汽量,保证系统蒸汽压力平稳。
6. 随着反应负荷降低,调整富气压缩机转速,逐步降低反应压力至80KPa;再生压力相应降至100KPa。
7. 当重油进料量降至60t/h时,首先关闭轻燃油提升管进料,再投重油提升管进料联锁,切断进料,原料油改走关原
料油进料喷嘴切断回炼油回炼,。
V22202事故旁通线去
手阀。
8. 反应切断进料,两器循环烧焦2小时后,再生器喷燃烧油维持系统温降速度小于30℃/h。
9. 反应切断进料后,富气压缩机反飞动阀全开,此时反应压力改由富气机入口大、小放火炬阀控制,此时应控制好两器压力平衡,避免压力波动过大。
10. 视低压蒸汽用量,关闭富气压缩机透平蒸汽,停富气压缩机。
关闭富气压缩机进出口气动闸阀,润滑油油运30分钟后停润滑油循环。
二、转、卸催化剂
1. 反应切断进料,可启用再生器大型卸料线开始卸剂,控制卸料温度≯430℃,卸料过程应密切注意管线及催化剂罐受热情况。
2. 当提升管出口温度低于480℃,此时可进行转剂,应维持负压差(再生器压力100KPa,反应器压力120KPa),先关死两个再生滑阀(应现场手动摇死),将反应器内催化剂转入再生器。
待反应器藏量、密度回零,且沉降器汽提段压降、待生塞阀压降回零,说明反应器及待生立管催化剂卸净,此时,关闭待生塞阀(现场手动摇死),切断两器。
3. 反应沉降器加大蒸汽量尽快赶油气,当催化剂卸净后,关闭雾化、防焦蒸汽,保留预提升蒸汽和汽提蒸汽。
此
时分馏岗位方可停止油浆循环。
.
4. 催化剂全部转入再生器后,调整主风量,保证再生器的
藏量与密度,便于卸出催化剂。
5. 外取热器催化剂通过外取热器底部部卸料线卸出;重油
再生斜管和轻燃油再生斜管催化剂通过滑阀前卸料线卸出。
6. 待两器系统催化剂卸净,启用V22105底部卸料线,卸出三旋内催化剂。
三、装盲板SB22201/22205,两器吹扫,停主风机。
1. 再生器催化剂卸净后,将主风切出再生器,全开反
应器顶、盲板SB22201/22205前、提升管底部放空,停所有进反应器的蒸汽,与分馏岗位配合装盲板SB22201/22205。
2. 盲板SB22201/22205装好后,反应器给汽提蒸汽及
预提升蒸汽,吹扫12小时后,停所有蒸汽。
3. 再生器引入主风进行吹扫,全开烟机旁路双动滑阀,由烟囱直接放空,当再生器出口降至200℃,联系机组停主
风机。
4. 主风机停运后,关闭反-再系统所有工艺用反吹、松动风(汽),并关闭非净化风进两器总阀。
5. 联系检修单位开人孔、降温。
四、余热锅炉系统停车步骤
1. 随着反应降量,取热量减少,应及时调整V22401给%以上。
50液面V22401水量,保证.
2. 随着烟气温度的降低,应逐步减少进B22401的烟气量,增加烟囱的烟气直接排放量。
3. 适当加大外取热器汽水分离器排水量。
4. 当外取热中部温度降至150℃,可停止V22401上水,关闭外取热水循环,当E22215A、B油浆温度低于250℃时,停止V22402上水,同时也可停止V22403、V22404上水。
5. V22401、22402、22403、22404蒸汽放空,缓慢降压。
6. 锅炉给水泵P22402AB继续向开工锅炉补水,维持停工各装置用汽。