MODEL 2061使用手册北京雪迪龙
Model 2460 快速入门指南说明书
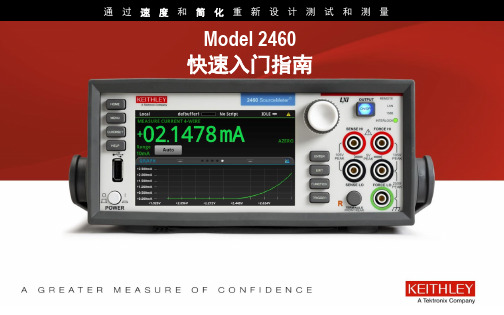
通过速度和简化重新设计测试和测量安全注意事项在使用本产品和任何相关仪器之前,请先阅读以下安全注意事项。
虽然一些仪器和附件通常在无害电压下使用,但是也可能出现对人体有害的情况。
本产品应由能辨别电击危险且熟悉避免潜在伤害的必要安全注意事项的合格人员使用。
使用此产品之前请仔细阅读并遵守所有的安装、操作和维护信息。
有关完整的产品规格,请参阅用户文档。
若以没有指定的方式使用产品,可能丧失产品保修所提供的保障。
产品的用户类型有:责任主体,是负责使用和维护机器,确保在设备规格和运行限制范围内使用设备,并确保操作人员经过充分培训的个人或小组。
操作人员,是负责使用产品特定功能的人员。
他们必须接受过电气安全流程和正确操作仪器方面的培训。
应当采取保护措施,防止他们遭到电击和触碰到危险的带电电路。
维护人员,负责产品日常维护以保持仪器运转正常,例如,设置线路电压或更换耗材。
用户文档中描述了维护步骤。
这些步骤都清楚描述了操作人员是否能够执行它们。
如果不能,那么只能由服务人员来执行这些操作。
服务人员,接受过培训,可操作带电电路,执行安全安装并修理产品。
只有受过正确训练的服务人员才能执行安装和服务流程。
美国吉时利仪器(Keithley Instruments) 公司的产品专门设计用于测量、控制和数据输入/输出连接等电气信号,而且不能直接连接到电网电压或具有瞬时高电压的电压源上。
Measurement Category II(引自IEC 60664 标准)连接要求针对本地交流电网连接经常发生的高瞬时电压采取保护措施。
某些吉时利测量仪器可以连接到电网上。
这些仪器将会标记为Category II 或更高级别。
除非在仪器规格、操作手册和仪器标签中明示允许,否则不要将任何仪器连接到电网上。
存在电击危险时,一定要小心谨慎。
电缆连接器插头或测试装置上可能存在致命电压。
美国国家标准学会(ANSI) 规定,超过30 V RMS、42.4V峰值或60 V DC 的电压水平存在电击的危险。
Bell 206L 型号 Snow Deflector 修改手册说明书

TECHNICAL BULLETIN 206L-23-25813 June 2023MODEL AFFECTED: 206L-1, 206L-3, and 206L-4SUBJECT: SNOW DEFLECTOR, MODIFICATION OF HELICOPTERS AFFECTED: Serial numbers 45154 through 45790, 51001through 51612 and 52001 through 52453 that havebeen modified by TB 206L-18-255.[Serial number 52454 and subsequent will have theintent of this bulletin accomplished prior to delivery.] COMPLIANCE: At customer’s option.DESCRIPTION:This bulletin provides instructions to modify the snow deflector assemblies 206-064-226-001/-002 in order to fit on helicopters modified by TB 206L-18-255. Applicability of this bulletin to any spare part shall be determined prior to its installation on an affected helicopter.APPROVAL:The engineering design aspects of this bulletin are Transport Canada Civil Aviation (TCCA) approved.CONTACT INFO:For any questions regarding this bulletin, please contact:Bell Product Support Engineering - Light HelicoptersTel:1-450-437-2862/1-800-363-8023/*****************************based on hands-on time and may vary with personnel and facilities available. WARRANTY: There is no warranty credit applicable for parts or labor associated with this bulletin. MATERIAL: Required Material: The following material is required for the accomplishment of this bulletin and may be obtained through your Bell Supply Center. Part Number Nomenclature Qty (Note) 407-704-034-109 Kit-mod 206 snow deflector 1 (1) Consisting of: 206-064-226-119 Chafing strip 1 206-064-226-121 Chafing strip 1 206-064-226-123 Chafing strip 1 206-064-226-125 110-076-1-07-0 Chafing strip Rubber extrusion 1 2Consumable Material: The following material is required to accomplish this bulletin, but may not require ordering, depending on the operator’s consumable material stock levels. This material may be obtained through your Bell Supply Center. Part Number Nomenclature Qty (Note) Reference * 407-704-034-119 Kit-consumable Consisting of: 1(1) 2000-09182-01 Adhesive 50 grams C-317 (299-947-100,Ty II, CL2) 2000-06022-00Adhesive, paste (299-947-107, Ty 1, CL1) 1 Pint C-324 2010-00216-00 Fairing compound 13.5 OZ C-323 (299-947-072, TYI) 2000-06013-01 Silicone adhesive 1 OZ C-300 (299-947-152, Ty I, CL1) 2620-06050-00Glass cloth (AMS-C-9084, CL2, TYIIIA) 12”X12” C-404 2620-06280-00 Glass cloth 12”X12” C-560 (AMS-C-9084, CL2, TYIII) 2000-11948-00 Adhesive 50 grams (2) C-363 (299-947-100,Ty II,CL 3)1. If required, order this kit to complete the 407-704-034-109 snow deflectormodification. Available on special order only.2. Not included in 407-704-034-119 kit. To be ordered separately.SPECIAL TOOLS:None required.WEIGHT AND BALANCE:Not affected.ELECTRICAL LOAD DATA:Not affected.REFERENCES:BHT-206L-SERIES-IPB, Illustrated Parts BreakdownBHT-206L1-MM, Maintenance ManualBHT-206L3-MM, Maintenance ManualBHT-206L4-MM, Maintenance ManualBHT-ALL-SRM, Structural Repair manualPUBLICATIONS AFFECTED:None affected.ACCOMPLISHMENT INSTRUCTIONS:1. Prepare the helicopter for maintenance.2. Remove and discard the existing edging (11, Figure 1, Detail E) and the existingchaffing strips (View B, 2 through 5) from the snow deflectors (1, View A).3. Remove paint and primer from the rework area (View B and Section C-C).4. Position the snow deflector (1) on a helicopter equipped with a 407-064-004 inletcowling. Install the four bolts on the forward edge and the two bolts on the bottom edge (View A).5. Using a fine tipped non-corrosive ink marker or equivalent, draw line L1 (View B)matching the contour of the 407-064-004 inlet cowling on the protruding edge of the snow deflector (1).6. Remove the snow deflector (1) from the helicopter.7. Draw line L2 (view B) at 3.0 inches (76 mm) from the line L1. Line L2 must be parallel to line L1.8. Draw two more lines (L3 and L4) in 0.50 inch (13 mm) increments from line L2. Both lines must be parallel to line L2.Repair doublers shall be dimensioned as indicated in steps 8 through 10.9. Repair doubler P1 (C-404) is to be dimensioned to fit between the edge of part and line L2.10. Repair doubler P2 (C-404) is to be dimensioned to fit between the edge of part and line L3.11. Repair doubler P3 (C-560) is to be dimensioned to fit between the edge of part and line L4.12. Perform lay up as follows:Ply orientation is optional.a. Prepare surfaces for bonding (BHT-ALL-SRM, Chapter 4, Paragraph 4-2-9).b. Wet plies using adhesive (C-363).c. Lay repair doublers on part as marked previously (Figure 1, View B and Section C-C).d. Remove excess adhesive squeeze-out.e. Allow to cure at room temperature for 24 hours applying a pressure of 0.5 to 1.0 PSI to repair area. For the alternate high temperature cure, refer to the Table 4-12 (BHT-ALL-SRM, Chapter 4).f. Inspect for voids and unbonded area(s). Voids shall not exceed 10 % of the total bonded area. No one void shall exceed 0.025 sq. inches (1.61cm²) in area.g. As required, fill and fair with fairing compound (C-323) and sand to contour. -NOTE- -NOTE-13. Position the snow deflector (1, Figure 1) on a helicopter equipped with a 407-064-004 inlet cowling. Install the four bolts on the forward edge and the two bolts on the bottom edge (View A).14. Mark and open three 0.233 to 0.239 inch (5.92 to 6.07 mm) diameter holes throughtop flange of the snow deflector (1). Hole positions should be located from the 407-064-004 inlet cowling (Note 3, View B)15. Install three bolts on the top flange of the snow deflector (1) (View A).16. Using a fine tipped non-corrosive ink marker or equivalent, draw a line matching thecontour of the 407-064-004 inlet cowling on the protruding edge of the snow deflector(1) (Note 2, View B).17. Remove the snow deflector (1).18. Trim the protruding edge of the snow deflector (1) as marked at step 16.19. Refinish as required.20. Install the four new chafing strips (6 through 9, View B) using adhesive (C-300).21. Install the two rubber extrusions (10, Detail E) using adhesive (C-324).22. Re-identify the L/H snow deflector with P/N 206-064-226-101FM and the R/H snowdeflector with P/N 206-064-226-103FM.23. Make an entry in the helicopter logbook and historical service records indicatingcompliance with this Technical Bulletin.Figure 1 – Snow Deflector (Sheet 1 of 3)Figure 1 – Snow Deflector (Sheet 2 of 3)Figure 1 – Snow Deflector (Sheet 3 of 3)。
Eaton Moeller Rapid Link速控器数据手册说明书
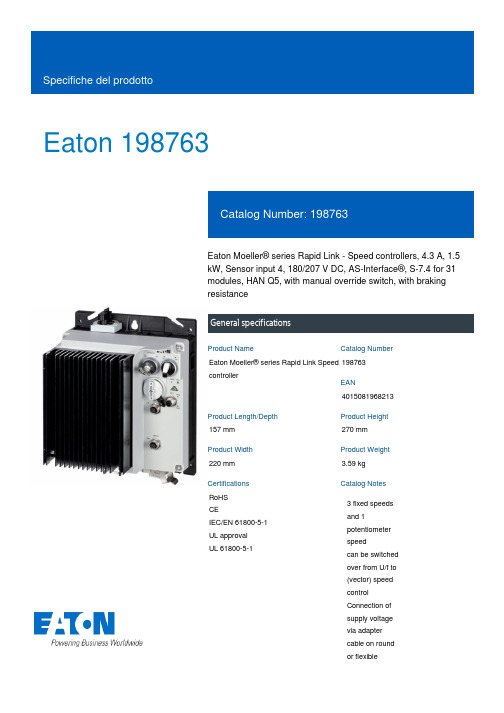
Eaton 198763Eaton Moeller® series Rapid Link - Speed controllers, 4.3 A, 1.5 kW, Sensor input 4, 180/207 V DC, AS-Interface®, S-7.4 for 31 modules, HAN Q5, with manual override switch, with braking resistanceGeneral specificationsEaton Moeller® series Rapid Link Speed controller1987634015081968213157 mm 270 mm 220 mm 3.59 kg RoHS CEIEC/EN 61800-5-1 UL approval UL 61800-5-1Product NameCatalog NumberEANProduct Length/Depth Product Height Product Width Product Weight Certifications Catalog Notes 3 fixed speeds and 1 potentiometer speedcan be switched over from U/f to (vector) speed control Connection of supply voltage via adapter cable on round or flexibleRASP5-4401A31-512R100S1Parameterization: FieldbusDiagnostics and reset on device and via AS-Interface Parameterization: drivesConnectParameterization: drivesConnect mobile (App) Parameterization: KeypadKey switch position OFF/RESETPTC thermistor monitoringKey switch position HANDBreaking resistanceIGBT inverterManual override switchTwo sensor inputs through M12 sockets (max. 150 mA) for quick stop and interlocked manual operationBraking resistanceThermo-click with safe isolationPC connectionSelector switch (Positions: REV - OFF - FWD)Internal DC linkKey switch position AUTOControl unit3 fixed speeds4-quadrant operation possibleBrake chopper with braking resistance for dynamic braking1 potentiometer speedFor actuation of motors with mechanical brake IP65NEMA 121st and 2nd environments (according to EN 61800-3)IIISpeed controllerASIAS-Interface profile cable: S-7.4 for 31 modulesC2, C3: depending on the motor cable length, the connected load, and ambient conditions. External radio interference suppression filters (optional) may be necessary.C1: for conducted emissions only2000 VCenter-point earthed star network (TN-S network)AC voltagePhase-earthed AC supply systems are not permitted.Vertical15 g, Mechanical, According to IEC/EN 60068-2-27, 11 ms, Half-sinusoidal shock 11 ms, 1000 shocks per shaftResistance: 6 Hz, Amplitude 0.15 mmResistance: According to IEC/EN 60068-2-6Resistance: 10 - 150 Hz, Oscillation frequencyResistance: 57 Hz, Amplitude transition frequency on accelerationModel CodeFeatures Fitted with:FunctionsDegree of protectionElectromagnetic compatibilityOvervoltage categoryProduct categoryProtocolRadio interference classRated impulse withstand voltage (Uimp)System configuration typeMounting positionShock resistanceVibrationbusbar junctionDiagnostics andreset on deviceand via AS-Interfaceintegrated PTCthermistormonitoring andThermoclick withsafe isolationoptional: 4sensor inputswith M12-Yadapter forswitchover tocreep speedoptional: Fasterstop if external24 V failsTwo sensorinputs throughM12 sockets(max. 150 mA)for quick stopand interlockedmanualoperationwith AUTO -OFF/RESET -HAND keyswitcheswith selectorswitch REV -OFF - FWDAbove 1000 m with 1 % performance reduction per 100 m Max. 2000 m-10 °C40 °C-40 °C70 °C< 95 %, no condensationIn accordance with IEC/EN 501780.4 - 4.3 A, motor, main circuit Adjustable, motor, main circuit< 10 ms, Off-delay< 10 ms, On-delay98 % (η)4.1 A3.5 mA120 %Maximum of one time every 60 seconds380 V480 V380 - 480 V (-10 %/+10 %, at 50/60 Hz)Synchronous reluctance motorsPM and LSPM motorsSensorless vector control (SLV)BLDC motorsU/f control0 Hz500 HzAt 40 °CFor 60 s every 600 s6.5 AAltitudeAmbient operating temperature - min Ambient operating temperature - max Ambient storage temperature - min Ambient storage temperature - max Climatic proofing Current limitationDelay timeEfficiencyInput current ILN at 150% overload Leakage current at ground IPE - max Mains current distortionMains switch-on frequencyMains voltage - minMains voltage - maxMains voltage toleranceOperating modeOutput frequency - minOutput frequency - maxOverload currentOverload current IL at 150% overload45 Hz66 Hz4.3 A at 150% overload (at an operating frequency of 8 kHz and an ambient air temperature of +40 °C)1.5 kW400 V AC, 3-phase480 V AC, 3-phase0.1 Hz (Frequency resolution, setpoint value)200 %, IH, max. starting current (High Overload), For 2 seconds every 20 seconds, Power section50/60 Hz8 kHz, 4 - 32 kHz adjustable, fPWM, Power section, Main circuitCenter-point earthed star network (TN-S network)AC voltagePhase-earthed AC supply systems are not permitted.2 HP≤ 0.6 A (max. 6 A for 120 ms), Actuator for external motor brakeAdjustable to 100 % (I/Ie), DC - Main circuit≤ 30 % (I/Ie)280/207 V DC -15 % / +10 %, Actuator for external motor brake765 VDC10 kAType 1 coordination via the power bus' feeder unit, Main circuit180/207 V DC (external brake 50/60 Hz)24 V DC (-15 %/+20 %, external via AS-Interface® plug)AS-InterfacePlug type: HAN Q5Max. total power consumption from AS-Interface® power supply C2 ≤ 5 m, maximum motor cable length C1 ≤ 1 m, maximum motor cable length C3 ≤ 25 m, maximum motor cable lengthRated frequency - minRated frequency - maxRated operational current (Ie)Rated operational power at 380/400 V, 50 Hz, 3-phase Rated operational voltageResolutionStarting current - maxSupply frequencySwitching frequencySystem configuration type Assigned motor power at 460/480 V, 60 Hz, 3-phase Braking currentBraking torqueBraking voltageSwitch-on threshold for the braking transistorRated conditional short-circuit current (Iq)Short-circuit protection (external output circuits) Rated control voltage (Uc)Communication interfaceConnectionInterfacesCable lengthunit (30 V): 190 mASpecification: S-7.4 (AS-Interface®)Number of slave addresses: 31 (AS-Interface®)Meets the product standard's requirements.Meets the product standard's requirements.Meets the product standard's requirements.Meets the product standard's requirements.Meets the product standard's requirements.Does not apply, since the entire switchgear needs to be evaluated.Does not apply, since the entire switchgear needs to be evaluated.Meets the product standard's requirements.Does not apply, since the entire switchgear needs to be evaluated.Meets the product standard's requirements.Does not apply, since the entire switchgear needs to be evaluated.Does not apply, since the entire switchgear needs to be evaluated.Is the panel builder's responsibility.Is the panel builder's responsibility.Is the panel builder's responsibility.Is the panel builder's responsibility.10.2.2 Corrosion resistance10.2.3.1 Verification of thermal stability of enclosures 10.2.3.2 Verification of resistance of insulating materials to normal heat10.2.3.3 Resist. of insul. mat. to abnormal heat/fire by internal elect. effects10.2.4 Resistance to ultra-violet (UV) radiation 10.2.5 Lifting10.2.6 Mechanical impact10.2.7 Inscriptions10.3 Degree of protection of assemblies10.4 Clearances and creepage distances 10.5 Protection against electric shock10.6 Incorporation of switching devices and components 10.7 Internal electrical circuits and connections 10.8 Connections for external conductors 10.9.2 Power-frequency electric strength 10.9.3 Impulse withstand voltageIs the panel builder's responsibility.The panel builder is responsible for the temperature rise calculation. Eaton will provide heat dissipation data for the devices.Is the panel builder's responsibility. The specifications for the switchgear must be observed.Is the panel builder's responsibility. The specifications for the switchgear must be observed.The device meets the requirements, provided the information in the instruction leaflet (IL) is observed.Rapid Link 5 - brochureDA-SW-USB Driver PC Cable DX-CBL-PC-1M5DA-SW-USB Driver DX-COM-STICK3-KITDA-SW-drivesConnect - installation helpDA-SW-Driver DX-CBL-PC-3M0DA-SW-drivesConnect - InstallationshilfeDA-SW-drivesConnectMaterial handling applications - airports, warehouses and intra-logisticseaton-bus-adapter-rapidlink-speed-controller-dimensions-003.eps eaton-bus-adapter-rapidlink-speed-controller-dimensions-004.eps eaton-bus-adapter-rapidlink-speed-controller-dimensions-002.eps eaton-bus-adapter-rapidlink-speed-controller-dimensions-005.epsETN.RASP5-4401A31-512R100S1.edzIL034085ZUramo5_v20.dwgrasp5_v20.stpConfiguration to Rockwell PLC for Rapid LinkGeneration change from RA-SP to RASP 4.0Generation Change RA-SP to RASP5Generation Change RASP4 to RASP5Generation change from RA-MO to RAMO 4.0Generation change RAMO4 to RAMO5DA-DC-00004508.pdfDA-DC-00003964.pdfDA-DC-00004514.pdfDA-DC-00004184.pdf10.9.4 Testing of enclosures made of insulating material10.10 Temperature rise10.11 Short-circuit rating10.12 Electromagnetic compatibility 10.13 Mechanical function BrochureDisegnieCAD modelIstruzioni di installazione mCAD modelNote per l'applicazione Report di certificazioneEaton Corporation plc Eaton House30 Pembroke Road Dublin 4, Ireland © 2023 Eaton. Tutti i diritti riservati. Eaton is a registered trademark.All other trademarks areproperty of their respectiveowners./socialmedia。
Model 3196 i-FRAME泵安装、运行与维护手册说明书
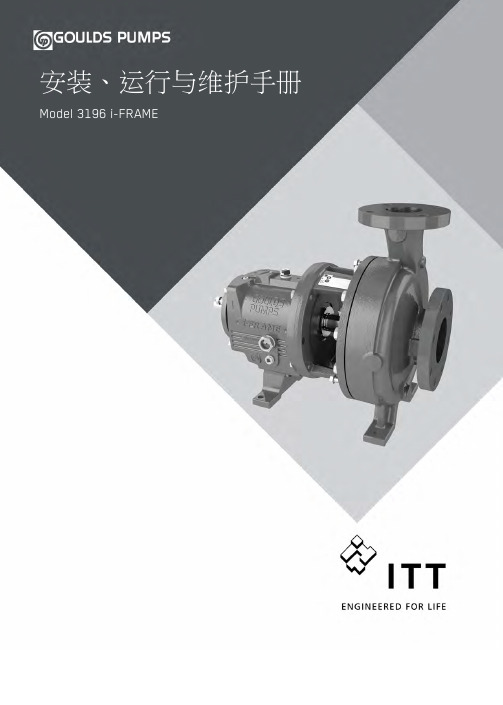
目录
目录
介绍与安装 .......................................................................................................................... 4 前言 ................................................................................................................................... 4 安全 ................................................................................................................................... 4 安全术语与标志 .............................................................................................................. 5 环境安全 ......................................................................................................................... 5 用户安全 ......................................................................................................................... 6 防爆认证产品 .................................................................................................................. 7 产品认证标准 .................................................................................................................... 8 产品保修 ........................................................................................................................... 8
攀登车 Cannondale 2019 车辆指南补充说明书

2019READ THIS SUPPLEMENT AND YOURCANNONDALE BICYCLE OWNER’S MANUAL. Both contain important safety information. Keep both for future reference.Trigger/JekyllOwner’s Manual SupplementSafety MessagesIn this supplement, particularly important information is presented in the following ways:The following symbols are used in this manual:1134942 Rev 1.EnglishCONTENTSSafety Information ............................2-6Technical Information ......................7-19Replacement Parts ........................28-29Tightening Torques ............................30Maintenance .......................................31Notes .. (32)Cannondale SupplementsThis manual is a “supplement” to your Cannondale Bicycle Owner’s Manual. This supplement provides additional and important model specific safety, maintenance, and technical information. It may be one of several important manuals/supplements for your bike; obtain and read all of them.Please contact your AuthorizedCannondale Dealer immediately if you need a manual or supplement, or have a question about your bike. You may also contact us using the appropriate country/region/location information. You can download Adobe Acrobat PDF versions of any manual/supplement from our website:Contacting CannondaleCannondale USACycling Sports Group, Inc. 1 Cannondale Way, Wilton CT, 06897, USA 1-800-726-BIKE (2453)Cycling Sports Group Europe B.V Mail: Postbus 5100 Visits: Hanzepoort 277575 DB, Oldenzaal, NetherlandsYour Cannondale DealerTo make sure your bike is serviced and maintained correctly, and that you protect applicable warranties, please coordinate all service and maintenance through your Authorized CannondaleDealer.2134942 Rev 1.Trigger / Jekyll - Owners Manual SupplementSAFETY INFORMATIONImportant CompositesMessageInspection & Crash Damage Of CarbonFrames/Forks3134942 Rev 1.EnglishIntended UseThe intended use of all models is ASTM CONDITION 4,All-Mountain.Servicing4134942 Rev 1.Trigger / Jekyll - Owners Manual SupplementMaximum Fork LengthMaximum Fork Length is an important frame safety testing specification for front suspension mountain bikes. You must observe the measurement when installing headset parts, headset adapters, installing and adjusting a fork, and selectingreplacement forks.To Center Of The Fork AxleEnglish Tire Size x Maximum Width134942 Rev 1.56134942 Rev 1.Trigger / Jekyll - Owners Manual SupplementMinimum Seat PostInsertRear ShocksEnglish TECHNICAL INFORMATION Specifications - Trigger 27.5134942 Rev 1.7Trigger / Jekyll - Owners Manual Supplement Specifications - Jekyll 27.5134942 Rev 1.8Specifications - Jekyll 29Geometry - TriggerDimensions = centimeterA Seat Tube Length 40.043.046.052.0B Top Tube Horizontal 57.660.262.765.5C Top Tube Actual ----D Head Tube Angle 66°***E Seat Tube Angle Effective 74.5°***F Standover 75.076.076.579.5G Head Tube Length 9.711.012.213.5H Wheelbase 113.6116.4119.0122.0I Front Center 71.674.477.180.0J Chain Stay Length 42.0***K Bottom Bracket Drop 1.2***L Bottom Bracket Height 34.5***M Fork Rake 4.4***N Trail 10.1***O Stack 57.658.859.961.0PReach41.643.946.148.6All Specifications subject to change without notice.* - Indicates same.Geometry - JekyllDimensions = centimeterJekyll 29 Jekyll 27.5A Seat Tube Length 40.043.046.052.0B Top Tube Horizontal 58.661.163.666.458.460.963.466.2C Top Tube Actual 56.858.961.364.153.756.258.762.1D Head Tube Angle 65°65°65°65°65°***E Seat Tube Angle Effective 75°75°75°75°75.0°***F Standover 76.076.677.678.87575.876.777.5G Head Tube Length 10.211.512.714.010.211.512.714H Wheelbase 117.9120.7123.4126.4116118.7121.4124.4I Front Center 73.876.579.282.37476.779.482.4J Chain Stay Length 44.2***42***K Bottom Bracket Drop 1.6 1.6 1.6 1.60.8***L Bottom Bracket Height 36.036.036.036.034.9***M Fork Rake 4.2*** 4.4***N Trail 13.0***11.4***O Stack 59.861.062.163.359.260.461.562.6PReach41.944.046.248.742.544.746.949.4All Specifications subject to change without notice.* - Indicates same.Chainstay Left (outer)Chainstay Right (outer)WELDProtector 1Protector 2align with edgeinsert tab into boltInside (wheel side)Inside Rightwider endtowarddropoutwider endwider endtowardbottom bracket Center on tubeDowntubeSeatstay6 NmLoctite 242 (blue)DropoutKey Information:A special service tool KP169/ contains parts necessary to service the assembly. The parts of this tool are shown shaded above.When connecting the seat stays to the dropouts, always insert the small end of pivot spacers into the dropout bearings . The flat side of the spacers should face out, as shown.When tightening the axles, insert the 5 mm hex key completely into the axle to prevent damage when turning the bolt. Always tighten with a torque wrench to the specified torque.MaintenanceThe condition of the bearings, pivot axles, and spacers should be inspected periodically. These are normal wear parts so plan to have them renewed as they wear-out.Inspection frequency should bebased upon how and where you ride. Evidence of damage would be excessive play, visible wear, or perhaps corrosion of bearings.If you find any damage to the parts, discontinue riding until all the parts (bearings, pivot axles, spacers) can be renewed. This will help prevent damage elsewhere.See the kits list in the back of this supplement for renewal kits.The Ai rear hub is offset 3 mm to the drive side. This both aligns the cassette with the Ai frame’s 55mm chainline, and aligns the rim/tire with frame’s centerline for correct tire clearance.Ai wheels have equal spoke angles and tension on both sides (non-dished wheel) which improves wheel stiffness, strength.• The 3mm offset is for 148 X 12mm spacing only!•Other Ai equipped bike with 142mm or135mm rear spacing use a 6mm offset. Asymmetric Integration - Ai Rear Wheel- 3 mm OffsetLockRBe sure to support the bike or swingarm to prevent personal injury or bike damage when removing/disconnecting linkages of an axle.To remove the LockR from the frame:1. Loosen the screw 4-6 turns using a T25 Torx key.2. Tap head of screw with a rubber mallet to un-seat the wedge bolt located on the opposite side..3. Remove the screw and wedge bolt from the still installed axle.4. If it did not come out with the screw, insert a 5 mm hex key and turn to free and remove it. If wedge still sticks insert a wooden or plastic dowel into the drive side and drive it out.5. To remove the axle itself, on non-drive side, insert a 6 mm hex key into the axle on the non-drive side and and turn counter-clockwise until it can be removed.To install the LockR from the frame:1. Disassemble and clean all parts of the LockR axle. Do not install it assembled. Inspect the parts for damage (burrs, scratches, deformity, wear). Replace the entire LockR assembly if any damage is found.2. Apply a light coating of a high-quality bicycle bearing grease to all parts.3. Align the linkage and bearing and insert the threaded end of the pivot axle (1) into the non-drive side.4. Tighten the inserted pivot axle to 1 Nm using a 6 mm hex key fitted torque wrench from the non-drive side.5. Insert the wedge bolt (2) into the drive side of the axle and insert the small end of the wedge (3) into the non-drive side axle head.6. Thread the screw (4) into wedge bolt with a wrench and tighten to 5.0 Nm.1 N-m5 N-mUnthread &tap mallet 4T25Correct tightening torque for the fasteners (bolts, screws, nuts) on your bicycle is very important to your safety, durability, and performance of your bicycle.We urge you to have your dealer correctly torque all fasteners using a torque wrench. If you decide to tighten fasteners yourself always use a calibrated torque wrench!Tightening TorquesHanger ReplacementHanger replacement kit is available as Cannondale kit - CK3257U00OS.The kit includes the hanger (1) and a new pivot bolt (3). Before installing a new hanger, be sure to clean any dirt or debris on the dropout with a nylon brush (old toothbrush). Inspect the area for any damage. Lightly grease the dropout surface. Apply Loctite 242 (blue) to the pivot bolt (4). Align the hanger on the opposite side of the dropout and tighten the bolt to the specified torque.2 N-mM5x25 5.The rubber grommets are pressed into the frame holes when no battery is installed.Battery InstallationFor Di2, use the seat post type battery(Shimano SM-BTR2)1. Remove fork and headset from the frame.2. Attach mounting plate (1) included in Cannondalekit K32027/ to the battery (2) using two 3mm nylon ties (3). Make sure the plate lip (a) is aligned withthe case groove on the battery nearer the cableconnection (b). See inset A.3. Tie a thin dental string (5) to the battery plate4. Plug in Di2 wire (to junction B) into the battery5. Use a shift cable inserted into the top tube holeand out the lower head tube to guide.6. Attached the end of the dental thread to the shiftcable and draw the dental thread through and outthe top tube hole.7. Insert the battery and plate in the bottom of thehead tube and use the dental thread to guide thebattery and plate into position. 5. With the batteryin position as shown, holding the string (5) taught,apply grease to the screw (6) and tighten to 2 Nm.The screw threads should cut the string so it can beremoved.Apply lightgrease to4mm 5 mm x 25 mm4mm5 4mm5 mm 4mm1 Nm1 Nm1 NmInternal Guides - KP436/Internal Frame Guides:Install plastic spiral wire wrap (5) over Di2 wires (6) passing through internal guide (7).Use the 4mm guide opening for Di2 wire.Use the guide inserts in open locations.Gemini Rear ShockTo set air pressure:1. Set handlebar remote to Flow mode: press the black handlebar remote button (a) so that the remote handlebar control is in the position shown below.(a)(b)2. Remove the Schrader valve cap (1) and pressurize the shock with a shock pump.3. Remove the shock pump.4. Cycle the shock 10 times to allow the positive and negative air pressures to equalize.NOTE: Air pressure measured at the pump will decrease after air has transferred from positive to negative chambers.5. Check sag to confirm your shock setup. Recommended seated sag with full riding gear is 30%6. If there is too much sag, add air pressure in 10 psi increments until correct sag is achieved. If there is too little sag, reduce air pressure in 10 psi increments until correct sag is achieved.7. Install the Schrader valve cap onto the air valve.8. Turn the red rebound adjuster clock-wise towards “slow” until it stops.a. Float X - Insert a 2mm hex wrench into a cutout in the red rebound knob located near the eyelet on the frame side of the shock. Use the wrench to turn the knob towards “slow” until it stops.b. Float DPS - Turn the red rebound knob located under the blue com-pression adjustment lever on the frame side of the shock clockwise towards “slow” until it stops.9. Turn the red rebound knob counter-clockwise towards “fast”, counting each detent click until you reach the recommended number of clicks based on the table below.Remote Cable Installation1. Cut a piece of derailleur housing that fits from Gemini’s housing stop to the Gemini remote without interfering with the rotation of the handle bars. Install a ferrule on one end of the housing.2. Place the Gemini remote in Flow mode by pressing the black button on the Gemini remote while placing upward pressure on the silver button.3. Insert a derailleur cable into the round hole below the silver button on the Gemini remote. Feed the cable through the remote until the cable head is fully seated.4. Insert the cable into the cable noodle end opposite the barrel adjuster. Slide the cable noodle along the cable until it is fully inserted into the remote.5. Insert the derailleur cable into the Gemini cable housing end with the ferrule and push it through until the housing is fully seated in the barrel adjuster on the cable noodle.6. Insert the derailleur cable through the housing stop on the Gemini shock, then pull the cable until the housing is fully seated in the housing stop. There should not be a housing ferrule on this side of the Gemini housing.7. Use a 2 mm hex wrench to loosen the set screw located on the rear of the Gemini shock cam until there are only 2 threads engaged.8. Insert the cable between the set screw and Gemini cam. Pull the cable so the cable and housing are fully seated and tight.9. Tighten the set screw to 1.2 Nm witha 2mm hex wrench to secure the cable.10. Function Test: Push on the remote’s silver Hustle mode button, then press the black Flow mode button.a. Cable is too tight: the remote cannot stay in Hustle mode. Reduce cable tension by turning barrel adjuster clockwise. If problem persists, reduce cable tension by loosening the set screw and resetting cable tension as described in steps 7-9.b. Cable is too loose: the cam will not turn as soon as you engage the lever. Increase cable tension by turning the barrel adjuster counter-clockwise. If problem persists increase cable ten-sion by loosening the set screw and resetting cable tension as described in steps 7-9.MAINTENANCEThe following table lists only supplemental maintenance items. Please consult yourfor more information on basic bike maintenance.Cannondale Bicycle Owner’s ManualREPLACEMENT PARTS29134942 Rev 1.30134942 Rev 1.Jekyll 27.5Trigger / Jekyll - Owners Manual Supplement31134942 Rev 1.EnglishTrigger / Jekyll - Owners Manual SupplementNOTESUse this page to write /record important information about your bike : (e.g. maintenance history,dealer contact information, settings, etc.)134942 Rev 1.32© 2019 Cycling Sports GroupTrigger/Jekyll Owner’s Manual Supplement 134942 Rev. 1CANNONDALE USA Cycling Sports Group, Inc.1 Cannondale Way, Wilton CT, 06897, USA1-800-726-BIKE (2453) CANNONDALE EUROPECycling Sports Group Europe, B.V.Hanzepoort 27, 7575 DB, Oldenzaal******************************CANNONDALE UKCycling Sports GroupVantage Way, The Fulcrum,Poole, Dorset, BH12 4NU+44 (0)1202732288***************************.uk。
Carlin Combustion Technology 模型60200FR 油燃器操作指南说明书
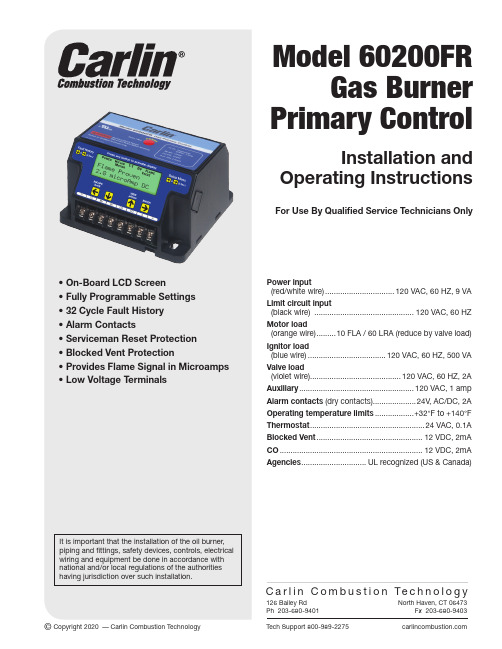
Model 60200FRGas Burner Primary ControlInstallation andOperating InstructionsFor Use By Qualified Service Technicians Only126 Bailey Rd North Haven, CT 06473Ph 203-680-9401Fx 203-680-9403Tech Support 800-989-2275© Copyright 2020 — Carlin Combustion TechnologyC a r l i n C o m b u s t i o n Te c h n o l o g yPower input(red/white wire) ................................120 VAC, 60 HZ, 9 VA Limit circuit input(black wire) ..............................................120 VAC, 60 HZ Motor load(orange wire) .........10 FLA / 60 LRA (reduce by valve load)Ignitor load(blue wire) ....................................120 VAC, 60 HZ, 500 VA Valve load(violet wire) ..........................................120 VAC, 60 HZ, 2A Auxiliary .....................................................120 VAC, 1 amp Alarm contacts (dry contacts)....................24V , AC/DC, 2A Operating temperature limits ..................+32°F to +140°F Thermostat .....................................................24 VAC, 0.1A Blocked Vent .................................................12 VDC, 2mA CO ..................................................................12 VDC, 2mA Agencies ..............................UL recognized (US & Canada)2Carlin Combustion TechnologyW A R N I N G S1. W arning – Do not attempt to confirm combustion simply by inspecting the flame visually. Y ou must use combustion test instru-ments. Failure to properly verify/adjust combustion could allow unsafe operation of the burner, resulting in severe personal injury,death or substantial property damage. Refer to the burner manual for proper setup instructions. 2. W arning – Never test an ignitor by placing a screwdriver (or other metallic object) across the high voltage clips. Check ignitors onlyby observing spark at appliance ignition electrodes, with fuel supply OFF . Using any other method could cause ignitor damage and severe personal injury. 3. D anger – Fire, explosion, or carbon monoxide hazard. Water damage can lead to unreliable operation or cause the control tomalfunction which could lead to severe personal injury or death. Do not install the control module where it can get wet. Always replace the control if it gets wet or if it has any signs of water residue. 4. W arning – Electrical shock hazard. T o prevent electrical shock, death, or equipment damage, disconnect power supply beforeinstalling or servicing control. Only qualified personnel may install or service this control in accordance with local codes and ordi-nances. Read instructions completely before proceeding. 5. W arning – Electrical shock hazard. The ignition circuit of the control can produce over 10,000 volts which can cause severe injuryor death. 6. W arning – Frozen pipes/water damage. This is not a freeze protection device. Central heating systems are prone to shut down asa result of power or fuel outages, safety related fault conditions or equipment failure. Installation of freeze protection monitoring or other precautions are recommended for unattended dwellings in climates subject to sustain below-freezing temperatures. 7. W arning – All work must be performed by a qualified and licensed professional in accordance with all applicable codes and ordi-nances. 8. Notice – Read these instructions completely before proceeding with the installation. 9. Notice – Retain these instructions for future reference.10. Notice – All wiring must comply with the National Electric Code or any other state or local codes or regulations.11. D anger – Carbon Monoxide Hazard. Improper application or use can result in dangerous flue products, such as carbon monox-ide, which can escape into the living space causing severe injury or death. All venting must be checked for proper operation beforeallowing the burner to run.InstallingThe 60200FR control must be installed and serviced only by a qualified service technician.Always disconnect power source before wiring to avoid electrical shock or damage to the control. All wiring mustcomply with applicable codes and ordinances.MountingThe control may be mounted on a 4" x 4" junction box in any convenient location on the burner, furnace or wall. The location must not exceed the ambient temperature limit, 140°F .3Carlin Combustion TechnologyField WiringWiring must comply with local and national electrical codes, and with the wiring diagram.The burner (motor, valve, ignitor, etc.) is prewired at the fac-tory. The following steps are for field wiring.Step 1 Remove the 60200FR control from the electrical junc-tion box to access the terminal strip located on the bottom of the control.Step 2 Connect incoming, 120 VAC Hot from the boiler/fur-nace service switch to the red wire with white stripe attached to (L1 IN). This will supply constant power to the control for post purge (motor delay off) operation and display functional-ity when in standby mode. Note: If a constant 120 VAC power source from the service switch is not available, connect the red/white wire attached to (L1 IN) to the black wire attached to (LIMIT IN).NOTE: Check polarity carefully. If hot and neutral wires are reversed at appliance power source, the control will lockout on flame failure.Step 3 Connect 120 VAC Neutral to the white wire attached to (L2).Step 4 Connect the ground wire to the green ground screw inside the junction box. Connect the “FR Ground Terminal” to the green ground screw inside the junction box. Confirm that the junction box is connected to earth ground.Important: If the ground wire is not secured, the control will not sense flame properly resulting in nuisance lockouts.Step 5 Connect the boiler/furnace limit output to the blackwire connected to (LIMIT IN).1. Remove old control from J-Box2. Remove Rajah connector from flame rod wire3. W ire nut the existing wires to the spade provided wires and connect to controlReplacing the old 60200FR control4Carlin Combustion TechnologyWiringCommercial Gas Train 120VFACTORY WIRING EZGas Pro 24VFACTORY WIRING EZGas 120VFACTORYWIRINGW iring must comply with local and national electrical codes, and with the wiring diagram.5Carlin Combustion TechnologyView or Change Control SettingsNOTE: The settings mode cannot be accessed during a run cycle, the burner must be in standby mode (or lockout) to enter setup.To enter the Settings Mode :Press the G and E buttons simultaneously for 2 seconds. The display will show –To View Current Settings:Press the E button to scroll through all Setting Modes (see table at the top of page 5 for Setting Mode options). The second line of the screen willdisplay the current setting for each Setting Mode –Pressing the E button again will leave the setting as is andmove to the next option –Spill Switch*ThermostatContactsTo Change a Setting: Scroll to the desired Setting Mode option using the E button (as described in table on page 5), then press the or H button to scroll through the avail-able Settings. When the desired setting is displayed on the screen press the E / ENTER button. The display will briefly indicate that the new setting has been “Entered” and the new setting will replace the previous setting on the second line of the screen. Continue pressing the E button to view the cur-rent setting for all options or H button to make any desired changes.To Exit the Setup Menu: Press the F / ESCAPE button for 3 seconds. NOTE: The control will automatically exit the Setup menu after 30 seconds of inactivity or by a call for heat.* B locked Vent/Spill Switch Operation: During each run cycle, the BV contacts will be checked beginning 30 seconds after ignition. If the BV contacts open (indicating the spill switch has detected a blocked vent), the control will shut down the burner. The control will either recycle the burner or will go immediately into Lockout dependent on the Allowed Recycle setting. The spill switch must be closed within 2 seconds on a call for heat. If not, it will retry 2 times before control goes into lockout.N OTE: If using a manual reset blocked vent spill switch, the control will lock out with the display reading BV Switch Open.Shaded box = default setting.* M A Code (“N” models) are non-recycling and will lock out on flame failure.**Changing this setting to ‘Yes’, with limits powered will exit Settings mode and result in immediate ‘Call For Heat’. †If flame is sensed during Pre-Purge, control will lockout immediately (except when Pre-Purge is set to 0 seconds).A V A I L AB L E S E T T I N G SSetup Menu Definitions•P re-Purge: Time period motor and ignitor are on prior to Trial for Ignition. Note: If flame is sensed during Pre-Purge, control will lockout immediately (except when Pre-Purge is set to 0 or 3 seconds).• Trial for Ignition: Flame-establishing period during ignition.•P ost-Purge: Time period the motor is on after the Call for Heat is satisfied to allow for evacuation of combustion gases. A call for heat during Post-Purge will result in a recycle.• A llowed Recycles: Number of Recycles allowed during a single Call for Heat prior to lockout.• T T Jumpered Internal: Allows TT to be “jumpered” by software program.• C lear Fault History: Allows all prior burner fault conditions stored in control to be cleared.• R estore Factory Defaults: Allows all factory defaults to be restored in control (refer to settings shaded in gray in the table above). Will reset and reboot control .6Carlin Combustion TechnologyStatus IconsStatus Icons will appear at the top of the 60200FR display to indicate the control’s current operating condition.POWER Indicates that the control is powered (flashes if voltage is too low or too high)HV LIM Indicates that the burner limit circuit is powered.TT D isplayed when the TT terminals are physically jumpered, jumpered in the set-up menu, or when thermostat is calling for heat.BV M onitors the BV contacts where a Blocked Vent Switch (Spill Switch) is connected. (Flashes if the Spill Switch contacts are open – indicating that the vent is blocked). See Blocked Vent Operation below for more information.FLAME Indicates the control is sensing flameFAULT Flashes in unison with other status icons indicating a problem exists in that areaMOTOR Indicates that the motor is energized (flashes if motor not detected)IGNITOR Indicates that the ignitor is energized (flashes if ignitor not detected)VALVE Indicates that the gas valve is energized (on entry to pump prime will flash if not detected)Operating SequenceWith power to the control and the gas valve open, setthermostat (and limit) to call for heat. NOTE: The thermostatcircuit must be closed and power must be coming to blackwire from limit circuit.During Pre-Purge, the motor starts.Following Pre-Purge, the control advances to a3 second Pre-IgnitionDuring Pre-Ignition, the ignitor turns on and enters Trial forIgnition.During Trial for Ignition, the gas valve opens. When flame isdetected, the screen will briefly display “Flame Detected” andthen procedes to Burner RunningWhen the Call for Heat ends (or a limit control interrupts theburner circuit), the gas valve will turn off. The motor remainson for the Post-Purge period. When the Post-Purge timerexpires, the control returns to Standby mode awaiting thenext call for heat.7 Carlin Combustion Technology8Carlin Combustion TechnologyFault HistoryThe 60200FR stores information from the last 32 cycles inwhich a fault condition occurred. To Enter the Fault History , simultaneously press and hold the H and E buttons for 2 seconds. The display below will appear –Press the E button to scroll through the history of fault conditions. Fault 1 is the most recent cycle in which a fault occurred. To view faults experienced in earlier run cycles, continue to press the E button. The control will display Fault 2 followed by Fault 3, etc.To view the details of any fault (ex. Fault 1 in the screen above), press the H button to see the Fault Message.Press the H button again to determine how many cycles ago the fault occurred.Press the H button again to determine if the fault resulted in a lockout or a recycle.Press the H button again to examine the Microamps at thetime of the fault.Continue pressing the H button to examine the following information recorded during the fault cycle.• Line Voltage • Recycle (Yes or No)• Motor Amps (OK or Low) • Burn Time • Ignitor Amps (OK or Low) • Flame Delay • Valve Amps (OK or Low)On any fault detail screen listed above, the E button can be pressed to view the same data in the previous fault cycle. For example, if in Fault 1 (the most recent fault), the Ignitor Amps were low, by pressing the E button, the Ignitor Amps in Fault 2 (the previous fault cycle) will be displayed.To Exit Fault History: Press and hold the F / ESCAPE but-ton for 3 seconds at any time.Total/Run HistoryIn addition to the Fault History (left),the 60200FR also logs the total run history of the control. To enter this menu, simultane-ously press the E and F buttons for 3 seconds. The display below will appear.To Exit Total History: Press and hold the / ESCAPE but-ton for 3 seconds at any time.Press H button to scroll through the history which includes: • Total On Time • Max Line Volts • Total Burn Time • Min Line Volts • Total Burner Run Cycles • Total Recycles • Faults Cleared (cycles ago)F A UL T H I S T O R YNOTE: Fault information in chart is representation only.9Carlin Combustion TechnologyMN60200FR1 091619© Copyright 2020 — Carlin Combustion TechnologyT E C H S U P P O R T H O T L I N E 800-989-2275C a r l i n C o m b u s t i o n T e c h n o l o g y126 Bailey Road North Haven, CT 06473 Phone 203–680–9401 Fax 203–764–1714e-mail us at: *************************FROZEN PIPES/WATER DAMAGEThis is not a freeze protection device. Suitable freeze protection monitoring or other precautions are recommended to protect against ruptured pipes/water damage caused by fuel outage, safety related fault conditions or equipment failure.Service and TroubleshootingLast Fault Display: When the control is reset from a lockout condition, if the burner resumes normal operation, the screen will toggle the last fault and its cause for five days (longer du-ration if control is not wired for constant power). This feature is designed to allow the service technician to easily see what caused the condition in the event the homeowner reset the control prior to their arrival. The screen will alternate between displaying what the last fault was and displaying how to clear the message hold ESC for 3 seconds.Display Voltage and Current:Press + for 3 seconds todisplay real time voltage and current.Lockout: If lockout occurs, the screen turns on, the fault icon flashes and a fault message is displayed on the screen. To Reset Push in and hold the red Reset button for 1 second, then release. NOTE: Recycling power to the control will not reset it from it from a lockout condition.Two fault conditions result in an immediate lockout. These include; Flame detected during pre-purge and flame failure during Trial for Ignition. All other faults will result in a Recycle (unless the Allowed Recycles is set to ‘None’ in the Set-up Menu). A Recycle results in the burner shutting down for 60 seconds then resuming operation in Standby (if there is no Call for Heat) or initiating the Operating Sequence above (if there is a Call for Heat).Latch-up: If the control locks out 3 times during a single Call for Heat, Latch-Up will be displayed on screen.To Reset the control after latch-up, press and hold the red Reset button for 30 seconds. WARNING: Only a qualified service technician should attempt to reset the control after latch-up. The problem that caused the repeat lock-outs must be corrected before returning the burner to normal operation. NOTE: Recycling power to the control will not reset it from it from a latch-up condition. Burner will not fire• Check line voltage to the control (at least 102 vac).• Check all electrical connections.Other no start problems:• Valve lead voltage on too early. Correct bad connection.• M otor relay welded. If valve has no voltage, and line voltage is okay (102 - 132 VAC), the issue is a welded motor relay. Replace the control.• Motor current less than 0.2 Amps.Blocked vent – not recycling:• Recycle only works on non-manual reset vent switch Repeated flame failures Check for: • E xcessive airflow or draft causing flame to leave burner head- check for proper air band setting and draft.• E xcessive back pressure causing flame to be erratic – check appliance and flue for sooting/plugging.• “Flame rod shorted” message in lockout – defective flame rod assembly.Control locks out at end of TFI• No fuel to burner – check fuel supply lines.• S horted electrodes – inspect for cracked porcelain and replace as needed.• Airflow too high – check air band setting.• Ignitor module defective – replace if no spark.• Check wiring connections.• Flame rod shorted to ground or defective.Toggle。
智能特斯流G2.0和智能特斯流G1.6T-GDi引擎系列用户手册说明书
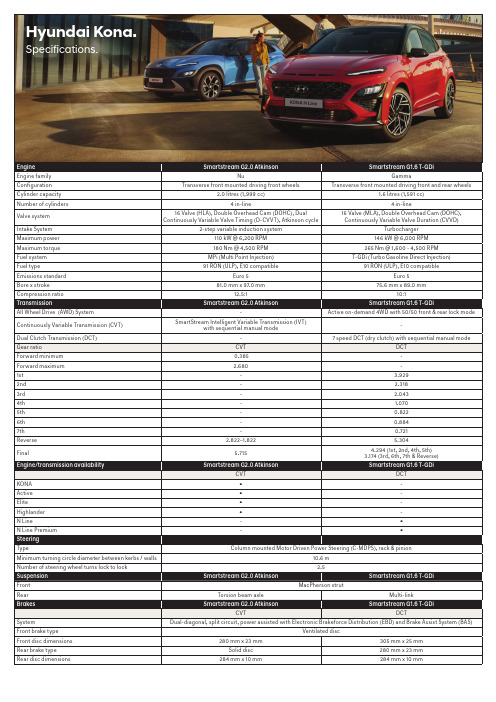
Hyundai Kona. Specifications.Weight Smartstream G2.0 Atkinson Smartstream G1.6 T-GDiCVT DCTKerb weight - lightest 1280 kg1395 kgKerb weight - heaviest1383 kg1504 kgGross Vehicle Mass (GVM)1835 kg1935 kgPermissible Axle Weight (PAW) - front1055 kg1055 kgPermissible Axle Weight (PAW) - rear935 kg960 kgRoof rack load limit80 kg80 kgTowing capacity wing capacity Smartstrea Smartstream G2.0 Atkinson m G2.0 Atkinson Smartstream Smartstream G1.6 T-GDi G1.6 T-GDiCVT DCTBraked1300 kg1250 kgUnbraked600 kg600 kgMaximum towball weight130 kg130 kgFuel consumption*sumption*Smartstre Smartstream G2.0 Atkinson am G2.0 Atkinson Smartstream G Smartstream G1.6 T-GDi 1.6 T-GDiCVT DCTCombined (L/100km) 6.2 6.9Urban (L/100km)8.38.2Extra Urban (L/100km) 5.0 6.1CO2- combined (g/km)148156Fuel tank volume50 L*Source: Australian Design Rule 81/02 static laboratory combined average city and highway cycle test. Real world fuel consumption will vary depending on a combination of driving habits, the condition of the vehicle, and other factors such as road, traffic and weather conditions. ADR 81/02 test results are meant for comparison purposes only.Dimensions KONA Active Elite Highlander N Line N Line Premium ExteriorLength4205 mm4215 mmWidth1800 mmHeight (with roof rails)1550 mm (1565 mm)1560 mm (1575 mm) Wheelbase2600 mmWheel track - front / rear1575 mm / 1584 mm1563 mm / 1572 mm1563 mm / 1572 mm1559 mm / 1568 mm1559 mm / 1568 mm Minimum ground clearance(based on kerb weight) 170mm177mm177mm178mm178mmApproach / departure / ramp break over angle14.8º / 30.7º / 16.1º15.5º / 29.9º / 16.8ºInteriorHead room front / rear (w/ Sunroof)1005 (965) / 961 mmLeg room front / rear1054 / 893 mmShoulder room front / rear1409 / 1385 mmHip room front / rear1355 / 1326 mmCargo area - VDA (minimum / maximum)374 L / 1156 LWheels & tyres KONA Active Elite Highlander N Line N Line Premium Wheel type Alloy Alloy Alloy Alloy Alloy (N Line)Alloy (N Line) Wheel dimensions16 x 6.5J +4417 x 7.0J +5017 x 7.0J +5018 x 7.5J +5218 x 7.5J +5218 x 7.5J +52 Tyre dimensions205/60 R16 92H215/55 R17 94V215/55 R17 94V235/45 R18 94V235/45 R18 94V235/45 R18 94VTyre brand---ContinentalPremiumContact 6ContinentalPremiumContact 6ContinentalPremiumContact 6Spare wheel type Temporary spacesaver Temporary spacesaverTemporary spacesaverTemporary spacesaverTemporary spacesaverTemporary spacesaverDriving convenience KONA Active Elite Highlander N Line N Line Premium Electronic Parking Brake (EPB)(with auto hold function)●●●●●●One touch turn signal - 3, 5, or 7 flashes●●●●●●Rain sensing wipers--●●●●Rear wiper - 2-stage, with auto wipe on reverse ●●●●●●Remote start - via Smart Key--●●●●Smart Key with push button start--●●●●Steering wheel mounted controls - audio,phone, cruise control & trip computer●●●●●●Tilt & telescopic steering column●●●●●●Driving engagement KONA Active Elite Highlander N Line N Line Premium Drive Mode - 4 settings(Eco, Comfort/Normal, Sport, Smart)●●●●●●Traction Mode - 3 settings (Snow, Mud, Sand)●●●●--Active safety KONA Active Elite Highlander N Line N Line Premium Electronic Stability Control (ESC) including;Anti-lock Braking System (ABS)●●●●●●Brake Assist System (BAS)●●●●●●Electronic Brakeforce Distribution (EBD)●●●●●●Downhill Brake Control (DBC)●●●●●●Hill-start Assist Control (HAC)●●●●●●Traction Control System (TCS)●●●●●●Vehicle Stability Management (VSM) ●●●●●●Active safety KONA Active Elite Highlander N Line N Line Premium Hyundai SmartSense ™ including;Blind-Spot Collision-Avoidance Assist (BCA)--●●●●Driver Attention Warning (DAW)●●●●●●Forward Collision-Avoidance Assist (FCA)- camera and radar type, including:●●●●●●- Car/Pedestrian/Cyclist detection- City/Urban/Interurban operational speedsHigh Beam Assist (HBA)---●-●Lane Following Assist (LFA)●●●●●●Lane Keeping Assist - Line/Road-edge(LKA-L/R)●●●●●●Rear Cross-Traffic Collision-AvoidanceAssist (RCCA)--●●●●Rear Occupant Alert (ROA)●●●●●●Safe Exit Warning (SEW)--●●●●Smart Cruise Control with Stop & Go(SCC w/ S&G)●●●●●●Other featuresEmergency Stop Signal (ESS)●●●●●●Parking Distance Warning-Front (PDW-F)- 4 sensors, with guidance display---●-●Parking Distance Warning-Reverse (PDW-R)- 4 sensors, with guidance display-●●●●●Rear view camera with dynamic guide lines●●----Rear View Monitor with Parking Guidance(RVM w/ PG)--●●●●Tyre Pressure Monitoring System (TPMS) -individual tyre pressure readout●●●●●●Passive safety KONA Active Elite Highlander N Line N Line Premium AirbagsFront airbags - driver & front passenger●●●●●●Side (thorax) airbags - driver & front passenger●●●●●●Side curtain airbags - 1st & 2nd row●●●●●●Roll-over Sensor●●●●●●DoorsImpact sensing auto door unlock●●●●●●Rear door child safety locks●●●●●●SeatbeltsPretensioners, load limiters & heightadjustable upper mounts on front seat belts●●●●●●Pretensioners & load limiters on rear seat belts●●●●●●Seat belt reminder - front & rear seatbelts●●●●●●SeatingHeight adjustable front head restraints withtilt function●●●●●●Height adjustable rear head restraints●●●●●●ISOFIX child restraint anchors(rear outboard seats)●●●●●●Top tether child restraint anchors (rear)- 3 anchors●●●●●●Security KONA Active Elite Highlander N Line N Line Premium Security systemActive lock/unlock operation(user configurable)●●●●●●Anti-theft alarm●●●●●●Central locking●●●●●●Engine immobiliser●●●●●●RemotesKeyless entry remote - 2x●●----Smart Key remote - 2x--●●●●Multimedia system KONA Active Elite Highlander N Line N Line Premium FunctionsApple CarPlay1 & Android Auto2 compatibility●●●●●●Bluetooth phone connectivity●●●●●●Satellite navigation --●●●●Live traffic updates (RDS-TMC)--●●●●Touch screen - 8” display●●----Touch screen - 10.25” display--●●●●Multimedia system KONA Active Elite Highlander N Line N Line Premium SpeakersAudio system - 6 speakers●●----Harman Kardon™ premium audio system- 8 speakers with external amplifier--●●●●Audio/media sourcesAM/FM radio●●●●●●Digital radio (DAB+)--●●●●Radio Data System (RDS)●●●●●●USB multimedia input●●●●●●Bluetooth audio streaming●●●●●●Quiet Mode - Speaker volume limitation fora quieter cabin●●●●●●Occupant comfort & convenience KONA Active Elite Highlander N Line N Line Premium Upholstery/trimLeather3 appointed interior - seats, steeringwheel & gear knob-●●●●●Front seatsDriver’s seat - height adjustable●●●●●●Driver’s seat - power adjustable - 10-way(including 2-way lumbar support) ---●-●Passenger’s seat - height adjustable●●●●●●Passenger’s seat - power adjustable - 8-way---●-●Front centre console storage cubby - poweroutlets - 2 x 12V outlets●●●●●●Front centre console - wireless charging pad(Qi standard)4●●●●●●Grip handles - 1x (passenger)●●●●●●Rear seatsCentre fold down armrest-●●●●●Grip handles - 2x●●●●●●Rear centre console - USB power outlet●●●●●●Windows/shadesAcoustic laminated windshield glass--●●●●Glass sunroof - tilt and slide panel ---●5-●5One touch window up & down function withanti-pinching safety feature - driver’s window●●●●●●Power windows - front & rear●●●●●●Rear privacy glass-●●●●●Solar control glass -●●●●●Sunvisor (extendable) - driver and frontpassenger●●●●●●Vision & sight KONA Active Elite Highlander N Line N Line Premium Interior mirrorElectro-chromatic Mirror (ECM)- auto-dimming---●-●Exterior mirrorsHeated-●●●●●Power adjustable ●●●●●●Power folding with auto fold function-●●●●●Instrument cluster/driving displaysHead-Up Display (HUD)---●-●Supervision cluster - 4.2” TFT colour LCDwith trip computer & digital speedometer●●●-●-Supervision cluster - 10.25” TFT colour LCDwith trip computer & digital speedometer---●-●Ventilation & heating KONA Active Elite Highlander N Line N Line Premium Air conditioningClimate control - single zone with auto defogfunction--●●●●Manual controls●●----Cabin air filter ●●●●●●Cooling/heating vents - rear floor●●●●●●Front seatsAir ventilated front seats---●-●Heated front seats---●-●Ventilation & heating KONA Active Elite Highlander N Line N Line Premium Rear seatsHeated rear outboard seats---●-●Other featuresHeated rear windshield●●●●●●Heated steering wheel---●-●Exterior styling KONA Active Elite Highlander N Line N Line Premium FrontFront bumper garnish insert - satin chrome--●●--Front bumper garnish insert - silver●●----Front grille lower - gloss black●●●●--Front grille upper - black●●----Front grille upper - gloss black--●●--Front skid plate - silver--●●--Front skid plate - grey●●----N Line-exclusive front bumper----●●N Line-exclusive mesh design grille----●●SideBody cladding - body colour----●●Body cladding - carbon grey--●●--Side garnish insert - silver--●●--N Line-exclusive side skirts----●●RearDual exhaust tips - chrome ----●●Skid plate - grey●●----Skid plate - silver--●●--Spoiler - roof colour matched, tailgatemounted ●●●●●●Tailgate garnish insert - chrome--●●--N Line-exclusive rear bumper----●●N Line-exclusive rear diffuser----●●Interior styling KONA Active Elite Highlander N Line N Line Premium TreatmentsBlack headlining----●●Cloth headlining---●5-●5 Charcoal grey inserts (interior door handles,steering wheel and air vents)----●●Coloured inserts, stitching & piping - red----●●(air vents, gear knob, gear shift boot, seatsand steering wheel)MaterialsPremium materials - door centre trim-●●●●●Sports pedals - alloy----●●DesignN Line-exclusive sports gear knob----●●N Line-exclusive sports front seats----●●N Line-exclusive sports steering wheel----●●Lighting KONA Active Elite Highlander N Line N Line Premium Exterior lighting - frontFog lights--●●--Daytime Running Lights (DRL) - LED●●●●●●Headlight functions - automatic dusksensing with escort and welcome●●●●●●Headlight type - LED (low/high beam)---●-●Headlight type - multi face reflector---●-●Headlight type - projector beam●●●-●-Indicator lights - LED---●-●Positioning lights - LED●●●●●●Exterior lighting - rearFog light●●●●●●High Mount Stop Light (HMSL) - LED●●●●●●Rear combination lights - LED (bulbreverse lights)---●-●Lighting KONA Active Elite Highlander N Line N Line Premium Exterior lighting - othersSide repeaters - LED, integratedinto side mirrors●●●●●●Interior lighting - frontFront ambient lighting - LED, in centreconsole cup holders and lower legroom---●-●Front room lights and map lights●●●●●●Glovebox compartment light●●●●●●Vanity mirror lights ●●●●●●Interior lighting - rearCentre room light●●●●●●Interior lighting - othersCargo area light●●●●●●Interior light fade-out delay●●●●●●Storage solutions KONA Active Elite Highlander N Line N Line Premium Front seatsCup holders - centre console ●●●●●●Front seat back pockets-●●●●●Glovebox compartment●●●●●●Retractable sunglasses compartment●●●●●●Ticket holders - sunvisors(driver and front passenger)●●●●●●Rear seatsCoat hooks - 1x●●●●●●Cup holders - armrest-●●●●●Rear seating split folding - 60:40●●●●●●Boot/Luggage areaBag hooks - 1x●●●●●●Cargo shelf●●●●●●Luggage compartment - 4x mounting points●●●●●●Luggage net ●●●●●●Side storage recess - right side●●----OthersDoors - map pockets and bottle bulges(front and rear)●●●●●●Roof Rails●●●●●●Option packages KONA Active Elite Highlander N Line N Line Premium Two-Tone Roof packPhantom Black two-tone roof and sidemirrors---○-○Notes:1. Apple CarPlay requires iPhone 5 or subsequent model (lightning cable) in order to operate.2. Android Auto requires a device with Android 5.0 operating system or subsequent version in order to operate.3. Finishes specified as leather may contain elements of genuine leather, polyurethane leather (leather substitute) or man-made materials, or a combination thereof.4. Wireless charging requires a Qi-enabled smartphone or adapter in order to operate.5. Feature not available when Two-tone roof is optioned.Key:● = Feature is available on trim○ = Feature is available on trim only as part of an option pack- = Feature is not available on trim。
Eaton Moeller series Rapid Link速控器198910产品说明说明书
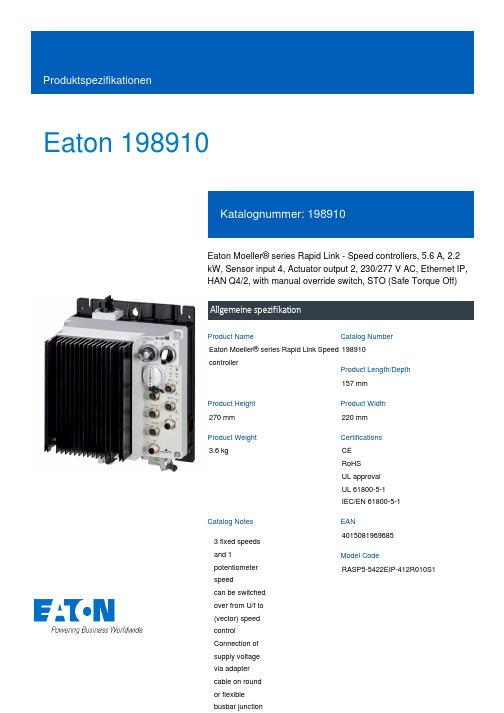
Eaton 198910Eaton Moeller® series Rapid Link - Speed controllers, 5.6 A, 2.2 kW, Sensor input 4, Actuator output 2, 230/277 V AC, Ethernet IP, HAN Q4/2, with manual override switch, STO (Safe Torque Off)Allgemeine spezifikationEaton Moeller® series Rapid Link Speed controller198910157 mm270 mm 220 mm 3.6 kgCE RoHS UL approval UL 61800-5-1 IEC/EN 61800-5-14015081969685RASP5-5422EIP-412R010S1Product NameCatalog NumberProduct Length/Depth Product Height Product Width Product Weight Certifications Catalog Notes EANModel Code3 fixed speeds and 1 potentiometer speedcan be switched over from U/f to (vector) speed control Connection of supply voltage via adapter cable on round or flexible busbar junctionParameterization: drivesConnectParameterization: FieldbusParameterization: KeypadParameterization: drivesConnect mobile (App)Manual override switchControl unitKey switch position AUTOKey switch position OFF/RESETKey switch position HANDPC connectionTwo sensor inputs through M12 sockets (max. 150 mA) for quick stop and interlocked manual operationSelector switch (Positions: REV - OFF - FWD)Thermo-click with safe isolationIGBT inverter2 Actuator outputsInternal DC linkPTC thermistor monitoring3 fixed speedsSTO (Safe Torque Off)For actuation of motors with mechanical brake1 potentiometer speed IP65NEMA 121st and 2nd environments (according to EN 61800-3)IIISpeed controllerEtherNet/IPC1: for conducted emissions onlyC2, C3: depending on the motor cable length, the connected load, and ambient conditions. External radio interference suppression filters (optional) may be necessary.2000 VPhase-earthed AC supply systems are not permitted.AC voltageCenter-point earthed star network (TN-S network)Vertical15 g, Mechanical, According to IEC/EN 60068-2-27, 11 ms, Half-sinusoidal shock 11 ms, 1000 shocks per shaftResistance: 6 Hz, Amplitude 0.15 mmResistance: According to IEC/EN 60068-2-6Resistance: 57 Hz, Amplitude transition frequency on accelerationResistance: 10 - 150 Hz, Oscillation frequency Above 1000 m with 1 % performance reduction per 100 m Max. 2000 m-10 °C40 °C-40 °C70 °CFeatures Fitted with:Functions Degree of protectionElectromagnetic compatibility Overvoltage categoryProduct categoryProtocolRadio interference classRated impulse withstand voltage (Uimp) System configuration typeMounting position Shock resistance Vibration AltitudeAmbient operating temperature - min Ambient operating temperature - max Ambient storage temperature - min Ambient storage temperature - max Climatic proofing< 95 %, no condensationIn accordance with IEC/EN 50178Current limitationAdjustable, motor, main circuit0.5 - 5.6 A, motor, main circuitDelay time< 10 ms, On-delay< 10 ms, Off-delayEfficiency98 % (η)Input current ILN at 150% overload5.3 ALeakage current at ground IPE - max3.5 mAMains current distortion120 %Mains switch-on frequencyMaximum of one time every 60 secondsMains voltage - min380 VMains voltage - max480 VMains voltage tolerance380 - 480 V (-10 %/+10 %, at 50/60 Hz)Operating modeSynchronous reluctance motorsBLDC motorsPM and LSPM motorsSensorless vector control (SLV)U/f controlOutput frequency - min0 HzOutput frequency - max500 HzOverload currentFor 60 s every 600 sAt 40 °COverload current IL at 150% overload8.4 A45 Hz66 Hz5.6 A at 150% overload (at an operating frequency of 8 kHz and an ambient air temperature of +40 °C)2.2 kW480 V AC, 3-phase400 V AC, 3-phase0.1 Hz (Frequency resolution, setpoint value)200 %, IH, max. starting current (High Overload), For 2 seconds every 20 seconds, Power section50/60 Hz8 kHz, 4 - 32 kHz adjustable, fPWM, Power section, Main circuitPhase-earthed AC supply systems are not permitted.AC voltageCenter-point earthed star network (TN-S network)3 HP≤ 0.6 A (max. 6 A for 120 ms), Actuator for external motor brake≤ 30 % (I/Ie)Adjustable to 100 % (I/Ie), DC - Main circuit230/277 V AC -15 % / +10 %, Actuator for external motor brake10 kAType 1 coordination via the power bus' feeder unit, Main circuit230/277 V AC (external brake 50/60 Hz)24 V DC (-15 %/+20 %, external via AS-Interface® plug)Ethernet IP, built inPlug type: HAN Q4/2Number of slave addresses: 31 (AS-Interface®)Max. total power consumption from AS-Interface® power supply unit (30 V): 250 mASpecification: S-7.4 (AS-Interface®)C2 ≤ 5 m, maximum motor cable length C1 ≤ 1 m, maximum motor cable length C3 ≤ 25 m, maximum motor cable lengthMeets the product standard's requirements.Rated frequency - minRated frequency - maxRated operational current (Ie)Rated operational power at 380/400 V, 50 Hz, 3-phase Rated operational voltageResolutionStarting current - maxSupply frequencySwitching frequencySystem configuration type Assigned motor power at 460/480 V, 60 Hz, 3-phase Braking currentBraking torqueBraking voltageRated conditional short-circuit current (Iq)Short-circuit protection (external output circuits) Rated control voltage (Uc)Communication interfaceConnectionInterfacesCable length10.2.2 Corrosion resistanceMeets the product standard's requirements.Meets the product standard's requirements.Meets the product standard's requirements.Meets the product standard's requirements.Does not apply, since the entire switchgear needs to be evaluated.Does not apply, since the entire switchgear needs to be evaluated.Meets the product standard's requirements.Does not apply, since the entire switchgear needs to be evaluated.Meets the product standard's requirements.Does not apply, since the entire switchgear needs to be evaluated.Does not apply, since the entire switchgear needs to be evaluated.Is the panel builder's responsibility.Is the panel builder's responsibility.Is the panel builder's responsibility.Is the panel builder's responsibility.Is the panel builder's responsibility.Elektromagnetische Verträglichkeit (EMV) Generationenwechsel RA-SP zu RASP5Generationentausch RA-SP zu RASP4.0Generation change from RA-MO to RAMO 4.0Configuration to Rockwell PLC for Rapid Link Generationentausch RA-MO zu RAMO4.0Configuration to Rockwell PLC Rapid Link 5Generation change RAMO4 to RAMO5Generation Change RA-SP to RASP5Generation change from RA-SP to RASP 4.0Anschluss von Frequenzumrichtern an Generatornetze Generationentausch RAMO4 zu RAMO5Generation Change RASP4 to RASP5Firmware Update RASP 4.0Generationswechsel RASP4 zu RASP5MN034004_DEMN040003_DERapid Link 5 - brochureDA-SW-drivesConnect - installation helpDA-SW-Driver DX-CBL-PC-3M0DA-SW-USB Driver DX-COM-STICK3-KITDA-SW-drivesConnect - InstallationshilfeDA-SW-USB Driver PC Cable DX-CBL-PC-1M5DA-SW-drivesConnectMaterial handling applications - airports, warehouses and intra-logistics ETN.RASP5-5422EIP-412R010S1.edzIL034093ZUDE | Rapid Link 5Sortimentskatalog Antriebstechnik-DE10.2.3.1 Verification of thermal stability of enclosures10.2.3.2 Verification of resistance of insulating materials to normal heat10.2.3.3 Resist. of insul. mat. to abnormal heat/fire by internal elect. effects10.2.4 Resistance to ultra-violet (UV) radiation10.2.5 Lifting10.2.6 Mechanical impact10.2.7 Inscriptions10.3 Degree of protection of assemblies10.4 Clearances and creepage distances10.5 Protection against electric shock10.6 Incorporation of switching devices and components10.7 Internal electrical circuits and connections10.8 Connections for external conductors10.9.2 Power-frequency electric strength10.9.3 Impulse withstand voltage10.9.4 Testing of enclosures made of insulating material Anmerkungen zur AnwendungBenutzerhandbücherBroschüreneCAD model Installationsanleitung InstallationsvideosKatalogeEaton Konzern plc Eaton-Haus30 Pembroke-Straße Dublin 4, Irland © 2023 Eaton. Alle Rechte vorbehalten. Eaton ist eine eingetrageneMarke.Alle anderen Warenzeichen sindEigentum ihrer jeweiligenBesitzer./socialmediaThe panel builder is responsible for the temperature rise calculation. Eaton will provide heat dissipation data for the devices.Is the panel builder's responsibility. The specifications for the switchgear must be observed.Is the panel builder's responsibility. The specifications for the switchgear must be observed.The device meets the requirements, provided the information in the instruction leaflet (IL) is observed.ramo5_v33.dwgrasp5_v33.stpeaton-bus-adapter-rapidlink-speed-controller-dimensions-005.eps eaton-bus-adapter-rapidlink-speed-controller-dimensions-002.eps eaton-bus-adapter-rapidlink-speed-controller-dimensions-004.eps eaton-bus-adapter-rapidlink-speed-controller-dimensions-003.eps10.10 Temperature rise10.11 Short-circuit rating10.12 Electromagnetic compatibility 10.13 Mechanical function mCAD model Zeichnungen。
Moog高级高力线性电机LCA、LCB、LCC、LCD和LCE线性编码器选项用户手册说明书

U SERS’ M ANUALF ORLinear Encoder Options LCA, LCB, LCC,LCD and LCEA VAILABLE W ITHM OOG A DVANCED-H IGH F ORCE L INEAR M OTORSUM-103 Revision BDate: 03/17/09Linear Encoder Option designed by Motor Option NumbersLCA, LCB, LCC, LCD and LCEMoog Components GroupSpringfield Operations750 West Sproul RoadSpringfield, PA 19064Ph: 610-328-4000, Toll Free: 800-510-6885Fx: 610-605-6216 2009E-mail: ************Web-site: /componentsPAGE INTENTIONALLY LEFT BLANKTable of Contents:1.SAFETY: (4)2.WARNINGS, CAUTIONS AND NOTES: (4)3.SCOPE: (7)4.INTRODUCTION: (8)4.1. Installation Sequence: (9)RMATION FOR DRIVE OR CONTROLLER SETUP: (10)6.MECHANICAL MOUNTING NOTES: (11)6.1. Encoder Alignment: (11)6.2. Dual-Face Mounting: (12)6.3. End-Stops: (12)6.4. Notes: (12)7.ENCODER CABLE CONNECTIONS: (14)7.1. Selecting the Linear Encoder Modular Cables: (14)7.2. Wiring the Linear Encoder to the Drive with the Pigtail Cable: (15)7.2.1. Pigtail Lead Terminations: (15)7.2.2. Pigtail cable signal descriptions: (16)7.2.2.1. Encoder and Hall Sensor Power: (16)7.2.2.2. Digital Quadrature Incremental Signals A and B: (17)7.2.2.3. Sin/Cos signals using Option LCE: (17)7.2.2.4. Encoder Misalignment Fault Alarm E: (17)7.2.2.5. Signal Quality / Alignment signal X: (17)7.2.2.6. Reference Mark (Z, Vo) and Limit Switch (Vq) signals: (18)7.2.2.7. Commutation (Hall Sensor) Connections: (19)7.2.2.8. Inner and Outer Shields: (20)7.2.2.9. Voltage Sense wires Vref+ and Vref-: (20)APPENDIX-A: (REVISION HISTORY) (21)!1. Moog motors are capable of producing high forces and velocities. Alwaysfollow appropriate safety precautions when installing and applying these motors. Equipment should be designed and utilized to prevent personnel from coming in contact with moving parts that could potentially cause injury.Safety:Read the Moog Linear Motor User’s Manual which applies to the motor you are using before attempting to operate this device.Read all cautions, warnings and notes before attempting to operate this device.Follow all applicable codes and standards.2. The following conventions are used on the equipment and found in thismanual. Please read all equipment labels and manuals before attempting to use Moog Linear Motors.Warnings, Cautions and Notes:A WARNING identifies information that is critical for identifying and avoiding a hazard that could lead to serious personnel injury or equipment damage.A CAUTION identifies information that is critical to prevent permanent equipment damage.A NOTE identifies information that is critical for successful application andunderstanding of the product.Follow all warnings and cautions listed in this manual and in the applicable Moog Linear Motor User’s Manual when working with Moog Components Group High Force Linear Motors..! WARNING: Do not remove the Linear Position Sensor Cover plates or otherwise disassemble the Linear Position Sensor. Hands, fingers or clothing may be pinched or caught in the moving parts. !3.Scope:This manual provides information for the installation of Linear Encoder Options LCA, LCB, LCC, LCD and LCE which are available with the Moog4020/5020 Linear Motors. For all other aspects of Linear Motor installation, please refer to the appropriate user’s manual.Linear Encoder Option on a 50204C Motor.Introduction:4.The Linear Encoder Option is provided as a mechanically integral part of the Linear Motor. Depending upon the motor drive system and the Linear Encoder option specified, it provides the required Position Feedback, Commutation data, Reference Mark, Limit switch and Encoder Fault alarm functions.Typical Servo System with Moog Motor:Moog Motor with Linear Scale Option LCXFig 4-1Options LCX provide Integral Motor Position Sensing as part of theLinear Motor System.4.1.Installation Sequence:Use the following sequence when installing a Moog linear motor the Linear Sensor Option. Those steps in bold apply specifically to this Linear Encoder Installation manual.1.Read the applicable motor installation manual and observe all warnings,cautions, and notes in Sections 1 and 2 of that manual.2.Read additionally and observe this manual’s warnings, cautions, and notes(Sections 1 and 2 of this manual).3.Properly mount the motor (Section 5 of the Motor Installation Manual).4.Ensure that no lateral loads or torques are applied to the motor shaftwhich will impair encoder operation (Section 6 of this manual).5.Configure Encoder position signals and Commutation signals to indicatepositive motion consistent with positive Drive effort and positive shaft movement (Section 7 of the Motor Installation Manual).6.Make the Encoder cable connections (Section 7 of this manual)7.Interconnect the motor to the control system (Section 6 of the MotorInstallation Manual).8.Ensure good electrical shielding and grounding throughout the system(Section 6.5 of the Motor Installation Manual).9.Initialize the motor with the control system, limits and controller / Drivesensing and commutation parameters for the Encoder option used) (Section7 of the Motor Installation manual).10.Attach the load in a manner that does not induce or cause binding when themotor is stationary or moving (Section 5.3 of the Motor Installation Manual).11.Tune the system for desired performance and accuracy (Section 7.4 of theMotor Installation Manual).rmation for Drive or Controller Setup:The motor part number specifies the Linear Encoder Option:CLD4020D06-LCX-T-CVLCX is either LCA, LCB, LCC, LCD or LCE. Linear Encoder options A through E provide different resolutions, signal types, and compatibility. The Interface Control Drawing for the Linear Encoder option contains the relevant specifications.Option Scale Resolution Feedback TypeLCA 5 micron 5080 cts/inch Quadrature IncrementalLCB 1 micron 25400 cts/inch Quadrature IncrementalLCC 0.5 micron 50800 cts/inch Quadrature IncrementalLCD 0.1 micron 254000 cts/inch Quadrature IncrementalLCE 20 micron See Note 1 Sin/CosTable 5-1. Summary of Linear Encoder OptionsNote 1: Resolution of the Sin/Cos encoder depends on the level of interpolation provided by the encoder interface of your control system.Note that all options provide 120 degree, Positive Hall format Commutation Signals per NEMA ICS 16.6. 6.1. Mechanical Mounting Notes:Encoder Alignment:The Linear Encoder Option provides Position Feedback, Commutation data, Indexing and Home switch functions required to control the Motor.With the encoder option, encoder and Hall device “heads” are mounted together on one end of the motor shaft. The heads move with the shaft and read positional and commutation data from separate, stationary tracks mounted to the encoder rail.Fig 6-1Side loads and Torques may impair encoder alignment.Linear bearings within the encoder rail physically align the heads and shaft with the stationary tracks. These bearings also prevent shaft rotation. Do not allow loads to apply torque or lateral loads to the shaft during installation or use. Do not apply lateral loads to the Encoder Rail housing. Excessive Torque or Lateral Loads will cause binding or reduce the life of the bearings within the encoder rail and result in misalignment of the encoder.Encoder heads are aligned at the factory before shipping and should not be adjusted by the user.6.2.Dual-Face Mounting:Dual-Face Mounting can only be utilized without an integral Moog position sensor. For information on Dual-Face Mounting please refer to the appropriate Moog user’s manual.6.3.End-Stops:Two End Stops are provided on the Moog Motor. The internal End Stop is not to be removed by the user.Fig 6-2LCX Option provides an internal End Stop.6.4. Notes:! !WARNING: Do not remove the Linear Position Sensor Coverplates or otherwise disassemble the Linear Position Sensor. Do not operate the Moog Linear Motor with Linear Position Sensor option when the Linear Position Sensor cover plates are removed. Hands, fingers or clothing may be pinched or caught in the moving parts.!7. Encoder cables are available from Moog in standard configurationscompatible with major Drive manufacturers. A pigtail version is also available which allows custom wiring to suit other Drives.Encoder Cable Connections:If you are using one of the Drives for which a standard cable is available, plug the Circular connector end of the cable into the Encoder connector on the Motor and the other end into the Drive. The position and commutation connections should at this point be properly wired. Motor End Typical Sensor Cable Drive EndEncoder Connector Drive and Temp Sense connectorsFigure 7-1Modular Cables connect the Drive / Amplifier with the Linear Motor.7.1.Selecting the Linear Encoder Modular Cables:Modular Cables.Wiring can be greatly simplified if a Drive or Amplifier isused for which a Moog standard cable already exists. See Moog product literature to select a cable on the basis of Drive model and required cable length.7.2.Wiring the Linear Encoder to the Drive with the Pigtail Cable:If you cannot use a modular cable, connect the drive using the following “pigtail” cable:FSC-EC-XXwhere XX = 02, 10 or 25, corresponds to cable length in feet.Figure 7-2Pigtail Cable provides termination to most compatible Drives.7.2.1. Pigtail Lead Terminations:The FSC-LC-XX cable is a 30 Conductor cable per AWM 2464. The Drive End is terminated in colored leads of 24 Gauge. When stripped, these can beterminated to Terminal Blocks, pins or sockets as required by the Drive connectors.7.2.2. Pigtail cable signal descriptions:In addition to sensor power, five general types of signals are accessed by the Linear Encoder connector: Position, Hall, Fault / Signal Quality, Reference Mark and Index. Additional, auxiliary pins are reserved for future use.Identify and wire the Encoder Power and signals for Position, Commutation, Encoder Fault, Reference Mark and Index functions per Figure 7-4 and the following signal descriptions.Drive Connector Motor Connector Drive Connector Motor ConnectorFigure 7-3Pinouts and Wire Colors for the FSC-EC-XX Cable / LCX Encoder option.7.2.2.1.Encoder and Hall Sensor Power:The Position Sensor requires DC Power at 5.0 V +/- 5% at the Encoder Cable leads providing at least 100 mA DC. The Encoder power supply is applied to +5V and GND at pins 1 and 2 respectively.The Hall sensor head is powered separately from the Encoder and requires DC Power at 5.0 V +/- 5% at the Encoder Cable leads, providing at least 20 mA DC. The Hall sensor power supply is applied to +5V and GND at pins 17 and 18 respectively.If both Hall sensor and Encoder are used, connect both grounds and +5V pins.7.2.2.2.Digital Quadrature Incremental Signals A and B:Encoder options LCA, LCB, LCC and LCD provide Differential Mode Digital Quadrature Incremental Encoder data lines A+, A-, B+ and B-. These 0 to 5V (TTL level) signals connect to both single ended and Differential mode “A quad B” inputs and are electrically compatible with the industry standard RS-422 transmissionprotocol using the 26LS31 Buffer IC per Figure 7-4.Figure 7-4Digital Quadrature and Analog Quadrature (Sin/Cos) signals.7.2.2.3.Sin/Cos signals using Option LCE:Encoder option LCE provides Differential Mode Quadrature Sin/Cos Incremental Encoder data lines V1+, V1-, V2+ and V2-. These 0.3 – 1.2Vpp signals connect to both single ended and industry standard Differential mode “Sin/Cos”inputs per Figure 7-4.7.2.2.4.Encoder Misalignment Fault Alarm E:Encoder options LCA, LCB, LCC and LCD provide a HIGH state on TTL level Differential alarm outputs E when the optical encoder signal falls below 45% nominal range.7.2.2.5.Signal Quality / Alignment signal X:Signal Quality pin X is provided only for encoder setup and alignment, and is not generally required by the Motor User. See the Installation manual for theRenishaw series RGH Encoder Heads for more information.7.2.2.6.Reference Mark (Z, Vo) and Limit Switch (Vq) signals:A Differential Mode TTL Level (0-5V) voltage signal, active “HIGH”provides an accurate absolute position reference to designate the rated Mid stroke shaft position. (The Reference Mark is designated “Z” in options LCA, LCB, LCC and LCD and “Vo” in option LCE).Figure 7-5Electrical ports for Reference Mark and Limit Switch signalsA Limit Switch signal Vq is pulled low by a single ended Open Collector TTLLevel (0 to 5V) signal when the shaft is within 0.25 inches (10 mm) of either End – of – Rated Stroke shaft position as shown in Figure 7-6.Figure 7-6Reference Mark Limit Switch Location.The Reference Mark is Synchronous with both Digital and Analog Quadrature signal phase.Repeatability of the Reference mark is limited in Digital and Analog sensors by one quadrature Line Count or by +0 / -18 degrees of Sin/Cos signal phaserespectively.Figure 7-7Reference Mark Signal is synchronous with Quadrature Encoder Signals.The Limit Switch signal Vq is asynchronous with respect to the Quadrature Encoder signal phase. Repeatability of the Limit Switch positions is +0 / -0.1 mm (.004 inches).mutation (Hall Sensor) Connections:0 to 5V (TTL level) Differential mode Hall sensor signals are electricallycompatible with the industry standard RS-422 transmission protocol using the26LS31 Buffer IC. These signals are compatible with Drive Hall sensor inputsequipped with or without pull up resistors.Figure 7-8Hall Sensor Outputs.7.2.2.8. Inner and Outer Shields:Inner and Outer shields mitigate the effects of electrical noise on the encoder signal. In typical installations the inner shield is connected to encoder and / or Hall input signal Ground, and the outer shield to the Drive / Controller chassis.Figure 7-9Inner and Outer Shield connections.Grounding and Shielding of the Drive cables are also important for safety and for proper sensor electrical noise immunity. For more detail in system Grounding and Shielding, please see the Moog Linear Motor User’s Manual.7.2.2.9.Voltage Sense wires Vref+ and Vref-:In Option LCE, Vref+ and Vref- provide remote voltage sensing for regulation of the Encoder Power Supply to compensate for Encoder Power Supply voltage drop in long encoder cables. If remote sensing is not provided in the Drive, Vref+ and Vref- can be used as additional (paralleled) encoder power conductors by connecting Vref- and Vref+ to Ground and +5V respectively..Appendix-A: (Revision History)ECO # Revision Change Date _0112 A Initial Release April 1, 2003B Moog Update March 17, 2009UM-102 21 of 21 Revision B。
TSI Model 8610 EVERWATCH MODBUS 通信应用说明书

_____________________________________TSI, TSI logo, and E VER W ATCH are registered trademarks of TSI Incorporated. Modbus is a trademark of Modicon Incorporated.TSI ® MODEL 8610 EVERWATCH ®MODBUS™ COMMUNICATIONSAPPLICATION NOTE LC-115Modbus ™ communications are installed in all Model 8610 fume hood face velocity monitors. Thisdocument provides the technical information needed to communicate between the host DDC system and the Model 8610 units. This document assumes the programmer is familiar with Modbus ™ protocol. Further technical assistance is available from TSI if your question is related to TSI interfacing to a DDC system. If you need further information regarding Modbus ™ programming in general, please contact:Modicon Incorporated One High Street North Andover, MA 01845 Phone (508) 794-0800The Modbus ™ protocol utilizes the RTU format for data transfer and Error Checking. Check the Modicon Modbus ™Protocol Reference Guide (PI-Mbus-300) for more information on CRC generation and message structures.The messages are sent at 9600 baud with 1 start bit, 8 data bits, and 2 stop bits. Do not use the parity bit. The system is set up as a master slave network. The TSI units act as slaves and respond to messages when there correct address is polled.Blocks of data can be read from each device. Using a block format will speed up the time for the data transfer. The size of the blocks is limited to 15 bytes. This means the maximum message length that can be transferred is 15 bytes. The typical response time of the device is around 0.05 seconds with a maximum of 0.1 seconds.Unique to TSIThe list of variable addresses shown below skips some numbers in the sequence due to internalModel 8610 functions. This information is not useful to the DDC system and is therefore deleted. Skipping numbers in the sequence will not cause any communication problems.RAM VariablesRAM variables can be read using the Modbus™ command 04 Read Input Registers. They can be written to using the Modbus™ command 06 Preset Single Register. The RAM variables can be read in blocks but must be written one variable at a time.8610 Fume Hood MonitorVariable Name VariableAddressInformation Provided to MasterSystem Integer DDC system receivesModel Number 0 Model Number 8610Face Velocity 1 Fume Hood Face Velocity Displayed in ft/min.Status Index 2 Status of EVERWATCH device 0 Normal 1 Low Alarm2 High Alarm3 Sensor Error5 Data ErrorLow Alarm 3 Low Alarm Setpoint Displayed in ft/min.High Alarm 4 High Alarm Setpoint Displayed in ft/min.Filter Index 5 Index for display averaging time 0 1 Second 1 2 Seconds2 3 Seconds 3 5 Seconds4 10 Seconds5 20 Seconds Alarm Mode6 Alarm Reset Mode 0 Unlatched 1 LatchedAudible Disable 7 Permanent Mute Capability 0 Off 1 OnOutput Mode 8 Analog Output Mode 0 Current 1 VoltageNetwork Protocol 9 Communications Protocol 0 Modbus 1 Cimetrics Network 10 Address of unit forcommunications.0-247Calibration CodeEnable17 Calibration pass code enable. 0 Off 1 OnConfiguration CodeEnable18 Configuration pass code enable 0 Off 1 On*Remote Low Alarm 21 Second low alarm setpoint forremote mode.Displayed in ft/min.*Remote High Alarm 22 Second high alarm setpoint forremote mode.Displayed in ft/min.*Setback Mode 23 Control mode of device. Write only variable, reading will alwaysgive a value of 2. Initiates modechange.1 put unit in setback or remote mode.0 put unit in normal mode.*Note: These items only available on 8610-AS version.EXAMPLE of 04 Read Input Registers function format.This example read variable addresses 1 and 2 (Face Velocity and Status Index).QUERY RESPONSEFieldName(Hex)FieldName(Hex)Slave Address 01 Slave Address 01Function 04Function 04Starting Address Hi 00 Byte Count 04Starting Address Lo 01 Data Hi Addr 0 00No. Of Points Hi 00 Data Lo Addr 0 64 (100 ft/min)No. Of Points Lo 02 Data Hi Addr 1 00Error Check (CRC) -- Data Lo Addr 1 00 (Normal- No Alarm)ErrorCheck(CRC)--–2–TSI Incorporated – Visit our website for more information.USA Tel: +1 800 874 2811 UK Tel: +44 149 4 459200 France Tel: +33 4 91 11 87 64 Germany Tel: +49 241 523030 India Tel: +91 80 67877200 China Tel: +86 10 8251 6588 Singapore Tel: +65 6595 6388LC-115 Rev. C©2013 TSI IncorporatedPrinted in U.S.A.EXAMPLE of 06 Preset Single Register function format. This example changes the low alarm setpoint to 60 ft/min.QUERY RESPONSE Field Name (Hex) Field Name (Hex) Slave Address 01 Slave Address 01 Function 06 Function 06 Address Hi 00 Address Hi 00 Address Lo 03 Address Lo 03 Data Hi 00 Data Hi 00 Data Lo 3C Data Lo 3C Error Check (CRC) -- Error Check (CRC) --。
MODEL 2061使用手册北京雪迪龙
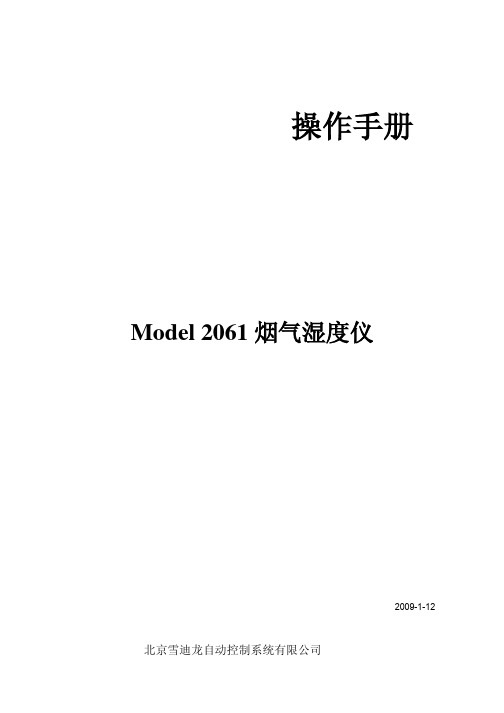
从低湿到高湿环境:10S
湿度传感器:
阻容式
温度传感器:
PT100 铂电阻
输出信号:
4…20mA
供电电源:
24VDC
模拟输出外接负载:
最大 500Ω(对地)
电流消耗:
最大 2 A
功耗(最大):
25W
工作温度范围:
传感器:
-40…+180°C
变送器及控制部分:
-10…+55°C
储存温度:
-40…+80°C
1
目
录
第一章 概述...................................................... 3 安全....................................................... 3 安全总则................................................... 3 和产品有关的安全注意事项................................... 3 防静电保护................................................. 3 环保........................................................4 反馈........................................................4 商标........................................................4 许可证协议................................................ 4 质保....................................................... 4
车载光棍说明书
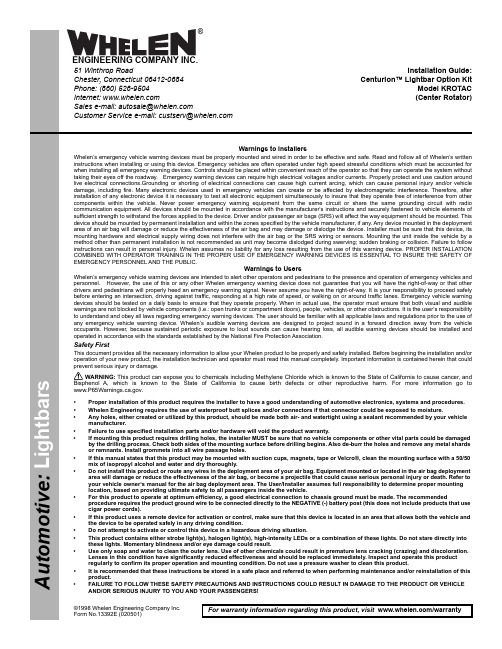
Page 1©1998 Whelen Engineering Company Inc.Form No.13392E (020501)A u t o m o t i v e : For warranty information regarding this product, visit /warranty•Proper installation of this product requires the installer to have a good understanding of automotive electronics, systems and procedures.•Whelen Engineering requires the use of waterproof butt splices and/or connectors if that connector could be exposed to moisture.•Any holes, either created or utilized by this product, should be made both air- and watertight using a sealant recommended by your vehicle manufacturer.•Failure to use specified installation parts and/or hardware will void the product warranty.•If mounting this product requires drilling holes, the installer MUST be sure that no vehicle components or other vital parts could be damaged by the drilling process. Check both sides of the mounting surface before drilling begins. Also de-burr the holes and remove any metal shards or remnants. Install grommets into all wire passage holes.•If this manual states that this product may be mounted with suction cups, magnets, tape or Velcro®, clean the mounting surface with a 50/50 mix of isopropyl alcohol and water and dry thoroughly.•Do not install this product or route any wires in the deployment area of your air bag. Equipment mounted or located in the air bag deployment area will damage or reduce the effectiveness of the air bag, or become a projectile that could cause serious personal injury or death. Refer to your vehicle owner’s manual for the air bag deployment area. The User/Installer assumes full responsibility to determine proper mounting location, based on providing ultimate safety to all passengers inside the vehicle.•For this product to operate at optimum efficiency, a good electrical connection to chassis ground must be made. The recommendedprocedure requires the product ground wire to be connected directly to the NEGATIVE (-) battery post (this does not include products that use cigar power cords).•If this product uses a remote device for activation or control, make sure that this device is located in an area that allows both the vehicle and the device to be operated safely in any driving condition.•Do not attempt to activate or control this device in a hazardous driving situation.•This product contains either strobe light(s), halogen light(s), high-intensity LEDs or a combination of these lights. Do not stare directly into these lights. Momentary blindness and/or eye damage could result.•Use only soap and water to clean the outer lens. Use of other chemicals could result in premature lens cracking (crazing) and discoloration. Lenses in this condition have significantly reduced effectiveness and should be replaced immediately. Inspect and operate this product regularly to confirm its proper operation and mounting condition. Do not use a pressure washer to clean this product.•It is recommended that these instructions be stored in a safe place and referred to when performing maintenance and/or reinstallation of this product.•FAILURE TO FOLLOW THESE SAFETY PRECAUTIONS AND INSTRUCTIONS COULD RESULT IN DAMAGE TO THE PRODUCT OR VEHICLE AND/OR SERIOUS INJURY TO YOU AND YOUR PASSENGERS!Warnings to InstallersWhelen’s emergency vehicle warning devices must be properly mounted and wired in order to be effective and safe. Read and follow all of Whelen’s written instructions when installing or using this device. Emergency vehicles are often operated under high speed stressful conditions which must be accounted for when installing all emergency warning devices. Controls should be placed within convenient reach of the operator so that they can operate the system without taking their eyes off the roadway. Emergency warning devices can require high electrical voltages and/or currents. Properly protect and use caution around live electrical connections.Grounding or shorting of electrical connections can cause high current arcing, which can cause personal injury and/or vehicle damage, including fire. Many electronic devices used in emergency vehicles can create or be affected by electromagnetic interference. Therefore, after installation of any electronic device it is necessary to test all electronic equipment simultaneously to insure that they operate free of interference from other components within the vehicle. Never power emergency warning equipment from the same circuit or share the same grounding circuit with radio communication equipment. All devices should be mounted in accordance with the manufacturer’s instructions and securely fastened to vehicle elements of sufficient strength to withstand the forces applied to the device. Driver and/or passenger air bags (SRS) will affect the way equipment should be mounted. This device should be mounted by permanent installation and within the zones specified by the vehicle manufacturer, if any. Any device mounted in the deployment area of an air bag will damage or reduce the effectiveness of the air bag and may damage or dislodge the device. Installer must be sure that this device, its mounting hardware and electrical supply wiring does not interfere with the air bag or the SRS wiring or sensors. Mounting the unit inside the vehicle by a method other than permanent installation is not recommended as unit may become dislodged during swerving; sudden braking or collision. Failure to follow instructions can result in personal injury. Whelen assumes no liability for any loss resulting from the use of this warning device. PROPER INSTALLATION COMBINED WITH OPERATOR TRAINING IN THE PROPER USE OF EMERGENCY WARNING DEVICES IS ESSENTIAL TO INSURE THE SAFETY OF EMERGENCY PERSONNEL AND THE PUBLIC.Warnings to UsersWhelen’s emergency vehicle warning devices are intended to alert other operators and pedestrians to the presence and operation of emergency vehicles and personnel. However, the use of this or any other Whelen emergency warning device does not guarantee that you will have the right-of-way or that other drivers and pedestrians will properly heed an emergency warning signal. Never assume you have the right-of-way. It is your responsibility to proceed safely before entering an intersection, driving against traffic, responding at a high rate of speed, or walking on or around traffic lanes. Emergency vehicle warning devices should be tested on a daily basis to ensure that they operate properly. When in actual use, the operator must ensure that both visual and audible warnings are not blocked by vehicle components (i.e.: open trunks or compartment doors), people, vehicles, or other obstructions. It is the user’s responsibility to understand and obey all laws regarding emergency warning devices. The user should be familiar with all applicable laws and regulations prior to the use of any emergency vehicle warning device. Whelen’s audible warning devices are designed to project sound in a forward direction away from the vehicle occupants. However, because sustained periodic exposure to loud sounds can cause hearing loss, all audible warning devices should be installed and operated in accordance with the standards established by the National Fire Protection Association.Safety FirstThis document provides all the necessary information to allow your Whelen product to be properly and safely installed. Before beginning the installation and/or operation of your new product, the installation technician and operator must read this manual completely. Important information is contained herein that could prevent serious injury or damage.WARNING: This product can expose you to chemicals including Methylene Chloride which is known to the State of California to cause cancer, and Bisphenol A, which is known to the State of California to cause birth defects or other reproductive harm. For more information go to .Installation Guide:Centurion™ Lightbar Option KitModel KROTAC (Center Rotator)51 Winthrop RoadChester, Connecticut 06412-0684Phone: (860) 526-9504Internet: Salese-mail:*******************CustomerServicee-mail:*******************®ENGINEERING COMPANY INC.Installation: Array 1.Remove the two Torx head screws that secure theend cap to the base. (Fig. 1)2.Slide the lens sections off the end of the base andremove the dividers to gain access to the lightbarbase (Fig. 2).Be sure to note the order the lenseswere installed on the lightbar.IMPORTANT:The lenses are seated very tightly intothe lens divider gaskets to prevent leaks. You will needto insert a screwdriver at each corner (between theblack endcap and aluminum base) and gently pry thelens out to break it free from the dividers. Pry each sideout a little at a time, alternating from one side to theother until the lens slides out easily. Before reassembling, apply a small amount of liquid dish detergent to the sides of the rubber gaskets to helpthem slide in easier and obtain a better seal.NOTE: If this is a replacement for an existing old style rotator, remove any remaining VHB adhesive tape (if present) from the base of the lightbar before proceeding (see page 3).3.Measure the base to locate the center point of thelightbar. Using this center mark, place the rotatorassembly on the base with the motor cradleoriented toward the front of the lightbar. Secure therotator assembly to the appropriate channel in thebase using the two flat washers and 3/8” hex headscrews provided (Pg. 3).4.Mount the 2 mirrors supplied as shown in theillustration. Note the mirror orientation as well asthe location and clearance dimensions. Secure themirrors using the 1/4” hex head screws provided. Wiring:1.Secure the ground lug for the rotator assembly tothe channel in the base using the internal toothlock washer and 1/4” hex head screw provided.2.Connect the ORANGE extension wire to the fastonconnector coming from the rotator assembly. Runthe input wire along the base as illustrated andconnect to the ORANGE wire (or any unused wire)in the lightbar wiring harness.3.Neatly dress and place any loose wires under thecable clamps in order to avoid interference withany moving parts.4.Replace and secure all domes.Page 2Page 3。
艾顿Moeller系列Rapid Link速控器产品说明书
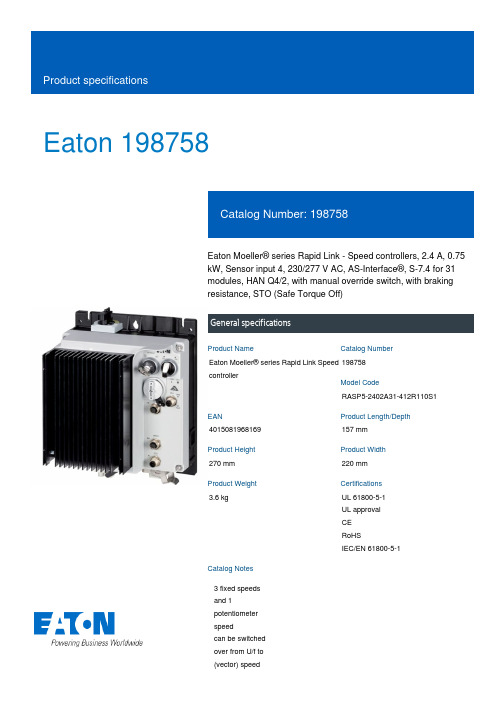
Eaton 198758Eaton Moeller® series Rapid Link - Speed controllers, 2.4 A, 0.75 kW, Sensor input 4, 230/277 V AC, AS-Interface®, S-7.4 for 31 modules, HAN Q4/2, with manual override switch, with braking resistance, STO (Safe Torque Off)General specificationsEaton Moeller® series Rapid Link Speed controller198758RASP5-2402A31-412R110S14015081968169157 mm 270 mm 220 mm 3.6 kgUL 61800-5-1 UL approval CE RoHSIEC/EN 61800-5-1Product NameCatalog NumberModel CodeEANProduct Length/Depth Product Height Product Width Product Weight Certifications Catalog Notes 3 fixed speeds and 1 potentiometer speedcan be switched over from U/f to (vector) speed480 V Is the panel builder's responsibility. The specifications for the switchgear must be observed.400 V AC, 3-phase 480 V AC, 3-phaseMeets the product standard's requirements.0.75 kW 500 VMeets the product standard's requirements.-40 °C380 V Control unit Key switch position AUTO Two sensor inputs through M12 sockets (max. 150 mA) for quick stop and interlocked manual operation Internal DC link IGBT inverter Breaking resistance Key switch position HAND PTC thermistor monitoring PC connectionSelector switch (Positions: REV - OFF - FWD) Braking resistanceThermo-click with safe isolation Manual override switch Key switch position OFF/RESET 0 HzMains voltage - max 10.11 Short-circuit rating Rated operational voltage 10.4 Clearances and creepage distances Output at quadratic load at rated output voltage - max Output voltage - max 10.2.3.1 Verification of thermal stability of enclosures Ambient storage temperature - min Mains voltage - min Fitted with:Output frequency - min control Connection of supply voltagevia adaptercable on round or flexiblebusbar junctionDiagnostics andreset on deviceand via AS-Interfaceintegrated PTC thermistor monitoring andThermoclick withsafe isolationoptional: 4 sensor inputs with M12-Yadapter for switchover to creep speedoptional: Fasterstop if external24 V fails Two sensor inputs through M12 sockets (max. 150 mA)for quick stop and interlocked manualoperationwith AUTO -OFF/RESET - HAND key switcheswith selectorswitch REV -OFF - FWD200 %, IH, max. starting current (High Overload), For 2 seconds every 20 seconds, Power section10 kA40 °CAS-Interface1 HP500 Hz8 kHz, 4 - 32 kHz adjustable, fPWM, Power section, Main circuitDiagnostics and reset on device and via AS-Interface Parameterization: FieldbusParameterization: drivesConnect mobile (App) Parameterization: drivesConnectParameterization: Keypad-10 °C≤ 0.6 A (max. 6 A for 120 ms), Actuator for external motor brakeDoes not apply, since the entire switchgear needs to be evaluated.2.4 ADoes not apply, since the entire switchgear needs to be evaluated.Does not apply, since the entire switchgear needs to be evaluated.Generation change from RA-MO to RAMO 4.0Connecting drives to generator suppliesGeneration change from RA-SP to RASP 4.0Generation Change RASP4 to RASP5Generation Change RA-SP to RASP5Electromagnetic compatibility (EMC)Configuration to Rockwell PLC for Rapid LinkGeneration change RAMO4 to RAMO5Rapid Link 5 - brochureDA-SW-drivesConnectDA-SW-USB Driver DX-COM-STICK3-KITDA-SW-drivesConnect USB Driver DX-COM-PCKITDA-SW-Driver DX-CBL-PC-3M0DA-SW-USB Driver PC Cable DX-CBL-PC-1M5DA-SW-drivesConnect - installation helpDA-SW-drivesConnect - InstallationshilfeMaterial handling applications - airports, warehouses and intra-logisticsProduct Range Catalog Drives EngineeringProduct Range Catalog Drives Engineering-ENDA-DC-00004184.pdfDA-DC-00004613.pdfDA-DC-00003964.pdfDA-DC-00004612.pdfeaton-bus-adapter-rapidlink-speed-controller-dimensions-003.eps eaton-bus-adapter-rapidlink-speed-controller-dimensions-002.eps eaton-bus-adapter-rapidlink-speed-controller-dimensions-005.eps eaton-bus-adapter-rapidlink-speed-controller-dimensions-004.epsETN.RASP5-2402A31-412R110S1.edzIL034085ZUStarting current - maxRated conditional short-circuit current (Iq)Ambient operating temperature - maxCommunication interfaceAssigned motor power at 115/120 V, 60 Hz, 1-phase Output frequency - maxSwitching frequencyFeaturesAmbient operating temperature - minBraking currentNumber of HW-interfaces (serial TTY)10.6 Incorporation of switching devices and components Nominal output current I2N10.2.6 Mechanical impact10.3 Degree of protection of assemblies Application notes BrochuresCatalogs Certification reports DrawingseCAD model Installation instructionsSpeed controllerC1: for conducted emissions onlyC2, C3: depending on the motor cable length, the connected load, and ambient conditions. External radio interference suppression filters (optional) may be necessary.0 W24 V DC (-15 %/+20 %, external via AS-Interface® plug) 230/277 V AC (external brake 50/60 Hz)1 HP120 %AS-Interface profile cable: S-7.4 for 31 modulesASIIs the panel builder's responsibility.IIINEMA 12IP6570 °C2000 VPlug type: HAN Q4/2At 40 °CFor 60 s every 600 s4-quadrant operation possible Rapid Link 5MZ040046_EN MN040003_EN MN034004ENrasp5_v26.stp ramo5_v26.dwgProduct categoryRadio interference classHeat dissipation capacity PdissRated control voltage (Uc)Assigned motor power at 460/480 V, 60 Hz, 3-phase Number of HW-interfaces (RS-422)Mains current distortionProtocol10.9.2 Power-frequency electric strength Overvoltage categoryDegree of protectionAmbient storage temperature - maxRated impulse withstand voltage (Uimp) ConnectionOverload currentFunctions Installation videos Manuals and user guidesmCAD model1 potentiometer speedSTO (Safe Torque Off)3 fixed speedsBrake chopper with braking resistance for dynamic brakingFor actuation of motors with mechanical brakeOutput at linear load at rated output voltage - max0.75 kWMains voltage tolerance380 - 480 V (-10 %/+10 %, at 50/60 Hz)Leakage current at ground IPE - max3.5 mAConverter typeU converter10.2.2 Corrosion resistanceMeets the product standard's requirements.Supply frequency50/60 Hz10.2.4 Resistance to ultra-violet (UV) radiationMeets the product standard's requirements.10.2.7 InscriptionsMeets the product standard's requirements.Shock resistance15 g, Mechanical, According to IEC/EN 60068-2-27, 11 ms, Half-sinusoidal shock 11 ms, 1000 shocks per shaftApplication in domestic and commercial area permittedYesNumber of inputs (analog)Number of phases (output)310.12 Electromagnetic compatibilityIs the panel builder's responsibility. The specifications for the switchgear must be observed.10.2.5 LiftingDoes not apply, since the entire switchgear needs to be evaluated.Number of HW-interfaces (RS-485)1Number of HW-interfaces (industrial ethernet)Efficiency97 % (η)System configuration typeCenter-point earthed star network (TN-S network)AC voltagePhase-earthed AC supply systems are not permitted.10.8 Connections for external conductorsIs the panel builder's responsibility.Switch-on threshold for the braking transistor765 VDCProtectionFinger and back-of-hand proof, Protection against direct contact (BGV A3, VBG4)Braking voltage230/277 V AC -15 % / +10 %, Actuator for external motor brakeApplication in industrial area permittedYesClimatic proofing< 95 %, no condensationIn accordance with IEC/EN 5017810.9.3 Impulse withstand voltageIs the panel builder's responsibility.Overload current IL at 150% overload3.6 AInput current ILN at 150% overload2.5 ANumber of HW-interfaces (RS-232)Number of inputs (digital)4Current limitationAdjustable, motor, main circuit0.2 - 2.4 A, motor, main circuitCable lengthC3 ≤ 25 m, maximum motor cable lengthC2 ≤ 5 m, maximum motor cable lengthC1≤ 1 m, maximum motor cable length10.5 Protection against electric shockDoes not apply, since the entire switchgear needs to be evaluated.Mounting positionVerticalMains switch-on frequencyMaximum of one time every 60 seconds10.13 Mechanical functionThe device meets the requirements, provided the information in the instruction leaflet (IL) is observed.10.9.4 Testing of enclosures made of insulating materialIs the panel builder's responsibility.Heat dissipation per pole, current-dependent Pvid0 WElectromagnetic compatibility1st and 2nd environments (according to EN 61800-3)Resolution0.1 Hz (Frequency resolution, setpoint value)Assigned motor power at 460/480 V, 60 Hz1 HPRelative symmetric net voltage tolerance10 %Rated operational current (Ie)2.4 A at 150% overload (at an operating frequency of 8 kHz and an ambient air temperature of +40 °C)Number of outputs (analog)Rated operational power at 380/400 V, 50 Hz, 3-phase0.75 kWNumber of HW-interfaces (USB)Operating modeU/f controlSynchronous reluctance motorsSensorless vector control (SLV)BLDC motorsPM and LSPM motorsRated frequency - min45 HzDelay time< 10 ms, On-delay< 10 ms, Off-delayNumber of outputs (digital)Power consumption32 W10.2.3.2 Verification of resistance of insulating materials to normal heatMeets the product standard's requirements.10.2.3.3 Resist. of insul. mat. to abnormal heat/fire by internal elect. effectsMeets the product standard's requirements.Number of HW-interfaces (other)1Rated frequency - max66 HzVibrationResistance: 57 Hz, Amplitude transition frequency on accelerationResistance: According to IEC/EN 60068-2-6Resistance: 10 - 150 Hz, Oscillation frequency Resistance: 6 Hz, Amplitude 0.15 mmShort-circuit protection (external output circuits)Type 1 coordination via the power bus' feeder unit, Main circuit10.7 Internal electrical circuits and connectionsIs the panel builder's responsibility.Braking torque≤ 30 % (I/Ie)Adjustable to 100 % (I/Ie), DC - Main circuitRelative symmetric net frequency tolerance10 %10.10 Temperature riseThe panel builder is responsible for the temperature rise calculation. Eaton will provide heat dissipation data for the devices.Number of HW-interfaces (parallel)Eaton Corporation plc Eaton House30 Pembroke Road Dublin 4, Ireland © 2023 Eaton. All Rights Reserved. Eaton is a registered trademark.All other trademarks areproperty of their respectiveowners./socialmedia1 HP Specification: S-7.4 (AS-Interface®)Number of slave addresses: 31 (AS-Interface®)Max. total power consumption from AS-Interface® power supply unit (30 V): 190 mA 327.5 W at 50% current and 90% speed 31.8 W at 100% current and 90% speed 33.5 W at 25% current and 50% speed 34.6 W at 50% current and 50% speed 35.1 W at 25% current and 0% speed 36.6 W at 100% current and 50% speed 36.8 W at 50% current and 0% speed 40.7 W at 100% current and 0% speed 0Max. 2000 mAbove 1000 m with 1 % performance reduction per 100 mAssigned motor power at 230/240 V, 60 Hz, 1-phase InterfacesNumber of phases (input)Heat dissipation at current/speed Number of interfaces (PROFINET)Altitude。
Roadranger RTLO-20918A-AS3 商品说明书
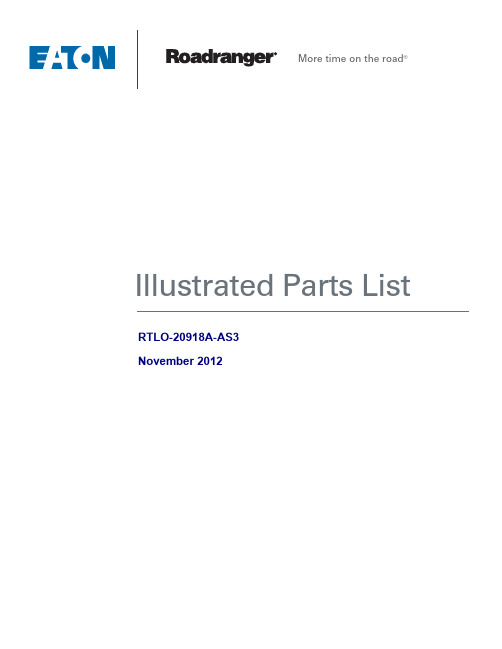
More time on the road®Illustrated Parts ListRTLO-20918A-AS3November 2012ContentsHow To Use The Illustrated Parts List (3)AFTERMARKET TRANSMISSIONS (4)AUXILIARY DRIVE GEAR (5)CASE (AUX) (7)CASE (FRONT) (8)CONTROLLER ECU & HARNESS (11)COUNTERSHAFT & BRGS(AUX) (12)COUNTERSHAFT ASSY (13)FILTER REGULATOR (15)HARNESS MOUNTING BRACKETS (16)HEAT EXCHANGER (18)INPUT SHAFT & DRIVE GEAR (19)INTEGRAL OIL PUMP (FORCED LUBE) (20)KITS & ASSEMBLIES (22)MAINSHAFT & SYNCHRO(AUX) (24)MAINSHAFT ASSY (26)MISCELLANEOUS (28)OIL COOLER (29)OIL FILTER (31)RANGE CYLINDER (33)REVERSE IDLER (35)SHIFT BAR HOUSING (37)SHIFT CONTROLS (39)SPLITTER CYLINDER (41)X-Y SHIFTER MODULE (43)2How To Use The Illustrated Parts ListThe information contained in this document is subject to frequent updates. Therefore, for the latest information available, please visit the interactive Electronic Parts Catalog at /epc.Model Designation or Nomenclature•For information regarding Model Designation and Nomenclature, visit .Kits and Assemblies (K/A's)•Kits and Assemblies contain groups of individual or assembled parts developed for optimal replacement or repair of a service problem.•Kits and Assemblies are shown with applicable parts groupings in the parts listings.Identifying Kits and AssembliesA- Part numbers beginning with the letter 'A' are pre-assembled Production AssembliesK- Part numbers beginning with the letter 'K' are kits that are not assembledS- Part numbers beginning with the letter 'S' are pre-assembled Service Assemblies•Note: Some Production Assemblies do not begin with a letter prefix (Midrange only).Illustrations•Illustrations show parts in assembly groups.•Item numbers on illustrations correspond with parts listings on pages adjacent to the illustration.•Notes are included on illustrations where additional information is needed.Parts ListingParts listings are defined by parts groupings and are broken down by service assemblies. Parts listings identify a part for servicing with the following categories•Item Number - corresponding with numbers on illlustrations for part identification.•Current Part - indentifies part as it is available for service.•Description - specifies part name or description.•Replaced Part - quantity quantity required for assembly.•Quantity - defines unique characteristics or requirements.•Notes - indicates Kits or Assemblies that contain a particular part.•Kits/Assy's Where Used3Group: AFTERMARKET TRANSMISSIONS AFTERMARKET TRANSMISSIONSItem CurrentPart Description ReplacedPartQty.Notes Kits/Assys WhereNeededTA-G19-12X RTLO-20918A-AS3 NEWSVC EXCH TRANS1WITH INTERNAL PUMP - NOCLUTCH HOUSINGTN-G19-12R RTLO-20918A-AS3REMAN TRANS1 WITH INTERNAL PUMPTN-G19-12X RTLO-20918A-AS3 NEWSVC EXCH TRANS1WITH INTERNAL PUMP - NOCLUTCH HOUSINGAutomated TransmissionAFTMKT 09A-12Generic Illustration - Not specific to part numbers listed below45Group: AUXILIARY DRIVE GEARAUXILIARY DRIVE GEARItemCurrent PartDescription Replaced Part Qty. NotesKits/Assys WhereNeeded 1 4304499 SPACER 125566510-BOXBEARING 5566510 1K-3512,K-35133 4304497 RETAINER 14 X-8-680 CAPSCREW 6 3/8"-16X1-1/2"5 4304500 SPACER 1 6691474AUXILIARY DRIVE GEAR17 4303185 WASHER 4300901 18 4301254 SNAP RING1K-3511,K-3512,K-35131234875610484-6-93Group: CASE (AUX)2511406-08-016CASE (AUX)Item CurrentPart Description ReplacedPartQty.Notes Kits/Assys WhereNeeded1 S-2501 SPEEDO ROTOR ASSY 4302242 1 MAGNETIC2 5568511 -O-RING 1 K-2918,S-2501,S-29133 K-2918 OIL SEAL KIT 4302322 4302323 1 "FOR MAGNETIC COVER" K-3512,K-35134 X-8-0801M CAPSCREW 3 M8 X 1.25 X 12MM5 S-2913 REAR BEARING COVERASSY 691637 ,4304651,430583316 1009551 GASKET - RED EDGEMOLDED 1RED EDGE MOLDED GASKET -UNCOMPRESSED THICKNESS.043 - .051 - NOTINTERCHANGEABLE WITH ANYOTHER GASKETK-2918,K-3509,S-29136 4302247 GASKET - PURPLE EDGEMOLDED 1NON EDGE MOLDED GASKET -UNCOMPRESSED THICKNESS -.013 - .018 - NOTINTERCHANGABLE WITH ANYOTHER GASKETK-2918,K-35097 X-8L-611 CAPSCREW 4 3/8"-16X3-1/4"7 X-8L-614 CAPSCREW 2 3/8"-16X2"8 X-8L-602 CAPSCREW 17 3/8"-16X1-1/2"8 X-8L-614 CAPSCREW 2 3/8"-16X2"9 4302320 COVER 21346 210 4305978 GASKET 4302246 2 K-3509,K-354711 K-2805 SHIM KIT 21452 K - 2106 1 K-3512,K-351312 14335 GASKET 1 K-350913 4303586 REARHOUSING 115 20815 LIFTINGEYE 17105 216 X-8L-604 CAPSCREW 8 3/8"-16X1-1/4" K-354723 K-3231 SPEED SENSOR KIT A - 6398 ,A - 6724 1 SINGLE PICK-UP (2 PIN)24 K-3523 SPEEDOPLUGKIT 4302707 225 4304653 SHIELD 1 S-291378Group: CASE (FRONT)CASE (FRONT)ItemCurrent PartDescription Replaced Part Qty. NotesKits/Assys WhereNeeded 1 S-3015 CASE ASSEMBLY 4305866 12 4304023 PLUG43037472 1-1/16" MAGNETIC, O-RINGINCLUDED3 A-7471 EXTENDED LUBE TUBEASSY 4305393 14 4305310 GASKET 4302810 1 K-35095 4302809 PTO COVER 16596 ,4300571 16X-8-725CAPSCREWX 8 72487/16"-14X7/8"7 4306584 CLUTCH HOUSINGGASKET 4304815,4305668 1K-3509,K-3671,K-4051 8 K-3671 FORCED LUBE CL HSGKIT A - 7148 1 #1 PULL IRON9 239614 SCREWX-8L-5094 5/16-18X.81 QUANTITYDEPENDENT ON DESIGN10 4305230 HAND HOLE COVER 11453 1#1 PULL10319E-05-0614Item CurrentPart Description ReplacedPartQty.Notes Kits/Assys WhereNeeded11 4306583 STUD 5966 612 X-10-1005 WASHER X 3 1000 ,X10 1000,X10 10046 1.23 X 6.60 K-405113 X-1-1012 HEXNUT X-1-1005 6 .625-18 K-405114 20550 FRONT BEARING COVER 1 2" PULL15 X-8L-604 CAPSCREW 6 3/8"-16X1-1/4" K-354716 20549 FRONT BEARING COVER 1 2" PUSH17 14311 GASKET 1 K-350918 12815 BUSHING 420 X-8C-830 HEX HEADSCREW/WASHER ASSYX-8C-826 4 .500-13 X 1.490 K-405120 X-8C-831 HEX HEADSCREW/WASHER ASSYX-8C-822 2 .500-13 X 3.460 K-405122 X-8-686 CAPSCREW 6 3/8"-16X3/4"23 14575 PTOCOVER 4302254 124 4305309 GASKET 1684 1 K-350927 14373 MAGNET 3 S-301528 18128 PIN 229 X-1-1012 HEXNUT 2 .625-18 K-405130 X-10-1005 WASHER X 3 1000 ,X10 1000,X10 10042 1.23 X 6.60 K-405131 14554 STUD 1632 ,6579 2 5/8" X 2-3/16"36 23104 PLUG 1712 237 X-8-1005 CAPSCREW 2 5/8"-11X1-1/4"38 20814 SPACER 239 X-12-802 PIPE PLUG X12 800 1 1/2"40 691447 PIN 1 S-301541 13835 -O-RING 242 13653 -O-RING 2 K-2803,K-2908,K-3510,K-400543 5568544 -O-RING 144 4305740 HEX HEAD PLUG 145 X-12-1212 PIPEPLUG 146 13834 -O-RING 1910CONTROLLER ECU & HARNESSItemCurrent PartDescription Replaced Part Qty. NotesKits/Assys WhereNeeded1 K-3736RX REMAN EXCH TRANSCONTROLLER KIT K-3736 12K-3681TRANS HARNESS KIT43059151 4 K-3682 RANGE/SPLITTER VALVEKIT 5561801 ,5561804 ,K - 2907 25 X-8-264 HEX FLANGE HEADSCREW X 8 2598 #10-24 X 1 1/46 K-2908-O- RING KIT1 FOR SOLENOID VALVE546Range Solenoid20322-10-0512COUNTERSHAFT & BRGS(AUX)ItemCurrent Part Description Replaced Part Qty. NotesKits/Assys WhereNeeded1 4301851-BOXBEARING 4301851 4K-3512,K-35132 A-6888 WELDEDCOUNTERSHAFT ASSY 2 C/S 4303143 - D/G 4304085 S/G43040873 4303124 SPACER210444-5/93 CS HelicalGroup: COUNTERSHAFT ASSY COUNTERSHAFT ASSYItem CurrentPart Description ReplacedPartQty.Notes Kits/Assys WhereNeeded1 4302082 SNAPRING 2 K-3511,K-3512,K-35132 4302712 BEARING 2 K-3512,K-35133 4304073 CNTRSHFT-W/REV & LO 24 X-6-E KEY 25 62511 ROLLPIN 26 4304840 KEY 19673 27 4304765 1ST GEAR-CNTRSHFT 4303702 ,4304520 28 4304518 2NDGEAR-CNTRSHFT 4303700 29 4303666 ODGEAR-CNTRSHFT 4304508,4304315 210 15953 PTO GEAR - LOWER 110 20840 PTO GEAR - UPPER 15952 111 4302666 DRIVEGEAR-CNTRSHFT 4303697,4304512 212 19198 SNAPRING 2 K-351113 4304599 BEARING 4302677, 4304598,43063322 K-3512,K-351314 4304605 RETAINER 19548 215 X-7-1005 CAPSCREW 2 5/8"-18X1-3/4"Group: FILTER REGULATORFILTER REGULATORItemCurrent Part Description Replaced Part Qty. NotesKits/Assys WhereNeeded 1 K-2170 FILTER REG KIT A - 5454 12 K-1698 -O- RING/ELEMENT KIT1 FOR FILTER REGULATOR 3X-8C-412CAPSCREWX 8S 412 21/4"-20X2-1/4"4 15114 -O- RING2K-2170,K-3365,K-3484,K-3510 5 X-12-208 PIPE PLUG 2 1/8" NPT 6 55505 HOSE ASSY 1 16" 7 12845 ELBOW1 1/8"K-336610131A-08-01CoverGroup: HARNESS MOUNTING BRACKETSHARNESS MOUNTING BRACKETSItemCurrent PartDescription Replaced Part Qty. NotesKits/Assys WhereNeeded1 4305801 STRAIN RELIEFBRACKET 12 4305870 NUT ASSEMBLY3 5/16-18 K-3734 3 4305919 NUT ASSEMBLY 3 (1/4-20) K-3734 4X-8-561BUTTON HEAD SCREW25/16 X 5/85 4305914 HARNESS BRACKET 16 K-3734 TRANS CONTROLLERMOUNTING KIT 17 4305871 WIRE BRACKET120323-07-06Latest DesignItem CurrentPart Description ReplacedPartQty.Notes Kits/Assys WhereNeeded8 4307036 HARNESS STRAPBRACKET19 K-4147 HARNESS CRADLEBRACKET KIT4306511 1Group: HEAT EXCHANGERHEAT EXCHANGERItemCurrent PartDescription Replaced Part Qty. NotesKits/Assys WhereNeeded 0 K-3902 MOUNTING BRACKET 4304665 1 NOT PICTURED0 X-8C-6111 SCREW2 3/8"-16X3/4" - NOT PICTURED,FOR MOUNTING BRACKET1 K-3956 HEAT EXCHANGER KIT 5586629 1 3/4" PORTS2 5588107 OIL HOSE ASSEMBLY 5586907 1 45.0" 35588108OIL HOSE ASSEMBLY5586908 152.0"4 17007 ELBOW 1 K-34415 4301123 ELBOW 1 K-34416 21425 STRAP2"A" Port"B" Port11525-11-04Group: INPUT SHAFT & DRIVE GEARINPUT SHAFT & DRIVE GEARItemCurrent Part Description Replaced Part Qty. NotesKits/Assys WhereNeeded 1 23559SEAL 1 NOT SOLD FOR SERVICE2 16980 SNAP RING1K-3511,K-3512,K-35133 81504 BEARING 1 K-3512,K-3513 4 16463 SPACER 15 14750 SNAP RING1K-3511,K-3512,K-3513 6 4304510 MAIN DRIVE GEAR 4303695 ,4304314 18 S-1659 INPUT SHAFT 20535 23566 ,4302661 1 2" PULL - USE W/FBC 20550 K-3513 8S-1660INPUT SHAFT20536 ,23567 12" PUSH - USE W/FBC 205499 16566 BUSHING1K-3512,S-1659,S-166010370-1/92 IS* For Shipping Only -- Do Not Replace*Group: INTEGRAL OIL PUMP (FORCED LUBE)INTEGRAL OIL PUMP (FORCED LUBE)Item CurrentPart Description ReplacedPartQty.Notes Kits/Assys WhereNeeded4 20823 PLUG 1Item CurrentPart Description ReplacedPartQty.Notes Kits/Assys WhereNeeded5 14765 -O-RING 1 K-3484,K-3510 6 K-4126 FASTENER KIT 20824, X-8-448 1 KIT CONTAINS 3 FASTENERS AND3 WASHERSK-33678 20825 DOWELPIN 19 4303773 RETAINER 110 K-3367 OIL PUMP KIT 4301829 ,4301948,4303776 ,4304529,4304572 A - 6963 ,A -7173111 K-3367 OIL PUMP KIT 4301829 ,4301948,4303776 ,4304529,4304572 A - 6963 ,A -7173112 20509 KEY 113 14853 SNAPRING 214 4303774 PUMP DRIVE GEAR 4304880 115 K-3367 OIL PUMP KIT 4301829 ,4301948,4303776 ,4304529,4304572 A - 6963 ,A -7173116 X-14-700 STEELBALL 1 7/16"17 4303775 SPRING 118 4305713 SUCTIONTUBE 4304628 1 O-RING INCLUDED ON SUCTIONTUBEK-336719 4304629 PLUG 121 X-8-686 CAPSCREW 2 3/8"-16X3/4"22 4305715 SPLITTER LUBE TUBE A - 7197 126 X-8-447 SCREW 227 20225 -O-RING 1999 K-3367 OIL PUMP KIT 4301829 ,4301948,4303776 ,4304529,4304572 A - 6963 ,A -71731KITS & ASSEMBLIESItem CurrentPart Description ReplacedPartQty.Notes Kits/Assys WhereNeededK-1698 -O- RING/ELEMENT KIT 1 FOR FILTER REGULATORK-1956 COOLER INSTLN KIT 1K-2170 FILTER REG KIT A - 5454 1K-2803 O-RING KIT - SPLITTER 1K-2805 SHIM KIT 21452 K - 2106 1 K-3512,K-3513 K-2908 -O- RING KIT 1 FOR SOLENOID VALVEK-2918 OIL SEAL KIT 4302322 4302323 1 "FOR MAGNETIC COVER" K-3512,K-3513 K-3231 SPEED SENSOR KIT 1K-3365 RANGE CYL COVER KIT 691442 1K-3366 SPLT CYL COVER KIT 691444 1K-3367 OIL PUMP KIT 4301829 ,4301948,4303776 ,4304529,4304572 A - 6963 ,A -71731K-3438 POSITION SENSOR KIT 691551 ,691926 1K-3441 OIL FILTER/ADAPTERKITA - 7174 1K-3484 O-RING KIT - RANGE 1K-3492 SYNCHRONIZER KIT K - 2446 1K-3497 SYNCHRONIZERREPLACEMENT KIT K - 3200 1 SLIDING CLUTCH INCLUDED INKITK-3509 GASKETKIT 1 K-3512,K-3513 K-3510 O-RING KIT - COMPLETE 1 K-3512,K-3513K-3511 SMALLPARTSKIT 1K-3512 BASIC REBUILD KIT 1K-3513 BASIC OVERHAUL KIT 1K-3523 SPEEDOPLUGKIT 4302707 1K-3671 FORCED LUBE CL HSGKITA - 7148 1 #1 PULL IRONK-3681 TRANS HARNESS KIT 4305915 1K-3682 RANGE/SPLITTER VALVEKIT 5561801 ,5561804 ,K -29071K-3734 TRANS CONTROLLERMOUNTING KIT1Item CurrentPart Description ReplacedPartQty.Notes Kits/Assys WhereNeededK-3736RXREMAN EXCH TRANSCONTROLLER KITK-3736 1K-3784RXREMAN EXCH GEN 3 X-YSHIFTER KIT A - 7670,K-3665,K-37841K-3979 SPACERKIT 1 INCLUDES (4) SPACERMOUNTING SCREWSK-3980 COBRA SHIFT LEVER KIT(RHO) K-3680 1(LEFT HAND DRIVE), ALSOKNOWN AS (RHO) RIGHT HANDOPERATIONK-3997 COBRA SHIFT LEVER KIT(RHO) W/MACK SWINGARM A - 7181,K-3680 1 (LEFT HAND DRIVE), ALSOKNOWN AS (RHO) RIGHT HANDOPERATION - FOR UNITS USINGTHE MACK 10MY559M SWINGARM BRACKETK-4005 SPLITTER CYLINDERREPAIR KIT1K-4051 RT CLUTCH HOUSINGSERVICE KIT1S-1404 OILFILTER 17238 1S-1659 INPUT SHAFT 20535 23566 ,4302661 1 2" PULL - USE W/FBC 20550 K-3513 S-1660 INPUT SHAFT 20536 ,23567 1 2" PUSH - USE W/FBC 20549S-2501 SPEEDO ROTOR ASSY 4302242 1 MAGNETICS-2913 REAR BEARING COVERASSY 691637 ,4304651,43058331S-3015 CASEASSEMBLY 4305866 1S-3021 SHIFT BAR HOUSINGASSY 4305895 1COMPLETES-3022 SHIFT BAR HOUSINGASSY 4305895 1HOUSINGONLYS-3108 MAINSHAFTASSY 4302658 ,4303403 ,S -2268,S-25601Group: MAINSHAFT & SYNCHRO(AUX) MAINSHAFT & SYNCHRO(AUX)Item CurrentPart Description ReplacedPartQty.Notes Kits/Assys WhereNeeded1 691934 SLIDING CLUTCH-SPLITTER4303822 12 X-7-1007 SCREW 1 5/8"-18X1-3/4"3 4301843 RETAINER 14 691473 SPLITTERGEAR 15 4300902-BOXTAPERED ROLLER BRG 4300902 1 K-3512,K-35136 4301844 BEARINGSLEEVE 18 4303424 SNAPRING 1 K-3511,K-3512,K-35139 14897 SPRING 3 K-3492,K-3497,K-3511,K-3512,K-351310 A-7331 SYNCHRONIZERASSY 4304396 4304397 A -5917 1 HIRANGE K-3492,K-349710438A-08-01Item CurrentPart Description ReplacedPartQty.Notes Kits/Assys WhereNeeded11 4301840 SLIDINGCLUTCH 4303386 1 K-349712 A-7254 SYNCHRONIZERASSEMBLYA - 4937 A - 5876 1 LO RANGE K-3492,K-349713 4303705 MAINSHAFT 114 4301842 WASHER 115 4301795 REDUCTIONGEAR 4301794 116 4300912 SPACER 117 5556503-BOX BEARING 55565031 K-3512,K-351319 K-4122 HEX FLANGE CRIMPEDNUT KIT4302321,4306520 1 K-3511Group: MAINSHAFT ASSYMAINSHAFT ASSYItemCurrent PartDescription Replaced Part Qty. NotesKits/Assys WhereNeeded 1 S-3108 MAINSHAFT ASSY4302658 ,4303403 ,S -2268,S-2560 12 62504 ROLL PIN 1 S-31083 4304615 3-SIDED KEY 4300120 14 14750 SNAP RING1K-3511,K-3512,K-35135 23653 REVERSE GEAR-MAINSHAFT 16 4302047 SPACER1 K-3511 7 4305997 SLIDING CLUTCH43014072 8 4303412 LO GEAR-MAINSHAFT 4303410 1 9 4303603 WASHER43023972 K-3511 10 4303701 1ST GEAR-MAINSHAFT 1 11 4304516 2ND GEAR-MAINSHAFT 4303699 1 12 4304514 OD GEAR-MAINSHAFT 4302664 ,4303698110337B-10-96Item CurrentPart Description ReplacedPartQty.Notes Kits/Assys WhereNeeded,430431613 4300382 WASHER.249-WHITE 1 K-351114 4302398 WASHER 4 K-351115 4305996 SLIDINGCLUTCH 691922 1 K-3513MISCELLANEOUSItem CurrentPart Description ReplacedPartQty.Notes Kits/Assys WhereNeeded5586260 SHIFT DIAGRAM LABEL 171203 SILICONE LUBE 1 8 OZ (236.59 CC)-FLEET SIZE71204 ADHESIVESEALANT 1 0.5 CC (SINGLE APPLICATIONSIZE)71205 SEALANT 1 2 CC (SINGLE APPLICATION SIZE) K-351371206 SILICONE LUBE 1 4 CC (SINGLE APPLICATION SIZE) K-2803,K-3484,K-3510,K-4005Group: OIL COOLEROIL COOLERItemCurrent PartDescription Replaced Part Qty. NotesKits/Assys WhereNeeded 1 18025 OIL COOLER 1 K-1956 2 19424 HOSE 1 25 FEET K-1956 3 X-8-535 CAPSCREW 2 5/16"-16X2-1/2" 4 X-3-506 LOCKWASHER 2 5/16" 5 18211 BRACKET 4 K-1956 6 19419 CONNECTOR6K-1956,K-3441,K-3547,S-1404 7 19415 SWIVEL 4 K-1956 8 X-10-501 WASHER2 5/16" 9 18209 PLUG-RUBBER MOUNT 2 K-1956 10 17190 STRAP 8 K-1956 11 19423 CLAMP 5 K-1956 12 18210NUT2K-1956*Adding Oil Filter and parts as shown is optional.Return / Outlet Location10525-4/92 CoolerItem CurrentPart Description ReplacedPartQty.Notes Kits/Assys WhereNeeded13 19422 ELBOW 4 K-195614 S-1404 OILFILTER 17238 115 17237 FILTERELEMENT 1 S-1404Group: OIL FILTEROIL FILTERItemCurrent PartDescription Replaced Part Qty. NotesKits/Assys WhereNeeded1 19419 CONNECTOR 1K-1956,K-3441,K-3547,S-1404 2 X-8-453 SCREW 4 K-3441 3 X-8-452 SCREW 1 K-3441 4 4304820 GASKET 1 K-3441 5 4301123 ELBOW1 K-3441 6 K-3441 OIL FILTER/ADAPTERKIT A - 7174174304827OIL FILTER ELEMENT1 K-3441,K-3547 8 17007 ELBOW1K-34419 K-3441 OIL FILTER/ADAPTERKIT 110 A-7300 AUX COUNTERSHAFTCOVER ASSY 1 K-354711 K-3547OIL FILTER COVER KIT1 CONTAINS A-730010539-3-00312427265891011Oil Filter Cover Kit (not pictured)- Contained in Item #11Group: RANGE CYLINDERRANGE CYLINDERItemCurrent PartDescription Replaced Part Qty. NotesKits/Assys WhereNeeded1 14347 GASKET 1K-3484,K-3509,K-3510 2 22823 SHIFT YOKE 16775 1 3 X-7-809 BOLTX 7 810 ,X 7 811 2 1/2"-20X1-3/4" 4A-6690RANGE CYLINDER ASSY4303595 16 14765 -O- RING 1 K-3484,K-35107 4303596 YOKE BAR 18 14341 PISTON 23353 19 14345 -O- RING 1 K-3484,K-3510 10 14344-O- RING1K-3484,K-351012461-08-01Item CurrentPart Description ReplacedPartQty.Notes Kits/Assys WhereNeeded11 X-1-1010 NUT 1 5/8"-1812 691955 GASKET 691440 1 K-3365,K-3484,K-3509,K-351013 K-3365 RANGE CYL COVER KIT 691442 114 X-8L-636 CAPSCREW 2 3/8"-16X3-3/4"15 X-12-208 PIPE PLUG 3 1/8" NPT16 X-8L-607 CAPSCREW 2 3/8"-16X2-1/4"17 K-2908 -O- RING KIT 1 FOR SOLENOID VALVE18 X-8-264 HEX FLANGE HEADSCREWX 8 259 4 #10-24 X 1 1/419 K-3682 RANGE/SPLITTER VALVEKIT 5561801 ,5561804 ,K -29071Group: REVERSE IDLERREVERSE IDLERItemCurrent PartDescription Replaced Part Qty. NotesKits/Assys WhereNeeded 3 4302982 WASHER 14282 44 14287 BEARING 4305020 2 K-3512,K-3513 516757REVERSE IDLER GEAR22409 28 4303336 RETAINING RING 4 9 4305513 IDLER SHAFT211382A-10-04Group: SHIFT BAR HOUSING99920237-10-05SHIFT BAR HOUSINGItem CurrentPart Description ReplacedPartQty.Notes Kits/Assys WhereNeeded1 S-3022 SHIFT BAR HOUSINGASSY 4305895 1HOUSINGONLY2 4302676 GASKET 14918 1 K-3509,S-3021,S-30225 20332 AIR VALVE SHAFT 17177 1 S-30217 X-12-603 PIPE PLUG X12 602 1 3/8" NPT10 21966 PLUNGER 111 4301372 SPRING 112 17179 GASKET 1 S-3021,S-302213 4303655 PLUG 17178 1 S-3021,S-302214 22941 NEUTRAL LIGHT SWITCH 12639 1 SWITCH NORMALLY CLOSED15 20815 LIFTINGEYE 17105 216 X-8L-602 CAPSCREW 5 3/8"-16X1-1/2"- TWO FOR LIFTINGEYES, 2 FOR HARNESS BRACKETAND 1 FOR STRAIN RELIEF VALVE16 X-8L-604 CAPSCREW 8 3/8"-16X1-1/4" K-354717 15899 PIN 218 15900 GASKET 2 S-3021,S-302219 22940 REVERSE LIGHTSWITCH 16830 1SWITCHNORMALLYOPEN20 4303656 PLUG 15917 1 S-3021,S-302221 691661 COMPRESSIONSPRING 3 K-3511,K-3513,S-302122 X-14-800 STEELBALL 3 1/2"23 691712 SHIFTYOKE 4301376 1 REVERSE/1ST S-302124 X-14-1200 STEELBALL 2 3/4"25 14658 SHIFTBLOCK 1 2ND/3RD S-302126 3220 LOCKSCREW 5 S-302127 1634 INTERLOCKPIN 1 K-3511,S-3021 28 14659 SHIFTBLOCK 1 4TH/5TH S-302129 691601 SHIFTYOKE 4302212 1 4TH/5TH S-302130 4301366 YOKEBAR 1 4TH/5TH S-302131 691600 SHIFTYOKE 4302994 1 2ND/3RD S-302132 4301365 YOKEBAR 1 2ND/3RD S-3021Item CurrentPart Description ReplacedPartQty.Notes Kits/Assys WhereNeeded33 4301364 YOKEBAR 1 REVERSE/1ST S-302134 K-3231 SPEED SENSOR KIT A - 6398 ,A - 6724 2 SINGLE PICK-UP (2 PIN)35 14142 -O-RING 2 S-302136 X-8C-409 CAPSCREW 2 1/4"-20X5/8"37 4303656 PLUG 15917 3 S-3021,S-302238 15900 GASKET 3 S-3021,S-302239 4305869 SCREW 3/8 & 5/16 3 USED FOR MOUNTING ECU40 4305870 NUTASSEMBLY 3 5/16-18, USED FOR MOUNTINGECUK-3734999 S-3021 SHIFT BAR HOUSINGASSY 4305895 1COMPLETEGroup: SHIFT CONTROLSSHIFT CONTROLSItemCurrent Part Description Replaced Part Qty. NotesKits/Assys WhereNeeded 1 4306043PUSHBUTTON ASSY A - 7466,S-3007 12 K-3997 COBRA SHIFT LEVER KIT(RHO) W/MACK SWING ARM4305447,K-3680 1 (LEFT HAND DRIVE), ALSOKNOWN AS (RHO) RIGHT HAND OPERATION - FOR UNITS USING THE MACK 10MY559M SWING ARM BRACKET3 5505111 SHIFT LEVER KNOBDECAL 14 5505110 SHIFT LEVER POSITIONSTRIP 15 K-3980 COBRA SHIFT LEVER KIT(RHO)K-3680 1 (LEFT HAND DRIVE), ALSOKNOWN AS (RHO) RIGHT HAND OPERATION6 A-7982 JUMPER HARNESSASSY110209-06-09VOLUME CONTROLSERVICESHIFTMANUALLOWEATON FULLER TRANSMISSIONSDN R 1PUSHBUTTON ASSEMBLYCOBRA LEVER - only for 243COBRA LEVER - Latest Design - for all use with 10MY559M Mack Swing Arm Bracket567applications with the exception of units using the 10MY559M Mack Swing Arm Bracket (see illustration to the left)Indicates part of Item 5Item CurrentPart Description ReplacedPartQty.Notes Kits/Assys WhereNeeded7 K-3979 SPACERKIT 1 INCLUDES (4) SPACERMOUNTING SCREWSGroup: SPLITTER CYLINDERSPLITTER CYLINDERItemCurrent Part Description Replaced Part Qty. NotesKits/Assys WhereNeeded 1 A-7012SPLITTER YOKE ASSY A - 6304 ,A - 6892 12 4303583 GASKET1K-2803,K-3509,K-3510,K-4005 3 4306632 SPLITTER CYLINDER 1 K-4005 3 K-4005 SPLITTER CYLINDERREPAIR KIT 43035821COMPLETE REPAIR KIT4 21208 -O- RING1K-2803,K-3510,K-4005 5 4306631 PISTON 4301964 1 K-4005 6 13653 -O- RING1K-2803,K-2908,K-3510,K-4005 7 X-1-805 NUT 1 K-4005 8 21209 -O- RING1K-2803,K-3510,K-40059 17073 GASKET 1K-2803,K-3366,K-3509,K-3510,K-4005 10 K-3366 SPLT CYL COVER KIT 691444 111X-12-208PIPE PLUG31/8" NPT12462-08-01Item CurrentPart Description ReplacedPartQty.Notes Kits/Assys WhereNeeded12 X-8L-540 CAPSCREW 4 5/16"-18X1-7/8"13 K-2908 -O- RING KIT 1 FOR SOLENOID VALVE14 X-8-264 HEX FLANGE HEADSCREWX 8 259 4 #10-24 X 1 1/415 K-3682 RANGE/SPLITTER VALVEKIT 5561801 ,5561804 ,K -29071999 K-3366 SPLT CYL COVER KIT 691444 1Group: X-Y SHIFTER MODULEX-Y SHIFTER MODULEItemCurrent PartDescription Replaced Part Qty. NotesKits/Assys WhereNeeded 1 K-3784RX REMAN EXCH GEN 3 X-YSHIFTER KIT A - 7670,K-3665,K-378412 4305452 GASKET 4301958 1 K-4009 3K-3438POSITION SENSOR KIT691551 ,691926 24 X-8C-615 CAPSCREW 45 4304602 BREATHER 23605 1 1/4" NPT 7 K-4009XY SHIFTER REPAIR KIT121320230-09-01457 XY Shifter Repair Kit。
Dali Model 6 用户指南说明书
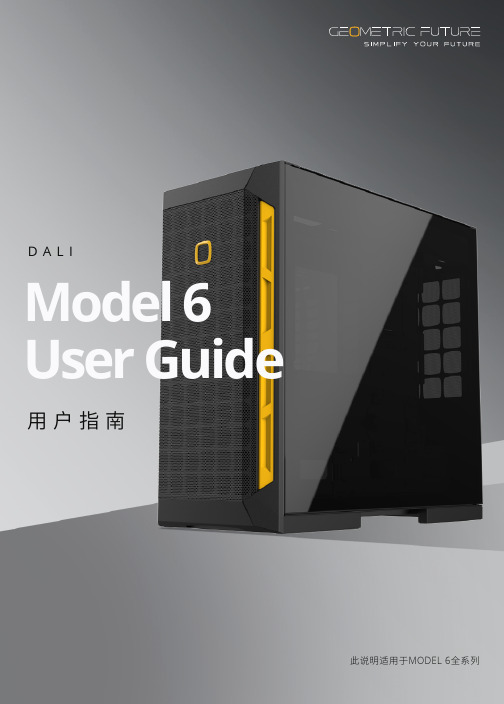
D A L I 用户指南简约游戏风格造型Modle 6 User GuideCONTENTS产品目录Mount the top fan/water cooler04050608101213161819202425拆除侧板及顶盖Remove side panels and top panel 安装主板I/O挡片Install the motherboard I/O baffle安装主板Install the motherboard 安装显卡Install the graphics card侧装显卡Side-mounted graphics card风扇及水冷安装选项Fan and water cooling mounting options安装底部风扇/水冷模组安装前部风扇/水冷Mount the front fan/water coolerMount the bottom fan/water cooler安装顶部风扇/水冷锁装电源安装硬盘Install the power cord线材整理绑线位置装回侧板与顶盖Install hard driveCable management & routingPut back the end panel and top panel01产品规格Specifications 02产品特点Feature26前置I/O接线示意Front I/O wiring schematic, provided for premium cases27注意事项Precautions28保修范围Warranty零件包内容03Parts Kit Includes04安装步骤How to assembleModle 6 User GuideSPECIFICATIONS产品规格CPU HeatsinkHeight < 162mm01Model Case Type MaterialProduct Dimension ( H x W x D )Drive Bay M/B Form Factor Power Supply I/O PortsExpansion Slots ( Maximum Space )Thermal SolutionMid TowerSteel T0.8 ,Tempered Glass T4.0450 x 215 x 450 mm 17.7“ x 8.5” x 17.7”Max :4 x 3.5”/2.5“ trayE-ATX (12” x 11”), ATX , Micro - ATX , Mini - ITX PSII :ATX 12V (Length < 180 mm )USB 3.0 x 2 , HD Audio (CTIA-SPK/MIC)PCI-E x 7:Length <350mm (No Cooling of bottom ) / Width <165mm Lateral PCI-E x 2:Length <360mm (No Cooling of bottom ) / Width <165mm / Height<54mmTop :120mm Fan x 1 120mm RadiatorFront :120mm Fan x 3 / 140mm Fan x 2240/280mm Radiator ( Length < 361mm / Thickness is related to the height limit of the main board ) Bottom :120/140mm Fan x 3360/280mm Radiator ( Length < 440mm )6Modle 6 User GuideFEATURE产品特点Excellent Heat DissipationSuperior CompatibilityEasy AccessPersonalized Installation Durable Materials 12" x 11" motherboard / 7 x fan mounts / dual 360/420mm water cooling mounts / cpu cooler height: 162mm / rtx™ 30series graphics card space: 360mm (l) x 165mm (w) x 61mm (h) / up to 4 hard drive bracketsRemovable & cleanable top panel / multifunctional hard drive bracket / removable & cleanable magnetic filterIndeformable vertically mounted graphics card /large cable routing spaceT0.8mm coated steel / t4.0mm tempered glassMinimalist Style Perfect Handfeel 极致触感航空针织面料 / 细软麻料 …极简视效扎实用料安装可靠度便捷操作超强兼容性优秀散热全面屏双侧透 / 全面网顶盖全烤漆钢板 T0.8mm / 全钢化玻璃 T4.0mm竖装显卡无形变 / 超大背线空间/电源双向换装可拆洗顶盖 / 多功能硬盘架 / 可拆洗磁吸滤网主板 12”x 11”/ 7组风扇位 / 360+240双水冷 / CPU散热器高162mm / 30系大显卡兼容空间 长360 x 宽165 x 厚61mm / 最多4组硬盘位垂直三面风道 / 全面网高通风率顶盖 / 电源风道优化Glass panels on two sides / meshy top panelAerospace-grade knitted fabric / soft fine linen...Vertical airflow/ full ventilation on three sides/ fast-ventilating meshy top panel / optimized零件包内容安装主板I/O挡片1PH2拧松侧板螺丝 / 并依箭头指示方向拆除两侧板依箭头指示方向拆除顶盖Loosen end panel screwsRemove both side panels and top panel in the direction indicated by arrows钢化玻璃拆装注意轻拿轻放!Modle 6 User GuideHOW TO ASSEMBLE安装步骤安装主板I/O挡片2Install the motherboard I/O baffle3主板孔位对照表ITXMicro—ATX ATX E-ATXI A M EEI / M / A / EM / A / EEM M A / E A / E E Motherboard mounting hole locations table3PH2X 9X 9X 14PH2拆显卡封条PH24锁装显卡Step 25侧装显卡( 显卡转接板组需另购 )PH2Side-mounted graphics card (graphics card adapter board needs to be purchased separately)拆显卡封条Remove the card seal sticker Step 1PH2x2侧装显卡( 显卡转接板组需另购 )Side-mounted graphics card (graphics card adapter board needs to be purchased separately)5锁装显卡Step 26PH2( 尺寸限制参照产品规格表描述 )360120280240140120120风扇X3280240140120(refer to product specifications for size limitation)Modle 6 User Guide HOW TO ASSEMBLE 安装步骤7安装底部风扇/水冷模组PH2Step 1 拆取底部磁吸滤网Mount rear panel 120/240/360 water cooler Remove water cooler bracket and bottom magnetic suction filter screenPH2Step 2 锁装风扇/水冷模组于机箱内(螺丝由风扇/水冷产品提供)Mount the water cooler bracket and radiator.Step 3 装回底部磁吸滤网Mount the water cooler bracket and radiator.88安装前部风扇/水冷拆取前置面板Mount the top fan/water cooler Step 1Remove the front glass panel PH2PH2安装前板风扇/水冷Step 2Install the front panel fan/water-cooling module 装回前置面板Step 39PH2X 410(最多支持4组硬盘位 / 不同机种标配硬盘支架数量不等)11PH2手拧螺丝 / 拆取硬盘支架Screw by hand / Remove the hard drive bracketPH2 11锁装2.5”HDD3.5”HDD3.5”HDD2.5”HDD2.5”HDDPH2X 8Mount the 2.5”HDD锁装3.5”HDD支架锁装硬盘支持多个方向选择3.5”HDD 2.5”HDD 2.5”HDD2.5”HDD3.5”HDD PH2X 811Hard drive may be installed in several directions Mount the 3.5”HDD硬盘安装完成示意图11Schematic diagram of hard drive installation12虚线为线材路径 黄色块为扎线位置where dotted line is wire routing and yellow block is cable bundle position13PH2Modle 6 User Guide FRONT I/O WIRING SCHEMATIC 前置I/O接线示意PH2POWER SW RESET SWHDD LED POWER LED HD AUDIO TYPE-C( 高阶版标配 ) (Provided For Premium Cases )USB 3.0Modle 6 User GuidePRECAUTIONS 注意事项注意事项1.请严格依照本使用手册所示步骤进行安装。
艾顿Moeller系列快速链接DOL电机启动器说明说明书

Eaton 198520Eaton Moeller® series Rapid Link - DOL starter, 6.6 A, Sensor input 2, 230/277 V AC, AS-Interface®, S-7.4 for 31 modules, HAN Q5, with manual override switchGeneral specificationsEaton Moeller® series Rapid Link DOL starter1985204015081963959RAMO5-D202A31-512RS1120 mm 270 mm 220 mm 1.8 kgCCC CE RoHS UL 60947-4-2 UL approval IEC/EN 60947-4-2Assigned motor rating: for normal internally and externally ventilated 4 pole, three-phase asynchronous motors with 1500 rpm at 50 Hz or 1800 min at 60 HzProduct NameCatalog NumberEANModel CodeProduct Length/Depth Product Height Product Width Product Weight Certifications Catalog NotesParameterization: FieldbusParameterization: KeypadDiagnostics and reset on device and via AS-Interface Parameterization: drivesConnectParameterization: drivesConnect mobile (App)Key switch position AUTOKey switch position HANDManual override switchShort-circuit releaseThermo-clickElectronic motor protectionKey switch position OFF/RESETThermistor monitoring PTCTwo sensor inputs through M12 sockets (max. 150 mA) for quick stop and interlocked manual operationExternal reset possibleFor actuation of motors with mechanical brakeTemperature compensated overload protection CLASS 10 AIP65NEMA 12Class A10,000,000 Operations (at AC-3)10,000,000 Operations (at AC-3)Direct starter0.3 A6.6 AIIIMotor starterAS-Interface profile cable: S-7.4 for 31 modulesASI4000 VPhase-earthed AC supply systems are not permitted. AC voltageCenter-point earthed star network (TN-S network) DOL starterDCFeatures Fitted with: Functions ClassDegree of protectionElectromagnetic compatibility Lifespan, electricalLifespan, mechanicalModelOverload release current setting - min Overload release current setting - max Overvoltage categoryProduct categoryProtocolRated impulse withstand voltage (Uimp) System configuration typeTypeVoltage typeVertical15 g, Mechanical, According to IEC/EN 60068-2-27, 11 ms, Half-sinusoidal shock 11 ms, 1000 shocks per shaftResistance: 10 - 150 Hz, Oscillation frequencyResistance: According to IEC/EN 60068-2-6Resistance: 6 Hz, Amplitude 0.15 mmResistance: 57 Hz, Amplitude transition frequency on acceleration Max. 2000 mAbove 1000 m with 1 % performance reduction per 100 m Max. 1000 m-10 °C55 °C-40 °C70 °CIn accordance with IEC/EN 50178< 95 %, no condensation0.3 - 6.6 A, motor, main circuit Adjustable, motor, main circuit6.6 A (at 150 % Overload)Maximum of one time every 60 seconds380 - 480 V (-15 %/+10 %, at 50/60 Hz)20 - 35 ms20 - 35 ms50/60 HzAC-53a 3 HP≤ 0.6 A (max. 6 A for 120 ms), Actuator for external motor brake230/277 V AC -15 % / +10 %, Actuator for external motor brake10 kA0 AType 1 coordination via the power bus' feeder unit, Main circuitMounting position Shock resistance Vibration AltitudeAmbient operating temperature - min Ambient operating temperature - max Ambient storage temperature - min Ambient storage temperature - max Climatic proofingCurrent limitationInput currentMains switch-on frequency Mains voltage tolerance Off-delayOn-delayOutput frequency Overload cycleRated frequency - min Assigned motor power at 460/480 V, 60 Hz, 3-phaseBraking currentBraking voltageRated conditional short-circuit current (Iq)Rated conditional short-circuit current (Iq), type 2, 380 V, 400 V, 415 VShort-circuit protection (external output circuits)47 Hz63 Hz6.6 A6.6 A6.6 A0.09 kW3 kW0 kW3 kW480 V AC, 3-phase 400 V AC, 3-phase 50/60 Hz, fLN, Main circuit Phase-earthed AC supply systems are not permitted. AC voltageCenter-point earthed star network (TN-S network)0 V0 V0 V0 V0 V0 V24 V DC (-15 %/+20 %, external via AS-Interface® plug) 230/277 V AC (external brake 50/60 Hz)Connections pluggable in power section Specification: S-7.4 (AS-Interface®)Number of slave addresses: 31 (AS-Interface®)Max. total power consumption from AS-Interface® power supply unit (30 V): 190 mA10 m, Radio interference level, maximum motor cable lengthMeets the product standard's requirements.Meets the product standard's requirements.Rated frequency - max Rated operational current (Ie)Rated operational current (Ie) at 150% overload Rated operational current (Ie) at AC-3, 380 V, 400 V, 415 V Rated operational power at 380/400 V, 50 Hz - min Rated operational power at 380/400 V, 50 Hz - max Rated operational power at AC-3, 220/230 V, 50 Hz Rated operational power at AC-3, 380/400 V, 50 Hz Rated operational voltage Supply frequencySystem configuration typeRated control supply voltage (Us) at AC, 50 Hz - min Rated control supply voltage (Us) at AC, 50 Hz - max Rated control supply voltage (Us) at AC, 60 Hz - min Rated control supply voltage (Us) at AC, 60 Hz - max Rated control supply voltage (Us) at DC - min Rated control supply voltage (Us) at DC - max Rated control voltage (Uc)ConnectionInterfacesNumber of auxiliary contacts (normally closed contacts)Number of auxiliary contacts (normally open contacts)Cable length10.2.2 Corrosion resistance10.2.3.1 Verification of thermal stability of enclosuresMeets the product standard's requirements.Meets the product standard's requirements.Meets the product standard's requirements.Does not apply, since the entire switchgear needs to be evaluated.Does not apply, since the entire switchgear needs to be evaluated.Meets the product standard's requirements.Does not apply, since the entire switchgear needs to be evaluated.Meets the product standard's requirements.Does not apply, since the entire switchgear needs to be evaluated.Does not apply, since the entire switchgear needs to be evaluated.Is the panel builder's responsibility.Is the panel builder's responsibility.Is the panel builder's responsibility.Is the panel builder's responsibility.Is the panel builder's responsibility.The panel builder is responsible for the temperature rise Generation change from RA-SP to RASP 4.0Connecting drives to generator suppliesGeneration change RAMO4 to RAMO5Generation change from RA-MO to RAMO 4.0Generation Change RASP4 to RASP5Configuration to Rockwell PLC for Rapid LinkElectromagnetic compatibility (EMC)Generation Change RA-SP to RASP5Rapid Link 5 - brochureDA-SW-USB Driver DX-COM-STICK3-KITDA-SW-drivesConnectDA-SW-drivesConnect - installation helpDA-SW-USB Driver PC Cable DX-CBL-PC-1M5DA-SW-Driver DX-CBL-PC-3M0DA-SW-drivesConnect USB Driver DX-COM-PCKITDA-SW-drivesConnect - InstallationshilfeMaterial handling applications - airports, warehouses and intra-logisticsProduct Range Catalog Drives EngineeringDA-DC-00004184.pdfDA-DC-00004525.pdfDA-DC-00003964.pdfDA-DC-00004523.pdfeaton-bus-adapter-rapidlink-reversing-starter-dimensions-002.eps eaton-bus-adapter-rapidlink-reversing-starter-dimensions-003.eps eaton-bus-adapter-rapidlink-speed-controller-dimensions-003.eps eaton-bus-adapter-rapidlink-speed-controller-dimensions-002.epsETN.RAMO5-D202A31-512RS1.edzIL034084ZU10.2.3.2 Verification of resistance of insulating materials to normal heat10.2.3.3 Resist. of insul. mat. to abnormal heat/fire by internal elect. effects10.2.4 Resistance to ultra-violet (UV) radiation10.2.5 Lifting10.2.6 Mechanical impact10.2.7 Inscriptions10.3 Degree of protection of assemblies10.4 Clearances and creepage distances10.5 Protection against electric shock10.6 Incorporation of switching devices and components10.7 Internal electrical circuits and connections10.8 Connections for external conductors10.9.2 Power-frequency electric strength10.9.3 Impulse withstand voltage10.9.4 Testing of enclosures made of insulating material10.10 Temperature rise Application notes BrochuresCatalogs Certification reportsDrawingseCAD model Installation instructions Installation videosEaton Corporation plc Eaton House30 Pembroke Road Dublin 4, Ireland © 2023 Eaton. All Rights Reserved. Eaton is a registered trademark.All other trademarks areproperty of their respectiveowners./socialmediacalculation. Eaton will provide heat dissipation data for the devices.Is the panel builder's responsibility. The specifications for the switchgear must be observed.Is the panel builder's responsibility. The specifications for the switchgear must be observed.The device meets the requirements, provided the information in the instruction leaflet (IL) is observed.Rapid Link 5MN040003_EN MN034004ENramo5_v4.stp ramo5_v4.dwg10.11 Short-circuit rating10.12 Electromagnetic compatibility 10.13 Mechanical function Manuals and user guides mCAD model。
艾顿Moeller系列Rapid Link速控器198917说明书
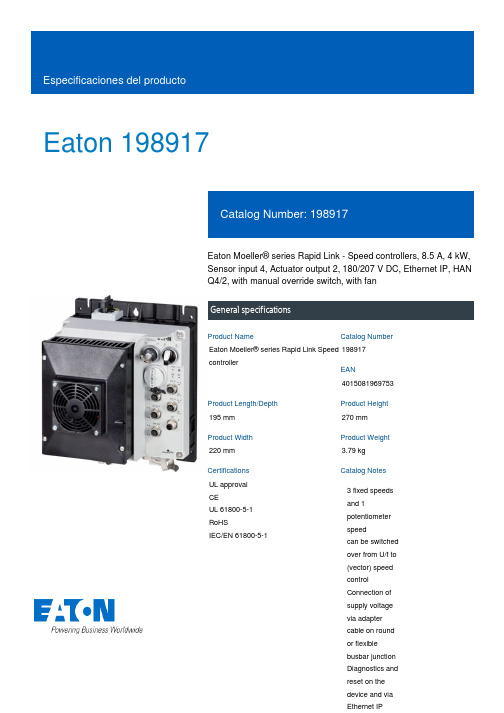
Eaton 198917Eaton Moeller® series Rapid Link - Speed controllers, 8.5 A, 4 kW, Sensor input 4, Actuator output 2, 180/207 V DC, Ethernet IP, HAN Q4/2, with manual override switch, with fanGeneral specificationsEaton Moeller® series Rapid Link Speed controller1989174015081969753195 mm 270 mm 220 mm 3.79 kg UL approval CEUL 61800-5-1 RoHSIEC/EN 61800-5-1Product NameCatalog NumberEANProduct Length/Depth Product Height Product Width Product Weight Certifications Catalog Notes 3 fixed speeds and 1 potentiometer speedcan be switched over from U/f to (vector) speed control Connection of supply voltage via adapter cable on round or flexible busbar junction Diagnostics and reset on the device and via Ethernet IP480 VIs the panel builder's responsibility. The specifications for the switchgear must be observed.400 V AC, 3-phase480 V AC, 3-phaseMeets the product standard's requirements.4 kW500 VMeets the product standard's requirements.-40 °C380 VFanInternal DC linkIGBT inverterPTC thermistor monitoringManual override switchKey switch position OFF/RESETSelector switch (Positions: REV - OFF - FWD)Key switch position HANDControl unitKey switch position AUTOThermo-click with safe isolation2 Actuator outputsPC connectionTwo sensor inputs through M12 sockets (max. 150 mA) for quick stop and interlocked manual operation0 Hz eaton-bus-adapter-rapidlink-speed-controller-dimensions-004.eps eaton-bus-adapter-rapidlink-speed-controller-dimensions-002.eps eaton-bus-adapter-rapidlink-speed-controller-dimensions-003.eps eaton-bus-adapter-rapidlink-speed-controller-dimensions-005.epsETN.RASP5-8421EIP-412R001S1.edzRapid Link 5 - brochureDA-SW-drivesConnect - installation helpDA-SW-Driver DX-CBL-PC-3M0DA-SW-drivesConnectDA-SW-USB Driver DX-COM-STICK3-KITDA-SW-USB Driver PC Cable DX-CBL-PC-1M5DA-SW-drivesConnect - InstallationshilfeMaterial handling applications - airports, warehouses and intra-logisticsIL034093ZUramo5_v32.dwgrasp5_v32.stpGeneration Change RASP4 to RASP5Generation Change RA-SP to RASP5Generation change from RA-SP to RASP 4.0Generation change from RA-MO to RAMO 4.0Configuration to Rockwell PLC for Rapid LinkGeneration change RAMO4 to RAMO5DA-DC-00004514.pdfDA-DC-00003964.pdfDA-DC-00004184.pdfDA-DC-00004508.pdfMains voltage - max10.11 Short-circuit ratingRated operational voltage10.4 Clearances and creepage distancesOutput at quadratic load at rated output voltage - max Output voltage - max10.2.3.1 Verification of thermal stability of enclosures Ambient storage temperature - minMains voltage - minFitted with:Output frequency - minStarting current - max DibujoseCAD modelFolletosInstrucciones de instalación mCAD modelNotas de aplicación Reportes de certificaciones200 %, IH, max. starting current (High Overload), For 2 seconds every 20 seconds, Power sectionRated conditional short-circuit current (Iq)10 kAAmbient operating temperature - max40 °CCommunication interfaceEthernet IP, built inAssigned motor power at 115/120 V, 60 Hz, 1-phase5 HPOutput frequency - max500 HzSwitching frequency8 kHz, 4 - 32 kHz adjustable, fPWM, Power section, Main circuitFeaturesParameterization: KeypadInternal and on heat sink, temperature-controlled Fan Parameterization: FieldbusParameterization: drivesConnect mobile (App) Parameterization: drivesConnectAmbient operating temperature - min-10 °CBraking current≤ 0.6 A (max. 6 A for 120 ms), Actuator for external motor brakeNumber of HW-interfaces (serial TTY)10.6 Incorporation of switching devices and componentsDoes not apply, since the entire switchgear needs to be evaluated.Nominal output current I2N8.5 A10.2.6 Mechanical impactDoes not apply, since the entire switchgear needs to be evaluated.10.3 Degree of protection of assembliesDoes not apply, since the entire switchgear needs to be evaluated.Product categorySpeed controllerRadio interference classC1: for conducted emissions onlyC2, C3: depending on the motor cable length, the connected load, and ambient conditions. External radio interference suppression filters (optional) may be necessary.Heat dissipation capacity Pdiss0 WRated control voltage (Uc)180/207 V DC (external brake 50/60 Hz)24 V DC (-15 %/+20 %, external via AS-Interface® plug)Assigned motor power at 460/480 V, 60 Hz, 3-phase5 HPNumber of HW-interfaces (RS-422)Mains current distortion120 %ProtocolEtherNet/IP10.9.2 Power-frequency electric strengthIs the panel builder's responsibility.Overvoltage categoryIIIDegree of protectionNEMA 12IP65Ambient storage temperature - max70 °CRated impulse withstand voltage (Uimp)2000 VConnectionPlug type: HAN Q4/2Overload currentAt 40 °CFor 60 s every 600 sFunctionsFor actuation of motors with mechanical brake3 fixed speeds1 potentiometer speedOutput at linear load at rated output voltage - max4 kWMains voltage tolerance380 - 480 V (-10 %/+10 %, at 50/60 Hz)Leakage current at ground IPE - max3.5 mAConverter typeU converter10.2.2 Corrosion resistanceMeets the product standard's requirements.Supply frequency50/60 Hz10.2.4 Resistance to ultra-violet (UV) radiationMeets the product standard's requirements.10.2.7 InscriptionsMeets the product standard's requirements.Shock resistance15 g, Mechanical, According to IEC/EN 60068-2-27, 11 ms, Half-sinusoidal shock 11 ms, 1000 shocks per shaftApplication in domestic and commercial area permittedYesNumber of inputs (analog)Number of phases (output)310.12 Electromagnetic compatibilityIs the panel builder's responsibility. The specifications for the switchgear must be observed.10.2.5 LiftingDoes not apply, since the entire switchgear needs to be evaluated.Number of HW-interfaces (RS-485)1Number of HW-interfaces (industrial ethernet)2Efficiency98 % (η)System configuration typePhase-earthed AC supply systems are not permitted.AC voltageCenter-point earthed star network (TN-S network)10.8 Connections for external conductorsIs the panel builder's responsibility.ProtectionFinger and back-of-hand proof, Protection against direct contact (BGV A3, VBG4)Braking voltage280/207 V DC -15 % / +10 %, Actuator for external motor brakeApplication in industrial area permittedYesClimatic proofing< 95 %, no condensationIn accordance with IEC/EN 5017810.9.3 Impulse withstand voltageIs the panel builder's responsibility.Overload current IL at 150% overload12.7 AInput current ILN at 150% overload7.8 ANumber of HW-interfaces (RS-232)Number of inputs (digital)4Current limitationAdjustable, motor, main circuit0.8 - 8.5 A, motor, main circuitCable lengthC3 ≤ 25 m, maximum motor cable lengthC1 ≤ 1 m, maximum motor cable lengthC2 ≤ 5 m, maximum motor cable length10.5 Protection against electric shockDoes not apply, since the entire switchgear needs to be evaluated.Mounting positionVerticalMains switch-on frequencyMaximum of one time every 60 seconds10.13 Mechanical functionThe device meets the requirements, provided the information in the instruction leaflet (IL) is observed.10.9.4 Testing of enclosures made of insulating materialIs the panel builder's responsibility.Heat dissipation per pole, current-dependent Pvid0 WElectromagnetic compatibility1st and 2nd environments (according to EN 61800-3)Resolution0.1 Hz (Frequency resolution, setpoint value)Assigned motor power at 460/480 V, 60 Hz5 HPRelative symmetric net voltage tolerance10 %Rated operational current (Ie)8.5 A at 150% overload (at an operating frequency of 8 kHz and an ambient air temperature of +40 °C)Number of outputs (analog)Rated operational power at 380/400 V, 50 Hz, 3-phase4 kWNumber of HW-interfaces (USB)Operating modeSensorless vector control (SLV)U/f controlBLDC motorsPM and LSPM motorsSynchronous reluctance motorsRated frequency - min45 HzDelay time< 10 ms, On-delay< 10 ms, Off-delayNumber of outputs (digital)2Power consumption95 W10.2.3.2 Verification of resistance of insulating materials to normal heatMeets the product standard's requirements.10.2.3.3 Resist. of insul. mat. to abnormal heat/fire by internal elect. effectsMeets the product standard's requirements.Number of HW-interfaces (other)Rated frequency - max66 HzVibrationResistance: 10 - 150 Hz, Oscillation frequencyResistance: 6 Hz, Amplitude 0.15 mmResistance: 57 Hz, Amplitude transition frequency on accelerationResistance: According to IEC/EN 60068-2-6Short-circuit protection (external output circuits)Type 1 coordination via the power bus' feeder unit, Main circuit10.7 Internal electrical circuits and connectionsIs the panel builder's responsibility.Braking torqueAdjustable to 100 % (I/Ie), DC - Main circuit≤ 30 % (I/Ie)Relative symmetric net frequency tolerance10 %10.10 Temperature riseThe panel builder is responsible for the temperature rise calculation. Eaton will provide heat dissipation data for the devices.Number of HW-interfaces (parallel)Assigned motor power at 230/240 V, 60 Hz, 1-phase5 HPInterfacesMax. total power consumption from AS-Interface® power supply unit (30 V): 250 mASpecification: S-7.4 (AS-Interface®)Number of slave addresses: 31 (AS-Interface®)Eaton Corporation plc Eaton House30 Pembroke Road Dublin 4, Ireland © 2023 Eaton. Todos los derechos reservados. Eaton is a registered trademark.All other trademarks areproperty of their respectiveowners./socialmedia351.6 W at 25% current and 0% speed 53.8 W at 25% current and 50% speed 60.9 W at 50% current and 0% speed 64 W at 50% current and 90% speed 65.4 W at 50% current and 50% speed 85.1 W at 100% current and 0% speed 94 W at 100% current and 50% speed 95.3 W at 100% current and 90% speed 0Above 1000 m with 1 % performance reduction per 100 m Max. 2000 mNumber of phases (input)Heat dissipation at current/speed Number of interfaces (PROFINET)Altitude。
Eaton RTLO-13和RTLO-18手动变速箱产品介绍说明书
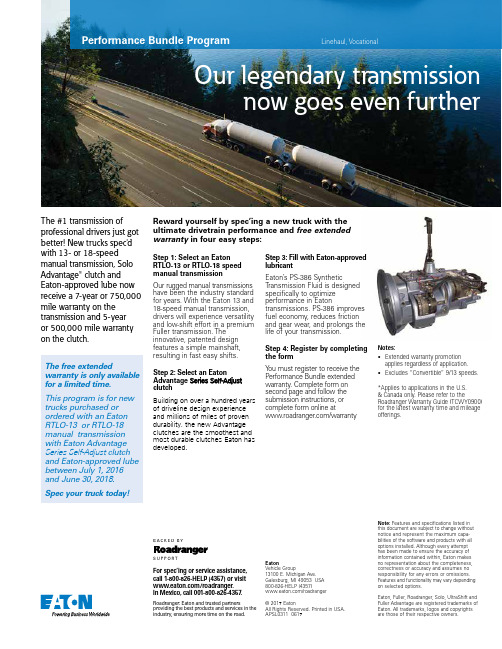
Performance Bundle ProgramThe #1 transmission ofprofessional drivers just gotbetter! New trucks spec'dwith 13- or 18-speedmanual transmission, SoloAdvantage® clutch andEaton-approved lube nowreceive a 7-year or 750,000mile warranty on thetransmission and 5-yearor 500,000 mile warrantyon the clutch.Linehaul, VocationalStep 1: Select an Eaton RTLO-13 or RTLO-18 speed manual transmissionOur rugged manual transmissions have been the industry standard for years. With the Eaton 13 and 18-speed manual transmission, drivers will experience versatility and low-shift effort in a premium Fuller transmission. The innovative, patented design features a simple mainshaft, resulting in fast easy shifts.Step 2: Select an Eaton Advantage Series Self-Adjust clutchBuilding on over a hundred years of driveline design experience and millions of miles of proven durability, the new Advantage clutches are the smoothest and most durable clutches Eaton has developed.Step 3: Fill with Eaton-approvedlubricantEaton’s PS-386 SyntheticTransmission Fluid is designedspecifically to optimizeperformance in Eatontransmissions. PS-386 improvesfuel economy, reduces frictionand gear wear, and prolongs thelife of your transmission.Step 4: Register by completingthe formY ou must register to receive thePerformance Bundle extendedwarranty. Complete form onsecond page and follow thesubmission instructions, orcomplete form online at/warranty*Applies to applications in the U.S.& Canada only. Please refer to theRoadranger Warranty Guide (TCWY0900)for the latest warranty time and mileageofferings.Notes:•Extended warranty promotionapplies regardless of application.•Excludes “Convertible” 9/13 speeds.S U P P O R TB AC K ED B YFor spec’ing or service assistance, call 1-800-826-HELP (4357) or visit /roadranger.In Mexico, call 001-800-826-4357. Roadranger: Eaton and trusted partners providing the best products and services in the industry, ensuring more time on the road.EatonVehicle Group13100 E. Michigan Ave.Galesburg, MI 49053 USA800-826-HELP (4357)/roadranger© 2017 EatonAll Rights Reserved. Printed in USA.APSL0311 0617Note: Features and specifications listed inthis document are subject to change withoutnotice and represent the maximum capa-bilities of the software and products with alloptions installed. Although every attempthas been made to ensure the accuracy ofinformation contained within, Eaton makesno representation about the completeness,correctness or accuracy and assumes noresponsibility for any errors or omissions.Features and functionality may vary dependingon selected options.Eaton, Fuller, Roadranger, Solo, UltraShift andFuller Advantage are registered trademarks ofEaton. All trademarks, logos and copyrightsare those of their respective owners.Reward yourself by spec’ing a new truck with theultimate drivetrain performance and free extendedwarranty in four easy steps:The free extendedwarranty is only availablefor a limited time.This program is for newtrucks purchased orordered with an EatonRTLO-13 or RTLO-18manual transmissionwith Eaton AdvantageSeries Self-Adjust clutchand Eaton-approved lubebetween July 1, 2016and June 30, 2018.Spec your truck today!Performance T ransmission Bundle Warranty Registration FormUse this form to activate extended warranty on:•Eaton RTLO-13 or RTLO-18 manual transmission •Eaton Advantage Series Self-Adjust clutchPerformance Bundle Warranty Instructions:1.Purchase of Eaton RTLO-13 or RTLO-18 speed manual transmission (models include RTLO-16913A, RTLO-18913A, RTLO-20913A, RTLO-16918B, RTLO-18918B, RTLO-20918B or RTLO-22918B), Eaton Advantage Series Self-Adjust clutch and Eaton-approved synthetic lubricant is required to activate extended warranty.2.Please enclose proof of purchase or repair order listing transmission and clutch along with this form to activate the warranty.3.Coverage confirmation will be sent by USPS mail.4.Convertible 9/13 speeds are not included in this program.Step 1: Enter owner/dealer informationOwner:____________________________________________________________Address:__________________________________________________________City:______________________________________________________________State/Prov:________________________ Postal Code:_____________________Phone:____________________________________________________________Email:____________________________________________________________Step 2: Enter vehicle/component informationOEM __________________________________ Date-In-Service ________________________Chassis VIN (17 characters): _______________________________________________________________________________________________________________T ransmission Model: ___________________________________________________ T ransmission Serial: ________________________________________________Clutch Part No.: ______________________________________________________ _Vehicle vocation (choose one only -– all applications qualify for this extended warranty promotion)Standard DutyRecreation Vehicleransit CoachSevere DutyHeavy Haulard TractorStep 3: Mail, fax or email this completed form with proof of purchase to:Mail: EatonFax:Email:c/o 360 Services, Inc.1-734-591-7899******************************275 E. 12 Mile Rd.Madison Heights, MI 48071Dealer Code:______________________________________________________Dealer:____________________________________________________________Dealer Contact:_____________________________________________________Dealer Contact Email:______________________________________________Address:__________________________________________________________City:______________________________________________________________State/Prov:________________________ Postal Code:_____________________Phone:____________________________________________________________S U P P O R T B A C K E D B Y© 2017 EatonCheck here for email confirmation of warranty submission (please ensure you enter your email address above).。
Eaton Moeller 系列快速链接速控器 198982 产品说明说明书
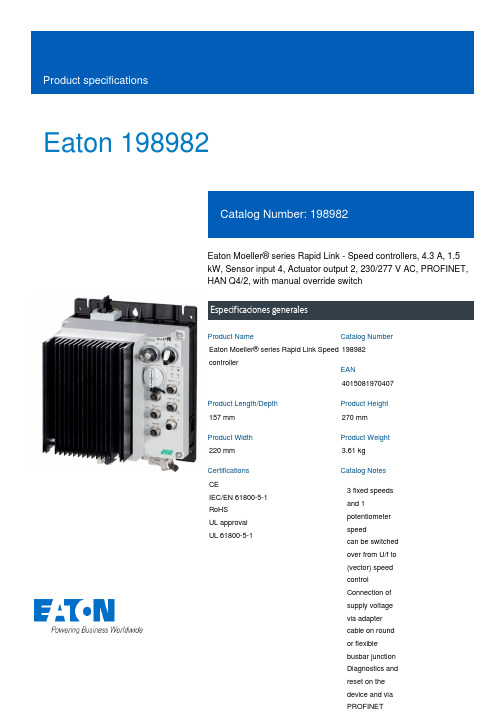
Eaton 198982Eaton Moeller® series Rapid Link - Speed controllers, 4.3 A, 1.5 kW, Sensor input 4, Actuator output 2, 230/277 V AC, PROFINET, HAN Q4/2, with manual override switchEspecificaciones generalesEaton Moeller® series Rapid Link Speed controller1989824015081970407157 mm 270 mm 220 mm 3.61 kg CEIEC/EN 61800-5-1 RoHS UL approval UL 61800-5-1Product NameCatalog NumberEANProduct Length/Depth Product Height Product Width Product Weight Certifications Catalog Notes 3 fixed speeds and 1 potentiometer speedcan be switched over from U/f to (vector) speed control Connection of supply voltage via adapter cable on round or flexible busbar junction Diagnostics and reset on the device and via PROFINET480 VIs the panel builder's responsibility. The specifications for the switchgear must be observed.480 V AC, 3-phase400 V AC, 3-phaseMeets the product standard's requirements.1.5 kW500 VMeets the product standard's requirements.-40 °C380 VKey switch position OFF/RESETSelector switch (Positions: REV - OFF - FWD)Key switch position AUTOPTC thermistor monitoringManual override switchKey switch position HANDControl unitTwo sensor inputs through M12 sockets (max. 150 mA) for quick stop and interlocked manual operationInternal DC linkPC connectionIGBT inverterThermo-click with safe isolation2 Actuator outputs0 Hz200 %, IH, max. starting current (High Overload), For 2 seconds eaton-bus-adapter-rapidlink-speed-controller-dimensions-002.eps eaton-bus-adapter-rapidlink-speed-controller-dimensions-004.eps eaton-bus-adapter-rapidlink-speed-controller-dimensions-005.eps eaton-bus-adapter-rapidlink-speed-controller-dimensions-003.epsETN.RASP5-4422PNT-412R000S1.edzRapid Link 5 - brochureDA-SW-USB Driver DX-COM-STICK3-KITDA-SW-drivesConnect - InstallationshilfeDA-SW-USB Driver PC Cable DX-CBL-PC-1M5DA-SW-drivesConnect - installation helpDA-SW-Driver DX-CBL-PC-3M0DA-SW-drivesConnectMaterial handling applications - airports, warehouses and intra-logisticsDA-DC-00004184.pdfDA-DC-00003964.pdfDA-DC-00004514.pdfDA-DC-00004508.pdfIL034093ZUrasp5_v31.stpramo5_v31.dwgGeneration Change RA-SP to RASP5Configuration to Rockwell PLC for Rapid LinkGeneration change from RA-MO to RAMO 4.0Generation change from RA-SP to RASP 4.0Generation Change RASP4 to RASP5Generation change RAMO4 to RAMO5Mains voltage - max10.11 Short-circuit ratingRated operational voltage10.4 Clearances and creepage distancesOutput at quadratic load at rated output voltage - max Output voltage - max10.2.3.1 Verification of thermal stability of enclosures Ambient storage temperature - minMains voltage - minFitted with:Output frequency - minStarting current - max DibujoseCAD modelFolletosInformes de certificaciónInstrucciones de montaje mCAD modelNotas de aplicaciónevery 20 seconds, Power sectionRated conditional short-circuit current (Iq)10 kAAmbient operating temperature - max40 °CCommunication interfacePROFINET, optionalAssigned motor power at 115/120 V, 60 Hz, 1-phase2 HPOutput frequency - max500 HzSwitching frequency8 kHz, 4 - 32 kHz adjustable, fPWM, Power section, Main circuitFeaturesParameterization: drivesConnectParameterization: KeypadParameterization: drivesConnect mobile (App) Parameterization: FieldbusAmbient operating temperature - min-10 °CBraking current≤ 0.6 A (max. 6 A for 120 ms), Actuator for external motor brakeNumber of HW-interfaces (serial TTY)10.6 Incorporation of switching devices and componentsDoes not apply, since the entire switchgear needs to be evaluated.Nominal output current I2N4.3 A10.2.6 Mechanical impactDoes not apply, since the entire switchgear needs to be evaluated.10.3 Degree of protection of assembliesDoes not apply, since the entire switchgear needs to be evaluated.Product categorySpeed controllerRadio interference classC1: for conducted emissions onlyC2, C3: depending on the motor cable length, the connected load, and ambient conditions. External radio interference suppression filters (optional) may be necessary.Heat dissipation capacity Pdiss0 WRated control voltage (Uc)24 V DC (-15 %/+20 %, external via AS-Interface® plug) 230/277 V AC (external brake 50/60 Hz)Assigned motor power at 460/480 V, 60 Hz, 3-phase2 HPNumber of HW-interfaces (RS-422)Mains current distortion120 %ProtocolPROFINET IO10.9.2 Power-frequency electric strengthIs the panel builder's responsibility.Overvoltage categoryIIIDegree of protectionIP65NEMA 12Ambient storage temperature - max70 °CRated impulse withstand voltage (Uimp)2000 VConnectionPlug type: HAN Q4/2Overload currentAt 40 °CFor 60 s every 600 sFunctions1 potentiometer speed3 fixed speedsFor actuation of motors with mechanical brakeOutput at linear load at rated output voltage - max1.5 kWMains voltage tolerance380 - 480 V (-10 %/+10 %, at 50/60 Hz)Leakage current at ground IPE - max3.5 mAConverter typeU converter10.2.2 Corrosion resistanceMeets the product standard's requirements.Supply frequency50/60 Hz10.2.4 Resistance to ultra-violet (UV) radiationMeets the product standard's requirements.10.2.7 InscriptionsMeets the product standard's requirements.Shock resistance15 g, Mechanical, According to IEC/EN 60068-2-27, 11 ms, Half-sinusoidal shock 11 ms, 1000 shocks per shaftApplication in domestic and commercial area permittedYesNumber of inputs (analog)Number of phases (output)310.12 Electromagnetic compatibilityIs the panel builder's responsibility. The specifications for the switchgear must be observed.10.2.5 LiftingDoes not apply, since the entire switchgear needs to be evaluated.Number of HW-interfaces (RS-485)1Number of HW-interfaces (industrial ethernet)Efficiency98 % (η)System configuration typeAC voltageCenter-point earthed star network (TN-S network)Phase-earthed AC supply systems are not permitted.10.8 Connections for external conductorsIs the panel builder's responsibility.ProtectionFinger and back-of-hand proof, Protection against direct contact (BGV A3, VBG4)Braking voltage230/277 V AC -15 % / +10 %, Actuator for external motor brakeApplication in industrial area permittedYesClimatic proofing< 95 %, no condensationIn accordance with IEC/EN 5017810.9.3 Impulse withstand voltageIs the panel builder's responsibility.Overload current IL at 150% overload6.5 AInput current ILN at 150% overload4.1 ANumber of HW-interfaces (RS-232)Number of inputs (digital)4Current limitationAdjustable, motor, main circuit0.4 - 4.3 A, motor, main circuitCable lengthC3 ≤ 25 m, maximum motor cable lengthC1 ≤ 1 m, maximum motor cable lengthC2 ≤ 5 m, maximum motor cable length10.5 Protection against electric shockDoes not apply, since the entire switchgear needs to be evaluated.Mounting positionVerticalMains switch-on frequencyMaximum of one time every 60 seconds10.13 Mechanical functionThe device meets the requirements, provided the information in the instruction leaflet (IL) is observed.10.9.4 Testing of enclosures made of insulating materialIs the panel builder's responsibility.Heat dissipation per pole, current-dependent Pvid0 WElectromagnetic compatibility1st and 2nd environments (according to EN 61800-3)Resolution0.1 Hz (Frequency resolution, setpoint value)Assigned motor power at 460/480 V, 60 Hz2 HPRelative symmetric net voltage tolerance10 %Rated operational current (Ie)4.3 A at 150% overload (at an operating frequency of 8 kHz and an ambient air temperature of +40 °C)Number of outputs (analog)Rated operational power at 380/400 V, 50 Hz, 3-phase1.5 kWNumber of HW-interfaces (USB)Operating modeSensorless vector control (SLV)BLDC motorsU/f controlSynchronous reluctance motorsPM and LSPM motorsRated frequency - min45 HzDelay time< 10 ms, Off-delay< 10 ms, On-delayNumber of outputs (digital)2Power consumption46 W10.2.3.2 Verification of resistance of insulating materials to normal heatMeets the product standard's requirements.10.2.3.3 Resist. of insul. mat. to abnormal heat/fire by internal elect. effectsMeets the product standard's requirements.Number of HW-interfaces (other)Rated frequency - max66 HzVibrationResistance: 10 - 150 Hz, Oscillation frequencyResistance: 57 Hz, Amplitude transition frequency on accelerationResistance: 6 Hz, Amplitude 0.15 mmResistance: According to IEC/EN 60068-2-6Short-circuit protection (external output circuits)Type 1 coordination via the power bus' feeder unit, Main circuit10.7 Internal electrical circuits and connectionsIs the panel builder's responsibility.Braking torque≤ 30 % (I/Ie)Adjustable to 100 % (I/Ie), DC - Main circuitRelative symmetric net frequency tolerance10 %10.10 Temperature riseThe panel builder is responsible for the temperature rise calculation. Eaton will provide heat dissipation data for the devices.Number of HW-interfaces (parallel)Assigned motor power at 230/240 V, 60 Hz, 1-phase2 HPInterfacesSpecification: S-7.4 (AS-Interface®)Number of slave addresses: 31 (AS-Interface®)Max. total power consumption from AS-Interface® power supply unit (30 V): 250 mANumber of phases (input)3Eaton Corporation plc Eaton House30 Pembroke Road Dublin 4, Ireland © 2023 Eaton. All Rights Reserved. Eaton is a registered trademark.All other trademarks areproperty of their respectiveowners./socialmedia32.3 W at 25% current and 0% speed 33.2 W at 25% current and 50% speed 35.2 W at 50% current and 90% speed 36.2 W at 50% current and 0% speed 37.6 W at 50% current and 50% speed 46.3 W at 100% current and 90% speed 48.7 W at 100% current and 0% speed 48.7 W at 100% current and 50% speed 2Above 1000 m with 1 % performance reduction per 100 m Max. 2000 mHeat dissipation at current/speed Number of interfaces (PROFINET)Altitude。
- 1、下载文档前请自行甄别文档内容的完整性,平台不提供额外的编辑、内容补充、找答案等附加服务。
- 2、"仅部分预览"的文档,不可在线预览部分如存在完整性等问题,可反馈申请退款(可完整预览的文档不适用该条件!)。
- 3、如文档侵犯您的权益,请联系客服反馈,我们会尽快为您处理(人工客服工作时间:9:00-18:30)。
2
第一章 概述
安全 安全总则 通过本手册,重要的安全注意事项有以下几点
警告
表示存在危险,提请用户对操作步骤、实际操作、实际条件等类事项加以注意, 如不正确执行或切实遵守,则有可能会导致人身伤害甚至死亡。
小心
表示存在危险,提请用户对操作步骤、实际操作、实际条件等类事项加以注意,
如不正确执行或切实遵守,则有可能会导致本产品部分或者全部发生损坏甚至损 毁。
注意 对重要信息进行强调。提请用户对必要的操作步骤、实际操作、
实际条件等类事项加以注意。
和产品有关安全警事项 您手中的Model 2061烟气湿度仪已由工厂进行安全测试和审核。请注意以下几点
警告 将机器接地,定期检查装置避免被雷击。
小心 不要修改计量单位,不当修改会损坏机器导致故障。
防静电保护 静电放电会直接或间接损坏电子电路。本公司的产品有充分的防静电措施。但在 触摸/移动设备内部电路或在设备内部接入其他设备时时,仍有可能产生静电损 害。 为了防止高压静电损害: —请在防静电工作台以及合理接地的情况下,处理静电敏感元件。
第二章 概述........................................................5 部件说明................................................... 6
第三章 安装........................................................7
7
电缆接线 配套使用带屏蔽的4芯电缆作为模拟输出/串口通讯电缆。电缆的定义与号码管的 对应如下:
220V-PE = 地 220V-L = 220VAC火线 220V-N = 220VAC零线 H2O(4-20mA+) =烟气湿度H2O输出信号的电缆+ H2O(4-20mA-) = 烟气湿度H2O输出信号的电缆-
4
第二章 概述
高温烟气一般指火电行业燃煤发电工程产生的气体,作为一种比较特殊的介 质,一般的温度范围在40-150度,特别情况下可能达到160度,另外烟气中一般 会存在粉尘和酸性物质如SO2、NOX等,如何克服高温、高粉尘和酸性物质而保证 烟气水分的在线测量,是一个十分困难的问题,目前在国内一般通过测量干湿烟 气中的氧量,通过计算获得烟气水分,是一种间接测量的方法,这种方法存在的 主要问题是测量值滞后而测量的精度低,不能满足高温烟气测量的需要。
从低湿到高湿环境:10S
湿度传感器:
阻容式
温度传感器:
PT100 铂电阻
输出信号:
4…20mA
供电电源:
24VDC
模拟输出外接负载:
最大 500Ω(对地)
电流消耗:
最大 2 A
功耗(最大):
25W
工作温度范围:
传感器:
-40…+180°C
变送器及控制部分:
-10…+55°C
储存温度:
-40…+80°C
减震材料以保护设备。请将报告一并放到箱中。 6. 将箱子寄到:
3
—如果上述情况不可能,在接触电路板前应释放身上静电。操作者应佩戴防静电 手腕和阻性接线塞绳。 —若上述情况不可能,应一只手接触导电体,另一只手触摸电路板。 —尽量把持电路板边缘,避免与元器件的直接接触。 环保
循环使用可再生材料。
根据当地法令处理废旧电池和仪表。不要和家庭垃圾一并处 理。
反馈 雪迪龙公司欢迎我们的用户对我们说明书的质量提出宝贵的意见和建议。如
第六章 校准和调校 校准.......................................................14
第七章 技术规范.................................................15 性能 ......................................................15 技术支持...................................................16 返修说明...................................................16
5
部件说明
图1 湿度仪结构示意图 数字对应上面的图1: 1 =加热线样气进口:Φ6mm,卡套式接头。 2 =烟气湿度仪(变送器、信号模块和加热部分等) 3 =样气出口: Φ6mm,卡套式接头。 4=加热指示灯 5=RS232接口
6
湿度仪安装示意图如图2,
第三章 安装
图2 湿度仪安装示意图 数字对应上图2 1 =加热线 2 =样气进口:Φ6mm,卡套式接头 3 =样气出口: Φ6mm,卡套式接头。 4 =供电电源线 5 =输出信号线 6=加热指示灯 7=RS232接口
操作手册
Model 2061 烟气湿度仪
北京雪迪龙自动控制系统有限公司
2009-1-12
未经版权持有人的事先书面许可,不得以任何形式或者任何手段,无论是电子的还是机械的 (其中包括影印),对本手册任何部分进行复制,也不得将其内容传达给第三方。 本说明手册内容如有变更,恕不另行通知。 需要注意的是此操作手册对客户并没有法律效力,双方的权利义务由双方的合同和销售当时 的情况而定。
针对上述现有技术的不足,Model 2061烟气湿度仪采用一种能克服高温烟气 的粉尘、高温和酸性腐蚀问题、可以在线长期稳定的测量高温烟气中水分的防磨 损和防腐蚀装置,以有效保护在线阻容式高温烟气水分仪,并在不影响测量精度 的条件下实现长期可靠的工作。
本操作手册介绍了关于雪迪龙公司Model 2061系列烟气湿度仪的安装、操作、 和维修。 Model 2061烟气湿度仪的测量范围是0-40Vol%。
果您发现了错误或是由其他改进的意见,请注明章节,段落,和页数。 许可证协议
雪迪龙公司和第三方拥有软件的所有权,用户只有在签订了合同或软件使用 许可证后方可使用。 质保
雪迪龙公司对本产品有为期一年的质保。质保不包括正常的磨损,非正常情 况的操作,安装和操作的疏忽,或是未经授权的改动。请注意供应合同或销售合 同关于每台机器质保的细节
常见的水分测量方法有:冷凝法,干湿球法,称重法,露点法和电子式传感 器法。电子式水分传感器产品及水分测量属于90年代兴起的行业,近年来,国内 外在水分传感器研发领域取得了长足进步,气体水分的测量在国外目前的发展方 向主要是利用电容式电子测量技术,但应用于高温烟气的测量,需要克服烟气高 温、灰尘、酸性物质对高分子薄膜电容的磨损和腐蚀问题。
服务端口的串口通信设置默认值
参数
值
波特率
2400
奇偶校验
无
数据位
8
停止位
1
流控制
无
用串口命令调校PPMV
1.至少要在5小时内保持传感器稳定。
2.将串口波特率调至2400bit
3. 等至少 1 个小时。
modi PPMV xx
用串口命令modi PPMV xx进行PPMV的调校。
用modi PPMV xx 命令进行调校。用 modi PPMV ? 查询修正PPMV
9
安装开孔尺寸图
10
第四章 操作
本章包括了操作该产品所需信息。 开始
Model 2061水分仪的启动时间总共大概20分钟。在 Model 2061上电后自动 进入启动预热状态,过完成后, 进入测量状态,输出数据正式启动。
11
串口通信
使用服务端口连接串口进行的RS-232连接。服务端口工作于固定的串口设置。
1
目
录
第一章 概述...................................................... 3 安全....................................................... 3 安全总则................................................... 3 和产品有关的安全注意事项................................... 3 防静电保护................................................. 3 环保........................................................4 反馈........................................................4 商标........................................................4 许可证协议................................................ 4 质保....................................................... 4
工作环境湿度:
0…100%RH
设备全重:
<1 Kg
15
技术支持 技术问题,请与技术部联系: E-mail Fax
返修说明 如果产品需要维修,请遵循以下说明以加快进程,避免额外成本。 1. 阅读质保信息。 2. 填写问题报告,并附上能对所述问题提供更多建议的技术人员的姓名和联
系方式。 3. 报告上请说明: -什么问题(什么工作/什么不工作)? -哪里出现的问题(位置和环境)? -什么时候出现的问题(日期,当时/不久前/周期性的/随意的) -多少问题(一个/其他或类似的/一个个体内的几个错误)? 4. 报告上要有详细寄信人地址,首选的运输方式。 5. 将问题设备装好,放到一个适合的结实的箱子中,要在箱子里填充缓冲及
例如:
>modi PPMV 0.5
OK
此时PPMV已经修正0.5%,可以用查询命令查看修正值。